管道无损检测方案
管道无损检测常用方法

管道无损检测常用方法全文共四篇示例,供读者参考第一篇示例:管道无损检测是指在不影响管道结构完整性的情况下,通过各种检测方法对管道进行检测,以判断管道的运行状态、安全性和维护需求。
管道无损检测是保障管道运行安全的重要手段,可以帮助管道运营单位及时发现管道的隐患和缺陷,有效预防事故发生。
目前,管道无损检测常用的方法包括超声波检测、磁粉检测、涡流检测、射线检测等多种技术手段,下面将分别介绍这些方法的原理、优缺点及应用范围。
超声波检测是一种常用的管道无损检测方法,通过发送和接收超声波信号来检测管道内部的缺陷和损伤。
超声波检测原理是利用声波在介质中传播的特性来识别管道内部的缺陷,不仅可以检测管道的腐蚀、裂纹等缺陷,还能测量管道的壁厚、管壁之间的结合情况等参数。
超声波检测具有检测精度高、适用范围广、操作简便等优点,但是对管道表面质量要求较高,且只能检测到管道表面下方一定深度范围内的缺陷。
磁粉检测是一种利用铁磁性粉末对管道表面进行覆盖,通过施加磁场来检测管道表面裂纹和缺陷的方法。
磁粉检测原理是利用磁铁吸引磁粉末,形成磁粉层,并通过观察磁粉层的变化来判断管道表面是否存在裂纹或缺陷。
磁粉检测方法适用于检测管道表面裂纹、焊缝质量和管道连接情况等问题,但是对表面处理要求较高,且只能检测到管道表面的缺陷。
涡流检测是一种利用感应电流在导体内部引起涡流现象来检测管道内部缺陷的方法。
涡流检测原理是通过在管道表面感应电磁场,当管道表面存在缺陷时,感应电流会发生变化,通过检测感应电流的变化来判断管道内部是否存在缺陷。
涡流检测方法适用于检测管道表面的裂纹、腐蚀和管壁材料变化等问题,具有灵敏度高、速度快、无需接触等优点。
射线检测是一种利用射线穿透物体后被不同组织结构吸收、散射或透射的特性来检测管道内部缺陷的方法。
射线检测原理是通过将射线源对准管道进行照射,通过检测射线在管道内部的吸收情况来判断管道内部是否存在缺陷。
射线检测方法适用于检测管道内部的腐蚀、结构松动、异物等问题,具有检测范围广、准确性高等优点,但是需要专业设备和专业人员操作。
管道无损检测施工方案
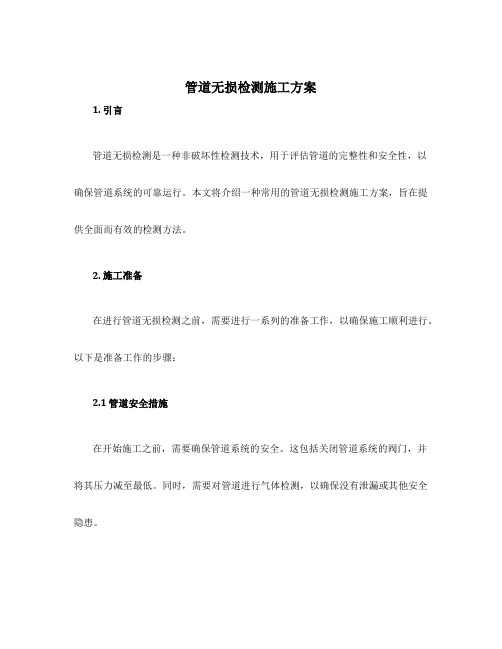
管道无损检测施工方案1. 引言管道无损检测是一种非破坏性检测技术,用于评估管道的完整性和安全性,以确保管道系统的可靠运行。
本文将介绍一种常用的管道无损检测施工方案,旨在提供全面而有效的检测方法。
2. 施工准备在进行管道无损检测之前,需要进行一系列的准备工作,以确保施工顺利进行。
以下是准备工作的步骤:2.1 管道安全措施在开始施工之前,需要确保管道系统的安全。
这包括关闭管道系统的阀门,并将其压力减至最低。
同时,需要对管道进行气体检测,以确保没有泄漏或其他安全隐患。
2.2 设备准备进行管道无损检测需要使用专业的设备。
在施工前,需要检查无损检测设备的工作状态,并确保其正常运行。
同时,还需要准备适当的探头和传感器,以便对管道进行准确的检测。
2.3 人员培训对于参与管道无损检测的人员,需要进行充分的培训。
他们需要了解无损检测的原理、操作步骤和安全注意事项。
只有经过培训的人员才能进行管道无损检测工作,以确保施工的准确性和安全性。
3. 施工步骤一旦准备工作完成,就可以开始进行管道无损检测的施工。
下面是施工步骤的详细说明:3.1 数据采集首先,需要使用无损检测仪器对管道进行数据采集。
根据无损检测的原理,可以选择合适的检测方法和技术。
常用的无损检测方法包括超声波检测、磁粉检测、液体渗透检测等。
通过这些方法,可以获取管道的各项数据,例如管道的壁厚、裂纹等。
3.2 数据处理采集到的数据需要进行处理和分析,以获得准确的检测结果。
数据处理通常包括去噪、滤波、信号增强等步骤。
通过这些处理,可以提高数据的质量和可靠性,并准确评估管道的健康状况。
3.3 结果评估根据处理后的数据,可以对管道的健康状况进行评估。
评估结果可以分为正常和异常两种情况。
对于异常情况,还需要进一步分析和确认问题的具体原因和严重程度。
3.4 生成报告最后,根据评估结果生成一份管道无损检测报告。
报告应包括管道的基本信息、检测方法、数据分析结果、问题描述和建议等内容。
管道无损检测方案

管道无损检测方案首先是准备工作。
在进行无损检测之前,需要对管道进行一系列准备工作。
首先是确定检测范围和目的,确定需要检测的管道段和检测方法;然后对管道进行清洗和除锈处理,以确保检测的准确性和可靠性;最后,需要准备相应的无损检测设备和材料。
其次是检测方法的选择。
根据管道的特点和需要检测的缺陷类型,选择适当的无损检测方法。
常见的无损检测方法包括超声波检测、射线检测、涡流检测、磁粉检测等。
每种方法适用于不同类型的管道缺陷,有其优缺点和适用范围。
在选择检测方法时,需要综合考虑管道材料、管道尺寸、缺陷类型和检测目的等因素。
然后是检测设备的配置和校准。
根据选择的检测方法,配置相应的无损检测设备。
无损检测设备通常包括检测仪器、传感器、探头、影像采集设备等。
这些设备需要进行校准和调试,以确保其测量和检测结果的准确性和可靠性。
校准包括对设备的线性度、分辨率、灵敏度等参数进行检查和调整。
接下来是进行管道的无损检测。
在进行无损检测过程中,需要严格按照操作规程和流程进行,确保检测结果的准确性和可靠性。
根据选择的检测方法,使用相应的设备和材料进行检测。
例如,在超声波检测中,通过发射和接收超声波波束来检测管道中的缺陷;在射线检测中,通过照射射线并通过感应器接收射线来检测管道中的缺陷。
在检测过程中,需要对检测数据进行记录和分析,以评估管道的质量和安全性能。
最后是检测结果的评估和处理。
在完成管道的无损检测后,需要对检测结果进行评估和处理。
根据检测的数据和缺陷的类型、大小等信息,对管道的质量和安全性能进行评估。
对于发现的缺陷,需要进行分析和判断其对管道的影响和危害程度。
如果存在严重的缺陷或安全隐患,需要及时采取相应的修复措施,以防止事故的发生。
综上所述,一个典型的管道无损检测方案包括准备工作、检测方法选择、检测设备的配置和校准、无损检测过程、检测结果的评估和处理等环节。
通过科学合理地实施无损检测,可以提高管道的质量和安全性能,预防事故的发生。
蒸汽、冷凝水管道无损检测专项方案

蒸汽、冷凝水管道装工程无损检测施工方案批准:审核:编制:委托单位:施工单位:1. 总则1.1本方案适用于现架空蒸汽管道、冷凝水管道安装工程管道对接焊缝的无损检测工作,检测类型有射线探伤、磁粉探伤,本方案依据设计图纸及有关规程、规定标准执行。
1.2 编制依据1.2.1 设计图纸要求1.2.2 《工业金属管道工程施工及验收规范》GB50184-20111.2.3 《承压设备无损检测》NB/T47013-20151.2.3 《承压设备焊接工艺评定》NB/T47014-20111.2.4 《承压设备用焊接材料订货技术条件》NB/T47018-20171.2.5 《设备无损检测第2部分射线检测》NB/T47013.2-2015中的AB级1.2.6《设备无损检测第4部分磁粉检测》NB/T47013.4-2015 1.3 探伤方法与探伤时机1.3.1所有对接焊缝应在焊接或返修完成24小时以后进行100%射线探伤。
1.3.5所有对接焊缝应在焊接或返修完成24小时以后进行100%超声波探伤。
1.4. 人员资格1.4.1 操作人员应在Ⅱ级或Ⅲ级人员的指导下进行相应的探伤操作和记录。
1.4.2 Ⅱ级或Ⅲ级人员有权评定检测结果并签发检测报告。
1.5 表面质量焊缝区域内应清除焊疤、焊渣、飞溅,并经检验人员检查合格方可探伤;射线探伤时,焊缝表面的不规则状态不应影响焊缝质量的评定,否则应进行修整。
磁粉探伤时,对所探伤的试件进行预清洗,将影响探伤的试件表面油脂及其他可能影响磁粉正常分布、影响磁粉堆积物的密集度、特性以及清晰度的杂质处理干净。
1.6 安全防护1.6.1 进入厂区的施工人员必须经过安全教育。
1.6.2 进入厂区严禁动用与本岗位无关的任何设备、仪表、仪器。
1.6.3 检测设备的各种联线表面应完好,工作时仪器必须可靠接地。
1.6.4 进入厂区必须戴好安全帽,地面2.0米以上应戴好安全带,并应检查脚手架及跳板是否牢固,防止高空坠落事故。
天然气管道无损检测方法

天然气管道无损检测方法天然气作为一种重要的能源资源,其输送管道的安全运行对于社会经济的发展至关重要。
然而,由于管道的长期使用和外界环境的影响,管道壁面可能会出现腐蚀、裂纹等缺陷,给管道的安全运行带来潜在风险。
因此,对天然气管道进行无损检测显得尤为重要和必要。
天然气管道无损检测是利用各种无损检测技术手段对管道进行检测的一种方法。
它通过对管道表面或内部进行探测和分析,可以实时监测管道的健康状况,及时发现和判定管道的缺陷情况,为管道的安全运行提供科学依据。
在天然气管道无损检测中,常用的技术手段包括超声波检测、磁粉检测、涡流检测、射线检测等。
超声波检测是一种利用超声波在材料中传播的特性来检测管道缺陷的方法。
通过超声波的发射和接收,可以获取管道内部的声波信号,并通过分析信号的强度、传播时间等参数,判断管道是否存在裂纹、腐蚀等缺陷。
磁粉检测是一种利用磁性粉末在管道表面形成磁纹来检测管道缺陷的方法。
通过在管道表面涂覆磁性粉末,当磁粉受到管道表面的磁场影响时,会形成磁纹,通过观察磁纹的分布和形态,可以确定管道是否存在缺陷。
涡流检测是一种利用涡流感应原理来检测管道缺陷的方法。
通过在管道表面放置一个交变电磁场源,当管道表面存在缺陷时,缺陷处会形成涡流,通过检测涡流的强度和分布,可以判断管道是否存在缺陷。
射线检测是一种利用射线在管道内部传播的特性来检测管道缺陷的方法。
通过在管道内部放射射线,并在管道外部接收射线信号,通过分析射线信号的强度、衰减等参数,可以确定管道内部是否存在裂纹、腐蚀等缺陷。
除了以上常用的无损检测技术,还有一些新兴的技术被应用于天然气管道的无损检测中,如红外热像检测、激光扫描检测等。
这些新技术通过不同的原理和手段,可以更加准确和全面地检测管道的缺陷情况。
在进行天然气管道无损检测时,需要注意以下几点。
首先,无损检测操作人员需要经过专门培训,熟悉检测仪器的使用和操作流程,确保检测结果的准确性和可靠性。
其次,无损检测需要对管道进行全面覆盖,包括管道的表面和内部,以确保发现潜在缺陷。
管道无损检测施工专项方案
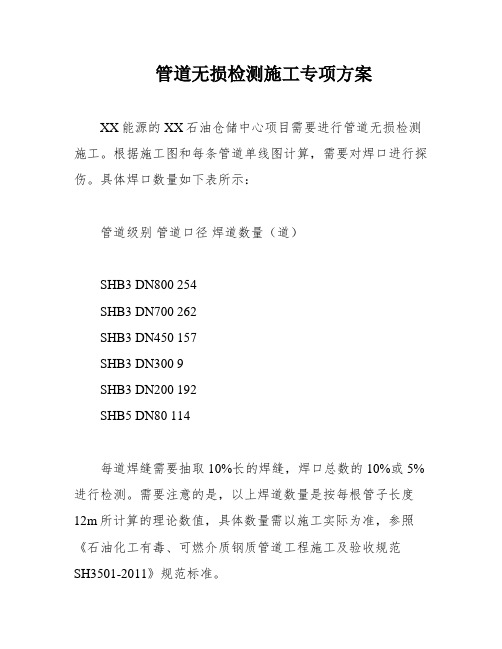
管道无损检测施工专项方案XX能源的XX石油仓储中心项目需要进行管道无损检测施工。
根据施工图和每条管道单线图计算,需要对焊口进行探伤。
具体焊口数量如下表所示:管道级别管道口径焊道数量(道)SHB3 DN800 254SHB3 DN700 262SHB3 DN450 157SHB3 DN300 9SHB3 DN200 192SHB5 DN80 114每道焊缝需要抽取10%长的焊缝,焊口总数的10%或5%进行检测。
需要注意的是,以上焊道数量是按每根管子长度12m所计算的理论数值,具体数量需以施工实际为准,参照《石油化工有毒、可燃介质钢质管道工程施工及验收规范SH3501-2011》规范标准。
该工程的特点在于,为了不影响施工进度和交叉施工作业人员安全,探伤作业将在晚上休息时间进行。
由于罐区施工的管道处在地面上,拍片作业比较方便。
然而,探伤位置相对不固定,探伤机有一定的重量,且场地凹凸不平,施工环境复杂,各单位的施工工期都比较紧张,因此安全将是整个施工中最大最严重的一个控制环节。
为了保证施工质量和安全,选用XXX作为无损检测机构。
该公司施工资质符合要求并专门从事该行业的施工,施工经验丰富,施工能力一流。
无损检测工作选派应由按《特种设备无损检测人员考核与监督管理规则》考试合格的三名经验丰富的具备无损检测Ⅱ级资格的人员担任。
最后需要注意文件控制,确保施工过程中的文件管理规范。
2.2.1 为了符合有关标准、规范和施工技术文件的要求,应结合现场工作条件编制无损检测工艺卡。
Ⅱ级或Ⅲ级以上的人员应编制无损检测工艺卡,而无损检测责任工程师则应审批工艺卡。
2.2.2 无损检测记录和报告应严格遵守公司和检测中心的相关规定。
2.2.3 无损检测资料应妥善保存,并在工程竣工后统一交给业主归档保管。
归档资料包括:探伤委托单、检测方案、工艺卡、射线底片、探伤记录、探伤报告和探伤位置示意图等。
2.3 施工工序2.3.1 对于焊口的检测,DN500以下(不含DN500)按照业主和监理现场抽检焊口选定。
管道无损检测服务计划方案

管道无损检测服务计划方案管道无损检测服务计划方案一、背景说明随着工业化的进程,管道在汽车、石油化工等行业中的应用越来越广泛。
然而,由于管道在运输、安装等过程中容易受到挤压、磨损等损坏,从而导致泄漏、爆炸等事故的发生,对生命财产造成了威胁。
为了确保管道运行的安全稳定,无损检测技术被广泛应用于管道的检测与评估。
本方案旨在为客户提供一套完整的管道无损检测服务计划。
二、服务内容1. 管道无损检测技术咨询服务:为客户提供咨询服务,包括无损检测技术的原理、应用范围、设备选型、操作指导等方面的内容。
根据客户的需求和实际情况,提供定制化的解决方案。
2. 管道无损检测设备租赁服务:提供各类管道无损检测设备的租赁服务,包括超声波检测设备、磁粉检测设备、涡流检测设备等。
设备租赁周期灵活,可根据客户需要提供长期或短期的租赁服务。
3. 管道无损检测服务:提供管道无损检测服务,包括超声波检测、磁粉检测、涡流检测等。
根据管道的具体情况和客户需求,选择合适的检测技术进行检测。
通过无损检测,对管道进行全面评估,及时发现管道的缺陷和隐患,提供有效的维修建议。
4. 管道无损检测人员培训服务:提供管道无损检测人员培训服务,包括超声波检测技术、磁粉检测技术、涡流检测技术等的培训。
培训内容包括理论知识和实际操作的培训,培训周期和内容可根据客户需求进行定制。
三、服务流程1. 需求评估:客户提出无损检测的需求,我们将与客户进行沟通,了解其具体需求和管道的情况。
根据评估结果,制定相应的无损检测方案。
2. 设备租赁或购买:根据客户需求,提供相应的管道无损检测设备租赁或购买服务。
设备将配备操作手册和使用指导,确保客户能够正确使用设备。
3. 检测服务执行:根据制定的无损检测方案,我们将派遣专业的无损检测人员到客户现场进行管道的无损检测。
检测过程中,我们将严格按照检测流程进行操作,并记录检测数据和结果。
4. 报告生成和分析:检测完成后,我们将生成检测报告,并进行相应的数据分析和评估。
管道无损检测技术方案
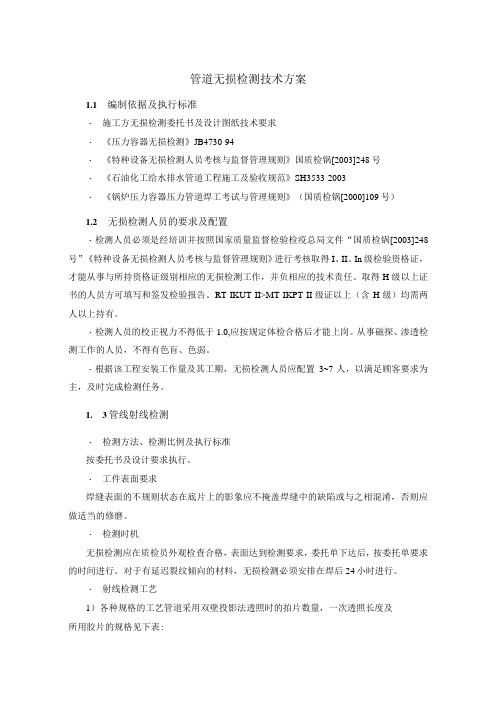
管道无损检测技术方案1.1编制依据及执行标准・施工方无损检测委托书及设计图纸技术要求・《压力容器无损检测》JB4730-94・《特种设备无损检测人员考核与监督管理规则》国质检锅[2003]248号・《石油化工给水排水管道工程施工及验收规范》SH3533-2003・《锅炉压力容器压力管道焊工考试与管理规则》(国质检锅[2000]109号)1.2无损检测人员的要求及配置・检测人员必须是经培训并按照国家质量监督检验检疫总局文件“国质检锅[2003]248号”《特种设备无损检测人员考核与监督管理规则》进行考核取得I、II、In级检验资格证,才能从事与所持资格证级别相应的无损检测工作,并负相应的技术责任。
取得H级以上证书的人员方可填写和签发检验报告。
RT-IKUT-II>MT-IKPT-II级证以上(含H级)均需两人以上持有。
・检测人员的校正视力不得低于1.0,应按规定体检合格后才能上岗。
从事磁探、渗透检测工作的人员,不得有色盲、色弱。
・根据该工程安装工作量及其工期,无损检测人员应配置3~7人,以满足顾客要求为主,及时完成检测任务。
1.3管线射线检测・检测方法、检测比例及执行标准按委托书及设计要求执行。
・工件表面要求焊缝表面的不规则状态在底片上的影象应不掩盖焊缝中的缺陷或与之相混淆,否则应做适当的修磨。
・检测时机无损检测应在质检员外观检查合格,表面达到检测要求,委托单下达后,按委托单要求的时间进行。
对于有延迟裂纹倾向的材料,无损检测必须安排在焊后24小时进行。
・射线检测工艺1)各种规格的工艺管道采用双壁投影法透照时的拍片数量,一次透照长度及所用胶片的规格见下表:a)外径≤①89rnm的钢管对接焊缝采用双壁双投影法透照两张片,两次透照方向相互垂直。
上下焊缝的影象在底片上呈椭圆形显示,焊缝投影间距以3~10mm为宜,最大间距不超过15mm ob)只有当上下两焊缝椭圆显示有困难时,才能做垂直透照,垂直透照可以适当提高管电压。
工艺管道无损检测方案
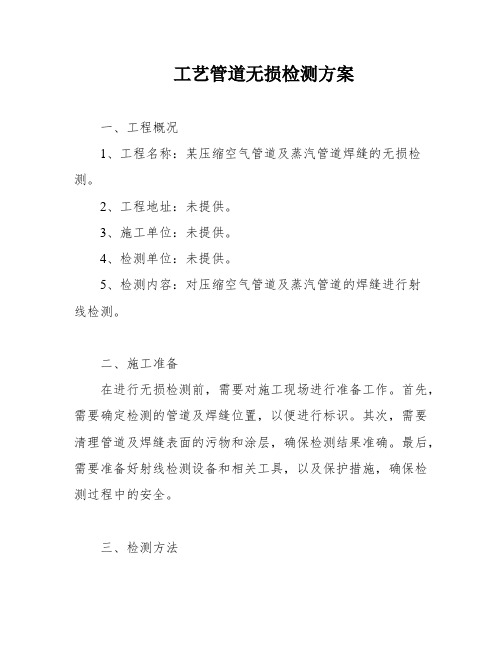
工艺管道无损检测方案一、工程概况1、工程名称:某压缩空气管道及蒸汽管道焊缝的无损检测。
2、工程地址:未提供。
3、施工单位:未提供。
4、检测单位:未提供。
5、检测内容:对压缩空气管道及蒸汽管道的焊缝进行射线检测。
二、施工准备在进行无损检测前,需要对施工现场进行准备工作。
首先,需要确定检测的管道及焊缝位置,以便进行标识。
其次,需要清理管道及焊缝表面的污物和涂层,确保检测结果准确。
最后,需要准备好射线检测设备和相关工具,以及保护措施,确保检测过程中的安全。
三、检测方法针对压缩空气管道及蒸汽管道的焊缝,采用射线检测方法进行无损检测。
在检测过程中,使用射线探测器对焊缝进行扫描,通过对射线照射后的影像进行分析,确定焊缝的质量和存在的缺陷。
四、检测部位本次无损检测的部位为压缩空气管道及蒸汽管道的焊缝。
需要对这些部位进行标识,以便进行检测。
五、检测标识在进行无损检测前,需要对检测部位进行标识。
标识应该清晰明确,以便进行检测。
六、检测时机本次无损检测的时机为在压缩空气管道及蒸汽管道焊接完成后,但在投入使用之前进行。
七、无损检测工艺方案针对压缩空气管道及蒸汽管道的焊缝,采用射线检测方法进行无损检测。
检测过程中,应该按照以下步骤进行:1.对检测部位进行标识。
2.清理管道及焊缝表面的污物和涂层。
3.进行射线检测,使用射线探测器对焊缝进行扫描。
4.对射线照射后的影像进行分析,确定焊缝的质量和存在的缺陷。
5.根据检测结果,对存在缺陷的部位进行修补或更换。
八、无损检测时的安全措施在进行无损检测时,需要采取以下安全措施:1.在检测现场设置警示标志,提醒人员注意安全。
2.检测人员应该佩戴防护服、手套、防护眼镜等个人防护用品。
3.射线检测设备应该经过专业人员的操作和维护,确保安全可靠。
4.检测过程中,应该保持现场整洁,防止发生意外事故。
5.2、本工程的检测执行标准包括设计图纸要求、设计变更以及JB/T4730-2005《承压设备无损检测》和《现场设备、工业管道焊接工程施工及验收规范》GB-98.6、本工程的质量标准要求达到总承包合同中的合格标准。
管道无损检测常用方法

管道无损检测常用方法
管道无损检测是指在不破坏管道结构的情况下,通过一系列的检测方法来评估管道的健康状况。
常用的方法包括:
1. 超声波检测,利用超声波在材料中传播的特性,通过探头和接收器来检测管道内部的缺陷、腐蚀、厚度变化等情况。
这种方法适用于各种材料的管道,包括金属和非金属材料。
2. X射线检测,通过使用X射线穿透管道材料,检测管道内部的缺陷、焊接质量、管壁厚度等情况。
这种方法对于金属管道的检测效果较好,但需要专业设备和操作人员,且对辐射安全有一定要求。
3. 磁粉检测,在管道表面涂覆磁粉,通过施加磁场,可以检测管道表面和近表面的裂纹、疲劳等缺陷。
这种方法适用于铁磁性材料的管道。
4. 声发射检测,通过监测管道结构在加载过程中产生的微小声波信号,来识别管道内部的裂纹、腐蚀、疲劳等问题。
这种方法可以实时监测管道的健康状况,对于高压管道尤为重要。
5. 磁致伸缩检测,利用管道材料在磁场中的磁致伸缩效应,来检测管道内部的应力、疲劳、腐蚀等情况。
这种方法对于金属管道的应力评估较为有效。
以上是常用的管道无损检测方法,每种方法都有其适用的材料和场景,综合使用这些方法可以全面评估管道的健康状况,确保管道运行安全。
油气管道无损检测技术

油气管道无损检测技术管道作为大量输送石油、气体等能源的安全经济的运输手段,在世界各地得到了广泛应用,为了保障油气管道安全运行,延长使用寿命,应对其定期进行检测,以便发现问题,采取措施。
一、管道元件的无损检测(一)管道用钢管的检测埋地管道用管材包括无缝钢管和焊接钢管。
对于无缝钢管采用液浸法或接触法超声波检测主要来发现纵向缺陷。
液浸法使用线聚焦或点聚焦探头,接触法使用与钢管表面吻合良好的斜探头或聚焦斜探头。
所有类型的金属管材都可采用涡流方法来检测它们的表面和近表面缺陷。
对于焊接钢管,焊缝采用射线抽查或100 %检测,对于100 %检测,通常采用X射线实时成像检测技术。
(二)管道用螺栓件对于直径> 50 mm 的钢螺栓件需采用超声来检测螺栓杆内存在的冶金缺陷。
超声检测采用单晶直探头或双晶直探头的纵波检测方法。
二、管道施工过程中的无损检测(一)各种无损检测方法在焊管生产中的配置国外在生产中常规的主要无损检测配置如下图一中的A、B、C、E、F、G、H工序。
我国目前生产中的检测配置主要岗位如下图中的A、C、D、E、F、G、H工序。
图一大口径埋弧焊街钢管生产无损检测岗位配置(二)超声检测全自动超声检测技术目前在国外已被大量应用于长输管线的环焊缝检测,与传统手动超声检测和射线检测相比,其在检测速度、缺陷定量准确性、减少环境污染和降低作业强度等方面有着明显的优越性。
全自动相控阵超声检测系统采用区域划分方法,将焊缝分成垂直方向上的若干个区,再由电子系统控制相控阵探头对其进行分区扫查,检测结果以双门带状图的形式显示,再辅以TOFD (衍射时差法)和B扫描功能,对焊缝内部存在的缺陷进行分析和判断。
全自动超声波现场检测时情况复杂,尤其是轨道位置安放的精确度、试块的校准效果、现场扫查温度等因素会对检测结果产生强烈的影响,因此对检测结果的评判需要对多方面情况进行综合考虑,收集各种信息,才能减少失误。
(三)射线检测射线检测一般使用X 射线周向曝光机或γ射线源,用管道内爬行器将射线源送入管道内部环焊缝的位置,从外部采用胶片一次曝光,但胶片处理和评价需要较长的时间,往往影响管道施工的进度,因此,近年来国内外均开发出专门用于管道环焊缝检测的X 射线实时成像检测设备。
管道无损检测方案

管道无损检测方案导言管道是现代工业生产中不可或缺的重要组成部分,对于保障工业生产的安全和稳定起着至关重要的作用。
然而,由于长时间的使用、环境因素、材料老化等原因,管道存在着各种潜在的隐患和缺陷,如腐蚀、裂纹、疲劳等问题。
因此,对管道进行无损检测是非常必要和重要的,本文将介绍一种管道无损检测方案。
一、背景管道无损检测是利用一系列无损检测技术手段对管道进行检测和评估,以发现管道内部的缺陷和隐患,为管道维修和保养提供依据。
传统的管道检测方法主要依赖于人工目视检查和使用有损检测工具进行检测,这样的方法存在着效率低、难以覆盖全面和对管道造成二次损伤等问题。
因此,研发一套高效、精准、无损的管道检测方案势在必行。
二、无损检测技术目前,应用于管道无损检测的技术包括磁粉检测、超声波检测、涡流检测、射线检测等。
这些技术各有优劣,可以根据实际需求和管道特点选择合适的技术进行检测。
1. 磁粉检测磁粉检测是一种通过施加外界磁场并覆盖磁粉颗粒的方法来检测管道表面和亚表面缺陷的技术。
通过观察磁粉在管道表面产生的磁粉覆盖线或磁粉粗集的形态,可以判断出管道的缺陷位置和性质。
2. 超声波检测超声波检测是一种通过将超声波传至管道内部,并接收返回的超声波信号来检测管道内部缺陷和问题的技术。
通过超声波在管道内部的传播速度和回波信号的特征,可以判断出管道的问题类型和位置。
3. 涡流检测涡流检测是一种利用涡流感应的原理来检测管道表面和亚表面缺陷的技术。
通过在管道表面通过涡流传导引起的电磁感应现象,可以获取到管道表面缺陷的信息和位置。
4. 射线检测射线检测是一种利用射线穿透物体并通过探测器接收射线经过后的削弱信号来检测管道内部缺陷的技术。
通过射线的吸收和散射情况,可以判断出管道内部的问题和位置。
三、管道无损检测方案基于以上不同的无损检测技术,我们可以综合运用多种技术手段来进行管道无损检测,提供一个全面而准确的评估结果。
首先,可以利用超声波检测技术对管道进行全面扫描,发现管道内的问题和缺陷。
工艺管道无损检测方案
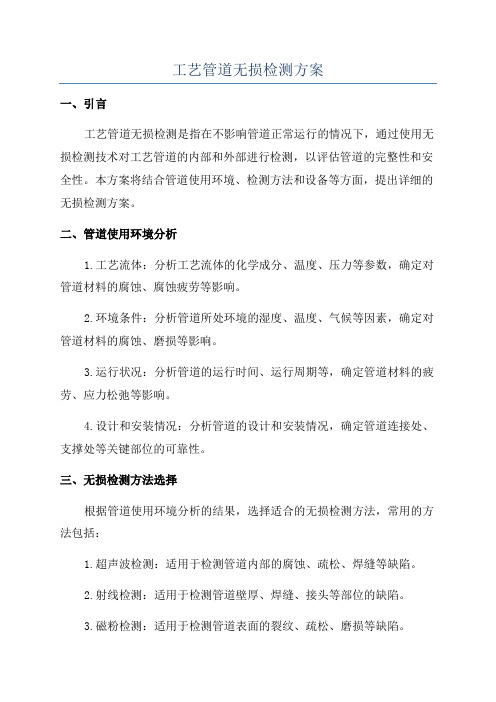
工艺管道无损检测方案一、引言工艺管道无损检测是指在不影响管道正常运行的情况下,通过使用无损检测技术对工艺管道的内部和外部进行检测,以评估管道的完整性和安全性。
本方案将结合管道使用环境、检测方法和设备等方面,提出详细的无损检测方案。
二、管道使用环境分析1.工艺流体:分析工艺流体的化学成分、温度、压力等参数,确定对管道材料的腐蚀、腐蚀疲劳等影响。
2.环境条件:分析管道所处环境的湿度、温度、气候等因素,确定对管道材料的腐蚀、磨损等影响。
3.运行状况:分析管道的运行时间、运行周期等,确定管道材料的疲劳、应力松弛等影响。
4.设计和安装情况:分析管道的设计和安装情况,确定管道连接处、支撑处等关键部位的可靠性。
三、无损检测方法选择根据管道使用环境分析的结果,选择适合的无损检测方法,常用的方法包括:1.超声波检测:适用于检测管道内部的腐蚀、疏松、焊缝等缺陷。
2.射线检测:适用于检测管道壁厚、焊缝、接头等部位的缺陷。
3.磁粉检测:适用于检测管道表面的裂纹、疏松、磨损等缺陷。
4.温度检测:适用于检测管道温度的变化,判断管道内部流体是否异常。
5.声发射检测:适用于检测管道内部材料的应力松弛、裂纹扩展等情况。
四、无损检测设备选择根据无损检测方法的选择,选取合适的无损检测设备,包括:1.超声波检测仪:用于超声波检测方法的管道内部缺陷检测。
2.射线检测仪:用于射线检测方法的管道缺陷检测。
3.磁粉检测仪:用于磁粉检测方法的管道表面缺陷检测。
4.温度计:用于管道温度检测,判断管道内部流体是否异常。
5.声发射探头:用于声发射检测方法的管道内部材料异常情况检测。
五、无损检测方案实施1.管道准备:对待检管道进行清洗和除锈处理,确保管道表面干净平整。
2.检测计划制定:根据管道的结构和使用情况,制定详细的检测计划,包括检测部位、方法、设备等。
3.检测操作:根据检测计划进行无损检测操作,将检测结果记录在检测报告中。
4.检测结果评估:对检测结果进行评估和分析,确定管道的完整性和安全性。
某天然气高压管道无损检测技术方案

某天然气高压管道无损检测技术方案随着石油和天然气行业的不断发展,高压管道的安全运行成为了一个重要的问题。
为了及时发现管道存在的缺陷和隐患,提高管道的使用寿命和安全性,有效的无损检测技术方案是必不可少的。
本文将介绍一种针对高压管道的无损检测技术方案。
一、方案概述该方案主要基于超声波无损检测技术,综合考虑到管道材料、压力、温度等因素,并结合专业的检测仪器和设备,实现对高压管道的快速、准确的无损检测。
二、方案具体内容1.管道准备工作在进行无损检测前,需要对高压管道进行准备工作。
首先,清除管道表面的污垢和涂层,确保无损检测仪器能够准确地接触到管道表面。
其次,检查管道的支撑和固定情况,确保管道不会因为振动或其他因素而影响检测结果。
2.超声波无损检测超声波无损检测是一种通过超声波传播和反射来检测管道内部缺陷的技术。
在管道表面涂覆特殊的耦合剂,然后使用超声波探头进行检测。
通过超声波信号的传入和反射,可以获得管道内部的缺陷情况。
3.数据分析和处理在进行超声波检测时,检测仪器会输出一系列的波形图和数字信号。
这些数据需要进行分析和处理,以得出管道内部缺陷的具体信息。
通过使用专业的无损检测软件,可以对数据进行滤波、放大、峰值检测等处理,同时可与标准、数据库对比,进一步判定管道内部的缺陷是否达到限定的安全标准。
4.缺陷评估和建议针对检测结果,可以对管道内部的缺陷进行评估和判定。
通过分析缺陷的尺寸、类型和位置,可以评估缺陷对管道的安全性产生的影响。
根据评估结果,还可以提出相应的处理建议,如修复或更换。
5.检测报告和记录对于每次的无损检测,需要编制相应的检测报告和记录。
报告中应包括管道的基本信息、检测结果、缺陷评估、处理建议等内容,以便于后续的跟踪和管理。
三、方案优势1.高效准确:超声波无损检测技术可以在短时间内对大面积管道进行检测,快速获得管道内部缺陷信息,不需要停产或需要破坏管道的情况下进行检测。
2.可靠性强:超声波无损检测技术准确度高,可以检测到小尺寸的缺陷,并且能够对管道的未来安全性进行预测,有效降低了管道事故的发生概率。
管道无损检测方案

1. 概述本工程各种管道约 15000 米,分不锈钢 SS304、SS316、碳钢、合金钢、PP/GRP、CS+PTFE 等多种材质。
根据工艺、技术的不同要求,现场需拍片约40000 张,硬度试验 900 点。
本方案编制参考了招标文件中技术说明 S-00-1540-002 以及美国 ASME 标准(1986)。
2.检验项目2. 1 射线探伤⑴ 射线探伤的检查比例,按照 JGC 在“技术说明”中的要求执行。
⑵ 射线探伤的检查比例应符合设计要求及有关技术条件的规定。
⑶ 要求 100%检查的管道应逐个焊口整圈 100%检查,确保不漏检。
⑷ 要求 10%抽检的管道应按相应焊工的相应焊缝按 10%比例整圈检查。
⑸ 管径≤3″厚度δ ≤7.62mm 采用双壁双影椭圆透照,每一个焊口间隔 90°各拍一张,共两张。
⑹ 管径=2″厚度≥8.74mm;管径=2-1/2″厚度≥9.53mm;管径=3″厚度≥11—13mm 时应采用双壁单影分段透照,拍摄四张。
⑺ 管径≥4″采用双壁单影或者单壁单影透照,每一个管口至少拍摄四张,T 各种规格管道焊缝的拍摄数量应与现场测试检查程序中的要求一致。
⑻胶片选用FUJI“100”型。
采用的铅箔增感屏,当采用 X 射线探伤时,前屏厚 0.03mm,后屏厚 0.1mm;当采用γ 射线探伤时,先后屏厚均为 0.1mm。
⑼ 10″以下包括10″的管道探伤时,胶片规格为10″×4″;12″-72″的管道探伤时,胶片规格为12″×3-1/3″。
有特殊要求的按要求执行。
⑽ 所摄底片应无划伤,水迹,伪缺陷,当采用 X 射线时 AB 级的底片黑度 D=1.8-3.5,当采用γ 射线时底片黑度 D=2.0-3.5,底片象质指数均应满足不同厚度的要求。
底片上标识应齐全(包括管段号,焊口号,焊工号,拍摄日期,返修次数)。
⑾ 用 Ir192γ射线探伤时,应加装准直器,以减少散射线对底片像质的影响。
管道无损检测方案
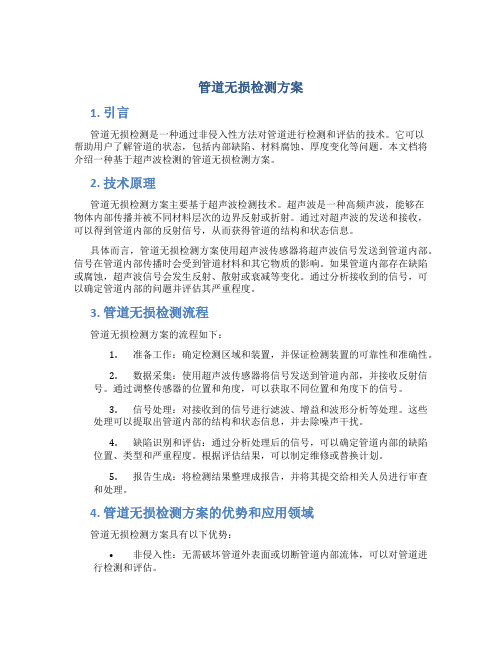
管道无损检测方案1. 引言管道无损检测是一种通过非侵入性方法对管道进行检测和评估的技术。
它可以帮助用户了解管道的状态,包括内部缺陷、材料腐蚀、厚度变化等问题。
本文档将介绍一种基于超声波检测的管道无损检测方案。
2. 技术原理管道无损检测方案主要基于超声波检测技术。
超声波是一种高频声波,能够在物体内部传播并被不同材料层次的边界反射或折射。
通过对超声波的发送和接收,可以得到管道内部的反射信号,从而获得管道的结构和状态信息。
具体而言,管道无损检测方案使用超声波传感器将超声波信号发送到管道内部。
信号在管道内部传播时会受到管道材料和其它物质的影响。
如果管道内部存在缺陷或腐蚀,超声波信号会发生反射、散射或衰减等变化。
通过分析接收到的信号,可以确定管道内部的问题并评估其严重程度。
3. 管道无损检测流程管道无损检测方案的流程如下:1.准备工作:确定检测区域和装置,并保证检测装置的可靠性和准确性。
2.数据采集:使用超声波传感器将信号发送到管道内部,并接收反射信号。
通过调整传感器的位置和角度,可以获取不同位置和角度下的信号。
3.信号处理:对接收到的信号进行滤波、增益和波形分析等处理。
这些处理可以提取出管道内部的结构和状态信息,并去除噪声干扰。
4.缺陷识别和评估:通过分析处理后的信号,可以确定管道内部的缺陷位置、类型和严重程度。
根据评估结果,可以制定维修或替换计划。
5.报告生成:将检测结果整理成报告,并将其提交给相关人员进行审查和处理。
4. 管道无损检测方案的优势和应用领域管道无损检测方案具有以下优势:•非侵入性:无需破坏管道外表面或切断管道内部流体,可以对管道进行检测和评估。
•高精度:通过使用超声波技术,可以获取管道内部的详细信息,包括缺陷位置、类型和严重程度。
•高效性:相对于传统的手工检测方法,管道无损检测方案可以实现自动化和快速检测。
管道无损检测方案可广泛应用于以下领域:•石油和化工行业:用于油气管道、化工管道等的监测和评估。
管道无损检测方案

管道无损检测方案1. 引言管道无损检测是一种常用的工程检测技术,它可以在不破坏管道结构的情况下,对管道的内部进行检测和评估。
本文将介绍一套全面有效的管道无损检测方案,包括无损检测的原理、常用的无损检测方法以及无损检测的应用场景。
2. 无损检测的原理无损检测是依据物质的内部或表面缺陷对其进行检测和评估的技术方法。
在管道无损检测中,主要采用以下几种原理进行检测:2.1 X射线检测X射线检测是一种常用的无损检测方法,它利用X射线的穿透能力对管道的内部进行检测。
X射线可以穿透金属等材料,当X射线经过管道时,被检测物质内部的缺陷会引起射线的散射或吸收,从而可以通过对射线的衰减程度来检测管道内部的缺陷。
2.2 超声波检测超声波检测是一种利用超声波在物质中传播和反射的原理对管道进行检测的方法。
通过将超声波传入管道中,当遇到管道内部的缺陷时,超声波将发生反射或散射,通过接收反射信号的强弱和时间来确定管道的缺陷位置和大小。
磁粉检测是一种利用磁性物质在管道表面产生磁场的原理对管道进行检测的方法。
通过在管道表面涂覆磁性粉末,在施加磁场的情况下,当管道表面存在裂纹或缺陷时,磁粉会在缺陷处集聚,从而可以通过观察磁粉的分布情况来检测管道表面的缺陷。
3. 常用的无损检测方法在管道无损检测中,根据不同的检测目的和要求,可以采用以下几种常用的无损检测方法:3.1 X射线射线检测X射线检测是一种广泛应用于管道无损检测的方法,它可以对管道内部的缺陷进行快速准确的检测。
X射线检测设备可以根据需要选择不同能量的射线,以适应不同材料和管道的检测需求。
3.2 超声波检测超声波检测是一种精密可靠的无损检测方法,它可以对管道内部的缺陷进行准确定位和定量评估。
超声波检测设备通常包含发射器和接收器,通过发射超声波并接收反射信号来确定缺陷的位置和大小。
磁粉检测是一种适用于管道表面缺陷检测的方法,它可以通过观察磁粉的分布情况来确定管道表面的缺陷。
磁粉检测设备通常包括磁场发生器和磁粉颗粒,通过施加磁场和观察磁粉的分布来检测管道表面的缺陷。
- 1、下载文档前请自行甄别文档内容的完整性,平台不提供额外的编辑、内容补充、找答案等附加服务。
- 2、"仅部分预览"的文档,不可在线预览部分如存在完整性等问题,可反馈申请退款(可完整预览的文档不适用该条件!)。
- 3、如文档侵犯您的权益,请联系客服反馈,我们会尽快为您处理(人工客服工作时间:9:00-18:30)。
管道无损检测方案
1. 概述
本工程各种管道约15000米,分不锈钢SS304SS316碳钢、合金钢、PP/GRP
CS+PTF等多种材质。
根据工艺、技术的不同要求,现场需拍片约40000张,硬
度试验900点。
本方案编制参考了招标文件中技术说明S-00-1540-002以及美国ASMES准
1986)。
2. 检验项目
2. 1 射线探伤
射线探伤的检查比例,按照JGC在“技术说明”中的要求执行。
射线探伤的检查比例应符合设计要求及有关技术条件的规定。
要求100%检查的管道应逐个焊口整圈100%检查, 确保不漏检。
要求10%抽检的管道应按相应焊工的相应焊缝按10%比例整圈检查。
管径W 3〃厚度SW 7.62mm采用双壁双影椭圆透照,每个焊口间隔
90°各拍一张, 共两张。
⑹ 管径=2〃厚度》8 74mm管径=2-1/2 〃厚度》9. 53mm管径=3〃厚
度》11 —13mm寸应采用双壁单影分段透照,拍摄四张。
⑺ 管径》4〃采用双壁单影或单壁单影透照,每个管口至少拍摄四张,T 各种规格管道焊缝的拍摄数量应与现场测试检查程序中的要求一致。
⑻ 胶片选用FUJI “ 100”型。
采用的铅箔增感屏,当采用X射线探伤时,
前屏厚0.03mm,后屏厚0.1mm当采用丫射线探伤时,前后屏厚均为0.1mm
⑼ 10〃以下包括10〃的管道探伤时,胶片规格为10〃x 4〃;12〃-
72〃的管道探伤时,胶片规格为12〃X 3-1/3 〃。
有特殊要求的按要求执行。
⑽ 所摄底片应无划伤,水迹,伪缺陷,当采用X射线时AB级的底片黑
度D=1.8—3.5,当采用丫射线时底片黑度D=2.0 —3.5,底片象质指数均应满足
不同厚度的要求。
底片上标识应齐全(包括管段号,焊口号,焊工号,拍摄日期,返修次数)。
(11)用Ir192 丫射线探伤时,应加装准直器,以减少散射线对底片像质的影响。
(12)所有要求做射线检查的焊口,必须在外观检查合格后进行,焊口表面
应无气孔,飞溅,裂纹,焊缝余高和咬边均应不超过ASMB31.3表341.3.2的
限值。
(13)射线探伤焊缝质量的评判应和ASME B31.3表341.3.2 一致,且符合
GB50236-98,评片时注意区分由于不锈钢晶粒粗大引起的伪缺陷。
(14)大口径管预制时,对接焊缝可采用环焊缝内透法或环缝外透法。
现场组对焊缝,可采用双壁双影或双壁单影法,具体方法见图示。
单壁单影
双壁单影
:2射线源
双壁双影
射线源
\ 1 1 -I-
/
/
1 f \
* \
1 1 1
[1
11 [
探伤设备的选用:当穿透厚度V 20mm 寸用X 光机探伤,其穿透力应能满足透照 工件的要求;当穿透厚度》20mm 寸用Ir192 丫探伤机,其影像应与X 光底片相同。
探伤机的操作机构应安全可靠,源强应能满足探伤工艺要求。
(15) 环焊缝透照的最小焦距:
小口径管环焊缝椭圆透照的最小焦距 L min=d xs /ug+ S
L —焦距mm L2—管件表面到胶片距离 mm d —焦点尺寸mm
T —母材厚度mm T’—斜向透照厚度 mm S —工件厚度mm U g -几何不清晰度
(16) 焊口返修不得超过2次,返修部位经重新探伤后,胶片上应加返修标 记,并按GB50235-97规范要求扩大抽查比例。
渗透探伤的检查比例应符合设计要求和有关技术条件的规 定。
L AB 级=10d X L 22/3
k=T ' / T > 1.1
(17) 检验结束时应对所检查的部位进行确认并打上标记。
2.2
渗透探伤
胶片
射线源
胶片
射线源
L
胶片
b
胶片
(椭
a
选用溶剂型渗透探伤试剂,检测试剂应低氯、低硫和磷要在有效期内,并有良好的检测性能,对工件无腐蚀作用,对人体基本无毒害作用。
对检测表面进行预清洗1分钟后施加渗透剂,渗透时间不少于5分
钟。
渗透液用清洗剂去除,但不能往复擦拭。
显像检查必须在7-30分钟完成,显像剂施加应薄而均匀,不能在
同一部位反复施加。
⑹ 检验结束时,在相同条件下,用同型号检测试剂及对比试块再进行
次校验,以保证探伤结果的正确。
JB4730-94。
3 .焊缝硬度检查 测试人员应有良好经验。
8〃V 管径<12 〃测2点 管径》14〃测3点
硬度测试仪用经过计量鉴定在有效期内的数字式硬度测试仪。
4. 检验单位及人员资质
4.1 担任本项目检测工作的检验单位具有江苏省建委和江苏省质量技术监 督局授权的安装
一级检测机构资质(见资质证明) 。
4.2 所有检验人员都具有江苏省锅炉压力容器无损检测考委会考核认可的 相关项目的资质
证明和江苏省建委和江苏省质量技术监督局考核颁发的无损检 测人员上岗证(见资质证明)
4.3 X 射线探伤和同位素检查的工程师为经全国锅炉压力容器无损检测考 委会考核发证
的高级人员(见资质证明) 。
⑺ 渗透探伤焊缝质量的评判应和
ASME B31.3 表 341.3.2 一致并符合
3.1 焊缝的硬度检查在热处理2 4小时后检查. 3.2 硬度测试数量:管径W6〃测一点
3.3 3.4 HB < 225
铅箱6mm 铅板
r 源(r 探伤机)\
y
J ■ ■ ■ ■ ■ ■ ■ ■ ■ ■
—:一 3
& :
• H H ■ 1 '■II n-n iiip^ j
检测仪器(见表)
序号
名称 型号
测量能力
数量 备注
1 X 射线探伤机
XXQ- 2505 120KV — 250KV 4台
2 Ir192 丫探伤机
TS — 1 100居里 2台
3
硬度测试仪
HL — D
HB80- 680
2台
6.检测过程和检验资料:
检验报告须提交JGC 格式事先须经JG-C 批准。
6.1所有需无损检测的焊口应由现场质检员指定并确认。
6.2 原始资料和检验报告都应画图准确,数据清楚,用词确切,签字齐全, 并经过无损检测
技术负责人审核。
6.3 原始记录还应详细写明工件材质,厚度,焊接方式,无损检测的操作条 件,缺陷的性
质,尺寸及部位。
7.安全措施
7.1X 射线机、r 源的现场存放: 射线机、r 探伤机在现场必须有专门固定的存放场所,指定专人负 责保管。
r 源除固定位置存放外,还有专门的铅罩,放在铝内并上锁,实行双人
双锁保管。
7.1.1X 7.1.2
铅罩
7.2 X 射线机、r 探伤机的领用:
7.2.1 现场需要射线探伤时,必须经现场探伤负责人同意方可领用探伤机 并办理领用手续。
7.2.2 需要用r 源探伤时,一定要有现场有关人员簦证的工作单,经确认后方 可领用。
7.3射线探伤现场申报:
7.3.1 射线探伤前,应向JGC 现场质检负责人填报:拍片地点、防护范围、 工作开始、结束时
间、工作人数,经同意后方可进行。
7.3.2 工作时,必须在规定的地点、时间内进行工作。
如有变动应及时通知 相关单位及人员。
7.4射线探伤防护区的划定:
射线照射区必须布置好警界绳、 警示灯、警示牌等明显的警示标志。
射线照相时,还应有专业人员负责在警界区巡检,防止非作业人员误
入照射区。
7.4.1 防护区划分应符合GB4792-84第11条规定。
7.4.2X 射线探伤时,防护区划定:以工作点为中心,三十米范围。
7.4.3r 射线探伤时,防护区划定:根据r 源强度大小划定防护区。
A.Kr.t
R-距离 A-r 源强度毫居里
t-照射时间(以8小时计)Kr-r 射线常数(4.72厘米2.伦/时毫居里) P-每天照射计量标准(0.02伦)
7.5
射线照射区的安全防护:
7.5.1 7.5.2
探伤人员工作时,必须配带报警器,保证不发生误照射。
在r 机的使用过程中,需经常检查输源管控制导管,以免损坏、发生
卡死现象。
7.7.3 夜间作业、现场必须有足够的照明度。
8. 发生意外事故的处理: 若因违反操作规程或其它原因造成事故,应维护好现场,不得私自
处理。
应
上报公安、卫生防疫部门拟定故障排除方案,及时处理。
7.6 射线探伤人员的岗位职责:
7.6.1 工作时严格遵守安全管理制度,不得随意离岗。
7.6.2 认真做好工作记录,工作结束时做好现场清洁工作。
7.7 射线探伤人员的安全防护:
7.7.1 7.7.2。