焦炉煤气制甲醇
焦炉煤气制甲醇技术
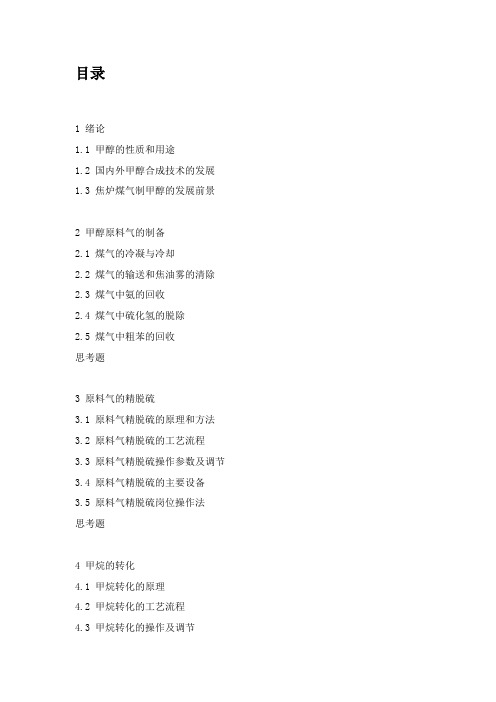
目录1 绪论1.1 甲醇的性质和用途1.2 国内外甲醇合成技术的发展1.3 焦炉煤气制甲醇的发展前景2 甲醇原料气的制备2.1 煤气的冷凝与冷却2.2 煤气的输送和焦油雾的清除2.3 煤气中氨的回收2.4 煤气中硫化氢的脱除2.5 煤气中粗苯的回收思考题3 原料气的精脱硫3.1 原料气精脱硫的原理和方法3.2 原料气精脱硫的工艺流程3.3 原料气精脱硫操作参数及调节3.4 原料气精脱硫的主要设备3.5 原料气精脱硫岗位操作法思考题4 甲烷的转化4.1 甲烷转化的原理4.2 甲烷转化的工艺流程4.3 甲烷转化的操作及调节4.4 甲烷转化的影响因素4.5 甲烷转化的催化剂4.6 甲烷转化的主要设备4.7 甲烷转化的岗位操作思考题5 甲醇的合成5.1 甲醇合成的原理和方法5.2 甲醇合成的工艺流程5.3 甲醇合成的操作及影响因素5.4 甲醇合成的催化剂5.5 甲烷合成的主要设备5.6 甲醇合成的岗位操作法思考题6 粗甲醇的精制6.1 粗甲醇精馏的原理和方法6.2 粗甲醇精馏的工艺流程6.3 粗甲醇精馏操作与工艺调节6.4 粗甲醇精馏的设备6.5 粗甲醇精馏的岗位操作思考题7 甲醇质量检验与生产监控7.1 甲醇成品分析7.2 甲醇中间品的控制分析7.3 气体中微量总硫和形态硫的测定7.4 分析室安全规则8 甲醇清洁生产与安全8.1 甲醇清洁生产8.2 甲醇安全生产知识补充资料一、HT-306中温氧化铁脱硫剂升温还原方案二、Z205/Z204转化催化剂技术规格三、C307型合成甲醇催化剂使用说明书四、焦炉煤气压缩机岗位操作法五、合成气压缩机岗位操作法六、综合练习题参考文献。
十万吨焦炉煤气制甲醇的操作规程
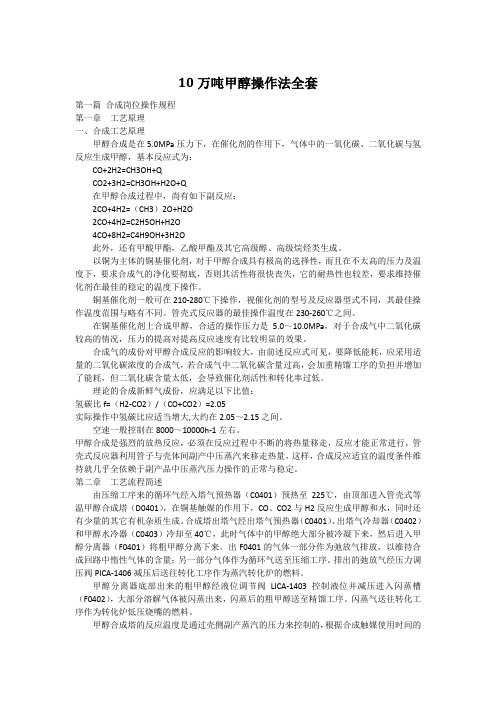
10万吨甲醇操作法全套第一篇合成岗位操作规程第一章工艺原理一、合成工艺原理甲醇合成是在5.0MPa压力下,在催化剂的作用下,气体中的一氧化碳、二氧化碳与氢反应生成甲醇,基本反应式为:CO+2H2=CH3OH+QCO2+3H2=CH3OH+H2O+Q在甲醇合成过程中,尚有如下副反应:2CO+4H2=(CH3)2O+H2O2CO+4H2=C2H5OH+H2O4CO+8H2=C4H9OH+3H2O此外,还有甲酸甲酯,乙酸甲酯及其它高级醇、高级烷烃类生成。
以铜为主体的铜基催化剂,对于甲醇合成具有极高的选择性,而且在不太高的压力及温度下,要求合成气的净化要彻底,否则其活性将很快丧失,它的耐热性也较差,要求维持催化剂在最佳的稳定的温度下操作。
铜基催化剂一般可在210-280℃下操作,视催化剂的型号及反应器型式不同,其最佳操作温度范围与略有不同。
管壳式反应器的最佳操作温度在230-260℃之间。
在铜基催化剂上合成甲醇,合适的操作压力是5.0~10.0MPa,对于合成气中二氧化碳较高的情况,压力的提高对提高反应速度有比较明显的效果。
合成气的成份对甲醇合成反应的影响较大,由前述反应式可见,要降低能耗,应采用适量的二氧化碳浓度的合成气,若合成气中二氧化碳含量过高,会加重精馏工序的负担并增加了能耗,但二氧化碳含量太低,会导致催化剂活性和转化率过低。
理论的合成新鲜气成份,应满足以下比值:氢碳比f=(H2-CO2)/(CO+CO2)=2.05实际操作中氢碳比应适当增大,大约在2.05~2.15之间。
空速一般控制在8000~10000h-1左右。
甲醇合成是强烈的放热反应,必须在反应过程中不断的将热量移走,反应才能正常进行,管壳式反应器利用管子与壳体间副产中压蒸汽来移走热量,这样,合成反应适宜的温度条件维持就几乎全依赖于副产品中压蒸汽压力操作的正常与稳定。
第二章工艺流程简述由压缩工序来的循环气经入塔气预热器(C0401)预热至225℃,由顶部进入管壳式等温甲醇合成塔(D0401),在铜基触媒的作用下,CO、CO2与H2反应生成甲醇和水,同时还有少量的其它有机杂质生成。
焦炉煤气制甲醇物料平衡计算
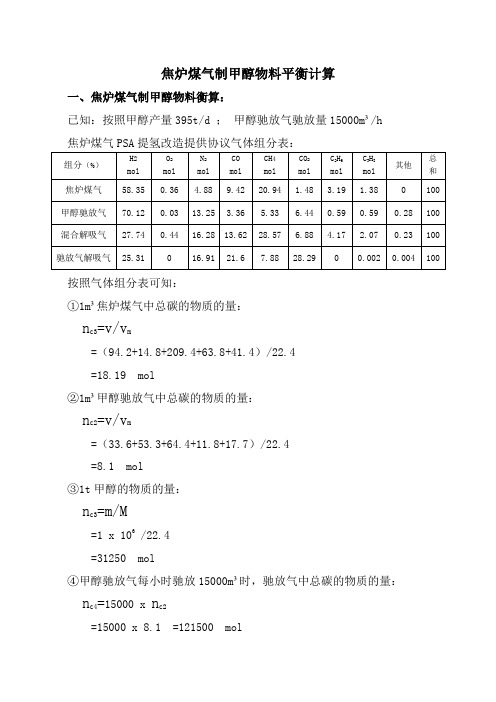
焦炉煤气制甲醇物料平衡计算一、焦炉煤气制甲醇物料衡算:已知:按照甲醇产量395t/d ;甲醇驰放气驰放量15000m³/h焦炉煤气PSA提氢改造提供协议气体组分表:按照气体组分表可知:①1m³焦炉煤气中总碳的物质的量:n c3=v/v m=(94.2+14.8+209.4+63.8+41.4)/22.4=18.19 mol②1m³甲醇驰放气中总碳的物质的量:n c2=v/v m=(33.6+53.3+64.4+11.8+17.7)/22.4=8.1 mol③1t甲醇的物质的量:n c3=m/M=1 x 106 /22.4=31250 mol④甲醇驰放气每小时驰放15000m³时,驰放气中总碳的物质的量:n c4=15000 x n c2=15000 x 8.1 =121500 mol⑤理论计算:生产1t甲醇所需焦炉煤气量为:V1= n c3/ n c3=31250/18.19 = 1718 m³⑥理论计算:每小时生产16.46t甲醇所需焦炉煤气量为:V2=V1*16.46 =28277.9m³/h⑦甲醇驰放气每小时驰放15000m³时,所需焦炉煤气的量为:V3=15000 /n c3=15000/18.19 =6679 m³/h由①②③④⑤⑥⑦式可知:每小时生产16.64t甲醇所需要焦炉煤气总量为:V总= V2+ V3 = 28277.9 + 6679 =34957.4 m³/h二、焦炉煤气和甲醇驰放气混合提氢物料计算已知:按照相关技术协议使用甲醇驰放气为原料提氢收率为81%;使用焦炉煤气为原料提氢收率为75%;按照供给总氢气量为18000m³/h:甲醇驰放气量15000 m³/h时:氢气=8520 m³/h ;解吸气量=6480 m³/h;焦炉煤气量21714 m³/h时:氢气=9480 m³/h ;解吸气量=12234 m³/h;。
焦炉煤气制甲醇工艺之合成操作规程
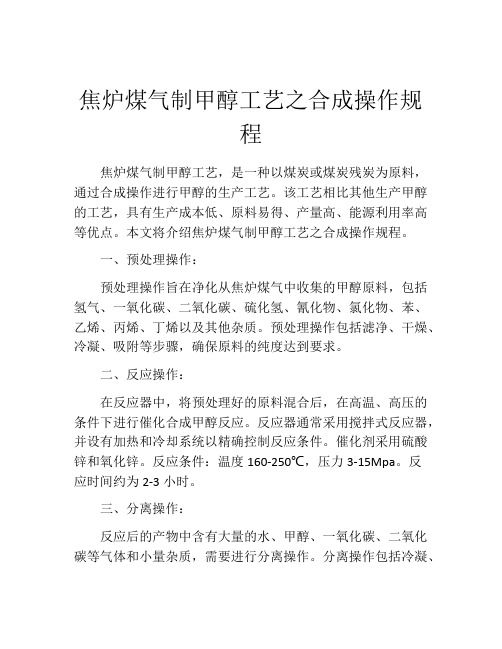
焦炉煤气制甲醇工艺之合成操作规程焦炉煤气制甲醇工艺,是一种以煤炭或煤炭残炭为原料,通过合成操作进行甲醇的生产工艺。
该工艺相比其他生产甲醇的工艺,具有生产成本低、原料易得、产量高、能源利用率高等优点。
本文将介绍焦炉煤气制甲醇工艺之合成操作规程。
一、预处理操作:预处理操作旨在净化从焦炉煤气中收集的甲醇原料,包括氢气、一氧化碳、二氧化碳、硫化氢、氰化物、氯化物、苯、乙烯、丙烯、丁烯以及其他杂质。
预处理操作包括滤净、干燥、冷凝、吸附等步骤,确保原料的纯度达到要求。
二、反应操作:在反应器中,将预处理好的原料混合后,在高温、高压的条件下进行催化合成甲醇反应。
反应器通常采用搅拌式反应器,并设有加热和冷却系统以精确控制反应条件。
催化剂采用硫酸锌和氧化锌。
反应条件:温度160-250℃,压力3-15Mpa。
反应时间约为2-3小时。
三、分离操作:反应后的产物中含有大量的水、甲醇、一氧化碳、二氧化碳等气体和小量杂质,需要进行分离操作。
分离操作包括冷凝、膜分离、吸附、蒸馏等步骤。
其中,蒸馏是分离操作中最为重要的一步,该步骤可将产物中甲醇的纯度提高至99.5%以上。
四、纯化操作:纯化操作是指进一步提高甲醇产品的纯度。
该操作主要采用蒸馏和吸附等方法,将残余的水、碳氢类杂质、酸类杂质、杂质甲醇等有机物和无机物从甲醇中提取出来。
纯化后的甲醇产品可以最终得到经过瓶装、桶装、罐装等方式进行包装装载。
五、安全操作:焦炉煤气制甲醇工艺是一种高温、高压、易爆等危险的工艺,因此安全操作尤为重要。
在运行过程中,需注意以下几点:必须使用标准的安全设施和防爆设备;操作工人必须接受专业的安全知识和技能培训;应定期检查设备的安全状况和参数;生产过程中应注意气体的引爆和毒性危害等问题。
六、总结:焦炉煤气制甲醇工艺之合成操作规程涉及预处理、反应、分离、纯化、安全等多个环节,其中每个环节都需要精细严谨的操作。
生产甲醇同时也要高度重视工厂的环保问题,合理规划废气、废水等排放,缩小环境污染,实现可持续发展的目标为行业健康快速发展奠定了基础。
焦炉煤气制甲醇工艺方案

焦炉煤气制甲醇工艺方案1.原料准备:焦炉煤气和一定比例的水蒸气是制备甲醇的原料。
焦炉煤气中含有一氧化碳、二氧化碳、氢气、氮气和少量烃类。
首先,对原料焦炉煤气进行预处理,除去其中的硫化物和一些杂质。
2.原料净化:焦炉煤气经过预处理后,进一步进行净化工艺。
通过冷却、除尘和脱硫等工序,去除颗粒物、酸性气体等污染物,以保证后续反应的顺利进行。
3.变换反应:焦炉煤气中的一氧化碳和二氧化碳需要经过变换反应,将其转化为甲醇。
该反应采用催化剂进行催化。
一氧化碳与水蒸气在一定温度和压力下通过催化剂反应生成甲醇。
在反应器内,采用适当的催化剂、反应温度和压力条件,可以提高甲醇的产率和选择性。
4.分离纯化:经过变换反应后,产生的反应混合物中含有甲醇、水、未反应的一氧化碳和二氧化碳等。
需要进行分离纯化工艺,将甲醇从混合物中提取出来。
常用的分离纯化方法包括蒸馏、吸附、结晶等。
5.回收利用:在分离纯化过程中,除了得到纯度较高的甲醇产品外,还会产生一些副产物和废弃物。
这些副产物和废弃物可以通过进一步处理和回收利用,以实现资源的综合利用和环境保护。
总的来说,焦炉煤气制甲醇工艺方案是将焦炉煤气中的一氧化碳和氢气转化为甲醇的过程。
通过预处理、净化、变换反应、分离纯化和废弃物处理等工序,实现了焦炉煤气的高效利用和甲醇产品的生产。
然而,在实际生产中,还需要根据具体情况进行工艺参数的调整和优化,以提高产量和甲醇的品质。
此外,还需要关注工艺过程中的能耗和环境污染问题,不断改进工艺方案,提高产能和资源利用效率,推动绿色发展。
焦炉煤气制甲醇

从转化率高低,废热回收利用优劣, 从转化率高低,废热回收利用优劣,温度差 大小排序。 大小排序。 管壳式最好 冷管型次之 绝热型最差
从大型化设备制造难易排序 绝热型最易 冷管型次之单,设备少但能耗高。 两塔工艺 流程简单,设备少但能耗高。 三塔工艺 节能显著
六、焦炉煤气制甲醇消耗指标和技 术经济
万吨/a 焦炉煤气生产 10 万吨 甲醇主要消耗指标如下表 消耗指标 项目名称 /h 规格 单位 消耗量 /吨甲醇 吨甲醇
LH V4300kCal/N m Pa 40℃ 焦炉煤气 0.004M 99% 0.004M Pa 40℃ 99.6% O2 2.5M Pa 100℃ Pa 蒸汽:转 蒸汽 转 化 3~3.6M 甲醇合成 饱和蒸汽
四、甲醇合成
甲醇合成压力: 一般5.5~ 甲醇合成压力 : 一般 ~ 11MPa,中型厂以下选低 , 特大型选中压10~ 压5.5~6MPa,特大型选中压 ~11MPa.。 ~ 特大型选中压 。 甲醇合成温度: 甲醇合成温度:230~250℃ ~ ℃ 甲醇合成催化剂: 甲醇合成催化剂:铜系催化剂 甲醇合成反应器: 甲醇合成反应器: 1) 绝热冷激型 ICI ) 2) 管壳式等温型 ) 管壳式等温型LurgiI 3) 冷管型(埋在催化床中) ) 冷管型(埋在催化床中) 4) 轴径向型 这些反应器都成熟可靠,但在单程转化率,废热回收, 这些反应器都成熟可靠,但在单程转化率,废热回收, 反应温度最佳,控制方面有显著的差别。 反应温度最佳,控制方面有显著的差别。
二、二院设计的焦炉煤气制甲 醇已投产、 醇已投产、正施工和设计的甲 醇工厂产能约200万吨 。 万吨/a 醇工厂产能约200万吨/a。
名称 规模万 t/a 备注 8 2004 年投产 云南曲靖甲醇厂 10 2005 年投产 河北建韬焦化厂 料2006 年 6月投 10 山东海化薜城焦化厂 原 料 月投 产 10 陕西韩城黑猫焦化厂 预计 2006 年投产 20 2005 年开工建设 云南曲靖焦化工程 30 山西天脊 正在建设中 20 山西焦化 详细设计中 10 山西天浩 详细设计中 内蒙庆华煤化工集团公司 20 详细设计中 10 黑龙江七台河焦化厂 详细设计中 10 河北旭阳 详细设计中 10 河南开滦焦化厂 详细设计中 10 河北邯郸峰峰焦化厂 详细设计中 10 内蒙呼市焦化厂 详细设计中 188 总计 详细设计中 完成焦炉煤气制甲醇可研报告, 年左右。 完成焦炉煤气制甲醇可研报告,产能约 150 吨/年左右。 年左右
焦炉煤气制甲醇 ppt课件
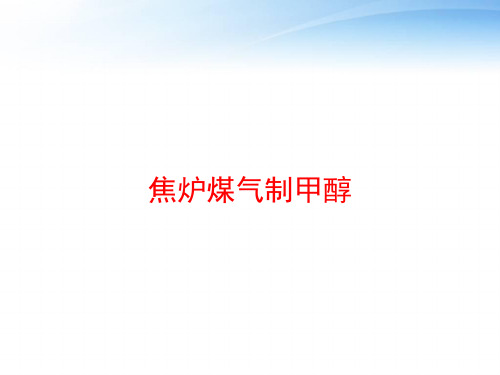
焦炉煤气制甲醇
10
第二节 焦炉气的净化
2. 有机硫低温水解+氧化铁、氧化锌脱硫
焦炉气先被引入有机硫水解槽,在有机硫水解槽中被 水解为硫化氢,再通入后序的氧化铁粗脱硫和氧化锌精脱硫 ,使硫含量满足后序工艺要求。
焦炉煤气制甲醇
19
19
三、影响甲烷转化的因素
1.温度 2. 甲烷转化反应是可逆吸热反应,提高温度对反应平衡 和反应速率有利。
3. 控制转化气出口温度的方法:控制氧气量和焦炉气的入炉温 度。
5. 转化炉加入氧气的目的:使部分焦炉气燃烧以提供转 化反应所需的热。
水解催化剂的使用条件:温度90℃,压力0.77~ 5.0MPa。由于该脱硫工艺采用低温水解脱硫,故最终的脱 硫温度较低,较易满足后序工艺对合成气温度的要求。
焦炉煤气制甲醇
11
11
第二节 焦炉气的净化
3. 铁钼+镍钼两级加氢、铁锰+氧化锌两级吸收
该工艺对传统铁(钴)钼催化加氢+氧化铁、氧化锌脱 硫二提出了一些改进。
焦炉煤气制甲醇
17
17
二、焦炉气转化工艺
2. 非催化部分氧化转化法
第一阶段: 2H2 + O2 → 2H2O
CH4 + 2O2 → CO2 + 2H2O 第二阶段: CH4 + H2O → CO + 3H2 控制步骤 优点:不需要催化剂、精脱硫可以后移,无需再加蒸汽
、转化气中CO2的含量较满足甲醇合成;
15
15
一、焦炉气转化的原理
焦炉煤气制甲醇

④ 焦炉煤气的深度净化
焦炉煤气的深度净化 ,就是精脱硫后再脱除Cl-和羰基金属。焦炉 煤气中含有的 Cl-将会导致催化剂活性大幅度下降 ,其对转化与合成催 化剂的危害更甚于硫。此外 , Cl-具有很高的迁移性 ,其造成催化剂中毒 往往是全床性的。Cl-还会严重腐蚀生产设备与管道。另外 ,焦炉煤气 中微量的羰基金属 (羰基铁、 羰基镍 )等杂质也会导致甲醇合成催化剂 中毒失活。因此焦炉煤气精脱硫后必须深度净化脱除氯和羰基金属 ,防 止其对甲醇合成催化剂的毒害。
近年来 ,随着钢铁工业对焦炭的巨大需求而高速发展起 来的炼焦产业 ,在焦炭产能无序扩张、产量大幅度增长的同 时 ,副产的大量焦炉煤气导致了焦炭产区的环境急剧恶化 , 不少单一炼焦的独立焦化企业“ 只焦不化 ” ,对大量炼焦 剩余的焦炉煤气采取点天灯方式燃烧排空 ,既严重污染环境 , 又造成资源浪费。作为贫油、 缺气的能源需求大国 ,充分、 合理利用大量点天灯外排的焦炉煤气 ,对建设资源节源型社 会 ,实现经济可持续发展具有重要意义。
焦炉煤气烷烃转化重整工艺目前主要有蒸汽转化工艺、 纯氧非催化部分氧化转化工艺、 纯氧催化部分氧化转化工 艺。 ① 蒸汽转化工艺 焦炉煤气蒸汽转化工艺类似于天然气制甲醇两段转化中的 一段炉转化机理 ,其主要反应为: CH4 +H2O=CO +3H2 反应 为吸热反应 ,提高温度 ,有利于甲烷的转化。反应中需 在反应管外燃烧燃料气间接外供热量 ,反应管需用耐高温的 镍铬不锈钢制造 ,转化炉喷嘴多 ,结构复杂 ,制造要求高 ,造 价高。
传统的钴钼加氢催化剂价格昂贵 ,主要用于以天然气 为原料的加氢转化精脱硫。在 CO、 CO2含量较高的气 体中 ,易发生析碳和甲烷化副反应。通常焦炉煤气中含有 体积分数为5% ~8%的 CO,不宜采用钴钼加氢催化剂脱硫 方案。根据焦炉煤气中有机硫的含量和形态 ,总结近几年 国内建设的几套焦炉煤气制甲醇加氢脱硫装置的经验教训 , 对焦炉煤气有机硫净化可采取铁钼 +镍钼两级加氢、 铁锰 +氧化锌两级吸收的方式。操作条件为 :温度约 350 ℃、 压力约 2. 3 MPa。
焦炉煤气制甲醇设计说明书

焦炉煤气制甲醇设计说明书本文档旨在介绍焦炉煤气制甲醇的背景和目的。
对于需要设计焦炉煤气制甲醇的项目,该说明书将提供必要的信息和指导。
焦炉煤气制甲醇是一种利用焦炉煤气作为原料生产甲醇的工艺。
焦炉煤气是炼焦过程中产生的一种混合煤气,包含一定的一氧化碳和氢气等成分,因此适合用于甲醇的合成。
通过焦炉煤气制甲醇,可以将焦炉煤气这种副产品转化为有价值的化学品甲醇。
甲醇是一种重要的化工原料,在合成材料、医药、涂料、清洁能源等领域有广泛的应用。
该设计说明书的目的是为正在设计焦炉煤气制甲醇项目的人员提供必要的指导和参考。
本文档将包括焦炉煤气制甲醇的工艺流程、设备设计要求、操作条件、安全规范等方面的内容,以确保项目的顺利进行和甲醇生产的稳定运行。
请使用本设计说明书作为设计焦炉煤气制甲醇项目的参考,并根据具体情况进行调整和优化。
任何需要修改本文档内容的更改都应遵循合适的法律法规及技术规范,并由经验丰富的专业人员进行审核和批准。
有关焦炉煤气制甲醇的具体技术和经济参数等内容,请参考相关的可靠资料和专业意见。
祝项目顺利进行!本设计说明书旨在提供焦炉煤气制甲醇项目设计时应遵循的原则和考虑因素。
以下是设计原则的要点:安全性:设计应始终以安全性为首要考虑因素。
确保设计方案符合相关安全标准,预防和减少事故风险。
环境友好性:设计应符合环境保护要求,减少对环境的负面影响。
优选低排放和清洁能源技术,降低甲醇生产过程中的污染物排放。
能源效率:设计应追求能源效率,最大程度地利用可再生能源和能源回收技术。
优化工艺流程,减少能源浪费,提高甲醇生产效益。
可持续性:设计应注重项目的长期可持续性。
考虑材料和设备的可持续供应,合理规划和管理资源,确保项目的可持续发展。
经济性:设计应在满足安全和环境要求的前提下,最大限度减少投资和运营成本。
优化工艺设计,提高生产效率,降低生产成本。
可操作性和维护性:设计应考虑到设备的操作和维护要求,使甲醇生产过程简化和可靠。
20万吨焦炉气制甲醇操作规程
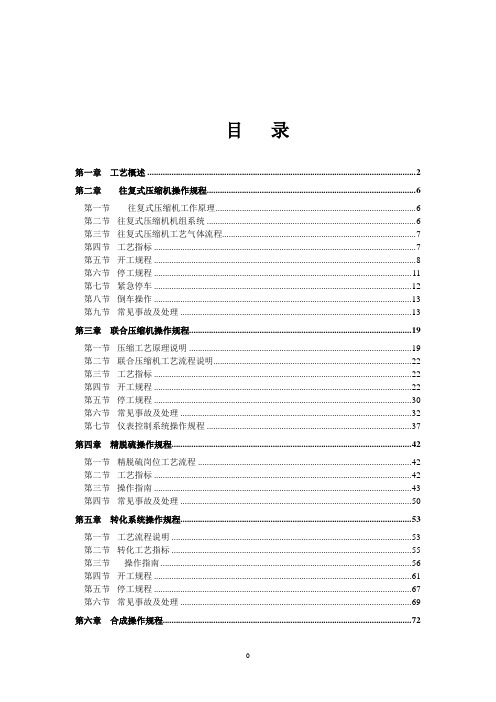
第六节
一、停车步骤
1)、接到调度停车通知后,注意检查各级压力,并做好停车准备工作,准备从高压端到低压端的顺序切气;
2)、减量:通知转化岗位准备减量,开一回一减量,当全开还需减量时,可开四回一进行大减量,减量的多少,应根据转化系统平稳状况,减到转化所需的压力时准备切气;
温度(供水/回水)
32/42℃
污垢系数
0.00034m2K/w
碳钢年腐蚀速度
<0.125mm/a
Cl-1
<100mg/L
SS
≤20 mg/L
PH值
6.5~9.5
浓缩倍数
K=3
4、生活用水和消防水
压力
0.5MPa(A)
温度
环境温度
5、精制脱盐水
压力
0.5MPa(A)
温度
≤40℃
电导率(25℃)
≤0.2us/cm
设计操作时间:8000小时/年
其工艺路线为:
1、脱油、粗脱硫、加氢串氧化锌干法脱硫
2、催化氧化
3、合成气及循环气联合压缩
4、低压法合成甲醇
5、粗甲醇3塔精馏
6、汽提法处理工艺冷凝液
二、主要工艺特点
1、采用2.3MPa(G)催化氧化制取甲醇合成气;
2、采用低压甲醇合成工艺以及副产中压蒸汽的管壳式等温甲醇合成塔,其能耗低,产品质量好,运行可靠,投资省;
7)、建立电机用油系统:由电工加入分析合格的润滑油进电机滑油系统,并保持油位2/3以上,最后检查是否有泄漏等情况,并处理至合格。
8)、建立注油系统:加入分析合格的润滑油进注油箱,保持油位1/2以上,然后用手盘动手柄数圈,无问题后开启注油器建立注油系统,并检查注油情况,如有泄漏、堵塞等现象,则停止注油,待处理合格后重新建立注油系统。
焦炉煤气制甲醇工艺的概述

焦炉煤气制甲醇工艺的概述摘要:本文介绍了利用焦炉副产品——焦炉煤气生产15万吨/年甲醇工艺及特点,并对此工艺进行了评价,提出了建议。
关键词:焦炉煤气;纯氧催化;制甲醇在未投建焦炉煤气制甲醇之前河北华丰能源科技发展有限公司焦炭的年综合生产能力已达到336万吨,此外还有3MW、6MW、2×15MW中温中压发电机组、30MW高温高压发电机组发电厂各一座。
为了抓住市场机遇,增加经济效益,充分利用丰富的焦炉煤气,河北华丰煤化电力有限公司总投资38475万元实施年产15万吨焦炉气制甲醇工程项目,以焦炉煤气为原料生产甲醇。
作一概述:1、生产规模和工艺路线本工程是利用每小时产35000标立米的焦炉煤气生产甲醇设计的,按年作业时间8000小时算,可年产甲醇15万吨,产品的质量指标达到GB338---92标准。
我公司生产的焦炉气甲烷含量达24%~28%,根据煤气组成采用纯氧催化部分转化工艺将甲烷及少量多碳烃转化为合成甲醇的有用成分一CO和H,以满足生产甲醇的基本要求。
工艺流程示意图2、工艺流程概述2.1预处理工序从焦化装置送来的焦炉气中还含有部分焦油、萘、粉尘等易凝或易结晶的物质,在常温常压下,这些物质也许不会凝结或结晶,但经加压后,由于其分压上升,造成其中部分物质凝结为液滴或固体颗粒,这些物质如不除去,将对后工序造成危害。
本工艺采用对焦炉气中焦油和萘具有极强吸附能力的焦炭颗粒做吸附剂,吸附焦油和萘后的焦炭颗粒进行相关处理。
该工艺的特点是:吸附剂廉价易得、吸附选择性好、吸附容量大、对焦油和萘的脱除率高(脱油率≥90%,脱萘率≥80%)且吸附条件温和(常温常压下即可实现)。
2.2气柜工序焦炉气的产生量是波动的,而甲醇装置的生产用气要求相对稳定,因此,在焦炉气供应系统设计中必须采取有效的稳压措施。
本装置采用外导架直升式湿式气柜,对原料焦炉气起着稳定供气的缓冲作用,可以有效地协调气源与后续工序用气之间的动态平衡。
焦炉煤气制甲醇的流程与注意事项
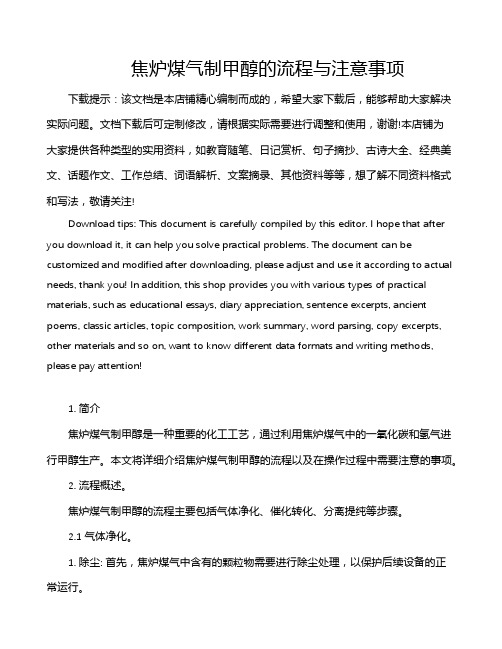
焦炉煤气制甲醇的流程与注意事项下载提示:该文档是本店铺精心编制而成的,希望大家下载后,能够帮助大家解决实际问题。
文档下载后可定制修改,请根据实际需要进行调整和使用,谢谢!本店铺为大家提供各种类型的实用资料,如教育随笔、日记赏析、句子摘抄、古诗大全、经典美文、话题作文、工作总结、词语解析、文案摘录、其他资料等等,想了解不同资料格式和写法,敬请关注!Download tips: This document is carefully compiled by this editor. I hope that after you download it, it can help you solve practical problems. The document can be customized and modified after downloading, please adjust and use it according to actual needs, thank you! In addition, this shop provides you with various types of practical materials, such as educational essays, diary appreciation, sentence excerpts, ancient poems, classic articles, topic composition, work summary, word parsing, copy excerpts, other materials and so on, want to know different data formats and writing methods, please pay attention!1. 简介焦炉煤气制甲醇是一种重要的化工工艺,通过利用焦炉煤气中的一氧化碳和氢气进行甲醇生产。
焦炉煤气制甲醇和制天然气对比分析
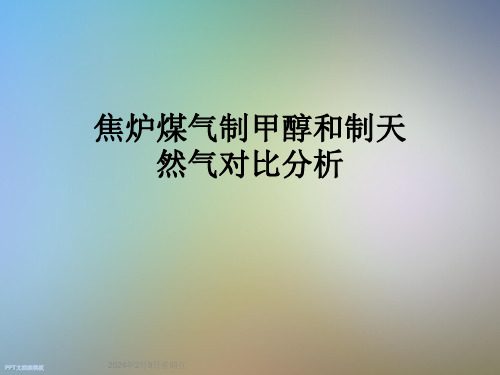
31.0926.77焦炉煤气制甲醇 28518 24000 190 160
甲醇 10 万吨/年
弛放气 2100 万m3/年
2100 21218 18555 1551 1164 11.07 7.51 8.26 73.43
2300 23189 18437 3326 2495 18.04 13.32 6.18 55.62
•故焦炉气制甲醇的 •能量利用率 •为51.1%~ •58.2%。
2024/2/9
•9
•两种产品经济性对比
•以25000 m3/h 焦炉气为基准
项目 项目总投资/万元
固定资产总投资/万元
占地面积/亩 定员/人
产品
产品价格 年均销售收入/万元 年均总成本费用/万元 年均利润总额/万元 年均税后利润/万元 财务税前收益率%
焦炉煤气制甲醇和制天 然气对比分析
2024年2月9日星期五
•国内焦炭及焦炉煤气利用情况
•2009年国内焦炭总量为:35364万吨,其中:钢铁联合焦化企业:13405万吨,独立 •焦化企业:21959万吨。
•按每吨焦炭副产430Nm3焦炉煤气计算,独立焦化企业每年副产焦炉煤气约940亿Nm3, •除企业自身作加热燃料和化工原料(制甲醇)外,每年有约220亿Nm3焦炉煤气需考虑 •出路问题。
因此,用焦炉气生产CNG/LNG,将产生较明显的经 济效益、环境效益与社会效益,对促进焦化与能 源行业的技术进步与产业发展具有重要的意义。
2024/2/9
•3
•两种产品工艺流程对比 •焦炉气制甲醇工艺流程
•空气
•空分
•焦炉煤气 •深度净化 •催化转化
•废热回收 •精脱硫
•蒸汽
•弛放气
•合成甲醇 •压缩
焦炉煤气制甲醇工艺改进与创新

焦炉煤气制甲醇的改进与创新我国的焦化行业,尤其是独立焦化企业剩余的焦炉煤气出路是个行业性的问题。
如果不能很好的解决这个问题,不仅造成企业的经济效益低下,更重要是的造成能源的极大浪费,并带来严重的环境污染,这与目前国家倡导的节能减排,清洁生产均不相符。
就如何合理利用剩余焦炉煤问题,近几年我国广大科技工作者进行深入研究和大胆尝试,焦炉煤气制甲醇就是解决这一问题的有效途径之一。
下面就10万吨/年甲醇装置的基本情况,运行实践和主要改进作一简要介绍。
一、生产工艺介绍。
利用焦炉煤气用纯氧部分氧化催化转化法制合成气生产甲醇装置,设计能力10万吨/年。
1、工艺流程。
图1.焦炉煤气制甲醇工艺流程框图2、各道工序的基本功能及组成变化(设计目标值)。
焦炉煤气部分氧化催化转化制甲醇根据各道工序的基本功能可分为以下五部分:一是空分功能,主要为转化提供合格的氧气以及生产过程所需要的氮气;二是脱硫净化功能,主要是为转化提供符合生产要求的原料煤气,同时满足合成气对硫、氯的净化要求;三是转化功能,主要是把煤气中的烃类物质经催化在水蒸汽的作用下转化为CO、CO2、H2满足合成需要的合成气;四是合成功能,主要是在合成催化剂的作用下将合成气合成甲醇;五是精馏功能,主要是将合成回收的粗醇加工成符合产品标准的甲醇和杂醇。
各工序工艺介质设计目标值见表1。
表1 各工序工艺介质设计目标值二、生产装置的选择。
1、空分装置。
为满足10万吨/年甲醇生产所需要的氧气、氮气,选用了KDON-6000/3000型空分装置一套。
主要参数如下:氧气6000Nm3/h,纯度99.6%;氮气3000 Nm3/h,纯度99.99%。
本装置采用目前较为先进的分子筛纯化增压流程,空气经袋式除尘后,由空压机增压至0.6MPa通过空冷塔冷却至16℃左右,进入分子筛纯化器,脱去空气中的水、二氧化碳、有机杂质等,然后分两路进入分馏塔,一路是大部分空气进入分馏塔中的主换热器,被返流气冷却至-172℃(其中小部分液空)进入下塔底部;另一路空气经增压机将压力增至0.8~0.9 MPa,经冷却后进入主换热器被冷至-108℃左右,再从主换热器中部抽出去透平膨胀机膨胀至0.14 MPa左右,以-165℃进入上塔进行精馏,获得产品氧气和氮气,部分污氮用作分子筛再生,出塔的氧气、氮气经氧压机、氮压机增压后送生产装置使用。
焦炉煤气制甲醇转化工艺研究

焦炉煤气制甲醇转化工艺研究摘要:焦炉煤气属于正常炼焦中的副产品,产量大且具备一定的回收再利用价值。
利用焦炉煤气生产制造甲醇,是较为有效的再利用措施,该技术的重难点在于净化脱硫与烷烃转化。
为了更好地推广这一技术,笔者总结自身工作经验,就这两个重难点进行了深入浅出的分析,就其工艺要求及技术方案进行了探讨,观点仅供参考关键词:焦炉煤气甲醇脱硫催化转化焦炉煤气属于炼焦副产品,主要组成成分为甲烷和氢气,可以充当燃料,但从其成分上分析,甲烷和氢气的原子组成正好满足甲醇的原子组成要求,如果能通过一定的化学手段将其焦炉煤气转化为甲醇,无疑能够为我们带来更高的经济效益。
本文首先从工艺上分析了该技术的可行性,并针对其中的重难点进行了详细分析,最后对该技术的前景进行了分析一、焦炉煤气制甲醇转化工艺分析1可行性分析以焦炉煤气制甲烷,是有效提升焦炉煤气经济效益的措施之一,最早由我国研发成功并推广开来。
其制备工艺主要经过了净化、气体组分转化、氢碳比调节、合成、精馏等步骤,如下所示首先,对预处理后的焦炉煤气进行净化,送入储气罐稳压、增压,加入一定量的氢气,以降低有机硫的含量,并降低后续反应中甲烷化的几率。
随后,将焦炉煤气中的各种碳氢化合物转化为氢气与一氧化碳,并补充一定量的碳多氢少的水煤气,使最终产物中的碳、氢、氧含量符合甲醇制备所需的原子比,这就是气体组分转化与碳氢比调节。
其中水煤气主要通过煤炭制备的。
接下来,对合成气进行压缩增压,并输送至合成塔进行粗合成最后,对上述粗合成的甲醇进行精馏,即准备得到了所需的精甲醇从上述步骤来开,只要能够对焦炉煤气进行有效的脱硫,并保证烷烃转化正常进行,即可使焦炉煤气转化为甲醇,可见,其具备一定的可行性,现就其中两个重难点,即脱硫与烷烃转化进行一定的分析。
下图所示,为焦炉煤气制甲醇流程图图1 焦炉煤气制甲醇流程图2焦炉煤气的脱硫、净化分析焦炉煤气组分较杂,含有大量的杂质,不适合直接参与甲醇转化,尤其是含硫化合物,会直接影响后续烷烃转化催化剂的活性,而最终使得无法生成甲醇,因此,必须要对原料煤气进行有效的净化与脱硫。
焦炉煤气制甲醇的原理
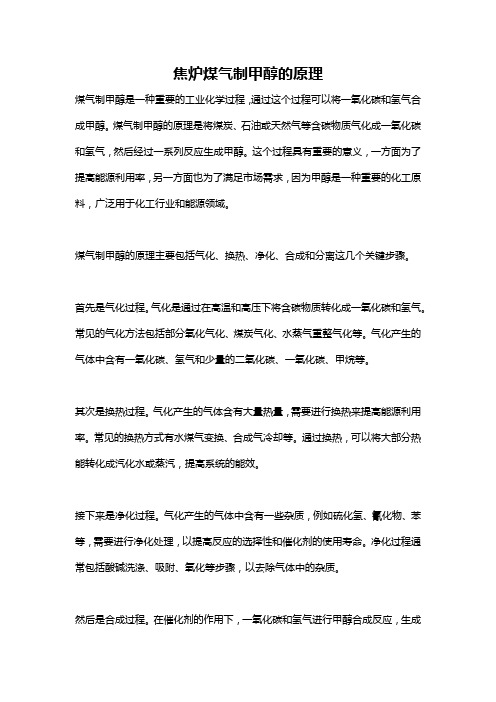
焦炉煤气制甲醇的原理煤气制甲醇是一种重要的工业化学过程,通过这个过程可以将一氧化碳和氢气合成甲醇。
煤气制甲醇的原理是将煤炭、石油或天然气等含碳物质气化成一氧化碳和氢气,然后经过一系列反应生成甲醇。
这个过程具有重要的意义,一方面为了提高能源利用率,另一方面也为了满足市场需求,因为甲醇是一种重要的化工原料,广泛用于化工行业和能源领域。
煤气制甲醇的原理主要包括气化、换热、净化、合成和分离这几个关键步骤。
首先是气化过程。
气化是通过在高温和高压下将含碳物质转化成一氧化碳和氢气。
常见的气化方法包括部分氧化气化、煤炭气化、水蒸气重整气化等。
气化产生的气体中含有一氧化碳、氢气和少量的二氧化碳、一氧化碳、甲烷等。
其次是换热过程。
气化产生的气体含有大量热量,需要进行换热来提高能源利用率。
常见的换热方式有水煤气变换、合成气冷却等。
通过换热,可以将大部分热能转化成汽化水或蒸汽,提高系统的能效。
接下来是净化过程。
气化产生的气体中含有一些杂质,例如硫化氢、氰化物、苯等,需要进行净化处理,以提高反应的选择性和催化剂的使用寿命。
净化过程通常包括酸碱洗涤、吸附、氧化等步骤,以去除气体中的杂质。
然后是合成过程。
在催化剂的作用下,一氧化碳和氢气进行甲醇合成反应,生成甲醇。
甲醇的合成反应通常在高压和高温下进行,常见的催化剂有铜锌或铜铝复合催化剂,也可以使用高压合成氨法的氮碘化铁作为催化剂。
最后是分离过程。
合成产物中还含有一些未反应的气体和液体,需要进行分离提取。
分离过程通常包括蒸馏、吸附、结晶等步骤,以分离出纯度较高的甲醇产品。
总体来说,煤气制甲醇的原理是通过气化、换热、净化、合成和分离这几个关键步骤,将含碳物质转化成甲醇。
这个过程需要合理设计反应条件,选择适当的催化剂和分离工艺,以提高甲醇的产率和纯度。
除了化学反应过程,还需要考虑能源利用、环境保护、安全生产等方面的问题。
煤气制甲醇的原理在工业化生产中得到了广泛应用,尤其是在能源匮乏的地区。
甲醇合成三种工艺的成本比较
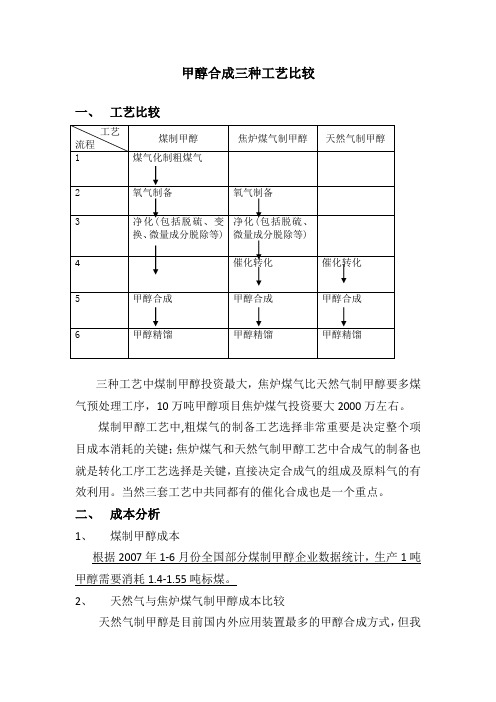
甲醇合成三种工艺比较一、工艺比较三种工艺中煤制甲醇投资最大,焦炉煤气比天然气制甲醇要多煤气预处理工序,10万吨甲醇项目焦炉煤气投资要大2000万左右。
煤制甲醇工艺中,粗煤气的制备工艺选择非常重要是决定整个项目成本消耗的关键;焦炉煤气和天然气制甲醇工艺中合成气的制备也就是转化工序工艺选择是关键,直接决定合成气的组成及原料气的有效利用。
当然三套工艺中共同都有的催化合成也是一个重点。
二、成本分析1、煤制甲醇成本根据2007年1-6月份全国部分煤制甲醇企业数据统计,生产1吨甲醇需要消耗1.4-1.55吨标煤。
2、天然气与焦炉煤气制甲醇成本比较天然气制甲醇是目前国内外应用装置最多的甲醇合成方式,但我国考虑到能源的有效利用,国家发改委于2007年8月30日正式颁布实施《天然气利用政策》,该政策明确规定,禁止以天然气为原料生产甲醇,要确保国家批准建设的化肥项目用气的长期稳定供应。
而推广焦炉煤气制甲醇项目,可以有效利用现有资源节能减排。
但焦炉煤气制甲醇要与现有的天然气制甲醇企业竞争,还要清楚各自的成本消耗情况。
(附:天然气及焦炉煤气制甲醇消耗定额及单位成本表)从成本表中可以看出,焦炉煤气和天然气制甲醇的主要成本均为原料气的消耗。
因此,在天然气价格为1.2元时,天然气与焦炉煤气制甲醇成本相当,如果天然气价格提高,焦炉煤气制甲醇不仅在政策、环保上,而且在成本上也会有相当的优势。
三、原料成分的影响理想的甲醇合成气组成为:合成气中(H2-CO2)/(CO+CO2)=2.05~2.1,CO2含量3~5%,惰性气体含量应尽量低。
表二:三种工艺原料气组成比较煤的影响:煤的热值直接影响到甲醇生产的消耗,全国大多数煤制甲醇企业吨甲醇消耗1.45吨标准煤。
根据宜宾提供的数据单耗煤2.7吨,哈气化有两套共14万吨Lurgi炉固定层煤制甲醇装置,由于煤灰分过高,单耗煤在3.4吨煤。
焦炉气制甲醇工艺流程

焦炉气制甲醇工艺流程焦炉气制甲醇工艺是一种利用焦炉煤气来制造甲醇的工艺。
甲醇是一种重要的化学原料,广泛应用于合成化学品、塑料、染料、涂料等领域。
本文将介绍焦炉气制甲醇的工艺流程。
焦炉煤气是焦炉生产焦炭时产生的一种副产品。
焦炭的主要成分是炭,但焦炉煤气中还含有一定的甲烷、氢气、氮气、一氧化碳等物质。
焦炉气制甲醇的工艺利用焦炉煤气中的甲烷和一氧化碳作为原料,通过一系列的反应和分离步骤最终制得甲醇。
首先,焦炉煤气经过除尘处理,去除其中的灰尘和颗粒物。
然后进入加热炉,在高温下进行加热,使其温度逐渐升高。
接下来,焦炉煤气经过预热、空气混合等步骤后进入主炉。
在主炉中,甲烷和一氧化碳发生催化反应,生成甲醇。
这个反应需要高温和压力作为条件,因此需要在主炉中提供适宜的反应条件。
在主炉中,焦炉煤气进入催化剂层,与催化剂接触后发生化学反应。
甲烷和一氧化碳在催化剂的作用下发生部分氧化反应生成甲醇。
同时,甲烷和一氧化碳也会发生副反应,产生一些副产物。
催化剂的选择和使用也是影响工艺效率的关键因素之一。
甲醇生成后,焦炉煤气中的其他组分如氢气、氮气等会通过分离步骤进行分离和回收利用。
这些物质对于后续的工艺步骤来说并不是主要原料,但它们可以被转化为其他有用的化学品。
最后,焦炉气制甲醇工艺也需要一个合适的能源供应系统,确保反应过程中的能量平衡和稳定供应。
这个系统包括锅炉、换热器、循环泵等设备。
总之,焦炉气制甲醇是一种利用焦炉煤气制造甲醇的工艺。
它可以将焦炉煤气中的甲烷和一氧化碳转化为甲醇,并且将其他组分进行分离和回收利用。
这个工艺在化工行业中有着广泛的应用前景,为能源的有效利用和环境保护做出了贡献。
- 1、下载文档前请自行甄别文档内容的完整性,平台不提供额外的编辑、内容补充、找答案等附加服务。
- 2、"仅部分预览"的文档,不可在线预览部分如存在完整性等问题,可反馈申请退款(可完整预览的文档不适用该条件!)。
- 3、如文档侵犯您的权益,请联系客服反馈,我们会尽快为您处理(人工客服工作时间:9:00-18:30)。
23
23
一、甲醇的合成
1. 合成甲醇的原理
CO + 3H2 → CH3OH CO2 + 3H2 → CO + H2O 2. 合成甲醇的工艺 甲醇合成工艺分为:高压、中压和低压法。 △H298=-90.8kJ/mol △H298=41.3kJ/mol CO2 + 3H2 → CH3OH + H2O △H298=-49.5kJ/mol
合成气冷却
弛放气
焦炉煤气
压缩
干法脱硫
煤气加热炉
甲醇精馏
煤气
甲醇
图12-1 焦炉气制甲醇工艺流程
7
7
第二节
焦炉气的净化
制甲醇用焦炉气的要求:总硫体积分数不大于 0.1ppm,烯烃、长链烷烃含量不能太高。 因此,精脱硫工序是焦炉煤气净化工艺中最重 要的一环。
8
8
第二节
焦炉气的净化
1. 铁(钴)钼催化加氢+氧化铁、氧化锌脱硫
赵云鹏
zhaoyp@
中国矿业大学化工学院
1
1
第十二章
第一节 第二节 第三节 第四节
焦炉煤气制甲醇
焦炉煤气制甲醇的原理 焦炉气的净化 焦炉气转化 甲醇的合成和精馏
2
2
第一节 焦炉煤气制甲醇的原理
CH4 + H2O → CO + 3H2 合成气制甲醇的反应:CO + 2H2 → CH3OH 甲醇合成气的要求主要包括以下三个方面:
合成气中的杂质:使催化剂失活得有毒物质 和惰性物质。
导致催化剂失活的有毒物质:硫化物、羰基
金属和Cl-。 总硫体积分数不大于0.1ppm,甲烷含量不大 于0.6%。
6
6
第一节 焦炉煤气制甲醇的原理
空气
O2 空气 N2 9.8MPa蒸汽 蒸汽 湿法脱硫 烟道气放空 甲醇合成 合成气压缩 转化
废热回收
度。
转化炉加入氧气的目的:使部分焦炉气燃烧以提供转化 反应所需的热。
19
19
三、影响甲烷转化的因素
2. 压力
降低反应压力有利于提高平衡转化率。
实际生产采用加压操作原因:使后序工段节
省压缩功、减少设备尺寸和催化剂用量。 平衡加压带来的不利影响措施:增大水碳比 和提高反应温度。
20
20
三、影响甲烷转化的因素
大; (4)催化剂中毒; (5)原料气中烃类碳原子数多,裂解析碳反应容易发 生。 15
15
二、焦炉气转化工艺
1. 纯氧催化部分氧化转化法
焦炉气纯氧催化部分转化是将焦炉气中的烃类进行部
分氧化和蒸汽转化反应,在转化炉中首先发生H2、CH4与 部分氧气燃烧反应,然后气体进入催化剂层进行烷烃与蒸 汽的转化反应。 第一阶段: 2H2 + O2 → 2H2O CH4 + 2O2 → CO2 + 2H2O 第二阶段: CH4 + H2O → CO + 3H2 CH4 + CO2 → 2CO + 2H2 16
焦炉气先被引入有机硫水解槽,在有机硫水解槽中被 水解为硫化氢,再通入后序的氧化铁粗脱硫和氧化锌精脱硫
,使硫含量满足后序工艺要求。
水解催化剂的使用条件:温度90℃,压力0.77~5.0MP
a。由于该脱硫工艺采用低温水解脱硫,故最终的脱硫温度
较低,较易满足后序工艺对合成气温度的要求。
10
10
第二节
焦炉气的净化
16
二、焦炉气转化工艺
2. 非催化部分氧化转化法
第一阶段: 2H2 + O2 → 2H2O
CH4 + 2O2 → CO2 + 2H2O
第二阶段: CH4 + H2O → CO + 3H2 控制步骤
优点:不需要催化剂、精脱硫可以后移,无需再加蒸汽 、转化气中CO2的含量较满足甲醇合成; 缺点:转化温度高(>1200℃)、合成气碳不足、单位 甲醇消耗原料气比纯氧催化转化工艺多30%、纯氧消耗高。 17
转化过程中可能会发生副反应,主要是析碳反 应: CH4 → C + 2H2 2CO → CO2 + C CO + H2 → C+ H2O
14
14
一、焦炉气转化的原理
发生析碳反应的原因: (1)水碳比过低,一般要求水碳比大于2.5; (2)水蒸气与原料气的混合不均匀;
(3)转化反应温度高,使得烃类裂解析碳的可能性增
3. 水碳比
水碳比:加入水蒸气的分子数与焦炉气中碳的原子数的 比值。 提高水碳比有利于转化反应进行,可以降低转化气中 残余甲烷的含量。 增大水碳比的好处:(1)转化率一定时,降低反应温 度和压力;(2)防止析碳现象。 水碳比过高的坏处:增大系统阻力,增加能耗。 实际生产中,水碳比不低于2.5,一般控制在3.8左右。 21
工艺。
25
25
一、甲醇的合成
过热器 压缩机 合成器 冷凝冷却器 重沸器
分离器
低沸物塔 Lurgi低压合成甲醇工艺流程 26
26
一、甲醇的合成
3. 合成甲醇的影响因素
(1)反应压力
增大压力有利于加快反应速率和提高平衡转
化率,一般采用5-10MPa。 (2)反应温度 开始采用较低温度,过一定时间后再升至适 宜温度。一般反应温度控制在220-270℃。
3. 铁钼+镍钼两级加氢、铁锰+氧化锌两级吸收
该工艺对传统铁(钴)钼催化加氢+氧化铁、氧化锌脱 硫二提出了一些改进。
操作条件:温度350℃,压力2.3MPa。
工艺流程:铁钼加氢转化→铁锰粗脱硫→镍钼加氢转
化→氧化锌精脱硫。
11
11
第三节
焦炉气的转化
一、焦炉气转化的原理
二、焦炉气转化工艺 三、影响甲烷转化的因素
17
二、焦炉气转化工艺
3. 蒸汽转化法 主要反应: CH4 + H2O → CO + 3H2 转化炉在高温下操作,对设备要求高,尤其是 喷嘴,结构复杂,材料要求高。 甲烷催化部分氧化采用一段转化炉。
18
18
三、影响甲烷转化的因素
1.温度
甲烷转化反应是可逆吸热反应,提高温度对反应平衡和 反应速率有利。 控制转化气质量措施:转化炉出口温度在960℃左右。 控制出口温度的方法:控制氧气量和焦炉气的入炉温
代表塔型:ICI冷激式绝热反应器、Lurgi管壳
式低压反应器、华东理工的管壳外冷-绝热复合式固
定床反应器、林达JW均温反应器。
29
29
一、甲醇的合成
合成气入口 催化剂 装入口
喷嘴
催化剂 卸出口
气体出口 冷管式反应器 30
30
冷激式反应器
一、甲醇的合成
Lurgi合成塔
31
31
一、甲醇的合成
32
32
(1)合理的氢碳比例;
(2)合理的二氧化碳和一氧化碳比例;
(3)合成气中中杂质的要求。
3
3
第一节 焦炉煤气制甲醇的原理
(1)合理的氢碳比例 合成气中CO和CO2都存在时,应满足f=(H2-CO2 )/(CO+CO2)=2.05~2.15。 氢过量的原因? 减少羰基碳和高级醇的生成 延长催化剂寿命
4
4
第一节 焦炉煤气制甲醇的原理
(2)合理的二氧化碳和一氧化碳比例
合成气中适量CO2存在的必要性? 使催化剂呈现高活性; 使催化剂床层温度易于控制; 合成气中CO2最佳含量,应根据催化剂与操 作温度而定。 CO2 + 3H2 → CH3OH + H2O
5
5
第一节 焦炉煤气制甲醇的原理
(3)合成气中杂质的要求
12
12
一、焦炉气转化的原理
焦炉气转化的原理:在高温的转化炉内,使得 以甲烷为主的烃类在催化剂作用下,与水蒸气发生 转化反应生成CO2、CO、H2,主要反应为:
CH4 + H2O → CO + 3H2
CO + H2O → CO2+ H2 CH4 + CO2 → 2CO + 2H2
13
13
一、焦炉气转化的原理
24
24
一、甲醇的合成
高压法特点:压力25~30MPa,温度360 ~4
00℃。催化剂活性低、设备要求高、动力消耗大、
产品质量低、成本高。
低压法特点:高活性铜锌催化剂,压力5~10 MPa,温度220 ~280℃。甲醇收率高、选择性高 、能耗低、设备简单。 典型低压甲醇合成工艺:ICI和Lurgi低压合成
27
27
一、甲醇的合成
(3)合成气的组成
CO含量过高:温度不宜控制、羰基碳在催化剂
上集聚。
H2/CO一般为(5-10):1, CO2体积分数为5 %。 (4)空速 空速一般控制在10000-30000 h-1。
28
28
一、甲醇的合成
4. 甲醇合成反应器
按反应器中反应热的移出方式分为直接冷却的
冷激式和间接冷却的管壳式。
一、甲醇的合成
林达JW均温反应器
33
33
二、甲醇的精馏
目前粗甲醇主要有双塔精馏工艺和三塔精馏工 艺。
34
34
二、甲醇的精馏
回 预 流 精 槽 馏 塔
主 精 馏 塔
液封
双塔精馏工艺
35
35
二、甲醇的精馏
粗甲醇贮槽
36
3621三、影源自甲烷转化的因素4. 空速空速是由设备生产能力决定,选择合适空速
,保证转化反应完全的同时使生产能力最大化。
5. 催化剂 甲烷转化反应采用的催化剂是镍催化剂,由 活性组分NiO、承载活性组分的耐热载体和少量 的助催化剂组成。
22