三聚氰胺工艺技术方案解读
三聚氰胺生产工艺完整文档
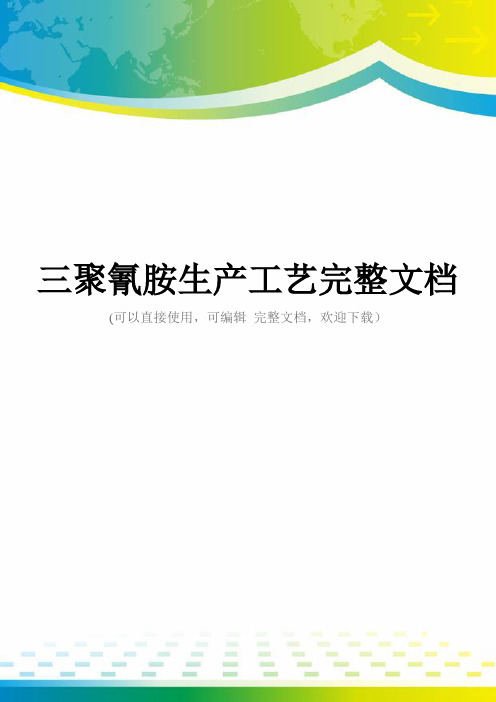
三聚氰胺生产工艺完整文档(可以直接使用,可编辑完整文档,欢迎下载)三聚氰胺生产工艺以尿素为原料生产三聚氰胺分为高压法、中压法、低压法和常压法四种工艺。
(1)低压尿素分解法(见图1)肥料级尿素在贮罐中熔融后,用几个喷嘴喷入反应器中,以流态化的氧化铝为催化剂,将预热至400℃的循环氨气通入反应器保持流态化,反应压力为常压或稍高于大气压。
反应吸热,反应器内装有加热盘管,以熔融盐作为加热介质,维持反应温度380℃左右。
喷入的尿素自行蒸发,反应生成三聚氰胺、二氧化碳和氨,转化率为95%。
反应气体从反应器顶部出来,先进入气体冷却器,冷却后的温度在三聚氰胺的露点以上。
在此温度下,密勒胺和密白胺等高沸点副产物结晶析出,和催化剂粉末一起经过滤器除去。
过滤后的气体进升华器,以冷却至140℃的循环气使升华器的温度维持在170℃~200℃,98%的三聚氰胺以微粒状结晶析出,而未转化的尿素仍留在气体中,三聚氰胺晶体和气体通过旋风分离器分离,得到的产品纯度达99.9%,分离效率为99%[4]。
从旋风分离器出来的循环气体进入尿素洗涤塔,冷却至140℃,循环气中未被回收的固体和气体三聚氰胺及未转化的尿素在尿素洗涤塔内被洗涤回收。
从洗涤塔出来的气体,一部分作为升华器的介质,一部分加压预热后循环入反应器,另一部分可返回尿素装置。
(2)中压尿素分解法(见图2)肥料级尿素以熔融状加入内热式的一段反应器中,与氧化铝催化剂进行流化接触反应,反应压力0.7MPa,反应温度390℃,反应吸热,以熔盐载体循环加热。
气体氨经加压升温至与反应器相同的温度后进入反应器,作为载体和流化介质。
反应气体从反应器顶部放出并进入饱和器(操作压力与反应器同),在饱和器中立即被母液骤冷,骤冷后生成饱和氨和二氧化碳以及稀的三聚氰胺结晶料浆。
料浆经洗涤器后到组式分离器,获得浓缩的三聚氰胺结晶料浆,分离出的母液回饱和器。
浓缩浆液送入蒸出塔,将溶解在料浆中的氨汽提吹出。
吹出之氨气,以系统生成的冷凝水吸收,后与新鲜氨混合,作为吸收塔上部的吸收液。
三聚氰胺工艺技术方案

三聚氰胺工艺技术方案三聚氰胺,化学式为C3H6N6,是一种无色结晶粉末,广泛用于制造胶合板、纺织品、油墨、塑料及化妆品等领域。
然而,由于三聚氰胺在高温条件下会分解释放出有毒气体,对人体健康造成严重危害,因此,探索一种安全、高效的三聚氰胺工艺技术方案变得尤为重要。
以下是一种可能的三聚氰胺工艺技术方案:1.原料准备:在三聚氰胺生产过程中,需准备尿素和氨气作为原料。
其中,尿素为三聚氰胺的重要中间体,而氨气则是反应过程中的重要催化剂。
2.反应设备:选择一种高效、安全的反应设备,比如封闭型反应釜或批式反应设备。
确保设备能够在高温和高压条件下进行反应,以提高反应速率和产量。
同时,要配备相应的安全措施,如压力安全阀、爆破片和泄漏报警装置等,以防止设备运行中出现意外情况。
3.反应条件控制:在反应过程中,需要控制适当的反应温度和压力。
通常情况下,三聚氰胺的合成温度在150-200摄氏度之间,压力在20-40大气压之间。
这样的反应条件既能保证反应的高效进行,又能降低产生有害气体的风险。
4.催化剂选择:合适的催化剂选择对于提高三聚氰胺的产率至关重要。
传统上,采用金属氰化物系催化剂进行三聚氰胺的合成,如氰化钾、氰化钙等。
然而,这些催化剂具有毒性和腐蚀性,不利于工艺安全和环境保护。
因此,应优先考虑使用非重金属催化剂和可再生催化剂,以降低工艺过程中对环境的影响。
5.分离和纯化:三聚氰胺合成反应结束后,需要将反应产物中的杂质和副产物进行分离和纯化。
这可以使用吸附、结晶、蒸馏等方法进行,并根据产品的要求进行进一步处理和提纯。
6.废物处理:三聚氰胺的工艺过程中会产生一定量的废物和副产物,如氰化物、氨和有机废水等。
这些废物需要进行集中处理和处置,遵循环保要求,以防止对环境造成污染。
总结:该三聚氰胺工艺技术方案在原料准备、反应设备、反应条件控制、催化剂选择、分离和纯化、废物处理等方面进行了综合考虑,以提高三聚氰胺的生产效率、降低生产成本,同时兼顾工艺安全和环境保护。
三聚氰胺生产工艺模板

三聚氰胺生产工艺以尿素为原料生产三聚氰胺分为高压法、中压法、低压法和常压法四种工艺。
(1)低压尿素分解法(见图1)肥料级尿素在贮罐中熔融后,用多个喷嘴喷入反应器中,以流态化氧化铝为催化剂,将预热至400℃循环氨气通入反应器保持流态化,反应压力为常压或稍高于大气压。
反应吸热,反应器内装有加热盘管,以熔融盐作为加热介质,维持反应温度380℃左右。
喷入尿素自行蒸发,反应生成三聚氰胺、二氧化碳和氨,转化率为95%。
反应气体从反应器顶部出来,优异入气体冷却器,冷却后温度在三聚氰胺露点以上。
在此温度下,密勒胺和密白胺等高沸点副产物结晶析出,和催化剂粉末一起经过滤器除去。
过滤后气体进升华器,以冷却至140℃循环气使升华器温度维持在170℃~200℃,98%三聚氰胺以微粒状结晶析出,而未转化尿素仍留在气体中,三聚氰胺晶体和气体经过旋风分离器分离,得到产品纯度达99.9%,分离效率为99%[4]。
从旋风分离器出来循环气体进入尿素洗涤塔,冷却至140℃,循环气中未被回收固体和气体三聚氰胺及未转化尿素在尿素洗涤塔内被洗涤回收。
从洗涤塔出来气体,一部分作为升华器介质,一部分加压预热后循环入反应器,另一部分可返回尿素装置。
(2)中压尿素分解法(见图2)肥料级尿素以熔融状加入内热式一段反应器中,和氧化铝催化剂进行流化接触反应,反应压力0.7MPa,反应温度390℃,反应吸热,以熔盐载体循环加热。
气体氨经加压升温至和反应器相同温度后进入反应器,作为载体和流化介质。
反应气体从反应器顶部放出并进入饱和器(操作压力和反应器同),在饱和器中立即被母液骤冷,骤冷后生成饱和氨和二氧化碳和稀三聚氰胺结晶料浆。
料浆经洗涤器后到组式分离器,取得浓缩三聚氰胺结晶料浆,分离出母液回饱和器。
浓缩浆液送入蒸出塔,将溶解在料浆中氨汽提吹出。
吹出之氨气,以系统生成冷凝水吸收,后和新鲜氨混合,作为吸收塔上部吸收液。
骤冷后气体(关键为氨、二氧化碳和水蒸汽)去吸收塔,吸收后大部分不含二氧化碳氨气从顶部以干气逸出,然后经预热循环入反应器。
三聚氰胺工艺技术方案解读

三聚氰胺工艺技术方案解读三聚氰胺(Melamine)工艺技术是一种化工工艺,能够将尿素及其它氮含有化合物裂解为三聚氰胺。
三聚氰胺广泛用于制造塑料、胶粘剂、涂料、纸张和橡胶等产品。
本文将对三聚氰胺工艺技术方案进行解读。
一、方案概述1.原料准备三聚氰胺的主要原料是尿素和氨气。
尿素作为反应的氮源,氨气则作为催化剂。
在原料准备阶段,需要将尿素和氨气按照一定的比例混合,并确保原料的纯度和稳定性。
2.反应装置三聚氰胺的反应装置通常采用连续流化床反应器。
该反应器具有较大的反应面积,能够提高反应效率。
此外,反应器还需要具备良好的密封性能和温度控制能力,以确保反应过程稳定。
3.反应过程控制三聚氰胺的反应过程受控制参数主要包括反应温度、压力和催化剂的投入速率。
在反应过程中,需要通过合理控制这些参数,以提高三聚氰胺的产率和质量。
4.产品处理三聚氰胺的产物需经过处理才可得到纯度较高的产品。
一般来说,原始产物中还会含有一些杂质和未反应的废料,需要通过过滤、结晶等步骤进行分离和纯化。
处理后的产品可以直接用于制造各种终端产品。
二、方案解读1.低成本生产三聚氰胺的原料尿素价格低廉,而氨气作为催化剂的投入量相对较小。
因此,采用该工艺技术可以实现较低成本的生产。
2.高产率和高纯度采用连续流化床反应器可以提高产率和纯度,确保产品的质量。
此外,通过合理控制反应参数,还可进一步提高产量和纯度。
3.环保可持续4.广泛应用领域三聚氰胺作为一种重要的化工中间体,在塑料、涂料、纸张、橡胶等领域有着广泛的应用。
采用该工艺技术可以满足不同领域的需求。
5.过程可控性强通过合理设置反应参数和控制装置,可以实现三聚氰胺工艺的稳定和可控。
生产过程中可监测和调整的参数较多,操作灵活性大。
三、结论三聚氰胺工艺技术方案是一种成熟的化工工艺,能够实现对尿素等原料的高效转化,产出高纯度的三聚氰胺产品。
该方案具备低成本、高产率、环保可持续等优势,在塑料、涂料、纸张等领域有着广泛应用。
三聚氰胺工艺技术方案

三聚氰胺工艺技术方案一、方案背景与目标三聚氰胺是一种有机物,其化学名称为三聚氰胺,并具有很高的氮含量。
它具有耐磨损、耐高温、耐化学腐蚀等特点,因而广泛应用于合成树脂、胶粘剂、导热材料等领域。
然而,三聚氰胺的生产过程中存在一系列的环境污染问题,例如产生大量有毒废水和废气、消耗大量能源等。
本方案旨在探讨一种环境友好的三聚氰胺工艺技术,以降低对环境的污染,提高能源利用效率。
二、工艺方案1.原料选择:优先选择环保型原料,减少工艺中有毒有害物质的产生。
对于有害物质难以避免的情况,采取回收再利用或安全处理的方法,最大限度减少对环境的影响。
2.变电站设计:采用高效的变电站,以确保稳定的供电,并在可能的情况下利用可再生能源,如太阳能或风能,减少对传统能源的依赖。
3.生产工艺改进:优化三聚氰胺的生产工艺,减少副产物和废弃物的产生。
具体措施包括:1)优化反应条件,以提高反应效率,减少副产品的生成率。
2)建立废物回收系统,对产生的有机废物进行回收和再利用,减少废物排放。
3)采用节能设备,如高效循环水冷却系统、余热回收装置等,减少能源消耗。
4.废水处理:建立废水处理系统,对废水进行初级处理和二次处理,使其符合环境排放标准。
初级处理包括物理除泥、沉淀等,二次处理包括生化处理或其他适用的技术,以确保废水排放的安全和合规。
5.废气处理:建立废气处理系统,对排出的废气进行收集、净化和处理。
常用的处理方法包括吸收、活性炭吸附、催化氧化等,以降低废气中有害物质的浓度,达到环境排放标准。
6.整合资源回收利用:建立废弃物回收利用系统,对产生的废物进行分类、回收和利用。
例如,废液中的有机成分可以用于生产其他化工产品,废石蜡可以用于制备润滑油等。
三、预期效果通过采用以上的工艺技术,预期可以达到以下效果:1.环境友好:减少废水和废气排放,降低对环境的污染,提高生态环保水平。
2.资源节约:优化反应工艺,减少副产物和废弃物的生成,实现资源的最大利用。
三聚氰胺的工艺流程

三聚氰胺的工艺流程
《三聚氰胺的工艺流程》
三聚氰胺是一种重要的化工原料,广泛应用于合成树脂、胶粘剂和涂料等领域。
下面简要介绍三聚氰胺的工艺流程。
首先,三聚氰胺的生产通常采用尿素和氰胺为原料,通过高温和高压的合成反应合成而成。
具体来说,首先将尿素和氰胺按一定的比例混合,然后加入催化剂,在高温高压的条件下进行缩合反应,生成三聚氰胺。
其次,合成得到的三聚氰胺需要进行进一步的精制和提纯过程。
这一步通常通过结晶和结晶分离、溶剂萃取、再结晶等方法来实现。
通过这些工艺,可以去除杂质,提高三聚氰胺的纯度和品质。
最后,通过干燥和包装等工艺,将提纯后的三聚氰胺产品打包成为商业化的成品。
在这个过程中,需要确保产品符合相关的质量标准和安全要求,并做好相应的包装和标识工作,以便于运输和销售。
总的来说,三聚氰胺的工艺流程主要包括合成反应、精制提纯和成品包装等环节。
通过科学的工艺流程和严格的质量控制,可以生产出高质量、符合要求的三聚氰胺产品,满足市场需求。
三聚氰胺工艺技术方案解读
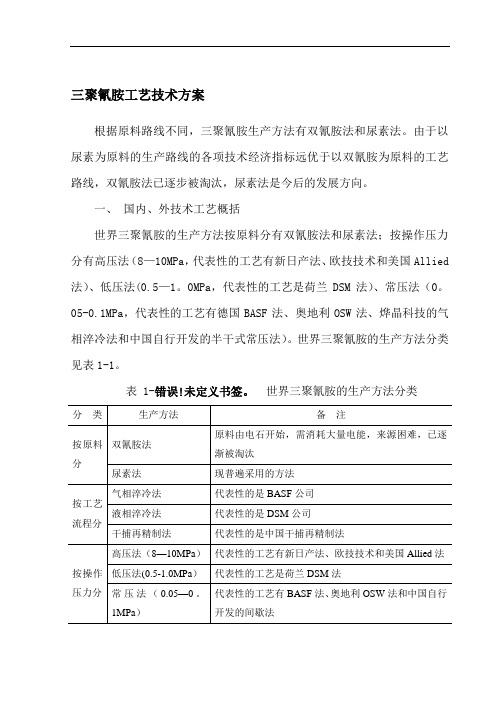
三聚氰胺工艺技术方案根据原料路线不同,三聚氰胺生产方法有双氰胺法和尿素法。
由于以尿素为原料的生产路线的各项技术经济指标远优于以双氰胺为原料的工艺路线,双氰胺法已逐步被淘汰,尿素法是今后的发展方向。
一、国内、外技术工艺概括世界三聚氰胺的生产方法按原料分有双氰胺法和尿素法;按操作压力分有高压法(8—10MPa,代表性的工艺有新日产法、欧技技术和美国Allied 法)、低压法(0.5—1。
0MPa,代表性的工艺是荷兰DSM法)、常压法(0。
05-0.1MPa,代表性的工艺有德国BASF法、奥地利OSW法、烨晶科技的气相淬冷法和中国自行开发的半干式常压法)。
世界三聚氰胺的生产方法分类见表1-1。
表 1-错误!未定义书签。
世界三聚氰胺的生产方法分类目前世界三聚氰胺生产普遍采用尿素原料路线。
以尿素为原料生产三聚氰胺可分为高压法、低压法和常压法等三种主要生产工艺.无论哪种工艺技术,其生产都有反应、淬冷和尾气回收三个工序。
1)反应过程:以熔融尿素为原料,在一定温度、压力下尿素转化为三聚氰胺,同时放出NH3和CO2.三聚氰胺的化学合成反应方程式如下:2)淬冷过程:反应后生成物可用水、母液或气体进行急冷,以防止高温下产物水解,减少反应副产物的生成。
3)尾气回收:三聚氰胺生产中生成的NH3和CO2:必须回收后循环利用,国内外对尾气回收技术均十分重视,是三聚氰胺生产工艺技术中不可分割的重要内容.1、国外技术工艺概括目前,世界上技术先进、竞争力较强的三聚氰胺生产工艺主要有日本的Nissan和意大利的Montedison高压法以及荷兰DSM和德国BASF的低压法。
1)Nissan工艺Nissan工艺是将熔融尿素加压至10.0 MPa,经高压洗涤塔吸收反应器释放的尾气中残余的三聚氰胺和未反应的尿素后进入三聚氰胺反应器,同时与加压、加热至10.0 MPa,400 ℃的液氨进入反应塔,在10.0 MPa和380~400℃的条件下,尿素转化为三聚氰胺。
三聚氰胺工艺技术方案建议书

三聚氰胺工艺技术方案建议书一、前言三聚氰胺是一种重要的有机化工原料,具有广泛的应用领域。
为了满足市场需求,提高生产效率和产品质量,特制定本三聚氰胺工艺技术方案建议书。
二、工艺原理三聚氰胺的生产通常基于尿素的热解和缩合反应。
在高温高压的条件下,尿素发生分解和聚合,生成三聚氰胺以及氨气、二氧化碳等副产物。
三、工艺流程1、尿素溶解与预热将固体尿素溶解在去离子水中,形成一定浓度的尿素溶液。
然后通过热交换器将溶液预热至适宜的温度。
2、尿素热解预热后的尿素溶液进入热解反应器,在高温高压下进行热解反应。
反应条件通常为 380 400℃,8 15 MPa。
3、三聚氰胺生成与分离热解产物进入三聚氰胺结晶器,通过冷却和降压使三聚氰胺结晶析出。
然后通过过滤或离心等方式将三聚氰胺晶体与母液分离。
4、尾气处理反应产生的氨气、二氧化碳等尾气经过吸收、净化等处理后达标排放,或者回收利用。
5、产品精制分离得到的三聚氰胺晶体经过干燥、粉碎等处理,得到符合质量标准的三聚氰胺产品。
四、主要设备1、尿素溶解槽用于溶解固体尿素,通常采用不锈钢材质,配备搅拌装置和加热装置。
2、预热器采用列管式或板式换热器,将尿素溶液预热至反应所需温度。
3、热解反应器为高压反应釜,能够承受高温高压条件,内部装有特殊的搅拌装置和加热装置,以确保反应均匀进行。
4、结晶器用于三聚氰胺的结晶,可采用冷却结晶或减压结晶方式,材质一般为不锈钢。
5、过滤器或离心机用于分离三聚氰胺晶体和母液,根据生产规模和工艺要求选择合适的设备型号。
6、干燥器常见的有流化床干燥器或喷雾干燥器,用于干燥三聚氰胺晶体,去除水分。
7、尾气处理装置包括吸收塔、净化器等设备,用于处理尾气中的有害物质。
五、原材料及能源需求1、原材料主要原材料为尿素,要求尿素纯度达到一定标准,以保证三聚氰胺的质量和收率。
2、能源需求(1)蒸汽用于加热、蒸发等过程,压力和温度根据工艺要求确定。
(2)电力驱动搅拌装置、泵、风机等设备运行。
三聚氰胺工艺技术方案
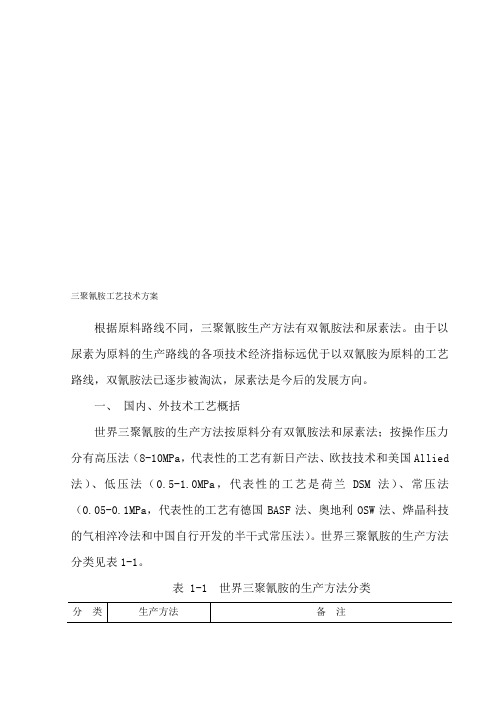
三聚氰胺工艺技术方案根据原料路线不同,三聚氰胺生产方法有双氰胺法和尿素法。
由于以尿素为原料的生产路线的各项技术经济指标远优于以双氰胺为原料的工艺路线,双氰胺法已逐步被淘汰,尿素法是今后的发展方向。
一、国内、外技术工艺概括世界三聚氰胺的生产方法按原料分有双氰胺法和尿素法;按操作压力分有高压法(8-10MPa,代表性的工艺有新日产法、欧技技术和美国Allied 法)、低压法(0.5-1.0MPa,代表性的工艺是荷兰DSM法)、常压法(0.05-0.1MPa,代表性的工艺有德国BASF法、奥地利OSW法、烨晶科技的气相淬冷法和中国自行开发的半干式常压法)。
世界三聚氰胺的生产方法分类见表1-1。
表 1-1 世界三聚氰胺的生产方法分类目前世界三聚氰胺生产普遍采用尿素原料路线。
以尿素为原料生产三聚氰胺可分为高压法、低压法和常压法等三种主要生产工艺。
无论哪种工艺技术,其生产都有反应、淬冷和尾气回收三个工序。
1)反应过程:以熔融尿素为原料,在一定温度、压力下尿素转化为三聚氰胺,同时放出NH 3和CO 2。
三聚氰胺的化学合成反应方程式如下:2)淬冷过程:反应后生成物可用水、母液或气体进行急冷,以防止高温下产物水解,减少反应副产物的生成。
3)尾气回收:三聚氰胺生产中生成的NH 3和CO 2:必须回收后循环利用,国内外对尾气回收技术均十分重视,是三聚氰胺生产工艺技术中不可分割的重要内容。
6H N-CO-NH 2 2 热压力三聚氰胺尿素+ 2 +3CO 36NH N N N 2NH 22NH 氨二氧化碳1、国外技术工艺概括目前,世界上技术先进、竞争力较强的三聚氰胺生产工艺主要有日本的Nissan和意大利的Montedison高压法以及荷兰DSM和德国BASF的低压法。
1)Nissan工艺Nissan工艺是将熔融尿素加压至10.0 MPa,经高压洗涤塔吸收反应器释放的尾气中残余的三聚氰胺和未反应的尿素后进入三聚氰胺反应器,同时与加压、加热至10.0 MPa,400 ℃的液氨进入反应塔,在10.0 MPa和380~400℃的条件下,尿素转化为三聚氰胺。
三聚氰胺工艺流程
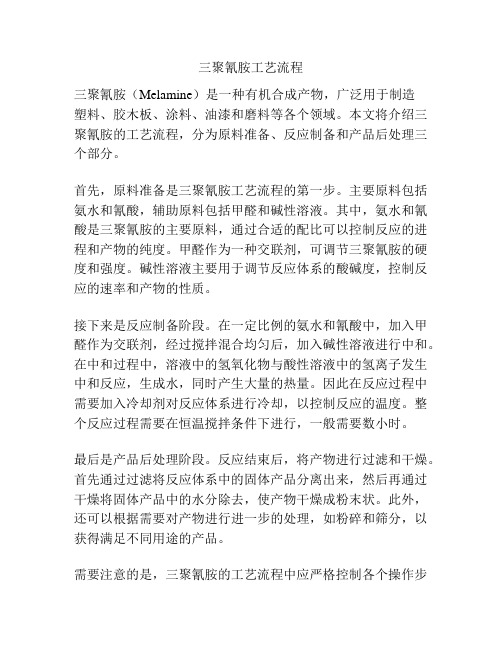
三聚氰胺工艺流程三聚氰胺(Melamine)是一种有机合成产物,广泛用于制造塑料、胶木板、涂料、油漆和磨料等各个领域。
本文将介绍三聚氰胺的工艺流程,分为原料准备、反应制备和产品后处理三个部分。
首先,原料准备是三聚氰胺工艺流程的第一步。
主要原料包括氨水和氰酸,辅助原料包括甲醛和碱性溶液。
其中,氨水和氰酸是三聚氰胺的主要原料,通过合适的配比可以控制反应的进程和产物的纯度。
甲醛作为一种交联剂,可调节三聚氰胺的硬度和强度。
碱性溶液主要用于调节反应体系的酸碱度,控制反应的速率和产物的性质。
接下来是反应制备阶段。
在一定比例的氨水和氰酸中,加入甲醛作为交联剂,经过搅拌混合均匀后,加入碱性溶液进行中和。
在中和过程中,溶液中的氢氧化物与酸性溶液中的氢离子发生中和反应,生成水,同时产生大量的热量。
因此在反应过程中需要加入冷却剂对反应体系进行冷却,以控制反应的温度。
整个反应过程需要在恒温搅拌条件下进行,一般需要数小时。
最后是产品后处理阶段。
反应结束后,将产物进行过滤和干燥。
首先通过过滤将反应体系中的固体产品分离出来,然后再通过干燥将固体产品中的水分除去,使产物干燥成粉末状。
此外,还可以根据需要对产物进行进一步的处理,如粉碎和筛分,以获得满足不同用途的产品。
需要注意的是,三聚氰胺的工艺流程中应严格控制各个操作步骤的条件,尤其是反应温度、压力和搅拌速度等关键参数。
过高或过低的温度可能导致反应速度过快或过慢,影响产物的质量和产率。
搅拌速度过快或过慢可能导致反应体系不均匀,影响反应的进行。
因此,在操作过程中需要根据实际情况进行调整和控制。
综上所述,三聚氰胺的工艺流程包括原料准备、反应制备和产品后处理三个阶段。
通过合适的原料配比和反应条件控制,可以获得高质量的三聚氰胺产品。
此外,工艺流程中的每个步骤都要严格控制,以确保产品的质量和产量。
三聚氰胺的生产工艺

三聚氰胺生产工艺以尿素为原料生产三聚氰胺分为高压法、中压法、低压法和常压法四种工艺。
(1)低压尿素分解法(见图1)肥料级尿素在贮罐中熔融后,用几个喷嘴喷入反应器中,以流态化的氧化铝为催化剂,将预热至400℃的循环氨气通入反应器保持流态化,反应压力为常压或稍高于大气压。
反应吸热,反应器内装有加热盘管,以熔融盐作为加热介质,维持反应温度380℃左右。
喷入的尿素自行蒸发,反应生成三聚氰胺、二氧化碳和氨,转化率为95%。
反应气体从反应器顶部出来,先进入气体冷却器,冷却后的温度在三聚氰胺的露点以上。
在此温度下,密勒胺和密白胺等高沸点副产物结晶析出,和催化剂粉末一起经过滤器除去。
过滤后的气体进升华器,以冷却至140℃的循环气使升华器的温度维持在170℃~200℃,98%的三聚氰胺以微粒状结晶析出,而未转化的尿素仍留在气体中,三聚氰胺晶体和气体通过旋风分离器分离,得到的产品纯度达99.9%,分离效率为99%[4]。
从旋风分离器出来的循环气体进入尿素洗涤塔,冷却至140℃,循环气中未被回收的固体和气体三聚氰胺及未转化的尿素在尿素洗涤塔内被洗涤回收。
从洗涤塔出来的气体,一部分作为升华器的介质,一部分加压预热后循环入反应器,另一部分可返回尿素装置。
(2)中压尿素分解法(见图2)肥料级尿素以熔融状加入内热式的一段反应器中,与氧化铝催化剂进行流化接触反应,反应压力0.7MPa,反应温度390℃,反应吸热,以熔盐载体循环加热。
气体氨经加压升温至与反应器相同的温度后进入反应器,作为载体和流化介质。
反应气体从反应器顶部放出并进入饱和器(操作压力与反应器同),在饱和器中立即被母液骤冷,骤冷后生成饱和氨和二氧化碳以及稀的三聚氰胺结晶料浆。
料浆经洗涤器后到组式分离器,获得浓缩的三聚氰胺结晶料浆,分离出的母液回饱和器。
浓缩浆液送入蒸出塔,将溶解在料浆中的氨汽提吹出。
吹出之氨气,以系统生成的冷凝水吸收,后与新鲜氨混合,作为吸收塔上部的吸收液。
三聚氰胺的工艺
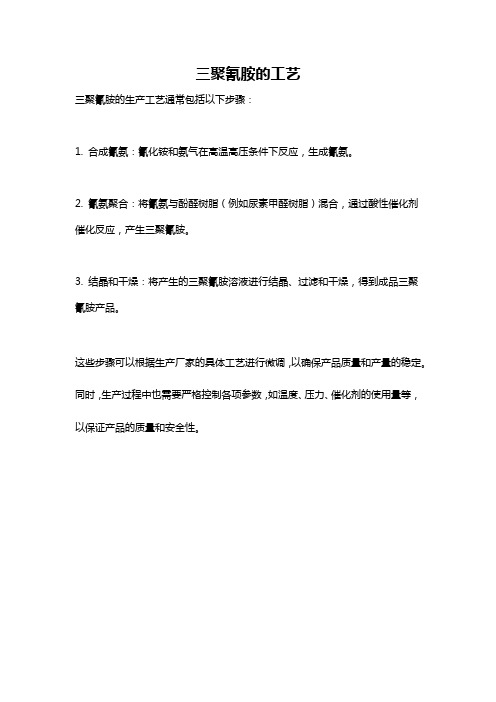
三聚氰胺的工艺
三聚氰胺的生产工艺通常包括以下步骤:
1. 合成氰氨:氰化铵和氨气在高温高压条件下反应,生成氰氨。
2. 氰氨聚合:将氰氨与酚醛树脂(例如尿素甲醛树脂)混合,通过酸性催化剂催化反应,产生三聚氰胺。
3. 结晶和干燥:将产生的三聚氰胺溶液进行结晶、过滤和干燥,得到成品三聚氰胺产品。
这些步骤可以根据生产厂家的具体工艺进行微调,以确保产品质量和产量的稳定。
同时,生产过程中也需要严格控制各项参数,如温度、压力、催化剂的使用量等,以保证产品的质量和安全性。
三聚氰胺工艺技术方案解读

三聚氰胺工艺技术方案解读
首先,原料准备。
三聚氰胺的主要原料是氰氨和氨水。
在工艺方案中,应注明原料的纯度要求和质量控制要点。
此外,还应考虑到原料的供应和
储存问题,确保生产过程的连续性和稳定性。
其次,反应条件。
三聚氰胺的合成反应是一种缩合反应,通常在碱性
条件下进行。
通过调节反应物的摩尔比例、反应温度和pH值等参数,可
以控制反应的速率和产物的收率。
在工艺方案中,应明确反应条件的选择
和优化方法。
第三,反应控制。
三聚氰胺的合成反应属于有机合成反应,需要进行
反应控制以保证产品质量和产量。
在工艺方案中,应详细描述反应控制的
方法和策略,包括温度、压力、时间和搅拌速度等参数的控制。
第四,产品分离与提纯。
合成反应结束后,需要对产物进行分离和提纯。
在工艺方案中,应说明分离的方法和步骤,如过滤、析出和结晶等。
此外,还应考虑到废水和废气处理的问题,确保环保要求的满足。
最后,工艺管控与质量控制。
在生产过程中,需要进行工艺管控和质
量控制,以确保产品的一致性和合格率。
在工艺方案中,应详细描述工艺
管控和质量控制的措施和要求,包括检测方法、质量标准和纠正措施等。
综上所述,三聚氰胺工艺技术方案是一种全面考虑原料准备、反应条件、反应控制、产品分离与提纯以及工艺管控与质量控制等要素的方案。
它对于三聚氰胺的制备和生产具有重要的指导意义,可以实现高产量和高
质量的生产目标。
在实际应用中,还需根据具体情况进行调整和改进,以
满足不同生产条件和要求。
三聚氰胺 生产工艺

三聚氰胺生产工艺
三聚氰胺是一种有机化合物,其分子式为C3H6N6。
它是由三个氰胺基团通过共轭作用连接而成的。
三聚氰胺的生产工艺主要包括合成反应和后续的处理工艺。
合成反应通常采用氰胺和甲醛作为原料。
首先,将氰胺与甲醛按照一定的比例加入反应釜中,通过加热将反应釜升温至约140℃左右。
在一定的温度和压力条件下,氰胺和甲醛发生缩合反应,生成三聚氰胺。
合成反应的过程中,需要注意控制反应的温度、压力和原料的配比。
过高的温度和压力会导致反应副产物的生成,降低产品的质量。
而反应釜中缺氧环境也有利于反应的进行,可以减少副产物的生成。
合成反应完成后,需要对产物进行后续的处理工艺。
首先,通过加热和蒸汽压力的作用,将反应釜中的三聚氰胺进行干燥。
接下来,将干燥后的产物进行粉碎和筛分,得到符合要求的粒度。
粉碎和筛分后的三聚氰胺可以直接使用,也可以进行其他加工工艺。
比如,在一些特殊场合,可以将三聚氰胺进行烧结,以提高其物理性能,并使其更加耐高温。
三聚氰胺的生产工艺需要注意反应条件的控制和产品的后续处
理。
合理的生产工艺可以提高产品的质量,并满足不同领域的需求。
三聚氰胺生产工艺

三聚氰胺生产工艺
三聚氰胺是一种有机化合物,化学式为C3H6N6。
它具有高热
稳定性、高硬度、高强度和抗划伤等特点,被广泛应用于合成树脂、皮革、纺织品、胶粘剂、染料、杀菌剂等领域。
三聚氰胺的生产工艺分为以下几个步骤:
1. 氧化氨法制备氰氨:首先将氨气和空气以一定的比例通入氨化炉中,使氨气与空气在高温下发生反应生成氰氨。
2. 氰氨和氰化钠反应生成叠氮化钠:将氰氨溶液和氰化钠溶液以一定的比例混合后,在一定的温度和压力下进行反应,生成叠氮化钠。
3. 叠氮化钠和二氯甲烷反应生成三聚氰胺:将叠氮化钠和二氯甲烷以一定的比例混合后,在一定的温度和压力下进行反应,生成三聚氰胺。
这是三聚氰胺的传统生产工艺,也是目前广泛采用的工艺。
然而,这种工艺存在一些问题,如反应条件苛刻、原料利用率低、产物纯度不高等。
为了解决这些问题,研究人员进行了许多改进和创新。
一种改进的工艺是采用氰尿酸法生产三聚氰胺。
该工艺的主要步骤如下:
1. 氨气和二氧化碳反应生成氰尿酸:将氨气和二氧化碳以一定
的比例混合后,在一定的温度、压力和催化剂的作用下进行反应,生成氰尿酸。
2. 氰尿酸和氰化钠反应生成三聚氰胺:将氰尿酸溶液和氰化钠溶液以一定的比例混合后,在一定的温度和压力下进行反应,生成三聚氰胺。
与传统工艺相比,氰尿酸法具有以下优点:反应条件温和、原料利用率高、产物纯度高等。
总的来说,三聚氰胺的生产工艺主要有氧化氨法和氰尿酸法两种。
随着科技发展和工艺改进,生产工艺将不断优化,以提高生产效率、降低成本,并满足市场需求。
三聚氰胺生产工艺简介整理版
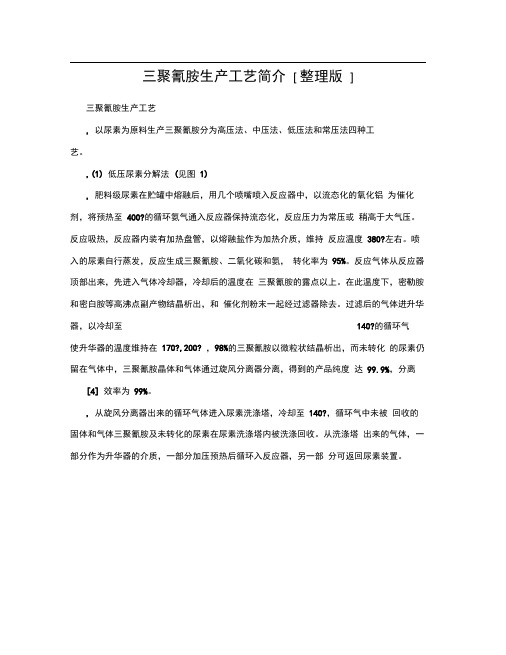
三聚氰胺生产工艺简介[ 整理版]三聚氰胺生产工艺, 以尿素为原料生产三聚氰胺分为高压法、中压法、低压法和常压法四种工艺。
,(1) 低压尿素分解法(见图1), 肥料级尿素在贮罐中熔融后,用几个喷嘴喷入反应器中,以流态化的氧化铝为催化剂,将预热至400?的循环氨气通入反应器保持流态化,反应压力为常压或稍高于大气压。
反应吸热,反应器内装有加热盘管,以熔融盐作为加热介质,维持反应温度380?左右。
喷入的尿素自行蒸发,反应生成三聚氰胺、二氧化碳和氨,转化率为95%。
反应气体从反应器顶部出来,先进入气体冷却器,冷却后的温度在三聚氰胺的露点以上。
在此温度下,密勒胺和密白胺等高沸点副产物结晶析出,和催化剂粉末一起经过滤器除去。
过滤后的气体进升华器,以冷却至140?的循环气使升华器的温度维持在170?,200? ,98%的三聚氰胺以微粒状结晶析出,而未转化的尿素仍留在气体中,三聚氰胺晶体和气体通过旋风分离器分离,得到的产品纯度达99.9%,分离[4] 效率为99%。
, 从旋风分离器出来的循环气体进入尿素洗涤塔,冷却至140?,循环气中未被回收的固体和气体三聚氰胺及未转化的尿素在尿素洗涤塔内被洗涤回收。
从洗涤塔出来的气体,一部分作为升华器的介质,一部分加压预热后循环入反应器,另一部分可返回尿素装置。
,(2)中压尿素分解法(见图2),肥料级尿素以熔融状加入内热式的一段反应器中,与氧化铝催化剂进行流化接触反应,反应压力0.7MPa,反应温度390?,反应吸热,以熔盐载体循环加热。
气体氨经加压升温至与反应器相同的温度后进入反应器,作为载体和流化介质。
反 应气体从反应器顶部放出并进入饱和器(操作压力与反应器同),在饱和器中立即被 母液骤冷,骤冷后生成饱和氨和二氧化碳以及稀的三聚氰胺结晶料浆。
料浆经洗涤 器后到组式分离器,获得浓缩的三聚氰胺结晶料浆,分离出的母液回饱和器。
浓缩 浆液送入蒸出塔,将溶解在料浆中的氨汽提吹出。
吹出之氨气,以系统生成的冷凝 水吸收,后与新鲜氨混合,作为吸收塔上部的吸收液。
三聚氰胺工艺过程概述
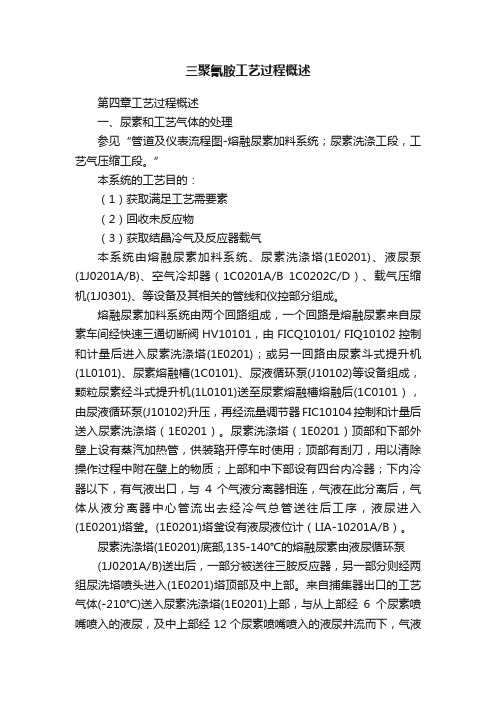
三聚氰胺工艺过程概述第四章工艺过程概述一、尿素和工艺气体的处理参见“管道及仪表流程图-熔融尿素加料系统;尿素洗涤工段,工艺气压缩工段。
”本系统的工艺目的:(1)获取满足工艺需要素(2)回收未反应物(3)获取结晶冷气及反应器载气本系统由熔融尿素加料系统、尿素洗涤塔(1E0201)、液尿泵(1J0201A/B)、空气冷却器(1C0201A/B 1C0202C/D)、载气压缩机(1J0301)、等设备及其相关的管线和仪控部分组成。
熔融尿素加料系统由两个回路组成,一个回路是熔融尿素来自尿素车间经快速三通切断阀 HV10101,由 FICQ10101/ FIQ10102 控制和计量后进入尿素洗涤塔(1E0201);或另一回路由尿素斗式提升机(1L0101)、尿素熔融槽(1C0101)、尿液循环泵(J10102)等设备组成,颗粒尿素经斗式提升机(1L0101)送至尿素熔融槽熔融后(1C0101),由尿液循环泵(J10102)升压,再经流量调节器FIC10104控制和计量后送入尿素洗涤塔(1E0201)。
尿素洗涤塔(1E0201)顶部和下部外壁上设有蒸汽加热管,供装臵开停车时使用;顶部有刮刀,用以清除操作过程中附在壁上的物质;上部和中下部设有四台内冷器;下内冷器以下,有气液出口,与4 个气液分离器相连,气液在此分离后,气体从液分离器中心管流出去经冷气总管送往后工序,液尿进入(1E0201)塔釜。
(1E0201)塔釜设有液尿液位计(LIA-10201A/B)。
尿素洗涤塔(1E0201)底部,135-140℃的熔融尿素由液尿循环泵(1J0201A/B)送出后,一部分被送往三胺反应器,另一部分则经两组尿洗塔喷头进入(1E0201)塔顶部及中上部。
来自捕集器出口的工艺气体(-210℃)送入尿素洗涤塔(1E0201)上部,与从上部经6个尿素喷嘴喷入的液尿,及中上部经12个尿素喷嘴喷入的液尿并流而下,气液充分密切混合,完成传热传质,经尿素洗涤塔洗涤后,工艺气体中的未反应的尿素和未被捕集器(1L0702A/B)捕集下来的三聚氰胺细粉被熔融尿素洗涤下来,并混入尿素之中得以回收利用,工艺气体温度降至135-140℃,而液尿的温度则则达到135-140℃。
三聚氰胺工艺技术方案建议书

三聚氰胺工艺技术方案建议书一、引言三聚氰胺是一种重要的有机化工原料,具有广泛的应用领域。
为了满足市场需求,提高生产效率和产品质量,特制定本三聚氰胺工艺技术方案建议书。
二、三聚氰胺的性质和用途三聚氰胺,化学式为 C₃H₆N₆,是一种白色单斜晶体。
它具有耐高温、阻燃、耐水、耐腐蚀等特性,因此被广泛应用于塑料、涂料、胶粘剂、造纸、纺织等行业。
在塑料工业中,三聚氰胺可用于生产三聚氰胺甲醛树脂,这种树脂具有良好的耐热性、耐水性和机械强度,常用于制造餐具、电器外壳等;在涂料行业,三聚氰胺可以提高涂料的硬度、光泽度和耐腐蚀性;在胶粘剂领域,三聚氰胺甲醛胶粘剂具有较高的粘接强度和耐水性;在造纸工业中,三聚氰胺可用于纸张的增强和抗水剂;在纺织行业,三聚氰胺可用于织物的阻燃处理。
三、现有三聚氰胺生产工艺概述目前,三聚氰胺的生产工艺主要有高压法、低压法和常压法三种。
高压法是最早开发的三聚氰胺生产工艺,反应压力高达 80 100 MPa,温度为 370 450℃。
该工艺的优点是技术成熟、产品质量高,但设备投资大、操作条件苛刻、能耗高。
低压法的反应压力一般在 05 10 MPa,温度为 380 420℃。
与高压法相比,低压法的设备投资和能耗有所降低,但产品质量稍逊一筹。
常压法是近年来发展起来的一种新工艺,反应压力接近常压,温度为 350 400℃。
常压法具有投资少、能耗低、操作简单等优点,但目前技术还不够成熟,工业化应用较少。
四、推荐的三聚氰胺生产工艺经过综合比较和分析,我们推荐采用低压法生产三聚氰胺。
以下是该工艺的详细流程:1、尿素合成以氨气和二氧化碳为原料,在一定的温度和压力下合成尿素溶液。
2、三聚氰胺合成将尿素溶液送入三聚氰胺合成反应器,在催化剂的作用下,经过加热分解和缩合反应生成三聚氰胺。
反应方程式如下:6(NH₂)₂CO → C₃H₆N₆+ 6NH₃+ 3CO₂3、气体分离反应生成的气体混合物包括氨气、二氧化碳和水蒸气等,通过冷却、吸收等方式进行分离,回收氨气和二氧化碳循环使用。
三聚氰胺的工艺流程
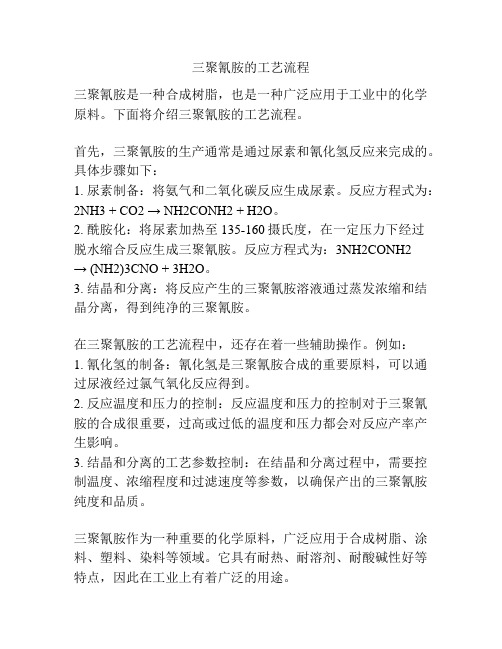
三聚氰胺的工艺流程
三聚氰胺是一种合成树脂,也是一种广泛应用于工业中的化学原料。
下面将介绍三聚氰胺的工艺流程。
首先,三聚氰胺的生产通常是通过尿素和氰化氢反应来完成的。
具体步骤如下:
1. 尿素制备:将氨气和二氧化碳反应生成尿素。
反应方程式为:2NH3 + CO2 → NH2CONH2 + H2O。
2. 酰胺化:将尿素加热至135-160摄氏度,在一定压力下经过
脱水缩合反应生成三聚氰胺。
反应方程式为:3NH2CONH2
→ (NH2)3CNO + 3H2O。
3. 结晶和分离:将反应产生的三聚氰胺溶液通过蒸发浓缩和结晶分离,得到纯净的三聚氰胺。
在三聚氰胺的工艺流程中,还存在着一些辅助操作。
例如:
1. 氰化氢的制备:氰化氢是三聚氰胺合成的重要原料,可以通过尿液经过氯气氧化反应得到。
2. 反应温度和压力的控制:反应温度和压力的控制对于三聚氰胺的合成很重要,过高或过低的温度和压力都会对反应产率产生影响。
3. 结晶和分离的工艺参数控制:在结晶和分离过程中,需要控制温度、浓缩程度和过滤速度等参数,以确保产出的三聚氰胺纯度和品质。
三聚氰胺作为一种重要的化学原料,广泛应用于合成树脂、涂料、塑料、染料等领域。
它具有耐热、耐溶剂、耐酸碱性好等特点,因此在工业上有着广泛的用途。
总结起来,三聚氰胺的工艺流程主要包括尿素制备、酰胺化反应、结晶和分离等步骤。
通过合理的控制工艺参数,可以生产出高纯度的三聚氰胺,满足各种工业需要。
三聚氰胺工艺技术方案
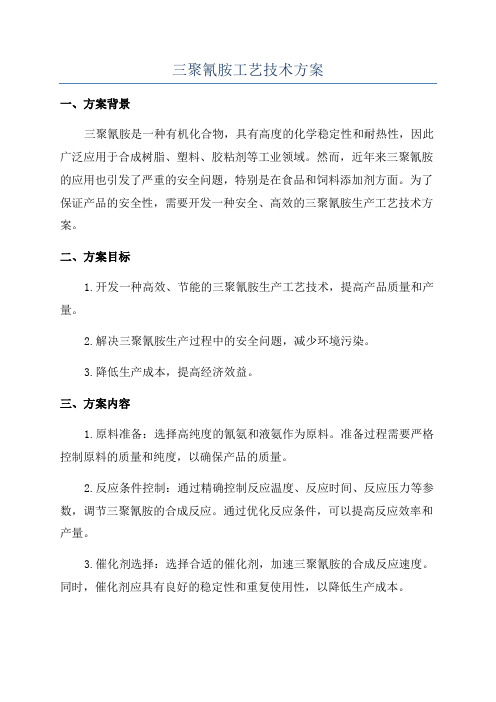
三聚氰胺工艺技术方案一、方案背景三聚氰胺是一种有机化合物,具有高度的化学稳定性和耐热性,因此广泛应用于合成树脂、塑料、胶粘剂等工业领域。
然而,近年来三聚氰胺的应用也引发了严重的安全问题,特别是在食品和饲料添加剂方面。
为了保证产品的安全性,需要开发一种安全、高效的三聚氰胺生产工艺技术方案。
二、方案目标1.开发一种高效、节能的三聚氰胺生产工艺技术,提高产品质量和产量。
2.解决三聚氰胺生产过程中的安全问题,减少环境污染。
3.降低生产成本,提高经济效益。
三、方案内容1.原料准备:选择高纯度的氰氨和液氨作为原料。
准备过程需要严格控制原料的质量和纯度,以确保产品的质量。
2.反应条件控制:通过精确控制反应温度、反应时间、反应压力等参数,调节三聚氰胺的合成反应。
通过优化反应条件,可以提高反应效率和产量。
3.催化剂选择:选择合适的催化剂,加速三聚氰胺的合成反应速度。
同时,催化剂应具有良好的稳定性和重复使用性,以降低生产成本。
4.分离纯化:采用蒸馏、结晶等技术对反应产物进行分离纯化,得到高纯度的三聚氰胺产品。
5.污水处理:在三聚氰胺生产过程中产生的废水含有高浓度的有机物和氮化物,需要进行高效处理,以减少对环境的污染。
6.安全措施:制定严格的操作规程,配备必要的安全设备,并定期进行安全培训,以确保工作人员的安全。
四、方案优势1.高效节能:通过优化反应条件和催化剂的选择,提高反应效率,减少能量消耗。
2.产品质量高:通过控制原料质量和精确的反应条件控制,提高产品纯度和一致性。
3.环境友好:采用高效的污水处理技术,减少对环境的污染。
4.安全性高:制定严格的操作规程和安全措施,减少安全事故的发生。
五、方案实施计划1.锁定原料供应商,确保原料的质量和供应稳定性。
2.设计和建设三聚氰胺生产设备,包括反应釜、分离装置、污水处理系统等。
3.进行试点生产,验证工艺技术方案的可行性和效果。
4.优化工艺参数,改进设备和工艺细节,提高生产效率和质量。
- 1、下载文档前请自行甄别文档内容的完整性,平台不提供额外的编辑、内容补充、找答案等附加服务。
- 2、"仅部分预览"的文档,不可在线预览部分如存在完整性等问题,可反馈申请退款(可完整预览的文档不适用该条件!)。
- 3、如文档侵犯您的权益,请联系客服反馈,我们会尽快为您处理(人工客服工作时间:9:00-18:30)。
三聚氰胺工艺技术方案根据原料路线不同,三聚氰胺生产方法有双氰胺法和尿素法。
由于以尿素为原料的生产路线的各项技术经济指标远优于以双氰胺为原料的工艺路线,双氰胺法已逐步被淘汰,尿素法是今后的发展方向。
一、国内、外技术工艺概括世界三聚氰胺的生产方法按原料分有双氰胺法和尿素法;按操作压力分有高压法(8-10MPa,代表性的工艺有新日产法、欧技技术和美国Allied法)、低压法(0.5-1.0MPa,代表性的工艺是荷兰DSM法)、常压法(0.05-0.1MPa,代表性的工艺有德国BASF法、奥地利OSW法、烨晶科技的气相淬冷法和中国自行开发的半干式常压法)。
世界三聚氰胺的生产方法分类见表1-1。
表1-1 世界三聚氰胺的生产方法分类目前世界三聚氰胺生产普遍采用尿素原料路线。
以尿素为原料生产三聚氰胺可分为高压法、低压法和常压法等三种主要生产工艺。
无论哪种工艺技术,其生产都有反应、淬冷和尾气回收三个工序。
1)反应过程:以熔融尿素为原料,在一定温度、压力下尿素转化为三聚氰胺,同时放出NH3和CO2。
三聚氰胺的化学合成反应方程式如下:2)淬冷过程:反应后生成物可用水、母液或气体进行急冷,以防止高温下产物水解,减少反应副产物的生成。
3)尾气回收:三聚氰胺生产中生成的NH3和CO2:必须回收后循环利用,国内外对尾气回收技术均十分重视,是三聚氰胺生产工艺技术中不可分割的重要内容。
1、国外技术工艺概括目前,世界上技术先进、竞争力较强的三聚氰胺生产工艺主要有日本的Nissan和意大利的Montedison高压法以及荷兰DSM和德国BASF的低压法。
1)Nissan工艺Nissan工艺是将熔融尿素加压至10.0 MPa,经高压洗涤塔吸收反应器释放的尾气中残余的三聚氰胺和未反应的尿素后进入三聚氰胺反应器,同时与加压、加热至10.0 MPa,400 ℃的液氨进入反应塔,在10.0 MPa和380~400℃的条件下,尿素转化为三聚氰胺。
反应尾气在尾气回收塔中用稀甲铵液吸收,产生的浓甲铵液送往尿素合成装置。
从反应塔出来的溶液(大部分是三聚氰胺)与热气氨混合后进一步反应,然后淬冷至180℃,得到含三聚氰胺质量分数为20%一30%的溶液,待压力达到1.5 MPa时去氨汽提塔汽提出大部分的氨,再经过滤、结晶、干燥后得到产品。
Nissan工艺技术属于较早的高压法技术,它吸收了低压法的一些优点,又改良了湿法工艺的缺点,基本上为人们所接受,但日本Nissan公司只限于自己使用该技术。
2)Montedison工艺Montedison工艺是将熔融尿素加压、加热至8.5 MPa和135℃,然后与8.5 MPa,420℃的氨混合后进入三聚氰胺反应器中,在反应压力为8.0 MPa、温度380℃的条件下,尿素在反应器内直接转化为三聚氰胺。
反应器出料减压至2.5 MPa,反应生成的混合物在淬冷塔内被来自吸收塔的甲铵液冷却至160℃,出塔顶的反应尾气经处理后去尿素装置,塔底溶液减压至0.5 MPa进入汽提塔,汽提出的残余NH3和CO2:在吸收塔中被吸收成稀甲铵液,然后返回淬冷塔作为冷却液。
出汽提塔的三聚氰胺溶液被循环母液稀释,经活性炭净化、脱色后过滤、结晶、分离、干燥即得三聚氰胺产品,收率为85%~90%。
离心分离产生的母液经氨回收和废水处理,氨和工艺水重新加以回收利用。
3)DSM工艺DSM工艺是将熔融尿素通过喷嘴喷入反应塔,尾气回收的气氨加压升温后返回反应塔,反应压力为0.7 MPa,反应温度390℃,需使用催化剂。
离开反应塔顶部的气流(含有三聚氰胺,NH3,CO2,少量的副产物及催化剂粉尘)在淬冷塔中经旋流器上部溢流液喷淋,温度由390℃降至126℃,气体再经洗涤塔洗涤后去氨回收系统的吸收塔。
从吸收塔塔顶出来的气氨经加压、升温后返回反应塔,塔底稀甲铵液返回尿素装置。
含三聚氰胺质量分数8%~14%的溶液经旋流器浓缩分离后,在解析塔中用蒸汽汽提出残余的NH3和CO2,然后送混合槽,同时加入经氨回收系统预热的结晶循环母液和助滤剂,使三聚氰胺全部溶解,再加入活性炭脱色,浆液滤去不溶性杂质后在结晶器中结晶。
离心分离得到的晶体经空气干燥、粉碎即得三聚氰胺产品;结晶母液一部分去洗涤塔洗涤反应尾气,其余经氨回收系统加热后加入混合槽。
4)BASF工艺该工艺先将熔融尿素送入贮槽,然后部分进入流化床反应器,其余冷却后去洗涤塔,洗涤循环反应尾气中未反应的尿素和未分离的三聚氰胺。
循环反应尾气(主要是NH3和CO2)经洗涤后加热至400℃进入反应器,雾化尿素并使催化剂流化,尿素在常压、380—400℃和AL2O3催化剂作用下反应生成三聚氰胺,反应所需的热量由熔盐系统提供。
反应气在余热回收系统副产2.3 MPa的蒸汽,其温度降至330℃后进入过滤器过滤副产物结晶和催化剂粉尘,净化气进入结晶器。
用来自尿素洗涤塔140℃循环气急冷,使结晶器温度维持在190—210℃,得到三聚氰胺结晶。
三聚氰胺晶粒经旋风分离器分离,由螺旋输送机送至包装机包装成袋。
出旋风分离器的尾气经尿素洗涤塔后,部分作反应器的流化气,部分作结晶器的冷却气,其余经处理后去尿素装置。
2 、国内技术工艺概括我国是世界上三聚氰胺实际应用技术最全的国家。
我国三聚氰胺生产起步于1958年的天津卫津化工厂,以双氰胺为原料,采用常压法间歇干捕工艺,年产三聚氰胺100 t。
1980年,川化股份有限公司引进荷兰DSM公司12 kt/a低压法生产装置。
20世纪90年代,河南中原大化首家引进意大利欧技公司12.5 kt/a高压法生产装置,此后川化、福建三明、乌石化和重庆建峰相继引进欧技公司高压法生产技术。
1)烨晶科技的低压气相淬冷生产技术进入21世纪,山东海化、江苏化工设计院和北京清大华业(烨晶科技)联合开发了与BASF公司流程相似的低压气相淬冷法生产工艺,并建成12 kt/a装置,其主要应用企业有山东魁星、南京金陵石化、山西丰荷、四川化工、河南骏化等,目前已成功开发出30 kt/a和50 kt/a装置技术。
最近几年,烨晶科技开发的低压气相淬冷生产技术不断改进,在装置规模扩大、能耗降低、投资减少方面都取得了明显成效,受到国内越来越多用户的欢迎,成为国内低压法生产三聚氰胺的热门技术。
低压气相淬冷法的工艺过程为:熔融尿液由尿液泵送往三聚氰胺反应器,使用雾化气喷入第1组熔盐盘管上方,反应后的混合气从反应器顶部排出,被引入热气冷却器管内,换热后热气温度下降,气相中的脱氨产物由于温度降低而发生凝聚。
出热气冷却器的混合气经热气过滤器除去脱氨产物和催化剂碎粒等机械杂质后,从结晶器顶部进入,在结晶器内与来自尿液洗涤塔的部分冷气混合,温度继续下降,在此条件下三聚氰胺结晶析出。
三聚氰胺结晶随气流进人旋风分离器,分离出的三聚氰胺晶体从底部排料口经螺旋输送机送出,用气流送往包装系统。
从旋风分离器顶排出的含NH3和CO2的气流送往尿液洗涤塔,从洗涤塔引出的气体部分经载气压缩机加压后送往反应器作载气,部分送至结晶器作冷却气,其余送尾气处理装置。
2)玖源科技开发的低压生产技术玖源化工引进美国氰胺公司转让装置,该装置美国氰胺公司上世纪七十年代DSM 技术的一套二手装置建厂,于1971 年建成投产,2004 年工厂因非技术和设备原因停产关闭。
该装置生产正常运行历时33年,原设计生产能力96t/d(3.168 万t/d)。
装置投产后,经过几次重大技术改造,使装置保持了设备完好性和技术先进性,生产能力也达到113.5 t/d(3.86 万t/d)。
该装置虽然最初建厂时间为上世纪七十年代,但厂方不断进行技术改造,从美方提供的资料看,无论其工艺技术、原料消耗、产品质量均处于国际领先水平。
在我国现有同类装置中具有技术先进、能耗低、无污染、产品质量高的优势。
产品质量稳定,纯度可达99.99%。
玖源科技三聚氰胺技术利用原有引进装置,在原DSM气相反应和液相淬冷工艺的基础上,通过优化工艺参数、缩短工艺流程、改变分离净化方式等措施,达到节约能源、降低消耗的目的。
玖源科技三聚氰胺工艺是将熔融尿素通过喷嘴喷入三聚氰胺反应器,反应器是流化床反应器,操作压力为0.7MPa(表压),反应温度390℃,使用微球状Si-Al氧化物作为催化剂,催化剂在载气——氨的作用下,在反应器内上下流动。
反应后的混合气(含有三聚氰胺及脱氨产物,NH3,CO2,少量的副产物及催化剂粉尘)从反应器顶部排出,加入约77℃冷氨气与反应气体混合,将反应气体温度降至约360℃左右,使脱氨产物几乎全部结晶而三聚氰胺只有极少量的结晶,降温后的反应气体夹带着催化剂颗粒和脱氨产物结晶进入热气过滤器。
过滤后的反应气体进入结晶器,与循环风机送来的温度为200~220℃的循环气体混合后,温度降至约300℃。
氨和二氧化碳气体以及结晶的三聚氰胺一起从结晶器底部流出,利用流体自身的动能输送到旋风分离器中。
旋风分离器将大部分的粒度较大的三聚氰胺分离下来,依靠重力作用进入三聚氰胺接收槽;较小的三胺颗粒随着气流从旋风分离器顶部流出,进入袋式过滤器。
在此条件下三聚氰胺结晶析出。
三聚氰胺结晶随气流进入旋风分离器。
经旋风和袋滤器分离的三聚氰胺经过接收槽、三胺减压槽、脱气槽。
经过脱气处理的三聚氰胺颗粒经过一台成品冷却器,将产品冷却到60℃以下。
三聚氰胺晶体从底部排料口经螺旋输送机送出,用气流送往包装系统。
3)间歇法以尿素为原料,以氨为载气、硅胶为催化剂,在常压和380-400℃的温度下,催化缩合成三聚氰胺。
间歇法工艺过程分为粗制工段和精制工段两部分,粗制工段工艺过程为:已脱除二氧化碳的干燥氨气,经氨预热器加热后送入流化床底部,通过弯形管预分布,再经分布板上锥形泡罩的缝隙均匀吹入床内,使床内催化剂呈流化态。
原料尿素经计量过筛后以压缩空气压送至尿素罐,通过加料管用稍高于床内压力的冷氨气,定量地吹入流化床内进行反应。
反应生成的三聚氰胺和副产物由进床氨气携带,经旋风分离器回收夹带的部分硅胶催化剂后进入热气过滤器,滤除硅胶细粉和副产物,再经干捕器降温,三聚氰胺凝华为固体粉末,沉降在干捕器底部。
定期出料,即为三聚氰胺粗品,作为精制原料。
已分离出三聚氰胺的循环气体经洗塔除二氧化碳并降温除湿、干燥,再经氨压缩机升压后导至氨气柜。
洗塔底部碳铵含量达规定浓度时,送碳铵贮槽。
精制工段工艺过程为:将已计量的粗品三聚氰胺投入加好母液的溶解槽中,加热溶解,调节好溶液温度和PH值,趁热过滤,滤液导入结晶槽冷却结晶,经离心机脱水后,送去干燥,最后粉碎即得精制三聚氰胺。
二、工艺技术方案的比较以尿素为原料生产三聚氰胺的技术路线有多种,拥有专利技术和专有技术的公司也有多家。
目前各种三聚氰胺生产工艺技术的开发都向着规模大、能耗低和环境污染少的方向发展,国内三聚氰胺技术也有较大的突破,在激烈的竞争中,三聚氰胺生产技术将快速发展,生产技术日臻成熟。