化学沉铜原理及异常 共42页
印制电路板化学沉铜详解4

印制电路板化学沉铜详解(四)假若不经过加速处理,化学铜槽内的沉积反应会减慢,同时也可能冒着这样的风险:一些疏松吸附在板面孔壁的胶体钯活性颗粒会污染沉铜液,造成槽液的稳定性变差甚至分解。
同时氢氧化亚锡会在活化的水洗过程中形成(正如我们在水洗槽中看到的混浊的状况)会覆盖在活性的钯颗粒上,遮蔽钯颗粒并影响它的活性。
氢氧化亚锡在水溶液呈明胶状,覆盖住钯活性颗粒。
加速的目的也是为了溶解这些亚锡的化合污染物,使之从钯活性颗粒上去除。
一些亚锡被去除同时一些附着不良的钯活性颗粒也会被速化在加速液中。
加速后的活性颗粒具有更强的活性,可以快速的诱发化学铜的沉积。
大多数加速也是酸性的,可以溶解在活化和加速之间水洗过程中产生的铜的氧化物。
一般情况下,当加速液中的铜含量达到1克/升则需要及时更换。
加速液通常都是由一些可溶解锡的化学药品组成,正因为如此,所以要注意生产工件不能再此溶液中停留过长时间。
在极端的条件下,加速过度,槽液在溶解锡时,也会从底部将钯颗粒从孔壁板面上速化掉,这样会使这些表面失去活性颗粒。
另外,一般的加速液都是以含氟的化合物为原料的,尽管可能氟的含量很低。
氟离子的存在会攻击孔壁中的玻璃纤维,继而使吸附玻璃纤维上的钯活性颗粒除掉,这样可能会造成电镀铜后玻纤断面处的镀层空洞(又叫截点)。
一些加速液可能会含有还原剂,可以吸附在生产板表面内带入沉铜槽与活化钯颗粒一起快速启动无电铜的沉积反应。
我们花费大量的时间讨论前处理而非化学铜本身,原因是为了保证化学铜的沉积,许多处理步骤都要小心的执行。
化学铜是化学铜制程的最终结果,正是因为如此,一些意想不到的结果的发生,往往是由于许多无法控制的因素造成。
包括附表一也是我们讨论的生产工艺简图。
无电铜槽/化学铜槽/沉铜槽槽液的组成:1.铜盐2.还原剂(甲醛)3.络合剂(EDTA,QUADROL,TART等)4.稳定剂,5.光泽剂等6.润湿剂化学铜:甲醛和氢氧根离子为金属铜的沉积提供了化学还原力。
沉铜
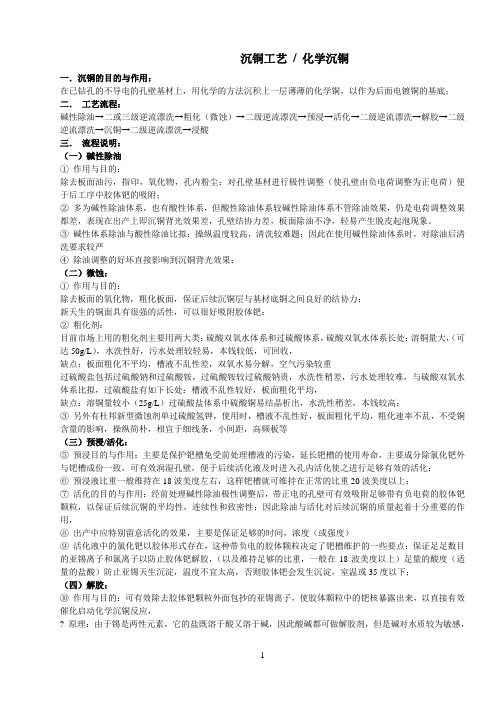
沉铜工艺/ 化学沉铜一.沉铜的目的与作用:在已钻孔的不导电的孔壁基材上,用化学的方法沉积上一层薄薄的化学铜,以作为后面电镀铜的基底;二.工艺流程:碱性除油→二或三级逆流漂洗→粗化(微蚀)→二级逆流漂洗→预浸→活化→二级逆流漂洗→解胶→二级逆流漂洗→沉铜→二级逆流漂洗→浸酸三.流程说明:(一)碱性除油①作用与目的:除去板面油污,指印,氧化物,孔内粉尘;对孔壁基材进行极性调整(使孔壁由负电荷调整为正电荷)便于后工序中胶体钯的吸附;②多为碱性除油体系,也有酸性体系,但酸性除油体系较碱性除油体系不管除油效果,仍是电荷调整效果都差,表现在出产上即沉铜背光效果差,孔壁结协力差,板面除油不净,轻易产生脱皮起泡现象。
③碱性体系除油与酸性除油比拟:操纵温度较高,清洗较难题;因此在使用碱性除油体系时,对除油后清洗要求较严④除油调整的好坏直接影响到沉铜背光效果;(二)微蚀:①作用与目的:除去板面的氧化物,粗化板面,保证后续沉铜层与基材底铜之间良好的结协力;新天生的铜面具有很强的活性,可以很好吸附胶体钯;②粗化剂:目前市场上用的粗化剂主要用两大类:硫酸双氧水体系和过硫酸体系,硫酸双氧水体系长处:溶铜量大,(可达50g/L),水洗性好,污水处理较轻易,本钱较低,可回收,缺点:板面粗化不平均,槽液不乱性差,双氧水易分解,空气污染较重过硫酸盐包括过硫酸钠和过硫酸铵,过硫酸铵较过硫酸钠贵,水洗性稍差,污水处理较难,与硫酸双氧水体系比拟,过硫酸盐有如下长处:槽液不乱性较好,板面粗化平均,缺点:溶铜量较小(25g/L)过硫酸盐体系中硫酸铜易结晶析出,水洗性稍差,本钱较高;③另外有杜邦新型微蚀剂单过硫酸氢钾,使用时,槽液不乱性好,板面粗化平均,粗化速率不乱,不受铜含量的影响,操纵简朴,相宜于细线条,小间距,高频板等(三)预浸/活化:⑤预浸目的与作用:主要是保护钯槽免受前处理槽液的污染,延长钯槽的使用寿命,主要成分除氯化钯外与钯槽成份一致,可有效润湿孔壁,便于后续活化液及时进入孔内活化使之进行足够有效的活化;⑥预浸液比重一般维持在18波美度左右,这样钯槽就可维持在正常的比重20波美度以上;⑦活化的目的与作用:经前处理碱性除油极性调整后,带正电的孔壁可有效吸附足够带有负电荷的胶体钯颗粒,以保证后续沉铜的平均性,连续性和致密性;因此除油与活化对后续沉铜的质量起着十分重要的作用,⑧出产中应特别留意活化的效果,主要是保证足够的时间,浓度(或强度)⑨活化液中的氯化钯以胶体形式存在,这种带负电的胶体颗粒决定了钯槽维护的一些要点:保证足足数目的亚锡离子和氯离子以防止胶体钯解胶,(以及维持足够的比重,一般在18波美度以上)足量的酸度(适量的盐酸)防止亚锡天生沉淀,温度不宜太高,否则胶体钯会发生沉淀,室温或35度以下;(四)解胶:⑩作用与目的:可有效除去胶体钯颗粒外面包抄的亚锡离子,使胶体颗粒中的钯核暴露出来,以直接有效催化启动化学沉铜反应,? 原理:由于锡是两性元素,它的盐既溶于酸又溶于碱,因此酸碱都可做解胶剂,但是碱对水质较为敏感,易产生沉淀或悬浮物,极易造成沉铜孔破;盐酸和硫酸是强酸,不仅不利与作多层板,由于强酸会攻击内层黑氧化层,而且轻易造成解胶过度,将胶体钯颗粒从孔壁板面上解离下来;一般多使用氟硼酸做主要的解胶剂,因其酸性较弱,一般不造成解胶过度,且实验证实使用氟硼酸做解胶剂时,沉铜层的结协力和背光效果,致密性都有显著进步;(五)沉铜? 作用与目的:通过钯核的活化诱发化学沉铜自催化反应,新天生的化学铜和反应副产物氢气都可以作为反应催化剂催化反应,使沉铜反应持续不断进行。
化学沉铜原理及异常

板件从除油槽取出时,应注意滴液,尽量减少槽液带出 损失,已造成不必要的浪费和增加后清洗的困难度;
除油后水洗要充分,建议采用热水洗后,加1-2道自来 水洗;
清洁-调整剂对界面活性的调节机理
除胶渣后的孔壁表面
清洁后的孔壁表面
微蚀 成分及操作条件:
培训大纲
1.PTH介绍 2.化学沉铜原理介绍 3.化学沉铜异常及处理
PTH简要介绍
双面板或多层复合板各层铜箔之间原本是绝 缘层,有时为了实现某些要求功能,需要各层间 的连接与导通,此时就需在铜箔上镀导通孔即
PTH(Plating Throught Hole)
通孔横截面模型
PTH的方式
• 黑孔(Black Hole)+电镀 • 化学沉铜+电镀
预浸
注意点: 预浸液维护主要是槽液的比重和盐酸含量;槽液的
比重主要取决于亚锡离子和氯离子的含量,盐酸主 要是防止亚锡离子的水解和清洗板面氧化物; 预浸槽槽液一般按生产板平米数来添加更换,有时 也用铜含量作为参考控制项目,一般铜含量控制在1 克/升以下;开缸时多采用预浸液原液开缸,补充时 采用预浸盐; 板件从水洗槽取出进入预浸槽前,应注意减少滴水 带入,以免稀释预浸液,降低槽液酸度,造成亚锡 水解,槽液变混浊,同时也会污染活化槽;板件经 预浸槽后直接进入活化槽;
化学沉铜原理介绍
流程简介
膨松→除胶渣→中和 Desmear
调整→清洁→调整剂→微蚀→ 预 浸→活化→加速→化铜 PTH
膨松
成分及操作条件:
NaOH 已二醇乙醚 已二醇 水 温度 时间
20g/l 30/l 2g/l 其余 60-80℃ 5min
沉铜

化学镀铜(PTH)Chapter 1 沉铜原理(Shipley)一概述化学镀铜:俗称沉铜,是一种自身催化氧化还原反应,可以在非导电的基体上进行沉积,化学镀铜的作用是实现孔金属化,从而使双面板,多层板实现层与层之间的互连,随着电子工业的飞速发展对线路板制造业的要求越来越高,线路板的层次越来越多,同一块板的孔数越来越多,孔径越来越小,这些孔的金属化质量将直接影响到电气的性能和和可靠性。
二去钻污原理:1 去钻污的必要性:由于钻孔过程钻嘴的转速很高,可达16~~18万rpm,而环氧玻璃基材为不良导体,钻孔时会在短时间内产生高温,高温会在孔壁上留下许多树脂残渣,从而形成一层薄的环氧树脂钻污,由于此树脂钻污与孔壁的结合力不牢,当直接沉铜时,就会影响化学铜与孔壁的结合力,特别是多层板,会影响化学铜层与内层铜的导通,去钻污就是清除这些残渣,改善孔壁结构。
2 去钻污方法的选择:利用碱性KMnO4溶液作强氧化剂,在高温下将孔壁树脂氧化,这种处理不仅可以除掉这些钻污,而且还可以改善孔壁树脂表面结构,经过碱性KMnO4处理后的树脂表面被微蚀形成许多孔隙,呈蜂窝状,这样大大促进了化学铜与孔壁树脂的结合力,此法是目前去钻污流程使用最广泛的方法,具有高稳定性,既经济又高效,管理操作简便。
3 去钻污原理:①溶胀:Swelling利用有机溶剂渗入到孔壁的树脂中,使其溶胀,形成结构疏松的环氧树脂,从而有利于碱性KMnO4的氧化除去,一般的溶胀剂都是有机物,反应条件要求高温及碱性环境。
需采用不锈钢工作液槽。
MLB211膨胀剂是淡黄色,不混浊,不易燃的水溶液,含有有机物(10%左右的已烯基丁二醇—丁乙酸),对树脂有一定的溶解作用,但主要作用是使环氧树脂溶胀,溶胀剂不与树脂起直接反应,但随着长时间的高温处理,溶胀剂易老化而需更换,换缸视生产量而定,一般为6000m2/次。
②去钻污Desmearing:反应原理:在碱性及高温条件下,KMnO4对溶胀的树脂起氧化作用。
沉铜讲义

沉铜讲义一、 沉铜目的沉铜的目的是使孔壁上通过化学反应而沉积一层0.3um-0.5um 的铜,使孔壁具有导电性,通常也称作化学镀铜、孔化。
二、 沉铜原理络合铜离子(Cu 2+-L )得到电子而被还原为金属铜;通常是利用甲醛在强碱性环境中所具有的还原性并在PdCu2+Cu 2++2HCHO +40H Cu +O - 三、 工艺流程去毛刺→膨胀→去钻污→三级水洗→中和→二级水洗→除油调整→三级水洗→微蚀→二级水洗→预浸→活化→二级水洗→加速→二级水洗→沉铜→二级水洗→板面电镀→幼磨→铜检四、 工艺简介1. 去毛刺由于钻孔时的板面会因钻头上升和下降时产生的毛刺(披锋),若不将其除去会影响金属化孔的质量和成品的外观,所用的方法为:用含碳化硅磨料的尼龙棍刷洗,再用高压水冲洗孔壁,冲洗附在孔壁上大部分的微粒和刷下的铜屑。
2. 膨胀因履铜板基材树脂为高分子化合物,分子间结合力很强,为了使钻污树脂被有效地除去,通过膨胀处理使其分解为小分子单体。
3. 除胶(去钻污)使孔壁环氧树脂表面产生微观上的粗糙,以提高孔壁与化学铜之间的接合力,并可提高孔壁对活化液的吸附量,其原理是利用KMnO 4在碱性环境听强氧化性将孔壁表面树脂氧化:C(树脂)+2KMnO4→2MnO2+CO2↑+2KOH (副)1. 4KMnO4+4KOH→4K2MnO4+2H2O+O2↑(再生)2. 3K2MnO4+2 H22KMnO4+MnO2+4KOH若K2MnO4含量过高,会影响KMnO4去钻污效果,固此在槽中用电极使生成的K2MnO4再生为KMnO4。
4.中和经碱性KMnO4处理后的板经三级水洗后能洗去附在板面和孔内大部分的KMnO4,但对于后工序的影响也很大(KMnO4有很强的氧化性,和处理液本身为强碱性),必须用具酸性和还原的中和剂处理,在生产中通常用草酸作中和还原处理(H2C2O4)反应:2MnO4-+H2C2O4+16H+→Mn2++10CO2↑+8H2OMnO2++C2O4-+4H+→Mn2++CO2↑+2H2O有时为了对孔壁上的玻璃纤维进行蚀刻和粗化作用,在中和槽中加入NH4HF+H2SO4作为玻璃蚀刻剂。
化学沉铜工艺知识讲解
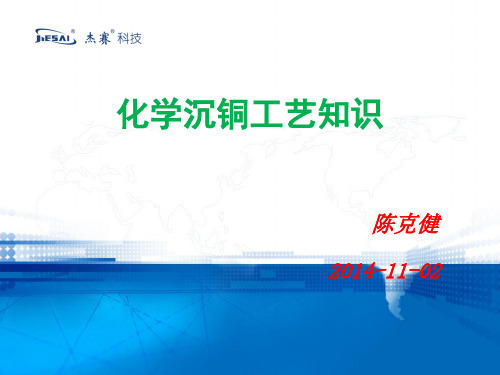
三、工艺流程简介-Desmear
再生电极:
结构截面示意图
电解再生器外观图
再生原理
第 13 页
三、工艺流程简介-Desmear
3.3.3 MLB 中和剂216(酸性强还原剂)
作用: 能将残存在板面或孔壁死角处的二氧化锰或高锰酸盐中和除去;
第 14 页
三、工艺流程简介-沉铜工艺
4. 沉铜工艺 4.2 设备要求 4.1 流程
Before PTH
After PTH
After Plating
第 3 页
二、工艺流程
plamsa 磨板
等离子处理 Deburr 去毛刺
特殊板材的除胶渣、表面活化. 去除孔口披风、清洗孔内粉尘 使孔壁上的胶渣软化、膨松. 溶解孔壁少量树脂及粘附孔壁内的胶渣。 将除胶渣后残留的高锰酸钾盐除去. 除掉铜表面轻微的手印、油渍、氧化等 使孔壁呈正电荷后,提高孔壁对钯的吸附 粗化铜箔表面,增强铜面与孔化之间的结合 防止板子带杂质、水分进入昂贵的活化槽 使胶体钯微粒均匀吸附到板面和孔壁上 剥去胶体钯微粒外层的Sn+4外壳,露出 钯核, 形成孔化时的反应中心 。
3.3.1 MLB 膨松剂 211
使孔壁上的胶渣得以软化,膨松并渗入树脂聚合后之交联处,从而降低其键结 的能量,使易于进行树脂的溶解。
第 11 页
三、工艺流程简介-Desmear
3.3.2 MLB 除钻污剂 214(主要成分高锰酸钾+液碱)
作用:
高锰酸钾具有强氧化性,在高温及强碱的条件下,与树脂发生化学反 应使其分解溶去。
放大镜
光 源
第 28 页
第 24 页
(我司采用)
三、工艺流程简介-沉铜工艺
沉铜常见问题及对策

1.检查钻孔条件,钻头质量和研磨质量。
2.加强去毛刺高压水洗。
各槽清洗不足,有污染物积聚,在孔里或表面残留
定期进行槽清洁保养。
水洗不充分,使各槽位的药水相互污染
检查水洗能力,水量/水洗时间。
加速处理液失调或失效
调整或更换工作液。
电镀后孔壁无铜
化学镀铜太薄被氧化
增加化学镀铜厚度。
电镀前微蚀处理过度
活化剂性能恶化,在铜箔表面发生置换反应
检查活化处理工艺浓度/温度/宋体; mso-hansi-font-family: 'Times New Roman'; mso-ascii-font-family: 'Times New Roman'">时间以副产物含量。必要时应更换槽液。
活化处理过度,铜表面吸附过剩的Pd/Sn,在其后不能被除去
加设摇摆、震动等。
化学镀铜液的活性差
检查NaOH、HCHO、Cu2+的浓度以及溶液温度等。
反应过程中产生气体无法及时逸出
加强移动、振动和空气搅拌等。以及降低温度表面张力。
化学镀铜层分层或起泡
层压板在层压时铜箔表面粘附树脂层
加强环境管理和规范叠层操作。
来自钻孔时主轴的油,用常规除油清洁剂无法除去
定期进行主轴保养。
活化液浓度偏低影响pd吸附检查活化处理工艺补充活化剂加速处理过度在去除sn的同时pd也被除掉检查加速处理工艺条件温度us时间浓度如降低加速剂浓度或浸板时间水洗不充分使各槽位的药水相互污染检查水洗能力水量水洗时间
【沉铜常见问题及对策】
故障现象
可能原因
措施对策
化学镀铜存在空洞
钻孔粉尘孔化后脱落
1.检查吸尘器,调整钻头的钻孔参数。
沉铜讲义

沉铜讲义一、 沉铜目的沉铜的目的是使孔壁上通过化学反应而沉积一层0.3um-0.5um 的铜,使孔壁具有导电性,通常也称作化学镀铜、孔化。
二、 沉铜原理络合铜离子(Cu 2+-L )得到电子而被还原为金属铜;通常是利用甲醛在强碱性环境中所具有的还原性并在PdCu2+Cu 2++2HCHO +40H Cu +O - 三、 工艺流程去毛刺→膨胀→去钻污→三级水洗→中和→二级水洗→除油调整→三级水洗→微蚀→二级水洗→预浸→活化→二级水洗→加速→二级水洗→沉铜→二级水洗→板面电镀→幼磨→铜检四、 工艺简介1. 去毛刺由于钻孔时的板面会因钻头上升和下降时产生的毛刺(披锋),若不将其除去会影响金属化孔的质量和成品的外观,所用的方法为:用含碳化硅磨料的尼龙棍刷洗,再用高压水冲洗孔壁,冲洗附在孔壁上大部分的微粒和刷下的铜屑。
2. 膨胀因履铜板基材树脂为高分子化合物,分子间结合力很强,为了使钻污树脂被有效地除去,通过膨胀处理使其分解为小分子单体。
3. 除胶(去钻污)使孔壁环氧树脂表面产生微观上的粗糙,以提高孔壁与化学铜之间的接合力,并可提高孔壁对活化液的吸附量,其原理是利用KMnO 4在碱性环境听强氧化性将孔壁表面树脂氧化:C(树脂)+2KMnO4→2MnO2+CO2↑+2KOH (副)1. 4KMnO4+4KOH→4K2MnO4+2H2O+O2↑(再生)2. 3K2MnO4+2 H22KMnO4+MnO2+4KOH若K2MnO4含量过高,会影响KMnO4去钻污效果,固此在槽中用电极使生成的K2MnO4再生为KMnO4。
4.中和经碱性KMnO4处理后的板经三级水洗后能洗去附在板面和孔内大部分的KMnO4,但对于后工序的影响也很大(KMnO4有很强的氧化性,和处理液本身为强碱性),必须用具酸性和还原的中和剂处理,在生产中通常用草酸作中和还原处理(H2C2O4)反应:2MnO4-+H2C2O4+16H+→Mn2++10CO2↑+8H2OMnO2++C2O4-+4H+→Mn2++CO2↑+2H2O有时为了对孔壁上的玻璃纤维进行蚀刻和粗化作用,在中和槽中加入NH4HF+H2SO4作为玻璃蚀刻剂。
沉铜机理

1。
槽液的负载量:浓缩液的补充量一般与槽液在一定温度下的平均负载量有关(单位槽体积所能够处理的工件的表面积)。
在一定的温度和时间作用下,一些副反应特别是甲醛和氢氧化钠之间的副反应会在特定的温度下按照一定的速率进行。
双液型的浓缩液按一定的比率补充铜含量是根据设定的槽液负载来添加的。
当槽液中的板面积低于供应商给定的负载量时,我们会发现槽液中甲醛和氢氧化钠的浓度降低,需要额外补充。
假若槽液中板面积超过供应商给定的数据,甲醛和氢氧化钠的含量会随着时间而逐渐升高。
同时,早一些高温槽中,当槽液的负载量较低时,槽液的蒸发量可能会超过了槽液的补充添加量,槽液的体积会随时间慢慢减少,可能需要另外补充纯水。
一般情况下,化学铜槽液的负载量一般在1-1.5平方英尺/加仑工作液,如上所述最适的负载量也是基于如上考虑的.4.机械摇摆:一般说法是在化学铜槽液中穿孔方向的摇摆可及时更新孔内和反应区域内的槽液,帮助去除沉积过程中产生而吸附在工件上的氢气.当然要注意板子之间不可以互相碰撞,也不可以接触槽壁以及其他设备和鼓气管等.当活化后的生产板件进入槽内,她表面的活性粒子可能会污染/沾附在其他表面上,从而使其它表面也具有了催化活性,继而在其表面发生化学铜反应并沉积铜层.5.挂具的材质无电铜挂具一般都采用不锈钢316制作.化学铜会沉积在挂具材料上.我们希望的是沉积在挂具上的化铜具有一定的结合力而不至于脱落在槽液中而继续反应.插入式挂具如塑料( PVC)或铁弗龙TEFLON在吸附一些活化剂后最终也会沉积上铜,但是结合力疏松,铜皮经常会脱落掉入到槽液内。
6.槽体的清洁/清洗每个槽子始终都会有化学铜析出在槽壁上(槽底,槽壁,溢流口等),因为一些活化剂带入污染和槽液中一些悬浮活性粒子的沉淀。
正因为如此,槽体需要定期彻底的清洁和清洗以除去析出的化铜,特别是过滤泵也要做必要的清洁清理工作,然后再将槽液倒回到干净镀槽中。
(也就是所谓的翻/倒槽)7. 镀槽的设计:聚丙烯PP或聚乙烯PE是制作化铜槽的很好的材料,主要因它们有相当的惰性,一定的抗冲击能力,在一定温度下不会软化,很多情况下化学铜槽需要加温。
化学沉铜
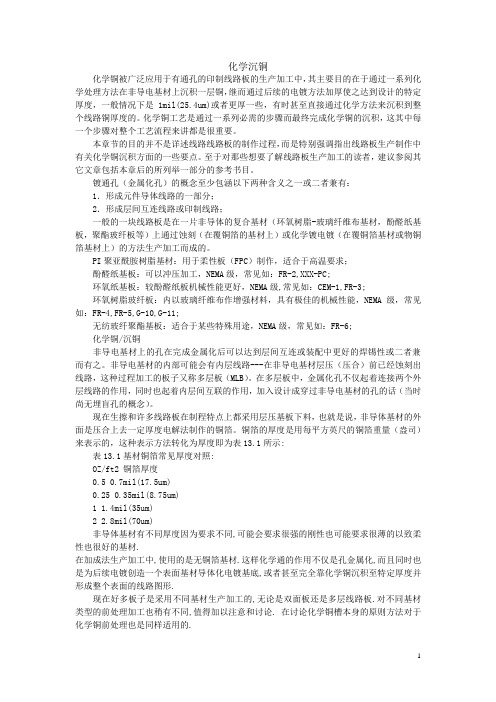
化学沉铜化学铜被广泛应用于有通孔的印制线路板的生产加工中,其主要目的在于通过一系列化学处理方法在非导电基材上沉积一层铜,继而通过后续的电镀方法加厚使之达到设计的特定厚度,一般情况下是1mil(25.4um)或者更厚一些,有时甚至直接通过化学方法来沉积到整个线路铜厚度的。
化学铜工艺是通过一系列必需的步骤而最终完成化学铜的沉积,这其中每一个步骤对整个工艺流程来讲都是很重要。
本章节的目的并不是详述线路线路板的制作过程,而是特别强调指出线路板生产制作中有关化学铜沉积方面的一些要点。
至于对那些想要了解线路板生产加工的读者,建议参阅其它文章包括本章后的所列举一部分的参考书目。
镀通孔(金属化孔)的概念至少包涵以下两种含义之一或二者兼有:1.形成元件导体线路的一部分;2.形成层间互连线路或印制线路;一般的一块线路板是在一片非导体的复合基材(环氧树脂-玻璃纤维布基材,酚醛纸基板,聚酯玻纤板等)上通过蚀刻(在覆铜箔的基材上)或化学镀电镀(在覆铜箔基材或物铜箔基材上)的方法生产加工而成的。
PI聚亚酰胺树脂基材:用于柔性板(FPC)制作,适合于高温要求;酚醛纸基板:可以冲压加工,NEMA级,常见如:FR-2,XXX-PC;环氧纸基板:较酚醛纸板机械性能更好,NEMA级,常见如:CEM-1,FR-3;环氧树脂玻纤板:内以玻璃纤维布作增强材料,具有极佳的机械性能,NEMA级,常见如:FR-4,FR-5,G-10,G-11;无纺玻纤聚酯基板:适合于某些特殊用途,NEMA级,常见如:FR-6;化学铜/沉铜非导电基材上的孔在完成金属化后可以达到层间互连或装配中更好的焊锡性或二者兼而有之。
非导电基材的内部可能会有内层线路---在非导电基材层压(压合)前已经蚀刻出线路,这种过程加工的板子又称多层板(MLB)。
在多层板中,金属化孔不仅起着连接两个外层线路的作用,同时也起着内层间互联的作用,加入设计成穿过非导电基材的孔的话(当时尚无埋盲孔的概念)。
沉铜

化学镀铜(PTH)Chapter 1 沉铜原理(Shipley)一概述化学镀铜:俗称沉铜,是一种自身催化氧化还原反应,可以在非导电的基体上进行沉积,化学镀铜的作用是实现孔金属化,从而使双面板,多层板实现层与层之间的互连,随着电子工业的飞速发展对线路板制造业的要求越来越高,线路板的层次越来越多,同一块板的孔数越来越多,孔径越来越小,这些孔的金属化质量将直接影响到电气的性能和和可靠性。
二去钻污原理:1 去钻污的必要性:由于钻孔过程钻嘴的转速很高,可达16~~18万rpm,而环氧玻璃基材为不良导体,钻孔时会在短时间内产生高温,高温会在孔壁上留下许多树脂残渣,从而形成一层薄的环氧树脂钻污,由于此树脂钻污与孔壁的结合力不牢,当直接沉铜时,就会影响化学铜与孔壁的结合力,特别是多层板,会影响化学铜层与内层铜的导通,去钻污就是清除这些残渣,改善孔壁结构。
2 去钻污方法的选择:利用碱性KMnO4溶液作强氧化剂,在高温下将孔壁树脂氧化,这种处理不仅可以除掉这些钻污,而且还可以改善孔壁树脂表面结构,经过碱性KMnO4处理后的树脂表面被微蚀形成许多孔隙,呈蜂窝状,这样大大促进了化学铜与孔壁树脂的结合力,此法是目前去钻污流程使用最广泛的方法,具有高稳定性,既经济又高效,管理操作简便。
3 去钻污原理:①溶胀:Swelling利用有机溶剂渗入到孔壁的树脂中,使其溶胀,形成结构疏松的环氧树脂,从而有利于碱性KMnO4的氧化除去,一般的溶胀剂都是有机物,反应条件要求高温及碱性环境。
需采用不锈钢工作液槽。
MLB211膨胀剂是淡黄色,不混浊,不易燃的水溶液,含有有机物(10%左右的已烯基丁二醇—丁乙酸),对树脂有一定的溶解作用,但主要作用是使环氧树脂溶胀,溶胀剂不与树脂起直接反应,但随着长时间的高温处理,溶胀剂易老化而需更换,换缸视生产量而定,一般为6000m2/次。
②去钻污Desmearing:反应原理:在碱性及高温条件下,KMnO4对溶胀的树脂起氧化作用。
化学镀铜(沉铜)技术

一流企业 2012-8-13 科学管理 卓越品质 满意服务
SHEN ZHEN SUN&LYNN CIRCUITS CO.,LTD.
5
• 第二种干法处理: • 该法是用等离子蚀刻的方法在真空筒内去除环氧
玷污,由于此方法生产效率低,只是在特殊情况 下才使用,例如制造聚酰亚胺与环氧玻璃复合的 多层板,用等离子去除钻孔孔壁上的树脂玷污。 2)孔壁的调整处理: 用H2SO4/HF进行凹蚀处理后,使用常规的清洗剂 处理,然后进行化学镀铜,在孔壁上会产生大量 的黑色斑点,剖孔检查这些黑点是玻璃纤维交叉 中间环氧树脂表面部位没有.
13
一流企业 2012-8-13 科学管理 卓越品质 满意服务
SHEN ZHEN SUN&LYNN CIRCUITS CO.,LTD.
• 2)胶体钯活化液反应机理 • 胶体钯活化液的活性和稳定性取决于A液中Sn2+/Pd2+离子浓度比值,以及溶液的配制
•
一流企业 2012-8-13 科学管理 卓越品质 满意服务
SHEN ZHEN SUN&LYNN CIRCUITS CO.,LTD.
10
2.3.1分步活化法
• 化学镀铜的活化方法多年来一直采用敏化-活化两步处理法。首先用5%的氯 • • • •
化亚锡水溶液进行敏化处理,然后再用1%-3%的Pdcl2,Aucl3,AgNO3的水溶 液进行活化处理。在基体表面上产生金属沉积的离子反应方程式 为:Sn+2+Pd+2=Sn+4+pd 这种分步活化的方法存在两个严重的问题, 一是孔金属化的合格率低,在化学镀铜后总是发现有个别孔沉不上铜,其主 要原因有两方面,一,Sn+2离子对环氧玻璃的基体表面湿润性不是很强,二, Sn+2很易氧化,特别是敏化后水清洗时间稍长,Sn+2被氧化为Sn+4,造成 失去敏化效果,使孔金属化后个别孔沉积不上铜。 另外一个严重的问题是活化剂采用的单盐化合物,它们和铜箔产生置换反应, 结果在铜的表面上产生一层松散的贵金属置换层,如果在上面直接化学镀铜, 会造成镀层结合不牢,特别是多层板造成金属化孔和内层导线联接不可靠。 在60年代出现多层印制板时为了解决金属化孔内层印制导线连接不可靠,曾 实验了很多种方法防止在铜上不产生置换层,最后真正用于实际生产的是一 次活化法的胶体钯活化液,和分步活化法的螯合离子钯活化法。这两种活化 法从根本上解决了Pd离子和铜之间产生置换反应的问题。
《沉铜和板电工艺培训讲解》

三、PTH各 药水缸成份及其作用
(12)二、化学铜缸(需机械摇摆、空气搅拌和循环过滤)
最后,所镀出的化学铜层又可作为自我催化的基地, Cu2+又在此已催化的基础上被电子还原成金属铜,如此不 断,直至减弱
O 催化
H-C-H+OH+
[H-C-H]- → H-C-OH+HOH
Cu2++2H- → Cu ↓
二、板电各药水 成份及设备的作用
(1) 硫酸铜:供给液铜离子的主源; (2) 硫 酸:导电及溶解阳极的功用(AR级的纯H2SO4); (3) 氯离子:有助阳极的溶解及光泽剂的发挥功能,使阳极
2、CU-160A 开缸量为7%(V/V), CU-160A 标准添加量为2.0L/10平米; 3、CU-160B 开缸量为7%(V/V), CU-160B 标准添加量为2.0L/10平米; ; 其它成份控制范围内:1、Cu2+ 1.6-2.2g/L,标准(1.8g/L); 2、NaOH 9-14g/L,标准(11g/L); 3、HCHO 5-7g/L,标准(6g/L);
(9)活化缸(二、需机械搅拌和循环过滤)
温 度:35-44℃ 处理时间:5-8min(标准6min) 反应方程式:PdCl2+SnCl2→PdSnCl4(中间态)
PdSnCl4→变成绿色锡离子 PdSnCl4+6PdCl2→SnPd7Cl16(催化剂)
负 反 应:Pd2++Sn2+→Pd0+ Sn4+
板电原理讲义
一、电镀基础理论
(1)法拉第一定律:在溶液中进行电解 (电镀)时,阴极上所沉积出的重量(或 阳极上所溶解掉的重量)与溶液中所通的 电量成正比。 (2)法拉第第二定律:在不同的电解液中, 因相同电量所沉积出不同的金属重量(或 溶解的重量)与其化学当量成正比。
沉铜的作用原理

1:沉铜的作用:沉铜也称化学镀铜它的作用是在孔壁非导电体(绝缘体)表面沉积一层铜,以确保内层导体与电路的可靠连接。
磨板的作用:除去板面的氧化,油污,手指印,及其它污物,在板面上形成微观粗糙表面。
同时利用靡板机的超音波水洗及高压水洗冲洗孔内起到清洁孔壁,减少孔内披锋的作用。
3.2化学镀铜反应机理化学镀铜时,Cu2+离子得到电子还原成金属铜Cu2++2e Cu.- ①电镀时,电子是由电镀电源提供的,而在化学镀铜时,电子是由还原剂甲醛所提供。
2H-C=o-H+4OH- 2H-C=o-0-+2H2 +2e----②在化学镀铜过程中反应①和反应②为共扼反应。
两反应同时进行,甲醛放出的电子直接给Cu2+,整个得失电子的过程是在短路状下进行的。
外部看不出交换电流的流通。
结合反应①和②可以得到反应③Cu2++2CH2O+4OH- Pdo/cu CU+2-C=-o-o-+2H2O+2H2 --③反应式③表明化学镀铜反应必须个备以下基本条件:1)化学镀铜液为强碱性,甲醛的还原能力取决于溶液中的碱性强弱程度,即溶液的PH值。
2)在强碱条件下,要保证Cu2+离子不形成,Cu(OH) 2沉淀,必须加入足够的Cu2+离子结合剂(由于络合剂在化学镀铜反应中不消耗,所以反应③式中省略了络合剂。
)。
3)从反应可以看出,每沉积1M的铜要消耗2M甲醛,4M氢氧化钠。
要保持化学镀铜速率恒定,和化学镀铜层的质量,必须及时补加相应的消耗部分。
4)只有在催化剂(Pd或Cu)存在的条件下才能沉积出金属铜,新沉积出的铜本身就是一种催化剂,所以在活化处理过的表面,一旦发生化学镀铜反应,此反应可以继续在新生的铜面上继续进行。
利用这一特性可以沉积出任意厚度的铜,加成法制造印制板的关键就在于此。
加有甲醛的化学镀铜液,不管使用与否,总是存在以下两个副反应,由于副反应的存在使化学镀铜液产生自然分解。
Cu20的形成反应2Cu2+H-C=o-H+5OH-=Cu20+H-C=o-O-+3H2O反应④所形成的Cu20在强碱条件下形成溶于碱的Cu+,存在下面的可逆反应。
化学沉铜介绍范文
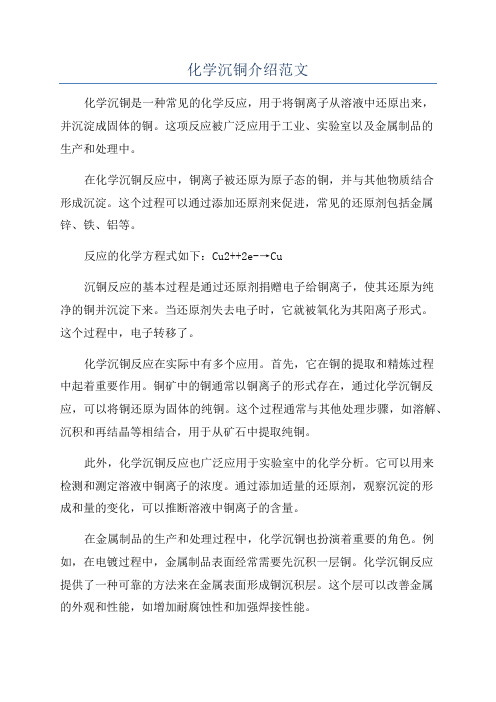
化学沉铜介绍范文化学沉铜是一种常见的化学反应,用于将铜离子从溶液中还原出来,并沉淀成固体的铜。
这项反应被广泛应用于工业、实验室以及金属制品的生产和处理中。
在化学沉铜反应中,铜离子被还原为原子态的铜,并与其他物质结合形成沉淀。
这个过程可以通过添加还原剂来促进,常见的还原剂包括金属锌、铁、铝等。
反应的化学方程式如下:Cu2++2e-→Cu沉铜反应的基本过程是通过还原剂捐赠电子给铜离子,使其还原为纯净的铜并沉淀下来。
当还原剂失去电子时,它就被氧化为其阳离子形式。
这个过程中,电子转移了。
化学沉铜反应在实际中有多个应用。
首先,它在铜的提取和精炼过程中起着重要作用。
铜矿中的铜通常以铜离子的形式存在,通过化学沉铜反应,可以将铜还原为固体的纯铜。
这个过程通常与其他处理步骤,如溶解、沉积和再结晶等相结合,用于从矿石中提取纯铜。
此外,化学沉铜反应也广泛应用于实验室中的化学分析。
它可以用来检测和测定溶液中铜离子的浓度。
通过添加适量的还原剂,观察沉淀的形成和量的变化,可以推断溶液中铜离子的含量。
在金属制品的生产和处理过程中,化学沉铜也扮演着重要的角色。
例如,在电镀过程中,金属制品表面经常需要先沉积一层铜。
化学沉铜反应提供了一种可靠的方法来在金属表面形成铜沉积层。
这个层可以改善金属的外观和性能,如增加耐腐蚀性和加强焊接性能。
另外,化学沉铜也可以用于制备铜的纳米颗粒。
通过控制反应条件,可以调节沉淀物的形状和尺寸,从而得到具有特定性质的纳米铜材料。
这些纳米铜材料在催化、电子器件和能源存储等领域有广泛的应用。
化学沉铜反应的控制和优化是一个复杂的课题。
反应速率、产物纯度和沉积层的质量都受到反应条件的影响。
一般来说,较高的温度、较高的还原剂浓度和较长的反应时间可以促进反应的进行。
此外,调节pH值、控制气氛和添加适量的络合剂等也可以影响反应的效果。
尽管化学沉铜反应已经有了广泛的应用,但仍有很多挑战需要解决。
例如,目前很多工业生产过程中使用的还原剂对环境有一定的污染性。
- 1、下载文档前请自行甄别文档内容的完整性,平台不提供额外的编辑、内容补充、找答案等附加服务。
- 2、"仅部分预览"的文档,不可在线预览部分如存在完整性等问题,可反馈申请退款(可完整预览的文档不适用该条件!)。
- 3、如文档侵犯您的权益,请联系客服反馈,我们会尽快为您处理(人工客服工作时间:9:00-18:30)。
调整
• 成份:清洁-调整剂 DI水 • 功能:除去板面轻微氧化物及轻微污渍,
对树脂界面活性调整有极好的效果; 直接影响沉铜的背光效果. • 原理:酸性溶液,与氧化物反应而使之溶 去;有机清洁剂,对有机油污具有 溶解作用.整孔性高分子吸附于孔壁表面 使孔壁表面显正电性.
通孔横截面模型
PTH的方式
• 黑孔(Black Hole)+电镀 • 化学沉铜+电镀
化学沉铜原理介绍
流程简介
膨松→除胶渣→中和 Desmear
调整→清洁→调整剂→微蚀→ 预浸→活化→加速→化铜 PTH
膨松
成分及操作条件:
NaOH 已二醇乙醚 已二醇 水 温度 时间
20g/l 30/l 2g/l 其余 60-80℃ 5min
调整
注意点:
应根据生产板面积累加来及时补充药品,达到一定产量 后,槽液需要更换,重新开缸;
过滤系统:一般建议除油槽加装过滤系统,不仅可以有 效过滤槽液中的粉尘杂质,同时也可有效搅拌槽液,增 强槽液对孔壁的清洗调整效果;滤芯一般使用5~10um 的PP滤芯,每小时过滤4-6次;
板面经除油水洗后,应该没有油污,氧化斑存在,即为 除油效果良好;
微蚀前后的铜面状况
微蚀前
微蚀后
预浸
成分及操作条件:
主要成分: HCL 、SnCL2 aq 比重: 1.120--1.150 温度: 常温 时间: 1--2 min
预浸
• 功能:防止板子带杂质污物进入昂贵的钯 槽;防止板面太多的水带入钯槽而导致局 部水解;
• 预浸槽与活化槽除无钯之外,其它成份完 全一致;
粗化效果不良,板面发花或粗化深度不够,沉铜电镀后,铜层结合力不足, 易产生起泡脱皮现象;粗化过度,孔口铜基材很容易被蚀掉,形成孔口露 基材,造成不必要的报废;另外槽液的温度特别是夏天,一定要注意,温 度太高,粗化太快或温度太低,粗化太慢或不足都会产生上述质量缺陷; 微蚀槽如使用过硫酸盐体系时,铜含量一般控制在25克/升以下,铜含量 太高,会影响粗化效果和微蚀速率;另外过硫酸盐的含量应控制在80— 120克/升; 微蚀槽在开缸时,应留约1/4的旧槽液,以保证槽液中有适量的铜离子, 避免新开缸槽液粗化速率太快,过硫酸盐补充应按50平米/3—6公斤来及 时补充;另外微蚀槽负载不宜过大,亦即开缸时应尽量开大些,防止槽液 因负载过大而造成槽液温度升高过快,影响板面粗化效果; 板面经微蚀处理后,颜色应为均匀粉红色;否则说明除油不足或除油后水 洗不良或粗化不良(可能是时间不足,微蚀剂浓度太低,槽液铜含量太高 等原因造成),应及时检查反馈并处理; 板件从水洗槽进入微蚀槽应注意滴水,尽量减少滴水带入,造成槽液稀释 和温度变化过大,同时板件从微蚀槽取出时,也应注意滴液时间充分;
Date: 10.July. 2019
化学沉铜原理介绍
培训大纲
1.PTH介绍 2.化学沉铜原理介绍 3.化学沉铜异常及处理
PTH简要介绍
双面板或多层复合板各层铜箔之间原本是绝 缘层,有时为了实现某些要求功能,需要各层间 的连接与导通,此时就需在铜箔上镀导通孔即
PTH(Plating Throught Hole)
板件从除油槽取出时,应注意滴液,尽量减少槽液带出 损失,已造成不必要的浪费和增加后清洗的困难度;
除油后水洗要充分,建议采用热水洗后,加1-2道自来 水洗;
清洁-调整剂对界面活性的调节机理
除胶渣后的孔壁表面
清洁后的孔壁表面
微蚀
成分及操作条件:
H2SO4 H2O2 NH2CH2NH2 温度 时间
预浸
注意点: 预浸液维护主要是槽液的比重和盐酸含量;槽液的
比重主要取决于亚锡离子和氯离子的含量,盐酸主 要是防止亚锡离子的水解和清洗板面氧化物; 预浸槽槽液一般按生产板平米数来添加更换,有时 也用铜含量作为参考控制项目,一般铜含量控制在1 克/升以下;开缸时多采用预浸液原液开缸,补充时 采用预浸盐; 板件从水洗槽取出进入预浸槽前,应注意减少滴水 带入,以免稀释预浸液,降低槽液酸度,造成亚锡 水解,槽液变混浊,同时也会污染活化槽;板件经 预浸槽后直接进入活化槽;
100mL/l 80ML/l 10g/l 20 ℃ ~30 ℃ 1~2min
微蚀
• 功能: a.除去铜表面的有机薄膜; b.微观粗化铜表面。
• 原理: Cu+ Cu2+ →2 Cu+ Cu++ H2O2 → Cu2++2OH-
微蚀
注意点: 微蚀槽生产主要是注意时间控制,一般时间在1-2分钟左右,时间过短,
除胶渣
成分及操作条件:
NaOH KMnO4 NaCIO 温度 时间
35g/l 55g/l 0.5g/l 75℃ 10min
除胶渣
• 功能:利用KMnO4的强氧化性,在高温及强碱条件下与树脂 发生化学反应,使其分解溶去。
• 原理:在高温碱性条件下,高锰酸钾使环氧树脂碳链氧化 裂解: 4MnO4-+C环氧树脂+4OH-→4MnO42-+CO2↑+2H2O 同时,高锰酸钾发生以下副反应: 4MnO4- +40H- = 4MnO42- + O2(g) + 2H2O MnO42-在碱性介质中也发生以下副反应: MnO42- + 2H2O + 2e- = MnO2(s) + 40HNACIO作为高膨松
• 功能:利用溶剂膨松软化树脂胶渣 • 原理:环氧树脂是高聚形化合物,具有优良的耐
蚀性。其腐蚀形式主要有溶解、溶胀和化学裂解 (如:浓硫酸对环氧树脂主要是溶解作用,其凹 蚀作用是十分明显的)。根据“相似相溶”的经 验规律,醚类有机物一般极性较弱,且有与环氧 树脂有相似的分子结构(R-O-R‘),所以对环氧 树脂有一定的溶解性。因为醚能与水发生氢键缔 合,所以在水中有一定的溶解性。因此,常用水 溶性的醚类有机物作为去钻污的溶胀剂。 • 注意点:溶胀液中的氢氧化钠含量不能太高,否则, 会破坏氢键缔合,使有机链相分离。
中和
成分及操作条件:
H2SO4 NaC2O4
温度 时间
100mL/l 30g/l
40--50℃ 5--7 min
中和
• 功能:除去残存在板面及孔壁死角处的MnO2 和高锰酸盐。
• 原理:锰离子是重金属离子,它的存在会引起 “钯中毒”,使钯离子或原子失去活化活性, 从而导致孔金属化的失败。因此,化学沉铜前 必须去除锰的存在。 在酸性介质中: