完整word版液压系统回路设计
液压基本回路(有图)
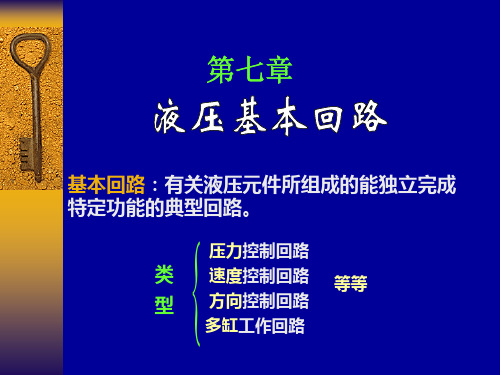
快速-慢速的换接回路
AT1
采用调速阀串联的慢 速-慢速的换接回路
AT2 AT1
AT2
AT1
AT1 ≠AT2 采用调速阀并联的慢速-慢速的换接回路
类型:
启动、停止(包括锁紧)和换向回路。
一、启停回路
执行元件需频繁启动或停止的液压系统中,一般不采 用启动和停止电机的方法。
采用二位二通、二位三通电磁阀或中位为O,Y,M型 的三位四通换向阀来实现。
活塞运动速度(负载特性方程):
v
q2 Α2
ΚΑΤ ΔPm Α2
ΚΑΤ(Pp A1 R)m Α2m 1
分析: ①当R=0 时,
v KAT PP A1m A2m 1
(空载)
②当R=PP A1 时,v=0(停止运动)
速度刚度: Th
R v
PP A1 R mv
Tj
v AT1
3、变量泵-变量马达组成的容积调速回路
属上述二者的组合,可满足低速时有大转矩,高速时有 大功率。
p1
qP
TM
nM VM
p2
4、容积调速回路特点
① 无节流损失和溢流损失,回路效率高,系统发热小。 ② 速度稳定性好,但随着负载增加,容积效率降低,导
致低速时速度稳定性比采用调速阀的节流调速回路差。 ③ 泵和马达结构复杂,成本高。 ④ 适用于高速、大功率调速系统。
AT2
即:回油节流调速的v-R 特性与进油 AT3
节流调速完全相同。两者特性曲线完
全相同。
0
AT1 > AT2 > AT3
Rmax R
(2)特点
① ∵P2≠ 0,有背压,∴运动平稳性较好;随负载变化, 速度变化,速度稳定性差。即V-R特性软。
液压系统基本回路(识图)

3.2减压回路
、二级减压回路
二级减压回路
说明:在减压阀2的遥控口通过电磁阀4接入小规格调压阀3,便可获得两种 稳定的低压,减压阀2的出口压力由其本身来调定。当电磁阀4通电时,减 压阀2的出口压力就由调压阀3进行设定。
3.2减压回路
、多路减压回路
多路减压回路
说明:在同一液压源供油的系统里可以设置多个不同工作压力的减压回 路。如图所示:两个支路分别以15Mpa和8Mpa压力工作时可分别用各自的 减压阀进行控制。
卸荷阀卸荷回路
3.6平衡回路
、用液控单向阀的平衡回路
说明:液压缸停止运动时,依靠 液控单向阀的反向密封性,能锁 紧运动部件,防止自行下滑。回 路通常都串入单向节流阀2,起 到控制活塞下行速度的作用。以 防止液压缸下行时产生的冲击及 振荡。
用液控单向阀的平衡回路
3.6平衡回路
、用远控平衡阀的平衡回路
用单向节流阀的平衡回路
四、速度控制回路
在液压系统中,一般液压源是共用的,要解决各执行元件的 不同速度要求,只能用速度控制回路来调节。
4.1节流调速回路
节流调速装置都是通过改变节流口的大小来控制流量,故调速范围 大,但由节流引起的能量损失大、效率低、容易引起油液发热;
以节流元件安装在油路上的位置不同,可分为进口节流调速、出口节 流调速、旁路节流调速及双向节流调速。
旁路节流调速回路
4.2增速回路
差动连接增速回路
说明:当手动换向阀处于左 位时,液压缸为差动连接,活 塞快速向右运行。液压泵供 给液压缸的流量为qv,液压缸 无杆腔和有杆腔的有效作用 面积分别为A1和A2,则液压缸 活塞运动速度为V=qv/(A1-A2)
差动连接增速回路
4.2增速回路
液压系统基本回路

板书设计或授课提纲
课堂教学安排
分组讨论
二位四通电磁换向阀的换向回路
三位四通手动换向阀的换向回路
2.锁紧回路
O型中位机能三位四通电磁换向阀的锁紧
回路
二、压力控制回路
1.调压回路
调压回路的功用:
使液压系统或某一部分的压力保持恒定
或不超过某个数值。
调压功能主要由溢流
5.带领学生共同
总结结论
5.在教师的引
导下,分析动
画,与教师一起
总结出板书
阀完成
2.支路减压回路
支路减压回路的功用:
使系统中某一部分油路具有较低的稳定压力
3.增压回路
功用:使系统中局部油路或个别执行元件的压力得到比主系统压力高得多的压力。
4.卸荷回路
功用:使液压泵驱动电动机不频繁启闭,让液压泵在接近零压的情况下运转,以减少功率损失和系统发热,延长泵和电动机的使用寿命。
三、速度控制回路
控制执行元件运动速度的回路
1.调速回路
用于调节工作行程速度的回路
2.速度换接回路
速度换接回路是使不同速度相互转换的回路
(1)液压缸差动连接速度换接回路(2)短接流量阀速度换接回路
(3)串联调速阀速度换接回路
(4)并联调速阀速度换接回路
四、顺序动作控制回路
采用两个单向顺序阀的压力控制顺序动作回路
该回路可实现液压缸6和液压缸7按照“A1—B1—B0—A0”的顺序动作
五、汽车升降平台液压传动系统
1.汽车升降平台的结构。
液压基本回路设计
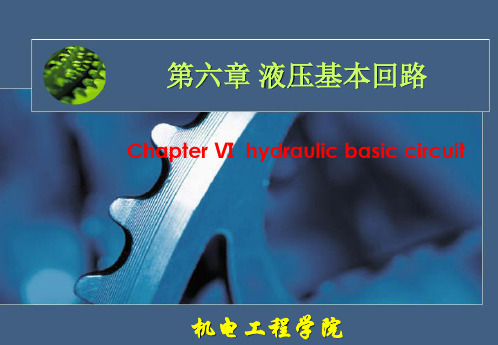
机构的回油腔吸油。闭式回路结构紧凑,只需很小的补油箱,但 冷却条件差,为了补偿工作中油液的泄漏,一般设补油泵,补油 泵的流量为主泵流量的10%~15%,压力调节为3×105~10×105Pa。
节流调速回路分类
支路(旁路)节流调速
(1)工作原理 溢流阀正常工作是关闭
的,只有过载时才打开, 作安全阀使用。见右图。
支路(旁路)节流调速
(2)速度—负载特性
pT p1 F A1
qT
CT AT
pTm
CT
AT
(
F A1
)m
q1 qB qT
v
q1
qB
CT
AT
(
F A1
)m
A1
A1
支路(旁路)节流调速
当m 0.5时
3
Kv
dF dv
2A12 F CT AT
2 A1F qB A1v
支路(旁路)节流调速
支路(旁路)节流调速
支路(旁路)节流调速
结论:
➢这种回路只有节流损失而无溢流损失;泵压随 负载变化,即节流损失和输入功率随负载而增 减。因此,本回路比前两种回路效率高。
➢由于本回路的速度-负载特性很软,低速承载 能力差,故其应用比前两种回路少,只用于高 速、重载、对速度平稳性要求不高的较大功率 的系统,如牛头刨床主运动系统、输送机械液 压系统等。
蓄能器保压回路
利用限压式变量油泵的保压回路
在讲单作用式叶片变量泵 时,已提到过,当定子与转 子圆心偏移量(单作用式叶 片变量泵)很小或斜盘倾斜 角很小时,泵的流量仅能维 持自身泄漏,对油路不输出 油液,但泵仍在一定压力下 运转,对外输出恒定压力, 则可使系统压力恒定(参见 泵一章有关内容),此时泵 输出功率较小(功率=流量 ×压力)。
(完整版)液压传动课程设计-液压系统设计举例

液压系统设计计算举例液压系统设计计算是液压传动课程设计的主要内容,包括明确设计要求进行工况分析、确定液压系统主要参数、拟定液压系统原理图、计算和选择液压件以及验算液压系统性能等。
现以一台卧式单面多轴钻孔组合机床动力滑台液压系统为例,介绍液压系统的设计计算方法。
1 设计要求及工况分析1.1设计要求要求设计的动力滑台实现的工作循环是:快进 → 工进 → 快退 → 停止。
主要性能参数与性能要求如下:切削阻力F L =30468N ;运动部件所受重力G =9800N ;快进、快退速度υ1= υ3=0.1m/s ,工进速度υ2=0.88×10-3m/s ;快进行程L 1=100mm ,工进行程L 2=50mm ;往复运动的加速时间Δt =0.2s ;动力滑台采用平导轨,静摩擦系数μs =0.2,动摩擦系数μd =0.1。
液压系统执行元件选为液压缸。
1.2负载与运动分析(1) 工作负载 工作负载即为切削阻力F L =30468N 。
(2) 摩擦负载 摩擦负载即为导轨的摩擦阻力: 静摩擦阻力 N 196098002.0s fs =⨯==G F μ 动摩擦阻力 N 98098001.0d fd =⨯==G F μ (3) 惯性负载N 500N 2.01.08.99800i =⨯=∆∆=t g G F υ(4) 运动时间快进 s1s 1.0101003111=⨯==-υL t工进 s 8.56s 1088.0105033222=⨯⨯==--υL t快退s5.1s 1.010)50100(33213=⨯+=+=-υL L t设液压缸的机械效率ηcm =0.9,得出液压缸在各工作阶段的负载和推力,如表1所列。
表1液压缸各阶段的负载和推力工况 负载组成液压缸负载F /N液压缸推力F 0=F /ηcm /N启 动 加 速 快 进 工 进 反向启动 加 速 快 退fs F F = i fd F F F += fd F F = L fd F F F += fs F F = i fd F F F += fd F F =1960 1480 980 31448 1960 1480 9802180 1650 1090 34942 2180 1650 1090根据液压缸在上述各阶段内的负载和运动时间,即可绘制出负载循环图F -t 和速度循环图υ-t ,如图1所示。
(完整word版)液压系统回路设计

1、液压系统回路设计1.1、 主干回路设计对于任何液压传动系统来说, 调速回路都是它的核心部分。
这种回路可以通过事先的调整或在工作过程中通过自动调整来改变元件的运行速度, 但它的主要功能却是在传递动力(功率)。
根据伯努力方程: 2d v p q C x ρ∆= (1-1)式中 q ——主滑阀流量d C ——阀流量系数v x ——阀芯流通面积p ∆——阀进出口压差ρ——流体密度其中 和 为常数, 只有 和 为变量。
液压缸活塞杆的速度:q v A= (1-2) 式中A 为活塞杆无杆腔或有杆腔的有效面积一般情况下, 两调平液压缸是完全一样的, 即可确定 和 所以要保证两缸同步, 只需使 , 由式(1-2)可知, 只要主滑阀流量一定, 则活塞杆的速度就能稳定。
又由式(1-1)分析可知, 如果 为一定值, 则主滑阀流量 与阀芯流通面积成正比即: ,所以要保证两缸同步, 则只需满足以下条件:, 且此处主滑阀选择三位四通的电液比例方向流量控制阀,如图1-1所示。
图1-1 三位四通的电液比例方向流量控制阀它是一种按输入的电信号连续地、按比例地对油液的流量或方向进行远距离控制的阀。
比例阀一般都具有压力补偿性能, 所以它输出的流量可以不受负载变化的影响。
与手动调节的普通液压阀相比, 它能提高系统的控制水平。
它和电液伺服阀的区别见表1-1。
表1-1 比例阀和电液伺服阀的比较项目 比例阀 伺服阀低, 所以它被广泛应用于要求对液压参数进行连续远距离控制或程序控制, 但对控制精度和动态特性要求不太高的液压系统中。
又因为在整个举身或收回过程中, 单缸负载变化范围变化比较大(0~50T), 而且举身和收回时是匀速运动, 所以调平缸的功率为, 为变功率调平, 为达到节能效果, 选择变量泵。
综上所可得, 主干调速回路选用容积节流调速回路。
容积节流调速回路没有溢流损失, 效率高, 速度稳定性也比单纯容积调速回路好。
为保证值一定, 可采用负荷传感液压控制, 其控制原理图如图1-2所示。
(完整word版)液压系统设计方法
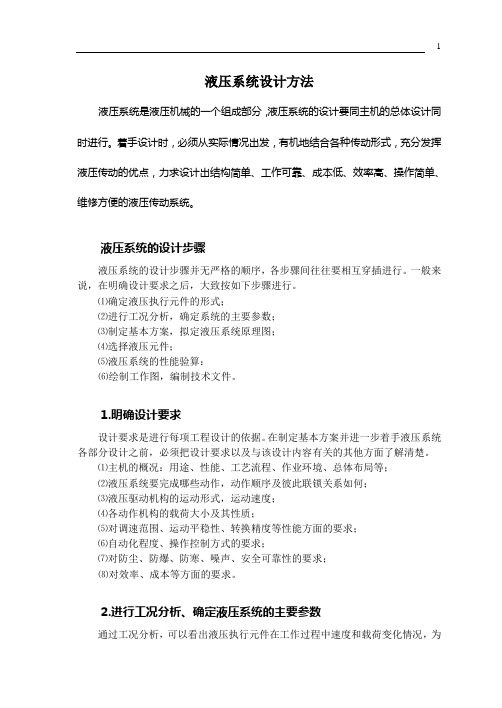
液压系统设计方法液压系统是液压机械的一个组成部分,液压系统的设计要同主机的总体设计同时进行。
着手设计时,必须从实际情况出发,有机地结合各种传动形式,充分发挥液压传动的优点,力求设计出结构简单、工作可靠、成本低、效率高、操作简单、维修方便的液压传动系统。
液压系统的设计步骤液压系统的设计步骤并无严格的顺序,各步骤间往往要相互穿插进行。
一般来说,在明确设计要求之后,大致按如下步骤进行。
⑴确定液压执行元件的形式;⑵进行工况分析,确定系统的主要参数;⑶制定基本方案,拟定液压系统原理图;⑷选择液压元件;⑸液压系统的性能验算:⑹绘制工作图,编制技术文件。
1.明确设计要求设计要求是进行每项工程设计的依据。
在制定基本方案并进一步着手液压系统各部分设计之前,必须把设计要求以及与该设计内容有关的其他方面了解清楚。
⑴主机的概况:用途、性能、工艺流程、作业环境、总体布局等;⑵液压系统要完成哪些动作,动作顺序及彼此联锁关系如何;⑶液压驱动机构的运动形式,运动速度;⑷各动作机构的载荷大小及其性质;⑸对调速范围、运动平稳性、转换精度等性能方面的要求;⑹自动化程度、操作控制方式的要求;⑺对防尘、防爆、防寒、噪声、安全可靠性的要求;⑻对效率、成本等方面的要求。
2.进行工况分析、确定液压系统的主要参数通过工况分析,可以看出液压执行元件在工作过程中速度和载荷变化情况,为确定系统及各执行元件的参数提供依据。
液压系统的主要参数是压力和流量,它们是设计液压系统,选择液压元件的主要依据。
压力决定于外载荷。
流量取决于液压执行元件的运动速度和结构尺寸。
2.1载荷的组成和计算2.1.1液压缸的载荷组成与计算图1表示一个以液压缸为执行元件的液压系统计算简图。
各有关参数已标注在图上,其中F W是作用在活塞杆上的外部载荷。
F m是活塞与缸壁以及活塞杆与导向套之间的密封阻力。
作用在活塞杆上的外部载荷包括工作载荷F g,导轨的摩擦力F f和由于速度变化而产生的惯性力F a。
(完整word版)飞机起落架液压系统设计

前言任何人造的飞行器都有离地升空的过程,而且除了一次性使用的火箭导弹和不需要回收的航天器之外,绝大部分飞行器都有着陆或回收阶段。
对飞机而言,实现这一起飞着陆功能的装置主要就是起落架。
起落架就是飞机在地面停放、滑行、起飞着陆滑跑时用于支撑飞机重力,承受相应载荷的装置。
简单地说,起落架有一点象汽车的车轮,但比汽车的车轮复杂的多,而且强度也大的多,它能够消耗和吸收飞机在着陆时的撞击能量。
概括起来,起落架的主要作用有以下四个:1)承受飞机在地面停放、滑行、起飞着陆滑跑时的重力;2)承受、消耗和吸收飞机在着陆与地面运动时的撞击和颠簸能量;3)滑跑与滑行时的制动;4)滑跑与滑行时操纵飞机。
在过去,由于飞机的飞行速度低,对飞机气动外形的要求不十分严格,因此飞机的起落架都是固定的,这样对制造来说不需要有很高的技术。
当飞机在空中飞行时,起落架仍然暴露在机身之外。
随着飞机飞行速度的不断提高,飞机很快就跨越了音速的障碍,由于飞行的阻力随着飞行速度的增加而急剧增加,这时,暴露在外的起落架就严重影响了飞机的气动性能,阻碍了飞行速度的进一步提高。
因此,人们便设计出了可收放的起落架,当飞机在空中飞行时就将起落架收到机翼或机身之内,以获得良好的气动性能,飞机着陆时再将起落架放下来。
然而,有得必有失,这样做的不足之处是由于起落架增加了复杂的收放系统,使得飞机的总重增加。
但总的说来是得大于失,因此现代飞机不论是军用飞机还是民用飞机,它们的起落架绝大部分都是可以收放的,只有一小部分超轻型飞机仍然采用固定形式的起落架。
所以说设计设计一种安全可靠性能良好和轻便的飞机起落架液压控制系统是十分必要的。
本次设计就一这论题展开设计。
1 绪论液压技术是一门古老而又兴起的学科,随着技术的不断革新近百年来又长足的进展。
它被广泛的应用在各行各业中,诸如,机床液压、矿山机械、石油化工、冶炼技术以及航天航空等方面。
可以说液压技术的发展,密切关系着我国计民生的许多方面。
- 1、下载文档前请自行甄别文档内容的完整性,平台不提供额外的编辑、内容补充、找答案等附加服务。
- 2、"仅部分预览"的文档,不可在线预览部分如存在完整性等问题,可反馈申请退款(可完整预览的文档不适用该条件!)。
- 3、如文档侵犯您的权益,请联系客服反馈,我们会尽快为您处理(人工客服工作时间:9:00-18:30)。
1、液压系统回路设计
1.1、主干回路设计
对于任何液压传动系统来说,调速回路都是它的核心部分。
这种回路可以通过事先的调整或在工作过程中通过自动调整来改变元件的运行速度,但它的主要功能却是在传递动力(功率)。
根据伯努力方程:
2?pxq?C(1-1)vd?式中——主滑阀流量q C——阀流量系数d x——阀芯流通面积v——阀进出口压差p??——流体密度
?xC和为变量。
为常数,只有其中和p?vd液压缸活塞杆的速度:
q (1-2)?v A式中为活塞杆无杆腔或有杆腔的有效面积A A?AA?A所一般情况下,两调平液压缸是完全一样的,即可确定和21112212q?q,由式(1-2)可知,只要主滑阀流量一定,以要保证两缸同步,只需使21则活塞杆的速度就能稳定。
又由式(1-1)分析可知,如果为一定值,则主滑p?q?x,所以要保证两缸同步,则只需满足以阀流量与阀芯流通面积成正比即:q v下条件:
?p?c?p?cx?x,且112v2v21此处主滑阀选择三位四通的电液比例方向流量控制阀,如图1-1所示。
三位四通的电液比例方向流量控制阀图1-1
它是一种按输入的电信号连续地、按比例地对油液的流量或方向进行远距离控制所以它输出的流量可以不受负载变化的比例阀一般都具有压力补偿性能,的阀。
.影响。
与手动调节的普通液压阀相比,它能提高系统的控制水平。
它和电液伺服阀的区别见表1-1。
表1-1 比例阀和电液伺服阀的比较
与电液伺服阀相比,它虽在某些性能方面稍逊色些,但它的结构简单,成本低,但对控制所以它被广泛应用于要求对液压参数进行连续远距离控制或程序控制,精度和动态特性要求不太高的液压系统中。
,)又因为在整个举身或收回过程中,单缸负载变化范围变化比较大(0~50T为为变功率调平,而且举身和收回时是匀速运动,所以调平缸的功率为,Fv?P 达到节能效果,选择变量泵。
综上所可得,主干调速回路选用容积节流调速回路。
容积节流调速回路没有溢流损失,效率
高,速度稳定性也比单纯容积调速回路好。
p?所示。
值一定,可采用负荷传感液
压控制,其控制原理图如图为保证1-2驱动多个执行元件,可用单泵(或一组泵)它主要利用负荷传感和压力补偿技术,而与各执行元件的负载压力和其各执行元件运动速度仅依赖于各节流阀开启度,各执行元即使当泵的输出流量达不到实际需要时,它执行元件的工作状态无关。
此系统的这一特有的独立调速功能大件运动速度的比例关系仍然可以得到保持。
不但显著提高了作业大减少了作业中操纵者协调各执行元件动作所花费的时间,能够以最节省能量的方式实现效率,而且有效减轻了操作者的劳动强度。
另外,在工作间系统无溢流损失,并以推动执行元件动作所需的最低压力供油。
调速,系统自动调节泵的排量不动作),各执行元件处于无载状态,(隙发动机不停机,所以它是一种性能较可以有效降低功率损耗、到最小值。
减小液压系统的温升,好的新型液压系统。
.一般的同步回路还有:机械连接同步回路;用分流阀或分流集流阀的同步回路;用调速阀的同步回路;串联缸的同步回路等,但这些同步回路同步精度一般比较低,而且大多数只是保证速度同步而不能保证位置同步,受负载变化的影响较大。
同步控制系统原理图图1-2 LS图中两个执行元件中的最高压力,可以通过单向阀选出,作为负荷传感压力P分别引到负荷传感阀和各压力补偿阀的弹簧腔。
当负荷传感阀芯及各压力补LS Pp加上负荷传感阀下腔偿阀芯达到平衡时,各节流口前压力为负荷传感压力LS1pPp加上压力补偿阀左腔均为负荷传感压力弹簧压力; 各节流口后压力LS2KL p,两节流口压力差为:弹簧压力
KC?p?p?p?p?p KC21KL可知,只与两弹簧弹力有关,所以只要保证两弹簧压力差恒定,则值基本p?p?为一定值。
因而通过各节流口流向执行元件的流量与各节流口大小有关,而与每一执行元件的负载压力无关。
为保证桅杆工作时的垂直度,选用一种倾角传感器,将检查到的角度偏差信号转换成电信号,控制电液比例方向流量控制阀,从而调节桅杆的垂直度。
组干
所示。
1-3回路如图
图1-3 主干回路
1、2 其它回路选择
1、平衡回路
平衡回路的功用在于防止垂直或倾斜放置的液压缸和与之相连的工作部件因自重而自行下落。
桅杆后仰和前倾时都要平衡,因此连接油缸两端的回油路上都要设有起平衡作用的阀。
下面主要考虑两种平衡回路,分别如图1-4和1-5所示。
.
图1-4 用直控平衡阀的平衡回路
用直控平衡阀的平衡回路。
调整平衡阀的开启压力,使其稍大于立式液压缸活塞及其工作部件自重在液压缸下腔所产生的压力,活塞部件则不会因自重而下落。
活塞下降时,运动平稳,但功耗较大。
用远控平衡阀平衡的回路1-5 图
用远控平衡阀平衡的平衡回路。
远控平衡阀的开启取决于控制压力,与载荷无关。
在活塞下行时,平衡阀被控制油打开,被压很小,故系统效率较高。
但活塞部件有可能加速下滑,以致产生振荡,所以应在平衡阀的控制口接入节流阀。
2、锁紧回路
锁紧回路的功用是在液压执行元件不工作时切断其进、出油通道,确切地使是它保持在既定的位置上。
下面也主要考虑两种锁紧回路,如图1-6和1-7所
示。
图1-6 用换向阀锁紧的回路
用换向阀锁紧的回路。
三位四通换向阀在中位时,分别与油缸相连的两油路被封闭,构成了双向锁紧回路。
采用换向阀锁紧,回路简单,但是锁紧精度较低。
图1-7 用液控单向阀双向锁紧的回路
用液控单向阀双向锁紧的回路。
用两个液控单向阀可实现对液压缸的双向锁紧。
图示位置时,液压泵卸荷,两个液控单向阀均为关闭,活塞被所在不动。
活塞可以在任意位置被锁紧。
考虑桅杆的功能要求:由于桅杆自身重力的作用,举身过程要比较平稳,而且在任意位置要能被锁定,所以被压阀的压力值要设得比较小;工作是也要很再考虑所以被压阀值要设得比较大。
前倾是也要平稳和能被锁住,好的被锁住;
到平衡和锁紧的功能,可以使用液控平衡阀来同时实现这两个作用。
其原理如图
1-8所示。
图1-8 用液控平衡阀的平衡锁紧回路
举身过程中,开始时桅杆自重对液压缸的压力比较大,进油路压力很大,所以回油路上的被压值很小,随着举身过程的进行桅杆自重对缸的压力减小,回油路上的被压值也随着增加。
前倾过程中,进油路上压力值很小,所以回油路上的被压值特别大,收回过程和此分析相反。
要锁紧时可以可以用换向阀切断进油路,从而靠平衡阀直接锁住。
1、3 液压回路综合
把上面选出的各种回路组合画在一起,再经过修改、整理后,可得到总的液压系统原理图,如图1-9所示。
图1-9液压系统原理图
单向阀 5-平衡阀 4-三位四通电液比例换向阀 3-单向阀 2-负荷传感变量泵1-滤油器 10-压力补偿阀 9-压力切断阀 8-负荷传感阀 7-梭阀6-。