加氢裂化装置生产原理及工艺流程
两段加氢裂化工艺流程
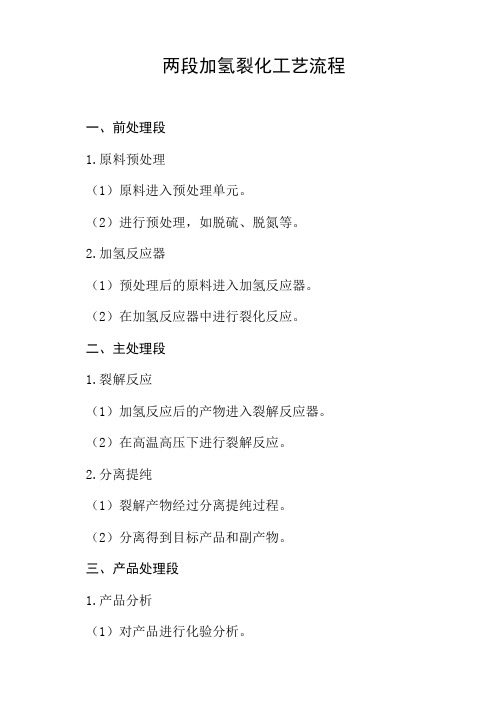
两段加氢裂化工艺流程
一、前处理段
1.原料预处理
(1)原料进入预处理单元。
(2)进行预处理,如脱硫、脱氮等。
2.加氢反应器
(1)预处理后的原料进入加氢反应器。
(2)在加氢反应器中进行裂化反应。
二、主处理段
1.裂解反应
(1)加氢反应后的产物进入裂解反应器。
(2)在高温高压下进行裂解反应。
2.分离提纯
(1)裂解产物经过分离提纯过程。
(2)分离得到目标产品和副产物。
三、产品处理段
1.产品分析
(1)对产品进行化验分析。
(2)确定产品质量和组分。
2.产品储存
(1)合格产品进行储存。
(2)设立储罐或储存设施。
四、废料处理段
1.副产物处理
(1)对副产物进行处理。
(2)如废水处理、废气处理等。
2.资源回收
(1)尽可能回收废料中的有用物质。
(2)减少废料对环境的影响。
五、安全环保措施
1.安全生产
(1)加强生产安全管理。
(2)实施安全防护措施。
2.环保措施
(1)配备污染治理设施。
(2)确保废料处理符合环保标准。
加氢裂化装置生产原理及工艺流程
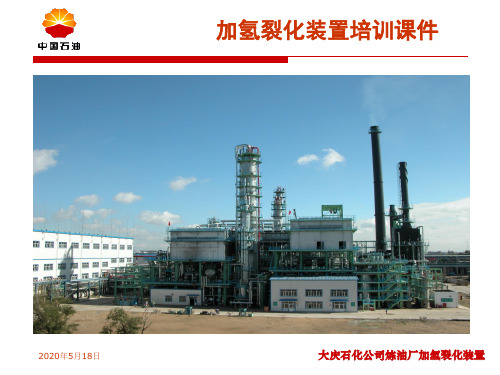
H3C
CH3 CH3
2015年8月15日
大庆石化公司炼油厂加氢裂化装置
二、生产方法及反应机理单环芳烃加氢饱和:源自R多环芳烃加氢饱和:
+ 3H2
+ 2H2 R R
R
R
+ 3H2
R
+ 2H2
R
2015年8月15日
大庆石化公司炼油厂加氢裂化装置
二、生产方法及反应机理
芳烃加氢脱烷基:
R
+ H2
+ RH
环烷烃加氢脱烷基:
2015年8月15日
大庆石化公司炼油厂加氢裂化装置
反应系统 从冷高压分离器(D-3105)分离出来的气体(循环 氢),在循环氢分液罐(D-3107)中分液后,液体 进入冷低压分离器(D-3106),气体经循环氢压缩 机(K-3102)升压后,一路作为急冷氢注入催化剂 床层;一路作为吹扫用循环气去反应进料泵(P3102)出口后路;一路与自新氢压缩机 (K-3101)来的补充新氢混合,经氢气/热高分气换 热器(E-3102)与热高分气换热后与原料油混合, 进入混氢油/反应产物换热器(E-3101),返回反 应系统。冷高分油经减压后进入冷低压分离器(D3106),继续气、油、水三相分离。热低分气相经 过热低分气空冷器(A-3102)冷却后也进入冷低压 分离器(D-3106)。冷高压分离器(D-3105)界控 脱除的含硫污水减压后与冷低压分离器(D-3106) 脱除的含硫污水汇合出装置至污水汽提装置处理,
柴油成品罐区
尾油产品52.69(43.91%)
工业氢1.85
乙烯裂解
2015年8月15日
大庆石化公司炼油厂加氢裂化装置
2、反应系统
循环氢压缩机 新氢压缩机
加氢裂化工艺及过程PPT课件

◎ 1925年建成了第一套褐煤焦油加氢裂化装置,1943年已有12套
装置投入生产。
◎ 二次大战后期,为德国提供了95%的航空汽油和47%的烃类产
品。
◎ 英、法、日(在中国东北-当时的“满洲”)、韩国都进行过类
似的尝试;
◎ 类似技术的研究, 在美国则是直接面向重石油馏分加氢转化技术
的开发。
.
7
催化加氢技术
石化公司建成投产。 ◎ 80年代中期以来, 相继在抚顺、镇海、辽阳、吉林、天津和山东
等地建设了40 140 万吨/年规模的多套加氢裂化装置。 ◎ 90年代末, 大连 WEPEC 和茂名石化公司分别建成了200万吨/年
渣油固定床加氢处理装置。表明我国已具备开发成套催化加氢 技术的能力, 步入了世界加氢技术先进水 平的行列。 ◎ 在清洁燃料的生产中, 加氢技术必将会得到稳步持续地发展。
.
9
催化加氢技术
◎ 1959年Chevron研究公司宣布“加氢异构裂化工艺”在里奇蒙炼 厂
投入工业运转, 证实该发明的催化剂可允许在200400 ℃ 、3.5 14MPa 的条件下操作后, 加氢裂化从此走出低谷。 ◎ 1960年UOP公司开发了 “Lomax”加氢裂化工艺;Union oil 公司开发了“Unicacking”工艺; 60年代加氢裂化作为炼油 技术很快为人们所接受。 ◎ 1966年有7种加氢裂化技术获得了销售许可证; 60年代末 已投产和在建的有9种不同的工艺; 其催化剂的活性、稳 定性都好于早期催化剂, 特别是.分子筛催化剂得到工业 10
催化加氢技术
◎ 在60年代, 加氢裂化能满足石脑油、喷气燃料、柴油、润滑油基 础油、低硫燃料油、液化石油气及石油化工原料生产的要求, 充分证明加氢裂化技术具有极重要的作用和广泛的应用前景。
加氢裂化工艺流程介绍
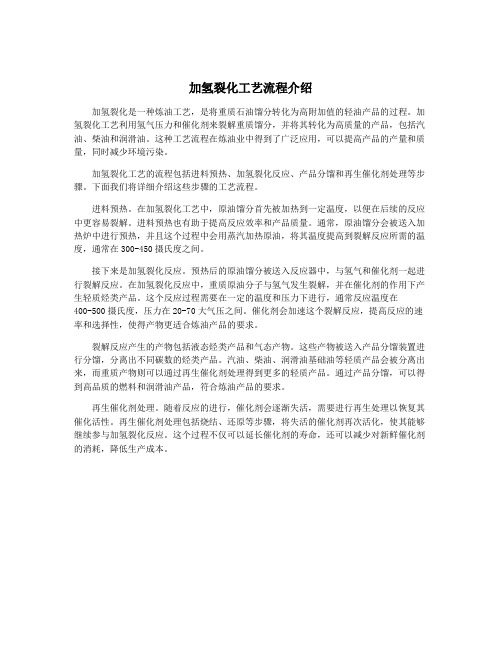
加氢裂化工艺流程介绍加氢裂化是一种炼油工艺,是将重质石油馏分转化为高附加值的轻油产品的过程。
加氢裂化工艺利用氢气压力和催化剂来裂解重质馏分,并将其转化为高质量的产品,包括汽油、柴油和润滑油。
这种工艺流程在炼油业中得到了广泛应用,可以提高产品的产量和质量,同时减少环境污染。
加氢裂化工艺的流程包括进料预热、加氢裂化反应、产品分馏和再生催化剂处理等步骤。
下面我们将详细介绍这些步骤的工艺流程。
进料预热。
在加氢裂化工艺中,原油馏分首先被加热到一定温度,以便在后续的反应中更容易裂解。
进料预热也有助于提高反应效率和产品质量。
通常,原油馏分会被送入加热炉中进行预热,并且这个过程中会用蒸汽加热原油,将其温度提高到裂解反应所需的温度,通常在300-450摄氏度之间。
接下来是加氢裂化反应。
预热后的原油馏分被送入反应器中,与氢气和催化剂一起进行裂解反应。
在加氢裂化反应中,重质原油分子与氢气发生裂解,并在催化剂的作用下产生轻质烃类产品。
这个反应过程需要在一定的温度和压力下进行,通常反应温度在400-500摄氏度,压力在20-70大气压之间。
催化剂会加速这个裂解反应,提高反应的速率和选择性,使得产物更适合炼油产品的要求。
裂解反应产生的产物包括液态烃类产品和气态产物。
这些产物被送入产品分馏装置进行分馏,分离出不同碳数的烃类产品。
汽油、柴油、润滑油基础油等轻质产品会被分离出来,而重质产物则可以通过再生催化剂处理得到更多的轻质产品。
通过产品分馏,可以得到高品质的燃料和润滑油产品,符合炼油产品的要求。
再生催化剂处理。
随着反应的进行,催化剂会逐渐失活,需要进行再生处理以恢复其催化活性。
再生催化剂处理包括烧结、还原等步骤,将失活的催化剂再次活化,使其能够继续参与加氢裂化反应。
这个过程不仅可以延长催化剂的寿命,还可以减少对新鲜催化剂的消耗,降低生产成本。
加氢裂化装置优化运行生产航煤技术攻关

加氢裂化装置优化运行生产航煤技术攻关为了提高航煤的品质,同时降低其生产成本,加氢裂化装置的优化运行成为了一项具有重要意义的技术攻关。
针对这一问题,本文将从以下三个方面进行探讨:加氢裂化装置的工艺原理和流程;装置优化运行的必要性和挑战;装置优化运行中的关键技术和应用方法。
一、加氢裂化装置的工艺原理和流程加氢裂化是利用催化剂和氢气使长链烃分子在高温下断裂成短链分子的工艺。
加氢裂化装置的主要部件包括加氢反应器、分馏塔、冷却器等。
其工艺流程如下图所示:[插入图片]在这一工艺中,原料油进入加氢反应器后,在氢气的存在下,经过高温高压的加氢反应,长链烃分子被断裂成短链烃分子。
随着反应的进行,反应器中不断有新的短链分子生成,同时也有短链分子进一步加氢,生成更短的分子。
这时,分馏塔将反应产物分为轻质和重质两部分,轻质部分包含甲烷、乙烷、丙烷等气态产品,重质部分则包含乙烯、丙烯、苯等液态产品。
最后,这些产品经过冷却器冷却,通过分选装置分离出不同产品。
二、装置优化运行的必要性和挑战加氢裂化装置的优化运行主要是为了提高产品的催化裂化效率和产品品质,同时降低生产成本。
具体来说,装置优化运行的必要性体现在以下几个方面:1.提高产品的品质。
通过优化反应的温度、压力、质量比等因素,可以使产物中不同组分的含量得到有效控制,从而提高产品的品质和附加值。
2.降低生产成本。
装置优化运行可以帮助企业在提高产品品质的同时,尽可能降低生产成本,提高经济效益和市场竞争力。
3.优化反应系统的安全性。
优化加氢裂化装置的运行参数,可以有效减少一些不必要的反应失控和事故风险,保证生产过程的稳定性和安全性。
然而,装置优化运行所面临的挑战也不容忽视。
首先,加氢裂化反应机理较为复杂,其反应产物不仅涉及到烃类气体和液体,还可能出现其他非烃类物质,例如硫化物、酸性物等。
其次,不同反应物质的加工条件和要求也不尽相同,因此在不同的工作状态下对不同反应物质进行加工还需要进行针对性的优化。
加氢裂化工艺流程
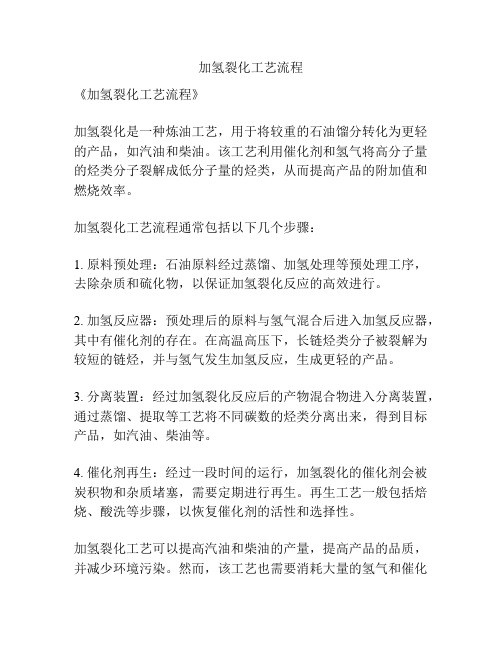
加氢裂化工艺流程
《加氢裂化工艺流程》
加氢裂化是一种炼油工艺,用于将较重的石油馏分转化为更轻的产品,如汽油和柴油。
该工艺利用催化剂和氢气将高分子量的烃类分子裂解成低分子量的烃类,从而提高产品的附加值和燃烧效率。
加氢裂化工艺流程通常包括以下几个步骤:
1. 原料预处理:石油原料经过蒸馏、加氢处理等预处理工序,去除杂质和硫化物,以保证加氢裂化反应的高效进行。
2. 加氢反应器:预处理后的原料与氢气混合后进入加氢反应器,其中有催化剂的存在。
在高温高压下,长链烃类分子被裂解为较短的链烃,并与氢气发生加氢反应,生成更轻的产品。
3. 分离装置:经过加氢裂化反应后的产物混合物进入分离装置,通过蒸馏、提取等工艺将不同碳数的烃类分离出来,得到目标产品,如汽油、柴油等。
4. 催化剂再生:经过一段时间的运行,加氢裂化的催化剂会被炭积物和杂质堵塞,需要定期进行再生。
再生工艺一般包括焙烧、酸洗等步骤,以恢复催化剂的活性和选择性。
加氢裂化工艺可以提高汽油和柴油的产量,提高产品的品质,并减少环境污染。
然而,该工艺也需要消耗大量的氢气和催化
剂,并且对原料的要求较高,因此需要精细的工艺控制和运行管理。
随着石油工业的不断发展,加氢裂化工艺也在不断完善和优化,以适应市场的需求和环保的要求。
加氢裂化装置简介教材

加氢裂化主催化剂性质
物化性质 孔容/mL/g 表面积/m2/g 堆密度/ g/100ml 压碎强度/ N/mm 烧减,mt% 磨耗,mt% 形状 条长/mm 直径/mm
3936 0.32-0.38 >160 88-94 >25 <2.0 <1.0 三叶草 3-8 1.2-1.4
ZHC-01 0.30-0.35 ≥240 96-102 >14.7 <3.0 柱状 3-8 1.5-1.7
加氢裂化装置概述 设计的原料组成为131.2万t/a中东高硫蜡油和8.8万t/a胜利 焦化蜡油,中试评价采用沙轻VGO:沙中VGO:科威特 VGO=46:8:46的混合油。所需H2 为联合布局的连续重整装 置和乙烯裂解装置产生的氢气经本装置PSA部分提纯至纯度 99.9% ,不足部分由制氢装置补充。2001年4月氢气流程动改 后,在连续重整装置停工的情况下,可由第二化肥厂天然气制 氢供给氢气。装置建设规模为140万t/a(175t/h),装置设计 运转周期为8000h(11个月)。 装置由反应、分馏、吸收稳定、气体脱硫、溶剂再生和氢 气提纯(PSA)等部分组成。 主要产品是液化气、石脑油、航煤、柴油和尾油,同时副 产部分气体。设计的转化率为60%,其中尾油做乙烯裂解的原 料。
加氢裂化装置主要影响因素
• 反应压力 反应压力是通过冷高分压力来控制的, 为使反应向有利于加氢裂化的方向进行, 应使反应系统维持尽可能高的氢分压,因 此冷高分应在尽可能高的压力下操作。考 虑到冷高分的设计压力,冷高分操作压力 不能超过16.3MPa。
加氢裂化装置流程说明
1.反应部分 2.分馏部分 3.吸收稳定部分 4.脱硫部分
2.加氢裂化反应器(R-402)共有四个床层,催化剂 装填数据见附表。ZHC-01为加氢裂化主催化剂,属 无定型类催化剂,含有一定量的分子筛。因此,其裂 化活性没有分子筛型的强,反应缓和,起始温度较高。 ZTS-3是后精制催化剂,用来饱和裂化反应产生的少 量不饱和烃。
加氢裂化装置工艺流程描述
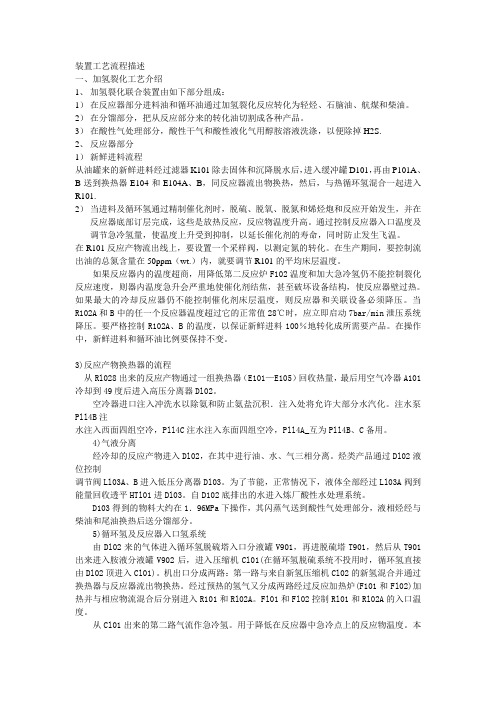
装置工艺流程描述一、加氢裂化工艺介绍1、加氢裂化联合装置由如下部分组成:1)在反应器部分进料油和循环油通过加氢裂化反应转化为轻烃、石脑油、航煤和柴油。
2)在分馏部分,把从反应部分来的转化油切割成各种产品。
3)在酸性气处理部分,酸性干气和酸性液化气用醇胺溶液洗涤,以便除掉H2S.2、反应器部分1)新鲜进料流程从油罐来的新鲜进料经过滤器K101除去固体和沉降脱水后,进入缓冲罐D101,再由P101A、B送到换热器E104和E104A、B,同反应器流出物换热,然后,与热循环氢混合一起进入R101.2)当进料及循环氢通过精制催化剂时,脱硫、脱氧、脱氮和烯烃炮和反应开始发生,并在反应器底部订层完成,这些是放热反应,反应物温度升高。
通过控制反应器入口温度及调节急冷氢量,使温度上升受到抑制,以延长催化剂的寿命,同时防止发生飞温。
在R101反应产物流出线上,要设置一个采样阀,以测定氮的转化。
在生产期间,要控制流出油的总氮含量在50ppm(wt.)内,就要调节R101的平均床层温度。
如果反应器内的温度超商,用降低第二反应炉F102温度和加大急冷氢仍不能控制裂化反应速度,则器内温度急升会严重地使催化剂结焦,甚至破坏设备结构,使反应器壁过热。
如果最大的冷却反应器仍不能控制催化剂床层温度,则反应器和关联设备必须降压。
当R102A和B中的任一个反应器温度超过它的正常值28℃时,应立即启动7bar/min泄压系统降压。
要严格控制R102A、B的温度,以保证新鲜进料100%地转化成所需要产品。
在操作中,新鲜进料和循环油比例要保持不变。
3)反应产物换热器的流程从Rl028出来的反应产物通过一组换热器(E101—E105)回收热量,最后用空气冷器A101冷却到49度后进入高压分离器Dl02。
空冷器进口注入冲洗水以除氨和防止氨盐沉积.注入处将允许大部分水汽化。
注水泵Pll4B注水注入西面四组空冷,Pll4C注水注入东面四组空冷,Pll4A_互为Pll4B、C备用。
加氢裂化工艺及过程 ppt课件

中国石油化工股份有限公司
CHINA PETROLEUM & CHEMICAL CORPORATION
金陵石化分公司炼油运行一部
PPT课件
1
催化加氢技术
1.0 概述 1.1 加氢裂化的沿革 1.2 国内加氢裂化技术发展历程 1.3 加氢裂化的基本原理及特点 1.4 加氢裂化原料油及产品 2.0 加氢裂化工艺流程 2.1 两段法加氢裂化 2.2 单段加氢裂化 2.3 一段串联(单程通过,未转化油全循环、部分循环)
PPT课件
12
催化加氢技术
1.2 国内加氢裂化技术的发展
◎ 50年代, 恢复了页岩粗柴油高压加氢, 发展了页岩油全馏分固定
床加氢裂化, 以及低温干馏煤焦油的高压三段加氢裂化技术。
◎ 60年代中期, 开发了107、219无定型加氢裂化催化剂和H-06沸石
催化剂;
◎ 1966年在大庆炼厂建成了40万吨/年加氢裂化装置, 加工大庆常三
为现代渣油悬浮床加氢以及馏分油固定加氢的基本模式奠定了基 础。
PPT课件
8
催化加氢技术
◎ 二战以后, 可多方获得中东油, 催化裂化技术的发展, 为重瓦斯 油(HVGO)转化生产汽油提供了更经济的手段, 加氢裂化的重要 性曾一度有所降低。
◎ 40年代末50年代初的“相关事件”, 铁路运输由蒸汽机车向柴油 机车驱动的转变,廉价天然气的供应使燃料油用量减少, FCC 发展导致富含芳烃难转化的循环油过剩, 汽车压缩比的提高和 高辛烷值汽油标准的实施等, 都迫切需要将难转化的原料加工 成汽油、柴油,导致对新的烃类转化技术需求的增产。
PPT课件
9
催化加氢技术
◎ 1959年Chevron研究公司宣布“加氢异构裂化工艺”在里蒙炼 厂
加氢裂化装置生产原理

加氢裂化装置生产原理原料进入装置与氢气混合,经加热到一定温度首先进入精制反应器,用床层冷氢控制合适的反应温度,在保护剂和精制催化剂的作用下,发生加氢脱金属(HDM)、加氢脱硫(HDS)、加氢脱氮(HSN)、加氢脱氧(HDO)及不饱和烃(烯烃类、芳烃)的加氢饱和等反应,生成杂质很低,且氮含量≯10ppm 的精制油,然后进入裂化反应器,用床层冷氢控制合适的反应温度,继续在裂化催化剂和后精制催化剂作用下,发生加氢异构化和裂化(包括开环)反应及部分精制反应,获得所需转化率下产品分布的裂化气,经初步降压降温分离后,大部分气相进入循环气系统,经循环机后在反应系统循环使用,维持反应系统压力和反应系统所需氢气,为保证循环气中的氢纯度,则由新氢机不断补充反应系统氢气的不足。
小部分气相经本装置脱硫塔后,与重整氢一起做PSA原料;液相则先进入脱丁烷和脱乙烷塔,进一步气液相分离,分离出液化气、干气和反应生成油,液化气出装置去二催化碱洗,干气经本装置轻烃吸收塔后,出装置去干气脱硫装置;生成油先进入常压塔,分离出轻、重石脑油、航煤、柴油和尾油,轻、重石脑油、航煤、柴油分别出装置,而尾油则进入减压塔,经过减压蒸馏,生产出乙烯料、轻、中、重润滑油,分别出装置。
其中部分的尾油循环到原料过滤器的入口再次加氢裂化。
1.1反应原理加氢裂化工艺过程的反应概括为两类:加氢精制:一般指杂原子烃中杂原子的脱除反应如加氢脱金属(HDM)、加氢脱硫(HDS)、加氢脱氮(HSN)、加氢脱氧(HDO)及不饱和烃(烯烃类、芳烃)的加氢饱和,这些反应主要发生在单段串联流程的第一反应器或两段流程的第一段加氢裂化:烃类的加氢异构化和裂化(包括开环)反应。
发生在单段串联流程的第二反应器或两段流程的第二段1.1.1加氢精制反应1.1.1.1 加氢脱金属就是通过加氢工艺从重油中把含金属的有机杂质脱除。
金属组分主要浓集在540℃以上的馏分中,石油中的金属组分主要是钒和镍,就馏份油加氢裂化装置而言,进料中还含有在原油一次加工过程中产生的铁,一般与硫、氮、氧等杂原子以化合物或络合物状态存在,在加氢脱硫、氮、氧时,也脱除了金属,相对而言,加氢脱金属反应进行比较容易;这些金属组分无论以任何形式在催化剂上沉积都可能造成催化剂微孔堵塞或催化剂活性位的破坏而导致催化剂失活,为降低床层催化剂失活速率和保证装置长周期运行,在精制反应前部床层一般装填大孔径、活性相对不高的保护剂,用于脱除进料中的金属组分,被脱除的金属组分在催化剂微孔、表面或间隙间沉积,所以对保护剂床层来讲,必须具备较强的容金属性,否则将造成床层压降在短时间内升高,严重时装置必须停工进行撇顶处理,因此,对装置长周期运行而言要严格控制进料中重金属含量。
【分享】加氢裂化工艺流程图
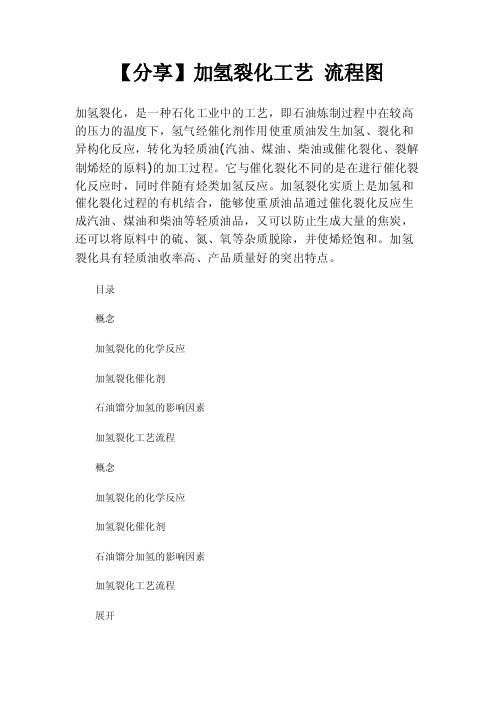
【分享】加氢裂化工艺流程图加氢裂化,是一种石化工业中的工艺,即石油炼制过程中在较高的压力的温度下,氢气经催化剂作用使重质油发生加氢、裂化和异构化反应,转化为轻质油(汽油、煤油、柴油或催化裂化、裂解制烯烃的原料)的加工过程。
它与催化裂化不同的是在进行催化裂化反应时,同时伴随有烃类加氢反应。
加氢裂化实质上是加氢和催化裂化过程的有机结合,能够使重质油品通过催化裂化反应生成汽油、煤油和柴油等轻质油品,又可以防止生成大量的焦炭,还可以将原料中的硫、氮、氧等杂质脱除,并使烯烃饱和。
加氢裂化具有轻质油收率高、产品质量好的突出特点。
目录概念加氢裂化的化学反应加氢裂化催化剂石油馏分加氢的影响因素加氢裂化工艺流程概念加氢裂化的化学反应加氢裂化催化剂石油馏分加氢的影响因素加氢裂化工艺流程展开编辑本段概念定义类型:石化工业术语拼音:jiaqingliehua英文名称:hydrocracking条件10-15兆帕(100-150大气压),400℃左右。
优缺点加氢裂化的液体产品收率达98%以上,其质量也远较催化裂化高。
虽然加氢裂化有许多优点,但由于它是在高压下操作,条件较苛刻,需较多的合金钢材,耗氢较多,投资较高,故没有像催化裂化那样普遍应用。
编辑本段加氢裂化的化学反应烃类在加氢裂化条件下的反应方向和深度,取决于烃的组成、催化剂性能以及操作条件,主要发生的反应类型包括裂化、加氢、异构化、环化、脱硫、脱氮、脱氧以及脱金属等。
加氢裂化①烷烃的加氢裂化反应。
在加氢裂化条件下,烷烃主要发生C-C键的断裂反应,以及生成的不饱和分子碎片的加氢反应,此外还可以发生异构化反应。
②环烷烃的加氢裂化反应。
加氢裂化过程中,环烷烃发生的反应受环数的多少、侧链的长度以及催化剂性质等因素的影响。
单环环烷烃一般发生异构化、断链和脱烷基侧链等反应;双环环烷烃和多环环烷烃首先异构化成五元环衍生物,然后再断链。
③烯烃的加氢裂化反应。
加氢裂化条件下,烯烃很容易加氢变成饱和烃,此外还会进行聚合和环化等反应。
加氢裂化

第十章加氢裂化第一节概述随着近代工业的迅速发展,要求石油炼制工业不但在数据上,而且在质量上提供更多更好的燃料油和润滑油,因而也就促进和要求对炼油技术的不断革命和改造。
催化加氢过程正是在这个前提下,为了完成石油的深度加工,最大限度的提高轻质油收率和产品质量而发展起来的新型工艺。
催化加氢过程包括为提高汽油、煤油、柴油质量的馏分油加氢精制;生产优质柴油、航空煤油、汽油或润滑油的重馏分油加氢裂化;用含碳或高含硫原油生产低硫燃料油的渣油加氢脱硫等。
石油馏分的加氢裂化是六十年代发展起来的新工艺,是近十多年来炼油技术发展的一个重要成就。
它是在较高压力(80-175大气压)、较高温度(260-480℃)和小号外部供应氢气(轻油体积比1::1000-2500)的情况下,在催化剂上进行不同的化学反应,将烃类原料转化为较低沸点生成油的催化加工过程。
加氢裂化催化剂是一种双功能催化剂,功能之一是将原料中的高沸点化合物裂化和异构化,功能之二是将原料和反应物中的烯烃等不饱和烃进行加氢使其变成饱和物。
目前以分子筛为担体或在担体上加入大量分子筛的催化剂多用于生产汽油和煤油,例如以Pd-Y型催化剂生产汽油和航空煤油有较好的活性、选择性和稳定性。
以无定型SiO2-Al2O3或SiO2-MgO为担体的非金属催化剂可用来生产低点柴油而保持较长的使用寿命。
加氢裂化过程是用加氢的办法来改变原料的碳氢比,在外界引入氢气并保持一定的氢压下,可抑制高分子缩合物和焦炭的生成;可使产品中不含烯烃而具有较好的安定性;可使原料中所含的硫、氮、氧等杂质除去;另外加氢裂化过程改变聊原料分子的结构,其产品中富有异构烃。
基于这些变化,就决定了加氢裂化过程有原料范围广、产品质量好的特点。
这对加工含硫特别是高含硫原料油,并从中制取优质产品具有十分重要的意义。
实际上加氢裂化原料油的范围极广,从粗汽油到重柴油,各种重油,甚至丙烷脱沥青油都可以加工,并生产出不同的优质产品。
加氢裂化装置课件
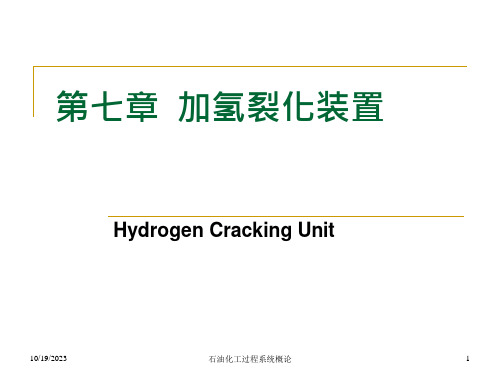
10/22/2023
8
石油化工过程系统概论
根据原料及目的产品的不同,固定床加氢裂 化大致分为下列几种流程。
1.单段加氢裂化流程 单段加氢裂化流程中只有一个反应器,原料油
加氢精制和加氢裂化在同一反应器内进行。反应 器上部为精制段,下部为裂化段。
10/22/2023
29
石油化工过程系统概论
有些设计自催化剂支持盘到 再分配盘之间设置几个连通 管,卸催化剂只要打开底封 头上的卸料口,就可以卸出 全部催化剂。
10/22/2023
30
石油化工过程系统概论
本章重点
1.加氢裂化的作用是什么? 2.加氢裂化有哪些特点? 3.加氢裂化如何分类? 4.根据介质是否直接接触金属器壁,高压加氢
10/22/2023
11
石油化工过程系统概论
2.两段加氢裂化流程 两段加氢裂化流程中有两个反应器,分别装
有不同性能的催化剂。
第一个反应器中主要进行原料油的精制; 第二个反应器中主要进行加氢裂化反应,形成 独立的两段流程体系。
10/22/2023
12
石油化工过程系统概论
汽提塔的作用:脱去NH3和H2S以及残留在油 中的气体。
10/22/2023
7
石油化工过程系统概论
(一)固定床加氢裂化 固定床是指将颗粒状的催化剂放置在反应器内,
形成静态催化剂床层。原料油和氢气经升温、升 压达到反应条件后进入反应系统,先进行加氢精 制以除去硫、氮、氧杂质和二烯烃,再进行加氢 裂化反应。反应产物经降温、分离、降压和分馏 后,目的产品送出装置,分离出含氢较高(80%、 90%)的气体,作为循环氢使用。
加氢裂化装置生产原理及工艺流程
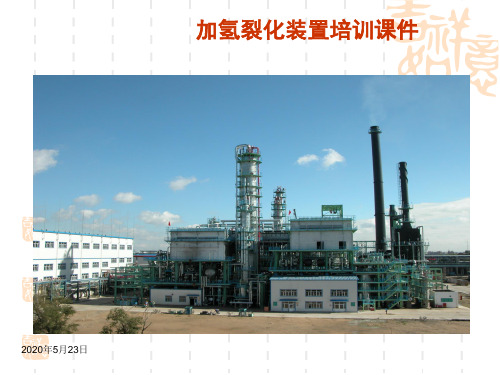
分馏进料 加热炉
汽提蒸汽
汽提蒸汽 柴油汽提塔
尾油泵
柴油泵
航煤泵
重石脑油泵
轻石脑油泵 轻石脑油水冷器
轻石脑油
石脑油 重沸器
尾油空冷
尾油缓冲罐
重石脑油
重石脑 重石脑 油空冷 油水冷
尾油接力泵
尾油
注:粗线为主流程
2020年5月23日
分馏系统
▪ 冷低分油在航煤/冷低分油换热器(E-3208)和航煤 产品换热后与热低分油混合进入脱气塔(C-3201) 第26层塔板,在脱气塔中脱除轻烃和硫化氢。塔顶气 相经脱气塔顶空冷器(A-3201)和脱气塔顶水冷器 (E-3201)冷却后进入脱气塔顶回流罐(D-3201) ,回流罐顶气体去制氢装置,液体经脱气塔顶回流泵 (P-3202)打回脱气塔做塔顶回流。脱气塔底油经泵 (P-3201)送至柴油/分馏进料换热器(E-3211)和 尾油/分馏进料换热器(E-3202)分别与柴油和尾油 产品换热后,去分馏塔进料加热炉(F-3201)加热至 要求的温度(346℃),之后进入主分馏塔(C-3202 )第8层塔板,在主分馏塔内实现分馏过程。分馏塔 顶
装置内高温高压法兰、分馏塔、塔底热油泵、高温高压循环油泵、产品泵, 压缩机管线等部位容易着火。
2020年5月23日
二、生产方法及反应机理
加氢裂化指在加氢反应过程中,原料油的分子有 10% 以上变小的那些加 氢技术。烷烃(烯烃)在加氢裂化过程中主要进行裂化、异构化和少量环化 的反应。烷烃在高压下加氢反应而生成低分子烷烃,包括原料分子某一处 C—C键的断裂,以及生成不饱和分子碎片的加氢。烯烃加氢裂化反应生成相 应的烷烃,或进一步发生环化、裂化、异构化等反应。
2020年5月23日
反应系统
加氢工艺

烷烃
18
多环芳烃的加氢裂化反应
反应十分复杂,包括逐环加氢、开环、环 异构、脱烷基等一系列平行、顺序反应
多环芳烃,第一环加氢饱和速率很快、生 成多环环烷芳烃
多环芳烃中的环烷环很易开环,并相继发 生异构、脱烷基等反应
19
多环芳烃的加氢裂化反应
多环芳烃中最后,次环芳烃的加氢饱和速 度则递减
含氧化合物反应活性顺序为: 呋喃环类>酚类>酮类>醛类>烷基醚类
烯烃饱和反应 烯烃饱和是将烯烃通过加氢转化为相应的烷烃,反
应如下: R–CH=CH–R' + H2 → R–CH2–CH2–R'
9
加氢脱金属 原料中以有机化合物形式存在的金属被吸附在催化剂
表面上而除去,反应如下:
R–M–R' + H2 + H2S → MS + RH + R'H 因此要注意原料中金属杂质含量,过高的浓度的沉积可 能导致催化剂活性位破坏而失活,从而催化剂撇头。 由以上反应可知,加氢精制可以使有机硫、氮、氧化物 与氢反应,分别生成H2S、NH3和H2O,它们很容易与烃 类分离,这样就达到了精制的目的。 这些非烃类化合物加氢时,它们的相对转化速率是不同 的,其转化速率为:
硫化及钝化、 换进原料油) 3.2 加氢裂化装置正常运转及相关工艺参数的影响 3.3 加氢裂化装置正常停工及紧急停工
3
1.概述
加氢裂化原料适应性强,可用范围宽,产品方案 灵活、质量好,液收高 能生产液化石油气、石脑油、喷气燃料、柴油等 多种优质产品,以及蒸汽裂解、润滑油基础油等石 油化工原料; 加氢裂化是从VGO直接制取清洁燃料的加工技术, 为炼油企业主要支柱技术之一。 (VGO,减压瓦斯 油,指原油经减压蒸馏所得到的沸程范围约为 350~500℃的馏分油的总称,是一种重质油)
加氢裂化 石脑油 辛烷值

加氢裂化石脑油辛烷值加氢裂化是一种常用的石脑油加工技术,其能够提高石脑油的辛烷值,从而提升石脑油的燃烧性能。
本文将从加氢裂化的原理、工艺流程和优势等方面进行详细介绍。
一、加氢裂化的原理加氢裂化是利用催化剂在高温高压下将长链烃分子裂解成较短链烃分子的过程。
在加氢裂化过程中,催化剂起到了重要的作用,它能够降低裂解反应的活化能,促进烃分子的裂解反应。
同时,加氢裂化还引入了氢气,通过与催化剂上的氢气发生反应,可以还原催化剂的活性,延长其使用寿命。
二、加氢裂化的工艺流程加氢裂化主要包括预热、催化裂化、加氢、分离等几个步骤。
首先,原料石脑油经过预热设备升温至合适的温度,以提高反应速率。
然后,进入催化裂化器,与催化剂接触,发生裂解反应。
此时,加入适量的氢气,通过与催化剂上的氢气发生反应,可以还原催化剂的活性,提高反应效果。
最后,通过分离装置将裂解产物进行分离,得到目标产品。
三、加氢裂化的优势1. 提高辛烷值:加氢裂化可以将长链烃分子裂解成较短链烃分子,从而提高石脑油的辛烷值。
辛烷值是衡量石脑油燃烧性能的重要指标,较高的辛烷值意味着石脑油具有更好的抗爆震性能和燃烧稳定性。
2. 提高产率:加氢裂化可以提高石脑油的产率,减少废料的生成。
通过裂解长链烃分子,可以将原本难以利用的石脑油转化为更有价值的产品,提高资源的利用效率。
3. 降低环境污染:加氢裂化可以将石脑油中的硫、氮等杂质去除,减少有害气体的排放。
同时,通过优化工艺条件和催化剂的选择,可以降低裂解反应的温度和压力,减少能源消耗和环境污染。
4. 增加产品多样性:加氢裂化可以根据市场需求调整工艺条件和催化剂的选择,从而生产出不同规格和质量的石脑油产品,增加产品的多样性和市场竞争力。
加氢裂化是一种能够提高石脑油辛烷值的重要技术。
通过裂解长链烃分子,加氢裂化可以提高石脑油的辛烷值,并带来诸多优势,如提高产率、降低环境污染和增加产品多样性等。
随着工艺的不断改进和催化剂的研发,加氢裂化将在石脑油加工领域发挥更加重要的作用。
加氢裂化装置生产原理及工艺流程讲课教案
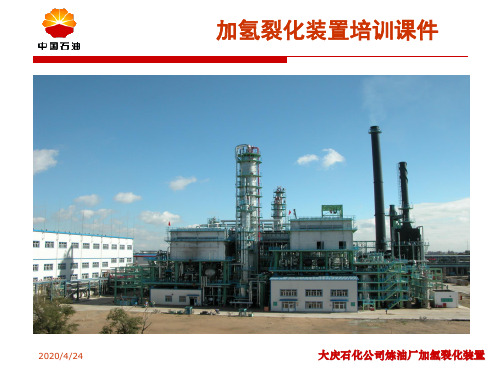
环烷烃加氢脱烷基:
R
+ H2
+ RH
+ RH
2020/4/24
大庆石化公司炼油厂加氢裂化装置
二、生产方法及反应机理
烷烃异构化:
CH3 R
CH3
CH3 R
CH3 CH3
2020/4/24
大庆石化公司炼油厂加氢裂化装置
三、工艺技术路线及流程
1、装置物料平衡 2、反应系统 3、分馏系统
2020/4/24
装置内高温高压法兰、分馏塔、塔底热油泵、高温 高压循环油泵、产品泵,压缩机管线等部位容易着火。
2020/4/24
大庆石化公司炼油厂加氢裂化装置
二、生产方法及反应机理
加氢裂化指在加氢反应过程中,原料油的分子有 10% 以上变小的那些加氢技术。烷烃(烯烃)在加氢 裂化过程中主要进行裂化、异构化和少量环化的反应。 烷烃在高压下加氢反应而生成低分子烷烃,包括原料 分子某一处C—C键的断裂,以及生成不饱和分子碎片 的加氢。烯烃加氢裂化反应生成相应的烷烃,或进一 步发生环化、裂化、异构化等反应。
典型的化学反应有以下:
2020/4/24
大庆石化公司炼油厂加氢裂化装置
二、生产方法及反应机理
加氢脱硫(HDS):
R
S + 6H2 R
加氢脱氮(HDN):
R
NH+ 6H2 R
CH3+ H2S CH3+ NH3
2020/4/24
大庆石化公司炼油厂加氢裂化装置
二、生产方法及反应机理
烯烃加氢饱和:
H3 C
大庆石化公司炼油厂加氢裂化装置
1、装置物料平衡
装置物料平衡表
物料
原料油 入 工业氢 方 合计
加氢裂化工艺及过程

04 加氢裂化工艺流程
原料预处理
原料选择
选择低硫、低氮、低芳烃的原料,如减压馏分油、 脱沥青油等。
原料切割
根据原料性质和加氢裂化要求,将原料切割成适 合的馏分。
预处理
通过加热、过滤、脱水和脱盐等手段,去除原料 中的水分、金属离子和杂质,提高原料的纯度。
产物选择性
加氢裂化产物复杂多样,如何提高目标产品的选择性是当前面临的 重要技术挑战。
能耗与环保
加氢裂化过程能耗较高,且产生一定量的废水和废气,如何降低能 耗并实现环保排放是一大挑战。
未来发展方向与展望
01
02
03
04
新材料的应用
探索新型的催化剂和材料,以 提高加氢裂化过程的效率和产
物选择性。
过程强化
质量调整
02
03
精制处理
通过调整温度、压力和添加催化 剂等手段,对产品进行质量调整, 以满足市场需求。
通过加氢精制、酸碱精制等方法, 去除产品中的杂质和有害物质, 提高产品的质量和稳定性。
05 加氢裂化技术发展与挑战
技术发展趋势
高效催化剂
随着催化剂科学的不断发展,高效、稳定的 催化剂是加氢裂化技术的重要发展方向,能 够提高转化率和产品选择性。
产品分离
通过蒸馏等方法将裂化产物分离成不同沸点的油品,如汽油、柴油、 液化气等。
加氢裂化与其他工艺的比较
与焦化工艺相比
焦化工艺主要通过热解重油生产焦炭和轻质油品,而加氢 裂化工艺通过加氢处理和催化裂化生产轻质油品,产品环 保性能更好。
与催化裂化工艺相比
催化裂化工艺主要通过酸性催化剂的作用将重质油品裂化 为汽油、柴油等,而加氢裂化工艺通过加氢处理降低了原 料中的硫、氮等杂质,产品品质更高。
- 1、下载文档前请自行甄别文档内容的完整性,平台不提供额外的编辑、内容补充、找答案等附加服务。
- 2、"仅部分预览"的文档,不可在线预览部分如存在完整性等问题,可反馈申请退款(可完整预览的文档不适用该条件!)。
- 3、如文档侵犯您的权益,请联系客服反馈,我们会尽快为您处理(人工客服工作时间:9:00-18:30)。
2020年1月24日
大庆石化公司炼油厂加氢裂化装置
装置特点
➢选用抚顺石油化工研究院开发的FC-16和大庆石化究院 开发的DZN单段双剂串联一次通过工艺。
➢反应部分采用炉前混氢流程。 ➢采用热高分流程,降低能耗,节省换热面积。 ➢分馏设置脱气塔,采用分馏进料加热炉和常压塔出柴油
方案。
➢原料油缓冲罐采用低压燃料气保护,防止其与空气接 触。
2314 152314
5024 4415 21135 23715 32160 65865 152314
t/d 3600 55.536 3655.537 120.5784 105.96 507.24 569.16 771.84 1580.76 3655.537
典型的化学反应有以下:
2020年1月24日
大庆石化公司炼油厂加氢裂化装置
二、生产方法及反应机理
加氢脱硫(HDS):
R
S + 6H2 R
加氢脱氮(HDN):
R
NH+ 6H2 R
CH3+ H2S CH3+ NH3
2020年1月24日
大庆石化公司炼油厂加氢裂化装置
二、生产方法及反应机理
烯烃加氢饱和:
H3 C
装置内高温高压法兰、分馏塔、塔底热油泵、高温 高压循环油泵、产品泵,压缩机管线等部位容易着火。
2020年1月24日
大庆石化公司炼油厂加氢裂化装置
二、生产方法及反应机理
加氢裂化指在加氢反应过程中,原料油的分子有 10% 以上变小的那些加氢技术。烷烃(烯烃)在加氢 裂化过程中主要进行裂化、异构化和少量环化的反应。 烷烃在高压下加氢反应而生成低分子烷烃,包括原料 分子某一处C—C键的断裂,以及生成不饱和分子碎片 的加氢。烯烃加氢裂化反应生成相应的烷烃,或进一 步发生环化、裂化、异构化等反应。
装置的基础设计部分由中国石化工程建设公司北京 设计院完成,详细设计部分由大庆石化设计院完成。 由反应、分馏、热工和公用工程等部分组成.
加氢裂化装置承担着大庆石化公司的成品油质量, 改善产品结构,并为乙烯提供优质裂解原料的重任。
2020年1月24日
大庆石化公司炼油厂加氢裂化装置
装置简介
加氢裂化装置原料为炼油厂常减压一套、二套装 置的常三、常四、减一、减二、减三线油以及一制蜡 装置的发汗蜡和蜡脱油装置的溶剂脱蜡油。2006年2月 装置原料优化后,原料为常减压一套、二套装置的常 三、常四、减一、减二油,以及焦化柴油、催化轻重 柴油。装置生产的主要产品为轻石脑油、重石脑油、 低凝柴油、轻柴油以及尾油。轻石脑油及尾油作为乙 烯裂解装置的优质原料,重石脑油为重整进料,低凝 柴油和轻柴油作为国Ⅳ柴油优质调和组分。
2020年1月24日
大庆石化公司炼油厂加氢裂化装置
装置特点和危险特性
加氢裂化装置生产特点和危险特性:具有炼油企 业之高温,高压,易燃易爆,高噪声且介质含H2S,工业 粉尘,汽油等.加氢裂化工艺属高温、高压、临氢工艺 过程。技术要求高,操作难度大,危险因素多。物料 介质中含有浓度较高的硫化氢等有毒有害物质,而硫 化氢在潮湿、低温的环境下,容易产生湿硫化氢腐蚀, 容器及管线设备容易被腐蚀穿孔,或者有管线爆裂、 法兰垫片撕裂等情况,都可能发生硫化氢泄漏事故。 因此,防爆防毒是车间安全工作的重点。
➢防止原料中固体杂质带入反应床层,采用原料自动反冲 洗过滤器。
➢催化剂采用干法硫化工艺。 ➢选用低氮油注氨的催化剂钝化方案。
2020年1月24日
大庆石化公司炼油厂加氢裂化装置
装置特点
➢催化剂采用器外再生方案。 ➢分馏塔设中段回流,回收热量,降低能耗。 ➢蒸汽凝结水、分流塔顶冷凝水、及污水汽提净化 水回用,节省除盐水。 ➢本装置运行条件苛刻,采用DCS进行实时控制。 ➢为确保装置安全运行,设置紧急停车系统ESD。
2020年1月24日
大庆石化公司炼油厂加氢裂化装置
装置简介
装置设计年开工时间为8000小时,设计能力为 120万吨/年,最大生产能力140万吨/年,设计低 转化率工况下的能耗为32.43千克油/吨。
2006年装置实际生产负荷142万吨,创装置加 工能力的最大历史水平。
2008年装置全年综合能耗累计24.71千克油/ 吨,创装置历史最好能耗水平。
CH3 + CH3
H2
H3C
CH3 CH3
2020年1月24日
大庆石化公司炼油厂加氢裂化装置
二、生产方法及反应机理
单环芳烃加氢饱和:
R
+ 3H2
R
多环芳烃加氢饱和:
R
+ 2H2 R
R
R
+ 2H2
R
+ 3H2
2020年1月24日
大庆石化公司炼油厂加氢裂化装置
二、生产方法及反应机理
芳烃加氢脱烷基:
R
2020年1月24日
大庆石化公司炼油厂加氢裂化装置
一、装置简介
加氢裂化装置于2002年10月开始筹建,2004 年6月1日工程正式中交,并于同年8月28日19时37 分实现装置一次投料成功,并生产出合格产品。由中 油第一建筑公司、大庆石化工程公司、大庆市建安集 团共同承建。装置总投资为59672.32万元,总占地 面积8479平方米。
大庆石化公司炼油厂加氢裂化装置
1、装置物料平衡
装置物料平衡表
物料
原料油 入 工业氢 方 合计
气体
W% 100 1.54 101.54 3.35
轻石脑油 出 重石脑油 方 航煤
柴油 尾油 合计
2.94 14.09 15.81 21.44 43.91 101.54
2020年1月24日
Kg/h 150000
+ H2
环烷烃加氢脱烷基:
R
+ H2
+ RH
+ RH
2020年1月24日
大庆石化公司炼油厂加氢裂化装置
二、生产方法及反应机理
烷烃异构化:
CH3 R
CH3
CH3 R
CH3 CH3
2020年1月24日
大庆石化公司炼油厂加氢裂化装置
三、工艺技术路线及流程
1、装置物料平衡 2、反应系统 3、分馏系统
2020年1月24日
加氢裂化装置培训课件
2020年1月24日
大庆石化公司炼油厂加氢裂化装置
前沿:装置简单流程介绍
2020年1月24日
大庆石化公司炼油厂加氢裂化装置
前沿:装置简单流程介绍
2020年1月24日
大庆石化公司炼油厂加氢裂化装置
一、加氢裂化装置介绍 二、生产方法及反应机理 三、工艺技术路线及流程 四、装置开停工过程中的关键操作 五、装置关键设备介绍 六、装置技术经济水平 七、装置生产中存在问题及解决措施 八、装置实际操作条件介绍 九、加氢裂化装置实际操作注意事项