电火花EDM加工原理介绍
数控电火花线切割加工
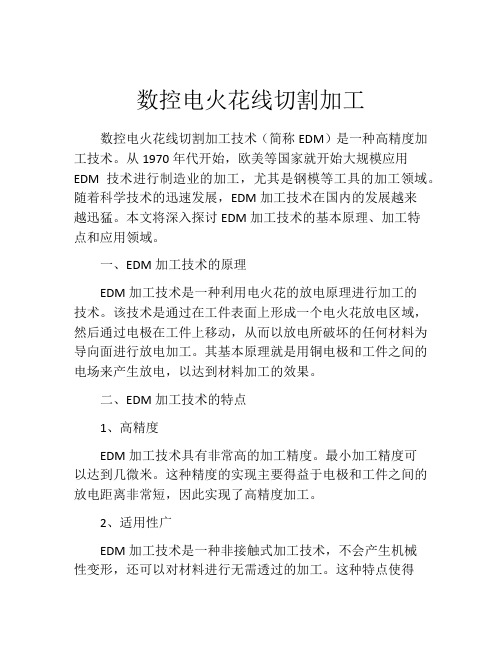
数控电火花线切割加工数控电火花线切割加工技术(简称EDM)是一种高精度加工技术。
从1970年代开始,欧美等国家就开始大规模应用EDM技术进行制造业的加工,尤其是钢模等工具的加工领域。
随着科学技术的迅速发展,EDM加工技术在国内的发展越来越迅猛。
本文将深入探讨EDM加工技术的基本原理、加工特点和应用领域。
一、EDM加工技术的原理EDM加工技术是一种利用电火花的放电原理进行加工的技术。
该技术是通过在工件表面上形成一个电火花放电区域,然后通过电极在工件上移动,从而以放电所破坏的任何材料为导向面进行放电加工。
其基本原理就是用铜电极和工件之间的电场来产生放电,以达到材料加工的效果。
二、EDM加工技术的特点1、高精度EDM加工技术具有非常高的加工精度。
最小加工精度可以达到几微米。
这种精度的实现主要得益于电极和工件之间的放电距离非常短,因此实现了高精度加工。
2、适用性广EDM加工技术是一种非接触式加工技术,不会产生机械性变形,还可以对材料进行无需透过的加工。
这种特点使得EDM加工技术被广泛应用于制造业的各个领域,如钢模、微孔加工、局部加热、特种材料加工等领域。
3、加工效率高EDM加工技术擅长处理小型工件,能够以高速度进行加工,并且适合加工硬度较高的材料。
其加工速度比传统加工方式快数倍。
同时,EDM加工技术还可以实现多种复杂形状的加工。
三、EDM加工技术的应用1、模具加工在模具的制造过程中,EDM加工技术几乎不可或缺。
在制造钢模等高精度模具时,人们越来越依赖EDM加工技术来提高高精度模具的生产效率和质量。
例如EDM加工技术可以用来制造汽车制动器,轮胎、零部件等。
2、微孔加工EDM加工技术在微细加工领域也具有潜力,可以用来加工出各类细小的孔洞和小圆形孔,例如墨盒的喷嘴孔、医疗器械的药孔等。
3、局部加热EDM在融合、碳化、钎焊和热处理等领域中,可充当局部加热剂,并被广泛地应用。
四、EDM加工技术发展趋势随着科学技术的不断发展,EDM加工技术还有很多的发展方向和潜力。
EDM加工原理介绍

电火花铣削 用来制作电气接插件的细小模具,进 行表面粗糙度要求均匀的大面积加工 以及任何不规则形状的加工。加工时 采用圆柱形电极,把材料一层层地去 除。 这种加工方法能采用便宜的电极来制 作复杂的模具形状。
在电极和工件上的蚀除量是不相等的, 这主要取决于极性,材料的热传导性、 熔点、放电的持续时间和强度。 在电极上产生的蚀除称为损耗,而在工 件上产生的蚀除称为材料去除量。
2020/3/3
GF AgieCharmilles
4
电火花加工的类型
电火花成形加工 用来制作注射模、特殊开头的模具以及 各种复杂形状的型腔。制作型腔时,要 采用与工件所需形状相反的电极。
2020/3/3
GF AgieCharmilles
2
电火花加工的物理原理
在这一电场作用下,电子和自由的正离 子被加速达到很高的速度,并将很快形 成一个导电的电离信道。
在这一阶段,两电极之间能通过电流和 产生火花,引起了粒子间无数次的碰撞。
这时形成了等离子区,它很快就达到了 8000到12000℃的极高温,在碰撞数持 续增长作用下形成的高温可在两导体表 面瞬时局部熔化一定量的材料。
2020/3/3
GF AgieCharmilles
1
电火花加工的物理原理
放电过程:
为了在两个电极之间产生放电,其上所 施加的电压必须高于GAP(电极和工件 之间的间隙)的击穿电压,这一击穿电 压取决于: - 电极和工件之间的距离。 - Байду номын сангаас作液的绝缘性能。 -在间隙中的污染程度(蚀除微粒)
edm加工原理

edm加工原理你知道 EDM 加工不?这玩意儿可神奇啦!EDM 呢,全称是电火花加工。
简单来说,就像是一场小小的“电花秀”。
想象一下,在一个工作台上,有一个要被加工的零件,还有一个电极。
它们俩就像是舞台上的主角。
这电极啊,可不是普通的东西,它可是带着电的“小能手”。
当电流通过的时候,会在电极和零件之间产生电火花。
这些电火花可厉害了,它们能把零件上不需要的部分一点点地给“烧掉”。
为啥能“烧掉”呢?这就得说说电火花的高温啦!那温度高得吓人,能瞬间把金属材料给熔化、气化。
就好像是一把超级厉害的“小火焰喷枪”,把多余的部分给清除掉。
而且哦,EDM 加工可精细了。
它能做出那些特别复杂、特别细小的形状。
比如说,一些很小很小的凹槽、很精细的花纹,它都能搞定。
这就像是一个超级细心的“小工匠”,一点点地雕琢出完美的作品。
你可能会想,那这电火花不会乱蹦跶,把不该加工的地方也给弄乱了吧?别担心!在 EDM 加工里,有一套很厉害的控制系统。
这个系统就像是一个聪明的“指挥官”,能精准地控制电火花产生的位置、时间和强度。
让电火花只在该工作的地方发挥作用,不乱来。
还有哦,EDM 加工对于那些硬度特别高的材料,也完全不在话下。
就算是那种硬得让人头疼的材料,电火花也能轻松应对。
这就好比是一个“大力士”,不管面对多硬的“骨头”,都能咬得动。
在整个加工过程中,工作液也起着很重要的作用。
它就像是给这场“电花秀”降降温、冲冲凉的“小助手”。
既能带走加工过程中产生的热量,又能把那些被熔化、气化的金属碎屑给冲走,保证加工的顺利进行。
怎么样,是不是觉得 EDM 加工很神奇?它就像是一个充满魔法的小世界,通过电火花的力量,把一个个零件变成我们想要的样子。
下次再看到那些精细又复杂的零件,你就知道,这背后可有 EDM 加工的一份大功劳呢!。
电火花加工的原理和应用范围

电火花加工的原理和应用范围原理电火花加工(Electrical Discharge Machining,简称EDM)是一种采用电脉冲的非接触式加工方法,通过在工件表面产生强烈的电火花放电来加工材料。
其原理如下:1.每个电火花发生时,电脉冲会在工件和电极之间产生高能量的放电,使工件表面的金属材料被熔化或蒸发。
2.这种放电过程产生的高能量热量能够使金属材料发生化学反应,并且被熔化的金属颗粒会被冲击力推开,从而实现对材料的加工和切削。
3.在放电过程中,电极和工件之间会切削摩擦,并在电极上形成坑槽。
通过控制放电时间、电流和电压等参数,可以实现对工件表面形状和尺寸的精确控制。
应用范围电火花加工技术具有以下特点,使其被广泛应用于各个工业领域:1.加工硬度高、脆性材料:电火花加工可以处理高硬度和脆性材料,例如硬质合金、陶瓷、石英等。
这些材料在传统机械加工中难以加工,而电火花加工可以通过放电破坏材料的结构来实现加工目的。
2.制造复杂形状和细小尺寸零件:电火花加工可以实现对工件表面的精确控制,因此适用于制造复杂形状和细小尺寸的零件。
例如模具、模塑部件和微细加工等领域。
3.加工高温材料:由于电火花加工过程中金属不直接接触,可以避免热影响区的产生。
因此,可以用于加工高温材料,例如高温合金和陶瓷复合材料。
4.效率高、成本低:相对于传统的机械加工方法,电火花加工可以提高加工效率和降低成本。
它不需要特殊刀具、适用于各种材料,并且可以同时加工多个工件,从而提高生产效率。
5.适用于特殊形状的孔洞加工:电火花加工可以实现对工件内部和特殊形状孔洞的加工,例如冲模、喷嘴和轴承等内部结构。
综上所述,电火花加工技术具有广泛的应用范围,并在诸多领域取得了成功应用。
在今后的发展中,随着科学技术的不断进步,电火花加工技术将进一步完善,为工业制造带来更多的便利和创新。
电火花加工原理
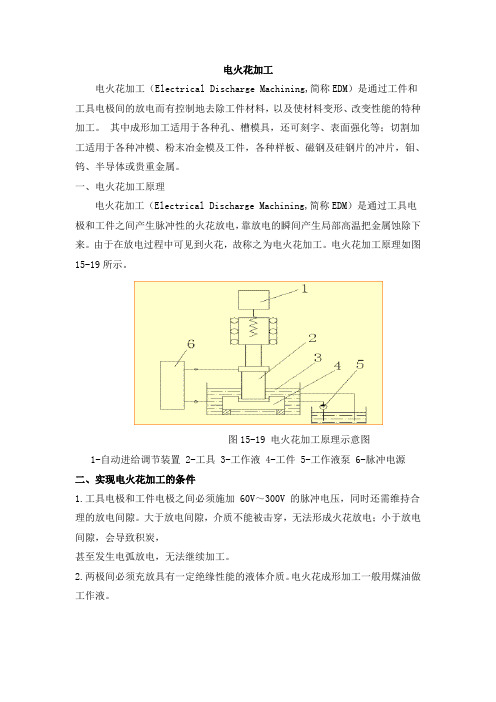
电火花加工电火花加工(Electrical Discharge Machining,简称EDM)是通过工件和工具电极间的放电而有控制地去除工件材料,以及使材料变形、改变性能的特种加工。
其中成形加工适用于各种孔、槽模具,还可刻字、表面强化等;切割加工适用于各种冲模、粉末冶金模及工件,各种样板、磁钢及硅钢片的冲片,钼、钨、半导体或贵重金属。
一、电火花加工原理电火花加工(Electrical Discharge Machining,简称EDM)是通过工具电极和工件之间产生脉冲性的火花放电,靠放电的瞬间产生局部高温把金属蚀除下来。
由于在放电过程中可见到火花,故称之为电火花加工。
电火花加工原理如图15-19所示。
图15-19 电火花加工原理示意图1-自动进给调节装置 2-工具 3-工作液 4-工件 5-工作液泵 6-脉冲电源二、实现电火花加工的条件1.工具电极和工件电极之间必须施加 60V~300V 的脉冲电压,同时还需维持合理的放电间隙。
大于放电间隙,介质不能被击穿,无法形成火花放电;小于放电间隙,会导致积炭,甚至发生电弧放电,无法继续加工。
2.两极间必须充放具有一定绝缘性能的液体介质。
电火花成形加工一般用煤油做工作液。
3.输送到两极间的脉冲能量应足够大,放电通道间的电流密度,一般为104~109A/cm2。
4.放电必须是短时间的脉冲放电。
一般放电时间为 1μs~1ms。
这样才能使放电产生的热量来不及扩散,从而把能量作用局限在很小的范围内。
5.脉冲放电需要多次进行,并且在时间上和空间上是分散的,以避免发生局部烧伤。
6.脉冲放电后的电蚀产物应能及时排放至放电间隙之外,使重复性放电能顺利进行。
三、电火花加工的特点1.适合于难切削材料的加工,能“以柔克刚” 。
2.工具电极与工件不接触,两者间作用力很小。
3.脉冲参数可调节,能在同一机床连续进行粗、半精、精加工,加工过程易于自动控制。
4.主要用于加工金属等导电材料,在一定条件下也可以加工半导体和非金属材料。
电火花加工的基本原理及四个阶段
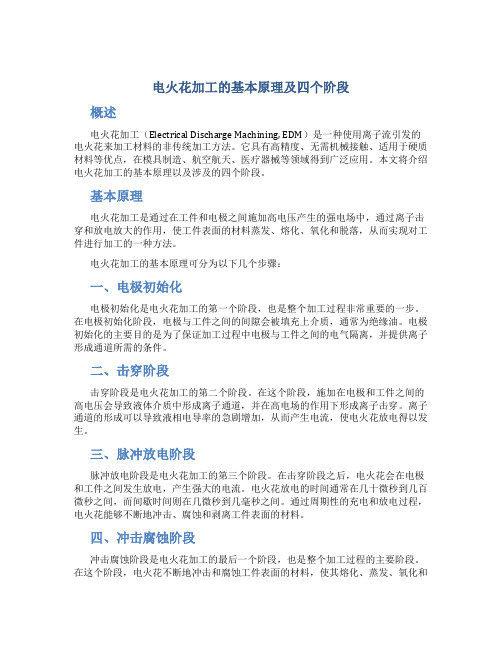
电火花加工的基本原理及四个阶段概述电火花加工(Electrical Discharge Machining, EDM)是一种使用离子流引发的电火花来加工材料的非传统加工方法。
它具有高精度、无需机械接触、适用于硬质材料等优点,在模具制造、航空航天、医疗器械等领域得到广泛应用。
本文将介绍电火花加工的基本原理以及涉及的四个阶段。
基本原理电火花加工是通过在工件和电极之间施加高电压产生的强电场中,通过离子击穿和放电放大的作用,使工件表面的材料蒸发、熔化、氧化和脱落,从而实现对工件进行加工的一种方法。
电火花加工的基本原理可分为以下几个步骤:一、电极初始化电极初始化是电火花加工的第一个阶段,也是整个加工过程非常重要的一步。
在电极初始化阶段,电极与工件之间的间隙会被填充上介质,通常为绝缘油。
电极初始化的主要目的是为了保证加工过程中电极与工件之间的电气隔离,并提供离子形成通道所需的条件。
二、击穿阶段击穿阶段是电火花加工的第二个阶段。
在这个阶段,施加在电极和工件之间的高电压会导致液体介质中形成离子通道,并在高电场的作用下形成离子击穿。
离子通道的形成可以导致液相电导率的急剧增加,从而产生电流,使电火花放电得以发生。
三、脉冲放电阶段脉冲放电阶段是电火花加工的第三个阶段。
在击穿阶段之后,电火花会在电极和工件之间发生放电,产生强大的电流。
电火花放电的时间通常在几十微秒到几百微秒之间,而间歇时间则在几微秒到几毫秒之间。
通过周期性的充电和放电过程,电火花能够不断地冲击、腐蚀和剥离工件表面的材料。
四、冲击腐蚀阶段冲击腐蚀阶段是电火花加工的最后一个阶段,也是整个加工过程的主要阶段。
在这个阶段,电火花不断地冲击和腐蚀工件表面的材料,使其熔化、蒸发、氧化和脱落。
通过不断重复脉冲放电和冲击腐蚀过程,工件的形状和尺寸最终得以加工完成。
总结电火花加工以其高精度、无需机械接触、适用于硬质材料等优点在工业领域得到广泛应用。
在电火花加工的过程中,电极初始化、击穿阶段、脉冲放电阶段和冲击腐蚀阶段是不可或缺的四个阶段。
电火花加工的基本原理特点及应用场合
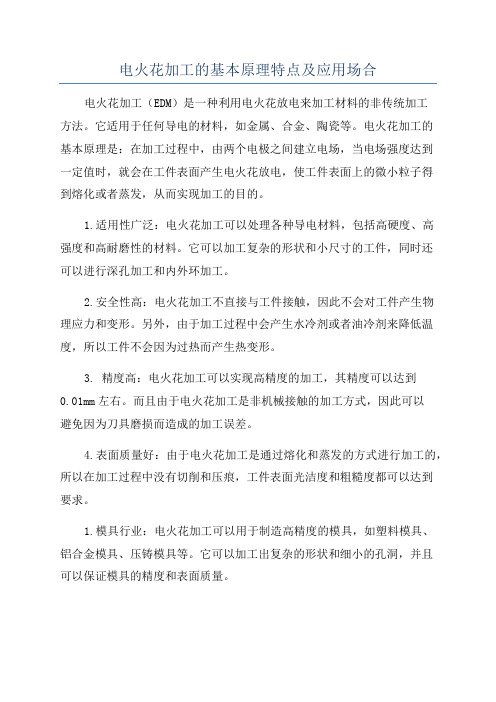
电火花加工的基本原理特点及应用场合电火花加工(EDM)是一种利用电火花放电来加工材料的非传统加工方法。
它适用于任何导电的材料,如金属、合金、陶瓷等。
电火花加工的基本原理是:在加工过程中,由两个电极之间建立电场,当电场强度达到一定值时,就会在工件表面产生电火花放电,使工件表面上的微小粒子得到熔化或者蒸发,从而实现加工的目的。
1.适用性广泛:电火花加工可以处理各种导电材料,包括高硬度、高强度和高耐磨性的材料。
它可以加工复杂的形状和小尺寸的工件,同时还可以进行深孔加工和内外环加工。
2.安全性高:电火花加工不直接与工件接触,因此不会对工件产生物理应力和变形。
另外,由于加工过程中会产生水冷剂或者油冷剂来降低温度,所以工件不会因为过热而产生热变形。
3. 精度高:电火花加工可以实现高精度的加工,其精度可以达到0.01mm左右。
而且由于电火花加工是非机械接触的加工方式,因此可以避免因为刀具磨损而造成的加工误差。
4.表面质量好:由于电火花加工是通过熔化和蒸发的方式进行加工的,所以在加工过程中没有切削和压痕,工件表面光洁度和粗糙度都可以达到要求。
1.模具行业:电火花加工可以用于制造高精度的模具,如塑料模具、铝合金模具、压铸模具等。
它可以加工出复杂的形状和细小的孔洞,并且可以保证模具的精度和表面质量。
2.航空航天行业:电火花加工可以用于制作航空航天行业的零部件,如叶片、导向器、火花塞等。
它可以实现复杂的形状和高精度的加工,并且可以保证零部件的强度和耐磨性。
3.医疗器械行业:电火花加工可以用于制造医疗器械的各种零部件,如人工关节、植入物等。
它可以加工出精确的形状和尺寸,并且可以保证医疗器械的表面光洁度和粗糙度。
4.电子行业:电火花加工可以用于制造微电子器件,如集成电路、芯片等。
它可以实现微米级别的加工精度,并且可以保证器件的电气性能和尺寸精度。
综上所述,电火花加工是一种非常灵活和高精度的加工方法,它具有广泛的适用性,并且可以在各个领域中实现高精度的加工。
电火花加工原理及应用
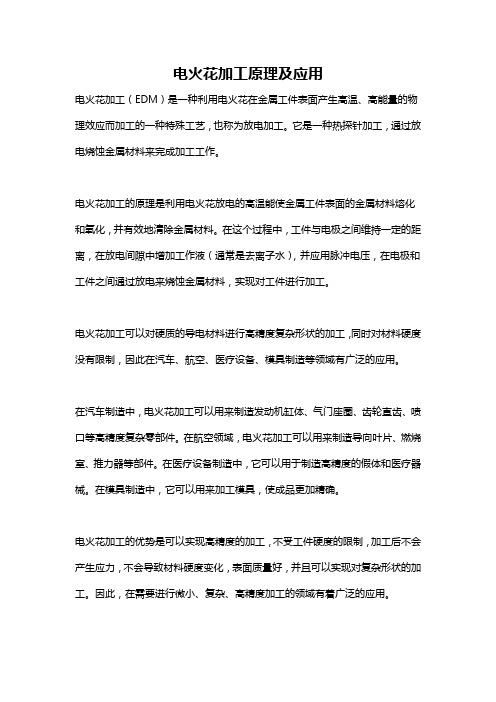
电火花加工原理及应用电火花加工(EDM)是一种利用电火花在金属工件表面产生高温、高能量的物理效应而加工的一种特殊工艺,也称为放电加工。
它是一种热探针加工,通过放电烧蚀金属材料来完成加工工作。
电火花加工的原理是利用电火花放电的高温能使金属工件表面的金属材料熔化和氧化,并有效地清除金属材料。
在这个过程中,工件与电极之间维持一定的距离,在放电间隙中增加工作液(通常是去离子水),并应用脉冲电压,在电极和工件之间通过放电来烧蚀金属材料,实现对工件进行加工。
电火花加工可以对硬质的导电材料进行高精度复杂形状的加工,同时对材料硬度没有限制,因此在汽车、航空、医疗设备、模具制造等领域有广泛的应用。
在汽车制造中,电火花加工可以用来制造发动机缸体、气门座圈、齿轮直齿、喷口等高精度复杂零部件。
在航空领域,电火花加工可以用来制造导向叶片、燃烧室、推力器等部件。
在医疗设备制造中,它可以用于制造高精度的假体和医疗器械。
在模具制造中,它可以用来加工模具,使成品更加精确。
电火花加工的优势是可以实现高精度的加工,不受工件硬度的限制,加工后不会产生应力,不会导致材料硬度变化,表面质量好,并且可以实现对复杂形状的加工。
因此,在需要进行微小、复杂、高精度加工的领域有着广泛的应用。
然而,电火花加工也存在一些局限性,如加工效率低、表面粗糙度较大、加工深度有限、加工平面需求限制等。
因此,在实际应用中,需要根据具体情况选择合适的加工方法。
总的来说,电火花加工作为一种先进的加工技术,在金属加工领域发挥着重要的作用,特别是在对材料硬度要求高、精度要求高的加工领域有着独特的优势。
随着科学技术的不断发展,电火花加工技术必将在未来得到更加广泛的应用。
EDM火花机的工作总结

EDM火花机的工作总结
EDM火花机是一种精密加工设备,它利用电脉冲放电的原理,通过电极和工
件之间的放电蚀削,来实现对金属材料的高精度加工。
在工业制造领域,EDM火
花机被广泛应用于模具制造、航空航天零部件加工、汽车零部件制造等领域。
下面我们来总结一下EDM火花机的工作原理和特点。
首先,EDM火花机的工作原理是利用电极和工件之间的放电蚀削来实现加工。
当电极和工件之间的间隙充满了工作液(通常是去离子水或矿物油),施加一定的电压,使电极和工件之间产生电火花放电。
这些电火花的高温和高能量可以瞬间熔化和蒸发金属材料,从而实现对工件的精密加工。
其次,EDM火花机具有高精度加工的特点。
由于电火花放电的能量非常集中,所以可以实现对工件的微小加工,精度可以达到数十微米甚至更高。
这使得EDM
火花机在制造高精度零部件时具有独特的优势。
另外,EDM火花机还具有加工复杂形状零件的能力。
由于电火花放电可以穿
透任意形状的工件,所以可以实现对复杂形状零件的加工,而不受工件形状的限制。
总的来说,EDM火花机是一种高精度、高效率的加工设备,它在工业制造领
域发挥着重要的作用。
随着科技的不断进步,相信EDM火花机的应用范围会越来
越广泛,为制造业的发展带来更多的可能性。
简述数控电火花成型加工的原理说明

简述数控电火花成型加工的原理说明数控电火花成型加工(简称EDM)是一种先进的加工方法,通过电火花的腐蚀作用,利用电脉冲的高能量释放,在工件与电极之间形成电火花放电间隙,从而实现对工件的精密加工和形状复杂表面的加工。
EDM加工的原理是利用电极与工件之间的放电现象来消耗材料,并将电极的形状精确地复制到工件上。
加工时,将带电火花电极靠近工件表面,在高频脉冲电压的作用下,电火花间隙中的电流会突然增大,形成放电,产生高温和高压的等离子体。
这些高温和高压等离子体会瞬间融化工件表面的材料,使之被腐蚀或溶化,并通过冲击力将溶化的材料从工件上排出,从而实现对工件的加工。
EDM加工具有独特的优点。
首先,它适用于对硬质、高强度、高硬度和脆性材料的加工,如钢、钛合金、硬质合金等。
其次,EDM加工可以加工出复杂形状和细小尺寸的零件,具有较高的加工精度和表面质量。
再次,由于是非接触式加工,不会产生切削力,因此不会对工件产生应力和变形,也不会产生刀具磨损,延长了工具的使用寿命。
在进行EDM加工时,需要注意一些操作要点。
首先,选择合适的电极材料和形状,根据工件材料的不同选择不同的电极材料,如铜、铜合金、石墨等。
其次,要控制好电极与工件之间的放电间隙,通常通过数控系统来控制,确保稳定的放电状态。
同时,还要根据加工要求选择合适的工艺参数,如放电脉冲频率、放电脉冲宽度和放电脉冲电流等。
最后,要定期检查电极磨损情况,及时更换磨损严重的电极,保证加工质量和效率。
总而言之,数控电火花成型加工是一种高效、精密的加工方法,广泛应用于航空航天、汽车、模具等领域。
通过深入理解EDM加工的原理和操作要点,可以更好地发挥其优势,提高加工质量和效率,推动制造业的发展。
电火花加工的原理及其应用
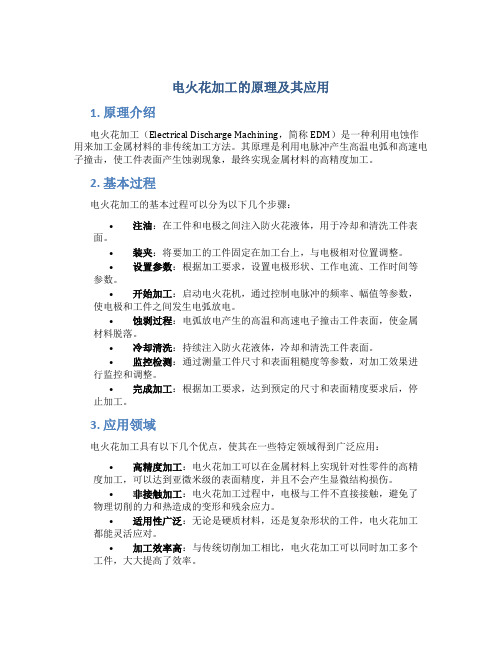
电火花加工的原理及其应用1. 原理介绍电火花加工(Electrical Discharge Machining,简称EDM)是一种利用电蚀作用来加工金属材料的非传统加工方法。
其原理是利用电脉冲产生高温电弧和高速电子撞击,使工件表面产生蚀剥现象,最终实现金属材料的高精度加工。
2. 基本过程电火花加工的基本过程可以分为以下几个步骤:•注油:在工件和电极之间注入防火花液体,用于冷却和清洗工件表面。
•装夹:将要加工的工件固定在加工台上,与电极相对位置调整。
•设置参数:根据加工要求,设置电极形状、工作电流、工作时间等参数。
•开始加工:启动电火花机,通过控制电脉冲的频率、幅值等参数,使电极和工件之间发生电弧放电。
•蚀剥过程:电弧放电产生的高温和高速电子撞击工件表面,使金属材料脱落。
•冷却清洗:持续注入防火花液体,冷却和清洗工件表面。
•监控检测:通过测量工件尺寸和表面粗糙度等参数,对加工效果进行监控和调整。
•完成加工:根据加工要求,达到预定的尺寸和表面精度要求后,停止加工。
3. 应用领域电火花加工具有以下几个优点,使其在一些特定领域得到广泛应用:•高精度加工:电火花加工可以在金属材料上实现针对性零件的高精度加工,可以达到亚微米级的表面精度,并且不会产生显微结构损伤。
•非接触加工:电火花加工过程中,电极与工件不直接接触,避免了物理切削的力和热造成的变形和残余应力。
•适用性广泛:无论是硬质材料,还是复杂形状的工件,电火花加工都能灵活应对。
•加工效率高:与传统切削加工相比,电火花加工可以同时加工多个工件,大大提高了效率。
•无需专门模具:电火花加工不需要专门制造模具,可以根据设计要求直接对工件进行加工。
•易于自动化:电火花加工具有较高的自动化程度,可以结合机器人、自动化生产线等设备进行多工位、多任务的加工。
基于以上优点,电火花加工在以下领域得到广泛应用:•航空航天:电火花加工可以用于加工航空发动机零件、涡轮叶片等高精度零件。
电火花EDM加工原理介绍
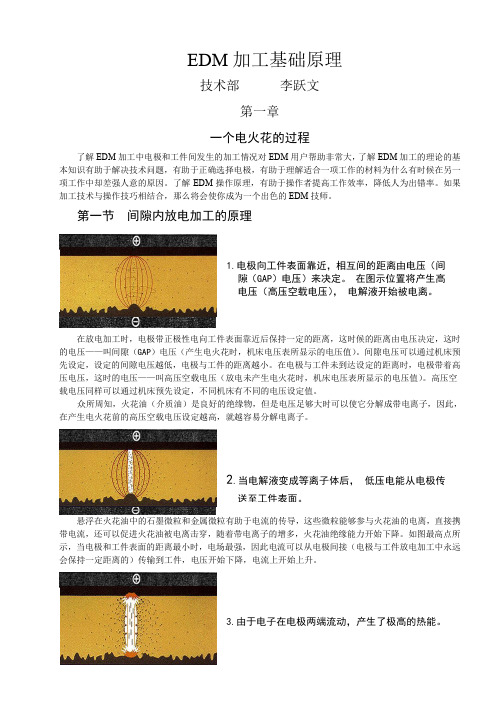
维持介质油容量和压力的平衡至关重要。进行粗加工时,放电间隙较大,因此为了达到较好的加工效 果需要较大的流量和较小的压力。而进行精加工时,放电间隙减小,则需要较高的压力,并加速介质油的 流动。
脉宽过长会影响加工效率。如果超出对应于每个电极和工件组合的最佳脉宽时,加工速度(MRR)实 际上是下降的。
电极——的脉冲可以使电极处于无损耗状态。但超过一定数值,再延长脉宽就会造成电极增长(负
损耗),就像电镀一样。
工件——有研究表明最佳脉宽可使工件金属的熔化层达到最深,而且热量能够散发,不再熔化更多
3.由于电子在电极两端流动,产生了极高的热能。
随着电流的上升增加,热量快速积聚,使部分火花油、工件和电极气化,形成放电通道,而产生电火 花。
4.随着电流流过电极 ,在电化学反应的作用下,产 生一个氢气泡。
随着不断的电流流过电极,热量不断上升,一个气泡试图向外膨胀,但由于离子受到强烈的电磁场作 用,不断冲向放电通道,这股冲力抑制了气泡的膨胀。此时,电流不断增加,电压继续下降。
当一进入间歇(休止),电压和电流就降至零。温度骤然下降和失去电磁场作用,导致气泡爆炸,熔 融的金属被抛离工件表面。由于爆炸力的作用,被抛离的金属物向周围排射而撞击到电极,若电极为脆性 或结构疏松的材料时,又或者电极此时得不到及时冷却时,电极因此亦会出现撞击损耗。
7.在周期结束时,由于材料被移除,工件上产生了 一个凹腔。未被抛离的熔融金属凝固成重铸层。
在一个电火花周期里,我们感觉是没办法判断出脉冲和间歇状态的,因为它们产生时间实在是太短的 原故。要分别出它们的状态和时间的长短,就要借助视波器来监测了。通常我们在加工过程中所看见机头
电火花机加工原理

电火花机加工原理
电火花机加工(Electrical Discharge Machining,EDM)是一种特殊的非接触式精密加工方法,其基本原理是利用电极与工件之间脉冲放电时产生的电蚀现象来蚀除金属材料,从而达到对工件进行精密加工的目的。
具体工作过程如下:
1、工具电极与工件电极设置:电火花机加工过程中,工件和工具电极(通常是铜或石墨)不直接接触,而是保持一定的放电间隙(一般在几十微米到几百微米之间)。
2、脉冲电源供电:工件和工具电极分别接到脉冲电源的两极,通过脉冲电源向间隙中施加电压,当电压达到一定程度时,工作液(如去离子水或矿物油)被击穿,形成电弧放电通道。
3、电蚀过程:在放电通道中,瞬时高温使极小区域内(微观级别)的金属材料瞬间熔化、气化,并在压力作用下以微小颗粒的形式被工作液冲走。
每次放电蚀除的金属量极小,但通过高频脉冲反复放电,累积起来就可以实现对工件的精确切割或成型。
4、自动进给:在加工过程中,工具电极通过伺服系统自动向工件靠近,保持稳定的放电间隙,以确保连续蚀除材料,实现三维轮廓的精确加工。
电火花机加工主要用于加工高硬度、高韧性、复杂形状或含有细微结构的零件,尤其适用于模具制造、航空航天零件加工以及精密仪器制造等领域。
2.1 电火花加工的基本原理和特点
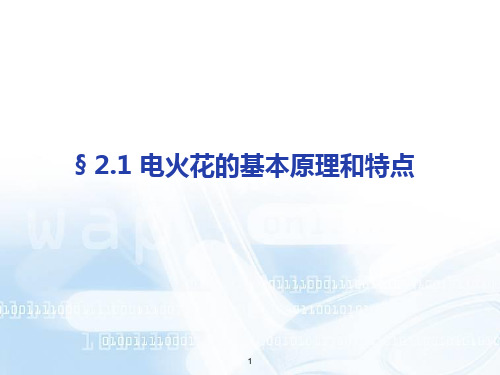
2、电火花加工系统与波形图
4
脉冲电源的放电电压及电流波形
正常工作后的电压、电流波形
5
电火花加工表面不同于普通金属切削表面具有规则的切 削痕迹,其表面是由无数个不规则的放电凹坑组成。
6
3、电火花加工的特点
优点:
1)适合于加工任何难切削导电材料 材料的可加工性主要取决于材料导电性及热学特性,与其力学性能(硬度、
8
§ 2.1 电火花的基本原理和特点
1
1、电火花加工的基本原理
所谓电火花加工(Electrical Discharge Machine简称EDM)是指在介质中, 利用两极(工具电极与工件电极)之间脉冲性火花放电时的电腐蚀现象对材料 进行加工,使零件的尺寸、形状和表面质量达到预定要求的加工方法。
在火花放电时,火花通道内瞬时产生的大量热致使电极表面的金属产生 局部熔化甚至气化而被蚀除下来。
强度等)无关。 2)可以加工特殊及复杂形状的表面和零件 没有机械加工的切削力,适宜加工低刚度工件及进行微细加工。 3)易于实现加工过程自动化
直接利用电能加工,而电能、电参数较机械量易于实现数字控制、适应 控制、智能化控制和无人化操作等; 4)通过改进结构设计,改善零件结构的加工工艺性
7
局限性:
1)一般只能加工金属等导电材料; 2)加工速度一般较慢; 3)存在电极损耗; 4)最小角部半径有限制; 5)加工表面有变质层甚至微裂纹。
2
利用电腐蚀现象进行尺寸加工,须解决三个问题 1.工具与工件之间必须保持一定的放电间隙,0.01mm—0.1mm
——必须具有工具电极的自动进给和调节装置
2.火花放电必须是脉冲性放电 ——必须使用脉冲电源
3.需绝缘强度达103~107Ω·cm的液态绝缘介质 ——工作液循环系统
简述电火花线切割原理

简述电火花线切割原理电火花线切割(Electrical Discharge Machining,简称EDM)是一种通过电火花放电来切割金属材料的加工方法。
它利用电火花放电的高能量和热能来熔化金属材料,从而实现切割的目的。
本文将从原理、设备和应用三个方面进行介绍。
一、原理电火花线切割的基本原理是利用电火花放电的高温和高能量来熔化金属材料,然后通过喷射冷却剂将其冷却和固化。
具体步骤如下:1. 电极与工件之间形成放电通道。
在电火花线切割中,通常使用一根细且导电性好的铜丝作为电极,它与工件之间保持一定的间距。
通过电源的控制,使电极与工件之间形成放电通道。
2. 电极与工件之间产生电火花放电。
电极和工件之间的放电通道中充满了绝缘介质,通常是脱脂石蜡。
当电源施加足够的电压时,放电通道中的电流会引发电火花放电。
3. 放电产生高温和高能量。
电火花放电会产生高温和高能量,使放电通道中的金属材料瞬间熔化。
同时,放电通道中的电流也会产生强大的电磁力,将熔化的金属材料冲击出去。
4. 冷却和固化。
在电火花放电的同时,冷却剂会被喷射到放电通道中,将熔化的金属材料冷却和固化。
冷却剂通常是脱离剂或脱脂石蜡,它们具有良好的冷却和固化效果。
二、设备电火花线切割设备主要由电源、控制系统、工作台和电极线等组成。
1. 电源。
电源是电火花线切割的核心部件,它提供足够的电压和电流来产生电火花放电。
常见的电源有脉冲电源和直流电源,它们可以根据不同的加工需求进行选择。
2. 控制系统。
控制系统用于控制电源的工作状态和放电通道的形成。
它可以通过调节电源的电压和电流来控制放电的强度和频率,从而实现对加工过程的控制。
3. 工作台。
工作台是放置工件的平台,它通常具有三个自由度的运动,可以实现工件在不同方向上的移动。
工作台的运动可以通过计算机数控系统来控制,从而实现复杂形状的切割。
4. 电极线。
电极线是电火花线切割中的重要部件,它负责将电源与工件连接起来,并传递电流和信号。
edm加工工艺
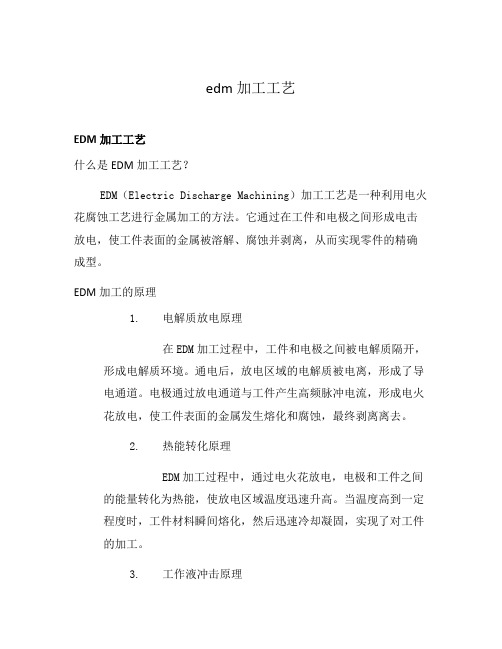
edm加工工艺EDM加工工艺什么是EDM加工工艺?EDM(Electric Discharge Machining)加工工艺是一种利用电火花腐蚀工艺进行金属加工的方法。
它通过在工件和电极之间形成电击放电,使工件表面的金属被溶解、腐蚀并剥离,从而实现零件的精确成型。
EDM加工的原理1.电解质放电原理在EDM加工过程中,工件和电极之间被电解质隔开,形成电解质环境。
通电后,放电区域的电解质被电离,形成了导电通道。
电极通过放电通道与工件产生高频脉冲电流,形成电火花放电,使工件表面的金属发生熔化和腐蚀,最终剥离离去。
2.热能转化原理EDM加工过程中,通过电火花放电,电极和工件之间的能量转化为热能,使放电区域温度迅速升高。
当温度高到一定程度时,工件材料瞬间熔化,然后迅速冷却凝固,实现了对工件的加工。
3.工作液冲击原理EDM加工中,工作液起到了重要的冷却和清洗的作用。
工作液通过射流的方式冷却电极和工件,同时冲洗腐蚀产物,保持加工质量和电极的稳定性。
EDM加工的优势•高精度加工EDM加工可以实现微小、复杂形状的零件加工,具有极高的加工精度和表面质量,适用于精密模具制造和航空航天领域。
•无机械切削,无变形EDM加工是一种非接触加工方法,无需刀具的直接接触,可以避免材料的变形和应力的积累,适用于硬质材料和具有脆性的材料。
•可加工任意导电材料EDM加工不受材料硬度的限制,可以对任何导电材料进行加工,包括钢、铝、铜、钛等。
•高效率加工EDM加工可同时对多个工件进行加工,提高了工作效率。
并且由于工作液的冲洗作用,加工过程中不会产生切屑,也不会对工件产生热影响区,缩短了加工周期。
EDM加工的应用领域•模具制造EDM加工在模具制造中广泛应用,能够生产出高精度、复杂形状的模腔、模块等模具部件。
•航空航天工业EDM加工可用于航空航天领域的复杂零部件加工,如发动机叶片、涡轮盘等。
•医疗器械制造EDM加工可用于生产微小、精密的医疗器械,如手术刀片、植入物等。
edm加工工艺
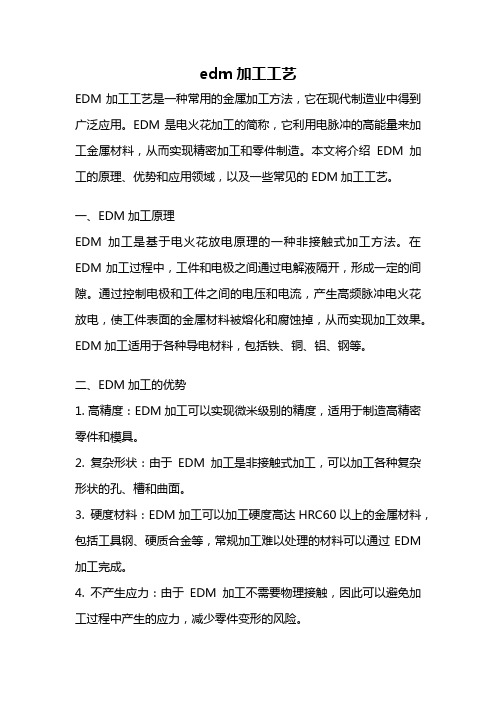
edm加工工艺EDM加工工艺是一种常用的金属加工方法,它在现代制造业中得到广泛应用。
EDM是电火花加工的简称,它利用电脉冲的高能量来加工金属材料,从而实现精密加工和零件制造。
本文将介绍EDM加工的原理、优势和应用领域,以及一些常见的EDM加工工艺。
一、EDM加工原理EDM加工是基于电火花放电原理的一种非接触式加工方法。
在EDM加工过程中,工件和电极之间通过电解液隔开,形成一定的间隙。
通过控制电极和工件之间的电压和电流,产生高频脉冲电火花放电,使工件表面的金属材料被熔化和腐蚀掉,从而实现加工效果。
EDM加工适用于各种导电材料,包括铁、铜、铝、钢等。
二、EDM加工的优势1. 高精度:EDM加工可以实现微米级别的精度,适用于制造高精密零件和模具。
2. 复杂形状:由于EDM加工是非接触式加工,可以加工各种复杂形状的孔、槽和曲面。
3. 硬度材料:EDM加工可以加工硬度高达HRC60以上的金属材料,包括工具钢、硬质合金等,常规加工难以处理的材料可以通过EDM 加工完成。
4. 不产生应力:由于EDM加工不需要物理接触,因此可以避免加工过程中产生的应力,减少零件变形的风险。
5. 高效率:EDM加工可以同时加工多个工件,提高生产效率。
三、EDM加工的应用领域1. 模具制造:EDM加工在模具制造中得到广泛应用,可以加工出复杂的模具结构和细小的模具零件。
2. 精密零件制造:由于EDM加工可以实现高精度和复杂形状的加工,因此在精密仪器、光学仪器等领域得到广泛应用。
3. 钣金加工:EDM加工可以用来加工钣金零件中的孔和槽,提高钣金加工的精度和质量。
4. 高硬度材料加工:EDM加工可以加工各种硬度高的金属材料,适用于工具钢、硬质合金等材料的加工。
5. 制造复杂形状零件:由于EDM加工可以实现复杂形状的加工,因此在飞机、船舶等领域的零件制造中得到广泛应用。
四、常见的EDM加工工艺1. 穿孔:穿孔是EDM加工中最基本的工艺,通过电火花放电的方式在工件上形成孔洞。
电火花加工的原理

电火花加工的原理电火花加工(Electric Discharge Machining,EDM)是一种非传统的金属加工技术,在航天、航空、汽车、模具、电子、医疗器械、手表等领域得到广泛应用。
其基本原理是在工件和电极间通过电弧放电击穿介质,利用电弧放电的高温高压作用,以腐蚀剥蚀的方式将工件上的材料去除,从而达到加工目的。
具有精度高、加工效率高、能够加工高硬度材料等优点。
本文将从原理、加工过程、影响因素、特点等方面对电火花加工进行详细介绍。
一、原理电火花加工是利用电脉冲的闪放放电从工件表面抽掉微小粒子的一种电化学加工方法。
其加工原理是利用电极间放电的高温高压效应,通过金属电极和工件上材料的反复电弧放电腐蚀、气化和溶解,使工件表面逐渐形成所需要的轮廓形状。
电弧放电腐蚀时会释放出高温和高压,将材料去除。
法则是在工件和电极之间形成电弧放电,在电极与工件接触底部的位置放电并生成热脱积过程,继而对工件进行加工。
二、加工过程1.热脱积过程当电极和工件接触之后,通过施加不同频率的脉冲电流,一系列闪电放电就在电极和工件之间反复发生,使工件表面材料被局部加热,压力蒸发产生的气体被排出,产生蚀刻物质。
2.形成水孔在每个放电的瞬间,电弧在工件和电极之间形成一个气态介质区域,这个地区的空气和蒸汽被抽出,形成一个小孔或某种形状的孔道。
当内腔填充时,材料被疏松起来。
3.清除工件表面的热脱积产物使用电极和工件之间的冷却剂来吹洗清理的剩余热脱积物质并加速加工物表面的光洁度。
三、影响因素1. 工作液质量也是影响加工精度的关键因素之一。
2. 电极材料和工作电流强度,也会影响加工效果,通常选择耐腐蚀性强的金属材料。
3. 工件材料也很重要,硬材料如钨合金、钢铁铸造件等可以使用电火花加工进行加工。
而软材料则不具备可切削性,难以加工。
4. 脉冲时间控制精度是主要的电火花加工参数。
5. 加工的形状、尺寸、表面状态和要求的加工精度等也会影响加工效果。
电火花加工原理

1943年,苏联学者拉扎连科夫妇研究发明电火花加工,之后随着脉冲电源和控制系统的改进,而迅速发展起来。
最初使用的脉冲电源是简单的电阻-电容回路。
50年代初,改进为电
工具电极相对损耗降低。
得以提高。
60年代中期,出现了晶体管和可控硅脉冲电源,提高了能源利用效率和降低了工具电极损耗,并扩大了粗精加工的可调范围。
最初简单地保持放电间隙,控制工具电极的进退,逐步发展到利用微型计算机,对电参数和
进行电火花加工时,工具电极和工件分别接脉冲电源的两极,并浸入工作液中,或将工作液充入放电间隙。
通过间隙自动控制系统控制工具电极向工件进给,当两电极间的间隙达到一定距离时,两电极上施加的脉冲电压将工作液击穿,产生火花放电。
能蚀除较多的金属,具有一定的生产率。
在保持工具电极与工件之间恒定放电间隙的条件下,一边蚀除工件金属,一边使工具电极不
的形状和工具电极与工件之间的相对运动方式,就能加工出各种复杂的型面。
在加工过程中,工具电极也有损耗,但小于工件金属的蚀除量,甚至接近于无损耗。
螺纹塞规、齿轮等的电火花共轭回转加工;小孔加工、刻印、表面合金化、表面强化等其他种类的加工。
动化;加工后表面产生变质层,在某些应用中须进一步去除;工作液的净化和加工中产生的烟雾污染处理比较麻烦。
电火花加工的主要用于加工具有复杂形状的型孔和型腔的模具和零件;加工各种硬、脆材料,。
- 1、下载文档前请自行甄别文档内容的完整性,平台不提供额外的编辑、内容补充、找答案等附加服务。
- 2、"仅部分预览"的文档,不可在线预览部分如存在完整性等问题,可反馈申请退款(可完整预览的文档不适用该条件!)。
- 3、如文档侵犯您的权益,请联系客服反馈,我们会尽快为您处理(人工客服工作时间:9:00-18:30)。
3.由于电子在电极两端流动,产生了极高的热能。
随着电流的上升增加,热量快速积聚,使部分火花油、工件和电极气化,形成放电通道,而产生电火 花。
4.随着电流流过电极 ,在电化学反应的作用下,产 生一个氢气泡。
随着不断的电流流过电极,热量不断上升,一个气泡试图向外膨胀,但由于离子受到强烈的电磁场作 用,不断冲向放电通道,这股冲力抑制了气泡的膨胀。此时,电流不断增加,电压继续下降。
此时新的火花(介质)油涌入型腔,冲走杂质,冷却工件和电极表面。在这时候,若没有足够的火花 油及油压把抛离出来的熔融金属冲走,重铸层变厚,蚀除量降低。但是大压力的冲油,又会把电极表面来 不及冷却的熔融层冲走,使电极损耗增大。熔点低的电极材料熔融层更厚,被冲走的会更多,所以当铜和 石墨做电极时,铜电极冲油过大会增加损耗就是这个原理,石墨的结构颗粒度比铜大及熔点比铜高,冲油 压力要比铜更大,排除杂物更好而不会增加损耗。
加工表面连成一片的蚀坑峰谷可用光洁度测量仪测定,通常用峰谷间算术平均值表示,单位是(μm Ra)。
第四节 工件材料
电火花加工时改变的不仅是工件表面,还有它的次表面。加工后的工件表面结构分为三层(图 1-3)。 电火花加工表面冲击层是由被抛出的熔融金属和少量电极微粒冲击而成。这一层很容易去除。 下一层是硬质层(氧化层)。电火花加工实质上改变了硬质层的冶金结构和特性。在介质油的作用下, 熔融金属迅速冷却,未被抛出去的熔融金属就凝固在型腔中形成了硬质层。这层硬而脆的氧化层会出现显 微裂纹。如果这一层太厚,或者通过抛光无法变薄或去除,那么这块工件可能在有些使用条件下过早损坏。 最后一层是受热层或退火层。它只是受热,并没有熔化。硬质层和受热层的厚度由工件材料的散热能 力和加工能量决定。不管如何,改变的金属层都会影响工件表面原来的属性。 数控电火花机床上的自动精加工电路能够有效减少硬质层的形成,但仍然无法消除退火层。
的金属,这时型腔底部的温度降至熔点以下。
间歇(脉冲中断时间)
图 2-1 每个电火花加工周期都由脉宽和间歇组成
从一个循环到下一个循环开始,必须有足 够长的间歇,这样才算完成一个周期。间歇会 影响加工速度和稳定性。理论上而言,间歇越 短,加工速度越快。但如果间歇过短,介质油 就无法将杂质冲洗干净,本身也无法消除电 离。收此造成下一次放电不稳定,循环变形, 伺服系统自动回撤,与较长且稳定的间歇相 比,反而会降低加工速度。
冲油的三种基本方式分别为:压力冲油、抽油和侧面冲油(图 1-1)。冲油方式的选择应根据具体加工 情况而定。电极的形状和尺寸也会限制冲油方式的选择。
侧面冲油
抽油
压力冲油
压力冲油
图 1-1 三种冲油方式
作为最常用的冲油方法,压力冲油使介质油在压力作用下强行通过电极中的冲油孔进入放电间隙,与
微粒一道从型腔边缘流出。由于液体从电极中通过,所以这种方法有助于电极的冷却。另一种类似的方法
是从工件上的小孔压入介质油。
二次放电和移动微粒的摩擦作用会磨损型腔侧壁,破坏表面光洁度。抽油法则可以避免这种缺陷。
二次放电
高温介质油沿著型腔侧壁流出放电间隙时能够造成大量热能的积聚。这些热能可以使型腔壁轻微膨
胀。这时,沿著型腔壁移动的导电微粒会产生二次放电。由于放电总在电阻最小的地方产生,所以它可能
图 1-3 电火花加工形成的三层层面。
第二章
火花控制
第一节 电火花加工周期
每个加工周期由脉宽和间歇组成(图 2-1),它们均以微秒为位。由于电蚀在放电时才进行,所以脉宽 及其频率至关重要。
脉宽(脉冲持续时间)
金属蚀除量同脉冲能量成正比。后者由峰值电流和脉宽决定。脉宽越长,蚀除的金属材料越多,产生 的蚀坑越深越宽,由此得到的工件表面比较粗糙。同时延长脉宽意味著更多的热能作用于工件并向下延展, 这样势必造成更厚的硬质层,而氧化层也更深了。
第二节 进入型腔内部的状态
在工件上进行熔蚀时会形成一个型腔。型腔越深,去除杂质越困难,电极和工件的冷却也越困难。要 使加工稳定进行,必须确保介质油冲过间隙,因此,冲油成了电火花加工过程中必要的组成部分。
成功的冲油可以清除放电间隙中熔蚀的工件微粒和损耗的电极微粒,让介质油顺利进入间隙。要维持 稳定的加工,防止产生电弧,就必须做到以上两点。
度。电压值越高,放电间隙越宽,冲油条件就越好,加工也比较稳定。但是,使用石墨作为电极时,高电
压会增加电极的损耗。
图 2-2 一旦电压产生了电离通 道,电流就开始增强,电压便降 至预设工作值。电流在加工周期 的有效脉宽时升至最高点。
极性
极性是指电极的极性,它决定了电流的方向。电极极性正负皆可。根据不同的加工情况,有时改变极
脉宽过长会影响加工效率。如果超出对应于每个电极和工件组合的最佳脉宽时,加工速度(MRR)实 际上是下降的。
电极——的脉冲可以使电极处于无损耗状态。但超过一定数值,再延长脉宽就会造成电极增长(负
损耗),就像电镀一样。
工件——有研究表明最佳脉宽可使工件金属的熔化层达到最深,而且热量能够散发,不再熔化更多
能量
电火花的能量由电流强度、电压和脉宽三者共
同决定。
电流——在脉冲持续时间内,电流从零一直上升到设定值,即电流峰值(图 2-2)。
电压——电流产生之前,放电间隙内的电压不断增加直到介质油中形成电离通道(图 2-2)。一旦电
流产生,电压便很快下降,并稳定在预设的工作间隙电压。该值决定了电极端面同工件之间放电间隙的宽
图 1-2 上图所示原为一块电极。未放出的气体一经电火 花点燃,会破坏有用的电极,造成火灾,甚至人员受伤。
第三节 电火花加工光洁度
电火花加工表面由无数次放电造成的微小蚀坑形成。每个电火花加工周期结束后,蚀坑的边缘又形成 新的高点,使之成为下一个周期熔蚀的优先位置,于是不同的蚀坑最终融合在一起,构成电火花加工表面 的随意性。由此得到的表面光洁度(SF)是电火花加工在众多行业中倍受青睐的魅力所在之一。
当一进入间歇(休止),电压和电流就降至零。温度骤然下降和失去电磁场作用,导致气泡爆炸,熔 融的金属被抛离工件表面。由于爆炸力的作用,被抛离的金属物向周围排射而撞击到电极,若电极为脆性 或结构疏松的材料时,又或者电极此时得不到及时冷却时,电极因此亦会出现撞击损耗。
7.在周期结束时,由于材料被移除,工件上产生了 一个凹腔。未被抛离的熔融金属凝固成重铸层。
当电极平动量大于冲油孔的半径时,工件型腔内便不会留下锥凸痕迹。
气泡
电火花产生的气泡集聚在盲孔中,可能像汽油机的气缸里发生的爆炸一样,会损伤电极和工件。如果 气泡累积过多,还会产生火灾隐患(图 1-2)。虽然现在自动监视装置和介质油温控设置已大大降低了火灾 的可能性,我们仍然必须牢记介质油是易然品。如果设计过程中预见到了气泡产生的可能性,就应采取措 施将气泡排到表面。例如在电极上加排气孔或工件型腔上保持通孔,而且还可以减除压力对放电稳定性的 影响,提高加工速度。
EDM 加工基础原理
技术部
Hale Waihona Puke 李跃文第一章一个电火花的过程
了解 EDM 加工中电极和工件间发生的加工情况对 EDM 用户帮助非常大,了解 EDM 加工的理论的基 本知识有助于解决技术问题,有助于正确选择电极,有助于理解适合一项工作的材料为什么有时候在另一 项工作中却差强人意的原因。了解 EDM 操作原理,有助于操作者提高工作效率,降低人为出错率。如果 加工技术与操作技巧相结合,那么将会使你成为一个出色的 EDM 技师。
第一节 间隙内放电加工的原理
1.电极向工件表面靠近,相互间的距离由电压(间 隙(GAP)电压)来决定。 在图示位置将产生高 电压(高压空载电压), 电解液开始被电离。
在放电加工时,电极带正极性电向工件表面靠近后保持一定的距离,这时候的距离由电压决定,这时 的电压——叫间隙(GAP)电压(产生电火花时,机床电压表所显示的电压值)。间隙电压可以通过机床预 先设定,设定的间隙电压越低,电极与工件的距离越小。在电极与工件未到达设定的距离时,电极带着高 压电压,这时的电压——叫高压空载电压(放电未产生电火花时,机床电压表所显示的电压值)。高压空 载电压同样可以通过机床预先设定,不同机床有不同的电压设定值。
8.被抛离的金属凝固成圆形小颗粒和电极上掉下来 的铜(碳)屑一起分散在介质油中。没有破碎的 气泡浮到表面。紧接着下一个放电周期又开始。
如果间歇(休止)不够长,,冲油状况不当,排除杂质困难,那么杂质可能会集结起来,影响放电的 稳定性。在这种情况下还可能会产生直流拉弧(二次放电),损坏电极和工件。
以上八张图示说明了单个电火花加工周期中发生的过程状态。一个电火花周期由脉冲和间歇构成。脉 冲和间歇以时间微秒(μs ,一百万分之一秒)为单位(机床的设定亦会以级数设置)。如下图示(以夏米 尔 EDM 为例),它们的时间可以各在 1.2 至 3200 微秒(1 至 8 级)内控制,每分钟最多可以循环 25 万次 电火花周期,但在某一个指定的时刻内只有一个循环。一旦了解了这个循环周期,我们就能通过控制脉冲 和间歇,让电火花加工为我们工作服务。
利用电极的抬刀升起,保证足够的时间清除放电间隙可以改善这一状况。但这样做却降低了加工速度。
不可平动的电极
由于电极上设有冲油孔,这就意味著工件的对应部位不能被蚀除,因此加工时型腔中会留下锥凸体。
根据不同的切削深度,有时需要停止电火花加工,去除锥凸的方法是人工去除或用后备电极(无冲油孔)
蚀除。
平动电极
平动电极能够简化冲油操作。由于较小的电极平动时,会使放电间隙的一边相对变宽,有利于介质油 和微粒从型腔中排出。电极的平动同时还有助于介质油的更新。如果平动功能灵活的 EDM 机床应用平动 加工,不单简化了冲油操作,而且加工效率和质量也得到提高。
众所周知,火花油(介质油)是良好的绝缘物,但是电压足够大时可以使它分解成带电离子,因此, 在产生电火花前的高压空载电压设定越高,就越容易分解电离子。
2.当电解液变成等离子体后, 低压电能从电极传