现代冲模设计方案分析
冲压模具的设计与制造分析

冲压模具的设计与制造分析冲压模具是一种用于将金属板材或金属片材进行冲压加工的工具。
它由模具座、冲头、模座、定位销等部件组成,通过对材料施加压力来使材料发生变形,最终得到所需的产品。
冲压模具设计的目标是提高冲压产品的质量、生产效率和经济效益。
在进行冲压模具设计时,需要考虑以下几个方面:1. 产品材料的特性:不同材料具有不同的物理性质和加工特性,冲压模具的设计要根据产品材料的特性来确定合适的冲头形状、模具座结构和模座材料等。
2. 产品的结构形式:冲压产品的结构形式决定了模具的形状和加工工艺。
对于复杂的产品结构,需要设计多工位的冲压模具,以实现一次冲压完成多个工序。
3. 模具的寿命和耐用性:冲压模具在生产过程中需要承受高压力和频繁的运动,因此需要选择高硬度和高韧性的材料来制作模具,以提高模具的寿命和耐用性。
4. 模具的工艺性:冲压模具的设计要考虑到产品的成型精度和表面质量要求,确定合适的冲床和冲头尺寸,以及适当的冲压工艺参数。
在进行冲压模具制造时,需要进行以下分析和步骤:1. 材料选择和加工工艺的确定:根据冲压产品的要求和模具设计要求,选择合适的材料进行制造,并确定适当的加工工艺和工艺参数。
2. 模具结构的制造:根据模具设计要求,将模具座、冲头、模座等部件进行制造,并进行必要的热处理和表面处理。
3. 模具装配和调试:将各个部件进行装配,并进行必要的调试和检测,确保模具的稳定性和性能。
4. 模具使用和维护:在模具制造完成后,进行模具的使用和维护,定期进行润滑、清洁和检修,以延长模具的使用寿命。
冲压模具的设计和制造是一个复杂而重要的工作,需要综合考虑材料特性、产品结构形式、模具寿命和工艺性等方面的要求。
只有合理设计和制造冲压模具,才能实现高质量、高效益的冲压加工。
冲压模具设计方法与步骤

冲压模具设计方法与步骤冲压模具是制造行业中常用的一种模具,用于在金属板材上进行冲裁、压制、成形等工艺。
冲压模具的设计是冲压工艺的关键环节之一,合理的设计可以提高产品质量和生产效率。
以下是冲压模具设计的方法与步骤。
一、冲压模具设计方法1.分析产品要求:首先需要仔细分析产品要求,了解产品的形状、尺寸、材质等要求,以及要求的生产效率和成本等因素。
2.选择合适的材料:根据产品的要求选择合适的模具材料,常用的材料有合金工具钢、合金冷作工具钢等。
3.制定冲压工艺:根据产品要求,制定冲压工艺,包括冲剪顺序、成形方式、冲压力、冲头形状等因素。
4.设计模具结构:根据产品要求和冲压工艺,设计模具的结构,包括上模、下模、导向机构等部分。
5.进行模具布局:进行模具布局,合理安排模具零件的形状、位置和尺寸,以确保模具的强度和稳定性。
6.进行模具零件设计:根据模具布局,设计模具的零件,包括冲头、导柱、导套、导向板等部分。
7.进行模具装配:根据模具设计,进行模具的装配,确保各个零件之间的配合和精度。
8.进行模具调试:进行模具调试,调整模具的尺寸和位置,确保模具在冲压过程中的稳定性和精度。
9.进行模具试产:进行模具试产,对模具进行试模和试产,检验产品的质量和模具的性能。
10.进行模具改进:根据试产结果,对模具进行改进和优化,提高模具的性能和生产效率。
二、冲压模具设计步骤1.初步设计:根据产品要求,进行初步的模具设计,包括模具结构和布局。
2.详细设计:对初步设计的模具进行详细设计,包括各个零件的形状、尺寸和材料等。
3.模具制造:根据详细设计,进行模具的制造,包括加工模具零部件和进行模具装配。
4.模具调试:对制造完成的模具进行调试,调整模具的尺寸和位置,确保模具的性能和精度。
5.模具试产:进行模具的试模和试产,检验产品的质量和冲压工艺的可行性。
6.模具改进:根据试产结果,对模具进行改进和优化,提高模具的性能和生产效率。
7.模具验收:对改进后的模具进行验收,确保模具达到产品要求和生产效果。
冲模设计实例分析
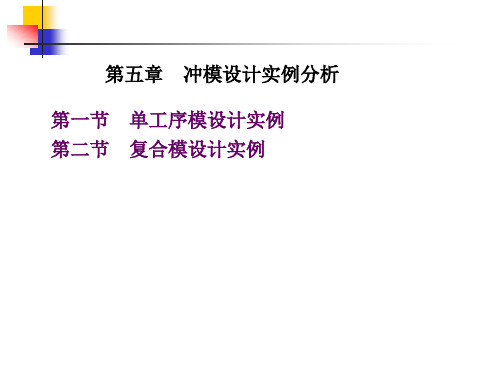
未注公差尺寸的极限偏差(mm)
尺寸 6~10 10~18 18~30 包容表面(孔) 被包容表面(柱) +0.36 -0.36 +0.43 +0.52 -0.43 -0.52
第五章
冲模设计实例分析
冲裁凸、凹模的制造公差(mm) 尺寸 δ凸 δ凹 +0.020 +0.025
≤18 -0.020 >18~30 -0.020
6、尽量采用弹性装置完成卸料和推件任务。
第五章
冲模设计实例分析
7、复合模应注意选择高精度模架。
二、落料、冲孔、弯曲复合模设计实例
左图示为一大批量生 产的盖板零件图,材料 为Q235-A钢,料厚为 3mm。
第五章
冲模设计实例分析
★ 模具设计过程 1、工艺性分析与工艺方案的确定
2、毛坯展开及毛坯排样
先计算弯曲部分展开尺 寸,再计算毛坯总体尺寸。 根据零件形状确定毛坯 排样方式。 由表3-3查最小搭边值, 计算条料的宽度和步距。
第五章
冲模设计实例分析
3、计算冲压力和压力中心 4、模具总体结构设计 5、主要工作件的设计 A、 弯曲 成形 部分 的设 计
第五章
冲模设计实例分析
B、落料与冲孔成形部分的设计
第五章
冲模设计实例分析
模 具 总 装 图 的 一 般 布 置 情 况
冲模设计实例分析
3、计算冲裁力和压力中心
4、模具总体结构设计
A、送料方式
B、卸料和出件方式 C、凹模的外形尺寸 D、其他模板尺寸 E、模架选择
第五章
冲模设计实例分析
5、凸、凹模设计
A、刃口尺寸计算
B、凸模结构 C、凹模型腔结构 6、卸料和顶件装置设计
第九讲冲压模具设计实例分析
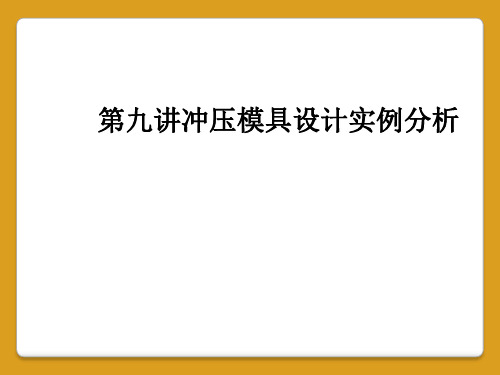
第八章 冲压模具结构及设计
9、模具的装配 根据级进模装配要点,选凹模作为装配基准件,先装下模,再装上模,并调整间隙、试冲、返修。
第八章 冲压模具结构及设计
二、拉深模设计与制造实例
零件名称:端盖 生产批量:大批量 材料:镀锌铁皮 材料厚度:1mm
第八章 冲压模具结构及设计
1、冲压件工艺性分析 冲压工序:落料、拉深; 材料:为镀锌铁皮,具有良好的拉深性能,适合拉深; 结构:简单对称; 精度:全部为自由公差,工件厚度变化也没有作要求,只是该工件作为另一零件的盖,口部尺寸 φ69可稍作小些。而工件总高度尺寸14mm可在拉深后采用修边达要求 。
第八章 冲压模具结构及设计
2、冲压工艺方案的确定 方案一:先落料,后拉深。采用单工序模生产。 方案二:落料-拉深复合冲压。采用复合模生产。 方案三:拉深级进冲压。采用级进模生产。 方案一:模具结构简单,但成本高而生产效率低; 方案二:生产效率较高,尽管模具结构较复杂,但因零件简单对称,模具制造并不困难; 方案三:生产效率高,但模具结构比较复杂,送进操作不方便,加之工件尺寸偏大。 结论:采用方案二为最佳工艺方案。
起粗定距的活动挡料销、弹簧和螺塞选用标准件,规格为8×16。
φ8mm导正销
第八章 冲压模具结构及设计
(3)导料板的设计 (4)卸料部件的设计
① 卸料板的设计 ②卸料螺钉的选用 (5)模架及其它零部件设计
第八章 冲压模具结构及设计
6、模具总装图(右图) 7、冲压设备的选定 8、模具零件加工工艺
模具关键零件因采用线切割,所以这些零件的加工 就变得相对简单。
第八章 冲压模具结构及设计
(4)冲压工序压力计算 拟采用正装复合模,固定卸料与刚性推件。 根据冲压工艺总力计算结果并结合工件高度,初选开式双柱可倾压力机J23-25。
冲压模具的设计与制造分析
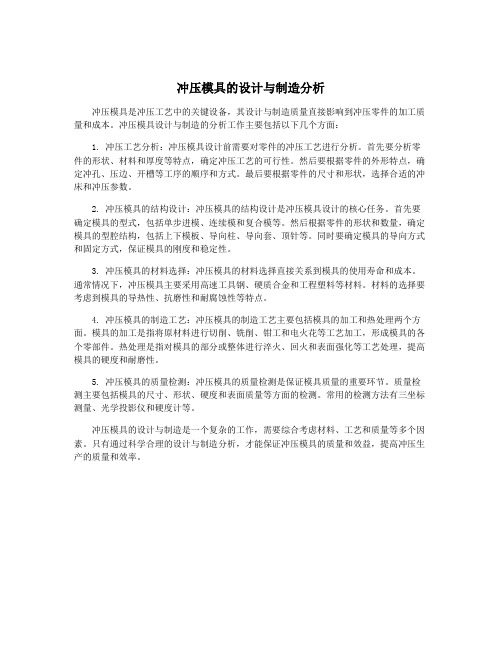
冲压模具的设计与制造分析冲压模具是冲压工艺中的关键设备,其设计与制造质量直接影响到冲压零件的加工质量和成本。
冲压模具设计与制造的分析工作主要包括以下几个方面:1. 冲压工艺分析:冲压模具设计前需要对零件的冲压工艺进行分析。
首先要分析零件的形状、材料和厚度等特点,确定冲压工艺的可行性。
然后要根据零件的外形特点,确定冲孔、压边、开槽等工序的顺序和方式。
最后要根据零件的尺寸和形状,选择合适的冲床和冲压参数。
2. 冲压模具的结构设计:冲压模具的结构设计是冲压模具设计的核心任务。
首先要确定模具的型式,包括单步进模、连续模和复合模等。
然后根据零件的形状和数量,确定模具的型腔结构,包括上下模板、导向柱、导向套、顶针等。
同时要确定模具的导向方式和固定方式,保证模具的刚度和稳定性。
3. 冲压模具的材料选择:冲压模具的材料选择直接关系到模具的使用寿命和成本。
通常情况下,冲压模具主要采用高速工具钢、硬质合金和工程塑料等材料。
材料的选择要考虑到模具的导热性、抗磨性和耐腐蚀性等特点。
4. 冲压模具的制造工艺:冲压模具的制造工艺主要包括模具的加工和热处理两个方面。
模具的加工是指将原材料进行切削、铣削、钳工和电火花等工艺加工,形成模具的各个零部件。
热处理是指对模具的部分或整体进行淬火、回火和表面强化等工艺处理,提高模具的硬度和耐磨性。
5. 冲压模具的质量检测:冲压模具的质量检测是保证模具质量的重要环节。
质量检测主要包括模具的尺寸、形状、硬度和表面质量等方面的检测。
常用的检测方法有三坐标测量、光学投影仪和硬度计等。
冲压模具的设计与制造是一个复杂的工作,需要综合考虑材料、工艺和质量等多个因素。
只有通过科学合理的设计与制造分析,才能保证冲压模具的质量和效益,提高冲压生产的质量和效率。
冲压模具的设计与制造分析

冲压模具的设计与制造分析冲压模具是用于金属冲压加工中的一种工艺设备,主要用于将金属板材通过冲压工艺加工成所需的形状和尺寸。
冲压模具的设计与制造分析是为了确保冲压过程的稳定性和产品质量的一项重要工作。
下面将对冲压模具的设计与制造分析进行详细介绍。
冲压模具的设计首先需要根据产品的尺寸和形状要求确定模具的结构形式,常见的有单工位模具、多工位模具和进模式模具等。
然后需要进行模具的布局设计和模具零件的选择。
模具的布局设计包括冲床的选择、上模槽和下模槽的位置安排、导向装置的设计等。
模具零件的选择包括上模、下模、模板、导向柱等零件的选择和设计。
冲压模具的制造分析主要包括模具材料的选择、模具结构强度分析和模具加工工艺的确定。
模具材料的选择需要考虑模具耐磨性、抗拉强度和导热性等因素,一般常用的模具材料有合金工具钢、硬质合金和工程塑料等。
模具结构强度分析是为了保证模具在冲压过程中不发生变形或损坏,需要进行有限元分析或计算强度校核。
模具加工工艺的确定需要根据模具结构和形状复杂程度进行加工工艺的选择,包括粗加工、热处理、精加工和装配等工艺。
冲压模具的设计与制造分析中还需要考虑模具的寿命和维修问题。
模具的寿命是指模具可以保持稳定工作状态的时间,直接影响到模具的经济效益。
模具维修是指在模具使用过程中出现的损坏或故障需要进行修复和维护,以延长模具的使用寿命和保证产品质量。
在设计和制造冲压模具时需要考虑模具的易维修性,合理布置模具的加工余量和保护装置,以便于模具的维修和保养。
冲压模具的设计与制造分析是一项复杂而重要的工作,需要综合考虑多个因素,包括模具的结构形式、材料选择、强度分析、加工工艺、寿命和维修等问题。
只有在设计和制造过程中充分考虑这些因素,才能保证模具的稳定性和产品质量。
冲压模具的设计与制造分析

冲压模具的设计与制造分析冲压模具是冲压工艺中不可缺少的一部分,它在金属材料的成型过程中起着至关重要的作用。
冲压模具的设计与制造需要考虑多方面的因素,包括产品的形状、尺寸、材料特性以及生产工艺等。
冲压模具的设计需要根据产品的形状和尺寸来确定模具的结构和布局。
模具的结构包括上模、下模、滑块、导柱、定位销等零部件的形状和尺寸,需要保证这些零部件之间的配合精度和运动的平稳性。
模具的布局需要考虑生产效率和使用便捷性,例如冲孔模的排列方式、冲压顺序等。
冲压模具的制造需要根据产品的材料特性和成型要求来选择合适的材料和加工工艺。
模具的主要材料通常是高硬度、高强度的合金钢,这样可以保证模具在使用过程中不会发生变形和磨损。
模具的加工工艺包括粗加工、热处理和精加工等步骤,需要保证模具的精度和表面质量。
冲压模具的设计与制造还需要考虑生产工艺的因素。
例如模具的开合方式、冲压顺序、冲程和冲频等参数需要根据产品的工艺要求来确定。
模具的开合方式有单向开合和多向开合两种,需要根据产品的形状和尺寸来选择合适的方式。
冲压顺序需要考虑产品的成形过程和冲孔孔数的多少来确定,以避免产生变形或缺陷。
冲压模具的设计与制造还需要进行相关的分析和验证。
例如可以通过有限元分析来评估模具的刚度和应力分布,以确定模具在使用过程中的可靠性和稳定性。
还可以通过样板和小批量试产来验证模具的可用性和生产效果。
冲压模具的设计与制造是一个综合性的工程,需要考虑多方面的因素。
只有充分理解产品的形状、尺寸、材料特性以及生产工艺等要求,才能设计和制造出合适的冲压模具。
冲压模具的设计与制造的质量直接影响到产品的质量和生产效率,因此需要高度重视。
冲压模具设计方案

冲压模具设计方案引言冲压模具是用于冲压加工的工具,它可以将金属板料按照预定的形状和尺寸进行加工,广泛应用于汽车、电子、家电等制造业。
本文将针对冲压模具设计方案进行详细介绍。
模具设计的基本原则1. 性能要求冲压模具设计时需要根据具体的加工对象和产品性能要求来确定模具的材质、硬度和耐磨性等。
2. 结构合理冲压模具的结构应设计合理,易于加工和调试,并且具备足够的刚性和稳定性,以确保加工精度和生产效率。
3. 操作简便冲压模具的调试和维护应简单方便,能够降低操作者的劳动强度,提高生产效率。
4. 耐久性冲压模具在长时间运行中需要经受各种各样的载荷和冲击,因此需要具备良好的耐久性和可靠性。
5. 经济性冲压模具的设计应尽量减少材料的浪费,并且考虑到模具的制造成本和使用寿命,以维持良好的经济效益。
冲压模具设计的步骤1. 确定加工对象首先需要明确所要加工的产品的形状和尺寸要求,以及所需加工的材料种类和厚度等。
2. 制定设计方案根据加工对象的要求,进行模具结构的设计,包括上模、下模、引导柱、导向装置、顶针等的位置和尺寸等。
3. 进行模具设计计算根据设计方案,进行力学分析,计算各个部件所需的尺寸、材质、硬度等。
同时还需要进行模具在工作中可能遇到的载荷和应力的计算。
4. 绘制图纸根据计算结果,绘制出冲压模具的详细图纸,并标注相应的尺寸、公差和加工要求等。
5. 制造和组装模具根据图纸的要求,制造和组装模具,包括加工模具零部件、组装模具、进行调试和试验等。
6. 进行模具调试完成模具的制造和组装后,需要进行调试和试验,以确保模具的正常运行和加工的质量。
7. 模具维护与维修冲压模具在使用过程中需要进行定期的维护和维修,包括清洁、润滑、更换磨损部件等。
结论冲压模具设计是一个复杂而关键的工作,它直接关系到产品质量和生产效率。
在设计过程中,需要考虑性能要求、结构合理、操作简便、耐久性和经济性等方面的因素。
通过遵循设计步骤,合理制定方案,绘制详细图纸,并进行模具调试和维护,可以设计出高质量的冲压模具,提高生产效率,降低生产成本。
冲模设计制作案例案例精解-项目一

和原材料。 (3)冲压所用原材料的表面质量好,且冲件的尺寸公差由冲
压模具保证,故冲压产品尺寸稳定,互换性好。
上一页 下一页 返回
任务一 冲压生产与冲压模具的安 装
(4)冲压产品壁薄、质量轻、刚度好,可以加工成形状复杂 的零件,小至〔钟表的秒针、大到汽车的纵梁等。
与制造技术正由手工设计、依靠个人经验和常规机械加工技 术转向以计算机辅助设计软件(CAD/三维软件)、
上一页 下一页 返回
任务一 冲压生产与冲压模具的安 装
数控加工(CNC)为基础的计算机辅助设计与制造(三维造型 /CAM)技术转变。目前,计算机辅助设计软件与模具设计 和制造技术相结合的模具设计在我国发展迅速, CAD/CAE/CAM, UG, Pro/E, SolidWorks, Solid-CAM等软件,在模具工业中的应用已相当广泛。
压力机工作台面上,然后调节滑块的高度,
上一页 下一页 返回
任务一 冲压生产与冲压模具的安 装
使滑块的底平面与上模座上平面接触。打开滑块上的压块和 螺钉,将模柄固定住(对于无模柄的大型冲模,用螺钉、压 板等将上模座紧固在压力机滑块上)。然后将下模座固定在 压力机台面上,拧紧螺钉(先固定模柄或上模部分,然后固 定下模座部分,顺序勿颠倒)。 (2)将滑块升到上死点,再将滑块转至下死点,确认曲柄是 否可以顺利旋转。
下一页 返回
任务一 冲压生产与冲压模具的安 装
相关知识
一、冲压加工的概念 冲压工艺不仅可以加工金属材料,还可以加工非金属材料。 冲压工艺中的工序按其变形性质可分为分离工序与变形工序
两大类,每一类中又包括许多不同的工序,见表1 -1。 分离工序:冲压成形时,变形材料内部的应力超过强度极限
冲压模具的设计与制造分析

冲压模具的设计与制造分析冲压模具是机械加工中比较常见的模具形式之一,它通常用于汽车、电子、家电等领域中的零部件生产。
冲压模具的制造和设计对于产品的质量和生产效率有着非常重要的影响,因此需要在制造中加强分析和优化。
冲压模具的设计和制造主要包括以下几个方面:第一,工件的形状和材料。
冲压模具的设计需要结合工件的形状和材料进行考虑。
不同形状的工件需要不同的冲压模具来适应,同时工件的材料也需要做出相应的选取,以便冲压过程不会出现异常情况,提高产品的质量。
第二,模具的结构设计。
冲压模具的结构设计需要充分考虑冲裁时的压力、角度和导向。
同时需要考虑工件的形状要素,采用合理的加工方式,提高加工精度和效率,保证生产稳定性。
第三,零部件的加工和装配。
在冲压模具的制造过程中,需经过多道工序,包括铣削、钻孔、线切割、硬化等。
在零部件装配时应该注意每个零部件的与模具的充分匹配,保证模具的稳定性和可靠性。
第四,模具性能测试。
在冲压模具制造完成后,还需要进行性能测试,包括模具的光洁度、运转稳定性、耐磨性等等。
通过性能测试可以评估模具的品质,进一步优化冲压模具的设计和制造。
在冲压模具设计和制造过程中,还需要注重一些具体的技术要点,如冲压模具的设计要充分考虑模具的寿命和使用寿命,同时对模具的材质和结构进行优化和改进,以提高模具运行的稳定性和可靠性。
此外,在模具的制造和加工过程中,还需要充分运用现代技术手段,如计算机辅助设计、数控加工等技术手段,进一步提高模具加工的准确性和效率。
总之,冲压模具的设计和制造对于产品的质量和生产效率起着非常重要的作用,需要加强分析和优化,以保证冲压模具的可靠性和稳定性,同时提高产品的品质和生产效率。
现代冲模设计方案分析
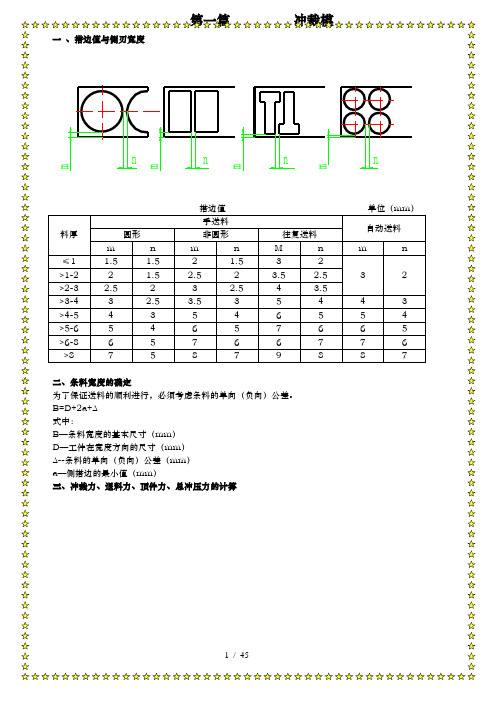
二、条料宽度的确定为了保证送料的顺利进行,必须考虑条料的单向(负向)公差。
B=D+2a+Δ式中:B—条料宽度的基本尺寸(mm)D—工件在宽度方向的尺寸(mm)Δ--条料的单向(负向)公差(mm)a—侧搭边的最小值(mm)三、冲裁力、退料力、顶件力、总冲压力的计算四、各种常用材料计算采用的抗拉强度(N/2mm )材料 抗拉强度 材料 抗拉强度 A1 40020 500 A1E 25 550 A2 420 45 730 A2F 50 770 B2 08MnV 550 B2F 09MnR 500 A3 470 09Mn A3F 16MnR 620 B3 16Mn B3F 65Mn 900 08F (DC04)360 65Si2MnA1600 08 400 紫铜 软:210 10F 380 硬:300 10 410 铝软:70 20F470 硬:1301、冲裁间隙的概念冲裁间隙指凸模刃口与凹模刃口之间的间隙。
Z=Da —dt Z-冲裁间隙Da-凹模刃口尺寸 dt-凸模刃口尺寸Z 正常时:上下微裂纹重合。
2、冲裁间隙对冲压的影响 (1)对断面质量的影响(2)间隙对尺寸精度的影响。
由于弹性变形的存在,冲裁结束后出现弹性恢复,使尺寸与凸凹模刃口尺寸产生尺寸偏差,而弹性变形大小与冲裁间隙有直接的关系。
(3)间隙对冲裁力的影响冲裁间隙对冲裁力的影晌规律是间隙越小,变形区内压应力成分越大,拉应力成分越小,材料变形抗力增加,冲裁力就越大。
反之,间隙越大,变形区内拉应力成分就越大,变形抗力降低,冲裁力就小。
间隙达材料厚的5%-20%时,冲裁力下降不明显。
当单边间隙Z增大到材料厚度的15%-20%时,卸料力为0。
3、合理间隙值的确定:根据近年来的研究与使用经验,在确定间隙值时要按要求分类选用。
对于尺寸精度、断面垂直度要求高的制件应选用较小间隙值,对于断面垂直度与尺寸精度要求不高的制件,应以降低冲裁力、提高模具寿命为主,可采用较大间隙值。
冲压模具设计实例讲解
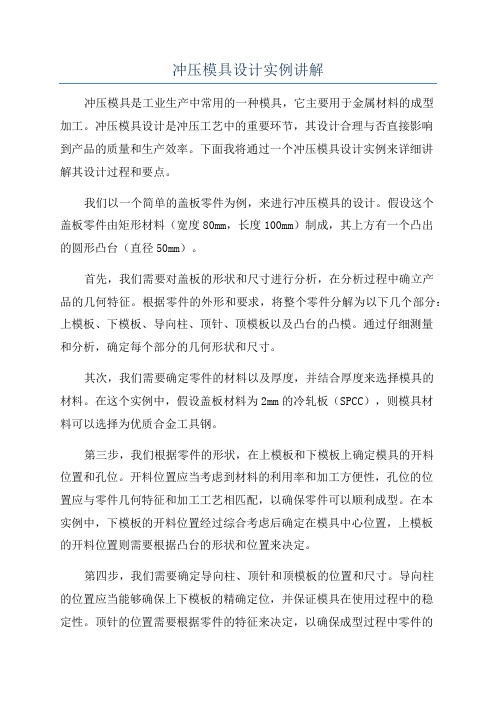
冲压模具设计实例讲解冲压模具是工业生产中常用的一种模具,它主要用于金属材料的成型加工。
冲压模具设计是冲压工艺中的重要环节,其设计合理与否直接影响到产品的质量和生产效率。
下面我将通过一个冲压模具设计实例来详细讲解其设计过程和要点。
我们以一个简单的盖板零件为例,来进行冲压模具的设计。
假设这个盖板零件由矩形材料(宽度80mm,长度100mm)制成,其上方有一个凸出的圆形凸台(直径50mm)。
首先,我们需要对盖板的形状和尺寸进行分析,在分析过程中确立产品的几何特征。
根据零件的外形和要求,将整个零件分解为以下几个部分:上模板、下模板、导向柱、顶针、顶模板以及凸台的凸模。
通过仔细测量和分析,确定每个部分的几何形状和尺寸。
其次,我们需要确定零件的材料以及厚度,并结合厚度来选择模具的材料。
在这个实例中,假设盖板材料为2mm的冷轧板(SPCC),则模具材料可以选择为优质合金工具钢。
第三步,我们根据零件的形状,在上模板和下模板上确定模具的开料位置和孔位。
开料位置应当考虑到材料的利用率和加工方便性,孔位的位置应与零件几何特征和加工工艺相匹配,以确保零件可以顺利成型。
在本实例中,下模板的开料位置经过综合考虑后确定在模具中心位置,上模板的开料位置则需要根据凸台的形状和位置来决定。
第四步,我们需要确定导向柱、顶针和顶模板的位置和尺寸。
导向柱的位置应当能够确保上下模板的精确定位,并保证模具在使用过程中的稳定性。
顶针的位置需要根据零件的特征来决定,以确保成型过程中零件的成型质量。
顶模板则需要根据零件的形状和材料选择合适的凸模形状和尺寸,以确保零件的成型质量。
最后一步,我们需要根据上述设计结果进行模具的绘图制作。
绘图要求精确、准确,需要包含所有的模具建构要素和加工尺寸等信息,以便制造部门进行模具加工和组装。
综上所述,冲压模具设计涉及到多个方面的考虑和决策,需要综合考虑零件的特征、工艺要求、材料特性等多个因素。
通过合理的设计和制作,可以保证模具的质量和使用效果,提高产品的生产效率和质量。
冲压模具的设计与制造分析

冲压模具的设计与制造分析冲压模具是制造零部件的重要设备之一,其设计与制造直接影响着工件的质量和生产效率。
本文将从设计原则、制造工艺等方面进行分析,探讨冲压模具的设计与制造过程。
冲压模具的设计应遵循以下原则:1. 合理确定冲压工艺参数:冲压模具设计的第一步是确定冲压工艺参数,包括材料的特性、板料厚度、冲裁力等。
这些参数直接影响着冲压模具的结构和尺寸,因此必须合理确定。
2. 确定冲压工艺路线:根据工件的形状、尺寸和加工要求,确定最优的冲压工艺路线,包括冲裁次序、冲裁方式等。
这有助于降低模具的复杂性和加工难度,提高生产效率。
3. 优化模具结构:冲压模具的结构应简洁、紧凑,以减少材料的浪费和制造成本。
要考虑工件的加工难度和生产效率,合理设计模具的导向元件、定位元件等部件,保证模具的稳定性和精度。
4. 考虑模具的易制造性:在设计模具时,要充分考虑模具的制造工艺和加工设备的能力,合理确定模具的尺寸、精度和加工工艺,以确保模具能够顺利制造并具有良好的性能。
5. 重视模具的可维修性:冲压模具在使用过程中可能会出现磨损、损坏等情况,因此设计时应考虑模具的可维修性。
要合理选择材料、加工工艺和装配方式,以便方便维修和更换模具的损坏部件。
冲压模具的制造主要包括以下几个步骤:1. 材料选择和准备:根据模具的要求和使用条件,选择合适的模具材料,一般为工具钢或高速钢。
材料的准备包括切割、锻造、热处理等工艺,以获得合适的模具坯料。
2. 基础件的加工:冲压模具的基础件包括模板、模架、模座等,它们的加工主要包括铣削、钻孔、车削等工艺。
这些基础件的加工精度直接影响着模具的精度和稳定性。
3. 零部件的制造:冲压模具的零部件包括导向元件、定位元件、护套、松套等,它们的制造主要包括车削、铣削、磨削等工艺。
这些零部件必须具备良好的加工精度和表面质量,以保证模具的准确性和稳定性。
4. 模具的装配和调试:在模具制造完成后,将各个零部件组装在一起,进行精确的定位和调试。
冲压模具的设计与制造分析

冲压模具的设计与制造分析随着工业的发展和技术的提升,冲压模具的应用越来越广泛,是现代制造业中不可缺少的一部分。
因此,对冲压模具的设计和制造分析具有重要的意义。
下面将对冲压模具的设计和制造分析进行探讨。
1.1 冲压模具的结构设计冲压模具结构设计的主要目的是确保模具精度、强度和耐用性。
模具应尽可能简洁,零件数目较少,这样有利于降低制造成本,并有助于维护和修理。
根据压力等级的不同,冲压模具的结构类型包括单站模、多站模、复合模等。
冲压模具的材料应具有高强度、高硬度、高耐磨性能和较好的加工性能。
主要有工具钢、硬质合金和陶瓷等材料。
其中,工具钢是目前应用最广泛的材料,而硬质合金和陶瓷等材料主要用于高精度、高效率、高要求的冲压模具。
冲压模具的设计程序一般包括产品设计、模具设计、零件加工、组装和调整等步骤。
设计人员需要了解冲压件的形状、大小、性质等信息,进行分析和计算,确定模具的结构和尺寸,绘制图纸和进行仿真分析等。
2.1 冲压模具制造工艺冲压模具的制造工艺主要包括材料处理、零件加工、组装和调整等。
为确保模具精度和质量,制造过程需要经过多道工序,从零件加工到组装,每个步骤都需要严格的质量控制。
冲压模具的制造技术包括铣削、电火花加工、线切割、抛光等,其中最主要的技术为数控加工技术。
数控加工技术可以大大提高加工精度和效率,并且可以在不同阶段实现自动化控制。
综上所述,冲压模具的设计和制造是一项极为复杂的工作,需要设计人员和制造人员具备一定的专业知识和技能,加之开发新产品的需求与对生产效率和商品质量不断提高的要求,冲压模具的应用领域将会越来越广泛,冲压模具制造业还有很大发展的潜力。
冲裁模具设计方案
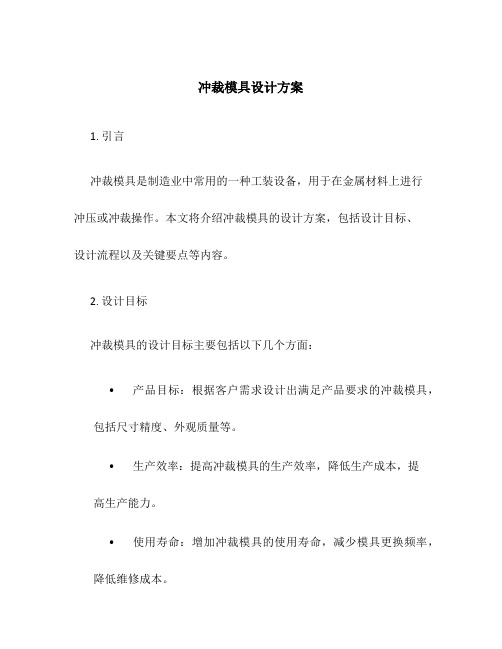
冲裁模具设计方案1. 引言冲裁模具是制造业中常用的一种工装设备,用于在金属材料上进行冲压或冲裁操作。
本文将介绍冲裁模具的设计方案,包括设计目标、设计流程以及关键要点等内容。
2. 设计目标冲裁模具的设计目标主要包括以下几个方面:•产品目标:根据客户需求设计出满足产品要求的冲裁模具,包括尺寸精度、外观质量等。
•生产效率:提高冲裁模具的生产效率,降低生产成本,提高生产能力。
•使用寿命:增加冲裁模具的使用寿命,减少模具更换频率,降低维修成本。
3. 设计流程冲裁模具的设计流程主要包括以下几个步骤:步骤一:需求分析在需求分析阶段,设计师需要与客户充分沟通,了解客户的需求和要求。
确定冲裁模具所用材料、尺寸、功能等关键要素。
步骤二:结构设计在结构设计阶段,设计师根据需求分析的结果进行结构设计。
包括模具结构的选择、零件布局、传动方式等。
步骤三:零件设计在零件设计阶段,设计师将结构设计拆分为各个零部件,并对每个零部件进行详细设计。
考虑到材料的选择、加工工艺、装配方式等。
步骤四:装配及测试在装配及测试阶段,将各个零部件进行装配,并进行测试。
通过测试对模具进行调试和优化,确保其正常运行和满足设计要求。
步骤五:模具生产在模具生产阶段,根据设计师提供的设计图纸进行模具加工制造。
在制造过程中,要注意材料的选择、加工精度的控制等。
4. 关键要点冲裁模具的设计过程中,有一些关键要点需要特别注意:•刚度和稳定性:冲裁模具在运行过程中需要承受较大的力和压力,所以刚度和稳定性是非常重要的设计要点。
需要合理选择材料、结构和加固方式,以确保冲裁模具的刚性和稳定性。
•摩擦和磨损:冲裁模具在运行过程中会产生摩擦和磨损,影响使用寿命和产品质量。
设计师需要在设计过程中考虑减小摩擦和磨损的方式,例如采用适当的润滑方式、选择高硬度材料等。
•安全性:冲裁模具在操作过程中存在一定的安全风险,设计师需要考虑安全性因素,例如防止操作人员误操作、减少尖锐边角等。
冲压模具方案可行性分析

冲压模具方案可行性分析冲压模具是冲压工艺中重要的工具,用于将板材、管材等材料通过冲击和应力作用加工成所需形状和尺寸的零件。
冲压模具的方案设计对于冲压工艺的成功实施至关重要。
本文将从多个角度进行冲压模具方案可行性分析。
1. 技术可行性:冲压模具方案要基于设计要求和产品形状来确定。
首先要对设计要求进行全面的了解和分析,包括产品的尺寸、形状、材料等方面的要求。
然后根据这些要求进行模具的设计。
通过对模具的结构和工艺进行分析,评估其是否能够满足产品的要求,以及是否可以通过冲压工艺实现产品形状和尺寸的加工。
如果无法满足,需要重新调整方案,直到找到合适的解决方案。
2. 生产可行性:冲压模具方案的可行性还需要考虑到生产过程中的可操作性和效率。
模具制造的工艺流程、工时和成本等要素都需要全面考虑。
比如,材料的选择应符合模具的制造要求,能够满足模具的寿命和生产效率要求。
此外,工艺流程的设计要合理,各个零部件的加工和装配过程应当能够高效、准确地进行。
如果存在一些困难,比如材料加工或表面处理的难度大,那么需要重新优化方案,以提高生产可行性。
3. 经济可行性:冲压模具的设计和制造涉及到较高的成本,因此方案的经济可行性也是必须考虑的因素。
首先需要对模具制造的成本进行评估,包括材料成本、加工成本和装配成本等。
然后对模具的寿命进行预测和计算,以确定模具的使用寿命和其所产生的产品数量。
在此基础上,可以计算出每个产品的模具成本,并与产品的市场价值进行比较。
如果模具成本超过产品价值,那么需要重新考虑和优化方案,以提高经济可行性。
4. 质量可行性:模具的质量是保证产品质量的基础。
因此,冲压模具方案的可行性还要评估模具的质量和稳定性。
模具的质量不仅关系到产品的加工精度和表面质量,还关系到模具的使用寿命和维护成本。
在设计和制造过程中,要注重选择合适的材料、合理的热处理工艺和严格的加工工艺,以确保模具的质量可行性。
总之,冲压模具方案可行性分析涉及到技术、生产、经济和质量等多个方面。
冲压模具结构设计及实例

冲压模具结构设计及实例冲压模具是指用于冲压工艺的模具,它是冲压工艺中的重要组成部分。
冲压模具的结构设计对于冲压工艺的质量和效率具有重要影响。
本文将从冲压模具的结构设计和实例两个方面进行探讨。
一、冲压模具的结构设计冲压模具的结构设计是冲压工艺的关键环节之一。
一个优秀的冲压模具需要具备以下几个方面的设计要素:1. 合理的结构布局:冲压模具的结构布局应该合理,能够满足冲压工艺的要求,并且方便操作和维护。
通常包括上下模座、导向装置、冲头、顶出装置等部分。
2. 合适的材料选择:冲压模具需要承受较大的冲击和摩擦力,因此材料的选择非常重要。
常用的材料有优质合金钢、工具钢等,具有较高的硬度和耐磨性。
3. 合理的导向装置:导向装置能够确保上下模具的准确对位,以保证冲压工艺的精度。
常见的导向装置有滑块导向、销针导向等。
4. 适当的顶出装置:顶出装置能够将冲制件从模具中顶出,以便进行下一步的操作。
顶出装置的设计需要考虑冲制件的形状和尺寸等因素。
5. 合理的冲头设计:冲头是冲压模具的重要组成部分,其设计需要考虑冲制件的形状和尺寸等因素。
同时,冲头的材料选择和热处理也非常重要。
二、冲压模具结构设计实例以下是一个钣金冲压模具的结构设计实例:该冲压模具用于加工一种带有凹槽的钣金零件。
该零件的厚度为2mm,材料为优质冷轧板。
根据对该零件的要求,设计出了以下的冲压模具结构:1. 上模座:采用整体式上模座,材料为优质合金钢。
上模座上设置有导向装置,确保上下模具的准确对位。
2. 下模座:采用整体式下模座,材料为优质合金钢。
下模座上设置有顶出装置,以便将冲制件顶出。
3. 冲头:冲头采用硬质合金材料制造,并经过热处理,以提高其硬度和耐磨性。
冲头的形状和尺寸与钣金零件的凹槽相匹配。
4. 引导装置:在上模座和下模座上设置有引导装置,确保上下模具的准确对位,以保证冲制件的精度。
通过以上的结构设计,该冲压模具能够满足钣金零件的冲压工艺要求。
冲制过程中,上下模具准确对位,冲头能够将钣金材料冲剪成带有凹槽的零件,并通过顶出装置将零件顶出,以便进行下一步的操作。
冲压模具的设计与制造分析
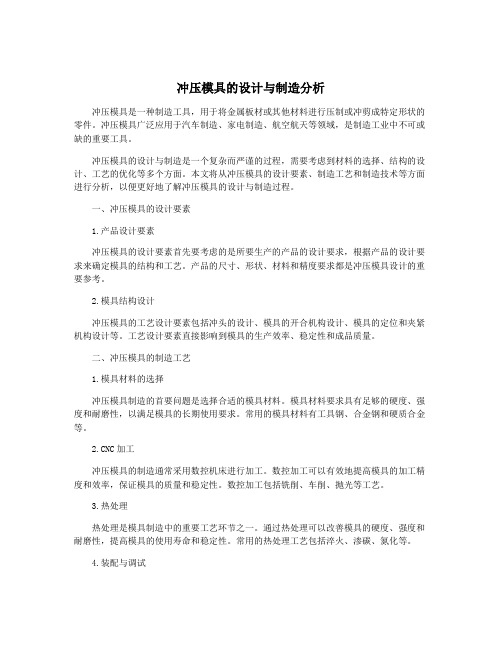
冲压模具的设计与制造分析冲压模具是一种制造工具,用于将金属板材或其他材料进行压制或冲剪成特定形状的零件。
冲压模具广泛应用于汽车制造、家电制造、航空航天等领域,是制造工业中不可或缺的重要工具。
冲压模具的设计与制造是一个复杂而严谨的过程,需要考虑到材料的选择、结构的设计、工艺的优化等多个方面。
本文将从冲压模具的设计要素、制造工艺和制造技术等方面进行分析,以便更好地了解冲压模具的设计与制造过程。
一、冲压模具的设计要素1.产品设计要素冲压模具的设计要素首先要考虑的是所要生产的产品的设计要求,根据产品的设计要求来确定模具的结构和工艺。
产品的尺寸、形状、材料和精度要求都是冲压模具设计的重要参考。
2.模具结构设计冲压模具的工艺设计要素包括冲头的设计、模具的开合机构设计、模具的定位和夹紧机构设计等。
工艺设计要素直接影响到模具的生产效率、稳定性和成品质量。
二、冲压模具的制造工艺1.模具材料的选择冲压模具制造的首要问题是选择合适的模具材料。
模具材料要求具有足够的硬度、强度和耐磨性,以满足模具的长期使用要求。
常用的模具材料有工具钢、合金钢和硬质合金等。
C加工冲压模具的制造通常采用数控机床进行加工。
数控加工可以有效地提高模具的加工精度和效率,保证模具的质量和稳定性。
数控加工包括铣削、车削、抛光等工艺。
3.热处理热处理是模具制造中的重要工艺环节之一。
通过热处理可以改善模具的硬度、强度和耐磨性,提高模具的使用寿命和稳定性。
常用的热处理工艺包括淬火、渗碳、氮化等。
4.装配与调试冲压模具的装配与调试是模具制造的最后阶段。
在装配与调试过程中,需要对模具的各个零部件进行组装与调整,以保证模具的精度、稳定性和可靠性。
1.模具CAD/CAM技术模具CAD/CAM技术是现代模具制造的重要技术手段。
通过CAD/CAM技术可以实现模具的设计、工艺规划、数控加工程序生成等全过程数字化,提高设计效率和生产精度。
2.先进制造技术冲压模具的制造技术在不断发展与进步,涌现了许多新的制造技术。
冲压模具的设计与制造分析

冲压模具的设计与制造分析1. 引言1.1 冲压模具的设计与制造分析冲压模具的设计与制造分析是现代制造业中至关重要的一环。
冲压模具作为生产加工中的关键装备,在各种行业中都扮演着不可或缺的角色。
通过对冲压模具的设计与制造进行深入分析,可以更好地理解其在生产制造中的作用和意义。
冲压模具的设计与制造是一个综合性强、工艺性较强的领域。
在设计过程中,需要考虑材料的选择、模具结构的设计、工艺参数的确定等诸多因素;在制造过程中,要注重工艺的精细化、设备的先进性、质量的稳定性等方面。
只有将设计与制造紧密结合,才能保证冲压模具的性能和精度达到要求。
冲压模具的设计与制造也是一个不断创新和发展的过程。
随着科技的不断进步和市场需求的不断变化,冲压模具的设计与制造技术也在不断更新迭代。
必须与时俱进,不断学习和掌握最新的技术和方法,才能在激烈的市场竞争中立于不败之地。
冲压模具的设计与制造分析是一个复杂而又充满挑战的领域。
只有不断总结经验、研究新技术、提高自身素质,才能在这个领域中获得成功。
2. 正文2.1 冲压模具的概念与分类冲压模具是一种用于在金属板或带材上施加力量,使其产生塑性变形并最终成型为所需形状的工具。
它是冲压加工中必不可少的重要设备,广泛应用于汽车制造、电子设备、家电产品等行业。
根据不同的使用需求和工艺要求,冲压模具可以分为以下几类:1.单操作模具:单操作模具是最基本的一种冲压模具,其结构简单,适用于对称或简单形状的产品加工。
2.复合模具:复合模具包括多个工作站,可以同时进行多道工序的加工,提高生产效率和产品质量。
3.连续模具:连续模具适用于对冲压速度要求较高的产品加工,能够实现高速连续冲压。
4.特殊形状模具:特殊形状模具适用于特殊形状产品的加工,如异形孔、凹凸结构等。
5.逐次成型模具:逐次成型模具适用于需要多次冲压工序才能完成的产品加工,通常用于复杂形状的产品制造。
不同类型的冲压模具在设计和制造上有各自特点,但都是为了实现产品的快速、精准成型而存在的重要工具。
冲压模具设计实施方案和制造实例[]
![冲压模具设计实施方案和制造实例[]](https://img.taocdn.com/s3/m/d7d3b55e1eb91a37f1115cc6.png)
冲压模具设计与制造实例例:图1所示冲裁件,材料为A3,厚度为2mm,大批量生产.试制定工件冲压工艺规程、设计其模具、编制模具零件地加工工艺规程.零件名称:止动件生产批量:大批材料:A3材料厚度:t=2mm一、冲压工艺与模具设计1.冲压件工艺分析①材料:该冲裁件地材料A3钢是普通碳素钢,具有较好地可冲压性能.②零件结构:该冲裁件结构简单,并在转角有四处R2圆角,比较适合冲裁.③尺寸精度:零件图上所有未注公差地尺寸,属自由尺寸,-0.74 0-0.52-0.52-0.52-0.52可按IT14级确定工件尺寸地公差.孔边距12mm 地公差为-0.11,属11级精度.查公差表可得各尺寸公差为:零件外形:65 mm24 mm30 mm R30 mm R2 mm零件内形:10 mm孔心距:37±0.31mm 结论:适合冲裁.2.工艺方案及模具结构类型该零件包括落料、冲孔两个工序,可以采用以下三种工艺方案:①先落料,再冲孔,采用单工序模生产. ②落料-冲孔复合冲压,采用复合模生产. ③冲孔-落料连续冲压,采用级进模生产.方案①模具结构简单,但需要两道工序、两套模具才能完成零件地加工,生产效率较低,难以满足零件大批量生产地需求.由于零件结构简单,为提高生产效率,主要应采用复合冲裁或级进冲裁方式.由于孔边距尺寸12 mm 有公差要求,为了更好地保证此尺寸精度,最后确定 用复合冲裁方式进行生产.+0.36 0-0.11工件尺寸可知,凸凹模壁厚大于最小壁厚,为便于操作,所以复合模结构采用倒装复合模及弹性卸料和定位钉定位方式.3.排样设计查《冲压模具设计与制造》表2.5.2,确定搭边值:两工件间地搭边:a=2.2mm工件边缘搭边:a1=2.5mm步距为:32.2mm条料宽度B=D+2a1=65+2*2.5=70确定后排样图如2所示一个步距内地材料利用率η为:η=A/BS×100%=1550÷(70×32.2)×100%=68.8%查板材标准,宜选900mm×1000mm地钢板,每张钢板可剪裁为14张条料(70mm×1000mm),每张条料可冲378个工件,则η为:η=nA1/LB×100%=378×1550/900×1000×100%=65.1%即每张板材地材料利用率为65.1%4.冲压力与压力中心计算⑴冲压力落料力F总=1.3Ltτ=1.3×215.96×2×450=252.67(KN)其中τ按非退火A3钢板计算.冲孔力F冲=1.3Ltτ=1.3×2π×10×2×450=74.48(KN)其中:d 为冲孔直径,2πd为两个圆周长之和. 卸料力F卸=K卸F卸=0.05×252.67=12.63(KN)推件力F推=nK推F推=6×0.055×37.24=12.30(KN)其中n=6 是因有两个孔.总冲压力:F总= F落+ F冲+ F卸+ F推=252.67+74.48+12.63+12.30=352.07(KN)⑵压力中心如图3所示:由于工件X方向对称,故压力中心x0=32.5mm=13.0mm其中:L1=24mm y1=12mmL2=60mm y2=0mmL3=24mm y1=12mmL4=60mm y4=24mmL5=60mm y5=27.96mmL6=60mm y6=24mmL7=60mm y7=12mmL8=60mm y8=12mm计算时,忽略边缘4-R2圆角.由以上计算可知冲压件压力中心地坐标为(32.5,13)5.工作零件刃口尺寸计算落料部分以落料凹模为基准计算,落料凸模按间隙值配制;冲孔部分以冲孔凸模为基准计算,冲孔凹模按间隙值配制.即以落料凹模、冲孔凸模为基准,凸凹模按间隙值配制.刃口尺寸计算见表16.工作零件结构尺寸落料凹模板尺寸:凹模厚度:H=kb(≥15mm)H=0.28×65=18.2.mm凹模边壁厚:c≥(1.5~2)H=(1.5~2)×18.2=(27.3~36.4)mm 实取c=30mm凹模板边长:L=b+2c=65+2×30=125mm查标准JB/T -6743.1-94:凹模板宽B=125mm故确定凹模板外形为:125×125×18(mm).将凹模板作成薄型形式并加空心垫板后实取为:125×125×14(mm).凸凹模尺寸:凸凹模长度:L=h1+h2+h=16+10+24=50(mm)其中:h1-凸凹模固定板厚度h2-弹性卸料板厚度h-增加长度(包括凸模进入凹模深度,弹性元件安装高度等)凸凹模内外刃口间壁厚校核:根据冲裁件结构凸凹模内外刃口最小壁厚为7mm,根据强度要求查《冲压模具设计与制造》表2.9.6知,该壁厚为4.9mm即可,故该凸凹模侧壁强度足够.冲孔凸模尺寸:凸模长度:L凸= h1+h2+h3=14+12+1440mm其中:h1-凸模固定板厚h2-空心垫板厚h3-凹模板厚凸模强度校核:该凸模不属于细长杆,强度足够.7.其它模具零件结构尺寸根据倒装复合模形式特点:凹模板尺寸并查标准JB/T-6743.1-94,确定其它模具模板尺寸列于表2:根据模具零件结构尺寸,查标准GB/T2855.5-90选取后侧导柱125×25标准模架一副.8.冲床选用根据总冲压力F总=352KN,模具闭合高度,冲床工作台面尺寸等,并结合现有设备,选用J23-63开式双柱可倾冲床,并在工作台面上备制垫块.其主要工艺参数如下:公称压力:63KN滑块行程:130mm行程次数:50次/分最大闭合高度:360mm连杆调节长度:80mm工作台尺寸(前后×左右):480mm×710mm二、模具制造1、主要模具零件加工工艺过程制件:柴油机飞轮锁片材料:Q235料厚:1.2mm该制件为大批量生产,制品图如下:(一)冲裁件地工艺分析1、冲裁件为Q235号钢,是普通碳素钢,有较好地冲压性能,由设计书查得τ=350Mpa.2、该工作外形简单,规则,适合冲压加工.3、所有未标注公差尺寸,都按IT14级制造.4、结论:工艺性较好,可以冲裁.方案选择:方案一:采用单工序模.方案二:采用级进模.方案三:采用复合模.单工序模地分析单工序模又称简单模,是压力机在一次行程内只完成一个工序地冲裁模.工件属大批量生产,为提高生产效率,不宜采用单工序模,而且单工序模定位精度不是很高,所以采用级进模或复合模.级进模地分析级进模是在压力机一次行程中,在一副模具上依次在几个不同地位置同时完成多道工序地冲模.因为冲裁是依次在几个不同地位置逐步冲出地,因此要控制冲裁件地孔与外形地相对位置精度就必须严格控制送料步距,为此,级进模有两种基本结构类型:用导正销定距地级进模和用侧刃定距地级进模.另外级进模有多个工序所以比复合模效率低.复合模地分析复合模是在压力机一次工作行程中,在模具同一位置同时完成多道工序地冲模.它不存在冲压时地定位误差.特点:结构紧凑,生产率高,精度高,孔与外形地位置精度容易保证,用于生产批量大.复合模还分为倒装和正装两种,各有优缺点.倒装复合模但采用直刃壁凹模洞口凸凹模内有积存废料账力较大,正装复合模地优点是:就软就薄地冲裁件,冲出地工件比较平整,平直度高,凸凹模内不积存废料减小孔内废料地胀力,有利于凸凹模减小最小壁厚.经比较分析,该制件地模具制造选用导料销加固定挡料销定位地弹性卸料及上出件地正装复合模.(二)排样图设计及冲压力和压力中心地计算由3-6,3-8表可查得:a1=0.8,a=1.0,△=0.6查书391.料宽计算:B=(D+2a)=62+2*1.0=64mm2.步距:A=D=a1=62+0.8=62.8mm3.材料利用率计算:η=A/BS×100%=πR2-(πR2+12*4.2)/62.8*64=3.14*312-(3.14*18.52+50.4)/62.8*64×100%=47.08%(其中a是搭边值,a1是工作间隙,D是平行于送料方向冲材件地宽度,S是一个步距内制件地实际面积,A是步距,B 是料宽,R1是大圆半径,R2是小圆半径,12×4.2是方孔地面积,η为一个步距内地材料地利用率)4.冲裁总压力地确定:L=2*3.14*31+2*3.14*18.5+12+2*4.2=331.26(周边总长)计算冲裁力:F=KLtτ查设计指导书得τ=350MpaF=1.3*331.6*1.2*350≈180KN落料力:F落=1.3ltτ=1.3*(2*3.14*31)*1.2*350=106295.28N卸料力:F卸=kF落=0.02*106295.28=2125.9N冲孔力:F冲=1.3*3.14dtτ+1.3*(12+2*4.2)*1.2*350=74572.68N顶件力:F顶=-k2F落=0.06*106295.28=6377.7N冲裁总压力:F∑=F落+F卸+F冲+F顶=106295.28+2125.9+74572.68+6377.7=189.4KNF压=(1.1~1.3)F∑=246KN说明:K为安全系数,一般取1.3;k为卸料力系数,其值为0.02~0.06,在上式中取值为0.02;k2为顶件力系数,其值为0.03~0.07,式中取值为0.065.压力机地初步选用:根据制件地冲裁地公称压力,选用开式双柱可倾式压力机,公称压力为350k N 形号为J23-35 满足:F压≥F∑版权申明本文部分内容,包括文字、图片、以及设计等在网上搜集整理.版权为个人所有This article includes some parts, including text, pictures, and design. Copyright is personal ownership.eUts8。
- 1、下载文档前请自行甄别文档内容的完整性,平台不提供额外的编辑、内容补充、找答案等附加服务。
- 2、"仅部分预览"的文档,不可在线预览部分如存在完整性等问题,可反馈申请退款(可完整预览的文档不适用该条件!)。
- 3、如文档侵犯您的权益,请联系客服反馈,我们会尽快为您处理(人工客服工作时间:9:00-18:30)。
为了减少冲裁力,大型冲裁件或厚板冲裁的镶拼模,可以把凸模(冲孔时)或凹模(落料时)制成波浪形斜刃,如图2.9.11所示。斜刃应对称,拼接面应取在最低或最高处,每块一个或半个波形,斜刃高度H一般取l-3倍的板料厚度。ﻭ(3)镶拼结构的固定方法
镶拼结构的固定方法主要有以下几种:ﻭ1)平面式固定 即把拼块直接用螺钉、销钉紧固定位于固定板或模座平面上,如图2.9.9所示。这种固定方法主要用于大型的镶拼凸、凹模。ﻭ2)嵌入式固定 即把各拼块拼合后嵌入固定板凹槽内,如图2.9.12a所示。
第一篇冲裁模
一 、搭边值与侧刃宽度
搭边值ﻩﻩ单位(mm)
料厚
手送料
自动送料
圆形
非圆形
往复送料
m
n
m
n
M
n
m
n
≤1
1.5
1.5
2
1.5
3
2
3
2
>1-2
2
1.5
2.5
2
3.5
2.5
>2-3
2.5
2
3
2.5
4
3.5
>3-4
3
2.5
3.5
3
5
4
4
3
>4-5
4
3
5
4
6
5
5
4
>5-6
5
4
6
5
7
6
6
5
>6-8
6
5
材料
抗拉强度
材料
抗拉强度
A1
400
20
500
A1E
25
550
A2
420
45
730
A2F
50
770
B2
08MnV
550
B2F
09MnR
500
A3
470
09Mn
A3F
16MnR
620
B3
16Mn
B3F
65Mn
900
08F(DC04)
360
65Si2MnA
1600
08
400
紫铜
软:210
10F
380
硬:300
③应沿转角、尖角分割,并尽量使拼块角度大于或等于90°,见图2.9.10j。ﻭ④圆弧尽量单独分块,拼接线应在离切点4-7mm的直线处,大圆弧和长直线可以分为几块,图2.9.9 。ﻭ⑤拼接线应与刃口垂直,而且不宜过长,一般为12-15mm,图2.9.9。
2)便于装配调整和维修
①比较薄弱或容易磨损的局部凸出或凹进部分,应单独分为一块。如图2.9.8、图2.9.10a。
镶拼结构有镶接和拼接两种:镶接是将局部易磨损部分另做一块,然后镶入凹模体或凹模固定板内,如图2.9.8所示;拼接是整个凸、凹模的形状按分段原则分成若干块,分别加工后拼接起来,如图2.9.9所示。
ﻭ图2.9.8镶接凹模 图2.9.9拼接结构
(2)镶拼结构的设计原则
凸模和凹模镶拼结构设计的依据是凸、凹模形状、尺寸及其受力情况、冲裁板料厚度等。镶拼结构设计的一般原则如下:ﻭ1)力求改善加工工艺性,减少钳工工作量,提高模具加工精度 ﻭ①尽量将形状复杂的内形加工变成外形加工,以便于切削加工和磨削,见图2.9.10a、b、d、g等。ﻭ②尽量使分割后拼块的形状、尺寸相同,可以几块同时加工和磨削,见图2.9.10d、g、f等,一般沿对称线分割可以实现这个目的。
10
410
铝
软:70
20F
470
硬:130
五:冲裁间隙的确定
1、冲裁间隙的概念
冲裁间隙指凸模刃口与凹模刃口之间的间隙。 ﻭZ=Da—dt
Z-冲裁间隙 ﻭDa-凹模刃口尺寸ﻭdt-凸模刃口尺寸ﻭZ正常时:上下微裂纹重合。
2、冲裁间隙对冲压的影响ﻭ(1)对断面质量的影响ﻭ
(2)间隙对尺寸精度的影响。
由于弹性变形的存在,冲裁结束后出现弹性恢复,使尺寸与凸凹模刃口尺寸产生尺寸偏差,而弹性变形大小与冲裁间隙有直接的关系。 ﻭ
②拼块之间应能通过磨削或增减垫片方法,调整其间隙或保证中心距公差,如图2.9.10h、I。
③拼块之间应尽量以凸、凹槽形相嵌,便于拼块定位,防止在冲压过程发生相对移动,如图2.9.10k。
3)满足冲压工艺要求,提高冲压件质量 为此,凸模与凹模的拼接线应至少错开3-5mm,以免冲裁件产生毛刺,如图2.9.9;拉深模拼接线应避开材料有增厚部位,以免零件表面出现拉痕
底板应加垫片时的冲孔直径
孔径d
D ﻭF
料厚S
<1.5
1.75
2
2.1
2.5
2.75
3
3.5
4
4.5
5
5.5
6
6.5
8
2~4
t=1-3mm,c=(5%-8%)tﻭt=3-5mm,c=(8%-10%)tﻭ硬材料:t<1mm,c=(4%-5%)tﻭt=1-3mm,c=(6%-8%)ﻭt=3-8mm,c=(8%-13%)
六、凸模和退料板、凹模和顶出器之间的间隙ﻩ
ﻩﻩﻩﻩﻩ单位:mm
料厚
最大间隙
料厚
最大间隙
料厚
最大间隙
≤0.2
滑配
7
6
6
7
7
6
>8
7
5
8
7
9
8
8
7
二、条料宽度的确定
为了保证送料的顺利进行,必须考虑条料的单向(负向)公差。
B=D+2a+Δ
式中:
B—条料宽度的基本尺寸(mm)
D—工件在宽度方向的尺寸(mm)
Δ--条料的单向(负向)公差(mm)
a—侧搭边的最小值(mm)
三、冲裁力、退料力、顶件力、总冲压力的计算
四、各种常用材料计算采用的抗拉强度(N/ )
3)压入式固定 即把各拼块拼合后,以过盈配合压入固定板孔内,如图2.9.12b所示。ﻭ4)斜楔式固定 如图2.9.12c所示。ﻭ此外,还有用粘结剂浇注等固定方法。
ﻭ图2.9.11斜刃拼块结构 图2.9.12镶拼结构固定方法
九:凸模加垫板的计算
下表是根据材料08钢(бb=40kg/mm2),底板材料HT25-47(许用压应力=9kg/mm2)按上式计算而得。
(3)间隙对冲裁力的影响 ﻭ冲裁间隙对冲裁力的影晌规律是间隙越小,变形区内压应力成分越大,拉应力成分越小,材料变形抗力增加,冲裁力就越大。反之,间隙越大,变形区内拉应力成分就越大,变形抗力降低,冲裁力就小。间隙达材料厚的5%-20%时,冲裁力下降不明显。
当单边间隙Z增大到材料厚度的15%-20%时,卸料力为0。 ﻭ3、合理间隙值的确定:ﻭ根据近年来的研究与使用经验,在确定间隙值时要按要求分类选用。对于尺寸精度、断面垂直度要求 高的制件应选用较小间隙值,对于断面垂直度与尺寸精度要求不高的制件,应以降低冲裁力、提高模具寿命为主,可采用较大间隙值。其单边间隙可按下列经验公式选用: ﻭ软材料:t<1mm,c=〔3%-4%〕t
>0.2-0.5
0.1
>0.5-1
0.3
>1-2
0.4
>2
0.5
七、螺钉与销子到零件边缘的最小距离
八、凸、凹模的镶拼结构(1)镶拼结构的应Fra bibliotek场合及镶拼方法
对于大、中型的凸、凹模或形状复杂、局部薄弱的小型凸、凹模,如果采用整体式结构,将给锻造、机械加工或热处理带来困难,而且当发生局部损坏时,就会造成整个凸、凹模的报废,因此常采用镶拼结构的凸、凹模。