管材超声波探伤优选稿
管道连接点探测报告(超声波)模板
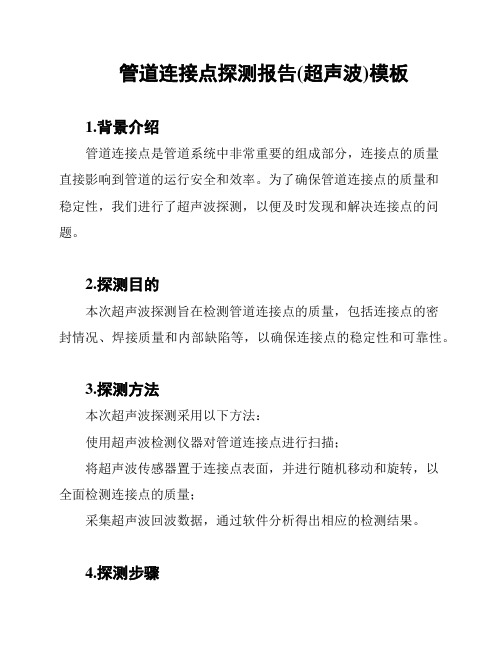
管道连接点探测报告(超声波)模板1.背景介绍管道连接点是管道系统中非常重要的组成部分,连接点的质量直接影响到管道的运行安全和效率。
为了确保管道连接点的质量和稳定性,我们进行了超声波探测,以便及时发现和解决连接点的问题。
2.探测目的本次超声波探测旨在检测管道连接点的质量,包括连接点的密封情况、焊接质量和内部缺陷等,以确保连接点的稳定性和可靠性。
3.探测方法本次超声波探测采用以下方法:使用超声波检测仪器对管道连接点进行扫描;将超声波传感器置于连接点表面,并进行随机移动和旋转,以全面检测连接点的质量;采集超声波回波数据,通过软件分析得出相应的检测结果。
4.探测步骤本次超声波探测的步骤如下:1.准备工作:确保探测仪器正常工作,校准仪器;清理连接点表面,确保没有杂质和污垢;确定探测方法和参数。
2.进行探测:将超声波传感器置于连接点表面,保持一定的压力;启动超声波探测仪器,开始扫描;边扫描边记录数据,包括回波信号和传感器位置。
3.数据分析:将采集到的数据输入到分析软件中;根据预设的参数和标准,对数据进行分析和解读;得出连接点的质量评估结果。
4.结果报告:将分析结果整理成报告,包括连接点的质量评估、存在的问题以及建议的解决方案;报告应包含探测日期、地点、探测员等相关信息。
5.结果与讨论根据我们的探测结果分析,连接点的质量良好且密封性良好,焊接质量满足要求,未发现任何内部缺陷。
我们对管道连接点的质量表示满意,并建议定期进行监测和维护,以确保连接点的长期稳定性。
6.结论本次超声波探测证实了管道连接点的良好质量和稳定性,为管道系统的正常运行提供了保障。
探测结果报告应被保留并作为管道连接点质量管理的参考依据。
以上是管道连接点探测报告(超声波)模板的内容,希望对您有所帮助。
小直径钢管超声波水浸法探伤分析

t i k e s o u n t . h a me t n lz d t e d f r n e b t e l a o i a e mme so t o n h c n s ,fc sa d e c At e s me t ,i a ay e h i e e c ewe n u t s n c w t ri t i f r rin meh d a d c n a t e e t n meh d n r d c d i d a tg s d s d a tg sa d r n e o s f l a o i tri o t c tc i t o ,i t u e t a v n a e , ia v n a e n a g fu eo t s n cwae d o o s u r mme so ,a d ri n n
中 ,纵波 直探头 垂 直 于钢管 表 面 ,且 离钢 管有 一 定 的距 离 ,用水 做耦 合 剂 ,经过折 射 作用 ,可在 钢管 内实 现 纯横 波 探 伤 。在 对 钢 管 进行 探 伤 时 , 为 了增 加水 对钢 管 表面 的润 湿作用 ,防止 钢管 生
锈 ,需 要 加入少 量 活性 剂和 适量 的 防腐剂 。
等 因素 的影 响 ,使 成 型后 管材 的表 面或 者 内部 出
现裂 纹 等缺 陷 。所 以在实 际应 用 之前 ,必 须对 管
材进 行严 格 的检测 ,而超 声波探 伤 技术 对 提高 和 保 证 产 品质 量 有 着 至 关 重 要 的作 用 ,以 其 快 速
性 、准确 性 、无 污染等 特性 已被 广 泛应 用 ,特 别
小 直 径 钢管 ( 径小 于 1 0mm) 国 民经 济 外 0 在
中 占有重 要 的地 位 ,广泛 应用 于航 空 、军 工 等领 域 。在 管材 的制造 过程 中 ,往往 由于材 料 中夹 渣
无损检测超声波探伤第7章 板材、管材
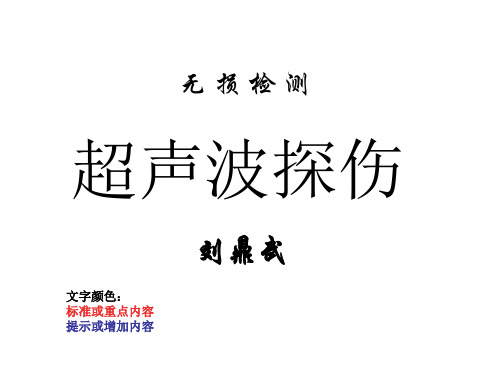
B1 F1
B2
50 F2
B1 F1
B2 50
F2
B1 B2
0
5
10
① (F1≥曲线)
0
5
10
② 双晶探头t<20mm (F1≥50%)
0
5
10
③ (B1<50%)
2.缺陷的测定 扫查发现缺陷后要测定缺陷的位置、大小,并评估缺陷的性质。 (1)缺陷位置的测定:包括深度位置和平面位置。
根据金属板材的材质不同,常见的金属板材有 钢板(CL5900、CS3230)、铝板(CL6260、CS3080)、 铜板(CL4700、CS2260)……等等。
实际生产中钢板的应用最广,因此这里以钢板 为例来说明板材的超声波探伤。
普通钢板是由钢锭轧制而成。普通钢板包括碳素钢、低合金钢以及奥 氏体钢板、镍及镍合金钢板和双相不锈钢板。
由于钢板加工方式的原因,钢板中的缺陷大多是面积形缺陷。缺陷的 形成一方面是由于材质特性造成,一方面是由于加工工艺造成。
分层、折叠缺陷是在轧制过程中形成,基本都与表面平行。
根据钢板厚度的不同,将钢板分为薄板、中厚板和厚板。
δ<6㎜ 薄板
6≤ δ ≥40㎜ 中厚板
δ >40㎜ 厚板
厚板的探伤常用垂直入射的纵波检测法,又称为垂直检测 法;薄板的探伤常用板波检测法。(详见第五章)
(4)缺陷边界范围和指示长度的测定:
47013标准5.3.6.2规定了缺陷边界的测定方法。 ① 检出缺陷后,应在他的周围继续进行检测,以确定缺陷的范围。 ② 板材<20㎜用双晶探头确定缺陷的边界范围或只是长度时,探头的 移动方向应与探头的隔声层相垂直,并使缺陷波下降到检测灵敏度条件 下显示屏满刻度的25%,探头中心点即为缺陷的边界点。 ③ 板材厚度20㎜~60㎜用双晶直探头确定缺陷的边界范围时,探头的 移动方向应与探头的隔声层相垂直,并使缺陷波下降到距离波幅曲线, 探头中心点即为缺陷的边界点。 ④ 用单直探头确定缺陷的边界范围或指示长度时,移动探头使缺陷第 一次波波高下降到距离波幅曲线,探头中心点即为缺陷的边界点。 ⑤ 确定底面第一次反射波波幅低于满屏50%时,探头移动(单探头或双 直探头)使底面第一次反射波升高到显示屏满刻度的50%,此时探头中 心点即为缺陷的边界点。
钢管超声波探伤报告

V型坡口
补偿(dB)
4dB
缺陷总长
0
焊接方法
手工电弧焊
检查面状况
打磨良好
返修情况
无返修
探 伤 面
焊缝单面双侧
探伤时机
焊后24小时
检测结果
合格
焊缝宽度
12-14㎜
探头参数
2.5P8×12K2
实测m
Z1
3089mm
Z2 H1
2700mm
焊缝编号
缺陷深度
MDJ7
MDJ4
MDJ5 MDJ6
2700㎜
缺陷深度
波幅dB
缺陷指示长度
缺陷性质
评定
备注
MDJ1
/
/
/
无应记录缺陷
BI级
合格
MDJ2
/
/
/
无应记录缺陷
BI级
合格
MDJ3
/
/
/
无应记录缺陷
BI级
合格
MDJ4
/
/
/
无应记录缺陷
BI级
合格
MDJ5
/
/
/
无应记录缺陷
BI级
合格
MDJ6
/
/
/
无应记录缺陷
BI级
超声波检测报告
工程名称:XXXXXXXXXX工程
设备名称:出水钢管(制作)
检测时间:2022年5月25日
报告编号:GYNY[2020525]
焊缝超声波探伤报告
工程名称
XXXXXX工程
仪器型号
CTS—9006
图 号
钢管名称
出水钢管-01#
探头型号
2.5P8×12K2
铜及铜合金管材超声波探伤方法 - 中国有色金属标准质量信息网

《铜及铜合金管材超声波探伤方法》编制说明(审定稿)一、任务来源对铜及铜合金管材内部缺陷的检测只有涡流探伤方法,且只适用于厚度小于6mm 的管材,而厚度大于6mm的管材没有探伤方法。
随着铜及铜合金管材特别是厚度大于10mm的管材在军工、航天航空、核电、船舶、冶金和汽车工业的广泛应用,以及出口的不断增加,用户对铜管内部质量要求越来越高,目前生产厂家主要靠折断口或低倍检测的方法来判断产品的好坏,但不能从根本上发现管材内部存在的缺陷,而超声波探伤最适合进行缺陷检测,因此有必要起草铜及铜合金管材超声波探伤方法。
根据工业和信息化部工信部《关于印发2012年第二批行业标准制修订计划的通知》(工信厅科[2012]119号)精神,全国有色金属标准化技术委员会以有色标委[2012] 28号文下达了修订《铜及铜合金管材超声波探伤方法》行业标准的计划(计划号2012-0730T-YS),该标准由中铝洛阳铜业有限公司、桂林漓佳金属有限公司、中国有色金属工业无损检测中心、江阴新华宏铜业有限公司、苏州龙骏无损检测设备有限公司负责修订。
二、起草过程标准起草单位首先查阅了国内外有关铜及铜合金产品超声波探伤方法的有关资料和标准。
国外没有铜管超声波探伤的有关标准,国内主要有GJB 3074-97《航天用锆无氧铜锻饼超声波检验方法》,GB/T3310-2010《铜及铜合金棒材超声波探伤方法》、YB/T585-2006《铜及铜合金板材超声波探伤方法》等,但没有铜及铜合金管材超声波探伤方法标准。
目前铜及铜合金管材已广泛应用于在军工、航天航空、核电、船舶、汽车和冶金工业,如航天发动机用铬青铜管、潜艇用白铜和铝青铜管、汽车同步器齿环管以及核工业用紫铜管均需进行超声波探伤,且各自对铜管的内部质量要求也不一样。
为此,近几年,标准起草单位根据用户的不同质量要求对不同厚度的铜及铜合金管材进行了超声波探伤试验,争取尽快起草出铜及铜合金管材超声波探伤方法标准,以满足国内、国际市场对铜及铜合金管材日益增加的需求。
4mm管焊缝超声波探伤报告
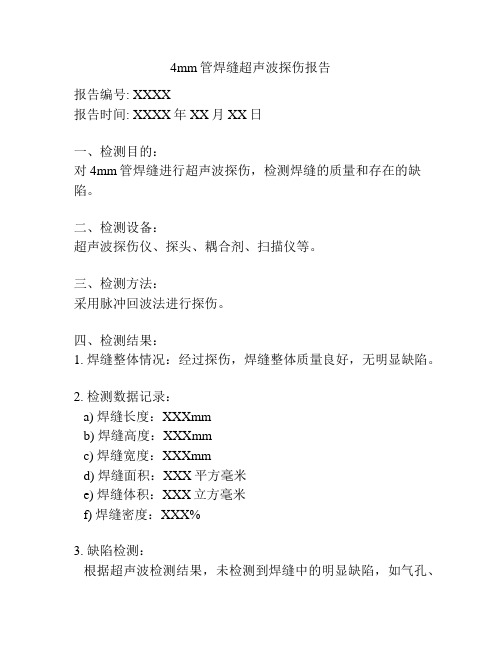
4mm管焊缝超声波探伤报告
报告编号: XXXX
报告时间: XXXX年XX月XX日
一、检测目的:
对4mm管焊缝进行超声波探伤,检测焊缝的质量和存在的缺陷。
二、检测设备:
超声波探伤仪、探头、耦合剂、扫描仪等。
三、检测方法:
采用脉冲回波法进行探伤。
四、检测结果:
1. 焊缝整体情况:经过探伤,焊缝整体质量良好,无明显缺陷。
2. 检测数据记录:
a) 焊缝长度:XXXmm
b) 焊缝高度:XXXmm
c) 焊缝宽度:XXXmm
d) 焊缝面积:XXX平方毫米
e) 焊缝体积:XXX立方毫米
f) 焊缝密度:XXX%
3. 缺陷检测:
根据超声波检测结果,未检测到焊缝中的明显缺陷,如气孔、
夹渣、裂纹等。
五、结论:
经过超声波探伤,焊缝质量良好,未发现明显缺陷。
六、检测人员:
XXX
备注:此报告仅针对超声波探伤结果,其他非超声波检测结果未包括在内。
如需评估整体焊接质量,请综合考虑其他检测结果。
小径薄壁管焊接接头超声波探伤方法探讨

小径薄壁管焊接接头超声波探伤方法探讨摘要:针对小直径薄壁钢管焊缝的超声检测,提出了以焊缝的普通根波和管壁反射波为参照波,对比判断焊缝的缺陷,并对其进行了分析。
关键词:变形波;超声波探伤;比较法1小径管对接焊缝超声波探伤所具有的特点1.1较小直径的管道具有较薄的管壁和较宽的焊缝从电力部发布的工业标准(主要是《电力建设施工及验收技术规范》)的要求可以看出,一般小直径管焊缝比管壁厚宽2-3倍,且常规焊接缝无法实现,如,小直径管壁厚4mm,焊接缝宽12mm。
由于其具有较高的尺寸精度要求,因此必须采用超声波探伤技术来完成对管道焊缝质量的控制。
按常规超声检测方法进行,利用一次波对焊缝根部缺陷进行了探测,那么探头入射角β正切值就会介于2.7-3.2之间,很难在焊缝的中部,中部、上部分缺陷得到了有效鉴定,很容易引起表面波,继而给缺陷定位与量化带来负面影响。
1.2对超声近声场区域进行有效处理的必要性超声检测时,由于声束近场区轴向最大声压较多,在探测中,一定要把近场区最大压力限制在三个或更大,以确保缺陷的发现。
特别适用于管径较小时,因管壁较厚,这个问题就更为严重了。
本文介绍了通过采用适当大小的换能器来减小近场区内的最大声压和利用声波传播理论进行分析计算而得到的解决方法。
该方法可以使近场区的面积达到最小,是比较行之有效的途径。
1.3在管道内部和外部存在较大的表面声能量损耗而小径管因管径小曲率大,其内、外表面超声波均可出现较明显聚束、发散等现象,应格外加以重视。
对于大直径的管子,则需进行特殊处理才能满足探伤要求。
介绍小直径钢管超声检测专用试片DL—1。
该试片由两个相同厚度的钢板焊接而成。
使用对应圆弧形状,增大接触区域。
2小径管超声波探伤过程中较为常见的技术性问题2.1选择测针超声波检测小直径管接焊缝过程中,要尽可能选择较大探针,为了使声束在所有焊缝截面上都能尽量被扫描。
由于采用了适当的探头位置和较长的时间来探测整个焊缝,所以能够准确地发现焊缝中存在的裂纹等微小缺陷。
钢管焊接质量评估报告(超声波)模板

钢管焊接质量评估报告(超声波)模板钢管焊接质量评估报告(超声波)模板1. 引言本报告旨在评估钢管焊接质量,并通过超声波检测结果给出相应的评估和建议。
钢管焊接是工业中常见的连接方法之一,其质量直接关系到工程的安全性和可靠性。
超声波检测作为一种非破坏性检测方法,在钢管焊接质量评估中具有重要的应用。
2. 超声波检测原理超声波检测利用超声波在材料中传播、反射和干涉的原理来检测材料的内部缺陷和变化。
在钢管焊接中,超声波可以有效地探测焊缝是否存在缺陷,如气孔、夹杂物、裂纹等。
3. 检测方法本次钢管焊接质量评估采用以下超声波检测方法:- 使用超声波探头对焊缝进行扫描,记录超声波信号。
- 分析超声波信号,检测焊缝中是否存在缺陷,并对缺陷进行分类和评估。
4. 检测结果根据超声波检测,以下为钢管焊缝的检测结果:1. 缺陷类型:气孔- 位置:焊缝中央处- 尺寸:直径约5mm- 数量:共发现3个气孔2. 缺陷类型:夹杂物- 位置:焊缝表面附近- 尺寸:长度约15mm,宽度约10mm- 数量:共发现2个夹杂物3. 缺陷类型:裂纹- 位置:焊缝内部- 尺寸:长度约30mm,宽度约0.5mm- 数量:共发现1条裂纹5. 评估与建议根据上述检测结果,钢管焊缝存在多个气孔、夹杂物和一条裂纹,这些缺陷严重影响了焊缝的强度和密封性,可能导致潜在的安全隐患。
为了确保焊接质量,建议采取以下措施:- 检查焊接设备和工艺参数是否合适,确保焊接过程中气孔、夹杂物和裂纹的产生得以有效控制。
- 对已存在的缺陷,应及时进行修补或再次焊接,确保焊缝的完整性和可靠性。
- 强化质量检验过程,使用超声波检测等非破坏性检测方法,及时发现和排除焊缝缺陷。
6. 总结本报告对钢管焊接质量进行了超声波检测评估,并给出了相应的检测结果、评估和建议。
通过超声波检测,我们发现焊缝存在气孔、夹杂物和裂纹等缺陷,这对焊接质量和工程安全性造成了一定的影响。
建议在焊接过程中加强质量控制,及时发现和修复焊缝缺陷,确保焊接的质量和可靠性。
铜及铜合金轧制板材超声波探伤方法

《铜及铜合金管材超声波检测方法》编制说明(征求意见稿)一、任务来源对铜及铜合金管材内部缺陷的检测只有涡流探伤方法,且只适用于厚度小于6mm 的管材,而厚度大于6mm的管材没有探伤方法。
随着铜及铜合金管材特别是厚度大于6mm的管材在军工、航天航空、核电、船舶、冶金和汽车工业的广泛应用,以及出口的不断增加,用户对铜管内部质量要求越来越高,目前生产厂家主要靠折断口或低倍检测的方法来判断产品的好坏,但不能从根本上发现管材内部存在的缺陷,而超声波探伤最适合进行缺陷检测,因此有必要起草铜及铜合金管材超声波探伤方法。
根据工业和信息化部工信部《关于印发2012年第二批行业标准制修订计划的通知》(工信厅科[2012]119号)精神,全国有色金属标准化技术委员会以有色标委[2012] 28号文下达了修订《铜及铜合金管材超声波检测方法》行业标准的计划(计划号2012-0730T-YS),该标准由中铝洛阳铜业有限公司、桂林漓佳金属有限公司、中国有色金属工业无损检测中心、江阴新华宏铜业有限公司、苏州龙骏无损检测设备有限公司负责修订。
二、起草过程标准起草单位首先查阅了国内外有关铜及铜合金产品超声波探伤方法的有关资料和标准。
国外没有铜板超声波探伤的有关标准,国内主要有GJB 3074-97《航天用锆无氧铜锻饼超声波检验方法》,GB/T3310-2010《铜及铜合金棒材超声波探伤方法》、YB/T585-2006《铜及铜合金板材超声波探伤方法》等,没有铜及铜合金管材超声波探伤方法标准。
目前铜及铜合金管材已广泛应用于在军工、航天航空、核电、船舶、汽车和冶金工业,如航天发动机用铬青铜管、潜艇用白铜和铝青铜管、汽车同步器齿环管以及核工业用紫铜管均需进行超声波探伤,且各自对铜管的内部质量要求也不一样。
为此,近几年,标准起草单位根据用户的不同质量要求对不同厚度的铜及铜合金管材进行了超声波探伤试验,争取尽快起草出铜及铜合金管材超声波探伤方法标准,以满足国内、国际市场对铜及铜合金管材日益增加的需求。
如何做好管材环缝的超声波探伤

前 富 在钢 管焊 接 中 , 由于焊接 之后 无法看 到焊 道 内部成型情 况 , 要想 保证 管材 环缝的焊接质量 , 就要通过探伤手段对管材环缝进行检测。 在传统探伤手段中, 针对管材环缝多采用射线探伤的方式检测内部缺陷。 但是由于射线探伤在实施 过程中存在大量辐射, 对操作人员有一定损伤, 并且射线探伤机在针对管材环 缝的探伤过程中存在一定的困难 , 总体探伤效率低。 而超声波探伤以其操作简 单ห้องสมุดไป่ตู้ 对身体辐射小, 探伤效率高, 逐渐得到了人们的青睐, 成为了管材环缝的主 要探伤 方 式 , 在 实际探 伤 中取得 了广 泛 的应用 。
料 孚 论 坛
C hi n a s ci e n ce a n d Te c h n el e g y R e v i e w
●l
如 何做 好 管材 环 缝 的超 声 波 探伤
孔 明
( 西安 三环 科 技开 发总 公 司 3 0 0 3 0 1 )
[ 摘 要] 在钢管焊接过程中, 环缝是主要的焊接形式 , 为了 保证焊接质量达到标准要求, 提高钢管的承压能力 , 应对钢管的环缝进行探伤处理 。 从目 前探伤 方法来看, 分为射线探伤、 超声波探伤、 磁粉探伤和渗透探伤。 从实际操作难度和探伤效果来看 , 超声波探伤在实际生产中较易实现, 并且对探伤操作人员的身体损 伤较小 , 整 体探 伤效果 比较理想 基于 这一 考虑 , 在管 材环 缝的探 伤 中, 超 声波探 伤得到 了重要 应用 出于 提高 整体探 伤 质量 的 目的 , 我们应 该认真 分析 超声 波探 伤 的特 点 , 并把 握超 声波 探伤 要 点 , 认 真 做好管 材 环缝 的超 声波探 伤 。 [ 关键 词] 管材 ,焊接 ,环缝 , 超 声 波探 伤 中图分 类号 : T G4 4 1 . 7 文献标 识码 : A 文章编 号 : 1 0 0 9 — 9 1 4 X ( 2 0 1 3 ) 3 8 - 0 4 5 1 - 0 1
板材和管材超声波探伤、第8章-锻件与铸件超声波探伤【范本模板】

第7章板材和管材超声波探伤姚志忠7.1板材超声波探伤板材分类:δ<6mm薄板6mm≤δ≤40 mm中板δ>40mm厚板7。
1。
1钢板中常见缺陷存在于内部分层——钢锭中非金属夹杂物,金属氧化物,硫化物以及夹渣在轧制过程中被轧扁而形成。
这些缺陷有的是钢水本身产生,如脱氧时加脱氧剂造成,或炼钢炉混入钢水中的耐火材料等,这些缺陷在钢锭中位置没有一定规律,故出现在钢板中位置也无序。
分层是以上缺陷轧制而成,大多与钢平行,且具有固定走向。
为平面状缺陷,严重时形成完全剥离的层状裂纹,对小的点状夹杂物则形成小的局部分层。
白点——存在于内部钢中氢在加工过程来不及向外扩散,在钢板成型后,氢原子逐渐在钢板中的微缺陷(如非断面呈白色故称白点.常见于锻钢中和厚钢板中。
折迭和重皮——存在于表面钢板表面因局部折、轧形成的双层金属,基本平行于表面。
裂纹——轧制工艺和温度不合适时造成。
存在于钢板表面,偶尔在内部。
裂纹较少见,如轧制工艺稳定,这类缺陷不常见.7.1.2 探伤方法1.直接接触法探头通过耦合层直接与钢板接触,当探头位于完好区时,仪器上出现底波多次反射.采用底波多次反射法探伤应满足下面三条件:①工件的探伤面与底面互相平行,确保产生多次反射。
(如工件加工倾斜就不合适).②钢板材质晶粒度必须均匀,保证无缺陷处底面多次反射波次数的稳定。
(各次相同).③材质对超声波的衰减要小。
保证反射底波有足够数量,以利探伤观察.一般碳钢、不锈钢均能满足这些条件. 2.水浸法在探伤仪荧光屏上将同时出现水层多次反射和钢板底面多次反射波,如水层厚度控制不好会互相干扰,不利探伤。
探伤时调节水层厚度,使水层波与某次底波重合。
水层厚H 和板厚δ关系为: H=4δδn C Cn =钢水,n 为重合次数.△对充水直探头的要求:① 为满足多次重合法要求,水层厚度要连续可调。
② 调至不同厚度时,必须保证发射的声束与钢板表面垂直。
③ 充水探头内水套管内径必须大于最大水层厚度时声束直径。
复合材料、板材和管材超声波探伤检测方法

7.2 铝及铝合金、钛及钛合金板材超声检测
7.2.1 铝及铝合金板材制造及常见缺陷 板材制造:铝锭→板坯→板材 ; 常见缺陷:气孔、夹杂、微细裂纹、厚板中可能有空腔。
7.2.2 铝及铝合金,钛及钛合金板材检测方法 1)检测方法:与钢板相同 2)探头与扫查方式 直探头、双晶直探头,频率2.5~5MHz; 扫查方式、扫查速度与钢板相同。 3)检测范围和灵敏度 检测范围:根据板厚与钢板相同; 检测灵敏度:基准灵敏度以完好部位B1=80%满幅。
≤10<25Ⅳ源自<150<100≤10
<25
Ⅴ
超过Ⅳ级者
注:Ⅳ级钢板主要用于与承压设备有关的支承件和结构件的制造安装。
4.1.8.2 在坡口预定线两侧各50mm(板厚大于100mm时,以 板厚的一半为准)内,缺陷的指示长度大于或等于50mm时, 应评为Ⅴ级。
4.1.8.3 在检测过程中,检测人员如确认钢板中有白点、裂纹 等危害性缺陷存在时,应评为Ⅴ级。
7.1 板材超声波探伤
7.1.6 质量等级判定:按JB/T4730-2005标准4.1.7条规定评定。
等级
单个缺陷 指示长度
mm
单个缺陷 指示面积
cm2
在任一1m×1m检测面 积内存在的缺陷面 积百分比%
以下单个缺陷 指示面积不计
cm2
Ⅰ
<80
<25
≤3
<9
Ⅱ
<100
<50
≤5
<15
Ⅲ
<120
<100
40mm以上钢板检测频率为2.5MHz。 晶片直径:Ф14~Ф25mm。 单晶直探头:适用于板厚δ较大的钢板检测; 双晶直探头:适用于板厚δ较薄的钢板检测。
板厚,mm 采用探头 公称频率,MHz
钛合金管材超声波探伤,无损探伤检测

钛合金管材超声波探伤,无损探伤检测无损检测是工业发展必不可少的有效工具,无损检测(NDT或无损探伤)是在不损害或不影响被检测对象使用性能的前提下,采用射线、超声、红外、电磁等原理技术并结合仪器对材料、零件、设备进行缺陷、化学、物理参数检测的技术。
无损检测可应用于设计阶段、制造过程、成品检验及在役检查等多方面。
常规的无损检测方法有:超声波探伤(UT)、射线探伤(RT)、磁粉探伤(MT)、渗透探伤(PT)、涡流探伤(ET)等。
钛合金管是利用钛合金制作的管子,钛合金按组织可分三类:1、钛中加入铝和锡元素;2、钛中加入铝铬钼钒等合金元素;3、钛中加入铝和钒等元素。
它们具有较高的力学性能、优良的冲压性能,并可进行各种形式的焊接,焊接接头强度可达基体金属强度的90%,且切削加工性能良好。
钛合金管广泛用于化工、石油、冶金、轻工机械、仪表、发电、海水淡化、医疗器械、氯碱制盐、电镀、环保、铜业等行业。
怎么进行钛合金管材超声波探伤?探伤方法1、在探头和管材相对作周向旋转和轴向移动的状态下,采用线聚焦探头利用横波进行水浸法探伤。
必要时,亦可选用点聚焦探头。
2、探伤时,超声波束应由管材横截面法线的一侧入射(即只沿一个圆周方向进行探伤),必要时,可增加轴向入射超声波束,以检测圆周方向的缺陷。
另外,需方要求并在合同中注明时,可在管材横截面法线的另一侧再增加一个方向的探伤。
参考:《钛及钛合金管材超声波探伤方法》GB/T 12969.1-2007广东精美检测实验室,取得CMA认可资质,坚持“科学、严谨、快捷、公平”的理念,严格按照相关标准,为客户提供专业的无损探伤检测,认真完成每一次检测委托,出具认可的第三方检测报告!文章部分内容来源网络,如有侵权,请告知我们删除!还有,内容仅供参考,如有错误,请联系我们修改!。
超声探伤检测报告

超声探伤检测报告1. 引言超声探伤是一种常用的无损检测方法,广泛应用于工程和科学领域。
本报告旨在详细描述一次超声探伤检测的过程、结果和分析。
2. 检测设备和参数本次超声探伤检测使用的设备是 XXX 型号的超声探伤仪。
检测参数如下: - 脉冲重复频率:2 MHz - 探头类型:单晶探头 - 检测模式:脉冲回波模式3. 检测对象和方法本次超声探伤检测的对象是一根长度为 X 米的金属管道。
检测目的是确定管道内部的缺陷情况和尺寸。
检测方法如下: 1. 将探头与被检测物表面接触,保持稳定。
2. 设置超声探伤仪的参数。
3. 通过向材料内部发射超声波,记录回声信号。
4. 分析回声信号,判断是否存在缺陷。
4. 检测结果经过超声探伤检测,我们得到了以下结果:1.缺陷 1:–位置:距离管道起点 X 米处–类型:表面裂纹–尺寸:长度约 X mm,深度约 X mm–形状:直线状–缺陷等级:A2.缺陷 2:–位置:距离管道起点 X 米处–类型:内部夹杂–尺寸:直径约 X mm–形状:不规则–缺陷等级:B5. 分析与讨论根据检测结果,我们可以得出以下结论:1.缺陷 1 的存在可能会对管道的强度和密封性产生一定影响,建议采取修复措施。
2.缺陷 2 的存在可能会导致材料耐久性降低,需要采取相应措施防止进一步扩展。
6. 结论本次超声探伤检测对目标管道的缺陷进行了详细的分析和评估。
在后续维护和修复过程中,应注意处理检测中发现的缺陷,以确保管道的正常运行和安全。
以上是本次超声探伤检测的报告内容,希望对您有所帮助。
注意:本报告仅基于本次超声探伤检测的结果,不考虑其他可能因素对管道的影响。
为了更全面、准确地评估管道的安全状况,建议进行更多的综合性检测和分析。
无缝钢管超声波探伤检验方法【整编】
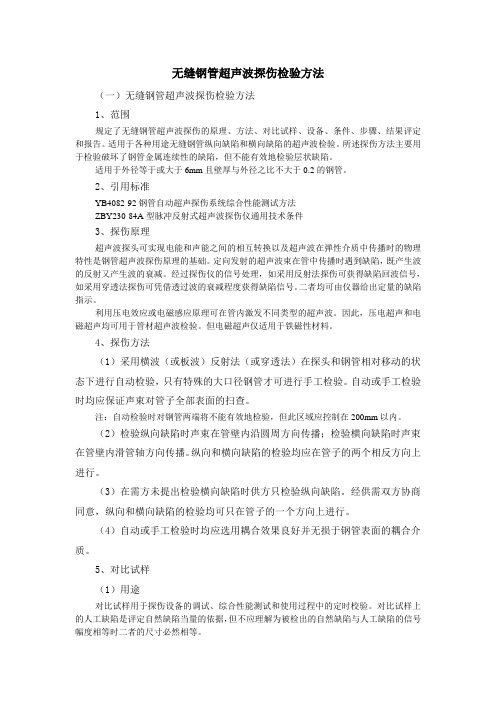
无缝钢管超声波探伤检验方法(一)无缝钢管超声波探伤检验方法1、范围规定了无缝钢管超声波探伤的原理、方法、对比试样、设备、条件、步骤、结果评定和报告。
适用于各种用途无缝钢管纵向缺陷和横向缺陷的超声波检验。
所述探伤方法主要用于检验破坏了钢管金属连续性的缺陷,但不能有效地检验层状缺陷。
适用于外径等于或大于6mm且壁厚与外径之比不大于0.2的钢管。
2、引用标准YB4082-92钢管自动超声探伤系统综合性能测试方法ZBY230-84A型脉冲反射式超声波探伤仪通用技术条件3、探伤原理超声波探头可实现电能和声能之间的相互转换以及超声波在弹性介质中传播时的物理特性是钢管超声波探伤原理的基础。
定向发射的超声波束在管中传播时遇到缺陷,既产生波的反射又产生波的衰减。
经过探伤仪的信号处理,如采用反射法探伤可获得缺陷回波信号,如采用穿透法探伤可凭借透过波的衰减程度获得缺陷信号。
二者均可由仪器给出定量的缺陷指示。
利用压电效应或电磁感应原理可在管内激发不同类型的超声波。
因此,压电超声和电磁超声均可用于管材超声波检验。
但电磁超声仅适用于铁磁性材料。
4、探伤方法(1)采用横波(或板波)反射法(或穿透法)在探头和钢管相对移动的状态下进行自动检验,只有特殊的大口径钢管才可进行手工检验。
自动或手工检验时均应保证声束对管子全部表面的扫查。
注:自动检验时对钢管两端将不能有效地检验,但此区域应控制在200mm以内。
(2)检验纵向缺陷时声束在管壁内沿圆周方向传播;检验横向缺陷时声束在管壁内滑管轴方向传播。
纵向和横向缺陷的检验均应在管子的两个相反方向上进行。
(3)在需方未提出检验横向缺陷时供方只检验纵向缺陷。
经供需双方协商同意,纵向和横向缺陷的检验均可只在管子的一个方向上进行。
(4)自动或手工检验时均应选用耦合效果良好并无损于钢管表面的耦合介质。
5、对比试样(1)用途对比试样用于探伤设备的调试、综合性能测试和使用过程中的定时校验。
对比试样上的人工缺陷是评定自然缺陷当量的依据,但不应理解为被检出的自然缺陷与人工缺陷的信号幅度相等时二者的尺寸必然相等。
超声波探伤实验报告

超声波探伤实验报告实验目的,通过超声波探伤技术,对不同材料的缺陷进行检测和分析,探究超声波在材料内部的传播规律,为材料质量检测提供依据。
实验原理,超声波探伤是利用超声波在材料中传播的特性,通过探头发射超声波,当超声波遇到材料内部的缺陷时,一部分超声波被反射回来,根据反射的超声波信号可以判断材料内部的缺陷情况。
实验材料,本次实验选用了铝合金、钢材和玻璃纤维增强塑料作为实验材料,这些材料在工程中应用广泛,对其进行超声波探伤具有一定的指导意义。
实验步骤:1. 准备工作,检查超声波探伤仪器和探头,确认其正常工作状态。
2. 样品制备,将铝合金、钢材和玻璃纤维增强塑料分别切割成不同尺寸的样品,确保样品表面平整、无明显损伤。
3. 超声波探伤,将超声波探头与样品表面紧密贴合,调节超声波探伤仪器,记录超声波在样品内部的传播情况。
4. 数据分析,根据实验数据,分析不同材料的超声波传播特点,判断样品内部是否存在缺陷,并对缺陷进行定性定量分析。
实验结果:1. 铝合金,经过超声波探伤,发现铝合金样品内部存在部分气孔和夹杂,这些缺陷对材料的强度和韧性造成一定影响。
2. 钢材,超声波探伤显示,钢材样品内部存在裂纹和夹杂,这些缺陷可能导致材料在使用过程中出现断裂。
3. 玻璃纤维增强塑料,实验结果表明,玻璃纤维增强塑料样品内部无明显缺陷,材料质量较好。
实验结论,超声波探伤技术可以有效检测不同材料的内部缺陷,为材料质量评估提供了一种可靠的手段。
通过本次实验,我们深入了解了超声波在材料内部的传播规律,为今后的材料质量检测工作提供了重要参考。
实验意义,超声波探伤技术在工程领域具有重要应用价值,可以用于航空航天、汽车制造、建筑结构等领域的材料质量检测和缺陷分析,对提高产品质量、保障工程安全具有重要意义。
通过本次实验,我们不仅学习了超声波探伤技术的基本原理和操作方法,还深入探讨了不同材料的超声波传播特性和内部缺陷情况,这对我们今后的工程实践具有重要的指导意义。
不锈钢管的超声波探伤方法简析5篇
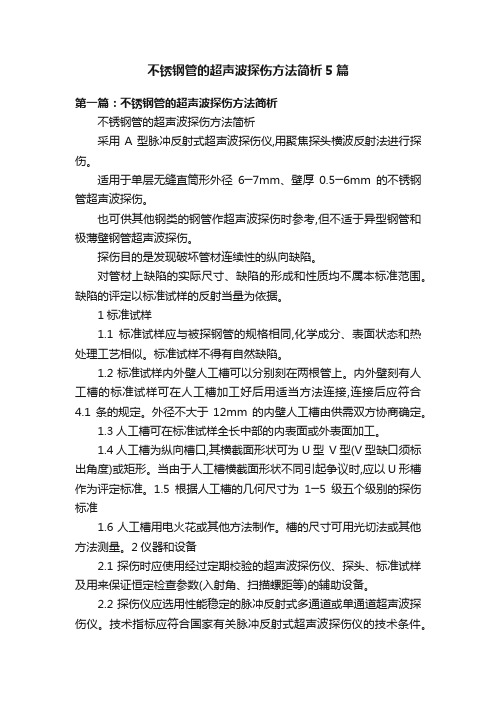
不锈钢管的超声波探伤方法简析5篇第一篇:不锈钢管的超声波探伤方法简析不锈钢管的超声波探伤方法简析采用A型脉冲反射式超声波探伤仪,用聚焦探头横波反射法进行探伤。
适用于单层无缝直筒形外径6─7mm、壁厚0.5─6mm的不锈钢管超声波探伤。
也可供其他钢类的钢管作超声波探伤时参考,但不适于异型钢管和极薄壁钢管超声波探伤。
探伤目的是发现破坏管材连续性的纵向缺陷。
对管材上缺陷的实际尺寸、缺陷的形成和性质均不属本标准范围。
缺陷的评定以标准试样的反射当量为依据。
1标准试样1.1标准试样应与被探钢管的规格相同,化学成分、表面状态和热处理工艺相似。
标准试样不得有自然缺陷。
1.2标准试样内外壁人工槽可以分别刻在两根管上。
内外壁刻有人工槽的标准试样可在人工槽加工好后用适当方法连接,连接后应符合4.1条的规定。
外径不大于12mm的内壁人工槽由供需双方协商确定。
1.3人工槽可在标准试样全长中部的内表面或外表面加工。
1.4人工槽为纵向槽口,其横截面形状可为U型V型(V型缺口须标出角度)或矩形。
当由于人工槽横截面形状不同引起争议时,应以U形槽作为评定标准。
1.5根据人工槽的几何尺寸为1─5级五个级别的探伤标准1.6人工槽用电火花或其他方法制作。
槽的尺寸可用光切法或其他方法测量。
2仪器和设备2.1探伤时应使用经过定期校验的超声波探伤仪、探头、标准试样及用来保证恒定检查参数(入射角、扫描螺距等)的辅助设备。
2.2探伤仪应选用性能稳定的脉冲反射式多通道或单通道超声波探伤仪。
技术指标应符合国家有关脉冲反射式超声波探伤仪的技术条件。
2.3探头选择频率为5─10MHz的线聚焦或点聚焦。
2.4机械传动设备除应符合4.3条的要求外,还应具有足够的精度。
3操作人员操作人员应由经有关无损检测鉴定部门考核取得Ⅲ级或Ⅲ级以上技术资格证书的人员担任。
4探伤条件及步骤4.1被探钢管的质量应符合有关技术标准的规定。
4.2用液浸法探伤时声耦合采用局部水浸法,耦合介质─水应保持洁净,无气泡,必要时可加入消气剂。
管道探伤报告
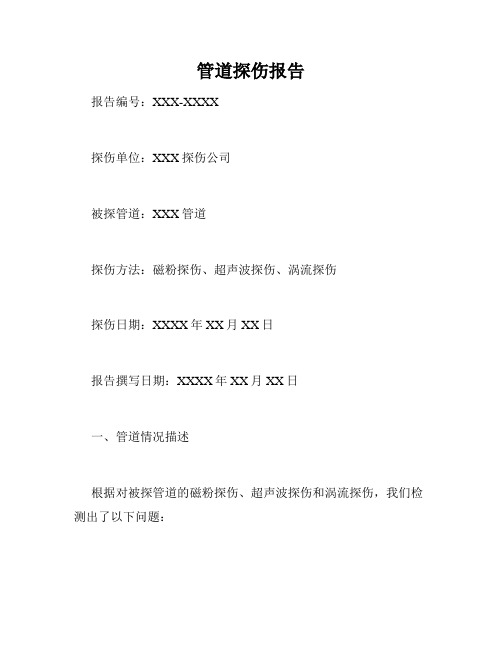
管道探伤报告
报告编号:XXX-XXXX
探伤单位:XXX探伤公司
被探管道:XXX管道
探伤方法:磁粉探伤、超声波探伤、涡流探伤
探伤日期:XXXX年XX月XX日
报告撰写日期:XXXX年XX月XX日
一、管道情况描述
根据对被探管道的磁粉探伤、超声波探伤和涡流探伤,我们检测出了以下问题:
1. 检测到管道表面存在3处较深的腐蚀点,最深处达到管道壁厚度的40%,需及时维修,避免出现泄漏事故。
2. 检测到管道焊缝存在一处裂纹,长度约为6mm,深度为
3mm,需立即修复。
3. 检测到管道的部分区域存在局部变形,造成了管道壁厚度的下降,需要找到原因及时修复。
二、建议及处理方案
1. 对于存在的腐蚀问题,建议采取刷涂防腐或更换管道的方式来解决。
2. 针对管道焊缝的裂纹问题,必须采用提供的焊接规范来保证焊缝的焊接质量。
3. 针对存在局部变形的管道部分,涡流探伤可用于检测管道内部的变形原因。
根据检测结果制定相应的处理方案。
三、结论
通过本次管道探伤,我们发现了管道存在的问题,并提出了相应的处理方案。
建议相关单位及时采取措施修复管道缺陷,以确保管道的安全稳定运行。
管材超声波探伤之欧阳文创编

第四节管材超声波探伤一、管材加工及常见缺陷管材种类很多,据管径不同分为小口径管和大口径管,据加工方法不同分为无缝钢管和焊接管。
无缝钢管是通过穿孔法和高速挤压法得到的,穿孔法是用穿孔机穿孔。
并同时用轧辊滚轧,最后用心棒轧管机定径压延平整成型。
高速挤压法是在挤压机中直接挤压成形,这中方法加工的管材尺寸精度高。
焊接管是先将板材卷成管形,然后用电阻焊或埋弧自动焊加工成型。
一般大口径管多用这种方法加工。
对于厚壁大口径管也可由钢锭经锻造、轧制等工艺加工而成。
管材中常见缺陷与加工方法有关。
无缝钢管中常见缺陷有裂纹、折迭、夹层等。
焊接管中常见缺陷与焊缝类似,一般为裂纹、气孔、夹渣、未焊透等.锻轧管常见缺陷与锻件类似,一般为裂纹、白点、重皮等。
用于高温、高压的管材及其它特殊用途的重要管材都必须进行超声波探伤。
据管材不同,分为钢管、铜管和铝管等。
下面以钢管为例来说明管材的超声波探伤方法:二、小口径管探伤超声波探伤的小口径管是指外径小于100mm的管材。
这种管材一般为无缝管,采用穿孔法或挤压法得到。
其中主要缺陷平行于管轴的径向缺陷(称纵向缺陷),有时也有垂直于轴的径向缺陷(称横向缺陷)。
对于管内纵向缺陷,一般利用横波进行周向扫查探测,如图5.23所示。
对于管内横向缺陷,一般利用横波进行轴向扫查探测,如图5.24所示。
按耦合方式不同,小口径管探伤分为接触法探伤和水浸法探伤。
(一)接触法探伤接触法探伤是指探头通过薄层耦合介质与钢管直接接触进行探伤的方法。
这种方法一般为受动探伤,检测效率低,但设备简单,操作方便,机动灵活性强。
适用于单件小批量及规格多的倩况。
接触法探伤小口径管时,由于其管径小,曲率大,常规横波斜探头与管材接触面小、耦合不良,波束严重扩散,灵敏度低。
为了改善耦合条件。
常将探头有机玻璃斜楔加工成与管材表面相吻合的曲面。
为了提高探伤灵敏度,可以采用接触聚焦探头来探伤。
下面分别介绍纵向缺陷和横向缺陷的一般探伤方法。
- 1、下载文档前请自行甄别文档内容的完整性,平台不提供额外的编辑、内容补充、找答案等附加服务。
- 2、"仅部分预览"的文档,不可在线预览部分如存在完整性等问题,可反馈申请退款(可完整预览的文档不适用该条件!)。
- 3、如文档侵犯您的权益,请联系客服反馈,我们会尽快为您处理(人工客服工作时间:9:00-18:30)。
管材超声波探伤集团文件版本号:(M928-T898-M248-WU2669-I2896-DQ586-M1988)第四节管材超声波探伤一、管材加工及常见缺陷管材种类很多,据管径不同分为小口径管和大口径管,据加工方法不同分为无缝钢管和焊接管。
无缝钢管是通过穿孔法和高速挤压法得到的,穿孔法是用穿孔机穿孔。
并同时用轧辊滚轧,最后用心棒轧管机定径压延平整成型。
高速挤压法是在挤压机中直接挤压成形,这中方法加工的管材尺寸精度高。
焊接管是先将板材卷成管形,然后用电阻焊或埋弧自动焊加工成型。
一般大口径管多用这种方法加工。
对于厚壁大口径管也可由钢锭经锻造、轧制等工艺加工而成。
管材中常见缺陷与加工方法有关。
无缝钢管中常见缺陷有裂纹、折迭、夹层等。
焊接管中常见缺陷与焊缝类似,一般为裂纹、气孔、夹渣、未焊透等.锻轧管常见缺陷与锻件类似,一般为裂纹、白点、重皮等。
用于高温、高压的管材及其它特殊用途的重要管材都必须进行超声波探伤。
据管材不同,分为钢管、铜管和铝管等。
下面以钢管为例来说明管材的超声波探伤方法:二、小口径管探伤超声波探伤的小口径管是指外径小于100mm的管材。
这种管材一般为无缝管,采用穿孔法或挤压法得到。
其中主要缺陷平行于管轴的径向缺陷(称纵向缺陷),有时也有垂直于轴的径向缺陷(称横向缺陷)。
对于管内纵向缺陷,一般利用横波进行周向扫查探测,如图5.23所示。
对于管内横向缺陷,一般利用横波进行轴向扫查探测,如图5.24所示。
按耦合方式不同,小口径管探伤分为接触法探伤和水浸法探伤。
(一)接触法探伤接触法探伤是指探头通过薄层耦合介质与钢管直接接触进行探伤的方法。
这种方法一般为受动探伤,检测效率低,但设备简单,操作方便,机动灵活性强。
适用于单件小批量及规格多的倩况。
接触法探伤小口径管时,由于其管径小,曲率大,常规横波斜探头与管材接触面小、耦合不良,波束严重扩散,灵敏度低。
为了改善耦合条件。
常将探头有机玻璃斜楔加工成与管材表面相吻合的曲面。
为了提高探伤灵敏度,可以采用接触聚焦探头来探伤。
下面分别介绍纵向缺陷和横向缺陷的一般探伤方法。
1.纵向缺陷探测(1)探头:探测纵向缺陷的斜探头,应加工成如图5.23所示的形状,使之与工件表面吻合良好。
探头压电晶片的长度或直径不大于25mm,探头的频率为2.5~5.0MHz。
(2)试块:探测纵向缺陷的对比试块应选取与被检管材规格相同,材质、热处理及表面状态相同或相似的管材制成。
对比试块上的人工缺陷为尖角槽,尖角槽的位置和尺寸见图5.25和表5.5。
(3)灵敏度调节:探头置于对比试块上作周向扫查探测,将试块上内壁尖角槽的最高回波调至满幅度的80%,再移动探头找外壁尖角槽的最高回波。
二者波峰的连线为距离一波幅曲线,作为基准灵敏度。
在基准灵敏度的基础上提高6dB作为扫查灵敏度。
(4)扫查探测:探头沿径向按螺旋线进行扫查探测。
具体扫查方式有三种:一是探头不动,管材旋转的同时作轴向移动。
二是探头作轴向移动,管材作转动。
三是管材不动,探头沿螺旋线运动。
探头扫查螺旋线的螺距不能太大,要保证超声波束对管材进行100%扫查,并有不小于15%的覆盖。
在扫查探测过程中,当发现缺陷时,要将仪器调整到基准灵敏度、若缺陷回波幅度≥基准灵敏度,则判为不合格。
不合格晶允许在公差范围内采取修磨方法进行处理。
然后再复探管材合格级别由供需双方商定。
2.横向缺陷的探测(1)探头:探测横向缺陷的探头应加工成如图5.24所示的形状,探头的晶片长度或直径不大于25mm,探头的频率为2.5~5.0MHz。
(2)试块:探测横向缺陷用的对比试块,同样应选用与被检管材规格相同,材质、热处理及表面状态相同或相似的管材制成。
对比试块上的人工缺陷为周向尖角槽,尖角槽位置和尺寸见图5.26和表5.6对出试块上人工缺陷一般加工在外表面,只有当D≥80mm,且壁厚t≥10mm时,才同时在内外表面加工人工缺陷。
二者在轴向要有足够的距离,以免测试时互相影响。
(3)灵敏度调节:对于只有外表面人工缺陷的试块,可直接将对比试块上的人工缺陷最高回波调至50%作为基准灵敏度。
对于内外表面均有人工缺陷的试块.应将内表面人工缺陷最高回波凋至80%,然后找到外表面人工缺陷最高回波,二者波峰的连线为距离一波幅曲线,该曲线为基准灵敏度。
在基准灵敏度的基础上提高6dB作为扫查灵敏度。
(4)扫查探测:探头沿轴向按螺旋线进行扫查探测。
当发现缺陷时,仪器调回到基准灵敏度,若缺陷回波幅度≥基准灵敏度,则该管材为不合格。
不合格品允许在公差范围内进行修磨,修磨后复探。
合格级别由供需双方商定。
(二)水浸探伤小口径管水漫探伤是将水浸纵波探头置于水中,利用纵波倾斜入射到水/钢界面。
当入射角a=a1~a1时,可在钢管内实现纯横波探测。
如图5.29所示。
1.探测参数的选择(1)偏心距的选择:如图5.27所示,偏心距是指探头声束轴线与管材中心轴线的水平距离,常用χ表示。
入射角a随偏心距χ增大而增大,控制χ就可控制a。
偏心距范围由以下两个条件决定。
①纯横波探测条件②横波探测内壁条件同时满足纯横波探测内壁的条件为(5.5)对于水浸探伤钢管,cL1=1480m/s,cL2=5900m/s,cs2=3230m/s,有:0.251R≤χ0.458r (5.6)(5.7)式中?R一一小径管外半径;r—一小径管内半径。
(2)水层厚度的选择:如图5.28,在水浸探伤中.要求水层厚度日大于钢管中横波全声程的l/2(即H>χs)。
这是因为水中C水=14380m/s,钢中Cs=3230m/s,C水/Cs≈1/2。
当水层厚度大于钢管中横波声程的1/2时,水/钢界面的第二次回波S2将位于管子的缺陷波F内(一次波)、F外(二次波)之后,这样有利于对缺陷的判别。
(3)焦距的选择:用水浸聚焦探头探伤小径管,应使探头的焦点落在与声束轴线垂直的管心线上,如图5.29所示。
式中 F——焦距;H——水层厚度;R——钢管外半径:χ——偏心距。
例1,用有机玻璃聚焦探头水浸探伤φ42×4小管径,已知水中c水=1480m/s,钢中cL2=5900m/s,cL2=3230m/s。
求偏心距χ,水层厚度H,透镜曲率半径r′。
解:(1)求偏心距χ(平均值) R=21,r=R-t=21-4=17(2)求水层厚度H③求钢中横波全声程之半χ在图5.28的△ABO中,由正弦定律得又由正弦定律得④水层厚度选取:H>6.2mm,这里取H=10mm。
(3)求焦距F(4)求声透镜曲率半径r′由F=2.2r′得r′=0.455F=30×0.455=13.7(mm)例2,水浸聚焦探伤φ60×8小径管,声透镜曲率半径r′=36mm,求偏心距χ和水层厚度H。
解:(1)偏心距χ(2)求焦距FF=2.2r′-2.2×36=79.2(mm)(3)求水层厚度H2.探测条件的确定(1)探头;小径管水浸探伤,一般采用聚焦探头。
聚焦探头分为线聚焦和点聚焦。
一般钢管采用线聚焦探头。
对于薄壁管,为了提高检测能力,也可用点聚焦探头。
探头的频率为2.5~5.0MHz。
聚焦探头声透镜的曲率半径r应符合下述条件:(5.9)式中?C——声透镜中纵波波速;1C 2——水中波速;F ——水中焦距。
对于有机玻璃声透镜:C 1=2730m/s ,C 2=1480m/s(2)声耦合:小管径探伤常用耦合剂为水。
为了增强对钢管表面的润湿作用,需加入少量活性剂。
为了防止钢管生锈,需加入适量的防锈剂。
(3)扫查方式;小径管探伤时探头扫查方式为螺旋线。
一是探头不动,钢管作螺旋运动;二是探头沿管轴转动,钢管直线运动。
三是探头沿管移动,钢管转动。
螺距应小于或等予探头声束有效宽度,探头移动速度u 为U=n·t (5.10)式中 n ——管子转速;t ——螺距。
3.探伤灵敏度的调整和质量评定小管径探伤时,常用如图5.26所示的内外壁开有人工尖角槽的对比试样来调整灵敏度,试样材质及规格同被探钢管。
调整时,转动水中试样使内外壁人工槽回波均达50%基准高,以此作为基准灵敏度。
扫查探伤灵敏度比基准灵敏度高6dB 。
探伤中当缺陷回波≥基准灵敏度时,就判为不合格。
不合格品允许在壁厚的公差范围内进行打磨,然后再复探。
三、大口径管探伤超声波探伤中,大口径管一般是指外径大于100mm 的管材。
大口径管曲率半径较大,探头与管壁声耦合较好,通常采用接触法探伤.批量较大时也可采用水浸探伤。
采用接触法探伤时,若管径不太大,为了实现更好的耦合,需将探头斜楔磨成与管材表面相吻合的曲面,也可在探头加装与管材吻合良好的滑块,如图5.30所示。
1.探测方法的选择大口径管成型方法较多,如穿孔法、高速挤压法、锻造法和焊接法等。
因此大口径管内缺陷比较复杂。
既可能有平行于轴线的径向和周向缺陷,又可能有垂直于轴线的径向缺陷。
不同类型的缺陷需要采用不同的方法来探测。
常用的方法有纵波垂直探伤法,横波周向、轴向探伤法。
(1)纵渡垂直探伤法:如图5.31所示,对于与管轴平行的周向缺陷,一般采用纵波单直探头或联合双直探头探伤。
当缺陷较小时,缺陷波F与底波B同时出现。
这时可根据F波的高度来评价缺陷的当量大小。
当缺陷较大时,底波B将会消失,这时可用半波高度法来测定缺陷的面积大小。
(2)横波周向探伤法:如图5.32所示,对于与管轴平行的径向缺陷,常采用横渡单斜探头或双斜探头进行周向探测。
单斜探头探伤如图5.32(a),这时缺陷的粼剐与普通斜探头探伤类似。
考虑到缺陷的取向不同,探测时,探头应作正反两个方向的全面扫查,以免漏检。
双斜探头探伤如图5.32(b),这时两个探头单独收发,同一缺陷在示波屏上可能同时出现两个缺陷波,如图中F′、F″就是探头1、2接收到的同一缺陷回波,它们处于180°的两侧对称位置。
当探头沿管外壁作周向移动时,F′、F″在180°的两侧作对称移动。
据此可对缺陷进行判别。
(3)横波轴向探伤法:如图5.33所示,对于与管轴垂直的径向缺陷,常用单斜探头或联合双斜探头进行轴向探伤。
图5.33(a)为单斜探头探伤,这时声束在内壁的反射波更进一步发散,声能损失大,因此外壁缺陷灵敏度较低,探伤时要注意这一点。
图5.33(b)为联合双斜探头探伤,这时只要内外壁缺陷处于两晶片发射声场交集区内,则内外壁缺陷灵敏度基本一致。
(4)水浸聚焦探伤法:图5.34为水浸聚焦探伤大口径管堵塞情况,这时聚焦探头声束敛聚。
能量集中,灵敏度高。
一般采用线聚焦探头,焦点调在管材中心线上。
这样横波声柬在管内外壁多次反射,产生多次敛聚发散。
在整个管子截面上形成平均宽度基本一致的声束,这样不仅探伤灵敏度较高,而且内外壁缺陷检出灵敏度大致相同。
2.周向探伤缺陷定位与修正横波轴向探伤管材时,缺陷定位与平板工件类似,但横波周向探伤时,缺陷定位与平板工停不同,如图5.35所示,这时不但入射到管材内壁的入射角增加了,而且一次波声程和跨距也都增加了。