焦炉气制甲醇
焦炉气制甲醇工艺

焦炉气制甲醇工艺工艺流程说明来自压缩工段的焦炉气(123℃,3.0MPaA)经加热炉预热后,与来自空分的经氧气加热器加热后 3.5MPaA氧气经转化炉喷嘴混合后在转化炉内发生不完全燃烧反应,放出大量的热量,气体温度迅速升高,同时CH4发生转化反应。
转化炉出口的高温转化气(CH4<0.4)直接进入中压废热锅炉,产生4.0MPaG蒸汽。
降温后的转化气进入蒸汽过热器/锅炉给水加热器,过热甲醇合成来的2.5MPaG饱和蒸汽,加热甲醇合成废锅和本工段中压废热锅炉用锅炉给水。
然后转化气经脱盐水加热器降温后进入水洗塔降温洗涤后,送至NHD脱硫工段。
水洗塔塔底分离掉的冷凝液送至造气的浊循环水系统。
脱盐水站来脱盐水经脱盐水加热器加热后送至锅炉房。
氧气加热器用本工段产的4.0MPaG饱和蒸汽加热。
中压废热锅炉产的4.0MPaG饱和蒸汽除部分供氧气加热器用,其余经加热炉加热至450℃后送至管网。
加热炉用燃料气主要为甲醇合成闪蒸气和甲醇精馏不凝气及甲醇合成非渗透气。
**焦炉煤气经过过滤器滤去油雾和预脱硫槽脱除无机硫后,经加氢转化器加氢转化进入中温脱硫槽脱除绝大部分无机硫,经过二级加氢转化器将残余的有机硫进一步转化,再经中温氧化锌脱硫槽把关,使气体中的总硫达到0.1ppm,出氧化锌脱硫槽的气体送往转化装置。
焦炉煤气和氧气分别进入转化炉上部后立即进行氧化反应放出热量,并很快进入催化剂层,反应后的转化气由转化炉底部引出经一些列管换热冷凝后,由气液分离器分离工艺冷凝液,经氧化锌脱硫槽脱除气体中残余的硫并送往合成气压缩工段。
转化气经合成压缩机一、二段压缩至5.5MPa,然后进入循环段与来自甲醇合成的循环气在缸内混合,压缩至6.0MPa后送至甲醇合成工段。
公司用电(万KWh)17145.4:主要生产14498.4,辅助2647。
甲醇生产:焦炉煤气(万m3)41268 折标0.6052电力(万KWh)10546.3蒸汽(t)511240输出驰放气(万m3)16664 产量(t)211339蒸汽(t)329591。
十万吨焦炉煤气制甲醇的操作规程
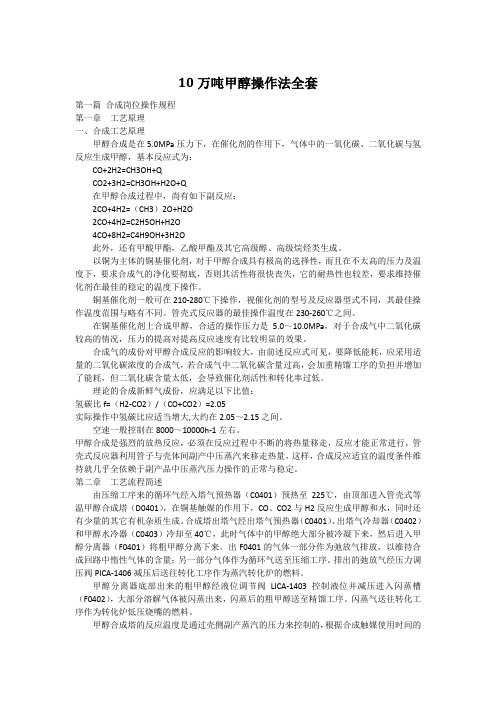
10万吨甲醇操作法全套第一篇合成岗位操作规程第一章工艺原理一、合成工艺原理甲醇合成是在5.0MPa压力下,在催化剂的作用下,气体中的一氧化碳、二氧化碳与氢反应生成甲醇,基本反应式为:CO+2H2=CH3OH+QCO2+3H2=CH3OH+H2O+Q在甲醇合成过程中,尚有如下副反应:2CO+4H2=(CH3)2O+H2O2CO+4H2=C2H5OH+H2O4CO+8H2=C4H9OH+3H2O此外,还有甲酸甲酯,乙酸甲酯及其它高级醇、高级烷烃类生成。
以铜为主体的铜基催化剂,对于甲醇合成具有极高的选择性,而且在不太高的压力及温度下,要求合成气的净化要彻底,否则其活性将很快丧失,它的耐热性也较差,要求维持催化剂在最佳的稳定的温度下操作。
铜基催化剂一般可在210-280℃下操作,视催化剂的型号及反应器型式不同,其最佳操作温度范围与略有不同。
管壳式反应器的最佳操作温度在230-260℃之间。
在铜基催化剂上合成甲醇,合适的操作压力是5.0~10.0MPa,对于合成气中二氧化碳较高的情况,压力的提高对提高反应速度有比较明显的效果。
合成气的成份对甲醇合成反应的影响较大,由前述反应式可见,要降低能耗,应采用适量的二氧化碳浓度的合成气,若合成气中二氧化碳含量过高,会加重精馏工序的负担并增加了能耗,但二氧化碳含量太低,会导致催化剂活性和转化率过低。
理论的合成新鲜气成份,应满足以下比值:氢碳比f=(H2-CO2)/(CO+CO2)=2.05实际操作中氢碳比应适当增大,大约在2.05~2.15之间。
空速一般控制在8000~10000h-1左右。
甲醇合成是强烈的放热反应,必须在反应过程中不断的将热量移走,反应才能正常进行,管壳式反应器利用管子与壳体间副产中压蒸汽来移走热量,这样,合成反应适宜的温度条件维持就几乎全依赖于副产品中压蒸汽压力操作的正常与稳定。
第二章工艺流程简述由压缩工序来的循环气经入塔气预热器(C0401)预热至225℃,由顶部进入管壳式等温甲醇合成塔(D0401),在铜基触媒的作用下,CO、CO2与H2反应生成甲醇和水,同时还有少量的其它有机杂质生成。
焦炉煤气制甲醇物料平衡计算
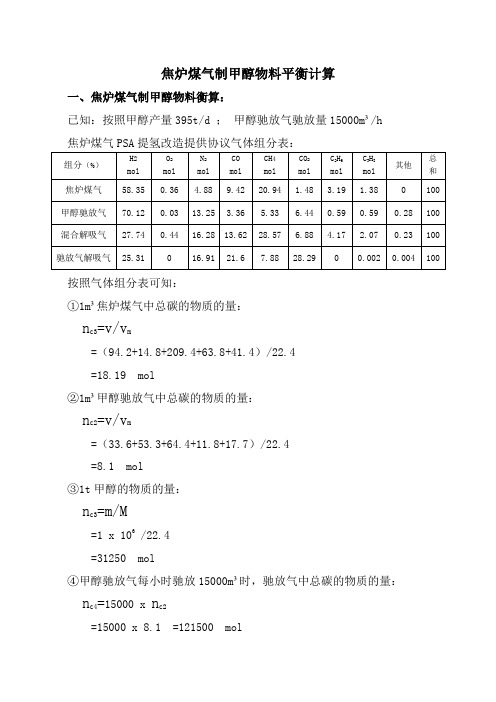
焦炉煤气制甲醇物料平衡计算一、焦炉煤气制甲醇物料衡算:已知:按照甲醇产量395t/d ;甲醇驰放气驰放量15000m³/h焦炉煤气PSA提氢改造提供协议气体组分表:按照气体组分表可知:①1m³焦炉煤气中总碳的物质的量:n c3=v/v m=(94.2+14.8+209.4+63.8+41.4)/22.4=18.19 mol②1m³甲醇驰放气中总碳的物质的量:n c2=v/v m=(33.6+53.3+64.4+11.8+17.7)/22.4=8.1 mol③1t甲醇的物质的量:n c3=m/M=1 x 106 /22.4=31250 mol④甲醇驰放气每小时驰放15000m³时,驰放气中总碳的物质的量:n c4=15000 x n c2=15000 x 8.1 =121500 mol⑤理论计算:生产1t甲醇所需焦炉煤气量为:V1= n c3/ n c3=31250/18.19 = 1718 m³⑥理论计算:每小时生产16.46t甲醇所需焦炉煤气量为:V2=V1*16.46 =28277.9m³/h⑦甲醇驰放气每小时驰放15000m³时,所需焦炉煤气的量为:V3=15000 /n c3=15000/18.19 =6679 m³/h由①②③④⑤⑥⑦式可知:每小时生产16.64t甲醇所需要焦炉煤气总量为:V总= V2+ V3 = 28277.9 + 6679 =34957.4 m³/h二、焦炉煤气和甲醇驰放气混合提氢物料计算已知:按照相关技术协议使用甲醇驰放气为原料提氢收率为81%;使用焦炉煤气为原料提氢收率为75%;按照供给总氢气量为18000m³/h:甲醇驰放气量15000 m³/h时:氢气=8520 m³/h ;解吸气量=6480 m³/h;焦炉煤气量21714 m³/h时:氢气=9480 m³/h ;解吸气量=12234 m³/h;。
焦炉煤气制甲醇工艺之合成操作规程
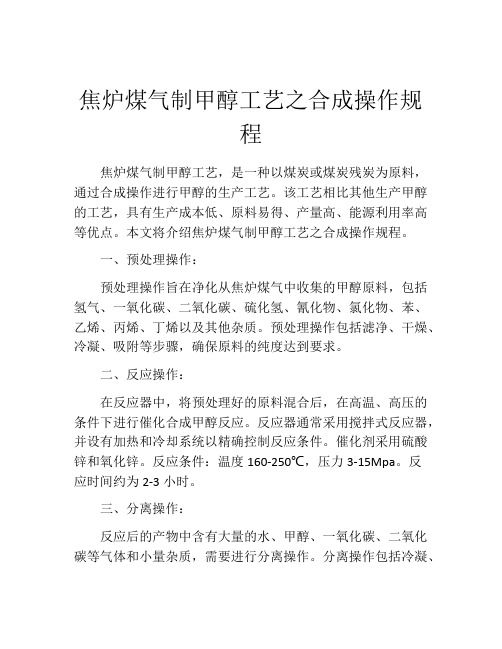
焦炉煤气制甲醇工艺之合成操作规程焦炉煤气制甲醇工艺,是一种以煤炭或煤炭残炭为原料,通过合成操作进行甲醇的生产工艺。
该工艺相比其他生产甲醇的工艺,具有生产成本低、原料易得、产量高、能源利用率高等优点。
本文将介绍焦炉煤气制甲醇工艺之合成操作规程。
一、预处理操作:预处理操作旨在净化从焦炉煤气中收集的甲醇原料,包括氢气、一氧化碳、二氧化碳、硫化氢、氰化物、氯化物、苯、乙烯、丙烯、丁烯以及其他杂质。
预处理操作包括滤净、干燥、冷凝、吸附等步骤,确保原料的纯度达到要求。
二、反应操作:在反应器中,将预处理好的原料混合后,在高温、高压的条件下进行催化合成甲醇反应。
反应器通常采用搅拌式反应器,并设有加热和冷却系统以精确控制反应条件。
催化剂采用硫酸锌和氧化锌。
反应条件:温度160-250℃,压力3-15Mpa。
反应时间约为2-3小时。
三、分离操作:反应后的产物中含有大量的水、甲醇、一氧化碳、二氧化碳等气体和小量杂质,需要进行分离操作。
分离操作包括冷凝、膜分离、吸附、蒸馏等步骤。
其中,蒸馏是分离操作中最为重要的一步,该步骤可将产物中甲醇的纯度提高至99.5%以上。
四、纯化操作:纯化操作是指进一步提高甲醇产品的纯度。
该操作主要采用蒸馏和吸附等方法,将残余的水、碳氢类杂质、酸类杂质、杂质甲醇等有机物和无机物从甲醇中提取出来。
纯化后的甲醇产品可以最终得到经过瓶装、桶装、罐装等方式进行包装装载。
五、安全操作:焦炉煤气制甲醇工艺是一种高温、高压、易爆等危险的工艺,因此安全操作尤为重要。
在运行过程中,需注意以下几点:必须使用标准的安全设施和防爆设备;操作工人必须接受专业的安全知识和技能培训;应定期检查设备的安全状况和参数;生产过程中应注意气体的引爆和毒性危害等问题。
六、总结:焦炉煤气制甲醇工艺之合成操作规程涉及预处理、反应、分离、纯化、安全等多个环节,其中每个环节都需要精细严谨的操作。
生产甲醇同时也要高度重视工厂的环保问题,合理规划废气、废水等排放,缩小环境污染,实现可持续发展的目标为行业健康快速发展奠定了基础。
焦炉煤气制甲醇工艺方案

焦炉煤气制甲醇工艺方案1.原料准备:焦炉煤气和一定比例的水蒸气是制备甲醇的原料。
焦炉煤气中含有一氧化碳、二氧化碳、氢气、氮气和少量烃类。
首先,对原料焦炉煤气进行预处理,除去其中的硫化物和一些杂质。
2.原料净化:焦炉煤气经过预处理后,进一步进行净化工艺。
通过冷却、除尘和脱硫等工序,去除颗粒物、酸性气体等污染物,以保证后续反应的顺利进行。
3.变换反应:焦炉煤气中的一氧化碳和二氧化碳需要经过变换反应,将其转化为甲醇。
该反应采用催化剂进行催化。
一氧化碳与水蒸气在一定温度和压力下通过催化剂反应生成甲醇。
在反应器内,采用适当的催化剂、反应温度和压力条件,可以提高甲醇的产率和选择性。
4.分离纯化:经过变换反应后,产生的反应混合物中含有甲醇、水、未反应的一氧化碳和二氧化碳等。
需要进行分离纯化工艺,将甲醇从混合物中提取出来。
常用的分离纯化方法包括蒸馏、吸附、结晶等。
5.回收利用:在分离纯化过程中,除了得到纯度较高的甲醇产品外,还会产生一些副产物和废弃物。
这些副产物和废弃物可以通过进一步处理和回收利用,以实现资源的综合利用和环境保护。
总的来说,焦炉煤气制甲醇工艺方案是将焦炉煤气中的一氧化碳和氢气转化为甲醇的过程。
通过预处理、净化、变换反应、分离纯化和废弃物处理等工序,实现了焦炉煤气的高效利用和甲醇产品的生产。
然而,在实际生产中,还需要根据具体情况进行工艺参数的调整和优化,以提高产量和甲醇的品质。
此外,还需要关注工艺过程中的能耗和环境污染问题,不断改进工艺方案,提高产能和资源利用效率,推动绿色发展。
焦炉气制甲醇工艺

焦炉气的精制是以炼焦剩余的焦炉气为生产原料;经化工产品回收焦炉气的粗制;再经压缩后2.55MPa;进入脱硫转化工段;脱硫采用NHD湿法脱硫和干法精脱硫技术;总硫脱至0.1×10-6;转化采用烃类部分氧化催化技术;制得合格的甲醇合成新鲜气又称精制气;送去压缩工段合成气压缩机;最后进入甲醇合成塔制得甲醇..第1章焦炉气成分分析1.1典型焦炉气的组成焦炉气的主要成分为甲烷26.49%、氢气58.48%、一氧化碳6.20%和二氧化碳2.20%等;还有少量的氮气、不饱和烃、氧气、焦油、萘、硫化物、氰化物、氨、苯等杂质..焦炉气基础参数:流量62967m3/h2台焦炉生产的剩余焦炉气;温度25℃;压力0.105MPaa煤气柜压力..1.2焦炉气的回收利用焦炉气是良好的合成氨、合成甲醇及制氢的原料..根据焦炉气组成特点;除H2、CO、CO2为甲醇合成所需的有效成分外;其余组分一部分为对甲醇合成有害的物质如多种形态的硫化物;苯、萘、氨、氰化物、不饱和烃等..如焦炉气中的硫化物不仅会与转化催化剂的主要活性成分Ni迅速反应;生成NiS使催化剂失去活性;而且还会与甲醇合成催化剂的主要活性组分Cu迅速反应;生成CuS;使催化剂失去活性;并且这两种失活是无法再生的..又如;不饱和烃会在转化催化剂表面发生析碳反应;堵塞催化剂的有效孔隙及表面活性位;使催化剂活性降低..另一部分为对甲醇合成无用的物质对甲醇合成而言为惰性组分;如CH4、N2等..惰性气体含量过高;不仅对甲醇合成无益;而且会增加合成气体的功耗;从而降低有效成分的利用率..第2章焦炉气的精制2.1硫的脱除及加氢净化焦炉气制甲醇工艺中;焦炉气精制的首要工作是“除毒”;将对甲醇合成催化剂有害的物质脱除到甲醇合成催化剂所要求的精度..这是因为甲醇合成催化剂对硫化物的要求要高于转化催化剂..甲醇合成催化剂要求总硫<0.1×10-6;转化催化剂要求总硫<0.×10-6..第二就是要减少惰性组分的含量..脱除“毒物”的方法;根据系统选择工艺方案的不同而有所差别..而降低惰性气体的组分含量主要是采用将烃类部分氧化催化转化的方法;使其转化为甲醇合成有用的CO和H2;同时达到降低合成气中惰性组分的目的..2.1.1无机硫的脱除焦炉气中硫质量浓度高达6g/m3;氰化物质量浓度约为 1.5g/m3..在焦炉气净化工艺中设有脱硫、脱氰、蒸苯、焦油电捕捉等一系列净化装置;除为了减轻硫化氢和氰化物对后续装置的腐蚀;另一方面是减轻焦炉气作燃料气时对大气的污染;或作化工原料时;对催化剂的毒害..煤气净化装置是将焦炉气经过捕捉、冷却、分离、洗涤等多种化工操作;脱除焦炉气中的焦油、萘、硫化氢、氰化氢、氨、苯等物质;以满足后续装置对气体质量的要求;并回收焦油、硫、氨、苯等..本系统采用NHD湿法脱硫后;焦炉气中的HS质量浓度在15mg/m3左右;同时2可脱除焦炉气中部分有机硫..但有机硫含量仍然很高;达95mg/m3左右..如不经过精脱硫直接送入下工段;将使转化系统催化剂很快因硫中毒而失活;所以必须采用精脱硫工艺对焦炉气进行处理..2.1.2有机硫的脱除精脱硫根据对国内现有焦炉气净化技术的分析和比较;考虑到COS低温水解工艺路线存在的缺陷;对焦炉气的精脱硫采用高温加氢转化技术路线..这是因为焦炉气中含有的硫化物形态较为复杂;如:硫醇、硫醚、噻酚等硫化物在低温水解环境下很难脱除..本系统采用铁-钼加氢脱硫转化剂;在高温环境下;将气体中的有机硫转化;生成易于脱除的硫化氢;然后再采用固体铁-锰脱硫剂吸收转化后气体中的硫化氢..这样可使有机硫加氢转化完全;净化度大为提高;而且配套干法脱硫剂的硫容也高;并且可将不饱和烯烃进行加氢饱和..氧气加氢燃烧;达到对毒物的脱除;满足转化甲醇合成气对气体“毒物”的净化要求..本工艺克服了COS 低温水解催化剂对氧敏感的弱点;以及二氧化碳含量影响有机硫水解的缺陷;解决了高浓度CO 2影响水解反应进行;以及无法脱除复杂硫化物的难题..现有焦炉气净化工艺的有机硫的加氢转化;一般采用铁-钼加氢催化剂;在350℃-430℃下使有机硫加氢转化为硫化氢;固体脱硫剂使用便宜的但硫容低的铁-锰脱硫剂;最后使用价格较贵但硫容较高的氧化锌把关..2.1.3关键技术高浓度CO 、CO 2的焦炉气加氢净化时;遇到的问题:1如何避免CO 、CO 2在加氢催化剂上产生甲烷化反应..2如何避免CO 歧化析碳和甲烷的分解析碳..3如何防止铁钼催化剂床层产生的温升..2.1.4解决方法在加氢过程的主要反应中;含有烯烃、有机硫化物及氧的焦炉气在催化剂上进行的主要反应有:2H 2+O2=2H 2O+Q 1C 2H 2+2H2→C 2H 6 2C 3H 6+H 2→C 3H 8 3COS+H 2→CO+H 2S 4COS+H 2O →CO 2+H 2S 5RSH 硫醇+H 2→RH+H 2S 6R 1SR 2硫醚+2H 2→R 1H+R 2H+H 2S 7CS 2+4H 2→2H 2S+CH 4+Q 8C 4H 4S 噻酚+4H 2→C 4H 10+H 2S 9可能出现的副反应有:2CO →C+CO 2+Q 10CO+3H 2→CH 4+H 2O 11CH 4→C+2H 2+Q 12反应1、8、10为强放热反应;可能会引起催化剂床层“飞温”..反应10所出现的歧化积碳反应产生的碳会堵塞催化剂孔道;导致催化剂活性位减少;因此应设法避免上述反应..另外;焦炉气体中的油类由于焦炉气压缩机气缸采用少油润滑;可能在焦炉气中带有少量的润滑油、苯和焦油在加氢转化器内;经加氢裂解、饱和;避免了这些微量物质对后续工段的不利影响..我们在工艺设置上;采用严格的350℃控制;设有冷激副线;及时调整加氢转化器床层温度..通过监测床层压差变化;及时调整床层温度以及分析槽内积碳程度;达到抑制析碳的目的..2.2烃类的部分氧化催化转化烃类的转化是将焦炉气中的甲烷转化成合成甲醇所用的有效气体CO 和H 2..为使甲醇合成气的氢碳比尽量靠近甲醇合成所需要的最佳氢碳比;本装置焦炉气中烃类的转化选用部分氧化纯氧+蒸汽催化转化..2.2.1部分氧化催化转化原理焦炉气部分氧化催化转化法;是将焦炉气中的烃类甲烷、乙烷等进行部分氧化和蒸汽转化反应;在转化炉中首先发生H 2、CH 4与O 2的部分氧化燃烧反应;然后气体进入催化剂层进行甲烷、乙烷等与蒸汽的转化反应;所以这个方法也称为自热转化法..生产原理可以简单解释为甲烷、蒸汽、氧混合物的复杂的相互作用:第一阶段为部分氧化反应;主要是氢气与氧接触发生燃烧氧化反应;生成H2O..该反应是剧烈的放热反应:2H 2+O 2=2H 2O+Q 13在这个阶段;焦炉气体中微量的氧与配入的氧完全反应;反应后的气体中氧体积分数仅为0.05%;不会对转化催化剂活性造成影响..第二阶段为水蒸气和二氧化碳氧化性气体在催化剂的作用下;与CH4进行蒸汽转化反应;该反应是吸热反应:CH 4+H 2O →CO+3H 2-Q 14CH 4+CO 2→2CO+2H 2-Q 15上述两阶段的反应可合并成一个总反应式:2CH 4+CO 2+O 2→3CO+3H 2+H 2O 16由于第二个阶段反应是吸热反应;当转化温度越高时;甲烷转化反应就越完全;反应后气体中的残余甲烷就越低..甲烷部分氧化通常加入一定量的蒸汽;目的是避免焦炉气在受热后发生析碳的反应;使甲烷进行蒸汽转化反应;在转化反应的同时;也起到抑制炭黑的生成..转化反应在镍催化剂作用下;反应速度加快;反应温度降低;反应平衡温距减小到1℃-5℃;在960℃残余CH 4<0.4%..转化后的气体成分见表2.1..表2.1转化后的气体成分由表2.1可见;焦炉气催化纯氧转化制得甲醇合成气中虽然氢气过剩;但其他组分比例较好;完全能够满足甲醇合成需要..2.2.2工艺流程焦炉气中烃类部分氧化催化转化工艺流程示于图2.1..图2.1焦炉气部分氧化催化转化工艺流程示意图2.2.3过程特点转化催化剂的主要活性组分为Ni;对硫化物非常敏感;因此;焦炉气进入转化炉之前;必须将其中大量的硫化物脱除到转化催化剂和甲醇合成催化剂对硫精度的要求..焦炉气和氧气在进入转化炉之前;与一定比例的蒸汽混合;为防止水蒸气冷凝;焦炉气和氧气需在加热炉中加热;一方面防止蒸汽冷凝;另一方面加热后的焦炉混合气与氧气在进入转化炉后;能迅速发生燃烧反应..为防止液状或固体颗粒进入高速运转的离心机合成气压缩机;损坏转子;本装置在焦炉气压缩前;对焦炉气进行洗涤;利用焦炭过滤;采用4台往复活塞式压缩机;提高气体压力至脱硫系统所需压力2.55MPa..焦炉气中的硫形态比较复杂;转化前采取一系列脱硫;直至总硫<0.1×10-6..实践证明;转化前未脱除的硫主要是噻吩;经过铁钼加氢转化;在高温环境下;已经全部转化为易于脱除的H2S和C4H10;此时将转化气中总硫脱除到所需精度很容易..甲醇系统驰放气主要用作转化加热炉燃料;剩余的返回燃料气管网;顶替部分炼焦用燃料焦炉气;把焦炉气送回甲醇生产系统进行脱硫转化;压缩合成..本装置设置大型加热炉;除加热转化系统物料外;还将转化副产 6.4MPa、282℃次高压饱和蒸汽;加热至480℃..经降温降压至3.82MPa、450℃的过热蒸汽;作为空压和合成气压缩汽轮机透平动力蒸汽..全系统蒸汽完全自给..系统副产蒸汽压力等级较多;能够适应不同需要..本装置主要副产 6.4MPa 饱和蒸汽加热后减压3.82MPa;450℃过热蒸汽..1.2MPa过热蒸汽由高压汽包直接降压获得;并入1.2MPa管网;与来自甲醇合成的1.2MPa过热蒸汽作为甲醇精馏和溶液再生的热源..0.3MPa低压蒸汽主要作除氧热源和厂区冬季采暖..冷凝液的回收利用..全系统冷凝液可回收利用;增设一气体饱和塔;用系统冷凝液通过加热炉加热;进行饱和增湿..既可减少系统蒸汽用量;又合理利用了冷凝液;省略了工艺冷凝液的排放和处理;消除了环境的污染因素;这是一项节能环保的技术..三废治理及环境保护与实际效果..本装置在设计中严格执行国家有关标准、地方规定;具有完善的“三废”及噪声治理措施..1废气治理在开停车及事故工况下;转化工段和脱硫工段排放的工艺废气焦炉气和合成气送本工程火炬系统焚烧后排放..甲醇合成系统的驰放气和膨胀气;甲醇精馏预塔不凝气作为加热炉燃料全部消耗;不排放到空气中..NHD脱硫系统产生的含硫化氢废气;送入Cluas硫回收装置;尾气中SO2浓度达标排放..2废水治理甲醇装置的废水量不大;甲醇精馏废水采用汽提预处理回收甲醇;而后送污水处理站进行生化处理..3废渣治理各类废催化剂分类送催化剂制造厂回收;不能回收的并无毒害作用的如:废锰矿石用于铺路或填坑;不存在废固堆放现象..因此;本装置废渣对环境影响不大..第3章关键的工艺技术和设备3.1焦炉气湿法脱硫NHD脱硫技术主要是脱除焦炉气中的大部分无机硫H2S和少量有机硫COS;并将脱硫回收的酸性气体送回硫回收..3.2焦炉气精脱硫干法脱硫是将经过湿法脱硫的焦炉气中的有机硫;利用铁钼触媒进行加氢反应;转化成易于脱除的无机硫;同时也使不饱和烃加氢饱和;而后通过锰矿脱硫剂和氧化锌脱硫剂;将硫化氢脱除;使经过干法脱硫的焦炉气中总硫<0.1×10-6;达到甲醇合成触媒要求的精度..3.3焦炉气部分氧化催化转化转化是将脱硫后焦炉气中的CH4及其他烃类在转化炉内;与纯氧进行部分氧化及蒸汽转化反应;生产H2、CO、CO2等甲醇合成气;同时回收转化反应余热;副3.4主要设备3.4.1加热炉加热炉采用两段辐射、一段对流设计;辐射段主要加热焦炉气混合气和高压废锅产次高压饱和蒸汽;对流段共加热4种介质:饱和塔循环热水、富氧蒸汽、NHD湿脱硫气和预热加热炉助燃空气..3.4.2转化炉转化炉采用圆筒式纯氧转化炉;炉体为钢结构+耐火绝热材料+冷却水夹套..炉内装二段转化催化剂;顶部为蒸汽冷却套中心管式烧嘴;转化所需热量通过氧气与焦炉气中氢气发生部分燃烧反应提供;燃烧后的高温气体在催化剂床层发生甲烷与蒸汽的转化反应..转化炉出口温度控制为960℃-980℃;残余CH的体4积分数为<0.4%..3.4.3高压废锅高压废锅是转化生产中最重要的设备;本装置采用的高压废锅温差达到600℃以上出高压废锅工艺气体温度达340℃;并且高压废锅与转化炉直连;管道内浇筑2层刚玉浇筑料;与高压废锅的浇筑料在烘炉时;需形成一体耐火隔热层..高压废锅共分2端;一端为高热端;有4根汽液上升管和热水下降管;内筑有耐火浇筑料..另一端为低热端;有2根汽液上升管和热水下降管..另配有汽包1个;供应高压锅炉给水;并实现汽液分离..本系统考虑到COS低温水解工艺路线存在的缺陷;对焦炉气的精脱硫采用高温加氢转化技术路线..采用铁-钼加氢脱硫转化剂;在高温环境下;将气体中的有机硫转化;生成易于脱除的硫化氢;然后再采用固体铁-锰脱硫剂吸收转化后气体中的硫化氢..这样可使有机硫加氢转化完全;净化度大为提高 ;并且可将不饱和烯烃进行加氢饱和..氧气加氢燃烧;达到对毒物的脱除;满足转化甲醇合成气对气体“毒物”的净化本工艺克服了COS低温水解催化剂对氧敏感的弱点;以及二氧化碳含量影响有机硫水解的缺陷;解决了高浓度CO影响水解反应进行;以及无法脱除复杂2硫化物的难题..参考文献:1 裴雪国.焦炉气制甲醇J.煤化工;2006;6:32-342 李建锁.焦炉煤气制甲醇技术M.北京:化学工业出版社20093 谢克昌;房鼎业.甲醇工艺学M.北京:化学工业出版社20104 张子锋.甲醇生产技术M.北京:化学工业出版社2008谢辞感谢各位老师三年来的教诲;感谢胡德双老师毕业论文的指导..。
焦炉煤气制甲醇
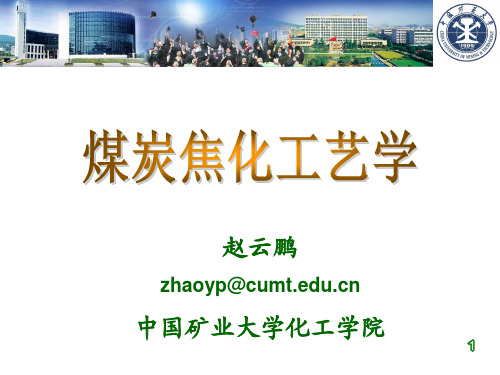
23
23
一、甲醇的合成
1. 合成甲醇的原理
CO + 3H2 → CH3OH CO2 + 3H2 → CO + H2O 2. 合成甲醇的工艺 甲醇合成工艺分为:高压、中压和低压法。 △H298=-90.8kJ/mol △H298=41.3kJ/mol CO2 + 3H2 → CH3OH + H2O △H298=-49.5kJ/mol
合成气冷却
弛放气
焦炉煤气
压缩
干法脱硫
煤气加热炉
甲醇精馏
煤气
甲醇
图12-1 焦炉气制甲醇工艺流程
7
7
第二节
焦炉气的净化
制甲醇用焦炉气的要求:总硫体积分数不大于 0.1ppm,烯烃、长链烷烃含量不能太高。 因此,精脱硫工序是焦炉煤气净化工艺中最重 要的一环。
8
8
第二节
焦炉气的净化
1. 铁(钴)钼催化加氢+氧化铁、氧化锌脱硫
赵云鹏
zhaoyp@
中国矿业大学化工学院
1
1
第十二章
第一节 第二节 第三节 第四节
焦炉煤气制甲醇
焦炉煤气制甲醇的原理 焦炉气的净化 焦炉气转化 甲醇的合成和精馏
2
2
第一节 焦炉煤气制甲醇的原理
CH4 + H2O → CO + 3H2 合成气制甲醇的反应:CO + 2H2 → CH3OH 甲醇合成气的要求主要包括以下三个方面:
合成气中的杂质:使催化剂失活得有毒物质 和惰性物质。
导致催化剂失活的有毒物质:硫化物、羰基
金属和Cl-。 总硫体积分数不大于0.1ppm,甲烷含量不大 于0.6%。
6
6
焦炉气制甲醇系统危险有害性分析

焦炉气制甲醇系统危险有害性分析摘要:甲醇生产是一个复杂而危险的过程,在其生产过程中必须做好安全防护措施。
本文概述了焦炉气制甲醇流程,分析了工艺流程中的危险有害性,然后,针对生产、设计等过程提出防护措施,并对可能发生的意外事故提出了应急救援方案。
关键词:焦炉气;甲醇;防护措施甲醇在化工制造业、洁净能源利用中占有非常重要的地位。
随社会经济的进步和发展,甲醇的需求量与日俱增。
但其属于易燃易爆的危险品,每年都会发生大量的甲醇事故,造成生命和财产损失,因此做好甲醇的安全防护工作显得尤为重要。
一、焦炉气制甲醇流程焦炉气制甲醇的基本步骤如下:以焦炉荒煤气为原料,首先进行焦炉荒煤气的初步脱硫及净化处理,然后将其压缩二度脱硫并深度净化,并将检测合格的脱硫净化气泵入合成塔中,严格按照相关规定要求和步骤催化合成甲醇,初步分离处理后将粗产品进行精馏处理,并采用按照相关精馏工艺手段获得合格的甲醇产品。
二、危险有害性分析1.毒性危险性分析从处理焦炉荒煤气开始直至获得合格的工业甲醇产品,整个生产过程中会产生co、h2s、ch3oh等有毒物质。
所以在甲醇生产、存储及运输过程中,要严格遵守相关操作规范要求,若不小心发生甲醇泄漏事故会造成甲醇及其中有毒物质的扩散,周围人畜若吸入或误食等会造成严重的中毒事故,应立即采取措施并赴医院就医。
2.易燃易爆危险性分析甲醇生产全过程必须在高温高压下才能实现,并且焦炉荒煤气生产甲醇的过程中,绝大多数产品及最终产物均为易燃易爆的危险品。
按照国家对危险化学品危险类别分类标准,从原料焦炉荒煤气到合格甲醇产品及生产过程中的中间气体均被划为甲类危险品。
生产过程中,若因操作失误或合成装置存在泄漏等造成气体泄漏,与空气混合后达到其燃爆浓度时,极易引发爆炸事故;在检查修理相关设备时,应该事先用氦气等惰性气体吹扫相关设备,降低合成过程中产生的滞留气体浓度,避免其在与空气充分混合接触后产生爆炸事故;此外,合成过程中若压力超过安全压力阀值,相关设备很有可能会因压力超载而发生爆炸事故,造成人员伤亡以及设备的破坏,因此必须要对生产过程中的压力严格监控,并装备必要的泄压设备以防事故发生。
天然气制甲醇与焦炉气制甲醇工艺优化对比
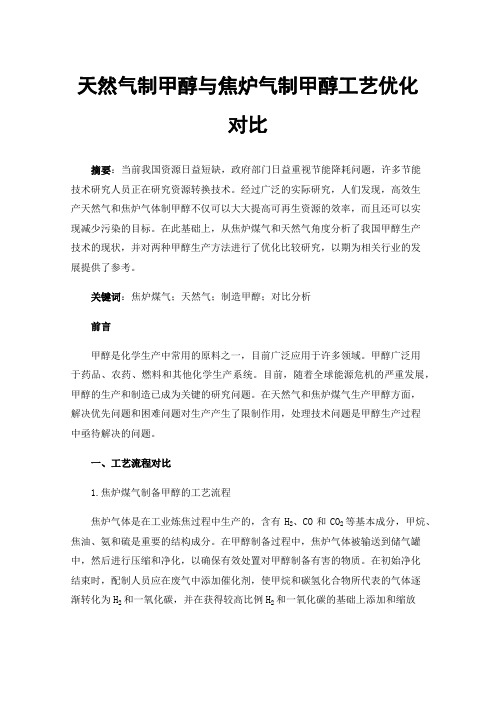
天然气制甲醇与焦炉气制甲醇工艺优化对比摘要:当前我国资源日益短缺,政府部门日益重视节能降耗问题,许多节能技术研究人员正在研究资源转换技术。
经过广泛的实际研究,人们发现,高效生产天然气和焦炉气体制甲醇不仅可以大大提高可再生资源的效率,而且还可以实现减少污染的目标。
在此基础上,从焦炉煤气和天然气角度分析了我国甲醇生产技术的现状,并对两种甲醇生产方法进行了优化比较研究,以期为相关行业的发展提供了参考。
关键词:焦炉煤气;天然气;制造甲醇;对比分析前言甲醇是化学生产中常用的原料之一,目前广泛应用于许多领域。
甲醇广泛用于药品、农药、燃料和其他化学生产系统。
目前,随着全球能源危机的严重发展,甲醇的生产和制造已成为关键的研究问题。
在天然气和焦炉煤气生产甲醇方面,解决优先问题和困难问题对生产产生了限制作用,处理技术问题是甲醇生产过程中亟待解决的问题。
一、工艺流程对比1.焦炉煤气制备甲醇的工艺流程焦炉气体是在工业炼焦过程中生产的,含有H2、CO和CO2等基本成分,甲烷、焦油、氨和硫是重要的结构成分。
在甲醇制备过程中,焦炉气体被输送到储气罐中,然后进行压缩和净化,以确保有效处置对甲醇制备有害的物质。
在初始净化结束时,配制人员应在废气中添加催化剂,使甲烷和碳氢化合物所代表的气体逐渐转化为H2和一氧化碳,并在获得较高比例H2和一氧化碳的基础上添加和缩放碳,通过气体压缩形成粗甲醇最后,应用精细蒸馏技术纯化原甲醇,实现精细甲醇的制备。
在甲醇制备过程中,主要工艺包括焦炉气体的净化、净化气体的转化以及精制甲醇的制备和合成。
所以在生产过程中也要控制技术要点。
首先,在焦炉煤气净化过程中,要注意净化程度的控制。
焦炉煤气中硫化物的不合理净化会严重影响甲醇的生产。
一般而言,有机脱硫是其技术应用的核心,操作人员必须确保每立方米净化气体的硫含量不超过100毫克。
第二,净化气体初转化时,应注意甲烷合成碳比的调整。
具体而言,在转换过程中,氢含量的增加应注意提高反应效率,避免二次反应,从而更好地控制成本。
焦炉煤气制甲醇工艺方案

化学Second Design Institute of Chemical Industry可行性研究4 工艺技术方案4.1 工艺技术方案的选择4。
1。
1原料路线确定的原则和依据根据焦炉气的组成及甲醇合成对原料气的要求,确定工艺路线如下。
由焦化厂送来的焦炉气是经过化产后的焦炉气,压力1000mmH2O,温度40℃,H2S含量100mmg/Nm3,有机硫250 mmg/Nm3,首先进入焦炉气压缩机压缩到2.5MPa,再进入精脱硫装置,进行有机硫加氢转化及无机硫脱除,将焦炉气中总硫脱至0。
1ppm以下,以满足转化催化剂及合成催化剂对原料气中硫含量的要求.脱硫后的焦炉气进入转化工段,在这里进行加压催化部分氧化,使焦炉气中的甲烷和高碳烃转化为甲醇合成的有效成分氢气和一氧化碳。
为保证脱硫精度,转化后仍串有氧化锌脱硫槽。
转化气经合成气压缩机提压后进行甲醇合成,生成的粗甲醇进入甲醇精馏制得符合国标GB338—2004优等品级精甲醇.甲醇合成的弛放气一部分送转化装置的预热炉作燃料,剩余的弛放气和回收氢后的尾气去焦化公司锅炉房作燃料.转化采用纯氧部分氧化,所需氧气由空分提供。
全厂方框流程图及物料平衡表见附图。
化学Second Design Institute of Chemical Industry可行性研究本文件包含化学工业第二设计院技术成果,未经本院许可不得转给第三方或复制。
4-2This document contains proprietary information of SEDIN. To be kept confidential.4.1.2工艺技术方案的比较和选择4.1.2。
1焦炉气压缩由焦化厂送来的焦炉气H2S小于100mg/Nm3,有机硫约250 mg/Nm3,压力为常压,在进一步处理前,必须进行气体的压缩。
本工程焦炉气量较大,可选择的压缩机有往复式和离心式两种。
往复式压缩机技术成熟,价格便宜,但单机打气量小,机器庞大,噪音高,惯性力强,需要强固的基础.此外,往复式压缩机易损件多,容易停车,检修频繁,维修费用高,必须考虑备机,如采用往复式压缩机,需两开一备,占地大,电耗稍高。
20万吨焦炉气制甲醇操作规程
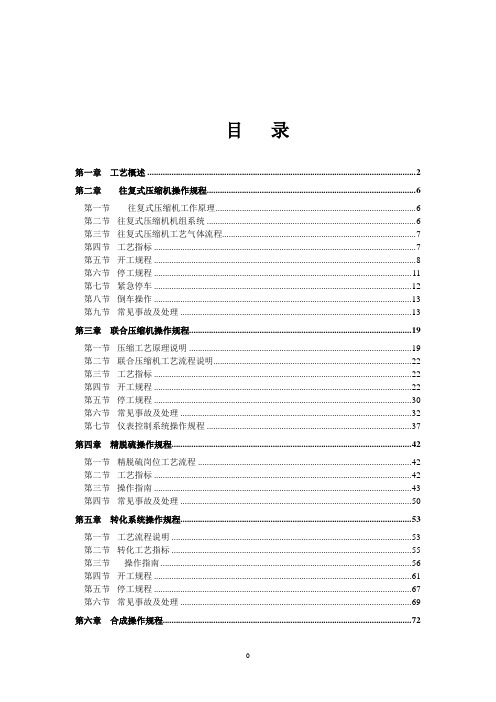
第六节
一、停车步骤
1)、接到调度停车通知后,注意检查各级压力,并做好停车准备工作,准备从高压端到低压端的顺序切气;
2)、减量:通知转化岗位准备减量,开一回一减量,当全开还需减量时,可开四回一进行大减量,减量的多少,应根据转化系统平稳状况,减到转化所需的压力时准备切气;
温度(供水/回水)
32/42℃
污垢系数
0.00034m2K/w
碳钢年腐蚀速度
<0.125mm/a
Cl-1
<100mg/L
SS
≤20 mg/L
PH值
6.5~9.5
浓缩倍数
K=3
4、生活用水和消防水
压力
0.5MPa(A)
温度
环境温度
5、精制脱盐水
压力
0.5MPa(A)
温度
≤40℃
电导率(25℃)
≤0.2us/cm
设计操作时间:8000小时/年
其工艺路线为:
1、脱油、粗脱硫、加氢串氧化锌干法脱硫
2、催化氧化
3、合成气及循环气联合压缩
4、低压法合成甲醇
5、粗甲醇3塔精馏
6、汽提法处理工艺冷凝液
二、主要工艺特点
1、采用2.3MPa(G)催化氧化制取甲醇合成气;
2、采用低压甲醇合成工艺以及副产中压蒸汽的管壳式等温甲醇合成塔,其能耗低,产品质量好,运行可靠,投资省;
7)、建立电机用油系统:由电工加入分析合格的润滑油进电机滑油系统,并保持油位2/3以上,最后检查是否有泄漏等情况,并处理至合格。
8)、建立注油系统:加入分析合格的润滑油进注油箱,保持油位1/2以上,然后用手盘动手柄数圈,无问题后开启注油器建立注油系统,并检查注油情况,如有泄漏、堵塞等现象,则停止注油,待处理合格后重新建立注油系统。
焦炉气制甲醇工艺介绍

焦炉气制甲醇工艺介绍作者:陈晨曦来源:《科技资讯》 2011年第25期陈晨曦(新疆中泰化学(集团)股份有限公司乌鲁木齐 830009)摘要:焦炉煤气制甲醇是资源合理利用的变废为宝项目,具有广阔的前景,本文重点分析了焦炉气制甲醇工艺中的关键技术。
关键词:焦炉煤气净化脱硫催化转化催化剂氢碳比中图分类号:TQ53 文献标识码:A 文章编号:1672-3791(2011)09(a)-0119-011 焦炉煤气1.1 焦炉煤气的组成与杂质含量一般焦炉煤气的主要成份为H2、CO、CH4、CO2等,各成份所占比例如表1所示。
同时也含有一些杂质如表2所示。
1.2 焦炉煤气的利用焦炉煤气是极好的气体燃料,同时又是宝贵的化工原料气,焦炉煤气被净化后可以作为城市燃气来使用,从其成份上来看也是制造甲醇、合成氨、提取氢气的很好的原料。
2 焦炉煤气制甲醇的基本工艺流程如图1所示,为焦炉煤气制造甲醇最基本的工艺流程,净化与转化在整个焦炉煤气制甲醇流程中的关键技术。
3 焦炉煤气的净化工艺焦炉气的净化总的来说有三大步骤:(1)焦炉气经过捕捉、洗涤、脱酸蒸氨等化工过程,将有害的物质脱除到甲醇合成催化剂所要求的精度,进入焦炉气柜;(2)脱硫,分无机硫的脱除和有机硫的脱除,具体的方法根据系统选择工艺方案而改变;(3)焦炉煤气的深度净化,在精脱硫后再深度脱除氯离子和羰基金属,防止其对甲醇合成催化剂的毒害。
脱硫工艺技术方案:(1)几乎全部的无机硫和极少部分的有机硫能够在焦化厂化产湿法脱硫时脱掉;(2)绝大部分的有机硫的脱除采用的是干法脱除,具体的有分为4种:吸收法、水解法、热解法和加氢转化法,其中水解法和加氢转化法在国内外化工工艺上用的最为普遍。
4 焦炉煤气的烷烃转化技术目前具体的方法有:蒸汽转化工艺、纯氧非催化部分氧化转化工艺、纯氧催化部分氧化转化工艺。
4.1 蒸汽转化工艺其原理类似于天然气制甲醇两段转化中的一段炉转化机理,不过考虑到焦炉煤气的甲烷含量只有天然气的1/4,所以在焦炉煤气制造甲烷的实际工艺选择中,该方法一般不被采用。
焦炉煤气制甲醇工艺的概述

焦炉煤气制甲醇工艺的概述摘要:本文介绍了利用焦炉副产品——焦炉煤气生产15万吨/年甲醇工艺及特点,并对此工艺进行了评价,提出了建议。
关键词:焦炉煤气;纯氧催化;制甲醇在未投建焦炉煤气制甲醇之前河北华丰能源科技发展有限公司焦炭的年综合生产能力已达到336万吨,此外还有3MW、6MW、2×15MW中温中压发电机组、30MW高温高压发电机组发电厂各一座。
为了抓住市场机遇,增加经济效益,充分利用丰富的焦炉煤气,河北华丰煤化电力有限公司总投资38475万元实施年产15万吨焦炉气制甲醇工程项目,以焦炉煤气为原料生产甲醇。
作一概述:1、生产规模和工艺路线本工程是利用每小时产35000标立米的焦炉煤气生产甲醇设计的,按年作业时间8000小时算,可年产甲醇15万吨,产品的质量指标达到GB338---92标准。
我公司生产的焦炉气甲烷含量达24%~28%,根据煤气组成采用纯氧催化部分转化工艺将甲烷及少量多碳烃转化为合成甲醇的有用成分一CO和H,以满足生产甲醇的基本要求。
工艺流程示意图2、工艺流程概述2.1预处理工序从焦化装置送来的焦炉气中还含有部分焦油、萘、粉尘等易凝或易结晶的物质,在常温常压下,这些物质也许不会凝结或结晶,但经加压后,由于其分压上升,造成其中部分物质凝结为液滴或固体颗粒,这些物质如不除去,将对后工序造成危害。
本工艺采用对焦炉气中焦油和萘具有极强吸附能力的焦炭颗粒做吸附剂,吸附焦油和萘后的焦炭颗粒进行相关处理。
该工艺的特点是:吸附剂廉价易得、吸附选择性好、吸附容量大、对焦油和萘的脱除率高(脱油率≥90%,脱萘率≥80%)且吸附条件温和(常温常压下即可实现)。
2.2气柜工序焦炉气的产生量是波动的,而甲醇装置的生产用气要求相对稳定,因此,在焦炉气供应系统设计中必须采取有效的稳压措施。
本装置采用外导架直升式湿式气柜,对原料焦炉气起着稳定供气的缓冲作用,可以有效地协调气源与后续工序用气之间的动态平衡。
焦炉煤气制甲醇和制天然气对比分析
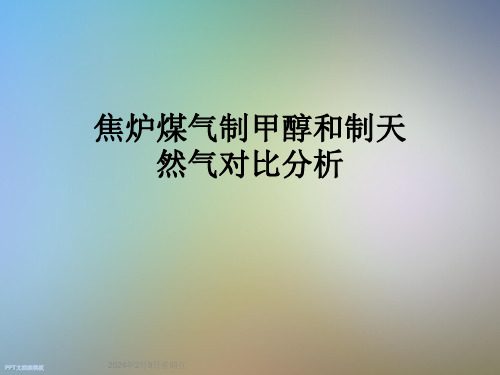
31.0926.77焦炉煤气制甲醇 28518 24000 190 160
甲醇 10 万吨/年
弛放气 2100 万m3/年
2100 21218 18555 1551 1164 11.07 7.51 8.26 73.43
2300 23189 18437 3326 2495 18.04 13.32 6.18 55.62
•故焦炉气制甲醇的 •能量利用率 •为51.1%~ •58.2%。
2024/2/9
•9
•两种产品经济性对比
•以25000 m3/h 焦炉气为基准
项目 项目总投资/万元
固定资产总投资/万元
占地面积/亩 定员/人
产品
产品价格 年均销售收入/万元 年均总成本费用/万元 年均利润总额/万元 年均税后利润/万元 财务税前收益率%
焦炉煤气制甲醇和制天 然气对比分析
2024年2月9日星期五
•国内焦炭及焦炉煤气利用情况
•2009年国内焦炭总量为:35364万吨,其中:钢铁联合焦化企业:13405万吨,独立 •焦化企业:21959万吨。
•按每吨焦炭副产430Nm3焦炉煤气计算,独立焦化企业每年副产焦炉煤气约940亿Nm3, •除企业自身作加热燃料和化工原料(制甲醇)外,每年有约220亿Nm3焦炉煤气需考虑 •出路问题。
因此,用焦炉气生产CNG/LNG,将产生较明显的经 济效益、环境效益与社会效益,对促进焦化与能 源行业的技术进步与产业发展具有重要的意义。
2024/2/9
•3
•两种产品工艺流程对比 •焦炉气制甲醇工艺流程
•空气
•空分
•焦炉煤气 •深度净化 •催化转化
•废热回收 •精脱硫
•蒸汽
•弛放气
•合成甲醇 •压缩
焦炉气制甲醇工艺流程
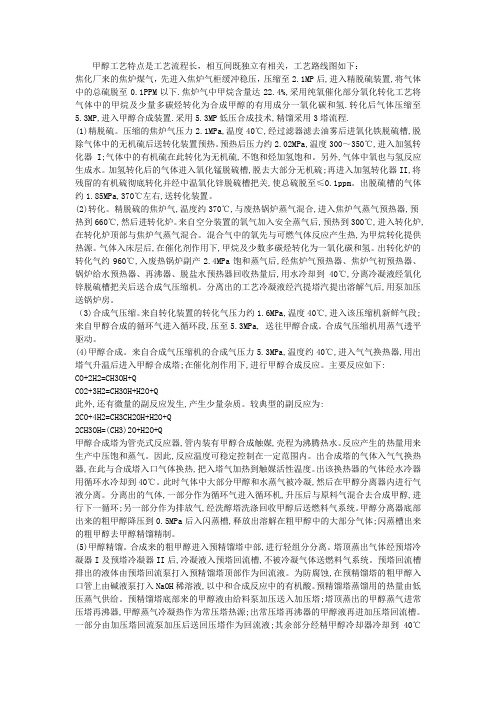
甲醇工艺特点是工艺流程长,相互间既独立有相关,工艺路线图如下:焦化厂来的焦炉煤气,先进入焦炉气柜缓冲稳压,压缩至2.1MP后,进入精脱硫装置,将气体中的总硫脱至0.1PPM以下.焦炉气中甲烷含量达22.4%,采用纯氧催化部分氧化转化工艺将气体中的甲烷及少量多碳烃转化为合成甲醇的有用成分一氧化碳和氢.转化后气体压缩至5.3MP,进入甲醇合成装置.采用5.3MP低压合成技术,精馏采用3塔流程.(1)精脱硫。
压缩的焦炉气压力2.1MPa,温度40℃,经过滤器滤去油雾后进氧化铁脱硫槽,脱除气体中的无机硫后送转化装置预热。
预热后压力约2.02MPa,温度300~350℃,进入加氢转化器I;气体中的有机硫在此转化为无机硫,不饱和烃加氢饱和。
另外,气体中氧也与氢反应生成水。
加氢转化后的气体进入氧化锰脱硫槽,脱去大部分无机硫;再进入加氢转化器II,将残留的有机硫彻底转化并经中温氧化锌脱硫槽把关,使总硫脱至≤0.1ppm。
出脱硫槽的气体约1.85MPa,370℃左右,送转化装置。
(2)转化。
精脱硫的焦炉气,温度约370℃,与废热锅炉蒸气混合,进入焦炉气蒸气预热器,预热到660℃,然后进转化炉。
来自空分装置的氧气加入安全蒸气后,预热到300℃,进入转化炉,在转化炉顶部与焦炉气蒸气混合。
混合气中的氧先与可燃气体反应产生热,为甲烷转化提供热源。
气体入床层后,在催化剂作用下,甲烷及少数多碳烃转化为一氧化碳和氢。
出转化炉的转化气约960℃,入废热锅炉副产2.4MPa饱和蒸气后,经焦炉气预热器、焦炉气初预热器、锅炉给水预热器、再沸器、脱盐水预热器回收热量后,用水冷却到40℃,分离冷凝液经氧化锌脱硫槽把关后送合成气压缩机。
分离出的工艺冷凝液经汽提塔汽提出溶解气后,用泵加压送锅炉房。
(3)合成气压缩。
来自转化装置的转化气压力约1.6MPa,温度40℃,进入该压缩机新鲜气段;来自甲醇合成的循环气进入循环段,压至5.3MPa, 送往甲醇合成。
10万吨焦炉气制甲醇操作法资料
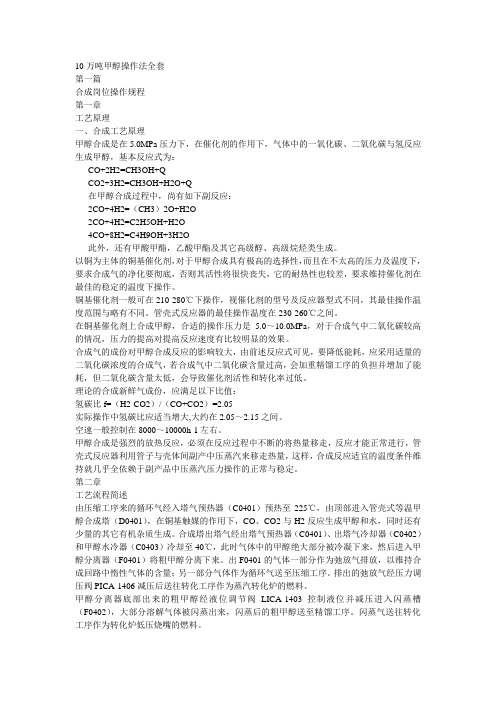
10万吨甲醇操作法全套第一篇合成岗位操作规程第一章工艺原理一、合成工艺原理甲醇合成是在5.0MPa压力下,在催化剂的作用下,气体中的一氧化碳、二氧化碳与氢反应生成甲醇,基本反应式为:CO+2H2=CH3OH+QCO2+3H2=CH3OH+H2O+Q在甲醇合成过程中,尚有如下副反应:2CO+4H2=(CH3)2O+H2O2CO+4H2=C2H5OH+H2O4CO+8H2=C4H9OH+3H2O此外,还有甲酸甲酯,乙酸甲酯及其它高级醇、高级烷烃类生成。
以铜为主体的铜基催化剂,对于甲醇合成具有极高的选择性,而且在不太高的压力及温度下,要求合成气的净化要彻底,否则其活性将很快丧失,它的耐热性也较差,要求维持催化剂在最佳的稳定的温度下操作。
铜基催化剂一般可在210-280℃下操作,视催化剂的型号及反应器型式不同,其最佳操作温度范围与略有不同。
管壳式反应器的最佳操作温度在230-260℃之间。
在铜基催化剂上合成甲醇,合适的操作压力是 5.0~10.0MPa,对于合成气中二氧化碳较高的情况,压力的提高对提高反应速度有比较明显的效果。
合成气的成份对甲醇合成反应的影响较大,由前述反应式可见,要降低能耗,应采用适量的二氧化碳浓度的合成气,若合成气中二氧化碳含量过高,会加重精馏工序的负担并增加了能耗,但二氧化碳含量太低,会导致催化剂活性和转化率过低。
理论的合成新鲜气成份,应满足以下比值:氢碳比f=(H2-CO2)/(CO+CO2)=2.05实际操作中氢碳比应适当增大,大约在2.05~2.15之间。
空速一般控制在8000~10000h-1左右。
甲醇合成是强烈的放热反应,必须在反应过程中不断的将热量移走,反应才能正常进行,管壳式反应器利用管子与壳体间副产中压蒸汽来移走热量,这样,合成反应适宜的温度条件维持就几乎全依赖于副产品中压蒸汽压力操作的正常与稳定。
第二章工艺流程简述由压缩工序来的循环气经入塔气预热器(C0401)预热至225℃,由顶部进入管壳式等温甲醇合成塔(D0401),在铜基触媒的作用下,CO、CO2与H2反应生成甲醇和水,同时还有少量的其它有机杂质生成。
焦炉煤气制甲醇的原理
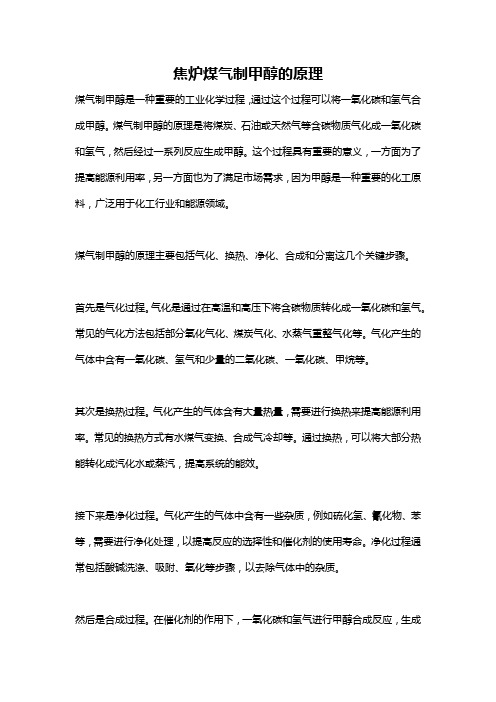
焦炉煤气制甲醇的原理煤气制甲醇是一种重要的工业化学过程,通过这个过程可以将一氧化碳和氢气合成甲醇。
煤气制甲醇的原理是将煤炭、石油或天然气等含碳物质气化成一氧化碳和氢气,然后经过一系列反应生成甲醇。
这个过程具有重要的意义,一方面为了提高能源利用率,另一方面也为了满足市场需求,因为甲醇是一种重要的化工原料,广泛用于化工行业和能源领域。
煤气制甲醇的原理主要包括气化、换热、净化、合成和分离这几个关键步骤。
首先是气化过程。
气化是通过在高温和高压下将含碳物质转化成一氧化碳和氢气。
常见的气化方法包括部分氧化气化、煤炭气化、水蒸气重整气化等。
气化产生的气体中含有一氧化碳、氢气和少量的二氧化碳、一氧化碳、甲烷等。
其次是换热过程。
气化产生的气体含有大量热量,需要进行换热来提高能源利用率。
常见的换热方式有水煤气变换、合成气冷却等。
通过换热,可以将大部分热能转化成汽化水或蒸汽,提高系统的能效。
接下来是净化过程。
气化产生的气体中含有一些杂质,例如硫化氢、氰化物、苯等,需要进行净化处理,以提高反应的选择性和催化剂的使用寿命。
净化过程通常包括酸碱洗涤、吸附、氧化等步骤,以去除气体中的杂质。
然后是合成过程。
在催化剂的作用下,一氧化碳和氢气进行甲醇合成反应,生成甲醇。
甲醇的合成反应通常在高压和高温下进行,常见的催化剂有铜锌或铜铝复合催化剂,也可以使用高压合成氨法的氮碘化铁作为催化剂。
最后是分离过程。
合成产物中还含有一些未反应的气体和液体,需要进行分离提取。
分离过程通常包括蒸馏、吸附、结晶等步骤,以分离出纯度较高的甲醇产品。
总体来说,煤气制甲醇的原理是通过气化、换热、净化、合成和分离这几个关键步骤,将含碳物质转化成甲醇。
这个过程需要合理设计反应条件,选择适当的催化剂和分离工艺,以提高甲醇的产率和纯度。
除了化学反应过程,还需要考虑能源利用、环境保护、安全生产等方面的问题。
煤气制甲醇的原理在工业化生产中得到了广泛应用,尤其是在能源匮乏的地区。
焦炉气制甲醇工艺流程

焦炉气制甲醇工艺流程焦炉气制甲醇工艺是一种利用焦炉煤气来制造甲醇的工艺。
甲醇是一种重要的化学原料,广泛应用于合成化学品、塑料、染料、涂料等领域。
本文将介绍焦炉气制甲醇的工艺流程。
焦炉煤气是焦炉生产焦炭时产生的一种副产品。
焦炭的主要成分是炭,但焦炉煤气中还含有一定的甲烷、氢气、氮气、一氧化碳等物质。
焦炉气制甲醇的工艺利用焦炉煤气中的甲烷和一氧化碳作为原料,通过一系列的反应和分离步骤最终制得甲醇。
首先,焦炉煤气经过除尘处理,去除其中的灰尘和颗粒物。
然后进入加热炉,在高温下进行加热,使其温度逐渐升高。
接下来,焦炉煤气经过预热、空气混合等步骤后进入主炉。
在主炉中,甲烷和一氧化碳发生催化反应,生成甲醇。
这个反应需要高温和压力作为条件,因此需要在主炉中提供适宜的反应条件。
在主炉中,焦炉煤气进入催化剂层,与催化剂接触后发生化学反应。
甲烷和一氧化碳在催化剂的作用下发生部分氧化反应生成甲醇。
同时,甲烷和一氧化碳也会发生副反应,产生一些副产物。
催化剂的选择和使用也是影响工艺效率的关键因素之一。
甲醇生成后,焦炉煤气中的其他组分如氢气、氮气等会通过分离步骤进行分离和回收利用。
这些物质对于后续的工艺步骤来说并不是主要原料,但它们可以被转化为其他有用的化学品。
最后,焦炉气制甲醇工艺也需要一个合适的能源供应系统,确保反应过程中的能量平衡和稳定供应。
这个系统包括锅炉、换热器、循环泵等设备。
总之,焦炉气制甲醇是一种利用焦炉煤气制造甲醇的工艺。
它可以将焦炉煤气中的甲烷和一氧化碳转化为甲醇,并且将其他组分进行分离和回收利用。
这个工艺在化工行业中有着广泛的应用前景,为能源的有效利用和环境保护做出了贡献。
- 1、下载文档前请自行甄别文档内容的完整性,平台不提供额外的编辑、内容补充、找答案等附加服务。
- 2、"仅部分预览"的文档,不可在线预览部分如存在完整性等问题,可反馈申请退款(可完整预览的文档不适用该条件!)。
- 3、如文档侵犯您的权益,请联系客服反馈,我们会尽快为您处理(人工客服工作时间:9:00-18:30)。
焦炉气制甲醇焦炉煤气制甲醇的工艺技术研究2008-06-05 14:49 吴创明(新奥集团股份有限公司,河北廊坊065001) 近年来,随着钢铁工业对焦炭的巨大需求而高速发展起来的炼焦产业,在焦炭产能无序扩张、产量大幅度增长的同时,大量副产的焦炉煤气导致了焦炭产区的环境急剧恶化,不少单一炼焦的**焦化企业“只焦不化”,将大量的焦炉煤气采取点天灯的方式燃烧放散,既严重污染环境,又造成资源浪费。
作为贫油、缺气的能源需求大国,如何充分、合理地利用大量点天灯的焦炉煤气,对建设资源节源型社会,实现经济可持续发展具有重要意义。
1 焦炉煤气的利用途径1.1 焦炉煤气的组成与杂质含量焦炉煤气的主要组分为H2、CO、CH4、CO2等,随着炼焦配比和操作工艺参数的不同,焦炉煤气的组成略有变化。
一般焦炉煤气的组成见表1,杂质含量见表2。
表1 焦炉煤气的组成组分 H2 CO CO2 CH4 CmHn N2 O2,(V) 54.0,59.0 5.0,8.0 2.0,4.0 23.0,27.0 2.0,3.0 3.0,6.0 0.2,0.4 表2 焦炉煤气中的杂质含量(mg/m3)名称焦油苯萘硫化氢 COS 二硫化碳氨噻吩类杂质含量微量 2000,5000 300 100 100 80,100 300 20,501.2 焦炉煤气的综合利用途径焦炉煤气是很好的气体燃料和宝贵的化工原料气,净化后的焦炉煤气除用作城市燃气外,还可用于制造甲醇、合成氨、提取氢气和发电,其中以制造甲醇的附加值最高,经济效益最好。
若将全国每年放散的350×108 m3焦炉煤气全用于制造甲醇,可产甲醇1 600万吨,可大大缓解我国石油供应的紧张局面,从而带动经济高速发展。
2 焦炉煤气制甲醇的工艺技术2.1 焦炉煤气制甲醇的工艺流程 2004年底,世界上第一套8万t/ a焦炉煤气制甲醇项目在云南曲靖建成投产以来,目前国内已有近10套焦炉煤气制甲醇装置已投入商业运行,单套装置设计规模多为10,20万t/a,其工艺流程见图1。
首先,将来自焦化厂经过预处理的焦炉煤气送进储气罐缓冲稳压、压缩增压,接着进行加氢转化精脱硫,使其总硫体积分数?0. 1×10,6,此即焦炉煤气的净化;然后通过催化或非催化方法将焦炉煤气中的CH4、CmHn转化为合成甲醇的有效气体组分(H2 + CO),再通过补碳(即用煤炭制气、压缩、脱硫、脱碳,制成碳多氢少的水煤气加进原料气中)调整原料气的氢碳比,就制成了氢碳比符合甲醇合成所需的合成气;将合成气压缩增压后送入甲醇合成塔进行合成反应,生成粗甲醇,然后对粗甲醇进行精馏,就制成了煤基清洁能源和用途广泛的有机化工原料精甲醇。
在上述工艺流程中,净化与转化是整个焦炉煤气制甲醇的关键技术。
2.2 焦炉煤气的净化工艺 (1)焦炉煤气的净化要求。
焦炉煤气中的杂质含量高,净化难度大,净化成本高,制约了其作为化工原料气的用途和经济性。
通常经过焦化厂净化处理的焦炉煤气,仍然含有微量焦油、苯、萘、氨、氰化氢、Cl,、不饱和烯烃、硫化氢、噻吩、硫醚、硫醇、COS和二硫化碳等杂质。
其中,焦油、苯、萘、不饱和烯烃会在后续的焦炉煤气转化和甲醇合成中分解析碳而影响催化剂的活性;由无机硫与有机硫组成的混合硫化物和C1,及羰基金属等杂质是焦炉煤气转化和甲醇合成催化剂的毒物,会导致转化与合成催化剂永久性中毒而失活。
因此,彻底脱除杂质,深度净化焦炉煤气,是焦炉煤气资源化利用的关键。
图1 焦炉煤气制甲醇的工艺流程焦炉煤气中含有的噻吩、硫醚、硫醇等有机硫,形态复杂,化学稳定性高,现有的湿法脱硫对其几乎不起作用,必须采取干法脱硫将有机硫脱除。
若来自焦化厂的煤气是未脱硫的粗煤气,则必须先进行化产湿法脱硫,使原料气中的硫含量尽可能减少,以减轻干法脱硫的负担,延长加氢转化脱硫剂的使用寿命。
然后再进行干法加氢转化精脱硫,即采取湿法与干法脱硫相结合的方式进行净化精制。
首先,粗煤气先经冷凝、电捕焦油、湿法脱硫、脱氰、脱氨、洗苯等操作,脱除焦炉煤气中的焦油、萘、硫化氢、氰化氢、氨、苯等物质,并加以回收。
经上述处理后,可将焦炉煤气中的硫化氢脱至20 mg/m3以下,同时可脱去少量有机硫,但有机硫含量仍然较高。
然后再进行干法精脱硫,使焦炉煤气满足净化后总硫体积分数?0. 1×10-6的要求。
(2)精脱硫的技术方案。
焦炉煤气中含有的绝大部分无机硫和极少部分有机硫可在焦化厂的湿法脱硫时脱掉,而绝大部分有机硫只能采用干法脱除。
干法脱除有机硫有4种方法,即吸收法、热解法、水解法、加氢转化法,目前国内外主要采用水解法和加氢转化法脱除有机硫。
水解法脱除有机硫时,由于操作温度为中低温,可避免强放热的甲烷化副反应发生,是目前国内外脱除煤气中有机硫十分活跃的研究领域。
但水解催化剂的活性随温度的升高和煤气中氧含量的增大而急剧下降,且对COS和二硫化碳的水解效果较好,对煤气中的噻吩、硫醚、硫醇基本不起作用,这是水解法脱除有机硫的致命缺陷。
焦炉煤气经湿法脱硫后可脱去绝大部分硫化氢和少量的有机硫。
脱硫的技术瓶颈是如何深度脱除形态复杂、难以用常规方法分解的有机硫,尤其是化学稳定性高、难以分解的噻吩、硫醚、硫醇类有机硫,一般需采用加氢转化法将其转化为无机硫后再脱除。
常用的有机硫加氢转化催化剂有钴钼、铁钼、镍钼等类型,加氢转化的氢气来自于焦炉煤气。
由于焦炉煤气含有较高浓度的CO和CO2,选择加氢脱硫方案时应注意几点: ? 对噻吩类有机硫加氢分解性能好的加氢催化剂会诱导碳氧化物发生对加氢工艺不利的强放热的甲烷化反应,应尽可能避免或减轻CO和CO2在加氢催化剂上发生甲烷化反应。
? 应尽可能提高噻吩、硫醚、硫醇等有机硫的加氢转化率。
? 应避免CO和不饱和烯烃在加氢转化时分解析碳而降低催化剂的活性。
传统的钴钼加氢催化剂的价格昂贵,主要用于以天然气为原料的加氢转化精脱硫。
在CO、CO2含量较高的气体中,易发生析碳和甲烷化副反应。
通常焦炉煤气中含有体积分数为5,,8,的CO,不宜采用钴钼加氢催化剂的脱硫方案。
根据焦炉煤气中有机硫的含量和形态,总结近几年国内建设的几套焦炉煤气制甲醇加氢脱硫装置的经验教训,对焦炉煤气有机硫净化可采取铁钼十镍钼两级加氢、铁锰,氧化锌两级吸收的方式。
操作条件为:温度约350?、压力约2. 3 MPa。
工艺流程为:铁钼加氢转化?铁锰粗脱硫?镍钼加氢转化?氧化锌精脱硫。
先采用活性较低、反应平缓的铁钼加氢催化剂(JT,8)打头阵,避免反应激烈使催化剂床层温升太快,原料气经过一级加氢转化后,用便宜但硫容较低的铁锰脱硫剂脱除转化的硫化氢; 再用活性高、有机硫转化率高的镍钼催化剂(JT,1)进行二级加氢转化;最后用价格贵但硫容较高的氧化锌精脱硫剂把关,保证经精脱硫后原料气的总硫体积分数?0. 1×10 -6,同时可将不饱和烃加氢转化为饱和烃,将微量的氧气与氢气反应生成水,使原料气中的杂质满足后续转化与合成的要求。
其主要化学反应为: C4H4S+4H2 ? C4H10,H2S (1) R-SH+H2 ? RH+H2S (2) R1-S-R2+2H2 ? R1H,R2H,H2S (3) COS,H2 ? CO,H2S (4) COS,H2O ? CO2,H2S (5) CS2,4H2 ? CH4,2H2S (6) C2H4,H2 ? C2H6 (7) C2H2,2H2 ? C2H6 (8) O2,2H2 ? 2H2O (9) MnO,H2S ? MnS,H2O (10) Fe3O4,3H2S,H2 ? 3 FeS,4H2O (11) ZnO,H2S ? ZnS,H2O (12) 该方案在河北、山东、陕西等省焦炉煤气制甲醇的净化工段使用,脱除有机硫效果良好。
(3)焦炉煤气加氢转化的技术难点。
采用加氢转化效果良好的铁钼、镍钼催化剂,虽然可将焦炉煤气中的化学性质稳定的噻吩类有机硫加氢分解为易于脱除的无机硫,使不饱和烃在加氢条件下转化为饱和烃,减少了杂质含量,但由于原料气中同时含有高浓度的CO和CO2,在加氢催化剂作用下,会发生如下副反应: CO,3H2 ? CH4,H2O (13) CO2,4H2 ? CH4,2H2O (14) 2CO ? C,CO2 (15) 反应式(13)、(14)是强放热的甲烷化反应,对原料气净化精制极其有害;反应式(15)为强放热的CO歧化析碳反应。
这些副反应放出的反应热会引起催化剂床层温度迅速升高,促使烃类分解,析碳增多,会堵塞催化剂孔道和活性点,导致催化剂活性位减少,使催化剂床温失控,引起催化剂过热失活。
这是使用对噻吩类加氢分解性能好的加氢转化催化剂的技术难点,应采取相应的工艺措施,抑制上述副反应的发生,将催化剂床层温度严格控制在350?以下“,防止催化剂过热老化。
(4)焦炉煤气的深度净化。
焦炉煤气的深度净化,就是精脱硫后再脱除Cl,和羰基金属。
焦炉煤气中含有的Cl,将会导致催化剂活性大幅度下降,其对转化与合成催化剂的危害更甚于硫。
此外,Cl,具有很高的迁移性,其造成催化剂中毒往往是全床性的。
Cl,还会严重腐蚀生产设备与管道。
另外,焦炉煤气中微量的羰基金属(羰基铁、羰基镍)等杂质也会导致甲醇合成催化剂中毒失活。
因此焦炉煤气精脱硫后必须深度净化脱除氯和羰基金属,防止其对甲醇合成催化剂的毒害。
2.3 焦炉煤气的烷烃转化技术通常,焦炉煤气中CH4的体积分数约23%,27%, CmHn的体积分数约2,,3%,在甲醇合成中,CH4和CmHn都不参与甲醇的合成反应,其作为惰性气体存在于合成气中并往复循环。
如何将占焦炉煤气体积分数约30,的烷烃(CH4和CmHn )全部转化为合成气的有效组分(H2,CO),提高合成效率,最大限度地降低了不参加甲醇合成反应的气体组分(CH4、CmHn、N2、Ar),减少甲醇合成回路的循环气量,降低单位甲醇产量的功耗,是焦炉煤气制甲醇的关键技术和难点之一。
焦炉煤气烷烃转化重整工艺目前主要有蒸汽转化工艺、纯氧非催化部分氧化转化工艺、纯氧催化部分氧化转化工艺。
(1)蒸汽转化工艺。
焦炉煤气的蒸汽转化工艺类似于天然气制甲醇两段转化中的一段炉转化机理,其主要反应为: CH4,H2O ? CO,3H2 (16) 反应式(16)为吸热反应,提高温度,有利于甲烷的转化。
反应中需在反应管外燃烧燃料气间接外供热量,反应管需用耐高温的镍铬不锈钢制造,转化炉喷嘴多,结构复杂,制造要求高,造价高。
常用于天然气的一段转化,焦炉煤气的甲烷含量仅为天然气的1/4,一般不采用蒸汽转化工艺。
(2)纯氧非催化部分氧化转化工艺。
在纯氧非催化部分氧化转化工艺中,主要的转化反应分两个阶段,第一阶段为CH4、H2和CO的燃烧放热反应;第二阶段为甲烷转化为H2和CO阶段,是吸热的二次反应,为整个转化工艺的控制步骤,其反应式为: CH4,H2O ? CO,3H2 (17) 合成甲醇时,要求新鲜合成气中CH4的体积分数低于0.4%。