催化裂化生产中的常见问题200904讲解
催化裂化催化剂失活原因
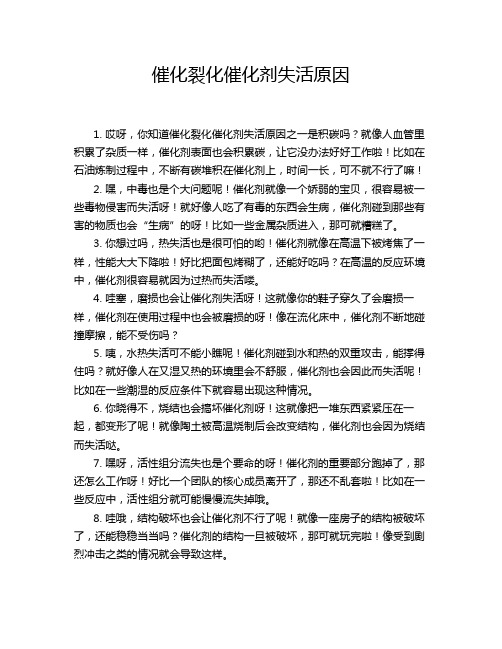
催化裂化催化剂失活原因1. 哎呀,你知道催化裂化催化剂失活原因之一是积碳吗?就像人血管里积累了杂质一样,催化剂表面也会积累碳,让它没办法好好工作啦!比如在石油炼制过程中,不断有碳堆积在催化剂上,时间一长,可不就不行了嘛!2. 嘿,中毒也是个大问题呢!催化剂就像一个娇弱的宝贝,很容易被一些毒物侵害而失活呀!就好像人吃了有毒的东西会生病,催化剂碰到那些有害的物质也会“生病”的呀!比如一些金属杂质进入,那可就糟糕了。
3. 你想过吗,热失活也是很可怕的哟!催化剂就像在高温下被烤焦了一样,性能大大下降啦!好比把面包烤糊了,还能好吃吗?在高温的反应环境中,催化剂很容易就因为过热而失活喽。
4. 哇塞,磨损也会让催化剂失活呀!这就像你的鞋子穿久了会磨损一样,催化剂在使用过程中也会被磨损的呀!像在流化床中,催化剂不断地碰撞摩擦,能不受伤吗?5. 咦,水热失活可不能小瞧呢!催化剂碰到水和热的双重攻击,能撑得住吗?就好像人在又湿又热的环境里会不舒服,催化剂也会因此而失活呢!比如在一些潮湿的反应条件下就容易出现这种情况。
6. 你晓得不,烧结也会搞坏催化剂呀!这就像把一堆东西紧紧压在一起,都变形了呢!就像陶土被高温烧制后会改变结构,催化剂也会因为烧结而失活哒。
7. 嘿呀,活性组分流失也是个要命的呀!催化剂的重要部分跑掉了,那还怎么工作呀!好比一个团队的核心成员离开了,那还不乱套啦!比如在一些反应中,活性组分就可能慢慢流失掉哦。
8. 哇哦,结构破坏也会让催化剂不行了呢!就像一座房子的结构被破坏了,还能稳稳当当吗?催化剂的结构一旦被破坏,那可就玩完啦!像受到剧烈冲击之类的情况就会导致这样。
9. 哎呀呀,堵塞也会让催化剂失效呀!这就像血管被堵住了一样,反应都没法正常进行啦!比如一些杂质把催化剂的孔道堵住了,那可就糟糕透顶了。
10. 哼,老化也是不可避免的呀!催化剂就像人会慢慢变老一样,性能也会逐渐衰退呢!时间长了,它自然就没那么好用啦!这可真是没办法的事呀!我的观点结论就是:催化裂化催化剂失活的原因有很多,我们得重视这些问题,想办法去解决,不然会影响生产效率和质量的呀!。
催化裂化非正常操作及事故处理

催化裂化非正常操作及事故处理㈠流量不足,输出压力不够的原因及处理:1.入口管线,过滤网,叶轮堵塞凝结,切换泵,清扫检修.2.入口阀未开或开度过小,阀板掉等,切换泵,并配合切换流程处理.3.入口管线及泵体内有气体,泵出口放空阀排气.4.泵体及入口管线有漏气处.5.叶轮损坏或装反,切换检修.6.电机反转,切换泵,联系电工处理.7.吸入高度不够,提高液面或入口升压.8.油品温度低,粘度大,提高温度,降低粘度.9.口环磨损或内壳体各部间隙大,切换泵检修.㈡泵抽空不上量的原因及处理1.塔底,罐底液面过低或抽空,联系有关岗位处理液面,关泵出口阀憋压.2.切换流程时冷油进入泵体,联系有关岗位处理流程,关出口阀憋压.3.扫线蒸汽不严,蒸汽串入泵体,联系有关岗位检查各吹扫蒸汽阀是否关严.4.泵予热不当,排尽泵体水,汽及冷油,缓慢予热.5.油品中含水量大,过热汽化,联系有关岗位处理脱水.6.油品中轻油组分含量高,入泵后产生气阻,联系有关岗位调整工艺条件,检查工艺流程.7.塔201底油浆温度过低,联系分馏岗位,提高塔底温度.8.汽油,柴油,液态烃温度高,泵体喷淋水降温,联系有关岗位降温.9.汽油泵,液态烃泵入口压力下降,联系提高入口压力,憋压.10.泵内抽进杂物或入口堵塞,切换泵检修.11.端面密封安装不好,或动环静环磨损,向泵内串水,切换泵检修.12.打封量不合格,量大,适当降低封油量.13.泵入口阀开度小,泵壳压力太小,开大泵入口阀.14.泵入口管线,设备阀门漏,联系配合有关岗位处理,切换泵等.15.机泵故障,切换泵检修.㈢电机超负荷,发热爱有原因及处理1.循环量过大,泵出入口管连通阀和备用泵出口阀开度大,关小连通阀和备用泵出口阀.2.油品粘度过大,联系调节油温.3.机泵打水时,流量过大,适当关小出口阀,降流量.4.电机反转,切换泵,联系电工调整电路.5.叶轮中有杂物,切换泵,抢修,清洗杂物.6.电机与泵轴不同心,切换泵,重新找正.7.转子磨擦,口环磨损,切换泵抢修.8.轴承损坏切换泵,抢修.9.盘根压得过紧,机油无法润滑,适当松动盘根压盖.10.电压过大,过小,联系电工查找原因.11.电机故障,如电机受潮,定子绝缘不不良,三相电路断相,切换泵联系电工处理.㈣轴承发热的原因与处理1.泵轴与机轴线不对或震动,切换泵,重新找正.2.润滑脂,润滑油量少,注意油或切换泵,清洗轴承,润滑脂压温盒.3.润滑脂变质,润滑油乳化,含杂质等,切换泵,换油脂,清洗轴承.4.冷却水中断或不足,调节冷却水量.5.油环脱落,油环运行不正常,切换泵调整.6.电机负荷过大,电机发热,查找原因处理.㈤轴封泄漏过多的原因与处理1.泵抽空,使弹簧不能压紧,端面密封泄漏,切换泵.2.端面密封中有催化剂,使动环,静环磨损,联系降低油浆固含量,切换泵检修.3.预热不当,重油粘在弹簧上,伸缩受影响,使端面密封泄漏,预热好后,才能启动泵,可联系钳工处理,必要时切换泵处理.4.端面密封材料不合格,装配质量不好,切换泵处理.5.转子不平衡,震动剧烈,切换泵检修.6.中心线偏斜,切换泵找正.7.轴或轴套磨损,切换泵检修.8.轴弯曲,切换泵检修.9.盘根箱填料磨损,停泵,更换填料.10.盘根箱填料函盖不正,调整或切换泵检修.11.冷却,润滑不好,调整冷却水量和封油量.12.轴或轴套与盘根底套间隙过大,致使盘根被挤进泵内,切换泵检修.㈥机泵抱轴的原因与处理1.轴承缺油,造成温度高.2.轴承箱缺冷却水,造成温度高.3.轴承损坏,摩擦发热,温度高. 处理方法:切换泵抢修. ㈦泵振动或有噪音的原因与处理1.泵抽空,不上量,联系调整,必要时切换.2.地脚螺栓松动,紧固.3.泵实际流量远远小于设计流量,调大流量.4.叶轮中有异物或叶轮松动,切换泵,检修.5.泵与电机同心度有偏差,切换泵检修.6.轴承磨损后间隙增大或串轴,抱轴,切换泵检修.7.泵体或来液管内有气体,排除气体.8.吸入压力与耗油蒸汽压力相近,提高来油压力.9.轴弯曲或转子不平衡,切换泵检修.10.转子与定子产生摩擦,切换泵检修.11.泵体过热,查找原因处理.㈧电机起动不起来的原因与处理1.电压过低,联系电工查找原因.2.电路不通或接触不良,联系电工处理.3.电机负荷过大,查找原因处理.4.泵体内有异物卡住或安装不当,联系钳工处理.5.开关失灵,按钮不好用,熔断器的熔件烧断,联系电工处理.。
综述催化裂化装置机组故障处理措施

综述催化裂化装置机组故障处理措施摘要: 催化裂化装置机组由于装置生产工况的变化,机组运行状况不很理想,故障发生频繁。
通过采用新技术、新工艺,不断优化机组的运行状况,保证了机组的安全平稳运行。
本文结合实际主要针对重油催化裂化装置锅炉给水泵循环线气蚀故障处理,烟气轮机故障处理,提高富气压缩机入口压力,等提出相应处理措施。
关键词: 催化裂化装置锅炉给水泵烟气轮机故障富气压缩机处理措施一、催化裂化装置锅炉给水泵循环线气蚀原因分析及措施1 装置简介陕西延长石油永坪炼油厂二套催化裂化车间于2004年4月建成投产,加工能力为120万吨/年。
2 故障现象分析2. 1 故障现象。
二套催化裂化装置锅炉给水泵P2501,由除氧器( V2506)抽出除氧水分别向三路供水:余热锅炉B2501、外取热汽包V2401和中压锅炉V2502。
因为余热锅炉的热源是装置余热,其负荷经常变化。
因此,2009 年6月,将P2501 出口DN50 mm 循环线改为DN80 mm 循环线,将部分除氧水返回V2506。
这样,通过调节循环线阀门开度,可调节P2501 出口压力和余热锅炉供水量。
①2009 年 5 月,改造前P2501 为DN50 mm循环线,循环线阀门出现过节流冲刷阀板磨损造成阀门内漏的情况,但阀板没有穿孔; ②改造后的2009 年6 月至2010 年5 月,P2501 先后2 道循环线阀门出现节流冲刷,造成阀板磨损内漏严重,无法起到节流调节作用,影响向余热锅炉正常供水。
③2010 年6月装置检修更换循环线 2 道阀门,检查发现阀门阀板节流处磨损不严重,但阀板中心穿孔; 参照2009年 6 月改造前DN50 mm 循环线阀门磨损的经验,当时怀疑阀门质量有问题,更换阀门; ④2011 年6月循环线上节流阀门再次出现阀门内漏,更换时发现阀门阀板中心再次穿孔。
由此可见,改造后循环线阀门故障问题与改造前不同,应认真分析,彻底处理,以便解决问题。
催化裂化油浆结焦原因及对策

催化裂化油浆结焦原因及对策标签:催化裂化;油浆结焦;解决对策在我国炼油厂的催化裂化过程当中,油浆系统当中产生的结焦结垢问题直接影响到了催化裂化设备的正常工作,主要是因为产生大量的结焦结垢物质,直接降低了热换器的热转化效率,同时提高了管道当中材料输送的阻力,进而造成了蜡油渣油的热转换效率降低。
系统内部产生的蒸汽量减少,同时整个反应设备在工作过程当中的能源消耗量加大,油浆当中多余的热量无法及时被排除,进而造成了整个反应系统内部的热平衡性下降,严重的情况下还直接造成油浆输送系统堵塞,进而影响到了整个生产过程的正常进行。
在最近几年发展过程当中,我国炼油厂的催化裂化原材料质量都不是非常理想,外加上在加油的催化裂化技术方面一直是难以攻克的难题。
因此,催化裂化油浆结焦和结垢的问题受到了各大化工企业的广泛关注,必须要采取相应的解决措施来解决这一问题。
1.催化裂化油浆结焦问题分析1.1温度问题的影响从催化裂化的整个反应过程中可以看出,该反应过程中会受到温度的影响,在相同的催化设备当中分馏塔的底部温度越高,那么出现的结焦现象就越明显。
针对己经产生结焦问题来讲,随着温度不断提高整个反应过程的结焦问题就更加明显,就在模拟FCC油浆的结焦单元当中所得出的结论非常明显。
1.2氧含量的影响通过模拟实验分析了FCC油浆当中产生结焦单元的具体原因,通过向试管当中通入一定量的空气或者是氧气,可以看出在不同量的空气和氧气掺入的情况下,对结焦问题的影响比较明显,其中如果空气或者氧气的参与量较大,那么结焦的问题就越严重。
由此可以看出氧气含量的多少对结焦问题的影响非常明显。
1.3固体和电效应影响通过实际的生产过程可以看出,在催化裂化反应过程当中,如果增加油浆内部的沉降器和过滤器设备之后,在产生结焦和结垢的问题上有着明显的缓解。
因此,这一现象也可以得到充分的证明,从中可以得出催化裂化反应过程中油浆当中,所存在的固体杂质对结焦问题的影响比较明显。
催化裂化装置关键设备故障分析及对策

催化裂化装置关键设备故障分析及对策天津 300270摘要:催化裂化装置是石油加工工艺中的重要环节之一,同时也是炼油厂中最需要注重安全的场所之一。
在催化裂化装置运行过程中,可能会出现一些故障,这不仅会影响设备的性能和生产质量,还可能会对人员的生命财产造成威胁。
因此,下文将对催化裂化装置的关键设备故障进行详细的介绍和分析,以期提高我们对催化裂化装置的故障了解和维护能力。
关键词:催化裂化装置;关键设备;故障分析;对策;引言:催化裂化装置在石油加工工艺中占据着重要的地位,是炼油厂的关键设备之一。
然而,在其长期运行的过程中,可能会出现各种各样的故障,如催化剂失活、热点堵塞、噪声故障、泄漏故障等,这些故障都会对设备的性能和生产质量产生严重影响,甚至危及人员生命财产安全。
针对这些可能出现的故障,我们需要深入探究其原因和对策,及时制定应对方案。
例如,对于催化剂失活故障,需要重视对催化剂的清洗及维护;对于热点堵塞故障,需要定期对反应器进行清洗,保证设备的正常运行;对于噪声故障,需要加强设备的维护保养和调整;对于泄漏故障,需要进行紧急处理和加强安全防范措施等等。
在日益严格的环保和安全要求下,催化裂化装置的关键设备故障处理显得愈发重要,需要我们对其进行深入探究和分析,从而找到有效的对策方案,保障设备的正常运行,提高生产效率和产品质量。
本文将对催化裂化装置关键设备故障进行详细论述和分析,并提出一系列的对策希望能为行业发展做出一点贡献。
一、催化裂化装置简介催化裂化装置是一种高度技术化的炼油装置,用于将石油或石油产品中的高分子化合物裂解成较小的分子。
它采用一系列反应器、加热器、冷却器、催化剂等设备,通过改变化学反应条件,实现高分子化合物分解与分解产物再结合的反应过程。
在催化裂化装置中,原料石油或石油产品经过预热后,进入到第一反应器中,在高温(600℃-700℃)、低压(0.2-0.3MPa)的反应条件下,遇到催化剂开始反应。
重油催化裂化结焦原因及改进措施

重油催化裂化结焦原因及改进措施重油催化裂化是润滑油加工工艺的一个重要环节,是提高润滑油的质量的关键技术。
在重油催化裂化过程中,结焦是一个常见的问题,会严重降低催化裂化的效率。
重油催化裂化结焦的原因,主要有三个方面:首先,催化剂受污染。
催化剂通常是复合物,容易受到空气、产品成分和其他物质的侵蚀、混入或碳化,受到污染时,催化剂性能会受到严重影响,从而导致结焦。
其次,催化剂不可逆变化。
重油催化裂化温度高,使重油催化剂发生不可逆变化,催化剂的性能也下降,从而导致结焦等问题。
最后,温度控制不当。
重油催化裂化的温度控制是很重要的,太高或太低的温度都会影响催化剂的功能,导致结焦。
为了解决重油催化裂化结焦问题,应采取一些有效的措施。
首先,科学选用催化剂。
重油催化裂化中使用的催化剂一般是催化剂复合物,应根据实际需要科学选择恰当的催化剂,降低催化剂受污染的可能性。
其次,采用稳定性好的催化剂。
重油催化裂化时,要选择温度稳定性较好的催化剂,不变性的催化剂能有效降低结焦的可能性。
再次,做好温度控制。
重油催化裂化时,温度应稳定在一定范围内,太高或太低的温度都会影响催化剂的功能,因此应做好温度控制,以保证重油催化裂化效果。
最后,改善反应条件和催化裂化技术。
采用新型催化剂和剂的组合,改善反应条件,控制反应温度和反应压力,改进催化裂化技术,进一步提高重油催化裂化的效率。
综上所述,重油催化裂化结焦的主要原因是催化剂受污染、催化剂不可逆变化以及温度控制不当。
要改善这种情况,应采取有效的措施,如科学选用催化剂、采用稳定性好的催化剂、做好温度控制、改善反应条件和催化裂化技术等。
只有真正落实这些措施,才能有效防止重油催化裂化结焦,达到质量理想。
催化裂化装置结焦原因分析及对策研究
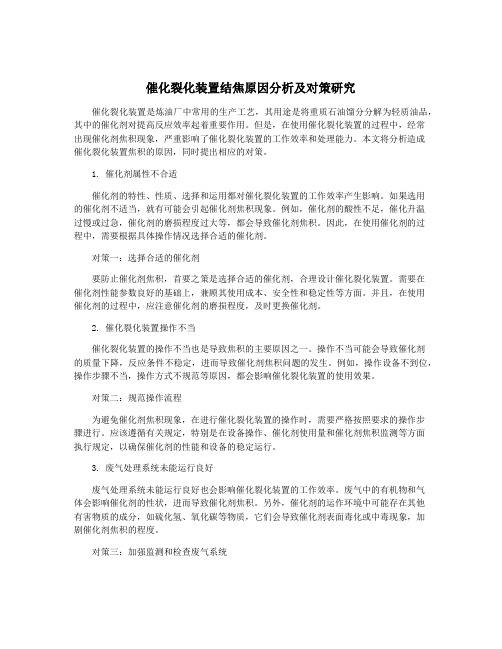
催化裂化装置结焦原因分析及对策研究催化裂化装置是炼油厂中常用的生产工艺,其用途是将重质石油馏分分解为轻质油品,其中的催化剂对提高反应效率起着重要作用。
但是,在使用催化裂化装置的过程中,经常出现催化剂焦积现象,严重影响了催化裂化装置的工作效率和处理能力。
本文将分析造成催化裂化装置焦积的原因,同时提出相应的对策。
1. 催化剂属性不合适催化剂的特性、性质、选择和运用都对催化裂化装置的工作效率产生影响。
如果选用的催化剂不适当,就有可能会引起催化剂焦积现象。
例如,催化剂的酸性不足,催化升温过慢或过急,催化剂的磨损程度过大等,都会导致催化剂焦积。
因此,在使用催化剂的过程中,需要根据具体操作情况选择合适的催化剂。
对策一:选择合适的催化剂要防止催化剂焦积,首要之策是选择合适的催化剂,合理设计催化裂化装置。
需要在催化剂性能参数良好的基础上,兼顾其使用成本、安全性和稳定性等方面。
并且,在使用催化剂的过程中,应注意催化剂的磨损程度,及时更换催化剂。
2. 催化裂化装置操作不当催化裂化装置的操作不当也是导致焦积的主要原因之一。
操作不当可能会导致催化剂的质量下降,反应条件不稳定,进而导致催化剂焦积问题的发生。
例如,操作设备不到位,操作步骤不当,操作方式不规范等原因,都会影响催化裂化装置的使用效果。
对策二:规范操作流程为避免催化剂焦积现象,在进行催化裂化装置的操作时,需要严格按照要求的操作步骤进行。
应该遵循有关规定,特别是在设备操作、催化剂使用量和催化剂焦积监测等方面执行规定,以确保催化剂的性能和设备的稳定运行。
3. 废气处理系统未能运行良好废气处理系统未能运行良好也会影响催化裂化装置的工作效率。
废气中的有机物和气体会影响催化剂的性状,进而导致催化剂焦积。
另外,催化剂的运作环境中可能存在其他有害物质的成分,如硫化氢、氧化碳等物质,它们会导致催化剂表面毒化或中毒现象,加剧催化剂焦积的程度。
对策三:加强监测和检查废气系统为避免催化剂焦积现象的发生,需要严格监测和检查废气系统,确保其正常运行。
催化裂化装置结焦原因分析及对策研究

催化裂化装置结焦原因分析及对策研究催化裂化装置是炼油厂的关键设备之一,其作用是将重质石油馏分分解成轻质产品,包括汽油、柴油和液化石油气等。
由于操作不当或设备故障等原因,催化裂化装置很容易出现结焦现象,严重影响生产效率和产品质量。
对催化裂化装置结焦原因进行分析,并制定相应的对策,对于炼油厂的稳定运行和产品质量具有重要意义。
1. 温度控制不当催化裂化装置工作温度的控制是避免结焦的关键因素之一。
如果温度过高,容易导致催化剂在装置中的积炭过多,从而引发结焦现象。
温度过低也会使催化剂在反应过程中不能充分活化,同样容易导致结焦。
保持合适的工作温度是避免结焦的重要手段。
2. 催化剂质量不良催化裂化装置中使用的催化剂质量的好坏直接影响装置的运行情况。
如果催化剂中存在杂质或者受到空气污染,会导致催化剂的活性降低,从而影响反应的进行,最终导致结焦。
3. 操作人员不当操作催化裂化装置是复杂的设备,需要操作人员具备一定的专业知识和技能。
如果操作人员不当操作,比如在设备运行时不按规定添加催化剂,或者不及时清理催化剂床中的积炭,都会加重结焦的程度。
4. 设备故障设备故障是导致催化裂化装置结焦的另一重要原因。
比如设备堵塞、管道泄漏等故障,都会导致催化剂无法正常流动或者反应不能顺利进行,最终导致结焦。
二、催化裂化装置结焦对策研究为了避免催化裂化装置结焦,首先需要严格控制工作温度。
可以通过安装温度传感器和控制系统,不断监测和调节催化裂化装置的工作温度,保证其在安全范围内稳定运行。
选择高质量的催化剂是避免催化裂化装置结焦的重要措施。
可以通过提高催化剂的制备工艺、严格控制原料质量和加强催化剂检测等手段,提高催化剂的活性和稳定性。
催化裂化装置的操作人员需要接受系统的培训,掌握装置的结构与工作原理,熟悉操作规程,了解可能影响反应的因素,提高操作技能,以减少因操作不当而导致的结焦情况。
4. 定期检查与维护为了预防催化裂化装置结焦,需要定期检查设备的运行情况,发现问题及时处理。
催化裂化装置结焦原因分析及对策研究

催化裂化装置结焦原因分析及对策研究催化裂化装置作为炼油厂重要的催化反应器,在生产中经常发生结焦问题,给生产带来很大的影响,甚至导致设备损坏,因此对催化裂化装置结焦问题进行原因分析,并提出有效的对策十分必要。
1. 催化剂中杂质含量高由于催化剂生产和再生过程中无法完全除去常见的混合杂质和小颗粒杂质,会导致催化剂孔道堵塞,进而造成结焦问题。
2. 反应温度过高在高温条件下,不仅会加速化学反应过程,增加产品产量,同时也会增加碳代谢物生成的速度,导致催化剂的失活,反应产物中的重组物、聚合物和部分不饱和烃最终结焦生成焦炭,造成催化裂化装置的结焦问题。
3. 催化剂失活程度高催化剂的失活程度不仅与反应温度有关,还与催化剂寿命、催化剂产地、催化剂再生情况等因素有关。
催化剂失活对于催化裂化反应来说是十分严重的问题,因为失活催化剂难以发挥催化作用,反应会出现明显的减缓,产生结焦现象。
4. 再生效果不好在催化裂化反应中,催化剂在反应过程中会失活,在达到一定的失活程度后需要经过再生,再生后催化剂重新活化,恢复催化作用。
若再生效果不好,催化剂的失活仍没有得到很好的处理,则催化剂对重复使用无力,即使更换了新催化剂也会出现结焦现象,加剧催化裂化装置的结焦情况。
1. 增加催化剂的选择性和活性增加质量优良的催化剂,能够提高催化反应选择性,增加催化剂活性,减少结焦问题。
提高催化裂化装置的控制温度,尽可能减少炉内温度过高,能有效减少产生结焦现象的几率。
应该通过一定的方法来简化操作程序,降低操纵参数之间的变量,精度控制反应温度,以对避免产生大量结焦反应物及焦炭的生成。
3. 催化剂后续处理简单地减少现有催化剂中的杂质含量是不行的,需要加强催化剂的再生和处理过程,从催化剂再生,酸洗处理和干燥等方面入手,能够有效减少催化剂的失活程度,降低结焦发生的绝对值。
4. 悬浮固定床催化剂技术采用悬浮固定床催化剂技术,能有效提高孔道的通透性,获得更高的选率和活性,有选择性地促进催化裂化反应的进行,降低产生结焦现象的几率。
催化裂化危险因素的分析及防范措施

催化裂化危险因素的分析及防范措施催化裂化是一项重要的炼油工艺,它可以将高分子烃分解为低分子烃,从而提高石油产品的价值。
然而,催化裂化过程中存在着一定的危险因素,如果不加以妥善的防范和控制,可能会引起爆炸、火灾等事故,造成严重的人员伤亡和财产损失。
因此,本文将对催化裂化的危险因素进行分析,并提出相应的防范措施。
一、危险因素分析1. 蒸汽泄漏催化裂化工艺中需要使用大量的高温高压蒸汽,如果出现泄漏,会造成严重的安全隐患。
特别是在强风环境下,蒸汽泄漏会进一步扩散,加重事故的后果。
2. 高温、高压催化裂化过程需要维持高温高压的条件,这也是造成事故的主要原因之一。
在高温高压下,烃类物质易燃易爆,容易引起爆炸、火灾等事故。
3. 液态氨泄漏催化裂化工艺中需要使用液态氨作为催化剂,如果出现泄漏,会产生氨气,对人体和环境都有较大的危害。
液态氨的燃点极低,一旦泄漏着火,难以控制,可能导致爆炸事故。
4. 催化剂中毒催化裂化过程中需要使用各种催化剂,这些催化剂一般都含有有毒物质,如氧化铝、氧化硅等。
如果操作不当,易造成催化剂中毒,对人体健康有一定的危害。
5. 电气设备事故催化裂化装置中常常使用大量的电气设备,如果电气设备发生故障、短路等问题,容易引发火灾、爆炸等事故。
二、防范措施1. 加强设备检测和维护设备的检测和维护是防范事故的重要措施之一。
必须定期对设备进行检测和维护,特别是对安全阀、气体检测仪等设备要进行重点检查。
2. 设备安全保护必须加装安全阀、疏水阀、超温保护等设备,确保设备在操作过程中不超载、不渗漏,防止出现过热、过压等危险情况。
3. 对员工进行安全教育必须加强员工的安全意识,确保员工操作规范、操作正确,提高员工对催化裂化工艺的认识和理解,降低事故的风险。
4. 建立应急预案必须建立完善的应急预案和应急机制,对事故进行快速反应和处理,减少事故的损失和影响。
5. 加强安全监控必须加强安全监控,监测温度、压力、液位、气体浓度等参数,及时发现和处理设备异常情况,保证操作的安全性和可靠性。
催化裂化装置长周期运行问题分析及对策

热过热器管束结垢; 6、对于装置存在的隐患制定监护方案。 7、对于装置运行过程中出现的异常情况,按规定第一时间逐级反
应,主管部门组织召开现场专题分析会议,研究问题的性质,确定 采取的方案。
8、公用工程系统出现波动时,装置迅速反应给调度,调度迅速联 系解决,避免因公用工程问题导致装置出现大的波动。
认其运行状态,确认是否需要改进。 7、对运行过程中出现的问题要建立“问题台帐”,运行中
处理不了的,检修期间一并处理,避免出现漏项; 8、做好重点部位的检验工作,把事故消灭在萌芽状态。
装置长周期运行管理方法
装置长周期瓶颈管理:
催化裂化装置长周期运行管理的核心工作就是解决影响装 置长周期运行的瓶颈问题。各个装置问题不同,需要做出不同 的对策。
典型快分VQS
典型反应再生型式
典型反应再生型式
典型反应再生型式
典型反应再生型式
典型反应再生型式
典型反应再生型式
典型反应再生型式
典型反应再生型式
典型反应再生型式
典型反应再生型式
典型反应再生型式
外取热器两段再生
外循环管烧焦罐
高速床串联两段再生
内会造成料腿堵,跑催化剂。 穹顶和沉降器内的结焦,会在温度变化后,
脱落掉入汽提段格栅上,影响待生催化剂的下料。 部分小的焦块掉落在待生滑阀上部会造成催化剂 终止流化,待生管内结焦也会影响催化剂的流化。 2、油气管道结焦:
造成油气管道压降大,使反应器出口至气压 机入口压降增大,影响装置能耗。
结焦对长周期运行的影响
影响催化裂化长周期运行的因素
油浆泵管道结焦
分馏塔底结焦
影响催化裂化长周期运行的因素
催化裂化生产中的常见问题200904
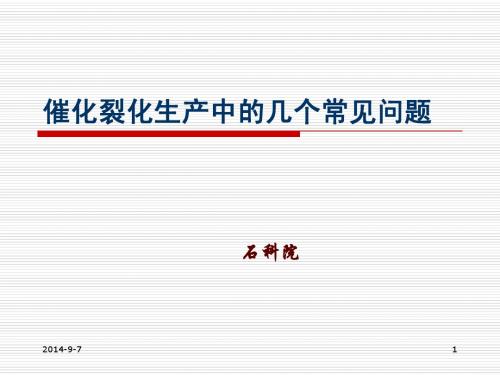
2014-9-7
72
湿法处理再生烟气示意图
2014-9-7
73
EDV技术特点
1、含有催化剂粉尘和SO2的烟气进入喷淋 净化塔,喷淋水由循环泵分多层喷入喷淋 塔内 2、喷淋水含有碱性试剂,如NaOH等。 在喷淋塔内气液逆流或错流接触,烟气被 多层喷淋后,吸收,冷凝,并趋于饱和吸 收
2014-9-7 74
90
RFS的硫平衡工业结果
29
再生器尾燃原因分析
2014-9-7
30
再生器尾燃原因分析
2014-9-7
31
再生器尾燃原因分析
2014-9-7
32
再生器改造前后的效果示意
2014-9-7
33
改造前后的再生稀密相温差
2014-9-7
34
关注—加剂(活性和温度)引起的周期性尾燃
2014-9-7
注:若稀相催化剂密度为15kg/m3,则其热容约为烟气的12倍
1、下行式反应器 2、高反应温度550~650C 3、高剂油比15~25 4、短剂油接触时间0.5S 5、高丙烯17~25%, 汽油高RON99、高芳71%
2014-9-7 53
HS-FCC中试结果
常规FCC 干气 4.6 HSFCC 5.5
丙烯
丁烯 汽油 LCO+HCO 焦炭
2014-9-7
10.7
控制并平稳原料质量:
密度<0.935g/cm3,H>12.0%, UOPK>12.0, CR<7% 加强管理,确保操作平稳
2014-9-7
25
催化裂化的尾燃现象
2014-9-7
26
再生器尾燃原因分析
2014-9-7
催化裂化装置烟道焊缝开裂故障分析及对策

催化裂化装置烟道焊缝开裂故障分析及对策摘要:催化裂化装置中,反应再生单元高温烟道连接再生器、第三旋风分离器(以下简称三旋)、烟气轮机等设备,具有大直径、长跨距、复杂结构特征。
催化裂化装置生产运行中,三旋至烟机入口段高温烟道常发泄漏故障,严重影响装置的安全、平稳、长周期运行。
关键词:催化裂化装置;烟道焊缝;开裂故障;对策1催化裂化装置烟道焊缝开裂故障分析某催化裂化装置三旋出口烟道器壁接管(材质为304H)与虾米腰对接焊缝出现长约1m、宽约6mm裂纹。
采用带压捻缝方式堵漏、补焊后,对泄漏焊缝处进行贴钢板、增加拉筋补强处理。
通过相关研究分析,具体总结出催化裂化装置烟道焊缝开裂故障原因主要有以下相关情况造成。
1.1高温环境下材料出现劣化三旋至烟机入口段烟道工作温度在650~700℃,为了防止衬里块脱落对烟机过流部件造成损害,该段烟道设计为无衬里形式,材质多选用304H或316H。
高温下,300系列不锈钢的晶界滑移和位错会导致材料变形和硬化,金属原子的扩散还会使得材料硬化消除。
在时间、应力与温度的共同作用下,硬化—硬化消除过程交替出现,导致金属内部出现多种析出相,材料宏观性能不断劣化。
此外,温度升高还会使材料的断裂方式发生改变,由穿晶断裂逐渐转变成沿晶断裂。
当管道内部应力高于材料的高温强度极限时,就会导致管道发生开裂。
尤其是当三旋至烟机入口烟道出现多次或严重超温时,就可能在短时间内出现开裂问题。
1.2应力太过于集中相当一部分烟道开裂部位位于烟道与膨胀节对接焊缝处,且裂纹多以近膨胀节铰链板部位为中心。
结构方面,三旋至烟机入口管系竖直段上多采用单式铰链型膨胀节,该类型膨胀节可以吸收与铰链转动方向一致的较大弯曲变形,但对管道轴向变形和与铰链转动方向垂直的弯曲变形,吸收过程容易导致轴向和垂直于铰链转动方向较高水平的拉应力,从而在靠近膨胀节两侧铰链板的焊缝位置产生应力集中。
焊接方面,部分膨胀节的端管(端管壁厚28mm)与烟道母材厚度(烟道壁厚20mm)偏差较大,虽打磨坡口,焊接后仍然存在应力集中。
催化裂化装置运行存在的问题与改造措施分析
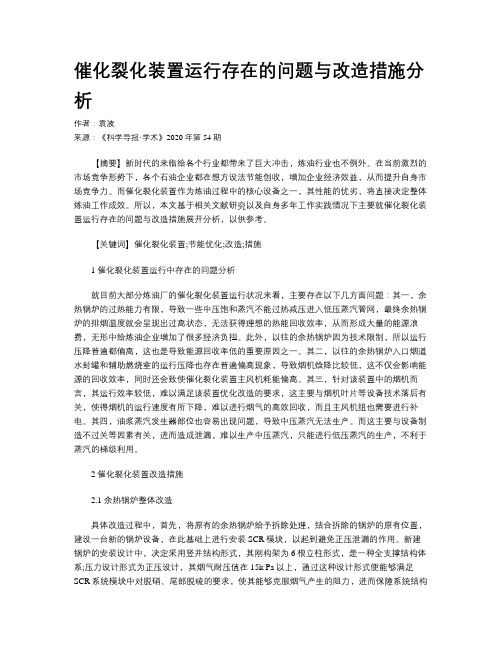
催化裂化装置运行存在的问题与改造措施分析作者:袁波来源:《科学导报·学术》2020年第54期【摘要】新时代的来临给各个行业都带来了巨大冲击,炼油行业也不例外。
在当前激烈的市场竞争形势下,各个石油企业都在想方设法节能创收,增加企业经济效益,从而提升自身市场竞争力。
而催化裂化装置作为炼油过程中的核心设备之一,其性能的优劣,将直接决定整体炼油工作成效。
所以,本文基于相关文献研究以及自身多年工作实践情况下主要就催化裂化装置运行存在的问题与改造措施展开分析,以供参考。
【关键词】催化裂化装置;节能优化;改造;措施1 催化裂化装置运行中存在的问题分析就目前大部分炼油厂的催化裂化装置运行状况来看,主要存在以下几方面问题:其一,余热锅炉的过热能力有限,导致一些中压饱和蒸汽不能过热减压进入低压蒸汽管网,最终余热锅炉的排烟温度就会呈现出过高状态,无法获得理想的热能回收效率,从而形成大量的能源浪费,无形中给炼油企业增加了很多经济负担。
此外,以往的余热锅炉因为技术限制,所以运行压降普遍都偏高,这也是导致能源回收率低的重要原因之一。
其二,以往的余热锅炉入口烟道水封罐和辅助燃烧室的运行压降也存在普遍偏高现象,导致烟机焓降比较低,这不仅会影响能源的回收效率,同时还会致使催化裂化装置主风机耗能偏高。
其三,针对该装置中的烟机而言,其运行效率较低,难以满足该装置优化改造的要求,这主要与烟机叶片等设备技术落后有关,使得烟机的运行速度有所下降,难以进行烟气的高效回收,而且主风机组也需要进行补电。
其四,油浆蒸汽发生器部位也容易出现问题,导致中压蒸汽无法生产。
而这主要与设备制造不过关等因素有关,进而造成泄漏,难以生产中压蒸汽,只能进行低压蒸汽的生产,不利于蒸汽的梯级利用。
2 催化裂化装置改造措施2.1 余热锅炉整体改造具体改造过程中,首先,将原有的余热锅炉给予拆除处理,结合拆除的锅炉的原有位置,建设一台新的锅炉设备,在此基础上进行安装SCR模块,以起到避免正压泄漏的作用。
催化裂化油浆系统运行中的问题及对策

表 3 催化裂化油浆性质
项
目
一套催化
密度 (20 ℃) / kg·m - 3 运动粘度 (80 ℃) / mm2·s - 1 残炭/ % 凝点/ ℃ ω(碳) / % ω(氢) / % 族组成/ % 饱和烃 芳香烃 胶质 + 沥青质 石油醚不溶物
收稿日期 :2000206219 。 作者简介 :刘怀元 ,1991 年毕业于西北大学有机化工专业 ,现
在兰州炼化公司炼油一厂技术科从事催化裂化装置的管理工 作 ,发表论文 2 篇 。
66
石 油 炼 制 与 化 工 2001 年 第 32 卷
表 2 油浆在换热器中的线速度
表 1 油浆在分馏塔底的停留时间
一套催化
重催
项 目
体积/ m3
停留时 间/ min
体积/ m3
停留时 间/ min
液面
5 % 20 % 50 % 80 % 100 % 油浆密度 (20 ℃) /
10. 56 3. 20 20. 73 2. 40 13. 28 4. 00 28. 26 3. 30 18. 72 5. 70 43. 32 5. 10 24. 17 7. 30 58. 38 6. 80 27. 80 8. 40 68. 42 8. 00
摘要 针对影响催化裂化装置油浆系统长周期运行的因素 , 结合兰州炼化公司两套催化裂化 装置在运行过程中出现结焦 、堵塞等问题 , 报道通过改进工艺流程 、优化操作条件如降低分馏塔 层的温度及液面 , 增加油浆换热时的线速 , 及采用油浆阻垢剂等技术 , 可以使油浆系统长周期运 行。
催化裂化油浆系统运行中的问题及对策

催化裂化油浆系统运行中的问题及对策王华琛,曹生伟,王守庆(中原油田石油化工总厂,河南濮阳 457165)摘 要:针对催化裂化油浆系统在满负荷状态运行时出现的问题进行分析,提出了解决问题所采取的对策。
关键词:催化裂化;油浆;冲洗油;结焦中图分类号:TE624.41 文献标识码:B 文章编号:1003-3467(2005)12-0031-02 油浆系统的结焦问题是制约装置长周期运行的主要因素之一,如何保证油浆系统在生产运行中的平稳,避免因结焦堵塞造成装置非计划停工抢修,中原油田石油化工总厂在这方面做了有益地探索,并做了大胆地尝试,取得了较好的效果。
1 概况 中原油田石油化工总厂自2004年9月开工后不久,油浆泵就出现了晃量的趋向,但各换热器压降正常,基本上能满足工艺的需求;但随着运行周期的延长,油浆系统经常地出现问题:塔底温度上涨,各换热器压降增大,取热效果变低,下返分布器堵塞严重等,对这些问题如果处理不当或处理不及时,可能导致油浆系统的瘫痪,被迫停工抢修。
由于工期紧,检修时间短,沉降器、油气大管线、整个油浆系统存在问题没有得到彻底解决。
进料后不久,油浆泵出现晃量,及时倒泵清理油浆泵过滤网,发现有许多大的硬焦块,怀疑沉降器或油气大管线中的松动使焦块被油气带到了泵的入口。
2 结焦堵塞的原因分析 催化裂化反应同时伴随着热裂化反应和过裂化反应,热裂化反应的存在使反应后的油气中含有不饱和双烯烃,经过芳构化,易缩合成多环芳烃,发生生焦反应,反应起始温度100~200℃,而油浆系统中的温度一般都超过200℃;另一方面,提升管出口油气中尚带有部分有一定活性的催化剂,油气还存在一定程度的过裂化反应,最终生成焦炭,部分被带到分馏塔。
多环芳烃属于结焦前身物,而油浆是多环芳烃含量最高的成分。
在高温条件下,多环芳烃、胶质、沥青质脱氢聚合条件成熟,产生一系列芳烃自由基,后者相互结合形成分子量更大的缩合物,直至焦炭。
油浆中各类不饱和烃在高温下,由氧和金属引发催化作用,通过自由基链反应而产生高分子聚合物。
- 1、下载文档前请自行甄别文档内容的完整性,平台不提供额外的编辑、内容补充、找答案等附加服务。
- 2、"仅部分预览"的文档,不可在线预览部分如存在完整性等问题,可反馈申请退款(可完整预览的文档不适用该条件!)。
- 3、如文档侵犯您的权益,请联系客服反馈,我们会尽快为您处理(人工客服工作时间:9:00-18:30)。
2020/2020/8/15
26
再生器尾燃原因分析
2020/8/15
27
再生器尾燃原因分析
2020/8/15
28
再生器尾燃原因分析
2020/8/15
29
再生器尾燃原因分析
催化裂化生产中的几个常见问题
石科院
2020/8/15
1
内容
➢ 减少生焦和避免结焦 ➢ 催化裂化的尾燃现象 ➢ 分馏塔结盐现象 ➢ 催化裂化的其它技术 ➢ 催化裂化的清洁生产技术 ➢ 未来的发展方向
2020/8/15
2
生焦的利与弊
➢ 为反应提供热量 ➢ 为系统提供蒸汽 ➢ 增加能耗 ➢ 增加投资 ➢ 结焦的前提
RxCAT技术
提升管
再生立管
15.6
7.8
722
0.35
+3.8 +4.9 5.46
0.70
2020/8/15
45
UOP的RefCAT技术示意图
技术特点: 1、两个反应器独立 2、公用一个再生器 3、汽油回炼 4、降烯烃,降硫、高液收
2020/8/15
46
UOP的RefCAT技术特点
2020/8/15
5 0
80
22.9
13.6
8.8
6.2
4.6
3.6
2.9
2.4
2
100 120 140 160 180 200 220 240 260
温度,C
2020/8/15
20
避免结焦的措施(2)
适度的预提升线速,2~4m/s、 >300g/cm3
较高的剂油混合温度, > 540 ℃ 缩短油气在沉降器的停留时间,<5s 采用先进的快分技术,VQS、VSS、软连
2020/8/15
5
结焦发生的位置
2020/8/15
6
提升管喷嘴上部结焦
2020/8/15
7
提升管喷嘴上部结焦
2020/8/15
8
提升管喷嘴上部结焦
2020/8/15
9
结焦发生的位置
2020/8/15
10
沉降器VSS密闭旋分外腔
浮 焦
2020/8/15
11
催化装置沉降器顶结焦
2020/8/15
47
UOP的MSCC的结构示意图
2020/8/15
48
UOP的MSCC的结构示意图
2020/8/15
35
分馏塔结盐分析
分馏塔结盐--现象
分馏塔压降增加,增值达 20~40kpa
柴油抽不出来,冲塔 塔顶温度难以控制,无法正常操作 产品不合格
37
分馏塔结盐—原因(1)
原料中有 Cl,N化物的存在 Cl 的盐水解生成HCl N化物在FCC条件下生成NH3 NH3和HCl在低温部位生成NH4Cl
38
分馏塔结盐--原因(2)
通常分离塔顶条件下,水的露点在 90℃以上,而顶回流返塔温度较低 ~80℃ ,形成局部析水,溶盐
NH4Cl溶于水,并随水向下流动 随温度升高,脱水,析盐,堵塞降液
管和塔盘
39
分馏塔结盐—处理(水洗)
40
分馏塔结盐—处理(水洗)
进料量以维持操作为准,分馏塔底液面由油浆 外甩量控制
40~80
>80
含量 (%)
16.4
54.7
9.0
19.9
2020/8/15
19
避免结焦的措施(1)
采用高效雾化喷嘴, KH, LPC, BWJ……
小喷嘴,对称安装 足够的雾化蒸汽量,>5% 适度的预热温度,<5mm2/s,预热温度>200℃
粘度,mm2/s
50 45 44 40 35 30 25 20 15 10
接……
2020/8/15
21
避免结焦的措施(3)
足够的防焦蒸汽,不留死区、死角 开工喷油温度要够, > 530 ℃
最好用蜡油开工,逐步置换 提出口温度不宜过低, > 480 ℃ 提高衬里水平,无热点,避免露点冷凝 提高检修水平,清焦彻底
2020/8/15
22
避免结焦的措施(4)
大油气管线线速35~45m/s 分馏塔底 <350 ℃ 油浆密度<1.1g/cm3 油浆线速 >1.5m/s 用好油浆阻垢剂
特点: ➢提高转化率 ➢增加汽油产率 ➢降低干气产率 ➢在恒定转化率下,降低焦炭 ➢增加再生时间 ➢降低两器循环量 ➢减少烟气排放
2020/8/15
44
UOP的RxCAT与常规FCC的比较
剂油比 再生温度,C
转化率,lv% 汽油,lv% 焦炭,m% 碳差
常规FCC
8.27 718 Base Base 5.62 0.68
2020/8/15
3
减少生焦
➢ 催化剂的重油转化能力 ➢ 催化剂的焦炭选择性 ➢ 催化剂的可汽提性 ➢ 喷嘴的雾化性能 ➢ 雾化、汽提蒸汽用量 ➢ 工艺参数的选择(预热温度、反应温度、反应
时间、操作方式等)
2020/8/15
4
结焦发生的位置
➢ 提升管喷嘴上部 ➢ 反应沉降器空间 ➢ 旋分器的表面 ➢ 汽提段 ➢ 转油线 ➢ 油浆循环系统
2020/8/15
30
再生器尾燃原因分析
2020/8/15
31
再生器尾燃原因分析
2020/8/15
32
再生器改造前后的效果示意
2020/8/15
33
改造前后的再生稀密相温差
2020/8/15
34
关注—加剂(活性和温度)引起的周期性尾燃
2注020:/8/若15稀相催化剂密度为15kg/m3,则其热容约为烟气的12倍
2020/8/15
23
避免结焦的措施(5)
油浆在分馏塔底停留时间 <5min 分馏塔底蒸汽搅拌,+滤焦器 合理使用终止剂,减少二次裂化 选择重油裂化能力强的催化剂,
MA>60/64
2020/8/15
24
避免结焦的措施(6)
平衡剂上的钒含量 <0.8% 钙铁含量 <1.5% 控制并平稳原料质量:
补水和粗汽油构成冷回流,并控制顶温 90~95℃ ,逐步停顶循,粗汽油改污油罐
顶循温度控制 105~115℃ ,排水至油水分离 罐,防止水下流
若柴油带水,应控制水量 水洗水分析至Cl-稳定为止,一般2~5h
41
分馏塔结盐—水洗水中Cl含量变化
42
催化裂化的其它技术
2020/8/15
43
UOP的RxCAT技术
12
结焦发生的位置
2020/8/15
13
结焦发生的位置
2020/8/15
14
汽提段格栅上的大焦块
2020/8/15
15
结焦发生的位置
2020/8/15
16
旋分器锥体外壁结焦
2020/8/15
17
结焦发生的位置
2020/8/15
18
沉降器焦块中催化剂筛分
筛分 数据 (μm)
0~20
20~40