铣加工参数自动计算表
UG数控加工的参数设置【大全】

切削参数打开“切削参数”图标,系统会显示“切削参数”对话框,第一栏:策略(既一些加工参数值的设定)1、切削方向:顺铣:刀具一般多采用顺铣,因为由顺铣加工完成时工件的表示光洁度比较好!另一个原因是顺铣时刀具的受损要比逆铣轻的多!所以多采用顺铣。
从外向内用逆洗。
从内向外用顺洗。
2、逆铣:多适用于一些粗糙的工件开粗,加工完成后工件的光洁度不好,而且刀具受损严重!所以一般不利用逆铣。
3、切削角:当使用“单向式”切削,“往复式”切削“单向带轮廓”铣切削三种方法时在切削参数里才显示切削角的定义,其意思为所生成的刀轨是平行X向为零,平行于Y向为90度,可根据自己的要求定义切削角度,多采用45度斜进刀可在切削角下的度数栏内,输入所定义的角度值,如果想看一下角度方向时,可点示显示切削方向的图标。
3、壁:当使用“单向铣削”,“往复式铣削”和“跟随周边”时切削参数里面才有壁选项,“单向”和“往复”铣削里面只有三项。
其一:无,它的意思为只切削腔,不去清壁,其二,在起点:刀具在下刀后先把壁清理完,然后再切削腔。
其三,在终点:刀具在下刀后把腔切削完成后,到最后一刀把壁清理干净,无论是“起点”清壁还是“终点”清壁,都是以层为单位,如果没有“自动”清壁的情况使用在“终点”清壁。
如果有“自动”清壁时优先使用“自动”清壁,“自动”清壁的意思是:系统给计算一个最适合清壁时清壁。
4、添加精割削刀路数本功能是以UG5.0版本才增加的新功能,它能有效的控制几何体的余量更加均匀,所以在型腔铣开粗时打上对号,让其忝加“1”刀路数,精加工的步距可根据情况而定,但本步距最好要小一些。
5、毛坯:1、本栏下的毛坯距离和外部(面铣削对话框中)毛坯距离相同。
2。
Extend to part outline :是指毛坯延展,默认延展至体的最大外形轮廓线因此我们不采用。
3、合并距离:当所加工的平面为两个或两个以上时,指定距离大于或等于两个面之间的距离,想要学习UG编程领取学习资料在群496610960可以帮助你两个面刀路会自动合并成一个刀路,但要求所选择的面必须在同一高度上,所指定的值可使用刀具的百分比或mm。
机加工时间计算器

机加工时间计算器
(最新版)
目录
1.机加工时间计算器的概念和作用
2.机加工时间计算器的主要参数和输入数据
3.机加工时间计算器的使用方法和步骤
4.机加工时间计算器的应用实例
5.机加工时间计算器的优缺点及发展趋势
正文
一、机加工时间计算器的概念和作用
机加工时间计算器是一种用于计算机械加工过程中各个工序所需时间的工具,可以帮助工程师和操作人员快速、准确地估算出零件加工所需的时间,从而提高生产效率、降低成本。
二、机加工时间计算器的主要参数和输入数据
机加工时间计算器主要需要输入以下数据:零件的工艺路线、各工序的加工方式、切削速度、进给速度、刀具类型、刀具直径等。
根据这些数据,计算器将自动计算出每个工序所需的加工时间。
三、机加工时间计算器的使用方法和步骤
1.输入零件的工艺路线:首先需要输入零件的工艺路线,包括各个工序的加工方式、加工顺序等。
2.输入加工参数:根据工艺路线,输入各个工序的加工参数,如切削速度、进给速度、刀具类型、刀具直径等。
3.启动计算:输入完所有数据后,启动计算器,计算器将自动计算出每个工序的加工时间。
4.查看结果:查看计算结果,确认无误后,可将结果用于制定生产计划、调度人员和设备等。
四、机加工时间计算器的应用实例
以加工一个轴类零件为例,其工艺路线包括:铣削外圆、车削端面、钻孔、攻丝等工序。
输入相应的数据后,计算器将自动计算出每个工序所需的时间,从而帮助工程师制定合理的生产计划。
五、机加工时间计算器的优缺点及发展趋势
优点:计算速度快、准确性高,有助于提高生产效率、降低成本。
缺点:需要输入的数据较多,对操作人员的技术水平有一定要求。
工时计算方法大全(各机床工时、各工序工时)
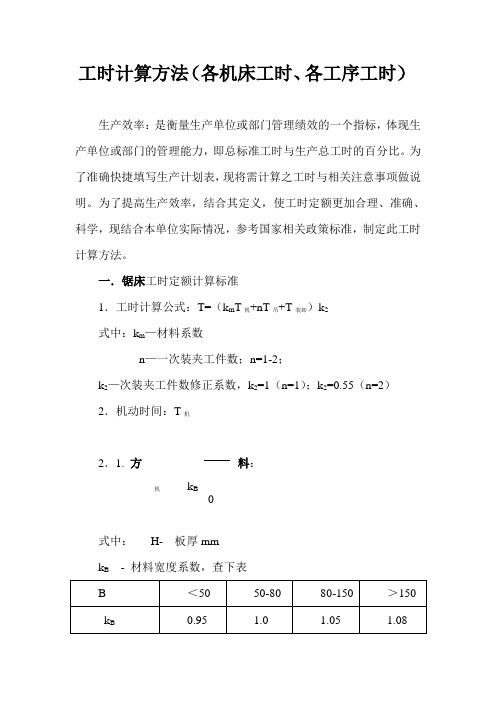
工时计算方法(各机床工时、各工序工时)生产效率:是衡量生产单位或部门管理绩效的一个指标,体现生产单位或部门的管理能力,即总标准工时与生产总工时的百分比。
为了准确快捷填写生产计划表,现将需计算之工时与相关注意事项做说明。
为了提高生产效率,结合其定义,使工时定额更加合理、准确、科学,现结合本单位实际情况,参考国家相关政策标准,制定此工时计算方法。
一.锯床工时定额计算标准1.工时计算公式:T=(k m T 机+nT 吊+T 装卸)k 2 式中:k m —材料系数n —一次装夹工件数;n=1-2;k 2—次装夹工件数修正系数,k 2=1(n=1);k 2=0.55(n=2) 2.机动时间:T 机 2.1. 方料:式中: H- 板厚mm k B - 材料宽度系数,查下表T 机=k BH22.2.棒料:式中D —棒料外径 mm2.3. 管料:式中d 0—管料内径;mm2.4..方管:式中:H—方管外形高mm ;H 0—方管内腔高mm ; B 0—方管内腔宽mm ;3.吊料时间:4.装卸料时间及其它时间:T机=D24T 机=D —d 02 2410000T 机=H—H 0*B 0208000T吊=L 1000 T装卸LD综上所述:方料:T=(0.12+n0.0519H+0.001L )k 2-0.00013 H 0*B 0 (min ) 圆料:T=(0.12+n0.0429D+0.001L )k 2-0.0001 d 02 (min ) n —一次装夹工件数;n=1-2;k 2—次装夹工件数修正系数,k 2=1(n=1);k 2=0.55(n=2)二.剪板冲压折弯工时定额计算标准1..剪板工时定额计算方法剪板单件工时定额:a —每块工时系数、见表b —剪角次数剪板工时系数表=0.12+1800840T =k *a+b a3注:准备工时按100件基数计算,每件0.2,共计200分剪板毛刺工时:T=0.3 + 处理长度/400剪板校正T校=k*T材料系数K=1~1.52.冲压每冲一次工时3..折弯工时定额计算方法折弯工时定额:t2=Σa i折弯工时定额系数表注:规格栏中,为折弯长度,a为每折一刀的工时(理论计算:每刀0.15分×折1.5=0.225+0.2=0.425→0.5)↓准备工时三.风割焊接工时定额计算标准1.风割工时公式:修磨工时含补焊工时: T 修磨 = T 风割 /22.焊接单件工时: T 焊接=T 工件装卸+T 点焊+ T 全焊 2.1 装卸工件工时:T 工件装卸=(T 01+0.2n )B式中:T 01—装卸基本工时;(取T 01=0.2); n-- 工件数 B-- 重量系数(见表)2.2. 点焊单件工时:T 点焊= T 02+0.1J+0.1N式中:T 02—点焊基本工时;J —点焊数;N —点焊时工件翻转次数;2.3. 全焊单件工时:T 全焊= T 03+0.1M+0.1N+L Σ/200+0.2NC 式中:T 03—全焊基本工时;M —焊缝段数;N —全焊时工件翻转次数;L Σ--焊缝长 NC---焊接参数调节次数注:小件装卸与点焊工时合并,统称点焊工时; 重量系数(B )T风割=风割长度×3+1.5V1、飞溅按焊接工时的二分之一计算+0.12、校正按焊接工时的二分之一计算+0.13、有辅助工帮助表卸模,从焊接工时中分取三分之一4、焊接有准备工时按每项20分钟5、点焊螺母按0.5分钟一个四.钻床工时定额1、T=kT机+ T装卸其中k—难度系数有工差要求k=1.5 有深度要求k=1.1 扩孔及攻丝k=0.82、机动时间:T机注:L/D≥8时,须另增排屑时间60%。
锯片铣刀切削速度计算【干货经验】
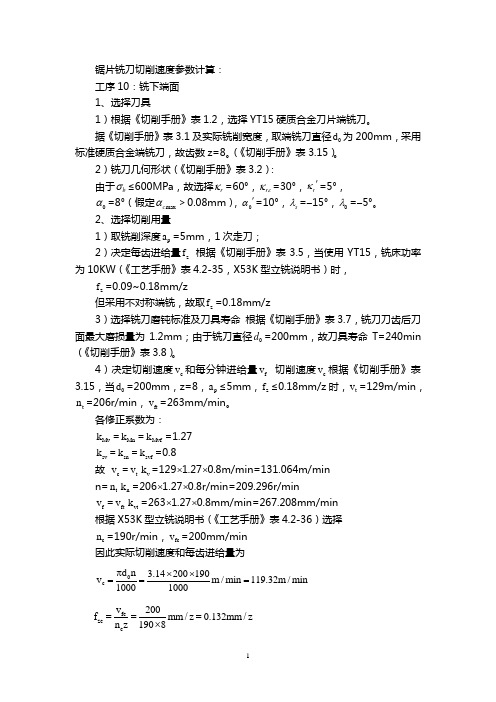
锯片铣刀切削速度参数计算: 工序10:铣下端面 1、选择刀具1)根据《切削手册》表1.2,选择YT15硬质合金刀片端铣刀。
据《切削手册》表3.1及实际铣削宽度,取端铣刀直径0d 为200mm ,采用标准硬质合金端铣刀,故齿数z=8。
(《切削手册》表3.15)。
2)铣刀几何形状(《切削手册》表3.2):由于b σ≤600MPa ,故选择r κ=60°,r εκ=30°,r κ'=5°,0α=8°(假定max c α>0.08mm ),0α'=10°,s λ=-15°,0λ=-5°。
2、选择切削用量1)取铣削深度p a =5mm ,1次走刀;2)决定每齿进给量z f 根据《切削手册》表3.5,当使用YT15,铣床功率为10KW (《工艺手册》表4.2-35,X53K 型立铣说明书)时,z f =0.09~0.18mm/z但采用不对称端铣,故取z f =0.18mm/z3)选择铣刀磨钝标准及刀具寿命 根据《切削手册》表3.7,铣刀刀齿后刀面最大磨损量为1.2mm ;由于铣刀直径0d =200mm ,故刀具寿命T=240min (《切削手册》表3.8)。
4)决定切削速度c v 和每分钟进给量f v 切削速度c v 根据《切削手册》表3.15,当0d =200mm ,z=8,p a ≤5mm ,z f ≤0.18mm/z 时,t v =129m/min ,t n =206r/min ,ft v =263mm/min 。
各修正系数为:Mv k =Mn k =Mvf k =1.27 sv k =sn k =svf k =0.8故 c v =t v v k =129⨯1.27⨯0.8m/min=131.064m/min n=t n n k =206⨯1.27⨯0.8r/min=209.296r/minf v =ft v vt k =263⨯1.27⨯0.8mm/min=267.208mm/min 根据X53K 型立铣说明书(《工艺手册》表4.2-36)选择c n =190r/min ,fc v =200mm/min 因此实际切削速度和每齿进给量为0c d n 3.14200190v m /min 119.32m /min 10001000π⨯⨯=== fc zc c v 200f mm /z 0.132mm /z n z 1908===⨯5)校验机床功率 根据《切削手册》表3.23,当b σ<560MPa ,e a ≤138mm ,p a ≤5.9mm ,0d =200mm ,z=8,f v =200mm/min ,近视为cc P =7.8KW根据X53K 型立铣说明书(《工艺手册》表4.2-35),机床主轴允许的功率为cM P =10⨯0.85KW=8.5KW故cc P <cM P ,因此所选择的切削用量可以采用,即p a =5mm ,f v =200mm/min ,n=190r/min ,c v =119.32m/min ,z f =0.132mm/z 。
数控铣加工参数自动计算表

机加工时间计算器
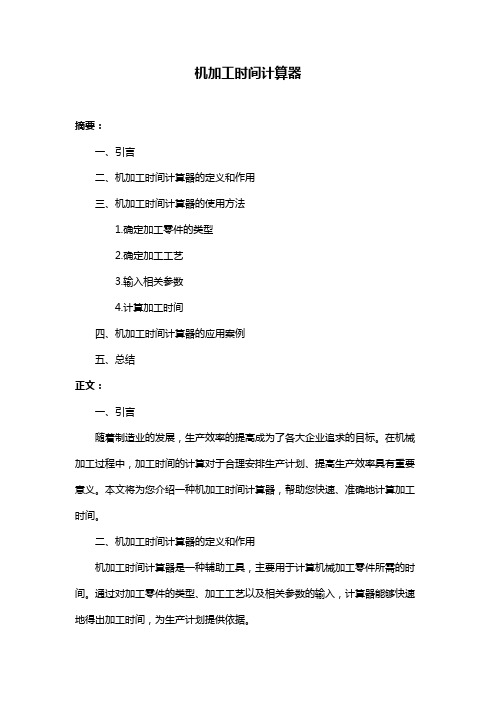
机加工时间计算器摘要:一、引言二、机加工时间计算器的定义和作用三、机加工时间计算器的使用方法1.确定加工零件的类型2.确定加工工艺3.输入相关参数4.计算加工时间四、机加工时间计算器的应用案例五、总结正文:一、引言随着制造业的发展,生产效率的提高成为了各大企业追求的目标。
在机械加工过程中,加工时间的计算对于合理安排生产计划、提高生产效率具有重要意义。
本文将为您介绍一种机加工时间计算器,帮助您快速、准确地计算加工时间。
二、机加工时间计算器的定义和作用机加工时间计算器是一种辅助工具,主要用于计算机械加工零件所需的时间。
通过对加工零件的类型、加工工艺以及相关参数的输入,计算器能够快速地得出加工时间,为生产计划提供依据。
三、机加工时间计算器的使用方法1.确定加工零件的类型:首先,您需要明确要加工的零件属于哪一种类型,例如轴类零件、盘类零件等。
不同类型的零件,其加工工艺和所需时间有所差异。
2.确定加工工艺:在明确零件类型后,您需要确定加工工艺,如车削、铣削、钻孔等。
每种工艺的加工时间计算方法不同,因此需要选择正确的工艺。
3.输入相关参数:根据所选工艺,您需要输入一些关键参数,如零件直径、长度、材料等。
这些参数将影响加工时间计算的准确性。
4.计算加工时间:在输入完所有参数后,点击“计算”按钮,计算器将自动为您计算出加工时间。
四、机加工时间计算器的应用案例某企业生产部门需要为一批轴类零件安排生产计划,他们使用机加工时间计算器进行计算。
首先,他们确定零件类型为轴类零件;然后,选择车削工艺;接着,输入相关参数,如零件直径、长度、材料等;最后,计算器自动计算出每个零件的加工时间为2 小时。
生产部门根据计算结果,合理安排生产计划,确保生产效率的提高。
五、总结机加工时间计算器是一种实用的工具,能够帮助企业快速、准确地计算加工时间,为生产计划提供依据。
机械零件加工工时计算公式

0.3
500.00 10
>硬质合金端铣、周精铣平面、凸台、凹槽理论工时计算<
零件参数 材料种类 材料硬度 HBS
加工特征类型
刀具、机床参数
灰铸铁 刀具直径 mm
300.0
150-225 刀具齿数
18
平面 走刀路径长度
430.00
表面粗糙度要求Ra
加工余量 mm
3.00
0.8
工件速度
5
工作台充满系数
0.25
工件要求尺寸精度
0.02
推荐磨削参数
15 0.3 0.15 0.04600 12.80
0.80 0.80
1.4
>>>>>>>高速钢半精铣平面、凸台、凹槽理论工时计算<<<<<<<
材料种类 材料硬度 HBS 加工特征类型 走刀路径长度 mm
零件、刀具参数 铝镁合金 刀具类型
1、该表 中每一种 加工方式 的理论工 时为单道 工步的切 削时间, 仅用于参 考,总的 切削时间 为所有工 步切削时 间的总和
2、总加 工成本可 以参考以 下计算公 式: C总 = 单位时 间机床的 切削成本 * 切削时 间 + 单位 时间机床 非切削成 本 * 所有 装夹、换 刀等动作 时间 + 其 它非加工 费用
车间内某 一工序的 生产率限 制了整个 车间的生 产率的提 高时,该 工序的刀 具寿命要 选得低 些;当某 工序单位 时间内所 分担到的 全厂开支 M较大 时,刀具 寿命也应 选得低些 。
大件精加 工时,为 保证至少 完成一次 走刀,避 免切削时 中途换 刀,刀具 寿命应按 零件精度 和表面粗 糙度来确 定。
机械加工工时定额(车、铣、镗)切削用量参考表
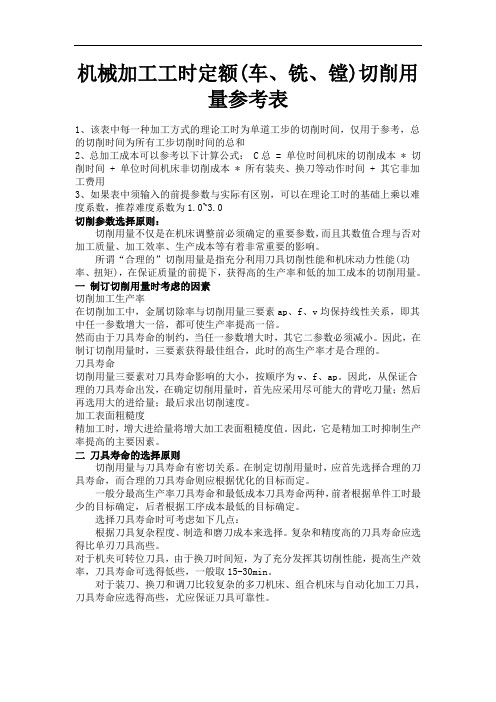
机械加工工时定额(车、铣、镗)切削用量参考表1、该表中每一种加工方式的理论工时为单道工步的切削时间,仅用于参考,总的切削时间为所有工步切削时间的总和2、总加工成本可以参考以下计算公式: C总 = 单位时间机床的切削成本 * 切削时间 + 单位时间机床非切削成本 * 所有装夹、换刀等动作时间 + 其它非加工费用3、如果表中须输入的前提参数与实际有区别,可以在理论工时的基础上乘以难度系数,推荐难度系数为1.0~3.0切削参数选择原则:切削用量不仅是在机床调整前必须确定的重要参数,而且其数值合理与否对加工质量、加工效率、生产成本等有着非常重要的影响。
所谓“合理的”切削用量是指充分利用刀具切削性能和机床动力性能(功率、扭矩),在保证质量的前提下,获得高的生产率和低的加工成本的切削用量。
一制订切削用量时考虑的因素切削加工生产率在切削加工中,金属切除率与切削用量三要素ap、f、v均保持线性关系,即其中任一参数增大一倍,都可使生产率提高一倍。
然而由于刀具寿命的制约,当任一参数增大时,其它二参数必须减小。
因此,在制订切削用量时,三要素获得最佳组合,此时的高生产率才是合理的。
刀具寿命切削用量三要素对刀具寿命影响的大小,按顺序为v、f、ap。
因此,从保证合理的刀具寿命出发,在确定切削用量时,首先应采用尽可能大的背吃刀量;然后再选用大的进给量;最后求出切削速度。
加工表面粗糙度精加工时,增大进给量将增大加工表面粗糙度值。
因此,它是精加工时抑制生产率提高的主要因素。
二刀具寿命的选择原则切削用量与刀具寿命有密切关系。
在制定切削用量时,应首先选择合理的刀具寿命,而合理的刀具寿命则应根据优化的目标而定。
一般分最高生产率刀具寿命和最低成本刀具寿命两种,前者根据单件工时最少的目标确定,后者根据工序成本最低的目标确定。
选择刀具寿命时可考虑如下几点:根据刀具复杂程度、制造和磨刀成本来选择。
复杂和精度高的刀具寿命应选得比单刃刀具高些。
对于机夹可转位刀具,由于换刀时间短,为了充分发挥其切削性能,提高生产效率,刀具寿命可选得低些,一般取15-30min。
数控加工切削参数计算公式

注:在红色字体位置处,输入你们刀具或工件的实际直径,以及刀具齿数,即可自动计算出相关主轴转速和进给速度。
1.切削速度=3.14*直径*转速/1000;
2.每转进给量=每齿进给量*刀具齿数;
3.每分钏进给量=主轴转速*每转进给量
1000
Dn
V c π=
f
Z f *=
切削速度背吃刀量
每转进
给量
主轴转速
((((
))))
外圆
粗加
工
4010.240318.4713376外圆
精加
工
200.150.0841155.351872切槽
加工
200.0830212.3142251外圆
粗加
工
100 1.50.235909.9181074外圆
精加
工
1300.40.0550828.0254777切槽
加工
1000.0845707.7140835
外圆
粗加
工
150 1.50.2351364.877161外圆
精加
工
1500.40.05401194.267516
切槽加工1000.0845707.7140835
2.每转进给量=每齿进给量*刀具齿数;
3.每分钏进给量=主轴转速*每转进给量
车床切削参数计算参考
刀具材料高速钢
硬质合金钢加工
类型
工件直径
z
f
Z
n
nf
F*
*
=
=
z
f
Z
f*
=
;量
;量。
基于MastercamX铣削的刀具参数和加工参数设置
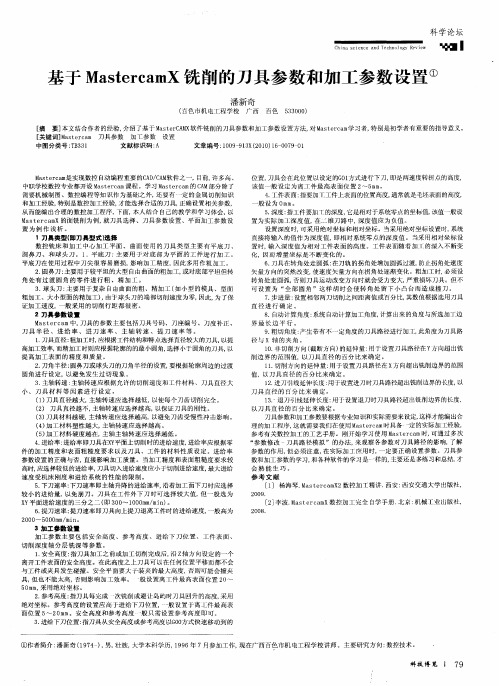
潘新奇
( 色 市机 电:= 学校 I = 程 广西 百色 5 30 ) 30 0 [ 要] 摘 本文 结合 作者 的经 验, 介绍 了基 于 M s eC M 软件 铣 削 的刀具 参数和 加 工参数 设 置方法 , M se cm 习者 , a t rA X 对 atra学 特别 是初 学者 有重 要的指 导意 义 。 [ 关键词 ]a t r a 刀 具参 数 加 工参 数 设置 M se cm 中图 分类 号 :B 3 T3 1 文献 标识 码 : A 文 章编 号 :0 99 3 (0 0 1—0 9 O 10 — 1X2 1)6 0 7~ 1
位 置, 刀具 会在 此位 置 以设定 的G 1 O 方式进 行 下刀, 即是两速 度转 折点 的高度, 该 值 一般 设定 为 离:= I _ 件最 高表面 位 置 2 5 m ~ m 。 4 工件表面 : 要加 T工件 上表面 的位置 高度, . 指 通常就 是毛坯表面 的高度 , 般 设 为 0l i f m。 5深度 : 工件要加 T 的深 度, . 指 它是相 对于系 统零 点的坐标 值, 该值 一 般设
直径进行确 定 。 8 自 计算 角度 : 统 自动计 算加工 角度 , 算出来 的 角度与 所选) i边 . 动 系 计 Ji Ni 界最长边平 行 。 9 粗切 角度 : 生带 有不 ‘ 角度 的刀 具路径 进行 D - , . 产 定 R :此角度 为 刀具路 I 径 与 x轴 的 夹 角 。 1. 0 非切 削 方 向 ( 断方 向) 截 的延伸 量 : 于设置刀 具路径 在 Y 向超 出铣 用 方 削边 界 的 范围 值,以刀 具直 径 的 百分 比来确 定 。 1. 削方 向的延 伸 量 : 1切 用于 设 置刀 具路径 在 x 向超 出铣 削边 界的 范围 方 值 ,以刀具 直 径 的 百分 比来 确 定 。 l. 2 进刀 引线延伸 长度 : 于设置进 刀 时刀 具路径 超 出铣 削边界 的 长度, 用 以
车床件计价公式

合计人民币(元):
自动车床行业工时成本RMB/小时 加工工序
工序
设备
1
自动车
2
数控车
3
铣
4
钻
5
磨
6
7
8
单个工时 (秒)
2
0.00 (2)加工费用
40 标准单价
元/秒 元/秒 元/秒 元/秒 元/秒 元/秒 元/秒 元/秒 元/秒
数控车床行业工时成本RMB/小时
加工费
加工工序
工时/次 数/
0.00 0.00 0.00 0.00 0.00
镀镍
100
单价
加工费
元/秒 元/秒 元/秒 元/秒 10.00 元/Kg
0.00 0.00 0.00 0.00 0.00
合计人民币(元):
项目 材料费 加工费 包装费
系数 2.00%生产周来自 结算方式 估价有效期数值 0.00 0.00 0.00
0.00 (3)总体费用
项目
系数
运输费
1.00%
管理费
2.00%
加工利润 税收
6.00% 3.00%
销售利润率 #DIV/0!
数值 0.000 0.000 0.000 0.000
10天 月结30天 镍价波动RMB10000以内
其他事项:
总计人民币(元) 0.00
车削件成本分析表
物料名称 品名:
材质代号 密度g/cm3
不锈钢螺柱
图纸号
20210548
外径 (mm)
内径 (mm)
(1)材料费用
长度 (mm)
原料棒 毛料重量 材尺寸 (kg) A
损耗重量 (kg) B
材料单价 C (元
数控加工切削参数计算公式
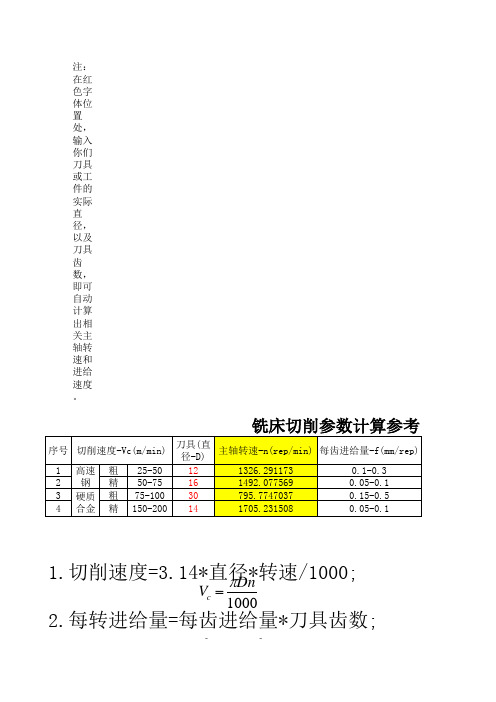
1061.032938 477.4648222 716.1972333
0.9
1534.708357
; 量
; 量
编程进给 量F
(mm/min )
63.694268 12.42815 16.985138 181.98362 41.401274 56.617127
272.97543 59.713376 56.617127
注: 在红 色字 体位 置 处, 输入 你们 刀具 或工 件的 实际 直 径, 以及 刀具 齿 数, 即可 自动 计算 出相 关主 轴转 速和 进给 速度 。
铣床切削参数计算参考
序号
切削速度-Vc(m/min)
刀具(直 径-D)
主轴转速-n(rep/min) 每齿进给量-f(mm/rep)
1 高速 粗 25-50
12
2 钢 精 50-75
16
3 硬质 粗 75-100 30
4 合金 精 150-200 14
1326.291173 1492.077569 795.7747037
1705.231508
0.1-0.3 0.05-0.1 0.15-0.5
0.05-0.1
1.切削速度=3.14*Vc直 1径0D0n*0转速/1000; 2.每转进给量=每齿进给量*刀具齿数;
f Z* fz
3.每分钏进给量=主轴转速*每转进给量
1.切削速度=3.14*直径*转速/1000;
2.每转进给量=每齿进给量*刀具齿数;
f Z* fz
3.每分钏进给量=主轴转速*每转进给量
F nf n* Z * fz
车床切削参数计算参考
刀具 材料
高速 钢
硬质 合金
钢
加工 类型
各种机械加工工时计算公式E cel表格
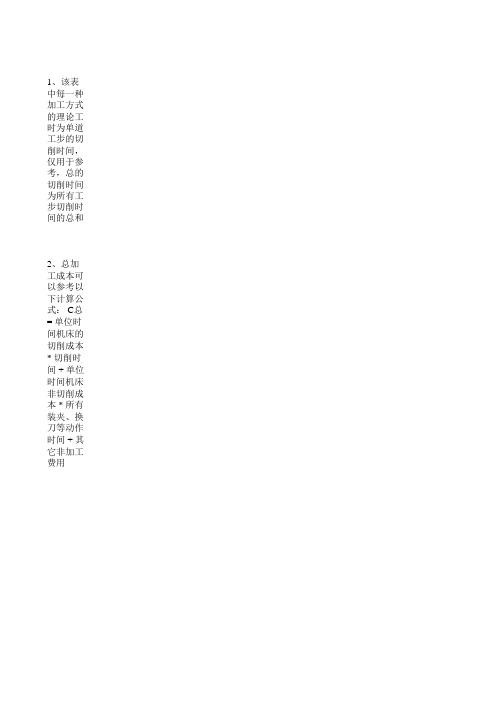
砂轮耐用度(T) S
900
加工面长度 mm
400.00 纵向进给量与砂轮宽度比值
0.6
加工面宽度 mm
300.00 工作台充满系数
0.25
平面磨
工件速度 m/min
6
推荐磨削参数
磨削余量 mm
0.3
磨削公差 f mm
0.15
单行程磨削深度
0.042000
理论工时 min
5.2
**时间为工作台单
行程
磨削深度修正系数 K1=
1、该表 中每一种 加工方式 的理论工 时为单道 工步的切 削时间, 仅用于参 考,总的 切削时间 为所有工 步切削时 间的总和
2、总加 工成本可 以参考以 下计算公 式: C总 = 单位时 间机床的 切削成本 * 切削时 间 + 单位 时间机床 非切削成 本 * 所有 装夹、换 刀等动作 时间 + 其 它非加工 费用
零件参数
刀具、机床参数
灰铸铁 刀具类型
镶齿立铣刀
230-290 刀具可选直径范围 平面 刀具齿数
20-25 3
1500.00 步距 ae mm
5.0
5.00 切削深度ap mm
推荐铣削参数
0.05 10 159 请输入实际切削参数
20.0 0.12 200.00 62.5
2.0
0.10 18 286
5.00 切削深度ap mm
推荐铣削参数
0.16 12 637 请输入实际切削参数
0.2 800.00 14.0625
2.0
0.24 25 1326
算<<<<<<<
推荐切削参数
铰削余量 mm 每转进给量 f mm 切削速度 m/min
SIEMENS802D加工中心操作

S I E M E N S802D铣、加工中心机床面板操作SIEMENS802D系统面板1.1面板简介恢复运行检查急停按钮是否松开,若未松开,将急停按钮松开。
1)进入回参考点模式系统启动之后,机床将自动处于“回参考点”模式在其他模式下,依次点击按钮和进入“回参考点”模式2)回参考点操作步骤Z轴回参考点:点击按钮,Z轴将回到参考点,回到参考点之后,Z轴的回零灯将从变为;X轴回参考点:点击按钮,X轴将回到参考点,回到参考点之后,X轴的回零灯将从变为;Y轴回参考点:点击按钮,Y轴将回到参考点,回到参考点之后,Y轴的回零灯将从变为;回参考点前的界面如图9-2-2-1所示:回参考点后的界面如图9-2-2-2所示:图9-2-2-1机床回参考点前CRT界面图9-2-2-2机床回参考点后CRT界面图1.3对刀数控程序一般按工件坐标系编程,对刀的过程就是建立工件坐标系与机床坐标系之间的关系的过程。
常见的是将工件上表面中心点(铣床及加工中心),工件端面中心点(车床)设为工件坐标系原点。
本使用手册就采用将工件上表面中心点(铣床及加工中心),工件端面中心点(车床)设为工件坐标原点的方法介绍。
将工件上其它点设为工件坐标系原点的对刀方法类似。
下面分别具体说明铣床、卧式加工中心、车床和立式加工中心的对刀方法。
1.3.1X ,Y 轴对刀铣床及加工中心在X ,Y 方向对刀时一般使用的是基准工具。
基准工具包括“刚性靠棒”和“寻边器”两种。
(1)刚性靠棒刚性靠棒采用检查塞尺松紧的方式对刀,具体过程如下:X 轴方向对刀 点击操作面板中的按钮进入“手动”方式;通过点击,,按钮,将机床移动到X 方向一侧大致位置。
移动到大致位置后,可以采用手轮调节方式移动机床,基准工具和零件之间被插入塞尺。
将工件坐标系原点到X 方向基准边的距离记为2X ;将塞尺厚度记为3X (此处为1mm );将基准工具直径记为4X (可在选择基准工具时读出,刚性基准工具的直径为14mm ),将2X +3X +2/4X 记为DX 点击软键,进入“工件测量”界面,如图9-4-1-4所示。
机械加工初步报价自动计算(含各种工时费)

客户:
材料名称 Q235 材 料 费 方 料 圆 管 圆 棒 设备名称 1 2 加 3 工 4 费 5 6 7 8 9 配 1 件 2 费 3 4 处理内容 表 面 处 理 1 2 3 4 5 调质 淬火 退火 发黑 渗氮 重量 (KG) 单价 2.5 1.5 1 1.5 4 金额 6 7 8 9 10 普车 普铣 数控车 线切割 平面磨床 外圆磨 放电 CNC1 CNC2 配件名称 规格 2.5 数量 单价 材质 钢 铜 铝 电木 钢 铜 铝 钢 铜 铝
数量 1 理论重量 (KG) 151.2
单 价 (元/KG)
金额(元) ¥1,209.60
小计 (元)
8
¥1,209.60
设备名称 10 11 12 13 14 15 16 攻牙机 喷砂 抛光 锯床 大水磨元)
40 50 80 60 50 120 80 80 金额
设计费 工时 单价 包装费用 包装人工 元/个 包装材料费 元/个 运输费用 单价 公里数 费用名称 费用计算说明 1 难度级别 一级报废率加5%,二级加10%,三级加15%,四级加30% 其 一般情况收10%-20% 5 管理费 它 一般情况收15%-30% 6 利润 7 税收
金额(元)
¥305.19 ¥305.19 ¥345.88
¥956.26
总成本: 核准: 表示需要填 复核: 核算:
¥2,990.86
13
60 560 13 5 65
¥825.00
200 17 18 配件名称 5 6 7 8 处理内容 黑色阳极氧化 镀环保锌 镀化学镍 镀亮镍 喷砂 金 数量 规格 数量 单价 金额(元)
重量 (KG)
单价 (元/KG)
金额(元)
加工费计算完整版
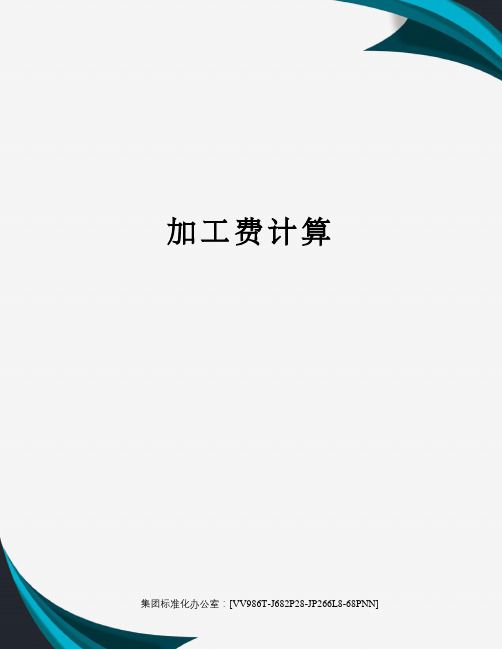
加工费计算集团标准化办公室:[VV986T-J682P28-JP266L8-68PNN]经常有刚创业的机械加工的朋友为工时计算发愁,也有些朋友为如何计算外发件的成本而苦恼。
老金根据网上的一些资料和实践经验,总结了一些常用的对外机械加工工时价格计算方法供大家参考。
其实各种工种的工时价格并没有固定的,具体情况要具体分析。
可以根据工件的难易,设备的大小,性能的不同而有不同的计算方法,当然关键是看加工的量是有多少,批量越大价格相对越低。
不过一般来说机械加工工时都有一个基本价,根据不同情况在基本价之间浮动。
一以工时记价办法记时单位从接手加工开始至加工完成验收合格结束1.车基本价:20-40具体的有根据实际情况而定,象小件,很简单的工时就小于20元;有时甚至只有10元例如一些大的皮带轮,加工余量大,老板只赚铁沫子的钱就够了;有时如果工件大的话,一般市面上没法加工的就可以高点,两三倍,别人也没办法.2.磨基本价:25-453.铣基本价:25-454.钻基本价:15-355.刨基本价:15-356.快走丝线切割基本价:3-4/1200平方毫米7.电火花基本价:10-40,单件一般按50/件(小于1个小时)8.数控机床基本价:比普通的贵2-4倍9.雕刻:一般都是单件的,50-500/件10、钳工基本价:15-35二以根据零件,数量,精度要求收费办法。
1、钻孔加工一般材料,深径比不大于2.5倍的直径25MM以下按钻头直径*0.05直径25-60的按钻头直径*0.12(最小孔不低于0.5元)深径比大于2.5的一般材料收费基价*深径比*0.4收取对孔径精度要求小于0.1MM或对中心距要求小于0.1MM的按基价*5收费对攻丝收费标准按丝锥直径*0.2收费(以铸铁为标准,钢件另*1.2)在批量加工时以标准基价*0.2-0.8收取(根据批量大小与加工难易程度)2、车床加工类一般精度光轴加工长径比不大与10的按加工件毛坯尺寸*0.2收费(最底5元)长径比大于10的按一般光轴基价*长径比数*0.15精度要求在0.05MM以内的或要求带锥度的以一般光轴基价*2收取一般阶梯轴(风机轴,泵轴,减速器轴,砂轮轴,电机轴,主轴等)以一般精度光轴加工基价*2收取阶梯轴如有带锥度,内外罗纹,的按一般精度光轴加工基价*3收取一般用途丝杠按一般精度光轴加工基价*4收取一般兰盘类零件收费标准按材料直径*0.07收取,直径大于430MM的按材料直径*0.12收取。
怎样在UG软件中设置数控加工编程的切削参数
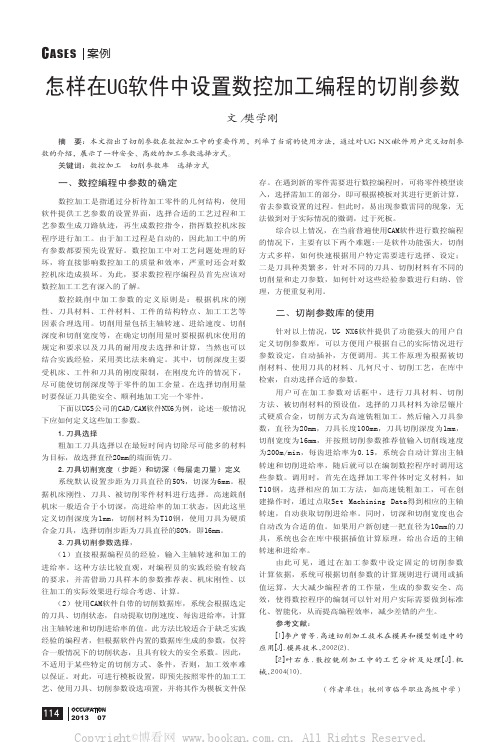
案例C ASESOCCUPATION2013 07114怎样在UG软件中设置数控加工编程的切削参数文/樊学刚摘 要:本文指出了切削参数在数控加工中的重要作用,列举了当前的使用方法,通过对UG NX6软件用户定义切削参数的介绍,展示了一种安全、高效的加工参数选择方式。
关键词:数控加工 切削参数库 选择方式一、数控编程中参数的确定数控加工是指通过分析待加工零件的几何结构,使用软件提供工艺参数的设置界面,选择合适的工艺过程和工艺参数生成刀路轨迹,再生成数控指令,指挥数控机床按程序进行加工。
由于加工过程是自动的,因此加工中的所有参数都要预先设置好。
数控加工中对工艺问题处理的好坏,将直接影响数控加工的质量和效率,严重时还会对数控机床造成损坏。
为此,要求数控程序编程员首先应该对数控加工工艺有深入的了解。
数控銑削中加工参数的定义原则是:根据机床的刚性、刀具材料、工件材料、工件的结构特点、加工工艺等因素合理选用。
切削用量包括主轴转速、进给速度、切削深度和切削宽度等,在确定切削用量时要根据机床使用的规定和要求以及刀具的耐用度去选择和计算,当然也可以结合实践经验,采用类比法来确定。
其中,切削深度主要受机床、工件和刀具的刚度限制,在刚度允许的情况下,尽可能使切削深度等于零件的加工余量。
在选择切削用量时要保证刀具能安全、顺利地加工完一个零件。
下面以UGS公司的CAD/CAM软件NX6为例,论述一般情况下应如何定义这些加工参数。
1.刀具选择粗加工刀具选择以在最短时间内切除尽可能多的材料为目标,故选择直径20mm的端面铣刀。
2.刀具切削宽度(步距)和切深(每层走刀量)定义系统默认设置步距为刀具直径的50%,切深为6mm。
根据机床刚性、刀具、被切削零件材料进行选择。
高速銑削机床一般适合于小切深,高进给率的加工状态,因此这里定义切削深度为1mm,切削材料为T10钢,使用刀具为硬质合金刀具,选择切削步距为刀具直径的80%,即16mm。
机械加工初步报价自动计算(含各种工时费)
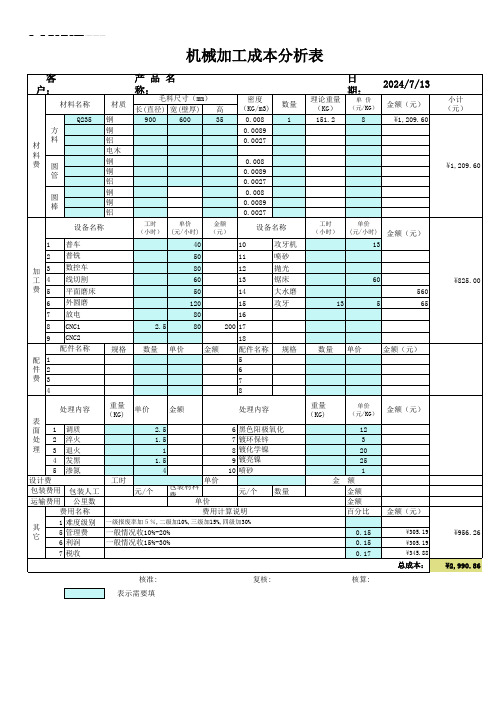
金额(元)
处理内容
表 面 1 调质 处 2 淬火
重量 (KG)
单价
金额
2.5 1.5
处理内容
6 黑色阳极氧化 7 镀环保锌
理 3 退火
1
8 镀化学镍
4 发黑
1ห้องสมุดไป่ตู้5
9 镀亮镍
5 渗氮
4
10 喷砂
设计费 包装费用 包装人工 运输费用 公里数
工时 元/个
单价 包装材料
费
单价
元/个 数量
费用名称
费用计算说明
总成本:
核准: 表示需要填
复核:
核算:
小计 (元) ¥1,209.60
¥825.00
¥956.26 ¥2,990.86
抛光
60
13
锯床
50
14
大水磨
120
15
攻牙
80
16
2.5
80
200 17
数量 单价
金额
18 配件名称 5 6 7 8
规格
日 期:
2024/7/13
理论重量 (KG)
单价 (元/KG)
金额(元)
151.2
8
¥1,209.60
工时 (小时)
单价
(元/小时) 金额(元)
13
60
560
13
5
65
数量 单价
洛
德
机
械
(
上
海
)
有
® 限
公 M P r e 司 o c d h u / a c L n t M i c a S l
机械加工成本分析表
客 户:
材料名称
数控铣床加工过程能耗计算预测方法

文章编 号 : 1 0 0 1— 2 2 6 5 ( 2 0 1 7 ) 0 7— 0 0 8 6— 0 3
D O I : 1 0 . 1 3 4 6 2 / j . c n k i . m m t a m t . 2 0 1 7 . 0 7 . 0 2 0
数 控 铣 床 加 工 过 程 能 耗 计 算 预测 方 法 术
o d, b a s e d o n Ma s t e r CAM a n d VB. Us i n g Ma s t e r CAM s o f t wa r e f o r mo d e l i n g a n d s i mu l a t i o n p r o c e s s i n g g e n —
第 7期 2 0 1 7年 7月
组 合 机 床 与 自 动 化 加 工 技 术
Mo du l a r Ma c h i ne To o l& Aut o ma t i c Ma n u f a c t u r i ng Te c h ni q ue
No. 7
J u 1 .2 0 1 7
c o n s u mp t i o n e s t i ma i t o n mo d e l s , P r o p o s e d a k i n d o f o n l i n e mo n i t o i r n g e n e r g y c o n s u mp i t o n o p t i mi z a t i o n me h— t
e r a t e NC p r o g r a m a n d us e e n e r g y c o ns u mp t i o n mo d e l a n d wr it e y o u r o wn VB p r o g r a m t o r e a d he t N C p r o — g r a m c o d e,a c c o r di n g t o he t if d f e r e n t mi l l i n g p ra a me t e r s,a u t o ma i t c c a l c u l a t i o n o f e n e r g y c o n s u mpt i o n,a n d
铣刀功率和切削力计算【秘籍】

大家知道铣刀功率和切削力计算是怎样的吗?下面,小编为大家简单介绍一下,一起来看看吧。
一、按照主轴转速1000rpm ,进给速度0.1mm/转,钻穿1.8mm 约需要时间1s 。
切削力Ff刀具材料:高速钢加工方式:钻公式:Ff=309*D*f^(0.8)*(Kp)功率:D = 8功率:f = 0.1功率:Kp = 0.75(按铜合金多相平均HB>120)计算结果= 293.839切削力矩M工件材料:灰铸铁(HB190)刀具材料:高速钢加工方式:钻公式:M=0.21*D^(2)*f^(0.8)*(Kp)功率:D = 8功率:f = 0.1功率:Kp = 0.75(按铜合金多相平均HB>120)计算结果= 1.597二、铣削切削力计算:铣削切削力计算类别:工件材料:碳钢、青铜、铝合金、可锻铸铁等刀具材料:高速钢铣刀类型:端铣刀公式:F=(Cp)*(ap)^(1.1)*(fz)^(0.80)*D^(-1.1)*B^(0.95)*z*(Kp) 功率:Cp = 294功率:ap = 1.8功率:fz = 0.5功率:D = 8功率:B = 8功率:z = 4功率:Kp = 0.75计算结果= 707.914扩展资料:钻铣床铣刀切削力计算方法:一切削力的来源,切削合力及其分解,切削功率研究切削力,对进一步弄清切削机理,对计算功率消耗,对刀具、机床、夹具的设计,对制定合理的切削用量,优化刀具几何参数等,都具有非常重要的意义。
金属切削时,刀具切入工件,使被加工材料发生变形并成为切屑所需的力,称为切削力。
切削力来源于三个方面:克服被加工材料对弹性变形的抗力;克服被加工材料对塑性变形的抗力;克服切屑对前刀面的摩擦力和刀具后刀面对过渡表面与已加工表面之间的摩擦力。
切削力的来源上述各力的总和形成作用在刀具上的合力Fr(国标为F)。
为了实际应用,Fr 可分解为相互垂直的Fx(国标为Ff)、Fy(国标为Fp)和Fz(国标为Fc)三个分力。
- 1、下载文档前请自行甄别文档内容的完整性,平台不提供额外的编辑、内容补充、找答案等附加服务。
- 2、"仅部分预览"的文档,不可在线预览部分如存在完整性等问题,可反馈申请退款(可完整预览的文档不适用该条件!)。
- 3、如文档侵犯您的权益,请联系客服反馈,我们会尽快为您处理(人工客服工作时间:9:00-18:30)。
设定参数:请按提示选择或输入参数 根据设定之参数得到的机床信息 机床类型 机床设定 工件设定