典型工艺规程目录QLB17
生产工艺和操作规程

生产工艺和操作规程生产车间岗位职责建湖子木实业有限公司魔芋小结生产操作规程序言:根据Q/JHCG0001S-2010制定以下操作规程。
一、个人生产前清洁卫生1.所有员工必须穿着统一工作服、工作鞋,戴工作帽,换衣后内衣不得外露,裤脚必须塞在工作鞋里,头发和耳朵不得露在帽子外面。
2.进入生产区域不得佩戴首饰,不得留有长指甲,每周检查一次。
3.洗手消毒:清水洗→洗手液→清水冲洗→消毒液浸泡30秒→烘干4.用滚轮除去身上灰尘和毛发。
二、生产前设备检查、工具清洗消毒1.生产前对设备进行检查,排除故障和安全隐患。
2.生产前工器具清洗后用消毒液消毒。
3.设备清洗后100℃蒸汽消毒。
4.预先配好定型流槽的专用水。
5.定型流水槽放水前清洗,检查槽壁。
6.检查管道口是否清洁,放掉管道内的剩水,待清洁水色正常后方可放水。
三、配制工艺用水和生产用水1.配制定型流槽用水:1700升清水,加入1.1千克食用氢氧化钙,完全溶解。
pH值: 11.0-11.7。
2.配制养护水:按照6.5-7.0‱比例,在清水内加入食用氢氧化钙,完全溶解。
pH值: 11.5-11.8。
3.配制塑封水:按照6.0-6.5‱比例,在清水内加入食用氢氧化钙,完全溶解。
pH值: 11.6-12.04.各种工艺用水和生产用水调节pH值,用清水或食用氢氧化钙。
5.质检人员全程监督配制过程,并且将检测和调整数据记录在案。
四、备料1.质检部门对每一批次原料都应该进行仔细检查,检查内容包括:产地、包装、数量、清洁度、白洁度和统一性。
2.质检部门对每一批次原料都应该事先做小样试验,计算好膨胀倍率,将结果填写在备用原料单(货卡)上。
3.质检部门对每一批次食用氢氧化钙以及辅料进行严格检查和测试。
4.生产时操作工应该按照领料单说明,向仓库领取指定批号的原料及辅料。
5.领取指定批号的原料及辅料时,应该做到两人复核。
五、投料1.向清洗好的搅拌桶内注入清水,至750升时质检员取第一次水样。
典型工艺规程(10月30日)
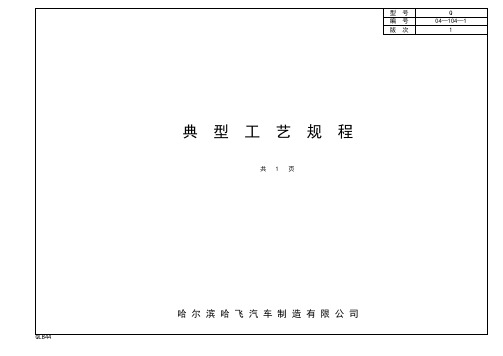
胶条与工作室内底板间应留有一定空隙,避免接触损坏胶条。
3.3
XST数显调节仪由主管工艺操作,其它任何人不得使用。
3.4
操作人员应经常清理箱内杂物,保持箱内清洁。
3.5
除加热胶条外,本设备严禁它用。
工艺
指导工艺
校对
审核
更改标记
修改单号
修改的简要内容
签字
日期
检验
QLB45
型号
Q
编号
04—104—2
止按钮,停止加油并必须立即把转换开关放到自动位置。
5.3
因A、B两线的加注机共用一个油泵,故南北线任意一加注机切换至手动位置时另一加注机即失去自动功能;同时由于两线加注机油箱的相互保护是由电磁阀
实现的,因此当手动操作完成后必须立即把转换开关切换至自动位置关闭电磁阀,以免另一加注机加油时也对本加注机进行加油。
将MRC/ XRC电源旋至ON。
3.3
打开供给机器人的压缩空气开关,并检查气压是否正常(气源压力应为0.45MPa)。
3.4
在主操作盘上,按下“MRC电源开”按钮。
3.5
按“MRC /XRC遥控按钮,灯亮。
3.6
按“MRC伺服ON”按钮/按“XRC再现”按钮,灯亮。
3.7
按“调用主程序”按钮两次,灯亮(对XRC控制柜)。
5.4
因南北线每组加注机油泵控制电源均由南线供给,因此当南线加注机出现故障或停产时,应把转换开关切换至空位上,不能关掉加注机总电源。
5.5
当“油液补充中”灯已亮,而液位显示计中的液面并未上升或还在下限位时,操作者应马上按下急停钮并通知维修站及时处理。
更改标记
修改单号
修改依据
签字
GB国标压力容器取证-二级程序文件QP-17-2017 设计和开发控制程序
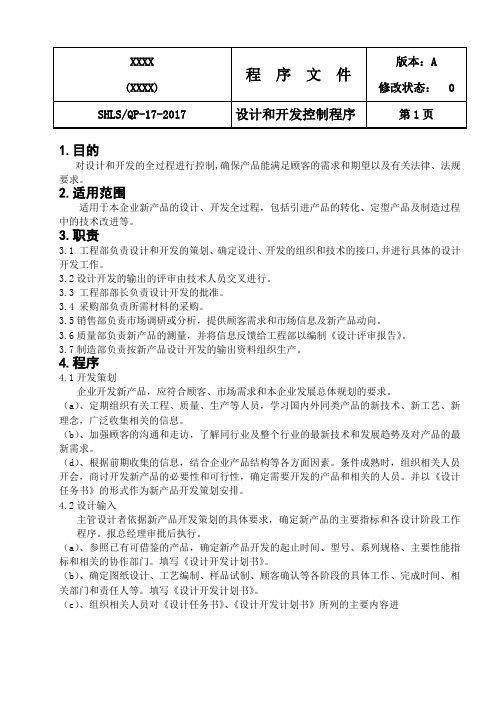
1.目的对设计和开发的全过程进行控制,确保产品能满足顾客的需求和期望以及有关法律、法规要求。
2.适用范围适用于本企业新产品的设计、开发全过程,包括引进产品的转化、定型产品及制造过程中的技术改进等。
3.职责3.1 工程部负责设计和开发的策划、确定设计、开发的组织和技术的接口,并进行具体的设计开发工作。
3.2设计开发的输出的评审由技术人员交叉进行。
3.3 工程部部长负责设计开发的批准。
3.4 采购部负责所需材料的采购。
3.5销售部负责市场调研或分析,提供顾客需求和市场信息及新产品动向。
3.6质量部负责新产品的测量,并将信息反馈给工程部以编制《设计评审报告》。
3.7制造部负责按新产品设计开发的输出资料组织生产。
4.程序4.1开发策划企业开发新产品,应符合顾客、市场需求和本企业发展总体规划的要求。
(a)、定期组织有关工程、质量、生产等人员,学习国内外同类产品的新技术、新工艺、新理念,广泛收集相关的信息。
(b)、加强顾客的沟通和走访,了解同行业及整个行业的最新技术和发展趋势及对产品的最新需求。
(d)、根据前期收集的信息,结合企业产品结构等各方面因素。
条件成熟时,组织相关人员开会,商讨开发新产品的必要性和可行性,确定需要开发的产品和相关的人员。
并以《设计任务书》的形式作为新产品开发策划安排。
4.2设计输入主管设计者依据新产品开发策划的具体要求,确定新产品的主要指标和各设计阶段工作程序。
报总经理审批后执行。
(a)、参照已有可借鉴的产品,确定新产品开发的起止时间、型号、系列规格、主要性能指标和相关的协作部门。
填写《设计开发计划书》。
(b)、确定图纸设计、工艺编制、样品试制、顾客确认等各阶段的具体工作、完成时间、相关部门和责任人等。
填写《设计开发计划书》。
(c)、组织相关人员对《设计任务书》、《设计开发计划书》所列的主要内容进行评审,确认其正确性、合理性、可行性等,必要时进行修改,并且建立《设计开发输入清单》,保证输入的完整性。
BL-17工序检验与试验控制程序(2013)

生效日期 2013.04.26文件名称 工序检验和试验控制程序 本页码 第1页 共3页 1.目的为使产品在生产过程中,有明确的检验、测试及质量状况标识以确保半成品及成品符合规定要求.2.范围适用于本公司生产的所有制程中工艺参数和产品的检查3.定义3.1首件(或首批)检查:指上班(或换班),调、试、修机,换型号(或换板),换材料,更改工艺或作业程序等后,对所生产的首件(或首批)产品进行的检验和试验。
3.2巡回检验:指生产过程中对生产产品设备机台、生产工艺、作业方法与标准及产品质量情况进行的检验与检查。
3.3逐批检验:指QC对逐批生产的产品实施规定的抽样检验。
3.4自检与互检:指生产加工人员对本工序生产的产品进行自检,下工序对上工序生产的产品进行互检。
4.职责4.1Q C主管4.1.1督导品管人员确实执行各项检验判定及标识工作.4.1.2重大质量问题的协商处理并推动相关部门改善.4.2生产主管4.2.1督导生产人员确实与品管配合执行检验及标识区分工作.4.2.2重大质量问题的协商处理及解决方案的落实.4.3线上品管4.3.1确实按品管检验规范及标签使用规范执行各项检验判定及标识工作.4.3.2发现异常时及时报告与协助处理.4.4生产作业员4.4.1按工序检查作业要求及标准对生产条件及机台、产品生产过程进行控制作业和检查。
4.4.2对生产异常及时发现和反馈,并协助按要求措施处理执行。
5.控制程序5.1.1首件检查具体参照详见《生产过程检验文件》、《生产工序首检流程规范》、《TP最终检验规范》.5.1.2巡检检查参照《生产过程检验文件》、《TP最终检验规范》.5.1.3逐批检查具体参照各相关工位检验指引.5.1.4工序间产品标识和产品质量状态标识生效日期 2013.04.26文件名称 工序检验和试验控制程序 本页码 第2 页 共3 页5.1.5工序间产品标识和产品质量状态标识按《产品标识和可追朔性程序》执行.检查不合格品的控制5.1.6工序间检查发现的不合格品依《不合格品控制程序》进行处理.5.2检验记录上述所有检验的检验结果在各工序相应窗体上予以记录,记录上须有相应权责人员的确认.5.3人员资格要求5.3.1实施工序间检查的检验人员和对检验记录进行确认的权责人员须具备已被认可的岗位技能和资格.5.3.2工序间检查除按上述相应的要求检查外,当客户有特殊要求时则按客户要求检验.6.相关记录6.1各工序首检控制表6.2品质异常报告单6.3工序检验记录台帐。
轴承座零件的机械加工工艺规程及工艺装备设计(钻13×17孔夹具设计)

课程设计任务书一、设计题目轴承座零件的机械加工工艺规程及工艺装备设计(钻13×17孔夹具设计)二、原始资料(1) 被加工零件的零件草图 1张(2) 生产类型: 50000件/年三、上交材料(1) 被加工工件的零件图 1张(2) 工件的毛坯图 1张(3) 机械加工工艺过程卡片 1张(4) 与所设计夹具对应那道工序的工序卡片 1张(5) 夹具装配图 1张(7) 课程设计说明书(7000-8000字) 1份说明书主要包括以下内容(章节)①目录②摘要(中外文对照的,各占一页)③零件工艺性分析④机械加工工艺规程设计⑤指定工序的专用机床夹具设计⑥方案综合评价与结论⑦体会与展望⑧参考文献列出参考文献(包括书、期刊、报告等,10条以上)课程设计说明书一律用A4纸、纵向打印.四、进度安排(参考)(1) 熟悉零件,画零件图 2天(2) 选择工艺方案,确定工艺路线,填写工艺过程综合卡片 5天(3) 工艺装备设计(画夹具装配图及夹具体图) 9天(4) 编写说明书 3天(5) 准备及答辩 2天五、指导教师评语成绩:指导教师日期成绩评定采用五级分制,即优秀、良好、中等、及格和不及格。
优秀:设计方案合理并新颖,设计说明书及设计图纸规范、内容丰富。
在设计过程中勤奋好学、有创新思想;良好:设计方案合理,设计说明书及设计图纸比较规范、内容比较丰富。
在设计过程中勤奋好学、有创新思想;中等:设计方案一般,设计说明书及设计图纸欠规范、内容一般。
在设计过程中比较勤奋、创新思想不明显;及格:设计方案不完善,存在一些小错误,说明书及设计图纸欠规范、内容一般。
在设计过程中勤奋精神不够:不及格:设计方案有严重错误,设计说明书及设计图纸不规范、内容浅薄。
在设计过程中勤奋好学精神不够。
摘要本次课程轴承座的加工工艺的规程,以及13×17孔工艺装备的设计,首先基本了解一下加工的零件,确定轴承座的生产类型,然后确定毛坯的种类和制造,然后拟定工艺路线,做出工艺卡片和工序卡片,加工余量和工序尺寸的确定和时间定额的确定,金属切削机床的选定,机床夹具的设计包括定位方案的设计和对刀及导向装置的设计,夹紧装置的设计,夹具体的设计,画出夹具装配图和夹具图确定过程。
【通用】通用工艺规程.doc

车用燃气气瓶安装通用工艺规程汇编版次:02修改码:0受发放编号:2013年1月1日发布2013年1月20日实施山东世界汽车有限公司汽车维修厂目录操作规程GYP02-01-2013 型材切割机操作规程GYP02-02-2013 汽车举升机操作规程GYP02-03-2013 真空泵操作规程GYP02-04-2013 水压试验机操作规程GYP02-05-2013 交流电焊机操作规程GYP02-06-2013 空气压缩机操作规程工艺规程GYP02-07-2013 ------------CNG或LPG汽车原车入厂检测规程GYP02-08-2013 ------------- CNG汽车专用装置加装技术规程GYP02-09-2013 ------------- LPG汽车专用装置加装技术规程GYP02-10-2013 ------------ CNG或LPG汽车气瓶支架强度试验规程GYP02-11-2013 ------------ CNG或LPG汽车氮气置换与气密性试验检验规程GYP02-12-2013 ------------ CNG或LPG汽车检验调试与出厂验收规程1.范围1.1本规程对型材切割机的使用规则作了规定,以确保人身安全。
1.2本规程适用于固定式或移动式型材切割机。
2.实施步骤2.1 使用场所要求2.1.1 设备的安装方位应使砂轮旋转方向尽量避开附近的工作人员,并应尽可能用防护屏等将型材切割机隔离。
2.1.2 设备的安装位置应有足够的供堆积加工最长工件的场地,并保证最长工件不伸入人行道。
2.1.3 型材切割机不宜安装在有腐蚀性气体的场所,不允许安装在有爆炸性粉尘的场所。
2.2 使用前的检查与调整2.2.1 供杠杆移动的导轨应平整、光滑、腰圆孔应完好。
2.2.2 夹紧装置应操作灵活,夹紧可靠,手轮、丝杠、螺母等应完好,螺杠的螺纹不得有滑丝,乱扣现象。
2.2.3 严禁在手轮或丝杆上,使用套管等加长动力臂来夹紧或松开被切割的工件。
波纹管生产工艺操作规程

波纹管生产工艺操作规程波纹管的性能试验2气密试验台操作规程3制管机操作规程4打波机操作规程5牵引式不锈钢波纹管光亮退火炉操作规程6液氨分解炉操作规程8网带回火炉工艺操作规程9挤塑机工艺操作规程 11气密试压工艺操作规程13空压机操作规格14台式钻床操作规程15冲床操作规程16挤塑机操作规程17波纹管的性能试验试验项目性能要求拉伸的强度在长度小于500mm的原管两端,分别和管件连接固定,从连接好的管件一端注入0.3MPa(?型)或0.1MPa(ц型)的空气,另一端拉伸负荷拉伸5min,然后保持静止1min,确认无裂纹、无泄漏。
压扁性将长度100mm的原管夹在2块铁板之间,将其中50mm 压扁至外径的1/2后,目测确认原管表面无裂纹,无损伤。
原管焊缝置于受力方向(压缩方向)成90°的位置。
耐冲击性将原管注入0.3MPa(?型)或0.1MPa(ц型)的空气状态下,置于水泥地面上,在离地面1m高度处,将4kg(?型)或2kg (ц型)的钢球落到管中间,确认无裂纹、无泄漏。
弯曲性将被覆管注入0.3MPa(?型)或0.1MPa(ц型)的空气状态下,固定一端,直径为50mm圆,弯曲180°.左右两次弯曲看作一次循环,弯曲速率控制在5次循环/min,交替进行共6次循环(?型)或8次循环(ц型)后,确认原管无裂纹、无泄漏,被覆层无裂纹。
扭曲性将各种规格长度的被覆管注入0.3MPa(?型)或0.1MPa (ц型)的空气状态下,将管的一端固定,以管的轴线为中心,左右方向为一次,交替合计6次90°扭曲,确认无裂纹、无泄漏,被覆层无裂纹。
气密性在2m原管的两端,分别和管件连接固定,将连接好的管件一端堵住,从另一端注入0.3MPa(?型)或0.1MPa(ц型)的空气,保持1min,确认无泄漏。
按规定放入水中检查。
耐压性在原管的两端,根据管件构造分别固定,堵住一端,从另一端缓慢注入1.6MPa(?型)或0.1MPa(ц型)水压,保持1min,目测确认无裂纹、无泄漏。
工艺规程目录

工艺规程目录第一章坯料、产品及工艺流程一、坯料1.1坯料的钢种,规格和长度1.2坯料验收标准二、产品2.1产品的规格2.2产品验收标准三、工艺流程第二章加热工艺规程一、设备参数1.1加热炉设备参数1.2煤气发生炉设备参数1.3仪表房设备参数1.4推钢机设备参数二、加热工艺规程2.1入炉工艺要求2.2出钢工艺要求2.3司炉工艺要求2.3.1加热炉2.3.2煤气发生炉第三章轧钢工艺规程一、轧机设备参数及轧机操作要点二、1#、2#、3#飞剪的技术性能及操作要点三、预穿水装置技术性能和操作要点四、活套五、压下规程六、主控台技术操作规程七、开车前检查八、成品检查第四章成品的冷却、剪切、精整和包装工艺规程一、冷却工艺要求二、冷床区主要设备的工艺参数及操作规程三、冷剪区主要设备的工艺参数及操作规程四、传送站五、打捆收集区工艺参数及操作规程六、棒材成品称重、挂牌七、成品库工艺规程第一章坯料、产品及工艺流程一坯料1.1坯料的钢种,规格和长度钢种:低合金结构钢,普通碳素结构钢,优质碳素结构钢HRB335、HRB400规格:150×150mm长度:12m1.2坯料验收标准见表1坯料验收,产品生产执行的有关标准表1-1序标准编号标准名称号1 GB1499.2-2007 钢筋混凝土用热轧带肋钢筋2 GB/T702-2004 热轧圆钢和方钢尺寸、外形、重量及允许偏差3 GB/T20066-2006 钢和铁化学成分测定用试样的取样和制样方法4 GB/T222-2006 钢的成品化学成分允许偏差5 GB/T223.5-1997 钢铁及合金化学分析方法还原型硅钼盐酸光度法测定酸溶硅含量6 GB/T223.11-1991 钢铁及合金化学分析方法过硫酸铵氧化容量法测定铬量7 GB/T223.12-1991 钢铁及合金化学分析方法碳酸钠分离-二苯碳酰二肼光度法测定铬量8 GB/T223.14-2000 钢铁及合金化学分析方法钽试剂萃取光度法测定钒量9 GB/T223.17-1989 钢铁及合金化学分析方法二安替吡啉甲烷萃取光度法测定钛量10 GB/T223.19-1989 钢铁及合金化学分析方法新亚铜灵-三氯甲烷萃取光度法测定铜量11 GB/T223.23-1994 钢铁及合金化学分析方法丁二酮肟镍直接光度法测定镍量12 GB/T223.24-1994 钢铁及合金化学分析方法丁二酮肟-三氯甲烷萃取光度法测定镍量13 GB/T223.25-1994 钢铁及合金化学分析方法丁二酮肟重量法测定镍量14 GB/T223.26-1989 钢铁及合金化学分析方法硫氰酸盐直接光度法测定钼量15 GB/T223.27-1994 钢铁及合金化学分析方法硫氰酸盐-乙酸丁酯萃取光度法测定钼量16 GB/T223.37-1989 钢铁及合金化学分析方法蒸馏分离-靛酚蓝光度法测定氮量17 GB/T223.40-1994 钢铁及合金化学分析方法离子交换分离-氯磺酚S光度法测定铌量18 GB/T223.59-1987 钢铁及合金化学分析方法锑磷钼蓝光度法测定磷量19 GB/T223.63-1988 钢铁及合金化学分析方法高碘酸钠(钾)光度法测定锰量20 GB/T223.68-1997 钢铁及合金化学分析方法管式炉内燃烧后碘酸钾滴定法测定硫含量21 GB/T223.69-1997 钢铁及合金化学分析方法管式炉内燃烧后气体容量法测定碳含量22 GB/T228-2002 金属材料室温拉伸试验方法23 GB/T232-1999 金属材料弯曲试验方法24 GB/T4336-2002 碳素钢和中低合金钢火花源原子发射光谱分析方法(常规法)25 GB/T17505-1998 钢及钢产品交货一般技术要求26 YB/T081-1996 冶金技术标准的数值修约与检测数值的判定原则27 YB/T5126-2003 钢筋混凝土用钢筋弯曲和反向弯曲试验方法28 GB/T2101-1989 型钢验收,包装,标志和质量证明书的一般规定29 YB/T2011-2004 连续铸钢方坯和矩形坯二、产品2.1产品的规格:Φ12~Φ32带肋钢筋2.2产品验收标准:(见表1-1)三工艺流程坯料验收—入炉辊道—加热炉加热—出炉辊道—粗轧550×4+500×2轧制—1#飞剪剪头尾—中轧机组450×6轧制—预穿水冷却—2#飞剪剪切—精轧机组350×6轧制—穿水冷却—3#飞剪倍尺剪切—冷却(冷床)—冷床输出辊道—300t冷剪剪切(定尺)—收集打包—称重挂牌入库第二章加热区域工艺操作规程一、设备参数加热炉设备参数名称单位设计参数实际参数加热炉名称燃煤气连续式加热炉炉子有效尺寸m 33.8×12.86装炉方式冷装炉加热能力t/h 180 180燃料煤气发生炉供应热煤气燃料性质热发生煤的黄煤气燃料发热值Kcal/kg ≥6500≥6500烧嘴前温度℃430-480煤消耗Kg/t 450 450炉底热负荷×10 Kcal/㎡.h 26.25×10 26.25×10出钢形式侧出侧出出钢温度℃1250±501250±50断面温差℃≯30 ≯301.2煤气发生炉设备参数序号名称特性和基本参数1 炉膛直径 3.4米2 炉膛断面积9.07m23 适用燃料不粘煤、弱粘煤、长焰煤、气煤、贫煤、部分褐煤4 燃料块度13-25mm,25-50mm,60-60mm5 燃料消耗量2540-2720kg/h6 煤气产量7500-9500m3/h7 煤气热值(低热值)上段煤气(1600-1700)×4.18KJ/m3下段煤气(1200-1300)×4.18KJ/m3混合煤气(1450-1550)×4.18KJ/m38出口煤气温度上段煤气100-150℃下段煤气400-500℃9 炉出口煤气压力上段煤气980-1960pa(100-200mmH2O)下段煤气1960-2940pa(200-300mmH2O)1炉底鼓风压力7.0kpa11鼓风饱和温度50-65℃12水套受热面积18.1m213水套蒸汽压力70(294)kpa 14水套蒸汽产量550kg/h15灰盘转速 1.5r/h16加煤机、灰盘液压站功率11kw1 7 煤气出口公称直径上段DN300下段DN100018探火孔蒸汽压力294kpa 19炉底鼓风管公称直径DN4001.3 仪表房设备名称台数型号数字显示仪8 XMZ-1000-P02-0数字显示仪 6 XMZ-1000-P12-0压力数字显示仪12 XMT-1000-A4Z-0变频器 4 N2-410-M3 7.5Kw电阻远传压力表 4 YSG-3 0-1Mpa M20×1.5 1.4 推钢机设备参数型式推力台数推速行程链条推进60T×4 4 200mm/sic 1600mm二、加热区域工艺规格2.1入炉工艺要求:2.1.1坯料入炉严格执行生产调度通知,称量准确,记录求实。
工艺规程概念、零件图、毛坯、基准及其分类、加工余量、尺寸链课件
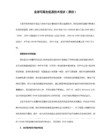
A是B、C的 设计基准 A是B面平行度 的设计基准
2) 工艺基准: 是加工、测量和装配过程中使用的基 准,又称制造基准。 a、 工序基准: 是指在工序图上,用来确定加工表 面位置的基准。它与加工表面有尺寸、位置要求。
b、 定位基准: 是加工过程中,使工件相对机床或刀 具占据正确位置所使用的基准。
n—每台产品中该零件的数量(件/台);
α—备品率(%),汽车、拖拉机产品中为20~30%; β—废品率(%),汽车、拖拉机产品中为0.3%。
3.1 基本概念
2.生产类型※: 企业(或车间)生产专业化程度的分类。 ●单件生产 单个地生产不同结构、尺寸的产品,且很少重复或完全不重复 。 如机械配件加工、专用设备制造、 ●成批生产 重型机械制造、新产品试制。 一年中分批地制造相同的产品,制造过程有一定的重复性→周 期性的重复生产。 如汽车、拖拉机、轴承、发 ●大量生产 动机、自行车、洗衣机等的 产品的数量很大,大多数工作地按照一定的生产节拍进行某种 生产。按工艺特点分: 如通用机床制造。 单件小批生产 小批生产 零件的某道工序的重复加工。
■减少加工工作量→提高配合精度:
3.2 零件的加工工艺性分析与毛坯的选择
■使加工面等长度或成倍数,直径沿一个方向递减→便于 刀具布置,在多刀半自动车床上加工,提高生产效率:
3.2 零件的加工工艺性分析与毛坯的选择
■连轴齿轮,轴径和齿轮直径相差太大,废工废料,也不 便于锻造→分离
3.2 零件的加工工艺性分析与毛坯的选择
中批生产 大批大量生产
中批生产 大批生产
3.1 基本概念
3.工艺特点: 生产类型不同,零件和产品制造工艺、所用设备及工艺装备、 对工人的技术要求、采取的技术措施和达到技术经济效果也会 不相同。 各种生产类型的工艺特征如表3.4所示。
工业锅炉典型工艺规程锅筒制造
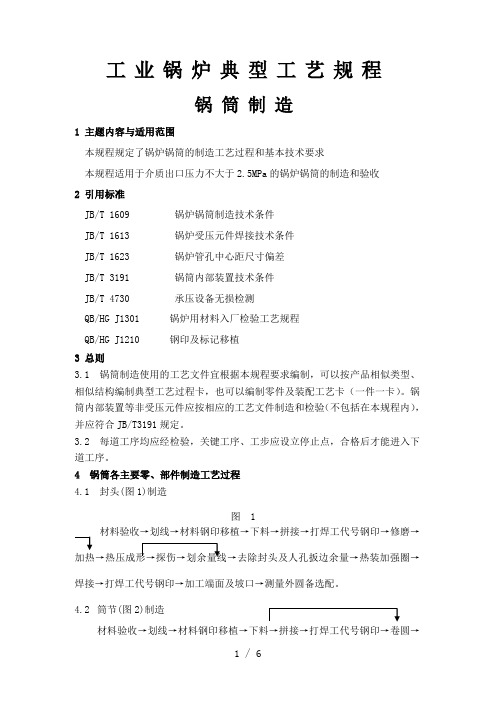
工业锅炉典型工艺规程锅筒制造1 主题内容与适用范围本规程规定了锅炉锅筒的制造工艺过程和基本技术要求本规程适用于介质出口压力不大于2.5MPa 的锅炉锅筒的制造和验收 2 引用标准JB/T 1609 锅炉锅筒制造技术条件JB/T 1613 锅炉受压元件焊接技术条件JB/T 1623 锅炉管孔中心距尺寸偏差JB/T 3191 锅筒内部装置技术条件JB/T 4730 承压设备无损检测QB/HG J1301 锅炉用材料入厂检验工艺规程QB/HG J1210 钢印及标记移植3 总则3.1 锅筒制造使用的工艺文件宜根据本规程要求编制,可以按产品相似类型、相似结构编制典型工艺过程卡,也可以编制零件及装配工艺卡(一件一卡)。
锅筒内部装置等非受压元件应按相应的工艺文件制造和检验(不包括在本规程内),并应符合JB/T3191规定。
3.2 每道工序均应经检验,关键工序、工步应设立停止点,合格后才能进入下道工序。
4 锅筒各主要零、部件制造工艺过程4.1 封头(图1)制造材料验收→划线→材料钢印移植→下料→拼接→打焊工代号钢印→修磨→焊接→打焊工代号钢印→加工端面及坡口→测量外圆备选配。
4.2筒节(图2)制造材料验收→划线→材料钢印移植→下料→拼接→打焊工代号钢印→卷圆→图 1纵缝定位焊→焊接→打焊工代号钢印→校圆(→无损探伤)→加工端面及坡口→测量外圆备选配。
图 24.3法兰管座(图3)制造4.44.54.5.1快装组装出厂锅炉锅筒筒节与筒节装配定位焊→焊接→打焊工代号钢印→划筒体中心线及预焊件位置线→筒体与一端封头装配定位焊→焊接→打焊工代号钢印→筒体与另一端封头装配定位焊→焊接→打焊工代号钢印→无损探伤→划管座孔位置线及管孔、排孔位置线→加工管孔及排孔→管座装配定位焊→内装预焊件定位焊→焊管座及内装预焊件→打焊工代号钢印→清除毛刺及杂物→待装配。
4.5.2散装出厂锅炉锅筒筒节与筒节装配定位焊→焊接→打焊工代号钢印→划筒体中心线及预焊件位置线→筒体与一端封头装配定位焊→焊接→打焊工代号钢印→筒体与另一端封头装配定位焊→焊接→打焊工代号钢印→无损探伤→划管座孔位置线→加工管座孔→管座装配定位焊→焊接→预焊件定位焊→焊接→水压试验→划排孔位置线→加工排孔→清除毛刺及杂物→内件组装或放置待工地组装→封闭人孔盖→油漆包装。
《工艺规程模板》word版

5.7 物料、中间产品、成品储存注意事项 5.7.1 原辅料贮存于中间站内,一个整包装未能一次性用完时,将剩余原辅料称量后,按原包装密 闭封存,附内外标签(一张置于两层聚乙烯袋中间,另一张贴在最外层聚乙烯袋上或物料桶外), 置于中间站暂存,并作为下一次优先使用。
5.7.2 生产过程中的混粉用两层聚乙烯袋装好,胶囊用两层聚乙烯袋装好,并尽量将内空气挤出, 扎紧封闭,置于白色洁净干燥物料桶中加盖,附内外标签(一张置于两层聚乙烯袋中间,另一张贴 在物料桶外),,贮存于中间站,贮存时间不超过 72 小时。
5 程序 5.1 工艺流程及环境区域划分
十万级洁净区
原辅料
非洁净区
中间产品检验
内包装材料
成品检验
生产 车间 生产 工序 辅料 处理 称量 配料
操作间
湿法制粒 间
称量配料 间(1)
房间号 XXXX XXXX
外包装
外包装材料
成品经检验合格入库 XXXX 车间
洁净 级别 十万 级 十万 级
温湿度及压差
温湿度 :XX℃~XX℃ 相对压差:XX%~XX%
氯化物鉴别
本品为硬胶囊,内容物为白色至类白色颗粒和粉末 供试品溶液主峰的保留时间与盐酸贝那普利对照品峰的保留时间保持一致
应呈正反应
溶出度
限度为标示量的 80%
限度为标示量的 85%
含量均匀度 A+1.80S≤15.0,应符合规定
A+1.80S≤13.0,应符合规定
检
供试品溶液的色谱图中单个最大杂质的峰面积不得过对照溶液的主峰面积
XXXX
XXXX 张
物料代码 XXXX XXXX XXXX XXXX XXXX XXXX
XX 粒/盒 消耗定额 XX 粒 XXkg XX XX 张 XX 个 XX 张
楷达力矩扳手检定仪典型工艺规程
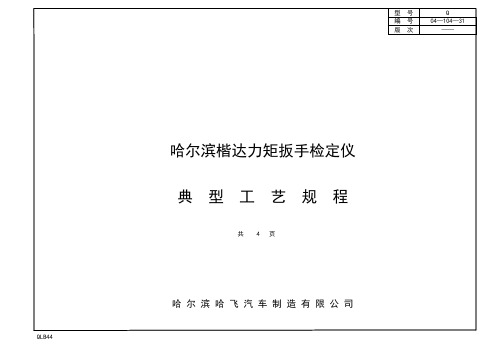
5
维护
版次
——
5.1 仪器应保持清洁,长期不用须每三个月通电一次,通电时间不少于 24 小时 5.2 本仪器应按公司有关文件规定定期校验。
更改标记 QLB46
修改单号
修改依据
签字
日期
04—104—31
版次
——
实时 峰值 辅助 打印
运行 N.m
调零钮
屏幕
选择键 确认键
开关
图
更改标记 QLB46
修改单号
3 3.1 3.2
3.3 3.4 3.5
3.7
操作步骤
接通 220V 电源,打开右侧电源开关,指示灯亮(见图 1)。
仪器自检,屏幕显示 LJC—2 后屏闪,等待自检完毕后,仪器自动归零,屏幕显示“F=000.0”(如不为零调调零旋钮至零)。此时为实
时测试状态,在此状态下测量的扭矩值是随用力大小而变化的,检测不到峰值。
4
注意事项
4.1 请使用 220V,50HZ 电源。
4.2 接入电源的接线插座或接线板不与其它设备共用。
4.3 不要使仪器掉落地上或受到强烈冲击。
4.4 避免在高温多湿、接近强电设备的场所使用本仪器。
4.5 当仪器出现异常情况时,班长应及时报告工具库。
4.6 检定仪量程范围是 10~100Nm,在有效量程内校验。
工指 艺导
工 艺
校 对
审 核
更修修签日检 改改改字期验 标单 的 记号简
要 内 容
QLB45
04—104—31
3.8 3.9 3.9.1 3.9.2 3.9.3 3.9.4
测量完成后在 BB-QJ-95《月份力矩扳手班前校准记录》上做好记录。 表格填写说明: 工段、班组、月份、日由班长统一填写。 工位、检定编号由力矩扳手使用者填写。 在空格处一列填写力矩扳手测量值,一列填写使用者姓名。 右下角由力矩扳手所在班组的班长签名。
钢制容器制造通用工艺规程完整
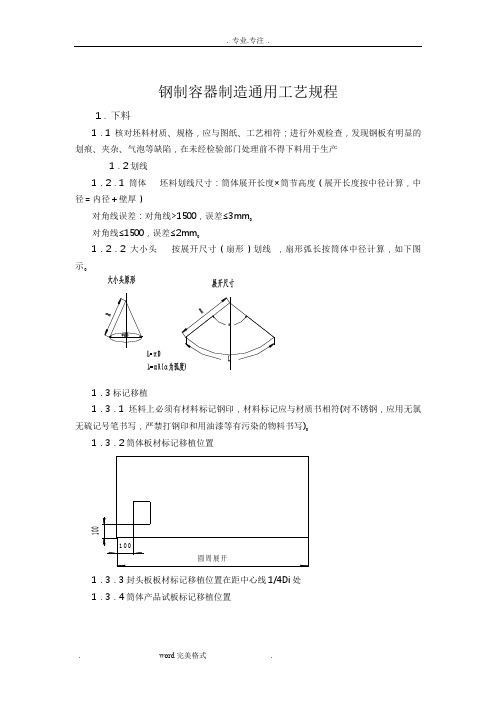
钢制容器制造通用工艺规程1.下料1.1核对坯料材质、规格,应与图纸、工艺相符;进行外观检查,发现钢板有明显的划痕、夹杂、气泡等缺陷,在未经检验部门处理前不得下料用于生产1.2划线1.2.1筒体 坯料划线尺寸:筒体展开长度×筒节高度(展开长度按中径计算,中径=内径+壁厚)对角线误差:对角线>1500,误差≤3mm 。
对角线≤1500,误差≤2mm 。
1.2.2大小头 按展开尺寸(扇形)划线 ,扇形弧长按筒体中径计算,如下图示。
1.3标记移植1.3.1坯料上必须有材料标记钢印,材料标记应与材质书相符(对不锈钢,应用无氯无硫记号笔书写,严禁打钢印和用油漆等有污染的物料书写)。
1.3.2筒体板材标记移植位置1.3.3封头板板材标记移植位置在距中心线1/4Di 处 1.3.4筒体产品试板标记移植位置1.4坡口加工1.4.1筒体纵、环缝坡口内坡口(一般当Di ≥600时打内坡口)时,坡口制在标记反面,如下左图;外坡口时,坡口制在标记面,如下右图。
坡口尺寸按图纸要求,图样无规定时按附录一。
1.4.2坡口清理除锈焊缝二侧用砂轮打磨除锈,范围应>20mm ;打磨除锈后,应在当天施焊,否则须重新清理。
2.筒体(大小头)成形2.1预弯2.1.1材料标记钢印应卷在外面。
2.1.2钢板放入卷板机口,应使钢板边缘与卷辊轴线平行,避免偏斜。
2.1.3利用弯模在卷板机上踏头,踏头长度≥200mm ,用内径R 卡板测量踏头R ,边缘直边部分应<10mm 。
2.2卷圆成形、点固2.2.1钢板放入卷板机后,应使钢板边缘与卷辊轴线平行,避免偏斜。
2.2.2分几次调节上辊筒卷制,用R 卡板随时测量,防止过卷。
组对间隙按图纸2.2.3纵缝对口错边量b 应符合规定:当δS ≤12:时,b ≤1/4δS ;当δS>12:时b ≤3,对复合钢板,错边量应不大于钢板复层厚度的50%。
且不大于2㎜。
3.纵缝施焊3.1筒节上接产品试板和引熄弧板(对非标设备无产品试板,筒体接引熄弧板),不得在筒节其他部位随意引弧。
无损检测通用工艺规程

无损检测通用工艺规程(总65页)--本页仅作为文档封面,使用时请直接删除即可----内页可以根据需求调整合适字体及大小--无损检测通用工艺规程编制:审核:批准:日期:目录第1章编制说明 (3)第2章射线检测通用工艺规程 (5)第3章超声波检测通用工艺规程 (21)第1节承压设备对接焊接接头超声检测及质量分级 (24)第2节承压设备钢板超声检测及质量分级 (29)第3节承压设备用钢锻件超声检测及质量分级 (32)第4章磁粉检测通用工艺规程 (35)第5章渗透检测通用工艺规程 (39)第6章工艺卡附表 (44)第1节射线检测工艺卡 (44)第2节超声检测工艺卡 (45)第3节磁粉检测工艺卡 (46)第4节渗透检测工艺卡 (47)第一章编制说明范围本规程规定了对金属原材料、零部件和焊接接头进行射线检测、超声检测、磁粉检测、渗透检测的基本要求。
本规程适用于本公司钢制压力容器产品的无损检测工作。
引用标准和编制依据下列标准包含的条文,通过在本规程中引用而构成本规程的条文,在规程出版时,所有版本均为有效。
所有标准都会被修订,使用本规程的各方应探讨使用下列标准最新版本的可能性。
压力容器安全技术监察规程(1999年版)GB150-1998 《钢制压力容器》GB151-1999 《管壳式换热器》JB/~《承压设备无损检测》《特种设备无损检测人员资格考核实施细则》《放射卫生防护基本标准》Q/《质量保证手册》人员资格及职责从事无损检测的人员必须持有国家质量监察机构颁发的并与其工作相适应的资格等级证书。
从事无损检测的人员校正视力不得低于,从事磁粉、渗透检测工作人员,不得有色盲、色弱。
检测人员严格执行有关条例、规程、标准和技术规范,保证工作质量。
评片人员的视力应每年检查一次,要求距离400mm能读出的一组印刷体字母。
检测操作人员必须按委托单要求并同时根据检测工艺规程进行操作,做好检测记录及签发检测报告。
无损检测责任工程师的职责见《岗位职责》。