脱水技术在PTA加氢精制工艺中的应用
聚醚多元醇脱水方法

聚醚多元醇脱水方法一、脱水方法的原理聚醚多元醇脱水方法是通过加热和脱水剂的作用将聚醚多元醇中的水分蒸发或吸附去除,从而得到低水分的聚醚多元醇产品。
聚醚多元醇是一种重要的化工原料,在聚氨酯、涂料、塑料、弹性体等领域有广泛应用。
由于聚醚多元醇对水分敏感,水分的存在会降低其性能和稳定性,因此需要进行脱水处理。
二、脱水方法的步骤1. 准备聚醚多元醇和脱水剂:选择适当的聚醚多元醇和脱水剂。
一般常用的脱水剂有碳酸钠、硅胶、分子筛等。
2. 混合聚醚多元醇和脱水剂:将聚醚多元醇和脱水剂按一定比例混合。
混合的目的是使脱水剂能够吸附或吸收聚醚多元醇中的水分。
3. 加热混合物:将混合物加热至一定温度,通常在80-120摄氏度之间。
加热的目的是促进水分蒸发或脱附,加快脱水过程。
4. 分离脱水剂:待混合物冷却后,通过过滤或离心等方法将脱水剂与聚醚多元醇分离。
脱水剂中吸附或吸收的水分也随之一起分离。
5. 检测水分含量:使用水分测定仪器检测脱水后的聚醚多元醇中水分的含量。
根据产品要求,选择合适的水分含量。
三、脱水方法的应用领域1. 聚氨酯制备:聚醚多元醇是聚氨酯的重要原料,通过脱水处理可以得到低水分的聚醚多元醇,提高聚氨酯的性能和稳定性。
2. 涂料和胶粘剂:聚醚多元醇在涂料和胶粘剂中的应用也需要低水分的产品,脱水处理可以提高产品的质量和使用性能。
3. 塑料和弹性体:聚醚多元醇也广泛应用于塑料和弹性体中,脱水处理可以减少产品中的气泡和缺陷,提高产品的力学性能和耐候性。
总结:聚醚多元醇脱水方法是一种常用的处理聚醚多元醇中水分的方法。
通过加热和脱水剂的作用,可以将聚醚多元醇中的水分去除,得到低水分的产品。
脱水方法的步骤包括混合、加热、分离和检测水分含量。
聚醚多元醇脱水方法在聚氨酯、涂料、塑料、弹性体等领域有广泛应用。
通过脱水处理,可以提高产品的质量和性能,满足不同领域的需求。
pta工艺技术简介
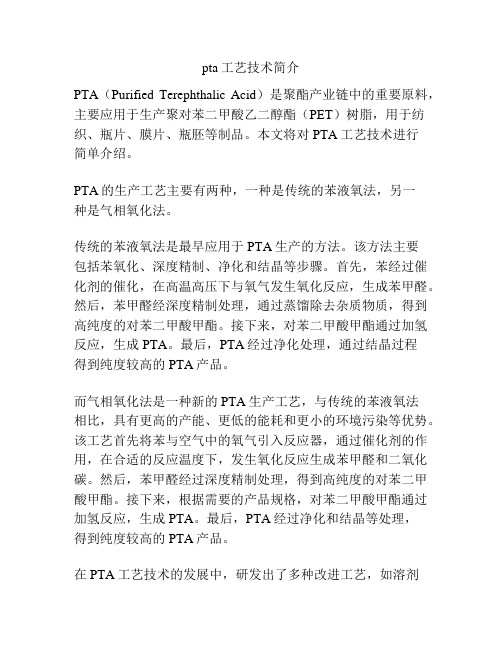
pta工艺技术简介PTA(Purified Terephthalic Acid)是聚酯产业链中的重要原料,主要应用于生产聚对苯二甲酸乙二醇酯(PET)树脂,用于纺织、瓶片、膜片、瓶胚等制品。
本文将对PTA工艺技术进行简单介绍。
PTA的生产工艺主要有两种,一种是传统的苯液氧法,另一种是气相氧化法。
传统的苯液氧法是最早应用于PTA生产的方法。
该方法主要包括苯氧化、深度精制、净化和结晶等步骤。
首先,苯经过催化剂的催化,在高温高压下与氧气发生氧化反应,生成苯甲醛。
然后,苯甲醛经深度精制处理,通过蒸馏除去杂质物质,得到高纯度的对苯二甲酸甲酯。
接下来,对苯二甲酸甲酯通过加氢反应,生成PTA。
最后,PTA经过净化处理,通过结晶过程得到纯度较高的PTA产品。
而气相氧化法是一种新的PTA生产工艺,与传统的苯液氧法相比,具有更高的产能、更低的能耗和更小的环境污染等优势。
该工艺首先将苯与空气中的氧气引入反应器,通过催化剂的作用,在合适的反应温度下,发生氧化反应生成苯甲醛和二氧化碳。
然后,苯甲醛经过深度精制处理,得到高纯度的对苯二甲酸甲酯。
接下来,根据需要的产品规格,对苯二甲酸甲酯通过加氢反应,生成PTA。
最后,PTA经过净化和结晶等处理,得到纯度较高的PTA产品。
在PTA工艺技术的发展中,研发出了多种改进工艺,如溶剂精制工艺、生物法和电解法等。
这些改进工艺在提高产品质量、提高生产效率和降低环境污染等方面都有积极的意义。
总的来说,PTA是聚酯产业链中的重要原料,生产PTA的工艺技术主要有传统的苯液氧法和气相氧化法两种。
随着技术的发展,改进工艺方法也逐渐涌现,为PTA生产提供更好的选择。
毕业设计(论文)-年产44万吨精对苯二甲酸(pta)工段设计[管理资料]
![毕业设计(论文)-年产44万吨精对苯二甲酸(pta)工段设计[管理资料]](https://img.taocdn.com/s3/m/e240640b770bf78a64295451.png)
年产44万吨精对苯二甲酸(PTA)工段设计摘要本文以44万吨PTA生产装置氧化工段流程为对象,建立了氧化工段核心流程以及氧化工段全流程的严格机理模型。
PTA(精对苯二甲酸)是合成聚酯纤维和塑料的重要原料,主要采用对二甲苯(PX)空气氧化法和加氢精制生产。
复杂工业过程的建设,模拟和优化一直是过程系统工程(PSE)领域的核心研究内容。
本文详细论述了工艺路线论证,工艺流程设计,全流程的物料衡算,热量衡算,主要设备的选型,车间布置设计,自动控制与优化,公用工程(劳动保护、安全生产、三废处理),工程设计概算,以及在本设计过程中所遇到的问题和针对问题提出的建议等内容。
关键词:PTA 工段设计加氢精制Annual output of 44 tons of purified terephthalic acid (PTA)Section of DesignABSTRACTIn the thesis,the steady state simulation and oplimization of PTA oxidation process are studied. PTA(purified terephthalic acid ) is producing compound polyester pibre and plastic importance materials, mainly paraxylene(PX) production by air oxidation and by hydro-refining .Modeling,simulation and optimization are the key to process systems engineering. This article discusses in detail the expound of technological line, the design of the process flows, the whole process of material balance,energybalance, the selection of the main equipment, general layout of the shop, automatic control and optimization, utilities system(labor protection, safety in production, waste treatment), engineering estimates, along with the problems in the design process and some suggestions for these problems are made.Keywords: purified terephthalic acid the design of the section hydro-refining目录摘要................................................ ABSTRACT (I)目录 (II)1 绪论 0 0 0PTA的概况 0PTA生产原理 (1) (1)PTA生产技术选择 (1)PTA工艺路线论证 (2)工艺流程设计 (3) (3)工艺流程简图 (4)国内外市场情况 (4) (4) (5)PTA国内外生产工艺技术发展情况 (6) (6) (6) (7)2 物料衡算 (8) (8)有关物料衡算技术数据 (8) (9)反应主要副产物的分配 (10) (10) (11)3 热量衡算 (12) (12)4 工艺设备技术方案 (14) (14) (14) (14) (15) (15)5 工段工艺流程优化 (17) (17) (17),降低原料和能量消耗 (17)PTA母液固体回收利用 (18) (18)、改进设备 (18) (18) (18) (18)6 车间布置设计 (19) (19) (19) (19)分区说明 (19) (20)7 自动控制与优化 (21) (21) (21) (21)8 公用工程 (22) (22) (22) (22) (23) (23) (23) (23) (24)9 工程设计概算 (25) (25) (25)10 结束语 (26)参考文献 (27)附录一 (28)附录二 (29)附录三 (30)1 绪论本设计依据材料下达任务书进行编制。
PTA工艺技术简介

SSEC封面主讲人:李真泽中国石化集团上海工程有限公司PTA 生产技术和主要专利商简介PTA工艺流程原材料及公用工程消耗主要工艺设备装置布置投资及经济效益国内PTA供需分析及预测SSEC在PTA领域中的业绩目录PTA生产工艺技术简介PTA 生产技术和主要专利商简介PTA生产工艺技术简介氧化反应方程式:H3C-C6H4-CH3+ 3O2→HOOC-C6H4-COOH + 2H2O + 318.7 千卡/克分子加氢反应方程式:HOOC-C6H4-CHO + 2H2→HOOC-C6H4-CH3+ H2OPTA生产工艺技术简介PTA 生产技术和主要专利商简介当前世界上最主要的PTA技术专利商:9BP(原Amoco)9INVISTA(原属ICI,后归Dupont,再独立为INVISTA)9Mitsui(三井化学)其他还有以BP技术为蓝本发展起来:9Mitsubishi(三菱化学)9Daw Chemical(原属INCA,后被Daw并购)其中以BP生产技术的市场占有率为最高。
PTA 生产工艺流程PTA生产工艺技术简介氧化单元9空气压缩9进料配置9氧化反应9结晶9过滤9干燥9溶剂回收9溶剂脱水精制单元9进料配置9加氢反应9结晶9离心分离9过滤9干燥9排气洗涤和溶剂回收9母液中固体回收PTA 生产工艺流程PTA 生产工艺技术简介工艺空气压缩催化剂配制氧化配料氧化反应闪蒸结晶真空过滤干燥尾气冷凝尾气催化氧化闪蒸汽冷凝溶剂回收蒸汽及凝水系统精制配料加氢预热加氢反应闪蒸结晶压力离心分离真空过滤产品干燥气流输送母固回收残渣回收包装储存高压蒸汽空气Co,Mn,Br -PX循环溶剂溶剂回收脱离子水蒸汽透平膨胀透平闪蒸蒸汽氢气废水催化剂残渣废水循环溶剂母液醋酸溶剂回收反应尾气HAC母液中固体排入大气废水处理装置H 2O尾气洗涤典型PTA 装置工艺流程示意图PTA 生产工艺流程PTA 生产工艺技术简介工艺空气压缩2催化剂配制氧化反应2闪蒸结晶真空过滤干燥尾气冷凝1尾气洗涤和吸附1闪蒸汽冷凝洗涤共沸蒸馏溶剂回收蒸汽及凝水系统精制配料加氢预热加氢反应闪蒸结晶压力离心分离真空过滤产品干燥气流输送母固回收催化剂回收PET 装置低压蒸汽及凝水空气Co, Mn, Br PX,HAC循环溶剂溶剂回收脱离子水膨胀透平1闪蒸蒸汽氢气废水催化剂废水循环溶剂母液回收的醋酸溶剂反应尾气母液中固体废水处理装置醋酸正丁酯排入大气离心分离排入大气残渣至回收WQ工艺空气压缩1氧化反应1尾气冷凝2Q 尾气洗涤和吸附2膨胀透平2再生气处理排入大气W 中石化百万吨级PTA 装置流程示意图PTA 生产工艺流程PTA 生产工艺技术简介四级冷凝冷却分别回收0.29、0.24、0.098和-0.029MPaG副产蒸汽四级冷凝冷却分别回收0.35和0.2MPaG 副产蒸汽四级冷凝冷却分别回收0.43和0.2MPaG 副产蒸汽四级冷凝冷却分别回收0.3、0.24、0.1和-0.03MPaG 副产蒸汽3. 反应尾气冷凝冷却系统CS /Ti CS /Ti CS /Ti CS /Ti 反应器材质下进轴锚式搅拌上进轴、涡轮式及浆式三级搅拌上进轴、涡轮式及浆式二级搅拌底进轴变速锚式搅拌氧化反应器搅拌机1台立式罐顶端设蒸馏塔1台立式罐1台立式罐2台立式罐顶部设分离塔氧化反应器气液相鼓泡反应带强烈搅拌的气液相鼓泡反应带强烈搅拌的气液相鼓泡反应气液相鼓泡反应氧化反应类型186℃1.0 MPa 201℃1.5 MPa 191℃1.26 MPa 185~189℃0.97~1.12 MPa 氧化反应条件2. 氧化反应50万吨/年60万吨/年90万吨/年100万吨/年1. 最大生产能力MitsuiINVISTA BP 中国石化项目主要PTA 生产技术的特点比较PTA 生产工艺流程PTA 生产工艺技术简介60块板1座316L /317L /Ti60块板1座316L /双相钢90块板1座316L /317L /Ti 60块板1座316L /317L /Ti 醋酸精馏塔共沸蒸馏设共沸剂回收塔共沸蒸馏设共沸剂回收塔直接精馏共沸蒸馏设共沸剂回收塔工艺流程7. 溶剂回收系统真空鼓式2台真空鼓式2台真空鼓式2台真空鼓式4台6. 真空过滤立式离心机3台无无立式离心机6台5. 氧化离心立式罐带搅拌(浆料罐)立式罐带搅拌立式罐带搅拌立式罐带搅拌结晶器形式1台3台串联3台串联2台串联结晶器台数4. 结晶系统MitsuiINVISTA BP 中国石化项目主要PTA 生产技术的特点比较PTA 生产工艺流程PTA 生产工艺技术简介13014011014512. 综合能耗指标kg 标油/t 产品压力离心分离后真空过滤分离压力离心分离后真空过滤分离压力离心分离后真空过滤分离压力过滤分离后真空过滤分离11. 产品分离系统采用结晶器闪蒸汽副产蒸汽加热直接采用结晶器闪蒸汽和蒸汽凝液加热直接采用结晶器闪蒸汽加热直接采用结晶器闪蒸汽加热10. 精制预热系统蒸汽利用催化燃烧高压催化燃烧催化燃烧再生热氧化燃烧9. 氧化尾气处理设置催化剂回收装置,回收催化剂水溶液,经浓缩后,送氧化反应器。
PTA装置生产过程危险性分析

PTA装置生产过程危险性分析1 装置概况1.1 概述洛阳石油化工总厂PTA装置采用美国BP—AMOCO公司的专利技术,并由该公司提供工艺包。
日本千代田公司总承包,洛阳石化工程公司负责工程详细设计,中国石化集团第五建筑公司负责施工。
工程总投资13.5亿人民币,占地面积16000平方米。
于1998年2月21日正式开工建设,并于2000年3月18日正式中交,2000年5月25日一次投料生产成功。
装置设计生产能力22.5万吨/年,小时生产量为32吨,操作弹性范围70%~100%,年开工时间7600小时。
2003年7月完成扩能改造工程,生产能力达到32.5万吨/年PTA。
小时产量42.76吨,操作时间7600小时。
1.2 装置组成PTA装置主要由氧化单元、精制单元、公用工程和辅助设施等四部分组成。
(1)氧化单元:主要包括空气压缩、进料准备、氧化反应、结晶、过滤分离、干燥、溶剂回收等。
(2)精制单元:主要包括浆料制备、加氢反应、PTA结晶、分离过滤、干燥和产品输送等。
(3)辅助设施:主要包括控制室、变配电所、MCC、化验室、原料及化工原料中间罐区、成品包装。
1.3 装置工艺概况1.3.1工艺流程简述在氧化装置中,以对二甲苯(PX)为原料,醋酸为溶剂,醋酸钴、醋酸锰为催化剂,氢溴酸为促进剂,与氢反应生成对苯二甲酸。
反应在191℃和1256KPa 条件下进行,反应过程属剧烈放热反应。
反应尾气经四级冷却进行能量回收,凝液返回反应器,不凝气体一部分进入尾气透平进一步回收能量,另一部分用于气流输送物料。
反应产物经结晶、过滤分离、干燥后得到粗对苯二甲酸(CTA )粉末。
粗对苯二甲酸中含有氧化反应副产物对甲基苯甲酸(TOL )和对羧基苯甲醛(4-CBA )杂质。
过滤分离过程中大约90%以上的母液返回到催化剂配制系统,其余送入残渣蒸发器,固体残渣送污水处理装置。
装置所有尾气进入溶剂回收单元,用以回收醋酸溶剂。
精制装置采用加氢还原法除去氧化反应副产物。
pta工艺技术

pta工艺技术PTA工艺技术是指通过对纯对苯和纯异丙醇进行反应合成的对苯二甲酸(PTA)的工艺技术。
PTA工艺技术在纺织、石化、塑料等行业具有重要的应用价值和发展潜力。
本文将介绍PTA工艺技术的原理、过程和应用。
PTA工艺技术的原理是利用催化剂催化对苯和异丙醇进行酯化反应,生成酯化物。
然后通过高温下的脱水反应,将酯化物转化为PTA。
PTA是一种重要的化工原料,广泛用于生产聚酯纤维、塑料、涤纶等产品。
PTA工艺技术的主要过程包括前处理、酯化反应、脱水反应和蒸馏等。
前处理主要是对原料进行精制,去除杂质,并调节反应物的浓度和比例。
酯化反应是PTA工艺技术的关键步骤,需要合适的催化剂和反应条件。
脱水反应是将酯化物转化为PTA的过程,需要高温和脱水剂的作用。
蒸馏是对产物进行分离和净化,得到高纯度的PTA。
PTA工艺技术具有很多优点。
首先,PTA工艺技术可以利用丰富的对苯和异丙醇资源,减少了对化石能源的依赖,具有较高的可持续性。
其次,PTA工艺技术可以提高PTA的产量和质量,降低生产成本。
此外,PTA工艺技术还具有操作简单、生产周期短、产品纯度高的特点。
PTA工艺技术在纺织行业中的应用广泛。
PTA可以合成涤纶纤维,涤纶纤维是一种优良的合成纤维,具有柔软、耐磨、耐酸碱等特点,广泛用于纺织品、家居用品和工业用品等领域。
PTA还可以用于合成PET瓶片,PET瓶片是一种常见的塑料包装材料,具有耐高温、抗冲击、透明度高的特点,被广泛应用于食品、饮料和日用品的包装领域。
除了纺织行业,PTA工艺技术还可以在石化、塑料和化妆品等行业中得到应用。
在石化行业中,PTA可以作为油田水处理剂,用于去除油田水中的杂质和有机物。
在塑料行业中,PTA可以用于生产PET塑料制品,如瓶子、片材和纤维等。
在化妆品行业中,PTA可以用于合成染发剂、香水和化妆品等。
综上所述,PTA工艺技术是一种重要的工艺技术,具有广泛的应用前景。
随着纺织、石化、塑料等行业的发展,PTA工艺技术将会得到更多的应用和研究。
国内PTA生产技术的应用及新一代工艺介绍

国内PTA生产技术的应用及新一代工艺介绍PTA是生产聚酯的主要原料,全称精对苯二甲酸,据公开资料统计目前国内产量总和已达到全球总产能的56%左右,截止2018年1月嘉兴石化二期投产后国内产能总和达到了5131.5萬吨/年。
本文对目前国内已投产主流专利进行简单介绍,并对新一代PTA技术进行介绍和解析。
标签:PTA生产技术;PTA新工艺1 国内已投产PTA生产技术简介我国投产的PTA应用的技术包括BP、INVISTA、昆仑、日立、三菱+东帝士、EASTMAN、早期BP+AMOCO工艺、三井工艺等,产能市场份额从打到小依次是INVISTA、日立、三菱+东帝士、昆仑、BP,截止2018年8月各占37.45%、26.11%、13.15%、12.08%、7.79%。
从上世纪五十年代开始,BP-Amoco(简称BP)公司和DuPont-ICI(后转让给INVISTA)公司几乎同时对PTA生产工艺进行研发,不断完善逐步发展和形成氧化、精制专利技术,其他的生产工艺都是这两家工艺技术的基础上,通过进行研发而形成的具有自身特点的专有工艺技术。
因BP专利在2015年开始出售专利授权,之前国内除了珠海BP以外并没有其他使用其专利的工厂,其国内技术应用比例并不大。
而INVISTA专利在1995年、1996年开始对辽阳石化、乌鲁木齐石化出售其专利技术,截止2018年8月国内有20套采用INVISAT的装置已建设完成。
国产工艺为中国昆仑工程公司(原来的中国纺织工业设计院)的专利技术,其专利技术以三井工艺技术为基础进行工艺改进优化,重庆市涪陵蓬威石化有限责任公司是第一个采用该技术的PTA装置,之后海伦石化120万吨/年、浙江远东石化(现已被华杉集团收购)140万吨/年、虹港石化150万吨/年PTA装置也均采用该技术,但其能耗、物耗与同期的BP、INVISTA工艺仍有差距。
2 PTA新工艺介绍目前PTA新技术开发提供技术转让的主要有BP、INVISTA、昆仑三家,其中BP最新工艺技术于2015年7月在珠海BP三期投产,INVISTA最新P8技术2018年1月在嘉兴桐昆二期投产,虽然在试运行阶段设备故障和工艺稳定方面存在一定的问题,但经过相关改造,装置运行已趋于平稳,技术已接近成熟。
PTA装置溶剂脱水塔模拟及塔板效率分析
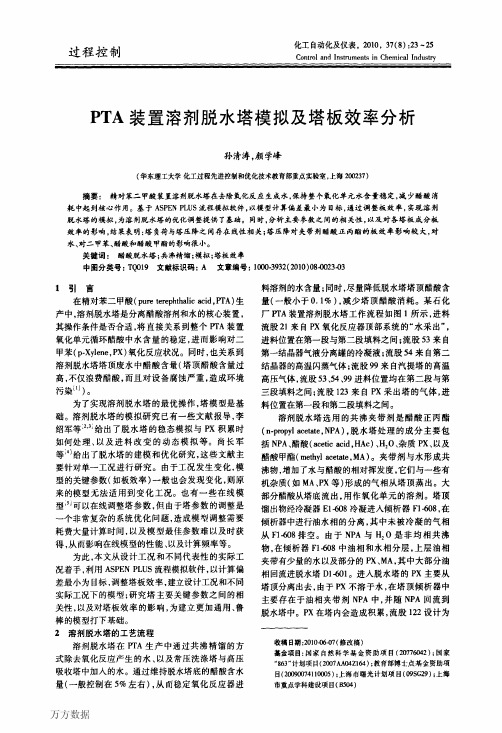
[8]KUROOKA T,YAMASHITA Y。NISHITANI H,et a1.DynlHnic Simulation and Nonlinear Control System Design of a Heteroge- neous Azeotropic Distillation Column[J].Computers and Chemical Engineering,2000,24(7):887—892.
收稿日期:2010-06-07(修改稿) 基金项目:国家自然科学基金资助项目(20776042);国家 “863”计划项目(2007AA042164);教育部博士点基金资助项 目(20090074110005);上海市曙光计划项目(09SG29);上海 市重点学科建设项目(B504)
万方数据
·24·
万方数据
第8期
孙清涛等.PTA装置溶剂脱水塔模拟及塔板效率分析
·25·
因此,可以通过塔压降来表征塔的处理量。
图4塔压降随总进料量的变化
图5塔压降随总进料量与回流量之和的变化
基于以上12组代表性工况模型,分析不同处理 量(即不同塔压降)情况下,塔的运行效率,即不同 处理量对塔板效率的影响。发现对于不同处理量, 只有中段(21-45块板)NPA组分板效率发生变化, 其它组分的板效率,以及其它段的板效率都没有明 显变化。图4给出了12个代表性工况下,中段NPA 成分板效率与塔压降(表征处理量)的关系曲线。 从图5和图6可以看出:随着溶剂脱水塔的总进料 接近设计总进料,NPA塔板效率也逐渐接近设计工 况时的NPA板效率,且一般在设计负荷下塔具有最 好的分离效果,即塔板效率最高。当进料总量低于 或超过设计工况的进料总量时,塔压降也随着降低 或增加,此时,NPA塔板效率都呈现逐渐下降,即偏 离设计负荷、塔板效率都呈下降趋势。
PTA装置共沸精馏塔脱水系统

PTA装置共沸精馏塔脱水系统时在国(仪征化纤股份有限公司化工厂,江苏仪征21 1900)PTA是合成聚酯的重要原料,是以对二甲苯(PX)为原料,醋酸(AeOH)为溶剂,在一定温度和压力下用空气氧化生成。
为保证反应的顺利进行,必须及时从系统中移走氧化反应产生的、常压吸收塔以及高压吸收塔处理工艺气体时加入的水,将水移出,同时尽可能从水中回收醋酸,降低醋酸消耗,目前先进的醋酸单耗约为44kg。
溶剂回收系统的作用为:①从尾气中回收醋酸;②除去溶剂中的副产物和杂质;③将水由醋酸溶液中分离出来。
所以,回收系统工作状况影响PTA生产成本的高低和产品质量。
仪化PTA装置引进DuPont专利,溶剂脱水塔为目前较先进的共沸精馏塔,在塔中加共沸剂,降低了溶剂脱水塔的高度,减少脱水所需的热量消耗,工艺指标要求塔顶馏出物AeOH的质量分数小于0.1%,塔底馏出物中水的质量分数约5%。
现结合氧化生产运行的实际工况,对溶剂脱水塔作一简单分析讨论。
1 工艺原理醋酸与水不形成共沸物,且其相对挥发度较低,采用普通精馏法进行分离所需的理论塔板数和回流比较大,相应的能耗也较高。
因此普通精馏法主要用于含水量较小的粗醋酸的提纯。
溶剂脱水系统的介质为AeOH、H:0、PX、醋酸甲酯(AeOMe)、丙醇等的多元体系,AcOH和H20的沸点虽相差17℃,但由于二者之间的非理想汽液平衡性质,要将它们完全分离,需较多的理论板数和较高的能量输入。
共沸精馏是指在2组分共沸液或挥发度相近的物系中加入共沸剂,共沸剂能与原料液中的某一个或几个组分形成新的共沸液,从而使料液能用普通精馏法分离。
采用共沸精馏法分离水和醋酸时,要求原料液中醋酸含量较高、共沸剂组成稳定。
共沸精馏的操作过程:共沸剂和原料液一起进入共沸精馏塔,在精馏过程中水随共沸剂被蒸出,经冷却后与共沸剂分层分离,共沸剂返回塔中,水排放,在塔釜中即得到醋酸。
共沸精馏时一般选用形成低沸点共沸物的共沸剂,其加入量应严格控制,以减少分离过程的能耗。
PTA合成工艺简介

PTA生产技术及工艺流程简述目前世界PTA生产厂家采用的技术虽有差异,但归纳起来,大致可分为以下两类:(1)精PTA工艺此工艺采用催化氧化法将对二甲苯(PX)氧化成粗TA,再以加氢还原法除去杂质,将CTA精制成PTA。
这种工艺在PTA生产中居主导地位,代表性的生产厂商有:英国石油(BP)、杜邦(Dupont)、三井油化(MPC)、道化学-因卡(Dow-INCA)、三菱化学(MCC)和因特奎萨(Interquisa)等。
(2)优质聚合级对苯二甲酸(QTA、EPTA)工艺此工艺采用催化氧化法将PX氧化成粗TA,再用进一步深度氧化方法将粗TA精制成聚合级TA。
此工艺路线的代表生产厂商有三菱化学(MCC)、伊斯特曼(Eastman)、杜邦(Dupont)、东丽(Toray)等。
生产能力约占PTA总产能的16%。
两种工艺路线差异在于精制方法不同,产品质量也有所差异。
即两种产品所含杂质总量相当,但杂质种类不一样。
PTA产品中所含PT酸较高(200ppm左右),4-CBA较低(25ppm 左右),而QTA(或EPTA)产品中所含杂质与PTA相反,4-CBA 较高(250ppm左右),PT酸较低(25ppm以下)。
两种工艺路线的产品用途基本相同,均用于聚酯生产,最终产品长短丝、瓶片的质量差异不大。
目前,钴-锰-溴三元复合体系是PX氧化的最佳催化剂,其中钴是最贵的,所以目前该方面的一直进行降低氧化催化剂能耗的研究。
PTA生产过程中所用TA加氢反应催化剂为Pd/C,目前研究的主要问题是如何延长催化剂的使用寿命。
工业化的精对苯二甲酸制备工艺很多,但随着生产工艺的不断发展,对二甲苯高温氧化法成为制备精对苯二甲酸的最主要的生产工艺,这种工艺在对苯二甲酸的制备工艺中占有绝对优势。
对二甲苯高温氧化工艺是在高温、高压下进行的,副反应较多;而且由于温度高、压力大对设备本身的要求就高。
因此工艺改进主要就集中在降低氧化反应温度和降低氧化反应的压力两个方面。
对苯二甲酸加氢精制催化剂影响因素的研究
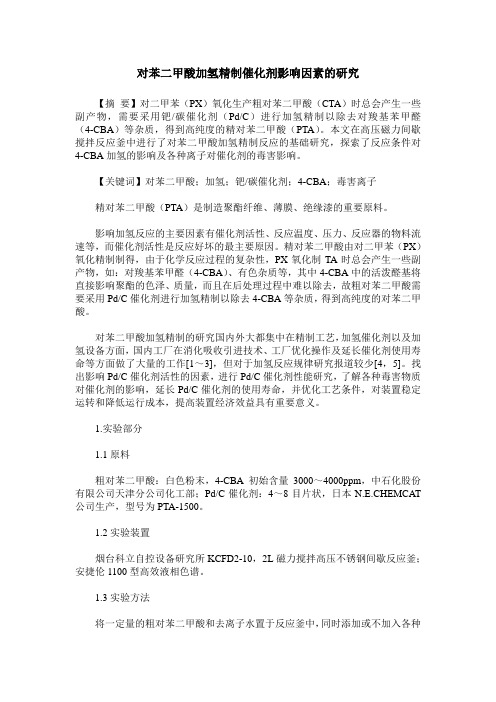
对苯二甲酸加氢精制催化剂影响因素的研究【摘要】对二甲苯(PX)氧化生产粗对苯二甲酸(CTA)时总会产生一些副产物,需要采用钯/碳催化剂(Pd/C)进行加氢精制以除去对羧基苯甲醛(4-CBA)等杂质,得到高纯度的精对苯二甲酸(PTA)。
本文在高压磁力间歇搅拌反应釜中进行了对苯二甲酸加氢精制反应的基础研究,探索了反应条件对4-CBA加氢的影响及各种离子对催化剂的毒害影响。
【关键词】对苯二甲酸;加氢;钯/碳催化剂;4-CBA;毒害离子精对苯二甲酸(PTA)是制造聚酯纤维、薄膜、绝缘漆的重要原料。
影响加氢反应的主要因素有催化剂活性、反应温度、压力、反应器的物料流速等,而催化剂活性是反应好坏的最主要原因。
精对苯二甲酸由对二甲苯(PX)氧化精制制得,由于化学反应过程的复杂性,PX氧化制TA时总会产生一些副产物,如:对羧基苯甲醛(4-CBA)、有色杂质等,其中4-CBA中的活泼醛基将直接影响聚酯的色泽、质量,而且在后处理过程中难以除去,故粗对苯二甲酸需要采用Pd/C催化剂进行加氢精制以除去4-CBA等杂质,得到高纯度的对苯二甲酸。
对苯二甲酸加氢精制的研究国内外大都集中在精制工艺,加氢催化剂以及加氢设备方面,国内工厂在消化吸收引进技术、工厂优化操作及延长催化剂使用寿命等方面做了大量的工作[1~3],但对于加氢反应规律研究报道较少[4,5]。
找出影响Pd/C催化剂活性的因素,进行Pd/C催化剂性能研究,了解各种毒害物质对催化剂的影响,延长Pd/C催化剂的使用寿命,并优化工艺条件,对装置稳定运转和降低运行成本,提高装置经济效益具有重要意义。
1.实验部分1.1原料粗对苯二甲酸:白色粉末,4-CBA初始含量3000~4000ppm,中石化股份有限公司天津分公司化工部;Pd/C催化剂:4~8目片状,日本N.E.CHEMCAT 公司生产,型号为PTA-1500。
1.2实验装置烟台科立自控设备研究所KCFD2-10,2L磁力搅拌高压不锈钢间歇反应釜;安捷伦1100型高效液相色谱。
PTA加氢精制Pd_C催化剂活性降低原因及处理
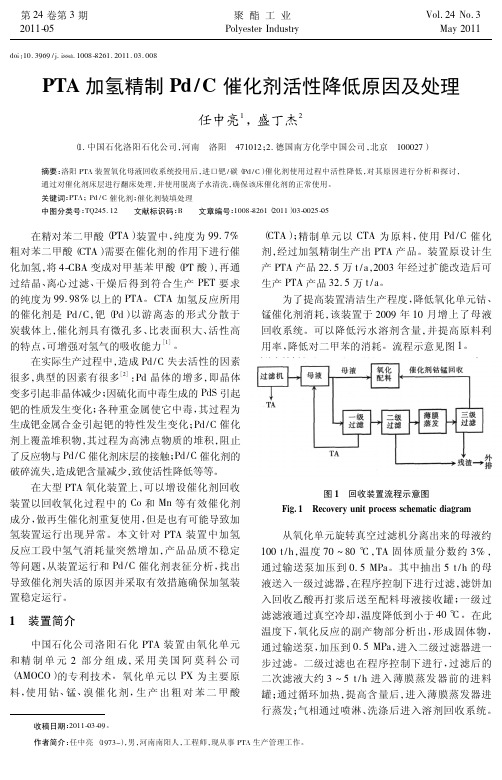
通过分析还可以看出 Pd 的质量分数为0. 46% , 说明催化剂中仍有可观的 Pd 金属,流失不明显,基 本接近新鲜催化剂。
从以上结果可以看出,在装置运行期间,加氢催 化剂 H2MAX-HD 从上游装置收到了很多的杂质,覆 盖在 Pd 的活性位上,被覆盖的 Pd 逐渐降低了催化 活性。
3 催化剂处理
从氧化单元旋转真空过滤机分离出来的母液约 100 t / h,温度 70 ~ 80 ℃ ,TA 固体质量分数约 3% , 通过输送泵加压到 0. 5 MPa。其中抽出 5 t / h 的母 液送入一级过滤器,在程序控制下进行过滤,滤饼加 入回收乙酸再打浆后送至配料母液接收罐; 一级过 滤滤液通过真空冷却,温度降低到小于 40 ℃ 。在此 温度下,氧化反应的副产物部分析出,形成固体物, 通过输送泵,加压到 0. 5 MPa,进入二级过滤器进一 步过滤。二级过滤也在程序控制下进行,过滤后的 二次滤液大约 3 ~ 5 t /h 进入薄膜蒸发器前的进料 罐; 通过循环加热,提高含量后,进入薄膜蒸发器进 行蒸发; 气相通过喷淋、洗涤后进入溶剂回收系统。
为了提高装置清洁生产程度,降低氧化单元钴、 锰催化剂消耗,该装置于 2009 年 10 月增上了母液 回收系统。可以降低污水溶剂含量,并提高原料利 用率,降低对二甲苯的消耗。流程示意见图 1。
图 1 回收装置流程示意图 Fig. 1 Recovery unit process schematic diagram
由于 增 加 了 回 收 系 统,对 装 置 的 操 作 要 求 更 高,当运行条件不稳定,或操作失误时会导致 Co 和 Mn 离子随着 TA 粗原料进入加氢单元,从而影响下 一加氢反应工序。
2 催化剂活性降低原因
2. 1 事情经过 该装置加氢工序采用德国南方化学 H2MAX-HD
pta 工艺技术
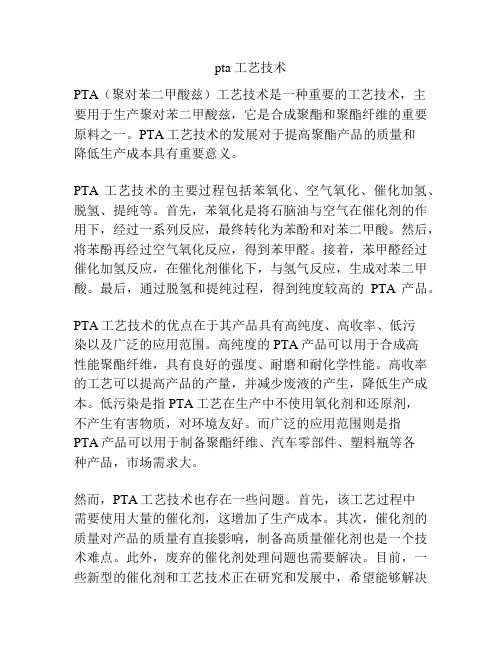
pta 工艺技术PTA(聚对苯二甲酸兹)工艺技术是一种重要的工艺技术,主要用于生产聚对苯二甲酸兹,它是合成聚酯和聚酯纤维的重要原料之一。
PTA工艺技术的发展对于提高聚酯产品的质量和降低生产成本具有重要意义。
PTA工艺技术的主要过程包括苯氧化、空气氧化、催化加氢、脱氢、提纯等。
首先,苯氧化是将石脑油与空气在催化剂的作用下,经过一系列反应,最终转化为苯酚和对苯二甲酸。
然后,将苯酚再经过空气氧化反应,得到苯甲醛。
接着,苯甲醛经过催化加氢反应,在催化剂催化下,与氢气反应,生成对苯二甲酸。
最后,通过脱氢和提纯过程,得到纯度较高的PTA产品。
PTA工艺技术的优点在于其产品具有高纯度、高收率、低污染以及广泛的应用范围。
高纯度的PTA产品可以用于合成高性能聚酯纤维,具有良好的强度、耐磨和耐化学性能。
高收率的工艺可以提高产品的产量,并减少废液的产生,降低生产成本。
低污染是指PTA工艺在生产中不使用氧化剂和还原剂,不产生有害物质,对环境友好。
而广泛的应用范围则是指PTA产品可以用于制备聚酯纤维、汽车零部件、塑料瓶等各种产品,市场需求大。
然而,PTA工艺技术也存在一些问题。
首先,该工艺过程中需要使用大量的催化剂,这增加了生产成本。
其次,催化剂的质量对产品的质量有直接影响,制备高质量催化剂也是一个技术难点。
此外,废弃的催化剂处理问题也需要解决。
目前,一些新型的催化剂和工艺技术正在研究和发展中,希望能够解决这些问题。
为了进一步提高PTA工艺技术的质量和效率,我们可以从以下几个方面进行改进。
首先,优化催化剂的制备工艺,提高催化剂的质量和稳定性,减少生产成本。
其次,改进反应条件和工艺参数,优化反应过程,提高产品收率和纯度。
再次,通过发展新型催化剂和工艺技术,提高PTA工艺技术的效率和环境友好性。
此外,加强废弃物的处理和回收利用,实现资源的可循环利用。
总之,PTA工艺技术是一种重要的工艺技术,对于提高聚酯产品质量和降低生产成本具有重要意义。
年140万吨PTA的氧化反应-结晶系统工艺设计----氧化结晶器的设计【文献综述】

文献综述化学工程与工艺年140万吨PTA的氧化反应-结晶系统工艺设计----氧化结晶器的设计[前言]目前世界PTA生产厂家采用的技术虽有差异,但归纳起来,大致可分为以下两类:(1) 精PTA工艺此工艺采用催化氧化法将对二甲苯(PX)氧化成粗TA,再以加氢还原法除去杂质,将CTA精制成PTA,这种工艺在PTA生产中居主导地位。
(2) 优质聚合级对苯二甲酸(QTA、EPTA)工艺,此工艺采用催化氧化法将PX 氧化成粗TA,再用进一步深度氧化方法将粗TA精制成聚合级TA。
两种工艺路线产品质量有所差异,即两种产品所含杂质总量相当,但杂质种类不一样。
PTA产品中所含PT酸较高(200ppm左右),4-CBA较低(25ppm左右),而QTA(或EPTA)产品中所含杂质与PTA相反,4-CBA较高(250ppm左右),PT 酸较低(25ppm以下)。
我所研究的是PTA生产由粗对苯二甲酸制备(氧化单元)和粗对苯二甲酸精制(精制单元)组成,CTA氧化单元主要由工艺空气压缩机系统,催化剂调配系统。
氧化反应及冷凝系统,结晶,分离,干燥系统,溶剂脱水及MA回收,母液处理系统,尾气洗涤、处理及干燥系统和醋酸收集系统等组成。
反应过程中,原料对二甲苯和醋酸混合物在钴锰催化剂,以溴化氢为促进剂,与空气中氧化反应,生成对苯二甲酸,该反应为放热反应,生成的对苯二甲酸大部分在反映其中结晶出来形成浆料。
由此引出我研究的课题,自氧化反应器出来的浆料经过三个串联的结晶器降温、降压后,由泵送入旋转真空过滤器(RVF)进行固液分离。
结晶阶段的目的是为了减少反应产品的压力和温度,以便通过旋转真空分离器从母液中分离TA晶体。
此外结晶器还在反应段和产品回收段之间提供缓冲能力。
[主题]氧化结晶来自氧化反应器的浆料通过液位控制进入氧化第一结晶器内乙酸和水被闪蒸掉,蒸汽通过氧化第一CTA结晶器冷凝器冷冷凝。
蒸汽在氧化第一结晶器出口冷凝器中得到进一步的冷却。
PTA氧化催化剂技术及其应用
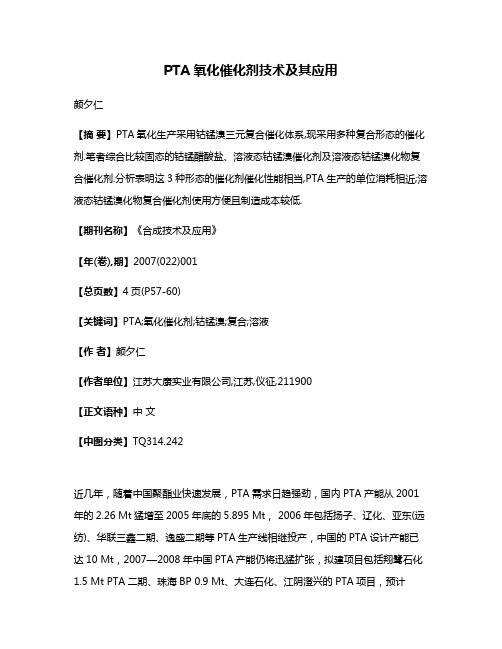
PTA氧化催化剂技术及其应用颜夕仁【摘要】PTA氧化生产采用钴锰溴三元复合催化体系,现采用多种复合形态的催化剂.笔者综合比较固态的钴锰醋酸盐、溶液态钴锰溴催化剂及溶液态钴锰溴化物复合催化剂.分析表明这3种形态的催化剂催化性能相当,PTA生产的单位消耗相近;溶液态钴锰溴化物复合催化剂使用方便且制造成本较低.【期刊名称】《合成技术及应用》【年(卷),期】2007(022)001【总页数】4页(P57-60)【关键词】PTA;氧化催化剂;钴锰溴;复合;溶液【作者】颜夕仁【作者单位】江苏大康实业有限公司,江苏,仪征,211900【正文语种】中文【中图分类】TQ314.242近几年,随着中国聚酯业快速发展,PTA需求日趋强劲,国内PTA产能从2001年的2.26 Mt猛增至2005年底的5.895 Mt, 2006年包括扬子、辽化、亚东(远纺)、华联三鑫二期、逸盛二期等PTA生产线相继投产,中国的PTA设计产能已达10 Mt,2007—2008年中国PTA产能仍将迅猛扩张,拟建项目包括翔鹭石化1.5 Mt PTA二期、珠海BP 0.9 Mt、大连石化、江阴澄兴的PTA项目,预计2008年中国PTA实际产能可达15 Mt。
以中国PTA加工成本(含辅料成本、公用工程、财务费用及折旧)1 200 元/t计,PTA 氧化催化剂钴锰溴合计成本约为60元/t(催化剂不回收,以钴40万元/t、溴素1.3万元/t计),占PTA加工成本的5%,即使采用美国杜邦公司(DuPont)PTA催化剂回收技术,虽理论上可减少近50%的新鲜催化剂的使用量[1],但实际生产中PTA 氧化催化剂钴锰溴合计成本也达到40元/t。
因此降低催化剂的成本已成为降低PTA生产成本的一个重要方面,研究优质、高效且成本较低的PTA氧化催化剂已显得尤为重要。
1 PTA主流生产工艺目前聚合级PTA生产技术主要有两种,即加氢精制工艺及氧化精制工艺。
加氢精制工艺生产的PTA品质较高,也称为精PTA 工艺。
PTA生产技术及工艺流程简述
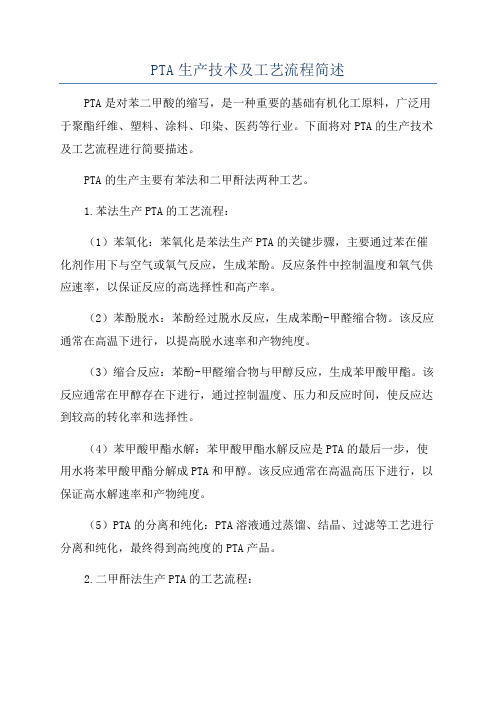
PTA生产技术及工艺流程简述PTA是对苯二甲酸的缩写,是一种重要的基础有机化工原料,广泛用于聚酯纤维、塑料、涂料、印染、医药等行业。
下面将对PTA的生产技术及工艺流程进行简要描述。
PTA的生产主要有苯法和二甲酐法两种工艺。
1.苯法生产PTA的工艺流程:(1)苯氧化:苯氧化是苯法生产PTA的关键步骤,主要通过苯在催化剂作用下与空气或氧气反应,生成苯酚。
反应条件中控制温度和氧气供应速率,以保证反应的高选择性和高产率。
(2)苯酚脱水:苯酚经过脱水反应,生成苯酚-甲醛缩合物。
该反应通常在高温下进行,以提高脱水速率和产物纯度。
(3)缩合反应:苯酚-甲醛缩合物与甲醇反应,生成苯甲酸甲酯。
该反应通常在甲醇存在下进行,通过控制温度、压力和反应时间,使反应达到较高的转化率和选择性。
(4)苯甲酸甲酯水解:苯甲酸甲酯水解反应是PTA的最后一步,使用水将苯甲酸甲酯分解成PTA和甲醇。
该反应通常在高温高压下进行,以保证高水解速率和产物纯度。
(5)PTA的分离和纯化:PTA溶液通过蒸馏、结晶、过滤等工艺进行分离和纯化,最终得到高纯度的PTA产品。
2.二甲酐法生产PTA的工艺流程:(1)二甲酐合成:将甲醇和二氧化碳反应,在催化剂的作用下生成二甲酐。
该反应通常在高压高温下进行,比苯法生产PTA的反应条件更加严苛。
(2)二甲酐氧化:将二甲酐在空气或氧气气氛中进行氧化反应,生成苯酐。
该反应通常在高温下进行,以保证高转化率和产物纯度。
(3)苯酐脱羧:苯酐经过脱羧反应,生成苯酚。
该反应通常在高温下进行,通过控制反应条件,使反应达到较高的选择性和产率。
(4)苯酚脱水、缩合和水解:与苯法生产PTA的工艺流程相同,依次进行苯酚脱水、缩合和水解反应,最终得到纯度较高的PTA产品。
(5)PTA的分离和纯化:与苯法生产PTA的工艺流程相同,通过蒸馏、结晶、过滤等工艺进行分离和纯化,最终得到高纯度的PTA产品。
总的来说,PTA的生产技术及工艺流程包括苯氧化、苯酚脱水、缩合反应、苯甲酸甲酯水解、PTA的分离和纯化等步骤。
有机化学中的脱水反应
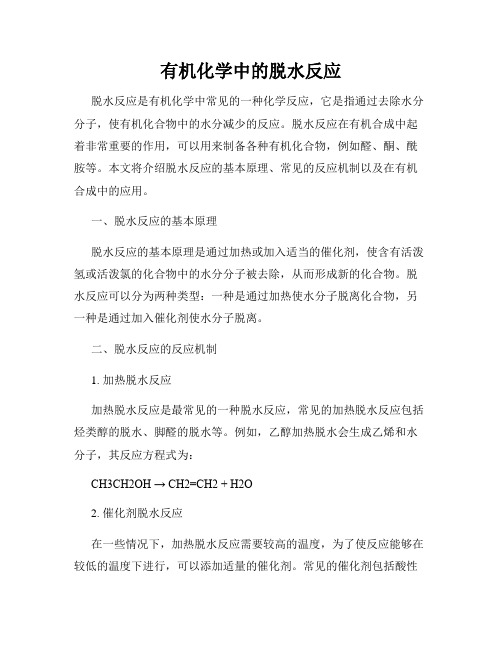
有机化学中的脱水反应脱水反应是有机化学中常见的一种化学反应,它是指通过去除水分分子,使有机化合物中的水分减少的反应。
脱水反应在有机合成中起着非常重要的作用,可以用来制备各种有机化合物,例如醛、酮、酰胺等。
本文将介绍脱水反应的基本原理、常见的反应机制以及在有机合成中的应用。
一、脱水反应的基本原理脱水反应的基本原理是通过加热或加入适当的催化剂,使含有活泼氢或活泼氯的化合物中的水分分子被去除,从而形成新的化合物。
脱水反应可以分为两种类型:一种是通过加热使水分子脱离化合物,另一种是通过加入催化剂使水分子脱离。
二、脱水反应的反应机制1. 加热脱水反应加热脱水反应是最常见的一种脱水反应,常见的加热脱水反应包括烃类醇的脱水、脚醛的脱水等。
例如,乙醇加热脱水会生成乙烯和水分子,其反应方程式为:CH3CH2OH → CH2=CH2 + H2O2. 催化剂脱水反应在一些情况下,加热脱水反应需要较高的温度,为了使反应能够在较低的温度下进行,可以添加适量的催化剂。
常见的催化剂包括酸性催化剂和碱性催化剂。
酸性催化剂可使醇类、酚类、酰胺等化合物中的水分子脱离,而碱性催化剂则可使酰胺、酸酐等化合物中的水分子脱离。
催化剂脱水反应广泛应用于有机合成中,常见的反应有酯化反应、酰胺化反应等。
三、脱水反应在有机合成中的应用脱水反应在有机合成领域有广泛的应用。
以酯化反应为例,酯化反应是通过酸催化剂催化酸与醇反应,形成酯的反应。
这种反应用于许多化学行业,例如食品产业中的香精制备、医药行业中的药物合成等。
另一个例子是酰胺化反应,通过在碱性环境下进行的酰胺化反应可以制备出各种酰胺类化合物,这些化合物广泛应用于农药、染料等领域。
总结:脱水反应作为一种常见的有机化学反应,具有重要的理论和应用价值。
它通过去除有机化合物中的水分分子,来合成各种有机化合物,具有广泛的应用前景。
在实际应用中,我们需要针对不同的化合物选择适当的脱水反应条件,以获得最终合成目标化合物。
- 1、下载文档前请自行甄别文档内容的完整性,平台不提供额外的编辑、内容补充、找答案等附加服务。
- 2、"仅部分预览"的文档,不可在线预览部分如存在完整性等问题,可反馈申请退款(可完整预览的文档不适用该条件!)。
- 3、如文档侵犯您的权益,请联系客服反馈,我们会尽快为您处理(人工客服工作时间:9:00-18:30)。
通用机械
脱
扬子石油化工股份有限公司化工厂副总工程师 沈品德
PTA 加氢精制工艺中的应用
图 PTA精制工艺流程图
1.混合罐
2.溶解罐
3.加氢反应器
4.第一结晶器
5.第二结晶器
6.第五结晶器
7.压力离心机
8.真空过滤机
9.干燥机
脱水技术在
2008年 第 4 期
33
通
二、压力离心机系统
PTA生产中,要保证压力离心机系统稳定运行。
压力离心机系统是控制产品质量的重要环节,离心机分离效果的好坏直接影响到产品中PT酸和其他杂质的含量。
因此,要定期对离心机系统进行检查,保证离心机油路系统的正常运行,并定期对离心机系统做一些常规处理。
由于T A料和P T酸易在压力离心机的转鼓、支架、进料管和出料管线处粘壁,降低压力离心机的处理能力,使得滤饼中的含湿量增加,从而影响到产品质量。
另外由于压力离心机内转子和支架上的结料,会增加离心机的振动,使离心机的故障率增加,因此,要对离心机进行水洗和碱洗操作,包括定期和不定期的处理,从而延长离心机的运行周期,减少检修频次。
(1)水洗 切断离心机进料,切进冲洗水,对压力离心机进行在线冲洗,大约5~10m i n,水洗后恢复进料。
保证每天水洗一次。
(2)碱洗 停机进料,切水冲洗;停止水洗,降温降压隔离;进料管进碱,根据工艺及设备要求确定碱洗时间;停止碱洗,切为水洗,至排出液呈中性为止;系统升温升压,解除隔离进料。
一般情况下1个月碱洗1次;特殊情况下,根据产品的质量和离心机的运行情况而定,当产品中的P T酸含量偏高或离心机的振动偏大时,要进行碱洗。
三、真空过滤技术的应用
1.进料温度的控制
如果温度过高,会引起溶液闪蒸,造成滤布堵塞,控制时在过滤机进料处加入脱离子水,降低溶液的温度,使其降到89℃左右。
2.进料浓度的控制
进料浓度的控制主要是用来控制滤饼的厚度,滤饼过厚会引起洗涤效果差,滤饼的含湿量增加,影响产品的质量,因此料浆浓度应控制在35%~45%。
3.真空度的控制
真空度过高会引起滤饼厚度增加,造成过滤机的负荷过高,前后物料不能平衡,真空度过低会引起滤饼的含湿量增加,影响产品质量,因此过滤机的真空度应控制在-0.045~0.049MPa范围内。
4.溢流堰高度的调节
如果溢流堰太高会引起滤饼的厚度增加,造成滤
饼的含湿量增加,影响产品的质量,并造成前后物料不平衡。
如果溢流堰过低,要增加过滤机的转速,同样造成滤饼的含湿量增加。
5.反吹气量的控制
反吹气量控制过低,滤饼不能有效地吹下,影响过滤效果,如果过高会造成料斗中浆料喷料,缩短滤布的使用周期,因此,生产中反吹气量应控制在15~40kPa。
6.洗涤水量的控制
洗涤水量的控制主要是用来控制产品的质量,洗涤水量过低会造成产品中的杂质含量高,影响产品的质量;如果洗涤水量过高会增加滤饼的含湿量,增加干燥机的能量损耗,因此洗涤水量控制在8~15m 3/h。
7.应用效果
以真空过滤机为核心设备的过滤系统取代常压离心机后,系统运转平稳,故障率低,完全满足生产工艺要求。
(1)检修费用低 常压离心机由于转鼓经常结料,因此维护保养较为困难,经常发生易熔塞化、剪切销断裂等故障,并需经常更换齿轮箱、大轴承和轴瓦等备件,每年检修费用约60万元/台。
而采用真空过滤机后,除滤布定期更换外,其他基本上可实现每两年一修,大大降低了检修成本。
(2)运行成本低 该单元采用真空过滤机系统比采用常压离心机系统每小时可节能约200kW·h。
同时每年可节约10~15万元的油脂、润滑油等费用。
(3)产品质量提供 采用真空过滤机后,产品中P T含量比采用常压离心机时整体下降了约10m g/k g,特别是可以通过调节真空过滤机洗液量来调节产品中的P T含量,解决了精制生产中P T酸波动幅度大的难题,产品质量得到了有效控制。
(4)处理能力大 常压离心机单台处理量小,产能低,满负荷生产时,3台离心机必须全部运行。
采用真空过滤机后,实现了“一开一备”模式,且两套真空系统可以互为备用,极大地提高了精制单元后系统的处理能力。
四、PTA物料干燥
P T A物料干燥机为倾斜回转列管式干燥设备,用于干燥含湿量约10%~15%P T A滤饼,除去其中的水分,
通用机械
脱
得到干燥粉状物料。
1.传统干燥工艺
传统的工艺路线为常压离心机分离得到P T A滤饼,进入离心机下料导向螺旋,然后由干燥机入口螺旋输送入干燥机,经干燥后的P T A进入正反螺旋输送器分配到风送系统的旋转阀。
传统干燥系统中以往出现的问题有干燥机入口出口螺旋输送器物料输送不畅,超载跳车;物料在干燥机入口加热管上堆积,堵塞载气通道,造成干燥机内压升高,使生产能力下降。
2.优化干燥机单元
(1)干燥机入口流程优化 真空过滤机滤饼较常压离心机下料的含湿量高约2%左右,增大螺旋推力,增加在干燥机内蒸发量。
干燥机入口由一级螺旋改为两级螺旋输送,第二级由实体螺旋改为螺带输送器,增加载气通道的流通能力。
(2)稳定载气系统运行 ①定期检查真空喷射系统,增加过滤器滤网,防止喷嘴堵塞,造成干燥机内压波动。
②确保真空过滤机下料滤饼低含湿量,避免在干燥机内过大的蒸发量。
③定期检查干燥机下料旋转阀抽气系统,防止反窜气量过大,影响干燥机内压。
五、结束语
以上扬子石化P T A加氢精制工艺脱水单元的操作经验是通过工业化生产装置操作经验和同类装置类比分析得出的。
在产品质量符合要求的前提下,缩短工艺流程,降低生产成本,是下一步的研究方向。
精制单元产品分离的最新技术是压力过滤技术,采用压力过滤机的
一级分离取代传统工艺的二级分离,这一技术代表着精制产品分离工业的最新发展趋势。
目前,扬子石化正与院校联合开发压力过滤机,中试已经完成,下一步准备开发处理能力50t/h(干基)PTA物料在压力过滤机及与其配套的50t/h(干基)PTA物料旋转阀。