管道无损检测焊口片子数量规定
管道的焊接及探伤的相关规范要求
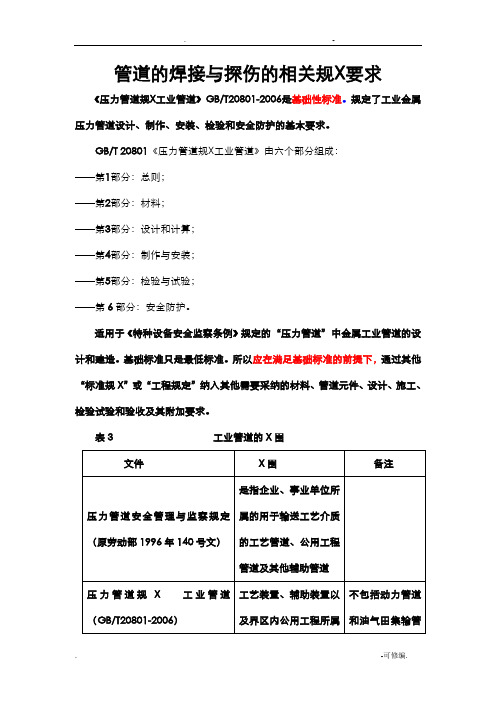
管道的焊接与探伤的相关规X要求《压力管道规X工业管道》GB/T20801-2006是基础性标准。
规定了工业金属压力管道设计、制作、安装、检验和安全防护的基本要求。
GB/T 20801《压力管道规X工业管道》由六个部分组成:——第1部分:总则;——第2部分:材料;——第3部分:设计和计算;——第4部分:制作与安装;——第5部分:检验与试验;——第6部分:安全防护。
适用于《特种设备安全监察条例》规定的“压力管道”中金属工业管道的设计和建造。
基础标准只是最低标准。
所以应在满足基础标准的前提下,通过其他“标准规X”或“工程规定”纳入其他需要采纳的材料、管道元件、设计、施工、检验试验和验收及其附加要求。
表3 工业管道的X围GB/T20801-2006对焊接与探伤都作了全面的、基础性规定GB/T20801.4-2006 压力管道规X—工业管道第4部分:制作与安装对焊接作了基础性规定7 焊接7.1 焊接工艺评定和焊工技能评定7.2 焊接材料7.3 焊接环境7.4 焊前准备7.5 焊接的基本要求7.6 焊缝设置等作了详细可操作的规定。
TSG D0001-2009《压力管道安全技术监察规程-工业管道》第六十七条对应当采用氩弧焊焊接的金属管道作了规定,GC1 级管道的单面对接焊接接头,设计温度低于或者等于-200C的管道,淬硬倾向较大的合金钢管道,不锈钢以及有色金属管道应当采用氩弧焊进行根部焊接,且表面不得有电弧擦伤。
GB/T20801.5-2006 压力管道规X—工业管道第5 部分检验与试验对检验与试验作了基础性规定6.1.1一般规定a)压力管道的检查等级分为Ⅰ、Ⅱ、Ⅲ、Ⅳ、Ⅴ五个等级,其中Ⅰ级最高,Ⅴ级最低;6.1.2按管道级别和剧烈循环工况确定管道检查等级:a) GC3 级管道的检查等级应不低于Ⅴ级;b) GC2 级管道的检查等级应不低于Ⅳ级;c) GC1 级管道的检查等级应不低于Ⅱ级;d) 剧烈循环工况管道的检查等级应不低于Ⅰ级。
管道焊缝无损探伤拍片数量的确定
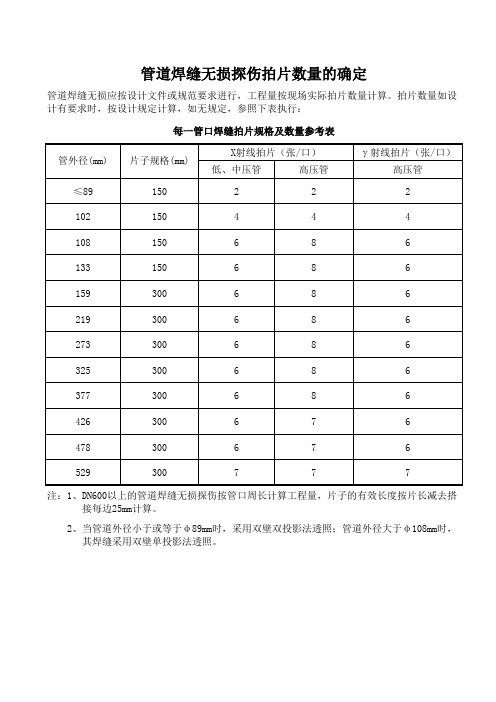
片数量如设
管道焊缝无损探伤拍片数量的确定
管道焊缝无损应按设计文件或规范要求进行,工程量按现场实际拍片数量计算。拍片数量如设 计有要求时,按设计规定计算,如无规定,参照下表执行:
每一管口焊缝拍片规格及数量参考表
管外径(mm)
片子规格(mm)
X射线拍片(张/口)
低、中压管
高压管
γ 射线拍片(张/口) 高压管
≤89
150
2
2
2
102
150
4
4
4
108
150
6
8
6
133
150
6
8
6
159
300
6
8
6
219
30068 Nhomakorabea6
273
300
6
8
6
325
300
6
8
6
377
300
6
8
6
426
300
6
7
6
478
300
6
7
6
529
300
7
7
7
注:1、DN600以上的管道焊缝无损探伤按管口周长计算工程量,片子的有效长度按片长减去搭 接每边25mm计算。
管道的焊接及探伤的相关规范方案要求
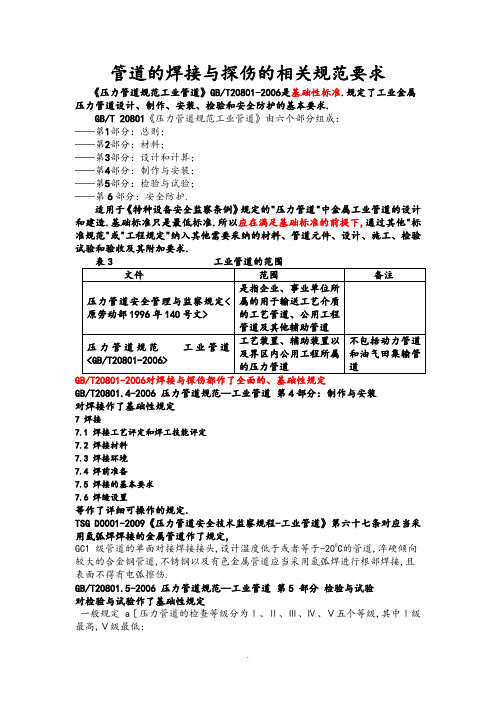
管道的焊接与探伤的相关规范要求《压力管道规范工业管道》GB/T20801-2006是基础性标准.规定了工业金属压力管道设计、制作、安装、检验和安全防护的基本要求.GB/T 20801《压力管道规范工业管道》由六个部分组成:——第1部分:总则;——第2部分:材料;——第3部分:设计和计算;——第4部分:制作与安装;——第5部分:检验与试验;——第6部分:安全防护.适用于《特种设备安全监察条例》规定的"压力管道"中金属工业管道的设计和建造.基础标准只是最低标准.所以应在满足基础标准的前提下,通过其他"标准规范"或"工程规定"纳入其他需要采纳的材料、管道元件、设计、施工、检验试验和验收及其附加要求.GB/T20801.4-2006 压力管道规范—工业管道第4部分:制作与安装对焊接作了基础性规定7 焊接7.1 焊接工艺评定和焊工技能评定7.2 焊接材料7.3 焊接环境7.4 焊前准备7.5 焊接的基本要求7.6 焊缝设置等作了详细可操作的规定.TSG D0001-2009《压力管道安全技术监察规程-工业管道》第六十七条对应当采用氩弧焊焊接的金属管道作了规定,GC1 级管道的单面对接焊接接头,设计温度低于或者等于-200C的管道,淬硬倾向较大的合金钢管道,不锈钢以及有色金属管道应当采用氩弧焊进行根部焊接,且表面不得有电弧擦伤.GB/T20801.5-2006 压力管道规范—工业管道第5 部分检验与试验对检验与试验作了基础性规定一般规定 a〔压力管道的检查等级分为Ⅰ、Ⅱ、Ⅲ、Ⅳ、Ⅴ五个等级,其中Ⅰ级最高,Ⅴ级最低;按管道级别和剧烈循环工况确定管道检查等级:a〔 GC3 级管道的检查等级应不低于Ⅴ级;b〔 GC2 级管道的检查等级应不低于Ⅳ级;c〔 GC1 级管道的检查等级应不低于Ⅱ级;d〔剧烈循环工况管道的检查等级应不低于Ⅰ级.按材料类别和公称压力确定管道检查等级:a〔除GC3 级管道外,公称压力不大于PN50 的碳钢管道<本规范无冲击试验要求>的检查等级应不低于Ⅳ级;b〔除GC3 级管道外,以下管道的检查等级应不低于Ⅲ级:1〔公称压力不大于PN50 的碳钢<本规范要求冲击试验>管道;2〔公称压力不大于PN110 的奥氏体不锈钢管道.c〔以下管道的检查等级应不低于Ⅱ级:1〔公称压力大于PN50 的碳钢<本规范要求冲击试验>管道;2〔公称压力大于PN110 的奥氏体不锈钢管道;3〔低温含镍钢、铬钼合金钢、双相不锈钢、铝及铝合金管道;d〔以下管道的检查等级应不低于Ⅰ级:1〔钛及钛合金、镍及镍基合金、高铬镍钼奥氏体不锈钢管道;2〔公称压力大于PN160 的管道.注2:角焊缝包括承插焊和密封焊以及平焊法兰、支管补强和支架的连接焊缝;注3:支管连接焊缝包括支管和翻边接头的受压焊缝;注4:对碳钢、不锈钢及铝合金无此要求;注5:适用于≥DN100 的GB50517-2010石油化工金属管道工程施工质量验收规范9.3 焊接接头的无损检测管道焊接接头无损检测除设计文件另有规定外,厚度小于或等于30mm的焊缝应采用射线检测,厚度大于30mm的焊缝可采用超声检测,检测数量与验收标准应按表规定进行,并应符合以下规定:1 射线检测的技术等级应为AB 级;2 超声检测的技术等级应为B 级.检查方法:核查管道单线图和无损检测报告.注:表中检测方法RT与UT、MT与PT的关系为"或".GB50517-2010石油化工金属管道工程施工质量验收规范条文说明表1石油化工管道分级与压力管道安全技术监察规程—工业管道分级对照GB50184―2011工业金属管道工程施工质量验收规范8.2 焊缝射线检测和超声波检测3 检验数量:应符合设计文件和以下规定:1>管道焊缝无损检测的检验比例应符合表的规定.个:"5%"、 "15%"、"100%".焊缝的无损检测,应符合以下规定:1焊缝外观质量,应符合本规范第条的规定;2无损检测的抽检数量和焊缝质量,应符合设计或随机技术文件的规定;无规定时,应符合表的规定;注:表中的Ⅲ级、Ⅱ级、Ⅰ级为现行国家标准《金属熔化焊接接头射线照相》GB/T3323规定的焊缝质量等级.3按规定抽查的无损检测不合格时,应加倍抽查该焊工的焊缝数量,当仍不合格时,应对其全部焊缝进行无损检测.GB/T20801.5-2006压力管道规范-工业管道局部无损检测的焊接接头位置及检查点应由建设单位或检验机构的检验人员选择或批准.目前大多数建设单位委托工程监理确定局部无损检测的焊接接头位置及检查点,习惯称拍片点口.GB 50517—2010石油化工金属管道工程施工质量验收规范管道焊接接头按比例抽样检查时,应按以下原则选定焊接接头:1焊接接头固定口检测不应少于检测数量的40%;2应覆盖施焊的每名焊工;3按比例均衡各管道编号分配检测数量;4交叉焊缝部位应包括检查长度不小于38mm的相邻焊缝.管道组成件的选用及其限制GB/T20801.2中的6.3管子与管件碳钢、奥氏体不锈钢钢管及其对焊管件应符合表1的规定.第二十八条碳钢、奥氏体不锈钢钢管以及由其制造的对接焊管件的使用限制应当符合表1规定.表1钢管及其对接焊管件的使用限制<与上述规定相同>。
无损检测拍片数量

城镇天然气钢管无损检测拍片数量一、无损检测质量等级根据国家发展改革委员会颁布的《承压设备无损检测》JB/T4730.2-2005第六条“承压设备管子及压力管道熔化焊环向对接焊接接头射线检测质量分级”规定,厚度T≥2mm的碳素钢、低合金钢、奥氏体不锈钢、镍及镍合金、铜及铜合金制承压设备管子及压力管道的熔化焊环向对接焊接接头射线检测的质量分级。
根据对接接头中存在的缺陷性质、数量和密集程度,其质量等级可划分为: I 、II 、III 、IV 级。
I级对接焊接接头内不允许存在裂纹、未融合、未焊透、条形缺陷、根部内凹、根部咬边。
II级和 III 级对接焊接接头内不允许存在裂纹、未融合、双面焊以及加垫板单面焊中的未焊透。
对接焊接接头中缺陷超过 III 级者为 IV 级。
当各类缺陷评定的质量级别不同时,以质量最差的级别作为对接焊接接头的质量级别。
二、等级评判依据综合集团所用管材厚度一般不超过 25mm;因此评定区间为 10mm*10mm;1、圆形缺陷点数按下表换算:圆形缺陷点数换算表缺陷长≤ 1>1~2>2~3>3~4>4~6>6~8>8径, mm缺陷点数1234101525各级别允许的圆形缺陷点数评定区10mm*10mm备注母材公称厚度 T≤10mm当母材公称I1厚度不同II3时,取较薄III6板的厚度IV缺陷点数大于 III级或缺陷长径大于 T/2对致密性要求高的对接焊接接头,底片评定人员应考虑将圆形缺陷的黑度作为评级的依据。
通常将黑度大的圆形缺陷定义为深孔缺陷,当对接焊接接头存在深孔缺陷时,其质量级别应评为IV 级。
2、管材厚度T≤25mm,按照 II级片的规定,单个条形缺陷最大长度为≤ T/3 (最小为4)且≤ 20,一般来说,因我们所用管材厚度多为10mm 以下,因此在评片中,一组条形缺陷累计最大长度也可按照4mm来比较。
条形缺陷评定区是指与焊缝方向平行具有一定宽度的矩形,当 T≤25mm 时,宽度为 4mm。
工艺管线焊接无损检测管理办法
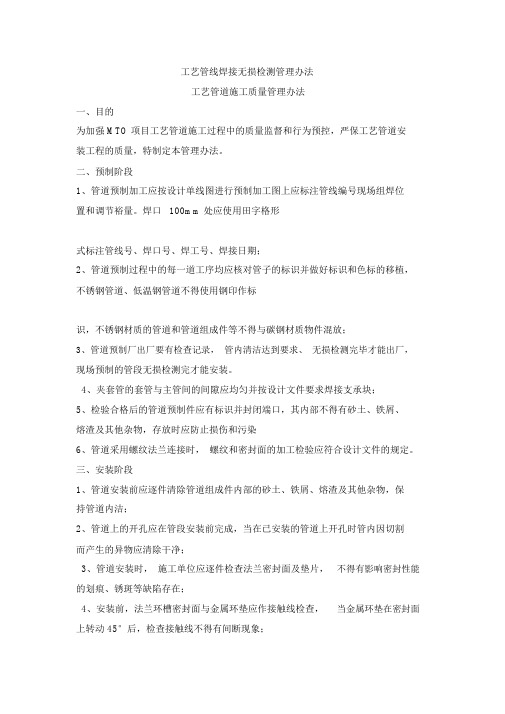
工艺管线焊接无损检测管理办法工艺管道施工质量管理办法一、目的为加强 MTO 项目工艺管道施工过程中的质量监督和行为预控,严保工艺管道安装工程的质量,特制定本管理办法。
二、预制阶段1、管道预制加工应按设计单线图进行预制加工图上应标注管线编号现场组焊位置和调节裕量。
焊口100mm 处应使用田字格形式标注管线号、焊口号、焊工号、焊接日期;2、管道预制过程中的每一道工序均应核对管子的标识并做好标识和色标的移植,不锈钢管道、低温钢管道不得使用钢印作标识,不锈钢材质的管道和管道组成件等不得与碳钢材质物件混放;3、管道预制厂出厂要有检查记录,管内清洁达到要求、无损检测完毕才能出厂,现场预制的管段无损检测完才能安装。
4、夹套管的套管与主管间的间隙应均匀并按设计文件要求焊接支承块;5、检验合格后的管道预制件应有标识并封闭端口,其内部不得有砂土、铁屑、熔渣及其他杂物,存放时应防止损伤和污染6、管道采用螺纹法兰连接时,螺纹和密封面的加工检验应符合设计文件的规定。
三、安装阶段1、管道安装前应逐件清除管道组成件内部的砂土、铁屑、熔渣及其他杂物,保持管道内洁;2、管道上的开孔应在管段安装前完成,当在已安装的管道上开孔时管内因切割而产生的异物应清除干净;3、管道安装时,施工单位应逐件检查法兰密封面及垫片,不得有影响密封性能的划痕、锈斑等缺陷存在;4、安装前,法兰环槽密封面与金属环垫应作接触线检查,当金属环垫在密封面上转动 45°后,检查接触线不得有间断现象;5、流量孔板上、下游直管的长度应符合设计文件要求,且在此范围内的焊缝内表面应与管道内表面平齐,打磨光滑;6、连接法兰的螺栓应能在螺栓孔中顺利通过;7、与机器连接的管道及其支、吊架安装完毕后,应卸下接管上的法兰螺栓。
在自由状态下,所有螺栓应能在螺栓孔中顺利通过;8、机器试车前应对管道与机器的连接法兰进行最终连接检查;9、有静电接地要求的不锈钢管道,导线跨接或接地引线应采用不锈钢板过渡,不得与不锈钢管直接连接;10、管道安装时应同时进行支、吊架的固定和调整工作,支吊架位置应正确安装,应牢固。
无损检测施工管理规定

东营联合石化有限责任公司无损检测施工管理规定一、目的为了明确东营联合石化有限责任公司项目施工阶段对无损检测的要求,使参与建设的各承包商、监理单位、检测单位从质保体系、人员配备、检测工艺、检测设备等方面确保无损检测过程及结果达到质量标准要求,进而保证工程质量和施工安全,特编制本规定。
本规定解释和修改权在工程部。
二、范围适用于东营联合石化有限责任公司项目施工阶段无损检测。
三、定义(一)东营联合石化有限责任公司抽检单位指东营联合石化有限责任公司成立的由取得《特种设备检验检测核准证》的单位或一定数量的检测人员组成的专业抽检、复审组织。
(二)检测人员“检测人员”指持有国家质量监督检验检疫总局颁发的、并与其从事检测项目、级别相适应资格证书的人员。
(三)第三方检测单位“第三方检测单位”指具备“检测单位”资质,与业主签订了检测承包合同,实施独立第三方检测的单位。
(四)复审“复审”指东营联合石化有限责任公司组织的,对第三方检测单位射线底片重新评定审核,以验证后者的工作质量。
(五)抽检“抽检”指东营联合石化有限责任公司对进场材料、设备及工程实体(主要是焊缝)的抽样检查。
四、职责(一)质量部1、负责整个工程项目的无损检测质量监督管理工作,制定各项目部无损检测管理要求并监督执行。
2、负责对施工承包商、监理公司和第三方检测单位无损检测工作质量的监督检查。
3、负责施工现场有关无损检测工作的组织和协调工作。
4、协助HSE管理部做好施工现场无损检测安全技术管理和监督工作。
5、在工程实施过程中将不定期对检测单位的质保体系运转、检测工艺执行、检测过程质量实行监督与检查;对各类检测报告进行抽查,并做好监督与检查记录。
(二)HSE管理部1、负责本工程有关无损检测项目的安全管理、沟通、协调工作。
2、负责对进入本工程施工现场的γ射线源进行登记,并强化γ射线源保管、储存及检测作业时的监督、管理。
(三)基建部1、做好所管辖工程无损检测工作的管理、协调、监督检查,为工程项目的顺利实施提供服务。
管道无损检测施工专项方案
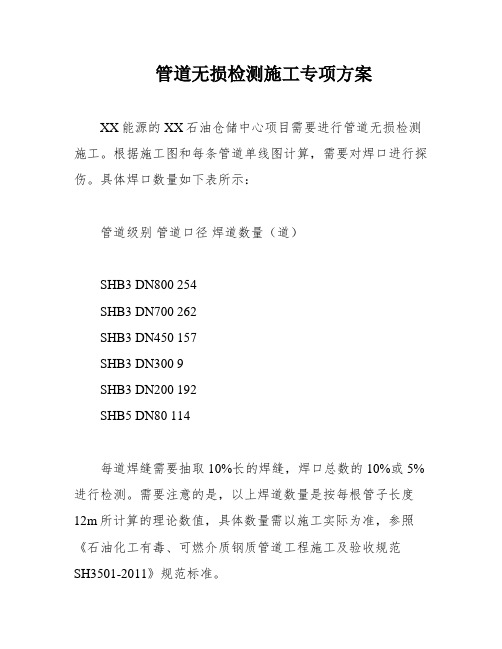
管道无损检测施工专项方案XX能源的XX石油仓储中心项目需要进行管道无损检测施工。
根据施工图和每条管道单线图计算,需要对焊口进行探伤。
具体焊口数量如下表所示:管道级别管道口径焊道数量(道)SHB3 DN800 254SHB3 DN700 262SHB3 DN450 157SHB3 DN300 9SHB3 DN200 192SHB5 DN80 114每道焊缝需要抽取10%长的焊缝,焊口总数的10%或5%进行检测。
需要注意的是,以上焊道数量是按每根管子长度12m所计算的理论数值,具体数量需以施工实际为准,参照《石油化工有毒、可燃介质钢质管道工程施工及验收规范SH3501-2011》规范标准。
该工程的特点在于,为了不影响施工进度和交叉施工作业人员安全,探伤作业将在晚上休息时间进行。
由于罐区施工的管道处在地面上,拍片作业比较方便。
然而,探伤位置相对不固定,探伤机有一定的重量,且场地凹凸不平,施工环境复杂,各单位的施工工期都比较紧张,因此安全将是整个施工中最大最严重的一个控制环节。
为了保证施工质量和安全,选用XXX作为无损检测机构。
该公司施工资质符合要求并专门从事该行业的施工,施工经验丰富,施工能力一流。
无损检测工作选派应由按《特种设备无损检测人员考核与监督管理规则》考试合格的三名经验丰富的具备无损检测Ⅱ级资格的人员担任。
最后需要注意文件控制,确保施工过程中的文件管理规范。
2.2.1 为了符合有关标准、规范和施工技术文件的要求,应结合现场工作条件编制无损检测工艺卡。
Ⅱ级或Ⅲ级以上的人员应编制无损检测工艺卡,而无损检测责任工程师则应审批工艺卡。
2.2.2 无损检测记录和报告应严格遵守公司和检测中心的相关规定。
2.2.3 无损检测资料应妥善保存,并在工程竣工后统一交给业主归档保管。
归档资料包括:探伤委托单、检测方案、工艺卡、射线底片、探伤记录、探伤报告和探伤位置示意图等。
2.3 施工工序2.3.1 对于焊口的检测,DN500以下(不含DN500)按照业主和监理现场抽检焊口选定。
焊缝合格标准

焊缝合格级别及无损检测要点一、长输管道:1.SY0410—98《输油输气管道线路工程施工及验收规范》第7.3.2条:RT执行SY4056—93;UT执行SY4065—93合格级别:输油:P设≤6.4MPa Ⅲ级P设>6.4MPa Ⅱ级输气:P设≤4MPa 一、二级地区Ⅲ级;三、四级地区Ⅱ级P设>4MPa Ⅱ级第7.3.4条:输油管道的探伤比例可任选下面其中之一:100%UT后,对每个焊工或机组每天完成数量的5%作射线复验只进行RT抽查,抽查比例为每个焊工或作业机组每天完成数量的15% 。
第7.3.5条:输气管道的探伤比例:100%UT后,对每个焊工或作业机组每天完成数量的抽查比例:一级地区5%二级地区10%三级地区15%四级地区20%只进行RT抽查,对每个焊工或作业机组每天完成数量的抽查比例:一级地区10%二级地区15%三级地区40%四级地区75%第7.3.6条:抽查时,如每天的焊口数量比例达不到比例要求时,可以每公里为一个检验段,并按规定的比例数随焊随查,均匀的复验、抽查。
第7.3.7条:射线探伤复验,抽查中,有一个焊口不合格,应对该焊工或机组段焊接焊口加倍检查,再不合格,则其余焊口逐个RT探伤第7.3.8条:穿越焊口,钢管与弯头连接的焊口,试压后连头的碰口应进行100%RT。
第7.3.9条:×60及以上级别管材,返修后应按《常压钢制焊接储罐及管道渗透检测技术标准》SY/T0443进行渗透检查。
第7.3.10条:探伤人员应取得相关主管部门颁发的证书。
2.SY0470—2000《石油天然气跨越工程施工及验收规范》第5.3.2条:焊缝外观检查合格之后,应进行无损探伤。
焊缝无损探伤应符合下列规定:跨越管道环向焊缝应进行100%射线探伤。
对射线探伤难度大的个别环向焊缝部位,经有关部门共同商定可用超声波探伤代替射线探伤,但其数量不准超过总数10%。
RT符合SY4056 Ⅱ级合格;UT符合SY4065 Ⅱ级合格二、集输管道:1.SY0466—97《天然气集输管道施工及验收规范》第5.2条无损探伤:第5.2.1条:无损探伤人员必须具备劳动部门颁发的Ⅰ级以上资格证,评片人员具有Ⅱ级及其以上资格;第5.2.2条:焊缝无损探伤必须在外观质量检验合格后进行;第5.2.3条:设计无规定时,管道环缝100%UT,每个焊工所焊的各类焊缝应第5.2.5条:当RT复验不合格,应对该焊工所焊该类焊缝按原射线探伤复验数量补充探伤,仍不合格,停止其工作,并对其于焊工所焊焊缝进行100%RT 复验。
工艺管道无损检测(x射线)

应根据每台X光机,胶片和增感屏制作曝光曲线,以此作为曝光规范。当焦距为700㎜时,曝光量应≥15mA·min,当焦距改变时可按平方反比定律对曝光量的推荐值进行换算。
2散射线的屏蔽
为防止散射线的影响应用厚度不小于2mm的铅板屏蔽背散;为检查背散射防护是否合格,应暗袋背面贴附一个“B”字标记。当底片上较黑背景上出现“B”字较淡影像时,说明背散射防护不够,应予重新透照。
6.1.3焊接工作结束后进行无损探伤工作,但具有裂纹倾向的材质,应在焊接完成24h以后才能进行探伤工作。。
6.2一般项目
6.2.1被检测焊缝及热影响区的表面质量(包括余高高度)应经外观检查合格,其表面不得存在:裂纹、气孔、弧坑、咬边和肉眼可见的夹渣等缺陷,焊接接头两侧的飞溅和熔渣,必须清除。
6.2.2底片的黑度应为2.0-4.0,像质计摆放正确,并能观察到标准规定的钢丝影像,标记齐全且不覆盖焊缝,在有效评定范围内不得有影响底片评定的划伤、水迹、脱膜、污斑等,否则应重新拍片。
6.2.3加强过程控制,严把质量关,不合格材料不准进入现场。检查不合格的工序,不得进行下工序,做到“上工序服务下工序,下工序监督上工序”,每道工序经检查人员认可后方可进行下工序,并做好质量记录,具有可追溯性,保证底片编号与单线图焊口编号、记录及报告一一对应。
7
7.1对于整理好的底片应存放在通风、干燥的地方。
7.2在探伤过程中注意被检测工件的保护、不得损坏。
8
8.1环境因素控制措施
8.1.1探伤操作产生的固体废弃物应分类投放到专用垃圾箱内。
8.1.2废显影、定影药液应稀释50倍后测定PH值,当PH值为6-9时,方可排放。
8.2危险源控制措施
8.2.1进入施工现场的探伤人员必须经过安全及射线防护知识的教育,使全体检测人员掌握射线设备操作方法、安全防护、辐射事故预防、事故处理有关安全规定。
压力管道定期检验-无损检测
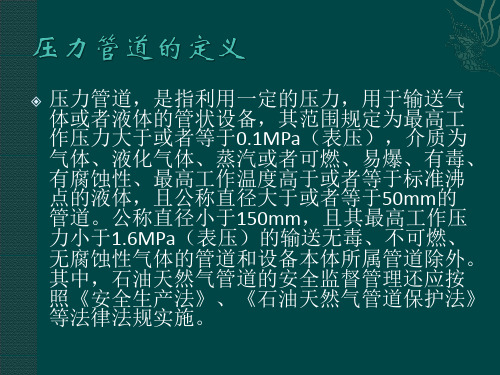
(2)在实际工况下,材料韧性良好,并且未出现材料 性能劣化以及劣化趋向;
(3)壁厚局部减薄以及其附近无其他表面缺陷或者埋 藏缺陷;
(4)壁厚局部减薄处剩余壁厚大于2mm; (5)管道不承受疲劳载荷。
5、其他 一)RT检测时必须放置对比试块; 二)对比试块的高度需和需要和评级时需要对比
3、扩拍要求
抽查发现安全状况等级3级或者4级的缺 陷,应当增加抽查比例,增加的抽查比例 由检验人员与使用单位结合管道运行参数 和实际情况进行协商确定。
注:对于3级的缺陷尽量进行返修,否则下 次检验周期不一致,会增加企业定检压力。
4、缺陷描述
(一)咬边
GC1咬边深度不超过0.5mm,GC2、GC3咬边 深度不超过0.8mm,不影响定级,否则,应打磨 消除,并且按照局部减薄评级。(咬边缺陷描述: 深度,长度(打磨消除))
(五)未熔合
GC1级管道的单个焊接接头未熔合总长度不大
于焊接接头长度的50%时,按照表4-4定级,否则 定为4级;GC2级、GC3级管道未熔合的长度不限, 按照表4-4定级。 (未熔合缺陷描述:长度,自身 高度)
有效厚度
安全状况等级
压力管道探伤口数量计算说明
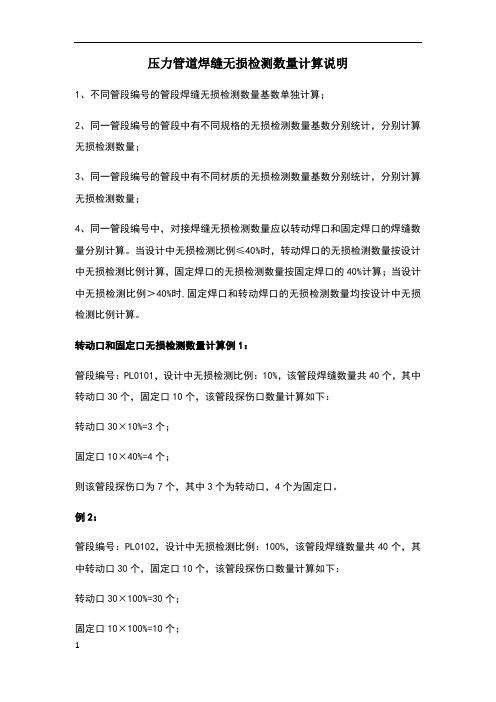
压力管道焊缝无损检测数量计算说明
1、不同管段编号的管段焊缝无损检测数量基数单独计算;
2、同一管段编号的管段中有不同规格的无损检测数量基数分别统计,分别计算无损检测数量;
3、同一管段编号的管段中有不同材质的无损检测数量基数分别统计,分别计算无损检测数量;
4、同一管段编号中,对接焊缝无损检测数量应以转动焊口和固定焊口的焊缝数量分别计算。
当设计中无损检测比例≤40%时,转动焊口的无损检测数量按设计中无损检测比例计算,固定焊口的无损检测数量按固定焊口的40%计算;当设计中无损检测比例>40%时,固定焊口和转动焊口的无损检测数量均按设计中无损检测比例计算。
转动口和固定口无损检测数量计算例1:
管段编号:PL0101,设计中无损检测比例:10%,该管段焊缝数量共40个,其中转动口30个,固定口10个,该管段探伤口数量计算如下:
转动口30×10%=3个;
固定口10×40%=4个;
则该管段探伤口为7个,其中3个为转动口,4个为固定口。
例2:
管段编号:PL0102,设计中无损检测比例:100%,该管段焊缝数量共40个,其中转动口30个,固定口10个,该管段探伤口数量计算如下:
转动口30×100%=30个;
固定口10×100%=10个;
则该管段探伤口为40个,其中30个为转动口,10个为固定口。
压力管道探伤口数量计算说明完整版

压力管道探伤口数量计
算说明
HEN system office room 【HEN16H-HENS2AHENS8Q8-HENH1688】
压力管道焊缝无损检测数量计算说明
1、不同管段编号的管段焊缝无损检测数量基数单独计算;
2、同一管段编号的管段中有不同规格的无损检测数量基数分别统计,分别计算无损检测数量;
3、同一管段编号的管段中有不同材质的无损检测数量基数分别统计,分别计算无损检测数量;
4、同一管段编号中,对接焊缝无损检测数量应以转动焊口和固定焊口的焊缝数量分别计算。
当设计中无损检测比例≤40%时,转动焊口的无损检测数量按设计中无损检测比例计算,固定焊口的无损检测数量按固定焊口的40%计算;当设计中无损检测比例>40%时,固定焊口和转动焊口的无损检测数量均按设计中无损检测比例计算。
转动口和固定口无损检测数量计算例1:
管段编号:PL0101,设计中无损检测比例:10%,该管段焊缝数量共40个,其中转动口30个,固定口10个,该管段探伤口数量计算如下:
转动口30×10%=3个;
固定口10×40%=4个;
则该管段探伤口为7个,其中3个为转动口,4个为固定口。
例2:
管段编号:PL0102,设计中无损检测比例:100%,该管段焊缝数量共40个,其中转动口30个,固定口10个,该管段探伤口数量计算如下:
转动口30×100%=30个;
固定口10×100%=10个;
则该管段探伤口为40个,其中30个为转动口,10个为固定口。
管道的焊接与探伤的相关规范要求

管道的焊接与探伤的相关规范要求《压力管道规范工业管道》GB/T20801-2006是基础性标准。
规定了工业金属压力管道设计、制作、安装、检验和安全防护的基本要求。
GB/T 20801《压力管道规范工业管道》由六个部分组成:——第1部分:总则;——第2部分:材料;——第3部分:设计和计算;——第4部分:制作与安装;——第5部分:检验与试验;——第6部分:安全防护。
适用于《特种设备安全监察条例》规定的“压力管道”中金属工业管道的设计和建造。
基础标准只是最低标准。
所以应在满足基础标准的前提下,通过其他“标准规范”或“工程规定”纳入其他需要采纳的材料、管道元件、设计、施工、检验试验和验收及其附加要求。
GB/T20801.4-2006 压力管道规范—工业管道第4部分:制作与安装对焊接作了基础性规定7 焊接7.1 焊接工艺评定和焊工技能评定7.2 焊接材料7.3 焊接环境7.4 焊前准备7.5 焊接的基本要求7.6 焊缝设置等作了详细可操作的规定。
TSG D0001-2009《压力管道安全技术监察规程-工业管道》第六十七条对应当采用氩弧焊焊接的金属管道作了规定,GC1 级管道的单面对接焊接接头,设计温度低于或者等于-200C的管道,淬硬倾向较大的合金钢管道,不锈钢以及有色金属管道应当采用氩弧焊进行根部焊接,且表面不得有电弧擦伤。
GB/T20801.5-2006 压力管道规范—工业管道第5 部分检验与试验对检验与试验作了基础性规定6.1.1一般规定 a)压力管道的检查等级分为Ⅰ、Ⅱ、Ⅲ、Ⅳ、Ⅴ五个等级,其中Ⅰ级最高,Ⅴ级最低;6.1.2按管道级别和剧烈循环工况确定管道检查等级:a) GC3 级管道的检查等级应不低于Ⅴ级;b) GC2 级管道的检查等级应不低于Ⅳ级;c) GC1 级管道的检查等级应不低于Ⅱ级;d) 剧烈循环工况管道的检查等级应不低于Ⅰ级。
6.1.3 按材料类别和公称压力确定管道检查等级:a)除GC3 级管道外,公称压力不大于PN50 的碳钢管道(本规范无冲击试验要求)的检查等级应不低于Ⅳ级;b) 除GC3 级管道外,下列管道的检查等级应不低于Ⅲ级:1)公称压力不大于PN50 的碳钢(本规范要求冲击试验)管道;2) 公称压力不大于PN110 的奥氏体不锈钢管道。
工艺管道无损检测(X射线)
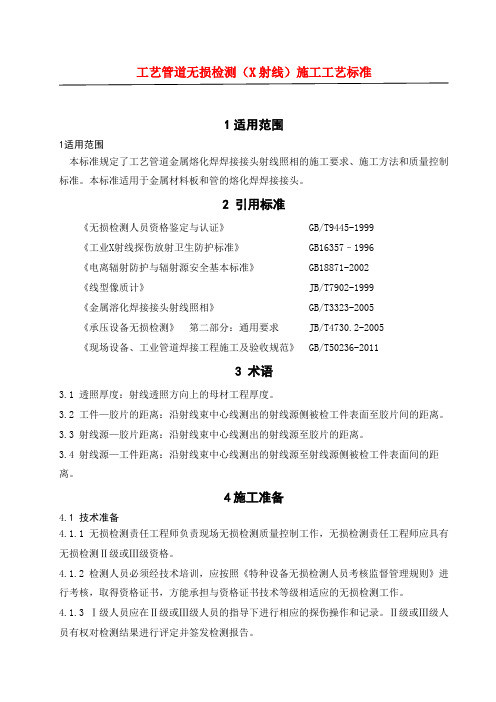
工艺管道无损检测(X射线)施工工艺标准1适用范围1适用范围本标准规定了工艺管道金属熔化焊焊接接头射线照相的施工要求、施工方法和质量控制标准。
本标准适用于金属材料板和管的熔化焊焊接接头。
2 引用标准《无损检测人员资格鉴定与认证》 GB/T9445-1999《工业X射线探伤放射卫生防护标准》 GB16357–1996《电离辐射防护与辐射源安全基本标准》 GB18871-2002《线型像质计》 JB/T7902-1999《金属溶化焊接接头射线照相》 GB/T3323-2005《承压设备无损检测》第二部分:通用要求 JB/T4730.2-2005《现场设备、工业管道焊接工程施工及验收规范》 GB/T50236-20113 术语3.1 透照厚度:射线透照方向上的母材工程厚度。
3.2 工件—胶片的距离:沿射线束中心线测出的射线源侧被检工件表面至胶片间的距离。
3.3 射线源—胶片距离:沿射线束中心线测出的射线源至胶片的距离。
3.4 射线源—工件距离:沿射线束中心线测出的射线源至射线源侧被检工件表面间的距离。
4施工准备4.1 技术准备4.1.1 无损检测责任工程师负责现场无损检测质量控制工作,无损检测责任工程师应具有无损检测Ⅱ级或Ⅲ级资格。
4.1.2 检测人员必须经技术培训,应按照《特种设备无损检测人员考核监督管理规则》进行考核,取得资格证书,方能承担与资格证书技术等级相适应的无损检测工作。
4.1.3 Ⅰ级人员应在Ⅱ级或Ⅲ级人员的指导下进行相应的探伤操作和记录。
Ⅱ级或Ⅲ级人员有权对检测结果进行评定并签发检测报告。
4.1.4 射线检测人员未经矫正或经矫正的视力应不低于1.0,从事评片的人员每年检查一次视力。
4.2 物资准备4.2.1 胶片应使用锅炉压力容器安全监察机构监制认可的胶片,或性能符合要求的其他胶片。
如天津Ⅲ型、AGFA-C7等。
4.3 施工设施准备4.3.1 本施工工艺标准施工过程中使用的机具有:X射线探伤机、增感屏、观片灯、裁片刀、像质计、字码。
氧气管道无损检测要求

氧气管道无损检测要求
1.现场焊接的管道及管道组成件的承插焊焊缝、支吊架与管道直接焊接的焊缝,以及管道上的其他角焊缝,其表面应进行磁粉检测或渗透检测。
检测比列按照《工业金属管道工程施工质量验收规范》GB50184-2011的规定。
2.现场焊接的管道及管道组成件的对接纵缝和环缝、对接式支管连接焊缝,应进行焊缝接头的射线检测。
当采用水压试验时,检测的数量和标准应按下表要求执行:
氧气管道焊缝检测要求
当采用气体做压力试验时,焊缝的射线检测要求如下:
1)设计压力不大于0.6MPa时,检测比例不小于15%,焊缝质量等级不低于III级;
2)设计压力大于0.6MPa时,且下于或等于4.0MPa时,检测比例为100%,焊缝质量等级不低于II级。
被检焊接接头的选择应当包括每个焊工所焊的焊接接头。
对未要求做无损检测的焊缝,质检人员应对全部焊缝的可见部分进行外观加检查,其质量应符合GB50236和GB/T20801.5的要求。
套管内的管道不应有焊缝,如内管必须有焊缝时,焊缝应当100%射线检测。
管道的焊接与探伤的相关规范要求【范本模板】

管道的焊接与探伤的相关规范要求《压力管道规范工业管道》GB/T20801-2006是基础性标准.规定了工业金属压力管道设计、制作、安装、检验和安全防护的基本要求.GB/T20801《压力管道规范工业管道》由六个部分组成:——第1部分:总则;——第2部分:材料;——第3部分:设计和计算;——第4部分:制作与安装;——第5部分:检验与试验;—-第6部分:安全防护。
适用于《特种设备安全监察条例》规定的“压力管道”中金属工业管道的设计和建造。
基础标准只是最低标准。
所以应在满足基础标准的前提下,通过其他“标准规范”或“工程规定”纳入其他需要采纳的材料、管道元件、设计、施工、检验试验和验收及其附加要求。
GB/T20801。
4-2006 压力管道规范—工业管道第4部分:制作与安装对焊接作了基础性规定7焊接7。
1 焊接工艺评定和焊工技能评定7.2 焊接材料7。
3焊接环境7.4 焊前准备7。
5 焊接的基本要求7.6 焊缝设置等作了详细可操作的规定。
TSGD0001—2009《压力管道安全技术监察规程—工业管道》第六十七条对应当采用氩弧焊焊接的金属管道作了规定,GC1级管道的单面对接焊接接头,设计温度低于或者等于—200C的管道,淬硬倾向较大的合金钢管道,不锈钢以及有色金属管道应当采用氩弧焊进行根部焊接,且表面不得有电弧擦伤.GB/T20801。
5—2006压力管道规范-工业管道第5 部分检验与试验对检验与试验作了基础性规定6。
1.1一般规定a)压力管道的检查等级分为Ⅰ、Ⅱ、Ⅲ、Ⅳ、Ⅴ五个等级,其中Ⅰ级最高,Ⅴ级最低;6。
1.2按管道级别和剧烈循环工况确定管道检查等级:a) GC3 级管道的检查等级应不低于Ⅴ级;b) GC2 级管道的检查等级应不低于Ⅳ级;c)GC1 级管道的检查等级应不低于Ⅱ级;d) 剧烈循环工况管道的检查等级应不低于Ⅰ级。
6.1。
3 按材料类别和公称压力确定管道检查等级:a)除GC3 级管道外,公称压力不大于PN50 的碳钢管道(本规范无冲击试验要求)的检查等级应不低于Ⅳ级;b) 除GC3 级管道外,下列管道的检查等级应不低于Ⅲ级:1)公称压力不大于PN50 的碳钢(本规范要求冲击试验)管道;2) 公称压力不大于PN110 的奥氏体不锈钢管道.c) 下列管道的检查等级应不低于Ⅱ级:1) 公称压力大于PN50的碳钢(本规范要求冲击试验)管道;2)公称压力大于PN110 的奥氏体不锈钢管道;3)低温含镍钢、铬钼合金钢、双相不锈钢、铝及铝合金管道;d) 下列管道的检查等级应不低于Ⅰ级:1)钛及钛合金、镍及镍基合金、高铬镍钼奥氏体不锈钢管道;2)公称压力大于PN160的管道.注2:角焊缝包括承插焊和密封焊以及平焊法兰、支管补强和支架的连接焊缝;注3:支管连接焊缝包括支管和翻边接头的受压焊缝;注4:对碳钢、不锈钢及铝合金无此要求;注5:适用于≥DN100的GB50517—2010 石油化工金属管道工程施工质量验收规范9。
压力管道安装施工有关无损检测的规定
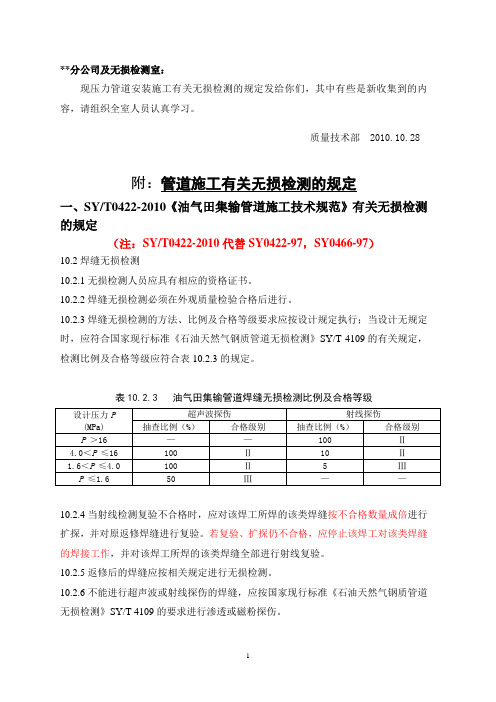
**分公司及无损检测室:现压力管道安装施工有关无损检测的规定发给你们,其中有些是新收集到的内容,请组织全室人员认真学习。
质量技术部 2010.10.28附:管道施工有关无损检测的规定一、SY/T0422-2010《油气田集输管道施工技术规范》有关无损检测的规定(注:SY/T0422-2010代替SY0422-97,SY0466-97)10.2焊缝无损检测10.2.1无损检测人员应具有相应的资格证书。
10.2.2焊缝无损检测必须在外观质量检验合格后进行。
10.2.3焊缝无损检测的方法、比例及合格等级要求应按设计规定执行;当设计无规定时,应符合国家现行标准《石油天然气钢质管道无损检测》SY/T 4109的有关规定,检测比例及合格等级应符合表10.2.3的规定。
表10.2.3 油气田集输管道焊缝无损检测比例及合格等级10.2.4当射线检测复验不合格时,应对该焊工所焊的该类焊缝按不合格数量成倍进行扩探,并对原返修焊缝进行复验。
若复验、扩探仍不合格,应停止该焊工对该类焊缝的焊接工作,并对该焊工所焊的该类焊缝全部进行射线复验。
10.2.5返修后的焊缝应按相关规定进行无损检测。
10.2.6不能进行超声波或射线探伤的焊缝,应按国家现行标准《石油天然气钢质管道无损检测》SY/T 4109的要求进行渗透或磁粉探伤。
二、《石油天然气建设工程施工质量验收规范站内工艺管道工程》SY/T 4203-2007有关无损检测的规定8.1.27 焊缝无损检测应由GB/T9445考试合格并取得相应资格证书的检测人员承担,评片应由取得Ⅱ级资格证书及以上的检测人员承担。
8.1.28 焊缝外观检查合格后应对其进行无损检测。
无损检测应按SY/T4109的管道执行。
8.1.29无损检测的比例及验收合格等级应符合设计要求。
如没有规定时,应按下列管道执行:a) 管道对接焊缝无损检测数量及合格等级应符合表8的规定。
b) 穿越站场道路的管道焊缝、试压后连头的焊缝应进行100%射线照相检查。
管道无损检测方案

管道无损检测方案1.概述本工程各种管道约15000米,分不锈钢SS304、SS316、碳钢、合金钢、PP/GRP、CS+PTFE 等多种材质;根据工艺、技术的不同要求,现场需拍片约40000张,硬度试验900点;本方案编制参考了招标文件中技术说明S-00-1540-002以及美国ASME标准1986;2.检验项目2.1射线探伤⑴射线探伤的检查比例,按照JGC在“技术说明”中的要求执行;⑵射线探伤的检查比例应符合设计要求及有关技术条件的规定;⑶要求100%检查的管道应逐个焊口整圈100%检查,确保不漏检;⑷要求10%抽检的管道应按相应焊工的相应焊缝按10%比例整圈检查;⑸管径≤3″厚度δ≤采用双壁双影椭圆透照,每个焊口间隔90°各拍一张,共两张;⑹管径=2″厚度≥8.74mm;管径=2-1/2″厚度≥9.53mm;管径=3″厚度≥11—13mm时应采用双壁单影分段透照,拍摄四张;⑺管径≥4″采用双壁单影或单壁单影透照,每个管口至少拍摄四张,T各种规格管道焊缝的拍摄数量应与现场测试检查程序中的要求一致;⑻胶片选用FUJI“100”型;采用的铅箔增感屏,当采用X射线探伤时,前屏厚,后屏厚;当采用γ射线探伤时,前后屏厚均为;⑼10″以下包括10″的管道探伤时,胶片规格为10″×4″;12″-72″的管道探伤时,胶片规格为12″×3-1/3″;有特殊要求的按要求执行;⑽所摄底片应无划伤,水迹,伪缺陷,当采用X射线时AB级的底片黑度D=-,当采用γ射线时底片黑度D=-,底片象质指数均应满足不同厚度的要求;底片上标识应齐全包括管段号,焊口号,焊工号,拍摄日期,返修次数;⑾用Ir192γ射线探伤时,应加装准直器,以减少散射线对底片像质的影响;⑿大口径管预制时,对接焊缝可采用环焊缝内透法或环缝外透法;现场组对焊缝,可采用双壁双影或双壁单影法,具体方法见图示;探伤设备的选用:当穿透厚度<20mm时用X光机探伤,其穿透力应能满足透照工件的要求;当穿透厚度≥20mm时用Ir192γ探伤机,其影像应与X光底片相同;探伤机的操作机构应安全可靠,源强应能满足探伤工艺要求;⒀环焊缝透照的最小焦距:LAB 级=10d×L22/3 k=T′/ T≯小口径管环焊缝椭圆透照的最小焦距Lmin=d×δ/ug+δL-焦距mm L2-管件表面到胶片距离mm d-焦点尺寸mmT-母材厚度mm T′-斜向透照厚度mm δ-工件厚度mmUg-几何不清晰度⒁焊口返修不得超过2次,返修部位经重新探伤后,胶片上应加返修标记,并按GB50235-97规范要求扩大抽查比例;⒂检验结束时应对所检查的部位进行确认并打上标记;渗透探伤⑴渗透探伤的检查比例应符合设计要求和有关技术条件的规定;⑵选用溶剂型渗透探伤试剂,检测试剂应低氯、低硫和磷要在有效期内,并有良好的检测性能,对工件无腐蚀作用,对人体基本无毒害作用;⑶对检测表面进行预清洗1分钟后施加渗透剂,渗透时间不少于5分钟;⑷渗透液用清洗剂去除,但不能往复擦拭;⑸显像检查必须在7-30分钟完成,显像剂施加应薄而均匀,不能在同一部位反复施加;⑹检验结束时,在相同条件下,用同型号检测试剂及对比试块再进行一次校验,以保证探伤结果的正确;3.焊缝硬度检查测试人员应有良好经验;焊缝的硬度检查在热处理24小时后检查.硬度测试数量:管径≤6″测一点8″<管径≤12″测2点管径≥14″测3点3.3硬度测试仪用经过计量鉴定在有效期内的数字式硬度测试仪;3.4HB≤2254.检验单位及人员资质担任本项目检测工作的检验单位具有江苏省建委和江苏省质量技术监督局授权的安装一级检测机构资质见资质证明;所有检验人员都具有江苏省锅炉压力容器无损检测考委会考核认可的相关项目的资质证明和江苏省建委和江苏省质量技术监督局考核颁发的无损检测人员上岗证见资质证明X射线探伤和同位素检查的工程师为经全国锅炉压力容器无损检测考委会考核发证的高级人员见资质证明;5.检测仪器见表6.检测过程和检验资料:检验报告须提交JGC,格式事先须经JG-C批准;所有需无损检测的焊口应由现场质检员指定并确认;原始资料和检验报告都应画图准确,数据清楚,用词确切,签字齐全,并经过无损检测技术负责人审核;原始记录还应详细写明工件材质,厚度,焊接方式,无损检测的操作条件,缺陷的性质,尺寸及部位;7.安全措施射线机、r源的现场存放:r源除固定位置存放外,还有专门的铅罩,放在铝内并上锁,实行双人双锁保管;X射线机、r探伤机的领用:射线探伤现场申报:射线探伤防护区的划定:R-距离 A-r源强度毫居里R2=P射线照射区的安全防护:射线探伤人员的岗位职责:射线探伤人员的安全防护:8.发生意外事故的处理:若因违反操作规程或其它原因造成事故,应维护好现场,不得私自处理;应上报公安、卫生防疫部门拟定故障排除方案,及时处理;。