PFMEA分析例子
PFMEA分析案例

型號 :審核者﹕批准者﹕表格編號﹕項目 :23/APR/2001日期﹕日期﹕版本﹕主要參加人員:采取的措施嚴重度發生度難檢度RPN2.來料檢查2.1 線路板(PCB)不良:線路短路;線路斷路;尺寸不符合要求;爛板(損傷);扭曲變形;混板;上錫PAD有綠油或污漬或氧化;絲印脫落;綠油脫落;無功能測試記號;線路欠損;線路刮花;線路間有銅箔渣;無V-CUT;V-CUT深或V-CUT淺;插件孔孔塞或嚴重披峰;補線路浮起或松動;報廢板未分開包裝;文字印刷嚴重移位;外標識與BOM要求不符.產生外觀不良或性能不良8供應商的4M1E管理不完善:a.人員培訓考核不完善或沒作人員變更管理;b.原材料不良或沒作物料變更管理;c.機器設備(包括儀器)保養維護不完善或沒作機器設備(包括儀器)變更管理;d.不按操作程序作業或操作程序不完善或沒作方法變更管理;e.溫濕度及5S管理不完善.3根據檢查指引抽查,發現有問題時通知供應商改善.5120通知供應商改善或要求供應商提供PFMEA分析.王剛山/2001/08/20通知供應商改善或要求供應商提供PFMEA分析.543602.2 貼片電容(CCAP)不良:電極氧化或發黑;損傷;混料;外標識與BOM要求不符;尺寸不符合要求;容值超差;電容漏電.產生外觀不良或性能不良8供應商的4M1E管理不完善:a.人員培訓考核不完善或沒作人員變更管理;b.原材料不良或沒作物料變更管理;c.機器設備(包括儀器)保養維護不完善或沒作機器設備(包括儀器)變更管理;d.不按操作程序作業或操作程序不完善或沒作方法變更管理;e.溫濕度及5S管理不完善.3根據檢查指引抽查,發現有問題時通知供應商改善.5120通知供應商改善或要求供應商提供PFMEA分析.王剛山/2001/08/20通知供應商改善或要求供應商提供PFMEA分析.543602.3 貼片電阻(CRES)不良:電極氧化或發黑;損傷;混料;外標識與BOM要求不符;尺寸不符合要求;阻值超差.產生外觀不良或性能不良8供應商的4M管理不完善:a.人員培訓考核不完善或沒作人員變更管理;b.原材料不良或沒作物料變更管理;c.機器設備(包括儀器)保養維護不完善或沒作機器設備(包括儀器)變更管理;d.不按操作程序作業或操作程序不完善或沒作方法變更管理;3根據檢查指引抽查,發現有問題時通知供應商改善.5120通知供應商改善或要求供應商提供PFMEA分析.王剛山/2001/08/20通知供應商改善或要求供應商提供PFMEA分析.543602.4 色碼電阻(LRES)不良:引腳氧化或變形或發黑;損傷;混料;絲印模糊;外標識與BOM要求不符;色環與阻值不符;阻值超差;功率與要求不符.產生外觀不良或性能不良8供應商的4M管理不完善:a.人員培訓考核不完善或沒作人員變更管理;b.原材料不良或沒作物料變更管理;c.機器設備(包括儀器)保養維護不完善或沒作機器設備(包括儀器)變更管理;d.不按操作程序作業或操作程序不完善或沒作方法變更管理;3根據檢查指引抽查,發現有問題時通知供應商改善.5120通知供應商改善或要求供應商提供PFMEA分析.王剛山/2001/08/20通知供應商改善或要求供應商提供PFMEA分析.54360發生度(O)現行的控制方法難檢度(D)RPN建議的措施責任人及完成時間第一頁共四頁措施結果工序名稱潛在的失效模式潛在的失效后果嚴重度(S)級別潛在的失效原因過程潛在的失效模式及后果分析(PFMEA)准備者﹕SMD-FM-B003PWB組裝日期﹕02.5插腳二極管(DIODE)不良:引腳氧化或變形或發黑;損傷;混料;絲印模糊;極性標識錯誤;實物絲印內容與BOM要求不符.外標識與BOM要求不符;尺寸不符合要求;電氣性能不良.產生外觀不良或性能不良8供應商的4M管理不完善:a.人員培訓考核不完善或沒作人員變更管理;b.或原材料不良或沒作物料變更管理;c.或機器設備(包括儀器)保養維護不完善或沒作機器設備(包括儀器)變更管理;d.或不按操作程序作業或操作程序不完善或沒作方法變更管理;3根據檢查指引抽查,發現有問題時通知供應商改善.5120通知供應商改善或要求供應商提供PFMEA分析.王剛山/2001/08/20通知供應商改善或要求供應商提供PFMEA分析.543602.6插腳三極管(TRAN)不良:引腳氧化或變形或發黑;損傷;混料;絲印模糊.實物絲印內容與BOM要求不符;外標識與BOM要求不符;尺寸不符合要求;極性錯誤;電氣性能不良.產生外觀不良或性能不良8供應商的4M管理不完善:a.人員培訓考核不完善或沒作人員變更管理;b.原材料不良或沒作物料變更管理;c.機器設備(包括儀器)保養維護不完善或沒作機器設備(包括儀器)變更管理;d.不按操作程序作業或操作程序不完善或沒作方法變更管理;3根據檢查指引抽查,發現有問題時通知供應商改善.5120通知供應商改善或要求供應商提供PFMEA分析.王剛山/2001/08/20通知供應商改善或要求供應商提供PFMEA分析.543602.7貼片三極管(TRAN)不良:電極氧化或變形或發黑;混料;損傷;絲印模糊;實物絲印內容與BOM要求不符;外標識與BOM要求不符;電氣性能不良.產生外觀不良或性能不良8供應商的4M管理不完善:a.人員培訓考核不完善或沒作人員變更管理;b.或原材料不良或沒作物料變更管理;c.或機器設備(包括儀器)保養維護不完善或沒作機器設備(包括儀器)變更管理;d.或不按操作程序作業或操作程序不完善或沒作方法變更管理;3根據檢查指引抽查,發現有問題時通知供應商改善.5120通知供應商改善或要求供應商提供PFMEA分析.王剛山/2001/08/20通知供應商改善或要求供應商提供PFMEA分析.543602.8直插式IC不良:引腳氧化或變形或發黑;封裝形式不符要求;損傷;混料;絲印模糊;絲印內容與BOM要求不符;外標識與BOM要求不符;尺寸不符合要求;電氣性能不良.產生外觀不良或性能不良8供應商的4M管理不完善:a.人員培訓考核不完善或沒作人員變更管理;b.或原材料不良或沒作物料變更管理;c.或機器設備(包括儀器)保養維護不完善或沒作機器設備(包括儀器)變更管理;d.或不按操作程序作業或操作程序不完善或沒作方法變更管理;3根據檢查指引抽查,發現有問題時通知供應商改善.5120通知供應商改善或要求供應商提供PFMEA分析.王剛山/2001/08/20通知供應商改善或要求供應商提供PFMEA分析.543602.9貼片式IC不良:引腳氧化或變形或發黑;封裝形式不符要求;損傷;混料;絲印模糊;實物絲印內容與BOM要求不符;外標識與BOM要求不符;尺寸不符合要求;電氣性能不良.產生外觀不良或性能不良8供應商的4M管理不完善:a.人員培訓考核不完善或沒作人員變更管理;b.或原材料不良或沒作物料變更管理;c.或機器設備(包括儀器)保養維護不完善或沒作機器設備(包括儀器)變更管理;d.或不按操作程序作業或操作程序不完善或沒作方法變更管理;3根據檢查指引抽查,發現有問題時通知供應商改善.5120通知供應商改善或要求供應商提供PFMEA分析.王剛山/2001/08/20通知供應商改善或要求供應商提供PFMEA分析.543602.10瓷片電容(LCAP)不良:引腳氧化或變形或發黑;損傷;混料;絲印模糊;絲印內容與容值不符;外標識與BOM要求不符;尺寸不符合要求;容值超差;耐壓值不符要求;電容漏電.產生外觀不良或性能不良8供應商的4M1E管理不完善:a.人員培訓考核不完善或沒作人員變更管理;b.原材料不良或沒作物料變更管理;c.機器設備(包括儀器)保養維護不完善或沒作機器設備(包括儀器)變更管理;d.不按操作程序作業或操作程序不完善或沒作方法變更管理;e.溫濕度及5S管理不完善.3根據檢查指引抽查,發現有問題時通知供應商改善.5120通知供應商改善或要求供應商提供PFMEA分析.王剛山/2001/08/20通知供應商改善或要求供應商提供PFMEA分析.543602.11排阻(NRES)不良:引腳氧化或發黑;損傷;混料;封裝形式不符要求;外標識與BOM要求不符;尺寸不符合要求;排阻的網絡阻值超差.產生外觀不良或性能不良8供應商的4M1E管理不完善:a.人員培訓考核不完善或沒作人員變更管理;b.原材料不良或沒作物料變更管理;c.機器設備(包括儀器)保養維護不完善或沒作機器設備(包括儀器)變更管理;d.不按操作程序作業或操作程序不完善或沒作方法變更管理;e.溫濕度及5S管理不完善.3根據檢查指引抽查,發現有問題時通知供應商改善.5120通知供應商改善或要求供應商提供PFMEA分析.王剛山/2001/08/20通知供應商改善或要求供應商提供PFMEA分析.543602.12晶振(RESONATOR)不良:引腳氧化或變形或發黑;損傷;混料;絲印模糊;外標識與BOM要求不符;實物絲印內容與BOM要求不符;尺寸不符合要求;電氣性能不良.產生外觀不良或性能不良8供應商的4M1E管理不完善:a.人員培訓考核不完善或沒作人員變更管理;b.原材料不良或沒作物料變更管理;c.機器設備(包括儀器)保養維護不完善或沒作機器設備(包括儀器)變更管理;d.不按操作程序作業或操作程序不完善或沒作方法變更管理;e.溫濕度及5S管理不完善.3根據檢查指引抽查,發現有問題時通知供應商改善.5120通知供應商改善或要求供應商提供PFMEA分析.王剛山/2001/08/20通知供應商改善或要求供應商提供PFMEA分析.543602.13貼片二極管(DIODE)不良:焊腳氧化或發黑;損傷;混料;實物絲印內容與BOM要求不符;外標識與BOM要求不符;尺寸不符合要求;極性標識錯誤;電氣性能不良.產生外觀不良或性能不良8供應商的4M1E管理不完善:a.人員培訓考核不完善或沒作人員變更管理;b.原材料不良或沒作物料變更管理;c.機器設備(包括儀器)保養維護不完善或沒作機器設備(包括儀器)變更管理;d.不按操作程序作業或操作程序不完善或沒作方法變更管理;e.溫濕度及5S管理不完善.3根據檢查指引抽查,發現有問題時通知供應商改善.5120通知供應商改善或要求供應商提供PFMEA分析.王剛山/2001/08/20通知供應商改善或要求供應商提供PFMEA分析.543602.14插座/排插(SOCKET)不良:引腳氧化或發黑;損傷;混料;實物絲印內容與BOM要求不符;外標識與BOM要求不符;尺寸不符合要求;針腳氧化或變形或針腳高或針腳低或少針或多針;電氣性能不良.產生外觀不良或性能不良8供應商的4M1E管理不完善:a.人員培訓考核不完善或沒作人員變更管理;b.原材料不良或沒作物料變更管理;c.機器設備(包括儀器)保養維護不完善或沒作機器設備(包括儀器)變更管理;d.不按操作程序作業或操作程序不完善或沒作方法變更管理;e.溫濕度及5S管理不完善.3根據檢查指引抽查,發現有問題時通知供應商改善.5120通知供應商改善或要求供應商提供PFMEA分析.王剛山/2001/08/20通知供應商改善或要求供應商提供PFMEA分析.543602.15貼片電解電容(SMD ECAP)不良:電極氧化或發黑;損傷(壓痕);混料;編帶反向.絲印模糊;實物絲印內容與BOM要求不符;外標識與BOM要求不符;尺寸不符合要求;容值超差;電容漏電.產生外觀不良或性能不良8供應商的4M1E管理不完善:a.人員培訓考核不完善或沒作人員變更管理;b.原材料不良或沒作物料變更管理;c.機器設備(包括儀器)保養維護不完善或沒作機器設備(包括儀器)變更管理;d.不按操作程序作業或操作程序不完善或沒作方法變更管理;e.溫濕度及5S管理不完善.3根據檢查指引抽查,發現有問題時通知供應商改善.5120通知供應商改善或要求供應商提供PFMEA分析.王剛山/2001/08/20通知供應商改善或要求供應商提供PFMEA分析.543602.16直插式電解電容(ECAP)不良:引腳氧化或發黑;損傷(包括PVC套管破損、移位);極性電容正負極標識錯誤;防爆帽凸出;編帶反向.混料;絲印模糊;實物絲印內容與BOM 要求不符;外標識與BOM要求不符;尺寸不符合要求;電氣性能不符要求.產生外觀不良或性能不良8供應商的4M1E管理不完善:a.人員培訓考核不完善或沒作人員變更管理;b.原材料不良或沒作物料變更管理;c.機器設備(包括儀器)保養維護不完善或沒作機器設備(包括儀器)變更管理;d.不按操作程序作業或操作程序不完善或沒作方法變更管理;e.溫濕度及5S管理不完善.3根據檢查指引抽查,發現有問題時通知供應商改善.5120通知供應商改善或要求供應商提供PFMEA分析.王剛山/2001/08/20通知供應商改善或要求供應商提供PFMEA分析.543602.17線圈(COIL)不良:引腳氧化或變形或發黑;損傷;混料;外標識與BOM要求不符;尺寸不符合要求;電氣性能不良.產生外觀不良或性能不良8供應商的4M1E管理不完善:a.人員培訓考核不完善或沒作人員變更管理;b.原材料不良或沒作物料變更管理;c.機器設備(包括儀器)保養維護不完善或沒作機器設備(包括儀器)變更管理;d.不按操作程序作業或操作程序不完善或沒作方法變更管理;e.溫濕度及5S管理不完善.3根據檢查指引抽查,發現有問題時通知供應商改善.5120通知供應商改善或要求供應商提供PFMEA分析.王剛山/2001/08/20通知供應商改善或要求供應商提供PFMEA分析.543602.18開關(SWITCH)不良:焊腳氧化或變形或發黑;損傷;混料;外標識與BOM要求不符;尺寸不符合要求;機械性能不良;電氣性能不良.產生外觀不良或性能不良8供應商的4M1E管理不完善:a.人員培訓考核不完善或沒作人員變更管理;b.原材料不良或沒作物料變更管理;c.機器設備(包括儀器)保養維護不完善或沒作機器設備(包括儀器)變更管理;d.不按操作程序作業或操作程序不完善或沒作方法變更管理;e.溫濕度及5S管理不完善.3根據檢查指引抽查,發現有問題時通知供應商改善.5120通知供應商改善或要求供應商提供PFMEA分析.王剛山/2001/08/20通知供應商改善或要求供應商提供PFMEA分析.543602.19插腳火牛不良:插腳氧化或變形或發黑;損傷;混料;外標識與BOM要求不符;尺寸不符合要求;電氣性能不良.產生外觀不良或性能不良8供應商的4M1E管理不完善:a.人員培訓考核不完善或沒作人員變更管理;b.原材料不良或沒作物料變更管理;c.機器設備(包括儀器)保養維護不完善或沒作機器設備(包括儀器)變更管理;d.不按操作程序作業或操作程序不完善或沒作方法變更管理;e.溫濕度及5S管理不完善.3根據檢查指引抽查,發現有問題時通知供應商改善.5120通知供應商改善或要求供應商提供PFMEA分析.王剛山/2001/08/20通知供應商改善或要求供應商提供PFMEA分析.54360??序號號IPQC抽檢不適用,因為研究RPN值達不到24,屬低風險.??序號QA抽檢不適用,因為研究RPN值達不到24,屬低風險.2.20跳線(JUMPER WIRE)不良:焊腳氧化或變形或發黑;損傷;混料;外標識與BOM要求不符;尺寸不符合要求;性能不良.(特別注意:這項僅適用于BJH-3122)產生外觀不良或性能不良8供應商的4M1E管理不完善:a.人員培訓考核不完善或沒作人員變更管理;b.原材料不良或沒作物料變更管理;c.機器設備(包括儀器)保養維護不完善或沒作機器設備(包括儀器)變更管理;d.不按操作程序作業或操作程序不完善或沒作方法變更管理;e.溫濕度及5S管理不完善.3IQC根據檢查指引抽查,發現有問題時通知供應商改善.5120通知供應商改善或要求供應商提供PFMEA分析.王剛山/2001/08/20通知供應商改善或要求供應商提供PFMEA分析.54360備注:這份來料檢查的PFMEA僅供參考,如制作PFMEA時必須根據BOM的要求刪除或增加(目前應不需要增加)某些項目,如有問題,請聯絡品質一部---陳偉業(內線208).。
pfmea例子
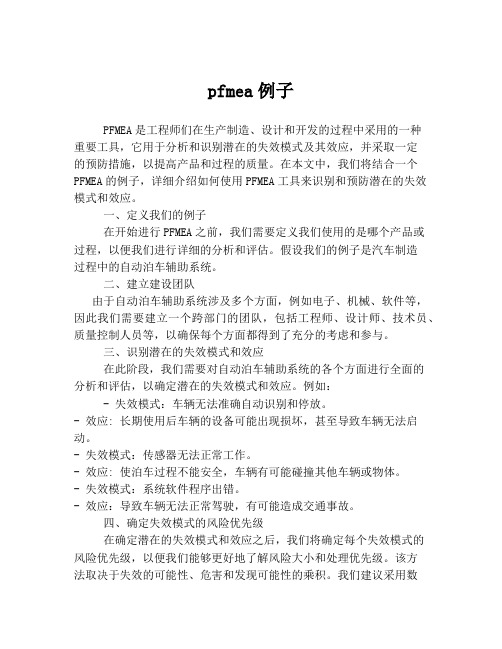
pfmea例子PFMEA是工程师们在生产制造、设计和开发的过程中采用的一种重要工具,它用于分析和识别潜在的失效模式及其效应,并采取一定的预防措施,以提高产品和过程的质量。
在本文中,我们将结合一个PFMEA的例子,详细介绍如何使用PFMEA工具来识别和预防潜在的失效模式和效应。
一、定义我们的例子在开始进行PFMEA之前,我们需要定义我们使用的是哪个产品或过程,以便我们进行详细的分析和评估。
假设我们的例子是汽车制造过程中的自动泊车辅助系统。
二、建立建设团队由于自动泊车辅助系统涉及多个方面,例如电子、机械、软件等,因此我们需要建立一个跨部门的团队,包括工程师、设计师、技术员、质量控制人员等,以确保每个方面都得到了充分的考虑和参与。
三、识别潜在的失效模式和效应在此阶段,我们需要对自动泊车辅助系统的各个方面进行全面的分析和评估,以确定潜在的失效模式和效应。
例如:- 失效模式:车辆无法准确自动识别和停放。
- 效应: 长期使用后车辆的设备可能出现损坏,甚至导致车辆无法启动。
- 失效模式:传感器无法正常工作。
- 效应: 使泊车过程不能安全,车辆有可能碰撞其他车辆或物体。
- 失效模式:系统软件程序出错。
- 效应:导致车辆无法正常驾驶,有可能造成交通事故。
四、确定失效模式的风险优先级在确定潜在的失效模式和效应之后,我们将确定每个失效模式的风险优先级,以便我们能够更好地了解风险大小和处理优先级。
该方法取决于失效的可能性、危害和发现可能性的乘积。
我们建议采用数字大小为1到10,数字越高则表示失效的严重性越高。
五、建立控制措施在确定失效模式和风险优先级之后,我们需要建立相应的控制措施,以减轻或避免失效的效应。
例如:- 采用多个传感器以提高准确性并减少失效的可能性。
- 建立合适的故障检测与纠正系统,在操作系统出错时的同时修复它。
- 明确系统的软件设计和开发的标准,以保证其正确性和适应性。
六、建立检测和监测措施在建立了相应的控制措施之后,我们需要建立检测和监测措施,以确保实施有效并及时告知需要采取改进措施的数据。
新版PFMEA案例

新版PFMEA案例
过程失
面无锈蚀、磕碰
、划痕
清洗洁度,机体安装
后,能够降低发动
机产生异响的概率
过程失效模式及后果分析(PFMEA)
2.每季度对维护保养计划的执行情况进行检查确认。
3.每月度对清洗剂的更换频次进行检查确认。
量异常;
对最终用户影响:无
点;
料:清洗剂不能满足除污、防锈要求,清洗剂过期,未得到监控法:超声波清洗机内的液体未及时更换,液体变质:
进行维护保养;3.确定清洗剂液体更换周期,并明确在作业标准中。
对机体表面100%检查针对失效起因:
1.每半年对人员的能力评影响交付或交付后顾客投诉;
对主机厂影响:表面存在锈斑、有磕碰点和划痕人员取放工件
时与传输带表面碰撞;
机:传输带长时间训,提高质量意识。
2.制定维护保养
措施。
六步法pfmea案例

六步法pfmea案例全文共四篇示例,供读者参考第一篇示例:案例背景:某家汽车零部件制造公司在生产过程中发现了一个频繁出现的问题:某零部件的尺寸偏差过大,导致装配时无法完全契合,进而影响产品的性能和质量。
为了解决这一问题,公司决定使用六步法PFMEA 进行分析和改进。
步骤一:确定分析范围团队确定了分析的范围为某零部件的生产工艺。
他们明确了问题的具体表现,以及对产品性能和质量的影响。
团队还确定了分析的目的是为了找出可能引起零部件尺寸偏差的潜在故障模式,并制定相应的控制措施。
步骤二:收集相关信息团队开始收集相关信息,包括零部件的设计图纸、生产工艺流程、设备参数、材料性质等。
他们还对生产现场进行实地考察,观察生产过程中的关键环节,并与相关工程师和操作人员进行沟通交流,了解他们对问题的认识和看法。
步骤三:识别潜在故障模式通过分析收集到的信息,团队识别出了可能导致零部件尺寸偏差的潜在故障模式。
包括:材料供应质量不稳定、设备操作不规范、工艺参数设置不当等。
每个故障模式都被赋予一个风险等级,以确定其重要性和优先级。
步骤四:确定故障影响团队分析每个故障模式的影响范围,包括对产品性能、质量、交付时间等方面的影响。
他们还评估了每个故障模式的可能性和频率,以确定其潜在风险。
步骤五:制定改进控制措施基于对故障模式和影响的分析,团队制定了一系列改进控制措施,以降低潜在风险。
加强材料供应商管理、优化生产工艺流程、规范设备操作规程等。
每个控制措施都被赋予一个责任人和执行时间表,以确保实施和落实。
步骤六:跟踪和持续改进团队制定了一个跟踪和持续改进计划,以监控改进控制措施的执行情况和效果。
他们定期对实施情况进行评估和审查,继续识别和解决可能存在的风险和问题,确保质量和性能的持续提升。
通过六步法PFMEA的分析和改进,该汽车零部件制造公司成功解决了零部件尺寸偏差的问题,提高了产品的质量和性能,降低了生产过程中的风险和损失,进一步提升了企业的竞争力和市场地位。
PFMEA实例分析

风险评价
(重要性B/严重度)
本例中考虑的缺陷后果是:“输入轴总成制造有缺 陷”。
为确定重要性S/严重度,需评价将会对汽车因而对
外部顾客(最终用户)造成何种缺陷后果。在评价
重要性时,这种情况下将产品系统FMEA中“潜在 的最严重的缺陷后果”的重要性评价为S=8,这是 因为它会引起汽车(整个系统)潜在的缺陷后果。
调整员 操作员
输入轴总成 生产总过程
滚珠轴承轴 承座与滑 动油封的磨
削过程
磨床
SE“磨床”的深层结构 夹紧系统 驱动系统 控制系统
机座 磨削工装
冷却/润滑系统
图2:“滚珠轴承轴承座的磨削过程…”分系统结构
环境
机器的固定基础 磨床冷却剂的供给
系统单元和系统结构
功能交接点:
图3表明了结构中对两个SE“磨削送料过程”与“轴承座的磨削 过程…”进行分解而形成的交接点。 通过输送链向磨床的夹紧系统传送工件的例子表明了“磨削送 料过程”与“轴承座的磨削过程…”之间的交互。 若下一步制定功能结构时可能会超越系统结构的这些界限, 则要对功能之间的相互关系进行完整的描述。
缺陷分析
(交互概念及运用)
图7(见下页)中,将不同产品系统FMEA的交互 进一步导引到过程系统FMEA中。根据这样的交互 ,可以把SE产品(例如,传动器)的失效功能追 溯到某一构件或总成的的制造方法的失效功能。在 所提及的实例中,潜在的缺陷原因最终被追溯到磨 床的驱动转速上。
缺陷分析
(交互图范例)
驱动轴的清洗过程 装配送料过程
把轴承装到轴 上的装配过程 装配输出过程
装配工 装配设备 轴承
油脂
PFMEA第五版实例

Item (Part #):Process Responsi bilityModelYear(s)/Program(s)Core Team:FAMILY OF PARTS: P1市场部/开发部/制造部/采购部/物流部/质保部POTENTIALFAILURE MODE AND EFFECTS ANALYSIS(PROCESS FMEA)APQP TEAM外购件领取(1);buyer:无影响(1)位料(2);存储在不开箱数量差异(6);buyer:无影响(1)视检查不足(3);操作员和不对成品产生损伤对成品产生损伤supplier:部分(小于100%)外购件需要报废(6);Coustomer:不合格产品流入客户(6);buyer:无影响(1)6检验员技能不合格4技能评定/培训培训记录/技能矩阵更新61442装车方法正确装车方法不正确supplier:产品变形或损坏(6);Coustomer:不合格产品流入客户(6);buyer:无影响(1)6仓管员技能不合格4技能评定/培训培训记录/技能矩阵更新71682产品防护正确产品防护不正确supplier:产品变形或损坏(6);Coustomer:不合格产品流入客户(6);buyer:无影响(1)6仓管员技能不合格4技能评定/培训培训记录/技能矩阵更新71682出货检验240发运Preparedby:FMEADate (Orig.)FMEADate (Rev.)。
PFMEA的严重度频度探测度评分准则
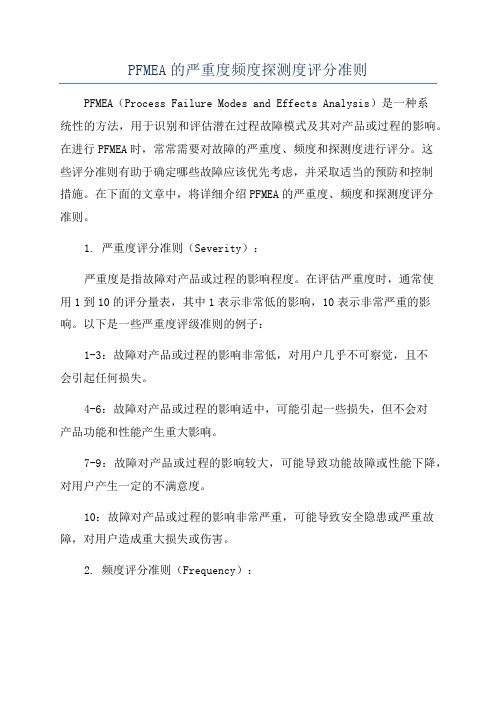
PFMEA的严重度频度探测度评分准则PFMEA(Process Failure Modes and Effects Analysis)是一种系统性的方法,用于识别和评估潜在过程故障模式及其对产品或过程的影响。
在进行PFMEA时,常常需要对故障的严重度、频度和探测度进行评分。
这些评分准则有助于确定哪些故障应该优先考虑,并采取适当的预防和控制措施。
在下面的文章中,将详细介绍PFMEA的严重度、频度和探测度评分准则。
1. 严重度评分准则(Severity):严重度是指故障对产品或过程的影响程度。
在评估严重度时,通常使用1到10的评分量表,其中1表示非常低的影响,10表示非常严重的影响。
以下是一些严重度评级准则的例子:1-3:故障对产品或过程的影响非常低,对用户几乎不可察觉,且不会引起任何损失。
4-6:故障对产品或过程的影响适中,可能引起一些损失,但不会对产品功能和性能产生重大影响。
7-9:故障对产品或过程的影响较大,可能导致功能故障或性能下降,对用户产生一定的不满意度。
10:故障对产品或过程的影响非常严重,可能导致安全隐患或严重故障,对用户造成重大损失或伤害。
2. 频度评分准则(Frequency):频度是指故障发生的可能性或发生的次数。
在评估频度时,通常使用1到10的评分量表,其中1表示非常低的发生频率,10表示非常高的发生频率。
以下是一些频度评级准则的例子:1-3:非常低的频度,可能发生的概率非常低,甚至几乎不会发生。
4-6:中等频度,可能在一段时间内发生一次或多次,但不会频繁发生。
7-9:较高的频度,可能在一段时间内频繁发生,但不是持续性的。
10:非常高的频度,可能持续性地发生,对产品或过程造成持续的风险。
3. 探测度评分准则(Detection):探测度是指发现和检测故障的能力。
在评估探测度时,通常使用1到10的评分量表,其中1表示非常低的探测度,10表示非常高的探测度。
以下是一些探测度评级准则的例子:1-3:非常低的探测度,几乎没有任何探测手段,难以发现故障。
PFMEA的例子
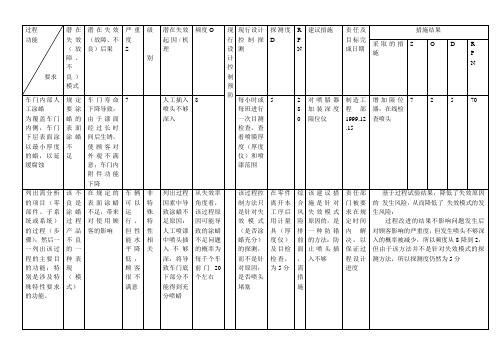
在规定的表面涂蜡不足,带来对使用顾客的影响
车辆可以运行,但性能水平降低,顾客很不满意
非特殊特性相关
列出过程因素中导致涂蜡不足原因:人工喷漆中喷头插入不够深,将导致车门底下部分不能得到充分喷蜡
从失效率角度看,该过程原因可能导致的涂蜡不足问题的概率为每千个车前门20个左右
RPN
建议措施
责任及目标完成日期
措施结果
采取的措施
S
O
D
R
P
N
车门内部人工涂蜡
为覆盖车门内侧,车门下层表面涂以最小厚度的蜡,以延缓腐蚀
规定要涂蜡的表面涂蜡不足
车门寿命下降导致:由于漆面经过长时间后生锈,使顾客对外观不满意;车门内附件功能下降
7
人工插入喷头不够深入
8
每小时或每班进行一次目测检查,查看厚度(厚度仪)和喷漆范围
7
人工插入喷头不够深入
8
每小时或每班进行一次目测检查,查看喷膜厚度(厚度仪)和喷漆范围
5
280
对喷腊器加装深度限位仪
制造工程部1999.12.15
增加限位器,在线检查喷头
7
2
5
70
列出需分析的项目(零部件、子系统或系统)的过程(步骤);然后一一列出该过程的主要目的功能;特别是涉及特殊特性要求的功能。
过程改进的结果不影响问题发生后对顾客影响的严重度,但发生喷头堵塞的概率被减少,所有频度从5降到1(完全不会发生),但由于该方法并不是针对失效模式的探测方法,所有探测度仍然为5分。
ቤተ መጻሕፍቲ ባይዱ过程
功能
要求
潜在失效(故障、不良)模式
潜在失效(故障、不良)后果
严重度
PFMEA第五版实例全篇

PFMEA第五版实例Item (Part #):Process Responsi bilityModelYear(s)/Program(s)Core Team:FAMILY OF PARTS: P1市场部/开发部/制造部/采购部/物流部/质保部POTENTIALFAILURE MODE AND EFFECTS ANALYSIS (PROCESS FMEA)APQP TEAM外购件领取(1);buyer:⽆影响(1)位料(2);存储在不开箱数量差异(6);buyer:⽆影响(1)视检查不⾜(3);操作员和不对成品产⽣损伤对成品产⽣损伤supplier:部分(⼩于100%)外购件需要报废(6);Coustomer:不合格产品流⼊客户(6);buyer:⽆影响(1)6检验员技能不合格4技能评定/培训培训记录/技能矩阵更新61442装车⽅法正确装车⽅法不正确supplier:产品变形或损坏(6);Coustomer:不合格产品流⼊客户(6);buyer:⽆影响(1)6仓管员技能不合格4技能评定/培训培训记录/技能矩阵更新71682产品防护正确产品防护不正确supplier:产品变形或损坏(6);Coustomer:不合格产品流⼊客户(6);buyer:⽆影响(1)6仓管员技能不合格4技能评定/培训培训记录/技能矩阵更新71682出货检验240发运Preparedby:FMEADate (Orig.)FMEADate (Rev.)。
PFMEA分析范例
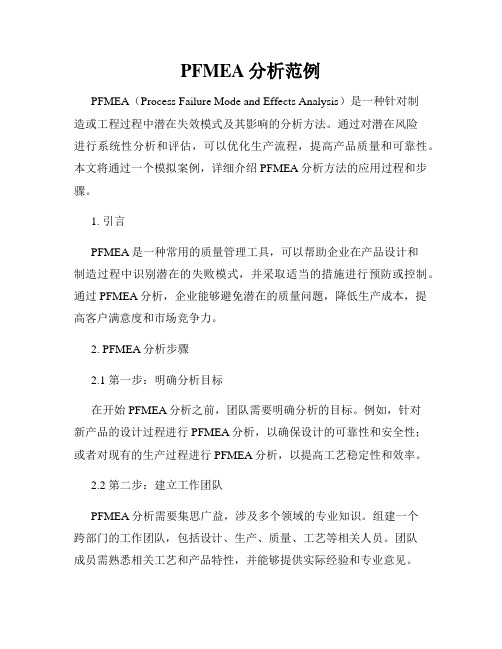
PFMEA分析范例PFMEA(Process Failure Mode and Effects Analysis)是一种针对制造或工程过程中潜在失效模式及其影响的分析方法。
通过对潜在风险进行系统性分析和评估,可以优化生产流程,提高产品质量和可靠性。
本文将通过一个模拟案例,详细介绍PFMEA分析方法的应用过程和步骤。
1. 引言PFMEA是一种常用的质量管理工具,可以帮助企业在产品设计和制造过程中识别潜在的失败模式,并采取适当的措施进行预防或控制。
通过PFMEA分析,企业能够避免潜在的质量问题,降低生产成本,提高客户满意度和市场竞争力。
2. PFMEA分析步骤2.1 第一步:明确分析目标在开始PFMEA分析之前,团队需要明确分析的目标。
例如,针对新产品的设计过程进行PFMEA分析,以确保设计的可靠性和安全性;或者对现有的生产过程进行PFMEA分析,以提高工艺稳定性和效率。
2.2 第二步:建立工作团队PFMEA分析需要集思广益,涉及多个领域的专业知识。
组建一个跨部门的工作团队,包括设计、生产、质量、工艺等相关人员。
团队成员需熟悉相关工艺和产品特性,并能够提供实际经验和专业意见。
2.3 第三步:识别潜在失效模式团队成员根据自身经验和知识,共同识别与分析对象相关的潜在失效模式。
失效模式可以包括设计缺陷、材料问题、加工工艺不当等。
团队成员应尽可能全面地讨论和归纳,并记录在PFMEA表中。
2.4 第四步:评估失效影响针对每一个潜在失效模式,团队成员需要评估其对产品质量、客户满意度和生产效率的影响程度。
评估标准可以根据实际情况进行设计,通常包括质量损失程度、生产变更的难易程度、不良事件的概率等。
2.5 第五步:确定原因和现有控制措施对于每一个潜在失效模式,团队需要分析其潜在原因并列出现有的控制措施。
原因分析可以采用5W1H(Who、What、When、Where、Why和How)的方法,识别可能导致失效的根本原因。
PFMEA分析案例(供参考) - 副本

相关资料 FMEA分析小组架构图、职责
表
项目计划表
结构树
结构树图
功能树
功能树图
功能失效矩阵
失效链矩阵表
S、O、D和AP
S、O、D评分标准及AP措施优 先级表
/改善Βιβλιοθήκη 施表/FMEA分析报告
PFMEA分析计划
序号 1 2
项目 成立PFMEA分析小
组
确定项目周期
负责部门 技术部 技术部/FMEA小组
负责人 完成日期 XXX XXXX-XX-XX XXX XXXX-XX-XX
3 确定要分析的范围 技术部/FMEA小组
XXX XXXX-XX-XX
4
功能分析
技术部/FMEA小组
5
失效分析
技术部/FMEA小组
6
风险分析(确定 S\O\D)评分表
技术部/FMEA小组
7
改善措施
技术部/FMEA小组
8 FMEA结果文件化 技术部/FMEA小组
XXX XXXX-XX-XX XXX XXXX-XX-XX XXX XXXX-XX-XX XXX XXXX-XX-XX XXX XXXX-XX-XX
计划
使用工具 / /
aiag vda pfmea例子
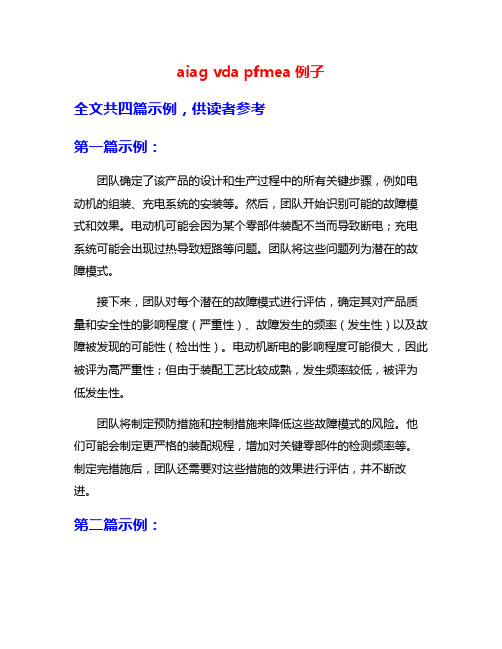
aiag vda pfmea例子全文共四篇示例,供读者参考第一篇示例:团队确定了该产品的设计和生产过程中的所有关键步骤,例如电动机的组装、充电系统的安装等。
然后,团队开始识别可能的故障模式和效果。
电动机可能会因为某个零部件装配不当而导致断电;充电系统可能会出现过热导致短路等问题。
团队将这些问题列为潜在的故障模式。
接下来,团队对每个潜在的故障模式进行评估,确定其对产品质量和安全性的影响程度(严重性)、故障发生的频率(发生性)以及故障被发现的可能性(检出性)。
电动机断电的影响程度可能很大,因此被评为高严重性;但由于装配工艺比较成熟,发生频率较低,被评为低发生性。
团队将制定预防措施和控制措施来降低这些故障模式的风险。
他们可能会制定更严格的装配规程,增加对关键零部件的检测频率等。
制定完措施后,团队还需要对这些措施的效果进行评估,并不断改进。
第二篇示例:AIAG VDA PFMEA是指根据国际汽车行业标准组织(AIAG)和德国汽车工程师协会(VDA)共同制定的一种过程失效模式及影响分析方法。
这种方法是为了帮助汽车行业的供应链伙伴在产品设计和生产过程中识别和解决潜在的故障模式,从而提高产品质量和可靠性。
在本文中,我们将以实际案例为例,介绍AIAG VDA PFMEA的具体应用及其重要性。
故障模式及影响分析(FMEA)是一种常见的质量管理工具,其目的是通过系统性地识别和排除产品和过程中的潜在故障模式,以确保产品的质量和可靠性。
在汽车行业,产品设计和生产过程中存在着各种各样的潜在故障模式,如设计错误、工艺不当、零部件失效等,这些故障模式可能会导致产品的功能失效、安全性降低,甚至对用户造成伤害。
AIAG VDA PFMEA是结合了AIAG和VDA两个国际汽车行业标准组织的最佳实践而制定的一种FMEA方法。
它强调了全面性和系统性,要求参与方从产品设计、制造、测试、维修等全过程来考虑潜在故障模式,并评估其可能的影响程度和频率。
pfmea案例

pfmea案例PFMEA案例。
PFMEA(Process Failure Mode and Effects Analysis)是一种用于识别和评估制造过程中潜在故障模式及其影响的方法。
它可以帮助企业在生产过程中提前识别潜在的问题,并采取相应的措施进行预防,从而提高产品质量和生产效率。
下面我们将通过一个实际的案例来介绍PFMEA的应用。
在某汽车零部件生产企业,他们使用PFMEA来分析生产线上的焊接工艺。
首先,团队收集了关于焊接工艺的所有相关信息,包括焊接设备、焊接材料、操作流程等。
然后,团队针对每个潜在的故障模式进行分析,包括焊接接头断裂、焊接温度过高、焊接时间过长等。
接着,团队对每种故障模式的可能影响进行评估,比如焊接接头断裂可能导致产品失效,焊接温度过高可能导致材料变形等。
最后,团队制定了针对每种故障模式的预防措施,比如加强对焊接工艺的监控,优化焊接参数,加强员工培训等。
通过PFMEA的分析,该企业发现了一些潜在的问题,并及时采取了相应的措施进行预防,从而避免了可能导致产品质量问题的故障发生。
这不仅提高了产品质量,也降低了生产成本,提高了生产效率。
通过以上案例可以看出,PFMEA作为一种有效的质量管理工具,在生产过程中发挥着重要作用。
它可以帮助企业在生产过程中及时发现潜在的问题,并采取预防措施,从而提高产品质量,降低生产成本,提高生产效率。
因此,建议更多的企业在生产过程中引入PFMEA方法,以提升竞争力,满足市场需求。
综上所述,PFMEA在制造业中具有重要意义,通过对潜在故障模式和影响进行分析和评估,有助于企业提前预防问题的发生,提高产品质量和生产效率。
希望更多的企业能够重视PFMEA的应用,从而在激烈的市场竞争中脱颖而出。
PFMEA分析案例

PFMEA分析案例PFMEA (Process Failure Mode and Effects Analysis) 是一种基于逻辑的风险评估方法,可以帮助企业识别并预防潜在的产品或过程故障,并采取适当的措施以降低风险。
下面以一个汽车制造企业的案例来说明PFMEA分析的过程和方法。
该汽车制造企业正在开发一种新型的发动机,该发动机具有更高的效率和更低的排放。
为了确保其性能和可靠性,企业决定使用PFMEA分析来评估制造过程中的潜在风险。
首先,需要组成一个跨职能团队,由从事设计、生产、质量控制、供应链等不同领域的专家组成。
团队成员将一起参与分析过程,并根据各自的专业知识和经验,提供各种潜在故障模式和可能导致故障的原因。
接下来,团队需要确定所有与发动机制造相关的过程步骤。
这些步骤可能包括原材料采购、零部件加工、总装等。
对于每个步骤,团队成员将系统地分析可能的故障模式,并为每种故障模式评估其影响和概率。
以其中一步骤为例,如发动机总装。
团队可能提出以下故障模式:1)零部件安装错误;2)零部件损坏;3)工人操作失误等。
对于每种故障模式,团队将考虑以下因素进行评估:A)故障模式对质量的影响,如可能导致发动机故障或性能下降;B)故障模式发生的概率,如是否存在操作失误的可能性以及其频率;C)故障模式是否可以被探测到,即是否有能够检测到这种故障模式的方法。
根据评估结果,团队将对被认为是高风险的故障模式采取相应的预防措施和纠正措施。
例如,对于零部件安装错误的故障模式,团队可能建议改进零部件标识和引导,并进行培训以提高工人的操作准确性。
对于零部件损坏的故障模式,团队可能建议加强供应商的质量管控,实施更严格的目视检查等。
最后,团队将整理和汇总所有的故障模式、原因、影响和措施,并生成PFMEA报告。
该报告将被用于指导发动机制造过程的改进和优化,并作为质量管理体系的一部分进行监控和追踪。
通过PFMEA分析,该汽车制造企业能够识别潜在的风险和故障,并采取适当的措施进行预防。
PFMEA经典案例

5
280
给喷蜡枪加装深度限位器
制造工程
9X,10,15
增加限位器,在线上检查喷蜡枪
7
2
5
70
使喷蜡作业自动化
制造工程9X,12,15
由于同一条线上不同的门复杂程度不同,因此拒绝该项
7
喷头堵塞
-粘度太高
-温度太低
-压力太低
5
在开始和停机后试验喷雾形状,按照预防维护程序清洗喷头
7
1
7
49
潜在失效模式及后果分析
过程FMEA
FMEA编号:1450 (1)
页码:第1页共1页
项目名称:左前门/H8HX–000–A (2)过程责任部门:车身工程师/装配部(3)编制者:J. Ford–X6512–装配部门(4)
车型年度/车辆类型:199X/狮牌4门/旅行车(5)关键日期:9X.03.01 9X 08 26工序#1(6)FMEA日期:(编制)9X.05.17 (修订)9X.11.06 (7)
核心小组:A. Tade–车身工程师J. Smith–作业控制R. James–生产部、J. Jones–维修部(8)
项目
(9)
功能
潜在
失效模式
(10)
潜在
失效后果
(11)
严重
度
(S)
分类
(13)
潜在失效
起因/机理
(14)
频
度
(0)
现行预防过程控制
(16)
现行探测过程控制
(16)
探测
度
(D)
风险
顺序
每小时进行目测检查,每班检查一次喷膜厚度(深度计)和范围
PFMEA案例(7.2)
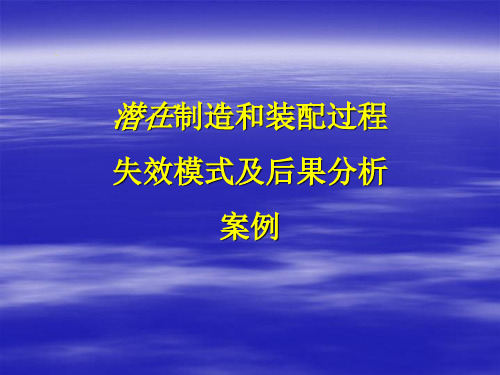
失效模式及后果分析
案例
do
something
案例一、导气筒PFMEA分析
表1:导气筒《工艺潜在失效模式及后果(PFMEA)分析表》
案例一、导气筒PFMEA分析
表1:导气筒《工艺潜在失效模式及后果(PFMEA)分析表》
案例一、导气筒PFMEA分析
表1:导气筒《工艺潜在失效模式及后果(PFMEA)分析表》
案例六
表1:导气筒《工艺潜在失效模式及后果(PFMEA)分析表》
感谢阅读
感谢阅读
案例六
表1:导气筒《工艺潜在失效模式及后果(PFMEA)分析表》
案例六
表1:导气筒《工艺潜在失效模式及后果(PFMEA)分析表》
案例六
表1:导气筒《工艺潜在失效模式及后果(PFMEA)分析表》
案例六
表1:导气筒《工艺潜在失效模式及后果(PFMEA)分析表》
案例六
表1:导气筒《工艺潜在失效模式及后果(PFMEA)分析表》
案例二、摇架工艺 PFMEA分析
表1:导气筒《工艺潜在失效模式及后果(PFMEA)分析表》
案例三、摇架工艺 PFMEA分析
表1:导气筒《工艺潜在失效模式及后果(PFMEA)分析表》
案例四、排壳排链器PFMEA分析
表1:导气筒《工艺潜在失效模式及后果(PFMEA)分析表》
案例五、排壳排链器PFMEA分析
表1:导气筒《工艺潜在失效模式及后果(PFMEA)分析表》
案例六
表1:导气筒《工艺潜在失效模式及后果(PFMEA)分析表》
案例六
表1:导气筒《工艺潜在失效模式及后果(PFMEA)分析表》
案例六
表1:导气筒《工艺潜在失效模式及后果(PFMEA)分析表》
PFMEA案例

30
检查与评估现有的操纵方法
生产部
7﹑
装扣钩
漏装扣钩/扣钩装的位置不正确
线束装入车辆时困难或者安装失败
6
操作员未依规定操作
3
培训操作人员并重点标注图面要求
依照图面规定操作/100%外观检验
2
54
检查与评估现有的操纵方法
生产部
6
扣钩插入的深度不充分
2
培训操作人员并重点标注图面要求
依照图面规定操作/100%外观检验
装线盆入线不正确
3
用正确的装线盆/架
操作员检验
3
36
绝缘破皮,导线断线
端子铆线困难/导通测试不良
4
*裁线机故障/刀片设置太低/刀片用旧;*短路或者开路
5
保护保养/点检
100%检查
2
40
2﹑
压端子
端子变形
铆线端子插入壳仔困难
6
送料爪的变化导致端子经导流板时不正确
2
加大清洁/润滑端子机活动部门的频次
PQC每小时巡检/操作员自检
3
பைடு நூலகம்36
检查与评估现有的操纵方法
工程部
铆线端子插入壳仔后不合格
6
端子在导流板卡住而被硬拉出铆线
2
加大清洁/润滑端子机活动部位的频次
PQC每小时巡检/操作员自检
3
36
检查与评估现有的操纵方法
工程部/品管部/生产部
拉力不够
端子铆线不正确
8
▲
模座/刀座松动
2
保护保养/操纵正确的C/H
每小时拉力测试;巡检
3
48
灯炮装配线束时困难
5
检查图面脏污或者褪色未及时更换
PFMEA分析范例

PFMEA分析范例PFMEA(流程故障模式及影响分析,Process Failure Mode and Effects Analysis)是一种常用的质量管理工具,旨在通过识别和评估潜在的流程故障模式及其可能的影响,以及制定相应的预防控制措施。
下面将针对PFMEA分析进行详细介绍,包括其基本原理、步骤和实施方法。
一、基本原理PFMEA分析的基本原理是通过提前分析和评估流程中可能发生的故障模式及其潜在影响,以及制定相应的控制和预防措施,从而最大程度地减少产品或服务质量问题的发生。
它能够帮助组织识别和解决潜在的质量问题,提高产品或服务的质量可靠性和可用性。
二、步骤1.确定分析范围首先,确定需要进行PFMEA分析的具体流程范围。
该范围应该明确、具体,并确保涵盖了可能影响产品或服务质量的关键环节。
2.建立团队组建一个多学科的团队来执行PFMEA分析工作。
团队成员应包括质量工程师、生产工程师、设计工程师和操作人员等。
3.识别潜在故障模式对于确定的流程范围,团队成员需要开展头脑风暴和讨论,以识别可能的故障模式。
这些故障模式可能包括材料问题、操作失误、设备故障等。
4.评估故障影响对于每个已识别的故障模式,团队成员需要评估其潜在的影响。
影响可以包括产品质量下降、客户投诉增加、安全事故发生等。
通过评估故障影响,确定需要特别关注的故障模式。
5.确定控制措施为了减少故障模式的发生和减轻其影响,团队成员需要制定相应的控制措施。
这些控制措施可以包括质量检查、培训、设备维护等方面的改进。
6.优先级排序根据每个故障模式的潜在影响和控制措施的成本和可行性,对故障模式进行优先级排序。
这有助于组织合理分配资源,以最大限度地提高质量管理的效果。
7.实施控制措施根据优先级排序的结果,组织需要实施确定的控制措施。
这包括在流程中增加质量检查点、开展操作培训、改进设备维护计划等。
8.监控和改进完成控制措施的实施后,需要定期监控其效果,并根据实际情况对措施进行调整和改进。
PFMEA分析范例
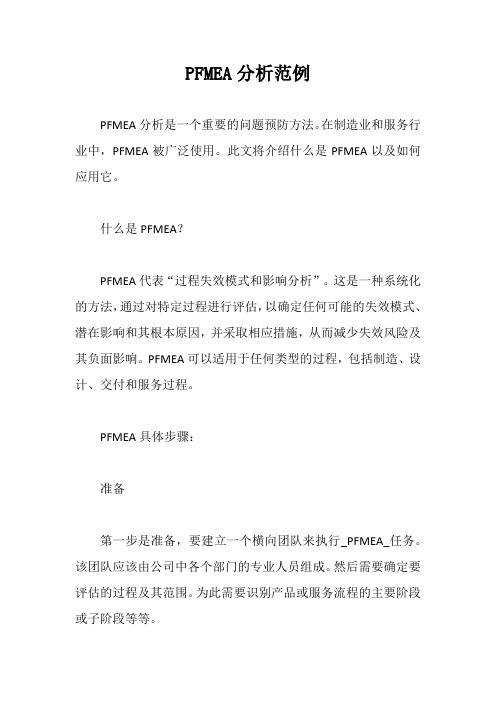
PFMEA分析范例PFMEA分析是一个重要的问题预防方法。
在制造业和服务行业中,PFMEA被广泛使用。
此文将介绍什么是PFMEA以及如何应用它。
什么是PFMEA?PFMEA代表“过程失效模式和影响分析”。
这是一种系统化的方法,通过对特定过程进行评估,以确定任何可能的失效模式、潜在影响和其根本原因,并采取相应措施,从而减少失效风险及其负面影响。
PFMEA可以适用于任何类型的过程,包括制造、设计、交付和服务过程。
PFMEA具体步骤:准备第一步是准备,要建立一个横向团队来执行_PFMEA_任务。
该团队应该由公司中各个部门的专业人员组成。
然后需要确定要评估的过程及其范围。
为此需要识别产品或服务流程的主要阶段或子阶段等等。
评估下一步是评估,评估的目的是按照每个步骤分别分析该步骤中存在的所有失效模式、可能导致这些失效模式的根本原因,评估排除或减轻这些失效的现有控制措施,并放置必要的预防措施。
步骤1:清单采取行动第一步是收集有关过程的所有基本信息。
这包括产品或服务流程图、工艺/操作说明、过程流程图等等。
同时,还需要列出与这个过程相关的所有可能的失效模式。
这些失效模式可以通过历史数据来确定、文献资料、讨论等等。
步骤2:规定过程变量和流程参数在此步骤中定义影响特定过程的所有变量和参数。
例如,所用在特定生产线的材料、设备和人员等等,都必须如实记录。
步骤3:识别失效模式然后,针对每个可能存在的失效模式进行归纳整理,以确定其概率和严重性。
促使这些失效模式的原因也需要被认清。
步骤4:剖析并改进已经存在的控制措施下一步是检查任何现有的防范措施,并判断它们是否足够有效,如果不是,则需要加强或更新现有的控制措施。
步骤5:评估新的控制措施该团队应该定期回顾每个部门的PFMEA工作表,并随时注意重新评估过程以确保没有新的失效模式、变量或参数被漏掉,以及对失效控制所采取的所有行动都是正确和充分的。
注意-评估必须包括所有可能导致失败的原因和根本原因,而不仅仅是现有的故障。
- 1、下载文档前请自行甄别文档内容的完整性,平台不提供额外的编辑、内容补充、找答案等附加服务。
- 2、"仅部分预览"的文档,不可在线预览部分如存在完整性等问题,可反馈申请退款(可完整预览的文档不适用该条件!)。
- 3、如文档侵犯您的权益,请联系客服反馈,我们会尽快为您处理(人工客服工作时间:9:00-18:30)。
型
號:
項
目:
主要參加人員:
BJH-3150AA/BB(??客戶型號)
張志江 謝加云
PWB組裝 陳偉業 李端陽
過程潛在的失效模式及后果分析(PFMEA)
准備者 日 ﹕期
潘儒鋒
﹕ 23/APR/2001
審核者﹕ FM-B003
2.3 貼片電阻(CRES)不良:電
極氧化或發黑;損傷;混料;外 標識與BOM要求不符;尺寸不
產生外觀不良或性能不良
8
符合要求;阻值超差.
供應商的4M1E管理不完善: a.人員培訓考核不完善或沒 作人員變更管理; b.原材料不良或沒作物料變 更管理; c.機器設備(包括儀器)保養 維護不完善或沒作機器設備 (包括儀器)變更管理; d.不按操作程序作業或操作 程序不完善或沒作方法變更 管理; e.溫濕度及5S管理不完善.
根據檢查指引抽查,發現 3 有問題時通知供應商改 5
善.
120
通知供應商改善或要求供應商提供PFMEA 分析.
王剛山/2001/08/20
通知供應商改善或要求供應商提供PFMEA 分析.
5
4
3 60
120
通知供應商改善或要求供應商提供PFMEA 分析.
王剛山/2001/08/20
通知供應商改善或要求供應商提供PFMEA 分析.
版 本﹕
0
第一頁共四頁
工序名稱
潛在的失效模式
潛在的失效后果
嚴 重級 度別 (S)
潛在的失效原因
發
難
R
生 度
現行的控制方法
檢 度
(O)
(D)
P N
建議的措施
責任人及完成時間
措施結果 采取的措施
嚴發難 R 重生檢 P 度度度 N
2.來料檢查
2.1 線路板(PCB)不良:線路
短路;線路斷路;尺寸不符合
要求;爛板(損傷);扭曲變形;
王剛山/2001/08/20
通知供應商改善或要求供應商提供PFMEA 分析.
5
4
3 60
120
通知供應商改善或要求供應商提供PFMEA 分析.
王剛山/2001/08/20
通知供應商改善或要求供應商提供PFMEA 分析.
5
4
3 60
120
通知供應商改善或要求供應商提供PFMEA 分析.
王剛山/2001/08/20
5
4
3 60
2.4 色碼電阻(LRES)不良:引 腳氧化或變形或發黑;損傷; 混料;絲印模糊;外標識與BOM 產生外觀不良或性能不良 8 要求不符;色環與阻值不符; 阻值超差;功率與要求不符.
供應商的4M管理不完善: a.人員培訓考核不完善或沒 作人員變更管理; b.原材料不良或沒作物料變 更管理; c.機器設備(包括儀器)保養 維護不完善或沒作機器設備 (包括儀器)變更管理; d.不按操作程序作業或操作 程序不完善或沒作方法變更 管理;
供應商的4M管理不完善: a.人員培訓考核不完善或沒 作人員變更管理; b.或原材料不良或沒作物料 變更管理; c.或機器設備(包括儀器)保 養維護不完善或沒作機器設 備(包括儀器)變更管理; d.或不按操作程序作業或操 作程序不完善或沒作方法變 更管理;
根據檢查指引抽查,發現 3 有問題時通知供應商改 5
根據檢查指引抽查,發現 3 有問題時通知供應商改 5
善.
供應商的4M管理不完善: a.人員培訓考核不完善或沒 作人員變更管理; b.原材料不良或沒作物料變 更管理; c.機器設備(包括儀器)保養 維護不完善或沒作機器設備 (包括儀器)變更管理; d.不按操作程序作業或操作 程序不完善或沒作方法變更 管理;
善.
供應商的4M管理不完善: a.人員培訓考核不完善或沒 作人員變更管理; b.原材料不良或沒作物料變 更管理; c.機器設備(包括儀器)保養 維護不完善或沒作機器設備 (包括儀器)變更管理; d.不按操作程序作業或操作 程序不完善或沒作方法變更 管理;
根據檢查指引抽查,發現 3 有問題時通知供應商改 5
供應商的4M1E管理不完善: a.人員培訓考核不完善或沒 作人員變更管理; b.原材料不良或沒作物料變 更管理; c.機器設備(包括儀器)保養 維護不完善或沒作機器設備 (包括儀器)變更管理; d.不按操作程序作業或操作 程序不完善或沒作方法變更 管理; e.溫濕度及5S管理不完善.
根據檢查指引抽查,發現 3 有問題時通知供應商改 5
善.
120
通知供應商改善或要求供應商提供PFMEA 分析.
王剛山/2001/08/20
通知供應商改善或要求供應商提供PFMEA 分析.
5
4
3 60
120
通知供應商改善或要求供應商提供PFMEA 分析.
王剛山/2001/08/20
通知供應商改善或要求供應商提供PFMEA 分析.
5
4
3 60
120
通知供應商改善或要求供應商提供PFMEA 分析.
善.
供應商的4M管理不完善: a.人員培訓考核不完善或沒 作人員變更管理; b.或原材料不良或沒作物料 變更管理; c.或機器設備(包括儀器)保 養維護不完善或沒作機器設 備(包括儀器)變更管理; d.或不按操作程序作業或操 作程序不完善或沒作方法變 更管理;
根據檢查指引抽查,發現 3 有問題時通知供應商改 5
根據檢查指引抽查,發現 3 有問題時通知供應商改 5
善.
120
通知供應商改善或要求供應商提供PFMEA 分析.
王剛山/2001/08/20
通知供應商改善或要求供應商提供PFMEA 分析.
5
4
3 60
2.2 貼片電容(CCAP)不良:電 極氧化或發黑;損傷;混料;外 標識與BOM要求不符;尺寸不 產生外觀不良或性能不良 8 符合要求;容值超差;電容漏 電.
產生外觀不良或性能不良
8
尺寸不符合要求;極性標識錯
誤;電氣性能不良.
2.14插座/排插(SOCKET)不 良:引腳氧化或發黑;損傷;混 料;實物絲印內容與BOM要求 不符;外標識與BOM要求不符; 產生外觀不良或性能不良 8 尺寸不符合要求;針腳氧化或 變形或針腳高或針腳低或少 針或多針;電氣性能不良.
通知供應商改善或要求供應商提供PFMEA 分析.
5
4
3 60
2.10瓷片電容(LCAP)不良:引 腳氧化或變形或發黑;損傷; 混料;絲印模糊;絲印內容與 容值不符;外標識與BOM要求 產生外觀不良或性能不良 8 不符;尺寸不符合要求;容值 超差;耐壓值不符要求;電容 漏電.
2.11排阻(NRES)不良:引腳氧 化或發黑;損傷;混料;封裝形 式不符要求;外標識與BOM要 產生外觀不良或性能不良 8 求不符;尺寸不符合要求;排 阻的網絡阻值超差.
供應商的4M1E管理不完善: a.人員培訓考核不完善或沒 作人員變更管理; b.原材料不良或沒作物料變 更管理; c.機器設備(包括儀器)保養 維護不完善或沒作機器設備 (包括儀器)變更管理; d.不按操作程序作業或操作 程序不完善或沒作方法變更 管理; e.溫濕度及5S管理不完善.
供應商的4M1E管理不完善: a.人員培訓考核不完善或沒 作人員變更管理; b.原材料不良或沒作物料變 更管理; c.機器設備(包括儀器)保養 維護不完善或沒作機器設備 (包括儀器)變更管理; d.不按操作程序作業或操作 程序不完善或沒作方法變更 管理; e.溫濕度及5S管理不完善.
混板;上錫PAD有綠油或污漬
或氧化;絲印脫落;綠油脫落;
無功能測試記號;線路欠損; 線路刮花;線路間有銅箔渣;
產生外觀不良或性能不良
8
無V-CUT;V-CUT深或V-CUT淺;
插件孔孔塞或嚴重披峰;補線
路浮起或松動;報廢板未分開
包裝;文字印刷嚴重移位;外
標識與BOM要求不符.
供應商的4M1E管理不完善: a.人員培訓考核不完善或沒 作人員變更管理; b.原材料不良或沒作物料變 更管理; c.機器設備(包括儀器)保養 維護不完善或沒作機器設備 (包括儀器)變更管理; d.不按操作程序作業或操作 程序不完善或沒作方法變更 管理; e.溫濕度及5S管理不完善.
2.12晶振(RESONATOR)不良:
引腳氧化或變形或發黑;損
傷;混料;絲印模糊;外標識與 BOM要求不符;實物絲印內容
產生外觀不良或性能不良
8
與BOM要求不符;尺寸不符合
要求;電氣性能不良.
2.13貼片二極管(DIODE)不
良:焊腳氧化或發黑;損傷;混
料;實物絲印內容與BOM要求 不符;外標識與BOM要求不符;
善.
根據檢查指引抽查,發現 3 有問題時通知供應商改 5
善.
根據檢查指引抽查,發現 3 有問題時通知供應商改 5
善.
根據檢查指引抽查,發現 3 有問題時通知供應商改 5
善.
根據檢查指引抽查,發現 3 有問題時通知供應商改 5
善.
120
通知供應商改善或要求供應商提供PFMEA 分析.
王剛山/2001/08/20
5
4
3 60
120
通知供應商改善或要求供應商提供PFMEA 分析.
王剛山/2001/08/20
通知供應商改善或要求供應商提供PFMEA 分析.
5
4
3 60
120
通知供應商改善或要求供應商提供PFMEA 分析.
王剛山/2001/08/20
通知供應商改善或要求供應商提供PFMEA 分析.
5
4
3 60
2.15貼片電解電容(SMD ECAP)不良:電極氧化或發黑; 損傷(壓痕);混料;編帶反向. 絲印模糊;實物絲印內容與 產生外觀不良或性能不良 8 BOM要求不符;外標識與BOM要 求不符;尺寸不符合要求;容 值超差;電容漏電.