共沸精馏
共沸精馏纯化的原理
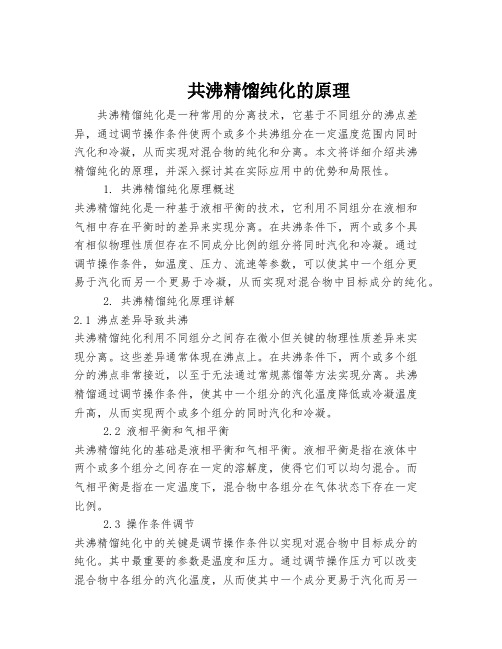
共沸精馏纯化的原理共沸精馏纯化是一种常用的分离技术,它基于不同组分的沸点差异,通过调节操作条件使两个或多个共沸组分在一定温度范围内同时汽化和冷凝,从而实现对混合物的纯化和分离。
本文将详细介绍共沸精馏纯化的原理,并深入探讨其在实际应用中的优势和局限性。
1. 共沸精馏纯化原理概述共沸精馏纯化是一种基于液相平衡的技术,它利用不同组分在液相和气相中存在平衡时的差异来实现分离。
在共沸条件下,两个或多个具有相似物理性质但存在不同成分比例的组分将同时汽化和冷凝。
通过调节操作条件,如温度、压力、流速等参数,可以使其中一个组分更易于汽化而另一个更易于冷凝,从而实现对混合物中目标成分的纯化。
2. 共沸精馏纯化原理详解2.1 沸点差异导致共沸共沸精馏纯化利用不同组分之间存在微小但关键的物理性质差异来实现分离。
这些差异通常体现在沸点上。
在共沸条件下,两个或多个组分的沸点非常接近,以至于无法通过常规蒸馏等方法实现分离。
共沸精馏通过调节操作条件,使其中一个组分的汽化温度降低或冷凝温度升高,从而实现两个或多个组分的同时汽化和冷凝。
2.2 液相平衡和气相平衡共沸精馏纯化的基础是液相平衡和气相平衡。
液相平衡是指在液体中两个或多个组分之间存在一定的溶解度,使得它们可以均匀混合。
而气相平衡是指在一定温度下,混合物中各组分在气体状态下存在一定比例。
2.3 操作条件调节共沸精馏纯化中的关键是调节操作条件以实现对混合物中目标成分的纯化。
其中最重要的参数是温度和压力。
通过调节操作压力可以改变混合物中各组分的汽化温度,从而使其中一个成分更易于汽化而另一个更易于冷凝。
3. 共沸精馏纯化的优势3.1 高效纯化共沸精馏纯化是一种高效的分离技术,它可以在较低的温度下实现对混合物的纯化。
相比于传统蒸馏技术,共沸精馏可以减少能量消耗,提高分离效率。
3.2 适用范围广共沸精馏纯化适用于各种混合物的分离和纯化。
无论是液体混合物还是气体混合物,无论是有机物还是无机物,共沸精馏都可以实现对目标成分的高效分离。
共沸精馏技术
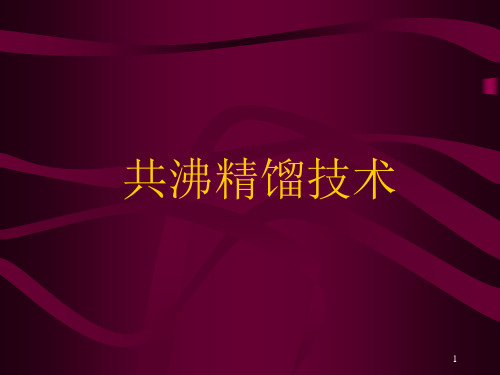
10
共沸精馏技术
1
一、共沸剂的特性
二、共沸剂的选择
三、共沸精馏流程 四、共沸精馏与萃取精馏比较
2
一、共沸剂的特性
ቤተ መጻሕፍቲ ባይዱ
• 共沸物的形成对于采用精馏方法分离体混合物的条件 有很大的影响 • 共沸物可以使二元的,也可以是多元的;可以是易挥 发的塔顶产品,也可以是难挥发的塔底产品,最好是 前者 • 多元系较二元系情况复杂的多
5
三、共沸精馏流程
(一)二元非均相共沸物的精馏 如果二组分能够形成非均相共沸物,那么不必另加 共沸剂便可实现二组分的完全分离。
6
X1
共沸物Xa
Xb
Xw
分离非均相共沸物的流程
7
其他:
分离有共沸剂的非均相共沸物 分离均相共沸物 塔顶产品为三元共沸物的分离 。。。
8
四、共沸精馏与萃取精馏比较
共同点: 基本原理相同,都是通过加入适量的质量分离剂,改变 组分之间的相互作用,增大组分的挥发度差异,实现精 馏分离。 不同点: (1)共沸精馏中加入的共沸剂必须与原溶液中的一个或 几个组分形成共沸物,而萃取精馏中的溶剂无此限 制,共沸剂的选择范围相对较窄; (2)共沸精馏中共沸剂以汽态离塔,消耗的潜热较多, 萃取精馏中萃取剂基本不变化,因此共沸精馏的能 耗一般比萃取精馏大; (3)在同样压力下,共沸精馏的操作温度通常比萃取精 馏低,故共沸精馏更适用于分离热敏性物料; (4)共沸精馏可连续操作,也可间歇操作,萃取精馏一 般只能连续操作。
3
共沸精馏
共沸精馏又称恒沸精馏。 分离原理:
称为共沸物、夹带剂,携带剂
在一些难以用普通精馏方法分离的体系中加入一个 新的组分,共沸剂与待分离关键组分形成共沸物,而使 体系中的组分得到分离。
天津大学—共沸精馏实验报告
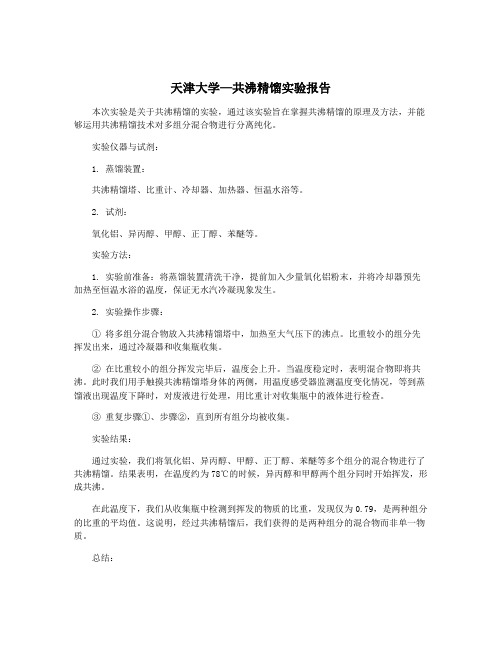
天津大学—共沸精馏实验报告本次实验是关于共沸精馏的实验,通过该实验旨在掌握共沸精馏的原理及方法,并能够运用共沸精馏技术对多组分混合物进行分离纯化。
实验仪器与试剂:1. 蒸馏装置:共沸精馏塔、比重计、冷却器、加热器、恒温水浴等。
2. 试剂:氧化铝、异丙醇、甲醇、正丁醇、苯醚等。
实验方法:1. 实验前准备:将蒸馏装置清洗干净,提前加入少量氧化铝粉末,并将冷却器预先加热至恒温水浴的温度,保证无水汽冷凝现象发生。
2. 实验操作步骤:① 将多组分混合物放入共沸精馏塔中,加热至大气压下的沸点。
比重较小的组分先挥发出来,通过冷凝器和收集瓶收集。
② 在比重较小的组分挥发完毕后,温度会上升。
当温度稳定时,表明混合物即将共沸。
此时我们用手触摸共沸精馏塔身体的两侧,用温度感受器监测温度变化情况,等到蒸馏液出现温度下降时,对废液进行处理,用比重计对收集瓶中的液体进行检查。
③ 重复步骤①、步骤②,直到所有组分均被收集。
实验结果:通过实验,我们将氧化铝、异丙醇、甲醇、正丁醇、苯醚等多个组分的混合物进行了共沸精馏。
结果表明,在温度约为78℃的时候,异丙醇和甲醇两个组分同时开始挥发,形成共沸。
在此温度下,我们从收集瓶中检测到挥发的物质的比重,发现仅为0.79,是两种组分的比重的平均值。
这说明,经过共沸精馏后,我们获得的是两种组分的混合物而非单一物质。
总结:通过本次实验,我们成功运用了共沸精馏技术,对多组分混合物进行了分离纯化。
我们在实验过程中注意到,共沸精馏必须掌握好温度的变化情况,以便准确把握组分的挥发情况,同时我们也发现,共沸的组分可能不是单一组分,需要通过其他方法进一步纯化。
在未来的实验中,我们还需进一步探究并掌握其他的分离方法以满足不同物质的分离需求。
共沸精馏

2)共沸剂与原溶剂中二个组分分别形成两个二元正偏差共沸物;
3)共沸剂与原溶剂中二个组分形成一个三元正偏差共沸物,其沸 点比任何二元共沸物沸点都低,一般要求低10℃以上,且组分不 同,若非均相更好。
二、共沸剂的选择
1.共沸剂选择原则
(2)分离共沸物 1)生成一个二组分正偏差共沸物,其沸点比原共沸物低; 且组成不同于原共沸物。 2)生成一个三组分正偏差共沸物,其沸点比原共沸物低,
共沸进料 丁 醇 塔
直接蒸汽
水 塔
正丁醇
水
图3-33 分离非均相共沸物的流程
20
四、共沸精馏的计算
共沸物精馏体系非理想性强、组分多、变
量多,不宜使用简捷法,而严格计算也变得 非常复杂。
21
五、共沸精馏与萃取精馏的比较
共同点: 基本原理相同,都是通过加入适量的质量分离剂,改变组分之
间的相互作用,增大组分的挥发度差异,实现精馏分离。
3.2.2 共沸精馏
一、共沸物的特性与其组成的计算 二、共沸剂的选择 三、共沸精馏流程 四、共沸精馏的计算 五、共沸精馏与萃取精馏比较
一、共沸物的特性与其组成的计算
1、名词解释
1)共沸物:指在一定压力下,沸腾温度、生成的汽相 组成和液相组成不变的的一类溶液。 2)正偏差共沸物:如溶液的蒸汽压相比理想溶液发生正 偏差,即形成正偏差共沸物(最低共沸物)。 3)负偏差共沸物:如溶液的蒸汽压相比理想溶液发生负 偏差,即形成负偏差共沸物(最高共沸物)。
2)平衡计算 除考虑汽液平衡外,还要考虑液液平衡。 计算方程:
1I x1I 1II x1II
校核方程:
s I 1 1 I 1
I II 2 (1 x1 ) I 2 (1 x1 ) II
共沸精馏

3.2.2 共沸精馏
当 x1 1时,
互溶度很小 x2 1
P1s P1
1
1
2
1
E
P1s P2s
x2 x2
1
定性估算能否形成非均相共沸物
1
x1
x 11
2
(1
x1
)
2
(1
x1 )
计算恒沸 T , xi
P
③共沸剂用过量(T//点):
A H T H AT
塔顶产物(恒沸物D)量:
D T T B ( A H ) T B
DB
DB
塔底产物量(B//点) :
( A和B的混合物)
B T T D ( A H ) T D
BD
BD
反应; ⑤ 无腐蚀,无污染; ⑥ 价廉,易得。
NO.17 2020/3/7
Cui Qun
化工分离工程
(3)连续共沸精馏塔两端产品的确定 3.2.2 共沸精馏
具有共沸物系统的精馏过程与普通精馏不同, 表现在精馏产物不仅与塔的分离能力有关, 与全部进料总组成落在哪个浓度区域, 还与共沸剂加入量有关。
3.2.2 共沸精馏
共沸精馏的基本原理与萃取精馏相同,不同点仅在于共 沸剂在影响原溶液组分的相对挥发度的同时,还与原溶 液的一个组分或数个组分形成共沸物。
共沸物是二元或三元恒沸物。 并且此恒沸物的沸点比原料中任一组分的沸点和原料 中原恒沸物的沸点都低得多, 此恒沸物成为恒沸精馏塔的塔顶产品而排出,使原料 液得以分离。
NO.12 2020/3/7
什么是恒沸精馏(共沸精馏)

一、什么是恒沸精馏(共沸精馏)在被分离的物系中加入共沸剂(或者称共沸组分),该共沸剂必须能和物系中一个或几个组分形成具有最低沸点的恒沸物,以至于使需要分离的集中物质间的沸点差(或相对挥发度)增大。
在精馏时,共沸组分能以恒沸物的形式从精馏塔顶蒸出,工业上把这种操作称为恒沸精馏。
下面以制取无水酒精为例,说明恒沸精馏的过程,水和酒精能形成具有恒沸点的混合物,所以用普通的精馏方法不能获得纯度超过96%(体积)的乙醇,若在酒精和水的溶液中加入共沸组分-苯,则可构成各种恒沸混合物,但以酒精、苯和水所组成的三组分恒沸混合物的沸点为最低(64.84℃)。
当精馏温度在64.85℃时,酒精、苯和水的三元混合物首先被蒸出;温度升至68.25℃时,蒸出的是酒精与苯的二元恒沸混合物;随着温度继续上升,苯与水的二元恒沸混合物和酒精与水的二元恒沸混合物也先后蒸出,这些恒沸物把水从塔顶带出,在塔釜可以获得无水酒精。
工业上广泛地用于生产无水酒精的方法,就是根据此原理。
恒沸精馏的过程中,所加入的共沸组分必须从塔顶蒸出,而后冷凝分离,循环使用。
因而恒沸精馏消耗的能量(包括汽化共沸剂的热量和输送物料的电能)较多。
二、什么是萃取精馏?在被分离的混合物中加入萃取剂,萃取剂的存在能使被分离混合物的组分间的相对挥发度增大。
精馏时,其在各板上基本保持恒定的浓度,而且从精馏塔的塔釜排出,这样的操作称为萃取精馏。
例如,从烃类裂解气的碳四馏分费力丁二烯时,由于碳四馏分的各组分间沸点相近及相对挥发度相近的特点,而且丁二烯与正丁烷还能形成共沸物,采用普通的精馏方法是难以将丁二烯与其它组分加以分离的。
如果采用萃取精馏的方法,在碳四馏分中加入乙腈做萃取剂,则可增大组分间的相对挥发度,使得用精馏的方法能将沸点相近的丁二烯、丁烷和丁烯分离。
碳四馏分经过脱碳三、和碳五馏分后,进入丁二烯萃取剂精馏塔,在萃取剂乙腈的存在下,使丁二烯(包括少量的炔烯)、乙腈与其它组分分开,从塔釜采出并进入解析塔,在此塔中,丁二烯、炔烯从乙腈中解析出来,萃取剂循环使用。
化工厂共沸精馏实例

化工厂共沸精馏实例化工厂共沸精馏实例:混合二甲苯的分离共沸精馏是一种广泛应用于化学工业的分离技术,尤其在化工厂中。
其原理是利用两种或多种物质间的共沸特性,将混合物分离成各自纯组分。
下面是一个化工厂共沸精馏的实例,即混合二甲苯的分离。
一、背景介绍二甲苯是一种重要的有机化工原料,广泛应用于溶剂、树脂、燃料等领域。
在化工厂中,由于生产过程中产生的二甲苯组分不同,往往得到的是多种不同比例的混合二甲苯。
为了满足不同产品的需求,需要将这些混合二甲苯进行分离。
二、共沸精馏分离原理共沸精馏的原理是利用混合物中各组分的相对挥发度差异,通过加入一种或多种共沸剂,与原料混合物形成共沸物,从而改变各组分的相对挥发度。
通过精馏操作,使得各组分在塔板上实现分离。
三、混合二甲苯的共沸精馏分离过程1. 原料准备:将化工厂产生的混合二甲苯作为原料,准备好共沸剂。
2. 混合物加热:将原料加热至沸腾,同时加入共沸剂。
3. 精馏操作:控制加热温度和压力,使得各组分在塔板上实现分离。
塔板温度的控制需根据组分的沸点进行调节。
4. 产品收集:根据需要,收集不同塔板上的产品,得到各种纯度的二甲苯组分。
5. 共沸剂回收:对共沸剂进行回收再利用。
四、实例分析假设化工厂产生的混合二甲苯中含有三种二甲苯组分:邻二甲苯、间二甲苯和对二甲苯,其含量分别为30%、40%和30%。
目标是将这三种二甲苯组分分离成各自纯产品。
通过加入适量的共沸剂,与混合二甲苯形成共沸物,改变各组分的相对挥发度。
经过共沸精馏操作,可以得到以下纯度的各组分:* 邻二甲苯:95%* 间二甲苯:98%* 对二甲苯:97%五、结论通过共沸精馏技术,化工厂成功地将混合二甲苯分离成各自纯产品。
这不仅提高了产品的质量,还为化工厂创造了更多的商业价值。
同时,共沸剂的回收再利用也降低了生产成本。
此实例表明,共沸精馏在化工厂的分离过程中具有广泛的应用前景。
共沸精馏分离正丁醇—水体系的方法

共沸精馏分离正丁醇—水体系的方法
共沸精馏是一种通过调节温度和压力来实现液体分离的方法。
在正丁醇—水体系中,正丁醇和水有相似的沸点,因此通过常规的精馏方法很难将它们完全分离。
为了实现共沸精馏分离,可以采用以下方法:
1. 添加助剂:可以添加一些物质作为助剂,帮助正丁醇和水更好地分离。
常用的助剂有苯、二甲苯等。
助剂的添加可以改变体系的相互作用力,使得两种液体的沸点差距增大,从而更容易进行分离。
2. 真空蒸馏:通过降低系统的压力,可以降低正丁醇和水的沸点,从而利用沸点差来进行分离。
真空蒸馏需要使用专门的真空设备,将体系中的压力降低到较低的水平,使得沸点降低,从而能够快速分离出正丁醇和水。
3. 添加分离剂:可以先添加一种具有亲水性或疏水性的溶剂,将正丁醇或水溶解在其中,然后通过改变溶剂的性质来实现分离。
例如,在正丁醇—水体系中,可以先添加一些醋酸乙酯或乙醇作为分离剂,然后改变溶剂的挥发性,从而将正丁醇和水分离出来。
需要注意的是,共沸精馏只能实现两种液体之间的部分分离,不能完全分离。
如果需要更高纯度的正丁醇或水,还需要进一步进行其他的分离方法,如萃取、结晶等。
- 1、下载文档前请自行甄别文档内容的完整性,平台不提供额外的编辑、内容补充、找答案等附加服务。
- 2、"仅部分预览"的文档,不可在线预览部分如存在完整性等问题,可反馈申请退款(可完整预览的文档不适用该条件!)。
- 3、如文档侵犯您的权益,请联系客服反馈,我们会尽快为您处理(人工客服工作时间:9:00-18:30)。
化工专业实验报告实验名称:共沸精馏实验人员:同组人:实验地点:天大化工技术实验中心624 室实验时间:2014年5月7日班级/学号:级班组号指导教师:实验成绩:共沸精馏一、实验目的1.通过实验加深对共沸精馏过程的理解;2.熟悉精馏设备的构造,掌握精馏操作方法;3.能够对精馏过程做全塔物料衡算;4.学会使用气相色谱分析气、液两相组成。
二、实验原理精馏是利用不同组份在气-液两相间的分配,通过多次气液两相间的传质和传热来达到分离的目的。
对于不同的分离对象,精馏方法也会有所差异。
例如,分离乙醇和水的二元物系。
由于乙醇和水可以形成共沸物,而且常压下的共沸温度和乙醇的沸点温度极为相近,所以采用普通精馏方法只能得到乙醇和水的混合物,而无法得到无水乙醇。
为此,在乙醇-水系统中加入第三种物质,该物质被称为共沸剂。
共沸剂具有能和被分离系统中的一种或几种物质形成最低共沸物的特性。
在精馏过程中共沸剂将以共沸物的形式从塔顶蒸出,塔釜则得到无水乙醇。
这种方法就称作共沸精馏。
乙醇-水系统加入共沸剂苯以后可以形成四种共沸物。
现将它们在常压下的共沸温度、共沸组成列于表1。
为了便于比较,再将乙醇、水、苯三种纯物质常压下的沸点列于表2。
表1乙醇水-苯三元共沸物性质从表1和表2列出沸点看,除乙醇-水二元共沸物的共沸物与乙醇沸点相近之外,其余三种共沸物的沸点与乙醇沸点均有10℃左右的温度差。
因此,可以设法使水和苯以共沸物的方式从塔顶分离出来,塔釜则得到无水乙醇。
整个精馏过程可以用图1来说明。
图中A、B、W分别为乙醇、苯和水的英文字头;AB Z,AW Z,BW Z代表三个二元共沸物,T表示三元共沸物。
图中的曲线为25℃下的乙醇、水、苯三元共沸物的溶解度曲线。
该曲线的下方为两相区,上方为均相区。
图中标出的三元共沸组成点T是处在两相区内。
以T为中心,连接三种纯物质A、B、W及三个二元共沸点组成点AB Z、AW Z、BW Z,将该图分为六个小三角形。
如果原料液的组成点落在某个小三角形内。
当塔顶采用混相回流时精馏的最终结果只能得到这个小三角形三个顶点所代表的物质。
故要想得到无水乙醇,就应该保证原料液的组成落在包含顶点A的小三角形内,即在ΔATAB Z或ΔATAW Z内。
从沸点看,乙醇-水的共沸点和乙醇的沸点仅差0.15℃,就本实验的技术条件无法将其分开。
而乙醇-苯的共沸点与乙醇的沸点相差10.06℃,很容易将它们分离开来。
所以分析的最终结果是将原料液的组成控制在ΔATAB Z中。
图1中F代表未加共沸物时原料乙醇、水混合物的组成。
随着共沸剂苯的加入,原料液的总组成将沿着FB连线变化,并与AT线交于H点,这时共沸剂苯的加入量称作理论共沸剂用量,它是达到分离目的所需最少的共沸剂量。
上述分析只限于混相回流的情况,即回流液的组成等于塔顶上升蒸汽组成的情况。
而塔顶采用分相回流时,由于富苯相中苯的含量很高,可以循环使用,因而苯的用量可以低于理论共沸剂的用量。
分相回流也是实际生产中普遍采用的方法。
它的突出优点是共沸剂的用量少,共沸剂提纯的费用低。
三、装置、流程及试剂1.装置本实验所用的精馏塔为内径Ф20×200mm的玻璃塔。
内部上层装有三角网环型Ф2×2 mm的高效散装填料,下部装有三角网环型的高效散装填料。
填料塔高度略高于1.2m。
塔釜为一只结构特殊的三口烧瓶。
上口与塔身相连:侧口用于投料和采样;下口为出料口;釜侧玻璃套管插入一只测温热电阻,用于测量塔釜液相温度,釜底玻璃套管装有电加热棒,采用电加热,加热釜料,并通过一台自动控温仪控制加热温度,使塔釜的传热量基本保持不变。
塔釜加热沸腾后产生的蒸汽经填料层到达塔顶全凝器。
为了满足各种不同操作方式的需要,在全凝器与回流管之间设置了一个特殊构造的容器。
在进行分相回流时,它可以用作分相器兼回流比调节器;当进行混相回流时,它又可以单纯地作为回流比调节器使用。
这样的设计既实现了连续精馏操作,又可进行间歇精馏操作。
此外,需要特别说明的是在进行分相回流时,分相器中会出现两层液体。
上层为富苯相、下层为富水相。
实验中,富苯相由溢流口回流入塔,富水相则采出。
当间歇操作时,为了保证有足够高的溢流液位,富水相可在实验结束后取出。
2.流程具体的实验流程见图2。
3.试剂实验试剂有乙醇(化学纯),含量95%;苯(分析纯),含量99.5%。
四、实验步骤本实验采用间歇精馏1.称取80克95%的乙醇和38.50g苯,先后依次加入塔釜中,打开冷却水龙头,开启总电源,记录初始时间、塔釜及塔顶的初始温度以及上段加热电流、下段加热电流、塔釜加热电流。
2.当全回流稳定后,开启回流比控制,调至5:1,再20分钟后调至3:1;3.溢流开始后,仍有水珠连续流出的条件下,将回流比调至1:1,再过10分钟后调至1:3至结束;4.每隔20分钟记录一次塔顶、塔釜温度以及上段加热电流、下段加热电流、塔釜加热电流。
并从塔釜取样进行气相色谱分析。
在实验期间,作原料苯与乙醇的色谱分析。
5.大约3小时后根据色谱分析结果,待塔釜中乙醇含量大于99.6%时,停止加热,让塔内持液全部流至塔釜,取出釜液,称重并进行气相色谱分析。
6.将塔顶馏出液取出,放入分液漏斗内,摇晃后静置,待其分层后,将分离后的富苯相和富水相分别称重,并分别进行气相色谱分析。
五、实验原始数据记录设备编号:03表4各阶段塔釜中液体气相色谱分析数据记录表表5 塔顶、塔釜及产物气相色谱分析数据记录表备注: 1. 气相色谱3分析条件:柱压力为0.065MPa ,柱箱温度为145℃,汽化室温度为150℃,检测室温度110℃。
2. 桥电流:100mA ,信号衰减:6,进样量:0.4μL3. 各物质校正因子:f(水)=0.698,f(乙醇)=1,f(苯)=1.162。
4. 实际百分含量计算公式为:p i %=ii i i A f A f ''六、 实验数据处理表7各阶段塔釜中液体气相色谱分析数据处理结果表续上表7表8塔顶、塔釜及产物气相色谱分析数据处理结果表表9原料乙醇和苯气相色谱分析数据处理结果表1.做全塔物料衡算,并对共沸物形成的富水相和富苯相进行分析和衡算,求出塔顶三元共沸物的组成。
1)对塔内乙醇进行物料衡算原料液中乙醇质量:80.00×0.9522726=76.182 g富水相中乙醇质量:9.46×0.5510023=5.212 g富苯相中乙醇质量:25.43×0.1658231=4.217 g塔釜液中乙醇质量:74.41×0.8586371=63.891 g则塔内残余乙醇的质量为:L a=76.182-5.212-4.217-63.891=2.862 g2)对塔内苯进行物料衡算原料液中苯质量:38.50×1=38.50 g富水相中苯质量:9.46×0.1418436=1.342 g富苯相中苯质量:25.43×0.8105606=20.613 g塔釜液中苯质量:74.41×0.1378997=10.261 g则塔内残余苯的质量为:L b=38.5-1.342-20.613-10.261=6.284 g3)对塔内水进行物料衡算原料液中水含量:80.00×(1-0.9522726)=3.818 g富水相中水含量:9.46×0.3071541=2.906 g富苯相中水含量:25.43×0.0236163=0.601 g塔釜液中水质量:74.41×0.0034632=0.258 g塔内残余水含量:L w=3.818-2.906-0.601-0.258=0.053 g4)塔内总持液量为:80.00+38.50-9.46-25.43-74.41=9.20 ≈2.862+6.284+0.053=9.1995)对物料衡算结果的分析:塔内总持液比例:ω=100%=7.763%从上述计算可以看出,塔内持液占了不小的比例,其中包括苯和乙醇。
两者质量比例大约为6.284:2.862=2.196:1。
当然除了塔内残留一部分外,可能还有一些乙醇通过各种可能途径挥发了。
6)塔顶三元共沸物组成计算组分乙醇所占比例:100%=27.0%相对误差:r A=︱185.0185.0270.0-︱×100%=45.9%组分苯所占比例:×100%=62.9%相对误差:r B=︱741.0741.0629.0-︱×100%=15.1%组分水所占比例:100%=10.1%相对误差:r W=︱074.0074.0101.0-︱×100%=36.5%总结上述结果得到下表:表10塔顶三元共沸物组成2.画出25℃下乙醇一水一苯三元物系的溶解度曲线。
在图上标明共沸物的组成点,画出加料线,并对精馏过程作简要的说明。
右图所示为25℃下水—乙醇—苯的三元相图,其中A、B、W分别代表乙醇、苯和水;AB Z、AW Z、BW Z代表三个二元共沸物,T表示三元共沸物;图中的曲线即为25℃下乙醇—水—苯三元物系的溶解度曲线;线段FB则为加料线。
将乙醇—水的混合物加入塔釜中,此时即对应右图中的F点,随着苯的加入,原料液的组成点逐渐的向B点迁移。
由三元相图原理可知,如果原料液的组成点落在某个小三角形内。
当塔顶采用混相回流时精馏的最终结果只能得到这个小三角形三个顶点所代表的物质。
所以如果想得到无水乙醇,就应该保证原料液的组成落在包含顶点A的小三角形内,即在ΔATAB z或ΔATAW z内。
从沸点看,乙醇—水的共沸点和乙醇的沸点仅差0.15℃,就本实验的技术条件无法将其分开。
而乙醇—苯的共沸点与乙醇的沸点相差10.06℃,很容易将它们分离开来。
所以应该将原料液的组成控制在ΔATAB z中。
也就是说,应该通过控制苯的加入量,使得原料液的组成点落在线段HI之间即可。
将适量的苯加入塔釜中,通过控制适宜的塔釜温度和塔顶回流比,即可以在塔釜中得到较为纯净的乙醇,塔顶得到两元和三元共沸物,从而达到了乙醇和水分离的目的。
七、思考题1.如何计算连续精馏中共沸剂的最小加入量?1)在指定的压力下,做水-乙醇-苯的三角相图;2)根据相关文献在图上确定共沸物组成点(自由度为1,所以务必确定是该压力下的共沸点组成),包括三元共沸物,所有可能的二元共沸物。
按照实验原理中的说明做出下面的连线。
由沸点参数可知,原料液组成应控制在ΔA TAB Z中;3)连接F,B两点,交ΔA TAB Z于H和I,这两点分别是加入共沸剂的最小量和最大量。
4)从图上可以读出各线段长度。
利用杠杆规则,若混合液的组成为I,则m B=m F*|IF|/|BI|;若混合液组成为H,则m B=m F*|HF|/|BH|。