半导体器件设备制作工艺的制作流程
半导体器件的制造工艺

半导体器件的制造工艺半导体器件是现代电子技术中不可或缺的重要组成部分,它们被广泛应用于计算机、通信、医疗、军事等领域。
而半导体器件的核心是芯片,芯片上集成着数亿个晶体管等器件,通过这些器件控制电流,完成信息的处理和传输。
那么,半导体器件的制造工艺是怎样的呢?首先,要制造一颗芯片,首先需要选择适合的半导体材料,例如硅、镓、锗等。
目前,硅是最常用的半导体材料,因为它的物理性质稳定、易于加工,并且具有较好的电学特性。
在材料选择后,需要洁净化处理,为后续的工艺步骤做好准备。
接下来,是制造半导体芯片的关键工艺——沉积。
沉积是指将物质沉积在半导体表面上,用于制造各种器件。
主要有化学气相沉积(CVD)、分子束外延(MBE)等技术。
其中,CVD是最常用的沉积工艺,它通过在高温下将气体分子分解成原子,然后使其在半导体表面沉积,形成一层薄膜。
完成沉积后,需要进行光刻工艺,在芯片表面上覆盖一层光阻,然后利用光刻机将需要制造的器件图形映射到光阻层上,最后使用化学溶液将未被覆盖的部分刻蚀掉,形成器件的图形。
接下来,就是最难的工艺:离子注入。
这一步需要将芯片表面注入所需要的杂质元素,通过控制注入剂量和质量比等参数,改变半导体材料的电学性质。
这一步需要高度精确的控制,因为注入的元素数量一定要精确,否则器件无法正常工作。
完成离子注入后,需要进行电极制作。
这一步需要将金属电极制作在芯片表面,为芯片提供电流。
这个过程非常重要,因为涉及到电极材料与半导体的粘附力、金属材料与半导体的反应性等问题。
注入的杂质元素本身也可以用作电极材料。
最后,进行封装和测试。
封装是将芯片封装在保护性的外壳中,以防止对芯片器件的损伤。
测试是检查芯片工作的正常性和稳定性,通常包括温度测试、电性测量和反复使用测试等。
然而,在制造半导体器件的过程中,还有很多其他的技术问题需要解决,例如微影工艺、微细加工技术、超精密仪器和设备等。
这些都是保证半导体芯片能够得到完美制造的重要技术要素。
半导体制作工艺流程
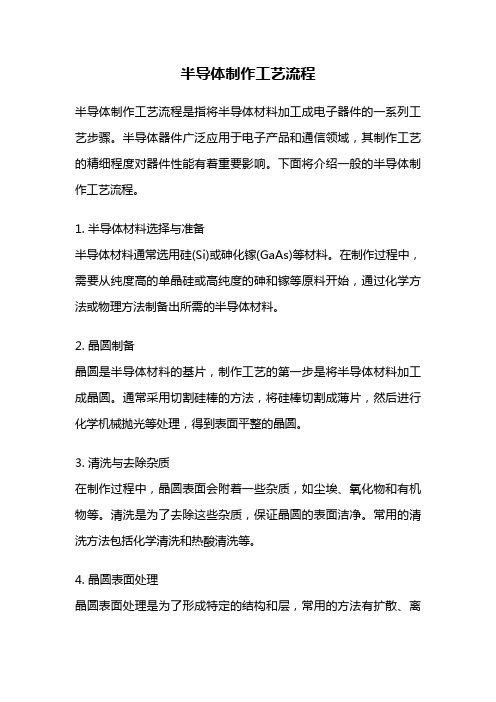
半导体制作工艺流程半导体制作工艺流程是指将半导体材料加工成电子器件的一系列工艺步骤。
半导体器件广泛应用于电子产品和通信领域,其制作工艺的精细程度对器件性能有着重要影响。
下面将介绍一般的半导体制作工艺流程。
1. 半导体材料选择与准备半导体材料通常选用硅(Si)或砷化镓(GaAs)等材料。
在制作过程中,需要从纯度高的单晶硅或高纯度的砷和镓等原料开始,通过化学方法或物理方法制备出所需的半导体材料。
2. 晶圆制备晶圆是半导体材料的基片,制作工艺的第一步是将半导体材料加工成晶圆。
通常采用切割硅棒的方法,将硅棒切割成薄片,然后进行化学机械抛光等处理,得到表面平整的晶圆。
3. 清洗与去除杂质在制作过程中,晶圆表面会附着一些杂质,如尘埃、氧化物和有机物等。
清洗是为了去除这些杂质,保证晶圆的表面洁净。
常用的清洗方法包括化学清洗和热酸清洗等。
4. 晶圆表面处理晶圆表面处理是为了形成特定的结构和层,常用的方法有扩散、离子注入、溅射等。
其中,扩散是通过高温加热将掺杂物扩散到晶圆表面,形成特定的电子掺杂浓度分布;离子注入是将掺杂离子注入晶圆表面,改变其电子性质;溅射是利用高能离子轰击晶圆表面,使其表面原子沉积形成特定结构和层。
5. 光刻与光刻胶光刻是将芯片上的图形投射到光刻胶上,在光刻胶上形成图形。
光刻胶是一种对紫外光敏感的聚合物,通过紫外光照射、显影等步骤,可以形成所需的图形。
6. 离子蚀刻与湿法蚀刻离子蚀刻是利用高能离子轰击晶圆表面,使其表面原子沉积形成特定结构和层。
湿法蚀刻是通过特定的化学液体,将晶圆表面的非遮蔽区域溶解掉,形成所需的结构。
7. 金属沉积与蚀刻金属沉积是将金属沉积在晶圆表面,形成导线、电极等结构。
常用的金属沉积方法有物理气相沉积、化学气相沉积和电镀等。
蚀刻是将多余的金属去除,使得只有所需的结构。
8. 封装与测试半导体器件制作完成后,需要进行封装和测试。
封装是将芯片封装在塑料或陶瓷封装体内,以保护芯片并方便与外部电路连接。
半导体工艺流程简介
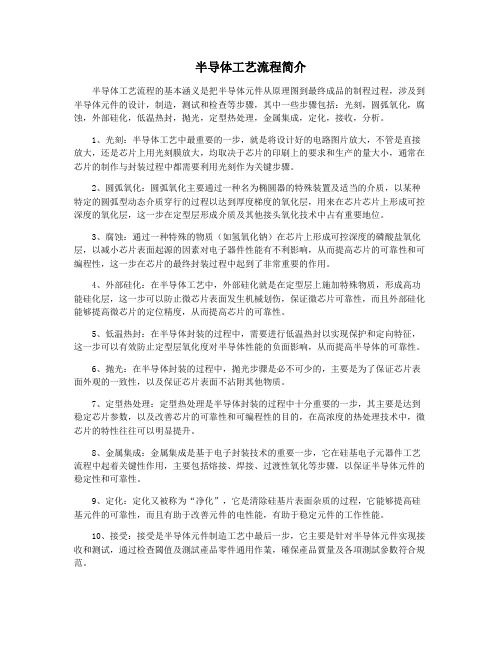
半导体工艺流程简介半导体工艺流程的基本涵义是把半导体元件从原理图到最终成品的制程过程,涉及到半导体元件的设计,制造,测试和检查等步骤,其中一些步骤包括:光刻,圆弧氧化,腐蚀,外部硅化,低温热封,抛光,定型热处理,金属集成,定化,接收,分析。
1、光刻:半导体工艺中最重要的一步,就是将设计好的电路图片放大,不管是直接放大,还是芯片上用光刻膜放大,均取决于芯片的印刷上的要求和生产的量大小,通常在芯片的制作与封装过程中都需要利用光刻作为关键步骤。
2、圆弧氧化:圆弧氧化主要通过一种名为椭圆器的特殊装置及适当的介质,以某种特定的圆弧型动态介质穿行的过程以达到厚度梯度的氧化层,用来在芯片芯片上形成可控深度的氧化层,这一步在定型层形成介质及其他接头氧化技术中占有重要地位。
3、腐蚀:通过一种特殊的物质(如氢氧化钠)在芯片上形成可控深度的磷酸盐氧化层,以减小芯片表面起源的因素对电子器件性能有不利影响,从而提高芯片的可靠性和可编程性,这一步在芯片的最终封装过程中起到了非常重要的作用。
4、外部硅化:在半导体工艺中,外部硅化就是在定型层上施加特殊物质,形成高功能硅化层,这一步可以防止微芯片表面发生机械划伤,保证微芯片可靠性,而且外部硅化能够提高微芯片的定位精度,从而提高芯片的可靠性。
5、低温热封:在半导体封装的过程中,需要进行低温热封以实现保护和定向特征,这一步可以有效防止定型层氧化度对半导体性能的负面影响,从而提高半导体的可靠性。
6、抛光:在半导体封装的过程中,抛光步骤是必不可少的,主要是为了保证芯片表面外观的一致性,以及保证芯片表面不沾附其他物质。
7、定型热处理:定型热处理是半导体封装的过程中十分重要的一步,其主要是达到稳定芯片参数,以及改善芯片的可靠性和可编程性的目的,在高浓度的热处理技术中,微芯片的特性往往可以明显提升。
8、金属集成:金属集成是基于电子封装技术的重要一步,它在硅基电子元器件工艺流程中起着关键性作用,主要包括熔接、焊接、过渡性氧化等步骤,以保证半导体元件的稳定性和可靠性。
半导体制造工艺流程大全
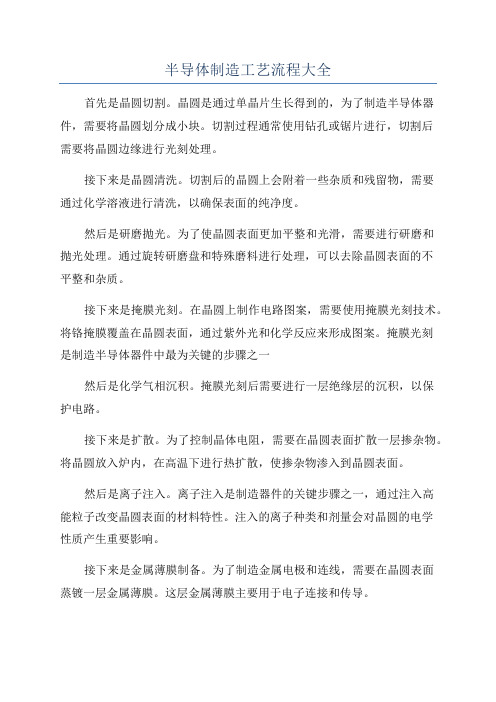
半导体制造工艺流程大全首先是晶圆切割。
晶圆是通过单晶片生长得到的,为了制造半导体器件,需要将晶圆划分成小块。
切割过程通常使用钻孔或锯片进行,切割后需要将晶圆边缘进行光刻处理。
接下来是晶圆清洗。
切割后的晶圆上会附着一些杂质和残留物,需要通过化学溶液进行清洗,以确保表面的纯净度。
然后是研磨抛光。
为了使晶圆表面更加平整和光滑,需要进行研磨和抛光处理。
通过旋转研磨盘和特殊磨料进行处理,可以去除晶圆表面的不平整和杂质。
接下来是掩膜光刻。
在晶圆上制作电路图案,需要使用掩膜光刻技术。
将铬掩膜覆盖在晶圆表面,通过紫外光和化学反应来形成图案。
掩膜光刻是制造半导体器件中最为关键的步骤之一然后是化学气相沉积。
掩膜光刻后需要进行一层绝缘层的沉积,以保护电路。
接下来是扩散。
为了控制晶体电阻,需要在晶圆表面扩散一层掺杂物。
将晶圆放入炉内,在高温下进行热扩散,使掺杂物渗入到晶圆表面。
然后是离子注入。
离子注入是制造器件的关键步骤之一,通过注入高能粒子改变晶圆表面的材料特性。
注入的离子种类和剂量会对晶圆的电学性质产生重要影响。
接下来是金属薄膜制备。
为了制造金属电极和连线,需要在晶圆表面蒸镀一层金属薄膜。
这层金属薄膜主要用于电子连接和传导。
最后是封装测试。
将制造好的晶圆进行封装,以保护器件免受环境和机械损坏。
通过测试和筛选,可以保证器件的质量和性能。
总结以上所述,半导体制造工艺流程包括晶圆切割、晶圆清洗、研磨抛光、掩膜光刻、化学气相沉积、扩散、离子注入、金属薄膜制备等多个关键步骤。
这些步骤不仅要求高度精确和耐心,而且需要高科技设备和专业技能的支持。
半导体制造工艺的不断改进和创新将推动半导体技术的进一步发展和应用。
半导体制造工艺流程

半导体制造工艺流程半导体制造工艺是半导体芯片制造的基础流程,也是一项复杂且精细的工艺。
下面是一份大致的半导体制造工艺流程,仅供参考。
1. 半导体材料的准备:半导体材料通常是硅,需要经过精细的提纯过程,将杂质降低到一定程度,以确保半导体器件的性能。
还需要进行晶体生长、切割和抛光等工艺,以制备出适用于制造芯片的晶片。
2. 晶片清洗和处理:经过前面的准备步骤后,晶片需要进行清洗,以去除表面的杂质和污染物。
清洗包括化学溶液浸泡和超声波清洗等步骤。
之后,通过化学气相沉积等工艺,在晶片上形成氧化层或氮化层,以保护晶片表面。
3. 光刻和光刻胶涂布:在晶片表面涂布一层光刻胶,然后通过光刻机将设计好的芯片图案投射在胶涂层上,形成光刻胶图案。
光刻胶图案将成为制作芯片电路的模板。
4. 蚀刻:将光刻胶图案转移到晶片上,通过干式或湿式蚀刻工艺,将未被光刻胶保护的部分材料去除,形成电路图案。
蚀刻可以通过化学溶液或高能离子束等方式进行。
5. 激光刻蚀:对于一些特殊材料或细微的电路结构,可以使用激光刻蚀来实现更高精度的图案形成。
激光刻蚀可以通过激光束对材料进行精确的去除。
6. 金属薄膜沉积:在晶片表面沉积金属薄膜,以形成电路中的金属导线和连接器。
金属薄膜通常是铝、铜等材料,通过物理气相沉积或化学气相沉积等工艺进行。
7. 金属薄膜刻蚀和清洗:对金属薄膜进行蚀刻和清洗,以去除多余的金属,留下需要的导线和连接器。
8. 测量和测试:对制造好的芯片进行电学性能的测试和测量,以确保其符合设计要求。
9. 封装和封装测试:将芯片封装在外部环境中,通常采用芯片封装材料进行密封,然后进行封装测试,以验证封装后芯片的性能和可靠性。
10. 最终测试:对封装好的芯片进行最终的功能和性能测试,以确保其满足市场需求和客户要求。
以上是半导体制造的基本流程,其中每个步骤都需要高度的精确性和专业技术。
半导体制造工艺的不断改进和创新,是推动半导体技术不断进步和发展的重要驱动力。
半导体制造流程及生产工艺流程
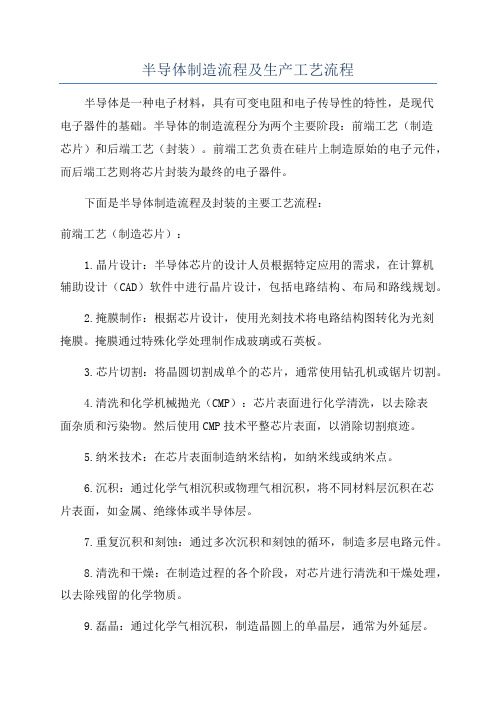
半导体制造流程及生产工艺流程半导体是一种电子材料,具有可变电阻和电子传导性的特性,是现代电子器件的基础。
半导体的制造流程分为两个主要阶段:前端工艺(制造芯片)和后端工艺(封装)。
前端工艺负责在硅片上制造原始的电子元件,而后端工艺则将芯片封装为最终的电子器件。
下面是半导体制造流程及封装的主要工艺流程:前端工艺(制造芯片):1.晶片设计:半导体芯片的设计人员根据特定应用的需求,在计算机辅助设计(CAD)软件中进行晶片设计,包括电路结构、布局和路线规划。
2.掩膜制作:根据芯片设计,使用光刻技术将电路结构图转化为光刻掩膜。
掩膜通过特殊化学处理制作成玻璃或石英板。
3.芯片切割:将晶圆切割成单个的芯片,通常使用钻孔机或锯片切割。
4.清洗和化学机械抛光(CMP):芯片表面进行化学清洗,以去除表面杂质和污染物。
然后使用CMP技术平整芯片表面,以消除切割痕迹。
5.纳米技术:在芯片表面制造纳米结构,如纳米线或纳米点。
6.沉积:通过化学气相沉积或物理气相沉积,将不同材料层沉积在芯片表面,如金属、绝缘体或半导体层。
7.重复沉积和刻蚀:通过多次沉积和刻蚀的循环,制造多层电路元件。
8.清洗和干燥:在制造过程的各个阶段,对芯片进行清洗和干燥处理,以去除残留的化学物质。
9.磊晶:通过化学气相沉积,制造晶圆上的单晶层,通常为外延层。
10.接触制作:通过光刻和金属沉积技术,在芯片表面创建电阻或连接电路。
11.温度处理:在高温下对芯片进行退火和焙烧,以改善电子器件的性能。
12.筛选和测试:对芯片进行电学和物理测试,以确认是否符合规格。
后端工艺(封装):1.芯片粘接:将芯片粘接在支架上,通常使用导电粘合剂。
2.导线焊接:使用焊锡或焊金线将芯片上的引脚和触点连接到封装支架上的焊盘。
3.封装材料:将芯片用封装材料进行保护和隔离。
常见的封装材料有塑料、陶瓷和金属。
4.引脚连接:在封装中添加引脚,以便在电子设备中连接芯片。
5.印刷和测量:在封装上印刷标识和芯片参数,然后测量并确认封装后的器件性能。
半导体器件制造

半导体器件制造半导体器件是现代电子技术的基础,广泛应用于计算机、通讯、医疗、汽车等各个领域。
而半导体器件的制造过程则是一个复杂而精细的工程,需要经过多个步骤才能得到高质量的产品。
本文将介绍半导体器件制造的一般过程,并深入讨论关键步骤和技术。
一、晶圆制备半导体器件的制造从准备晶圆开始,晶圆是一个平坦的硅片,通常直径为12英寸(300毫米)。
首先,选择高纯度的硅单晶材料作为晶圆的基材,然后通过石墨电弧炉等方法进行熔炼和拉晶,将硅材料拉制成使用尺寸。
二、晶圆清洗晶圆经过初步制备后,需要进行清洗以去除表面的杂质和污染物。
清洗流程一般包括多个步骤,如溶剂洗、酸洗、去膜等。
这些步骤可以确保晶圆表面的纯净度和光洁度达到制造要求。
三、光刻光刻是制造半导体器件中的关键步骤之一,通过光刻技术可以在晶圆表面形成所需的微细结构。
首先,在晶圆表面涂覆一层光刻胶,然后使用掩膜和紫外光刻机将光刻胶暴露于紫外光下,形成所需的图案。
随后,通过显影和清洗等工艺步骤,去除多余的光刻胶,形成希望得到的微细结构。
四、离子注入和扩散离子注入和扩散是控制半导体器件电性能的重要工艺步骤。
通过离子注入,将所需的杂质或离子注入晶圆表面,形成导电或绝缘区域。
而通过扩散,则是在高温下使杂质或离子在晶圆内部扩散,改变晶圆的导电性能。
这些步骤的精确控制和调整对于器件性能至关重要。
五、薄膜沉积薄膜沉积是形成半导体器件的关键步骤之一,通过化学气相沉积或物理气相沉积等方法,在晶圆表面沉积一层薄膜材料,用于形成电极、介电层或其他需要的结构。
沉积薄膜的材料种类繁多,如二氧化硅、聚酰亚胺、金属等,其选择和优化可以有效改善器件的性能。
六、金属线路的制作金属线路的制作是连接和布线半导体器件的重要步骤。
通过光刻和薄膜沉积等技术,在晶圆表面形成金属线路的图案,用于实现电子元器件之间的连接。
这些金属线路通常使用铝、铜或其他导电性能良好的材料制作,而且需要考虑线宽、线距、电阻率等因素。
八大半导体工艺顺序剖析

八大半导体工艺顺序剖析八大半导体工艺顺序剖析在现代科技领域中,半导体材料和器件扮演着重要的角色。
作为电子设备的基础和核心组件,半导体工艺是半导体制造过程中不可或缺的环节。
有关八大半导体工艺顺序的剖析将会有助于我们深入了解半导体制造的工作流程。
本文将从简单到复杂,逐步介绍这八大工艺的相关内容。
1. 排版工艺(Photolithography)排版工艺是半导体制造过程中的首要步骤。
它使用光刻技术,将设计好的电路图案转移到硅晶圆上。
排版工艺需要使用光刻胶、掩膜和曝光设备等工具,通过逐层叠加和显影的过程,将电路图案转移到硅晶圆上。
2. 清洗工艺(Cleaning)清洗工艺在排版工艺之后进行,用于去除光刻胶和其他污染物。
清洗工艺可以采用化学溶液或高纯度的溶剂,保证硅晶圆表面的干净和纯净。
3. 高分辨率电子束刻蚀(High-Resolution Electron BeamLithography)高分辨率电子束刻蚀是一种先进的制造技术。
它使用电子束在硅晶圆表面进行刻蚀,以高精度和高分辨率地制作微小的电路图案。
4. 电子束曝光系统(Electron Beam Exposure Systems)电子束曝光系统是用于制造高分辨率电子束刻蚀的设备。
它具有高能量电子束发射器和复杂的控制系统,能够精确控制电子束的位置和强度,实现微米级别的精细曝光。
5. 高能量离子注入(High-Energy Ion Implantation)高能量离子注入是半导体器件制造中的一项重要工艺。
通过将高能量离子注入到硅晶圆表面,可以改变硅晶圆的电学性质,实现电路中的控制和测量。
6. 薄膜制备与沉积(Film Deposition)薄膜制备与沉积是制造半导体器件的关键工艺之一。
这个工艺将薄膜材料沉积在硅晶圆表面,包括化学气相沉积、物理气相沉积和溅射等方法。
这些薄膜能够提供电介质、导电材料或阻挡层等功能。
7. 设备和工艺完善(Equipment and Process Optimization)设备和工艺完善的步骤是优化半导体制造工艺的关键。
半导体制造工艺流程_图文

SiO2 P+
AL
N+ N-epi
P-SUB
Al P+
主要制程介绍
矽晶圓材料(Wafer)
圓晶是制作矽半導體IC所用之矽晶片,狀似圓 形,故稱晶圓。材料是「矽」, IC( Integrated Circuit)厂用的矽晶片即為 矽晶體,因為整片的矽晶片是單一完整的晶體 ,故又稱為單晶體。但在整體固態晶體內,眾 多小晶體的方向不相,則為复晶體(或多晶體 )。生成單晶體或多晶體与晶體生長時的溫度 ,速率与雜質都有關系。
外延层电阻
SiO2
R
N+
R
P+
P
P+
N-epi
P-SUB
集成电路中电阻5
MOS中多晶硅电阻
多晶硅
SiO2氧化层Si源自其它:MOS管电阻集成电路中电容1
SiO2 P+
A-
N+E P+-I
N+-BL P-SUB
B+
A-
B+
N P+ Cjs
发射区扩散层—隔离层—隐埋层扩散层PN电容
集成电路中电容2
N+
後段backend构装packaging测试制程initialtestandfinaltest一晶圆处理制程晶圆处理制程之主要工作为在矽晶圆上制作电路与电子元件如电晶体电容体逻辑闸等为上述各制程中所需技术最复杂且资金投入最多的过程以微处理器microprocessor为例其所需处理步骤可达数百道而其所需加工机台先进且昂贵动辄数千万一台其所需制造环境为为一温度湿度与含尘particle均需控制的无尘室cleanroom虽然详细的处理程序是随著产品种类与所使用的技术有关
半导体制造工艺流程简介
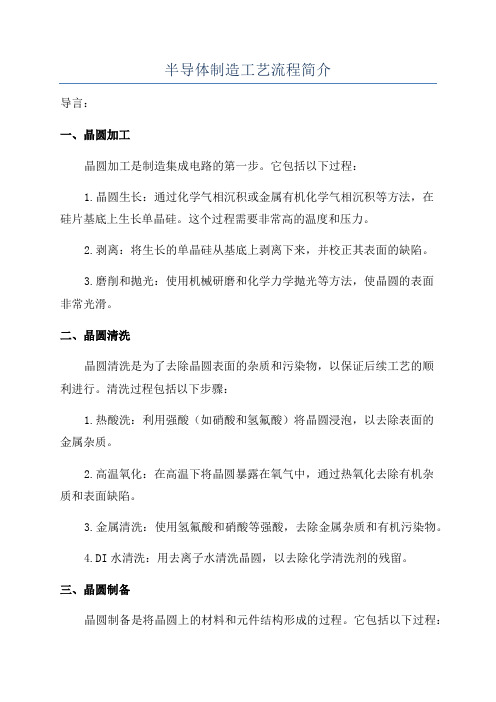
半导体制造工艺流程简介导言:一、晶圆加工晶圆加工是制造集成电路的第一步。
它包括以下过程:1.晶圆生长:通过化学气相沉积或金属有机化学气相沉积等方法,在硅片基底上生长单晶硅。
这个过程需要非常高的温度和压力。
2.剥离:将生长的单晶硅从基底上剥离下来,并校正其表面的缺陷。
3.磨削和抛光:使用机械研磨和化学力学抛光等方法,使晶圆的表面非常光滑。
二、晶圆清洗晶圆清洗是为了去除晶圆表面的杂质和污染物,以保证后续工艺的顺利进行。
清洗过程包括以下步骤:1.热酸洗:利用强酸(如硝酸和氢氟酸)将晶圆浸泡,以去除表面的金属杂质。
2.高温氧化:在高温下将晶圆暴露在氧气中,通过热氧化去除有机杂质和表面缺陷。
3.金属清洗:使用氢氟酸和硝酸等强酸,去除金属杂质和有机污染物。
4.DI水清洗:用去离子水清洗晶圆,以去除化学清洗剂的残留。
三、晶圆制备晶圆制备是将晶圆上的材料和元件结构形成的过程。
它包括以下过程:1.掩膜制作:将光敏材料涂覆在晶圆表面,通过光刻技术进行曝光和显影,形成图案化的光刻胶掩膜。
2.沉积:通过物理气相沉积或化学气相沉积等方法,在晶圆上沉积材料层,如金属、氧化物、硅等。
3.腐蚀:采用湿法或干法腐蚀等技术,去除晶圆上不需要的材料,形成所需的结构。
4.清洗:再次进行一系列清洗步骤,以去除腐蚀产物和掩膜残留物,保证材料层的质量。
四、材料获取材料获取是指在晶圆上制造晶体管、电阻器、电容器等器件结构的过程。
它包括以下步骤:1.掺杂:通过离子注入或扩散等方法,在晶圆上引入有选择性的杂质,以改变材料的导电性或断电性能。
2.退火:通过高温热处理,消除杂质引入过程中的晶格缺陷,并使掺杂的材料达到稳定状态。
3.金属-绝缘体-金属(MIM)沉积:在晶圆上沉积金属、绝缘体和金属三层结构,用于制造电容器。
4.金属-绝缘体(MIS)沉积:在晶圆上沉积金属和绝缘体两层结构,用于制造晶体管的栅极。
五、封装和测试封装是将晶圆上制造的芯片放在封装底座上,并封装成可插入其他设备的集成电路。
半导体器件及其制备方法、存储器及电子设备与流程
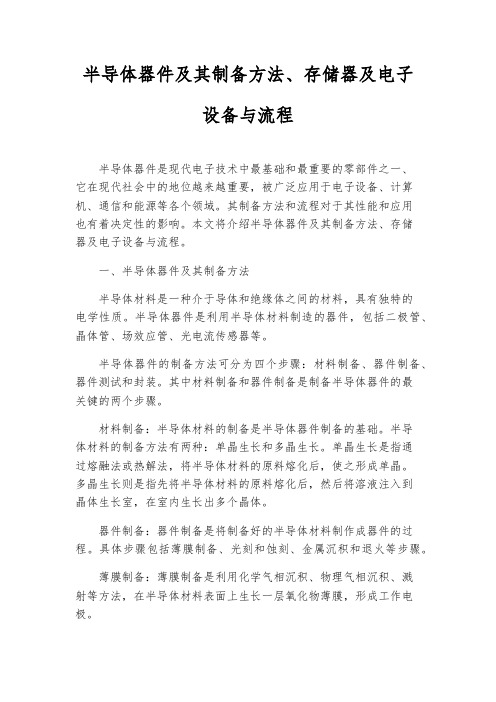
半导体器件及其制备方法、存储器及电子设备与流程半导体器件是现代电子技术中最基础和最重要的零部件之一、它在现代社会中的地位越来越重要,被广泛应用于电子设备、计算机、通信和能源等各个领域。
其制备方法和流程对于其性能和应用也有着决定性的影响。
本文将介绍半导体器件及其制备方法、存储器及电子设备与流程。
一、半导体器件及其制备方法半导体材料是一种介于导体和绝缘体之间的材料,具有独特的电学性质。
半导体器件是利用半导体材料制造的器件,包括二极管、晶体管、场效应管、光电流传感器等。
半导体器件的制备方法可分为四个步骤:材料制备、器件制备、器件测试和封装。
其中材料制备和器件制备是制备半导体器件的最关键的两个步骤。
材料制备:半导体材料的制备是半导体器件制备的基础。
半导体材料的制备方法有两种:单晶生长和多晶生长。
单晶生长是指通过熔融法或热解法,将半导体材料的原料熔化后,使之形成单晶。
多晶生长则是指先将半导体材料的原料熔化后,然后将溶液注入到晶体生长室,在室内生长出多个晶体。
器件制备:器件制备是将制备好的半导体材料制作成器件的过程。
具体步骤包括薄膜制备、光刻和蚀刻、金属沉积和退火等步骤。
薄膜制备:薄膜制备是利用化学气相沉积、物理气相沉积、溅射等方法,在半导体材料表面上生长一层氧化物薄膜,形成工作电极。
光刻和蚀刻:光刻是将半导体材料表面上的氧化层刻写成所需的形状图案。
蚀刻是将光刻后的图案用化学腐蚀法刻在半导体材料表面上。
金属沉积和退火:金属沉积是在制造器件的过程中,将金属沉积在半导体材料上,通过电化学或物理汽相沉积完成。
金属沉积后,需要进行退火,使金属和半导体材料间形成较好的接触。
二、存储器及电子设备随着电子技术的不断发展,存储器和电子设备的重要性越来越突出,已经成为现代社会中不可或缺的一部分。
存储器是一种用于存储电子信息的电子器件,如DRAM、SRAM、FRAM、ROM等;而电子设备则是利用半导体器件制作的各种电子产品,如手机、电视、电脑等。
半导体生产工艺流程

半导体生产工艺流程半导体生产工艺流程半导体是现代电子设备的基础,通过精细加工和控制,在硅、锗、砷化镓等材料上制造出晶体管、集成电路等微小电子器件。
半导体生产工艺流程是一个非常复杂的过程,通常包括以下几个步骤。
首先是材料制备。
半导体材料通常是通过高纯度的硅、锗等原料制备而成。
原料经过多道精细的提纯工艺,去除杂质,使得半导体材料的纯度达到极高的水平。
其次是掩膜工艺。
所谓掩膜工艺,是指在半导体材料表面进行掩膜(Mask)处理,以形成具有特定结构和形状的器件,用于分离、连接和传导电流。
这个工艺是半导体生产中的核心步骤,决定了器件的性能和功能。
然后是光刻工艺。
光刻工艺是利用光刻胶、光罩和紫外光等来制作图案的一种工艺。
通过将光刻胶涂覆在半导体材料表面上,然后使用光刻机来曝光和显影,最终得到所需要的图案。
这个阶段的精度要求非常高,可以制作出微米级以上的图案。
随后是化学气相沉积工艺。
化学气相沉积工艺是一种将气体通过化学反应转化成固体颗粒的工艺。
通过将具有特定功能的化学物质蒸发,使其在半导体表面上形成薄膜。
这个工艺主要用于制备氧化物、金属等材料的膜层,用于提高器件的性能和稳定性。
最后是制程测试和封装工艺。
在半导体生产过程中,需要对器件进行严格的测试和调试来确保其质量和性能。
同时,还需要对器件进行封装,以保护器件免受外界环境的影响,同时方便与其他设备的连接。
以上就是半导体生产工艺流程的大致步骤。
当然,实际的生产过程会更加复杂和精细,并且随着技术的不断进步和创新,生产工艺也在不断演化和改进。
半导体工艺的高精度、高纯度要求使得半导体生产成本较高,但受益于这一产业的规模效应和技术进步,半导体设备的性能越来越高,应用范围也越来越广泛。
半导体制造工艺流程简介
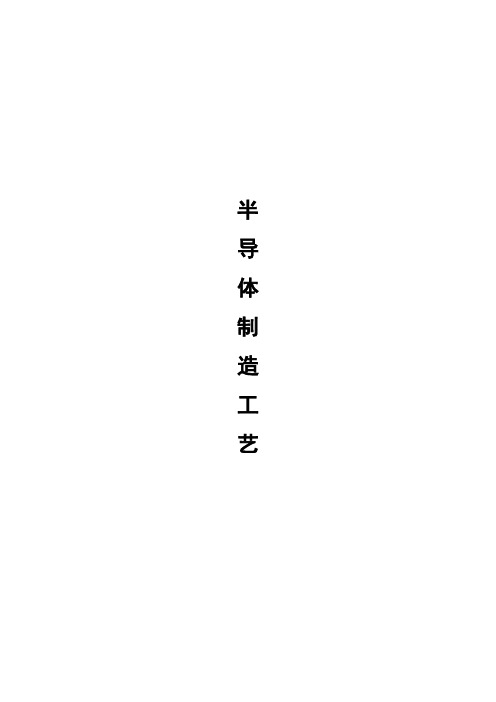
半导体制造工艺NPN高频小功率晶体管制造的工艺流程为:外延片——编批——清洗——水汽氧化——一次光刻——检查——清洗——干氧氧化——硼注入——清洗——UDO淀积——清洗——硼再扩散——二次光刻——检查——单结测试——清洗——干氧氧化——磷注入——清洗——铝下CVD——清洗——发射区再扩散——三次光刻——检查——双结测试——清洗——铝蒸发——四次光刻——检查——氢气合金——正向测试——清洗——铝上CVD——检查——五次光刻——检查——氮气烘焙——检查——中测——中测检查——粘片——减薄——减薄后处理——检查——清洗——背面蒸发——贴膜——划片——检查——裂片——外观检查——综合检查——入中间库。
PNP小功率晶体管制造的工艺流程为:外延片——编批——擦片——前处理——一次氧化——QC检查(tox)——一次光刻——QC检查——前处理——基区CSD涂覆——CSD预淀积——后处理——QC检查(R□)——前处理——基区氧化扩散——QC检查(tox、R□)——二次光刻——QC检查——单结测试——前处理——POCl3预淀积——后处理(P液)——QC检查——前处理——发射区氧化——QC检查(tox)——前处理——发射区再扩散(R□)——前处理——铝下CVD——QC检查(tox、R□)——前处理——HCl氧化——前处理——氢气处理——三次光刻——QC检查——追扩散——双结测试——前处理——铝蒸发——QC检查(t Al)——四次光刻——QC检查——前处理——氮气合金——氮气烘焙——QC检查(ts)——五次光刻——QC检查——大片测试——中测——中测检查(——粘片——减薄——减薄后处理——检查——清洗——背面蒸发——贴膜——划片——检查——裂片——外观检查)——综合检查——入中间库。
GR平面品种(小功率三极管)工艺流程为:编批——擦片——前处理——一次氧化——QC检查(tox)——一次光刻——QC检查——前处理——基区干氧氧化——QC检查(tox)——一GR光刻(不腐蚀)——GR硼注入——湿法去胶——前处理——GR基区扩散——QC检查(Xj、R□)——硼注入——前处理——基区扩散与氧化——QC检查(Xj、tox、R□)——二次光刻——QC检查——单结测试——前处理——发射区干氧氧化——QC检查(tox)——磷注入——前处理——发射区氧化和再扩散——前处理——POCl3预淀积(R□)——后处理——前处理——铝下CVD——QC检查(tox)——前处理——氮气退火——三次光刻——QC检查——双结测试——前处理——铝蒸发——QC检查(t Al)——四次光刻——QC检查——前处理——氮气合金——氮气烘焙——正向测试——五次光刻——QC检查——大片测试——中测编批——中测——中测检查——入中间库。
半导体制程及原理介绍

半导体制程及原理介绍半导体是一种介于导体和绝缘体之间的材料,具有优良的电气特性。
在现代电子技术中,半导体材料被广泛应用于电子器件和集成电路中。
半导体器件的制造过程被称为半导体制程,本文将介绍半导体制程的工艺流程,以及制作半导体器件时涉及到的原理和技术。
半导体工艺流程半导体制程包含多个工序,一般分为六个步骤:1.前工艺:前工艺包含晶圆清洗、分切、抛光和衬底烘烤。
在这一阶段,旨在确保晶圆表面光滑无瑕疵,为后续的工艺提供良好的基础。
2.沉积工艺:沉积工艺主要包括化学气相沉积和物理气相沉积。
这个步骤的主要目的是对晶圆表面进行原子层沉积,形成薄膜,如硅酸盐。
3.光刻工艺:光刻工艺是在晶圆上印刷图案的过程,主要利用紫外光照射。
这个步骤的目的是在晶圆表面添加一层遮光剂,以保护晶圆的某些区域,防止化学腐蚀。
4.蚀刻工艺:蚀刻工艺是“刻蚀”晶圆表面的化学过程,一般利用氢氟酸蚀刻掉不需要的部分。
这个步骤的目的是通过蚀刻去除遮光剂之外的区域,形成所需的结构。
5.离子注入:离子注入工艺是向晶圆表面注入离子,以改变其电学性质。
这个步骤的目的是在特定区域(如接线)注入特定的材料,从而改变半导体的导电性能。
6.后工艺:后工艺包括切割晶圆、清洗、烧结蓝宝石和金属连接。
这个步骤的目的是完成器件的制造过程,并确保器件能够正常工作。
半导体器件的制作原理半导体制程中的制作原理是在半导体材料内部控制杂质浓度,从而控制其导电性能,从而制造高性能的半导体器件。
半导体材料通常分为p型半导体和n型半导体。
p型半导体中掺杂的杂质主要是硼、铝和镓,n型半导体中掺杂的杂质主要是砷、锑和磷。
在p型半导体和n型半导体中,杂质浓度的差异导致了不同的载流子浓度和导电性能。
当p型半导体和n型半导体结合时,形成了PN结构。
在PN结构中存在一个空间电荷区,该区域是导体和绝缘体之间的过渡区域,称为“耗尽层”。
PN结构中的电子可以从n型半导体流向p型半导体,形成电流。
半导体制作工艺流程
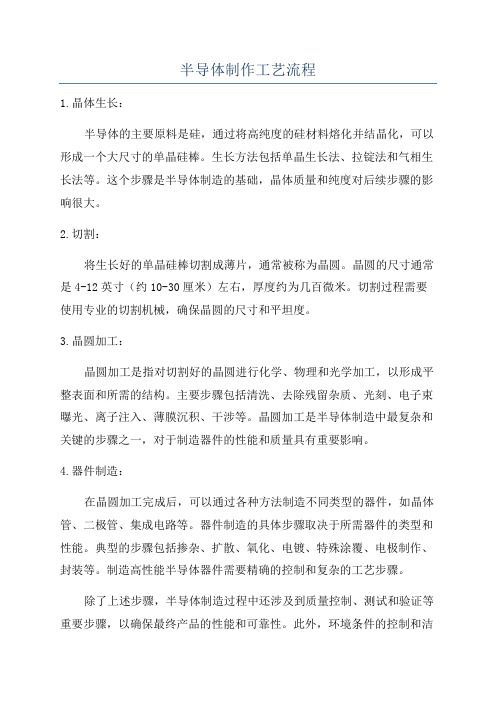
半导体制作工艺流程
1.晶体生长:
半导体的主要原料是硅,通过将高纯度的硅材料熔化并结晶化,可以形成一个大尺寸的单晶硅棒。
生长方法包括单晶生长法、拉锭法和气相生长法等。
这个步骤是半导体制造的基础,晶体质量和纯度对后续步骤的影响很大。
2.切割:
将生长好的单晶硅棒切割成薄片,通常被称为晶圆。
晶圆的尺寸通常是4-12英寸(约10-30厘米)左右,厚度约为几百微米。
切割过程需要使用专业的切割机械,确保晶圆的尺寸和平坦度。
3.晶圆加工:
晶圆加工是指对切割好的晶圆进行化学、物理和光学加工,以形成平整表面和所需的结构。
主要步骤包括清洗、去除残留杂质、光刻、电子束曝光、离子注入、薄膜沉积、干涉等。
晶圆加工是半导体制造中最复杂和关键的步骤之一,对于制造器件的性能和质量具有重要影响。
4.器件制造:
在晶圆加工完成后,可以通过各种方法制造不同类型的器件,如晶体管、二极管、集成电路等。
器件制造的具体步骤取决于所需器件的类型和性能。
典型的步骤包括掺杂、扩散、氧化、电镀、特殊涂覆、电极制作、封装等。
制造高性能半导体器件需要精确的控制和复杂的工艺步骤。
除了上述步骤,半导体制造过程中还涉及到质量控制、测试和验证等重要步骤,以确保最终产品的性能和可靠性。
此外,环境条件的控制和洁
净室技术也是半导体制造工艺的重要组成部分,因为微小的杂质和污染物都可能对器件性能造成影响。
总而言之,半导体的制作工艺流程是一个复杂而精密的过程,需要依靠先进的设备和技术,以确保生产的半导体器件能够满足高性能、高可靠性和高效率的要求。
半导体制程工艺流程

半导体制程工艺流程
半导体制程工艺流程主要包括:芯片清洗、芯片干燥、地址制作、图形制作、芯片表面处理、芯片机械加工、芯片图形结晶、芯片表面
沉积、芯片电性测试、芯片布线制作、芯片表面完善。
首先,芯片清洗是进行制程的第一步,通常采用大规模集成电路(IC)清洗、芯片浸渍、光刻蚀刻等手段对芯片表面进行清洗,以去
除芯片表面油污,为下一步工序做好准备。
其次,芯片干燥采用真空干燥、烘干等方式,确保芯片表面湿度
较低,消除潮气影响,同时进行芯片表面驱动,以降低表面电阻。
接着,地址制作是半导体芯片制程中的一项重要工序,用于对半
导体器件的地址位置进行分配,以确定其相对位置。
然后,图形制作用于在芯片表面制作电路和连接图形,使物理结
构与逻辑电路图吻合。
接下来,芯片表面处理是将芯片表面处理成晶体结构,这样可以
增加半导体器件特性,改善其电气性能。
紧接着,芯片机械加工是将晶片结构切割并完成封装,以确保芯
片表面结构的完整性。
接着,芯片图形结晶是一个通常是室温环境下结晶图形的加工过程,以改善芯片性能。
继而,芯片表面沉积是一个在芯片表面涂覆材料的自动沉积加工
过程,可以改善表面结构,同时增加材料的抗热阻和抗腐蚀性能。
之后,芯片电性测试用于测试芯片的电气特性,确保半导体器件
性能。
然后,芯片布线制作用于将电路板上的元件和焊盘连接起来,实
现器件之间的电子连接。
最后,芯片表面完善是一项加工过程,用于实现芯片表面的保护、平整和光滑的表面,以保证芯片的可靠性。
半导体制作流程
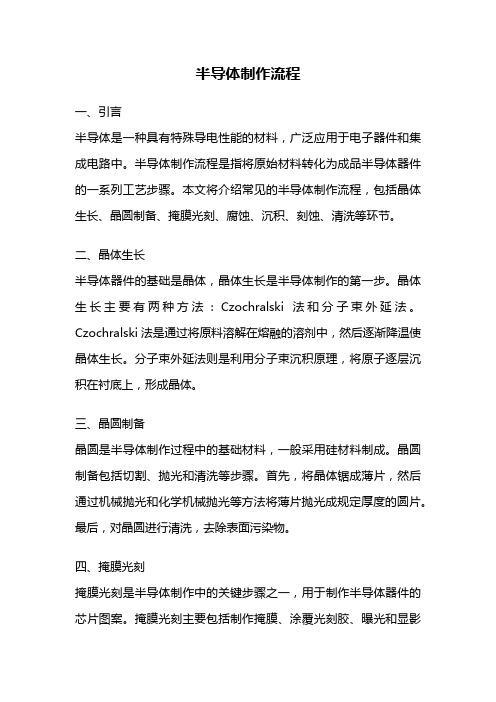
半导体制作流程一、引言半导体是一种具有特殊导电性能的材料,广泛应用于电子器件和集成电路中。
半导体制作流程是指将原始材料转化为成品半导体器件的一系列工艺步骤。
本文将介绍常见的半导体制作流程,包括晶体生长、晶圆制备、掩膜光刻、腐蚀、沉积、刻蚀、清洗等环节。
二、晶体生长半导体器件的基础是晶体,晶体生长是半导体制作的第一步。
晶体生长主要有两种方法:Czochralski法和分子束外延法。
Czochralski法是通过将原料溶解在熔融的溶剂中,然后逐渐降温使晶体生长。
分子束外延法则是利用分子束沉积原理,将原子逐层沉积在衬底上,形成晶体。
三、晶圆制备晶圆是半导体制作过程中的基础材料,一般采用硅材料制成。
晶圆制备包括切割、抛光和清洗等步骤。
首先,将晶体锯成薄片,然后通过机械抛光和化学机械抛光等方法将薄片抛光成规定厚度的圆片。
最后,对晶圆进行清洗,去除表面污染物。
四、掩膜光刻掩膜光刻是半导体制作中的关键步骤之一,用于制作半导体器件的芯片图案。
掩膜光刻主要包括制作掩膜、涂覆光刻胶、曝光和显影等步骤。
首先,制作掩膜,即将芯片图案转移到光刻胶上。
然后,将光刻胶均匀涂覆在晶圆表面。
接着,通过光刻机对光刻胶进行曝光,使其固化形成芯片图案。
最后,通过显影将未固化的光刻胶去除,形成芯片的图案。
五、腐蚀腐蚀是半导体制作中的重要工艺,用于去除不需要的材料。
腐蚀分为湿腐蚀和干腐蚀两种。
湿腐蚀是利用酸性或碱性溶液对晶圆表面进行腐蚀,去除多余材料。
干腐蚀则是利用化学气相沉积的方法,在特定温度和气氛下,使晶圆表面发生化学反应,并去除不需要的材料。
六、沉积沉积是半导体制作中的重要工艺,用于在晶圆表面沉积新的材料。
常见的沉积方法有化学气相沉积和物理气相沉积。
化学气相沉积是通过将气体反应在晶圆表面,使新材料沉积。
物理气相沉积则是通过蒸发、溅射等物理方法将材料沉积在晶圆表面。
七、刻蚀刻蚀是半导体制作中的重要工艺,用于去除不需要的材料。
刻蚀分为湿刻蚀和干刻蚀两种。
先进半导体器件前中后工艺流程

先进半导体器件前中后工艺流程
先进半导体器件的前、中、后工艺流程如下:
前工序(前道工艺):
1. 成膜淀积工艺:在晶圆上形成各种薄膜材料,包括导体、半导体和介质材料等。
这些薄膜材料由不同的元素和化合物组成,形成器件的关键结构。
2. 光刻工艺:在薄膜上形成图案并刻蚀,加工成确定形状。
光刻是半导体制造中的关键环节,通过光刻技术将设计好的电路图案转移到光敏材料上,然后进行刻蚀和剥离,形成电路图样。
3. 掺杂工艺:在半导体中掺入微量导电性杂质,以控制器件的电学性能,如导电类型、载流子浓度等。
掺杂工艺是实现半导体器件导电性能的关键步骤之一。
中工序(中道工艺):
1. 刻蚀工艺:将经过光刻和掺杂后的晶圆表面进行刻蚀,以形成各种半导体器件的结构和电路。
刻蚀工艺是实现器件微观结构的关键步骤之一。
2. 镀膜工艺:在器件表面镀上一层薄膜,以保护器件免受环境影响,提高器件的稳定性和可靠性。
镀膜工艺对于提高器件性能和延长使用寿命具有重要意义。
后工序(后道工艺):
1. 封装工艺:将制作好的芯片进行封装,以实现芯片与外部电路的连接和保护。
封装工艺是半导体制造中的重要环节,对于保证芯片的性能和可靠性具有重要意义。
2. 测试与可靠性验证:对封装好的芯片进行测试和可靠性验证,以确保其性能符合要求。
测试环节是保证芯片性能和可靠性的关键步骤之一。
以上是先进半导体器件的前、中、后工艺流程的简要介绍,每个环节都有其特定的作用和要求,只有严格控制每个环节的质量和工艺参数,才能制造出高性能、高可靠性的半导体器件。
半导体制造主要设备及工艺流程

半导体制造主要设备及⼯艺流程半导体产品的加⼯过程主要包括晶圆制造(前道,Front-End)和封装(后道,Back-End)测试,随着先进封装技术的渗透,出现介于晶圆制造和封装之间的加⼯环节,称为中道(Middle-End)。
由于半导体产品的加⼯⼯序多,所以在制造过程中需要⼤量的半导体设备和材料。
⼀、晶圆制造在这⾥,我们以最为复杂的晶圆制造(前道)和传统封装(后道)⼯艺为例,说明制造过程的所需要的设备和材料。
晶圆⽣产线可以分成7个独⽴的⽣产区域:扩散(Thermal Process)、光刻(Photo- lithography)、刻蚀(Etch)、离⼦注⼊(Ion Implant)、薄膜⽣长(Dielectric Deposition)、抛光(CMP)、⾦属化(Metalization)。
这7个主要的⽣产区和相关步骤以及测量等都是晶圆洁净⼚房进⾏的。
在这⼏个⽣产区都放置有若⼲种半导体设备,满⾜不同的需要。
例如在光刻区,除了光刻机之外,还会有配套的涂胶/显影和测量设备。
传统封装(后道)测试⼯艺可以⼤致分为背⾯减薄、晶圆切割、贴⽚、引线键合、模塑、电镀、切筋/成型和终测等8个主要步骤。
与IC晶圆制造(前道)相⽐,后道封装相对简单,技术难度较低,对⼯艺环境、设备和材料的要求远低于晶圆制造。
三、半导体⼯艺解析半导体制造⼯艺是集成电路实现的⼿段,也是集成电路设计的基础。
⾃从1948年晶体管发明以来,半导体器件⼯艺技术的发展经历了三个主要阶段:1950年采⽤合⾦法⼯艺,第⼀次⽣产出了实⽤化的合⾦结三极管;1955年扩散技术的采⽤是半导体器件制造技术的重⼤发展,为制造⾼频器件开辟了新途径;1960年平⾯⼯艺和外延技术的出现是半导体制造技术的重⼤变⾰,不但⼤幅度地提⾼了器件的频率、功率特性,改善了器件的稳定性和可靠性,⽽且也使半导体集成电路的⼯业化批量⽣产得以成为现实。
⽬前平⾯⼯艺仍然是半导体器件和集成电路⽣产的主流⼯艺。
- 1、下载文档前请自行甄别文档内容的完整性,平台不提供额外的编辑、内容补充、找答案等附加服务。
- 2、"仅部分预览"的文档,不可在线预览部分如存在完整性等问题,可反馈申请退款(可完整预览的文档不适用该条件!)。
- 3、如文档侵犯您的权益,请联系客服反馈,我们会尽快为您处理(人工客服工作时间:9:00-18:30)。
本技术属于建筑材料领域,尤其是一种半导体器件制备工艺,针对现有只是将晶粒利用包装盒进行包装,这样的包装方式容易导致晶粒损坏的问题,现提出如下方案,其包括S1:首先将成卷的碳纤维复合膜放置在支撑架上,然后进行开卷,S2:将碳纤维复合膜放置在工作台上,支撑台上设有导向机构,以此可以防止碳纤维复合膜出现走偏的问题,S3:在支撑台的一侧卡装有夹紧机构,将碳纤维复合膜的一侧放置在夹紧机构上,并由夹紧机构对碳纤维复合膜进行夹紧。
本技术通过将圆晶棒经过切割、打磨、过筛、抽真空以及密封包装,以此可以实现对圆晶粒进行真空包装的目的,可有效避免圆晶粒上附着水汽,所以便不会造成圆晶粒损坏。
权利要求书1.一种半导体器件制备工艺,其特征在于,包括以下步骤:S1:首先将圆晶棒放入干燥剂中,将晶粒上所含有的水汽进行吸附;S2:将干燥完后的圆晶棒放入振荡筛中,以此可以将圆晶棒与干燥剂进行分离;S3:将放置于在Fab中,利用Fab可对晶圆棒完成切割;S4:在对圆晶棒进行切割后,将圆晶粒放入打磨箱内,并利用搅拌器对圆晶粒进行搅拌,以此可以实现对圆晶粒的外表面进行打磨;S5:在打磨之后,利用筛网对圆晶粒进行过筛,以此可以得到大小均匀的圆晶粒;S6:将圆晶粒放入漏斗内,并且漏斗上设有关门装置,使得圆晶粒通过漏斗投放寨包装袋内;S7:利用抽风机将包装袋内进行抽真空处理,之后利用热封机对包装袋进行封口处理;S8:将软质填充入放入包装箱内,之后将经过真空处理后的圆晶粒放入包装箱内;S9:将干燥剂放入包装箱,之后将包装箱封装一层保护膜,在利用热风枪对保护膜,使得保护膜受热处于紧绷状态。
2.根据权利要求1所述的一种半导体器件制备工艺,其特征在于,所述S1中,干燥剂的成分是无水氯化钙,且无水氯化钙与圆晶棒的比例为3.5:100。
3.根据权利要求1所述的一种半导体器件制备工艺,其特征在于,所述S2中,振荡筛的工作频率为10Hz,且振荡筛的孔径为5目。
4.根据权利要求1所述的一种半导体器件制备工艺,其特征在于,所述S3中,Fab设定尺寸为3微米,切割频率为1Hz。
5.根据权利要求1所述的一种半导体器件制备工艺,其特征在于,所述S4中,打磨箱内设有打磨球,利用打磨球对圆晶粒进行打磨,且搅拌器的转速为20r/min。
6.根据权利要求1所述的一种半导体器件制备工艺,其特征在于,所述S5中,筛网的孔径为15目,并且筛网由振动电机进行驱动。
7.根据权利要求1所述的一种半导体器件制备工艺,其特征在于,所述S6中,漏斗上设有推杆马达,且推杆马达与关门装置进行连接,以此利用推杆马达带动关门装置对漏斗进行开启或者关闭,漏斗上设有颗粒计数器,且颗粒计数器与推杆马达电性连接,利用颗粒技术器可以对圆晶粒进行计数,且数量在49-51之间,以此可以保证包装袋内的圆晶粒的数量基本一致。
8.根据权利要求1所述的一种半导体器件制备工艺,其特征在于,所述S7中,热封机的温度设置为180摄氏度,热风机的工作时长为30s。
9.根据权利要求1所述的一种半导体器件制备工艺,其特征在于,所述S8中,软质填充物为块状的珍珠海绵,具有隔热、防震和柔韧弹性好的优点,广泛用于电子、电脑、箱包、家具、工艺品等产品的内外包装,且珍珠海绵上开设有多个大小一致的凹槽,以此便于将装有圆晶粒的包装袋放入包装箱内,防止圆晶粒出现随意移动的问题。
10.根据权利要求1所述的一种半导体器件制备工艺,其特征在于,所述S9中,热风枪的温度为200度,且保护膜的材质为聚氯乙烯。
技术说明书一种半导体器件制备工艺技术领域本技术涉及技术领域,尤其涉及一种半导体器件制备工艺。
背景技术集成电路制备工艺中,通常首先在晶圆(wafer)中制备器件,之后对晶圆进行切割(Dicing)形成多个晶粒(Die),并对各个晶粒进行CP测试,接着对晶粒进行引线封装。
通常,wafer工艺由制造厂商完成,Dicing工艺、CP测试、引线封装部分则交由其他封装厂商完成。
封装测试过程中,封装厂商例如采用机械切割或激光切割的方式将wafer切割成多个晶粒,再对晶粒进行CP测试、封装,然而现有的封装方式只是将晶粒利用包装盒进行包装,这样的包装方式容易导致晶粒损坏,所以我们提出一种半导体器件制备工艺,用于解决上述所提出的问题。
技术内容基于背景技术存在封装方式只是将晶粒利用包装盒进行包装,这样的包装方式容易导致晶粒损坏的技术问题,本技术提出了一种半导体器件制备工艺。
本技术提出的一种半导体器件制备工艺,包括以下步骤:S1:首先将圆晶棒放入干燥剂中,将晶粒上所含有的水汽进行吸附;S2:将干燥完后的圆晶棒放入振荡筛中,以此可以将圆晶棒与干燥剂进行分离;S3:将放置于在Fab中,利用Fab可对晶圆棒完成切割;S4:在对圆晶棒进行切割后,将圆晶粒放入打磨箱内,并利用搅拌器对圆晶粒进行搅拌,以此可以实现对圆晶粒的外表面进行打磨;S5:在打磨之后,利用筛网对圆晶粒进行过筛,以此可以得到大小均匀的圆晶粒;S6:将圆晶粒放入漏斗内,并且漏斗上设有关门装置,使得圆晶粒通过漏斗投放寨包装袋内;S7:利用抽风机将包装袋内进行抽真空处理,之后利用热封机对包装袋进行封口处理;S8:将软质填充入放入包装箱内,之后将经过真空处理后的圆晶粒放入包装箱内;S9:将干燥剂放入包装箱,之后将包装箱封装一层保护膜,在利用热风枪对保护膜,使得保护膜受热处于紧绷状态。
优选地,所述S1中,干燥剂的成分是无水氯化钙,且无水氯化钙与圆晶棒的比例为3.5:100。
优选地,所述S2中,振荡筛的工作频率为10Hz,且振荡筛的孔径为5目。
优选地,所述S3中,Fab设定尺寸为3微米,切割频率为1Hz。
优选地,所述S4中,打磨箱内设有打磨球,利用打磨球对圆晶粒进行打磨,且搅拌器的转速为20r/min。
优选地,所述S5中,筛网的孔径为15目,并且筛网由振动电机进行驱动。
优选地,所述S6中,漏斗上设有推杆马达,且推杆马达与关门装置进行连接,以此利用推杆马达带动关门装置对漏斗进行开启或者关闭,漏斗上设有颗粒计数器,且颗粒计数器与推杆马达电性连接,利用颗粒技术器可以对圆晶粒进行计数,且数量在49-51之间,以此可以保证包装袋内的圆晶粒的数量基本一致。
优选地,所述S7中,热封机的温度设置为180摄氏度,热风机的工作时长为30s。
优选地,所述S8中,软质填充物为块状的珍珠海绵,具有隔热、防震和柔韧弹性好的优点,广泛用于电子、电脑、箱包、家具、工艺品等产品的内外包装,且珍珠海绵上开设有多个大小一致的凹槽,以此便于将装有圆晶粒的包装袋放入包装箱内,防止圆晶粒出现随意移动的问题。
优选地,所述S9中,热风枪的温度为200度,且保护膜的材质为聚氯乙烯。
本技术的有益效果:首先将圆晶棒放入干燥剂中,将晶粒上所含有的水汽进行吸附,之后将干燥完后的圆晶棒放入振荡筛中,以此可以将圆晶棒与干燥剂进行分离,这时将放置于在Fab中,利用Fab可对晶圆棒完成切割,使得圆晶棒呈现为3微米的小颗粒,在对圆晶棒进行切割后,将圆晶粒放入打磨箱内,并利用搅拌器对圆晶粒进行搅拌,以此可以实现对圆晶粒的外表面进行打磨,以此可以得到大小均匀,且外表光滑的圆晶粒;在打磨之后,利用筛网对圆晶粒进行过筛,以此可以得到大小均匀的圆晶粒,将圆晶粒放入漏斗内,并且漏斗上设有关门装置、推杆马达以及颗粒计数器,利用颗粒计数器对圆晶粒进行计数,在数量达到要求时,颗粒计数器就会启动推杆马达,使得关门装置对漏斗进行封堵,使得圆晶粒通过漏斗投放寨包装袋内,并且数量基本一致,接着利用抽风机将包装袋内进行抽真空处理,之后利用热封机对包装袋进行封口处理,将软质填充入放入包装箱内,之后将经过真空处理后的圆晶粒放入包装箱内,将干燥剂放入包装箱,之后将包装箱封装一层保护膜,在利用热风枪对保护膜,使得保护膜受热处于紧绷状态;本技术通过将圆晶棒经过切割、打磨、过筛、抽真空以及密封包装,以此可以实现对圆晶粒进行真空包装的目的,可有效避免圆晶粒上附着水汽,所以便不会造成圆晶粒损坏。
具体实施方式下面结合具体实施例对本技术作进一步解说。
本技术提出的一种半导体器件制备工艺,包括以下步骤:S1:首先将圆晶棒放入干燥剂中,将晶粒上所含有的水汽进行吸附;S2:将干燥完后的圆晶棒放入振荡筛中,以此可以将圆晶棒与干燥剂进行分离;S3:将放置于在Fab中,利用Fab可对晶圆棒完成切割;S4:在对圆晶棒进行切割后,将圆晶粒放入打磨箱内,并利用搅拌器对圆晶粒进行搅拌,以此可以实现对圆晶粒的外表面进行打磨;S5:在打磨之后,利用筛网对圆晶粒进行过筛,以此可以得到大小均匀的圆晶粒;S6:将圆晶粒放入漏斗内,并且漏斗上设有关门装置,使得圆晶粒通过漏斗投放寨包装袋内;S7:利用抽风机将包装袋内进行抽真空处理,之后利用热封机对包装袋进行封口处理;S8:将软质填充入放入包装箱内,之后将经过真空处理后的圆晶粒放入包装箱内;S9:将干燥剂放入包装箱,之后将包装箱封装一层保护膜,在利用热风枪对保护膜,使得保护膜受热处于紧绷状态。
本实施例中,S1中,干燥剂的成分是无水氯化钙,且无水氯化钙与圆晶棒的比例为3.5:100。
本实施例中,S2中,振荡筛的工作频率为10Hz,且振荡筛的孔径为5目。
本实施例中,S3中,Fab设定尺寸为3微米,切割频率为1Hz。
本实施例中,S4中,打磨箱内设有打磨球,利用打磨球对圆晶粒进行打磨,且搅拌器的转速为20r/min。
本实施例中,S5中,筛网的孔径为15目,并且筛网由振动电机进行驱动。
本实施例中,S6中,漏斗上设有推杆马达,且推杆马达与关门装置进行连接,以此利用推杆马达带动关门装置对漏斗进行开启或者关闭,漏斗上设有颗粒计数器,且颗粒计数器与推杆马达电性连接,利用颗粒技术器可以对圆晶粒进行计数,且数量在49-51之间,以此可以保证包装袋内的圆晶粒的数量基本一致。
本实施例中,S7中,热封机的温度设置为180摄氏度,热风机的工作时长为30s。
本实施例中,S8中,软质填充物为块状的珍珠海绵,具有隔热、防震和柔韧弹性好的优点,广泛用于电子、电脑、箱包、家具、工艺品等产品的内外包装,且珍珠海绵上开设有多个大小一致的凹槽,以此便于将装有圆晶粒的包装袋放入包装箱内,防止圆晶粒出现随意移动的问题。
本实施例中,S9中,热风枪的温度为200度,且保护膜的材质为聚氯乙烯。
首先将圆晶棒放入干燥剂中,将晶粒上所含有的水汽进行吸附,之后将干燥完后的圆晶棒放入振荡筛中,以此可以将圆晶棒与干燥剂进行分离,这时将放置于在Fab中,利用Fab可对晶圆棒完成切割,使得圆晶棒呈现为3微米的小颗粒,在对圆晶棒进行切割后,将圆晶粒放入打磨箱内,并利用搅拌器对圆晶粒进行搅拌,以此可以实现对圆晶粒的外表面进行打磨,以此可以得到大小均匀,且外表光滑的圆晶粒,在打磨之后,利用筛网对圆晶粒进行过筛,以此可以得到大小均匀的圆晶粒,将圆晶粒放入漏斗内,并且漏斗上设有关门装置、推杆马达以及颗粒计数器,利用颗粒计数器对圆晶粒进行计数,在数量达到要求时,颗粒计数器就会启动推杆马达,使得关门装置对漏斗进行封堵,使得圆晶粒通过漏斗投放寨包装袋内,并且数量基本一致,接着利用抽风机将包装袋内进行抽真空处理,之后利用热封机对包装袋进行封口处理,将软质填充入放入包装箱内,之后将经过真空处理后的圆晶粒放入包装箱内,将干燥剂放入包装箱,之后将包装箱封装一层保护膜,在利用热风枪对保护膜,使得保护膜受热处于紧绷状态,本技术综上所述通过将圆晶棒经过切割、打磨、过筛、抽真空以及密封包装,以此可以实现对圆晶粒进行真空包装的目的,可有效避免圆晶粒上附着水汽,所以便不会造成圆晶粒损坏。