FMEA分析报告
软件需求FMEA分析报告,1200字

软件需求FMEA分析报告软件需求FMEA分析报告一、引言软件需求FMEA(Failure Mode and Effects Analysis)是一种常用的风险分析方法,用于识别软件需求中的潜在故障模式及其对系统的影响。
本报告旨在对某软件需求进行FMEA分析,以识别潜在风险并提出相应的预防措施。
二、FMEA分析过程1. 确定需求首先,我们明确分析的软件需求是什么。
在本次分析中,为了简化,我们选取了一个简单的需求:用户登录功能。
2. 识别潜在故障模式接下来,我们识别可能存在的潜在故障模式。
对于用户登录功能,可能的潜在故障模式包括:用户无法通过用户名和密码登录、系统无反应或崩溃、登录成功但无法访问受限资源等。
3. 评估故障影响程度针对每个潜在故障模式,我们评估其对系统的影响程度。
例如,用户无法通过用户名和密码登录会导致用户无法使用系统的功能,影响程度较高;而系统无反应或崩溃可能导致用户丧失工作进度,影响程度较高。
4. 评估故障发生概率除了影响程度,我们还需要评估每个故障模式的发生概率。
这可以通过历史数据、模拟测试或专家意见等方式获取。
在本次分析中,我们假设用户登录功能的故障发生概率较低。
5. 计算风险优先级数值根据故障影响程度和发生概率的评估结果,我们可以计算每个故障模式的风险优先级数值。
通过将影响程度乘以发生概率,我们可以对故障模式进行排序,以便后续处理。
6. 提出预防措施根据故障模式的风险优先级数值,我们可以确定需要采取的预防措施。
对于风险优先级较高的故障模式,我们可能需要采取更多的预防措施,例如增加输入校验、加强系统稳定性等。
三、分析结果和预防措施经过上述分析过程,我们得到了用户登录功能的FMEA分析结果如下:1. 用户无法通过用户名和密码登录风险优先级数值:高预防措施:增加输入校验、使用强密码策略、添加登录重试机制等。
2. 系统无反应或崩溃风险优先级数值:高预防措施:加强系统稳定性、进行性能测试、增加异常处理等。
fmea报告模板

FMEA报告模板1. 引言故障模式与影响分析(Failure Mode and Effects Analysis,简称FMEA)是一种系统性的方法,用于识别和评估潜在的故障模式,并预测它们可能引起的影响。
本报告旨在提供一个FMEA报告模板,以便团队能够按照一致的结构和标准进行FMEA分析,并记录所得出的结果。
2. FMEA分析流程2.1 确定FMEA的范围在开始FMEA分析之前,需要明确定义FMEA的范围。
确定范围时,需要明确产品或过程的边界,以便团队可以集中精力进行分析。
2.2 识别故障模式在这一步骤中,团队需要列出所有可能的故障模式。
这些故障模式可以通过多种途径获得,包括过去的经验、相关文献和专家意见等。
2.3 评估故障影响对于每个故障模式,团队需要评估其可能引起的影响。
这些影响可以包括安全风险、质量降低、生产停止、客户满意度下降等。
2.4 确定故障原因在这一步骤中,团队需要分析每个故障模式的根本原因。
通过识别原因,团队可以采取相应的预防措施来减少故障的发生。
2.5 评估现有控制措施团队需要评估现有的控制措施,以确定它们对于减轻故障影响和预防故障的效果。
如果控制措施被认为不足或不可靠,团队需要考虑采取额外的措施。
2.6 制定改进措施根据之前的分析结果,团队需要制定改进措施,以降低故障模式的发生概率或减少其影响。
这些措施可以包括工艺改进、设计修改、培训和培训等。
2.7 实施改进措施在这一步骤中,团队需要实施之前制定的改进措施,并监控其效果。
必要时,可以进行调整和再次评估。
3. FMEA报告模板以下是一个FMEA报告的模板,可以根据实际情况进行调整:3.1 项目信息•项目名称:•项目编号:•项目负责人:•报告日期:3.2 FMEA范围•产品/过程边界:•分析目的和要求:3.3 FMEA分析团队•团队成员及职责:3.4 故障模式识别3.4.1 故障模式1•故障模式描述:•潜在原因:•潜在影响:•现有控制措施:•建议改进措施:3.4.2 故障模式2•故障模式描述:•潜在原因:•潜在影响:•现有控制措施:•建议改进措施:…3.5 故障影响评估•故障模式1影响评估:•故障模式2影响评估:•…3.6 故障原因分析•故障模式1原因:•故障模式2原因:•…3.7 现有控制措施评估•故障模式1现有控制措施评估:•故障模式2现有控制措施评估:•…3.8 改进措施制定•故障模式1改进措施:•故障模式2改进措施:•…3.9 改进措施实施•故障模式1改进措施实施情况:•故障模式2改进措施实施情况:•…4. 结论根据以上的FMEA分析结果,团队可以得出结论,并提出进一步的建议和行动计划。
变压器产品制程FMEA分析总结报告

分析总结﹕
结论:
1.线包高压管控重点在于穿线针作业前需打磨处理;
2.内PIN虚焊因浸锡时间不够,导入定时器可有效管制时间;
3.内PIN短路为毛刺过长浸锡后造成相邻端子连锡,组立后导入CCD视检可有效检验毛刺;
4.外PIN端子歪斜因浸锡后产品直接放置清洗篮,超声波振动造成端子碰撞,将清洗篮更为
平放清洗治具可有效改善此问题;
5.外PIN镀锡不良为作业员镀锡手法不当所致,纠正作业员镀锡手法可有效改善此问题;
6.成品高壓因外PIN浸锡与锡面高度未管控导致漆包线被烫伤,导入限位治具、锡面管控可有效改善此问题.
變壓器產品制程FMEA 分析總結報告
風險優先係數:RPN (Risk Priority Number)名詞定義:(在客戶收到產品前,目前流程檢測出失效的能力) →(影響的)嚴重度:對客戶需求所造成之影響的重重要性[1=不嚴重~ 10=非常嚴重] →(原因的)發生度:特定原因發生並產生失效模式的頻率[1=不常發生~10=時常發生] →(現行管制能力)偵測度:現行管制計劃的偵測力[1=可偵測出來~10=不能偵測出來] ※等級尺度應由小組決定
※ 風險優先係數評點法:
→排列RPN 的優先順序,對最優先問題採取適當的措施. →RPN=(嚴重度*發生率*偵測度)1/3
C 1 : 影響機能故障的嚴重程度(嚴重度) C 2 : 故障發生的頻度(發生率)
C 3 : 故障發生檢測的難易度(偵測度) Cs : 故障評點
Cs = ( C 1˙C 2˙C 3 )1/3
表1. C 1的評價點 表2. C 2的評價點 表3. C 3的評價點 表4. C S 與故障等級之關
校准: 审核: 制定: 时间:。
FMEA分析报告

FMEA分析报告FMEA(Failure Mode and Effects Analysis)是一种系统性的风险评估方法,常用于分析产品或过程中的潜在问题和可能的影响。
这篇报告将介绍FMEA分析的目的,步骤和优势,并通过一个实例进行详细说明。
一、FMEA分析的目的二、FMEA分析的步骤1.确定分析的范围:明确需要分析的产品或过程的范围和目标。
2.收集团队:组建一个多学科的团队,包括设计人员、工程师、生产人员等。
3.识别潜在的故障模式:对产品或过程进行详细审查,识别可能出现的故障模式。
4.评估故障的严重程度:分析每个故障模式可能引发的后果,评估其对产品性能和安全性的影响。
5.评估故障发生的可能性:分析每个故障模式发生的概率或频率,并将其与已有的统计数据或历史记录进行比较。
6.评估故障的检测能力:评估现有的探测和防范措施对于检测和防止故障的效果。
7.计算风险优先级:根据故障的严重程度、发生可能性和检测能力计算每个故障模式的风险优先级,确定应优先处理的故障模式。
8.制定改进措施:根据风险优先级,制定相应的改进措施,减少或消除故障的可能性和后果。
9.实施改进措施:将改进措施应用到产品设计或过程中,确保其有效性和可持续性。
10.监控和追踪效果:通过定期监测和追踪,评估改进措施的效果和持续性,并根据需要进行调整和改进。
三、FMEA分析的优势1.预测潜在问题:通过系统性的分析,FMEA能够预测产品或过程中可能出现的问题,并提前采取措施避免或降低潜在的风险。
2.提高产品质量:通过识别并改进潜在问题,FMEA能够改善产品的质量和可靠性,提高顾客满意度。
3.降低故障率和维修成本:通过消除或减少故障的可能性,FMEA能够降低产品或过程的故障率和维修成本。
4.加强团队协作:FMEA需要一个多学科的团队进行分析和讨论,促进了团队成员之间的协作和沟通。
5.持续改进:FMEA是一个持续改进的过程,通过监测和追踪改进措施的效果,不断优化和改进产品或过程。
汽车发动机的fmea分析报告

汽车发动机的FMEA分析报告1. 引言FMEA(Failure Mode and Effects Analysis)是一种常用的风险评估方法,被广泛应用于汽车制造等领域。
本报告旨在通过对汽车发动机的FMEA分析,识别潜在的故障模式,评估其对系统性能和可靠性的影响,并提出相应的改进措施,以提高汽车发动机的质量和可靠性。
2. FMEA分析过程2.1. 选定分析范围本次FMEA分析的范围为汽车发动机及其相关系统,包括燃油供给系统、点火系统、冷却系统等。
2.2. 识别潜在故障模式在识别潜在故障模式时,我们参考了历史故障数据、设计规范、专家意见等多方信息,对发动机的各个组成部分进行了仔细的分析。
以下是我们识别出的一些潜在故障模式:2.2.1. 燃油供给系统•燃油泵失效:燃油泵镶嵌的轴承磨损可能导致泄漏或无法提供足够的燃油压力,影响发动机的燃油供应。
•燃油喷嘴堵塞:燃油喷嘴内积聚的沉积物可能导致喷嘴堵塞,影响燃油的均匀喷射。
2.2.2. 点火系统•点火线圈故障:点火线圈的绝缘损坏可能导致火花能量不足或点火信号中断,影响燃烧效率。
•点火塞老化:点火塞经长时间使用后可能出现电极磨损或腐蚀,影响点火效果。
2.2.3. 冷却系统•散热器堵塞:冷却系统中的散热器可能受到灰尘、沉积物等的堵塞,导致发动机过热。
2.3. 评估故障后果针对每个潜在故障模式,我们评估了其可能引发的后果,涉及到发动机性能、安全性和可靠性等方面。
以下是我们对一些故障后果的评估:2.3.1. 燃油供给系统•燃油泵失效:可能导致发动机无法启动或在运行过程中突然熄火,影响车辆的可靠性和安全性。
•燃油喷嘴堵塞:可能导致燃烧不完全、动力下降、油耗增加等,影响发动机的性能和可靠性。
2.3.2. 点火系统•点火线圈故障:可能导致发动机无法启动或在运行过程中突然熄火,影响车辆的可靠性和安全性。
•点火塞老化:可能导致燃烧不完全、动力下降等,影响发动机的性能和可靠性。
DFMEA报告

职责及目
严发
标 完成日期
采取措施和 重 生 生效日期 度 率
D
PRN
SO
LECU固定螺钉选型有
误,振动时松动脱
对LECU固定螺钉进
8 落,导致在LECU壳体 4
行材质及尺寸的测 2 64
中滚动,引起板子短
试验证
路BMU固定螺钉选型有
电池系统内
误,振动时松动脱
对BMU固定螺钉进行
电池管理 的高压器件 8 落,导致在BMU壳体 4
2
报警,输入输出
BMU软硬件
控制
版本号读取 8
数据存储错误 2
失败
故障检测错 误
8
故障触发条件判断错 误
2
BMS故障
预警与处 高压互锁功
理
能失效
8
高压互锁采样或控制 电路故障
2
碰撞开关功 能失效
8
碰撞开关检测电路故 障
2
BMS诊断 诊断功能失
功能
效
8
诊断代码错误 2
备注: 在下列三种失效条件下,须制定相应的改善措施: (1)最优原则:S≥9时,必须分析设计控制或建议措施 (2) 严重度S≤8,风险顺序数RPN≥80时(或依顾客需求) (3)关键特性发生失效时。
2 32
拉力试验
2 64
CAN通讯功 8 通讯接插件端子松脱 4
能失效 8
通讯程序bug
2
8 继电器控制电路故障 2 放电回路继
电器失效 管理功能
下降
8
放电启动或停止条件 错误
2
检测电池状态, 计量SOC,整车 通信,电滥用保 护,故障识别及
8 继电器控制电路故障 2 慢充回路继
fame潜在风险分析报告

fame潜在风险分析报告
FMEA可以描述为一组系统化的活动,其目的是:
(a)认可并评价产品过程中的潜在失效以及失效的后果:
(b)确定能够消除或减少潜在失效发生机会的措施;
(c)将全部过程形成文件。
FMEA是对确定设计或过程必须做那些事情才能使顾客满意这一过程的补充。
所有的FMEA都关注设计,无论是产品设计或者是过程设计。
在进行FMEA时有三种基本的情形,每一种都有其不同的范围或关注焦点:
情形1:新设计、新技术或新过程。
FMEA的范围是全部设计、技术或过程。
情形2:对现有设计或过程的修改(假设对现有设计或过程已有FMEA)。
FMEA的范围应集中于对设计或过程的修改、由于修改可能产生的相互影响以及现场的历史情况。
情形3:将现有的设计或过程用于新的环境、场所或应用(假设对现有设计或过程已有FMEA)1>.FMEA的范围是新环境或场所对现有设计或过程的影响。
fmea报告模板范例
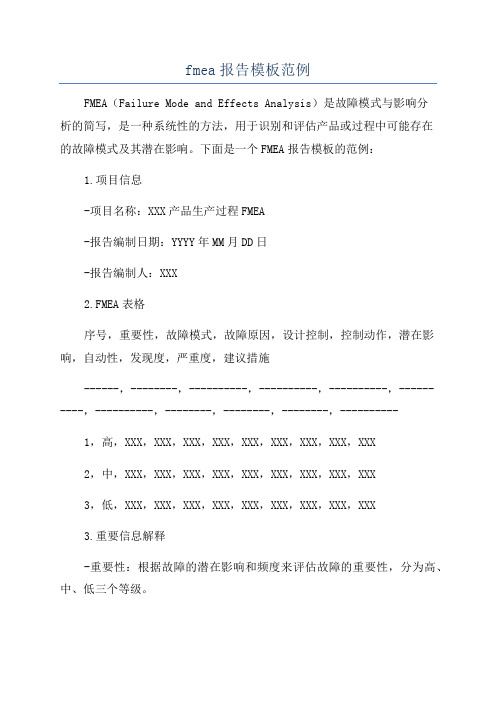
fmea报告模板范例FMEA(Failure Mode and Effects Analysis)是故障模式与影响分析的简写,是一种系统性的方法,用于识别和评估产品或过程中可能存在的故障模式及其潜在影响。
下面是一个FMEA报告模板的范例:1.项目信息-项目名称:XXX产品生产过程FMEA-报告编制日期:YYYY年MM月DD日-报告编制人:XXX2.FMEA表格序号,重要性,故障模式,故障原因,设计控制,控制动作,潜在影响,自动性,发现度,严重度,建议措施------,--------,----------,----------,----------,----------,----------,--------,--------,--------,----------1,高,XXX,XXX,XXX,XXX,XXX,XXX,XXX,XXX,XXX2,中,XXX,XXX,XXX,XXX,XXX,XXX,XXX,XXX,XXX3,低,XXX,XXX,XXX,XXX,XXX,XXX,XXX,XXX,XXX3.重要信息解释-重要性:根据故障的潜在影响和频度来评估故障的重要性,分为高、中、低三个等级。
-故障模式:记录故障出现的模式或类型,例如机器停机、设备损坏等。
-故障原因:识别导致故障的根本原因,例如零部件磨损、操作错误等。
-设计控制:标记故障模式是否由设计决策引起。
-控制动作:记录已经或将要采取的控制措施来减少或消除故障模式。
-潜在影响:分析故障可能带来的影响,如生产延误、产品质量下降等。
-自动性:描述人工检查效果,区分人工检查的故障发现自动性高低。
-发现度:根据控制措施可能发现的故障数量进行评估。
-严重度:根据故障带来的影响评估故障的严重性,分为高、中、低三个等级。
-建议措施:记录针对每个故障模式采取的应对措施和改进建议。
4.分析结果总结-根据FMEA表格中的评估和分析,我们可以得出以下结论:-高重要性的故障模式需要优先处理,并采取相应措施进行风险控制。
失效模式分析(FMEA)心得报告

失效模式分析(FMEA)心得報告----報告人紀志龍一、FMEA導入的步驟:1.研究PROCESS/PRODUCT2.BRAINSTORM可能失效模3.列出每一失效模式潛在結果4.Assign嚴重度分數5.鑑定每一失效模式之原因6.Assign發生度分數7.鑑定目前偵測失效模式8.Assign難檢度分數9.計算RPN(先其風險評估)10.決定失效模式優先順序11.採取矯正行動12.重新計算RPN二、FMEA製作時機1.原型樣品前2.試產前3.產品製程變異4.製程不穩定/或能力不足三、FEMA用途1.是一種分析技術2.認明產品設計或製程上可能不良模式3.評估缺點對客戶的可能影響4.認明缺點對客戶的可能影響5.認明產生該不良模式之可能原因6.認明有關之重要製程變數7.研訂改善措施8.建立預防管制方法四、FMEA表格(上課實習內容、主要針對加油站的設立所產生的FEMA並加以預防)※R PN直愈大表示潛在風險愈高,第10項計畫之後也是回歸到矯正行動,一直到RPN 值降到最低為止。
五、結論課程中談到我們可以透過RPN、製定行動方案、降低失效模式;但QS-9000認證系統可能停止運作,改由ISO/TS 16949替代,目前是台積電最早申請通過,未來所有汔車零件相關產業都會要求通過此認證,因此他們也建議若要申請QS-9000系統倒不如直接申請ISO/TS 16949,因為ISO/TS 16949是由QS-9000(APQP、SPC、MSA、PPAP、FMEA、QSA)加上生產者特定要求及歐洲VDA-VOLUMES所組成,其內容較QS-9000更完整更詳細,也由於FEMA 太深還有許多地方不能詳盡敘述,可能須導入試RUN才能了解,未來公司也不排除申請ISO/TS 169469 ,若要實際導入建議須有專案專責負責人才行。
--完畢。
FMEA分析报告
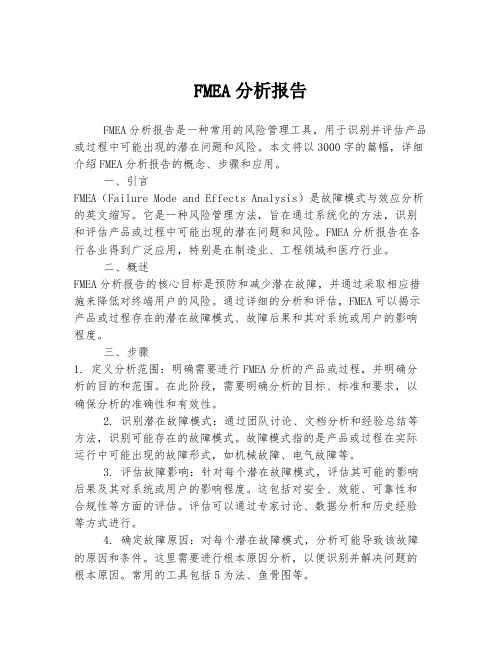
FMEA分析报告FMEA分析报告是一种常用的风险管理工具,用于识别并评估产品或过程中可能出现的潜在问题和风险。
本文将以3000字的篇幅,详细介绍FMEA分析报告的概念、步骤和应用。
一、引言FMEA(Failure Mode and Effects Analysis)是故障模式与效应分析的英文缩写。
它是一种风险管理方法,旨在通过系统化的方法,识别和评估产品或过程中可能出现的潜在问题和风险。
FMEA分析报告在各行各业得到广泛应用,特别是在制造业、工程领域和医疗行业。
二、概述FMEA分析报告的核心目标是预防和减少潜在故障,并通过采取相应措施来降低对终端用户的风险。
通过详细的分析和评估,FMEA可以揭示产品或过程存在的潜在故障模式、故障后果和其对系统或用户的影响程度。
三、步骤1. 定义分析范围:明确需要进行FMEA分析的产品或过程,并明确分析的目的和范围。
在此阶段,需要明确分析的目标、标准和要求,以确保分析的准确性和有效性。
2. 识别潜在故障模式:通过团队讨论、文档分析和经验总结等方法,识别可能存在的故障模式。
故障模式指的是产品或过程在实际运行中可能出现的故障形式,如机械故障、电气故障等。
3. 评估故障影响:针对每个潜在故障模式,评估其可能的影响后果及其对系统或用户的影响程度。
这包括对安全、效能、可靠性和合规性等方面的评估。
评估可以通过专家讨论、数据分析和历史经验等方式进行。
4. 确定故障原因:对每个潜在故障模式,分析可能导致该故障的原因和条件。
这里需要进行根本原因分析,以便识别并解决问题的根本原因。
常用的工具包括5为法、鱼骨图等。
5. 确定风险等级:根据故障的严重性、频率和检测难度,确定每个故障模式的风险等级。
一般采用风险矩阵或风险评估矩阵来进行评估。
风险等级越高,意味着该故障对系统或用户的影响越严重。
6. 提出改进措施:基于风险等级,制定相应的改进措施,以减少故障的发生概率或降低其对系统或用户的影响。
FMEA分析报告方法

SAE-ARP-4761(1996)FMEA是一种系统的,自下而上的方法,用于识别系统,项目或功能的故障模式,并确定对下一个更高级别的影响。
它可以在系统中的任何级别(例如,零件,功能,黑盒等)执行。
软件还可以使用功能FMEA方法进行定性分析。
通常,FMEA用于解决单个故障导致的故障影响。
FMEA的范围应该与请求它的用户协调。
分析可以是部件FMEA或功能FMEA。
如果从功能FMEA导出的故障率允许满足PSSA概率预算,则可以不需要零件FMEA。
FMEA 通常包括以下信息。
a、组件、功能或/和功能的识别;b、故障模式和相关的硬件故障率(数值或分类);c、失效效应(直接和/或在下面更高级水平);d、可检测性和检测手段;FMEA也包括以下信息:a、补偿动作(即自动或手动);b、发生故障的飞行阶段;c、故障影响的严重性FMEA可以与概率技术(例如FTA或DD)结合使用以产生定量分析。
此外,FMEA 可以用于通过从下到上提供故障效应的补充列表来补充FTA / DD。
故障模式和影响分析(FMEA)1、介绍故障模式和影响分析(FMEA)是一种系统方法,用于识别系统,项目,功能或零件的故障模式,并确定对下一个更高级别设计的影响。
还可以确定每个故障模式的检测方法(如果有的话)FMEA可以是定量或定性分析,并且可以在所有类型的系统(例如,电气,电子或机械系统)上执行。
如果正在执行定量FMEA,则针对每个故障模式确定故障率。
FMEA的结果可以用于生成故障模式和效果概要(FMES),并且通常用于支持系统安全评估(SSA)过程的其他分析技术,例如故障树分析(FTA),依赖关系图DD)或马尔可夫分析(MA)。
故障的组合通常不被认为是FMEA的一部分。
2、范围通过假定所选级别的具体实现可能失败的方式对给定级别(系统,项目等)执行FMEA。
每个故障模式的影响在给定等级下确定,并且通常是设备的每个操作模式的下一较高等级。
有时,FMEA可能需要专注于特定操作场景以支持自上而下的FTA,DD或MA。
FMEA分析

FMEA分析FMEA事实上就是一套严密的“预防措施”之识别、控制、提高的管理过程;其不仅可在汽车零组件行业可予使用,也可应用于任何期望能严格控制潜在问题出现的行业,尤其是产品(或服务)质量的好坏可能会极大影响到顾客利益的领域;因此,FMEA能在QS9000及ISO/TS16949一类的汽车业质量管理体系中运用,其同样可应用于其他管理体系之中,而且同样可以在企业内部形成一种严密的“预防措施”系统。
执行FMEA,其实并不困难,它是一种分析技术,即:在一张包括诸多要求的表单上进行分析并加以控制和应用便可达成的过程控制;美国三大车厂在《潜在失效模式及后果分析》一书中已有明确给定了这种表单的格式;该表单包含了如下主要内容:(1)“功能要求”:填写出被分析过程(或工序)的简单说明;(2)“潜在失效模式”:记录可能会出现的问题点;(3)“潜在失效后果”:列出上述问题点可能会引发的不良影响;(4)“严重度”:对上述问题点的不良影响进行评价并赋予分值(得分1~10分),分值愈高则影响愈严重;(5)“潜在失效起因或机理”:该潜在问题点可能出现的原因或产生机理分析;(6)“频度”:上述“起因或机理”出现的几率大小(得分1~10分),分值愈高则出现机会愈大;(7)“现行控制”:列出目前本企业对这一潜在问题点所运用的控制方法;(8)“探测度”:在采用“现行控制”的方法来控制时,该潜在问题可以被检查出来的难易程序(得分:1~10分),得分愈高则愈难以被检出;(9)“风险顺序数”:将上述“严重度”、“频度”、“探测度”得分相乘所得出的结果;该数值愈大则这一潜在问题愈严重,愈应及时采取“预防措施”;(10)“建议措施”:列出对“风险顺序数”较高之潜在问题点所制定的“预防措施”,以防止其发生;(11)“责任及目标完成日期”:写出实施上述“预防措施”的计划案;(12)“措施结果”:对上述“预防措施”计划案之实施状况的确认。
从上述内容项目不难看出这已经包含了处理“预防措施”之识别、控制所需的全部基本要求。
FMEA分析报告方法

SAE-ARP-4761(1996)FMEA是一种系统的,自下而上的方法,用于识别系统,项目或功能的故障模式,并确定对下一个更高级别的影响。
它可以在系统中的任何级别(例如,零件,功能,黑盒等)执行。
软件还可以使用功能FMEA方法进行定性分析。
通常,FMEA用于解决单个故障导致的故障影响。
FMEA的范围应该与请求它的用户协调。
分析可以是部件FMEA或功能FMEA。
如果从功能FMEA导出的故障率允许满足PSSA概率预算,则可以不需要零件FMEA。
FMEA通常包括以下信息。
a、组件、功能或/和功能的识别;b、故障模式和相关的硬件故障率(数值或分类);c、失效效应(直接和/或在下面更高级水平);d、可检测性和检测手段;FMEA也包括以下信息:a、补偿动作(即自动或手动);b、发生故障的飞行阶段;c、故障影响的严重性FMEA可以与概率技术(例如FTA或DD)结合使用以产生定量分析。
此外,FMEA可以用于通过从下到上提供故障效应的补充列表来补充FTA / DD。
故障模式和影响分析(FMEA)1、介绍故障模式和影响分析(FMEA)是一种系统方法,用于识别系统,项目,功能或零件的故障模式,并确定对下一个更高级别设计的影响。
还可以确定每个故障模式的检测方法(如果有的话)FMEA可以是定量或定性分析,并且可以在所有类型的系统(例如,电气,电子或机械系统)上执行。
如果正在执行定量FMEA,则针对每个故障模式确定故障率。
FMEA的结果可以用于生成故障模式和效果概要(FMES),并且通常用于支持系统安全评估(SSA)过程的其他分析技术,例如故障树分析(FTA),依赖关系图 DD)或马尔可夫分析(MA)。
故障的组合通常不被认为是FMEA的一部分。
2、范围通过假定所选级别的具体实现可能失败的方式对给定级别(系统,项目等)执行FMEA。
每个故障模式的影响在给定等级下确定,并且通常是设备的每个操作模式的下一较高等级。
有时,FMEA可能需要专注于特定操作场景以支持自上而下的FTA,DD或MA。
故障模式及影响分析报告模板

XX
故障模式及影响(FMEA)分析
xx公司
XX年XX月
目录
1系统定义 (1)
1.1功能及组成 (1)
1.2严酷度类别 (1)
1.3故障模式发生的概率等级 (1)
1.4信息来源 (1)
2填写FMEA表 (1)
3结论 (1)
第I页共I 页
1系统定义
1.1功能及组成
XX功能与组成简介。
1.2严酷度类别
武器装备常用的严酷度类别的定义见表1。
表1 武器装备常用的严酷度类别及定义
1.3故障模式发生的概率等级
故障模式发生概率的等级划分见表2。
表2 故障模式发生概率等级划分
1.4信息来源
XX可靠性和维修性预估。
2填写FMEA表
XXFMEA分析填写结果详见附表一。
3结论
通过对XX进行FMEA分析找出了结构变形、连接损坏、元器件失效等薄弱环节,并采取了有针对性的预防改进措施,进而提高了XX的可靠性。
第3页共3 页
第2页共3 页
附表一故障模式及影响分析(FMEA)表
第3页共3 页。
产品设计fmea报告

产品设计fmea报告1. 引言在产品设计过程中,为了减少设计缺陷对产品质量和用户体验的影响,我们进行了一个产品设计的FMEA(Failure Mode and Effects Analysis)分析。
本报告将介绍我们所进行的FMEA分析的方法和结果。
2. FMEA分析过程FMEA分析是一种系统性的方法,用于评估产品设计中可能出现的故障模式及其对系统性能的影响。
我们按照以下步骤进行了FMEA分析:2.1 选择评估项目我们选择了产品设计中的关键步骤和关键组件进行分析,以确保我们重点关注可能的故障模式。
2.2 列举潜在故障模式针对每个评估项目,我们仔细考虑了可能的故障模式,并列出了所有可能的故障模式。
2.3 评估故障的发生概率对于每个故障模式,我们进行了定量评估,评估其发生的概率。
我们考虑了材料质量、制造过程、使用环境等多个因素,来评估发生概率。
2.4 评估故障对系统的影响对于每个故障模式,我们评估了其对系统性能的影响,包括安全性、可靠性、性能等方面。
我们使用了一个评分系统,将影响程度进行量化评估。
2.5 提出改进和预防措施在评估故障对系统的影响后,我们提出了一系列改进和预防措施。
这些措施旨在减少故障发生的概率和降低故障对系统的影响。
3. FMEA分析结果我们进行了详细的FMEA分析,得出了以下结果:3.1 评估项目1:电池组件3.1.1 潜在故障模式- 电池短路- 电池漏液- 电池寿命过短3.1.2 发生概率评估根据我们的评估,电池短路的发生概率较低(2/10),电池漏液的发生概率中等(5/10),电池寿命过短的发生概率较高(8/10)。
3.1.3 故障影响评估电池短路对于系统的影响程度较低(1/10),电池漏液对于系统的影响程度中等(5/10),电池寿命过短对于系统的影响程度高(9/10)。
3.1.4 改进和预防措施针对电池短路,我们将改进电池设计,采用更安全的电池连接方式。
针对电池漏液,我们将加强电池外壳的密封性能。
电机fmea分析报告

电机FMEA分析报告1. 引言本报告旨在对电机的FMEA(失效模式与影响分析)进行详细分析,以识别潜在的失效模式和确定必要的纠正措施,从而提高电机的可靠性和性能。
2. FMEA概述FMEA是一种系统的、结构的和量化的方法,用于识别并减少潜在的系统、设计或过程中的失效。
它通过评估失效模式及其对系统性能的影响程度,确定相关风险,并制定相应的纠正和预防措施。
3. FMEA过程FMEA过程包括以下几个主要步骤:3.1 识别失效模式首先,我们需要识别潜在的失效模式。
失效模式是指系统、设计或过程中可能导致功能损失或性能下降的方式。
3.2 评估失效影响对于每个失效模式,我们需要评估其对电机性能的影响程度。
这包括考虑失效对电机功能、可靠性和安全性的影响。
3.3 评估失效发生概率我们还需要评估每个失效模式发生的概率。
这包括考虑电机使用环境、运行条件和维护情况等因素。
3.4 计算风险优先级通过将失效影响和失效发生概率相乘,我们可以计算每个失效模式的风险优先级。
这有助于确定哪些失效模式是最紧急需要解决的。
3.5 制定纠正措施根据风险优先级,我们可以制定相应的纠正措施。
这包括改进设计、加强质量控制、提供备用部件或进行培训等。
3.6 实施纠正措施最后,我们需要实施制定的纠正措施,并跟踪其有效性。
这有助于确保电机的可靠性和性能得到持续改进。
4. 电机FMEA分析结果在本次FMEA分析中,我们识别了以下几个主要失效模式和其对电机的影响:1.轴承磨损:由于长时间运行或不良润滑,电机轴承可能会磨损,导致噪音和振动增加,影响电机的性能和寿命。
2.绕组短路:由于绕组材料老化或绝缘不良,电机绕组可能出现短路,导致电机过热、烧毁甚至引发火灾。
3.供电电压不稳定:当供电电压波动较大时,电机可能无法正常工作,导致功率输出不稳定,影响电机性能和使用寿命。
4.散热不良:如果电机散热设计不良或散热系统堵塞,电机可能会过热,降低效率和寿命。
基于对失效影响和发生概率的评估,我们计算出了每个失效模式的风险优先级。
- 1、下载文档前请自行甄别文档内容的完整性,平台不提供额外的编辑、内容补充、找答案等附加服务。
- 2、"仅部分预览"的文档,不可在线预览部分如存在完整性等问题,可反馈申请退款(可完整预览的文档不适用该条件!)。
- 3、如文档侵犯您的权益,请联系客服反馈,我们会尽快为您处理(人工客服工作时间:9:00-18:30)。
微小
在源头探测问题
探测失效模式当场-操作员目视/触觉/听声方法,或
过程后-用计数型量具(go/no-go,手动扭力扳手等)
7
很小
在过程后探测问题
探测失效模式,过程后-操作员用计量值量具;或
当场-操作员用计数型量具(go/no-go,手动扭力扳手等)
6
小
在源头探测问题
探测失效模式,当场-操作员用计量值量具;或
潜在失效模式和效应分析(FMEA)
系统设计过程
系统 / 子系统 / 零部件 /项目名称:
责任者:
编号:者:
核心小组:
FMEA日期(制定)
修订
项目/
过程
步骤/
功能
要求
潜在
失效
模式
潜在
失效
后果
严
重
度
S
分类
失效
原因
现行系统/
设计/过程
控制
預防
频
度
O
现行系统/
设计/过程
十分低:不太可能
1
失效可用预防控制消除
探测度(Detection)
探测机会
准则:
以探测为过程控制的可能性
级别
探测
可能性
没有探测的机会
没有现行过程控制;无法探测或没有分析
10
几乎不可能
几乎在任何阶段都不能探测
失效模式或错误(原因)不容易探测(例:随机审核)
9
很微小
在过程后探测问题
探测失效模式,过程后-操作员目视/触觉/听声方法
8
主要功能丧失或降级
主要功能降级(项目不能运行,但不影响项目安全运行)
7
主要功能降级(项目能运行,表现水平下降)
6
次级功能丧失或降级
次级功能降级(项目能运行,但舒适/方便性的功能不运行)
5
次级功能降级(项目能运行,但舒适/方便性的功能表现水平下降)
4
烦恼
外观或能听到的噪音,项目能运行,不符合,大部分客户都能察觉(大于75%)
3
外观或能听到的噪音,项目能运行,不符合,很多顾客能察觉(50%)
2
外观或能听到的噪音,项目能运行,不符合,敏感顾客能察觉(小于25%)
1
没有影响
未有可识别影响
频度(Occurrence)
后果
级别
准则:原因的发生
十分高:持续失效
10
≥100件/每1000件
1: 10
高:经常失效
9
50件/每1000件
控制
探测
探测
度
D
风险
优先
数
RPN
建议
措施
负责
和
目标完成
日期
措施执行结果
采取的
措施
严
重
度
S
频
度
O
探测
度
D
R
P
N
严重度(Severity)
级别
后果
影响产品的严重度(客户影响)
10
不能符合安全和/或法规要求
潜在失效模式影响项目运行和/或涉及违反政府法规-没有警告
9
潜在失效模式影响项目安全运行和/或涉及违反政府法规-带有警告
或错误(原因)自动控制探测缺陷零件或通知操作员(光、蜂鸣器等)
执行作业前准备和首件测定检查(只适用作业前准备的原因)
5
中等
在过程后探测问题
探测失效模式,过程后-自动控制探测缺陷零件和自动扣留零件以防止进入下工序
4
中上
在源头探测问题
探测失效模式,当场-自动控制探测缺陷零件和自动扣留零件以防止进入下工序
1: 20
8
20件/每1000件
1: 50
7
10件/每1000件
1: 100
中等:偶然失效
6
2件/每1000件
1: 500
5
0.5件/每1000件
1: 2,000
4
0.1件/每1000件
1: 10,000
低:很少失效
3
0.01件/每1000件
1: 100,000
2
≤ 0.001件/每1000件
1:1,000,000
3
高
错误探测和/或问题预防
探测错误(原因),当场-自动控制探测错误和防止产生缺陷零件
2
很高
防止错误;不采用探测
防止错误(原因),夹具、机器或零件设计
过程/产品设计了防错法,不会产生缺陷零件
1
几乎肯定