管道焊缝无损探伤拍片数量的确定
管道焊口无损探伤

管道焊口无损探伤一、管道焊缝应按照设计要求的检验方法和数量进行无损探险伤二、管口焊接含量取定可参考下表:序号项目10米直管焊口含量(个)10米管件焊口含量(个)单根管取定长度(m)碳钢、不锈钢、铬钼钢、有缝低温钢管、≤DN2501.27 20.6 6碳钢、不锈钢、铬钼钢、有缝低温钢管、≥DN3001 20.6 8碳钢板卷管、DN200~600 1.56 20.6 6.4碳钢板卷管、DN700~900 1.96 20.6 6.4碳钢板卷管、DN1000~1400 2.48 20.6 4.8碳钢板卷管、DN1600~3000 2.38 20.6 4.8螺旋卷管0.67 20.6 12三、无损探伤的拍片张数按设计规定计算的探伤焊缝总长度除以定额取定的胶片有效长度计算。
定额取定的胶片有效长度为250mm,设若计无明确规定,可参照下表计算,结算时按现场实际拍片张数计算。
管道焊口透视拍片张数表序号管外径底片规格张数序号管外径底片规格张数1 ≤89 1502 12 ≤1020 300 132 ≤133 1504 13 ≤1220 300 153 ≤159 2404 14 ≤1420 300 184 ≤273 300 4 15 ≤1620 300 205 ≤377 300 5 16 ≤1820 300 236 ≤478 300 6 17 ≤2020 300 257 ≤529 300 7 18 ≤2220 300 288 ≤630 300 8 19 ≤2420 300 309 ≤720 300 9 20 ≤2620 300 3310 ≤820 300 10 21 ≤2820 300 3511 ≤920 300 12 22 ≤3020 300 38四:管道探伤计算方法:每10米管道含有1.27个焊缝,X射线张数=1.27×延长米数×一圈管道所需的张数×0.2。
工艺管道焊接知识及拍片比例

工业管道焊接及拍片比例管道焊接对焊接方式和焊接质量,应按设计规定套用相应定额。
如设计无规定时,可参考以下规定套用相应定额项目。
1.Ⅰ、Ⅱ级焊缝以及管内壁清洁度要求严格,且焊后不易清理的管道(如透平机入口管、锅炉给水管、机组的循环油、控制油、密封油管道等)单面焊缝、宜采用氩电联焊。
合金钢管焊缝采用氩弧焊打底时,焊缝内侧宜充氩气保护。
2.奥氏体不锈钢管单面焊的焊缝,宜采用手工钨极氩弧焊打底,手工电弧焊填充盖面(氩电联焊)。
公称直径在50毫米以下的采用氩弧焊。
3.Ⅲ级以下焊缝碳钢管,公称直径在50毫米以下的(壁厚在3.5毫米以下)采用氧炔焊。
4.管道分类见表1注:⑴剧毒介质的管道按Ⅰ类管道。
⑵有毒介质,甲、乙类火灾危险物质的管道均升一类。
⑶“工作压力”项内任意为不分压力均为一级管道。
5.管口焊前预热和焊后热处理要求见表2。
注:⑴当焊接环境温度低于零度时,除规定壁厚必须作预热要求的金属外,其余金属壁厚也均应作适当的预热,使被焊接母材有手温感。
规定必须作预热要求的金属,定额项目内的预热消耗已考虑了温度变化因素,故不再增加预热。
⑵有应力腐蚀的碳素钢、合金钢,不论其壁厚条件,均应进行焊后热处理。
6.管口焊缝无损探伤计算规定数据:(1)管口焊接含量取定见表3。
(2)每个管口焊缝X光拍片张数,如无规定者可按表4计算。
注:⑴公称直径80毫米以下的管道焊缝X光透视检查拍片,一个焊口要求至少拍两张片。
定额中采用的胶片为85×300毫米的,实际上可用85×150毫米的胶片,执行定额时,人工和机械使用费壁变,材料费乘0.5系数。
⑵片子有效长度按片长减去搭接每边25毫米计算。
⑶管道焊口透视拍片的张数=管道等级规定的探伤百分比×焊口数量×张数(见表4)(3)管道各级焊缝射线探伤数量,应按设计规定计算。
如设计无规定时,按表5规定计算。
注:每条管线上最低探伤不得少于一个焊口。
钢管焊接焊口无损探伤拍片数量表
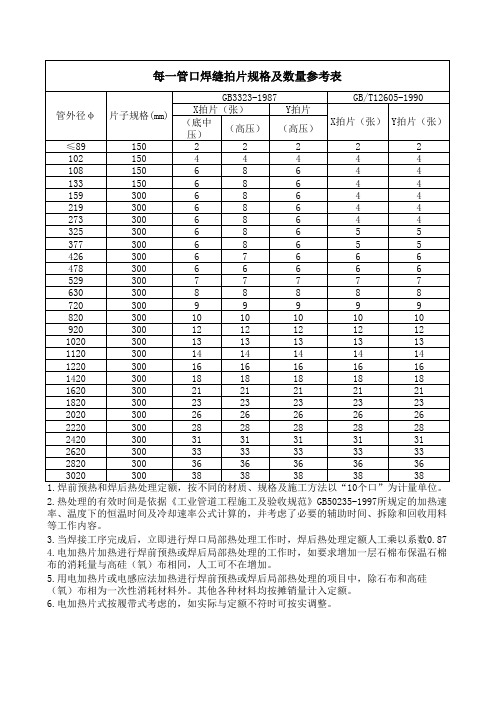
2.热处理的有效时间是依据《工业管道工程施工及验收规范》GB50235-1997所规定的加热速率、温度下的恒温时间及冷却速率公式计算的,并考虑了必要的辅助时间、拆除和回收用料等工作内容。
3.当焊接工序完成后,立即进行焊口局部热处理工作时,焊后热处理定额人工乘以系数0.87
4.电加热片加热进行焊前预热或焊后局部热处理的工作时,如要求增加一层石棉布保温石棉布的消耗量与高硅(氧)布相同,人工可不在增加。
5.用电加热片或电感应法加热进行焊前预热或焊后局部热处理的项目中,除石布和高硅(氧)布相为一次性消耗材料外。
其他各种材料均按摊销量计入定额。
6.电加热片式按履带式考虑的,如实际与定额不符时可按实调整。
管道焊接热处理及拍片比例表
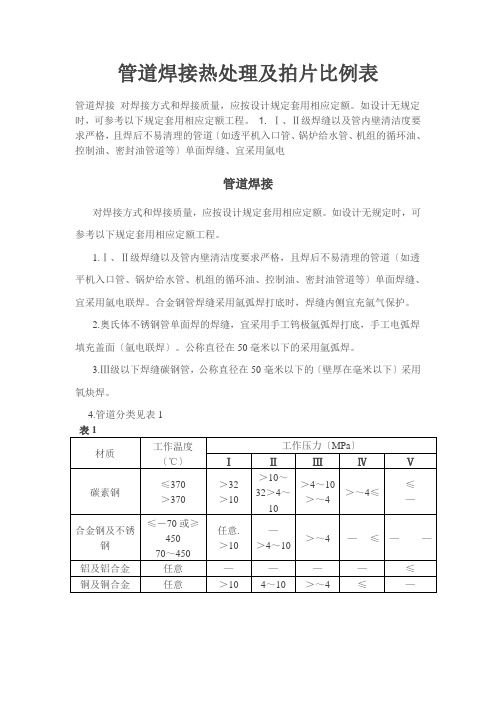
管道焊接热处理及拍片比例表
管道焊接对焊接方式和焊接质量,应按设计规定套用相应定额。
如设计无规定时,可参考以下规定套用相应定额工程。
1. Ⅰ、Ⅱ级焊缝以及管内壁清洁度要求严格,且焊后不易清理的管道〔如透平机入口管、锅炉给水管、机组的循环油、控制油、密封油管道等〕单面焊缝、宜采用氩电
注:⑴当焊接环境温度低于零度时,除规定壁厚必须作预热要求的金属外,其余金属壁厚也均应作适当的预热,使被焊接母材有手温感。
规定必须作预热要求的金属,定额工程内的预热消耗已考虑了温度变化因素,故不再增加预热。
⑵有应力腐蚀的碳素钢、合金钢,不管其壁厚条件,均应进展焊后热处理。
6.管口焊缝无损探伤计算规定数据:
〔1〕管口焊接含量取定见表3。
表3
注:⑴公称直径80毫米以下的管道焊缝X光透视检查拍片,一个焊口要求至少拍两张片。
定额中采用的胶片为85×300毫米的,实际上可用85×150毫米的胶片,执行定额时,人工和机械使用费壁变,材料费乘系数。
⑵片子有效长度按片长减去搭接每边25毫米计算。
注:每条管线上最低探伤不得少于一个焊口。
管道焊缝无损探伤拍片数量的确定
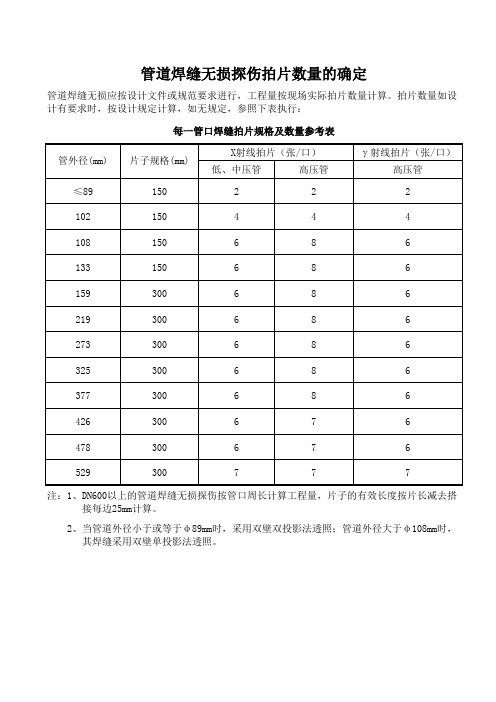
片数量如设
管道焊缝无损探伤拍片数量的确定
管道焊缝无损应按设计文件或规范要求进行,工程量按现场实际拍片数量计算。拍片数量如设 计有要求时,按设计规定计算,如无规定,参照下表执行:
每一管口焊缝拍片规格及数量参考表
管外径(mm)
片子规格(mm)
X射线拍片(张/口)
低、中压管
高压管
γ 射线拍片(张/口) 高压管
≤89
150
2
2
2
102
150
4
4
4
108
150
6
8
6
133
150
6
8
6
159
300
6
8
6
219
30068 Nhomakorabea6
273
300
6
8
6
325
300
6
8
6
377
300
6
8
6
426
300
6
7
6
478
300
6
7
6
529
300
7
7
7
注:1、DN600以上的管道焊缝无损探伤按管口周长计算工程量,片子的有效长度按片长减去搭 接每边25mm计算。
工艺管道焊接知识及拍片比例

工业管道焊接及拍片比例管道焊接对焊接方式和焊接质量,应按设计规定套用相应定额。
如设计无规定时,可参考以下规定套用相应定额项目。
1.Ⅰ、Ⅱ级焊缝以及管内壁清洁度要求严格,且焊后不易清理的管道(如透平机入口管、锅炉给水管、机组的循环油、控制油、密封油管道等)单面焊缝、宜采用氩电联焊。
合金钢管焊缝采用氩弧焊打底时,焊缝内侧宜充氩气保护。
2.奥氏体不锈钢管单面焊的焊缝,宜采用手工钨极氩弧焊打底,手工电弧焊填充盖面(氩电联焊)。
公称直径在50毫米以下的采用氩弧焊。
3.Ⅲ级以下焊缝碳钢管,公称直径在50毫米以下的(壁厚在3.5毫米以下)采用氧炔焊。
4.管道分类见表1注:⑴剧毒介质的管道按Ⅰ类管道。
⑵有毒介质,甲、乙类火灾危险物质的管道均升一类。
⑶“工作压力”项内任意为不分压力均为一级管道。
5.管口焊前预热和焊后热处理要求见表2。
注:⑴当焊接环境温度低于零度时,除规定壁厚必须作预热要求的金属外,其余金属壁厚也均应作适当的预热,使被焊接母材有手温感。
规定必须作预热要求的金属,定额项目内的预热消耗已考虑了温度变化因素,故不再增加预热。
⑵有应力腐蚀的碳素钢、合金钢,不论其壁厚条件,均应进行焊后热处理。
6.管口焊缝无损探伤计算规定数据:(1)管口焊接含量取定见表3。
(2)每个管口焊缝X光拍片张数,如无规定者可按表4计算。
注:⑴公称直径80毫米以下的管道焊缝X光透视检查拍片,一个焊口要求至少拍两张片。
定额中采用的胶片为85×300毫米的,实际上可用85×150毫米的胶片,执行定额时,人工和机械使用费壁变,材料费乘0.5系数。
⑵片子有效长度按片长减去搭接每边25毫米计算。
⑶管道焊口透视拍片的张数=管道等级规定的探伤百分比×焊口数量×张数(见表4)(3)管道各级焊缝射线探伤数量,应按设计规定计算。
如设计无规定时,按表5规定计算。
注:每条管线上最低探伤不得少于一个焊口。
管道焊口无损探伤预算计算方法

序号
管外径(mm)
底片规格(mm)
张数
序号
管外径(mm)
底片规格(mm)
张数
1
≤89
150
2
12
1020
300
13
2
≤133
150
4
13
1220
300
15
3
159
240
4
14
1420
300
18
4
≤273
300
4
15
1620
300
20
5
≤377
300
5
16
1820
300
23
6
478
管口焊接含量取定可参考下表:
项目
10米直管焊口含量(个)
10件管件焊口含量(个)
单根管取定长度(M)
碳钢、不锈钢、铬钼钢、钛管、有缝低温钢管、DN≤250
1.27
20.6
6
碳钢、不锈钢、铬钼钢、钛管、有缝低温钢管、DN≥300
1.00
20.6
8
碳钢板卷管、DN200┄600
1.56
20.6
6.4
碳钢板卷管、DN700┄900
1.96
20.6
6.4
碳钢板卷管、DN1000┄1400
Байду номын сангаас2.48
20.6
4.8
碳钢板卷管、DN1600┄3000
2.38
20.6
4.8
螺旋卷管
0.67
20.6
12
无损探伤的拍片张数按设计规定计算的探伤焊缝总长度除以定额的胶片有效长度计算。定额取定的胶片有效长度为250mm,若设计无明确规定,可参照表下计算,结算时按现场实际拍片张数计算。
燃气无损探伤
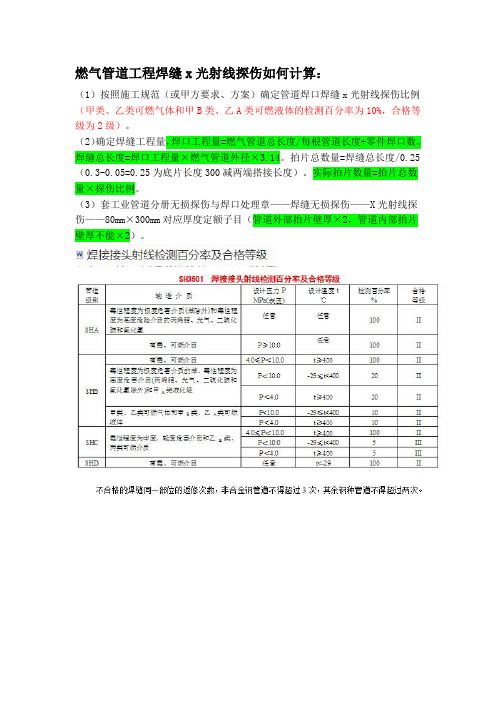
燃气管道工程焊缝x光射线探伤如何计算:
(1)按照施工规范(或甲方要求、方案)确定管道焊口焊缝x光射线探伤比例(甲类、乙类可燃气体和甲B类、乙A类可燃液体的检测百分率为10%,合格等级为2级)。
(2)确定焊缝工程量,焊口工程量=燃气管道总长度/每根管道长度+零件焊口数。
焊缝总长度=焊口工程量×燃气管道外径×3.14。
拍片总数量=焊缝总长度/0.25(0.3-0.05=0.25为底片长度300减两端搭接长度)。
实际拍片数量=拍片总数量×探伤比例。
(3)套工业管道分册无损探伤与焊口处理章——焊缝无损探伤——X光射线探伤——80mm×300mm对应厚度定额子目(管道外部拍片壁厚×2,管道内部拍片壁厚不能×2)。
钢管焊口不合格扩拍比例规定

《城镇燃气输配工程施工及验收规范》CJJ33-2005
5.2.9 焊缝内部质量的抽样检验应符合下列要求:
1 管道内部质量的无损探伤数量,应按设计规定执行。
当设计无规定时,抽查数量不应少于焊缝总数的15%,且每个焊工不应少于一个焊缝。
抽查时,应侧重抽查固定焊口。
2 对穿越或跨越铁路、公路、河流、桥梁、有轨电车及敷设在套管内的管道环向焊缝,必须进行100%的射线照相检验。
3当抽样检验的焊缝全部合格时,则此次抽样所代表的该批焊缝应为全部合格;当抽样检验出现不合格焊缝时,对不合格焊缝返修后,按下列规定扩大检验:
1)每出现一道不合格焊缝,应再抽检两道该焊工所焊的同一批焊缝,按原探伤方法进行检验。
2)如第二次抽检仍出现不合格焊缝,则应对该焊工所焊全部同批的焊缝按原探伤方法进行检验。
对出现的不合格焊缝必须进行返修,并应对返修的焊缝按原探伤方法进行检验。
3)同一焊缝的返修次数不应超过2 次。
管道焊缝射线探伤数量和合格级别

SY4056<<石油天然
气钢制管道对接焊缝射线照相及质量
分级>>
SY4065<<石油天然
气钢制管道对接焊缝超声波探伤及质量分级>>
焊缝的射线探伤可用超声波代替,合格级别与射线探伤相同,超声波探伤数量不少于射线探伤数量。
当选用超声波探伤时,应对超声波探伤部位作射线复验,复验数量为规定探伤数量5%,且不得少于一条焊缝。
设计压力大于1.6Mpa 的管道环焊缝宜选用射线探伤。
注汽管道的焊缝的无损探伤除符合上述规定外,合格级别为Ⅱ级的焊缝不得有未焊透缺陷,当选用超生探伤时,应对超生探伤的部位作20%的射线复验。
油田集输管道类别和等级划分方法
管道焊缝射线探伤数量和合格级别
焊接层数及焊条直径
焊道焊接应采用多层焊,焊道熔渣应清除干净,并进行外观检查,合格后可进行下道焊接。
低氢焊条在常温下4h应重新烘干,重复烘干次数不得超过两次。
焊口拍片规定

每个管口焊缝X光拍片张数,如无规定者可按计算。
* e& H( q9 b/ w. @2 \# W! U4 J0 j( A; `3 _, |- o* S0 e* ?管径Dg 15 20 25 32 40 50 65 80d* c* a7 x/ W) g! bX光片张2 2 2 2 2 2 2 27 {! |* l* P0 \3 h: @管径Dg 100 125 150 200 250 300 350 4003 m* X, j$ A8 c9 A* sX光片张3 3 34 4 45 58 j- K4 ~ g8 B6 U1 j: o0 w& c管径Dg 450 500 600 700 800 900 1000 1200* p( m/ \( g! zX光片张6 7 8 9 10 12 13 159 f+ N2 \1 T8 E6 G4 J" ^管径Dg 1400 1600 1800 2000 2200 2400 2600 2800- R0 K& Y x ^* M0 O6 {X光片张18 20 23 25 28 30 33 356 u' H, Q: H$ W- [% D. f管径Dg 3000 / n7 o" P& b, f @# PX光片张38 ! a! m) G. o( X& j注:⑴公称直径80毫米以下的管道焊缝X光透视检查拍片,一个焊口要求至少拍两张片。
定额中采用的胶片为85×300毫米的,实际上可用85×150毫米的胶片,执行定额时,人工和机械使用费不变,材料费乘0.5系数。
; B s" x) W3 g& u: x+ p ⑵片子有效长度按片长减去搭接每边25毫米计算。
本文来自: 造价新家园论坛() 详细出处参考:/thread-9274-1-1.html说明一、本定额的主要和适用范围为:1、厂区范围内的车间、装置、站、罐区及相互之间各种生产用介质输送管道。
管道焊缝无损探伤拍片数量的确定

管道焊缝无损应按设计文件或规范要求进行,工程量按现场实际拍片数量计算。拍片数量如设 计有要求时,按设计规定计算,如无规定,参照下表执行: 每一管口焊缝拍片规格及数量参考表 管外径(mm) ≤89 102 108 133 159 219 273 325 377 426 478 529 片子规格(mm) 150 150 150 150 300 300 300 300 300 300 300 300 X射线拍片(张/口) 低、中压管 2 4 6 6 6 6 6 6 6 6 6 7 高压管 2 4 8 8 8 8 8 8 8 7 7 7 γ 射线拍片(张/口) 高压管 2 4 6 6 6 6 6 6 6 6 6 7
注:1、DN600以上的管道焊缝无损探伤按管口周长计算工程量,片子的有效长度按片长减去搭 接每边25mm计算。 2、当管道外径小于或等于φ 89mm时,采用双壁双投影法透照;管道外径大于φ 108mm时, 其焊缝采用双壁单投影法透照。
片数量如设ຫໍສະໝຸດ
管道焊接拍片数量确定

管道焊接对焊接方式和焊接质量,应按设计规定套用相应定额。
如设计无规定时,可参考以下规定套用相应定额项目。
1.1、n级焊缝以及管内壁清洁度要求严格,且焊后不易清理的管道(如透平机入口管、锅炉给水管、机组的循环油、控制油、密封油管道等)单面焊缝、宜采用氩电联焊。
合金钢管焊缝采用氩弧焊打底时,焊缝内侧宜充氩气保护。
2•奥氏体不锈钢管单面焊的焊缝,宜采用手工钨极氩弧焊打底,手工电弧焊填充盖面(氩电联焊)。
公称直径在50毫米以下的采用氩弧焊。
3•川级以下焊缝碳钢管,公称直径在50毫米以下的(壁厚在3.5毫米以下)采用氧炔焊。
4. 管道分类见表1注:⑴剧毒介质的管道按类管道。
⑵有毒介质,甲、乙类火灾危险物质的管道均升一类。
⑶“工作压力”项内任意为不分压力均为一级管道。
5. 管口焊前预热和焊后热处理要求见表2。
也均应作适当的预热,使被焊接母材有手温感。
规定必须作预热要求的金属,定额项目内的预热消耗已考虑了温度变化因素,故不再增加预热。
⑵有应力腐蚀的碳素钢、合金钢,不论其壁厚条件,均应进行焊后热处理。
6. 管口焊缝无损探伤计算规定数据:(1)管口焊接含量取定见表3。
)每个管口焊缝光拍片张数,如无规定者可按表计算。
注:⑴公称直径毫米以下的管道焊缝光透视检查拍片,一个焊口要求至少拍两张片。
定额中采用的胶片为85X 300毫米的,实际上可用85X 150毫米的胶片,执行定额时,人工和机械使用费不变,材料费乘0.5系数。
⑵片子有效长度按片长减去搭接每边25毫米计算。
⑶管道焊口透视拍片的张数=管道等级规定的探伤百分比X焊口数量X张数(见表4)(3)管道各级焊缝射线探伤数量,应按设计规定计算。
如设计无规定时,按表5规定计算。
表5。
工艺管道射线探伤拍片数量计算
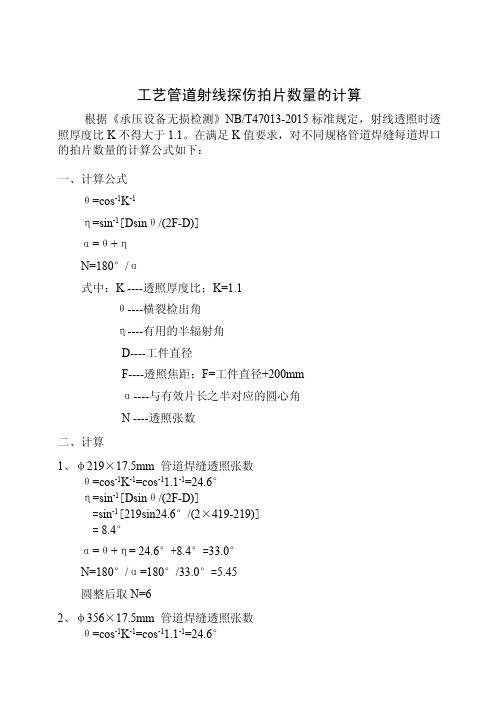
工艺管道射线探伤拍片数量的计算根据《承压设备无损检测》NB/T47013-2015标准规定,射线透照时透照厚度比K不得大于1.1。
在满足K值要求,对不同规格管道焊缝每道焊口的拍片数量的计算公式如下:一、计算公式θ=cos-1K-1η=sin-1[Dsinθ/(2F-D)]α=θ+ηN=180°/α式中:K----透照厚度比;K=1.1θ----横裂检出角η----有用的半辐射角D----工件直径F----透照焦距;F=工件直径+200mmα----与有效片长之半对应的圆心角N----透照张数二、计算1、φ219×17.5mm管道焊缝透照张数θ=cos-1K-1=cos-11.1-1=24.6°η=sin-1[Dsinθ/(2F-D)]=sin-1[219sin24.6°/(2×419-219)]=8.4°α=θ+η=24.6°+8.4°=33.0°N=180°/α=180°/33.0°=5.45圆整后取N=62、φ356×17.5mm管道焊缝透照张数θ=cos-1K-1=cos-11.1-1=24.6°η=sin-1[Dsinθ/(2F-D)]=sin-1[356sin24.6°/(2×556-356)]=11.3°α=θ+η=24.6°+11.3°=35.9°N=180°/α=180°/35.9°=5.03圆整后取N=6同理,φ273的管道焊缝也是透照6张φ325以上的管道焊缝也是透照8张级满足NB/T47013.2-2015标准的要求。
通过以上计算,可以看出,上述管道焊缝根据NB/T47013.2-2015标准,φ273只需要透照6张φ325以上的管道只需要透照8张即可满足标准要求。
管道焊接热处理及拍片比例表
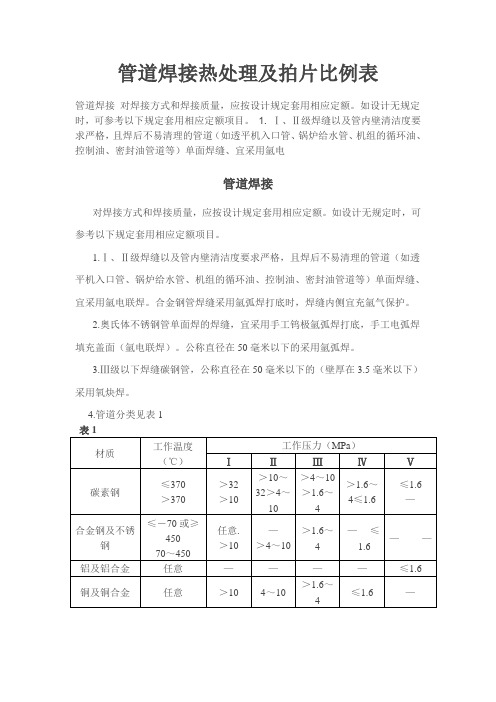
管道焊接对焊接方式和焊接质量,应按设计规定套用相应定额。如设计无规定时,可参考以下规定套用相应定额项目。1.Ⅰ、Ⅱ级焊缝以及管内壁清洁度要求严格,且焊后不易清理的管道(如透平机入口管、锅炉给水管、机组的循环油、控制油、密封油管道等)单面焊缝、宜采用氩电
管道焊接
对焊接方式和焊接质量,应按设计规定套用相应定额。如设计无规定时,可参考以下规定套用相应定额项目。
12CrMoV
ZG20CrMoV
ZG15CrMoV
≥6
200~300
250~300
>6
700~750
12Cr2MoWVB
12Cr3MoWVSiTiB
Cr5Mo
≥6
250~350
任意
750~780
铝及铝合金
任意
150~200
—
—
铜及铜合金
任意
350~550
—
—
注:⑴当焊接环境温度低于零度时,除规定壁厚必须作预热要求的金属外,其余金属壁厚也均应作适当的预热,使被焊接母材有手温感。规定必须作预热要求的金属,定额项目内的预热消耗已考虑了温度变化因素,故不再增加预热。
6.000
铝合金管
1.27
22.10
6.000
铝合金板卷管
1.27
21.50
6.000
无缝铜管
1.27
22.40
6.000
铜板卷管
2.00
22.60
5.000
(2)每个管口焊缝X光拍片张数,如无规定者可按表4计算。
表4
管径
Dg
15
20
25
32
40
50
65
80