冷作模具失效分析及优化对策
冷作模具热处理后变形与预防及工艺优化
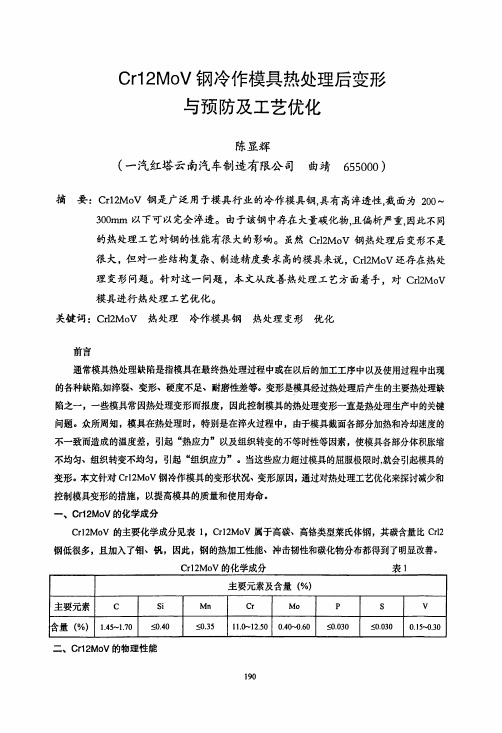
/、 Lj
o
,_、
(__)
o
邋 礴
遗
璃
时同(h)
时献Min)
图6
图7
小碳化物的完全溶解,另一方面促进了大碳化物尖角的局部溶解,使钢中的碳化物形态和分布 得到改善,从而减少了模具的变形。Crl2MoV高温调质工艺如图7所示。 (三)采用二次回火。淬火加热温度在1020~1050℃范围内,将回火温度由250℃提高到400"t2, 并进行二次回火,这样模具最终硬度可达到57~58HRC,不但可以减少了模具的变形,同时可以使
临界点 温度(℃)
Acl 810
表2 膨胀系数
A∞
1200
Arl 760
温度(℃) 膨胀系数
2啦!OO
10.9x10.6
2m400
11.4x10_6
2口击00
12.2x10.6
三、Orl2MoV钢经不同温度淬火后在不同温度回火后的硬度及其金相组织
(一)Crl2MoV钢经不同温度淬火和不同温度回火后的硬度见表3。根据实验数据绘制其关系
Crl
2MoV钢冷作模具热处理后变形 与预防及工艺优化
陈显辉
(一汽红塔云南汽车制造有限公司
曲靖655000)
摘要: Crl2MoV钢是广泛用于模具行业的冷作模具钢,具有高淬透性,截面为200—
300mm以下可以完全淬透。由于该钢中存在大量碳化物,且偏析严重,因此不同 的热处理工艺对钢的性能有很大的影响。虽然Cd2MoV钢热处理后变形不是 很大,但对一些结构复杂、制造精度要求高的模具来说,Crl2MoV还存在热处 理变形问题。针对这一问题,本文从改善热处理工艺方面着手,对Crl2MoV 模具进行热处理工艺优化o 关键词: Cd2MoV热处理冷作模具钢热处理变形优化
《钢管冷拔模具磨损失效分析及再制造研究》范文

《钢管冷拔模具磨损失效分析及再制造研究》篇一一、引言钢管冷拔工艺是金属制品加工领域中一种重要的加工方法,而模具作为冷拔工艺的关键部件,其性能和寿命直接影响着生产效率和产品质量。
随着工业化进程的加速,钢管冷拔模具的磨损失效问题逐渐凸显,并成为了制约行业发展的关键因素之一。
因此,对钢管冷拔模具磨损失效进行分析,并研究其再制造技术,对于提高生产效率和产品质量、降低生产成本具有重要意义。
二、钢管冷拔模具磨损失效分析1. 磨损失效原因钢管冷拔模具的磨损失效原因主要包括以下几个方面:一是由于金属材料的硬度高、强度大,导致模具表面在冷拔过程中产生磨损;二是由于模具与钢管之间的摩擦作用,使得模具表面产生热疲劳裂纹;三是由于模具设计不合理、制造精度不足等因素,导致模具在使用过程中出现应力集中、变形等问题。
2. 磨损失效形式钢管冷拔模具的磨损失效形式主要包括磨损、断裂、热疲劳裂纹等。
其中,磨损是最常见的失效形式,表现为模具表面的划痕、凹坑等;断裂则是由模具内部应力过大或外部冲击引起的;热疲劳裂纹则是由于模具在高温下反复受热而产生的裂纹。
三、再制造技术研究针对钢管冷拔模具的磨损失效问题,再制造技术成为了一种有效的解决方案。
再制造技术是指对废旧产品进行高技术含量的修复和改造,使其性能达到或超过原产品,同时实现资源的再利用。
在钢管冷拔模具的再制造过程中,主要涉及以下技术:1. 表面处理技术表面处理技术是再制造过程中的关键技术之一。
通过喷丸、喷涂、激光熔覆等手段,对模具表面进行强化处理,提高其硬度、耐磨性和耐腐蚀性。
同时,对于已经出现磨损、划痕等缺陷的模具表面,可以采用研磨、抛光等手段进行修复。
2. 修复与改造技术对于已经断裂或出现热疲劳裂纹的模具,需要采用修复与改造技术。
首先,对断裂或裂纹部位进行清理、修补,然后采用焊接、机械加工等手段进行修复和改造。
在修复和改造过程中,需要保证模具的精度和性能达到原设计要求。
3. 优化设计技术优化设计技术是再制造过程中的重要环节。
《钢管冷拔模具磨损失效分析及再制造研究》

《钢管冷拔模具磨损失效分析及再制造研究》篇一一、引言钢管冷拔工艺中,模具的磨损失效是影响生产效率和产品质量的关键因素。
本文针对钢管冷拔模具的磨损失效问题,通过深入分析其失效机理及影响因素,探讨再制造技术的研究与应用,旨在提高模具的使用寿命和降低生产成本。
二、钢管冷拔模具磨损失效分析1. 磨损失效原因钢管冷拔模具的磨损失效主要由于机械磨损、热磨损、化学腐蚀等多种因素共同作用所致。
其中,机械磨损是导致模具失效的主要原因为,由于钢管与模具之间的摩擦力,使得模具表面产生磨损;热磨损则是由于冷拔过程中产生的热量导致模具材料热膨胀、硬度降低;化学腐蚀则是由于工作环境中的杂质、化学物质对模具的腐蚀作用。
2. 磨损失效特征钢管冷拔模具的磨损失效特征主要表现为模具表面出现划痕、裂纹、凹坑等缺陷,导致模具尺寸精度降低、表面粗糙度增大,进而影响产品的尺寸精度和表面质量。
此外,模具的磨损失效还会导致生产效率降低、成本增加。
三、再制造技术研究针对钢管冷拔模具的磨损失效问题,再制造技术是一种有效的解决方案。
再制造技术通过对失效模具进行修复、改造和优化,使其性能达到或超过原设计要求,从而实现模具的再生利用。
1. 再制造流程钢管冷拔模具的再制造流程主要包括预处理、修复、性能检测和出厂验收等步骤。
预处理阶段主要是对失效模具进行清洗、检测和评估;修复阶段则是通过机械加工、电镀、喷涂等手段对模具进行修复和改造;性能检测阶段是对修复后的模具进行性能测试,确保其达到设计要求;出厂验收阶段则是对修复后的模具进行全面检查,确保其质量符合标准。
2. 再制造技术方法针对钢管冷拔模具的再制造,常用的技术方法包括机械加工法、电镀法、喷涂法等。
机械加工法主要是通过切削、研磨等手段对模具进行修复;电镀法则是通过在模具表面镀一层金属,提高其硬度和耐磨性;喷涂法则是将特殊涂料喷涂在模具表面,形成一层保护膜,提高模具的耐腐蚀性和耐磨性。
四、结论通过对钢管冷拔模具磨损失效的分析及再制造技术的研究,我们可以得出以下结论:1. 钢管冷拔模具的磨损失效主要受机械磨损、热磨损和化学腐蚀等多种因素影响,导致模具表面出现划痕、裂纹、凹坑等缺陷。
《钢管冷拔模具磨损失效分析及再制造研究》

《钢管冷拔模具磨损失效分析及再制造研究》篇一一、引言随着现代工业的快速发展,钢管冷拔工艺在制造领域中占有重要地位。
而钢管冷拔模具作为该工艺的核心部件,其性能的稳定性和持久性直接影响到生产效率和产品质量。
然而,模具在使用过程中常常会出现磨损和失效问题,这不仅影响了生产效率,还增加了生产成本。
因此,对钢管冷拔模具磨损失效进行分析及再制造研究具有重要意义。
本文将就钢管冷拔模具的磨损失效原因、影响因素、再制造方法及再制造后性能评估等方面进行深入探讨。
二、钢管冷拔模具磨损失效原因分析1. 机械磨损:在冷拔过程中,模具表面会受到钢管与模具之间的摩擦力作用,导致模具表面材料逐渐磨损,从而影响模具的尺寸精度和形状精度。
2. 热磨损:冷拔过程中产生的摩擦热会使模具表面温度升高,导致模具材料软化,进而加剧了模具的磨损。
3. 化学腐蚀:模具在长期使用过程中,会受到工作环境中的化学物质腐蚀,使模具表面产生腐蚀坑,降低了模具的使用寿命。
三、影响钢管冷拔模具磨损失效的因素1. 材质因素:模具材质的硬度、韧性、耐磨性等性能直接影响其抗磨损能力。
2. 工艺因素:冷拔过程中的摩擦力、压力、温度等工艺参数会影响模具的磨损程度。
3. 使用环境:工作环境中的化学物质、湿度、温度等因素也会对模具的抗腐蚀性和耐磨性产生影响。
四、钢管冷拔模具再制造方法研究1. 表面强化技术:通过喷丸、激光熔覆等表面强化技术提高模具表面的硬度、耐磨性和抗腐蚀性。
2. 修复技术:采用焊接、粘接、机械加工等方法对磨损严重的模具进行修复,恢复其使用性能。
3. 优化设计:根据实际生产需求,对模具结构进行优化设计,提高其抗磨损和抗腐蚀能力。
五、再制造后性能评估1. 精度检测:通过高精度测量设备对再制造后的模具进行尺寸和形状精度检测,确保其满足生产要求。
2. 性能测试:在模拟生产环境中对再制造后的模具进行性能测试,评估其抗磨损、抗腐蚀等性能。
3. 寿命预测:根据再制造后的性能测试结果,预测模具的使用寿命,为后续生产提供参考依据。
《钢管冷拔模具磨损失效分析及再制造研究》范文

《钢管冷拔模具磨损失效分析及再制造研究》篇一一、引言钢管冷拔模具作为重要的工艺装备,广泛应用于钢管制造领域。
随着工业化进程的加速,钢管的产量和质量要求日益提高,使得冷拔模具的使用寿命和磨损失效问题成为关注的焦点。
因此,本文将对钢管冷拔模具的磨损失效原因进行分析,并探讨其再制造技术的研究与应用。
二、钢管冷拔模具磨损失效分析1. 磨损失效原因钢管冷拔模具的磨损失效主要与模具材料、使用环境、加工工艺等因素有关。
首先,模具材料的选择直接影响其耐磨性能和使用寿命。
其次,模具在使用过程中会受到温度、压力等复杂环境因素的影响,导致磨损加剧。
此外,加工工艺也会对模具的表面质量和耐磨性能产生影响。
2. 失效形式钢管冷拔模具的磨损失效形式主要包括磨损、断裂、裂纹等。
其中,磨损是最常见的失效形式,表现为模具表面的划痕、凹坑等。
这些磨损会导致模具的尺寸精度和表面质量下降,进而影响钢管的尺寸精度和表面质量。
三、再制造技术研究1. 再制造技术概述再制造技术是指将废旧产品或零部件进行修复、改造、升级等处理,使其达到或超过原产品性能的技术。
对于钢管冷拔模具而言,再制造技术可以延长模具的使用寿命,降低生产成本,减少资源浪费。
2. 再制造技术方法(1)表面强化技术:通过喷丸、激光熔覆等手段对模具表面进行处理,提高其硬度、耐磨性等性能。
(2)热处理技术:采用淬火、回火等热处理手段对模具进行改性处理,提高其整体性能。
(3)修复技术:采用焊接、粘接等手段对磨损部位进行修复,恢复其尺寸精度和表面质量。
四、再制造技术应用及效果分析1. 应用领域再制造技术广泛应用于各种钢管冷拔模具的修复和改造,包括进口模具的本土化改造、老旧模具的升级换代等。
2. 效果分析通过再制造技术的应用,可以显著提高钢管冷拔模具的使用寿命和性能。
一方面,再制造技术可以修复磨损部位,恢复模具的尺寸精度和表面质量;另一方面,通过表面强化技术和热处理技术等手段,可以提高模具的硬度、耐磨性等性能,延长其使用寿命。
模具失效及解决方法实例

模具失效及解决方法实例一、引言模具是工业生产中必不可少的工具,它能够成型出各种形状和尺寸的产品。
然而,模具在使用过程中会受到各种因素的影响,导致失效。
模具失效不仅会影响生产效率,增加生产成本,还会影响产品的质量。
因此,了解模具失效的原因和解决方法非常重要。
本文将介绍模具失效的类型、原因以及一些常见的解决方法实例。
二、模具失效类型1. 磨损:模具在使用过程中,其工作表面会与材料不断接触,导致工作表面磨损。
2. 腐蚀:模具受到化学或电化学作用,导致腐蚀损坏。
3. 塑性变形:材料在模具内塑性变形,导致模具变形。
4. 热疲劳:模具在工作过程中频繁冷热交替,导致热疲劳损坏。
5. 裂纹扩展:由于制造、使用过程中产生的裂纹在交变应力作用下扩展导致破坏。
三、模具失效原因1. 操作不当:如超负荷生产、材料硬度过高、材料中有杂质等都会导致模具过早磨损或腐蚀。
2. 维护不当:润滑不足、冷却系统不良等都会导致模具过热或腐蚀。
3. 材料问题:模具材料的选择不当,如硬度、耐腐蚀性、耐磨性等都会影响模具的使用寿命。
4. 制造问题:制造过程中的缺陷,如铸造缺陷、热处理不当等都会导致模具产生裂纹或塑性变形。
四、解决方法实例1. 磨损修复:对于磨损的模具,可以采用堆焊、喷涂等方法进行修复。
例如,对于磨损的凸轮表面,可以采用堆焊的方式进行修复,选择耐磨性好、焊前流动性好的合金堆焊焊条。
在修复过程中,需要注意控制热输入,避免热影响扩大。
同时,对于一些磨损严重的模具,还可以采用喷涂的方法进行修复,选择耐磨性好、耐腐蚀的涂层材料,如金属陶瓷、镍基涂层等。
2. 腐蚀防护:对于腐蚀的模具,可以采用镀层、表面处理等方法进行防护。
例如,对于受腐蚀的模具钢表面,可以采用镀铬或镀锌等防腐方法进行防护。
此外,还可以采用表面处理的方法提高模具表面的抗腐蚀性能,如采用氧化处理、磷化处理等。
3. 温度控制:对于塑性变形的模具,可以通过调整生产工艺、选择合适的材料等方法来降低模具工作时的温度。
冷挤压模具失效分析与提高模具寿命途径
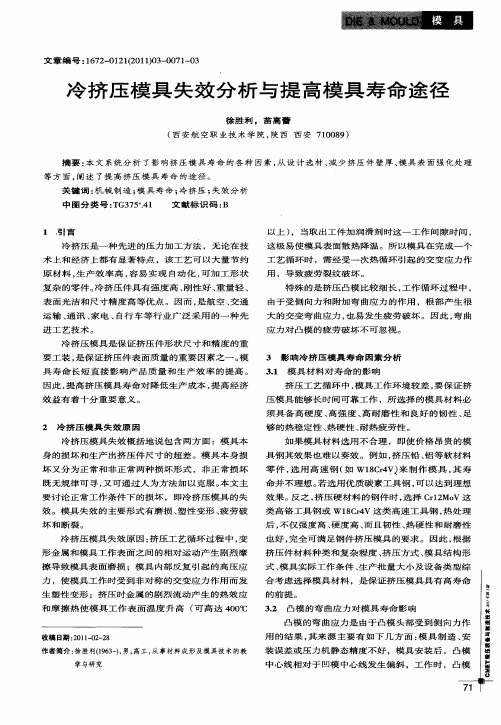
零 件 , 用 高 速 钢 ( W1 ̄a 来 制 作模 具 , 寿 选 如 8 rV ̄ 其
命 并不 理想 。 选用 优 质碳 素工具 钢 , 以达 到理想 若 可
效 果 。反 之 , 压 硬 材 料 的 钢 件 时 , 择 Cr2 V 这 挤 选 l Mo
擦 导 致 模 具 表 面 磨 损 ;模 具 内 部 反 复 引 起 的 高 压 应 力 ,使 模 具 工 作 时 受 到 非 对 称 的交 变 应 力 作 用 而 发
生 塑 性 变 形 ;挤 压 时 金 属 的 剧 烈 流 动 产 生 的 热 效 应
和摩 擦 热 使模 具 工作 表面 温度 升 高 ( 高达 40 可 0 ℃
中 图 分 类 号 : G3 5. T 7 ̄ 41 文 献标 识码 : B
1 . 言 引
以上 ) 当取 出工件 加润 滑剂 时这一 工 作 间隙 时间 , ,
冷 挤 压 是 一 种 先 进 的 压 力 加 工 方 法 ,无 论 在 技 术 上 和 经 济 上 都 有 显 著 特 点 ,该 工 艺 可 以 大 量 节 约
冷 挤 压 模 具 是 保 证 挤 压 件 形 状 尺 寸 和 精 度 的 重 要 工装 , 保证 挤压 件表 面质 量 的重要 因素 之一 。 是 模
3 影 响 冷 挤 压 模 具 寿 命 因 素 分 析
具 寿命 长 短 直 接影 响产 品 质量 和生 产 效率 的提 高 。
因 此 , 高 挤 压 模 具 寿 命 对 降 低 生 产 成 本 , 高 经 济 提 提
2 冷 挤 压 模 具 失 效 原 因
够 的热稳 定性 、 硬 性 、 热 疲劳性 。 热 耐 如 果 模 具 材 料 选 用 不 合 理 ,即 使 价 格 昂 贵 的 模 具 钢 其 效 果 也 难 以奏 效 。 例 如 , 压 铅 、 等 软 材 料 挤 铝
冷冲压模具改进设计实例分析

冷冲压模具改进设计实例分析冷冲压模具是一种用于制造金属零件的工具,它通过在金属表面施加压力使其变形,同时具备一定的冷却功能。
冷冲压模具的设计直接影响到产品的质量和生产效率。
本文将以一款汽车零部件模具为例,对其进行改进设计分析。
首先,我们需要对原有的冷冲压模具进行分析,并识别出存在的问题和改进的空间。
该模具用于制造汽车车门锁芯零件,主要问题如下:1.模具使用寿命较短:由于该模具在长时间使用后容易出现磨损,并且需要定期更换,这导致了生产效率的下降和成本的增加。
2.产品变形和尺寸不准确:由于金属材料的收缩和热变形,以及模具本身的精度问题,导致制成的零件存在一定的变形和尺寸不准确性,影响了产品的质量。
3.制造周期长:该模具需要多道工序进行制造,且每道工序之间的处理时间较长,导致整个制造周期过长,无法满足快速交付的需求。
基于以上问题,我们可以提出以下改进设计方案:1.优化材料选择:选择更耐磨、抗拉力更强的材料制作模具。
优化后的模具材料能够增加使用寿命,减少更换次数,提高生产效率和降低成本。
2.设计增加辅助冷却系统:在模具设计中增加冷却孔和冷却水道,通过冷却水的流动来降低模具温度,以减缓模具和金属材料的热变形,从而改善零件的尺寸准确性。
3.采用多道工序一体化加工:通过模具设计的一体化,将原本需要多次装配和加工的工序合并在一个模具中完成。
这样可以减少制造时间和人力资源的浪费,缩短制造周期,提高生产效率。
4.优化模具结构和形状:通过对模具结构和形状的优化,减少零件变形的可能性。
例如,采用适当的辅助结构和强度加固设计,以及减小模具开缝的尺寸,从而提高模具的准确度和稳定性。
5.引入模具设计软件和先进制造工艺:利用模具设计软件进行模拟和仿真,对模具进行优化设计。
同时,引入先进的制造工艺,如数控加工和电脉冲成型等,以确保模具的精度和稳定性。
经过以上的改进设计方案,我们预计可以得到以下改进结果:1.提高模具使用寿命:通过优化材料选择和增加冷却系统,降低模具磨损和温度变形的可能性,从而提高模具的使用寿命。
冷作模具的常见失效形式及热处理质量检验
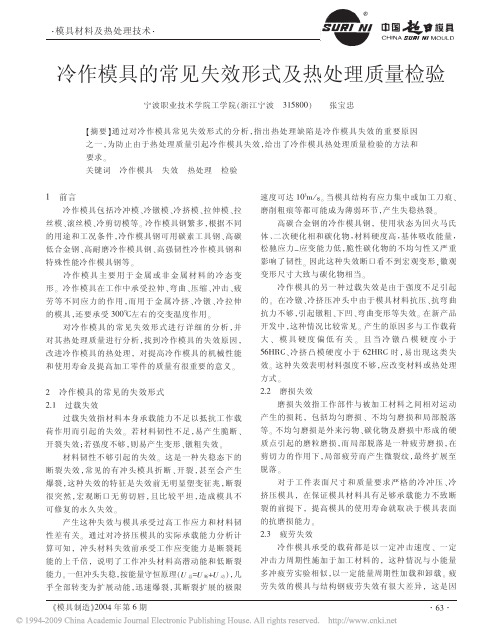
材料韧性不够引起的失效) 这是一种失稳态下的 断裂失效(常见的有冲头模具折断*开裂(甚至会产生 爆裂(这种失效的特征是失效前无明显塑变征兆(断裂 很突然(宏观断口无剪切唇(且比较平坦(造成模具不 可修复的永久失效)
产生这种失效与模具承受过高工作应力和材料韧 性差有关) 通过对冷挤压模具的实际承载能力分析计 算可知( 冲头材料失效前承受工作应变能力是断裂耗 能的上千倍( 说明了工作冲头材料高潜动能和低断裂 能力) 一但冲头失稳(按能量守恒原理$! 总+! 断,! 动%(几 乎全部转变为扩展动能(迅速爆裂(其断裂扩展的极限
冷作模具承受的载荷都是以一定冲击速度* 一定 冲击力周期性施加于加工材料的( 这种情况与小能量 多冲疲劳实验相似(以一定能量周期性加载和卸载) 疲 劳失效的模具与结构钢疲劳失效有很大差异( 这是因
!!"!
!!模具材料及热处理技术!
为脆性材料疲劳裂纹的产生周期占总寿命的绝大部 分$很多情况下产生与扩展无明显界限$似乎不存在稳 态扩展阶段% 疲劳失效实际上是应力应变下微裂纹的 产生过程$当产生约 "%&’’ 尺寸微裂纹$即可能发生瞬 间断裂% 实际应用中疲劳产生源有很多$其断口形状与 脆断极相似%
正火&退火零件的硬度用布氏试验机检查% 淬火工 件用洛氏硬度法检查% 表面硬化工件常用维氏硬度检 验法检查% 大型零件硬度测试$可用锤击式布氏&肖氏 或里氏硬度测试法检查%
关于模具使用寿命及失效问题分析
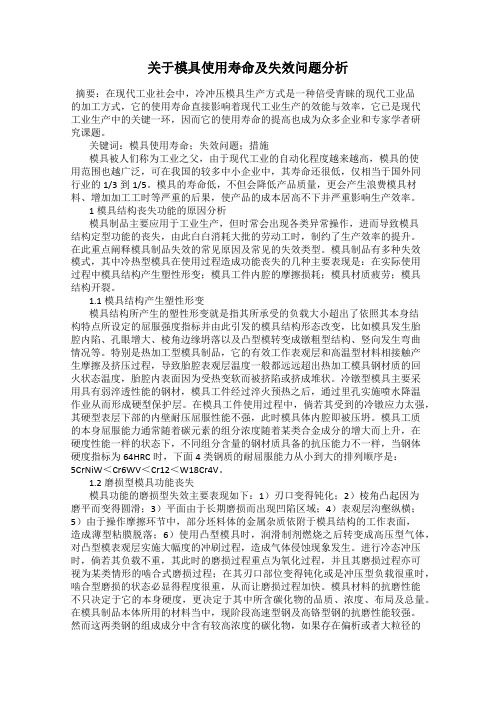
关于模具使用寿命及失效问题分析摘要:在现代工业社会中,冷冲压模具生产方式是一种倍受青睐的现代工业品的加工方式,它的使用寿命直接影响着现代工业生产的效能与效率,它已是现代工业生产中的关键一环,因而它的使用寿命的提高也成为众多企业和专家学者研究课题。
关键词:模具使用寿命;失效问题;措施模具被人们称为工业之父,由于现代工业的自动化程度越来越高,模具的使用范围也越广泛,可在我国的较多中小企业中,其寿命还很低,仅相当于国外同行业的1/3到1/5。
模具的寿命低,不但会降低产品质量,更会产生浪费模具材料、增加加工工时等严重的后果,使产品的成本居高不下并严重影响生产效率。
1模具结构丧失功能的原因分析模具制品主要应用于工业生产,但时常会出现各类异常操作,进而导致模具结构定型功能的丧失,由此白白消耗大批的劳动工时,制约了生产效率的提升。
在此重点阐释模具制品失效的常见原因及常见的失效类型。
模具制品有多种失效模式,其中冷热型模具在使用过程造成功能丧失的几种主要表现是:在实际使用过程中模具结构产生塑性形变;模具工件内腔的摩擦损耗;模具材质疲劳;模具结构开裂。
1.1模具结构产生塑性形变模具结构所产生的塑性形变就是指其所承受的负载大小超出了依照其本身结构特点所设定的屈服强度指标并由此引发的模具结构形态改变,比如模具发生胎腔内陷、孔眼增大、棱角边缘坍落以及凸型模转变成镦粗型结构、竖向发生弯曲情况等。
特别是热加工型模具制品,它的有效工作表观层和高温型材料相接触产生摩擦及挤压过程,导致胎腔表观层温度一般都远远超出热加工模具钢材质的回火状态温度,胎腔内表面因为受热变软而被挤陷或挤成堆状。
冷镦型模具主要采用具有弱淬透性能的钢材,模具工件经过淬火预热之后,通过里孔实施喷水降温作业从而形成硬型保护层。
在模具工件使用过程中,倘若其受到的冷镦应力太强,其硬型表层下部的内壁耐压屈服性能不强,此时模具体内腔即被压坍。
模具工质的本身屈服能力通常随着碳元素的组分浓度随着某类合金成分的增大而上升,在硬度性能一样的状态下,不同组分含量的钢材质具备的抗压能力不一样,当钢体硬度指标为64HRC时,下面4类钢质的耐屈服能力从小到大的排列顺序是:5CrNiW<Cr6WV<Cr12<W18Cr4V。
《钢管冷拔模具磨损失效分析及再制造研究》范文

《钢管冷拔模具磨损失效分析及再制造研究》篇一一、引言钢管冷拔工艺是金属制品加工中重要的一环,而模具作为冷拔过程中的关键设备,其磨损失效直接影响到生产效率和产品质量。
本文针对钢管冷拔模具的磨损失效问题展开分析,并提出再制造的优化策略,以期提升模具使用寿命,提高生产效益。
二、钢管冷拔模具磨损失效原因分析1. 材料因素:模具材料的选择对耐磨性有着直接的影响。
如果材料硬度不足,抗拉强度低,将容易产生磨损失效。
2. 工艺因素:冷拔过程中的润滑不良、压力控制不当、冷却不足等都会加速模具的磨损。
3. 使用环境:钢管的材质、硬度、表面粗糙度等也会对模具的磨损产生影响。
4. 维护保养:模具的定期维护保养工作不到位,如不及时清理模具内的杂质、不进行定期的润滑保养等,都会加速模具的磨损失效。
三、钢管冷拔模具再制造技术研究针对上述磨损失效原因,本文提出以下再制造技术策略:1. 材料优化:选择高硬度、高抗拉强度的模具材料,以提高其耐磨性和抗拉强度。
2. 工艺改进:优化冷拔过程中的润滑、压力控制、冷却等工艺参数,减少模具的磨损。
3. 表面处理技术:采用表面强化技术如喷丸强化、激光淬火等,提高模具表面的硬度和耐磨性。
4. 维护保养策略:制定定期的模具维护保养计划,包括清理模具内的杂质、定期润滑保养等,以延长模具的使用寿命。
四、再制造技术应用实践以某钢管生产企业为例,该企业采用高硬度合金钢制作冷拔模具,但在使用过程中仍出现磨损失效问题。
针对这一问题,企业采用了以下再制造技术措施:1. 优化材料选择:将原合金钢材料替换为更高硬度和抗拉强度的材料,提高了模具的耐磨性。
2. 工艺改进:调整冷拔过程中的润滑、压力控制、冷却等工艺参数,使模具在更好的工作环境下运行。
3. 表面处理技术应用:对模具表面进行喷丸强化和激光淬火处理,提高了模具表面的硬度和耐磨性。
4. 维护保养计划实施:制定定期的模具维护保养计划,包括每周清理模具内的杂质、每月进行润滑保养等。
冷挤压模具失效分析与提高模具寿命途径

冷挤压模具失效分析与提高模具寿命途径一、引言1.1 主题意义1.2 研究背景1.3 研究目的二、冷挤压模具失效原因2.1 金属疲劳失效2.2 粘结磨损失效2.3 温度腐蚀失效2.4 应力集中失效三、模具寿命测试与评估3.1 超声波检测3.2 电化学腐蚀测试3.3 显微镜观察四、提高模具寿命途径4.1 选用高强度材料4.2 优化模具结构设计4.3 加强模具养护管理4.4 关注生产工艺参数五、结论与展望5.1 实验结论5.2 前景展望一、引言1.1 主题意义随着冷挤压技术的不断发展,冷挤压模具的寿命成为制约生产效率和产品质量的重要因素。
冷挤压模具的常见失效形式包括金属疲劳、粘结磨损、温度腐蚀、应力集中等。
对于这些失效形式,必须采取相应的措施,提高模具的使用寿命。
1.2 研究背景冷挤压技术是一种常用的金属加工方法,广泛应用于汽车、机械、航空航天等领域。
而冷挤压模具则是实现该技术的重要工具,模具的性能和使用寿命直接影响到产品质量和生产效率。
目前,国内外的研究表明,冷挤压模具的失效主要包括金属疲劳、粘结磨损、温度腐蚀和应力集中等多种形式,这些失效的原因各异,研究其原因和有效的提高模具使用寿命的方法,对于冷挤压技术的发展至关重要。
1.3 研究目的本文主要研究冷挤压模具失效的原因和提高模具使用寿命的方法。
针对模具在使用过程中出现的金属疲劳、粘结磨损、温度腐蚀和应力集中等失效形式,对模具寿命测试与评估方法进行介绍,并提出选用高强度材料、优化设计、加强管理和关注生产工艺参数等措施,以提高模具使用寿命,降低生产成本,提高产品质量。
二、冷挤压模具失效原因2.1 金属疲劳失效金属疲劳是指金属材料在反复交替加/减载作用下发生的断裂失效现象。
在冷挤压加工中,金属疲劳导致的模具断裂常常会出现,严重影响生产效率和生产成本。
金属疲劳的原因主要包括金属内部缺陷、表面缺陷、材料及工艺性缺陷等。
这些缺陷使得模具在长时间的使用过程中失去原有的韧性和强度,从而导致疲劳断裂。
《钢管冷拔模具磨损失效分析及再制造研究》范文

《钢管冷拔模具磨损失效分析及再制造研究》篇一一、引言钢管冷拔模具作为制造工艺中的关键设备,其性能和寿命直接关系到钢管的生产效率和产品质量。
然而,随着生产过程中不断的磨损和失效,模具的再制造成为了亟待解决的问题。
本文将针对钢管冷拔模具的磨损失效原因进行深入分析,并探讨其再制造的方法与途径。
二、钢管冷拔模具磨损失效分析1. 磨损类型及原因分析钢管冷拔模具的磨损主要分为机械磨损、热磨损和化学磨损三种类型。
机械磨损主要是由于金属材料在冷拔过程中与模具表面发生摩擦所导致的;热磨损则是由于模具在高温环境下长时间工作,导致表面材料软化或熔化;化学磨损则是由于模具材料与工作环境中的化学物质发生化学反应而导致的。
2. 失效模式与影响随着磨损的加剧,模具的形状精度和尺寸精度逐渐降低,甚至出现裂纹、断裂等失效模式。
这不仅会影响到钢管的生产效率,还会增加生产成本,降低产品质量,严重时甚至可能导致生产事故的发生。
三、再制造技术研究1. 再制造的必要性鉴于冷拔模具的高昂成本和更换模具的巨大费用,对失效模具进行再制造,不仅可以降低生产成本,还能减少资源浪费,实现可持续发展。
2. 再制造方法与途径(1)表面强化技术:通过喷丸、喷涂等手段对模具表面进行处理,提高其硬度、耐磨性和耐腐蚀性。
(2)修复技术:采用激光熔覆、电火花沉积等技术对模具表面的损伤进行修复,恢复其原有的尺寸精度和形状精度。
(3)优化设计:根据实际生产需求,对模具的结构进行优化设计,提高其使用性能和寿命。
四、再制造技术应用实例分析以某钢管生产企业为例,通过对冷拔模具的再制造技术应用,实现了模具寿命的显著提升。
首先,通过对失效模具的检测和分析,确定了再制造的重点和方向;其次,采用表面强化技术和修复技术对模具进行再制造;最后,对再制造后的模具进行性能测试和生产验证。
结果表明,再制造后的模具性能和使用寿命均得到了显著提升,有效降低了生产成本,提高了生产效率。
五、结论与展望通过对钢管冷拔模具磨损失效原因的分析和再制造技术的研究,我们可以得出以下结论:再制造技术可以有效延长钢管冷拔模具的使用寿命,降低生产成本,提高生产效率;同时,再制造技术的应用还有利于实现资源的循环利用,促进可持续发展。
冷挤压模具的失效分析和提高寿命的途径 (2)

冷挤压模具的失效分析和提高寿命的途径日期: 2009-2-7 9:27:28浏览: 417来源: 学海网收集整理作者: 未知冷挤压技术具有明显的经济效益,所以自二次世界大战以来,世界各国竞相开发此项技术,我国在六十年代时期在有色金属冷挤压方面取得了很快的发展,黑色金属的冷挤压也有少量应用。
我厂八十年代末开发了冷挤压技术,从调试开始自今,经历了不少波折,克服了许多困难,取得了许多宝贵的经验,终于使冷挤压技术在火花塞壳体上获得了成功应用,使我厂自行开发的冷挤压技术领先于同行业。
本文就是根据我们的实际经验对于冷挤压模具的失效形式和提高寿命的途径谈谈自己的一些体会。
冷挤压模具的失效在冷挤压过程中,模具失效的形式主要有四种,即磨损、塑性变形、疲劳破坏和断裂,其中磨损和疲劳破坏属正常失效形式。
磨损冷挤时,由于被挤材料在模具表面激烈地流动,造成模具工作表面容易磨损,按照磨损机理的不同,冷挤压模具的磨损又分为粘着磨损、磨料磨损、疲劳磨损和腐蚀磨损。
粘着磨损由于冷挤时被挤金属在模具表面的激烈流动,所以被挤金属与凹凸模工作表面产生相对运动,于是分别构成了滑动摩擦付,当表面不平时,便会出现峰顶接触,由于接触面积小,峰顶压力很高,足以引起塑性变形,导致接触还发生粘着现象。
在相对滑动情况下,粘着点被剪切,塑性材料就会转移到另一工件表面上,于是出现粘着─剪切─再粘着的循环过程,这就形成了粘着磨损,我们的凹模芯及凹模出现的“拉毛”现象就属于此类。
引起粘着磨损的有以下几个因素:材料特性脆性材料比塑性材料的抗粘能力强。
性大的材料组成的摩擦付粘着倾向大,互容性小的材料(异种金属或晶格不相近的金属)组成的摩擦付粘着倾向力小。
从金相组织上看,多相金属比单相金属粘着倾向力小,化合物相比单相固溶体粘着倾向小。
因此,对冷挤压毛坯及模具进行表面处理来避免金属相互摩擦。
如对豆料进行磷化处理,模具涂层处理就是基于此种原理。
因此,在有条件时应对模具进行表面处理。
《2024年钢管冷拔模具磨损失效分析及再制造研究》范文

《钢管冷拔模具磨损失效分析及再制造研究》篇一一、引言钢管冷拔工艺是金属制品加工领域中常用的技术手段,其关键环节在于模具的选用与维护。
模具的磨损失效直接关系到生产效率、产品质量及企业经济效益。
因此,对钢管冷拔模具磨损失效进行分析,并探讨其再制造技术,对于提升企业的生产效益和竞争力具有重要意义。
本文将围绕钢管冷拔模具的磨损失效原因及再制造技术进行深入研究。
二、钢管冷拔模具磨损失效分析(一)磨损原因1. 材料因素:模具材料的选择直接关系到其耐磨性能。
若材料硬度不足,易导致模具在冷拔过程中磨损严重。
2. 工艺因素:冷拔过程中的摩擦热、金属流动等工艺因素对模具的磨损产生重要影响。
3. 使用环境:工作温度、润滑条件等使用环境因素也会加速模具的磨损。
(二)失效模式1. 表面划痕与凹陷:由于金属表面与模具表面摩擦,导致模具表面出现划痕和凹陷。
2. 尺寸变化:模具在长期使用过程中,因磨损导致尺寸发生变化,影响产品质量。
3. 断裂与破损:模具在承受较大压力时可能发生断裂或破损,导致模具失效。
三、再制造技术研究(一)再制造流程1. 检测与评估:对磨损的模具进行检测,评估其再制造价值及修复难度。
2. 修复与处理:采用机械加工、电镀、喷涂等技术对模具进行修复,恢复其几何尺寸和表面质量。
3. 性能测试:对修复后的模具进行性能测试,确保其满足生产要求。
(二)再制造技术手段1. 机械加工:通过车削、磨削等手段去除模具表面的磨损层,恢复其几何尺寸。
2. 电镀与喷涂:在模具表面覆盖一层耐磨、耐腐蚀的材料,提高模具的耐磨性能和抗腐蚀性能。
3. 热处理:通过淬火、回火等热处理手段提高模具材料的硬度和韧性。
四、案例分析以某钢管生产企业为例,分析其冷拔模具的磨损失效及再制造过程。
首先,通过对该企业冷拔模具的磨损情况进行调查,发现其主要磨损原因为材料硬度不足和润滑条件不佳。
针对这些问题,采用机械加工、电镀和热处理等技术手段对模具进行再制造。
冷挤压模具的失效分析

内容摘要自从我国加入WTO之后,模具产品已提升到技术装备总体水平至关重要的一个环节,其中,尤其是冷挤压模具,它是实现少、无切削加工的重要工艺装备,在现代生产加工中日益得到广泛的应用。
但在冷挤压加工时,常常遇到一些妨碍正常投产的重要问题,就是模具受到损坏,最终导致模具失效。
本文结合工厂实际的生产状况,对冷挤模具应用,冷挤模具的失效形式,以及对所产生的各种失效形式进行分析,而后找出解决的办法,提高生产效益,减少成本,使冷挤压得到广泛的应用。
关键词:冷挤压加工冷挤模具失效目录引言 (1)一、挤压的实质及方法分类 (2)(一)冷挤压加工的实质 (2)(二)冷挤压的方法分类 (2)二、冷挤压的特点 (2)(一)冷挤压的优点 (3)(二)冷挤压的缺点 (4)三、冷挤压的实现形式 (5)(一)冷挤压模具的构造及特点 (5)(二)对冷挤压模具的基本要求 (6)四、冷挤压模具的失效性 (6)(一)模具失效出现的过程 (6)(二)模具失效的形式 (7)五、冷挤模具的工作条件 (14)六、模具损坏的各种具体因素 (14)(一)模具材料的影响 (14)(二)模具结构的影响 (15)(三)模具制造工艺的影响 (16)七、模具工作条件和使用维护的影响 (17)(一)被加工材料的影响 (17)(二)润滑条件的影响 (18)参考文献 (19)致谢 (20)冷挤压模具的失效性分析冷挤压加工的发展在初期是极其缓慢的,长期以来一直局限于铅和锡等几种较软的金属材料。
18世纪末,法国人首先成功地冷挤压出铅棒。
直到19世纪20世纪初,才开始应用于锌,锡,纯铜,无氧铜及黄铜等,如冷挤压生产锡制牙膏管,英国于1886年开始运用于冷挤压加工,某一工厂先从加工软金属开始,后来逐步实现冷挤压比较坚硬的有色金属,如锌,铝,铜极其合金。
1903年美国运用冷挤压制成薄壁黄铜管,随后,又采用预制成杯形坯料,然后再用正挤压的方法,成功地制成深孔杯形件,第一次世界大战期间,美国军火商采用这种挤压方法大批量生产黄铜弹壳,第一次世界大战后,德国用冷挤压方法可成批生产纯铝和纯锌电容器外壳等各种有色金属器件。
《钢管冷拔模具磨损失效分析及再制造研究》

《钢管冷拔模具磨损失效分析及再制造研究》篇一一、引言钢管冷拔工艺中,模具的磨损失效是影响生产效率和产品质量的关键因素。
本文旨在分析钢管冷拔模具的磨损失效原因,探讨其再制造的可行性和方法,以期提高模具的使用寿命和降低生产成本。
二、钢管冷拔模具的磨损失效分析(一)磨损原因1. 材料因素:模具材料的选择和使用性能对磨损程度有很大影响。
如硬度、强度、耐磨性等不足,易导致模具磨损。
2. 工艺因素:冷拔过程中,钢管与模具之间的摩擦、挤压、剪切等作用,使模具表面产生磨损。
此外,冷拔速度、温度、压力等工艺参数也会影响模具的磨损程度。
3. 使用环境:模具在恶劣的工作环境中长期使用,如高温、腐蚀性介质等,会加速模具的磨损和失效。
(二)失效模式1. 表面划痕:由于钢管表面存在杂质或划痕,导致模具表面产生划痕。
2. 裂纹与断裂:模具在承受较大压力和摩擦力时,易产生裂纹和断裂。
3. 塑性变形:模具在高温和高压下长期工作,易发生塑性变形,导致模具尺寸精度降低。
三、再制造方法研究(一)修复技术1. 机械修复:采用车削、研磨等方法去除模具表面的磨损层,恢复其几何形状和尺寸精度。
2. 电化学修复:利用电化学原理,对模具表面进行修复,可实现局部修复和整体修复。
3. 激光熔覆:利用激光熔覆技术,在模具表面覆盖一层具有高硬度、高耐磨性的合金材料,提高模具的耐磨性和使用寿命。
(二)强化处理1. 表面淬火:通过表面淬火处理,提高模具表面的硬度和耐磨性。
2. 渗碳淬火:将碳元素渗入模具表面,提高其硬度和耐磨性。
3. 镀层处理:在模具表面镀上一层具有防腐蚀、耐磨等性能的金属或非金属材料,提高模具的使用寿命。
四、再制造后的性能评估与优化策略(一)性能评估通过对再制造后的模具进行性能测试和实际使用情况观察,评估其耐磨性、硬度、强度等性能指标是否达到预期要求。
(二)优化策略根据性能评估结果,对再制造过程中的工艺参数、材料选择等进行优化,以提高再制造效率和效果。
模具失效的原因及预防措施
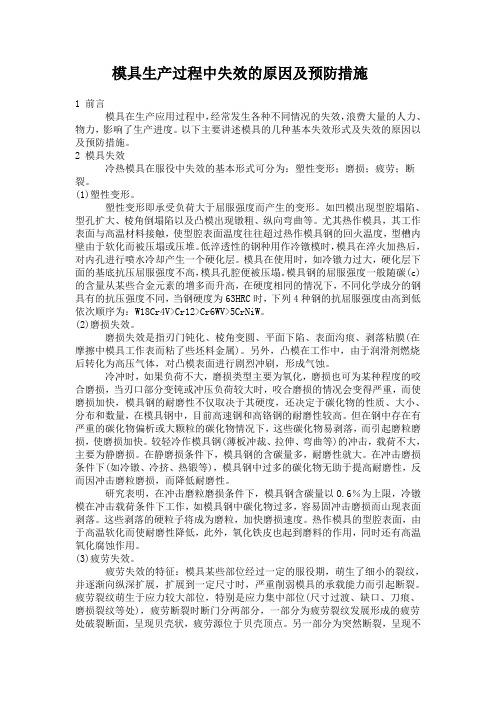
模具生产过程中失效的原因及预防措施1 前言模具在生产应用过程中,经常发生各种不同情况的失效,浪费大量的人力、物力,影响了生产进度。
以下主要讲述模具的几种基本失效形式及失效的原因以及预防措施。
2 模具失效冷热模具在服役中失效的基本形式可分为:塑性变形;磨损;疲劳;断裂。
(1)塑性变形。
塑性变形即承受负荷大于屈服强度而产生的变形。
如凹模出现型腔塌陷、型孔扩大、棱角倒塌陷以及凸模出现镦粗、纵向弯曲等。
尤其热作模具,其工作表面与高温材料接触,使型腔表面温度往往超过热作模具钢的回火温度,型槽内壁由于软化而被压塌或压堆。
低淬透性的钢种用作冷镦模时,模具在淬火加热后,对内孔进行喷水冷却产生一个硬化层。
模具在使用时,如冷镦力过大,硬化层下面的基底抗压屈服强度不高,模具孔腔便被压塌。
模具钢的屈服强度一般随碳(c)的含量从某些合金元素的增多而升高,在硬度相同的情况下,不同化学成分的钢具有的抗压强度不同,当钢硬度为63HRC时,下列4种钢的抗屈服强度由高到低依次顺序为:W18Cr4V>Cr12>Cr6WV>5CrNiW。
(2)磨损失效。
磨损失效是指刃门钝化、棱角变圆、平面下陷、表面沟痕、剥落粘膜(在摩擦中模具工作表而粘了些坯料金属)。
另外,凸模在工作中,由于润滑剂燃烧后转化为高压气体,对凸模表面进行剧烈冲刷,形成气蚀。
冷冲时,如果负荷不大,磨损类型主要为氧化,磨损也可为某种程度的咬合磨损,当刃口部分变钝或冲压负荷较大时,咬合磨损的情况会变得严重,而使磨损加快,模具钢的耐磨性不仅取决于其硬度,还决定于碳化物的性质、大小、分布和数量,在模具钢中,目前高速钢和高铬钢的耐磨性较高。
但在钢中存在有严重的碳化物偏析或大颗粒的碳化物情况下,这些碳化物易剥落,而引起磨粒磨损,使磨损加快。
较轻冷作模具钢(薄板冲裁、拉伸、弯曲等)的冲击,载荷不大,主要为静磨损。
在静磨损条件下,模具钢的含碳量多,耐磨性就大。
在冲击磨损条件下(如冷镦、冷挤、热锻等),模具钢中过多的碳化物无助于提高耐磨性,反而因冲击磨粒磨损,而降低耐磨性。
冷挤压模具损坏的分析
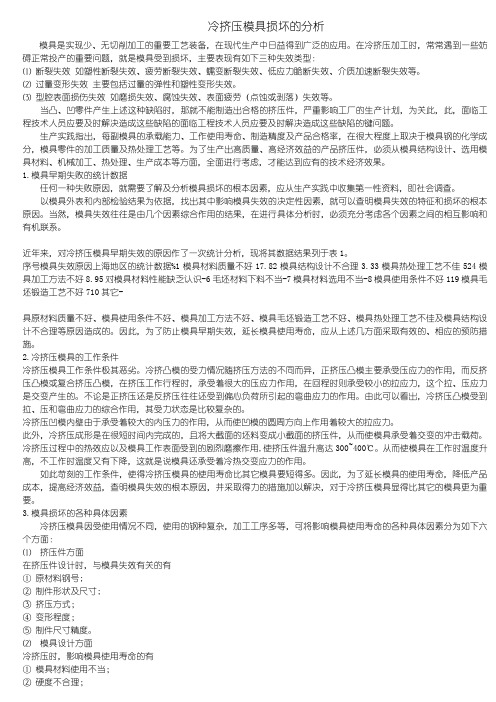
冷挤压模具损坏的分析模具是实现少、无切削加工的重要工艺装备,在现代生产中日益得到广泛的应用。
在冷挤压加工时,常常遇到一些妨碍正常投产的重要问题,就是模具受到损坏,主要表现有如下三种失效类型:⑴断裂失效如塑性断裂失效、疲劳断裂失效、蠕变断裂失效、低应力脆断失效、介质加速断裂失效等。
⑵过量变形失效主要包括过量的弹性和塑性变形失效。
⑶型腔表面损伤失效如磨损失效、腐蚀失效、表面疲劳(点蚀或剥落)失效等。
当凸、凹零件产生上述这种缺陷时,那就不能制造出合格的挤压件,严重影响工厂的生产计划,为关此,此,面临工程技术人员应要及时解决造成这些缺陷的面临工程技术人员应要及时解决造成这些缺陷的键问题。
生产实践指出,每副模具的承载能力、工作使用寿命、制造精度及产品合格率,在很大程度上取决于模具钢的化学成分,模具零件的加工质量及热处理工艺等。
为了生产出高质量、高经济效益的产品挤压件,必须从模具结构设计、选用模具材料、机械加工、热处理、生产成本等方面,全面进行考虑,才能达到应有的技术经济效果。
1.模具早期失败的统计数据任何一种失败原因,就需要了解及分析模具损坏的根本因素,应从生产实践中收集第一性资料,即社会调查。
以模具外表和内部检验结果为依据,找出其中影响模具失效的决定性因素,就可以查明模具失效的特征和损坏的根本原因。
当然,模具失效往往是由几个因素综合作用的结果,在进行具体分析时,必须充分考虑各个因素之间的相互影响和有机联系。
近年来,对冷挤压模具早期失效的原因作了一次统计分析,现将其数据结果列于表1。
序号模具失效原因上海地区的统计数据%1模具材料质量不好17.82模具结构设计不合理3.33模具热处理工艺不佳524模具加工方法不好8.95对模具材料性能缺乏认识-6毛坯材料下料不当-7模具材料选用不当-8模具使用条件不好119模具毛坯锻造工艺不好710其它-具原材料质量不好、模具使用条件不好、模具加工方法不好、模具毛坯锻造工艺不好、模具热处理工艺不佳及模具结构设计不合理等原因造成的。
- 1、下载文档前请自行甄别文档内容的完整性,平台不提供额外的编辑、内容补充、找答案等附加服务。
- 2、"仅部分预览"的文档,不可在线预览部分如存在完整性等问题,可反馈申请退款(可完整预览的文档不适用该条件!)。
- 3、如文档侵犯您的权益,请联系客服反馈,我们会尽快为您处理(人工客服工作时间:9:00-18:30)。
冷作模具失效分析及优化对策
摘要:冷作模具失效是冷作模具常见质量问题,不仅会影响冷作模具使用性能的良好性,而且还会缩短模具使用寿命,同时也会增大生产加工成本,不利于零件加工的高质量、高效率、低成本完成,所以,就需要采取有效优化对策,避免出现冷作模具失效现象,确保其应用价值和作用的充分发挥。
文章对几种常见的冷作模具失效类型及具体进行了详细分析,提出了几条预防冷作模具失效的合理化对策,具有一定的借鉴和参考价值。
关键词:冷作模具;失效类型;失效原因;优化对策
冷冲压模、冷挤压模和冷镦模,是应用最为广泛的冷作模具,任何一种冷作模具的工作条件都比较恶劣,模具受力情况复杂,在多种应力的长期作用下,冷作模具内部的组织结构便会发生变化,出现多种组织损伤,进而造成冷作做模具失效,影响零件生产的顺利进行。
为了减少冷作模具失效现象,改良其结构性能,延长其使用寿命,就需要从模具设计及加工等环节入手,做好冷作模具失效预防措施。
1.冷作模具失效类型及原因
1.1断裂失效及原因
断裂失效主要是冷作模具在使用过程中,因其表面出现裂纹或者破损所造成的一种失效现象,常见于冷挤压模和冷镦模中,分别表现为脆断和开裂脆断或掉块,凸凹膜破裂、刃口崩刃、冲头折断都属于断裂失效中比较典型的情况。
冷作模具断裂失效与制作材质有着直接的关系,当材质强度和韧度达不到标准时,便会出现断裂失效现象。
对于冷挤压模和冷镦模来讲,在对金属零件塑形过程中,其表面温度会因为挤压受力而迅速升高,容易产生疲劳裂纹,引发断裂失效现象[1]。
1.2磨损失效及原因
冷作模具在运行过程中,工作部件与被加工材料处于不断摩擦状态,长时间下去便会造成磨损失效。
冷作模具常见磨损形式主要有均匀磨损、不均匀磨损、局部脱落等,在冲压模中出现几率较高,而冷挤压模和冷镦模中的磨损失效,主要出现在模具型腔位置。
冷作模具磨损是一种必然现象,如果模具工作部件与被加工材料之间的摩擦状态比较稳定,则属于正常磨损,这种磨损与模具材料的抗磨损性能有关;如果模具在局部高压高温状态下,与被加工材料摩擦,便会出现非正常摩擦,两者之间活发生咬合现象,在加工零件表面留下划痕等缺陷。
1.3变形失效及原因
变形失效属于一种比较严重的冷作模具失效现象,如图1所示,会对其结构造成不可修复的损坏,模具弯曲、型腔凹陷、凸模镦粗、模孔胀大等,都属于典型的变形失效。
当模具抗弯强度较小时,会出现弯曲变形失效;而模具所受应力较高,大于其屈服强度时,也会发生变形失效;当模具所受压压力超过材料的抗压极限时,会出现凸模镦粗变形失效;当模具材料硬度较小时,也容易出现变形失效。
2.预防冷作模具失效的优化对策
要想避免冷作模具出现失效现象,就需要在了解其失效类型及原因的基础上,采取必要的优化对策,对其进行预防。
2.1优化设计形式
受力不复杂是造成冷作模具失效的一种主要原因,这就需要对其设计形式进行优化,使外部荷载能够科学的分布在整个模具上,来提高其强度和韧性。
一方面,冷作模模具过渡部位,应优先设计为圆角形式,避免因尖角形式造成应力集中于某一点,超过材质荷载极限而引起模具失效,比如冷镦模的凹模入口处。
应另一方面,应该在确保冷作模具结构刚度达标的基础上,尽可能的设计为镶块形式,各个部件之间用最简单的方式组合在一起,对于冲裁模来讲,应控制好凸凹模之间的间隔[2]。
2.2科学选择材质
材料也是引起冷作模具失效的主要因素之一。
一般情况下,在选择模具材料的时候,是按照碳素工具钢、高碳低合金钢、高合金钢、高速钢的顺利进行的,但是,在实际选择的过程中,需要对冷作模具的受力情况、制作成本、使用要求、性能参数、使用条件等进行综合分析,选择最为合适的材质。
比如,对于冷镦模来讲,在运行使用过程中,其凹模会长时间受到较大压力冲击,需使用强度较大、韧性较强、耐磨性能较好的高合金钢。
2.3严格控制加工
加工工艺也会对冷作模具的使用寿命造成影响。
在将加工过程中,应使模具表面足够粗糙,以便将其表面的细小裂纹加以消除。
同时,在通电加工作业时应进行差额补偿,使电能供应间隔固定的时间,保持导导轮匀速转动,以高精度完成冷作模具加工。
另外,完成通电加工作业后,进行回火处理,避免出现应力效应引起的裂缝现象。
2.4采取热处理措施
对冷作模具进行热处理,可以有效提升其使用性能、延长其使用寿命,在预防模具失效方面发挥了重要作用。
在对冷作模具进行热处理时,应根据加工条件及加工要求,选择最为合适的淬火方法,并严格控制好淬火温度、时间、回火次数等,避免因淬火温度过高引起早期断裂,避免因淬火温度较低降低其硬度和耐磨性能。
同时,为了确保冷作模具硬度及韧性都满足使用要求,在进行热处理时,需对其表面进行保护处理,以此来提高其硬度及韧性,延长其使用寿命。
3.总结
冷作模具失效既会降低其应用性能,又不利于零件加工的顺利完成,同时还会增加模具维修维护成本,造成众多不利影响。
通过对冷作模具常见失效类型和具体原因进行分析,采取优化设计、科学选材、控制加工、热处理等措施,实现对冷作模具的优化,降低模具失效现象的发生几率,进而才能提高冷作模具的质量及性能,为零件加工的顺利完成提供坚实保障。
参考文献:
[1]丁海,于汇泳,程芳.压铸模具的失效分析及寿命提高措施[J].铸造技术,2013,(3):308-310.
[2]赵璐.冷冲模具失效原因分析与对[J].工程技术:文摘版,2016,(11):291-291.。