7 丁腈橡胶和氢化丁腈橡胶_二_
氢化丁腈橡胶与丁腈橡胶的区别
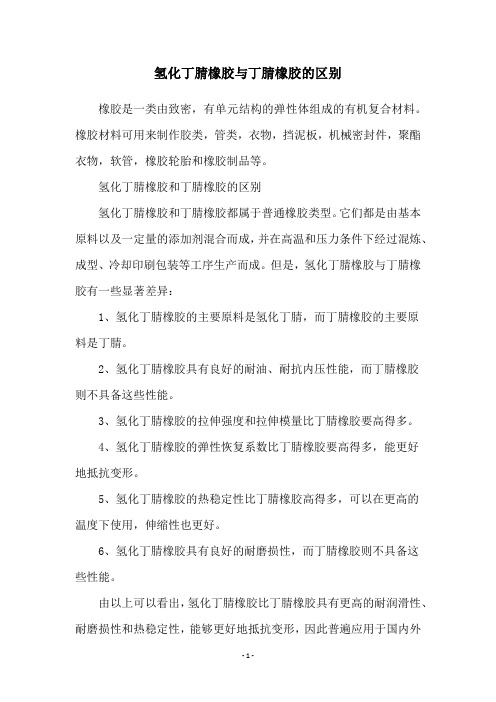
氢化丁腈橡胶与丁腈橡胶的区别橡胶是一类由致密,有单元结构的弹性体组成的有机复合材料。
橡胶材料可用来制作胶类,管类,衣物,挡泥板,机械密封件,聚酯衣物,软管,橡胶轮胎和橡胶制品等。
氢化丁腈橡胶和丁腈橡胶的区别氢化丁腈橡胶和丁腈橡胶都属于普通橡胶类型。
它们都是由基本原料以及一定量的添加剂混合而成,并在高温和压力条件下经过混炼、成型、冷却印刷包装等工序生产而成。
但是,氢化丁腈橡胶与丁腈橡胶有一些显著差异:1、氢化丁腈橡胶的主要原料是氢化丁腈,而丁腈橡胶的主要原料是丁腈。
2、氢化丁腈橡胶具有良好的耐油、耐抗内压性能,而丁腈橡胶则不具备这些性能。
3、氢化丁腈橡胶的拉伸强度和拉伸模量比丁腈橡胶要高得多。
4、氢化丁腈橡胶的弹性恢复系数比丁腈橡胶要高得多,能更好地抵抗变形。
5、氢化丁腈橡胶的热稳定性比丁腈橡胶高得多,可以在更高的温度下使用,伸缩性也更好。
6、氢化丁腈橡胶具有良好的耐磨损性,而丁腈橡胶则不具备这些性能。
由以上可以看出,氢化丁腈橡胶比丁腈橡胶具有更高的耐润滑性、耐磨损性和热稳定性,能够更好地抵抗变形,因此普遍应用于国内外很多行业。
氢化丁腈橡胶的应用氢化丁腈橡胶具有良好的耐油、耐高温、耐腐蚀、耐老化等特点,因此在工业和冶金行业中有广泛的应用。
由氢化丁腈橡胶制造的产品包括汽车制动器件、车桥销、轮胎和其它润滑工件等。
此外,氢化丁腈橡胶还可用于生产聚苯乙烯、热塑性橡胶、行走和发动机轴承、管道密封件等。
丁腈橡胶的应用丁腈橡胶具有良好的抗冲击性、热稳定性、耐腐蚀性和耐老化性,因此普遍用于汽车行业,如汽车发动机、变速器、轮胎、制动器等。
此外,丁腈橡胶还可用于制造阀体、轴承、绝缘套等。
综上所述,氢化丁腈橡胶与丁腈橡胶有着诸多不同之处,从而应用于不同行业和制造不同产品。
它们是橡胶行业中不可或缺的重要组成部分,为行业的发展和使用提供了有力的支持。
丁腈橡胶概述

丁腈橡胶概述丁腈橡胶(Nitrile Butadiene Rubber,NBR)是由丁二烯(CH2═CH—CH═CH2)和丙烯腈(CH2═CH—CN)通过乳液共聚而成的一种合成橡胶。
丁腈橡胶于1930年首先由德国进行研究,在1931年制成丁二烯与丙烯腈的共聚物,发现其具有优异的耐油、耐老化及耐磨等性能。
1937年由德国法本公司投入工业化生产,以商品名BunaN问世。
1941年,美国也开始大规模生产。
此后不久,一些国家也相继开始生产丁腈橡胶,现在世界上已有很多国家能够生产各种牌号的丁腈橡胶。
1.丁腈橡胶的分类根据丙烯腈含量不同有如下品种:2.丁腈橡胶的结构、性能与应用(1)丁腈橡胶的结构与性能丁腈橡胶的化学结构式如下:丁腈橡胶聚合物中,丁二烯的结合方式不同,性能也会不同。
当丁二烯顺式-1,4加成时有利于提高弹性,降低玻璃化转变温度;当丁二烯反式-1,4加成时拉伸强度提高,热塑性好,弹性降低;当丁二烯1,2加成时支化度和交联度提高,凝胶含量高,加工性不好,低温性能变差,力学性能和弹性降低。
丁腈橡胶中丙烯腈的含量是影响丁腈橡胶性能的重要指标,其含量一般在15%~50%范围内,目前丙烯腈含量有42%~46%、36%~41%、31%~35%、25%~30%、18%~24%五种。
丙烯腈含量越多,大分子极性越大,内聚能密度提高,加工性能变好,硫化速度加快,耐热性、耐磨性、气密性提高,但弹性降低,耐寒性能下降。
它可以在120℃的空气中或在150℃的油中长期使用。
此外,它还具有良好的耐水性、气密性及优良的黏结性能。
丁腈橡胶聚合物的平均分子量在70万左右,分子量大时,分子间作用力增大,大分子链不易移动,拉伸强度和弹性提高,可塑性降低,加工性变差;分子量分布较宽时,分子间作用力相对较弱,分子易于移动,改进了可塑性和加工性。
分子量分布过宽时,影响硫化交联,拉伸强度和弹性等力学性能受到损害。
丁腈橡胶属于非结晶性的极性不饱和橡胶,由于分子结构中含有腈基,因而具有较高的对油如矿物油、动植物油、液体燃料和溶剂的稳定性,丁腈橡胶的耐油性(尤其是烷烃油)优于天然橡胶、丁苯橡胶和氯丁橡胶,仅次于聚硫橡胶、氟橡胶、丙烯酸酯橡胶。
丁腈橡胶和氢化丁腈橡胶_一_
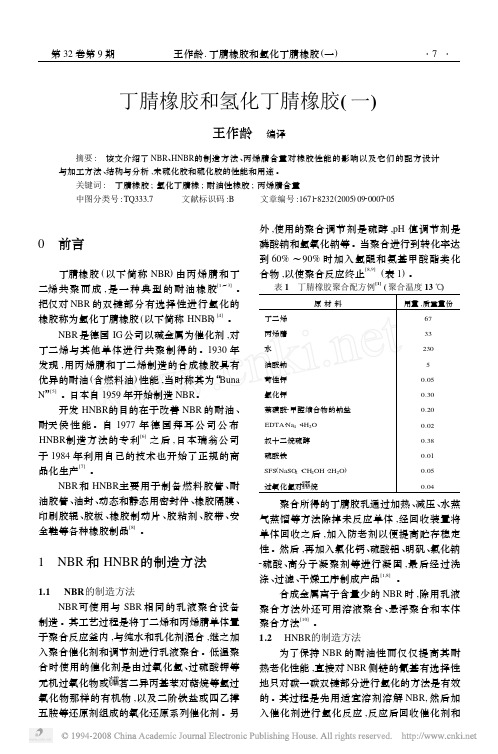
第 32 卷第 9 期
王作龄. 丁腈橡胶和氢化丁腈橡胶 (一) ·7 ·
丁腈橡胶和氢化丁腈橡胶( 一)
王作龄 编译
摘要 : 该文介绍了 NBR、HNBR的制造方法 、丙烯腈含量对橡胶性能的影响以及它们的配方设计 与加工方法 、结构与分析 ,未硫化胶和硫化胶的性能和用途 。
关键词 : 丁腈橡胶 ; 氢化丁腈橡 ; 耐油性橡胶 ; 丙烯腈含量 中图分类号 : TQ333.7 文献标识码 :B 文章编号 :167128232(2005) 0920007205
·8 ·
世 界 橡 胶 工 业
2005
溶剂 ,再经凝固 、干燥制得 HNBR[11] 。
2 丙烯腈类橡胶的种类
在国际合成橡胶制造商协会 ( IISRP) 注册 的 NBR、HNBR制造厂家如表 2 所示[2] 。
表 2 NBR的生产公司 、国别和商品名[12]
生产公司
国名
商品名
1 NBR 和 HNBR的制造方法
1.1 NBR的制造方法 NBR可使用与 SBR 相同的乳液聚合设备
制造 。其工艺过程是将丁二烯和丙烯腈单体置 于聚合反应釜内 ,与纯水和乳化剂混合 ,继之加 入聚合催化剂和调节剂进行乳液聚合 。低温聚 合时使用的催化剂是由过氧化氢 、过硫酸钾等 无机过氧化物或 茗二异丙基苯对萜烷等氢过 氧化物那样的有机物 ,以及二阶铁盐或四乙撑 五胺等还原剂组成的氧化还原系列催化剂 。另
用二乙烯苯和二甲基丙烯酸乙二醇酯等多 官能单体作为第三单体 ,在 NBR 分子内自行交 联的三元共聚 NBR 也已投放市场 。该聚合物 的主要特征是在挤出 、压延和成形等加工过程 中胶料的收缩率小 ,半成品胶片表面光滑 。与 普通 NBR 相比 ,自身交联型 NBR 硫化胶的拉 伸强度和扯断伸长率等物理性能较差 ,因此 ,在 多半情况下它均与普通 NBR 并用[20] 。
HNBR讲稿
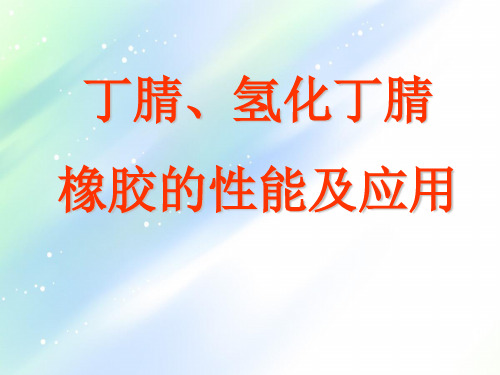
7
(用过氧化锌可改善胶料的疲劳性、压变的生热性能)
c、加工安全性配合 DTDM TMTD
2~4 3~5
组分或性能
HNBR 硬脂酸 氧化锌 N550炭黑 促进剂MBT 促进剂TMTD 硫化剂Sulfasan R 硫黄 促进剂Santocure 促进剂Pennac TM 促进剂MBTS 促进剂TMTM 氧化镁 硫化剂 DP—CP
HNBR硫化胶的代表性能
项 目 表3 HNBR硫化胶的代表性能
硬度(邵尔A) 拉伸强度
扯断伸长率
100%定伸强度 300%定伸强度 回弹率
度 MPa % MPa MPa %
压缩永久变形
%
磨耗量(1.61km)
cm3
指标
45~90 13~35 100~600 3~20 5~30 30~50(室温) 53~56(70℃) 15(23℃×70h) 20(150℃×70h) 25(200℃×70h) 0.03~0.05(室温) 0.04~0.06(150℃)
HNBR广泛用于汽车工业中的密封件,包括传动系统油 封(如曲轴前后油封、齿轮箱油封等)、H型轴封、燃油喷射 系统密封件、活塞缸减震密封件、水泵密封件、空调密封 条、汽缸盖密封件以及汽油泵、化油器用O型圈、皮碗等。
HNBR与NBR比较有很好的耐劣化燃油和耐臭氧性, 甚至较FKM更突出,故在汽车燃料系统密封零件上广泛使 用;现在润滑油中由于添加了各种添加剂,使用寿命都较 长,但添加剂对橡胶有劣化促进作用,且随着时间延长, 就会产生出含有金属淤渣的劣化油,更促进劣化,HNBR 有优异的耐劣化油和淤渣的性能,(即使在高温下),所以 在发动机油、高压机械油的循环系统的油封等方面使用量 越来越多;ACM虽然抗添加剂性能优异,但强度较低。
高饱和丁腈橡胶介绍

高饱和丁腈橡胶—HNBR(一)氢化丁腈橡胶(HNBR)也叫做高饱和丁腈橡胶与传统的丁腈橡胶(NBR)相比,其分子结构中含有少量或不含碳碳双键(C=C),它不仅具有NBR的耐油、耐磨、耐低温等性能,而且还具有更优异的耐热氧老化、耐臭氧、耐化学介质、良好的动态性能等,是目前最具发展潜力的橡胶品种之一,在许多方面已取代了氟橡胶等其它特种橡胶,已广泛地应用于汽车、油田等工业领域。
尤其是汽车用传动带,已占其用量的50%以上。
一、氢化丁腈橡胶(Hydrogenated nitrile rubber)氢化丁腈橡胶因烃链上的不饱和双键被氢化还原成饱和键,故也称高饱和丁腈橡胶,代号HNBR或HSN。
二、历史HNBR最早由德国Bayer公司于1984年小批量生产,商品名为Therban;日本Zeon公司也在同年建厂生产,商品名为Zetpol;随后加拿大的Polysar公司亦于1988年投产,商品名为Tornac(被Bayer兼并,已无此牌号);我国兰化公司于1999年开发成功,牌号:LH-9901、LH9902。
目前,世界HNBR总生产能力约7 500t/a,其中日本占五成、欧洲占三成、北美占二成。
在欧洲其消耗量55%为传动带、密封件20%、胶管11%、电缆5%、其它9%[1]。
三、制造方法:氢化丁腈橡胶制法有三:即乳液加氢化、丙烯腈-乙烯共聚法和丁腈橡胶乳液加氢法三种。
前两法尚在试验阶段,后一种制法已实现工业化。
丁腈橡胶乳液加氢法就是将制成的丁腈橡胶溶解,然后进行催化加氢而制得。
目前多致力于乳液催化加氢技术。
四、品种牌号国外生产氢化丁腈橡胶的厂家有日本瑞翁公司,德国Bayer公司和加拿大Polysar公司三家。
瑞翁公司牌号Zetpol HSN后缀以四位数字,前两位数字表示丙烯腈含量,10和20分别表示高和中高丙烯腈含;后两位数字表示碘值或不饱和度,10或20分别表示饱和度为95%和90%,数字后的字母L表示门尼粘度值低。
氢化丁腈橡胶 (2)

氢化丁腈橡胶简介氢化丁腈橡胶(Hydrogenated Nitrile Butadiene Rubber,HNBR)是一种合成橡胶,由合成橡胶领域的科学家开发出来,以满足特定的工业需求。
氢化丁腈橡胶在耐油性、耐热性、耐化学品等方面具备优异的性能,因此在汽车、航空航天、石油化工等领域得到广泛应用。
本文将介绍氢化丁腈橡胶的特性、制备方法、应用领域以及优缺点。
特性1. 耐油性氢化丁腈橡胶具有极佳的耐油性,可以在高温、高压和恶劣的工作环境下保持其性能稳定。
这使得氢化丁腈橡胶成为汽车发动机密封件、油封等耐油性要求较高的零部件的理想材料。
2. 耐热性HNBR具有优异的耐热性能,在高温环境下仍然可以保持良好的性能。
一般情况下,HNBR的使用温度范围可达-40℃至150℃,在一些特殊的应用场合下,甚至可以达到200℃。
3. 耐化学品性HNBR对于酸、碱等广谱化学物质具有较好的耐受性。
它可以在很多腐蚀性介质中长时间工作,不会因接触化学物质而引发化学反应。
4. 抗老化性HNBR具有较好的抗氧化和抗紫外线性能,其寿命更长。
这使得HNBR在户外设备、气候变化较大的环境下依然能够保持其原有的性能。
5. 弹性良好HNBR具有很好的弹性,即使在高温、高压情况下也能保持较好的弹性变形性能。
这使得HNBR广泛应用于密封件、振动隔离垫等领域。
制备方法氢化丁腈橡胶的合成方法通常是通过在丁腈橡胶的分子链上引入氢原子而实现的。
在这个过程中,需要使用催化剂来催化反应,以实现橡胶分子链上部分或全部丁烯基转化为丁烯基氢化物。
这样一来,氢化丁腈橡胶的分子链就引入了更多的饱和键,提高了其耐热性、耐油性等性能。
应用领域HNBR由于其优异的性能,在许多工业领域得到了广泛应用:1. 汽车行业氢化丁腈橡胶被广泛应用于汽车行业,特别是引擎系统中的耐油密封件。
它可以承受高温高压下的恶劣环境,保护引擎的正常运行。
2. 航空航天在航空航天领域,HNBR广泛应用于液压密封件、燃料储存系统等需要耐热、耐油性能的部件。
常用密封材料(精)

6、硅橡胶(MVQ)
• 使用温度: -60~230 ℃。 • 耐热、耐寒性好 • 压缩永久变形小、弹性好 • 机械强度低 • 不耐油(也有耐油的品种) • 适用于高温、低温条件密封。如罩式炉密封
职业教育“现代纺织技术”专业国家教学资源库
7、氢化丁腈橡胶(HNBR)
密封用纺织品
常用密封材料
职业教育“现代纺织技术”专业国家教学资源库
常用密封材料 1、聚四氟乙烯(PTFE) 2、氟橡胶(FKM) 3、丁腈橡胶(NBR) 4、夹布橡胶(FAB) 5、聚氨酯橡胶(PU) 6、硅橡胶(MVQ) 7、氢化丁腈橡胶(HNBR) 8、尼龙(PA) 9、聚甲醛(POM)
职业教育“现代纺织技术”专业国家教学资源库
4、夹布橡胶(FAB )
• 使用温度:-30 ℃ ~100 ℃ • 由NBR与棉布粘合压制而成 • 强度高,耐磨性好 • 耐油性比NBR略有下降,摩擦系数高 • 用于耐高压下的往复密封,在高压油缸中应用 广泛
职业教育“现代纺织技术”专业国家教学资源库
5、聚氨酯橡胶(PU)
• 使用温度: -30~80 ℃ • 耐磨性能好,机械强度高 • 弹性模量高,弹性好 • 耐油性能好,但压缩变形大 • 在空气中易发生水解,储存条件要求高(密封、 避光) • 适于通用油缸密封
• 使用温度:-55~150 ℃ • 高温条件下性能保持良好 • 与NBR相比,耐油、耐介质、耐温以及耐磨性 有明显提高 • 冶金设备,如线材轧机油膜轴承密封及板材轧 机工作辊密封和油膜轴承多肢密封。
职业教育“现代纺织技术”专业国家教学资源库
8、尼龙(PA)
• 使用温度:-40~120 ℃ • 耐油、耐温、耐磨性能好 • 抗压强度高,抗冲击性能较好 • 尺寸稳定性差 • 适用于制造导向环、支承环、压环、挡圈等
11-第十一章 氢化丁腈橡胶-120216
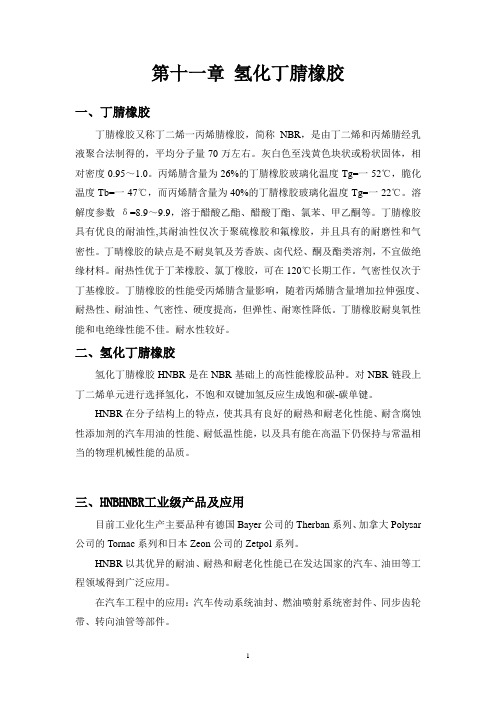
第十一章氢化丁腈橡胶一、丁腈橡胶丁腈橡胶又称丁二烯一丙烯腈橡胶,简称NBR,是由丁二烯和丙烯腈经乳液聚合法制得的,平均分子量70万左右。
灰白色至浅黄色块状或粉状固体,相对密度0.95~1.0。
丙烯腈含量为26%的丁腈橡胶玻璃化温度Tg=一52℃,脆化温度Tb=一47℃,而丙烯腈含量为40%的丁腈橡胶玻璃化温度Tg=一22℃。
溶解度参数δ=8.9~9.9,溶于醋酸乙酯、醋酸丁酯、氯苯、甲乙酮等。
丁腈橡胶具有优良的耐油性,其耐油性仅次于聚硫橡胶和氟橡胶,并且具有的耐磨性和气密性。
丁晴橡胶的缺点是不耐臭氧及芳香族、卤代烃、酮及酯类溶剂,不宜做绝缘材料。
耐热性优于丁苯橡胶、氯丁橡胶,可在120℃长期工作。
气密性仅次于丁基橡胶。
丁腈橡胶的性能受丙烯腈含量影响,随着丙烯腈含量增加拉伸强度、耐热性、耐油性、气密性、硬度提高,但弹性、耐寒性降低。
丁腈橡胶耐臭氧性能和电绝缘性能不佳。
耐水性较好。
二、氢化丁腈橡胶氢化丁腈橡胶HNBR是在NBR基础上的高性能橡胶品种。
对NBR链段上丁二烯单元进行选择氢化,不饱和双键加氢反应生成饱和碳-碳单键。
HNBR在分子结构上的特点,使其具有良好的耐热和耐老化性能、耐含腐蚀性添加剂的汽车用油的性能、耐低温性能,以及具有能在高温下仍保持与常温相当的物理机械性能的品质。
三、HNBHNBR工业级产品及应用目前工业化生产主要品种有德国Bayer公司的Therban系列、加拿大Polysar 公司的Tornac系列和日本Zeon公司的Zetpol系列。
HNBR以其优异的耐油、耐热和耐老化性能已在发达国家的汽车、油田等工程领域得到广泛应用。
在汽车工程中的应用:汽车传动系统油封、燃油喷射系统密封件、同步齿轮带、转向油管等部件。
在油田工程中的应用:井口密封、油赛密封、泵定子保护器、钻井平台配套软管等。
在机械工程中的应用:静、动密封场密封件。
其他应用:主要方向为塑料、橡胶的共混改性技术。
四、二硫化钼改性HNBR摩擦学性能及其在特大尺寸转塔密封圈中的应用某型密封圈是大型方位轴承和俯仰轴承及其转塔内机械、电器设备的动态密封屏障,必须具备两项使用性能:(1)密封性好;(2)滑动摩擦阻尼小。
氢化丁腈橡胶配方
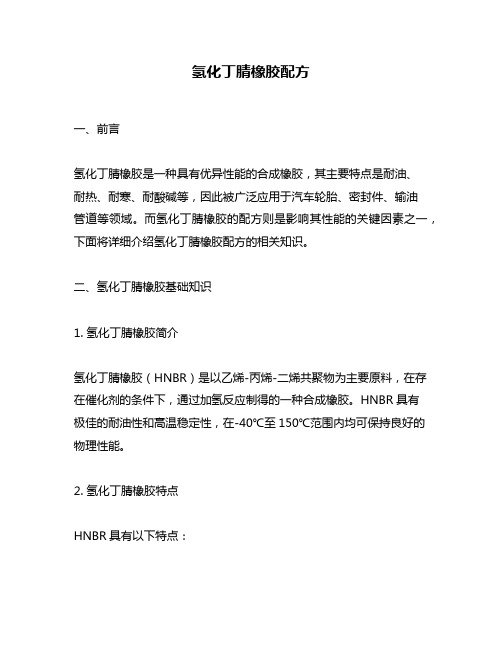
氢化丁腈橡胶配方一、前言氢化丁腈橡胶是一种具有优异性能的合成橡胶,其主要特点是耐油、耐热、耐寒、耐酸碱等,因此被广泛应用于汽车轮胎、密封件、输油管道等领域。
而氢化丁腈橡胶的配方则是影响其性能的关键因素之一,下面将详细介绍氢化丁腈橡胶配方的相关知识。
二、氢化丁腈橡胶基础知识1. 氢化丁腈橡胶简介氢化丁腈橡胶(HNBR)是以乙烯-丙烯-二烯共聚物为主要原料,在存在催化剂的条件下,通过加氢反应制得的一种合成橡胶。
HNBR具有极佳的耐油性和高温稳定性,在-40℃至150℃范围内均可保持良好的物理性能。
2. 氢化丁腈橡胶特点HNBR具有以下特点:(1)优异的耐油性能:HNBR在高温和高压下仍然可以保持良好的耐油性能,因此被广泛应用于汽车、航空、工程机械等领域。
(2)优异的耐热性能:HNBR在高温条件下仍然可以保持较好的物理性能,因此在高温环境下应用广泛。
(3)优异的耐寒性能:HNBR在低温条件下仍然可以保持较好的物理性能,因此在低温环境下应用广泛。
(4)优异的耐酸碱性能:HNBR具有出色的化学稳定性,可以抵抗各种酸碱介质和氧化剂的侵蚀。
三、氢化丁腈橡胶配方1. 氢化丁腈橡胶主要成分氢化丁腈橡胶主要由以下成分组成:(1)乙烯-丙烯-二烯共聚物(2)氢化催化剂(3)填料(4)增塑剂(5)硫化剂和促进剂2. 氢化丁腈橡胶配方设计原则设计氢化丁腈橡胶配方需要遵循以下原则:(1)根据应用领域选择不同的氢化丁腈橡胶种类。
(2)根据应用环境选择不同的填料和增塑剂。
(3)控制硫化剂和促进剂的用量,以达到理想的物理性能。
(4)保证配方稳定性,避免成分变化对产品质量造成影响。
3. 氢化丁腈橡胶配方设计步骤设计氢化丁腈橡胶配方需要遵循以下步骤:(1)确定应用领域和要求。
(2)选择合适的氢化丁腈橡胶种类。
(3)选择填料和增塑剂,控制其用量。
(4)确定硫化剂和促进剂种类及用量。
(5)进行试验验证,优化配方。
四、氢化丁腈橡胶配方试验方法1. 氢化丁腈橡胶物理性能测试氢化丁腈橡胶物理性能测试主要包括:(1)拉伸强度测试:通过试样在拉伸机上施加力来测定其最大拉伸强度、断裂伸长率等指标。
氢化丁腈橡胶与丁腈橡胶的区别

氢化丁腈橡胶与丁腈橡胶的区别氢化丁腈橡胶(HNBR)和丁腈橡胶(NBR)是两种常见的热塑性橡胶材料,除了他们的物理性能有所不同外,还有许多其他方面的差异。
在本文中,我们将介绍氢化丁腈橡胶和丁腈橡胶的原理,以及两者之间的差异。
首先,我们要解释一下两者的原理。
这是因为,氢化丁腈橡胶和丁腈橡胶都是化学上的改性橡胶,最初都来自于聚氯乙烯(PVC)。
氢化丁腈橡胶(HNBR)是将PVC进行氢化处理而得到的新材料。
它的特性是分子链上含有氢键,这些氢键使得其具有更高的耐热性和抗拉强度,因此它比纯丁腈橡胶有更高的温度稳定性。
丁腈橡胶(NBR)是由聚氯乙烯进行醇酸改性而得到的材料,相比氢化丁腈橡胶它的耐油性和耐化学性更好。
氢化丁腈橡胶和丁腈橡胶之间的区别是,氢化丁腈橡胶的耐温范围比丁腈橡胶更宽,它能承受更高的温度,但丁腈橡胶处理性能更好,可以通过改性来改善物理性能。
氢化丁腈橡胶实际上是将原材料进行氢化处理,但丁腈橡胶是通过醇酸改性而得到的。
因此,氢化丁腈橡胶的拉伸强度相对来说比丁腈橡胶要高得多,另外,氢化丁腈橡胶还具有抗拉伸性和热稳定性,而丁腈橡胶则表现出良好的耐油性和耐化学性。
然而,因为氢化丁腈橡胶与丁腈橡胶都是化学改性橡胶,其物理性能也存在一定的差异,其中包括耐温范围、弹性模量、拉伸强度和耐磨性等。
氢化丁腈橡胶的耐热性能优于丁腈橡胶,其耐温范围可达150℃以上,而丁腈橡胶的耐温范围最高只能达到120℃,此外,氢化丁腈橡胶的拉伸强度也要高于丁腈橡胶,其拉伸强度在25-32MPa 之间,而丁腈橡胶的拉伸强度往往只有7-8MPa。
不仅如此,氢化丁腈橡胶和丁腈橡胶在应用领域也存在差异。
氢化丁腈橡胶通常用于汽车、电子、液压和仪器等高温环境中,而丁腈橡胶则更适合用于润滑剂、油墨、油性涂料、汽油和柴油等石化行业。
以上就是氢化丁腈橡胶和丁腈橡胶的区别。
除了已经分析的各个方面的差异外,我们还可以知道,氢化丁腈橡胶的耐热性更高,耐温范围更广,拉伸强度更高,耐磨性也更好,而丁腈橡胶的耐油性和抗化学性更好,处理性能更好,但耐温范围有限。
氢化丁腈橡胶开发与生产方案(二)
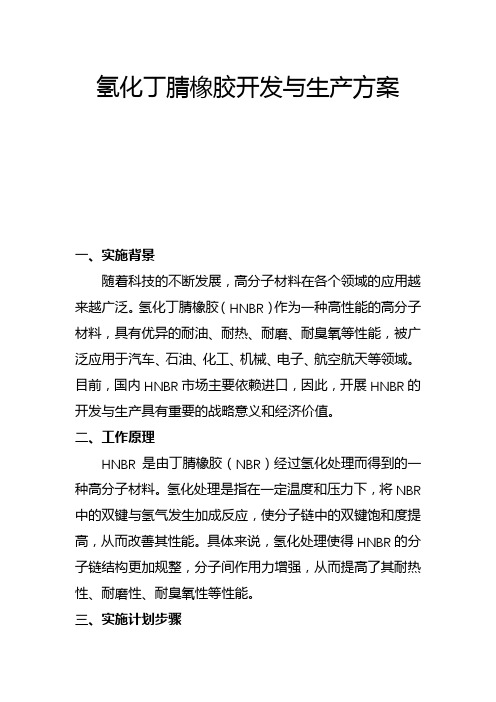
氢化丁腈橡胶开发与生产方案一、实施背景随着科技的不断发展,高分子材料在各个领域的应用越来越广泛。
氢化丁腈橡胶(HNBR)作为一种高性能的高分子材料,具有优异的耐油、耐热、耐磨、耐臭氧等性能,被广泛应用于汽车、石油、化工、机械、电子、航空航天等领域。
目前,国内HNBR市场主要依赖进口,因此,开展HNBR的开发与生产具有重要的战略意义和经济价值。
二、工作原理HNBR是由丁腈橡胶(NBR)经过氢化处理而得到的一种高分子材料。
氢化处理是指在一定温度和压力下,将NBR 中的双键与氢气发生加成反应,使分子链中的双键饱和度提高,从而改善其性能。
具体来说,氢化处理使得HNBR的分子链结构更加规整,分子间作用力增强,从而提高了其耐热性、耐磨性、耐臭氧性等性能。
三、实施计划步骤1. 原料准备:准备丁腈橡胶(NBR)原料,并根据需求进行配料。
2. 混炼:将NBR原料放入密炼机中,加入适量的助剂,进行混炼。
混炼的目的是使原料充分混合均匀,同时提高橡胶的可塑性。
3. 压片:将混炼好的橡胶放入压片机中,进行压片。
压片的目的是使橡胶具有一定的形状和厚度,便于后续的加工处理。
4. 硫化:将压好的橡胶片放入硫化机中,在一定的温度和压力下进行硫化处理。
硫化的目的是使橡胶分子链之间形成化学键连接,从而提高橡胶的物理性能和化学稳定性。
5. 氢化:将硫化好的橡胶片放入氢化反应釜中,在一定的温度和压力下进行氢化处理。
氢化的目的是使橡胶分子链中的双键与氢气发生加成反应,从而提高橡胶的耐热性、耐磨性、耐臭氧性等性能。
6. 后处理:将氢化好的橡胶片进行切割、打磨、包装等后处理工序,得到最终的HNBR产品。
四、适用范围HNBR因其优异的性能特点,被广泛应用于以下领域:1. 汽车工业:HNBR主要用于汽车密封件、O型圈、油封等部件的生产。
其优异的耐油性和耐高温性能能够满足汽车发动机等高温部件的密封要求。
2. 石油工业:HNBR可用于制作石油开采设备中的密封件、O型圈等部件。
氢化丁腈橡胶 高温 副产物

氢化丁腈橡胶高温副产物
氢化丁腈橡胶是一种高温耐性较好的橡胶材料,广泛应用于高温环境下的密封、绝缘、防护等领域。
副产物是在氢化丁腈橡胶制造过程中产生的次要产品或废弃物。
氢化丁腈橡胶的副产物可以包括以下几个方面:
1. 丁腈橡胶的制备过程中可能会生成一些副产物,如气体、废水和废气。
这些废弃物需要进行处理和排放,以符合环保要求。
2. 在氢化丁腈橡胶的生产过程中,可能会产生一些固体废弃物,如废料、剪切废物等。
这些废弃物通常会进行回收、再利用或者进行妥善处理和处置。
3. 氢化丁腈橡胶材料在使用过程中,可能会发生老化、磨损、损坏等情况,产生废弃的橡胶制品。
这些废品可以进行再生利用或者进行橡胶废弃物的回收、处理和处置。
针对上述副产物,需要采取有效的环保措施和处理方法,如废水处理系统、废气净化设备、固体废弃物处理设施等,以减少对环境的影响并实现资源的最大化利用。
同时,通过科学严谨的生产工艺和管理,尽量减少副产物的产生,达到绿色环保的生产方式。
丁腈橡胶与氢化丁腈橡胶的比较

丁腈橡胶与氢化丁腈橡胶的比较丁腈橡胶是由丁二烯和丙烯腈经乳液聚合法制得的,丁腈橡胶主要采用低温乳液聚合法生产,耐油性极好,耐磨性较高,耐热性较好,粘接力强。
其缺点是耐低温性差、耐臭氧性差,绝缘性能低劣,弹性稍低。
丁腈橡胶主要用于制造耐油橡胶制品。
简称NBR,由丁二烯与丙烯腈共聚而制得的一种合成橡胶。
是耐油(尤其是烷烃油)、耐老化性能较好的合成橡胶。
丁腈橡胶中丙烯腈含量(%)有42~46、36~41、31~35、25~30、18~24等五种。
丙烯腈含量越多,耐油性越好,但耐寒性则相应下降。
它可以在120℃的空气中或在150℃的油中长期使用。
此外,它还具有良好的耐水性、气密性及优良的粘结性能。
广泛用于制各种耐油橡胶制品、多种耐油垫圈、垫片、套管、软包装、软胶管、印染胶辊、电缆胶材料等,在汽车、航空、石油、复印等行业中成为必不可少的弹性材料。
NBR具有优异的耐油性。
丁二稀单体可共聚成顺式、反式和1,2-烧基三种不同的链结构。
典型的NBR结构中反式占约78%。
由于NBR 分子链结构中含有氰基,耐油性(如耐矿物油、液体燃料、动植物油和溶剂)优于天然橡胶、氯丁橡胶和丁苯橡胶。
与其他橡胶相比NBR有更宽域的使用温度,它的长期使用温度为120C,同时NBR具有良好的耐低温性能,最低玻璃化温度可达-55C。
NBR耐化学稳定性好,加工性能良好,随着其结构中的丙炼腈含量其相对密度增大,硫化速度加快,拉伸强度性能提高,但回弹性能下降,耐寒性变差。
由于NBR中的氰基容易电场极化,因而介电性能下降,是半导体橡胶。
NBR可以按ACN含量的高低,分为超高、高、中高、中和低丙稀腈5类。
生产方式分连续和间歇聚合法两种。
连续聚合法通常用于少品种和大生产量生产,消耗低。
间歇聚合法适用于多品种和小批量生产,聚合签使用数量少,工程建设消耗高。
目前为止,还看不出相互替代的趋势。
丁腈橡胶虽然具有优良的物理机械性和加工性能,但长期在在酸性汽油和高温(150C)环境中使用性能不如氟样胶和丙稀酸酷胶,为此德国公司,加拿大公司和日本公司开发出性能优异的氢化丁腈橡胶(HNBR) 。
丁晴橡胶

丁腈橡胶性能溶剂,不宜做绝缘材料。
耐热性优于丁苯橡胶、氯丁橡胶,可在120℃长期工作。
气密性仅次于丁基橡胶。
丁腈橡胶的性能受丙烯腈含量影响,随着丙烯腈含量增加,拉伸强度、耐热性、耐油性、气密性、硬度提高,但弹性、耐寒性降低。
丁腈橡胶耐臭氧性能和电绝缘性能不佳。
耐水性较好。
丁腈橡胶的伸长率可达300%,抗张强度大于10N/mm2。
丁腈橡胶对矿物油、植物油、苯、汽油、普通的稀酸和碱具有良好的耐受性。
但丁腈橡胶的唇形密封圈不能使用在高于80℃的条件下,因为在该温度下,丁腈橡胶对于溶剂的稳定下会下降。
主要用途丁腈橡胶的用途包括制造一次性医用手套、传送带、软管、O形圈、垫圈、油封产品、V形带、合成革、印刷辊以及电缆护套。
丁晴橡胶还被用于制造粘合剂。
丁腈橡胶的氢化版本被称为氢化丁腈橡胶(HNBR)常被用于生产空调用O形圈。
质量指标国外牌号有NBR2860,NBR3350,NBR3960(Petrofelex公司)、NB40S,N232S,N220SH(日本) 、Krynac 2750C,Krynac4060C,Krynac 4970C(加拿大)。
制作加工制作丁腈橡胶于1930年首先由德国进行研究,在1931年制成丁二烯与丙烯腈的共聚物,发现其具有优异的耐油、耐老化及耐磨等性能。
1937年由德国I.G.Faben公司投入工业化生产,以商品名BunaN问世。
1941年美国也开始大规模生产。
此后不久,一些国家也相继开始生产丁腈橡胶,世界上已有很多国家能够生产各种牌号的丁腈橡胶。
丁腈橡胶除具有优异的耐油性之外,还具有耐老化、耐磨耗、低透气和凝聚力高等特点,因此其应用领域是多方面的。
丁腈橡胶的需要量在全部橡胶需要量中所占的比例随各国的具体情况而异,一般工业先进国家约占2.5~3.5%,发展中国家的比例稍低一些。
制法(一)原料丁腈橡胶聚合用单体为丁二烯和丙烯腈。
聚合用辅助原料有如下几种。
聚合引发剂为:热聚合采用无机过氧化物(如过硫酸盐);冷聚合采用氧化还原引发剂(如过氧化氢和二价铁盐共存的催化体系)。
氢化丁腈橡胶与丁腈橡胶的区别
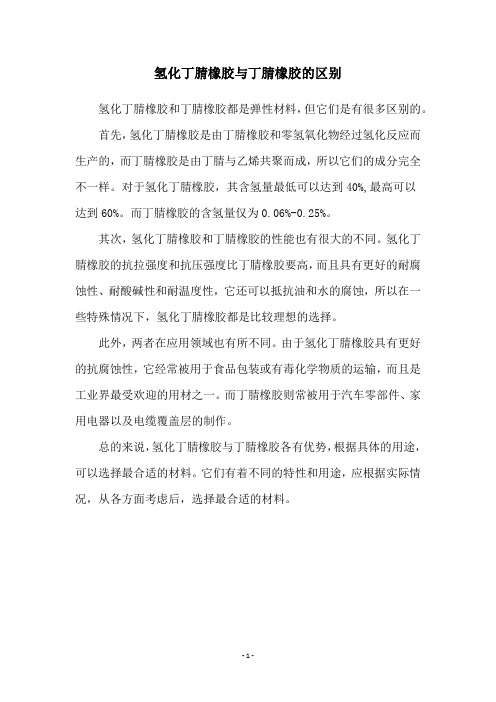
氢化丁腈橡胶与丁腈橡胶的区别
氢化丁腈橡胶和丁腈橡胶都是弹性材料,但它们是有很多区别的。
首先,氢化丁腈橡胶是由丁腈橡胶和零氢氧化物经过氢化反应而生产的,而丁腈橡胶是由丁腈与乙烯共聚而成,所以它们的成分完全不一样。
对于氢化丁腈橡胶,其含氢量最低可以达到40%,最高可以
达到60%。
而丁腈橡胶的含氢量仅为0.06%-0.25%。
其次,氢化丁腈橡胶和丁腈橡胶的性能也有很大的不同。
氢化丁腈橡胶的抗拉强度和抗压强度比丁腈橡胶要高,而且具有更好的耐腐蚀性、耐酸碱性和耐温度性,它还可以抵抗油和水的腐蚀,所以在一些特殊情况下,氢化丁腈橡胶都是比较理想的选择。
此外,两者在应用领域也有所不同。
由于氢化丁腈橡胶具有更好的抗腐蚀性,它经常被用于食品包装或有毒化学物质的运输,而且是工业界最受欢迎的用材之一。
而丁腈橡胶则常被用于汽车零部件、家用电器以及电缆覆盖层的制作。
总的来说,氢化丁腈橡胶与丁腈橡胶各有优势,根据具体的用途,可以选择最合适的材料。
它们有着不同的特性和用途,应根据实际情况,从各方面考虑后,选择最合适的材料。
- 1 -。
丁腈橡胶
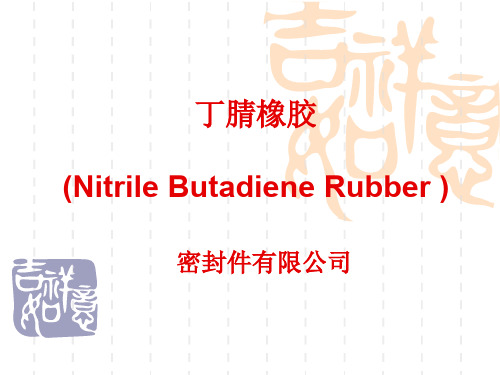
密封件有限公司
丁腈橡胶(Nitrile Butadiene Rub腈经乳
液聚合法制得的,丁腈橡胶主要采用低 温乳液聚合法生产。
丁腈橡胶分子结构式:
丁腈橡胶(Nitrile Butadiene Rubber )
2.3粉末丁腈橡胶(PNBR) 方便称量与使用。 主要用来进行PVC\树脂改性。 应用于胶粘剂、涂料等行业
丁腈橡胶(Nitrile Butadiene Rubber )
2.4液体丁腈橡胶(LNBR) 低分子量(1000)的液体丁腈,作为丁腈
橡胶的不挥发性、非抽出性增塑剂、加工 助剂使用。也可用于树脂改性及配制胶粘 剂。
1-4、氢化丁腈橡胶还具有优异的机械物理 性能:
高强度; 高撕裂性能; 高耐磨性能,是综合性能极为出色的橡胶
之一。
丁腈橡胶(Nitrile Butadiene Rubber )
2、氢化丁腈橡胶目前广泛用于油田、汽车 工业等方面。在使用条件极为苛刻的领域, 氢化丁腈橡胶有着良好的表现,被越来越 大量的采用。
丁腈橡胶(Nitrile Butadiene Rubber )
2.5丁腈和PVC共混胶 丁腈橡胶还可与其他橡胶或者塑料并用,
以改善各方面的性能,应用最多的是与聚 氯乙烯并用,由于在橡胶中加入PVC,提 高了橡胶的耐臭氧和耐候性,拓宽了丁腈 橡胶的使用范围。广泛用于耐油电缆外皮, 鞋底,胶管等领域。
丁腈橡胶(Nitrile Butadiene Rubber )
三、普通丁腈橡胶的命名 1、命名方法 如: N3350 N2865 N1965 等 A、丙烯腈含量(15-50%) B、门尼粘度(20~140)100 ℃条件下
氢化丁腈橡胶

氢化丁腈橡胶氢化丁腈橡胶(简称HNBR)是通过氢化丁腈橡胶主链上所含的不饱和双键而制得,又称为高饱和度丁腈橡胶。
由于HNBR具有合理的分子结构,因此不仅继承了NBR的耐油、耐磨等性能,而且还具有更优异的耐热、耐氧化、耐臭氧、耐化学品性能,可以与氟橡胶相媲美,在许多方面可取代氟橡胶、CR、NBR等特种橡胶。
一、发展状况日本瑞翁(Zeon)公司早在70年代就开展了HNBR的研究工作,1978年开发成功高活性,高选择性的以二氧化硅为载体的钯催化剂,1980年HNBR生产中试成功,并于1984年4月在日本高岗建厂,其牌号为Zetpol。
1982年Bayer公司开发出商业牌号Therban1707和1907,含腈量分别为34%和38%的HNBR。
加拿大Polysar公司于70年代与日本同步开始研制HNBR,1985年通过中试,1988年11月在美国得克萨斯州投产,产口牌号Tornac,产能为1600吨/年。
1991年Bayer公司收购了Polysar 的合成橡胶部分,还将在欧洲另建Therban生产厂,设计能力为3000吨/年。
1995年瑞翁公司的HNBR生产能力达到5300吨/年。
1992年,北京化工大学同台湾南帝化学工业股份公司合作率先开展NBR的加氢催化剂和加氢工艺的研究,随后,兰化公司化学研究所和吉化公司研究院也相继开始HNBR的研究工作,1999年我国兰化公司HNBR开发成功,牌号为LH-9901,LH-9902。
目前,世界HNBR生产能力达2.2万吨/年,生产厂家主要有德国Bayer公司(生产能力为1.0万t/a),日本Zeon公司(生产能力为1.2万吨/年)。
二、市场需求及预测2001年,世界HNBR 已占NBR市场份额的20%以上,可见HNBR这种特殊形态的NBR的地位日趋重要。
2007年世界 HNBR需求量约为1.9万t,预计2010年需求量达2.2万t。
目前国产HNBR的供应主要来自中国石油兰州化工研究中心,进口产品主要来自日本瑞翁,牌号为Z2010、Z2020。
丁腈橡胶和氢化丁腈橡胶(二)
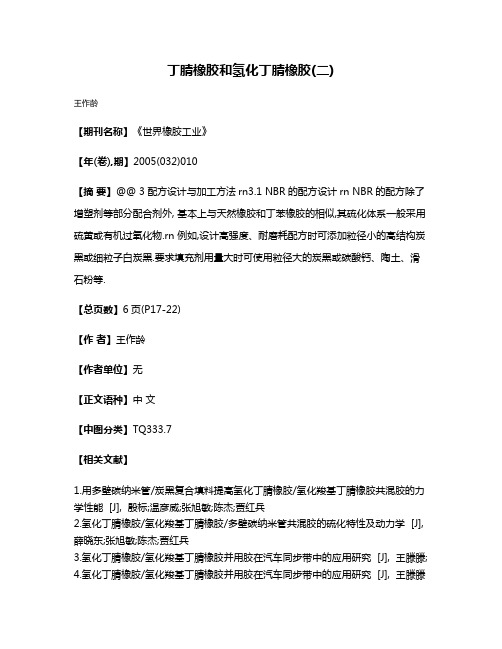
丁腈橡胶和氢化丁腈橡胶(二)
王作龄
【期刊名称】《世界橡胶工业》
【年(卷),期】2005(032)010
【摘要】@@ 3配方设计与加工方法rn3.1 NBR的配方设计rn NBR的配方除了增塑剂等部分配合剂外, 基本上与天然橡胶和丁苯橡胶的相似,其硫化体系一般采用硫黄或有机过氧化物.rn 例如,设计高强度、耐磨耗配方时可添加粒径小的高结构炭黑或细粒子白炭黑.要求填充剂用量大时可使用粒径大的炭黑或碳酸钙、陶土、滑石粉等.
【总页数】6页(P17-22)
【作者】王作龄
【作者单位】无
【正文语种】中文
【中图分类】TQ333.7
【相关文献】
1.用多壁碳纳米管/炭黑复合填料提高氢化丁腈橡胶/氢化羧基丁腈橡胶共混胶的力学性能 [J], 殷标;温彦威;张旭敏;陈杰;贾红兵
2.氢化丁腈橡胶/氢化羧基丁腈橡胶/多壁碳纳米管共混胶的硫化特性及动力学 [J], 薛晓东;张旭敏;陈杰;贾红兵
3.氢化丁腈橡胶/氢化羧基丁腈橡胶并用胶在汽车同步带中的应用研究 [J], 王滕滕;
4.氢化丁腈橡胶/氢化羧基丁腈橡胶并用胶在汽车同步带中的应用研究 [J], 王滕滕
5.红外光谱法测定氢化丁腈橡胶(HNBR)中丙烯腈、丁二烯和氢化丁二烯的比例第二部分工业用HNBR产品中残留双键[J], D.Brück;李玉娥
因版权原因,仅展示原文概要,查看原文内容请购买。
- 1、下载文档前请自行甄别文档内容的完整性,平台不提供额外的编辑、内容补充、找答案等附加服务。
- 2、"仅部分预览"的文档,不可在线预览部分如存在完整性等问题,可反馈申请退款(可完整预览的文档不适用该条件!)。
- 3、如文档侵犯您的权益,请联系客服反馈,我们会尽快为您处理(人工客服工作时间:9:00-18:30)。
丁腈橡胶和氢化丁腈橡胶(二)王作龄 编译 中图分类号:T Q333.7 文献标识码:B 文章编号:167128232(2005)10200172063 配方设计与加工方法3.1 NBR的配方设计NBR的配方除了增塑剂等部分配合剂外,基本上与天然橡胶和丁苯橡胶的相似,其硫化体系一般采用硫黄或有机过氧化物。
例如,设计高强度、耐磨耗配方时可添加粒径小的高结构炭黑或细粒子白炭黑。
要求填充剂用量大时可使用粒径大的炭黑或碳酸钙、陶土、滑石粉等。
非污染型防老剂可使用酚类、磷类、对苯二酚类化合物。
要求提高耐热性时,使用胺类防老剂效果较好,若添加二苯胺类和二氢喹啉等自由基补充剂或与咪唑的金属盐等氢过氧化物分解剂并用,其效果更好。
此外,NBR制品用于与燃油和润滑油等接触的场合也很多,对此,用户往往提出橡胶制品对这些油要耐抽出。
此时也可使用苯撑二胺类和二硫代酸金属盐等防老剂。
抗臭氧老化剂一般系将石蜡与对苯二胺类防老剂并用。
采用有机过氧化物硫化体系时,防老剂和抗臭氧剂有时会成为强有力的自由基抑制剂而阻碍硫化。
此时,必须考虑有机过氧化物硫化剂品种的选择和用量。
对于要求耐臭氧老化性好的丁腈橡胶制品,采取NBR与PVC并用的效果较好。
此时PVC的标准并用量为30份,根据用途不同,并用量可在15份~50份范围内波动,这样无损于制品的耐油性且可改善其抗臭氧老化性,但要注意其耐寒性。
NBR与三元乙丙橡胶并用也可改善制品的耐臭氧性,但有可能降低其耐油性。
因此,在进行配方设计时要充分考虑两者的相溶性和硫化速度的差异[25]。
添加增塑剂可降低NBR和H NBR加工时的粘度,对控制硫化胶在各种溶剂和润滑油中的体积膨胀率以及改善耐寒性也有效果。
增塑剂与NBR和H NBR的相溶性随这两种橡胶中丙烯腈含量的不同而各异。
相溶性大致可按物质的溶解度参数,即SP值推断,SP值相互接近的物质,其相溶性也好,可以多量添加。
NBR 用增塑剂的选择和PVC用增塑剂的选择相类似,因为它们的SP值较接近。
为避免因增塑剂用量过大而引起的喷霜,NBR的增塑剂的最大用量可通过硫化胶的浸渍试验,根据NBR吸收的增塑剂的量求出。
除了部分在橡胶中扩散慢的分子量较高的增塑剂之外,用该方法可充分推算出增塑剂的最大用量(图2、表6)[26、27]。
对于有非挥发性、非抽出性和非迁移性要求的制品,最好使用高分子量增塑剂或液体丁腈橡胶。
图2 NBR中丙烯腈含量与各种增塑剂的相溶性 NBR的硫化剂一般为硫黄或含硫化合物。
要求在较低温度下长时间硫化的厚壁制品和谋求廉价的硫化体系时可采用含1.5份硫黄及DM等的噻唑类促进剂硫化体系(图3)[7]。
要求快速硫化时,多半采用将噻唑类促进剂和二硫代酸金属盐(例:二硫代氨基甲酸盐)类促进剂并用的硫化体系。
要求制品具有低压缩永久表6 不同增塑剂在HNBR 中的可使用量[27]增塑剂化学名称HNBR 中丙烯腈含量36%44%邻苯二甲酸二甲酯(DMP )235285邻苯二甲酸二乙酯(DEP )254271邻苯二甲酸二丁酯(DBP )246213邻苯二甲酸二辛酯(DOP )10528邻苯二甲酸二异癸酯(DIDP )5812己二酸二辛酯(DOA )3611癸二酸二辛酯(DOS )204磷酸三辛酯(T OP )274磷酸三甲苯酯(TCP )215188己二酸二丁氧基乙氧基己酯(DBEE A )5033环氧化大豆油(E BO )174变形时,使用的硫黄为0.5份或以下,第一促进剂为二硫化四甲基秋兰姆即促进剂T MT D (TT ),为防止焦烧第二促进剂可少量使用次磺酰胺类和噻唑类促进剂。
这样的硫化体系也有效果[17]。
促进剂T MT D 与氧化锌反应生成二硫代氨基甲酸锌有防老化作用。
若用量过大,因它在NBR 中的溶解度低而容易引起喷霜,因此用量要限制[2,3]。
与硫黄硫化相比,有机过氧化物硫化的特点是制品的压缩永久变形小,耐热性优异,溶剂抽出沉淀性小;但存在着硫化周期长、硫化胶的扯断伸长率低和耐屈挠龟裂性差等问题。
NBR 使用的有机过氧化物以过氧化二异丙苯为标准型。
为了获得较低的压缩永久变形,可使用叔图3 NBR 的代表性硫化体系丁基过氧化二异丙苯等。
为了获得高伸长率、高耐屈挠龟裂性也可使用2,52二甲基22,52双(叔丁基过氧基)232己炔等。
有机过氧化物与三羟甲基丙烷三甲基丙烯酸酯(硫化剂T MPT )和三聚异氰酸三烯丙酯(硫化剂T AIC )等多官能单体并用,可降低NBR 混炼胶的粘度和改善硫化胶的压缩变形性能。
3.2 H NBR 的配方设计H N BR 的配方设计酷似N BR ,但需要考虑的是硫化体系的选择问题。
与N BR 相比,H N BR 的双键浓度低,对焦烧时间不必过多担心。
H NBR 的硫化体系与三元乙丙橡胶极为相似,用有机过氧化物硫化时其用量比NBR 的量稍多(2份~4份);用硫黄硫化时,除第一促进剂外,第二促进剂可采用将秋兰姆类和噻唑类并用的方法[28~30]。
3.3 NBR和H NBR的加工方法NBR和H NBR的加工工艺和加工装备械与天然橡胶、丁苯橡胶等橡胶的相同。
NBR和H NBR原则上可合成任意门尼粘度的聚合物,因此除了用作溶解用那部分之外,塑炼工序可省略。
对NBR有效的塑解剂目前尚未问世,因此欲通过塑炼来降低NBR的粘度是相当困难的[2]。
NBR和H NBR的混炼工序一般分为两段,第一段添加填充剂、活性剂、增塑剂等,第二段添加硫化剂,使用的混炼机械大都为本伯里密炼机、肖氏密炼机和捏炼机,二段混炼也可使用开炼机。
NBR对硫黄的溶解度较低,有时会出现硫化不均问题。
解决措施是在混炼开始时添加硫黄,或在半成品压延、挤出等成型工序之前进行热炼以减轻硫黄分散不均现象。
X NBR(羧基丁腈橡胶)通过氧化锌可进行交联反应,因此氧化锌多半在二段混炼时于冷却的开炼机上添加。
NBR和H NBR混炼胶的粘性较差,需要贴合成型的制品可使用增粘剂,例如非反应型烷基酚醛树脂、松香酸酯、古马隆2茚树脂和液体NBR的混合物。
经过混炼的胶料先由压延机或挤出机等进行预成型,尔后用平板硫化机、传递模压机、注射成型机或硫化罐等进行硫化,制成成品。
4 丙烯腈类橡胶的结构与物理性能影响NBR性能的因素有丙烯腈含量、组成分布、分子量、分子量分布、支化度、凝胶含量、丁二烯链段的微结构和链分布等。
表7为中高丙烯腈NBR的分子特性[20]。
4.1 结构与分析方法[31]可用红外线吸收光谱和热裂解气相色谱法(PG C)对NBR聚合物进行定性分析;共聚组成,即丙烯腈含量可用氮气分析法和PG C等方法进行分析;异构化结构和链分布等用核磁共振(NMR)法求取效果好。
分析NBR硫化胶中聚合物、填充剂等的用量配比时,采用热天平法比较简便。
表7 中高丙烯腈NBR ML1+4为50(100°C)的分子特性值[20]共聚组成 平均组成(丙烯腈结合量),%35 组成分布宽度,%±5.5丁二烯链段的微结构(13C2NMR) 反式21,4结构,%83 顺式21,4结构,%8 1,22结构,%9链分布(13C2NMR) BBB,%20 BBA,%53 ABA,%27 AAA,%4 AAB,%6 BAB,%90分子量及分子量分布 [η]30°C,甲乙酮 1.36 M n×10-4(Osm) 6.9 M w×10-4(G PC)22.6 M wΠ M n(G PC) 4.1支化度,λ×105 3.7 分析NBR生胶时,最好是先用甲醇,通过索氏萃取器或加热浸渍法,将NBR中所含的微量聚合助剂和防老剂等抽提掉。
NBR生胶因丙烯腈含量的不同其在溶剂中的溶解度多少有些差异。
NBR易溶于苯、甲苯、四氢呋喃和丙酮等,不溶于水、乙醇、己烷等。
用再沉淀法对NBR进行精制时,可将强溶剂与弱溶剂进行适当的组合。
NBR的红外光谱如图4所示。
图中波数970和910cm-1附近的光谱分别为丁二烯的反式21,4结构和反式21,2结构;波数2240cm-1附近的光谱是由于丙烯腈的C≡N伸缩振动所致,根据这种极富特征的光谱,即可容易地区分出与其他橡胶的差别。
根据波数2244-1和970-1的吸光度值也可求出丙烯腈结合量,一般采用凯氏(kjeldahis)定氮法进行氮气分析,精度较高。
H NBR的红外光谱如图5所示。
与NBR相比,由于二烯引起的碳2碳间的双键部分吸收小,而由亚甲基链引起的720cm -1附近的吸收增加。
此外,NBR 硫化胶热分解物的红外光谱吸收带如表8所示[32]。
图4 NBR 的红外光谱(丙烯腈含量27%,碘值280)图5 HNBR 的红外光谱(丙烯腈含量36%,碘值28) 据报道,H NBR 的氢化率也有采用以往的碘值测定法与NMR 和红外光谱法组合的测定方法[33,34]。
关于NBR 的分子量测定,数均分子量Mn 可用浸透压等方法测定,重均分子量M w 可用沉淀平衡法和光散射法测定,而粘均分子量可对固有粘度[η]进行测定,按表9所示的粘度换算式求出[5]。
表8 NBR 热分解物的红外吸收带[32]波数,cm -1属性2260(s )—C ≡N 1645~1603(br )—1450(s )—CH 2—1380—CH 31073(w )—1045(w )—990RHC =CH 2R 965(s )RHC =CHR ′(反式)908(s )R (CH 3)C =CH 2890(w )—表9 粘均分子量计算用常数[5]溶 剂a k 甲 苯0.64 4.9×10-4苯 0.55 1.3×10-4氯 仿0.68 5.4×10-4丙 酮0.645.0×10-4 [η]=K M a v 分子量分布可用热解气相色谱(G PC )测定法求出。
Mn 、M w 和M w ΠMn 通常用已知分子量的标准聚乙烯通过常规方法求出。
不溶解部分和凝胶用滤纸、金属网和波璃过滤器测出。
4.2 基本性能NBR 的基本性能和如表10所示[1,5,12,38~47]。
随着丙烯腈含量增加,NBR 的波璃化温度增高,脆性温度也大致表现同样的趋势(表11)[5]。
表10 NBR 的基本性能[1,5,12,38~47]性能数值密 度H :0.999[38];MH :0.978[12];M:0.968[38]线膨胀系数,×10-6Π°C -1H :150[5];MH :170[5];M:175[5];H :220[39];M:220[39];L :240[39](T g 以下H :73[39];M:70[39]L :80[39])质量热容,Cal Πg ・°CH :0.471[40]绝热压缩率,×10-12cm 2Πdyn H :35[41]导热系数,kal Πm ・h ・°CH :0.220[5];MH :0.215[5];M:0.215[5]玻璃化温度,°CH :-22;MH :-38;M:-46;L :-56[5]与振动频率的关系[42]HM L 1000周期Π分-20-36-45100周期Π分-24-38-4810周期Π分-26-41-511周期Π分-27-45-55与伸长率的关系[43]伸长100%变化-1.5°C音 速,cm Π秒 6.6~8.2×103[44]体积电阻,Ω・cm 1017~1011[45]功率因素,%5~6[45]介电常数,kH z 7~12[45]破坏电压,kV Πmm20[45]SP 值M:10.30;MH :9.64;M:9.38;L :8.7[46,47] NBR 的种类:H —高丙烯腈;MH —中高丙烯腈;M —中丙烯腈;L —低丙烯腈表11 NBR 中丙烯腈含量与玻璃化温度和脆性温度[5]丙烯腈含量,%T g ,°C脆性温度,°C0—-8020-56-5522-52-49.526-52-4729-46-4630-41-3831-43-33-37~-39-3337-34-26.539-26~-33-2340-22—52-16-16.5 NBR 的主要物理性质取决于聚合物的丙烯腈结合量。