粉体混合技术和原理分析
固体药物制剂工艺的混合过程及混合机理
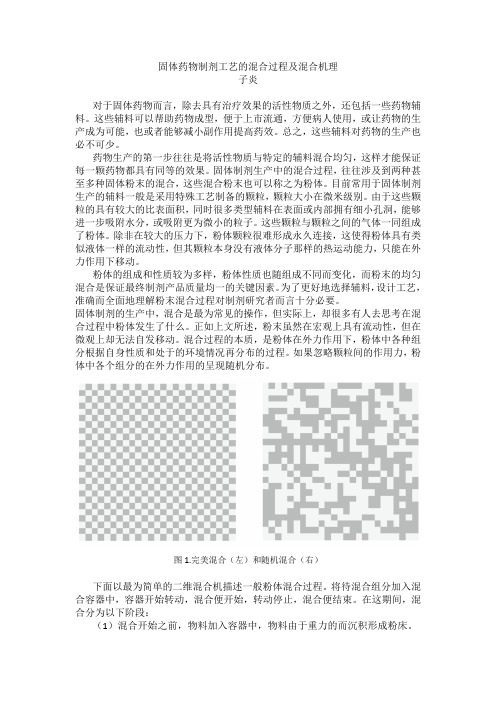
固体药物制剂工艺的混合过程及混合机理子炎对于固体药物而言,除去具有治疗效果的活性物质之外,还包括一些药物辅料。
这些辅料可以帮助药物成型,便于上市流通,方便病人使用,或让药物的生产成为可能,也或者能够减小副作用提高药效。
总之,这些辅料对药物的生产也必不可少。
药物生产的第一步往往是将活性物质与特定的辅料混合均匀,这样才能保证每一颗药物都具有同等的效果。
固体制剂生产中的混合过程,往往涉及到两种甚至多种固体粉末的混合,这些混合粉末也可以称之为粉体。
目前常用于固体制剂生产的辅料一般是采用特殊工艺制备的颗粒,颗粒大小在微米级别。
由于这些颗粒的具有较大的比表面积,同时很多类型辅料在表面或内部拥有细小孔洞,能够进一步吸附水分,或吸附更为微小的粒子。
这些颗粒与颗粒之间的气体一同组成了粉体。
除非在较大的压力下,粉体颗粒很难形成永久连接,这使得粉体具有类似液体一样的流动性,但其颗粒本身没有液体分子那样的热运动能力,只能在外力作用下移动。
粉体的组成和性质较为多样,粉体性质也随组成不同而变化,而粉末的均匀混合是保证最终制剂产品质量均一的关键因素。
为了更好地选择辅料,设计工艺,准确而全面地理解粉末混合过程对制剂研究者而言十分必要。
固体制剂的生产中,混合是最为常见的操作,但实际上,却很多有人去思考在混合过程中粉体发生了什么。
正如上文所述,粉末虽然在宏观上具有流动性,但在微观上却无法自发移动。
混合过程的本质,是粉体在外力作用下,粉体中各种组分根据自身性质和处于的环境情况再分布的过程。
如果忽略颗粒间的作用力,粉体中各个组分的在外力作用的呈现随机分布。
图1.完美混合(左)和随机混合(右)下面以最为简单的二维混合机描述一般粉体混合过程。
将待混合组分加入混合容器中,容器开始转动,混合便开始,转动停止,混合便结束。
在这期间,混合分为以下阶段:(1)混合开始之前,物料加入容器中,物料由于重力的而沉积形成粉床。
(2)仪器开始运转,容器的运动对粉末中粒子产生了作用力,粒子之间的作用力被激活,粒子之间形成间隙,这些间隙使得不同组分的粒子的穿插和交织成为可能。
粉末混合工艺
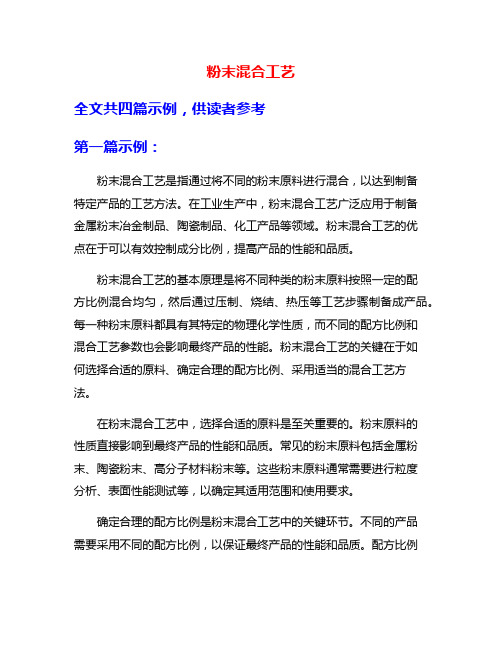
粉末混合工艺全文共四篇示例,供读者参考第一篇示例:粉末混合工艺是指通过将不同的粉末原料进行混合,以达到制备特定产品的工艺方法。
在工业生产中,粉末混合工艺广泛应用于制备金属粉末冶金制品、陶瓷制品、化工产品等领域。
粉末混合工艺的优点在于可以有效控制成分比例,提高产品的性能和品质。
粉末混合工艺的基本原理是将不同种类的粉末原料按照一定的配方比例混合均匀,然后通过压制、烧结、热压等工艺步骤制备成产品。
每一种粉末原料都具有其特定的物理化学性质,而不同的配方比例和混合工艺参数也会影响最终产品的性能。
粉末混合工艺的关键在于如何选择合适的原料、确定合理的配方比例、采用适当的混合工艺方法。
在粉末混合工艺中,选择合适的原料是至关重要的。
粉末原料的性质直接影响到最终产品的性能和品质。
常见的粉末原料包括金属粉末、陶瓷粉末、高分子材料粉末等。
这些粉末原料通常需要进行粒度分析、表面性能测试等,以确定其适用范围和使用要求。
确定合理的配方比例是粉末混合工艺中的关键环节。
不同的产品需要采用不同的配方比例,以保证最终产品的性能和品质。
配方比例经常通过试验和实践来确定,通常需要考虑到原料的化学成分、物理性质、烧结性能等因素。
混合工艺方法的选择也对最终产品的性能有重要影响。
常见的混合工艺方法包括机械混合、溶液混合、气液混合等。
机械混合是最常用的混合工艺方法,通过搅拌、研磨等机械力作用将粉末原料混合均匀。
溶液混合则是将粉末原料溶解在溶剂中,再进行混合。
气液混合则是将气体和液体一起混合,常用于颗粒状粉末原料的混合。
粉末混合工艺是一种重要的工艺方法,广泛应用于工业生产中。
通过选择合适的原料、确定合理的配方比例、采用适当的混合工艺方法,可以制备出高性能、高品质的产品。
粉末混合工艺的发展也为工业生产提供了更多的可能性,促进了产品的创新和升级。
希望随着科技的不断进步,粉末混合工艺能够得到更大的发展和应用。
第二篇示例:粉末混合工艺是工业生产中常用的一种工艺方法,它主要用于将不同性质的粉末原料混合在一起,以制备出符合特定要求的混合物。
粉体混合原理及常见工艺难题

粉体混合原理及常见工艺难题文章阐述了粉体混合的机理和影响混合的主要物理特性。
总结了粉体混合在实践过程常见的工艺难题,并对如何解决进行了探讨。
标签:粉体混合;颗粒;机理;影响因素混合是将不同物理性质和化学性质的颗粒在空间上分布均匀的过程[1],是两种以上的固态粉体物料在外力的作用下,其不均匀性降到最低的过程[2]。
如对粉末冶金生产而言,粉体混合質量将直接影响粉末冶金零件的内在质量。
1 混合的机理粉末混合的方法和所用的设备不一样,混合的效果肯定不一样,但是混合机理是基本相同的。
(1)扩散混合:粉体小规模分层扩散移动,在外力作用下分离的粉体移动到不断展现的新生层面上,使各组粉体在局部氛围内扩散实现分布均匀。
(2)对流混合:粉体大规模的随机移动,粉体在外力作用下产生类似流体的运动,粉体从物料的一处移至另一处,使粉体在大范围内对流实现均匀分布。
(3)剪切混合:对粉体物料团内进行剪切,在外力的作用下粉体间出现相互滑移现象,形成滑移面,使局部的粉体不断被剪切实现均匀分布。
以上三种混合原理虽各有不同,但是共同的本质则是施加适当形式的外力使混合物中各种组分粉体产生相互间的相对位移,这是发生混合的必要的条件。
不少学者把粉体混合的各个阶段大致用图1来标示[3]。
从图中分析得出,粉体混合的第Ⅰ阶段表现为宏观整体混合很快,为对流混合;第Ⅱ阶段的混合速度有所减慢,是对流和剪切的共同作用阶段;第Ⅲ阶段时,粉体的混合均匀度在某一值上下波动,表明粉体的混合与分离相平衡,粉体处于微观阶段,为扩散混合阶段[4]。
由于粉体本身的物化性质不同、设备结构与操作条件的不同,实际生产中粉体的混合过程是一个很复杂的过程,不仅可能三种混合方式同时存在,而且混合的常常伴随着粉体颗粒的分离。
(4)混合的随机性:以粒度相同的两种等量物料固体A和固体B混合为例,如A与B的密度相同,在理论上似可轻易达到完全的混合状态,只要使A和B 相互交错排列,即达到完全的理想的混合。
一种粉体混合方法

一种粉体混合方法粉体混合是一种在工业生产中非常常见的操作,主要用于将两种或更多种粉体物料混合在一起,以获得所需的均匀性和一致性。
粉体混合方法有很多种,每种方法有其特点和适用范围。
在下面的回答中,我将介绍几种常见的粉体混合方法。
1. 干式混合法:这种方法是将各种粉体物料直接加入混合设备中进行混合。
常见的设备包括高速混合器、卧式混合机和飞行式混合器等。
这种方法适用于对混合时间和混合速度要求较高的情况,但在处理某些易漂浮的物料时可能存在一定的困难。
2. 液体喷雾混合法:这是一种将液体添加到粉体物料中以实现混合的方法。
液体可以是水、溶液或悬浮液等。
这种方法通常使用喷雾干燥器或喷雾堆积器等设备。
液体喷雾混合法适用于对粉体物料进行湿式处理或需要加入特定成分的情况。
3. 批量混合法:这是一种将两种或多种粉体物料一次性混合在一起的方法。
通常使用的设备有高速混合机、双锥混合机和螺旋混合机等。
混合效果取决于混合设备的设计和操作条件,因此在使用批量混合法时需要注意设备的选择和操作技巧。
4. 连续混合法:这是一种将两种或多种粉体物料连续加入混合设备进行混合的方法。
常见的设备有连续流化床混合器、连续带式混合器和连续揉捏混合机等。
连续混合法适用于需要连续生产和大批量混合的情况。
5. 球磨混合法:这是一种将粉体物料放入球磨罐中,通过球磨媒体的运动来实现物料的混合的方法。
球磨混合法适用于需要将粉体物料细化和混合的情况,常见的设备有球磨机和三辊磨机等。
以上是几种常见的粉体混合方法,每种方法都有其适用的范围和特点,根据具体的物料性质和生产需求选择合适的混合方法对于确保混合质量和提高生产效率至关重要。
同时,在进行粉体混合操作时,需要注意设备的选型和操作参数的调整,以确保混合过程的稳定性和可靠性。
粉体混料器文献

粉体混料器文献粉体混料器是一种广泛应用于工业生产中的设备,用于混合和均匀分散粉体物料。
本文将介绍粉体混料器的原理、分类、应用领域以及发展趋势。
一、粉体混料器的原理粉体混料器通过机械运动和流体力学原理实现粉体物料的混合。
其主要原理包括:1. 机械运动:粉体混料器中的搅拌装置通过旋转、翻转或振动等运动方式,使粉体物料发生相对位移,从而达到混合的目的。
2. 流体力学原理:粉体物料在混料器中经过搅拌装置的作用,形成了复杂的流动状态,包括对流、弥散、剪切等,促进了物料之间的相互作用和混合。
二、粉体混料器的分类粉体混料器根据不同的混合原理和结构特点,可以分为以下几类:1. 强迫混合器:通过外力的作用,将粉体物料强制进行混合。
常见的强迫混合器有搅拌机、螺旋传送机、刮板混合器等。
2. 自由混合器:粉体物料在混料器中进行自由流动和碰撞,实现混合。
常见的自由混合器有容器式混合器、喷射混合器等。
3. 流化床混合器:粉体物料通过气体的流动形成流化床,在流化床中实现混合。
流化床混合器具有高效、连续运行等优点。
4. 旋转桶混合器:通过旋转桶体使粉体物料进行多向、多轴向的运动,实现混合。
旋转桶混合器适用于对物料要求较高的混合过程。
三、粉体混料器的应用领域粉体混料器在许多工业领域中都有重要应用,特别适用于以下几个方面:1. 化工领域:粉体混料器广泛应用于颜料、染料、塑料、橡胶等化工物料的混合过程。
2. 医药领域:药物的制备过程中需要对不同的成分进行混合,粉体混料器在制药工业中扮演着重要角色。
3. 食品领域:粉体混料器可以用于混合面粉、糖粉、调料等食品原料的加工。
4. 矿山领域:矿石选矿和冶炼过程中,常需要将不同粒度和成分的矿石进行混合,粉体混料器可以满足这一需求。
四、粉体混料器的发展趋势随着科学技术和工业生产的不断发展,粉体混料器也在不断改进和创新。
未来粉体混料器的发展趋势有以下几个方面:1. 数字化控制:通过引入自动化和智能化技术,提高设备的操作精度和稳定性,实现对混合过程的精确控制。
粉体制备原理与技术

粉体制备原理与技术粉体制备是指将原始材料通过机械、化学和物理方法处理,制成粉末状物质的技术。
粉体制备广泛应用于电子材料、陶瓷材料、金属材料、化工原料、医药、食品等领域。
粉体制备的原理和技术主要包括物理方法、机械方法、化学方法三种。
一、物理方法物理方法主要是利用气态、液态、固态外力(如磨削、撞击等)对物料进行处理,从而达到制备粉末的目的。
物理方法包括:1、凝结法凝结法是将高温金属蒸气通过冷凝器冷却,然后在表面沉积下来,形成一定的粉末形态。
凝结法适用于制备高纯度和特殊结构的金属和非金属材料。
2、气溶胶法气溶胶法是将气态的化学物质喷入高温气氛中,形成微米或亚微米细小颗粒,再利用自由下落或超离心等手段进行收集。
气溶胶法适用于制备特殊形态的粉末,如其形态为球状时,制备涂层材料的效果更佳。
3、溶胶-凝胶法溶胶-凝胶法是在液体介质中形成溶胶,利用物理或化学方法处理形成凝胶,再煅烧得到所需的粉末。
溶胶-凝胶法的特点是制备出的产品纯度高、颗粒尺寸均匀,但生产工艺复杂,成本较高。
二、机械方法机械方法主要是利用机械非均相作用力对原材料进行研磨、切割等处理,破碎成为粉末的方法。
机械方法包括:1、球磨法球磨法是一种通过机械碾磨将原料粉碎成微米甚至纳米级的粉末的方法。
通过球磨法制备出的粉末颗粒尺寸分布范围比较小,形态规则,可形成均匀的合金体系。
2、细化法细化法是通过高频振动、喷射流等力学作用和化学反应过程,使材料粉末实现亚微米级、甚至纳米级的颗粒级细化加工。
三、化学方法化学方法即通过化学反应形成晶体或沉淀,再将其煅烧后得到所需的粉末。
化学方法包括:1、软化化学反应法软化化学反应法是通过添加某些试剂,将反应组分分子分解成无机气相分子,而后这些分子再反应成所需的无机晶体,最后制成粉末。
软化化学反应法适用于制备难度较大的无机晶体粉末。
2、锔合成法锔合成法是先将所需的无机或有机化合物溶解在一定的有机溶剂或水溶剂中,制成溶液,然后将其快速蒸发和烘烤,得到所需的粉末。
粉体混合及输送讲解

气力输送特点:
输送过程为密闭式,无粉尘外扬和尘爆,安全可靠,改善了劳 动条件。输送线路简单、灵活,输送距离较大,吨公里运输成本低。 设备简单,投资低。
主要缺点:动力消耗大,噪音大,对物料的粒度(<30mm)、均匀 性、黏度、温度等有一定要求,使用于短途输送。
刮板输送机:在物料装卸、食品、轻工、煤炭、水泥等行业中。 主要种类:普通刮板输送机、埋刮板输送机两种。
刮板输送机
2.6.2气力输送
气力输送也称为管道输送,它是利用气体的流动动能 和压能,携带粉体物料沿管道从一处输送到另一处。
广泛用于各个行业,伴随无菌、卫生、防尘、便捷、 高质量、自动化等高标准工艺要求,气力输送将越来 越成为首选。
带式输送机的输送能力理论计算散体物料输送量:
Q KCvb
式中:
Q ——带式输送机的输送量,t/h;
K ——带上物料断面修正系数,查表;
C ——输送带倾斜角修正系数,查表 ;
——物料堆积密度,t/m3 ;
v ——输送带线速度,一般输送作业取0.8~2.5m/s,
产品检查或分选时取0.05~0.1m/s;
2.5 粉体的混合
物料的混合是最古老的生产工艺过程之一
(1)为了创造良好的反应条件而混合:如水泥原料、 陶瓷原料;
(2)为了提高强度和性能的混合:如冶金原料、玻璃原料; (3)为了提高药效的混合:如制药、药剂、复合药物; (4)为了提高味道和食欲的混合:如食品、烹饪等。
混合类型:
固体与固体、固体与液体、液体与液体、液体与气体、 固体-液体-气体
(4)胶带和螺旋输送为主: 如:煤炭、冶金等。
多组分粉体混合过程的理论分析与实验研究

亦为均化库的结构优化和实际操作参数的选取提供了重要的理论依据。随着科 学的进步与发展,数字图像处理技术已经成为研究颗粒性质的一种新方法,这
种方法使人们对粉体颗粒的微观结构和性质有了更深入的认识,已经成为了颗 粒分析的必要手段之一。论文针对粉粒体具有微观上离散性的特点,对微观性 能、形状各异的水泥熟料、矿渣组成的水泥粉体产品,进行了大量的相关实验 研究(包括各组分物性测定、微观形貌分析、各组成成分的平均原子序数、混 合物的显微图像分析等等),采用扫描电镜的背散射电子成像法对水泥成品的混 合均匀度进行了分析,在实验研究的基础上提出了一种新的、基于图像分析的 对混合料的混合均匀性进行定量分析研究的新方法。这种水泥粉体混合料均匀 性评价的新方法,通过相关工业实践数据的对比分析,证实了它的有效性以及 其具有的独特的优越性。
the
mixing
equipment
to
improve
their
characteristies.Powder mixture is widely used in food,medicine,and material,plastic
and metallurgy industry.The high-efficient mixture
microcosmic discretization.Because of this dual character,the
flow in
pneumatic
mixture
cement
manufacturing and synthetic process is very complex.It is quite the effects and
present,researchers have
粉体混合机的分类原理和阐述

【粉体混合机的分类原理和阐述】金昶泰粉体混合机一般用于粘性或有凝聚性的粉粒体的混合以及粉粒体中添加液体及糊状物料的混合,随着中国工业的不断发展,混合系统及混合设备的发展将越来越强大。
混合覆盖着整个工业领域,如化工、食品、建材、药品、化肥,我们每天每时使用的产品在生产中至少有一步混合工艺。
一、混合原理及概述:混合时要求所有参与混合的物料均匀分布。
混合的程度分为理想混合、随机混合和完全不相混三种状态。
各种物料在混合机械中的混合程度,取决于待混物料的比例、物理状态和特性,以及所用混合机械的类型和混合操作持续的时间等因素。
混合包括自流混合和机械混合。
自流混合指物料间运动,通过自身摩擦达到最后的均匀混合;机械混合指物料通过机械强制作用达到最后的均匀混合。
一般气体混合为自流混合;三维混合设备混合为自流混合与机械混合的结合;所有混合中混合容器不运动的混合均为机械混合。
二、粉体混合机种类粉体混合机的种类繁多,本文主要就机械混合设备中目前中国市场上常用设备双螺旋锥形混合机,卧式无重力混合机,卧式犁刀混合机,卧式螺带混合机作分析:(一)双螺旋锥形混合机A、混合空间为倒圆锥型,桶体内有两条、三条或单条螺旋轴在自转的情况下又沿着桶壁公转,电机减速机等动力装置处于混合机的上端。
B、混合物料适用范围大,对混合的物料密度偏差,粒径偏差要求不很严格,易控制物料的摩擦起热或起静电 C、混合物料时对晶体的破坏作用小。
D、设备混合时动力要求低,同样型号的设备电机功率大大降低。
E、设备型号可以扩大到很大,中国国产在用最大为30立方。
F、混合时间相对比较长,但大型设备制造成三螺旋形式,可以大大缩短混合时间。
G、主要应用与粉体与粉体的混合,可以在混合时往物料中喷入大量的液体,但混合的整个过程中物料体现为固态粉体,应用例染料、味精、添加剂、塑料粒子等。
粉体混合原理及混合质量分析
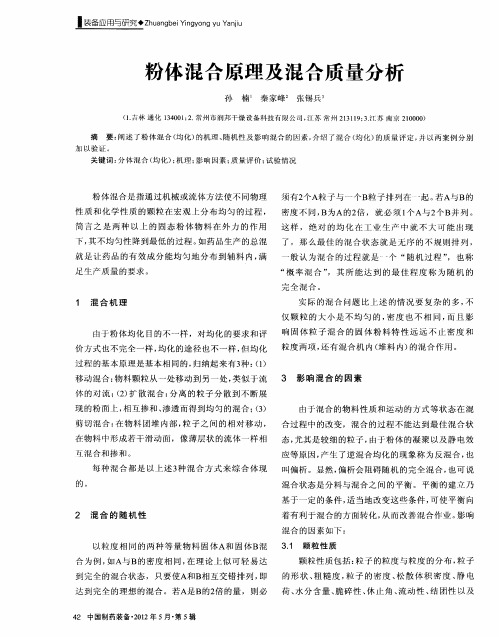
32 混 合 工 艺 .
运 转条 件包 括 : 料 在容 器 内的配 比量 的多少 , 物
…
平 均值 的计 算 公式 :平 均 值 : 。 + + + :
jX r
混合 的因素如 下 :
. 以粒度 相 同 的两 种 等 量物 料 固体 A和 固 体B混 3 1 颗 粒 性 质
合 为例 , 如A与B的密度 相 同 , 理 论 上 似 可轻 易达 在
颗粒 性质 包括 : 子 的粒度 与粒 度 的分 布 , 子 粒 粒 的形 状 、 糙 度 , 子 的 密度 、 散 体 积 密 度 、 电 粗 粒 松 静
一
就 是让 药 品 的有 效成 分 能 均匀 地 分 布到 辅料 内 , 满 足 生 产质量 的要 求 。
般 认 为混合 的过 程就 是 一 个 “ 机 过程 ” 随 ,也称
“ 率混合 ” 概 ,其 所 能 达 到 的最 佳 程 度 称 为 随机 的
完全 混合 。
1 混 合 机 理
表 1 两 组 平 均 值
用 : 1从 混合机 理来 看 , () 移动 混合 最少偏 析 , 合机 混 筒 体 内设 有 刮 板 和 运 动 方 式 采 用 摇 摆 移 动 混 合 方
式 ;2 在 混合 出料 时 , 备 的振动 和落 差小 , 证 出 () 设 保
料 时混合 的物料 均匀 ; 3 原料 的密 度 、 () 形状 、 糙度 粗
到完 全 的混 合状态 ,只要 使A和B 互 交错排 列 , 相 即
达 到完全 的理想 的混 合 。若A是B的2 的量 ,则必 荷 、 分 含 量 、 倍 水 脆碎 性 、 止 角 、 动 性 、 团性 以及 休 流 结
粉体混合(均化)原理及混合质量分析

粉体混合(均化)原理及混合质量分析一、概述粉体混合(均化)就是指二种以上的固态粉体物料在外力的作用下,使其不均匀性降到最低的过程。
例如药品生产过程的总混就是让药品的有效成份能均匀的分布到辅料内,满足生产质量的要求。
二、混合(均化)机理由于粉体均化目的不一样,对均化的要求和评价方式也不完全一样,均化的途径也是不一样的,但均化的过程的基本原理是基本相同的(这里主要讲固态粉体物料的均化混合和评价),归纳起来,主要有三种:1.对流混合:物料的团块从物料的一处移动到另一处,类似于流体的对流。
2.扩散混合:分离的粒子分散到不断展现的斜面上,如同一般的扩散作用那样,相互掺和、渗透而得到均匀的混合。
3.剪切混合:在物料团堆内部,粒子之间的相对移动,在物料中形成若干滑动面,像薄层状的流体一样相互混合和掺和。
三、混合的随机性以粒度相同的两种等量物料固体A和固体B为混合例,如A与B的密度相同,在理论上达到完全的混合状态,似应十分的简单,只要使A和B相互交错排列即可,即达到完全的理想的混合。
但A是B的一倍的量,则必须有两个A粒子与一个B粒子排列在一起。
有若A与B的密度不同,B为A的两倍,就必须一个A与2粒B并列。
这样一来绝对的均化在工业生产中就不大可能出现了,那么最佳的混合的状态就是无序的不规则排列了,一般认为混合的过程就是一个“随机过程”,也称“概率混合”,他能所达到的最佳程度称为随机完全混合。
实际的混合问题比上述的情况要复杂的多,不仅颗粒的大小是不均匀的,密度也不相同,而且影响固体粒子混合的固体粉料特性远远不止密度和粒度两项,还有混合机内(堆料内)的混合作用(指复杂的混合运动的状态)。
三、影响混合的因素由于混合的物料性质和运动的方式等状态在混合过程中的改变,使混合的过程不能达到最佳混合状态,尤其是较细的粒子,由于粉体的凝聚以及静电的效应的原因,产生了逆混合均化的现象称为反混合,也叫偏析。
显然偏析会阻碍随机的完全混合,由此也可说混合状态是分料与混合之间的平衡,平衡的建立乃基于一定的条件,适当的改变这些条件,可使平衡向着有利于混合的方面转化,从而改善混合作业。
【精品文章】一文认识粉体混合均匀度评价方法

一文认识粉体混合均匀度评价方法
粉体物料混合是工业生产中常见的工艺过程,目前在化工、制药、食品、建筑等领域都有非常广泛的应用。
粉体物料混合是指多种不同成分的粉体颗粒,在混料器中产生运动速度或方向的变化,最终使不同成分的颗粒在混料器中达到随机均匀分布的操作过程。
混合效果的好坏直接决定着产品的质量,所以对粉体物料进行高效混合非常重要。
由于混合过程中粉体的运动十分复杂,因此如何正确评价物料的混合效果成为研究的热点和难点。
一、混合原理
在粉体混合的过程中,通常按照粉体颗粒在混料器中的运动状态,其混合原理可以分为三种:对流混合;剪切混合;扩散混合。
粉体混合示意图
1、对流混合
对流混合是指在搅拌器的作用下,不同组分的固体颗粒进行大幅度的位置移动,在来回流动过程中进行混合。
2、剪切混合
剪切混合是指由于不同组分的固体颗粒的运动速度不同,在粉体中会形成很多滑移面,各个滑移面之间发生相对滑动,像薄层状的流体一样进行混合。
3、扩散混合
扩散混合是指在微观状态下,两个相邻的颗粒之间的局部混合,由于相邻颗粒问相互改变位置的改变,会引起粉体颗粒之间相互渗透、掺和,扩。
【精品文章】一文了解粉体混合均化及混合机应用

一文了解粉体混合均化及混合机应用
粉体混合是通过机械或流体方法使不同物理性质和化学性质的颗粒在宏观上分布均匀的过程,简言之是两种以上的固态粉体物料在外力的作用下,其不均匀性降到最低的过程。
随着新材料的研发和工业化应用高速发展,粉体复合材料的均匀混合越来越重要。
一、粉体混合定义及混合机理
(一)粉料混合定义
粉体混合是指将两种或两种以上的不同成分的粉体混合均匀的过程。
混合也是制备产品整个过程的第一步,混合物各组分质量的分布均匀至关重要,因为混料不均匀在后续工艺中是无法调整的。
粉体混合形式分类
(2)混合机理
粉体混合机理是粉体颗粒间相互扩散、对流、剪切,目前常用的混合方法有:三维混合,双锥混合、球磨混合及先进的双运动混合。
双运动混合是利用料桶的转动和料桶内部叶片的转动(转动速度是料桶转动速度的2倍)同时强制驱动粉体相互扩散、对流、剪切,形成复杂的运动,从而达到理想的混合效果。
粉体混合机理示意图
二、影响粉体混合均化工艺的因素
(一)颗粒大小
粗大的粉体颗粒具有较好的压缩性,但成形性差;细小粉体颗粒成形性好,但压缩性差,因此大小颗粒适当的搭配,能改善粉体的填充型,提高。
v型混合机的工作原理

v型混合机的工作原理
V型混合机是一种常见的粉体混合设备,它可以将多种不同性质的粉
体或颗粒物料进行均匀混合。
V型混合机采用V形容器,容器内壁光滑,无死角,内部结构简单,易于清洗。
它的工作原理主要包括以下
几个方面:
1. V型容器
V型混合机采用的是V形容器,其设计使物料在容器内充分翻转和滚动,并且在两个不同方向上交替运动。
这样可以使得物料能够在短时
间内达到均匀混合效果。
2. 搅拌装置
V型混合机的搅拌装置一般由两个或多个旋转的轴组成。
这些轴可以
分别沿着水平和垂直方向旋转,在搅拌过程中将物料反复抛起并落下,从而实现了均匀混合。
3. 物料加入和出料
在使用V型混合机时,需要将需要混合的物料加入到容器中,并通过
出口取出已经完成了均匀混合的物料。
为了保证出料口处不会有残留
物料,在出口处通常安装有刮板或者气动阀门。
4. 控制系统
V型混合机的控制系统通常由电控箱、电机和变频器等组成。
通过对
电机进行调速,可以控制搅拌轴的旋转速度,从而实现对混合质量的
控制。
总之,V型混合机是一种非常重要的粉体混合设备,其工作原理主要
包括V型容器、搅拌装置、物料加入和出料以及控制系统等几个方面。
在实际应用中,可以根据不同物料的特性进行适当调整和改进,以达
到更好的混合效果。
粉体混合(均化)原理及混合质量分析

粉体混合(均化)原理及混合质量分析粉体混合(均化)原理及混合质量分析一、概述粉体混合(均化)就是指二种以上的固态粉体物料在外力的作用下,使其不均匀性降到最低的过程。
例如药品生产过程的总混就是让药品的有效成份能均匀的分布到辅料内,满足生产质量的要求。
二、混合(均化)机理由于粉体均化目的不一样,对均化的要求和评价方式也不完全一样,均化的途径也是不一样的,但均化的过程的基本原理是基本相同的(这里主要讲固态粉体物料的均化混合和评价),归纳起来,主要有三种:1.对流混合:物料的团块从物料的一处移动到另一处,类似于流体的对流。
2.扩散混合:分离的粒子分散到不断展现的斜面上,如同一般的扩散作用那样,相互掺和、渗透而得到均匀的混合。
3.剪切混合:在物料团堆内部,粒子之间的相对移动,在物料中形成若干滑动面,像薄层状的流体一样相互混合和掺和。
三、混合的随机性以粒度相同的两种等量物料固体A和固体B为混合例,如A与B 的密度相同,在理论上达到完全的混合状态,似应十分的简单,只要使A和B相互交错排列即可,即达到完全的理想的混合。
但A是B的一倍的量,则必须有两个A粒子与一个B粒子排列在一起。
有若A与B的密度不同,B为A的两倍,就必须一个A与2粒B并列。
这样一来绝对的均化在工业生产中就不大可能出现了,那么最佳的混合的状态就是无序的不规则排列了,一般认为混合的过程就是一个“随机过程”,也称“概率混合”,他能所达到的最佳程度称为随机完全混合。
实际的混合问题比上述的情况要复杂的多,不仅颗粒的大小是不均匀的,密度也不相同,而且影响固体粒子混合的固体粉料特性远远不止密度和粒度两项,还有混合机内(堆料内)的混合作用(指复杂的混合运动的状态)。
三、影响混合的因素由于混合的物料性质和运动的方式等状态在混合过程中的改变,使混合的过程不能达到最佳混合状态,尤其是较细的粒子,由于粉体的凝聚以及静电的效应的原因,产生了逆混合均化的现象称为反混合,也叫偏析。
粉体-复配

粉体复配
粉体复配是指将多种粉状原料按照一定的配方比例混合在一起,形成所需的粉末混合物。
下面是一般的粉体复配步骤:
1. 确定配方:根据产品的要求,确定所需的原料种类和配方比例。
配方应考虑到原料的物理化学性质、相容性和效果等因素。
2. 准备原料:将所需的原料准备好,包括粉末原料和可能需要的辅助原料。
确保原料的质量和纯度。
3. 称量原料:按照配方比例,使用精确的称量设备将各种原料称量出来。
称量时要注意减少误差,确保粉末配方的准确性。
4. 混合原料:将称量好的原料放入混合设备中进行混合。
混合设备可以是搅拌器、混合机或者其他适合的设备。
混合的时间和速度要根据原料的特性和配方要求进行调整。
5. 筛选和研磨:混合完成后,可以进行筛选和研磨操作,以确保粉末的均匀性和细度。
筛选可以去除不需要的颗粒,研磨可以调整粉末的颗粒大小和形状。
6. 包装和储存:将复配好的粉末产品进行包装,可以使用袋装、罐装等方式。
包装要求密封良好,以防止潮湿、氧化等影响产品质量的因素。
储存时要注意避光、防潮、防火等。
需要注意的是,粉体复配的具体步骤和方法会因不同的产品和要求而有所差异,上述步骤仅为一般参考。
在实际操作中,应根据具体情况进行调整和优化。
粉体混合
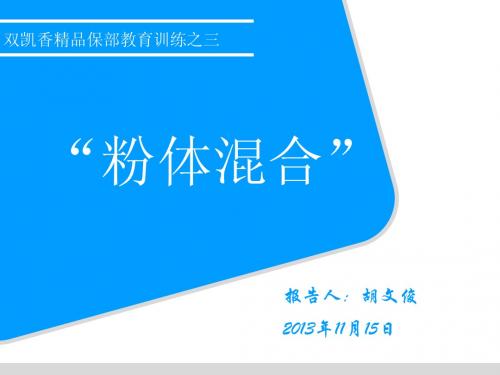
均值 (%) 92.5 92.0
质量范围90%~94%
仅合格率不能反映 全部样品的波动幅度
88
86 84 0 2 4 6 8 10 12
(2)标准偏差
•样本均值:抽出一个样本(一组样品),得到一 批数据,每组数据的算术平均值
1 1 x= (x1 +x 2 + +x n )= x i n n i=1
各种物料添加的操作
加料和放料
固定容器式混合机,应先启动混合机后再加 料,防止出现满负荷启动现象,而且要先卸完 料后才能停机;
旋转容器混合机则应先加料后启动,先停机, 后卸料; 对于V型混合机,加料时应分别从两个进料口 进料。
谢谢!
第二 组
102 100
94.1
93.9
92.5
93.5
90.2
94.8
90.5
89.5
91.5
89.9
92.0
98
96 94 92 90 88 86 84 0 2 4 6 8 10 12
第一组
第二组
第一组标准偏差: 4.68 第二组标准偏差: 1.96
总体的标准偏差,用σ表示:
1 ( X i a) n i 1
样品 第一 组 第二 组
102 100 98 96 94 92 90 第一组 第二组
1 99.5 94.1
2 93.8 93.9
3 94.0 92.5
4 90.2 93.5
5 93.5 90.2
6 86.2 94.8
7 94.0 90.5
8 90.3 89.5
9 98.9 91.5
10 85.4 89.9
混合均匀度 T=100%-R
粉体混合技术和原理分析
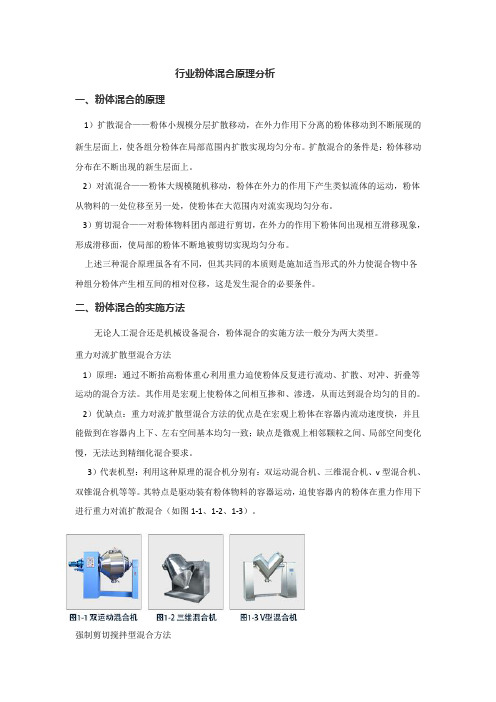
行业粉体混合原理分析一、粉体混合的原理1)扩散混合——粉体小规模分层扩散移动,在外力作用下分离的粉体移动到不断展现的新生层面上,使各组分粉体在局部范围内扩散实现均匀分布。
扩散混合的条件是:粉体移动分布在不断出现的新生层面上。
2)对流混合——粉体大规模随机移动,粉体在外力的作用下产生类似流体的运动,粉体从物料的一处位移至另一处,使粉体在大范围内对流实现均匀分布。
3)剪切混合——对粉体物料团内部进行剪切,在外力的作用下粉体间出现相互滑移现象,形成滑移面,使局部的粉体不断地被剪切实现均匀分布。
上述三种混合原理虽各有不同,但其共同的本质则是施加适当形式的外力使混合物中各种组分粉体产生相互间的相对位移,这是发生混合的必要条件。
二、粉体混合的实施方法无论人工混合还是机械设备混合,粉体混合的实施方法一般分为两大类型。
重力对流扩散型混合方法1)原理:通过不断抬高粉体重心利用重力迫使粉体反复进行流动、扩散、对冲、折叠等运动的混合方法。
其作用是宏观上使粉体之间相互掺和、渗透,从而达到混合均匀的目的。
2)优缺点:重力对流扩散型混合方法的优点是在宏观上粉体在容器内流动速度快,并且能做到在容器内上下、左右空间基本均匀一致;缺点是微观上相邻颗粒之间、局部空间变化慢,无法达到精细化混合要求。
3)代表机型:利用这种原理的混合机分别有:双运动混合机、三维混合机、v型混合机、双锥混合机等等。
其特点是驱动装有粉体物料的容器运动,迫使容器内的粉体在重力作用下进行重力对流扩散混合(如图1-1、1-2、1-3)。
强制剪切搅拌型混合方法1)原理:利用容器内的运动桨叶强制对粉体进行反复地搅拌、剪切等运动的混合方法。
其作用是微观上不断打散粉体颗粒之间的相邻关系,让粉体颗粒充分地移动、互换,达到粉体混合均匀的目的。
2)优缺点:强制搅拌剪切型混合方法的优点是微观上能够达到精细化混合均匀的目的,并因粉体内部流动效率高,而使混合效率比较高;缺点是没有有效措施实现容器内上下、左右宏观上整体均匀。
粉体刷筛混合技术

粉体刷筛混合技术1 背景介绍粉体混合是磨料、磨具、冶金、化工、食品、医药、饲料和陶瓷等行业中常见的操作,现有常用的粉体混合技术有三维混合、双锥混合、球磨混合、双运动混合等,其原理是通过搅拌、混合容器运动带动粉末颗粒在混合容器中运动,使不同成分的粉体颗粒在混合容器中随机分布,使混合容器中的粉体不均匀性逐渐降低,进而达到一定的均匀程度,其混合存在以下缺点。
耗时长。
通过运动中粉体颗粒的随机分布获得均匀性,这需要反复地长时间的运动,才能达到一定的均匀度。
有夹生。
受混合原理的缺陷、受混合容器边角等区域的影响、物料特性(黏性、附着性等)、静电等影响,混合容器中不可避免地存在不参与混合或运动不充分的部分,形成物料夹生以及部分区域不均匀。
质量稳定性差。
物料和生产环境的温度和湿度以及物料特性(黏性、附着性等)对混料工艺影响较大,尤其是季节性温度、湿度变化,影响混料的均匀性,导致生产质量波动。
为了解决现有粉体混合技术的上述缺点,我们提出粉体刷筛混合技术的概念模型。
并制作对应的自动混料装置进行验证,确定刷筛混合技术相对于现有的混合技术耗时可降低一半,可消除夹生现象,提高质量的稳定性。
2 粉体刷筛混合技术2.1 粉体刷筛混合技术原理刷筛混合技术原理为:根据粉体粒度,选择合适目数的特制筛网,将各种粉末通过刷子过筛,刷子旋转一圈则各种粉末通过筛网下漏一部分,在接料容器中形成一个薄层,刷子不断旋转,即可使粉末在接料容器中形成一个个薄层实现交叉混合,将粉体多次过筛即可快速完成均匀混合。
刷筛混合技术原理图如图1所示(1为各种混合的粉末原料,2为特制筛网,3为定制旋转刷,4为接料容器,5为层层交叉的混合物料)。
2.2 粉体刷筛混合技术优点现有粉体混合设备多为二维混合机、“V”型混合机、双锥混合机、双螺旋锥形混合机、卧式无重力混合机、卧式犁刀混合机、卧式螺带混合机、三维混合机、双运动混料机。
现有粉体混合技术的原理为将粉末原料装入混料容器中,驱动容器运动或搅拌容器,使容器内各种粉末相互扩散运动,实现混合。
粉体配料混合技术

粉体配料混合技术
《神奇的粉体配料混合技术》
嘿,你知道吗,有个东西叫粉体配料混合技术,这可真是个有意思的玩意儿!
就说我上次去一个工厂参观吧,那里面正在进行粉体配料混合呢。
我看到那些各种各样的粉体,就像一群小精灵似的,乖乖地待在各自的地方。
然后呢,那些巨大的机器就开始工作啦!就像大力士一样,把这些粉体一勺一勺地抓起来,再慢慢地放到一起。
那个搅拌的过程特别好玩,就好像是粉体们在开一场盛大的舞会。
它们在里面转啊转啊,你挤我我挤你,慢慢地就融合在一起啦,变得你中有我,我中有你。
我就站在旁边看着,感觉特别神奇。
这些小小的粉体,经过这么一番折腾,就变成了一种全新的东西。
而且哦,工作人员还特别认真地在旁边盯着,就好像是粉体们的大管家,生怕它们出什么岔子。
他们一会儿看看这个仪表,一会儿瞅瞅那个刻度,那专注的样子,真的是太专业啦!
哎呀呀,这粉体配料混合技术可真是不简单呐,能把这些小小的粉体变得这么有用。
我算是开了眼界啦,原来这背后还有这么神奇的技术在发挥作用呢!以后再看到那些由粉体做成的东西,我肯定就会想起这次有趣的经历,想起那一场粉体的“大舞会”呀!这就是粉体配料混合技术的魅力所在呀!。
- 1、下载文档前请自行甄别文档内容的完整性,平台不提供额外的编辑、内容补充、找答案等附加服务。
- 2、"仅部分预览"的文档,不可在线预览部分如存在完整性等问题,可反馈申请退款(可完整预览的文档不适用该条件!)。
- 3、如文档侵犯您的权益,请联系客服反馈,我们会尽快为您处理(人工客服工作时间:9:00-18:30)。
行业粉体混合原理分析
一、粉体混合的原理
1)扩散混合——粉体小规模分层扩散移动,在外力作用下分离的粉体移动到不断展现的新生层面上,使各组分粉体在局部范围内扩散实现均匀分布。
扩散混合的条件是:粉体移动分布在不断出现的新生层面上。
2)对流混合——粉体大规模随机移动,粉体在外力的作用下产生类似流体的运动,粉体从物料的一处位移至另一处,使粉体在大范围内对流实现均匀分布。
3)剪切混合——对粉体物料团内部进行剪切,在外力的作用下粉体间出现相互滑移现象,形成滑移面,使局部的粉体不断地被剪切实现均匀分布。
上述三种混合原理虽各有不同,但其共同的本质则是施加适当形式的外力使混合物中各种组分粉体产生相互间的相对位移,这是发生混合的必要条件。
二、粉体混合的实施方法
无论人工混合还是机械设备混合,粉体混合的实施方法一般分为两大类型。
重力对流扩散型混合方法
1)原理:通过不断抬高粉体重心利用重力迫使粉体反复进行流动、扩散、对冲、折叠等运动的混合方法。
其作用是宏观上使粉体之间相互掺和、渗透,从而达到混合均匀的目的。
2)优缺点:重力对流扩散型混合方法的优点是在宏观上粉体在容器内流动速度快,并且能做到在容器内上下、左右空间基本均匀一致;缺点是微观上相邻颗粒之间、局部空间变化慢,无法达到精细化混合要求。
3)代表机型:利用这种原理的混合机分别有:双运动混合机、三维混合机、v型混合机、双锥混合机等等。
其特点是驱动装有粉体物料的容器运动,迫使容器内的粉体在重力作用下进行重力对流扩散混合(如图1-1、1-2、1-3)。
强制剪切搅拌型混合方法
1)原理:利用容器内的运动桨叶强制对粉体进行反复地搅拌、剪切等运动的混合方法。
其作用是微观上不断打散粉体颗粒之间的相邻关系,让粉体颗粒充分地移动、互换,达到粉体混合均匀的目的。
2)优缺点:强制搅拌剪切型混合方法的优点是微观上能够达到精细化混合均匀的目的,并因粉体内部流动效率高,而使混合效率比较高;缺点是没有有效措施实现容器内上下、左右宏观上整体均匀。
3)代表机型:利用这种原理的混合机分别有:双运动混合机、槽式螺带混合机、单锥螺杆混合机、犁刀混合机等等。
其特点是容器内加有运动桨叶装置,对其中粉体进行强制搅拌剪切混合(如图1-4、1-5、1-6)。
在实际工作中,混合设备都以实现某一种混合原理为主,但也会伴随其他混合原理的发生。