SHIPLEY化学沉铜
B[2].化学沉铜学习资料.pdf
![B[2].化学沉铜学习资料.pdf](https://img.taocdn.com/s3/m/2a0fed86e53a580216fcfe1f.png)
SHIPLEY
A ROHM AND HAAS COMPANY
预浸
简 介: a. 早期预活化是将二价锡对非导体底材作预
浸着过程。
b. Shipley改变传统工艺而闻名于世。
■ 微蚀深度: 40 -- 80u" ( 1 -- 2um )
SHIPLEY
A ROHM AND HAAS COMPANY
微蚀前后的铜面状况
微蚀前
SHIPLEY
A ROHM AND HAAS COMPANY
微蚀后
微蚀后的铜面状况
SHIPLEY
A ROHM AND HAAS COMPANY
微蚀中可能出现的问题
SHIPLEY
A ROHM AND HAAS COMPANY
简 介:
活化
钯液中的Pd,是以SnPd7Cl16胶团存在的。SnPd7Cl16 的产生 是 PdCl2与SnCl2在酸性环境中经一系列的反应而最后产生的。
活化工序就是让SnPd7Cl16 附着在孔壁表面形成进一步反应 的据点。
Shipley 活化剂44特点
温。
3. 称重,W1 。 4. 从除油剂开始. 进入P.T.H线,并于沉铜水洗后取出,重复
(2)步骤 。
5. 称重,W2 。 6. 计算:
厚度(u”) =
(W1 - W2) x 106 6 x 6 x 2 x 8.9 x 2.54
n 槽液污染 – Cu含量和氯含量的升高由氯化铜的带入所致.在活 化后需保证具有良好的水洗.
SHIPLEY
一种化学沉铜液的组成及其制备方法

一种化学沉铜液的组成及其制备方法化学沉铜液是一种常用的电镀工业中的电镀液,其中包含了多种化学物质。
本文将对一种化学沉铜液的组成进行分析,并介绍其制备方法。
首先,化学沉铜液的主要成分是铜离子和氧化剂。
常用的铜离子有Cu2+和Cu+两种,而常用的氧化剂有过氧化氢、过氧化钠、氧气等。
在化学沉铜液中,铜离子和氧化剂的比例是很重要的,如果这两者的比例不合理,就会影响沉铜液的效果。
此外,化学沉铜液中还含有其他的辅助成分。
例如,可以加入碳酸氢钠作为缓冲剂,调节沉铜液的pH值;可以加入表面活性剂,提高沉铜液的流动性和附着性;可以加入抑菌剂,防止沉铜液中的细菌生长。
这些辅助成分的添加量也是很重要的,如果过多或过少都会影响沉铜液的效果。
接下来,我们来介绍一种化学沉铜液的制备方法。
首先,需要准备好所有的原料,包括铜粉、过氧化氢、碳酸氢钠和表面活性剂。
然后,将所有原料放入一个容器中,并按照一定的比例进行混合。
在混合的过程中,需要注意控制温度,避免过高或过低的温度对沉铜液的质量造成影响。
接着,将混合好的沉铜液进行过滤,以去除杂质。
最后,将过滤后的沉铜液装入密封容器中,并进行贮存。
总的来说,化学沉铜液是一种复杂的化学溶液,其组成包括铜离子和氧化剂,以及多种辅助成分。
在制备过程中,需要注意各种成分的比例和添加量,以及温度的控制。
只有这样,才能得到质量优良的化学沉铜液,从而满足电镀工业的需求。
化学沉铜液是电镀工业中的重要原料,其质量的好坏直接关系到电镀的效果。
本文介绍了一种化学沉铜液的组成和制备方法,并强调了在制备过程中应注意各种成分的比例和添加量,以及温度的控制。
希望这些内容能够对读者有所帮助,为制备优质的化学沉铜液提供参考。
Shipley化学沉铜与电镀简介

Shipley Acc19加速剂是HBF4型加速剂
SnCl2 + 2HBF4 Sn(OH)4 + 4HBF4 Sn(OH)Cl + 2HBF4 反应过程宜适可而止 Sn(BF4)2 + 2HCl Sn(BF4)4 + 4H2O Sn(BF4)2 + HCl + H2O
加速剂后的孔壁表面
化学沉铜
电镀铜的原理
直流 整流器
nene-
+
阳极 离子交换
电镀上铜层 阴极 (受镀物件) 镀槽
Cu
Cu2+ + 2e-
Cu2+ + 2e-
Cu
电镀液组成(H2O+CuSO4.5H2O+H2SO4+Cl +添加剂)
-
酸性鍍銅液各成分及特性簡介
酸性鍍銅液成分
— 硫酸銅(CuSO4.5H2O) — 硫酸 (H2SO4)
电镀液组成(H2O+SnSO4+H2SO4+添加剂)
电镀锡工艺
Ronastan EC 鍍純錫主要成份作用
— SnSO4 主鹽,提供 Sn2+ — H2 SO4 提供導電性,提高极化作用,提供一個較強的酸性 環境,防止錫离子水解。 — Part A 是一种光亮劑,可以鍍出細致、均勻的錫層 — Part B 分散劑、溶劑,是一种表面活性劑,可以增加 Part A 的溶解度
反应式:
CuSO4 + 2HCHO + 4NaOH Cu + Na2SO4 + 2HCOONa + 2H2O + H2
沉积化学铜后的孔壁表面
电镀铜工艺的功能
化学沉铜原理及异常 共42页

调整
• 成份:清洁-调整剂 DI水 • 功能:除去板面轻微氧化物及轻微污渍,
对树脂界面活性调整有极好的效果; 直接影响沉铜的背光效果. • 原理:酸性溶液,与氧化物反应而使之溶 去;有机清洁剂,对有机油污具有 溶解作用.整孔性高分子吸附于孔壁表面 使孔壁表面显正电性.
通孔横截面模型
PTH的方式
• 黑孔(Black Hole)+电镀 • 化学沉铜+电镀
化学沉铜原理介绍
流程简介
膨松→除胶渣→中和 Desmear
调整→清洁→调整剂→微蚀→ 预浸→活化→加速→化铜 PTH
膨松
成分及操作条件:
NaOH 已二醇乙醚 已二醇 水 温度 时间
20g/l 30/l 2g/l 其余 60-80℃ 5min
调整
注意点:
应根据生产板面积累加来及时补充药品,达到一定产量 后,槽液需要更换,重新开缸;
过滤系统:一般建议除油槽加装过滤系统,不仅可以有 效过滤槽液中的粉尘杂质,同时也可有效搅拌槽液,增 强槽液对孔壁的清洗调整效果;滤芯一般使用5~10um 的PP滤芯,每小时过滤4-6次;
板面经除油水洗后,应该没有油污,氧化斑存在,即为 除油效果良好;
微蚀前后的铜面状况
微蚀前
微蚀后
预浸
成分及操作条件:
主要成分: HCL 、SnCL2 aq 比重: 1.120--1.150 温度: 常温 时间: 1--2 min
化学沉铜原理及异常

化学沉铜原理介绍
流程简介
膨松→除胶渣→中和 Desmear
调整→清洁→调整剂→微蚀→ 预 浸→活化→加速→化铜 PTH
膨松
成分及操作条件:
NaOH 已二醇乙醚 已二醇 水 温度 时间
20g/l 30/l 2g/l 其余 60-80℃ 5min
膨松
• 功能:利用溶剂膨松软化树脂胶渣 • 原理:环氧树脂是高聚形化合物,具有优良的耐
加速反应
注意点: 解胶液主要是控制槽液浓度,时间控制在5分钟左右,
冬天应注意温度控制; 解胶液的更换一般也按生产板的平米数添加更换,
除此之外,解胶液的铜含量也作为一个参考监测项 目,铜含量一般控制在0.7克/升以下; 板件从水洗进入解胶槽或从解胶槽取出时应注意滴 水充分,保证槽液和生产的稳定性;板面水洗后, 颜色应均匀,无明显孔口流液痕迹;
粗化效果不良,板面发花或粗化深度不够,沉铜电镀后,铜层结合力不足, 易产生起泡脱皮现象;粗化过度,孔口铜基材很容易被蚀掉,形成孔口露 基材,造成不必要的报废;另外槽液的温度特别是夏天,一定要注意,温 度太高,粗化太快或温度太低,粗化太慢或不足都会产生上述质量缺陷; 微蚀槽如使用过硫酸盐体系时,铜含量一般控制在25克/升以下,铜含量 太高,会影响粗化效果和微蚀速率;另外过硫酸盐的含量应控制在80— 120克/升; 微蚀槽在开缸时,应留约1/4的旧槽液,以保证槽液中有适量的铜离子, 避免新开缸槽液粗化速率太快,过硫酸盐补充应按50平米/3—6公斤来及 时补充;另外微蚀槽负载不宜过大,亦即开缸时应尽量开大些,防止槽液 因负载过大而造成槽液温度升高过快,影响板面粗化效果; 板面经微蚀处理后,颜色应为均匀粉红色;否则说明除油不足或除油后水 洗不良或粗化不良(可能是时间不足,微蚀剂浓度太低,槽液铜含量太高 等原因造成),应及时检查反馈并处理; 板件从水洗槽进入微蚀槽应注意滴水,尽量减少滴水带入,造成槽液稀释 和温度变化过大,同时板件从微蚀槽取出时,也应注意滴液时间充分;
化学沉铜原理及异常

板件从除油槽取出时,应注意滴液,尽量减少槽液带出 损失,已造成不必要的浪费和增加后清洗的困难度;
除油后水洗要充分,建议采用热水洗后,加1-2道自来 水洗;
清洁-调整剂对界面活性的调节机理
除胶渣后的孔壁表面
清洁后的孔壁表面
微蚀 成分及操作条件:
培训大纲
1.PTH介绍 2.化学沉铜原理介绍 3.化学沉铜异常及处理
PTH简要介绍
双面板或多层复合板各层铜箔之间原本是绝 缘层,有时为了实现某些要求功能,需要各层间 的连接与导通,此时就需在铜箔上镀导通孔即
PTH(Plating Throught Hole)
通孔横截面模型
PTH的方式
• 黑孔(Black Hole)+电镀 • 化学沉铜+电镀
预浸
注意点: 预浸液维护主要是槽液的比重和盐酸含量;槽液的
比重主要取决于亚锡离子和氯离子的含量,盐酸主 要是防止亚锡离子的水解和清洗板面氧化物; 预浸槽槽液一般按生产板平米数来添加更换,有时 也用铜含量作为参考控制项目,一般铜含量控制在1 克/升以下;开缸时多采用预浸液原液开缸,补充时 采用预浸盐; 板件从水洗槽取出进入预浸槽前,应注意减少滴水 带入,以免稀释预浸液,降低槽液酸度,造成亚锡 水解,槽液变混浊,同时也会污染活化槽;板件经 预浸槽后直接进入活化槽;
化学沉铜原理介绍
流程简介
膨松→除胶渣→中和 Desmear
调整→清洁→调整剂→微蚀→ 预 浸→活化→加速→化铜 PTH
膨松
成分及操作条件:
NaOH 已二醇乙醚 已二醇 水 温度 时间
20g/l 30/l 2g/l 其余 60-80℃ 5min
化学沉铜

一.沉铜的目的与作用:在已钻孔的不导电的孔壁基材上,用化学的方法沉积上一层薄薄的化学铜,以作为后面电镀铜的基底;二.工艺流程:碱性除油→二或三级逆流漂洗→粗化(微蚀)→二级逆流漂洗→预浸→活化→二级逆流漂洗→解胶→二级逆流漂洗→沉铜→二级逆流漂洗→浸酸三.流程说明:(一)碱性除油①作用与目的:除去板面油污,指印,氧化物,孔内粉尘;对孔壁基材进行极性调整(使孔壁由负电荷调整为正电荷)便于后工序中胶体钯的吸附;②多为碱性除油体系,也有酸性体系,但酸性除油体系较碱性除油体系无论除油效果,还是电荷调整效果都差,表现在生产上即沉铜背光效果差,孔壁结合力差,板面除油不净,容易产生脱皮起泡现象。
③碱性体系除油与酸性除油相比:操作温度较高,清洗较困难;因此在使用碱性除油体系时,对除油后清洗要求较严④除油调整的好坏直接影响到沉铜背光效果;(二)微蚀:①作用与目的:除去板面的氧化物,粗化板面,保证后续沉铜层与基材底铜之间良好的结合力;新生成的铜面具有很强的活性,可以很好吸附胶体钯;②粗化剂:目前市场上用的粗化剂主要用两大类:硫酸双氧水体系和过硫酸体系,硫酸双氧水体系优点:溶铜量大,(可达50g/L),水洗性好,污水处理较容易,成本较低,可回收,缺点:板面粗化不均匀,槽液稳定性差,双氧水易分解,空气污染较重过硫酸盐包括过硫酸钠和过硫酸铵,过硫酸铵较过硫酸钠贵,水洗性稍差,污水处理较难,与硫酸双氧水体系相比,过硫酸盐有如下优点:槽液稳定性较好,板面粗化均匀,缺点:溶铜量较小(25g/L)过硫酸盐体系中硫酸铜易结晶析出,水洗性稍差,成本较高;③另外有杜邦新型微蚀剂单过硫酸氢钾,使用时,槽液稳定性好,板面粗化均匀,粗化速率稳定,不受铜含量的影响,操作简单,适宜于细线条,小间距,高频板等(三)预浸/活化:⑤预浸目的与作用:主要是保护钯槽免受前处理槽液的污染,延长钯槽的使用寿命,主要成分除氯化钯外与钯槽成份一致,可有效润湿孔壁,便于后续活化液及时进入孔内活化使之进行足够有效的活化;⑥预浸液比重一般维持在18波美度左右,这样钯槽就可维持在正常的比重20波美度以上;⑦活化的目的与作用:经前处理碱性除油极性调整后,带正电的孔壁可有效吸附足够带有负电荷的胶体钯颗粒,以保证后续沉铜的均匀性,连续性和致密性;因此除油与活化对后续沉铜的质量起着十分重要的作用,⑧生产中应特别注意活化的效果,主要是保证足够的时间,浓度(或强度)⑨活化液中的氯化钯以胶体形式存在,这种带负电的胶体颗粒决定了钯槽维护的一些要点:保证足够数量的亚锡离子和氯离子以防止胶体钯解胶,(以及维持足够的比重,一般在18 波美度以上)足量的酸度(适量的盐酸)防止亚锡生成沉淀,温度不宜太高,否则胶体钯会发生沉淀,室温或35度以下;(四)解胶:⑩作用与目的:可有效除去胶体钯颗粒外面包围的亚锡离子,使胶体颗粒中的钯核暴露出来,以直接有效催化启动化学沉铜反应,? 原理:因为锡是两性元素,它的盐既溶于酸又溶于碱,因此酸碱都可做解胶剂,但是碱对水质较为敏感,易产生沉淀或悬浮物,极易造成沉铜孔破;盐酸和硫酸是强酸,不仅不利与作多层板,因为强酸会攻击内层黑氧化层,而且容易造成解胶过度,将胶体钯颗粒从孔壁板面上解离下来;一般多使用氟硼酸做主要的解胶剂,因其酸性较弱,一般不造成解胶过度,且实验证明使用氟硼酸做解胶剂时,沉铜层的结合力和背光效果,致密性都有明显提高;(五)沉铜? 作用与目的:通过钯核的活化诱发化学沉铜自催化反应,新生成的化学铜和反应副产物氢气都可以作为反应催化剂催化反应,使沉铜反应持续不断进行。
化学沉铜
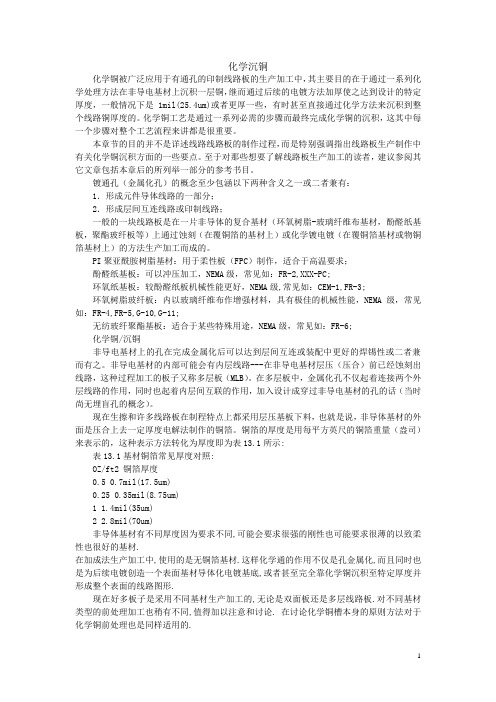
化学沉铜化学铜被广泛应用于有通孔的印制线路板的生产加工中,其主要目的在于通过一系列化学处理方法在非导电基材上沉积一层铜,继而通过后续的电镀方法加厚使之达到设计的特定厚度,一般情况下是1mil(25.4um)或者更厚一些,有时甚至直接通过化学方法来沉积到整个线路铜厚度的。
化学铜工艺是通过一系列必需的步骤而最终完成化学铜的沉积,这其中每一个步骤对整个工艺流程来讲都是很重要。
本章节的目的并不是详述线路线路板的制作过程,而是特别强调指出线路板生产制作中有关化学铜沉积方面的一些要点。
至于对那些想要了解线路板生产加工的读者,建议参阅其它文章包括本章后的所列举一部分的参考书目。
镀通孔(金属化孔)的概念至少包涵以下两种含义之一或二者兼有:1.形成元件导体线路的一部分;2.形成层间互连线路或印制线路;一般的一块线路板是在一片非导体的复合基材(环氧树脂-玻璃纤维布基材,酚醛纸基板,聚酯玻纤板等)上通过蚀刻(在覆铜箔的基材上)或化学镀电镀(在覆铜箔基材或物铜箔基材上)的方法生产加工而成的。
PI聚亚酰胺树脂基材:用于柔性板(FPC)制作,适合于高温要求;酚醛纸基板:可以冲压加工,NEMA级,常见如:FR-2,XXX-PC;环氧纸基板:较酚醛纸板机械性能更好,NEMA级,常见如:CEM-1,FR-3;环氧树脂玻纤板:内以玻璃纤维布作增强材料,具有极佳的机械性能,NEMA级,常见如:FR-4,FR-5,G-10,G-11;无纺玻纤聚酯基板:适合于某些特殊用途,NEMA级,常见如:FR-6;化学铜/沉铜非导电基材上的孔在完成金属化后可以达到层间互连或装配中更好的焊锡性或二者兼而有之。
非导电基材的内部可能会有内层线路---在非导电基材层压(压合)前已经蚀刻出线路,这种过程加工的板子又称多层板(MLB)。
在多层板中,金属化孔不仅起着连接两个外层线路的作用,同时也起着内层间互联的作用,加入设计成穿过非导电基材的孔的话(当时尚无埋盲孔的概念)。
沉铜

化学镀铜(PTH)Chapter 1 沉铜原理(Shipley)一概述化学镀铜:俗称沉铜,是一种自身催化氧化还原反应,可以在非导电的基体上进行沉积,化学镀铜的作用是实现孔金属化,从而使双面板,多层板实现层与层之间的互连,随着电子工业的飞速发展对线路板制造业的要求越来越高,线路板的层次越来越多,同一块板的孔数越来越多,孔径越来越小,这些孔的金属化质量将直接影响到电气的性能和和可靠性。
二去钻污原理:1 去钻污的必要性:由于钻孔过程钻嘴的转速很高,可达16~~18万rpm,而环氧玻璃基材为不良导体,钻孔时会在短时间内产生高温,高温会在孔壁上留下许多树脂残渣,从而形成一层薄的环氧树脂钻污,由于此树脂钻污与孔壁的结合力不牢,当直接沉铜时,就会影响化学铜与孔壁的结合力,特别是多层板,会影响化学铜层与内层铜的导通,去钻污就是清除这些残渣,改善孔壁结构。
2 去钻污方法的选择:利用碱性KMnO4溶液作强氧化剂,在高温下将孔壁树脂氧化,这种处理不仅可以除掉这些钻污,而且还可以改善孔壁树脂表面结构,经过碱性KMnO4处理后的树脂表面被微蚀形成许多孔隙,呈蜂窝状,这样大大促进了化学铜与孔壁树脂的结合力,此法是目前去钻污流程使用最广泛的方法,具有高稳定性,既经济又高效,管理操作简便。
3 去钻污原理:①溶胀:Swelling利用有机溶剂渗入到孔壁的树脂中,使其溶胀,形成结构疏松的环氧树脂,从而有利于碱性KMnO4的氧化除去,一般的溶胀剂都是有机物,反应条件要求高温及碱性环境。
需采用不锈钢工作液槽。
MLB211膨胀剂是淡黄色,不混浊,不易燃的水溶液,含有有机物(10%左右的已烯基丁二醇—丁乙酸),对树脂有一定的溶解作用,但主要作用是使环氧树脂溶胀,溶胀剂不与树脂起直接反应,但随着长时间的高温处理,溶胀剂易老化而需更换,换缸视生产量而定,一般为6000m2/次。
②去钻污Desmearing:反应原理:在碱性及高温条件下,KMnO4对溶胀的树脂起氧化作用。
化学沉铜工艺知识讲解
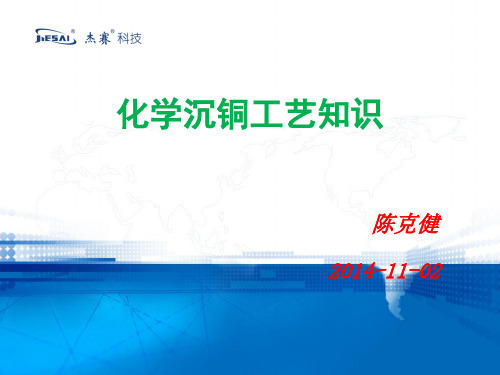
三、工艺流程简介-Desmear
再生电极:
结构截面示意图
电解再生器外观图
再生原理
第 13 页
三、工艺流程简介-Desmear
3.3.3 MLB 中和剂216(酸性强还原剂)
作用: 能将残存在板面或孔壁死角处的二氧化锰或高锰酸盐中和除去;
第 14 页
三、工艺流程简介-沉铜工艺
4. 沉铜工艺 4.2 设备要求 4.1 流程
Before PTH
After PTH
After Plating
第 3 页
二、工艺流程
plamsa 磨板
等离子处理 Deburr 去毛刺
特殊板材的除胶渣、表面活化. 去除孔口披风、清洗孔内粉尘 使孔壁上的胶渣软化、膨松. 溶解孔壁少量树脂及粘附孔壁内的胶渣。 将除胶渣后残留的高锰酸钾盐除去. 除掉铜表面轻微的手印、油渍、氧化等 使孔壁呈正电荷后,提高孔壁对钯的吸附 粗化铜箔表面,增强铜面与孔化之间的结合 防止板子带杂质、水分进入昂贵的活化槽 使胶体钯微粒均匀吸附到板面和孔壁上 剥去胶体钯微粒外层的Sn+4外壳,露出 钯核, 形成孔化时的反应中心 。
3.3.1 MLB 膨松剂 211
使孔壁上的胶渣得以软化,膨松并渗入树脂聚合后之交联处,从而降低其键结 的能量,使易于进行树脂的溶解。
第 11 页
三、工艺流程简介-Desmear
3.3.2 MLB 除钻污剂 214(主要成分高锰酸钾+液碱)
作用:
高锰酸钾具有强氧化性,在高温及强碱的条件下,与树脂发生化学反 应使其分解溶去。
放大镜
光 源
第 28 页
第 24 页
(我司采用)
三、工艺流程简介-沉铜工艺
化学沉铜工艺
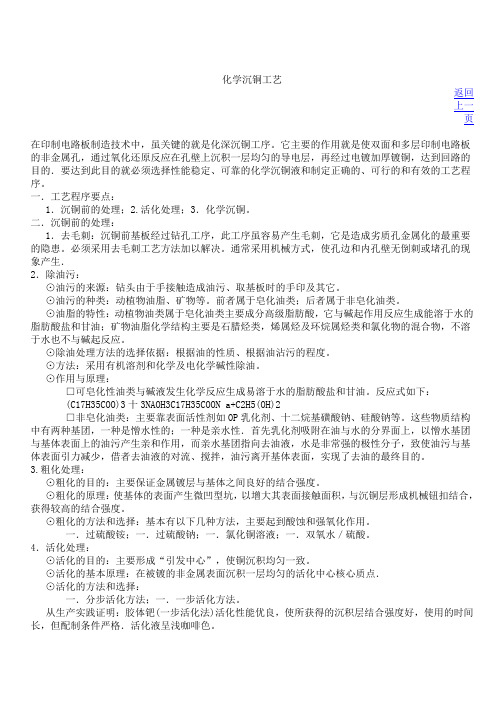
化学沉铜工艺返回上一页在印制电路板制造技术中,虽关键的就是化深沉铜工序。
它主要的作用就是使双面和多层印制电路板的非金属孔,通过氧化还原反应在孔壁上沉积一层均匀的导电层,再经过电镀加厚镀铜,达到回路的目的.要达到此目的就必须选择性能稳定、可靠的化学沉铜液和制定正确的、可行的和有效的工艺程序。
一.工艺程序要点:1.沉铜前的处理;2.活化处理;3.化学沉铜。
二.沉铜前的处理:1.去毛刺:沉铜前基板经过钻孔工序,此工序虽容易产生毛刺,它是造成劣质孔金属化的最重要的隐患。
必须采用去毛刺工艺方法加以解决。
通常采用机械方式,使孔边和内孔壁无倒刺或堵孔的现象产生.2.除油污:⊙油污的来源:钻头由于手接触造成油污、取基板时的手印及其它。
⊙油污的种类:动植物油脂、矿物等。
前者属于皂化油类;后者属于非皂化油类。
⊙油脂的特性:动植物油类属于皂化油类主要成分高级脂肪酸,它与碱起作用反应生成能溶于水的脂肪酸盐和甘油;矿物油脂化学结构主要是石腊烃类,烯属烃及环烷属烃类和氯化物的混合物,不溶于水也不与碱起反应。
⊙除油处理方法的选择依据:根据油的性质、根据油沾污的程度。
⊙方法:采用有机溶剂和化学及电化学碱性除油。
⊙作用与原理:□可皂化性油类与碱液发生化学反应生成易溶于水的脂肪酸盐和甘油。
反应式如下:(C17H35COO)3十3NAOH3C17H35COON a+C2H5(OH)2□非皂化油类:主要靠表面活性剂如OP乳化剂、十二烷基磺酸钠、硅酸钠等。
这些物质结构中有两种基团,一种是憎水性的;一种是亲水性.首先乳化剂吸附在油与水的分界面上,以憎水基团与基体表面上的油污产生亲和作用,而亲水基团指向去油液,水是非常强的极性分子,致使油污与基体表面引力减少,借者去油液的对流、搅拌,油污离开基体表面,实现了去油的最终目的。
3.粗化处理:⊙粗化的目的:主要保证金属镀层与基体之间良好的结合强度。
⊙粗化的原理:使基体的表面产生微凹型坑,以增大其表面接触面积,与沉铜层形成机械钮扣结合,获得较高的结合强度。
化学镀铜(沉铜)技术

2021/10/13
h
7
常用的粗化液配方如下: H2SO4 150-200g/1 H202 30-35g/1 稳定剂适量 操作条件可以室温,也可以加热 H2SO4/H202对铜的蚀刻速率快慢,主要取决于所采用的稳定剂类型。
铜在H2SO4/H202溶液 中反响式如下: Cu+H2O2+H2SO4=CuSO4+2H2O 如果不加稳定剂,溶解的铜离子会使H2O2迅速分解: 2H2O2 CU+2 2H2O+ O2 ↑ 参加稳定剂不但可阻止H2O2分解,而且可以改变蚀刻铜的速率。设不
配制后的B液不要求全部溶解。 将A与B液混合,搅拌至全部溶解。然后在450C恒温水浴中处理3小时,
最后加去离子水稀释至1升即可使用。
2021/10/13
h
13
2〕胶体钯活化液反响机理 胶体钯活化液的活性和稳定性取决于A液中Sn2+/Pd2+离子浓度比值,以及溶液的配制
方法。Sn2+离子和Pd2+离子浓度比为2:1时,所得到的活化液活化性能最好。这是由 于不同浓度的Sn+2/Pd+2比,所产生的化学反响不同。当A组液中Sn2+/Pd2+比值为2:1 时,Sn+2和Pd+2在溶液中反响形成不稳定的络合物。 Pd2++2Sn2+ 〔PdSn〕2+ 〔PdSn〕2+ Pd0+ Sn4+ + Sn2+ 在300C条件下〔PdSn〕2+络合物离子歧化反响12分钟,大约有90%以上的络合物离子 被复原成金属钯,它们呈现是极其细小的金属颗粒分散在溶液中,如果此时参加过量 的Sn2+和CL-,那么这些细小的钯核外表上很快吸附大量的Sn2+离子和CL-离子,形成带 负电性的胶体化合物Pd〔SnCL3〕n-。这些胶体化合物悬浮在水溶液中。因为它们都是 带负电的胶团,在水溶液中互相碰撞呈布朗运动状态,因而不会聚沉。印制板活化处 理之后在水洗时由于SnCL2水解形成碱式锡酸盐沉淀。
化学沉铜介绍演示幻灯片
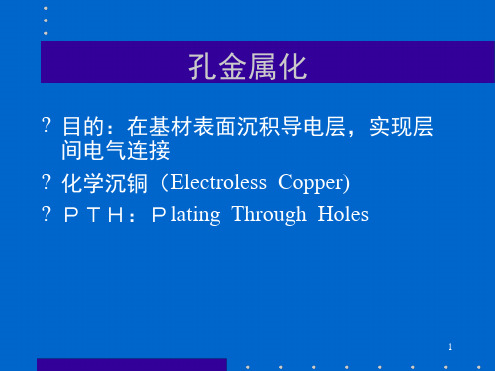
? MnO4+C+OH ? MnO42-+CO2+2H2O
? 副反应: MnO4-+OH-? MnO42-+O2+2H2O
?
MnO42-+H20 ? MnO2+O2+2OH-
工艺控制: 温度75-85°C
?
时间10-20 min
6
中和(Reducing)
? 目的:将残留于孔壁的MnO4-、MnO42-、
?
合良好.
?
2. 改善孔壁结构,加强结合力.
? 工艺流程: 溶胀 ? 去钻污 ? 中和
4
溶胀(Swelling)
? 目的: 使树脂表面膨胀,降低分子键能,利
?
于去钻污反应的进行.
? 工艺控制: 温度60-80°C
?
时间5-10 min
5
去钻污(Desmearing)
? 目的:利用KMnO4的强氧化性,将钻污除去 ? 反应原理:
? 目的:1. 清洁板面
?
2. 板面形成粗糙结构,保证沉铜层
?
与基材铜的结合力.
? 反应原理:Cu+Na2S2O8 ? CuSO4+Na2SO4 ? 工艺控制:温度25-35°C
?
时间1-3 min
10
预浸(Predip)
? 目的: 防止前工位处理对催化槽的污染
? 工艺控制:温度 常温
?
时间1-2 min
22
碳黑系列
? 常见工艺流程: ? (去钻污处理) ? 清洁 ? 整孔 ? 黑孔
化 ? 干燥 ? 微蚀准备 ? 微蚀 ? 水洗 ? 供应商:MacDermid、Electro-chemical等 ? 适用设备:水平线及垂直线
化学镀铜沉铜工艺流程介绍
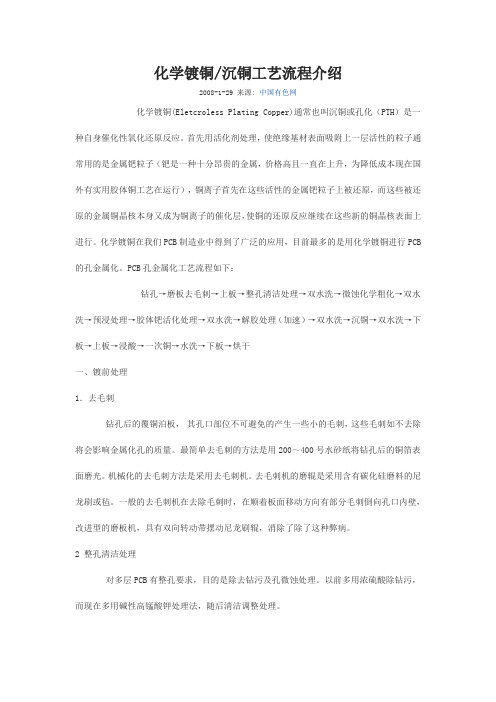
化学镀铜/沉铜工艺流程介绍2008-1-29 来源: 中国有色网化学镀铜(Eletcroless Plating Copper)通常也叫沉铜或孔化(PTH)是一种自身催化性氧化还原反应。
首先用活化剂处理,使绝缘基材表面吸附上一层活性的粒子通常用的是金属钯粒子(钯是一种十分昂贵的金属,价格高且一直在上升,为降低成本现在国外有实用胶体铜工艺在运行),铜离子首先在这些活性的金属钯粒子上被还原,而这些被还原的金属铜晶核本身又成为铜离子的催化层,使铜的还原反应继续在这些新的铜晶核表面上进行。
化学镀铜在我们PCB制造业中得到了广泛的应用,目前最多的是用化学镀铜进行PCB的孔金属化。
PCB孔金属化工艺流程如下:钻孔→磨板去毛刺→上板→整孔清洁处理→双水洗→微蚀化学粗化→双水洗→预浸处理→胶体钯活化处理→双水洗→解胶处理(加速)→双水洗→沉铜→双水洗→下板→上板→浸酸→一次铜→水洗→下板→烘干一、镀前处理1.去毛刺钻孔后的覆铜泊板,其孔口部位不可避免的产生一些小的毛刺,这些毛刺如不去除将会影响金属化孔的质量。
最简单去毛刺的方法是用200~400号水砂纸将钻孔后的铜箔表面磨光。
机械化的去毛刺方法是采用去毛刺机。
去毛刺机的磨辊是采用含有碳化硅磨料的尼龙刷或毡。
一般的去毛刺机在去除毛刺时,在顺着板面移动方向有部分毛刺倒向孔口内壁,改进型的磨板机,具有双向转动带摆动尼龙刷辊,消除了除了这种弊病。
2 整孔清洁处理对多层PCB有整孔要求,目的是除去钻污及孔微蚀处理。
以前多用浓硫酸除钻污,而现在多用碱性高锰酸钾处理法,随后清洁调整处理。
孔金属化时,化学镀铜反应是在孔壁和整个铜箔表面上同时发生的。
如果某些部位不清洁,就会影响化学镀铜层和印制导线铜箔间的结合强度,所以在化学镀铜前必须进行基体的清洁处理。
最常用的清洗液及操作条件列于表如下:清洗液及操作条件配方组分 1 2 3碳酸钠(g/l) 40~60 ——磷酸三钠(g/l) 40~60 ——OP乳化剂(g/l) 2~3 ——氢氧化钠(g/l)— 10~15 —金属洗净剂(g/l)—— 10~15温度(℃) 50 50 40处理时间(min) 3 3 3搅拌方法空气搅拌机械移动空气搅拌机械移动空气搅拌机械移动3.覆铜箔粗化处理利用化学微蚀刻法对铜表面进行浸蚀处理(蚀刻深度为2-3微米),使铜表面产生凹凸不平的微观粗糙带活性的表面,从而保证化学镀铜层和铜箔基体之间有牢固的结合强度。
一种化学沉铜液的配方[发明专利]
![一种化学沉铜液的配方[发明专利]](https://img.taocdn.com/s3/m/2c97c146b0717fd5370cdc54.png)
专利名称:一种化学沉铜液的配方专利类型:发明专利
发明人:杨彦涛
申请号:CN201410498947.X 申请日:20140926
公开号:CN104278259A
公开日:
20150114
专利内容由知识产权出版社提供
摘要:本发明公开了一种化学沉铜液的配方,硫酸铜9-12g/L,乙二胺四乙酸二钠30-32g/L,四羟丙基乙二胺15-16g/L,氢氧化钠12-15g/L,铁氰化钾0.09-0.1g/L,亚铁氰化钾0.01-0.03g/L,甲醛12-15g/L,提供了一种稳定性高,具有良好延伸率的一种化学沉铜液的配方。
申请人:无锡长辉机电科技有限公司
地址:214192 江苏省无锡市锡山经济技术开发区芙蓉中三路99号
国籍:CN
代理机构:南京苏高专利商标事务所(普通合伙)
代理人:成立珍
更多信息请下载全文后查看。
- 1、下载文档前请自行甄别文档内容的完整性,平台不提供额外的编辑、内容补充、找答案等附加服务。
- 2、"仅部分预览"的文档,不可在线预览部分如存在完整性等问题,可反馈申请退款(可完整预览的文档不适用该条件!)。
- 3、如文档侵犯您的权益,请联系客服反馈,我们会尽快为您处理(人工客服工作时间:9:00-18:30)。
电镀铜层的作用 – 作为孔的化学沉铜层的加厚层,通过全板镀铜达到厚度5-8微米, . 称为加厚 铜. – 作为图形电镀锡或镍的底层,其厚度可达20-25微米,称为图形镀 铜. 电镀铜的原理 直流 整流器 nene- + 阳极 离子交换 电镀上铜层 阴极 (受镀物件) 镀槽 Cu Cu2+ + 2e- Cu2+ + 2e- Cu 电镀液组成(H2O+CuSO4.5H2O+H2SO4+Cl +添加剂) - 酸性鍍銅液各成分及特性簡介 酸性鍍銅液成分 — — — 硫酸銅(CuSO4.5H2O) 硫酸 (H2SO4) g 氯離子(Cl-) — 添加劑 酸性鍍銅液各成分功能 — CuSO4.5H2O :主要作用是提供電鍍所需Cu2+及提高導電能力 — H2SO4 — Cl— 添加劑 :主要作用是提高鍍液導電性能,提高通孔電鍍的均勻性。 :主要作 用是幫助陽極溶解,協助改善銅的析出,結晶。 :主要作用是改善均鍍和深鍍性能, 改善鍍層結晶細密性。 PCB电镀铜工艺过程 PCB电镀铜工艺过程 g 图形电镀铜/ 图形电镀铜/锡工艺过程 酸性除油 水洗 微蝕 水洗 浸酸 鍍銅 水洗/ 浸酸 鍍錫 水洗 烘干 图形电镀铜/锡工艺过程 图形电镀铜 锡工艺过程 — 酸性除油 酸性除油的主要作用為除去 D/F 殘渣, 此殘渣為 D/F 和銅面賴 以結合的膠類 殘留, 其次為除去輕度氧化及輕度污漬和手印。 图形电镀铜/锡工艺过程 图形电镀铜 锡工艺过程 g 流程说明 — 浸 酸(10%硫酸) (10%硫酸 硫酸) 除去經過水洗后板面產生的輕微氧化,此酸 通常為 10%。 图形电镀铜/锡工艺过程 图形电镀铜 锡工艺过程 g 流程说明 — 电镀铜 使 用 Shipley Copper Gleam PCM Plus/125T-2/125TAB/2001/ST-9
p它杂质。 除去板子铜面上的氧化物及其它杂 质。 粗化铜表面,增强铜面与电解铜的齿结能 粗化铜表面, 力。 微蚀前后的铜面状况 微蚀前 微蚀后 预浸 简 介: a. 早期预活化是将二价锡对非导体底材作 预浸着过程。 预浸着过程 。 b. Shipley改变传统工艺而闻名于世。 Shipley改变传统工艺而闻名于世。 改变 传统工艺而闻名于世 作 用: 防止板子带杂质污物进入昂贵的钯槽。 a. 防止板子带 杂质污物进入昂贵的钯槽。 b. 防止板面太多的水量带入钯槽而导致局 部水解。 部 水解。 预活化槽与活化槽除了无钯之外, 预活化槽与活化槽除了无钯之外,其它完 全一致 。 简 介: 活化 胶团存在的。 钯液中的Pd,是以SnPd7Cl16胶团存在的。SnPd7Cl16 的产生 钯 液中的 是以 在酸性环境中经一系列的反应而最后产生的。 是 PdCl2与SnCl2在酸性 环境中经一系列的反应而最后产生的。 活化工序就是让S 活化工序就是让 nPd7Cl16 附着在孔壁表面形成进一步反应 的据点。 的据点。 活化剂44 44特点 Shipley 活化剂44特点 无烟。无腐蚀性烟,操作安全。 无烟。无腐蚀性烟,操作安全。 对多层板的黑 化层冲击小不包HCl 不包HCl。 对多层板的黑化层冲击小不包HCl。 极细的粒子,使 金属的沉积细而密,镀层可靠性强。 极细的粒子,使金属的沉积细而密,镀层可靠性 强。 操作稳定,使用寿命长。 操作稳定,使用寿命长。 操作及控制 维持亚锡与钯间的精巧平衡, 维持亚锡与钯间的精巧平衡,不可鼓气及任何漏 气现象存在 。 控制其处理时间,以防活化过强及过弱。 控制其处理时间,以防活化 过强及过弱。 活化后的孔壁 活化后的孔壁表面 加速剂 作 用: 剥去P 外层的S 外壳,露出P 金属; 剥去 d外层的 n+4外壳,露出 d金属; 清 除松散不实的钯团或钯离子、原子等。 清除松散不实的钯团或钯离子、原子等。 原 理: 钯胶团粘附的板子,在经水洗之后, 粒之外会形成S 钯胶团粘附的板子,在经 水洗之后,Pd粒之外会形成 n(OH)4 等外壳。 等外壳。 Sn(OH)4 Sn(OH)4 Snu2 Snu2Sn(OH)4 Snu2 Sn(OH) S nu 2 Sn(OH)4 4 S nu 2 S nu 2 Sn(OH)4 Sn(OH)4 Pd S nu 2 S nu 2 Acc19加速剂是 加速剂是HBF Shipley Acc19加速剂是HBF4型加速剂 SnCl2 + 2 HBF4 Sn(BF4)2 + 2HCl Sn(OH)4 + 4HBF4 Sn(BF4)4 + 4H2O Sn(OH)Cl + 2HBF4 Sn(B F4)2 + HCl + H2O 反应过程宜适可而止 加速剂后的孔壁表面 化学沉铜 化学沉铜的类型: a. 薄 铜:10  ̄ 20u" (0.25  ̄ 0.5um) 如: C/P 253 C/M2 4 b. 中速铜:40  ̄ 60u " (1  ̄ 1.5um) c. 厚化铜:80  ̄ 100u "(2  ̄ 2.5um) 组成 成份: 硫酸铜、氢氧化钠、甲醛、EDTA(乙二胺四乙酸二钠)。 或罗谢尔盐(四水合酒石 酸钾钠)。 如: C/P 250 如: C/P 251 反应式: CuSO4 + 2HCHO + 4NaOH → Cu + Na2SO4 + 2HCOONa + 2H2O + H2 ↑ 沉积化学铜后的孔壁表面 电镀铜工艺的功能
化学铜再电铜加厚后之切片放大图 化学铜再电铜加厚后之切片放大图 垂直电镀铜生产线 水平电镀铜生产线 Pro Bond 80/484 黑化与后浸的目的 Pro Bond 80/484氧化 氧 – 增强多层板的内层附着力. – 产生高的铜--树脂结合强度. PB Oxide Converter 后浸 – 将Pro Bond 80/484氧化膜表面转化为可抵制粉红 圈形成的结构. PTH ? ? ? ? ? ? ? ? ? ? CUPOSIT CLEANER CONDITIONER 清洁调整剂 1175A CUPO SIT CLEANER CONDITIONER 清洁调整剂 231 CUPOSIT CLEANER CONDITIONER 清洁调整 剂 233 CUPOSIT CLEANER CONDITIONER 除油-调整剂 3320 PREPOEIT? ETCH 微蚀剂 746W CATAPOSIT CATALYST 催化剂 44 CUPOSIT ACCELERATOR 加速剂 19 ANTI-TRANI SH 防氧化剂 7130 CUPOSIT 化学铜 253 CUPOSIT 化学铜 250 CUPOSIT 化学铜 385 DESMEAR ? ? ? ? ? CIRCUPOSIT? CIRCUPOSIT? CIRCUPOSIT? CIRCUPOSIT? CIRCUPOSIT? CIRCUPOSIT? MLB 调整剂 211 MLB 调整剂 212 MLB 促进剂 213 MLB 蚀刻树脂剂 2 14D-2 MLB 中和剂 216 MLB 中和剂 216-2 EN-DU ? ? ? CUPOSIT? 250 中速沉铜 CUPOSIT? 251 高速沉铜 CUPOSIT? 253 低速沉 铜 CUPOSIT? 385-2 低速沉铜 CRIMSON ? ? ? ? SENSITIZER 5110 敏化剂 CRIMSON 5300 活化剂 CRIMSON 5400 转化剂
本文由leilamila贡献 ppt文档可能在WAP端浏览体验不佳。建议您优先选择TXT,或下载源文件到本机 查看。 Shipley 化学沉铜与电镀简介 通孔电镀的目的 化学沉铜 – 在己催化的通孔孔壁上通过沉铜提供导电性. 在己催化的通孔孔壁上通过沉 铜提供导电性. 电镀铜 – 在化学沉铜层上通过电解方法沉积金属铜,以提供足够 在化学沉铜层上通过 电解方法沉积金属铜, 的导电性/厚度及防止导电电路出现热和机械缺陷. 的导电性/厚度及防止导电电 路出现热和机械缺陷. 通孔横截面模型 盲孔横截面模型 SHIPLEY CIRCUPOSIT 200 MLB系列 钻孔 CIRCUPOSIT MLB 膨松剂211 二级水洗(逆流) CIRCUPOSIT MLB 树脂蚀刻剂 214 三级逆流水洗 CIRCUPOSIT MLB 中和剂 216 二级逆流水洗 CIRCUPOSIT 化学沉铜工序 钻孔后 钻孔后 CIRCUPOSIT MLB 膨松剂 211 使孔壁上的胶渣得以软化,膨松并渗入树脂 聚合后之交联处,从而降低其键结 的能量,使易 于进行树脂的溶解。 CIRCUPOSIT MLB 除钻污剂 214 作用: 高锰酸钾的强氧化性,在高温及强碱的条件下,与 树脂发生化学反应,而分解溶去。 反应原理: 4MnO4- + 有机树脂 + 4OH(七价) 4 MnO4= + CO2 + 2H2O (六价) CIRCUPOSIT MLB中和剂 216 酸性强还原剂; 能将残存在板面或孔壁死角处的二氧化锰或高锰 酸盐中和除去 ; 经过CIRCUPOSIT? 200 去钻污 Shipley 化学沉铜工艺 清洁–调整剂 C/C233 三级水洗(逆流) 微蚀剂 Na P S 二级逆流水洗 预浸剂 C/P 404 活化剂 CAT 44 二级逆流水洗 加速剂 Acc 19 一级水洗 化学沉铜剂 C/P 253 二级逆流水洗 除胶渣后的孔壁 清洁-清洁--调整剂 --调整剂 能有效地除去线路板表面轻微氧化物及轻微污渍( 能有效地除去线路板表面轻微 氧化物及轻微污渍(如手 指印等). 指印等). 整孔功能: 整孔功能: 对环氧树脂及玻 璃界面活性调整有极好的 效果. 效果. 调整剂的控制直接影响沉铜的背光效果. 调整 剂的控制直接影响沉铜的背光效果. 清洁--调整剂后的孔壁 清洁--调整剂后的孔壁 微蚀剂
page 3
01/PPR 等 添加 剂的 铜电 镀 液中 电 镀加 厚 铜层 至 要求 厚 度。 图形电镀铜/锡工艺过程 图形电镀铜 锡工艺过程 g 预浸酸(10% H2SO4) 预浸酸 — 减轻前处理清洗不佳对电镀锡溶液之污染. — 保持电镀锡溶液中硫酸含量之 稳定。 图形电镀铜/锡工艺过程 图形电镀铜 锡工艺过程 g 电镀锡 — 为碱性蚀刻提供抗蚀层. 电镀锡的原理 直流 整流器 nene- + 阳极 离子交换 电镀上锡层 阴极 (受镀物件) 镀槽 Sn Sn2+ + 2e- Sn2+ + 2e- Sn 电镀液组成(H2O+SnSO4+H2SO4+添加剂) 电镀锡工艺 g 鍍純錫主要成份作用 Ronastan EC 鍍純錫主要成份作用 — SnSO4 主鹽,提供 Sn2+ — H2 SO4 提供導電性,提高极化作用,提供一個 較強的酸性 環境,防止錫离子水解。 — Part A 是一种光亮劑,可以鍍出細致、均 勻的錫層 — Part B 分散劑、溶劑,是一种表面活性劑,可以增加 Part A 的溶解度