精益管理的十大工具15页PPT
精益生产常用工具PPT课件
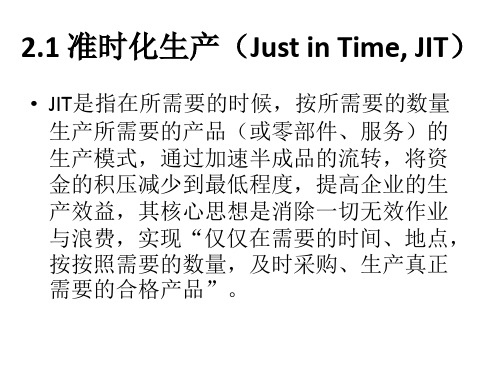
建立无间断操作流程
• “一个流”生产,即各工序只胡一个工作 在流动,使工序从毛坯到成品的加工过程 始终不停滞、不堆积、不超越的流动状态, 是一种工序间在制品向零挑战的生产管理 方式。“一个流”生产要以现场为管理中 心,实行三现主义(现场、现物、现策), 建立消防的安全体系、基于“5S”现场管 理思想形成文明生产环境,且要遵循以下 原则:物流同步、内部顾客、消除浪费。 “一个流”生产的实施要点,如表2-2所示。
• ③品质看板,主要内容有生产现场每日、每周、每月的 品质状况分析、品质趋势图、品质事故的件数及说明、 员工的技能状况、部门方针等。
• ④生产管理看板,包括作业计划、计划的完成率、生产 作业进度、设备运行与维护状况、车间的组织结构等内 容。
看板类型
• ⑤工序管理看板,主要指车间内在工序之间使用的 看板,如取料看板、下料看板、发货看板等。取料 看板,主要位于车间的各工序之间,其内容主要包 括工序序号、工序名称、工序操作者、下料时间、 数量、完工时间、首检等;发货状况管理看板,主 要位于生产车间,其内容主要包括工序序号、小组 名称、产品完成日期、发货日期、收货客户等内容。
按节拍生 严格按照一定的节拍进行生产,设法让“生产慢的设备快起来,生
3
产
产快的设备适当减慢速度”,使整个生产过程顺畅
站立式走 现场中坐着工作会产生很多辅助动作,增加浪费;要求作业人员站
4 动作业
立走动作业提高工作效率
培养多能 工人能够操作多台生产设备,培养多能工以均衡整个生产节拍,提升
5 工
员工素质
• 拉式生产方式是以生产看板、传递看板的看板 管理方式实现。
强调生产均衡化
• 杜绝浪费只是实现精益生产所必须要做的工作的1/3, 避免员工与设备的工作负荷过生、避免生产安排的 不均等,即在JIT实施过程中,生产均衡化同样重要。
精益生产十大工具PPT(精品课件).ppt
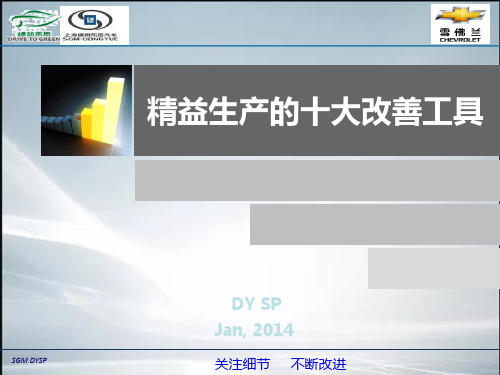
这是一种相当灵活的工具。既可以采用4M(人,材料,设备,方法)或6M(加上环
境和测量方法)为制造或生产型流程的进行根原因分析,又可用4P(价格,促销,地点,
产品)进行市场和销售的改善。
到目前为止,你已经识别出问题的根本原因,下一步准备实施相应的措施。所以你需
要一个行动计划。
SGM DYSP
关注细节 不断改进
恰当地使用上述九种工具会改进安全、质量、成本和交期等。这帮助公司拥有更多 的能力来生产新产品和提供服务。但哪一种产品和服务会给你带来市场优势呢?
SGM DYSP
关注细节 不断改进
10 卡诺模型
响应 客户之声/ 客户之思
当我们返回不断改进的起点,我们需要再次询问“什么是客户所需 要的?”。狩野纪昭教授的Kano模型帮助我们有效地回答这个问题。
驻足 现场
今天,“站在圈内”的练习是培训员工识别浪费非常有效的方法,为团队主管的日常 改进提供了结构化的方式,也为时间有限的高级主管提供了解现场的机会。
当你花上一段时间站在现场的大野耐一圈内,你会发现实际状态和目标状态之间的差 距。这时可采用帕累托原则确定缩小差距的开始区域。
SGM DYSP
关注细节 不断改进
SGM DYSP
关注细节 不断改进
9 海因里奇原则
关注 细微隐患
海因里奇原则(Heinrich Principle)教导我们如果要找出造成严重安全事故的根本 原因,就必须对最小的安全隐患予以重视。同样的原则也适用5S,消除浪费和增强质量 意识。精益管理需要每个人对最小的问题也要予以警惕。持续的教育和保持高度的敏感性 是必须的。
关注细节 不断改进
6 田口方法
田口方法主要运用 在产品设计开发中的试 验设计。田口玄一教授 采用费雪的试验设计的 思想来设法理解变异参 数的影响,而不仅仅采 用平均值。田口认为, 变异是研究的中心。
精益管理十大利器之十课件

精益管理十大利器之十
34
要运用看板管理方式来提高生产效益时, 必须先具备4个必要的前提条件: 1、后工序向前工序领用方式 2、平准化生产 3、品质保证 4、严守看板运行的规则
精益管理十大利器之十
35
看板管理的规则
1、后工序在必需的时候,只按必需的数量,向前 工序去领取必需的物品。
a如果没有看板,领取一概不能进行。 b超过看板枚数的领取一概不能进行。 c看板必须附在被运送的实物上。 2、前工序仅生产被后工序领取数量的物品。 3、不合格品绝对不能送到后工序。 4、必须把看板枚数减小到最小程度。 5、看板必须适应小幅度的需求变化。(通过看板 对生产进行微调整)
精益管理十大利器之十
18
八、减小批量的利器—快速换模
• 经济批量不经济; • 为何现在几乎所有的企业都
使用大批量生产的方法; • 减小批量将增加均衡生产的
可能性; • 减小批量可有效的缩短制造
周期。 • 方法——快速模具交换。
精益管理十大利器之十
19
快速换模七大手法
• 方法:彻底5S 内外有别,细分详算 消除螺栓运动 手动、脚和基准不动 取消调整 将转换标准化 取消换模
精益管理十大利器之十
16
制造型企业7大浪费:
1、制造过剩(成品库存,在制堆积品) 2、等待。(工艺不平衡) 3、搬运。(路线不合理) 4、加工。(物耗,非增值作业) 5、多余动作。(动作不合理) 6、库存。(资金占用) 7、不良品。(修理,检测重复)
精益管理十大利器之十
17
各种浪费中两种浪费最为严重 第一是人太多 第二是库存太大
· 初期清扫与自主维护
零 停滞
缩短 交货期长、延迟交货多 交货期 顾客投诉多,
精益生产之现场管理十大工具 ppt课件
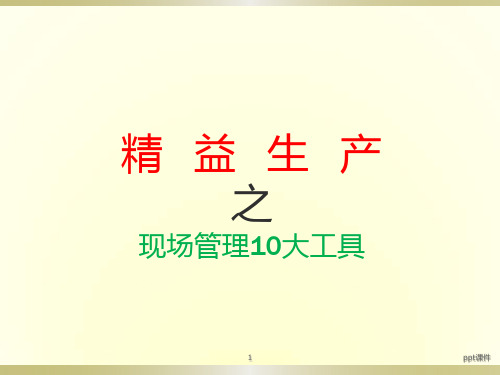
精益生产的精髓
5S
+
5
执行
ppt课件
八种浪费
1、过量生产(对在制品的控制); 2、库存(原材料、在制品、成品); 3、运输(无价值的转运); 4、等待(人等机器、机器等人、人等人、不均衡);
5、动作(换模具、换工装的工作时间、不标准动作对时间的浪费);
6、不必要的过程(如进货检验等不增值的行为); 7、次品(返工、返修、报废) 。 8.管理的浪费。
改善、交货、安全;
3、目视控制(视觉63%,听觉30%,嗅觉5%,触觉1.5%, 味觉0.5%)。
10
ppt课件
可视化管理量级:
A:B+如果异常,快速处置方式一目了然。 (处理方法、责任人、联系方式等)
B:C+正常和异常一目了然;(正常情况的标准)
C:周期性实时信息。
11
ppt课件
第三个工具——问题解决
6
ppt课件
精益屋
质量
质量
最优 看 板 ' 零 ' 库 存
交期
目标:零缺陷 工具:防错
自 动 化 防 错 零 缺 陷
目标:'零库存'(最优库存) 工具:看板 快速切换 制约管理
标准化作业 + 改善
5
+ 可视化管理 + 问题解决 +
7
ppt课件
精益生产的十大工具
第一个工具—5S 第六个工具—改善 第七个工具—防错
库存
材料清单
产能
原材料需求计划
生产计划
21
ppt课件
· 起源及定义:
看板起源于“仓储式超市”——大野耐一。 意思是:最优库存控制
· 生产计划的原理:
精益管理工具应用PPT课件

二、精益管理的基础理论
质量特性 质量特性是个非常重要的概念,有两点需要把握: 1.程序赋予的:是指产品生产过程所需的特性要求。 2.标准赋予的:指达到特定标准要求所需的特性要求。
1.“精”就是少投入、少消耗资源、少花费时间
内
涵
与
2.“益”就是多产出、多创造价值
本
质
3.归结起来,就是“用最少的投入创造最大的价值”, 就是“持续改善、追求卓越”
一、推进精益管理的背景和重要性
新形势下行业发展面临着增长速度回落、工商库存增加、结构空间 变窄、需求拐点逼近等四大难题。
推进精益管理是提升企业管理水平的需要
三、精益改善所使用的主要工具
5S现场管理
5S是一种管理方法,现代企业管理模式,5S即整理(SEIRI)、整顿(SEITON)、清 扫(SEISO)、清洁(SEIKETSU)、素养(SHITSUKE),又被称为“五常法则”。
国家局精益十佳评价标准: 1.制订办公场所现场管理办法,根据管理办法形成定期检查督导机制,得1分。 2.办公场所无不必要品(或未定位物品);办公桌、物品柜清洁有序,办公家具摆 放整齐,办公设施保持整洁;文件材料(含电子版)及时归、存档并设目录清单, 便于查找。符合3项得2分,符合2项得1分,其它情况不得分。
作业效果。
就是“持续改管善理、手追求段卓,越它” 与看板结合,成为丰田生产方式的重要组成部分。
Result(结果/个人感言) After Improvement “一不好”:指质量控制不好。 一、推进精益管理的背景和重要性 国家局精益十佳评价标准: 没有标准化,企业不可能维持在较高的管理水平。 符合3项得2分,符合2项得1分,其它情况不得分。 二、精益管理的基础理论 QC活动是融合应用管理思想、方法、工具,最为广泛、全面和经常的方法。 (7)一致性 (8)售后服务 (9)会意质量 (如果不看操作说明书,我们不知道压力的正常范围) Dept: Custom Interior 25%的人正在等待着什么; 制订办公场所现场管理办法,根据管理办法形成定期检查督导机制,得1分。 一、推进精益管理的背景和重要性
精益管理的十大工具
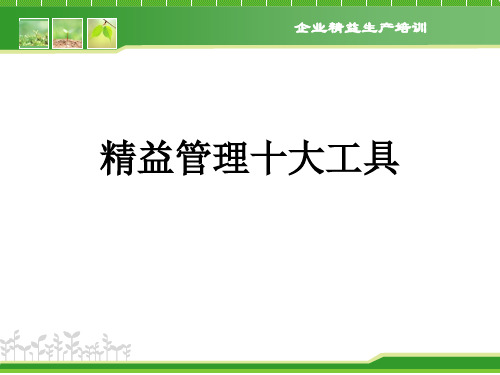
虽然精益生产管理是一个循序渐进、不断改
善的过程,但是熟悉这些工具对精益生产的实施
将会起到很大的帮助。
企业精益生产培训
企业精益生产培训
企业精益生产培训
精益管理十大工具
企业精益生产培训
精益生产的主要工具
“天下难事,必作于易;天下大事,必作于
细”。伴随着丰田汽车的神奇崛起,精益思想早
已被无数制造企业效仿和应用。那么,您是否真 正理解精益思想?企业推行精益管理需要具备哪 些条件?如何应对精益变革中的阻力?
企业精益生产培训
精益生产的主要工具
1、5S与目视化管理 2、全员生产维护(TPM) 3、准时化生产 4、标准作业
5、防错
企业精益生产培训
精益生产的主要工具
6、快速换型 7、看板管理
8、价值流分析
9、拉式系统 10、持续改善
企业精益生产培训
5S与目视管理
“5S”是整理(Seiri)、整顿(Seiton)、清扫
(Seiso)、清洁(Seikeetsu)和素养(Shitsuke)这5
种无库存的生产系统,或使库存达到最小的生产 系统。
企业精益生产培训
标准作业
有效地组合物质、机器和人,“丰田生产方
式”称这种组合过程为作业组合,这一组合汇总
的结果就是标准作业。
标准作业是以人的动作为中心、以没有浪费 的操作顺序有效地进行生产的作业方法。它由节 拍时间(Take Time,T﹒T)、作业顺序、标准手 持三要素组成。
是日本人在70年代提出的,是一种全员参与的生
产维修方式,其主要点就在“生产维修”及“全
员参与”上。通过建立一个全系统员工参与的生 产维修活动,使设备性能达到最优。
企业精益生产培训
精益生产管理的十大工具和实施步骤

精益生产管理的十大工具和实施步骤一、价值流分析(Value Stream Mapping):价值流分析是了解和改进产品或服务的价值流程的方法。
通过绘制价值流地图,可以清楚地看到从原料到最终交付的整个价值流程,以及其中存在的浪费和瓶颈。
通过分析和改进价值流程,可以实现生产过程的优化。
二、5S整理法:5S整理法是一种是一种工作环境整理和管理方法。
通过整理、整顿、清扫、标准化和维护这五个步骤,可以创造一个整洁、有序、高效的工作环境,提高工作效率和质量。
三、流程改进活动(Kaizen):Kaizen是一种小创新的方法,通过持续改善工作流程,减少或消除浪费,提高效率和质量。
它鼓励员工提出改进建议,并通过小规模试验和迭代改进的方式,不断优化工作流程。
四、单点教导法(One-Piece Flow):单点教导法是一种用来实现流程连续化和缩短生产周期的方法。
通过将生产任务拆分为较小的单元,并且一个接一个地完成,可以减少库存和等待时间,提高生产效率和质量。
五、标准化工作(Standardized Work):标准化工作是一种明确工作内容和作业要求的方法。
通过对工作流程进行详细的规范和记录,包括工作步骤、所需时间和所需材料等,可以确保工作一致性和质量,减少浪费和错误。
六、自动化(Automation):自动化是一种利用机械装置和技术来替代人力的方法。
通过引入自动化设备和技术,可以实现生产过程的标准化和高度自动化,提高生产效率和稳定性。
七、质量管控(Quality Control):质量管控是一种确保产品或服务质量的方法。
通过建立质量控制流程和标准,进行检验和测试,可以及时发现和纠正质量问题,保证产品或服务的一致性和可靠性。
八、产能平衡(Capacity Balancing):产能平衡是一种调整生产线中各个工位和机器的产能,以适应需求变化的方法。
通过平衡各个工位和机器的产能,可以避免瓶颈和浪费,提高整个生产线的效率。
九、持续改进(Continuous Improvement):持续改进是一种通过不断寻找和解决问题,优化工作流程和提高效率的方法。
精益生产管理十大工具

精益生产管理十大工具在现代制造业中,精益生产管理是一种重要的管理思想,旨在提高生产效率、降低成本、提高产品质量。
为了实现这一目标,精益生产管理应用了各种工具和技术。
以下是精益生产管理中最常用的十大工具:价值流映射价值流映射是一种识别和消除生产过程中浪费的工具。
通过绘制价值流图,生产管理者可以清晰地看到价值创造的流程,并找出其中的浪费,进而采取措施进行改善。
小批量生产采用小批量生产可以减少库存、降低生产成本,并提高生产效率。
通过减少生产周期,企业可以更加灵活地响应市场需求。
标准化工作制定和遵守标准化工作流程可以确保生产过程稳定、高效。
员工们在遵循标准操作流程的情况下工作,有助于减少产生的错误和浪费。
5S整理法5S整理法是一种工厂管理方法,通过整顿、清扫、清洁、清理、素养的五个步骤,使工作环境整洁有序,提高工作效率。
建议箱建议箱是鼓励员工提出改进建议的工具。
通过员工的参与,可以发现生产过程中存在的问题和改进的机会,从而不断优化生产流程。
好的团队沟通有效的团队沟通是实现精益生产管理的重要前提。
通过团队沟通,可以加强团队协作,促进信息共享,提高生产效率。
周生产会议定期召开周生产会议可以及时跟踪生产进度,识别问题并制定解决方案。
通过会议记录和持续改进,可以提高生产计划的准确性。
一体化生产计划一体化生产计划是整合市场需求、生产能力、物流等因素的生产计划模式。
通过一体化计划,企业可以优化资源配置,提高生产效率。
质量控制质量控制是确保产品质量符合标准的一系列措施。
通过质量控制,可以降低次品率,提高产品质量,增强企业竞争力。
持续改进持续改进是精益生产管理的核心理念。
通过不断地发现问题、分析原因、提出改进建议并实施改进措施,企业可以不断提高生产效率和产品质量。
以上就是精益生产管理中最常用的十大工具。
通过合理应用这些工具,企业可以不断优化生产流程,提高生产效率,降低成本,实现持续增长。
精益生产之精益工具概述(PPT 45张)
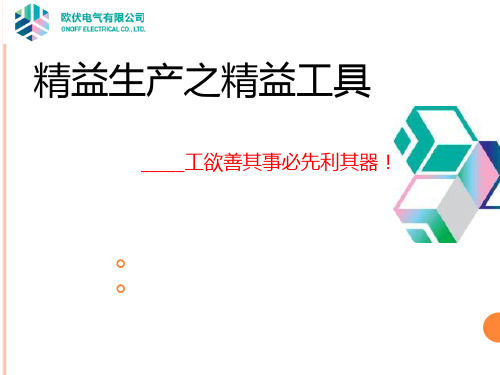
Dept 2
OUT
IN
OUT
IN
DONE
Dept 4
IN OUT
工作单元流程
DONE
4
3
单元内自然分组
IN
1
2
DONE
43
工作顺序可能与工 件流动顺序不同
IN
12
6
第一单元 识别浪费的九种关键工具
• 按批次排队加工
Process
A
Process
B
10 minutes 十分钟
10 minutes 十分钟
六、标准工作单
• 标准工作单显示你期望达到的以下目标:
– 工作单元的布局 – 工作单元中的人数 – 每人工作顺序 – 标准的生产中库存数量和位置
• 清楚‘应该’情况,与目前状况比较,发现浪费
17
第一单元 识别浪费的九种关键工具
七、标准工作组合票
• 组合票可显示
– 工作顺序 – 可用时间
Mandrel Cell - Op. A - 45 series - 2/3/00
16
4 5
换档总装
2 2 7 3 12
5
16
3 4
手制动手柄
• 谁负责做什么?我们需要多少人来做?
5 5 6 10 8
20
4 6
控制箱
14
第一单元 识别浪费的九种关键工具
四、“面条”图
• 目的:帮助了解人员行动 • 暴露人员动作及运输中的浪费
• 旁观流程,发现浪费 • 对工作单元中的每一个人画出 一张“面条”图000
real demand per shift
257
with backup data
每班的实际需求
精益管理工具应用ppt课件

;.
23
三、精益改善所使用的主要工具 自主改善
Name: Max Alley
My Idea
Dept: Engineering Date: 11/20/07
Before Improvement(改善前)
After Improvement(改善后)
We did not know the proper air pressure at the
围)
Anyone can see at a glance if the air
pressure is not acceptable.(任何人看一
眼,就知道压力是否在正常范围)
;.
24
三、精益改善所使用的主要工具 自主改善
;.
25
三、精益改善所使用的主要工具 自主改善(形象展示)
;.
26
三、精益改善所使用的主要工具 自主改善
新形势下行业发展面临着增长速度回落、工商库存增加、结构空间变窄、需求拐点逼近等四大 难题。
推进精益管理是提升企业管理水平的需要
推行精益管理的目的 和意义
推进精益管理是促进企业转型的需要
推行精益管理是挖掘企业发展潜力的需要
;.
3
二、精益管理的基础理论
精益管理的切入点
管理的定义 所谓管理,是指利用所拥有的资源,通过过程控制,完成增值或创造价值的过程。 这个定义突出强调了三个方面:即配置资源、过程控制和价值创造。
➢ 管理的本质,是“配置资源”。 ➢ 过程控制的思想,是对数据的收集、整理和
分析,监控过程的运行状态和水平,通过过 程管理,降低结果风险。 ➢ 价值创造的核心,是以最小的投入,获取最 大的利润。
;.
4
二、精益管理的基础理论
精益生产之现场管理十大工具课件
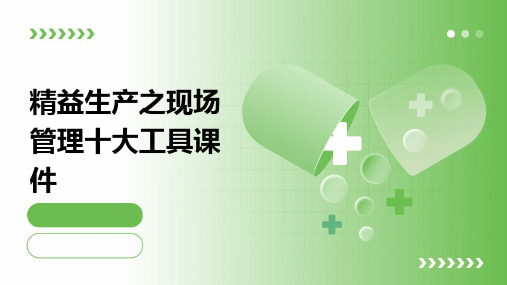
设计看板样式
根据信息内容,设计 看板的样式和布局, 确保信息清晰易懂。
制作看板
根据设计好的样式, 制作看板,并确保信 息的实时更新。
培训员工
培训员工如何使用看 板,了解看板上的信 息含义和作用。
监控与改进
定期检查看板的运行 情况,发现问题及时 处理和改进,以提高 生产效率和管理水平 。
08
价值流图析
精益生产之现场 管理十大工具课 件
目录
• 5S管理 • 目视化管理 • 标准化管理 • 快速换模 • 防错法
目录
• 单元化生产 • 看板管理 • 价值流图析 • 全员生产维护(TPM) • 持续改进活动(Kaizen)
01
5S管理
定义与特点
5S管理是一种现场管理方法,包括整理(Sort)、整 顿(Straighten)、清扫(Sweep)、清洁( Sanitize)和素养(Sustain)五个方面。
5S管理旨在创造一个整洁、有序、安全的工作环境, 提高工作效率,降低浪费和成本。
5S管理强调标准化、规范化和持续改进,通过不断的 整理、整顿和清扫,保持现场整洁有序,提高工作效
率和员工素养。
5S管理的重要性
提高工作效率
整洁有序的工作环境有助于减少寻找物品的 时间,提高工作效率。
提升员工素养
通过实施5S管理,培养员工养成规范、有序 的工作习惯,提高员工素养。
优化流程
通过价值流图析,企业可以全面 了解产品或服务的整个流程,从 而发现潜在的优化点,提高生产 效率。
战略规划
价值流图析可以为企业提供战略 规划的依据,帮助企业制定更加 科学、合理的生产计划。
价值流图析的实施步骤
确定研究对象
明确要分析的产品或服务,了解其整个生 产流程。
精益生产十大工具PPT(共12张PPT)
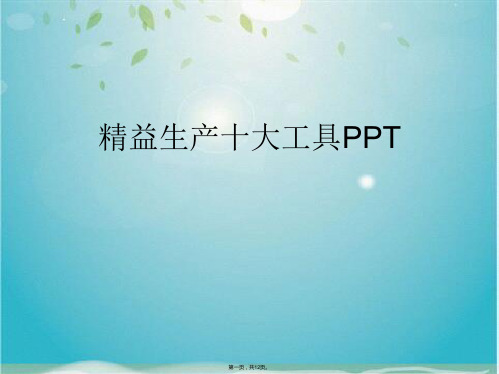
改进后,你需要有方法定
石川图(又称鱼骨图或因果图)是由 质量管理专家石川馨教授于1960年代提出,石川馨是川崎钢铁公司质量过程管理的先驱者,也是现代管理奠
基人之一是。 的心理学家,以其
期检查和评估以防止流程
但是,我们如何防止自满,保持不断改进呢?
田口认为人,类变需异是求研层究次的中理心论。而闻
其思路是在你的工厂尽可能防止产生视野阻隔。
目视化 管理
现场目视化程度越高,越多的问题可以得到解决,流程也就越稳定。但是,我们如何防止自满,保持不断 改进呢?
第九页,共12页。
9 海因里奇原则
关注 细微隐患
海因里奇原则(Heinrich Principle)教导我们如果要找出造成严重安全事故的根本原因,就必须对最 小的安全隐患予以重视。同样的原则也适用5S,消除浪费和增强质量意识。精益管理需要每个人对最小的问 题也要予以警惕。持续的教育和保持高度的敏感性是必须的。
恰当地使用上述九种工具会改进安全、质量、成本和交期等。这帮助公司拥有更多的能力来生产 新产品和提供服务。但哪一种产品和服务会给你带来市场优势呢?
第十页,共12页。
10 卡诺模型
响应 客户之声/ 客户之思
当我们返回不断改进的起点,我们需要再次询问“什么是客户所需要的?”。狩野纪 昭教授的Kano模型帮助我们有效地回答这个问题。
找出 根本原因
这是一种相当灵活的工具。既可以采用4M(人,材料,设备,方法)或6M(加上环境和测量方法)为 制造或生产型流程的进行根原因分析,又可用4P(价格,促销,地点,产品)进行市场和销售的改善。
到目前为止,你已经识别出问题的根本原因,下一步准备实施相应的措施。所以你需要一个行动计划。
第四页,共12页。