复合材料、板材和管材超声波探伤检测方法
金属管道超声波无损检测方法的研究
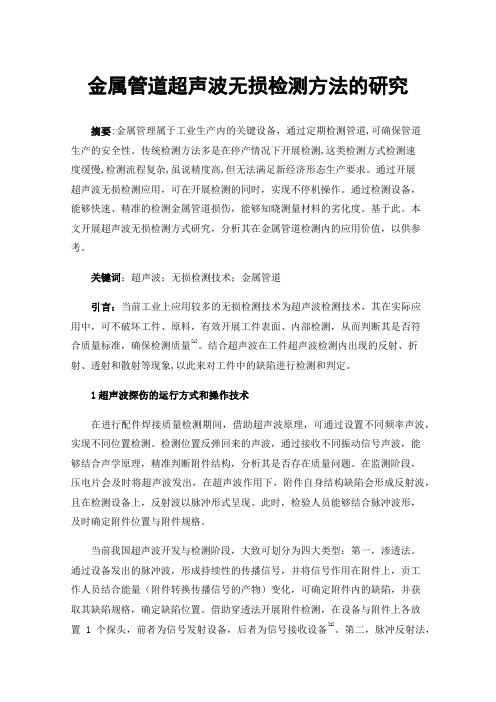
金属管道超声波无损检测方法的研究摘要:金属管理属于工业生产内的关键设备,通过定期检测管道,可确保管道生产的安全性。
传统检测方法多是在停产情况下开展检测,这类检测方式检测速度缓慢,检测流程复杂,虽说精度高,但无法满足新经济形态生产要求。
通过开展超声波无损检测应用,可在开展检测的同时,实现不停机操作。
通过检测设备,能够快速、精准的检测金属管道损伤,能够知晓测量材料的劣化度。
基于此。
本文开展超声波无损检测方式研究,分析其在金属管道检测内的应用价值,以供参考。
关键词:超声波;无损检测技术;金属管道引言:当前工业上应用较多的无损检测技术为超声波检测技术,其在实际应用中,可不破坏工件、原料,有效开展工件表面、内部检测,从而判断其是否符合质量标准,确保检测质量[1]。
结合超声波在工件超声波检测内出现的反射、折射、透射和散射等现象,以此来对工件中的缺陷进行检测和判定。
1超声波探伤的运行方式和操作技术在进行配件焊接质量检测期间,借助超声波原理,可通过设置不同频率声波,实现不同位置检测。
检测位置反弹回来的声波,通过接收不同振动信号声波,能够结合声学原理,精准判断附件结构,分析其是否存在质量问题。
在监测阶段,压电片会及时将超声波发出,在超声波作用下,附件自身结构缺陷会形成反射波,且在检测设备上,反射波以脉冲形式呈现。
此时,检验人员能够结合脉冲波形,及时确定附件位置与附件规格。
当前我国超声波开发与检测阶段,大致可划分为四大类型:第一,渗透法。
通过设备发出的脉冲波,形成持续性的传播信号,并将信号作用在附件上,贡工作人员结合能量(附件转换传播信号的产物)变化,可确定附件内的缺陷,并获取其缺陷规格,确定缺陷位置。
借助穿透法开展附件检测,在设备与附件上各放置1个探头,前者为信号发射设备,后者为信号接收设备[2]。
第二,脉冲反射法,工作人员通过发射波,可及时检测附件缺陷,整个检测过程开展基于缺陷回波法基础上开展,借助仪器设备快可及时获取相关信息。
管材超声波探伤
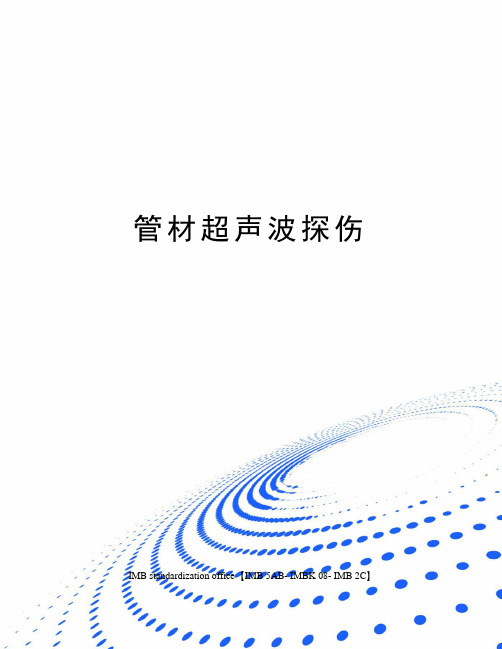
管材超声波探伤 IMB standardization office【IMB 5AB- IMBK 08- IMB 2C】第四节管材超声波探伤一、管材加工及常见缺陷管材种类很多,据管径不同分为小口径管和大口径管,据加工方法不同分为无缝钢管和焊接管。
无缝钢管是通过穿孔法和高速挤压法得到的,穿孔法是用穿孔机穿孔。
并同时用轧辊滚轧,最后用心棒轧管机定径压延平整成型。
高速挤压法是在挤压机中直接挤压成形,这中方法加工的管材尺寸精度高。
焊接管是先将板材卷成管形,然后用电阻焊或埋弧自动焊加工成型。
一般大口径管多用这种方法加工。
对于厚壁大口径管也可由钢锭经锻造、轧制等工艺加工而成。
管材中常见缺陷与加工方法有关。
无缝钢管中常见缺陷有裂纹、折迭、夹层等。
焊接管中常见缺陷与焊缝类似,一般为裂纹、气孔、夹渣、未焊透等.锻轧管常见缺陷与锻件类似,一般为裂纹、白点、重皮等。
用于高温、高压的管材及其它特殊用途的重要管材都必须进行超声波探伤。
据管材不同,分为钢管、铜管和铝管等。
下面以钢管为例来说明管材的超声波探伤方法:二、小口径管探伤超声波探伤的小口径管是指外径小于100mm的管材。
这种管材一般为无缝管,采用穿孔法或挤压法得到。
其中主要缺陷平行于管轴的径向缺陷(称纵向缺陷),有时也有垂直于轴的径向缺陷(称横向缺陷)。
对于管内纵向缺陷,一般利用横波进行周向扫查探测,如图所示。
对于管内横向缺陷,一般利用横波进行轴向扫查探测,如图所示。
按耦合方式不同,小口径管探伤分为接触法探伤和水浸法探伤。
(一)接触法探伤接触法探伤是指探头通过薄层耦合介质与钢管直接接触进行探伤的方法。
这种方法一般为受动探伤,检测效率低,但设备简单,操作方便,机动灵活性强。
适用于单件小批量及规格多的倩况。
接触法探伤小口径管时,由于其管径小,曲率大,常规横波斜探头与管材接触面小、耦合不良,波束严重扩散,灵敏度低。
为了改善耦合条件。
常将探头有机玻璃斜楔加工成与管材表面相吻合的曲面。
复合材料探伤方法

复合材料探伤方法
复合材料探伤方法是指用于检测复合材料中可能存在的缺陷或损伤的方法。
常用的复合材料探伤方法有以下几种:
1. 超声波探伤:通过超声波的传播和反射来检测材料内部的缺陷。
适用于检测复合材料的层间和层内缺陷。
2. 热红外成像:利用材料中缺陷的热传导性质来检测缺陷。
适用于检测复合材料中的局部缺陷。
3. X射线检测:利用X射线的透射和散射特性来检测材料的
缺陷和内部结构。
适用于检测复合材料中的金属缺陷和层间胶接质量。
4. 磁粉检测:通过在材料表面涂布磁粉,利用磁场的作用,观察磁粉在缺陷处积聚的情况,来检测材料的缺陷。
5. 声发射检测:利用材料在受到外力作用时会发生微小的声发射来检测材料的缺陷。
适用于检测复合材料的疲劳损伤和局部破裂。
6. 电磁波探测:利用电磁波的透射和反射特性来检测材料的缺陷。
可以应用于复合材料的层间和层内缺陷及电磁性能的检测。
以上是常用的复合材料探伤方法,其选择取决于复合材料的结构和要检测的缺陷类型。
不同的方法和设备可以相互补充和验证,提高探测的准确性和可靠性。
无损检测超声探伤UT基础讲义 (1)

培训教材之理论基础第一章无损检测概述无损检测包括射线检测(RT)、超声检测(UT)、磁粉检测(MT)、渗透检测(PT)和涡流检测(ET)等五种检测方法。
主要应用于金属材料制造的机械、器件等的原材料、零部件和焊缝,也可用于玻璃等其它制品。
射线检测适用于碳素钢、低合金钢、铝及铝合金、钛及钛合金材料制机械、器件等的焊缝及钢管对接环缝。
射线对人体不利,应尽量避免射线的直接照射和散射线的影响。
超声检测系指用A型脉冲反射超声波探伤仪检测缺陷,适用于金属制品原材料、零部件和焊缝的超声检测以及超声测厚。
磁粉检测适用于铁磁性材料制品及其零部件表面、近表面缺陷的检测,包括干磁粉、湿磁粉、荧光和非荧光磁粉检测方法。
渗透检测适用于金属制品及其零部件表面开口缺陷的检测,包括荧光和着色渗透检测。
涡流检测适用于管材检测,如圆形无缝钢管及焊接钢管、铝及铝合金拉薄壁管等。
磁粉、渗透和涡流统称为表面检测。
第二章超声波探伤的物理基础第一节基本知识超声波是一种机械波,机械振动与波动是超声波探伤的物理基础。
物体沿着直线或曲线在某一平衡位置附近作往复周期性的运动,称为机械振动。
振动的传播过程,称为波动。
波动分为机械波和电磁波两大类。
机械波是机械振动在弹性介质中的传播过程。
超声波就是一种机械波。
机械波主要参数有波长、频率和波速。
波长?:同一波线上相邻两振动相位相同的质点间的距离称为波长,波源或介质中任意一质点完成一次全振动,波正好前进一个波长的距离,常用单位为米(m);频率f:波动过程中,任一给定点在1秒钟内所通过的完整波的个数称为频率,常用单位为赫兹(Hz);波速C:波动中,波在单位时间内所传播的距离称为波速,常用单位为米/秒(m/s)。
由上述定义可得:C=? f ,即波长与波速成正比,与频率成反比;当频率一定时,波速愈大,波长就愈长;当波速一定时,频率愈低,波长就愈长。
次声波、声波和超声波都是在弹性介质中传播的机械波,在同一介质中的传播速度相同。
超声波检测的基本方法-a
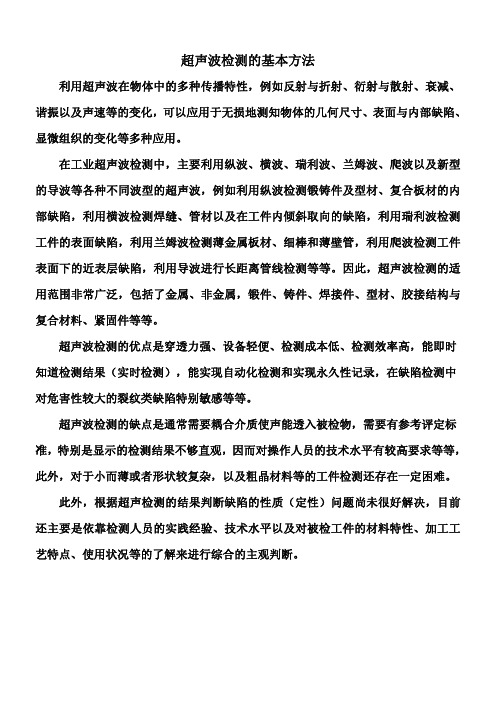
超声波检测的基本方法利用超声波在物体中的多种传播特性,例如反射与折射、衍射与散射、衰减、谐振以及声速等的变化,可以应用于无损地测知物体的几何尺寸、表面与内部缺陷、显微组织的变化等多种应用。
在工业超声波检测中,主要利用纵波、横波、瑞利波、兰姆波、爬波以及新型的导波等各种不同波型的超声波,例如利用纵波检测锻铸件及型材、复合板材的内部缺陷,利用横波检测焊缝、管材以及在工件内倾斜取向的缺陷,利用瑞利波检测工件的表面缺陷,利用兰姆波检测薄金属板材、细棒和薄壁管,利用爬波检测工件表面下的近表层缺陷,利用导波进行长距离管线检测等等。
因此,超声波检测的适用范围非常广泛,包括了金属、非金属,锻件、铸件、焊接件、型材、胶接结构与复合材料、紧固件等等。
超声波检测的优点是穿透力强、设备轻便、检测成本低、检测效率高,能即时知道检测结果(实时检测),能实现自动化检测和实现永久性记录,在缺陷检测中对危害性较大的裂纹类缺陷特别敏感等等。
超声波检测的缺点是通常需要耦合介质使声能透入被检物,需要有参考评定标准,特别是显示的检测结果不够直观,因而对操作人员的技术水平有较高要求等等,此外,对于小而薄或者形状较复杂,以及粗晶材料等的工件检测还存在一定困难。
此外,根据超声检测的结果判断缺陷的性质(定性)问题尚未很好解决,目前还主要是依靠检测人员的实践经验、技术水平以及对被检工件的材料特性、加工工艺特点、使用状况等的了解来进行综合的主观判断。
工业超声波检测方法的一般原理与分类一.根据采用超声波的种类分类(一)脉冲波法:超声波探头激发的是脉冲超声波,这是具有一定持续时间、按一定重复频率间歇发射的超声波,通常具有较大的频带宽度。
(1)脉冲波反射法:在超声波检测时,向被检对象发射脉冲超声波,利用超声波的反射特性,根据有无缺陷回波或工件底面反射回波、回波幅度的大小、回波信号数量、回波在示波屏时基线上的位置以及回波包络形状变化等对被检对象的质量情况进行评价。
UT超声波检测系列之超声波探伤工艺细则

附录B 超声波探伤工艺细则1目的该项工艺细则,对压力容器产品的超声波探伤实施有效控制。
2适用范围本规程适用于原材料板材及管材的探伤,并且也适用于加工产品锻件、铸件、焊接件的探伤。
3按波形分类1)纵波法使用直探头发射纵波进行探伤的方法,称为纵波法。
此法常将波束垂直入射至试件探测面,以不变的波形和方向透入试件,所以又称垂直法。
垂直法主要用于铸造、锻压、轧材及其制品的探伤。
2)横波法将纵波通过楔块、水等介质倾斜入射至试件探射面,利用波形转换得到横波进行探伤的方法,称为横波法。
此方法主要适用于管材及焊缝的探伤。
3)表面波法使用表面波进行探伤的方法,称为表面波法。
这种方法主要用于表面光滑的试件。
4)板波法使用板波法进行探伤的方法,主要用于薄板、薄壁管等形状简单的试件探伤。
4按探头数目分类1)单探头法使用一个探头兼作发射和接收超声波的探伤方法称为单探头法。
单探头法操作方便,大多数缺陷可以检出。
2)双探头法使用两个探头进行探伤的方法称为双探头法。
一个发射,一个接收。
主要是为发现单探头法难以检出的缺陷。
5探头的选择1)直探头直探头只能发射和接收纵波,波束轴线垂直于探测面。
主要用于探测与探测面平行的缺陷,如锻件、钢板中的夹层、折叠等缺陷。
2)斜探头(横波)斜探头是通过波形转换来实现横波探伤的,主要用于探测与探测面垂直或成一定角度的缺陷。
如焊缝中的未焊透、夹渣及未融合等缺陷。
3)表面波探头与双晶(分割)探头表面波探头用于探测工件表面缺陷;双晶探头用于探测工件近表面缺陷;聚焦探头用于水浸探测管材或板材。
6耦合剂超声偶合是指超声波在探测面上的声强透射率。
为了提高耦合效果,在探头与工件表面之间施加的一层透声介质称为耦合剂。
超声波探伤中常用耦合剂有机油、变压器油、甘油、水、水玻璃等。
更多资料:无损检测招聘网 中国无损检测论坛 中国焊接论坛 说明:本《超声波检测工艺规程》由检验处探伤室起草,并负责对其内容进行解释。
超声波探伤检测标准

超声波探伤检测标准:原理、应用与发展一、引言超声波探伤检测是一种广泛应用于工业领域的无损检测技术,通过对材料内部结构的声波传播特性进行分析,实现对材料缺陷、裂纹等问题的检测。
本文将从超声波探伤检测的原理、应用和发展趋势等方面进行详细阐述,以期提高读者对该技术的认识和了解。
二、超声波探伤检测原理超声波探伤检测是利用超声波在材料中传播的特性来检测材料内部缺陷的一种方法。
当超声波遇到材料内部的缺陷时,如裂纹、气孔等,声波的传播路径会发生变化,导致声波的能量衰减、反射或散射。
通过对反射或散射回来的声波信号进行分析和处理,可以确定材料内部缺陷的位置、大小和类型。
三、超声波探伤检测应用1. 金属材料检测:超声波探伤检测在金属材料检测中应用广泛,如钢铁、铝合金等。
通过对材料内部缺陷的检测,可以有效地控制产品质量,避免潜在的安全隐患。
2. 复合材料检测:随着复合材料在航空航天、汽车等领域的广泛应用,对其内部缺陷的检测需求也日益突出。
超声波探伤检测可以实现对复合材料内部缺陷的高精度检测,为产品的质量和安全性提供保障。
3. 压力容器检测:压力容器是工业领域中常见的设备,其安全性至关重要。
超声波探伤检测可以实现对压力容器焊缝、壁厚等部位的检测,确保其符合相关标准和规定。
4. 管道检测:管道输送是工业生产中的重要环节,而管道的安全性和可靠性直接关系到生产的安全和效率。
超声波探伤检测可以实现对管道焊缝、腐蚀等问题的检测,为管道的维护和修复提供依据。
四、超声波探伤检测发展趋势1. 高精度与高效率:随着科技的不断进步,对超声波探伤检测的精度和效率提出了更高的要求。
未来的发展趋势是在保证精度的前提下,提高检测速度,实现高效、快速的检测。
2. 多功能化:为满足不同材料和结构的检测需求,超声波探伤检测设备需要具备多种功能,如多频率、多角度等。
未来的发展趋势是研发具备更多功能的检测设备,以适应不同应用场景的需求。
3. 智能化与自动化:随着人工智能和自动化技术的发展,对超声波探伤检测的智能化和自动化程度提出了更高的要求。
超声波检测方法分类与特点
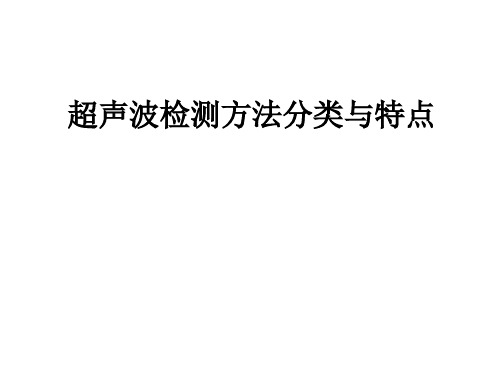
• 垂直法主要用于铸造、锻压、轧材及其制 品的检测, 该法对于与检测面平行的缺陷检 出效果最佳。由于垂直法检测时, 波型和传 播方向不变, 所以缺陷定位比较方便。
2.纵波斜探头法 将纵波倾斜入射至工件检测面,利用折射纵波
进行检测的方法,称为纵波斜探头法。此时,入射 角小于第一临界角a一,工件中既有纵波也有横波 ,由于纵波传播速度快,几乎是横波的两倍,因此 可利用纵波来识别缺陷和定量,但注意不要与横波 信号混淆。
• 相控阵可实现多种扫描成像方式,如前 所述的B、C.D扫描成像,较为特殊的是还可 形成S扫描成像,即在某入射点形成一定角
度的扇形扫查范围,又称扇形扫描成像, 如图5-21所示。
超声相控阵技术的优势在于: (1)由于可采用电子控制方法控制声束进行扫查,可在不移
动或少移动探头的情况下进行快速线扫查或扇形扫查, 从而大大提高了检测效率。
(2)由于可对声束角度进行控制,具有良好的声束可达性, 通过多个检测角度的设定, 可以进行复杂形状和在役 零件的检测。如核反应堆压力容器管嘴和其他接头、摩 擦焊发动机组件、发动机盘件及叶片的根部和叶盘结合 部的检测。
(3)通过动态控制声束的偏转和聚焦,可以实现焦点位置 的动态控制,避免了普通聚焦探头为实现全深度聚焦检 测而对不同深度范围频繁更换探头的麻烦。
• 阵元探头相位控制, 合成声束技术(移动, 转 角, 聚焦, 采样相控阵技术(SAMPLING PHASED ARRAY )
1.B、C.D扫描成像
– 扇形B扫描 – 线形B扫描 – 组合B扫描
• B型显示(亮度-时间扫查记录)
• B型显示(斜探头PE平行扫查)
• B型显示(TOFD非平行扫查)
• 5.1.4 共振法
• 依据试件的共振特性来判断缺陷情况和工 件厚度变化情况的方法称为共振法。常用 于试件测厚。共振法测厚的原理见4.1.6, 目 前已很少使用
板材超声波探伤

△ 利 用 F1 评 价 缺 陷 。 出 现 叠 加 效 应 时 , 当 板 厚 较 薄 时 可 用 F2 评 价 缺 陷 , 其 目 的 是 减 少 近 场 区 影 响 。 实 际 上 , 应 根 据 晶 片 直 径 的 尺 寸 大 小 及 F1 不 清 晰 时 , 可 用 F2 来 评 价 缺 陷 , 用 F2 和 B2 评 价 时 , 基 准 灵 敏 度 以 第二次反射波校正。 如 采 用 直 径 为 Ф 14 m m ~ 20 m m 的 直 探 头 探 伤 钢 板 , 一 般 当 板 厚 δ < 20 m m 时 , 可 采 用 F 2 评 价 缺 陷 。 1.3 探 头 与 扫 查 方 式 1. 3.1 频 率 2.5 ~ 5MHz ,40mm 以 下 钢 板 检 测 频 率 为 5MHz ,40mm 以 上 钢 板 检 测 频 率 为 2.5MHz 晶 片 直 径 : Ф14 ~ Ф25mm 探头形式: 单晶直探头 钢板检测 联合双晶直探头 适用于板厚 δ 较薄的钢板检测,因盲区小, 适 用 于 板 厚 δ 较 大 的 钢 板 检 测 ,用 于 20mm 以 上
1.7
钢板横波检验按附录 B 规定要求 非夹层性缺陷
适用范围 探头
K1 2MHz~5MHz 25mm 长 V 形 槽 深 为 板 厚 3 % V 形槽的距离-波幅曲线, 按 不 同 板 厚 根 据 B.4 规 定 调 节
人工缺陷 灵敏度
验 收 标 准 按 B.6 规 定 : 等 于 或 超 过 距 离 - 波 幅 曲 线 信 号 不 合 格 , 发现分层类缺陷按纵波检测规定处理。
8 / 26
1.6 质 量 等 级 判 定 : 按 JB/T4730-2005 标 准 4.1.7 条 规 定 评 定 。 单 个 缺 陷 指 示 长 度 按 4.1.7.1 规 定 , 单 个 缺 陷 指 市 面 积 按 4.1.7.2 规 定 。 JB/T4730-2005 标 准 标 准 中 表 3 钢 板 质 量 分 级 表 中 数 据 适 用 于 非 白点、裂纹等危险缺陷,即非危险缺陷。白点、裂纹等危险缺 陷,都判为 V 级。
超声波探伤

超声波探伤超声波探伤是利用超声能透入金属材料的深处,并由一截面进入另一截面时,在界面边缘发生反射的特点来检查零件缺陷的一种方法,当超声波束自零件表面由探头通至金属内部,遇到缺陷与零件底面时就分别发生反射波,在荧光屏上形成脉冲波形,根据这些脉冲波形来判断缺陷位置和大小。
1基本原理超声波在介质中传播时有多种波型,检验中最常用的为纵波、横波、表面波和板波。
用纵波可探测金属铸锭、坯料、中厚板、大型锻件和形状比较简单的制件中所存在的夹杂物、裂缝、缩管、白点、分层等缺陷;用横波可探测管材中的周向和轴向裂缝、划伤、焊缝中的气孔、夹渣、裂缝、未焊透等缺陷;用表面波可探测形状简单的铸件上的表面缺陷;用板波可探测薄板中的缺陷。
2主要特性超探仪是一种便携式工业无损探伤仪器,它能够快速便捷、无损伤、精确地进行工件内部多种缺陷(裂纹、夹杂、折叠、气孔、砂眼等)的检测、定位、评估和诊断。
既可以用于实验室,也可以用于工程现场。
本仪器能够广泛地应用在制造业、钢铁冶金业、金属加工业、化工业等需要缺陷检测和质量控制的领域,也广泛应用于航空航天、铁路交通、锅炉压力容器等领域的在役安全检查与寿命评估。
它是无损检测行业的必备。
(1)超声波在介质中传播时,在不同质界面上具有反射的特性,如遇到缺陷,缺陷的尺寸等于或大于超声波波长时,则超声波在缺陷上反射回来,探伤仪可将反射波显示出来;如缺陷的尺寸甚至小于波长时,声波将绕过缺陷而不能反射;(2)波声的指向性好,频率越高,指向性越好,以很窄的波束向介质中辐射,易于确定缺陷的位置.(3)超声波的传播能量大,如频率为1MHZ(1兆赫兹)的超生波所传播的能量,相当于振幅相同而频率为1000HZ(赫兹)的声波的100万倍。
[1]3主要优点①穿透能力强,探测深度可达数米;②灵敏度高,可发现与直径约十分之几毫米的空气隙反射能力相当的反射体;可检测缺陷的大小通常可以认为是波长的1/2。
③在确定内部反射体的位向、大小、形状及等方面较为准确;④仅须从一面接近被检验的物体;⑤可立即提供缺陷检验结果;⑥操作安全,设备轻便。
常用无损探伤及使用原则

工业无损探伤的方法很多,目前国内外最常用的探伤方法有五种,即人们常称的五大常规探伤方法.本文将首先介绍五大常规探伤方法及其特点,并结合电厂管道焊接的特定条件和需求,选出适合探伤方法。
除以上五大常规方法外,近年来又有了红外,声发射等一些新的探伤方法.五大常规方法是指:1、射线探伤法 RT:检测内部有气孔,夹渣、未焊透等体积型缺陷,不易发现裂纹等面积型缺陷。
2、超声波探伤法 UT:纵波,横波适用于探测内部缺陷, 表面波适宜于探测表面缺陷,但对表面的条件要求高.3、磁粉探伤法 MT:能探查气孔, 夹杂,未焊透等体积型缺陷, 但更适于检查因淬火, 轧制, 锻造,铸造,焊接,电镀,磨削,疲劳等引起的裂纹。
4、涡流探伤法 ET:能确定表面及近表面缺陷的位置和相对尺寸5、渗透探伤法 PT。
能确定表面开口缺陷的位置、尺寸和形状。
一、射线探伤方法:射线探伤是利用射线的穿透性和直线性来探伤的方法. 这些射线虽然不会像可见光那样凭肉眼就能直接察知,但它可使照相底片感光,也可用特殊的接收器来接收.常用于探伤的射线有 x 光和同位素发出的γ射线,分别称为x光探伤和γ射线探伤.当这些射线穿过(照射)物质时,该物质的密度越大,射线强度减弱得越多,即射线能穿透过该物质的强度就越小.此时,若用照相底片接收,则底片的感光量就小;若用仪器来接收,获得的信号就弱。
因此,用射线来照射待探伤的零部件时,若其内部有气孔,夹渣等缺陷,射线穿过有缺陷的路径比没有缺陷的路径所透过的物质密度要小得多,其强度就减弱得少些,即透过的强度就大些,若用底片接收,则感光量就大些,就可以从底片上反映出缺陷垂直于射线方向的平面投影; 若用其它接收器也同样可以用仪表来反映缺陷垂直于射线方向的平面投影和射线的透过量。
由此可见,一般情况下,射线探伤是不易发现裂纹的,或者说,射线探伤对裂纹是不敏感的.因此,射线探伤对气孔,夹渣,未焊透等体积型缺陷最敏感.即射线探伤适宜用于体积型缺陷探伤,而不适宜面积型缺陷探伤。
不锈钢复合钢板的超声波检测

如在冲制器皿落片下料时, 材料利用率可以提 高约 3 使用户的成本大幅度降低。在集装 %,
箱、 制罐等行业 , 可减少 因焊接而浪费的材料 。 太钢 冷轧 宽 厚 不 锈钢 板生 产 线 的投 产 ,
规格范 围可从 14~1r 后 部 成 品 酸洗 线 . 4 m, a
带有在线拉矫设备 与平整设备 , 可以保证生 产出高等级 的板形 与表面产品, 完全能够满
维普资讯
太 钢科 技
・3 3・
不锈钢复合 钢板 的超声波检测
技术 中心
摘
评判。
李
军
要
本 文对不锈 钢复合板超声波检测方法进行 了阐述 , 并对缺 陷是否可 以修 复做 出准 确
关键词 不 锈钢复合板
未结合缺 陷 复合率
过 程 中有 扩大危 险 的小 缺 陷更 显得 重要 。钢
为缺 陷 的边界 ) 。
波, 若存在未结合缺陷 , 则会出现缺陷波 F 。
() 2 不锈 钢复 合 钢板 的检 测 主要 是 针对
复合层的未结合缺 陷, 了使复合层 中的反 为 射波波形清晰 , 检测时应使用高频探头。由 于不锈钢复合钢板 缺陷的特殊性 , 未结合缺 陷波 F总是 出现在荧光屏 扫描基线 的固定
率, 提升 了产 品 档 次 , 有 广 阔 的发 展 前 景 。 具
冷轧机组主体设备, 均为引进国际知名品牌 , 生产出的冷轧 卷宽度可达 2 0 m 厚度可 0 0 m,
从 0 4~8 m, 品 卷 重 分 别 可达 4 t4 t . a r 产 0、8。
该生产 线前部 原料 酸洗退 火线 生产 出的产 品
位 置上 , 因此在 缺 陷波 F固定 位 置 以外 出现 的回波 , 视 为基 板 或 复板 内 的缺 陷 。爆 炸 均
超声波探伤作业指导书
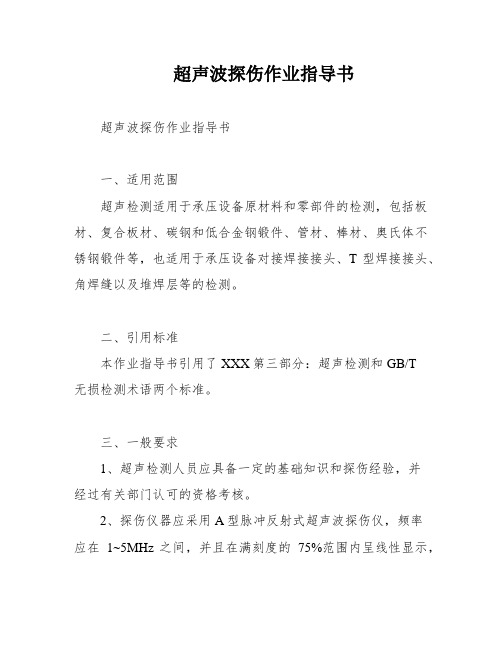
超声波探伤作业指导书超声波探伤作业指导书一、适用范围超声检测适用于承压设备原材料和零部件的检测,包括板材、复合板材、碳钢和低合金钢锻件、管材、棒材、奥氏体不锈钢锻件等,也适用于承压设备对接焊接接头、T型焊接接头、角焊缝以及堆焊层等的检测。
二、引用标准本作业指导书引用了XXX第三部分:超声检测和GB/T无损检测术语两个标准。
三、一般要求1、超声检测人员应具备一定的基础知识和探伤经验,并经过有关部门认可的资格考核。
2、探伤仪器应采用A型脉冲反射式超声波探伤仪,频率应在1~5MHz之间,并且在满刻度的75%范围内呈线性显示,垂直线性误差不得超过5%。
仪器的水平线性、分辨力和衰减器的精度等指标应符合JB/T 的规定。
3、探头应符合以下要求:①纵波直探头的晶片直径应在10~30mm之间,工作频率1~5MHz,误差不得超过±10%。
②横波斜探头的晶片面积应在100~400mm²之间,K值一般取1~3.③纵波双晶直探头晶片之间的声绝缘必须良好。
4、仪器系统的性能应符合以下要求:①在达到所探工件的最大检测声程时,其有效灵敏度余量不得小于10dB。
②仪器与探头的组合频率与公称频率误差不得大于±10%。
③仪器与直探头组合的始脉冲宽度(在基准灵敏度下):对于频率为5MHz的探头,宽度不大于10mm;对于频率为2.5MHz的探头,宽度不大于15mm。
④直探头的远场分辨力应不小于30dB,斜探头的远场分辨力应不小于6dB。
⑤仪器与探头的系统性能应按JB/T 9124和JB/T 的规定进行测试。
四、探伤时机及准备工作1、探伤一般应安排在最终热处理后进行。
若因热处理后工件形状不适于超声探伤,也可将探伤安排在热处理前,但热处理后仍应对其进行尽可能完全的探伤。
2、工件在外观检查合格后方可进行超声探伤,所有影响超声探伤的油污及其他附着物应予以清除。
3、探伤面的表面粗糙度Ra应为6.3μm。
五、探伤方法1、为确保检测时超声波声束能扫查到工件的整个被检区域,探头的每次扫查覆盖率应大于探头直径的15%。
超声波 复合材料 标准

超声波复合材料标准引言超声波复合材料是一种结构复杂、性能优越的材料,广泛应用于航空航天、汽车制造、建筑等领域。
为了保证超声波复合材料的质量和安全性,制定与之相关的标准是至关重要的。
本文将针对超声波复合材料的关键标准进行介绍和分析。
一、超声波检测标准1. 超声波探伤技术应用标准根据超声波探伤技术的应用对象和要求,制定适用于超声波探伤的标准,包括探测原理、设备要求、检测方法、评定标准等内容。
2. 超声波相控阵检测标准针对超声波相控阵技术在复合材料中的应用,制定适用的检测标准,明确其在复合材料中的应用范围、参数要求、灵敏度等指标。
二、复合材料制备标准1. 超声波复合材料成型工艺标准主要针对超声波辅助成型工艺中的工艺流程、设备要求、工艺参数等进行标准化,确保复合材料成型的质量和一致性。
2. 超声波复合材料结构设计标准制定适用于超声波复合材料结构设计的标准,包括设计原则、受力分析、结构参数等内容,保证复合材料结构的安全可靠性。
三、质量控制标准1. 超声波复合材料质量检测标准根据超声波复合材料的特点和使用要求,制定相应的质量检测标准,包括材料性能测试、外观检测、缺陷评定等内容。
2. 超声波复合材料质量管理体系标准建立适用于超声波复合材料生产和管理的质量管理体系标准,包括原材料采购、生产工艺、质量控制、产品追溯等内容。
四、安全标准1. 超声波复合材料安全应用标准针对超声波复合材料在不同领域的应用安全问题,制定相应的安全应用标准,明确其安全使用范围、注意事项、紧急处理措施等内容。
2. 超声波复合材料环保标准针对超声波复合材料生产和使用中可能的环境污染问题,制定环保标准,明确废弃物处理、资源循环利用、环保要求等内容。
结论超声波复合材料作为一种重要的结构材料,在其相关标准的制定和执行中起着至关重要的作用。
通过完善的标准体系,可以规范超声波复合材料的生产、检测、应用和环保,保障其质量和安全性,推动行业的健康发展。
希望各行业单位能充分认识到标准的重要性,加强标准的执行和落实,推动超声波复合材料行业的发展。
基于炭纤维复合材料的超声波探伤技术

基于炭纤维复合材料的超声波探伤技术超声波探伤技术是一种非破坏性检测技术,被广泛应用于材料、工业、医疗等领域。
其中,基于炭纤维复合材料的超声波探伤技术具有优异的性能,成为一个备受关注的领域。
一、炭纤维复合材料简介炭纤维复合材料是一种由碳纤维和高分子基体复合而成的材料。
碳纤维具有高强度、高刚度、低密度的特点,是一种优良的增强材料;高分子基体可以为材料提供良好的耐腐蚀性和耐热性能。
因此,炭纤维复合材料具有优异的力学性能和化学性能。
二、基于炭纤维复合材料的超声波探伤技术超声波探伤技术是一种利用超声波在材料内部传播的特性,检测材料内部缺陷的一种方法。
其中,基于炭纤维复合材料的超声波探伤技术具有以下优点:1.高灵敏度:炭纤维复合材料中存在的缺陷通常是微小的裂纹或空洞,但超声波探伤技术可以对这些缺陷进行高精度的检测。
2.高效率:由于炭纤维复合材料的良好传导性能,超声波探测可以在较短时间内完成,提高了检测效率和生产效率。
3.高安全性:相对于传统的破坏性检测方法,超声波探测是一种非破坏性检测方法,在检测过程中不会对材料造成伤害,也更安全可靠。
三、炭纤维复合材料超声波探伤技术的应用领域基于炭纤维复合材料的超声波探伤技术被广泛应用于各种领域,包括:1.航空航天领域:炭纤维复合材料是航空航天领域中广泛使用的材料,超声波探伤技术可以用于对飞行器、火箭等设备进行检测。
2.汽车制造领域:炭纤维复合材料在汽车制造领域有重要应用,超声波探测可以用于检测汽车部件中的缺陷,提高汽车生产的质量。
3.结构工程领域:炭纤维复合材料常用于桥梁、建筑等结构工程中,超声波探伤技术可以对这些结构进行检测,并提前预防可能出现的问题。
4.医疗领域:炭纤维复合材料在医疗领域中有广泛应用,超声波探测可以用于医疗器械和医疗设备中的质量检测,确保医疗设备的安全可靠。
四、未来发展趋势基于炭纤维复合材料的超声波探伤技术在未来将继续发展,主要趋势包括:1.高性能探测设备的开发:炭纤维复合材料的应用领域日益扩大,需要更高性能的超声波探测设备。
无损检测常规检测方法

Nea rfiel d Farfield
Phased Array Probe
ROWA – Core Flaws Testing
SI Gate Entrance Echo
40 °
A-SCAN 1: EE
Position 4
ห้องสมุดไป่ตู้
Setting EE gate for triggering
Gate EE
Gate Core Flaw 22°
超声波纵波反射法(直探头)缺陷波形表现方式
Phase Array Basics – Relation
Sound field
Virtual Probe
Single Element Probe
Counterpiece for probe
Sound field of a virtual probe is equal to the sound field of a single probe with the same size
Position 3
0 °
Gate Back Wall Echo
Position 2
SI
Position 1
EE
1.BWE
2.BWE
1st BWE
A-SCAN 2:
Setting BWE gate + core flaw gate
Gate BWE Gate Core Flaw
EE
1.BWE
GE Sensing & Inspection Technologies
无损检测常规检测方法 五大常规
超声波探伤
超声检测:是根据超声波与物质的相互作用,超声波在弹性 介质中的传播和在异质界面上的反射、折射等原理探测缺陷 的检测方法。 超声波探伤特点: ①、对裂纹、缩孔、白点、宏观夹杂等危险性缺陷灵敏度高。 ②、探测厚度范围大,几毫米至几米。 ③、适于各种管材、棒材、锻件、板材以及复合材料等检测。 ④、评定不直观、定性困难。
超声波无损检测I级第四部分。

2.纵波斜探头法 将纵波倾斜入射至工件检测面,利用折射纵波进
行检测的方法,称为纵波斜探头法。 入射角小于第一临界角α I ,工件中既有纵波又有
横波,纵波声速快,利用纵波来识别缺陷和定量。 对粗晶材料,如A体不锈钢焊接接头UT检测,常
采用纵波斜探头法检测。 在TOFD检测技术中,使用的探头一般也为纵波
25
谢谢大家 祝大家取得好成绩
26
17
5.4.3多探头法 使用两个以上的探头组合在一起进行检测
的方法。 主要通过增加声束来提高检测速度或发现
各种取向的缺陷。通常与多通道检测仪和 自动扫查装置配合。
18
5.5按探头接触方式分类的超声检测方法 5.5.1接触法和液浸法 探头与工件检测面之间涂有很薄的耦合剂层,因
9
5.1.4共振法 依据工件的共振特性来判断缺陷情况和工
件厚度变化情况的方法称为共振法。 用于工件测厚,现已很少使用。
10
5.2 A型显示和超声成像 5.2.1 A型显示 A型显示是一种波形显示,是将超声信号的幅度
与传播时间的关系以直角坐标的形式显示出来, 横坐标代表声波的传播时间,纵坐标代表信号幅 度。 目前特种设备行业执行的JB/T4730-2005标准规定 的就是A型脉冲反射法超声检测。 采用该方法时,检测结果受检测人员的素质、经 验等人为因素较多。
(纵坐标)对缺陷定量。 T——始波(校零时始波前沿置于零,校零后始波
前沿置于零刻度前。) F——伤波(缺陷面积大于声束截面,只有F1;缺陷
面积小于声束截面,视声能衰减情况,会出现 F1F2F3……) B——底波(底波回波情况视扫描比例、有无缺陷 及缺陷尺寸相对于声束截面大小。)
超声波检测的应用范围包括对接焊缝

超声波检测的应用范围包括对接焊缝、角焊缝、T型焊缝、板材、管材、棒材、锻件以及复合材料等的检测,除对接焊缝外,其余材料的内部缺陷的检测超声波是首选方法。
原理:
铁磁性材料和工件被磁化后,由于不连续性的存在,使工件表面和近表面的磁力线发生局部畸变而产生漏磁场,吸附施加在工件表面的磁粉,形成在合适光照下目视可见的磁痕,从而显示出不连续性的位置、形状和大小。
如图1-1所示。
磁粉探伤适用于检测铁磁性材料表面和近表面尺寸很小、间隙极窄(如可检测出长0.1mm、宽为微米级的裂纹),目视难以看出的不连续性。
不连续性离材料表面越近,形成的漏磁场越大,不连续性越容易检出。
非铁磁性材料由于不具有导磁特性,不连续性不能形成漏磁场,不适用磁粉检测
磁粉检测的特点
1、磁粉检测适用于铁磁性材料的表面及近表面缺陷的检测
2、磁粉检测具有检测速度快,灵敏度高,成本低等优点,缺点是
不能检测到工件材料的内部缺陷,对非铁磁性材料也不能检测
3、磁粉检测具有缺陷直观的优点,广泛应用于铁磁性材料的焊缝、
轴类锻件的检测。
- 1、下载文档前请自行甄别文档内容的完整性,平台不提供额外的编辑、内容补充、找答案等附加服务。
- 2、"仅部分预览"的文档,不可在线预览部分如存在完整性等问题,可反馈申请退款(可完整预览的文档不适用该条件!)。
- 3、如文档侵犯您的权益,请联系客服反馈,我们会尽快为您处理(人工客服工作时间:9:00-18:30)。
7.2 铝及铝合金、钛及钛合金板材超声检测
7.2.1 铝及铝合金板材制造及常见缺陷 板材制造:铝锭→板坯→板材 ; 常见缺陷:气孔、夹杂、微细裂纹、厚板中可能有空腔。
7.2.2 铝及铝合金,钛及钛合金板材检测方法 1)检测方法:与钢板相同 2)探头与扫查方式 直探头、双晶直探头,频率2.5~5MHz; 扫查方式、扫查速度与钢板相同。 3)检测范围和灵敏度 检测范围:根据板厚与钢板相同; 检测灵敏度:基准灵敏度以完好部位B1=80%满幅。
≤10<25Ⅳ源自<150<100≤10
<25
Ⅴ
超过Ⅳ级者
注:Ⅳ级钢板主要用于与承压设备有关的支承件和结构件的制造安装。
4.1.8.2 在坡口预定线两侧各50mm(板厚大于100mm时,以 板厚的一半为准)内,缺陷的指示长度大于或等于50mm时, 应评为Ⅴ级。
4.1.8.3 在检测过程中,检测人员如确认钢板中有白点、裂纹 等危害性缺陷存在时,应评为Ⅴ级。
7.1 板材超声波探伤
7.1.6 质量等级判定:按JB/T4730-2005标准4.1.7条规定评定。
等级
单个缺陷 指示长度
mm
单个缺陷 指示面积
cm2
在任一1m×1m检测面 积内存在的缺陷面 积百分比%
以下单个缺陷 指示面积不计
cm2
Ⅰ
<80
<25
≤3
<9
Ⅱ
<100
<50
≤5
<15
Ⅲ
<120
<100
40mm以上钢板检测频率为2.5MHz。 晶片直径:Ф14~Ф25mm。 单晶直探头:适用于板厚δ较大的钢板检测; 双晶直探头:适用于板厚δ较薄的钢板检测。
板厚,mm 采用探头 公称频率,MHz
探头晶片尺寸
6~20
双晶直探头
5
>20~40
单晶直探头
5
>40~250 单晶直探头
2.5
晶片面积不小于150mm2 φ14~φ20 mm φ20~φ25 mm
复合材料、板材和管材的超声波探伤
复合材料、板材、管材、铸锻件、不锈钢 中国高端数字超声解决方案的领军者
中国 ··济南 ·2014
目录
板材超声波探伤 铝及铝合金、钛及钛合金板材超声检测 复合材料超声波探伤 板材自动超声检测 管材超声波探伤
7.1 板材超声波探伤
❖板材分类: 薄板:δ<6mm; 中板: 6mm≤δ≤40 mm; 厚板:δ>40mm
7.1 板材超声波探伤
7.1.4 探测范围和灵敏度调整 1)探测范围调整 δ<30mm:B10; 30mm≤δ≤80mm:B5; ??
2)灵敏度调整 CBⅠ块法、 CBⅡ试块、底波法。
δ>80mm:B2~B5。
7.1 板材超声波探伤
7.1.4 探测范围和灵敏度调整 2)灵敏度调整:CBⅠ试块法、CBⅡ试块、底波法。 4.1.4.1 板厚不大于20mm时,用CBⅠ试块将工件等厚部位
7.1 板材超声波探伤
2)扫查
扫查方式:全面扫查、列线扫查、边缘扫查和格子扫 查。
扫查速度:手工检测≤0.2m/s; 水浸自动检测,脉冲间隔时间>60t。
4.1.5.3 扫查方式 a) 探头沿垂直于钢板压延方向,间距不大于100mm的平行线 进行扫查。在钢板剖口预定线两侧各50mm(当板厚超过100mm时,以板厚的一半为 准)内应作100%扫查。b) 根据合同、技术协议书或图样的要求,也可采用其他形式 的扫查。
➢ 即B1<50%时, 使/B1达50% 是探头中心移动 的距离为缺陷的指示长度,探头中心轨迹即为缺 陷边界。
7.1 板材超声波探伤
4)缺陷性质判断 分层:波形整齐陡直,底波明显下降或消
失;
折叠:不一定有缺陷波,底波明显下降, 次数减少或消失;
白点:波形密集尖锐活跃,底波明显下降, 次数减少,重复性差,移动探头回波此起 彼伏。
7.2.3 缺陷的判别与测定 1)缺陷判别 F1≥40%; F1<40%时,F1/ B1≥100%; B1<5%。 2)缺陷测定 JB/T4730-2005标准第5.3.5条。
7.2.4 缺陷评定 缺陷指示长度确定,符合JB/T4730标准规定; 缺陷指示面积确定,符合JB/T4730标准规定。
7.2.5 质量级别评定:按JB/T4730标准规定评级。
7.1 板材超声波探伤
3)缺陷定量(用测长法测定指示长度和面 积):根据JB/T4730-2005标准。
➢ 当F1≥50% 或F1/B1≥50% (B1<100% )时, 使 F1达25% 或F1/B1达50% 是探头中心移动的距 离为缺陷的指示长度(以较严重者为准) ,探头 中心轨迹即为缺陷边界。
7.3 复合材料超声波探伤
7.3.1 复合板材常见缺陷 制造方法:轧制、粘接、堆焊和爆炸。 常见缺陷:脱层和接合不良。
第一次底波高度调整到满刻度的50%,再提高10dB作为 基准灵敏度。
7.1 板材超声波探伤
4.1.4.2 板厚大于20mm时,应将CBⅡ试块φ5平底孔第一次反射波高调
整到满刻度的50%作为基准灵敏度。
试块编号
CBⅡ-1
被检钢板厚度
检测面到平底孔的 距离s
>20~40
15
试块厚 度T
≥20
CBⅡ-2
>40~60
30
≥40
CBⅡ-3
>60~100
50
CBⅡ-4
>100~160
90
CBⅡ-5
>160~200
140
≥65 ≥110 ≥170
CBⅡ-6
>200~250
190
≥220
4.1.4.3 板厚不小于探头的三倍近场区时,也可取钢板无缺 陷完好部位的第一次底波来校准灵敏度,其结果应与 4.1.4.2的要求相一致。
7.1.1 钢板中常见缺陷 分层、白点(存在于内部);折迭、重
皮、裂纹(存在于表面)。
7.1 板材超声波探伤
7.1.2 探伤方法 直接接触法、叠加效应、水浸法
出现叠加效应,一般应根据F1来评价缺陷。
7.1 板材超声波探伤
7.1.2 探伤方法 水浸法
H水
nc水 c钢
n钢
4
7.1 板材超声波探伤
7.1.3 探头与扫查方式 1)探头(解释) 频率:2.5~5MHz——40mm以下钢板检测频率为5MHz;
7.1 板材超声波探伤
7.1.5 缺陷判别与测定
1)缺陷判别:按JB/T4730-2005标准要求执行。 a) F1≥50%; b) 即B1<100%,而F1/B1≥50%; c) 即B1<50%。
2)缺陷位置测定 深度位置测定:直接从荧光屏读出缺陷位置;
平面位置测定:根据直探头在钢板上位置确定, 在板材表面画出缺陷的位置。