选矿回收率怎么计算
选矿回收率计算公式简单

选矿回收率计算公式简单选矿回收率是指在矿石经过选矿过程后,所能获得有价值矿石的比例,也是评估选矿工艺技术优劣的重要指标。
其计算公式为:回收率(%)= (有价值矿石的重量/原始矿石的重量) × 100%选矿回收率的计算公式虽然简单,但对于选矿工艺的优化与改进具有重要的指导意义。
高的选矿回收率意味着从原始矿石中获得更多的有价值矿石,能够提高矿石的经济效益,降低生产成本,并减少对矿石资源的开采压力。
要想实现高的选矿回收率,首先需要充分了解矿石的性质和成分。
不同矿石的物理化学性质各异,因此在选矿过程中需要制定不同的选矿方案和流程。
通过对矿石的采样分析,可以确定矿石的有价值成分和废石的成分,从而制定出科学的选矿方案,并选择适当的选矿设备。
其次,在选矿过程中需要合理地选择选矿工艺指标。
选矿工艺指标是衡量选矿工艺优劣的重要指标,包括矿石的粒度分布、浮选药剂的种类和用量、搅拌强度、选矿机械参数等。
通过调整这些指标,可以改善选矿工艺的效果,提高回收率。
再次,选矿过程中需要合理操作和控制选矿设备。
选矿设备的操作水平直接影响到回收率的提高与否。
在选矿过程中,需要根据矿石的性质和矿石的产量,合理调整选矿设备的参数,保持设备的稳定运行。
同时,需要合理配备操作人员,进行专业培训,提高其操作技能和业务水平。
只有设备正常运行、操作得当,才能保证选矿回收率的提高。
最后,需要对选矿过程进行全面的监测与控制。
通过对选矿过程的实时监测,可以发现问题并及时进行调整和改进。
可利用传感器、仪表等监测设备,对选矿过程的关键参数进行监测,如矿石的进料量、产出量、选矿液的流量与浓度等。
通过定时收集和分析这些数据,及时调整选矿工艺的参数和操作方式,以提高选矿回收率。
综上所述,选矿回收率的提高需要全面考虑矿石的性质、选矿工艺方案、选矿设备操作和监测控制等多个因素。
只有通过科学的方法和有效的措施,才能够实现选矿回收率的提高,从而提高矿石的经济效益,保护矿石资源,实现可持续发展。
采矿最终回收率计算公式

采矿最终回收率计算公式在选矿中,得到的某一产品的重量与原矿重量的百分比,称为该产品的产率;
在选矿流程中,也可以通过产品的品位计算精矿产率:
精矿产率=(原矿品位α-尾矿品位θ)÷(精矿品位β-尾矿品位θ)
选矿回收率有实际回收率与理论回收率两种:
实际回收率=[(实际精矿数量(吨)×精矿品位)÷(原矿处理量(吨)×原矿品位)]×100%
理论回收率=[β(α-θ)÷α(β-θ) ]×100% 式中符号同前
一般理论回收率要高于实际回收率,但不会差别太大。
选矿厂两种回收率都用,根据二者数据进行对比分析,掌握选矿中的不正常情况。
回收率包括绝对回收率和相对回收率。
绝对回收率考察的是经过样品处理后能用于分析的药物的比例。
因为不论是生物基质还是制剂辅料中的药物,经过样品处理都有一定的损失。
相对回收率严格来说有两种。
一种是回收试验法,另一种是加样回收试验法。
前者是在空白基质中加入药品,标准曲线也是同此,这种测定用得较多,但有标准曲线重复测定的嫌疑。
第二种是在已知浓度样品中加入药物,来和标准曲线比,标准曲线也是在基质中加药物。
则精矿产率可由它们的品位计算:=(α-δ)/(β-δ)×100%;α、β和δ分别代表给矿、精矿和尾矿的品位(%)。
这种由产品品位计得的产率,又称为理论产率。
选矿回收率怎么计算
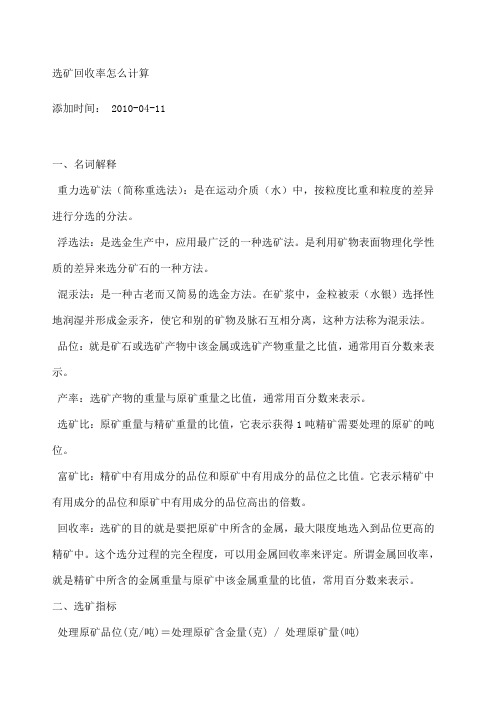
选矿回收率怎么计算添加时间: 2010-04-11一、名词解释重力选矿法(简称重选法):是在运动介质(水)中,按粒度比重和粒度的差异进行分选的分法。
浮选法:是选金生产中,应用最广泛的一种选矿法。
是利用矿物表面物理化学性质的差异来选分矿石的一种方法。
混汞法:是一种古老而又简易的选金方法。
在矿浆中,金粒被汞(水银)选择性地润湿并形成金汞齐,使它和别的矿物及脉石互相分离,这种方法称为混汞法。
品位:就是矿石或选矿产物中该金属或选矿产物重量之比值,通常用百分数来表示。
产率:选矿产物的重量与原矿重量之比值,通常用百分数来表示。
选矿比:原矿重量与精矿重量的比值,它表示获得1吨精矿需要处理的原矿的吨位。
富矿比:精矿中有用成分的品位和原矿中有用成分的品位之比值。
它表示精矿中有用成分的品位和原矿中有用成分的品位高出的倍数。
回收率:选矿的目的就是要把原矿中所含的金属,最大限度地选入到品位更高的精矿中。
这个选分过程的完全程度,可以用金属回收率来评定。
所谓金属回收率,就是精矿中所含的金属重量与原矿中该金属重量的比值,常用百分数来表示。
二、选矿指标处理原矿品位(克/吨)=处理原矿含金量(克) / 处理原矿量(吨)精矿品位:是指平均每吨精矿中的含金量,它是反映精矿质量的指标,计算公式为:精矿品位(克/吨)=精矿含金量(克) / 精矿数量(吨)精矿产率:是指产出的精矿量占原矿量的百分比,它是反映选矿厂质量的指标。
计算公式为:精矿产率(%)=精矿数量(吨) /原矿数量(吨) ×100%尾矿品位:是指选矿厂排弃的尾矿中,平均每吨尾矿中的含金量。
它是反映在选矿过程中金属损失程度的指标。
计算公式为:尾矿品位(克/吨)=尾矿含金量(克)/尾矿数量(吨)尾矿量(吨)=处理原矿量(吨)-精矿量(吨)选矿回收率:是指采用各种选矿方法获得的最终产品含金量占处理原矿含金量的百分比。
按理论和实际回收率两种方法计算。
选矿理论回收率(%)=精矿品位×(原矿品位-尾矿品位)/(原矿品位×(精矿品位-尾矿品位) ×100%=理论回收的金属量(克) /处理原矿金属量(克)×100%选矿实际回收率(%)=金精矿含金量(克)/原矿含金量(克)×100%(浮选回收率)浸出率:是指经浸出作业已溶解金的金属量占氰原矿金属量的百分比。
矿物回收率的计算公式
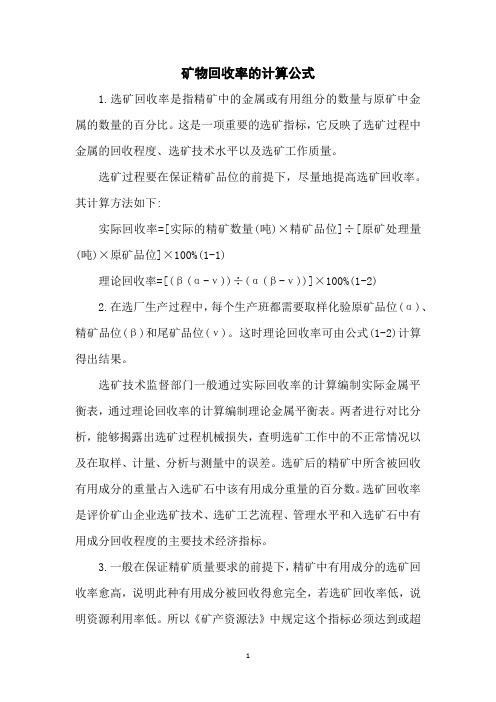
矿物回收率的计算公式1.选矿回收率是指精矿中的金属或有用组分的数量与原矿中金属的数量的百分比。
这是一项重要的选矿指标,它反映了选矿过程中金属的回收程度、选矿技术水平以及选矿工作质量。
选矿过程要在保证精矿品位的前提下,尽量地提高选矿回收率。
其计算方法如下:实际回收率=[实际的精矿数量(吨)×精矿品位]÷[原矿处理量(吨)×原矿品位]×100%(1-1)理论回收率=[(β(α-ν))÷(α(β-ν))]×100%(1-2)2.在选厂生产过程中,每个生产班都需要取样化验原矿品位(α)、精矿品位(β)和尾矿品位(ν)。
这时理论回收率可由公式(1-2)计算得出结果。
选矿技术监督部门一般通过实际回收率的计算编制实际金属平衡表,通过理论回收率的计算编制理论金属平衡表。
两者进行对比分析,能够揭露出选矿过程机械损失,查明选矿工作中的不正常情况以及在取样、计量、分析与测量中的误差。
选矿后的精矿中所含被回收有用成分的重量占入选矿石中该有用成分重量的百分数。
选矿回收率是评价矿山企业选矿技术、选矿工艺流程、管理水平和入选矿石中有用成分回收程度的主要技术经济指标。
3.一般在保证精矿质量要求的前提下,精矿中有用成分的选矿回收率愈高,说明此种有用成分被回收得愈完全,若选矿回收率低,说明资源利用率低。
所以《矿产资源法》中规定这个指标必须达到或超过设计选矿回收率指标。
在保证精矿质量的前提下,不断提高选矿回收率,不仅能充分回收矿产资源,而且能提高矿山经济效益。
损失部分包括:浮选机的跑槽及出现故障时的溢出物、浓缩机的溢流“跑浑”、皮带机的掉矿、球磨给矿处的漏矿、精矿运输车辆漏矿等等。
在操作过程中力求减少损失,以提高精矿的实际回收率。
选矿常用计算公式

选矿常用计算公式公司标准化编码 [QQX96QT-XQQB89Q8-NQQJ6Q8-MQM9N]选矿常用计算公式1、品位:一般用化学分析确定α一原矿品位,β—精矿品位,θ—尾矿品位2、产率:(1)用重量计算γ精= Q K/ Q n*(100%) γ尾= Q n- Q k/ Q n*(100%) 式中:Q n、Q k分别为原矿和精矿重量(吨)(2)用品位计算γ精=α-θ/β-θ*(100%) γ尾=1- γ精(3)用回收率计算γ精=α·ε/β*100%式中:ε为回收率3、选矿比:(1)用重量计算K重= Q k/ Q n(倍)(2)用品位计算K重=β-θ/α-θ(倍)4、富矿比:I n=β/α(倍)5、破碎比:I=D max/d min 式中:D max破碎前物料最大块直径(mm)d min破碎后物料最大块直径(mm)6、单个矿块粒度计算:d=(a+b+c)/3 式中:a、b、c分别为块矿的长、宽、高尺寸7、筛分效率:(1)E1=β(α-θ)/α(β-θ)*100%(2)E2=C/(θ*α)*100%式中:α、β、θ分别为给矿、筛下、筛上产物中小于筛孔尺寸粒级的百分含量,C为筛下产品重量8、破碎机作业率:?作=t实/t计*100% 式中:t实为破碎机实际开车小时数 t计为日历台数X台数X24小时(计开车小时数)9、球磨机作业率:计算方法同破碎机作业率10、球磨机台数能力:Q台= Q总/ t实(t/H)式中:Q台为球磨机1小时处理原矿吨数Q总为球磨机当班(或日、月、季、年等)处理原矿总吨数11、球磨机利用系数:?系= Q台/V(t/H·m3)式中:?系为球磨机单位体积单位时间内处理的原矿量V为球磨机有效容积(m3)12、磨矿效率:q-200= Q台(γ溢-γ给)/V(t/H·m3)式中:q-200为磨机单位时间单位容积磨出指定粒级的矿山重量γ溢为溢流中指定粒级含量的百分数γ给为给矿中指定粒级含量的百分数13、按电耗计算磨矿效率:C= q·V/N(t/瓦·时)式中:C为按电耗计算得磨矿效率q为磨机单位时间单位容积的-200的含量N为单位时间磨机耗电量(度)14、球磨机转数:(1)临界转数n临=√D(转/分)(2)实际转数n实 =√D-2b(转/分)(3)工作转数??2=??同/S(转/分)式中:D为球磨直径 b为球磨衬板厚度?同为同步机转数 S为球磨机大、小齿轮之比(转数)15、装球量公式:G=φ·V·△式中:G为装球量(吨)φ为充填系数百分数(取40-45%)△为钢球堆比重(取△=m3)16、装球直径(拉祖莫夫公式)D=f3√d式中:D为钢球直径(mm)f为矿石性质(硬度)系数(f在28-38-48)d为给矿最大直径(mm)17、介质球充填率:φ=50-127*b/D(%)式中:φ为钢(铁)球充填率(%)b为介质水平面距磨机筒体中心线高度(m)D为磨机有效直径(m)18、钢球重量:W=*(π/6)D3式中:W为单个钢球重量(g或kg)D为钢球直径(mm)19、分级效率:E=(α-θ)(β-α)/α(β·θ)(1-α)*100%式中:E为分级效率α为给矿中小于分级粒度含量(%)β为溢流中小于分级粒度含量(%)θ为沉砂中小于分级粒度含量(%)20、细筛筛分效率:计算公式同分级效率21、分级返砂循环负荷:C=(β-α)/(α-θ)*100%22、返砂比: C=S/ Q(%)式中:C为返砂比S为返砂量(吨)Q为新给矿量(吨)23、细筛分离粒度经验公式:(1)d=1/2·S·K式中:d为细筛分离粒度(mm)S 为筛孔尺寸(mm)K为系数(在~)(2)查表法S·d及倾角24、过滤效率:q精= Q总/∑m2·∑t(t/H·m3)式中:Q总为各台过滤机过滤干精矿之和(吨)∑m2为参加生产过滤机有效面积之和(m2)∑t为各台过滤机实际过滤时间之和(小时)25、回收率的计算:(1)实际回收率ε=(Q k*β)/(Q0*α)*100%(2)理论回收率ε=β(α-θ)/α(β-θ)*100%式中:Q k为精矿产量,Q0为尾矿产量磁选机磁场感应强度表示:1T(特斯拉)=1000mT(毫特斯拉)=10000GS(高斯)。
地矿科普:选矿基础解释及回收率

地矿科普:选矿基础解释及回收率选矿基础解释及回收率怎么计算⼀、名词解释重⼒选矿法(简称重选法):是在运动介质(⽔)中,按粒度⽐重和粒度的差异进⾏分选的分法。
浮选法:是选⾦⽣产中,应⽤最⼴泛的⼀种选矿法。
是利⽤矿物表⾯物理化学性质的差异来选分矿⽯的⼀种⽅法。
混汞法:是⼀种古⽼⽽⼜简易的选⾦⽅法。
在矿浆中,⾦粒被汞(⽔银)选择性地润湿并形成⾦汞齐,使它和别的矿物及脉⽯互相分离,这种⽅法称为混汞法。
品位:就是矿⽯或选矿产物中该⾦属或选矿产物重量之⽐值,通常⽤百分数来表⽰。
产率:选矿产物的重量与原矿重量之⽐值,通常⽤百分数来表⽰。
选矿⽐:原矿重量与精矿重量的⽐值,它表⽰获得1吨精矿需要处理的原矿的吨位。
富矿⽐:精矿中有⽤成分的品位和原矿中有⽤成分的品位之⽐值。
它表⽰精矿中有⽤成分的品位和原矿中有⽤成分的品位⾼出的倍数。
回收率:选矿的⽬的就是要把原矿中所含的⾦属,最⼤限度地选⼊到品位更⾼的精矿中。
这个选分过程的完全程度,可以⽤⾦属回收率来评定。
所谓⾦属回收率,就是精矿中所含的⾦属重量与原矿中该⾦属重量的⽐值,常⽤百分数来表⽰。
⼆、选矿指标处理原矿品位(克/吨)=处理原矿含⾦量(克) / 处理原矿量(吨)精矿品位:是指平均每吨精矿中的含⾦量,它是反映精矿质量的指标,计算公式为:精矿品位(克/吨)=精矿含⾦量(克) / 精矿数量(吨)精矿产率:是指产出的精矿量占原矿量的百分⽐,它是反映选矿⼚质量的指标。
计算公式为:精矿产率(%)=精矿数量(吨) /原矿数量(吨) ×100%尾矿品位:是指选矿⼚排弃的尾矿中,平均每吨尾矿中的含⾦量。
它是反映在选矿过程中⾦属损失程度的指标。
计算公式为:尾矿品位(克/吨)=尾矿含⾦量(克)/尾矿数量(吨)尾矿量(吨)=处理原矿量(吨)-精矿量(吨)选矿回收率:是指采⽤各种选矿⽅法获得的最终产品含⾦量占处理原矿含⾦量的百分⽐。
按理论和实际回收率两种⽅法计算。
选矿理论回收率(%)=精矿品位×(原矿品位-尾矿品位)/(原矿品位×(精矿品位-尾矿品位) ×100%=理论回收的⾦属量(克) /处理原矿⾦属量(克)×100%选矿实际回收率(%)=⾦精矿含⾦量(克)/原矿含⾦量(克)×100%(浮选回收率)浸出率:是指经浸出作业已溶解⾦的⾦属量占氰原矿⾦属量的百分⽐。
选矿常用计算公式
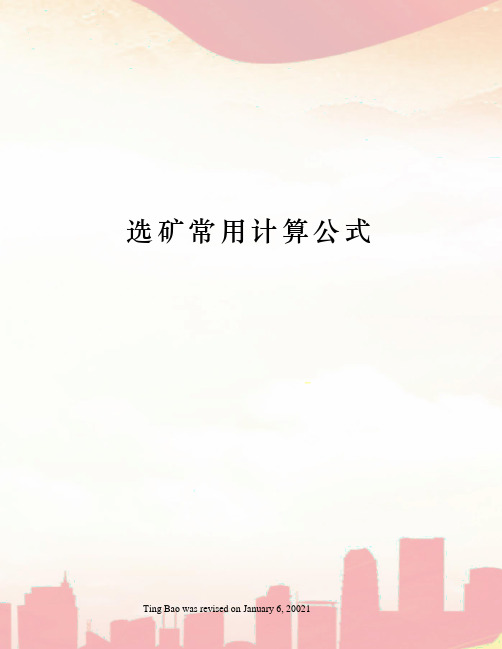
选矿常用计算公式 Ting Bao was revised on January 6, 20021选矿常用计算公式1、品位:一般用化学分析确定α一原矿品位,β—精矿品位,θ—尾矿品位2、产率:(1)用重量计算γ精=Q K/Q n*(100%)γ尾=Q n-Q k/Q n*(100%)式中:Q n、Q k分别为原矿和精矿重量(吨)(2)用品位计算γ精=α-θ/β-θ*(100%)γ尾=1-γ精(3)用回收率计算γ精=α·ε/β*100%式中:ε为回收率3、选矿比:(1)用重量计算K重=Q k/Q n(倍)(2)用品位计算K重=β-θ/α-θ(倍)4、富矿比:I n=β/α(倍)5、破碎比:I=D max/d min式中:D max破碎前物料最大块直径(mm)d min破碎后物料最大块直径(mm)6、单个矿块粒度计算:d=(a+b+c)/3式中:a、b、c分别为块矿的长、宽、高尺寸7、筛分效率:(1)E1=β(α-θ)/α(β-θ)*100%(2)E2=C/(θ*α)*100%式中:α、β、θ分别为给矿、筛下、筛上产物中小于筛孔尺寸粒级的百分含量,C为筛下产品重量8、破碎机作业率:作=t实/t计*100%式中:t实为破碎机实际开车小时数t计为日历台数X台数X24小时(计开车小时数)9、球磨机作业率:计算方法同破碎机作业率10、球磨机台数能力:Q台=Q总/t实(t/H)式中:Q台为球磨机1小时处理原矿吨数Q总为球磨机当班(或日、月、季、年等)处理原矿总吨数11、球磨机利用系数:3)系=Q台/V(t/H·m式中:系为球磨机单位体积单位时间内处理的原矿量V为球磨机有效容积(m3)12、磨矿效率:q-200=Q台(γ溢-γ给)/V(t/H·m3)式中:q-200为磨机单位时间单位容积磨出指定粒级的矿山重量γ溢为溢流中指定粒级含量的百分数γ给为给矿中指定粒级含量的百分数13、按电耗计算磨矿效率:C=q·V/N(t/瓦·时)式中:C为按电耗计算得磨矿效率q为磨机单位时间单位容积的-200的含量N为单位时间磨机耗电量(度)14、球磨机转数:(1)临界转数n临=42.2/√D(转/分)(2)实际转数n实=32.2/√D-2b(转/分)(3)工作转数2=同/S(转/分)式中:D为球磨直径b为球磨衬板厚度同为同步机转数S为球磨机大、小齿轮之比(转数)15、装球量公式:G=φ·V·△式中:G为装球量(吨)φ为充填系数百分数(取40-45%)△为钢球堆比重(取△=4.85t/m3)16、装球直径(拉祖莫夫公式)D=f3√d式中:D为钢球直径(mm)f为矿石性质(硬度)系数(f在28-38-48)d为给矿最大直径(mm)17、介质球充填率:φ=50-127*b/D(%)式中:φ为钢(铁)球充填率(%)b为介质水平面距磨机筒体中心线高度(m)D为磨机有效直径(m)18、钢球重量:W=7.8*(π/6)D3式中:W为单个钢球重量(g或kg)D为钢球直径(mm)19、分级效率:E=(α-θ)(β-α)/α(β·θ)(1-α)*100%式中:E为分级效率α为给矿中小于分级粒度含量(%)β为溢流中小于分级粒度含量(%)θ为沉砂中小于分级粒度含量(%)20、细筛筛分效率:计算公式同分级效率21、分级返砂循环负荷:C=(β-α)/(α-θ)*100%22、返砂比:C=S/Q(%)式中:C为返砂比S为返砂量(吨)Q为新给矿量(吨)23、细筛分离粒度经验公式:(1)d=1/2·S·K式中:d为细筛分离粒度(mm)S为筛孔尺寸(mm)K为系数(在0.75~1.25)(2)查表法S·d及倾角24、过滤效率:q精=Q总/∑m2·∑t(t/H·m3)式中:Q总为各台过滤机过滤干精矿之和(吨)∑m2为参加生产过滤机有效面积之和(m2)∑t为各台过滤机实际过滤时间之和(小时)25、回收率的计算:(1)实际回收率ε=(Q k*β)/(Q0*α)*100%(2)理论回收率ε=β(α-θ)/α(β-θ)*100%式中:Q k为精矿产量,Q0为尾矿产量磁选机磁场感应强度表示:1T(特斯拉)=1000mT(毫特斯拉)=10000GS(高斯)。
选矿回收率的计算公式
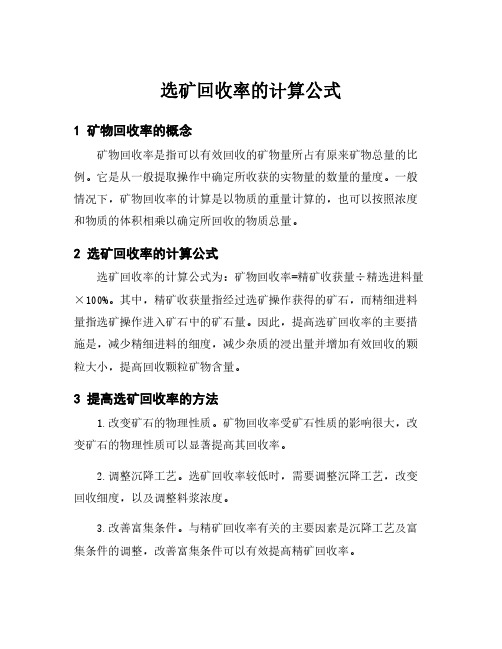
选矿回收率的计算公式
1矿物回收率的概念
矿物回收率是指可以有效回收的矿物量所占有原来矿物总量的比例。
它是从一般提取操作中确定所收获的实物量的数量的量度。
一般情况下,矿物回收率的计算是以物质的重量计算的,也可以按照浓度和物质的体积相乘以确定所回收的物质总量。
2选矿回收率的计算公式
选矿回收率的计算公式为:矿物回收率=精矿收获量÷精选进料量×100%。
其中,精矿收获量指经过选矿操作获得的矿石,而精细进料量指选矿操作进入矿石中的矿石量。
因此,提高选矿回收率的主要措施是,减少精细进料的细度,减少杂质的浸出量并增加有效回收的颗粒大小,提高回收颗粒矿物含量。
3提高选矿回收率的方法
1.改变矿石的物理性质。
矿物回收率受矿石性质的影响很大,改变矿石的物理性质可以显著提高其回收率。
2.调整沉降工艺。
选矿回收率较低时,需要调整沉降工艺,改变回收细度,以及调整料浆浓度。
3.改善富集条件。
与精矿回收率有关的主要因素是沉降工艺及富集条件的调整,改善富集条件可以有效提高精矿回收率。
4.创新矿物质提纯技术。
合理利用加速器质谱技术保证了矿物质的提纯,有利于提高精矿回收率。
4结论
矿物回收率是衡量选矿工艺效果的主要标志,提高矿物回收率是提高经济效益的关键。
调整沉降工艺、改善富集条件、改变矿石的物理性质以及合理利用加速器质谱技术等技术手段可以有效提高矿物回收率,从而节省材料开支、降低生产成本,提高经济效益。
铅锌选矿厂两种精矿产品回收率计算
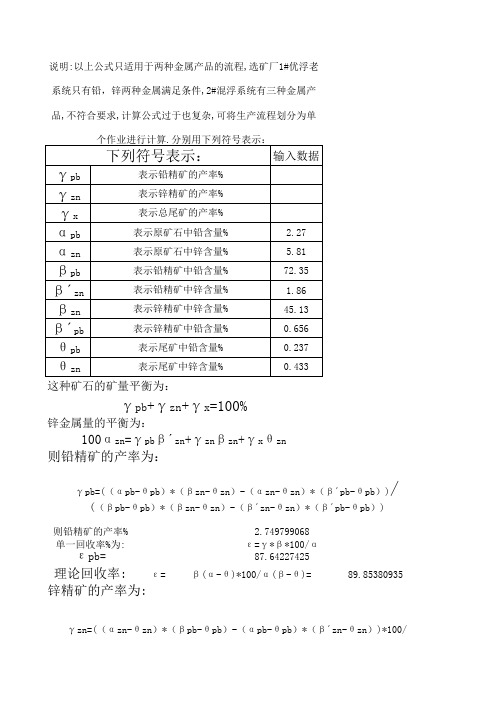
下列符号表示: γ pb γ zn γ x α pb α zn β pb β ´zn β zn β ´pb θ pb θ zn γ
则铅精矿的产率%为: 单一回收率%为: 2.749799068 ε =γ *β *100/α 87.64227425 = β (α -θ )*100/α (β -θ )= 89.85380935
ε pb= 理论回收率: ε 锌精矿的产率为:
γ zn=((α zn-θ zn)*(β pb-θ pb)-(α pb-θ pb)*(β ´zn-θ zn))*100/ ((β zn-θ zn)*(β pb-θ pb)-(β ´zn-θ zn)*(β ´pb-θ pb))
这种矿石的矿量平衡为: pb+γ zn+γ x=100% 锌金属量的平衡为:
100α zn=γ pbβ ´zn+γ 则铅精矿的产率为:
znβ zn+γ xθ zn
γ pb=((α pb-θ pb)*(β zn-θ zn)-(α zn-θ zn)*(β ´pb-θ pb))
/
((β pb-θ pb)*(β zn-θ zn)-(β ´zn-θ zn)*(β ´pb-θ pb))
γ zn=((α zn-θ zn)*(β pb-θ pb)-(α pb-θ pb)*(β ´zn-θ zn))*100/ ((β zn-θ zn)*(β pb-θ pb)-(β ´zn-θ zn)*(β ´pb-θ pb))
则锌精矿的产率为: 单一回收率%为:
选矿效率
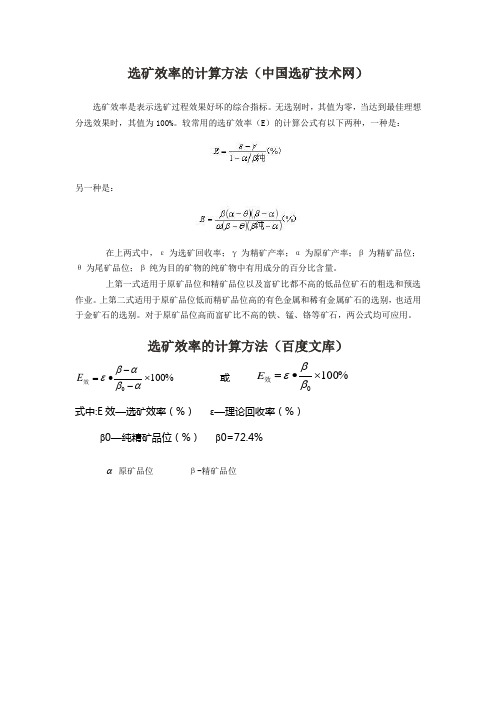
%1000
⨯∙=ββε效E 选矿效率的计算方法(中国选矿技术网)
选矿效率是表示选矿过程效果好坏的综合指标。
无选别时,其值为零,当达到最佳理想分选效果时,其值为100%。
较常用的选矿效率(E )的计算公式有以下两种,一种是:
另一种是:
在上两式中,ε为选矿回收率;γ为精矿产率;α为原矿产率;β为精矿品位;θ为尾矿品位;β纯为目的矿物的纯矿物中有用成分的百分比含量。
上第一式适用于原矿品位和精矿品位以及富矿比都不高的低品位矿石的粗选和预选作业。
上第二式适用于原矿品位低而精矿品位高的有色金属和稀有金属矿石的选别,也适用于金矿石的选别。
对于原矿品位高而富矿比不高的铁、锰、铬等矿石,两公式均可应用。
选矿效率的计算方法(百度文库)
%1000⨯--∙=αβαβε效E 或 式中:E 效—选矿效率(%) ε—理论回收率(%)
β0—纯精矿品位(%) β0=72.4%
α-原矿品位 β-精矿品位。
浮选精矿的回收率算法

浮选精矿的回收率是指经过浮选处理后,精矿中目标元素含量的百分比。
回收率通常受到浮选工艺、药剂制度、浮选条件等因素的影响。
为了提高浮选精矿的回收率,需要综合考虑这些因素并采取相应的措施。
浮选精矿的回收率可以通过以下算法进行计算:假设目标元素在浮选精矿中的含量为B,经过浮选处理后,实际回收量为R,则回收率Rc 可按以下公式计算:Rc = (B - R) / B ×100%其中,B为原始精矿中目标元素含量,R为实际回收量。
为了提高浮选精矿的回收率,可以从以下几个方面着手:1. 优化浮选工艺:根据矿石性质和目标元素含量,选择合适的浮选工艺和药剂制度。
例如,可以采用选择性捕收剂来提高目标元素的回收率。
2. 调整浮选条件:根据矿石性质和目标元素溶解度,控制浮选过程的温度、pH值、搅拌时间等条件,以提高目标元素的回收率。
3. 改进浮选设备:采用高效、可靠的浮选设备,减少浮选过程中的损失和浪费。
4. 精细操作:在浮选过程中,加强操作管理,确保浮选过程的稳定性和可靠性,避免因操作不当导致目标元素损失。
5. 综合利用:在提高回收率的同时,还应考虑资源的综合利用和环境保护。
例如,可以通过回收尾矿中的有用元素,实现资源的循环利用。
总之,提高浮选精矿的回收率需要综合考虑工艺、设备、药剂、条件等多个方面。
在实际生产中,应根据矿石性质和目标元素含量,制定合理的工艺流程和操作规程,并加强过程控制和管理,以确保浮选精矿的回收率达到最佳水平。
此外,随着科技的发展,新型的浮选技术和设备不断涌现,为提高浮选精矿的回收率提供了更多的可能性。
未来,通过不断探索和创新,有望实现更高水平的资源利用和环境保护,为推动绿色矿业发展做出更大的贡献。
选矿厂浮选回收率计算方法

立志当早,存高远
选矿厂浮选回收率计算方法
只有一种产品时计算方法: 回收率=(原矿品位-尾矿品位)X 精矿品位/(精矿品位-尾矿品位)X 原矿品位产率X 精矿品位/原矿品位=回收率两种产品时(以锌铅为例)计算方法:产率计算分母(锌含锌-锌尾)乘以(铅含铅-铅尾)-(铅含锌-锌尾)乘以(锌含铅-铅尾)锌产率分子(锌原矿-锌尾)乘以(铅含铅-铅尾)-(铅含锌-锌尾)乘以(铅原矿-
铅尾)锌产率=锌产率分子/产率计算分母回收率=锌产率X 锌精品位/锌原矿品位以下类同铅产率分子(锌含锌-锌尾)乘以(铅原矿-铅尾)-(锌原矿-锌尾)乘以(锌含铅-铅尾)三种产品时(以锌铅硫为例)计算方法:计算因数锌(A0-A3)铅(B0-B3)硫(C0-C3)
A0 锌原矿-锌尾B0 铅原矿-铅尾C0 硫原矿-硫尾
A1 锌含锌-锌尾B1 锌含铅-铅尾C1 锌含硫-硫尾
A2 铅含锌-锌尾B2 铅含铅-铅尾C2 铅含硫-硫尾
A3 硫含锌-锌尾B3 硫含铅-铅尾C3 硫含硫-硫尾计算产率分母=(A1B2C3+A2B3C1+A3B1C2)-(A1B3C2+A2B1C3+A3B2C1)锌产率分子=(A0B2C3+A2B3C0+A3B0C2)-(A0B3C2+A2B0C3+A3B2C0)铅产率分子=(A1B0C3+A0B3C1+A3B1C0)-(A1B3C0+A0B1C3+A3B0C1)。
选矿回收率与金属平衡表

立志当早,存高远
选矿回收率与金属平衡表
选矿回收率:指精矿中的金属(有用组分)的数量与原矿中金属(有用组分)的数量的百分比。
这是一项重要的选矿指标,它反映了选矿过程中金属的回收程度,选矿技术水平以及选矿工作质量。
选矿过程要在保证精矿品位的前提下,尽量地提高选矿回收率。
其计算方法如下:如某硫化铜矿原矿中铜品位为
0.9%,精矿中铜品位为18.0%,如果每昼夜处理原矿石重量为400t,得精矿重量为15t,实际回收率为乘以100%=75%。
原矿品位α、精矿品位β和尾矿品位θ (单位:%)
选矿技术监督部门一般通过实际回收率的计算,编制实际金属平衡表。
通过理论回收率的计算,编制理论金属平衡表。
两者进行对比分析,能够揭露出选矿过程机械损失,查明选矿工作中的不正常情况及在取样、计量、分析与测量中的误差。
通常理论回收率都高于实际回收率,但两者不能相差太大,在单一金属浮选厂一般流失不允许相差1%。
如果超过了该数字,说明选矿过程中金属流失严重。
入厂原矿中金属含量和出厂精矿与尾矿中的金属含量之间有一个平衡关系,若以表格形式列出即称之为金属平衡表。
Q--原矿量/吨
α--原矿品位/%
θ--尾矿品位/%
β精矿品位/%
K--精矿的重量/吨
V--尾矿的金属品位/%
Ss--损失部分的重量/吨
θs--损失部分的金属品位/%。
选矿厂浮选回收率计算方法
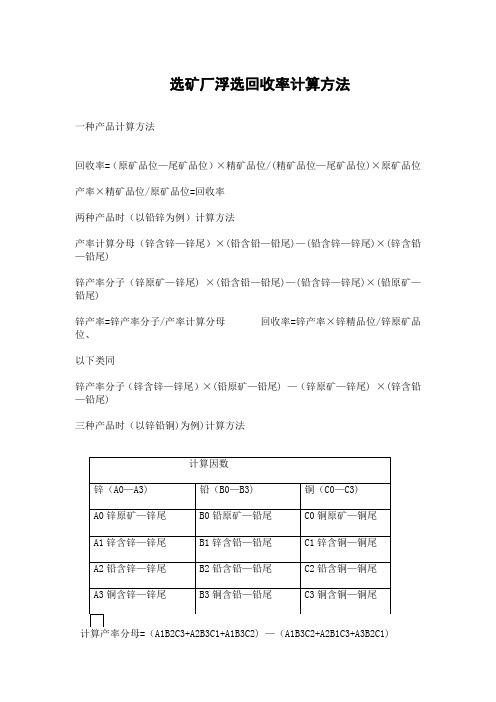
选矿厂浮选回收率计算方法
一种产品计算方法
回收率=(原矿品位—尾矿品位)×精矿品位/(精矿品位—尾矿品位)×原矿品位
产率×精矿品位/原矿品位=回收率
两种产品时(以铅锌为例)计算方法
产率计算分母(锌含锌—锌尾)×(铅含铅—铅尾)—(铅含锌—锌尾)×(锌含铅—铅尾)
锌产率分子(锌原矿—锌尾) ×(铅含铅—铅尾)—(铅含锌—锌尾)×(铅原矿—铅尾)
锌产率=锌产率分子/产率计算分母回收率=锌产率×锌精品位/锌原矿品位、
以下类同
锌产率分子(锌含锌—锌尾)×(铅原矿—铅尾) —(锌原矿—锌尾) ×(锌含铅—铅尾)
三种产品时(以锌铅铜)为例)计算方法
锌产率分子=(A0B2C3+A2B3C0+A3B0C2) —(A0B3C2+A2B0C3+A3B2C0) 铅产率分子=(A1B0C3+A0B3C1+A3B1C0) —(A1B3C0+A0B1C3+A3B0C1) 铜产率分子=(A1B2C0+A2B0C1+A0B1C2) —(A1B0C2+A2B1C0+A0B2C1)。
矿石回收率
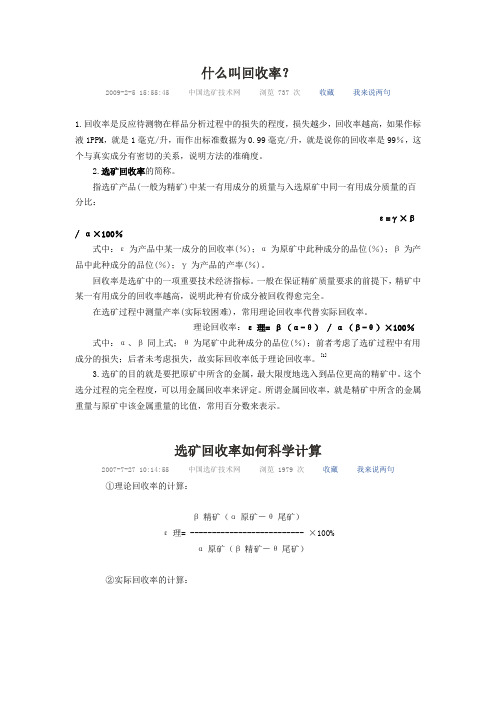
什么叫回收率?2009-2-5 15:55:45 中国选矿技术网浏览737 次收藏我来说两句1.回收率是反应待测物在样品分析过程中的损失的程度,损失越少,回收率越高,如果作标液1PPM,就是1毫克/升,而作出标准数据为0.99毫克/升,就是说你的回收率是99%,这个与真实成分有密切的关系,说明方法的准确度。
2.选矿回收率的简称。
指选矿产品(一般为精矿)中某一有用成分的质量与入选原矿中同一有用成分质量的百分比:ε=γ×β / α×100%式中:ε为产品中某一成分的回收率(%);α为原矿中此种成分的品位(%);β为产品中此种成分的品位(%);γ为产品的产率(%)。
回收率是选矿中的一项重要技术经济指标。
一般在保证精矿质量要求的前提下,精矿中某一有用成分的回收率越高,说明此种有价成分被回收得愈完全。
在选矿过程中测量产率(实际较困难),常用理论回收率代替实际回收率。
理论回收率:ε理= β(α-θ) / α(β-θ)×100%式中:α、β同上式;θ为尾矿中此种成分的品位(%);前者考虑了选矿过程中有用成分的损失;后者未考虑损失,故实际回收率低于理论回收率。
[1]3.选矿的目的就是要把原矿中所含的金属,最大限度地选入到品位更高的精矿中。
这个选分过程的完全程度,可以用金属回收率来评定。
所谓金属回收率,就是精矿中所含的金属重量与原矿中该金属重量的比值,常用百分数来表示。
选矿回收率如何科学计算2007-7-27 10:14:55 中国选矿技术网浏览1979 次收藏我来说两句①理论回收率的计算:β精矿(α原矿-θ尾矿)ε理= -------------------------- ×100%α原矿(β精矿-θ尾矿)②实际回收率的计算:精矿的金属量 K βε = -------------- = -------- ×100%原矿的金属量 Q α式中: K ——精矿重量吨β——精矿品位 %Q——原矿量吨α——原矿品位 %损失部分包括:浮选机的跑槽及出现故障时的溢出物、浓缩机的溢流“跑浑”、皮带机的掉矿、球磨给矿处的漏矿、精矿运输车辆漏矿等等。
采矿回采率计算公式
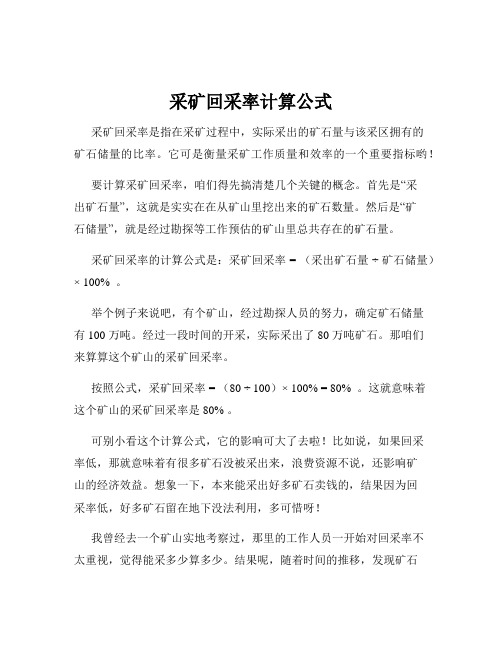
采矿回采率计算公式采矿回采率是指在采矿过程中,实际采出的矿石量与该采区拥有的矿石储量的比率。
它可是衡量采矿工作质量和效率的一个重要指标哟!要计算采矿回采率,咱们得先搞清楚几个关键的概念。
首先是“采出矿石量”,这就是实实在在从矿山里挖出来的矿石数量。
然后是“矿石储量”,就是经过勘探等工作预估的矿山里总共存在的矿石量。
采矿回采率的计算公式是:采矿回采率 = (采出矿石量 ÷矿石储量)× 100% 。
举个例子来说吧,有个矿山,经过勘探人员的努力,确定矿石储量有 100 万吨。
经过一段时间的开采,实际采出了 80 万吨矿石。
那咱们来算算这个矿山的采矿回采率。
按照公式,采矿回采率 = (80 ÷ 100)× 100% = 80% 。
这就意味着这个矿山的采矿回采率是 80% 。
可别小看这个计算公式,它的影响可大了去啦!比如说,如果回采率低,那就意味着有很多矿石没被采出来,浪费资源不说,还影响矿山的经济效益。
想象一下,本来能采出好多矿石卖钱的,结果因为回采率低,好多矿石留在地下没法利用,多可惜呀!我曾经去一个矿山实地考察过,那里的工作人员一开始对回采率不太重视,觉得能采多少算多少。
结果呢,随着时间的推移,发现矿石的开采越来越困难,成本越来越高。
因为前期开采的时候不注重技术和方法,导致很多容易开采的矿石采完了,剩下的都是难啃的“硬骨头”,回采率也一直上不去。
后来他们痛定思痛,引进了新的技术和设备,加强了管理,重新对矿山进行规划,一点点地把回采率给提了上来。
这过程可不容易,要对每一个开采环节进行仔细的分析和改进,从爆破方式到运输路线,都得精心设计。
在实际的采矿工作中,要提高采矿回采率,那可得下一番功夫。
比如说,采用更先进的采矿方法,像什么充填采矿法、崩落采矿法等等,这些方法都有各自的特点和适用范围,得根据矿山的具体情况来选择。
还有就是要加强地质勘探工作,把矿石储量摸得更清楚,这样才能更有针对性地进行开采。
- 1、下载文档前请自行甄别文档内容的完整性,平台不提供额外的编辑、内容补充、找答案等附加服务。
- 2、"仅部分预览"的文档,不可在线预览部分如存在完整性等问题,可反馈申请退款(可完整预览的文档不适用该条件!)。
- 3、如文档侵犯您的权益,请联系客服反馈,我们会尽快为您处理(人工客服工作时间:9:00-18:30)。
选矿回收率怎么计算添加时间:2010-04-11一、名词解释重力选矿法(简称重选法):是在运动介质(水)中,按粒度比重和粒度的差异进行分选的分法。
浮选法:是选金生产中,应用最广泛的一种选矿法。
是利用矿物表面物理化学性质的差异来选分矿石的一种方法。
混汞法:是一种古老而又简易的选金方法。
在矿浆中,金粒被汞(水银)选择性地润湿并形成金汞齐,使它和别的矿物及脉石互相分离,这种方法称为混汞法。
品位:就是矿石或选矿产物中该金属或选矿产物重量之比值,通常用百分数来表示。
产率:选矿产物的重量与原矿重量之比值,通常用百分数来表示。
选矿比:原矿重量与精矿重量的比值,它表示获得1吨精矿需要处理的原矿的吨位。
富矿比:精矿中有用成分的品位和原矿中有用成分的品位之比值。
它表示精矿中有用成分的品位和原矿中有用成分的品位高出的倍数。
回收率:选矿的目的就是要把原矿中所含的金属,最大限度地选入到品位更高的精矿中。
这个选分过程的完全程度,可以用金属回收率来评定。
所谓金属回收率,就是精矿中所含的金属重量与原矿中该金属重量的比值,常用百分数来表示。
二、选矿指标处理原矿品位(克/吨)=处理原矿含金量(克) / 处理原矿量(吨)精矿品位:是指平均每吨精矿中的含金量,它是反映精矿质量的指标,计算公式为:精矿品位(克/吨)=精矿含金量(克) / 精矿数量(吨)精矿产率:是指产出的精矿量占原矿量的百分比,它是反映选矿厂质量的指标。
计算公式为:精矿产率(%)=精矿数量(吨) /原矿数量(吨) ×100%尾矿品位:是指选矿厂排弃的尾矿中,平均每吨尾矿中的含金量。
它是反映在选矿过程中金属损失程度的指标。
计算公式为:尾矿品位(克/吨)=尾矿含金量(克)/尾矿数量(吨)尾矿量(吨)=处理原矿量(吨)-精矿量(吨)选矿回收率:是指采用各种选矿方法获得的最终产品含金量占处理原矿含金量的百分比。
按理论和实际回收率两种方法计算。
选矿理论回收率(%)=精矿品位×(原矿品位-尾矿品位)/(原矿品位×(精矿品位-尾矿品位) ×100%=理论回收的金属量(克) /处理原矿金属量(克)×100%选矿实际回收率(%)=金精矿含金量(克)/原矿含金量(克)×100%(浮选回收率)浸出率:是指经浸出作业已溶解金的金属量占氰原矿金属量的百分比。
计算公式为:浸出率=已溶解金的金属量(克)/氰原矿金属量(克)×100%=( 氰原矿金属量(克)-浸渣金属量(克) )/氰原矿金属量(克)×100%洗涤率:是指贵液中含金量占浸出溶解金的金属量的百分比。
计算公式为:洗涤率(%)= 贵液含金量(克) / 浸出已溶金的金属量(克)×100%=( 氰原矿金属量(克)-浸渣金属量(克) -排液金属量(克))/( 氰原矿金属量(克)-浸渣金属量(克) )×100%置换率:是指通过置换沉淀而析出的金泥含金量占贵液含金量的百分比。
计算公式为:置换率(%)=金泥含金量(克) /贵液含金量(克)×100%氰化回收率:是指氰化金泥含金量占氰原矿含金量的百分比。
计算公式为:氰化回收率(%)=金泥含金量(克)/氰原矿含金量(克)×100%=浸出率(%)×洗涤率(%)×置换率(%)氰化金泥冶炼回收率:是指冶炼后合质金含量占氰化金泥量的百分比。
计算公式为:冶炼回收率=合质金含金量(克)/金泥含金量(克)×100%氰化选冶回收率:是指氰化厂最终产品合质金含金量占氰原含金量的百分比。
计算公式为:氰化冶炼回收率=合质金含金量(克)/氰原含金量(克)×100%=氰化回收率(%)×金泥冶炼回收率(%) =浸出率(%)×洗涤率(%)×置换率(%)×金泥冶炼回收率选冶总回收率:是指选冶车间加工处理产出的各种最终合格产品的金属量总和与原矿金属量之百分比。
计算公式为:选冶厂回收率(%)=各种最终产品金属量之和(克)/原矿金属量(克)×100%选矿比:是指处理原矿量与选出精矿量的比例,即每选出一吨金精矿所需要原矿石吨数,以倍数表示:选矿比(倍)=原矿处理量(吨)/精矿量(吨)磨矿机利用系数:是指磨矿机每立方米有效容积在单位时间(小时)内所处理的新增合格粒度矿量。
计算公式为:磨矿机利用系数(吨/立方米.台时)=最终新增合格粒度产出率(%)×原矿处理量(吨) / (各台磨矿机容积(立方米)×作业小时数之和)磨矿机作业率:是指磨矿机实际作业时间占日历时间的百分比,计算公式为:磨矿机作业率(%)=各磨矿机实际作业台时数之和/磨矿机日历作业台时数之和×100%平均日处理量:平均日处理量是指平均每个选矿工作日所处理的原矿量。
计算公式为:平均日处理量(吨/日)=原矿处理量(吨)/ 选厂作业天数(日)选厂作业天数应以磨矿机是否开动来确定,只要开动就算一天,而不论当天开动时间的多少。
选矿车间全员实物劳动生产率:是指矿山选矿全部职工在报告期内,平均每人所完成的原矿处理量。
计算公式为:选矿车间全员实物劳动生产率(吨/人)=原矿处理量(吨)/ 选冶车间全部职工平均人数(人)选矿车间工人实物劳动生产率:是指选矿厂平均每个工人在报告期内所完成的原矿处理量。
计算公式为:选矿车间工人实物劳动生产率(吨/人)=原矿处理量(吨)/ 选矿车间工人平均人数(人)选氰物料消耗:是指在选矿、氰化过程中每处理一吨原矿石或金精矿所消耗的主要物料数量。
计算公式为:物料单耗(消耗量单位/吨)=某种物料耗用总量(消耗单位)/ 原矿处理量(吨) 或=某种物料耗用总量(消耗单位) /金精矿量选矿回收率是指精矿中的金属或有用组分的数量与原矿中金属的数量的百分比。
这是一项重要的选矿指标,它反映了选矿过程中金属的回收程度,选矿技术水平以及选矿工作质量。
选矿过程要在保证精矿品位的前提下,尽量提高选矿回收率。
其计算方法如下:实际回收率实际的精矿数量(吨)×精矿品位= ×100% (1-2)原矿处理量(吨)×原矿品位β (α ?Cθ)理论回收率= --×100% (1-3)α (β -θ)在选厂生产过程中,每个生产班都需要取样化验原矿品位(α)、精矿品位(β)和尾矿品位(θ)。
这时理论回收率可由公式(1-3)计算得出结果。
上述例1的铜精矿理论回收率为:β(α -θ)铜精矿理论回收率ε K = --×100%α(β-θ)22. 18×(1.23-0.04)= ×100%1.23×(22.18-0.04)= 96.92%选矿技术监督部门一般通过实际回收率的计算,编制实际金属平衡表。
通过理论回收率的计算,编制理论金属平衡表。
两者进行对比分析,能够揭露出选矿过程机构损失,查明选矿工作中的不正常情况以及在取样、计量、分析与测量中的误差。
通常理论回收率都高于实际回收率,但两者不能相差太大,在单一金属浮选厂一般不允许相差1%。
如果超过了该数字,说明选矿过程中金属流失严重。
理论金属平衡(也称工艺金属平衡)表是根据在平衡的期间内的原矿石和最终选矿产品(精矿与尾矿)所化验得到的品位算出的精矿产率和金属回收率,因未考虑过程中的损失,所以此回收率称为理论回收率,此金属平衡表称为理论金属平衡表。
它可以反映出选矿过程技术指标的高低。
一般按班、日、旬、月、季和年来编制。
可作为选矿工艺过程的业务评价与分析资料,并能够根据在平衡表期间内的工作指标,对个别车间、工段和班的工作情况进行比较。
实际金属平衡(也称商品金属平衡)表。
是根据在平衡表期间内所处理矿石的实际数量、精矿的实际数量(如出厂数量及留在矿仓、浓密机和各种设备中的数量)以及精矿化验品位算出的精矿产率和金属回收率,所以此回收率称之为实际金属回收率,此金属平衡表称之为实际金属平衡表。
它反映了选矿厂实际工作的效果。
一般实际金属平衡表按月、季、半年或一年编制选矿过程中金属流失集中反映在实际回收率理论回收率的差值上。
由于理论平衡表的金属回收率一般都高于实际平衡表的金属回收率,但有时也会出现反常现象,实际回收率高于理论回收率,这主要是因为取样的误差、原矿与选矿产品的化学分析及水分含量的测定的误差,以及原矿与选矿产品计量的误差等所造成的。
一般要求理论金属平衡表的回收率和实际金属平衡表的回收率之间的差值,对于浮选厂正差不能大于2%,不应出现负差。
选矿技术监督部门一般通过实际回收率的计算,编制实际金属平衡表。
通过理论回收率的计算,编制理论金属平衡表。
两者进行对比分析,能够揭露出选矿过程机构损失,查明选矿工作中的不正常情况以及在取样、计量、分析与测量中的误差。
通常理论回收率都高于实际回收率,但两者不能相差太大,在单一金属浮选厂一般不允许相差1%。
如果超过了该数字,说明选矿过程中金属流失严重。
金属平衡的作用:入厂原矿中金属含量和出厂精矿与尾矿中的金属含量之间有一个平衡关系,若以表格形式列出即称之为金属平衡表。
金属平衡表是选矿生产报表。
金属平衡表分为理论金属平衡(也称工艺金属平衡)表和实际金属平衡(也称商品金属平衡)表两种。
它可以反映出选矿过程技术指标的高低。
金属平衡是通过各种计量检测手段,查明金属去向,找出生产薄弱环节,以及分析各种误差对金属平衡的影响,同时,金属平衡工作是选矿厂全面质量管理的基础,是衡量选矿生产、技术、经营管理的重要标志,可作为选矿工艺过程的业务评价与分析资料,并能够根据在平衡表期间内的工作指标,对个别车间、工段和班的工作情况进行比较。
比较理论金属平衡表和实际金属平衡表,能够揭露出生产过程中金属流失的情况。
差值愈大、说明选厂在技术管理与生产管理方面存在的问题愈多。
这就要查明生产过程的不正常情况,以及取样、计量与各种分析和测量上的误差,并及时予以解决。
3、理论平衡的编制实际金属平衡的编制实际金属平衡是通过各种计量检测手段,考察原矿金属与精矿、尾矿金属之间的平衡关系,查明金属去向,找出生产薄弱环节,以及分析各种误差对金属平衡的影响,同时,金属平衡工作是选矿厂全面质量管理的基础,是衡量选矿生产、技术、经营管理的重要标志,因此,实际金属平衡应反映选矿厂及其工段在规定时间内,即班、日、月、季、年的工作情况。
一般金属平衡指标用理论回收率与实际回收率之差值表示。
金属平衡表的内容应包括:(1)原矿及各种产品的数量、品位及金属量;(2)理论回收率与实际回收率;(3)各种金属平衡的差值。
A= ? Pb—θPb B= ?Zn—θZnC=βPb—θPb D=β’Zn—θZnE=β’ Pb—θPb F=βZn—θZn即可得出下式:AF-BEγPb=×100%CF-DE选矿比:是指处理原矿量与选出精矿量的比例,即每选出一吨金精矿所需要原矿石吨数,以倍数表示:选矿比(倍)=原矿处理量(吨)/精矿量(吨)磨矿机利用系数:是指磨矿机每立方米有效容积在单位时间(小时)内所处理的新增合格粒度矿量。