TQRDC供应商评价标准 0314
供应商评估标准
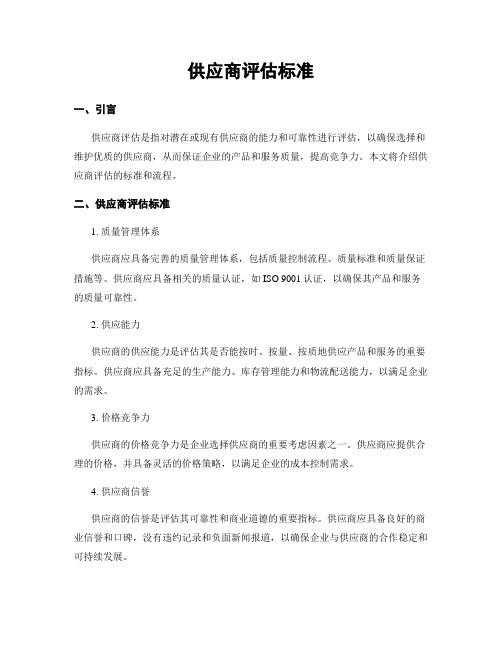
供应商评估标准一、引言供应商评估是指对潜在或现有供应商的能力和可靠性进行评估,以确保选择和维护优质的供应商,从而保证企业的产品和服务质量,提高竞争力。
本文将介绍供应商评估的标准和流程。
二、供应商评估标准1. 质量管理体系供应商应具备完善的质量管理体系,包括质量控制流程、质量标准和质量保证措施等。
供应商应具备相关的质量认证,如ISO 9001认证,以确保其产品和服务的质量可靠性。
2. 供应能力供应商的供应能力是评估其是否能按时、按量、按质地供应产品和服务的重要指标。
供应商应具备充足的生产能力、库存管理能力和物流配送能力,以满足企业的需求。
3. 价格竞争力供应商的价格竞争力是企业选择供应商的重要考虑因素之一。
供应商应提供合理的价格,并具备灵活的价格策略,以满足企业的成本控制需求。
4. 供应商信誉供应商的信誉是评估其可靠性和商业道德的重要指标。
供应商应具备良好的商业信誉和口碑,没有违约记录和负面新闻报道,以确保企业与供应商的合作稳定和可持续发展。
5. 技术能力供应商的技术能力是评估其创新能力和技术支持能力的重要指标。
供应商应具备先进的技术设备和专业的技术团队,能够提供技术支持和解决方案,以满足企业的需求和创新要求。
6. 供应商风险管理供应商的风险管理能力是评估其应对供应链风险的能力和措施的重要指标。
供应商应具备健全的风险管理体系,包括供应链可视化、供应链灵活性和备份供应商等,以应对突发事件和供应链中断的风险。
7. 可持续发展能力供应商的可持续发展能力是评估其环境责任和社会责任的重要指标。
供应商应具备环境管理体系和社会责任体系,包括环境保护措施、劳工权益保护和社区参与等,以确保企业与供应商的合作符合可持续发展的要求。
三、供应商评估流程1. 评估前准备确定评估的目标和范围,明确评估的重点和关注点,制定评估标准和评估指标,准备评估所需的文件和数据。
2. 信息收集收集供应商的相关信息,包括企业资质、财务状况、产品和服务介绍、质量管理体系认证等,通过面谈、问卷调查、现场考察等方式获取供应商的详细信息。
供应商考核系统TQRDC介绍
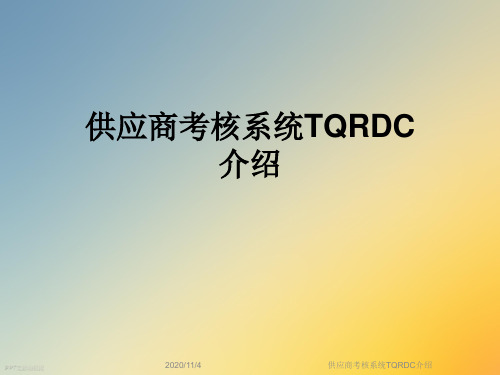
PPT文档演模板
2020/11/4
பைடு நூலகம்
供应商考核系统TQRDC介绍
Background
• TQRDC is Vendor Performance Measurement System based on below factors:
– T: TECHNOLOGY – Q:QUALITY – R:RESPONSIVENESS – D:DELIVERY – C:COST
Criteria/Results
Meet expectation on 3M request Not Meet expectation on 3M request
供应商考核系统TQRDC介绍
Q: Quality
• Material Accepting Rate (50%)
Points
100 90 80 60 50 40 30 20 0
PPT文档演模板
供应商考核系统TQRDC介绍
T: Technology 10%
• Prototype/Sample Capability (Critical vendor of nontrading vendor) (30%)
• Technical document professionalism (Critical vendor for non- trading vendor) (10%)
•3M China developed local TQRDC database Since 2002.
PPT文档演模板
供应商考核系统TQRDC介绍
Benefits of this improved system
• Can improve our vendor management efficiency; • 3Mers can take the initiative; • Including RM/CM/Trading/indirect vendors
供应商质量评价标准

供应商质量评价标准
一。
供应商的产品质量那可是重中之重。
1.1 产品得符合咱的标准和要求,不能有丝毫的马虎。
比如说,咱要的零件尺寸必须精准,材质得达标,不能有瑕疵。
1.2 产品的稳定性也得有保障。
不能这一批挺好,下一批就出岔子,质量忽高忽低可不行。
二。
服务质量也是关键。
2.1 供应商得按时交货,说啥时候到就得啥时候到,“言必信,行必果”,可不能拖延。
2.2 有问题得积极解决,不能推诿扯皮,得有个“敢作敢当”的态度。
2.3 能根据咱的需求提供个性化的服务,灵活应变,“随机应变”才能合作愉快。
三。
供应商的信誉那是必须考量的。
3.1 市场上得有好口碑,“金杯银杯不如口碑”,大家都说好那才是真的好。
3.2 过往的合作记录得漂亮,不能有啥不良的“案底”。
选供应商就像选合作伙伴,得方方面面都靠谱。
产品质量、服务质量、信誉,一个都不能少。
只有这样,咱们的生意才能顺风顺水,红红火火!。
tqrdcesg供应商评价标准

供应商评价标准一、引言1.1 供应商在企业采购管理中的重要性 1.2 供应商评价标准的必要性二、供应商评价标准的建立2.1 确定评价指标体系2.1.1 供应商质量管理能力2.1.2 供应商交货能力2.1.3 供应商成本管理能力2.1.4 供应商服务水平2.2 设定评价标准2.2.1 质量管理能力评价标准2.2.2 交货能力评价标准2.2.3 成本管理能力评价标准2.2.4 服务水平评价标准三、供应商评价过程3.1 评价标准的权重分配3.2 数据收集与分析3.3 评价结果汇总和报告四、供应商评价的改进与应用4.1 根据评价结果的实施改进4.1.1 供应商培训与沟通4.1.2 供应商绩效管理4.2 评价结果的应用4.2.1 供应商绩效奖惩机制4.2.2 供应商战略合作五、供应商评价标准的意义与影响5.1 保障产品质量与供货稳定5.2 降低采购成本5.3 促进供应链管理有效运作六、结论6.1 总结供应商评价标准的重要性6.2 展望未来供应商评价标准的发展趋势七、参考文献供应商评价标准一、引言在现代企业采购管理中,供应商的选择和评价是至关重要的环节。
合格的供应商不仅能够保障产品质量和交货稳定,还能够降低采购成本,促进供应链管理的有效运作。
而供应商评价标准的建立和执行则成为保障企业采购管理顺利进行的重要基础。
二、供应商评价标准的建立2.1 确定评价指标体系在建立供应商评价标准时,首先需要确定评价指标的体系。
一般来说,可以从供应商质量管理能力、供应商交货能力、供应商成本管理能力和供应商服务水平等方面进行考量。
2.1.1 供应商质量管理能力供应商的质量管理能力是衡量其产品质量稳定性的重要指标,可从其质量管理体系、质量控制手段和质量管理经验等方面进行评估。
2.1.2 供应商交货能力供应商的交货能力直接影响到生产计划的执行和客户订单的交付。
评价供应商的交货能力需要考虑其交货准时率、交货速度和交货稳定性等指标。
2.1.3 供应商成本管理能力供应商的成本管理能力直接关系到采购成本的控制和降低。
TQRDC供应商评价标准

25 不能提供国内领先水平的技术方案
产品质量管理政策,目标的树立流程及共有水平 每年都确定品质目标,为实现目标定有详细的流程和计划, 通过周期
100 性报告, 全体员工都比较了解品质政策和现状
建立质量 管理政策
75
每年都确定品质目标并且周期性向最高经营者提交报告,而且全体员 工对品质政策和现状的了解程度比较高
具有有关缩短交货时间的改善流程的规定,管理并监督为缩短交货时
100 间的改善活动的执行情况,具备了应对紧急交货的体系以及系统(系
交货改善 活动
统,流程,改善报告书)
75
具有为缩短交货时间的改善流程的规定和监督体系,但是缺乏具体改 善行动的执行, (系统,流程)
50
具有为缩短交货时间的改善流程的规定,但是没有监督体系,并且缺 乏具体改善行动的执行, (流程)
9
电子数据传输与 软件设计
与客户协同设计电子数据传输能力
10
T2
新品开发样品检 验合格
新品样品合格率
能否提供领先设计方案
100 能提供引领用户需求的设计方案作为海尔技术储备
11
T3
新品开发参与度
领先设计 方案
75 能提供代表未来技术发展趋势的行业领先设计方案并可落地
50 提供国内领先设计方案并可在短期内可落地
100 供应商对于高端技术的开发时间以及技术要求非常积极的响应。
30
R2
开发协作度
开发协作 度
75 对于高端技术开发的时间和技术要求,执行相应的措施
50
大部分情况下能够符合高端技术研发的时间和技术要求,但是偶尔会 发生不符合的情况
25
对于高新技术的开发要求很被动的响应,经常会发生不符合相应时间 或技术要求的情况
供应商考核系统TQRDC介绍
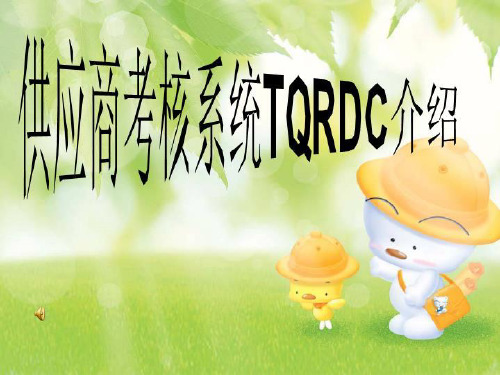
100
0
Product EHS & Regulation
Point
compliance
(30%)
100
0
Criteria/Results
No Record in System Any record in system
Criteria/Results
No Record in System Any record in system
<80%
Number of CAPA
0 >=1 Case
Quality Survey Results
> = 60 <60
R: Responsiveness 15%
Timeliness of Correction Active
Feedback
(20%)
Point
100 0
Criteria/Results
20
Payment Term
15%
15%
15%
15%
SMI Implemented
20%
20%
20%
20%
Competitive costs
15%
15%
15%
15%
Cost reductions
50%
50%
50%
50%
Login interface
• The web site address: http://cnoss01/bihome/QlikView/homepage.aspx User name is default as employee number;
Material Accepting Rate
50%
供应商评价标准

精心整理供应商评分标准一、工程类供应商评分标准(一)施工进度(20分)1、进度计划(10分):能够按照合同约定或甲方指令满足施工进度的,得10分;未按合同约定及甲方指令进行施工的,延误一次扣1分,扣完10分为止。
2、甲方指令(5分):能够根据甲方要求及时调整工期,不延误施工进度的,得5分;出现因施工单位未及时调整工期造成工期延误的,一次扣1分,扣完5分为止。
3、交叉施工(5分):交叉施工过程中,因推诿扯皮造成自身他方工期延误的,一次扣1分,扣完5分为止。
(二)施工质量(15分)1、质量合格(15分):按照合同约定未出现质量问题,达到施工质量要求并验收合格的,得15分;出现重大质量问题造成返工或者影响使用功能的,一次扣5分,扣完15分为止。
2、质量较合格(10分):按照合同约定未出现质量问题并验收合格,有部分瑕疵、不影响使用功能的,得10分。
3、质量不合格(0分):未按照合同约定的施工质量要求进行施工,验收不合格的,得0分。
(三)安全文明(10分)1、安全事故(4分):施工过程中未出现安全事故的,得4分;出现安全事故,未造成人员伤亡、财产损失的,一次扣1分;出现一次重大财产损失或人员伤亡的,此项不得分。
2、成品保护(2分):注重施工过程中的成品保护,得2分;对他人成品造成破坏的,一处扣1分,扣完2分为止。
3、乙供材料(2分):乙供材料符合甲方要求品牌,得2分;发现不符合甲方要求,一次扣1分,扣完2分为止。
4、甲供材管理(2分):甲供材的现场堆放与管理合理,得2分;未进行材料分类保护,一处扣1分,扣完2分为止。
(四)管理与配合(25分)1、百日会战配合到位(15分):a是否按时参加甲方例会(5分),缺勤一次扣0.5分;b服从甲方指令(10分)。
2、合理经济签证(10分):a提报时间、内容合理,无夸大成分得10分;b提报有夸大成分但无恶意成分,得5分;c签证恶意多报,得0分。
3、加分项:设计变更(+10分):施工过程中提出合理化施工建议,节约甲方成本或者提前工期的,此项合理加分,最高得10分。
供应商评价的一般性指标

供应商评价的一般性指标供应商是广义供应链中的重要环节之一;供应商管理是采购管理中的重要职能之一;供应商评价(供应商绩效考核)是供应商管理中的重要内容之一。
供应商评价指标,应根据企业不同发展阶段和不同行业特性,基于SMART原则量身定制出量化指标。
本文介绍一般性指标,可作为供应商评价体系的底层逻辑,供参考。
供应商评价的一般性指标,包括五项基础指标(TQRDC)和三项附加指标(ESG)。
1.五项基础指标(TQRDC)(1)T——Technology考察供应商技术研发能力、产品创新能力,表现为供应商新产品或新技术迭代频次、持有并未来可能获得专利数量、技术成果转化能力、可提供的技术指导次数等;(2) Q——Quality考察供应商品质管控能力,表现为QA/QC人员配备及水平、车间、仓库及实验室硬件情况、质量管理体系成熟度、供应商管理及索票索证情况、来料检测情况、过程管理情况、(半)成品不良品处理措施、成品质量合格率等;(3)R——Responsiveness考察供应商的响应速度及完成率,表现为响应的时间、是否达成目标等;(4)D——Delivery考察供应商的产品交付能力,包括交货及时率、交货满足率、交货准确率等;(5)C——Cost考察供应商的成本管控能力,体现供应商对上游供应链的整合能力、抗行情风险能力、精益化管理能力,表现为产品的综合性价比。
2. 三项附加指标(ESG)ESG是指环境(Environmental)、社会(Social)和公司治理(Governance),最早由联合国环境规划署在2004年提出,是衡量上市公司是否具备足够社会责任感的重要标准。
当企业发展到一定阶段,如计划上市或实施全球化战略时,对上游供应商在社会责任方面也相应提出更高的要求。
供应商考核系统TQRDC介绍
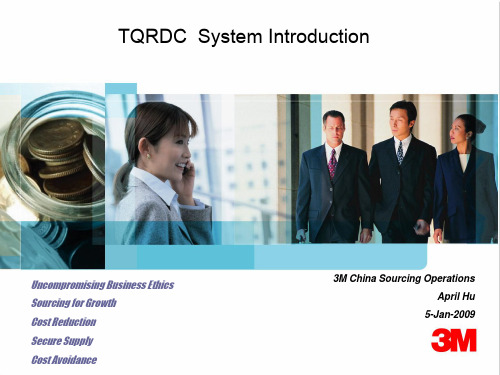
15%
15%
Product EHS & Regulation compliance
30%
30%
30%
30%
D
Non-Trading Vendor
25 Trading vendor
30
On Time Delivery
100%
100%
100%
100%
C
Non-Trading Vendor
20 Trading vendor
D: Delivery 25%
• Conformance to 3M need by date
(100%)
Point
100 90 80 70 60 50 40 30 20 10 0
Criteria/Results
100% Of promise dates are met >96% Of promise dates are met >92% Of promise dates are met >88% Of promise dates are met >84% Of promise dates are met >80% Of promise dates are met >75% Of promise dates are met >70% Of promise dates are met >65% Of promise dates are met >60% Of promise dates are met <60% Of promise dates are met
T: Technology 10%
• Prototype/Sample Capability
供应商业绩评分及分级考核标准

售后
让步接收一次扣0。2分,对同一零件连续三次让步使用发整改通知,如供方未能在整改期限内完成整改,扣1分。
退货一次扣0. 5分,对同一零件连续二次退货发整改通知,如供方未能在整改期限内完成整改,扣1分。
在产品的后工序加工过程中,发现产品不符合要求,经分析是供应商原因的,发生一次扣2分.
产品在客户处(包括直接用户、中间用户和最终用户)发现不合格,经分析是供应商原因的,发生一次扣5分。
A级
B级
C级
D级
1、增加订货量
2、减少检验频次
减少订货量
暂停订货,限期整改
淘汰
6。2。2每月《供方业绩汇总表》中被评为C级的供方,由质量部向供方发出《供方业绩整改单》要求供方限期整改.
6.2。3对于分数<60分的供方,列入淘汰供应商名单,由采购部填写《供应商准入/取消审批表》,按《供方管理程序》开发新的供方。
岳琦
A
王志坚
夏成林
原版
2015.1。15
1
对供方业绩进行评定,为确定供方等级提供依据,加强对供方的监控和管理。
2
适用于公司原材料、外协件、外购件、工装模具、工量具、包装等合格供方.
3
无
4
4。1质量部负责对原材料、外协件、外购件、工装模具、工量具、包装等合格供方进行业绩评定
及考核。
4。2采购部负责下月5日前提供上月采购物料的价格执行情况给质量部。
好
中
差
10
5
0
“好”:能在规定的时间内提供一切服务;
“中”:基本上能在规定的时间内提供一切服务;
“差":不能在规定时间内提供一切服务。
6
6
A级:分数≥90分;
供应商评估标准

供应商评估标准
标题:供应商评估标准
引言概述:
供应商评估是企业管理中非常重要的一环,它能够帮助企业选择合适的供应商,确保产品和服务的质量,降低采购成本,并提升整体供应链的效率。
因此,建立科学合理的供应商评估标准至关重要。
本文将从供应商评估的目的、内容、方法、标准和实施流程等方面进行详细介绍。
一、供应商评估的目的
1.1 确保产品和服务质量
1.2 降低采购成本
1.3 提升供应链效率
二、供应商评估的内容
2.1 供应商的资质和信誉
2.2 产品和服务的质量
2.3 供货能力和交货准时性
三、供应商评估的方法
3.1 问卷调查
3.2 现场考察
3.3 第三方评估机构评估
四、供应商评估的标准
4.1 质量管理体系认证
4.2 交货准时率
4.3 售后服务满意度
五、供应商评估的实施流程
5.1 制定评估计划
5.2 收集评估数据
5.3 分析评估结果并制定改进计划
结语:
建立科学合理的供应商评估标准对企业的发展至关重要,只有通过不断完善评估标准和流程,才能选择到最合适的供应商,确保产品和服务的质量,提升企业的竞争力。
希望本文对您有所帮助,谢谢阅读。
tqrdces供应商评估7要素

tqrdces供应商评估7要素在选择供应商的时候,所涉及到的因素是很复杂的。
加上在不同的国家、行业或企业也有不同的标准,就让供应商选择变得更加困难了。
所以呢,在这样的情况下,很多企业都开始把供应商选择的要素进行细分。
其实在供应商选择的时候,大部分企业都非常重视三个要素,分别是成本、质量和交期。
企业选择供应商的时候,一般会主要考虑7个因素。
(一)供应商的管理能力其中第一个因素就是供应商的管理能力,而且这个因素也是非常关键的。
为什么这么说呢?我们都知道在每个企业里面,管理层都在运营着整个企业,而且他们做的决策会影响到供应商的竞争力。
所以说,在选择供应商的时候,应该对它们的管理能力引起重视。
而在具体评估他们管理能力的时候,一般可以提问下面的问题。
比如说管理层有没有长期的发展计划?管理层是不是重视公司的全面质量管理和持续改善?再比如说还可以问管理层是不是把客户作为了中心?等等。
虽然说通过提问这些问题,并不能全面地了解一个供应商,可是最起码这些问题可以帮助企业了解它们的一些基本情况,这样对于后面选择供应商还是非常有用的。
(二)考察的技术能力除了管理能力,选择供应商还应该考察它们的技术能力。
而在看技术能力的时候,一般会首先看它技术开发人员使用的硬件和软件,然后还要看看它开发人员的基本情况,比如说数量、经验、学历等等。
当然了,不同行业对技术人员的要求也是不一样的,这个到时候可以根据企业的实际情况去考察。
但在评估能力的时候,我们应该特别注意产品认证能力。
不过这种能力却并不是所有的企业都具备的。
而且对技术能力的评估是一个非常复杂的活动,所以大部分时候都是需要研发工程师一起参与到里面的。
(三)财务能力在选择供应商的时候,还应该重视它们的财务能力。
那我们为什么要评估他们的财务状况呢?其实主要是因为它的财务状况就是它的经济实力。
而一个公司财务状况是不是好,资金情况是不是正常,都会关系到它未来的发展,也会影响到它供货的稳定性。
供应商质量风险等级评估标准

供应商质量风险等级评估标准供应商质量风险等级评估标准1、目的:识别供应商质量风险,并进行分级,然后根据供应商质量风险等级大小,管理供应商,重点是强化对高风险度的供应商管理。
2、定义:供应商质量风险等级分为A/B/C/D四等。
A-风险很小、B-风险小、C-风险中、D-风险大3、适用范围:适用于华为公司所有合格供应商。
4、操作方法:(1)每年评定1次,每年1月份,由TQC按此标准进行初步评定,然后分别与各个专家团进行评审确定,评审后将结果(包括不能达成共识的名单)一并提交TQC-LEADER,(2)TQC-LEADER 组织各CEG-leader进行评审确定。
(3)评定后由TQC-LEADER提交策略中心LEADER审核发布,策略中心LEADER可以根据采购策略和相关政策等综合因素给予适当调整,然后发布并上报采委会(4)一旦发布生效,则执行本管理制度。
(5)风险等级一旦评定,当年不得升级,当违反“批次质量表现无条件高压线”的G1款,则当年自动降为D级。
(6)每年风险等级评定时应考虑其上一年的评定结果,升级只能一年升一级,不得越级提升,可越级降级。
(7)上一年的D类供应商转为“C”类必须按照新供应商认证的质量体系标准,由TQC启动全面认证和评估,经过严格认证合格后才具备转级的必要条件。
5、评价标准首先按“质量保证体系”和“年度质量表现”两个维度分别评价,然后根据这两个维度评价结果进行综合评价,给出每个供应商风险等级A/B/C/D。
上一年的D类供应商转为“C”类必须按照新供应商认证的质量体系标准进行全面认证和评估,认证合格后方可转级。
◆非合格供应商质量风险等级自然为D◆当年引入的新供应商的质量风险等级最高为C5.1、质量保证体系评价标准5.1.1 质量体系分项评价序号项目内容 A B C D1.1 质量体系认证通过ISO9000等认证,流程文件执行规范。
多次稽查没有发现明显缺陷。
通过ISO9000等认证,大部分流程文件执行规范。
供应商绩效评估TQRD标准-基本要求
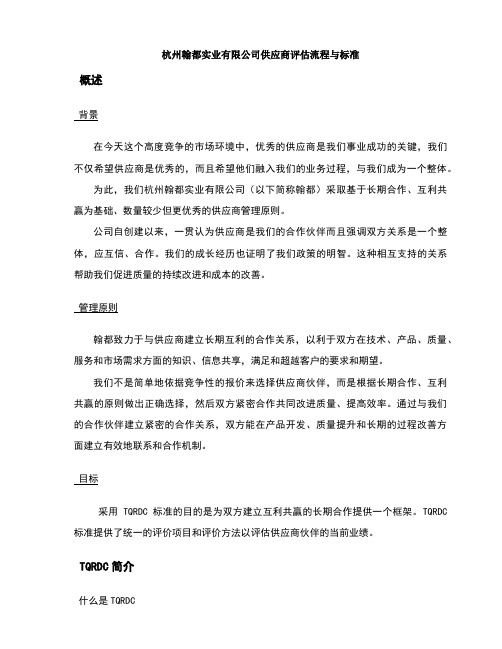
杭州翰都实业有限公司供应商评估流程与标准概述背景在今天这个高度竞争的市场环境中,优秀的供应商是我们事业成功的关键,我们不仅希望供应商是优秀的,而且希望他们融入我们的业务过程,与我们成为一个整体。
为此,我们杭州翰都实业有限公司(以下简称翰都)采取基于长期合作、互利共赢为基础、数量较少但更优秀的供应商管理原则。
公司自创建以来,一贯认为供应商是我们的合作伙伴而且强调双方关系是一个整体,应互信、合作。
我们的成长经历也证明了我们政策的明智。
这种相互支持的关系帮助我们促进质量的持续改进和成本的改善。
管理原则翰都致力于与供应商建立长期互利的合作关系,以利于双方在技术、产品、质量、服务和市场需求方面的知识、信息共享,满足和超越客户的要求和期望。
我们不是简单地依据竞争性的报价来选择供应商伙伴,而是根据长期合作、互利共赢的原则做出正确选择,然后双方紧密合作共同改进质量、提高效率。
通过与我们的合作伙伴建立紧密的合作关系,双方能在产品开发、质量提升和长期的过程改善方面建立有效地联系和合作机制。
目标采用TQRDC标准的目的是为双方建立互利共赢的长期合作提供一个框架。
TQRDC 标准提供了统一的评价项目和评价方法以评估供应商伙伴的当前业绩。
TQRDC简介什么是TQRDCTQRDC 包括一系列的绩效期望和评价标准以评估潜在新供应商和管理既有供应商目前的长期业务合作关系。
TQRDC 代表:技术(Technology),质量(Quality),响应速度(Responsiveness),交付(Delivery),成本(Cost)。
翰都对供应商伙伴的期望:- 使客户满意最大化;- 使整个系统的所有贡献者的利益最大化;- 对变化/更改做出最快的响应速度;和- 提供有效的沟通机制。
为达此目的,翰都对供应商伙伴的承诺:- 建立和维持长期的承诺;- 促进有效沟通;- 在期望和目标方面达成互利协议;- 把供应商的流程看作是自己流程的延伸;- 相互合作达到促进双方的绩效改进。
供应商等级评定评分标准

供应商等级评定评分标准建议对质量的评价将不良率等换算成质量损失成本,依据损失的质量成本来评分比较合理,如某一零件1%的不良率造成的质量损失成本为1万元,评分基准为每万元质量损失扣一分,这样就只扣1分,若1%的不良率造成的质量损失为2万元,而评分基准不变,则要扣2分。
当然计算质量损失成本要以整个产品因该零件的失效而导致的质量损失成本计,而不应该只是零件本身的成本损失而已。
供应商等级评定评分标准供应商等级评定评分标准1,批次合格率的评分标准(25分):批次合格率100%,每下降2%扣1分,扣完为止,每特采1批扣2分。
批次合格率计算方式:当月IQC检验合格批数÷交货总批数×100%执行MRB流程,取消代用称谓。
2,制程PPM值评分标准(25分):制程PPM值超过限度,每增加100PPM扣1分,扣完为止,客户对来料抱怨每次扣2分。
PPM值计算方式:当月生产线发生的不良数÷交货总数×10000003,交货及时率的评分标准(30分):交货准时配合度良好30分,每延期一天扣3分,当月延期交货累积超过5天以上,无论最终评分多少,不能评为C级以上。
交货及时率的确定方法:依据供应商交货及时率汇总表,采购部填写订单栏,仓库填写供应商实际交货日期、数量,确定交货及时率。
4,服务态度(5分):重工、批退配合度不好、处理不彻底每次扣2分。
5,品质改善及时性和效果(10分):同一不良现象改善不及时或效果不佳每次扣2分。
6,文件回覆及时性与合理性(5分):文件未按指定时间回覆每次扣1分,回覆不具体、不确实每次扣2分。
等级评定:绿色 A级 90-100分请保持兰色 B级 80- 89分正常抽样,请努力黄色 C级 70- 79分加严抽样,请改善红色D级70分以下列入考察,有关损失将扣款;连续三个月被评为D级,取消供应商资格注:评为B级以下的供应商,须对不良项目回覆改善对策;客户指定的供应商,如不符合要求,将向客户提出取消该供应商资格;每月评定的等级将分发给各供应商,并于收货区域专栏公布。
- 1、下载文档前请自行甄别文档内容的完整性,平台不提供额外的编辑、内容补充、找答案等附加服务。
- 2、"仅部分预览"的文档,不可在线预览部分如存在完整性等问题,可反馈申请退款(可完整预览的文档不适用该条件!)。
- 3、如文档侵犯您的权益,请联系客服反馈,我们会尽快为您处理(人工客服工作时间:9:00-18:30)。
25 不能提供国内领先水平的技术方案
产品质量管理政策,目标的树立流程及共有水平 每年都确定品质目标,为实现目标定有详细的流程和计划, 通过周期
100 性报告, 全体员工都比较了解品质政策和现状
建立质量 管理政策
75
每年都确定品质目标并且周期性向最高经营者提交报告,而且全体员 工对品质政策和现状的了解程度比较高
29
R1
采购协作度 采购协作 度
75
对于交货/价格要求等的采购要求事项响应水平高(根据情况需要督 促以及监督)
50 对于交货/价格要求等的采购要求事项响应水平一般(需要定期的监
响应 速度
R
25 对于交货/价格要求等的采购要求事项响应水平低(需要事先联系,
评定高端技术支援要求事项,以及为了遵守开发时限要求,供应商支援的迅速 性以及合作水平
{(采购预算价格– 实际采购价格) /采购预算价
23
C4
绝对成本降低金 额
(前期采购价格–
现期价格)
x
实际采购数量
缩短供应商交货时间,并满足交货期相关管理流程水平的需求
一般交货 管理体系
100
建有体系化的定时定量准确交货以及库存管理的流程程序,以遵守交 货要求成为监督管理标准,进行交货改善活动(系统,流程,改善报
25 缺乏为缩短交货时间的改善活动 有否与生产相关信息相结合的生产计划的制定/实行/更新
生产计划 制定
100
与生产相关信息有机的结合并且积极的使用,而且根据 日/周/月/年 的生产计划进行生产, 并定期的更新(具有系统)
75
制定生产计划时特别收集生产关联信息和数据,并且周期性的更新生 产计划,并根据计划按时完成计划(周/日 生产计划)
75
限于主要的生产现场进行管理/检查,及在发生问题之前就预防而且 为改善而建立了一系列体系 (具有每日生产报告管理, 预防性维护活
50
供应商不额外进行事先的预防性监控.只有当生产发生问题以后,他们 才进行改进活动 (具有例外情况回应报告)
25 没有为了提高生产成绩的分析以及对改善而进行的特别活动 现有产能必须满足海尔需求最高峰值的1.2倍
环境管理
75 年内环境管理计划(计划书)
2
M2 环境安全评价
50 具有环境管理证书(ISO,ROHS) 25 没有环境管理项目
作业环境安全及安全意识的管理
100 无事故日数在1年以上
管理 BE
安全管理
75 定期的安全教育及作业安全设施的实施(教育日程,安全设施报告 50 出事故时 安全教育及作业安全设施 25 没有安全管理活动
具有有关缩短交货时间的改善流程的规定,管理并监督为缩短交货时
100 间的改善活动的执行情况,具备了应对紧急交货的体系以及系统(系
交货改善 活动
统,流程,改善报告书)
75
具有为缩短交货时间的改善流程的规定和监督体系,但是缺乏具体改 善行动的执行, (系统,流程)
50
具有为缩短交货时间的改善流程的规定,但是没有监督体系,并且缺 乏具体改善行动的执行, (流程)
16
Q3 在线合格率 一定时期内的不良水平(PPM)以及批量不合格率
17
Q4 入厂检验合格率 (合格批次数/检查批次数)*100
18
封库事件 封库事件 发生次数
19
重大质量事故 重大质量事故 发生次数
成本计算和分析水平
成本管理 模型
100
供应商对直接和间接材料管理标准成本,并根据产品及公司总体整合 利润管理 (具有标准成本管理表格)
50 生产关联信息数据比较零散,不定期制定生产目标, 并不能及时的更
25 没有生产计划 生产工程的管理及改善体系水平
交付
D
生产工程
25
T4 生产效率管理
管理
生产设备情况的及时检查, 掌握问题工程并及时改善。设定管理点并
100 经常检查。(工程管理体系,工程及设备管理日志,标准作业步骤
书,预防报告书,检查矫正)
9
电子数据传输与 软件设计
与客户协同设计电子数据传输能力
10
T2
新品开发样品检 验合格
新品样品合格率
能否提供领先设计方案
100 能提供引领用户需求的设计方案作为海尔技术储备
11
T3
新品开发参与度
领先设计 方案
75 能提供代表未来技术发展趋势的行业领先设计方案并可落地
50 提供国内领先设计方案并可在短期内可落地
100 供应商对于高端技术的开发时间以及技术要求非常积极的响应。
30
R2
开发协作度
开发协作 度
75 对于高端技术开发的时间和技术要求,执行相应的措施
50
大部分情况下能够符合高端技术研发的时间和技术要求,但是偶尔会 发生不符合的情况
25
对于高新技术的开发要求很被动的响应,经常会发生不符合相应时间 或技术要求的情况
UG/PROE等三维数模软件应用能力
三维数模 100 软件应用能保障产品设计品质代表行业最高水平
研发用设备设施 软件应用
能力
能力
75 软件应用能保障产品设计品质代表行业水平
三维数模
8
研发用设备设施 软件应用
能力
能力
50 软件应用能有效保障产品设计品质
25 不能应用数模软件
满足客户各种需要的性能试验能力(包括寿命、耐久性、可靠性等)
机制
75 有NPI团队及NPI质量控制计划,按承诺保障NPI质量及进度
50 无NPI团队或NPI质量控制计划,影响到NPI质量及进度
25 无NPI团队或NPI质量控制计划,导致NPI延误
工程变更的控制能力
100
有完善的工程变更控制体系,且过去1年内未发生过工程变更导致的 品质或交付问题(供应商责任)
31
R3
质量协作度
质量协作 度
纠偏反馈得分/相应权重*100
删除 项 删除 项
T4 研发投资比重 研发投资比率 : (开发费用/年 销售额)*100 (根据损益表)
T5
(研发人员数量/ 总员工数)*100
(研发人员数量/总员工数)*100
75
制定成本降低目标,以及为了达成这一目标的计划,但是没有对于计 划执行的评价(成本降低计划)
50 制定成本降低目标,但是没有制定方案(成本降低目标)
25 没有制定成本降低目标,
21
C2 价格降低率 {(前期采购价格– 现期价格) /前期采购价格} x 100%
22
C3
新品价格合理性
对海尔目标价的支持程度和竞争力水平 格} x 100%
25 不能提供行业领先的模块化设计方案
技术 T
8
模块设计每年四新采用能力 (新材料、新技术、新设备、新工艺)
模块设计 100 提供的四新方案已获得专利,且能马上落地
每年四新 75 提供的四新方案已经过充分验证或通过权威的第三方认证,且能马上
采用能力 50 提供的四新方案具有可行性,需进一步验证
25 不能提供四新方案
50
虽然每年都有品质目标,但没有实现目标的详细计划,员工对品质政 策和目标了解不多
25 没有品质管理政策和目标
品质管理组织及专业水平
12
Q1 内部品质管理 质量管理 组织
100
品质的评价及管理的是由专门质管人员组织组成并且定期举行各种关 于品质改善和品质问题解决的会议
75
有关于品质评价及管理的专门组织,根据必要举办各种关于品质改善 及品质问题解决的会议
产能
100 产能在需求最高峰值1.2倍以上,且能在双方约定的时间内达成产能扩 75 产能在需求最高峰值1.2倍以上
50 产能在需求最高峰值1倍以上
26
产能与全球布局
25 产能仅能满足当前需求
满足客户多产品全球布局能力
全球布局 能力
100 满足国内四个以上区域及部分海外需求,或4个以上产品线需求 75 满足国内四个以上区域需求,或3个以上产品线需求 50 满足国内二个以上区域需求,或2个以上产品线需求
质量 Q
50
建有对 现状检查/评价等品质信息/数据 进行记录/管理的专门组 织,但对实际品质文件/记录等执行情况的管理不足
25 没有对 现状检查/评价等品质信息/数据 进行记录/管理的专门组织
NPI导入计划与管控机制
13
NPI导入计 NPI导入能力 划与管控
100
有专门的NPI团队及完整的NPI质量控制计划,确保NPI质量及进度完 全满足需求
50 虽然有品质评价没有品质专门组织
品质管理文件/记录管理的水平
质量文件/ 记录管理
100 75
建有对 品质现状检查/评价 等品质信息/数据 进行记录/管理的专门 组织,管理记录,并与相关人员沟通。 建有对 现状检查/评价等品质信息/数据 进行记录/管理的专门组 织,但因为相关信息/数据由相关人员各自管理, 信息共享不足
上 (完全技术创新的模块此项可不作为否决项)
无故意停产事故 (最近一年内)
5
商务合规 无廉政事件 (问题处理完毕并已结案完毕的例外)
中长期 研发规划的建立及对其相应的支持;设计创新被行业公认为引领
研发体系
100
具有企业附属研究所取得的研究成绩(新专利,知识产权,产品 化),以及具有从相关机关的获奖经历。
25 满足某一区域需求,或1个产品线需求
27
D2 交货准确性 1-(月T-1不到位批次的相应采购金额/供应商在搜购组中月采购总额)*100%
28
为海尔提供端到 端服务与团队
有为海尔提供专属服务的团队,人员包括设计、质量、供货、商务
评定供应行对于市场情报, 采购量调整等要求事项的合作程度