50t连续加料操作工艺
50t新概念电弧炉大纲(新)
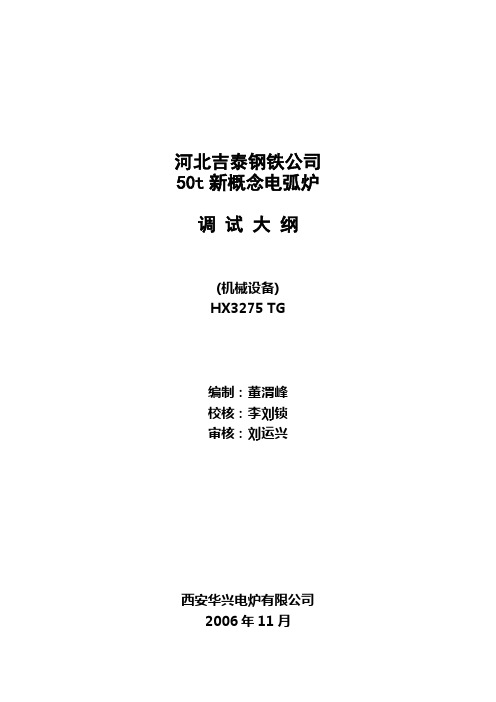
河北吉泰钢铁公司50t新概念电弧炉调试大纲(机械设备)HX3275 TG编制:董渭峰校核:李刘锁审核:刘运兴西安华兴电炉有限公司2006年11月目录1. 前言2. 设备调试2.1 设备冷态调试2.2 设备热态调试1. 前言该设备是为河北吉泰钢铁公司电炉厂新建50t新概念电弧炉而设计和制造。
用于该厂钢水的熔炼,其具体功能及主要技术参数见HX3275 SM(50t新概念使用说明书)。
该文件与HX3275 SM(机械设备)为配套文件,故该设备的布置形式及结构简介参见HX3275 SM相应部分。
2. 设备调试设备调试分设备冷态调试和热态调试。
2.1 设备冷态调试2.1.1 设备调试前的准备工作a. 设备调试应在设备安装初步验收合格的基础上进行,初步崐验收的主要内容含:①设备完整性验收;②设备安装主要尺寸验收;③设备安装精度验收;④设备公用设施供给验收;⑤设备安装主要技术要求验收;⑥设备修复件的主要尺寸及技术要求验收。
b. 设备操作人员培训①设备操作人员应熟悉该设备工作原理,设备组成及设备主要结构。
②设备操作人员应具备炉前操作的基本训练和培训。
③设备操作人员应接受安技教育并确认合格。
c. 设备操作的必要工具。
d. 设备检修的常用工具。
2.1.2 设备冷态调试a. 水冷炉盖及其提升机构、旋转机构。
(旋转支撑、水平锁定应到位)炉盖反复提升、旋转3次,检查炉盖行程,保证工作行程450mm;炉盖下沿圈应下降到下限位置时(即盖在炉体上时)旋转锁定插销应可靠地插入倾动平台相应的孔之中,炉盖提升至上限位置时,旋转锁定连杆插销,应可靠地提出倾动平台保证旋转动作,炉盖旋开角度≥70°;炉盖通水试验(水压1.0MPa)应无渗漏等异常现象;炉盖提升与下降、旋转时,炉盖进出水管(金属软管)应无扭折现象。
炉盖提升与下降、旋转时,应保持基本水平,否则应调整连接位置或节流阀的开口大小。
b. 电极升降装置①电极提升速度调整:~9m/min(max)②电极下降速度调整:~6m/min(max)③电极夹紧装置调整:夹紧力达到196 KN抱圈行程不小于40mm上述①~③项调整好后应分别运行3次。
最新年产50万吨短流程绿色电炉炼钢厂可行性研究报告

最新年产50万吨短流程绿色电炉炼钢厂可行性研究报告目录一、节能炼钢工艺 (1)二、供电 (10)三、自动化控制系统 (10)四、给排水设施 (11)五、通风除尘设施 (12)六、燃气设施 (13)七、热力设施 (15)八、检验设施............................................ .16九、土建............................................... .16十、投资估算........................................... .16十一、公司简介.......................................... .18一、节能炼钢工艺1、概述年产50万吨短流程绿色炼钢厂配置60t超高功率交流电弧炉一座,电炉配置一套DP60型废钢预热成套设备,利用电炉四孔高温烟气加热炉料,以提高电炉产量和节省电能,经过预热通道后的尾气仍有650℃的温度需进入余热锅炉再次利用,并将尾气温度降低至204℃以下,最后与电炉的二次烟气混合经布袋除尘器净化外排。
电炉节能炼钢工艺流程如下:四孔炉气→废钢预热通道→重力沉降与余热锅炉→一次烟气混合→布袋除尘器→排气筒。
电炉节能炼钢废钢预热输送成套设备是当今最先进、清洁、节能和利于环保的炼钢技术、设备,已被河南舞钢、冀南特钢、湖北华鑫特钢、芜湖新兴铸管有限责任公司、越南DANA-Y钢铁公司、世界顶尖钢铁企业韩国浦项制铁POSCO张家港不锈钢公司等企业广泛采用。
其工艺过程,能预热输送槽内的废钢,能够节约电能和化学能,同时也改善了工作环境,没有料篮加料过程中产生的二次烟尘,同时一次烟气预热废钢后仍以高温离开预热段,保证了烟尘中污染物的完全燃烧,避免了有味气体的产生。
连续式加料预热系统冶炼熔池平稳,和料蓝加料的电炉相比显著降低了对电网产生的冲击。
和其它炉型相比,连续式加料技术可降低车间内噪音和粉尘明显改善工作环境,由于这是一种高效的技术,可以减小和降低电炉、变电所、布袋除尘及冶炼设备的投资,提高了整个车间生产效率。
75t电炉连续加料冶炼工艺

75T连续加料电弧炉冶炼工艺操作规程闫利1、连续加料电炉冶炼工艺是一种电炉冶炼新工艺,采用的是加料不旋开炉盖而由连续加料装置将废钢连续送入炉中,在冶炼同时对炉料进行预热,送电熔化时,炉中产生的烟气将加料装置中的废钢预热。
送电熔化过程中平熔池冶炼,除新开炉第一炉料篮顶装存在传统的冶炼点弧、穿井,直接送电冶炼、主熔化、熔末、升温,其工艺主导是单渣冶炼,熔氧结合,综合脱氧,留钢、留渣操作。
2、送电伊始启动连续加料装置,加入白灰800-1000公斤,白云石300-400公斤,提前造渣。
3、炉门氧枪先中量供氧(~800Nm³/H),炉壁氧枪供氧量低氧(500-800Nm³/H)熔池形成,液面逐渐上升,炉内钢水大于40T时,提高炉壁氧枪供氧量(约800-1000Nm³/H),炉门氧枪供氧(约1000-1400Nm³/H),氧枪开启同时,喷碳操作,当水平加料停止送料时,炉门氧枪供氧量约(1000-1200Nm³/H),钢水全熔后炉壁氧枪选择500-600Nm³/H,炉门氧枪供大氧或超氧将炉渣吹稀做出钢准备,流渣操作;4、炉门氧枪小心操作,返氧时迅速调整氧枪位置并将供氧流量调小,不可顶住炉料吹氧,炉长观察炉内熔炼情况,作出相应操作指示,通知配电工停送电操作;5、连续加料装置前期适当提高送料速度,待废钢塌料至四孔加料口以下,或炉料熔化90%以上时,形成大熔池,补加600-800公斤石灰,补加白云石,碳枪根据炉内渣况调节喷碳量,全程平熔池埋弧操作,造泡沫渣,保证渣层厚度,全程埋弧操作,观察炉内情况,确定投入水平加料速度,炉壁及时氧枪投用,根据炉料情况调整炉壁氧枪供氧量;6、水平加料投入后,必须有专人负责检查水平加料所供废钢料型,以及四孔处废钢熔化状态;若出现堆起料墙的情况,可以减慢上料速度,吹氧助熔;7、炉料全熔后,炉门氧枪流量加大,深吹搅拌,此时注意控制升温速度,温度成分合格后,调整渣子碱度,组织出钢,留钢操作,留钢量30-40T;8、必须注意控制留钢量,每炉留钢量不少于30T,顶装料时,留钢量不小于20T,做到留钢留渣操作,严禁刻意排渣操作;9、炉料熔化90%左右,取参考样分析C、P等元素。
简述50T系统工艺流程及重要控制点
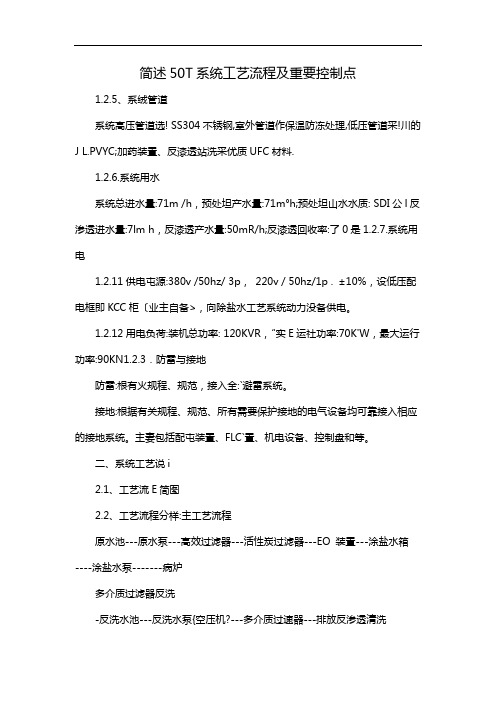
简述50T系统工艺流程及重要控制点1.2.5、系绒管道系统高压管道选! SS304不锈钢,室外管道作保温防冻处理,低压管道采!川的J L.PVYC;加药装置、反漆透站洗采优质UFC材料.1.2.6.系统用水系统总进水量:71m /h,预处坦产水量:71m°h;预处坦山水水质: SDI公l反渗透进水量:7lm h,反漆透产水量:50mR/h;反漆透回收率:了0是1.2.7.系统用电1.2.11供电屯源:380v /50hz/ 3p,220v / 50hz/1p . ±10%,设低压配电框即KCC柜〔业主自备>,向除盐水工艺系统动力没备供电。
1.2.12用电负荷:装机总功率: 120KVR,“实E运社功率:70K'W,最大运行功率:90KN1.2.3.防雷与接地防雷:根有火规程、规范,接入全:`避雷系统。
接地:根据有关规程、规范、所有需要保护接地的电气设备均可靠接入相应的接地系统。
主妻包括配屯装置、FLC`置、机电设备、控制盘和等。
二、系统工艺说i2.1、工艺流E简图2.2、工艺流程分样:主工艺流程原水池---原水泵---高效过滤器---活性炭过滤器---EO 装置---涂盐水箱----涂盐水泵-------病炉多介质过滤器反洗-反洗水池---反洗水泵{空压机?---多介质过速器---排放反渗透清洗除盐水箱-清沅水箱---洁洗水系—-—清洗洁器-——0组.件--—排版2.3、系统工艺描述根据工艺流程海木系统分为三个羊元来进行设备性能指迩:预处担单元、反渗透单元和控制羊元。
预处理单元:采用自动控制方式.预处坦的作用就是对不符合反渗透膜进水条件的原水进行处理,云除原水中的悬浮物、股体及部分有机物、改善供水环境,使之满足进入R0系统进水条什,充分保证出水满足污染指数小于4的反渗透的进水要求,减少、延锾膜的污染、延长其寿命。
它由:原水箱、原水复、反洗水泵、多介质过滤器及阻坛剂投加夜置红成。
连续加料炼钢工艺流程

连续加料炼钢工艺流程
下载温馨提示:该文档是我店铺精心编制而成,希望大家下载以后,能够帮助大家解决实际的问题。
文档下载后可定制随意修改,请根据实际需要进行相应的调整和使用,谢谢!
Download Tip: This document has been carefully written by the editor. I hope that after you download, they can help you solve practical problems. After downloading, the document can be customized and modified. Please adjust and use it according to actual needs. Thank you!
连续加料炼钢工艺流程:
①原料准备:将铁水、废钢等原材料预处理,确保成分符合炼钢要求。
②转炉冶炼:铁水倒入转炉,加入废钢,通过吹氧去碳,实现初步脱碳、脱磷、脱硫,同时控制温度和化学成分。
③连续加料:在吹氧炼钢过程中,根据化学分析结果,连续、精确地加入合金料和石灰等造渣材料,调整钢液成分。
④动态控制:采用计算机模型动态监控炉内反应,实时调整氧气流量、加料速度等,保证冶炼过程高效稳定。
⑤出钢与炉外精炼:一旦达到预定成分和温度,钢液被倾倒至钢包中,随后送入LF炉或RH炉进行炉外精炼,进一步去气、去夹杂,精确调整化学成分。
⑥连铸成型:精炼后的钢液连续浇注到连铸机中,通过水冷结晶形成初轧坯。
⑦切割与检验:连铸坯按设定长度切割,进行表面质量和内部质量的初步检验。
⑧缓冷或热送:根据后续加工需求,连铸坯进行缓冷或直接热送到轧钢厂。
50t连续加料操作工艺
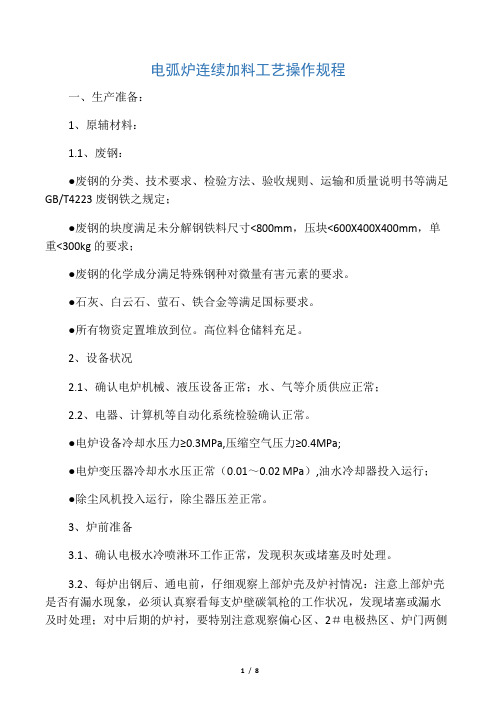
电弧炉连续加料工艺操作规程一、生产准备:1、原辅材料:1.1、废钢:●废钢的分类、技术要求、检验方法、验收规则、运输和质量说明书等满足GB/T4223废钢铁之规定;●废钢的块度满足未分解钢铁料尺寸<800mm,压块<600X400X400mm,单重<300kg的要求;●废钢的化学成分满足特殊钢种对微量有害元素的要求。
●石灰、白云石、萤石、铁合金等满足国标要求。
●所有物资定置堆放到位。
高位料仓储料充足。
2、设备状况2.1、确认电炉机械、液压设备正常;水、气等介质供应正常;2.2、电器、计算机等自动化系统检验确认正常。
●电炉设备冷却水压力≥0.3MPa,压缩空气压力≥0.4MPa;●电炉变压器冷却水水压正常(0.01~0.02 MPa),油水冷却器投入运行;●除尘风机投入运行,除尘器压差正常。
3、炉前准备3.1、确认电极水冷喷淋环工作正常,发现积灰或堵塞及时处理。
3.2、每炉出钢后、通电前,仔细观察上部炉壳及炉衬情况:注意上部炉壳是否有漏水现象,必须认真察看每支炉壁碳氧枪的工作状况,发现堵塞或漏水及时处理;对中后期的炉衬,要特别注意观察偏心区、2#电极热区、炉门两侧及下部等部位的镁碳砖侵蚀情况,及时通知外包施工队用喷补料进行喷补;炉前在每次出钢后要及时清理炉门并用补炉料补筑好炉门。
3.3、清理及填充EBT。
●清理掉EBT的残钢、残渣,确认EBT畅通。
●关闭EBT,对EBT进行填充,出钢口填充料应适当高出袖砖,外形呈馒头形。
●填好EBT后,摇炉到水平位置,整理好炉门准备新一炉炼钢操作。
●接好引流用氧气管。
●观察炉况。
3.4、接、换及调整电极。
二、配料、装料1、废钢的加入●水冷小车退出炉壳外,停在“退出停止”位置。
●新炉第一炉、出净钢水修补炉第一炉为新铺捣打料的炉坡、炉底,装料前应在炉坡、炉底铺一层薄铁板并加1~2吨石灰铺底。
料罐用废钢铁料以剪切料为主,料罐停放在电炉平台下。
2、废钢量的确定●新炉、修补炉:总装入量60吨左右,全部使用废钢,不使用生铁及中重型废钢铁料,以剪切废钢为主;出钢量45吨左右。
简述反应釜的主要工艺流程

简述反应釜的主要工艺流程
反应釜是一种用于进行化学反应的设备,广泛应用于化工、医药、食品等工业领域。
其主要工艺流程一般包括以下几个步骤:
1. 加料:将所需原料按照一定比例加入反应釜中。
加料方式可以是连续加料或一次性加料,取决于具体的反应要求。
2. 搅拌:在反应釜中进行搅拌。
搅拌的目的是使原料充分混合,加快反应速度,并保证反应均匀进行。
搅拌方式可以是机械搅拌、气体搅拌或液体循环搅拌等。
3. 加热或冷却:根据反应的要求,对反应釜进行加热或冷却。
加热可以采用蒸汽、电加热或火焰加热等方式,冷却可以通过冷却水或冷却剂进行。
4. 反应:在适当的温度、压力、反应时间等条件下进行化学反应。
反应的进程和速率取决于反应物的性质、反应条件和催化剂等。
5. 产品分离:反应完成后,对产生的产物进行分离和提取。
常用的分离方法包括蒸馏、结晶、过滤、离心、萃取等。
6. 清洗:对反应釜进行清洗,去除残留物和污垢,为下一次使用做准备。
需要注意的是,不同的反应釜在工艺流程上可能会有所差异,具体的步骤和顺序
需要根据实际情况进行调整。
此外,反应釜的操作需要严格控制温度、压力、搅拌速度等参数,以确保反应的安全性和有效性。
冷再生施工方案

一、工程概况补强段底基层采用水泥稳定碎石现场冷再生,翻修路段底基层采用旧路面铣刨料厂拌冷再生.补强段现场冷再生3。
94万平方米,翻修路段厂拌冷再生 5.13万平方米.二、施工方案路面结构层水稳冷再生的工作原理,就是利用原有的水泥稳定碎石基层,按设计要求,加入碎石、水泥、水等外加材料,利用冷再生设备,就地(或运输到拌合厂)完成对旧路的铣刨、破碎、添加料、拌合、摊铺等工序,随后进行整平与碾压,最后修建出一种特殊级配的道路基层。
(一)人员准备配备施工总负责1人、技术负责1人、现场施工技术员2人、质检人员2人、后勤保障及其他人员2人、施工生产人员20人。
(二)机械准备50T装载机2台,平地机1台,振动压路机1台,光轮压路机1台,洒水车1台,自卸车辆8辆。
(三)水稳冷再生施工方法1.现场冷再生水泥稳定基层(1)工艺流程:封闭交通→施工放样→准备原道路→准备新加料→冷再生机组就位→摆放和撒布水泥→冷再生机组铣刨与拌和→整平碾压→接缝和调头处处理→养生。
整个施工及养护过程中,应对再生路段封闭交通,各路口设置警牌.(2)施工放样在道路的两侧放置一系列的标桩作为基线,用来恢复道路中心线.标桩的间距,曲线距离为20m.直线距离为40m.(3)原道路清扫挖除后的基层顶面进行清扫,如存在泥土时,用洒水车冲刷和人工用钢丝刷清理,等路面干燥后用鼓风机清除表面浮灰,保证表面清洁无污染。
(4)铺石料用自卸车将碎石倒入施工现场工作面上,再用人工配合装载机将碎石均匀的摊铺在施工段落上,如有局部厚度不均时,用人工整平,保证碎石摊铺厚度在5c m左右。
(5)冷再生机组就位冷再生机组开到指定施工位置后,将所有与稳定剂添加量有关数据输入计算机,确定一些准备就绪后停机待命,对其他需用机械设备进行再一次全面的检查。
检查再生路段内的导向标志,确保导向标志明确.(6)摆放和撒布水泥根据现场计算得出每平方米水泥的添加量为.用人工将水泥均匀摊开,保证每袋水泥的撒布面积均等。
水泥磨知识简介及工艺操作要点

水泥磨学问简介及工艺操作要点一、设备规格、参数:1、规格:Φ3.8×13m双仓圈流磨入磨物料粒度:〈25mm出磨成品细度:3500cm2 驱动方式:中心传动用途:粉磨水泥生产力量:75t/h 磨机转速:16.3r/min 研磨体装载量:173t 磨机支承方式:两主轴承支承方式主轴承润滑方式:带高压浮升的稀油集中润滑。
2、主减速机型号:MFY250A 功率:2500 KW输入转速:740 r/min 输出转速:16.3 r/min3、主电机型号:YRKK800-8 功率:2500 KW 转速:745 r/min电压:6000 KV二、工作原理当磨机回转时,研磨体由于惯性离心力的作用,贴附在磨机筒体内壁的衬板上,与磨机一起回转并被带到肯定的高度,由于其本身的重力作用。
像抛射体一样落下,将筒体内的物料击碎。
此外,研磨体还有滑动和滚动现象,主要对物料起研磨作用;物料由前仓连续参加,随筒体一道回转运动,形成物料向后挤压。
加上进料端与出料端之间物料本身的料面高度差,以及磨内强制通风,因此磨机筒体虽然是水平安装,而物料由进料端缓慢地向出料端移动,完成粉磨作业。
三.开机操作1、开机的预备工作:中控操作员在接到上级指令后,马上通知总降人员,了解电力供给状况,是否允许开机;检查DCS 系统是否投入运行,系统设备是否备妥,并将主排挡板调至“零位”,通知现场人员对现场和设备进展确认,并符合开磨条件;通知化验室下达质量通知单,并通知现场人员做好入库预备工作;通知调度室、电气值班室。
2、开机操作经上述预备,在确认全部设备、计算机、DCS 系统都具备开机条件时,方可开机;开机程序:首先启动磨机系统各润滑油泵,待各油泵运行正常后,通知现场人员进展脱慢转;在 1 分钟内启动水泥输送袋收尘机组,待袋收尘机组启动后,马上启动水泥成品输送机组,在 2 分钟内完成,待水泥成品输送系统启动完毕后,马上启动水泥磨分别及输送机组,要求在 5 分钟内启动完毕;待付机系统启动完毕后,确认高压、慢转信号正常后,马上启动磨机 3915〔待一台磨机启动运转后,方可启动另一台磨机,一般间隔 5 分钟〕,在3915 启动 2 分钟后〔如磨机属跳停,5 分钟后开头喂料〕,启动喂料机组,开头喂料时,熟料的喂料量设定为 50t/h,在 30 分钟内将喂料量加至正常值,在加料过程中要防止一次性加料过多、过快而导致磨机工况不稳,以及依据运行参数的变化准时缓慢地调整 3936 风机挡板的开度和选粉机的转速,确保磨机系统的稳定运行。
50t循环流化床锅炉岗位操作法

设备动力部动力车间锅炉岗位操作法试用本编制:审核:批准:2009年2月27日2*50t/h锅炉操作法一、岗位任务与管理范围(一)、岗位任务1、监控锅炉及辅助设备装置安全稳定运行,为生产单位输送合格蒸汽。
2、履行设备巡检、维护保养和安全文明生产职责,努力降低运行成本消耗。
(二)、管理范围2×50吨锅炉所辖操作人员、原材料、设备装置及生产、生活主供汽管网。
二、工艺流程与操作指标(一)、工艺流程1、水汽流程:2、给料流程:(二)、操作指标额定蒸汽压力:3.82±0.05MPa 给水温度:95~105℃过热蒸汽温度:450±5℃炉膛下沸温度:900±40℃炉膛出口温度:≤980℃返料器温度:≤950℃返料风室压力:9~11kPa 炉膛出口烟气压力:-30~-50Pa 水冷风室风压:6~8kPa除氧压力:≤0.02 MPa锅炉水位:±75mm高压给水泵电流:≤30A引风机电流:≤50A 一次风机电流:≤60A油枪喷射压力:≤2 MPa三、开停机方法(一)、开机方法1、开机前的检查1.1、所有检修工作结束,人员已撤离。
1.2、检查引风、一次风、二次风机状况:1.2.1、引风机出口闸门开度≤5%;1.2.2、靠背轮连接良好,盘动灵活;1.2.3、地脚螺栓紧固,构件齐全;1.2.4、轴承箱油位正常,油质洁净;1.2.5、风门执行机构连接正常,开度与显示相符并处于关闭;1.2.6、风道内无杂物,人孔门均关闭;1.2.7、冷却水管道畅通,阀门调整灵活;1.3、返料器入口风门开启,处于调节状态。
1.4、播、送煤风及密封风门关闭,待给煤时开启。
1.5、火焰燃烧监视器冷却风门开启。
1.6、放渣管插板及放灰门完好关闭。
1.7、燃烧室四周清洁,观火孔玻璃完好、清晰、手柄灵活。
1.8、燃烧室检查:1.8.1、各风口、进料口外形正常,孔、口内杂物及灰渣已清除;1.8.2、四周内衬完好,壁面挂焦、松动浇筑料及杂物已清除;1.8.3、落煤管内无积煤,四壁光滑;1.8.4、布风板平整,风帽完好、孔眼畅通;1.8.5、热电隅前端及探头完好,未弯曲或磨损。
铝合金熔炼工艺流程和操作工艺
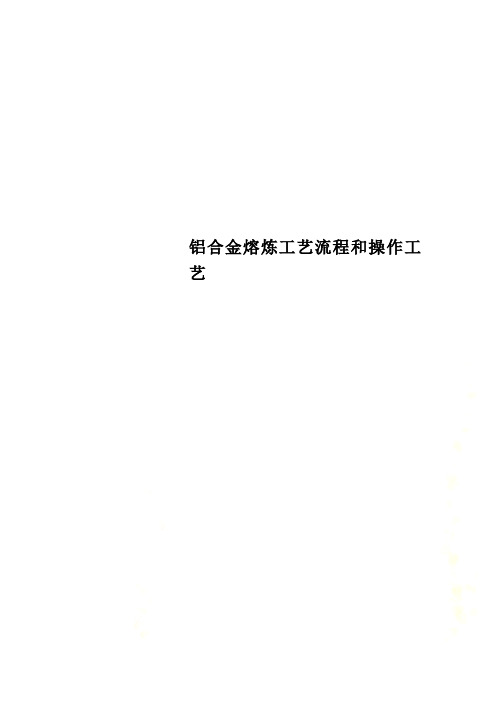
铝合金熔炼工艺流程和操作工艺铝合金熔炼工艺流程和操作工艺(一)装料熔炼时,装入炉料的顺序和方法不仅关系到熔炼的时间、金属的烧损、热能消耗,还会影响到金属熔体的质量和炉子的使用寿命。
装料的原则有:1、装炉料顺序应合理。
正确的装料要根据所加入炉料性质与状态而定,而且还应考虑到最快的熔化速度,最少的烧损以及准确的化学成分控制。
装料时,先装小块或薄片废料,铝锭和大块料装在中间,最后装中间合金。
熔点易氧化的中间合金装在中下层。
所装入的炉料应当在熔池中均匀分布,防止偏重。
小块或薄板料装在熔池下层,这样可减少烧损,同时还可以保护炉体免受大块料的直接冲击而损坏。
中间合金有的熔点高,如AL-NI和AL-MN合金的熔点为750-800℃,装在上层,由于炉内上部温度高容易熔化,也有充分的时间扩散;使中间合金分布均匀,则有利于熔体的成分控制。
炉料装平,各处熔化速度相差不多这样可以防止偏重时造成的局部金属过热。
炉料应进量一次入炉,二次或多次加料会增加非金属夹杂物及含气量。
2、对于质量要求高的产品(包括锻件、模锻件、空心大梁和大梁型材等)的炉料除上述的装料要求外,在装料前必须向熔池内撒20-30kg粉状熔剂,在装炉过程中对炉料要分层撒粉状熔剂,这样可提高炉体的纯洁度,也可以减少损耗。
3、电炉装料时,应注意炉料最高点距电阻丝的距离不得少于100mm,否则容易引起短路。
熔化炉料装完后即可升温。
熔化是从固态转变为液态的过程。
这一过程的好坏,对产品质量有决定性的影响。
A、覆盖熔化过程中随着炉料温度的升高,特别是当炉料开始熔化后,金属外层表面所覆盖的氧化膜很容易破裂,将逐渐失去保护作用。
气体在这时候很容易侵入,造成内部金属的进一步氧化。
并且已熔化的液体或液流要向炉底流动,当液滴或液流进入底部汇集起来时,其表面的氧化膜就会混入熔体中。
所以为了防止金属进一步氧化和减少进入熔体的氧化膜,在炉料软化下塌时,应适当向金属表面撒上一层粉状熔剂覆盖,其用量见表。
吨精炼车间工艺操作手册
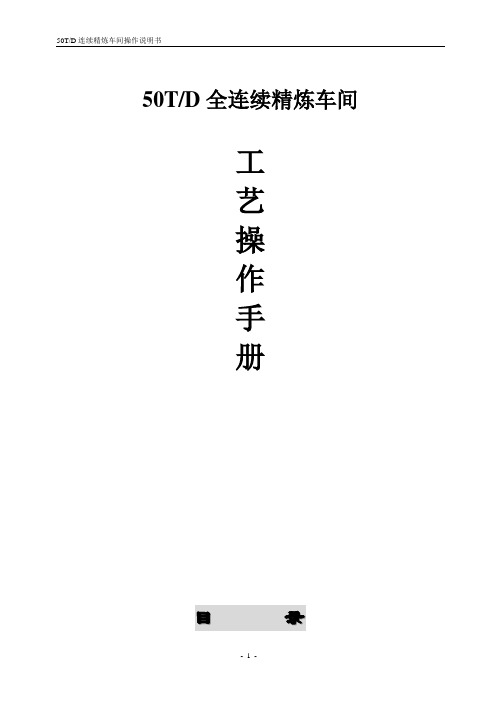
50T/D全连续精炼车间工艺操作手册目录工艺过程 (3)主要设备简介 (6)操作说明 (9)开车与停车 (15)事故处理与安全操作 (17)取样与化验 (22)1.工艺过程1.1.工艺流程:定量←磷酸碱或水↓↓毛油→毛油称→计量→加热→碱炼锅→酸油反应→碱炼锅→碱或水水↓↓→加热→离心分离→碱炼锅→加热→离心分离→碱炼锅→加热→↓皂脚真空↑离心分离→碱炼、脱胶油→加热→干燥器→冷却→三、四级油→换热调温↓废水真空真空↑↑→白土混合→脱色器→脱色过滤→脱色油→真空析气→油换热→加热→脱臭↑定量←白土→油换热→冷却→过滤→成品油↑定量←加柠檬酸1.2.概述:油脂精炼的目的是去除毛油中所含的固体杂质、游离脂肪酸、胶质、磷脂、蜡、色素、异味及有害物质等,以提高油脂的使用价值,从油脂精炼的副产品中也可以提取一些有用的成份,用于制药、化工、食品、纺织等方面。
本车间可用于精炼毛棉籽油、毛豆油、毛菜籽油、毛葵花籽油等植物油,分四个工序:(1)脱胶;(2)脱酸;(3)脱色;(4)脱臭。
一般情况下,按上述工序依此加工可得到棉籽二级油、葵花籽二级油、大豆、菜籽一级油,并且也可以生产符合国标的三、四级大豆油、棉籽油、菜籽油、葵花籽油。
如果生产不同品质的油,可根据实际情况选择不同的工序组合。
1.3.生产工序分述:1.3.1.脱胶:脱除毛油中胶体物质的工艺过程称为脱胶,毛油中的胶体物质,尤其是磷脂以及棉籽独有的棉酚成分,在碱炼脱酸时,能使油脂和碱液发生乳化现象,增加操作困难和炼耗,并影响到后面的脱色、脱臭工序。
另一方面,成品油中胶体物质含量过高会影响感观质量,使油色加深,透明度下降且影响工业与食品的使用效果。
油脂中的胶体主要成分是磷脂、蛋白质、粘液物等,磷脂(以卵磷脂为代表)属于“双亲媒性分子”,在其分子结构中,既有疏水性(亲油性)的非极性基团,又有亲水性的极性基团,后者具有较强的吸水能力,随着吸收水份的增加,磷脂分子体积膨胀,质点相互吸附形成胶团,比重增大。
电炉兑铁水
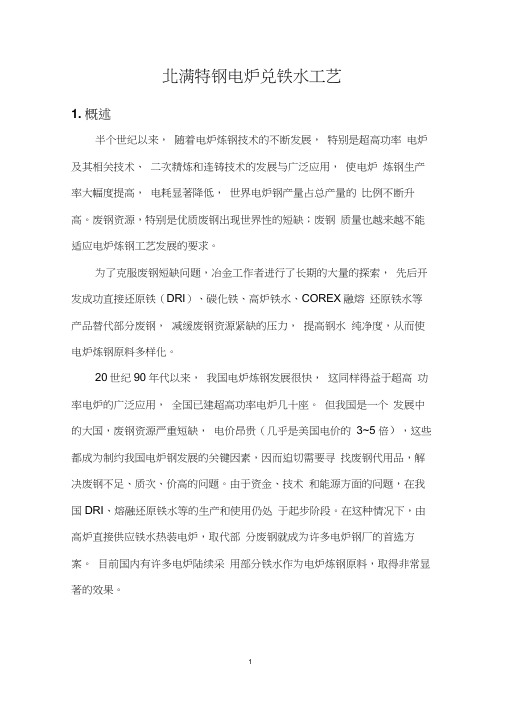
北满特钢电炉兑铁水工艺1. 概述半个世纪以来,随着电炉炼钢技术的不断发展,特别是超高功率电炉及其相关技术、二次精炼和连铸技术的发展与广泛应用,使电炉炼钢生产率大幅度提高,电耗显著降低,世界电炉钢产量占总产量的比例不断升高。
废钢资源,特别是优质废钢出现世界性的短缺;废钢质量也越来越不能适应电炉炼钢工艺发展的要求。
为了克服废钢短缺问题,冶金工作者进行了长期的大量的探索,先后开发成功直接还原铁(DRI)、碳化铁、高炉铁水、COREX融熔还原铁水等产品替代部分废钢,减缓废钢资源紧缺的压力,提高钢水纯净度,从而使电炉炼钢原料多样化。
20世纪90年代以来,我国电炉炼钢发展很快,这同样得益于超高功率电炉的广泛应用,全国已建超高功率电炉几十座。
但我国是一个发展中的大国,废钢资源严重短缺,电价昂贵(几乎是美国电价的3~5 倍),这些都成为制约我国电炉钢发展的关键因素,因而迫切需要寻找废钢代用品,解决废钢不足、质次、价高的问题。
由于资金、技术和能源方面的问题,在我国DRI、熔融还原铁水等的生产和使用仍处于起步阶段。
在这种情况下,由高炉直接供应铁水热装电炉,取代部分废钢就成为许多电炉钢厂的首选方案。
目前国内有许多电炉陆续采用部分铁水作为电炉炼钢原料,取得非常显著的效果。
2. 电炉热装铁水的效果2.1降低电炉炼钢成本在电炉冶炼碳素钢成本构成中钢铁料、电能、电极等分别居于前三位,约占炼钢成本的75%。
由此可见,这三项是影响成本的关键因素。
降低电炉炼钢成本首先应考虑降低这三项消耗。
我国废钢严重短缺,电费昂贵,对炼钢成本影响很大。
我国众多电炉钢厂之所以纷纷采用铁水热装工艺,最根本的原因也是从生产成本上考虑的。
自20世纪后期以来,我国废钢资源一直十分紧张,废钢价格居高不下,以致废钢价格普遍高于铁水价格250〜300元/t。
在此情况下,电炉钢生产成本较高,在市场竞争中非常被动,以部分铁水代替废钢,既缓解了废钢的紧张情况,又降低了生产成本。
电石生产操作规程-加料岗位操作规程

电石生产操作规程-加料岗位操作规程一、作业人员1.加料岗位操作必须由持有操作证的专业人员进行。
2.作业人员应具备电石生产操作规程相关知识,并接受过相应的培训。
3.作业人员应严格遵守操作规程和工艺流程,保证加料岗位的安全和生产质量。
二、安全措施1.作业前应检查设备和工具的完好性,确保无任何故障。
2.作业人员应佩戴个人防护装备,包括安全帽、防护服、防护眼镜、安全鞋等。
3.作业人员应定期接受体检,确保身体状况适宜从事相关工作。
4.作业现场应保持整洁和通风良好,防止发生火灾或有毒气体积聚。
5.在加料过程中,应随时注意设备运行状态,确保设备正常运转。
三、操作步骤1.根据工艺流程,将所需的原料准备好,确保原料的质量和数量无误。
2.根据实际情况选择合适的加料工具,并在操作前进行消毒和清洁。
3.将待加料的原料放入加料工具中,并注意控制加料量,避免超负荷运行。
4.将加料工具放置在设备的指定位置,确保安全可靠,并防止原料洒溅。
5.根据工艺流程要求,进行加料操作,确保加料的过程平稳和连续。
6.加料结束后,将加料工具进行清洁,以备下次使用。
四、事故处理1.如发生意外事件或事故,操作人员应立即停止操作,确保自身安全。
2.及时向上级汇报事故情况,并按照公司规定进行处理和调查。
3.全力保护生产设备和环境的安全,防止事故扩大和二次发生。
五、注意事项1.操作人员应根据实际情况进行加料,避免过量或不足的情况发生。
2.操作人员应随时注意设备运行状态,及时发现和解决设备故障。
3.加料过程中如发现原料有异常情况,应及时停止操作,并向上级报告。
4.加料工具的使用和保养要符合公司的相关规定,确保工具的安全和有效性。
5.操作人员应定期进行职业技能培训,提高操作水平和安全意识。
六、责任分工1.加料岗位负责人负责岗位的安排和工作的组织。
2.操作人员负责具体的加料操作,并按要求完成工作任务。
3.公司相关部门负责监督和检查加料岗位的操作情况,确保工作的安全和质量。
底吹炉设备操作规程

脉冲袋式除尘操作规程开机前检查各紧固件是否牢固,各转动部位周围是否有障碍物与固定部位无碰状及摩擦现象,风机的润滑油、风门是否正常,检查电源电压是否稳定,各仪表、仪表是否灵敏、齐全、准确,检查所烟气管路的门是否关闭,设备管道和接头是否泄露;检查每个过滤室的进出口风调节阀是否打开,确定无事故隐患后方可开机。
开机启动风机时应关闭风门,按下风机控制柜上启动按钮,待风机运行平稳后方可调节风门到适当位置。
风机运行正常;将除尘器启动,控制采用“手动”和“自动”;两种方式,可相互转换,自动分定阻和定时两种。
如果除尘器系统手动控制,将螺旋输送机星形排灰阀,然后依次关闭,1#汽缸阀,开启1#脉冲阀直至0,4组汽缸阀、脉冲阀运做一遍,将星形排灰阀、螺旋输送机停机然后再根据适当情况,安排时间重新开启。
运行中定期检查轴承润滑点温度是否合乎要求(油温≦65℃,轴承表温≦70℃),检查风机及脉冲阀是否有振动或异响,电流是否正常,各转动部位和固定部位是否有摩擦、碰撞现象,各部件是否松动,检查入口浓度﹤10g/nm3,出口浓度﹤50mg/nm3,是否正常。
风机运行中禁止加油、维修。
发现隐患立即处理或上报,严重时可立即停机。
停机正常停风机要先把风门关闭,禁止满负荷突然停机。
用PLC关闭除尘器,在滤袋清灰过程中或灰斗中还有积灰时,不能关闭输灰系统。
待风机停机后,反吹输灰系统运行3—5个循环再关闭。
将各控制按钮打至“0”位。
定期排放过滤器内的水及油污,检查注油器内油量(不得小于1/2)。
班中认真做好原始记录,校好设备现场卫生。
底吹炉操作规程开炉前的准备工作对炉体及各设备进行最后检查,确认试车正常,具备开炉条件。
与炉体相关的管网及附属设施运行正常,水套冷却水压力为0.2-0.3M Pa,压缩空气(或氮气)压力0.5-0.6MPa ,油压0.3MPa,阀门灵活,管道畅通,各处无泄漏。
氮氧管道吹扫干净,无杂物,各种手动气动阀门调节灵活、密封良好,并处于所需要的开、关状态。
装载机加料操作规程(3篇)
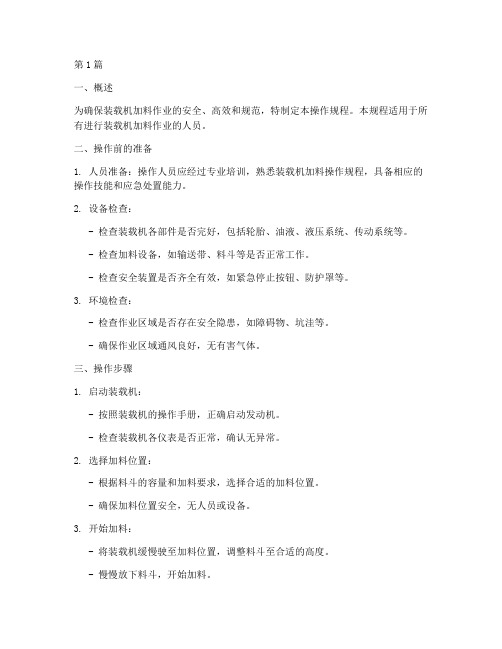
第1篇一、概述为确保装载机加料作业的安全、高效和规范,特制定本操作规程。
本规程适用于所有进行装载机加料作业的人员。
二、操作前的准备1. 人员准备:操作人员应经过专业培训,熟悉装载机加料操作规程,具备相应的操作技能和应急处置能力。
2. 设备检查:- 检查装载机各部件是否完好,包括轮胎、油液、液压系统、传动系统等。
- 检查加料设备,如输送带、料斗等是否正常工作。
- 检查安全装置是否齐全有效,如紧急停止按钮、防护罩等。
3. 环境检查:- 检查作业区域是否存在安全隐患,如障碍物、坑洼等。
- 确保作业区域通风良好,无有害气体。
三、操作步骤1. 启动装载机:- 按照装载机的操作手册,正确启动发动机。
- 检查装载机各仪表是否正常,确认无异常。
2. 选择加料位置:- 根据料斗的容量和加料要求,选择合适的加料位置。
- 确保加料位置安全,无人员或设备。
3. 开始加料:- 将装载机缓慢驶至加料位置,调整料斗至合适的高度。
- 慢慢放下料斗,开始加料。
- 加料过程中,注意观察料斗内物料情况,避免物料溢出。
4. 控制加料速度:- 根据加料要求,调整装载机的加料速度。
- 避免加料过快,造成物料堆积或输送带堵塞。
5. 停止加料:- 当达到加料要求或出现异常情况时,停止加料。
- 将料斗升起,避免物料滞留在料斗内。
6. 安全检查:- 加料完成后,检查作业区域是否有遗漏的物料。
- 确认装载机各部件无异常。
四、操作后的注意事项1. 关闭设备:- 关闭装载机的发动机。
- 关闭加料设备,如输送带、料斗等。
2. 清洁保养:- 清理装载机和加料设备上的物料。
- 检查设备磨损情况,进行必要的保养。
3. 记录:- 记录加料作业的相关数据,如加料量、时间等。
五、应急处置1. 发生故障:- 立即停止加料作业。
- 按照操作手册进行故障排除。
2. 紧急情况:- 按照应急预案进行处置。
- 确保人员安全。
本规程自发布之日起实施,如有未尽事宜,可根据实际情况进行修订。
- 1、下载文档前请自行甄别文档内容的完整性,平台不提供额外的编辑、内容补充、找答案等附加服务。
- 2、"仅部分预览"的文档,不可在线预览部分如存在完整性等问题,可反馈申请退款(可完整预览的文档不适用该条件!)。
- 3、如文档侵犯您的权益,请联系客服反馈,我们会尽快为您处理(人工客服工作时间:9:00-18:30)。
电弧炉连续加料工艺操作规程、生产准备:1、原辅材料:1.1、废钢:•废钢的分类、技术要求、检验方法、验收规则、运输和质量说明书等满足GB/T422 3废钢铁之规定;•废钢的块度满足未分解钢铁料尺寸<800mm,压块v600X400X400mm 单重<300kg 的要求;•废钢的化学成分满足特殊钢种对微量有害元素的要求。
•石灰、白云石、萤石、铁合金等满足国标要求。
•所有物资定置堆放到位。
高位料仓储料充足。
2、设备状况2.1、确认电炉机械、液压设备正常;水、气等介质供应正常;2.2、电器、计算机等自动化系统检验确认正常。
•电炉设备冷却水压力 > 0.3MP压缩空气压力> 0.4MPa;•电炉变压器冷却水水压正常(0.01〜0.02 MPa),油水冷却器投入运行;•除尘风机投入运行,除尘器压差正常。
3、炉前准备3.1、确认电极水冷喷淋环工作正常,发现积灰或堵塞及时处理。
3.2、每炉出钢后、通电前,仔细观察上部炉壳及炉衬情况:注意上部炉壳是否有漏水现象,必须认真察看每支炉壁碳氧枪的工作状况,发现堵塞或漏水及时处理;对中后期的炉衬,要特别注意观察偏心区、2#电极热区、炉门两侧及下部等部位的镁碳砖侵蚀情况,及时通知外包施工队用喷补料进行喷补;炉前在每次出钢后要及时青理炉门并用补炉料补筑好炉门。
3.3、清理及填充EBT。
•青理掉EBT的残钢、残渣,确认EBT畅通。
•关闭EBT对EBT进行填充,出钢口填充料应适当高出袖砖,外形呈馒头形。
•填好EBT后,摇炉到水平位置,整理好炉门准备新一炉炼钢操作。
•接好引流用氧气管。
•观察炉况。
3.4、接、换及调整电极。
二、配料、装料1、废钢的加入•水冷小车退出炉壳外,停在“退出停止”位置。
•新炉第一炉、出净钢水修补炉第一炉为新铺捣打料的炉坡、炉底,装料前应在炉坡、炉底铺一层薄铁板并加1~2 吨石灰铺底。
料罐用废钢铁料以剪切料为主,料罐停放在电炉平台下。
2、废钢量的确定•新炉、修补炉:总装入量60 吨左右,全部使用废钢,不使用生铁及中重型废钢铁料,以剪切废钢为主;出钢量45 吨左右。
新炉装料先用料罐分批加入废钢,至装入量达到40吨后启动连续加料,从连续加料加入废钢约18 吨;修补炉用料罐加入18 吨废钢以后方可启动连续加料。
•冷态空炉:总装入量60 吨左右,钢铁料配比:废钢80%左右、生铁20%左右(在除尘能力允许的情况下:如没有生铁或机生铁,加入碳球替代或无烟煤,在所有条件不具备情况下控氧操作),出钢量 钢,溶清后启动连续加料。
料槽中加料高度控制 500mm 左右,最高应小于 700mm 。
•正常连续式操作:总装入量 60±5吨,钢铁料配比:废钢 70~80%、生铁20~30%(在除尘能力允许的情况下如没有生铁或机生铁,加入碳球替代或无烟煤,在所有条件不具备情况下控氧操作)。
出钢量 45~50吨。
•炉内留钢量在正常生产时应保持 15~20吨,根据电炉炉龄和实际生产情况 可作调整。
留钢量少于 10吨时,必须先用料罐或连续加料加入废钢使炉内装入 量达到 20吨以上才能通电冶炼。
在电炉回到水平位置后,连接小车到达 “送料 开始 ”位,启动连接加料小车及链板输料开始直接往炉内加钢铁料。
3、生铁的加入•生铁加入的时间:生铁在炉内装入量 30吨以后时加入,在装入量达到 50 吨前加完。
•生铁的加入量:以机生铁为例的加入量一般为 8~12吨/炉,可根据冶炼钢种和废钢机械生铁含量的不同及对有害元素的特殊要求调整生铁的加入量。
•生铁的加入方式:主要由行车加入链板机料槽,由链板机输送给头部加料小车,要求生铁在料槽内分布要均匀、撒开。
4、渣料的加入 :•石灰、白云石的加入量:正常情况石灰的总加入量为 1200~1600Kg 炉,白云石的加入量300~450Kg 炉,在白云石含钙、镁达标,二氧化硅含量 <0.66%。
根据钢水中P 、S 含量进行调整。
新炉、 右,不使用白云石。
在进料罐前先加入入约500~1000Kg 石灰。
•正常连续式操作:石灰的加入量 300Kg~450kg 通过石灰加料系统加入连续加料料槽。
分2~3次加入,每次 15~200Kg 分别于通电开始、炉内20吨、炉内30吨、炉内45吨、炉内50吨 等时段加入,炉内熔清后如熔清样磷含量高,可由高位料仓补加石灰。
45 吨。
先加入 15-20吨废 中修炉第一炉:石灰加入量 2000Kg 左 1000~1500Kg 石灰;在连续加料时再加 1200Kg~1600kg 白云石的加入量三、冶炼操作1、供电1.1 电炉变压器电压分级功率1.2 新炉、修补炉第一炉装第一批料,以5~7级电压手动供电,熔清后停15~20分钟后加入第二批料,再以5~7级电压手动供电,熔清后停15〜20分钟左右后加入第三批料,以5~7级电压手动供电;基本熔清停30分钟左右后启动连续加料,以3~5级电压手动供电。
如因料罐小,进料次数多,熔清后的停炉时间可以适当减少。
新炉第一炉的冶炼时间大于210分钟;修补炉第一炉的冶炼时间大于150分钟。
1.3 冷炉第一炉装第一批料,以5~7级电压供电,熔清后加入第二批料,以5~7级电压供电,基本熔清后启动连续加料以3~5 级电压供电。
1.4 正常冶炼当电炉回到水平位置后,启动康斯迪加料,根据冶炼进度、炉内温度和泡沫渣情况,控制合适的加料速度及供电曲线,一般以2~4 级电压供电。
冶炼中造好泡沫渣,做到埋弧操作,控制供氧强度,避免大沸腾现象发生。
注意:电炉在生产过程中尽量避免有载调压!调压时提升电极,至电流归零,再调电压。
1.5 供电常见故障:•跳电:在冶炼过程中,遇到电流波动过大(如塌料等),会产生跳电现象,跳电炉高压开关只要在主控室按“复位”按钮解除即可继续合闸生产;如跳33KV 或220KV,则必须通知电工处理。
•允许合闸指示灯不亮:检查供电条件是否满足。
2、碳氧枪操作碳粉喷入量设定范围为15~30kg/mi n,以确保炉内泡沫渣良好为宜。
氧气流量设定:小流量一一800~1200Nm3/h大流量——1500~2200Nm3/h。
2.1 新炉第一炉在第一、第二、第三批料熔化过程中不进行吹氧,第三批料熔化后,用碳 氧枪小流量吹氧,同时视情况喷少量碳粉造泡沫渣。
启动康斯迪后,增大碳粉 量,氧气流量控制在小流量,碳粉喷吹流量控制在 20Kg/min 左右。
2.2进料阶段先启动水冷碳氧枪往炉内小流量吹氧喷碳形成泡沫渣后,再通 电进行正常的冶炼操作。
根据炉内钢水量确定氧气流量;装入量未达 20吨之前 用小流量约 800Nm3/h 供氧, 20 吨后用大流量供氧。
废钢未进到炉内不得使用 大流量氧气供氧;熔池温度低时碳氧枪以造泡沫渣为主,泡沫渣造好后碳氧枪 以切割废钢为主。
2.3升温阶段当钢水〔C 〕含量较高时,用氧枪大流量吹氧升温。
当钢水 〔C 〕含量较低时,可向炉内喷碳升温。
控制好炉内渣量,适量适时流渣,造好 泡沫渣,埋弧升温。
注意:根据配碳量、废钢情况和实时炉况合理控制氧气使 用流量及枪位,防止钢水过氧化及大沸腾。
3、溶池温度及成分的控制3.1 成分控制:3.1.1 装入量接近和达到目标值,便进入升温阶段,当熔池温度达到 左右时取第一个样作全分析,(如果炉内进有冷钢则要等冷钢基本熔化再取 样);根据分析结果决定是否取第二个样。
如果第一个样成分符合工艺要求, 至熔池温度达到1580 C 左右时取终点样;如第一个样〔C 〕高,吹氧脱〔 再取第二个样分析;如果〔P 〕高,流渣后补加石灰和适量萤石造渣脱〔 再取第二个样分析,成分合格后至熔池温度达到 1580 C 左右时取终点样。
微量有害元素的控制在低合金钢的生产中为了有害元素的控制是一项基本的要 求,一般包括: Cu 、Ni 、As 、Sb 、Sn 、Pb 、Bi 等,大多来源于废钢,为了控制 微量有害元素的含量,尽量地降低损失,要求做到:•在电炉熔清时发现微量有害元素超标则立即与储运调度联系,通知情况, 并请储运调换废钢。
•对于电炉炉内已经发生的微量有害元素超标的情况,电炉出钢时必须尽量 多倒出炉内钢水,请示领导处理。
•当班发生的微量有害元素超标的情况必须在值班记录上清楚反映,避免事 故的重复发生。
3.2 温度控制:1550C C 〕后 P 〕后 3.1.23.2.1 进料阶段由于变压器输出功率和化学能相对稳定,溶池温度控制主要由连续加料速度决定,为了保证溶池温度在碳沸腾温度范围,耗电控制在280~320Kwh/t为宜,此时炉内的钢水温度在1530~1580C范围内。
炉内钢水量达到目标值90~95%时,减慢连续加料速度,提升溶池温度,装入量达到97%停止加料,并进行取样、测温操作。
小车退出。
3.2.2 出钢阶段出钢温度:•普碳钢、低合金钢:1570 C;•合金加入量在1.2吨以上的钢种温度提高20C,如果Cr铁、Mo铁加入量大,再提高20C;•冷炉、全新钢包、备用钢包等视情况温度各提高30 士10。
3、出钢4.1 出钢条件•温度、化学成分满足工艺要求•钢包到达出钢位,接好氩气管,准备好氩气。
•准备好引流用氧气管。
•钢包称重正常且去皮归零。
4.2 出钢操作:⑴、头部小车退出到“OUT”,退出炉门碳氧枪;停电并将电极操作手柄打到“出钢”位置,摇炉控制权转移到炉后出钢操作台。
以下在炉后出钢操作台上进行:⑵、电炉倾动到+2〜5C,打开EBT如填料不能自动流出,可用氧气引流。
⑶、当包内钢水5~10t时,随钢流将配好的精练渣、铁合金加入钢包内。
铁合金的加入量以达到各钢种的合金成分下限为准,具体加入量可参考各钢种的《工艺操作要点》;精练渣加入量为10Kg/t钢。
⑷、出钢量依据钢包车上的称量系统控制目标50-55t钢水,如称重系统故障,可依据倾炉角度从5° 9° 15°控制,各位置均有设定的出钢量,同时根据钢包内钢水液面以及钢包的包龄估计钢包中的钢水量。
⑸、出钢量达到目标值时(目标值要随着钢包的状况随时调整),快速摇回电炉至-7°,同时启动钢包车退出,以防止氧化渣倒入钢包。
4.3预脱氧制度⑴、在冶炼Q215、Q235等普碳钢时在出钢时只加入0.5kg/吨钢脱氧剂、碳化硅进行预脱氧;⑵、在冶炼优钢、特钢时在电炉出钢时加入0.5〜1.0kg/吨钢脱氧剂进行预脱氧;4、炉衬修补、换炉最后一炉钢冶炼操作:5.1冶炼前期与正常操作一样,减少生铁加入量,炉内装入量控制在45t左右。
为便于检查连续加料设备,槽内的废钢料要走清。
5.2熔清后尽量流掉炉渣,使炉内渣量降到最低程度。
5.3倒钢时倾动角度达到20°。
5.4出钢到40t,快速回摇电炉。
5.5炉中剩余的钢渣倒在备用钢包里,倒去上层氧化渣,剩余钢水倒入精炼炉钢包中。