包钢炼钢厂连铸自动加渣控制系统应用
DCS系统在钢铁行业中的应用案例分享
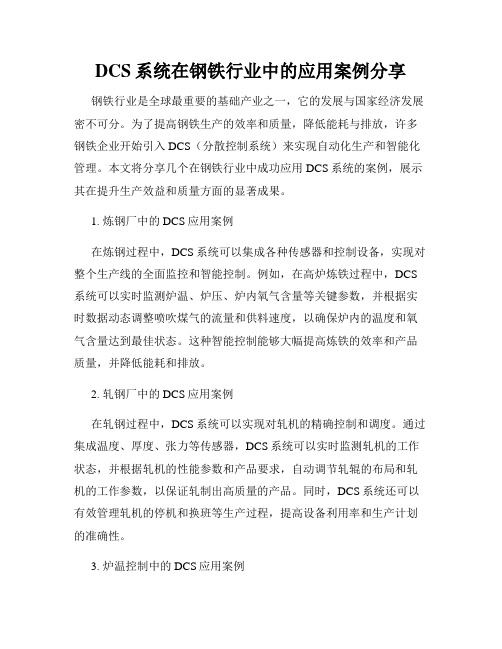
DCS系统在钢铁行业中的应用案例分享钢铁行业是全球最重要的基础产业之一,它的发展与国家经济发展密不可分。
为了提高钢铁生产的效率和质量,降低能耗与排放,许多钢铁企业开始引入DCS(分散控制系统)来实现自动化生产和智能化管理。
本文将分享几个在钢铁行业中成功应用DCS系统的案例,展示其在提升生产效益和质量方面的显著成果。
1. 炼钢厂中的DCS应用案例在炼钢过程中,DCS系统可以集成各种传感器和控制设备,实现对整个生产线的全面监控和智能控制。
例如,在高炉炼铁过程中,DCS 系统可以实时监测炉温、炉压、炉内氧气含量等关键参数,并根据实时数据动态调整喷吹煤气的流量和供料速度,以确保炉内的温度和氧气含量达到最佳状态。
这种智能控制能够大幅提高炼铁的效率和产品质量,并降低能耗和排放。
2. 轧钢厂中的DCS应用案例在轧钢过程中,DCS系统可以实现对轧机的精确控制和调度。
通过集成温度、厚度、张力等传感器,DCS系统可以实时监测轧机的工作状态,并根据轧机的性能参数和产品要求,自动调节轧辊的布局和轧机的工作参数,以保证轧制出高质量的产品。
同时,DCS系统还可以有效管理轧机的停机和换班等生产过程,提高设备利用率和生产计划的准确性。
3. 炉温控制中的DCS应用案例炉温是钢铁生产中非常重要的参数,它直接影响到钢材的质量和生产效益。
DCS系统在炉温控制中的应用可以帮助钢铁企业实现更加精确和稳定的温度控制。
通过采集炉温数据和环境数据,DCS系统可以根据事先设定的温度曲线,自动调节燃烧系统、送风系统等设备的工作参数,以实现最佳的炉温控制效果。
这种智能化控制不仅提高了产品的一致性和质量稳定性,还减少了人工干预和能耗浪费。
总结:DCS系统在钢铁行业中的应用案例丰富多样,从炼钢到轧钢,从生产线的控制到炉温的调节,都能发挥重要作用。
通过引入DCS系统,钢铁企业可以实现生产过程的智能化和自动化,提高生产效率,降低能耗和排放,提升产品质量稳定性和一致性。
钢铁冶炼中精益生产管理的运用-生产管理论文-管理学论文
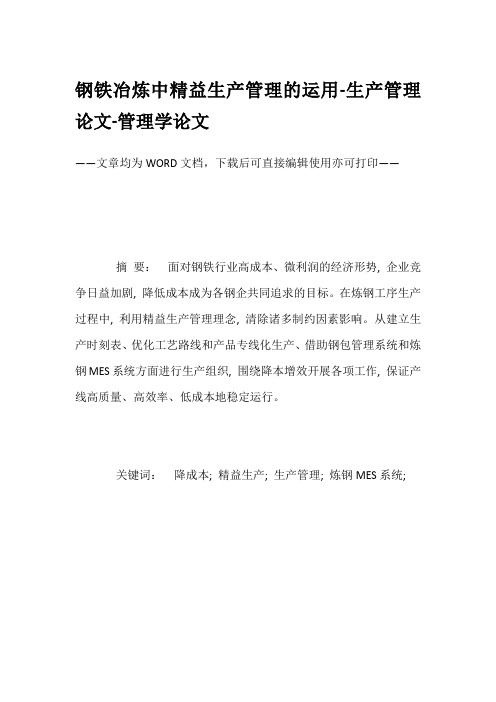
钢铁冶炼中精益生产管理的运用-生产管理论文-管理学论文——文章均为WORD文档,下载后可直接编辑使用亦可打印——摘要:面对钢铁行业高成本、微利润的经济形势, 企业竞争日益加剧, 降低成本成为各钢企共同追求的目标。
在炼钢工序生产过程中, 利用精益生产管理理念, 清除诸多制约因素影响。
从建立生产时刻表、优化工艺路线和产品专线化生产、借助钢包管理系统和炼钢MES系统方面进行生产组织, 围绕降本增效开展各项工作, 保证产线高质量、高效率、低成本地稳定运行。
关键词:降成本; 精益生产; 生产管理; 炼钢MES系统;Abstract:In the face of high cost and micro profit economic situation in iron and steel industry, the competition of enterprises is intensified and the reduction of the cost has become the common goal for the steelmaking companies.In the steelmaking production process, the lean production management concept is used to clear the influence of many constraint factors.Through the establishment of the production schedule, the optimization of process routes and product dedicated production, and the help of ladle management system and MES system for steelmaking production organization etc, various works were focused on the cost decreasing and benefit increasing to ensure the stable operation of the production line of high quality, high efficiency and low cost.Keyword:reducing costs; lean production; production management; MES system for steelmaking;在竞争激烈的市场环境下, 高效率低成本生产、提高产品质量和客户满意度成为钢铁企业提高竞争力的重要手段。
连铸加保护渣机器人系统研究与应用

连铸加保护渣机器人系统研究与应用发布时间:2022-09-13T02:20:10.874Z 来源:《科学与技术》2022年第5月9期作者:金盾[导读] 连铸加保护渣技术是钢铁冶金铸坯质量影响关键技术,生产过程中加保护渣以“少加、勤加、均匀加”为宜金盾湖南镭目科技有限公司机器人事业部,湖南长沙 410100摘要:连铸加保护渣技术是钢铁冶金铸坯质量影响关键技术,生产过程中加保护渣以“少加、勤加、均匀加”为宜。
传统的依靠人工加入保护渣方式很难满足工艺生产要求。
针对目前连铸加保护渣存在的问题,设计加保护渣机器人系统,实现向结晶器内加保护渣勤加、少加、均匀加的目标以及系统与工艺控制匹配性、系统可控性的效果。
文章详细介绍了系统设计思路,工作原理、系统组成、系统工艺流程和控制特点等。
系统通过投入铸坯生产大量实践,综合试验结果研究表明,连铸加保护渣机器人系统能够满足铺渣分布全面,渣厚均匀原则,该系统应用后保护渣厚均匀,铸坯表面质量无明显缺陷,测得的加渣量与理论计算量偏差小,铸机漏钢报警率明显降低。
关键词:连铸机;自动加渣;铸坯质量;结晶器;机器人1 概述连铸加保护渣是钢铁冶金铸坯质量影响关键技术,保护渣有防止钢液二次氧化、液面绝热保温、溶解吸收液面夹杂物、改善铸坯与结晶器界面润滑、控制铸坯与结晶器壁热传递等功能。
通过不断向连铸机结晶器内的液面加入保护渣,使其受热融化后在钢水液面上形成固渣层、烧结层、液渣层的三层渣结构。
液态渣不断流入结晶器与初生坯壳的间隙中,从而达到绝热保温、防止钢水二次氧化、润滑铸坯、减少铸坯与结晶器铜面粘结,降低黏结漏钢事故发生。
连铸工序的顺行和连铸生产质量效率的提高均与保护渣添加密切相关。
除保护渣的理化性能直接影响上述功能的发挥外,保护渣的加入方式及与生产工艺匹配更与铸坯质量紧密相关。
结晶器加保护渣的方式主要有人工手动推渣和机器自动加渣两种方式。
人工加渣随机性大,保护渣加入量及加入时间、频率由工人经验判断,结晶器内渣料消耗不稳定,渣层厚度不均,极易造成铸坯表面质量缺陷甚至粘结漏钢事故发生。
工业机器人在连铸系统中的应用

墓 裟
送 渣 振 动 交 流 电机I
均匀加是添加保护渣的一条重要 原则 。人工 添加保护 渣 时受操作者因素 的影响较 大 , 很难 保证 添加 的稳 定性 和 均匀性 。自动加渣 可 以有 效避 免这 些 问题 , 实现 均匀 加 渣, 这对 于宽板 坯连 铸生 产是 非常 重要 的。湖南 镭 目科
图 1 系 统 控 制 原 理 框 图
保 护渣 , 以满足系统加渣需求 。送 渣软管将料 仓 出 口与加渣装 置入 口连接起来 , 形 成一个 可弯 曲的保 护渣通 道 , 使 保 护渣顺 畅地落人加渣装置 的入渣 口。加渣 装置采 用螺旋 式 弹性定 量
装置 , 由伺 服 电机 驱 动 。弹 性 定 量 螺 旋 轴 能 有 效 减 少 颗 粒 保 护 渣被碾碎的现象 , 从 而 更 好 地 保 证 颗 粒 渣 的效 果 。 ( 4 )安 全 防 护 装 置 。该装 置 主 要 包 括 激 光 扫 描 仪 和 现 场 护 罩 。机 器 人 自 动加渣系统在行走 、 加渣 过程 中, 需 要 对 设 备 附 近 区 域 进 行 安
定量加渣装置将保护渣从料仓散 布到连铸结 晶器 内, 其特点是 系统 自动化程度高 , 操作 简便 , 加渣均匀 , 运行安全可靠 。
1 机 器 人 加 渣 系统 的 工 作 原 理 、 设 备 组成 及 技 术 参 数
工作原理 : 机 器 人 自动 加 渣 系 统 以 P L C为控制 中心 , 接 收
杨 龙胜 陆洪 周 倪 涛 郑 直。
( 1 . 沙 钢集 团宏 发炼 钢厂 一车 间 , 江苏 苏州 2 1 5 6 0 0 ; 2 . 湖南 镭 目科技 有 限公 司 , 湖南 长沙 4 1 0 1 0 0 )
智能化控制在钢铁冶炼中的应用

智能化控制在钢铁冶炼中的应用随着社会的进步和科技的发展,智能化控制越来越多的应用于工业制造中。
钢铁冶炼作为重要的制造产业,也逐渐掌握了智能化控制技术,并取得了良好的效果。
那么智能化控制技术在钢铁冶炼中的应用有哪些呢?一、智能化控制在炼钢中的应用1. 炼钢中的智能化控制技术智能化控制技术在炼钢过程中主要应用于炉料配料系统、炉外预处理系统、炉内自动控制系统、炉外回收系统等方面。
其中,炉料配料系统常采用智能化配料系统,该系统可以根据钢种、生产工艺和炉子的情况进行智能化控制,实现了炼钢生产的自动化和智能化。
2. 智能化控制技术的优势智能化控制技术在炼钢过程中具有控制精确、效率高、稳定性好、自动化程度高等诸多优势。
通过智能化控制技术,可以实现炼钢生产过程的智能化和高效化,大大提高了钢铁冶炼的生产效率和质量水平。
二、智能化控制在炼铁中的应用1. 炼铁中的智能化控制技术智能化控制技术在炼铁过程中主要应用于生铁制备系统、高炉自动控制系统、脱硫脱磷系统等方面。
其中,高炉自动控制系统采用智能化控制技术可以实现高炉自动调控,全面保证了高炉的正常运行和生产效率。
2. 智能化控制技术的优势智能化控制技术在炼铁过程中具有控制精确、效率高、稳定性好、自动化程度高等诸多优势。
通过智能化控制技术,可以实现炼铁生产过程的智能化和高效化,大大提高了钢铁冶炼的生产效率和质量水平。
三、智能化控制技术的未来智能化控制技术的发展前景十分广阔,未来可能应用于更多的制造领域中,包括汽车制造、机械制造、航空制造等。
在钢铁冶炼领域,智能化控制技术也将会在生产工艺、工作环境、设备维护等方面发挥更加重要的作用。
因此,智能化技术的掌握和应用将成为钢铁制造企业提高生产效率和质量水平的关键。
总之,智能化控制技术正在为钢铁冶炼领域带来新的机遇和挑战。
通过持续的技术创新和实践,钢铁制造企业将能够更加高效地进行生产,为现代工业的发展做出更大的贡献。
炼钢厂连铸自动化控制探讨
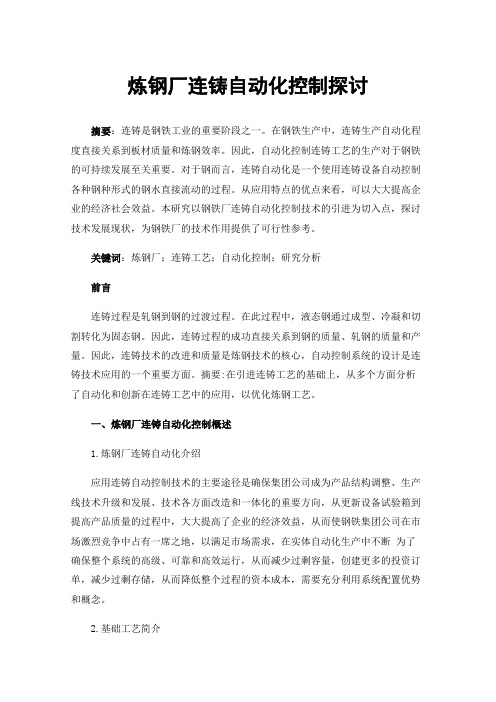
炼钢厂连铸自动化控制探讨摘要:连铸是钢铁工业的重要阶段之一。
在钢铁生产中,连铸生产自动化程度直接关系到板材质量和炼钢效率。
因此,自动化控制连铸工艺的生产对于钢铁的可持续发展至关重要。
对于钢而言,连铸自动化是一个使用连铸设备自动控制各种钢种形式的钢水直接流动的过程。
从应用特点的优点来看,可以大大提高企业的经济社会效益。
本研究以钢铁厂连铸自动化控制技术的引进为切入点,探讨技术发展现状,为钢铁厂的技术作用提供了可行性参考。
关键词:炼钢厂;连铸工艺;自动化控制;研究分析前言连铸过程是轧钢到钢的过渡过程。
在此过程中,液态钢通过成型、冷凝和切割转化为固态钢。
因此,连铸过程的成功直接关系到钢的质量、轧钢的质量和产量。
因此,连铸技术的改进和质量是炼钢技术的核心,自动控制系统的设计是连铸技术应用的一个重要方面。
摘要:在引进连铸工艺的基础上,从多个方面分析了自动化和创新在连铸工艺中的应用,以优化炼钢工艺。
一、炼钢厂连铸自动化控制概述1.炼钢厂连铸自动化介绍应用连铸自动控制技术的主要途径是确保集团公司成为产品结构调整、生产线技术升级和发展、技术各方面改造和一体化的重要方向,从更新设备试验箱到提高产品质量的过程中,大大提高了企业的经济效益,从而使钢铁集团公司在市场激烈竞争中占有一席之地,以满足市场需求,在实体自动化生产中不断为了确保整个系统的高级、可靠和高效运行,从而减少过剩容量,创建更多的投资订单,减少过剩存储,从而降低整个过程的资本成本,需要充分利用系统配置优势和概念。
2.基础工艺简介为了调整产品结构,进一步提高产品质量,钢铁在设备升级链中采用连铸自动控制流技术更新现有技术,以提高经济效益,作为技术升级、响应的现状作为当前生产的一部分,钢铁使自动化配置成为系统可靠性和进展的一个条件。
在系统的合理配置和功能配置方面,它具有明显显着的应用优势,有助于避免产能过剩,节约成本,建设和谐社会。
在设计应用阶段,将坯连铸机生产线作为生产线系统控制设备的基本控制领域,采用自动控制技术作为系统的基本结构,从而实现了其在自动控制中的生产要求。
炼钢厂连铸工艺操作流程
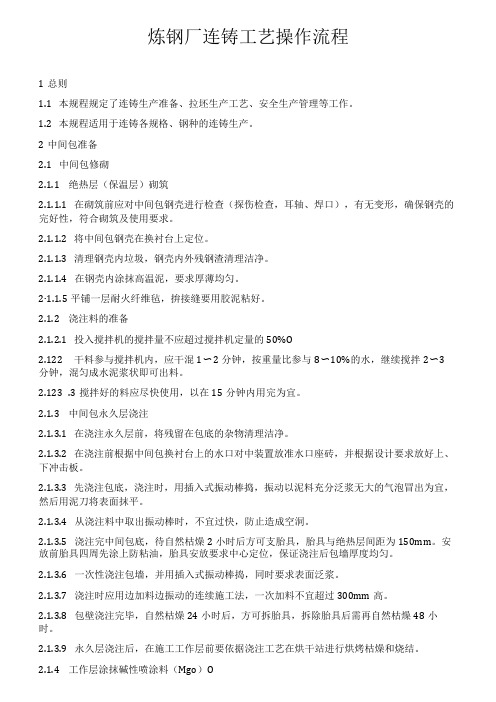
炼钢厂连铸工艺操作流程1总则1.1本规程规定了连铸生产准备、拉坯生产工艺、安全生产管理等工作。
1.2本规程适用于连铸各规格、钢种的连铸生产。
2中间包准备2.1中间包修砌2.1.1绝热层(保温层)砌筑2.1.1.1在砌筑前应对中间包钢壳进行检查(探伤检查,耳轴、焊口),有无变形,确保钢壳的完好性,符合砌筑及使用要求。
2.1.1.2将中间包钢壳在换衬台上定位。
2.1.1.3清理钢壳内垃圾,钢壳内外残钢渣清理洁净。
2.1.1.4在钢壳内涂抹高温泥,要求厚薄均匀。
2∙1.1.5平铺一层耐火纤维毡,拚接缝要用胶泥粘好。
2.1.2浇注料的准备2.1.2.1投入搅拌机的搅拌量不应超过搅拌机定量的50%O2.122干料参与搅拌机内,应干混1〜2分钟,按重量比参与8〜10%的水,继续搅拌2〜3分钟,混匀成水泥浆状即可出料。
2.123.3搅拌好的料应尽快使用,以在15分钟内用完为宜。
2.1.3中间包永久层浇注2.1.3.1在浇注永久层前,将残留在包底的杂物清理洁净。
2.1.3.2在浇注前根据中间包换衬台上的水口对中装置放准水口座砖,并根据设计要求放好上、下冲击板。
2.1.3.3先浇注包底,浇注时,用插入式振动棒捣,振动以泥料充分泛浆无大的气泡冒出为宜,然后用泥刀将表面抹平。
2.1.3.4从浇注料中取出振动棒时,不宜过快,防止造成空洞。
2.1.3.5浇注完中间包底,待自然枯燥2小时后方可支胎具,胎具与绝热层间距为150mm。
安放前胎具四周先涂上防粘油,胎具安放要求中心定位,保证浇注后包墙厚度均匀。
2.1.3.6一次性浇注包墙,并用插入式振动棒捣,同时要求表面泛浆。
2.1.3.7浇注时应用边加料边振动的连续施工法,一次加料不宜超过300mm高。
2.1.3.8包壁浇注完毕,自然枯燥24小时后,方可拆胎具,拆除胎具后需再自然枯燥48小时。
2.1.3.9永久层浇注后,在施工工作层前要依据浇注工艺在烘干站进行烘烤枯燥和烧结。
2.1.4工作层涂抹碱性喷涂料(Mgo)O1.1.1.1中间包内倒入干式料,用木板或其他工具刮平,厚度大于30mm,小于冲击板厚度20mm;在中间包烘烤器外表均匀涂一层石墨,将其放入中间包内,调整其位置,使其与冲击板下口吻合,并且与中间包四周的间距保持一致,大约30mm。
包钢生产实习之炼铁厂 炼钢厂 轨梁厂 薄板连铸厂具体报告

包钢生产实习报告目录引言 (2)1 炼铁厂生产实习报告 (3)1.1 炼铁厂生产工艺 (3)1.2 主要产品、生产规模 (3)1.3 主要设备工作原理 (4)1.4 设备维修管理 (4)2炼钢厂生产实习报告 (5)2.1 炼钢厂生产工艺 (5)2.2 主要产品、生产规模 (5)2.3 主要设备工作原理 (5)3轨梁厂生产实习报告 (6)3.1轨梁厂生产工艺 (7)3.2主要产品、生产规模 (7)3.3主要设备工作原理 (8)3.4设备维修管理 (8)4薄板连铸连轧厂生产实习报告 (9)4.1薄板胚连铸连轧生产工艺 (10)4.2主要产品生产规模 (11)4.3主要设备工作原理 (12)4.4设备的维修和管理 (13)实习总结 (15)参考文献:. 16引言一、实习目的:生产实习是我们机械专业知识结构中不可或缺的一部份。
通过这次对炼铁厂、炼钢厂、薄板连铸连轧厂、轨梁厂的生产实习,在工人师傅和老师的讲解,下以及自己在各个岗位的实践下,我对各个车间生产的主要设备和工艺流程,运输联系、工厂布置,有了一个比较全面的认识。
通过理论和实践的相结合更深入的学到了许多专业知识,同时也学到了一些安全技术知识。
这些实际知识对我学习后面的课程乃至以后的工作都是十分必要的基础。
这也是我们走向岗位的一次演练。
二、实习时间:2010年8月23日至9月3日三、实习地点:包头钢铁(集团)有限责任公司四、实习部门:炼铁厂、炼钢厂、薄板连铸连轧厂、轨梁厂五、包钢概况:包钢是我国重要的钢铁工业基地和全国最大的稀土生产、科研基地,是内蒙古自治区最大的工业企业,是自治区首家销售收入超过400亿元的企业。
1954年建厂,1998年改制为公司制企业。
公司总部位于内蒙古自治区包头市河西工业区,中心厂区占地面积37.5平方公里。
2009年年末从业人员为49378人。
拥有“包钢股份”和“包钢稀土”两个上市公司。
2009年,包钢销售收入达378.71亿元;钢产量达到1006.77万吨,同比增加22.87万吨,增长2.32%;上缴税金达到37.17亿元,为地方经济社会发展做出了应有的贡献。
炼钢控制系统实施方案
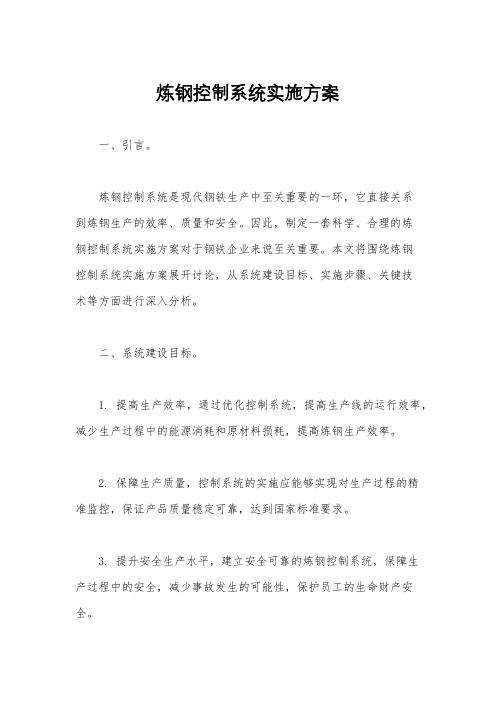
炼钢控制系统实施方案一、引言。
炼钢控制系统是现代钢铁生产中至关重要的一环,它直接关系到炼钢生产的效率、质量和安全。
因此,制定一套科学、合理的炼钢控制系统实施方案对于钢铁企业来说至关重要。
本文将围绕炼钢控制系统实施方案展开讨论,从系统建设目标、实施步骤、关键技术等方面进行深入分析。
二、系统建设目标。
1. 提高生产效率,通过优化控制系统,提高生产线的运行效率,减少生产过程中的能源消耗和原材料损耗,提高炼钢生产效率。
2. 保障生产质量,控制系统的实施应能够实现对生产过程的精准监控,保证产品质量稳定可靠,达到国家标准要求。
3. 提升安全生产水平,建立安全可靠的炼钢控制系统,保障生产过程中的安全,减少事故发生的可能性,保护员工的生命财产安全。
三、实施步骤。
1. 系统规划,明确系统建设的总体目标和具体需求,确定系统的功能模块和关键技术,制定详细的规划方案。
2. 技术选型,根据系统规划确定的功能需求,选择适合的硬件设备和软件系统,确保系统的稳定性和可靠性。
3. 系统集成,进行各功能模块的集成测试,确保系统各部分协调配合,实现系统的整体性能。
4. 系统调试,对系统进行全面调试,验证系统的稳定性和可靠性,保证系统在实际生产中的正常运行。
5. 系统运行,系统建设完成后,对系统进行持续监控和运行,及时发现和解决系统运行中的问题,确保系统的稳定运行。
四、关键技术。
1. 数据采集与处理技术,通过高效的数据采集设备和数据处理算法,实现对生产过程中各种参数的实时监测和分析。
2. 控制算法优化技术,优化炼钢生产过程中的控制算法,提高控制系统的精准度和响应速度,提高生产效率和产品质量。
3. 系统集成与通讯技术,实现控制系统与生产设备的无缝集成,确保各个部分之间的信息交互畅通,提高系统的整体性能和稳定性。
4. 安全监控技术,建立完善的安全监控系统,实现对生产过程中的安全隐患的实时监测和预警,保障生产安全。
五、总结。
炼钢控制系统实施方案的制定对于提高钢铁企业的生产效率、保障产品质量、提升安全生产水平具有重要意义。
宁钢中间包自动开浇技术的应用
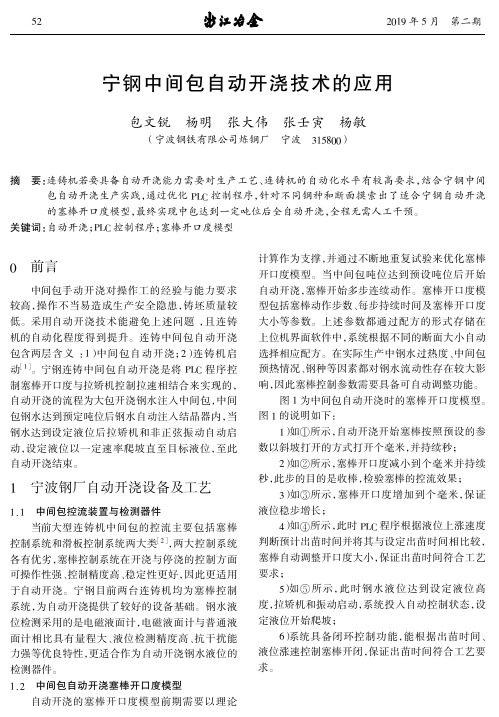
图 - 自动开浇系统界面截图
(下转第 .* 页)
#%
(%!) 年 $ “一罐到底”铁 水罐装量稳定率,同时,运用此工艺,促使炼钢在不 同的铁水条件下完善了冶炼工艺制度。由于铁水 带渣量有所减少,同时减少了倒罐的温降,在一定 程度上降低了炼钢的消耗和成本,还极大地改善了 职工的炉前工作环境及设备的使用情况,达到了环 保、节能减排的目的。
图 " 为中间包自动开浇时的塞棒开口度模型。 图 " 的说明如下:
")如!所示,自动开浇开始塞棒按照预设的参 数以斜坡打开的方式打开个毫米,并持续秒;
))如"所示,塞棒开口度减小到个毫米并持续 秒,此步的目的是收棒,检验塞棒的控流效果;
!)如#所 示,塞 棒 开 口 度 增 加 到 个 毫 米,保 证 液位稳步增长;
#)
)%"- 年 # 月 第二期
宁钢中间包自动开浇技术的应用
包文锐 杨明 张大伟 张壬寅 杨敏
(宁波钢铁有限公司炼钢厂 宁波 !"#$%%)
摘 要:连铸机若要具备自动开浇能力需要对生产工艺、连铸机的自动化水平有较高要求,结合宁钢中间 包自动开浇生产实践,通过优化 &’( 控制程序,针对不同钢种和断面摸索出了适合宁钢自动开浇 的塞棒开口度模型,最终实现中包达到一定吨位后全自动开浇,全程无需人工干预。
-)对塞棒间隙的取值不够准确,导致理论计算 出现偏差,进而导致塞棒开口度取值不合理。
针对以 上 问 题,通 过 收 集 现 场 人 工 开 浇 的 塞 棒开口度大小与持续时间等情况,从现场设备和工 艺入手进行优化,解决了对前三棒塞棒开度大小与 持续时间 把 握 不 够 准 确 的 问 题。 同 时 对 塞 棒 间 隙 值进行重新测量与估算,最终获得了较为准确的塞 棒间隙值。
连铸机自动化控制简介
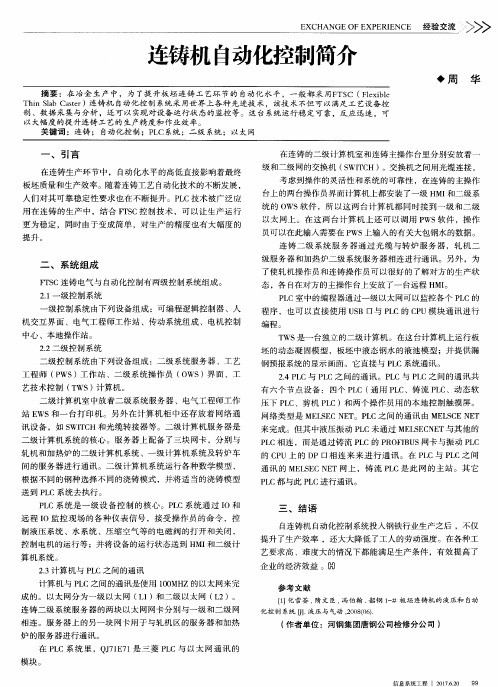
来完成 。但 其 中液压振 动 P L C未通 过 ME L S E C N E T与其 他 的 P L C相 连 ,而是通 过铸 流 P L C的 P R O F I B U S网卡与振 动 P L C 的C P U上 的 D P口相 连来 来 进 行 通 讯 。 在 P L C与 P L C之 间 通讯 的 ME L S E C N E T网上 ,铸 流 P L C是 此 网 的主 站 。其 它 P L C都与此 P L C进 行通 讯 。
压下 P L C、剪机 P L C)和两 个操 作员 用 的本地 控制 触摸 屏 。
网络 类 型是 ME L S E C N E T 。P L C之 问 的通讯 由 ME L S C E N E T
站E WS和一 台打 印机 。 另外 在 计算 机 柜 中还 存 放 着 网络 通
讯 设备 ,如 S WI T C H和 光缆 转接 器等 。二级 计算 机服 务器 是 二 级计 算 机系 统 的核心 。服务 器上 配备 了三块 网卡 ,分别 与 轧 机 和加热 炉 的二 级计算 机 系统 、一级 计算机 系统 及转 炉 车
E XC H ANGE OF E XP E RI E NC E 经 验交流
连铸机 自 动化控制简介
◆ 周 华
摘 要 :在 冶金 生产 中 ,为 了提 升板 坯 连铸 工 艺环 节的 自动 化 水平 ,一 般 都采 用F TS C( F 1 e x i b l e T h i n S l a b Ca s t e r )连 铸机 自动化 控 制 系统 采用世界 上 各种 先进技 术 ,该技 术 不但 可 以满足工 艺设备控
提升。
台上 的两 台操作员 界面计算 机上 都安装 了一 级 H M I 和二级 系
炼钢厂连铸岗位操作规程

岗位职责:按要求按时报拉速、开浇、停浇情况,并配合拉钢工送引锭。
负责填写本岗位报表、记录。
负责本岗位责任区域卫生。
严格执行安全规程。
1浇注前的准备;1.1将主控室操作台上的转换开关打在“浇注准备”位。
1.2检查操作台面上的指示灯、按钮、转换开关工作是否正常,并能熟练操作。
1.3检查操作站工作是否正常并能熟练操作,确认画面上显示的水、气、液压等参数以及二冷自动配水方式处于正常生产状态。
1.4准备好原始记录表和笔。
2浇注操作:2.1确认具备浇注条件后,提前通知调度送结晶器水和二冷水。
2.2启动二冷风机,供水系统的手动阀门处拉开位。
2.3浇注过程中,注意观察画面上显示的钢水温度、拉速,结晶器冷却水,二冷水的流量、压力等参数,设备的运行情况。
2.4大包、中包测温后及时通报。
2.5及时通报拉速变化情况。
2.6定时通报大包浇注时间及换包开浇、停浇等情况。
2.7详细记录生产报表上所要求的各项数据。
2.8做好与各系统的联系工作。
2.9当浇注中出现报警信号时,应立即通知机长。
3 浇铸结束操作:3.1当最后一流铸坯拉出二冷室后,关闭风机。
3.2停机后,确定不再拉钢时,通知调度停水。
3.3做好交接班准备或下一个次拉钢的准备工作。
岗位职责:检查各处水系统是否正常,发现问题及时处理;按各钢种条件进行水量调节,达到合理配水;密切观察铸坯情况,发现问题及时处理并汇报。
负责填写本岗位报表、记录。
负责本岗位责任区域卫生。
严格执行安全规程。
1、浇注前的准备:1.1冷却水系统检查:1.1.1二冷喷淋环、喷淋集管安装有无歪斜,是否对中,并及时调整,喷嘴有无堵塞,并及时处理。
1.1.2水系统管路阀门开闭调节是否灵活,有无漏水。
1.1.3各显示仪表工作是否正常。
1.1.4结晶器水、二冷水、设备冷却水的压力和流量是否达到工艺要求,过滤器工作是否正常。
1.1.5检查二冷自动配水系统工作情况,打开水系统所有阀门,检查供水是否正常。
熟练掌握各种配水方式。
优化炼钢工艺确保高效连铸的钢水质量
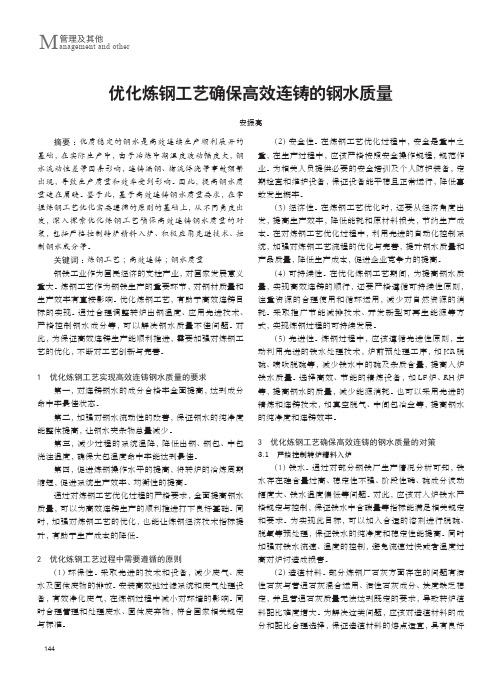
管理及其他M anagement and other优化炼钢工艺确保高效连铸的钢水质量安振亮摘要:优质稳定的钢水是高效连续生产顺利展开的基础,在实际生产中,由于冶炼中期温度波动幅度大,钢水流动性差等因素影响,连铸漏钢、堵流停浇等事故频繁出现,导致生产质量和效率受到影响。
因此,提高钢水质量迫在眉睫。
鉴于此,基于高效连铸钢水质量要求,在掌握炼钢工艺优化需要遵循的原则的基础上,从不同角度出发,深入探索优化炼钢工艺确保高效连铸钢水质量的对策,包括严格控制转炉精料入炉、积极应用先进技术、控制钢水成分等。
关键词:炼钢工艺;高效连铸;钢水质量钢铁工业作为国民经济的支柱产业,对国家发展意义重大。
炼钢工艺作为钢铁生产的重要环节,对钢材质量和生产效率有直接影响。
优化炼钢工艺,有助于高效连铸目标的实现。
通过合理调整转炉出钢温度、应用先进技术、严格控制钢水成分等,可以解决钢水质量不佳问题。
对此,为保证高效连铸生产能顺利推进,需要加强对炼钢工艺的优化,不断对工艺创新与完善。
1 优化炼钢工艺实现高效连铸钢水质量的要求第一,对连铸钢水的成分合格率全面提高,达到成分命中率最佳状态。
第二,加强对钢水流动性的改善,保证钢水的纯净度能整体提高,让钢水夹杂物总量减少。
第三,减少过程的系统温降,降低出钢、钢包、中包浇注温度,确保大包温度命中率能达到最佳。
第四,促进炼钢操作水平的提高,将转炉的冶炼周期缩短,促进系统生产效率、均衡性的提高。
通过对炼钢工艺优化过程的严格要求,全面提高钢水质量,可以为高效连铸生产的顺利推进打下良好基础。
同时,加强对炼钢工艺的优化,也能让炼钢经济技术指标提升,有助于生产成本的降低。
2 优化炼钢工艺过程中需要遵循的原则(1)环保性。
采取先进的技术和设备,减少废气、废水及固体废物的排放。
安装高效地过滤系统和废气处理设备,有效净化废气,在炼钢过程中减小对环境的影响。
同时合理管理和处理废水、固体废弃物,符合国家相关规定与标准。
PLC在冶金工业中的应用案例
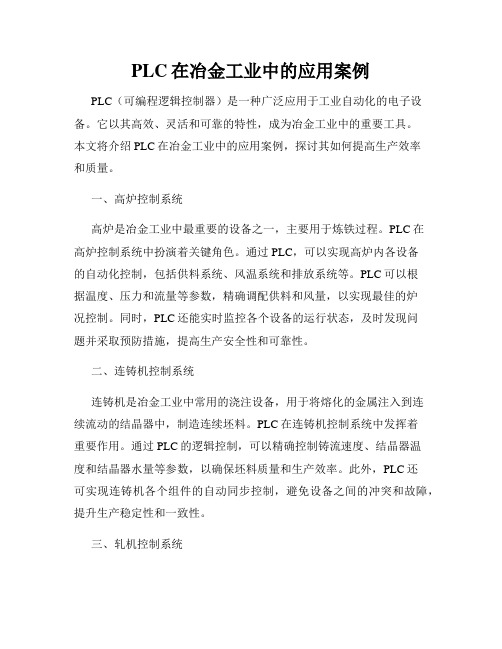
PLC在冶金工业中的应用案例PLC(可编程逻辑控制器)是一种广泛应用于工业自动化的电子设备。
它以其高效、灵活和可靠的特性,成为冶金工业中的重要工具。
本文将介绍PLC在冶金工业中的应用案例,探讨其如何提高生产效率和质量。
一、高炉控制系统高炉是冶金工业中最重要的设备之一,主要用于炼铁过程。
PLC在高炉控制系统中扮演着关键角色。
通过PLC,可以实现高炉内各设备的自动化控制,包括供料系统、风温系统和排放系统等。
PLC可以根据温度、压力和流量等参数,精确调配供料和风量,以实现最佳的炉况控制。
同时,PLC还能实时监控各个设备的运行状态,及时发现问题并采取预防措施,提高生产安全性和可靠性。
二、连铸机控制系统连铸机是冶金工业中常用的浇注设备,用于将熔化的金属注入到连续流动的结晶器中,制造连续坯料。
PLC在连铸机控制系统中发挥着重要作用。
通过PLC的逻辑控制,可以精确控制铸流速度、结晶器温度和结晶器水量等参数,以确保坯料质量和生产效率。
此外,PLC还可实现连铸机各个组件的自动同步控制,避免设备之间的冲突和故障,提升生产稳定性和一致性。
三、轧机控制系统轧机是冶金工业中用于将金属坯料轧制成板材或线材的设备。
PLC广泛应用于轧机控制系统中,实现轧机的自动化操作和控制。
通过PLC,可以实时监测和调整轧机的压力、速度和张力等参数,以确保产品尺寸和表面质量的一致性。
此外,PLC还能自动检测轧机轧辊的磨损程度,并根据需要进行自动调整,延长轧辊寿命,降低维护成本。
四、冶炼过程控制系统冶炼过程是冶金工业中的核心环节,PLC在冶炼过程控制系统中发挥着至关重要的作用。
通过PLC,可以实时监控和调控冶炼过程中的温度、压力和化学成分等参数,确保炉内条件的稳定和产品质量的一致性。
此外,PLC还可以与其他设备和系统进行联动控制,如喷吹系统、加料系统和废气处理系统等,实现全面的工艺控制和能源优化。
总结:PLC在冶金工业中的应用案例举不胜举,从高炉控制系统到冶炼过程控制系统,从连铸机到轧机控制系统,它为冶金工业的自动化生产和质量改进提供了强有力的支持。
钢包精炼渣系优化与应用(PDF)

钢包精炼渣系优化与应用王建国(湖南华菱湘潭钢铁集团有限公司, 湘潭 411101 )摘要钢包精炼渣系的选择和合适的渣成分组成,对实现快速造渣,改善精炼效果,缩短精炼时间,提高综合脱硫效果和稳定钢中Als含量,降低精炼造渣成本,满足炉机匹配、生产节奏要求有着非常重要意义。
湘钢宽厚板厂根据品种钢开发、生产工艺要求,通过对不同钢包精炼渣系的选择并优化,有效地改善了LF精炼效果,提高了综合脱硫效果,稳定了含铝钢生产,降低了精炼造渣成本,取得了较好的经济效益。
关键词钢包精炼渣系优化应用Hot Metal Ladle Refining Slag SystemOptimization and ApplicationWang Jianguo(Hunan Valin Xiangsteel, Xiangtan, 411101)Abstract The hot metal ladle refining slag department's choice and the appropriate dregs ingredient composition, to realize the fast slag formation, the improvement fining effect, reduces the refining time, enhances synthesis desulphurization effect and in the stable steel the Als content, reduces the fining slag formation cost, satisfies the stove machine match, the production rhythm request to have the very important meaning.The Xianggang Generous Lumber yard basis variety steel development, the technique of production request, through and optimizes to the different hot metal ladle refining slag department's choice, improved the LF fining effect effectively, raised the comprehensive desulphurization efficiency, has stabilized including the aluminum steel production, reduced the fining slag formation cost, has obtained the good economic efficiency.Key words hot metal ladle fining, Slag system, optimization, application1 引言铝镇静钢—即终脱氧采用铝完全脱氧方式。
浅述轧钢自动化控制系统应用优化

浅述轧钢自动化控制系统应用优化1. 引言1.1 背景介绍轧钢是钢铁生产过程中重要的一环,其质量和效率直接影响着整个生产线的运行。
随着自动化技术的不断发展,轧钢自动化控制系统在钢铁行业中得到了广泛应用。
这些控制系统可以实现对轧钢过程中各项参数的实时监测和调节,从而提高生产效率、降低生产成本、改善产品质量。
在以往的传统轧钢生产过程中,操作人员需要依靠经验和手动调节来控制设备运行,这种方式存在着操作不稳定、效率低下、人为因素影响大等问题。
而随着轧钢自动化控制系统的引入,可以实现对轧钢过程的全面监控和精确控制,从而提高生产效率和产品质量,减少人为因素带来的不确定性。
本文旨在对轧钢自动化控制系统的应用进行深入探讨,分析现有系统存在的问题,探讨优化控制系统应用的技术方案,以及通过案例分析来展示其在实际生产中的效果。
通过研究,希望可以为轧钢行业的自动化控制系统应用提供一定的借鉴和参考,推动钢铁行业的技术进步和产业升级。
1.2 问题提出在轧钢生产过程中,自动化控制系统扮演着至关重要的角色。
在使用和实践的过程中,我们也发现了一些问题。
现有系统在处理复杂生产环境下的稳定性和可靠性方面有待提高。
部分轧钢厂家在控制系统的选择和应用方面存在一定的局限性,导致生产效率和质量无法达到最佳状态。
一些厂家对于控制系统的更新换代速度较慢,导致装备水平与行业发展脱节,影响企业竞争力。
如何解决这些问题,提高轧钢自动化控制系统的应用效果,成为当下亟待解决的问题之一。
为此,本文将对轧钢自动化控制系统进行概述,分析现有系统存在的问题,并提出优化控制系统应用的方案,以期为轧钢生产过程的智能化和高效化发展提供有益借鉴。
1.3 研究意义轧钢自动化控制系统在现代钢铁生产中发挥着重要作用,其优化应用具有重要的研究意义。
优化控制系统的应用可以提高轧钢生产的生产效率和产品质量,降低生产成本,增加企业的竞争力和盈利能力。
通过对控制系统进行优化,可以实现生产过程的智能化、自动化,减少人为干预带来的误差和问题,提高生产的稳定性和一致性。
WAGO在方坯连铸智能布料系统中的应用

WAGO在方坯连铸智能布料系统中的应用摘要:本文通过设计方坯连铸智能加渣布料系统的制系统,并在工程实践中验证了WagoIO模块系列在该系统使用过程中的稳定性,满足了工程现场的需要,同时智能加渣布料系统大大减轻了现场操作工人的劳动强度,经济效益显著。
关键词:方坯连铸;智能加渣;Wago1工艺需求在连铸生产中,需要不断向结晶器内的液态钢表面添加保护渣,它可以绝热、保温、防止散热;隔开空气,防止空气中的氧气进入钢水发生二次氧化,影响钢的质量;吸收溶解从钢水中上浮到钢渣截面的夹杂物,净化钢液;在结晶器壁与凝固壳之间形成的渣膜起润滑作用,减少拉坯阻力,防止凝壳与铜板的粘结;填充与结晶器之间的气隙,改善结晶器传热,结晶器布料是不可缺少的工序。
国内除少数大型钢铁企业采用进口结晶器自动给料装置外,多数钢铁企业都采用人工加渣。
人工加渣随机性大,在结晶器中保护渣分布不均匀,易造成卷渣并引发产品质量问题。
针对方坯连铸生产的实际需求,设计并开发了方坯连铸智能布料控制系统。
2 智能布料系统设备组成1)料仓存储料仓有过滤筛网,过滤和清洁保护渣,防止大块(结块)进入输料管道,造成管道堵塞。
料仓设置一刀片状顶部尖利的物体,可以刺透保护渣包装袋,便于袋装保护渣能自动流入料仓。
2)渣料加热料仓加热是布料装置非常重要的环节,通过料仓加热,可以实现渣料的加热去湿,同时烘烤保护渣,保证下料时均匀,无水汽。
3)步进给料系统加料量的多少是和钢种、断面、拉速等工艺条件变化的,保护渣加入的快慢可以通过PLC控制给料电机转速,从而实现智能控制,精确加渣。
3 控制系统选择结合工艺系统需求,本智能布料系统选用WAGO现场控制器750-841 IO系统,其产品配置图见下表:表1:PLC模块配置该系统产品特点如下:1)高控制效率带有ETHERNET总线适配器的WAGO-I/O-SYSTEM在ETHERNET现场总线系统上可以作主站、也可以作从站。
该总线适配器能支持所有I/O模块并自动配置、生成包括数字量模块、模拟量模块和特殊功能模块的本地过程映像。
- 1、下载文档前请自行甄别文档内容的完整性,平台不提供额外的编辑、内容补充、找答案等附加服务。
- 2、"仅部分预览"的文档,不可在线预览部分如存在完整性等问题,可反馈申请退款(可完整预览的文档不适用该条件!)。
- 3、如文档侵犯您的权益,请联系客服反馈,我们会尽快为您处理(人工客服工作时间:9:00-18:30)。
包钢炼钢厂连铸自动加渣控制系统应用
摘要:本文讲述了包钢炼钢厂连铸自动加渣控制系统的开发与应用,该控制
系统能实时计算出结晶器内各渣层厚度,依据目标渣厚来实时控制保护渣的加入
速度。
应用效果表明,包钢炼钢厂应用该自动加渣控制系统后,结晶器内钢液面
更加稳定,液渣层准确控制在8-12mm之间,浸入式水口在结晶器流场中受冲刷
与侵蚀程度减轻,重轨钢坯洁净度得到提升,同时职工劳动强度也明显降低。
关键词:连铸;保护渣;自动加渣
1引言
在连铸过程中,保护渣被加入结晶器后,会很快的吸收高温钢水的热量,并
且迅速的在钢水液面上形成液渣层,靠近液渣层的保护渣还没有达到熔化温度时,已被烧结成烧结层,在烧结层上方是粉渣层,这就是所谓的保护渣三层结构——
液渣层,烧结层,粉渣层。
现代研究公认保护渣在连铸结晶器中有五大作用:绝
热保温,防止氧化,润滑,改善传热和吸收夹杂物[1]。
保护渣加入过程中,如果保护渣加入过少,液渣层减少,结晶器润滑效果下降,引起粘结漏钢。
而如果保护渣加入过多,结晶器内液渣层过厚,结晶器液面
渣圈严重并结团,保护渣结团会造成铸坯表面夹杂增加形成表面翻皮,夹渣及坯
内夹渣等缺陷。
甚至会影响操作造成结晶过程中表面夹渣,当凝固外壳出结晶器
下口时易重熔或被二冷水冲走造成夹渣漏钢。
结晶器内保护结团也会造成结晶坯
壳与结晶器表面润滑不良,形成粘结漏钢[2]。
因此正确的加渣方法:保护渣要做
到勤加少加,均匀铺盖。
目前国内绝大多数钢厂的结晶器保护渣加渣操作还是采用人工加渣。
人工加
渣在操作上需要操作者不定时的向结晶器内推入保护渣,这样的操作容易造成结
晶内钢液面的瞬间搅动,容易造成卷渣等缺陷。
由于人工加渣的效果很大程度上
依靠操作者的经验,所以一般不可能产生稳定的液渣层。
人工加渣操作无法解决
保护渣在储存过程中的返潮现象。
基于人工加渣的多种弊端,开发一种可以实现
自动化,精确控制加渣量的结晶器自动加渣机成为必不可少的需求。
2包钢炼钢厂自动加渣原理与开发
在20世纪70年代以前,各国连铸领域均采用人工方式加入保护渣。
之后,
随着技术的不断改进,开始逐步采用自动加入保护渣方法。
目前国外已开发出多
种类型的结晶器自动加渣技术,宝钢、太钢等国内大中型钢厂已引进并投入使用
国外进口的自动加渣机[2]。
保护渣自动加渣的控制方法有下面几种:
(1)依据拉速法控制加渣速度
这种控制方法就是依据铸机拉速来控制加渣速度,由现场操作人员提供不同
钢种、不同拉速下的渣耗,当拉速增大时,渣耗增大,加渣速度增大;拉速减小时,渣耗减小,加渣速度减小。
这种控制方法不能控制渣厚,只能间接的由拉速与渣耗量来加渣速度,渣厚
波动大,而且尤其在拉速突然变化时,加渣速度也会相应的突然变化,渣厚波动
剧烈。
同时此方法也不能反应浇铸温度的变化对渣厚带来的影响。
(2)依据现场检测法控制加渣速度
这种控制方法就是在连铸现场安装监测设备,具体就是在结晶器上方安装摄
像头,通过测量渣层温度来控制加渣时机与加渣速度。
其控制时序为监测装置实
时测量保护渣表面温度,当保护渣表面温度大于等于融化温度,此时保护渣表面
见红,控制程序通知加渣设备加渣,当保护渣加到规定厚度,控制程序停止加渣。
监测设备继续实时监测渣温。
这种控制方法需要在现场安装监测设备,投资较大,而且连铸现场高温、环
境恶劣,对监测设备损耗较大,影响设备使用寿命,后期维护费用也较高。
另外
此种方法只能采用间歇式的加渣方法,不能采用匀速加渣法,渣厚波动也较大。
(3)依据模型计算渣厚法动态控制加渣
这种方法是通过模型,依据浇铸钢种、断面尺寸、水口插入深度、浇铸温度、拉速、结晶器冷却水量、结晶器进出水温差、保护渣融化温度等数据,实时计算
铸坯厚度、结晶器表面钢水温度场等,然后依据与保护渣融化温度之间的温度梯
度动态计算保护渣的融化速度与渣耗速度,然后依据目标渣厚值,动态控制加渣
速度,使得保护渣厚度始终保持在目标渣厚值。
此种方法能够直接计算渣厚值,按目标渣厚值来控制加渣速度,当拉速突然
变化时,加渣速度会依据保护渣融化程度平缓变化,不会造成渣厚剧烈波动。
而
且当浇铸温度等影响保护渣融化的因素变化时,加渣速度也会相应变化,保证渣
厚始终保持在目标渣厚。
同时此方法不用在现场安装检测设备,投资低,控制系
统稳定、耐用、计算精度高。
包钢炼钢厂采用的就是北京科技大学开发的动态加渣控制模型。
该控制模型
计算结果与双丝法检测结果对比,误差在5%以内,能够满足包钢炼钢厂生产高质
量重轨工艺要求。
3包钢炼钢厂自动加渣系统设备与功能
包钢炼钢厂自动加渣系统的硬件由保护渣储存箱、步进电机、涡轮螺杆传输器、电控柜、气控柜、料位计、输送管道、加渣喷嘴等部件组成。
系统由动态加
渣模型二级控制,二级模型放在主控室计算机,模型将计算出的加渣速度信号传
输至现场PLC,由现场PLC控制各流的步进电机转速来控制加渣速度。
系统采用气动传输的原理来输送保护渣,保护渣储存箱安装在中包操作平台上,便于操作工将保护渣加入到储存箱中。
保护渣由储存箱中通过传输管道进入
涡轮螺杆传输器,由动态加渣模型通过现场PLC控制步进电机转速对加渣量进行
精确控制,然后保护渣由气动传输管道输送至各流的加渣喷嘴,动态均匀的布置
在结晶器钢水表面,实现结晶器动态加渣控制。
自动加渣模型对铸坯从结晶器钢水弯月面到结晶器出口进行全程的温度场实
时跟踪,实时描述整个结晶器内的温度场。
动态加渣模型依据浇注钢种、浇注温度、拉速、结晶器水量、结晶器水温差、水口插入深度、结晶器振动参数、目标
渣厚等参数,实时计算出结晶器内温度场依据结晶器内温度场计算出保护渣的表面温度、融化速度、保护渣厚,依据目标渣厚来实时控制保护渣的加入速度。
4自动加渣二级模型准确性测量试验
自动加渣模型在上线正式应用以前应当对其计算准确性进行验证,本模型用保护渣厚度测量验证法:
模型上线调试期间,采用三丝法对结晶器内保护渣厚度进行实测,将测量结果与模型将测量结果与模型计算结果进行对比,如果对比结果在允许误差范围之外,将微调模型的传热计算参数,将计算结果与实测结果的偏差控制允许误差之内,满足现场工艺要求。
表1 保护渣厚度测量试验数据
从试验测量结果可以看出,试验过程实际测量保护渣的液渣层、烧结层、粉
渣层三层厚度,与模型计算数据基本符合,最大偏差为+1.6%,最小偏差为
+0.96%,偏差均小于±2%,二级模型计算精度满足生产要求。
5应用效果:
(1)、结晶器液位及渣厚稳定
图1手动加渣与自动加渣液面及渣厚比较
使用自动加渣后,减少了液面的瞬间冲击造成的液面波动,液位波动从2-
4mm减少至1-2mm,结晶器内钢液面更加稳定,同时避免液面波动卷渣污染钢液。
液渣层控制在8-12mm之间,与手动加渣相当;粉渣层控制在20-30mm,较手动加
渣的20-50mm控制精度更高,渣厚更趋于稳定。
(2)、水口渣线侵蚀减轻
图2 使用自动加渣前后浸入式水口侵蚀比较
与人工加渣对比,使用自动加渣后,结晶器内钢液面更加稳定,水口渣线侵
蚀宽度减小。
浸入式水口在结晶器流场中受冲刷减轻,侵蚀程度降低,渣线宽度
减少约一半,从而提升了重轨钢坯洁净度。
(3)、职工劳动强度降低
与人工加渣对比,手动加渣每8min左右进行一次加渣,使用自动加渣后,
整浇次基本无须干预。
职工劳动强度明显降低。
6结论
(1)保护渣的合理准确加入对于连铸生产顺行与铸坯质量有着重要的影响,基于人工加渣的多种弊端,开发一种可以实现自动化,精确控制加渣量的结晶器
自动加渣机成为必不可少的需求。
(2)包钢炼钢厂采用动态加渣控制模型。
该控制模型能实时计算出结晶器
内各渣层厚度,依据目标渣厚来实时控制保护渣的加入速度,模型计算结果与双
丝法检测结果对比,误差在±2%以内,能够满足包钢炼钢厂生产高质量重轨工艺
要求。
(3)工业生产结果表明,包钢炼钢厂应用自动加渣控制系统后,结晶器内
钢液面更加稳定,液位波动从2-4mm减少至1-2mm,液渣层准确控制在8-12mm之间,避免液面波动卷渣污染钢液。
同时浸入式水口渣线侵蚀宽度减小,水口在结
晶器流场中受冲刷减轻,侵蚀程度降低,重轨钢坯洁净度得到提升。
职工劳动强
度也明显降低。
参考文献
[1]杜方. 连铸保护渣渣膜润滑模拟研究.重庆大学硕士学位论文, 2009-05.
[2]薛伟锋张文增罗利华马献德徐济民.板坯连铸结晶器自动加渣机的研制.No.1 March 2013.
1。