加氢裂化飞温事故过程分析
加氢裂化温事故处理方法探讨
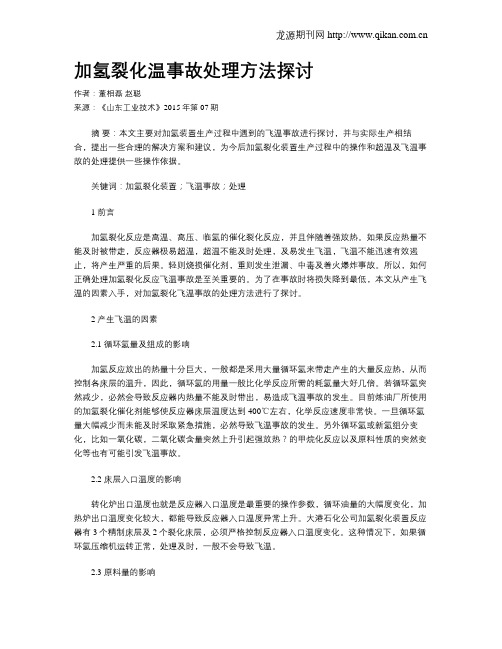
加氢裂化温事故处理方法探讨作者:董相磊赵聪来源:《山东工业技术》2015年第07期摘要:本文主要对加氢装置生产过程中遇到的飞温事故进行探讨,并与实际生产相结合,提出一些合理的解决方案和建议,为今后加氢裂化装置生产过程中的操作和超温及飞温事故的处理提供一些操作依据。
关键词:加氢裂化装置;飞温事故;处理1 前言加氢裂化反应是高温、高压、临氢的催化裂化反应,并且伴随着强放热。
如果反应热量不能及时被带走,反应器极易超温,超温不能及时处理,及易发生飞温,飞温不能迅速有效遏止,将产生严重的后果。
轻则烧损催化剂,重则发生泄漏、中毒及着火爆炸事故。
所以,如何正确处理加氢裂化反应飞温事故是至关重要的。
为了在事故时将损失降到最低,本文从产生飞温的因素入手,对加氢裂化飞温事故的处理方法进行了探讨。
2 产生飞温的因素2.1 循环氢量及组成的影响加氢反应放出的热量十分巨大,一般都是采用大量循环氢来带走产生的大量反应热,从而控制各床层的温升,因此,循环氢的用量一般比化学反应所需的耗氢量大好几倍。
若循环氢突然减少,必然会导致反应器内热量不能及时带出,易造成飞温事故的发生。
目前炼油厂所使用的加氢裂化催化剂能够使反应器床层温度达到400℃左右,化学反应速度非常快。
一旦循环氢量大幅减少而未能及时采取紧急措施,必然导致飞温事故的发生。
另外循环氢或新氢组分变化,比如一氧化碳,二氧化碳含量突然上升引起强放热?的甲烷化反应以及原料性质的突然变化等也有可能引发飞温事故。
2.2 床层入口温度的影响转化炉出口温度也就是反应器入口温度是最重要的操作参数,循环油量的大幅度变化,加热炉出口温度变化较大,都能导致反应器入口温度异常上升。
大港石化公司加氢裂化装置反应器有3个精制床层及2个裂化床层,必须严格控制反应器入口温度变化。
这种情况下,如果循环氢压缩机运转正常,处理及时,一般不会导致飞温。
2.3 原料量的影响原料量的突然减少,就会导致催化剂床层上原料油密度的下降或者不均匀分布,从而使反应热急剧的变化或者导致床层颈向温度差别较大,从而引起深度的二次加氢反应而引起飞温,先降温后降量是在原料油减少时我们尊守的原则,但反应床层上也有相当多的原料油量,如果原料减少时间较短,循环氢量没有变化的情况下,如果处理及时一般不会导致飞温。
加制氢装置安全事故案例
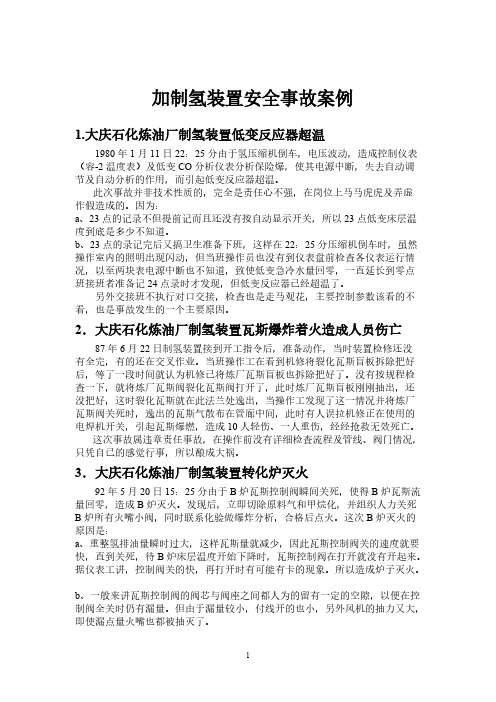
加制氢装置安全事故案例1.大庆石化炼油厂制氢装置低变反应器超温1980年1月11日22:25分由于氢压缩机倒车,电压波动,造成控制仪表(容-2温度表)及低变CO分析仪表分析保险爆,使其电源中断,失去自动调节及自动分析的作用,而引起低变反应器超温。
此次事故并非技术性质的,完全是责任心不强,在岗位上马马虎虎及弄虚作假造成的。
因为:a、23点的记录不但提前记而且还没有按自动显示开关,所以23点低变床层温度到底是多少不知道。
b、23点的录记完后又搞卫生准备下班,这样在22:25分压缩机倒车时,虽然操作室内的照明出现闪动,但当班操作员也没有到仪表盘前检查各仪表运行情况,以至两块表电源中断也不知道,致使低变急冷水量回零,一直延长到零点班接班者准备记24点录时才发现,但低变反应器已经超温了。
另外交接班不执行对口交接,检查也是走马观花,主要控制参数该看的不看,也是事故发生的一个主要原因。
2.大庆石化炼油厂制氢装置瓦斯爆炸着火造成人员伤亡87年6月22日制氢装置接到开工指令后,准备动作,当时装置检修还没有全完,有的还在交叉作业。
当班操作工在看到机修将裂化瓦斯盲板拆除把好后,等了一段时间就认为机修已将炼厂瓦斯盲板也拆除把好了。
没有按规程检查一下,就将炼厂瓦斯阀裂化瓦斯阀打开了,此时炼厂瓦斯盲板刚刚抽出,还没把好,这时裂化瓦斯就在此法兰处逸出,当操作工发现了这一情况并将炼厂瓦斯阀关死时,逸出的瓦斯气散布在管廊中间,此时有人误拉机修正在使用的电焊机开关,引起瓦斯爆燃,造成10人轻伤、一人重伤,经经抢救无效死亡。
这次事故属违章责任事故,在操作前没有详细检查流程及管线、阀门情况,只凭自己的感觉行事,所以酿成大祸。
3.大庆石化炼油厂制氢装置转化炉灭火92年5月20日15:25分由于B炉瓦斯控制阀瞬间关死,使得B炉瓦斯流量回零,造成B炉灭火。
发现后,立即切除原料气和甲烷化,并组织人力关死B炉所有火嘴小阀,同时联系化验做爆炸分析,合格后点火。
加氢裂化装置典型事故处理(二)
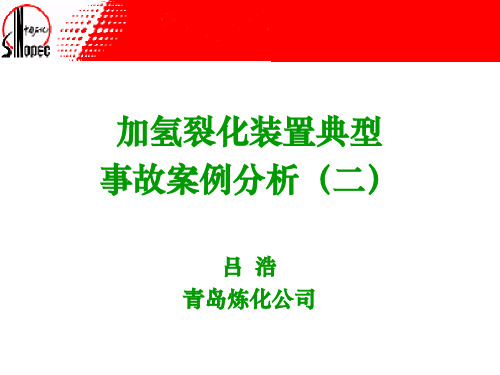
停电导致裂化反应器飞温
u 机组在1989r/min下运转15分钟后,裂化反应器四床 层TI1143温度开始上升,24:05最高达到470℃, 在场厂领导、技术部门、车间协商后决定立即启用 2.1MPa/min进行卸压,同时引入氮气进行置换。 u 停电前裂化反应温度CAT2为372℃,停电后22:17 裂化反应温度CAT2上升到391.7℃。但在24.:10循 氢机停机后,裂化反应器温度快速上升,停电前裂 化反应器四床中部温度TI1143B为373℃,24:00温 度为465℃,到24:58温度快速上升到了882℃。在 中压氮气引入反应系统后反应系统压力充至3.0MPa 后通过泄压阀进行泄压置换。
开工过程中飞温事故
三、事故教训 u 装置紧急泄压后,系统压力至0.1 MPa左右时,如果 反应器床层温度下降幅度不大(仍能大于300℃) ,则必须通过补入纯度99.99%的高纯氮气,边充边 放反应器床层降温至200℃后才可以重新恢复进料 。 u 循环机K102出口4.0MPa氮气日常生产中盲板要处于 通状态,三阀组双阀开,低点放空开,保证随时处 于备用状态。在紧急停工过程中及时联系化验对 4.0MPa氮气进行纯度分析,保证合格。 u 加强队反应器床层超温和循环机故障停运的反事故 处理能力培训工作。
停电导致裂化反应器飞温
此后精制裂化反应器各点温度逐步降低,9月5日 C1001开机前CAT1温度降至300℃,CAT2温度降至 326℃。 9月5日10:10左右,循氢机C1001再次启动,到11 :00左右,转速提至8000RPm,反应各点温度降低 速度加快,到9月5日20:00反应器各点温度都降到 了200℃以下。9月5日18:30装置启动P1001向反应 系统进低氮油进行了冲洗,到21:00停止冲洗。
加氢裂化反应器飞温的因素及控制措施
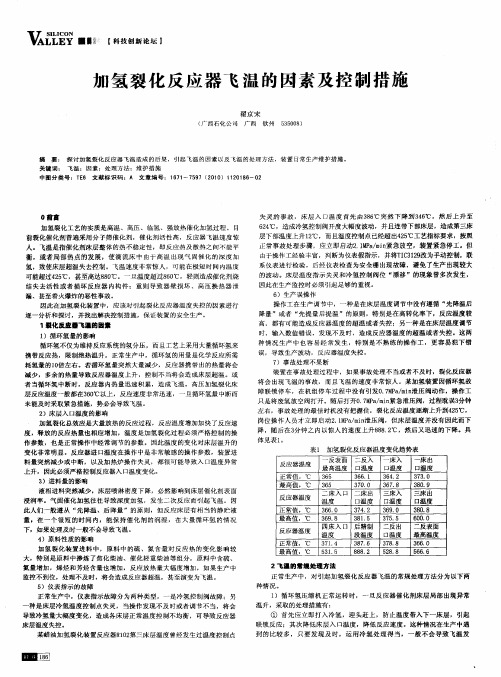
6 )生产 误操作
结 失去 活 性或 者 损 坏 反应 器 内构 件 ;重 则导 致 器 壁损 坏 、高压 换 热 器 泄
漏、甚 至着 火爆炸 的恶性 事故 。
因此在加 氢裂 化装 置 中,应 该对 引起裂 化反应 器温 度 失控 的因素 进行 逐一分 析和探 讨 ,并找 出解决控 制措 施 ,保 证装 置 的安 全生 产。
操作 工在 生产 调节 中, 一种是 在床 层温度 调 节 中没有 遵循 “ 降温 后 先
降量 ”或 者 “ 先提 量 后提 温 ”的原 则 ,特别 是在 高转 化 率下 ,反应 温度 较 高 ,都有 可 能造成 反 应器温 度 的超温 或 者失 控 ;另一 种 是在床 层温 度调 节
1曩 化反应 嚣飞 疆的 因素
可能超 过4 5 2 ℃,甚至 高达 80 。一旦温 度超过 80 8℃ 6 ℃,轻则造 成催化 剂烧
正常 事故 处理 步骤 ,应 立 即启 动2 1P/ J紧 急放 空 ,装置 紧 急停 工。但 . ̄a mn I 由于操 作工 经验丰 富 ,判断 为仪表假 指示 ,并将 TC 19 I32 改为手 动控 制 ,联 系 仪表 进行 检验 ,后经 仪表 检查 为安 全栅 出现 故 障,避 免 了生产 出现 较大 的波动 。床 层温 度 指示失 灵和 冷氢 控 制 阀位 “ 漂移 ”的现象 曾多次发 生 ,
一
反表面 二反入 一床入
一床 出 口温度 330 7.
上升 ,因此 必须严 格控 制反应 器入 口温度 变化 。
失 灵 的事 故 , 床层 入 口温 度 首先 由3 6C突 然 下 降到 3 6C, 然后 上 升 至 8" 4"
加氢裂化装置事故案例及分析

加氢裂化装置事故案例及分析李立权【摘要】针对加氢裂化装置近50年来发生的各类事故,包括电力事故、飞温事故、火灾事故、爆炸事故、泄漏事故、中毒事故、高压串低压事故、催化剂作业事故、仪表事故等,分析了事故发生的原因,总结需吸取的教训.指出:①电源故障造成集散控制系统(DCS)黑屏时,调节阀处于安全状态方能保证装置的本质安全;②飞温事故的安全处理必须坚持“一泄到底”原则;③防止火灾事故扩大必须紧急隔离火源,泄放可燃物;④高压管线、阀门、设备失效是爆炸、泄漏事故发生的主要原因,应定期检修、不定期在线检测;⑤正确执行防护管理规定,佩戴合适的防毒面具,可有效防止中毒事故发生;⑥加强高压仪表的防冻防凝可有效避免高压串低压事故的发生;⑦严格控制高压空冷器入口流速、Kp值、水相NH4HS浓度可有效防止腐蚀事故的发生;⑧原料氯离子含量高导致的垢下腐蚀是高压换热器事故的主要原因;⑨安全措施不到位是催化剂作业事故的主要原因;⑩维护保运不及时导致的仪表老化是仪表事故的主要因素;(⑥)腐蚀加高温是导致加热炉管事故的主要原因.【期刊名称】《炼油技术与工程》【年(卷),期】2016(046)012【总页数】5页(P5-9)【关键词】加氢裂化;事故;案例;分析;飞温;火灾;爆炸泄漏;中毒【作者】李立权【作者单位】中石化洛阳工程有限公司,河南省洛阳市471003【正文语种】中文加氢裂化装置处于高温、高压、临氢、易燃、易爆、有毒介质的操作环境,近50年来发生了多起安全生产事故,给企业造成了重大的经济损失,也导致了部分人员伤亡。
总结和分析这些事故原因,吸取教训,避免类似事故的发生对保障企业的安全生产意义重大。
事故案例:2000年的某日14∶27,某企业因110 kV变电所故障,引起加氢裂化装置晃电,造成装置机泵停运,废热锅炉过热段安全阀起跳,不间断电源(UPS)失灵,集散控制系统(DCS)停电黑屏,系统无法监测和控制DCS参数,只得人工启动2.1 MPa/min紧急泄压,装置紧急停工。
加氢裂化开工过程事故汇编解读
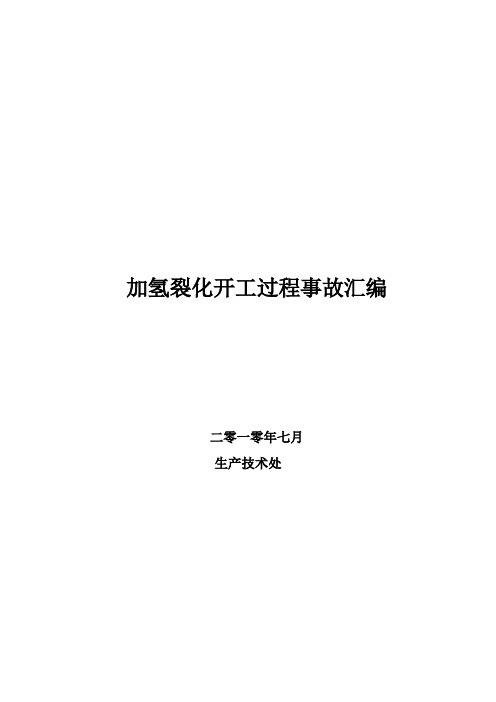
加氢裂化开工过程事故汇编二零一零年七月生产技术处1.循环氢压缩机故障循环氢压缩机及其辅机故障,严重制约了装置的顺利投产,反应系统气密过程中,当反应系统压力12.0~14.0MPa,因密封油泵压力不足,密封油系统热量分布不平衡,油冷却后温度较高,曾数次造成循环氢压缩机停机,影响气密进度,对密封油泵及冷却系统进行改造,16.0MPa氢气气密一次合格。
投料试生产后,循环氢压缩机频繁停机,且没有任何报警,给查找原因带来较大困难,其间陆续解决了润滑油泵出口安全阀弹簧损坏,调速油供油管径过小,DG505调速系统参数整定欠佳,冬季外供中压蒸汽管网过长,中压蒸汽温度低易带水,现场调速系统反馈信号接线短路等问题,使停机问题最终得以解决。
2.C101(循环氢压缩机)密封油液位导致机组联锁跳闸1986年7月9日,Q01机组在第一次试运中,8:05时密封油高位罐液位下降,电泵也无法维持液位。
8:08时由于高位罐液位低造成联锁跳闸,Q01自动停运。
事后发现液位自控回路调节阀处于关闭状态,经检查是该阀定位器供风定值器损坏,仪表风中断造成调节阀自动关闭,使密封油不能进入高位罐。
分析:调节阀出故障是操作中常见的现象,当运转设备正常而出现断流故障,应立即查看调节阀开度,必要时用旁路阀调节。
3. 1.0MPa蒸汽温度减温到180℃1986年8月21日,C101(循环氢压缩机)正在开机试运中,废热锅炉开除氧系统,(向CT1019循环氢压缩机蒸汽透平)背压蒸汽注碱温水,将1.0MPa蒸汽控制在250℃,由于除氧器温度升的过高液位波动,造成F106-P0lA泵(碱温水泵)抽空碱温水中断,背压汽温控表TC-713自动将注碱温水阀全开,备用泵起动后温控表调节滞后,大量碱温水注入C101背压汽中,使1.0MPa蒸汽温度降到180℃。
故障出现后,紧急将TC-713改手动将温度提回到250℃。
分析:加氢裂化装置的低压汽是排放到厂管网,1.0MPa蒸汽饱和温度为170℃,接近170℃时会造成蒸汽带水事故。
加氢裂化装置反应器飞温原因及处理对策

加氢裂化装置反应器飞温原因及处理对策摘要:加氢裂化装置反应器飞温原因较多,常见的有循环氢流量中断或减少、原料性质改变、床层径向温差较大。
为了提高加氢裂化装置反应器飞温处理效果,技术人员可从循环氢压缩机正常运转、对催化剂进行装填、硫化或钝化等方面着手,降低危险事故的发生率。
关键词:加氢裂化装置;反应器;飞温原因;处理对策飞温是反应器在非稳定操作条件下操作参数出现微扰动导致反应器温度升高的现象之一。
因加氢裂化装置活性较高,容易出现催化剂反应,增加了反应器的飞温速度,导致温度在短期内快速升高,催化剂烧结且失去活性,容易发生各类安全事故。
因此,为了保障加氢裂化装置及生产的安全,接下来本文就加氢裂化装置反应器飞温原因进行分析,提出相应的处理对策。
1加氢裂化装置反应器飞温原因1.1循环氢流量中断或减少反应器的床层放出的热量较多,需要通过循环氢携带,若出现循环氢流量中断或减少的情况,那么床层温度的能力就会失去。
从反应器温度控制方面分析,循环氢终端的影响相当重要,因为循氢机停运,无法往外携带热量,导致原料油和催化剂接触的滞留时间较长,和氢气在高温的反应器中容易继续发生反应且处于持续放热的状态,床层快速升温,必须第一时间采取有效的泄压方法[1]。
同时,还会出现个别床层入口冷氢量增加的问题,增加了其他床层入口氢气量被争夺的情况。
具体来说,循环氢压缩机停运发生的原因较多,常见的有干气密封泄漏量高连锁、冷高压分离器液位高联锁等。
1.2原料性质改变原料油的性质不同,若原料油的氮或含硫量智能机,又或者处理含烯烃量较多的原料时,精制催化剂所在的床层温升处于增加的趋势。
若精致床层的冷氢量较大,还会导致裂化床层入口冷氢降低。
因此,不仅要对加工减压蜡油进行考虑,掺炼焦化蜡油时,还要对混合原料油性质变化进行全面考虑。
针对采取尾油循环工艺装置,若循环油至反应系统流量发生变化,还会改变反应器进料性质。
1.3床层径向温差较大床层径向温差指的是在一个床层水平面上,不同位置的热电偶测量的最低和最高的温度差,可通过其反映不均匀的进料分配和催化剂装填问题,因而原料油在反应器横截面流量分布不够均匀,短路的问题比较常见[2]。
加氢裂化装置安全特点和常见事故分析

加氢裂化装置安全特点和常见事故分析摘要:对某公司五百万吨/年加氢裂化装置的工作原理进行了简单的阐述,并对该装置的安全特性、安全设计等方面进行了探讨,并对该装置的常见事故进行了归纳,并对该装置的运行和检修进行了分析。
关键词:加氢裂化;开工;安全一、装置的生产原理及简介加氢是指在高压条件下,碳氢和碳氢在催化上进行的催化分解和加氢,形成低分子的加氢工艺,以及加氢脱硫、脱氮和不饱和烃的加氢。
它的化学反应包括饱和,还原,裂化和异构。
碳氢化合物在加氢时的反应方向与深度与碳氢化合物组成、催化剂性能、运行环境有关。
加氢装置由反应、分馏、蒸汽发生三部分构成,利用 UOP单管双药全周期加氢裂解技术,实现了最大程度的中馏份,并将其用作洁净燃油的混合成分。
反应段为两组式串联全周期、预混氢、高温生产,并以湿法硫为原料进行硫化。
以低氮油钝化工艺对催化剂进行钝化,利用器外部再生技术对催化剂进行再生;分馏系统主要包括汽提塔、常压分馏塔和石脑油、航煤柴油等。
该设备的主要原材料是降压蜡和炼油,以液化石脑油、石脑油、航空煤油、轻柴油、重柴油等为主。
二、加氢裂化装置安全特点2.1临氢、易燃易爆氢是一种易扩散、燃烧和爆炸的气体。
氢是一种非常活跃的化学物质,它的火焰具有“不可见性”,它的燃烧非常迅速,如果是在空中,哪怕是一点点的火星,哪怕是剧烈的碰撞,都会引起它的爆炸。
2.2系统高温高压在此基础上,对加氢厂的加氢工艺进行了严格的实验研究,提出了高压15.89 MPa和382摄氏度的工艺要求,在生产过程中,必须保证液位的稳定性,避免了串压,不然会引起一场爆炸。
2.3有毒有害化学品多该设备含有大量有毒、有毒的化工原料,包括硫化剂、催化剂、碱液、液氨等,同时还会产生大量有毒的气体,如硫化氢、 CO、羰基镍、苯等,这些有毒的化合物中含有羰基镍和苯,硫化氢对神经系统的毒性很大,所以必须进行严格的监测。
能预防渗漏,熟悉危险化学品的特性和保护。
一旦发现问题,要立即进行处置,并向上级报告,避免事态进一步恶化。
加氢裂化停工总结.doc

2019.01.13循环机紧急停机处理总结一、事件经过1. 8:56:39时,混氢流量低报警,8:56:56时,UCV3103联锁动作反应炉停 炉;3s 后瓦斯停炉阀关闭。
(图1-1)2. 反应通知分憎停循环机,通知ESD 岗将联锁摘除;8:59:01时,分镭岗位 航煤抽出量FICQ3219和柴材抽出量FICQ3220大幅度降量;分係开始应急操作(图 1-1)3. 8:59:36 时 D-3105 液位低报、8:59:56 时 D-3103 液位低报;8:59:56 时 D-3105液位控制阀主操作改手动关阀;(图1-1)(图1-1后台操作记录1 )4. 8:59:50时,裂化笫二段(新鲜剂)出口温度TI3128C 高报409. 0°C (第一次温波),9:00:35时,按钮启动2. 1MP&放空,4s 后阀开;2O1G-X-J2 2016*1-12 2016-1-12 201C-1 i 2 Z0161-)^ g2^~i-i22015- 1 12 w 20^-1-lZ 8;j.“ 201J-1-12 8:Sfe ?482016- 4-12 R :6b ;40 慾兰~丄2 t :M :Z3 201^-1 -12 c ~ 2016-1-12 M16~l 12 2016-1 -12 202 6-1 t? !?01$ 1 12201<J-l -IN 2016-1 12 2016 2 13 2010-1 12 2016-1-12 201C-1-12 2016-1-12 20】—】2 201«-l 32 Z016-1-12 I 201^-1-12 2016 112 2016-1-12 2016-1-12 8:S9:01 2010 L )^ 0:59:2 2O1&-1-12 &50: 10 2010 ) 12 8:1.9:36 2016-1-12 8:S9:3T201 C l 12 8:EQ :37-12 8:59:50 -12 8:69:54 8:59:比 8:69:55 S :59:56 3:$0:57 吝:59:37 2:00:00 9:00:01201«-l 2016-1-12 2011-1 -12 201C 1-X2 2016-1-12 2016-1 12 2016 1-1Z 2016 1-12 2016-1-128:54:30 8曲” R :64"Q1I*217^2 LIAS"吃 L|AS1TJ2 UA5173? JS1I21H .XS1T21H K51TZIH MQ1 F1UI • KM*•6:38• S :M:38 * 8:%:” 8:S6:398心;曲 3:E6:5« 8惑:显 8:57:12 8:bT:23 3:57:468:57:48 8;S?:48 2:57:52 a :w :(w 8:W :058:58:09fI311<6 FT3il«u 卩⑶皿 irvjiaj FIQiayFTQlCOiirv^l03 f 1Q1OQC PIC34M XS1€2XC K3W2K KS1C-21G PI31« LICJIKrcxoiai LI311SFC20102LIC311?FICO3219LICS108FlW?Z :i» LIC31O8 PIC1T2^ PICJ728 TI3129C KS162TC TI312® LIC3114 T ⑶ 2SD KS162TC KS162TC f1005220 FI31250・:UUg U. JXaS 忙江E 13心刘 simUhte 口沅量IB 云WMX •: co M.j.eiot -s«) MRGOHH (0 u me -m ■ T0. 2 M M 3 4 . 103f-8 * W PV35.0 ■ to P7■g 八L0前 • 23.7 S Old- [旳轴]PV ■ <4.y ■ IXl穴 ■ 2J.0 QAi oW JX7( suaaMnd ⑹ 1FV & 39.9 * LLv -4W-C C wPV .2FV ,<G.O M PV - 410.3Hi ■AKPT >40T.1 £ H : PV - 0恥 KX SV =g 0 S 0.rv - 25£ C >ta3A*N R\V£YSt111133 RTA71o. wrd 2467 出 口毁"R ■AX Old^AUT i .:Fnf»«ttS0WWlOGWUll航坪*氐*泠JT 肥Q1心0匚久:站:g"58:嗨S L0M-3A Z/hi o〔ggwus35. 9:02:00 时,D-3105 压力降至 9. 969MPa, 9:02:50 时,D-3105 液位 60. 2% 咼报(图1 -4 );6. 9:09时,高压氮补充进装置,9:16时,高压氮关闭;9:22时,再次补充 高压氮,9:29时,高压氮关闭准备开循环机。
反应器飞温事故预案
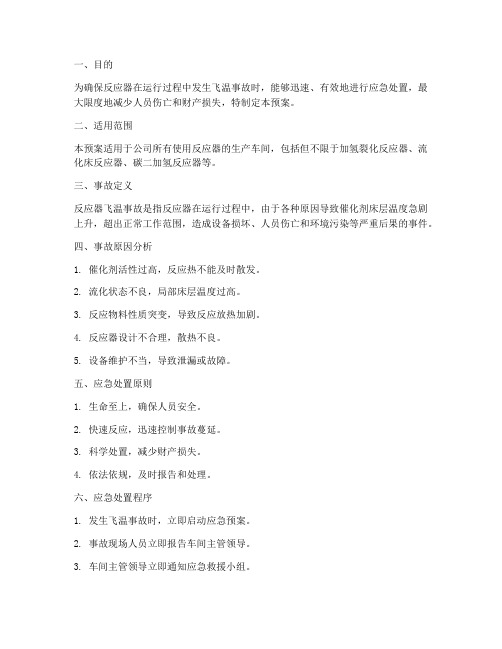
一、目的为确保反应器在运行过程中发生飞温事故时,能够迅速、有效地进行应急处置,最大限度地减少人员伤亡和财产损失,特制定本预案。
二、适用范围本预案适用于公司所有使用反应器的生产车间,包括但不限于加氢裂化反应器、流化床反应器、碳二加氢反应器等。
三、事故定义反应器飞温事故是指反应器在运行过程中,由于各种原因导致催化剂床层温度急剧上升,超出正常工作范围,造成设备损坏、人员伤亡和环境污染等严重后果的事件。
四、事故原因分析1. 催化剂活性过高,反应热不能及时散发。
2. 流化状态不良,局部床层温度过高。
3. 反应物料性质突变,导致反应放热加剧。
4. 反应器设计不合理,散热不良。
5. 设备维护不当,导致泄漏或故障。
五、应急处置原则1. 生命至上,确保人员安全。
2. 快速反应,迅速控制事故蔓延。
3. 科学处置,减少财产损失。
4. 依法依规,及时报告和处理。
六、应急处置程序1. 发生飞温事故时,立即启动应急预案。
2. 事故现场人员立即报告车间主管领导。
3. 车间主管领导立即通知应急救援小组。
4. 应急救援小组迅速到达现场,按照预案进行处置。
5. 切断事故反应器进料和氢气,降低反应器压力。
6. 关闭事故反应器进出口阀门,防止事故扩大。
7. 启动冷却系统,对反应器进行降温。
8. 对事故现场进行隔离,防止有毒有害气体扩散。
9. 检查设备设施,查找事故原因。
10. 对事故原因进行评估,提出整改措施。
11. 恢复生产,确保安全生产。
七、应急处置措施1. 人员疏散:立即组织现场人员疏散至安全区域,确保人员安全。
2. 设备切断:迅速切断事故反应器进料和氢气,降低反应器压力。
3. 阀门操作:关闭事故反应器进出口阀门,防止事故扩大。
4. 冷却降温:启动冷却系统,对反应器进行降温。
5. 隔离处理:对事故现场进行隔离,防止有毒有害气体扩散。
6. 事故调查:对事故原因进行评估,查找原因。
7. 整改措施:根据事故原因,提出整改措施,防止类似事故再次发生。
蜡油加氢裂化装置反应器飞温原因分析及对策
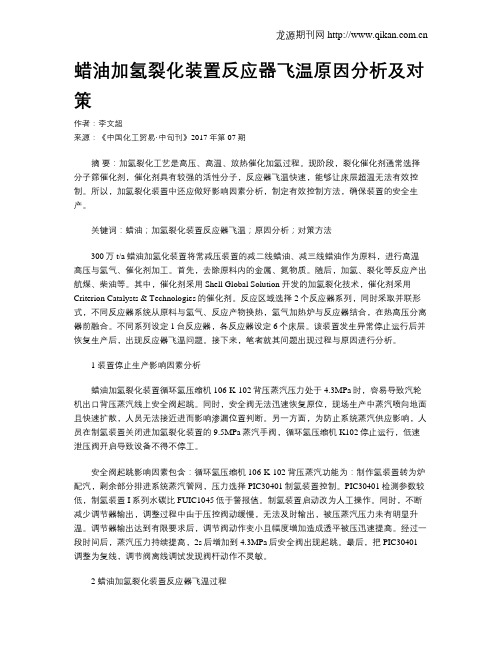
蜡油加氢裂化装置反应器飞温原因分析及对策作者:李文超来源:《中国化工贸易·中旬刊》2017年第07期摘要:加氢裂化工艺是高压、高温、放热催化加氢过程。
现阶段,裂化催化剂通常选择分子筛催化剂,催化剂具有较强的活性分子,反应器飞温快速,能够让床层超温无法有效控制。
所以,加氢裂化装置中还应做好影响因素分析,制定有效控制方法,确保装置的安全生产。
关键词:蜡油;加氢裂化装置反应器飞温;原因分析;对策方法300万t/a蜡油加氢化装置将常减压装置的减二线蜡油、减三线蜡油作为原料,进行高温高压与氢气、催化剂加工。
首先,去除原料内的金属、氮物质。
随后,加氢、裂化等反应产出航煤、柴油等。
其中,催化剂采用Shell Global Solution 开发的加氢裂化技术,催化剂采用Criterion Catalysts & Technologies的催化剂。
反应区域选择2个反应器系列,同时采取并联形式,不同反应器系统从原料与氢气、反应产物换热,氢气加热炉与反应器结合,在热高压分离器前融合。
不同系列设定1台反应器,各反应器设定6个床层。
该装置发生异常停止运行后并恢复生产后,出现反应器飞温问题。
接下来,笔者就其问题出现过程与原因进行分析。
1 装置停止生产影响因素分析蜡油加氢裂化装置循环氢压缩机106-K-102背压蒸汽压力处于4.3MPa时,容易导致汽轮机出口背压蒸汽线上安全阀起跳。
同时,安全阀无法迅速恢复原位,现场生产中蒸汽喷向地面且快速扩散,人员无法接近进而影响渗漏位置判断。
另一方面,为防止系统蒸汽供应影响,人员在制氢装置关闭进加氢裂化装置的9.5MPa蒸汽手阀,循环氢压缩机K102停止运行,低速泄压阀开启导致设备不得不停工。
安全阀起跳影响因素包含:循环氢压缩机106-K-102背压蒸汽功能为:制作氢装置转为炉配汽,剩余部分排进系统蒸汽管网,压力选择PIC30401制氢装置控制。
PIC30401检测参数较低,制氢装置I系列水碳比FUIC1045低于警报值。
加氢裂化事故案例

• 加氢裂化在高温(350425℃)、高压(10 18MPa)的临氢条件下运转,易发生故障;
• 如何减少装置故故障,确保长期案全运转,历来 是人们关注的焦点。
2
1. 设备本身的问题
18
表2. 生产管理问题造成的故障
厂家 操作 原料 蒸汽 助剂 器内 氢气
茂名 O O O O O
金陵 O
HD-C O O
三厂 O
DB-D O
0
DB-L O O
O
19
2.2 典型事例 2.2.1 茂名石化公司
(1)反应器催化剂床层有偏流现象,检修期间卸出催化剂 过程中,发现不正常的地方有烧焦了的灯头和电线, 系检查管理不严,装填催化剂作业时将安全灯遗留在 反应器内所致。
15
1.2.2 齐鲁石化公司
(1)高压放空管线固定卡子设计不良,调试启动紧 急卸压阀时,造成长距离管线从管架上坠地。
(2)反应器引入冷氢的分配系统设计欠佳,催化剂 床层温度分布不均匀,注入冷氢时造成同一截 面温差过大,第五床层温差高达52℃。
(3)制氢装置设计时也因对加热炉热膨胀考虑不周, 被迫停工改造。
7
1.1.2 茂名石化公司
(1)加氢高压热油循环泵开工后一直无法运转,致 使该装置一年未进行热油循环,能耗居高不下。
经查,该油泵系日本荏原制作所制造,采用美
国PACIFIC公司技术,首台产品即销往中国。
日方虽竭尽全力,但仍无法正常运转。一年后,
荏原制作所求助美方协助改造,才使油泵投入
使用。日方虽然做了赔偿,但远远不能弥补一
由于设备材质缺陷或选材不当而造成故障或事故 所占比例较大。其中可分为供货质量和设计质量 两大类。特别是供货质量引起的故障,应给予高 度重视设备故障居多。
加氢裂化装置事故处理讲解
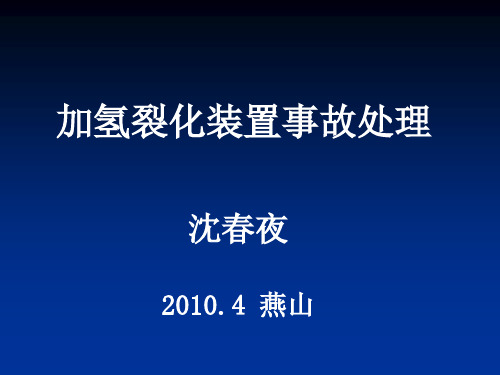
反应系统事故 —— 全装置停电
• 加热炉熄火,烟道挡板、快开风门全开 • 关闭炉前所有瓦斯阀 • 打开放空阀,按紧急降压处理 • 引入补充氢气,继续冷却反应器 • 引入氮气
√ 手动7巴泄压
√ 当床层温度低于正常温度30 ℃时,逐渐恢复正常操作条件 • 当以上处理无效时,如反应器床层最高点温度很快达到428 ℃时,则21巴紧急放空 处理。
反应系统事故 —— 新鲜进料中断
• 加热炉熄火,留长明灯
• 停新氢压缩机
• 循环气继续循环
• 反应器降温至325℃改进低氮油
• 降温至200 ℃时停低氮油,气体循环待命
反应系统事故——原料油带水
• 现象
√ 炉出口温度下降 √ 反应器床层温度下降
√ 反应器出入口压差增大,系统差压上升
√ 生成油颜色变深 • 处理
√ 加强原料油脱水,严重时切换原料罐
√ 防止系统超压 √ 注意系统压差,如果上升很快而降不下来,可减少进油量和氢气量, 严重时可按停原料油处理 √ 因原料油带水引起炉出口、反应器床层温度下降时,炉出口温度不能 提高过多,以免原料油不带水时引起床层超温
• 事故原因:高压串低压,H2爆炸
• 损失巨大:死亡45人,58人受伤,厂房被炸毁,设备、仪 器损坏严重,人的身心安全健康受损。
案例2
• 1987年3月22日7时,英国格朗季蒙斯炼油厂加氢裂化装 置低压分离器因超压发生爆炸,并继而发生大火。事故造
成一人死亡,装置严重损坏。
1.2 飞温事故
• 案例1 • 中石油某加氢裂化装置2007年发生停电事故,循环氢压缩
加氢处理装置安全特点和常见事故分析(汪加海)
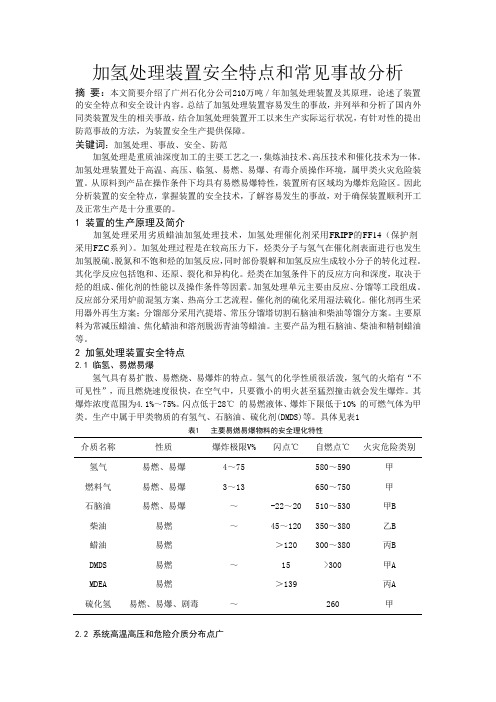
加氢处理装置安全特点和常见事故分析摘要:本文简要介绍了广州石化分公司210万吨/年加氢处理装置及其原理,论述了装置的安全特点和安全设计内容。
总结了加氢处理装置容易发生的事故,并列举和分析了国内外同类装置发生的相关事故,结合加氢处理装置开工以来生产实际运行状况,有针对性的提出防范事故的方法,为装置安全生产提供保障。
关键词:加氢处理、事故、安全、防范加氢处理是重质油深度加工的主要工艺之一,集炼油技术、高压技术和催化技术为一体。
加氢处理装置处于高温、高压、临氢、易燃、易爆、有毒介质操作环境,属甲类火灾危险装置。
从原料到产品在操作条件下均具有易燃易爆特性,装置所有区域均为爆炸危险区。
因此分析装置的安全特点,掌握装置的安全技术,了解容易发生的事故,对于确保装置顺利开工及正常生产是十分重要的。
1 装置的生产原理及简介加氢处理采用劣质蜡油加氢处理技术,加氢处理催化剂采用FRIPP的FF14(保护剂采用FZC系列)。
加氢处理过程是在较高压力下,烃类分子与氢气在催化剂表面进行也发生加氢脱硫、脱氮和不饱和烃的加氢反应,同时部份裂解和加氢反应生成较小分子的转化过程。
其化学反应包括饱和、还原、裂化和异构化。
烃类在加氢条件下的反应方向和深度,取决于烃的组成、催化剂的性能以及操作条件等因素。
加氢处理单元主要由反应、分馏等工段组成。
反应部分采用炉前混氢方案、热高分工艺流程。
催化剂的硫化采用湿法硫化。
催化剂再生采用器外再生方案;分馏部分采用汽提塔、常压分馏塔切割石脑油和柴油等馏分方案。
主要原料为常减压蜡油、焦化蜡油和溶剂脱沥青油等蜡油。
主要产品为粗石脑油、柴油和精制蜡油等。
2 加氢处理装置安全特点2.1 临氢、易燃易爆氢气具有易扩散、易燃烧、易爆炸的特点。
氢气的化学性质很活泼,氢气的火焰有“不可见性”,而且燃烧速度很快,在空气中,只要微小的明火甚至猛烈撞击就会发生爆炸。
其爆炸浓度范围为4.1%~75%。
闪点低于28℃的易燃液体、爆炸下限低于10% 的可燃气体为甲类。
蜡油加氢裂化装置反应器飞温问题研究

蜡油加氢裂化装置反应器飞温问题研究发布时间:2022-06-23T01:32:06.337Z 来源:《科学与技术》2022年第4期2月下作者:张岩[导读] 蜡油加氢裂化装置因具特殊的反应机理而易导致超温、飞温现象,日常工作中需做好超温、飞温的防控工作,降低飞温对催化剂的影响张岩中石油云南石化有限公司云南安宁 650300摘要:蜡油加氢裂化装置因具特殊的反应机理而易导致超温、飞温现象,日常工作中需做好超温、飞温的防控工作,降低飞温对催化剂的影响。
基于此,本文先从原料性质、循环氢流量等方面对蜡油加氢裂化装置反应器飞温原因进行分析,再从循环氢稳定控制、联锁控制策略等方面对飞温控制措施进行分析,提高解决方案的针对性,保障装置能够稳定运行。
关键词:蜡油加氢裂化装置;飞温控制引言:蜡油加氢裂化装置反应器温度的控制是实现装置稳定生产的关键,需要着重对飞温问题进行研究,在高氢分压的作用下,合理对反应参数进行调节,从而提高油品生产过程的安全性。
加氢裂化过程总体是放热反应,需要对温度进行严格控制,降低飞温对装置的影响,确保飞温应对措施的有效性。
1蜡油加氢裂化装置反应器飞温原因分析1.1原料性质发生改变原料组分的变化对飞温现象具有一定的影响,需要对原料组分变化情况进行关注与分析,防止反应热的释放导致温度升高。
在日常生产过程中,原料组分一般随着全厂加工方案的调节而变化,原料性质的改变直接导致加氢反应热的大小从而带来反应器床层温度的变化。
对于硫、氮或烯烃含量较高的原料,反应过程中因不饱和烃的加氢饱和,导致反应器床层温度增加,将会直接影响到反应器温度的稳定控制,增加反应器床层飞温隐患。
当原料中掺入二次加工油(焦化蜡油、催化柴油等)原料性质将会发生质的飞跃,反应过程更加剧烈,反应器床层的温度也会随之而升高。
另外,反应器床层温度还会受到氢气纯度的影响,氢气纯度的改变直接影响反应器内参与加氢反应氢分子的多少,从而改变反应热的释放。
加氢厂火灾事故分析怎么写
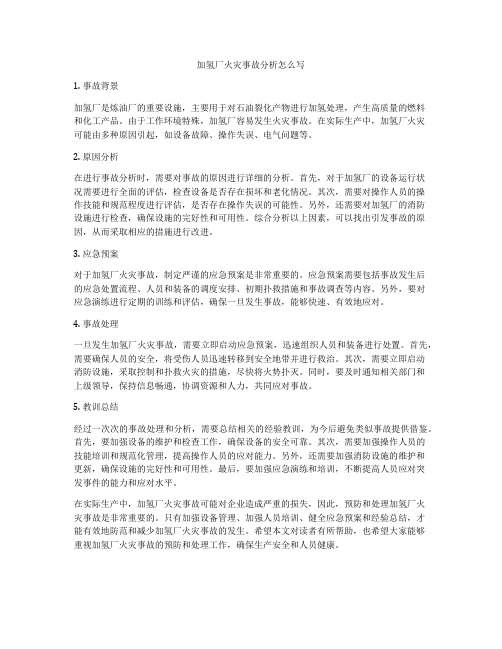
加氢厂火灾事故分析怎么写1. 事故背景加氢厂是炼油厂的重要设施,主要用于对石油裂化产物进行加氢处理,产生高质量的燃料和化工产品。
由于工作环境特殊,加氢厂容易发生火灾事故。
在实际生产中,加氢厂火灾可能由多种原因引起,如设备故障、操作失误、电气问题等。
2. 原因分析在进行事故分析时,需要对事故的原因进行详细的分析。
首先,对于加氢厂的设备运行状况需要进行全面的评估,检查设备是否存在损坏和老化情况。
其次,需要对操作人员的操作技能和规范程度进行评估,是否存在操作失误的可能性。
另外,还需要对加氢厂的消防设施进行检查,确保设施的完好性和可用性。
综合分析以上因素,可以找出引发事故的原因,从而采取相应的措施进行改进。
3. 应急预案对于加氢厂火灾事故,制定严谨的应急预案是非常重要的。
应急预案需要包括事故发生后的应急处置流程、人员和装备的调度安排、初期扑救措施和事故调查等内容。
另外,要对应急演练进行定期的训练和评估,确保一旦发生事故,能够快速、有效地应对。
4. 事故处理一旦发生加氢厂火灾事故,需要立即启动应急预案,迅速组织人员和装备进行处置。
首先,需要确保人员的安全,将受伤人员迅速转移到安全地带并进行救治。
其次,需要立即启动消防设施,采取控制和扑救火灾的措施,尽快将火势扑灭。
同时,要及时通知相关部门和上级领导,保持信息畅通,协调资源和人力,共同应对事故。
5. 教训总结经过一次次的事故处理和分析,需要总结相关的经验教训,为今后避免类似事故提供借鉴。
首先,要加强设备的维护和检查工作,确保设备的安全可靠。
其次,需要加强操作人员的技能培训和规范化管理,提高操作人员的应对能力。
另外,还需要加强消防设施的维护和更新,确保设施的完好性和可用性。
最后,要加强应急演练和培训,不断提高人员应对突发事件的能力和应对水平。
在实际生产中,加氢厂火灾事故可能对企业造成严重的损失,因此,预防和处理加氢厂火灾事故是非常重要的。
只有加强设备管理、加强人员培训、健全应急预案和经验总结,才能有效地防范和减少加氢厂火灾事故的发生。
加氢(裂化)装置生产运行管理及事故处理解读

加氢(裂化)装置生产运行管理及事故处理
中国石化集团健康、安全、环境(HSE)管理体系2001
年正式发布实施,确立了安全第康;科学管理,持续发展的 HSE方针。将健康、安全、环境有机地结合在一起,追求最
大限度地不发生事故、不损害人身健康、不破坏环境,创国
(三)正常生产过程中的工艺安全管理
1.总则
以下的规定必须遵守,以保证装置的运行平稳和安全操作: • 装置必须由当班岗位人员操作,并组成一个从装置主任、技术人员以至倒班人员 所遵守的指挥系统。 • 操作人员应对其本身的职责了解清楚。 • 应安排能通晓化学和机械情况的负责工艺和设备的技术人员(如装置主任)参加 装置的开工和停工。由于这些人员在紧急事故处理时不一定都能在场,所以必须 对操作人员在紧急事故处理步骤上进行良好的训练。 • 操作人员应与装置内部(如车间办公室)以及装置外部有关部门(如厂部调度部 门、原料供应、产品接纳、公用工程供应、化验室、变配电间、维修、消防部门、 急救部门等)保持着经常性的良好通讯联系。 在紧急事故处理和装置开停工操作时,保持这些通讯联系的畅通尤其重要。 • 交班的操作人员在交班前应对装置的情况检查一遍。交接班时交班操作人员应把 出现的异常现象书面交班并告诉接班操作人员。后者接班后必须立即对所有设备 和操作条件查对一次。 • 开关阀门、开停机泵和改变设备运行条件,应由现场操作人员在班长指导下进行。 原则上,除了事故时外操作人员不能按自己的判断对影响装置安全运行的操作进 行大的变动。 • 操作人员做完任何开关阀门、开停机泵和改变设备运行条件后须立即向班长报告, 并交班。
有否变化,如显示有变化时,则表明设备内可能有异常情况的迹象。
•有些联锁系统具有除了自动停的系统以外还有手动停系统,除非是在紧 急事故时,否则不得按动该手停按钮。
加氢裂化事故案例

制定详细的设备维护计划
根据设备特性和运行状况,制定合理的维护计划,确保设备得到 及时、有效的保养。
强化员工培训
定期组织员工参加安全培训和操作技能培训,提高员工的安全意识 和操作技能水平。
建立员工考核机制
对员工的安全知识和操作技能进行定期考核,确保员工具备相应的 安全素质。
成立现场指挥部,由企业负责人担任 指挥长,统一协调指挥应急处置工作。
人员疏散与安置情况
立即组织事故现场人 员疏散,确保人员安 全撤离危险区域。
对疏散人员进行妥善 安置,提供必要的生 活保障和心理疏导。
对受伤人员进行紧急 救治,并安排专人负 责伤员转运和医疗救 治工作。
消防力量投入及灭火过程描述
调集足够的消防力量和装备赶赴 现场,迅速展开灭火救援行动。
加氢裂化事故案例
contents
目录
• 事故背景与概述 • 事故原因分析 • 应急处置与救援措施 • 事故责任追究与处罚结果 • 经验教训总结与预防措施建议 • 未来展望与行业发展趋势分析
01 事故背景与概述
事故发生时间、地点及参与方
时间
01
XXXX年XX月XX日
地点
02
某石化公司加氢裂化装置
强化安全管理体系建设,提升应急处置能力
完善安全管理制度
建立健全的安全管理制度体系,明确各级人员的安全管理 职责和权限。
加强应急预案演练
定期组织应急演练活动,提高员工的应急处置能力和协同 配合能力。
强化安全监管和检查
加大对加氢裂化生产过程的安全监管和检查力度,及时发 现并整改潜在的安全隐患。
06 未来展望与行业发展趋势 分析
监管部门对企业处罚决定
企业被责令停产整顿,并处罚款数百万元。同时,监 管部门要求企业必须对生产装置进行全面检修和评估 ,确保符合安全生产条件后方可恢复生产。
- 1、下载文档前请自行甄别文档内容的完整性,平台不提供额外的编辑、内容补充、找答案等附加服务。
- 2、"仅部分预览"的文档,不可在线预览部分如存在完整性等问题,可反馈申请退款(可完整预览的文档不适用该条件!)。
- 3、如文档侵犯您的权益,请联系客服反馈,我们会尽快为您处理(人工客服工作时间:9:00-18:30)。
加氢裂化飞温事故过程分析作者:日期:2 01 0年3月5日蜡油加氢裂化装置事故开停工过程分析装置停工原因1. 1 0 6-K- 1 02背压蒸汽压力达到4.3MPa,造成汽轮机出口背压蒸汽线上安全阀(放空口为一向下弯头)起跳,并且安全阀未能及时复位,现场大量蒸汽喷向地面并向四周扩散,操作人员无法靠近,不能准确判断具体的泄漏位置,同时避免对系统蒸汽供应产生影响, 操作人员在1 0 9单元关闭进1 0 6装置的9.5MPa蒸汽手阀,循环氢压缩机K1 0 2停运,低速泄压阀启动,装置紧急停工。
事故停、开工经过3月5日5: 4 6装置紧急停工,K1 02停机,反应系统7b a r紧急泄压。
泄压前后床层温度对比如下:1. 3月5日7: 11时向反应系统补氢充压,同时通过7ba r放空泄压。
在开K1 02之前R 101A五床层温度升高约30C,升至38 0C,其他床层没有出现明显温升。
为了及时开启循环氢压缩机 K102恢复生产,通过新氢压缩机K101三回一将系统压力升至1.8MPa,9:38时开循环氢压缩机转速升至1 0 00rpm;3 7 .5m i n后转速升至31 0 0 rpm,防喘振阀打开,循环氢量20000m3/h;30min后循环氢压缩机转速升至5300rpm,R101 A第五床层温升得以控制;1 0min后(11: 05时)循环氢压缩机转速升至63 50r p m R101A/B第5、第6床层冷氢阀全开,此时R10 1A/B第六床层温度已快速升高,最终R 1 0 1A列在1 1: 14时出现下降拐点,而 R101B则在此时飞速上升,在11: 17时最高点温度达到800C, 3分钟后床层温度开始下降。
反应器床层继续循环降温至20 0C,反应系统压力逐渐往1 0M P a控制。
分馏系统热油运短循环,吸收稳定三塔循环。
2.3月5日19:06时开进料泵,反应系统开始进料,装置进入正常开工程序。
3月6日15: 00时柴油改入产品罐,15:36时重石改入产品罐;1 7: 05时轻石、航煤改入产品罐。
开工正常后遗留的主要问题及处理建议3月6日下午柴油产品质量发黄,尾油硫含量505p pm (正常小于3 0),热低分油S :31 8 pp m、N : 1 4 1 ppm(正常S :9 0 ;N:3-5)。
通过分别对E 104 A/ B 管程出口采样目测,发现R101 A生成油颜色蓝而透明,R 101B生成油颜色很黄,从而确定B系列高压换热器内漏,造成原料油泄漏至反应生成油中。
通过对E104 B、E 10 2 B/D、E10 1B管壳程出入口温度数据分析,怀疑E101B的内漏可能性最大。
1四经验教训1、对装置催化剂的性能估计认识不足,未预想到系统压力1 .8MPa左右,反应催化剂床层加氢反应激烈导致大量反应热产生,而此时由于 K102正在升速过程中,短时间内没有冷氢可用无法带走反应热。
2、反应器床层发生超温事故或循环机故障停运事故,系统泄压要一泄到底,至 0.1M Pa左右,避免催化剂床层温度进一步升高。
在反应床层温度超温阶段将反应系统压力泄放至最低是非常有效的降温方式。
3、循环机开机程序过程共需要1 .5h才能够带负荷运行。
延误了通过冷氢量来控制床层温度的时间。
4、装置紧急泄压后,系统压力至0.1 M Pa左右时,如果反应器床层温度下降幅度不大(仍能大于300 r ),则必须通过补入纯度99.99%的高纯氮气,边充边放反应器床层降温至2 00 r后才可以重新恢复进料。
5、循环机K102出口 4.0MPa氮气日常生产中盲板要处于通状态,三阀组双阀开,低点放空开,保证随时处于备用状态。
在紧急停工过程中及时联系化验对 4.0MPa 氮气进行纯度分析,保证合格。
6加强队反应器床层超温和循环机故障停运的反事故处理能力培训工作。
附件一 :PIC 30401操作记录M 2 010-03-05 0 t o Ma n ua 1 p M 20 10- 03-05 t o 47 . 7 0\par M2010-03-05 05 :14:1 7 P IC30401操作记录5 :14:12 1 0 9DM1 10903P_3 PI C 30 401 MA Au to a r 0 5:1 4: 17 1 09D M1 1 0 90 3 P 3 PIC 3 04 01 OUT 48.7 0 109DM1 1090 3 P _3 PIC30 401 O UT 47. 70 t op ar M 2010-03 - 05 0 5 :14:20 5 parM 20 1 0 - 0 3 -05 05: 1 4: 37 1 0 9DM1 1 0 90 3P_3 P IC 30401 OU T 4 5 .7 0M to 1 09 DM1 10903P_3P IC30401 O UT 4 6. 70 to 4 t o 44.70\p ar2 01 0-03-05 05:14 : 4 3. 7 0 pa r 3 7 109D M 1 1 090 3 P _3 PI C 304 01 OUT 44 .70 M2010-0 3 -05 05: 14: to 4 2.70\pa r M 2010-03-05 0 5: 14: o 41. 7 0\p a r M 2010-0 3 -05 to 40.7 0\ par2 0 1 0-03 -05 to 39 .05:14:53 8 1 0 9D M1 1 09 0 3P 3 P I C304 0 1 OUT 43.70 58 109DM1 1 09 03 P 3 PIC304 0 1 OUT 42.70 t 1 0 9D M 1 10903P_3 PIC3040 1 O UT 4 1. 7 0 05 :1 5 : P ar 0 1 10 9 DM1 10903 P_3 P I C30 4 01 O U T 40 .7 1 0 9DM1 109 0 3P _3 P I C30401 OUT 39.70 0 1 0 -03- 0 5 05:15:01 o 38. 7 0\pa r20 10- 0 3 -0 5 05:1 5 : 0 4 109 D M1 10903P_3 P IC 30 40 1 O UT 3 t M 8 .70 t o 37 . 7 0\pa rM 2 010-0 3 - 05 05 : 15:0 4 109 DM 1 10903P_3 PIC3 0 401 O U T 3 7. 70 to 36.70\p a r M 2010-03 — 05 05:15 : 1 1 1 09D M1109 03 P_3 PI C 30 4 01 O U T 3 6. 70 t o 35.70\pa r M 201 0- 03-05 0 5:15:12 109DM1 10903P _3 PI C 30401 OUT 35 .70 to 34. 7 0\par M 2010- 03-0 5 05: 1 5:13 109DML 10 9 03P_3 P IC 304 0 1 OUT to 33.70\pa rM 2010-03- 0 5 05: to M 32.15:18 10 9DM1 10 903P_3 PIC3 0 401 O U T 33. 3 4.70 3 2.7 2010-03 7 0 t o p ar 0 5 31. 0 5:15: 1 9 1 0 9 D M 1 109 0 3P_3 PIC 304 01 7 0\par O UT 5 0 5 :15 : 20 M 20 1 0 -03-0 to 3 0. 7 0 \ par M 2010- 0 3 - 0 5 0 5 :15:27 1 0.7 0 to 29. 7 0\ parM 2 0 10- 0 3- 05 05:1 5 :27109 DM1 10 903P 3 PIC30 4 01 OUT 31. 7 0 0 9D M1 1 0 9 03 P 3 PI C304 0 1 OUT 3 1 09DM1 10903 P_3 PIC30 4 01 OUT 2 9 .27 0 to 2 8.70\p a rM201 0 - 03 - 0 5 0 5: 15:28 1 0 9 DM110903 P _3 P I C30401 OUT28. 70 to 27. 7 0 pa rM 2010-03-05 0 5 : 1 5:35 6.70\ par M 20 1 0-03-05 05:15 : 35 to 25 . 70\par M 2010- 0 3 - 0 5 05: 5. 7 0 M 2 0 6.7 10 9DM1 10903P_3 PIC30401 O UT 27.70 to 109DML 10 9 03P 3 PIC 3 0401 OUT 2 6 .70 1 6: 03 1 0 9 DM1 1 09 0 3P_3 P I C3040 1 O U T 2 t o 2 6 1 0 - 0 3- 0 5 0 to 27.70 0 5 pa r 0 5: 1 6: 03 109D M 1 1 0 90 3 \ par05 : 1 6:04 1 0 9DM 1 10 P _3 PIC3 0 4 0 1 O UT 2 M 201 0-03 27.7 0 M20 1 0-03-0 5 o 2 9 p ar M2 0 1 0 -0 3 -05 05:16:04 o 30.7 0\p ar M 201 0- 0 3-05 05:16 : 05 3 1 .70\pa r M 2010 — 03 -05 0 5 : 1 6:05 1 09D M 1 1 09 0 3P_3 P I C 30401 O U T 3 1.7 0 to 3 2 .7 0 \p a r| M 201 0-03- 0 5 0 5: 1 6:0 7 1 09 DM1 109 03P_3 P I C 30 401 OU T 32 . 70 to 3 3.70\par M 20 10- 0 3— 0 5 0 5 :16:13 1 09DM1 1 0903P_3 PIC30401 O UT 33.70 to 3 2.7 0 \par M 2010-03-0 5 0 5: 1 6:31 1 0 9D M 1 1 0903P 3 P IC 30 4 01 M A Manua lto 2 8 .70\p a r 05: 1 6:04 109D M 1 109 0 3P _3 90 3P I p arP _3 P I C 3 0401 C30401 OUT28.70 OUT1 09D M11090 3P_3P I C 3 0 401 O U T2 9.70 10 9D M 1 109 0 3P3 PIC30401 OUT 30.70 toPIC 3 0 401趋势曲线图Mar 05 1005115:35.■'T< iriT.iiOUTA 10903P^3 picacwoi £5.70 100.00 0,O(KM)CLOSE人一■—I / J —、u H \J______________________________________ 、、、-05:10:00Mar 0505:15:00 Mar 0505:20:00 Mar 05update10903P_3 prcj040i MEAS6,0000 0,0000'=0 ------- i —C 304 0 1控制流程简图PI ■、.IIOLl] 4X1*0 < --------- ------ M_Thh4 ■吒—=_rf -- M ^S.- ■ I I I-.^E T - I ■ ■ P B -T-P 1-5 + T L - T +- ■-.£=■■ ■1-卩 彳扌~~I tJLcn 卜二二rFi —yiiuu L - -- 1 J *.Pi ITIU L131 I WKKlU(循环机转速与循环氢量的关系图)9 :38开循环氢压缩机,系统压力1.8M Pa,转速升至1 0 00 r p m ; 3 7 .5min 后转速逐渐升至3 1 00 rpm,循环氢2 0 000m 3/h 左右;3 0 mi n 后循环氢压缩机转速逐渐升至 5300rp m ,循环氢量40 0 0 0m3左右。