冲压生产的危险性分析与风险控制
冲压加工安全风险及应对措施

冲压加工安全风险及应对措施
冲压加工中的不安全因素包括以下几个方面:
1.冲压机本身存在的不安全因素,如冲压机的行程开关失灵、操作装置失灵、
模具及装置有缺陷等。
这些问题可能会导致冲压机无法正常运行,或者在运行过程中出现故障,从而对操作人员造成伤害。
2.操作人员的不安全行为,如未按照规定操作冲压机、在冲压机运行过程中
进行检修或调整、用手代替工具进行操作等。
这些行为都可能导致操作人员受伤或事故发生。
3.冲压加工过程中的危险因素,如冲压件被挤出、模具或工件崩裂等。
这些
危险因素可能会对操作人员的安全造成威胁,特别是在模具更换或工件装卸过程中更容易发生。
4.其他不安全因素,如工件或废料从高处坠落、设备维护不当导致泄漏等。
这些问题可能会对操作人员的安全造成威胁,同时也会对企业的生产造成影响。
为了确保冲压加工的安全性,企业需要采取一系列的安全措施,包括加强设备维护和检修、规范操作人员的行为、加强安全教育和培训等。
同时,政府也需要加强对企业的监管,确保企业能够遵守相关法律法规和标准,保障操作人员的安全和健康。
冲压厂安全隐患排查(3篇)

第1篇一、前言冲压厂作为现代工业生产的重要环节,其生产过程中涉及到大量机械设备和人员操作。
然而,由于设备老化、操作不当、管理不善等原因,冲压厂存在一定的安全隐患。
为了确保生产安全,预防事故发生,提高员工的安全意识,本报告对冲压厂的安全隐患进行排查,并提出相应的整改措施。
二、安全隐患排查范围1. 设备设施:包括机械设备、电气设备、安全防护装置等。
2. 人员操作:包括员工安全意识、操作技能、遵守规章制度等方面。
3. 环境因素:包括现场环境、通风、照明、防尘、防噪等方面。
4. 管理制度:包括安全管理制度、应急预案、培训教育等方面。
三、安全隐患排查结果1. 设备设施方面:(1)部分机械设备存在老化现象,如液压机、剪板机等,存在潜在的安全隐患。
(2)电气设备存在绝缘老化、接地不良等问题,存在触电风险。
(3)安全防护装置不全,如部分机械设备缺少防护罩、紧急停止按钮等。
2. 人员操作方面:(1)部分员工安全意识淡薄,对安全生产的重要性认识不足。
(2)员工操作技能不足,对机械设备操作不熟练,存在误操作风险。
(3)部分员工违反操作规程,如未佩戴安全帽、手套等防护用品。
3. 环境因素方面:(1)现场环境较差,存在乱堆乱放、地面湿滑等问题。
(2)通风不良,存在缺氧、有毒气体积聚的风险。
(3)照明不足,存在安全隐患。
4. 管理制度方面:(1)安全管理制度不完善,部分制度执行不到位。
(2)应急预案不健全,应急响应能力不足。
(3)培训教育不到位,员工安全意识、操作技能有待提高。
四、整改措施1. 设备设施方面:(1)对老化设备进行维修或更换,确保设备安全运行。
(2)对电气设备进行绝缘处理、接地检查,消除触电风险。
(3)完善安全防护装置,如安装防护罩、紧急停止按钮等。
2. 人员操作方面:(1)加强员工安全教育培训,提高员工安全意识。
(2)提高员工操作技能,确保员工熟练掌握操作规程。
(3)严格执行操作规程,佩戴防护用品,确保操作安全。
冲压危险预知及预防
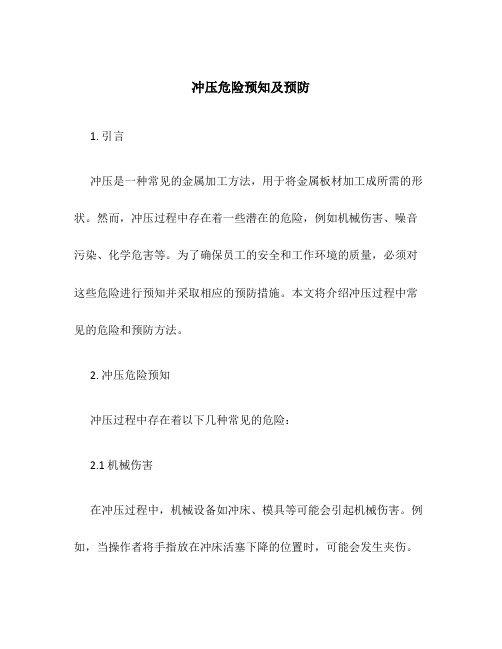
冲压危险预知及预防1. 引言冲压是一种常见的金属加工方法,用于将金属板材加工成所需的形状。
然而,冲压过程中存在着一些潜在的危险,例如机械伤害、噪音污染、化学危害等。
为了确保员工的安全和工作环境的质量,必须对这些危险进行预知并采取相应的预防措施。
本文将介绍冲压过程中常见的危险和预防方法。
2. 冲压危险预知冲压过程中存在着以下几种常见的危险:2.1 机械伤害在冲压过程中,机械设备如冲床、模具等可能会引起机械伤害。
例如,当操作者将手指放在冲床活塞下降的位置时,可能会发生夹伤。
此外,模具的移动部件也可能造成损伤。
因此,机械伤害是冲压过程中需要预防的重要危险之一。
2.2 噪音污染冲压过程中产生的噪音可能会对操作者的听力造成损害。
长时间暴露在高噪音环境中可能导致听力受损。
因此,噪音污染也是需要预防的危险之一。
2.3 化学危害在冲压过程中,可能会使用一些化学物质例如润滑油和冷却剂。
这些化学物质可能对员工的健康造成潜在危害,例如皮肤过敏、呼吸系统问题等。
因此,化学危害是需要预知并预防的危险之一。
3. 冲压危险的预防措施为了预防冲压过程中的危险,以下是一些常见的预防措施:•提供安全培训:对操作者进行冲压机械设备的安全培训,教授正确的操作方法和注意事项,以减少机械伤害的发生。
•安装安全防护装置:在冲床活塞下降的位置安装安全装置,例如光幕、压力传感器等,以防止夹伤事故的发生。
•定期检查设备状态:定期检查冲床和模具的状态,确保设备的正常运转,避免因设备故障导致的机械伤害。
3.2 噪音污染的预防•穿戴耳塞:提供耳塞给操作者,减少噪音对听力的影响。
通过降低噪音的级别,保护员工的听力健康。
•使用隔音设备:对冲压设备和周围环境进行隔音处理,减少噪音的传播,降低噪音污染的程度。
•控制噪音源:采取措施控制噪音源的声音产生,例如调整设备的工作速度、更换噪音较小的设备等。
•提供个人防护用品:为操作人员提供适当的个人防护用品,例如手套、护目镜、口罩等,以保护他们免受化学物质的伤害。
冲压生产线的安全
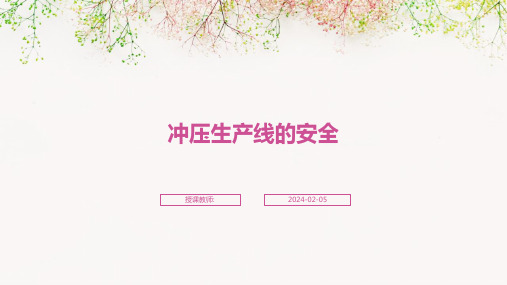
针对不同类型的安全风险,制定相应的应急预案
如机械伤害应急预案、电气伤害应急预案等。
演练计划组织实施
制定年度、季度、月度的应急演练计划
确保各类应急预案得到定期演练。
组织相关人员进行演练
包括生产线操作人员、安全管理人员、医疗救护人员等。
对演练过程进行全程记录
包括演练时间、地点、参与人员、演练内容、存在的问题等。
总结经验教训,持续改进
对每次应急演练和事故处理进行总结
分析存在的问题和不足之处。
针对总结出的经验教训,提出改进措施
如完善应急预案、加强人员培训、提高设备安全性能等。
将改进措施落实到实际工作中
确保冲压生产线的安全得到持续改进和提升。
定期对冲压生产线的安全状况进行评估
确保生产线的安全状况符合相关法规和标准的要求。
冲压生产线的安全
授课教师:
2024-02-05
目
CONTENCT
录
• 安全概述与重要性 • 设备安全设计与选型 • 操作规程与培训要求 • 现场管理与监督检查 • 应急预案与事故处理 • 法规符合性与认证要求
01
安全概述与重要性
冲压生产线定义及特点
冲压生产线是一种自动化、高效率的金属加工生产 线。
培训内容包括冲压生产线的基 本原理、设备结构、操作规程 等。
培训内容包括冲压生产线的基 本原理、设备结构、操作规程 等。
培训内容包括冲压生产线的基 本原理、设备结构、操作规程 等。
考核评估机制建立
制定考核标准,明确各岗位人员的考核要求和指 标。
对考核不合格的员工进行再培训,直至达到考核 要求。
采用定期考核和不定期抽查相结合的方式,确保 员工掌握操作技能和安全知识。
冲压机械的危险性分析与安全措施

冲压机械的危险性分析与安全措施
冲压机是一种常用的金属加工设备,用于将金属材料加工成所需形状的工艺,具有高效、高精度的特点。
然而,冲压机在操作过程中也存在很多安全隐患,如果不采取适当的安全措施可能会导致人身伤害甚至生命危险。
其次,冲压机的操作也存在操作人员的人为错误。
操作人员在操作冲压机时,如果没有经过专业培训或者掌握了错误的操作方法,容易造成操作失误,进而引发事故。
因此,企业应对操作人员进行全面的培训,包括冲压机的相关知识、操作规程、应急措施等,提高操作人员的安全意识和技能水平。
此外,冲压机的噪声和振动也是一种危害。
持续暴露在高噪声和振动环境下,容易引发听力损伤、神经病变等职业病。
为降低噪声和振动的危害,可以采取隔振隔音措施,如安装隔音门、隔音窗、隔音罩等,同时对操作人员提供耳塞、口罩等个人防护装备。
此外,冲压模具的更换也是一项危险的工作。
在更换模具时,操作人员需要接触到高温和高压的金属材料,容易烫伤和刺伤操作人员。
因此,在更换模具前,操作人员必须佩戴防烫手套、防刺手套等防护装备,确保操作人员的安全。
最后,冲压机还存在电气危险。
冲压机通常使用电力作为动力源,电气设备故障或不当操作可能导致电击事故。
为防止这种事故的发生,应定期检查电气系统的安全性,确保电气设备的接地良好、绝缘完好,并对操作人员进行必要的电气安全培训。
综上所述,冲压机械的危险性分析与安全措施是保障操作人员安全和设备正常运行的重要环节。
应当做好冲压机的防护设施建设,加强人员培训,强化岗位责任意识,确保冲压机操作过程的安全。
只有保证了冲压机的安全操作,才能提高生产效率,提升企业的竞争力。
冲压作业伤害分析及标识管理范文

冲压作业伤害分析及标识管理范文冲压作业是一种在工业生产中常见的金属加工方式,它可以实现对金属材料的成型、塑性变形和修整。
然而,由于冲压作业的特性和操作过程,工人在进行冲压作业时存在一定的伤害风险。
为了保护工人的安全和健康,必须进行伤害分析,并制定相应的标识管理措施。
本文将就冲压作业伤害分析及标识管理这一问题进行探讨。
首先,我们需要进行冲压作业的伤害分析。
冲压作业中可能引发的伤害主要包括机械伤害、化学伤害和物理伤害等。
机械伤害是指在冲压作业中,由于金属材料的高速变形和运动,工人容易受到金属材料与设备机械碰撞、夹伤等伤害。
化学伤害是指工人在冲压作业中接触到的化学品可能对皮肤、眼睛、呼吸系统等造成伤害。
物理伤害是指冲压作业中产生的噪声、震动、有害物质等会对工人的听力、神经系统、心血管系统等造成伤害。
针对这些潜在的伤害,我们可以采取一系列的措施进行管理。
首先,应对冲压作业进行全面的安全评估。
通过对作业过程、设备状态、操作技术等方面的评估,找出可能导致伤害的原因和存在的问题。
然后,针对不同类型的伤害,采取相应的防护措施。
机械伤害可以通过安装护栏、使用安全阀等设备进行防护;化学伤害可以通过进行化学品的评估和分类、安装通风系统、提供个人防护用品等方式进行防护;物理伤害可以通过进行噪声和震动控制、提供职业病防护用品等方式进行防护。
除了直接的防护措施,标识管理也是非常重要的一环。
首先,我们应在冲压作业现场设置明显的警示标识,以提醒工人注意安全。
例如,在机械设备周围设置“危险区域,禁止靠近”等标识,以防止工人误入危险区域。
其次,应对化学品进行标识管理。
化学品的容器应有明确的标识,标明化学品的危险性和相关安全注意事项,以防止工人对化学品的错误使用或触摸。
此外,在作业区域内还可以设置紧急情况应急电话等标识,以便及时求助。
最后,在工人的个人防护用品上也应进行标识管理。
例如,在防护眼镜上标明其防护等级,以便工人选择合适的防护用品。
冲压作业危险有害因素辩识及预防措施
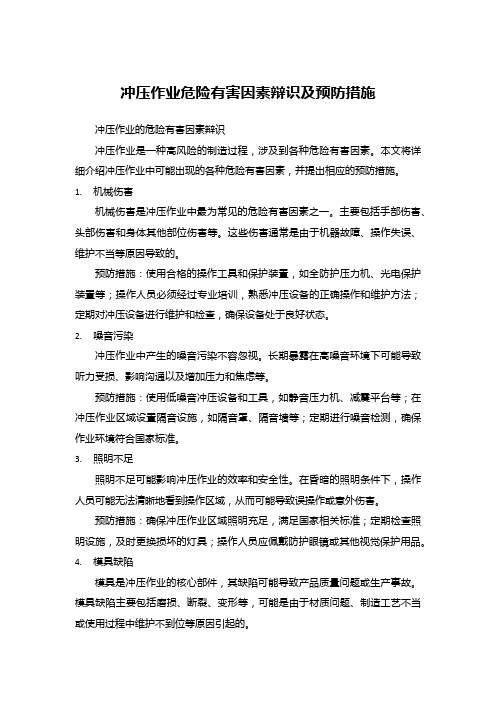
冲压作业危险有害因素辩识及预防措施冲压作业的危险有害因素辩识冲压作业是一种高风险的制造过程,涉及到各种危险有害因素。
本文将详细介绍冲压作业中可能出现的各种危险有害因素,并提出相应的预防措施。
1.机械伤害机械伤害是冲压作业中最为常见的危险有害因素之一。
主要包括手部伤害、头部伤害和身体其他部位伤害等。
这些伤害通常是由于机器故障、操作失误、维护不当等原因导致的。
预防措施:使用合格的操作工具和保护装置,如全防护压力机、光电保护装置等;操作人员必须经过专业培训,熟悉冲压设备的正确操作和维护方法;定期对冲压设备进行维护和检查,确保设备处于良好状态。
2.噪音污染冲压作业中产生的噪音污染不容忽视。
长期暴露在高噪音环境下可能导致听力受损、影响沟通以及增加压力和焦虑等。
预防措施:使用低噪音冲压设备和工具,如静音压力机、减震平台等;在冲压作业区域设置隔音设施,如隔音罩、隔音墙等;定期进行噪音检测,确保作业环境符合国家标准。
3.照明不足照明不足可能影响冲压作业的效率和安全性。
在昏暗的照明条件下,操作人员可能无法清晰地看到操作区域,从而可能导致误操作或意外伤害。
预防措施:确保冲压作业区域照明充足,满足国家相关标准;定期检查照明设施,及时更换损坏的灯具;操作人员应佩戴防护眼镜或其他视觉保护用品。
4.模具缺陷模具是冲压作业的核心部件,其缺陷可能导致产品质量问题或生产事故。
模具缺陷主要包括磨损、断裂、变形等,可能是由于材质问题、制造工艺不当或使用过程中维护不到位等原因引起的。
预防措施:选用合格的材料和制造工艺,确保模具质量;定期对模具进行检查和维护,及时发现并处理存在的缺陷;在模具使用过程中,加强对其状况的监控,防止出现安全事故。
5.操作不当冲压作业中的操作不当可能造成严重的危害。
操作人员不熟悉冲压设备的正确操作方法、未按照规定进行安全检查或违反安全规定等都可能引发事故。
预防措施:加强对操作人员的培训,确保他们熟悉冲压设备的操作方法和安全规定;操作人员在上岗前应经过充分的安全教育和考核;制定并执行严格的安全管理制度,严禁违章操作。
分析冲压作业存在的危险及预防措施

某飞机制造公司型材钣⾦冲压分⼚有4吨⾄450吨不同吨位的⼤⼩冲压设备30台。
由于航空⼯业的特点,该分⼚⽣产品种繁多,有各种冲压模具5000余套,⼯⼈每天⽤双⼿操作,⼿被伤害发⽣两起重⼤伤指事故。
请分析冲压作业存在的主要危险和导致的主要伤害,设为⾸页以及预防措施。
参考答案:
在机械⾏业,冲压作业伤指事故较多。
该⾏业曾流⾏⼀句话:⼗个冲⼯九个残。
客观原因是冲压机械滑块垂直下冲速度极快。
以⼀般100吨偏⼼冲床为例,滑块每分钟往复次数为75次,即单程⼀次只约需0.4秒。
采⽤⾏程为100毫⽶进⾏拉伸作业,若⼿在模内,冲床滑块下冲伤指的时间约为0.1秒。
⽽当操作者发现或感觉到滑块下冲时,反应到⼤脑,再由⼤脑指挥⼿缩回的时间约为0.2-0.3秒,显然⼿是来不及收回的。
因此常造成伤指事故。
把安全⼯程师站点加⼊收藏夹
为了保障操作⼯⼈的安全,企业必须重视冲压设备操作区的安全保护,安装必要的安全装置,采取有效的安全措施,将危险区与操作⼯⼈的⼿隔开或⽤强制的⽅法将操作⼯⼈的⼿推出危险区。
如防护栅栏保护装置、⼿推式保护装置、光电式防护装置、转板式护⼿装置及冲压拨⼿器、⾃动保护装置等。
另外冲压模具的安全化也⾮常重要。
设计模具时应把安全作为第⼀位来考虑,使操作者⼯作时有安全感。
如模具必须有排除危险的机构,防⽌操作者在送件、定位、取件或进⾏废料处理等操作时,不得不出现⾝体的某部分进⼊危险区域⽽触及模具可动部分被夹住或被弹出等危险情形。
冲压部品质管理中的过程控制与风险预防

冲压部品质管理中的过程控制与风险预防冲压工艺是一种广泛应用于制造业的加工方法,其在汽车、电子、家电等行业中扮演着重要角色。
在冲压过程中,保证产品质量的关键是过程控制与风险预防。
本文将探讨冲压部品质管理中的过程控制与风险预防的重要性,并介绍一些常用的方法与技术。
一、过程控制的重要性过程控制是指通过监测、调整和改进生产过程,以实现产品质量满足要求的一系列管理活动。
在冲压部品的制造过程中,仅仅依靠最终产品的质检是不够的。
由于冲压工艺涉及多个环节和复杂的制造流程,如果在过程控制上存在问题,会导致产品的偏差和缺陷。
因此,过程控制在冲压工艺中具有重要的地位。
首先,过程控制可以提高生产效率。
通过对冲压工艺参数进行监测和调整,可以及时发现和解决生产过程中的问题,避免生产中断和延误。
例如,对于冲压机的压力和速度进行实时监控,能够及时调整参数,保证生产效率的最大化。
其次,过程控制可以降低产品缺陷率。
在冲压过程中,产品出现尺寸不合格、表面质量差等问题是比较常见的。
通过对每个环节和工序的控制,可以及时发现并解决问题,保证产品的质量稳定性和一致性。
例如,在模具设计和制造中,使用先进的数控技术可以实现模具的高精度制造,减少产品尺寸误差。
最后,过程控制有助于提升产品的安全性和可靠性。
冲压部件在使用过程中,需要承受各种复杂的力和环境影响。
如果工艺参数不合理或操作不当,会导致产品的强度和密封性等性能下降,甚至出现安全隐患。
通过过程控制,可以确保产品在设计要求范围内的性能,提高产品的可靠性和安全性。
二、风险预防的策略与方法在冲压部品质管理中,风险预防是一个至关重要的环节。
通过预先发现和分析潜在的风险,可以采取相应的措施控制和消除风险,从而提升冲压部品生产的可靠性和稳定性。
首先,制定完善的制度和规范是预防风险的基础。
冲压部品的制造涉及多个环节和参与者,因此需要制定明确的工艺标准和操作规程,明确每个环节的职责和要求。
例如,在操作手册中详细规定操作流程、工艺参数、安全措施等内容,要求操作人员严格按照规定操作,减少操作误差和事故风险。
冲压安全风险点

冲压车间应保持良好的通风条件,以 降低空气中的粉尘和废气浓度,若通 风不良,将影响员工的健康和安全。
照明不足
车间内应有足够的照明设备,以保证 员工在操作过程中能够清晰地看到设 备和工件,若照明不足,将增加操作 失误和安全事故的风险。
PART 04
人员与培训风险
人员安全意识淡薄
安全操作规程未得到有效 执行
员工可能忽视或违反安全操作规程,导致冲 压设备操作不当,从而引发安全事故。
安全培训不足
员工缺乏必要的安全培训,对冲压设备的安 全操作和风险认知不足,容易引发安全事故
。
监督检查流于形式
监督检查频次不足
企业可能未对冲压设备进行定期的监督检查,导致设备存在的安全隐患无法及时发现和 整改。
定期检修维护不足
冲压设备需要定期进行全面的检修和维护,以确保其性能和 安全可靠性。但部分企业可能未能按照要求定期开展检修维 护工作,或者检修维护过程中存在漏检、漏修等问题,导致 设备的安全隐患无法及时发现和排除。
PART 02
物料与工艺风险
物料质量不稳定
1 2
原材料质量波动
由于供应商原因或运输过程中出现问题,导致原 材料质量不稳定,如板材厚度、硬度、表面质量 等不符合要求。
违规操作与疲劳工作
违规操作
操作人员可能违反安全操作规程,如超速、超载、超行程等,或者擅自改变设备的工作参数和状态, 从而引发安全事故。
疲劳工作
长时间连续工作或者熬夜工作可能导致操作人员疲劳过度,出现注意力不集中、反应迟钝等现象,增 加操作失误和事故发生的可能性。
应急处理能力不足
缺乏应急预案和演练
设备老化
冲压设备长时间使用后,可能会出 现磨损、腐蚀、疲劳等问题,导致 设备性能下降,安全可靠性降低。
安全风险点简述生产 冲压
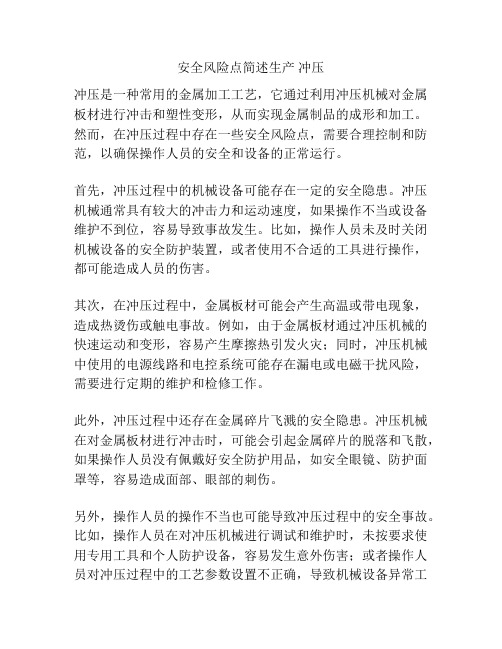
安全风险点简述生产冲压冲压是一种常用的金属加工工艺,它通过利用冲压机械对金属板材进行冲击和塑性变形,从而实现金属制品的成形和加工。
然而,在冲压过程中存在一些安全风险点,需要合理控制和防范,以确保操作人员的安全和设备的正常运行。
首先,冲压过程中的机械设备可能存在一定的安全隐患。
冲压机械通常具有较大的冲击力和运动速度,如果操作不当或设备维护不到位,容易导致事故发生。
比如,操作人员未及时关闭机械设备的安全防护装置,或者使用不合适的工具进行操作,都可能造成人员的伤害。
其次,在冲压过程中,金属板材可能会产生高温或带电现象,造成热烫伤或触电事故。
例如,由于金属板材通过冲压机械的快速运动和变形,容易产生摩擦热引发火灾;同时,冲压机械中使用的电源线路和电控系统可能存在漏电或电磁干扰风险,需要进行定期的维护和检修工作。
此外,冲压过程中还存在金属碎片飞溅的安全隐患。
冲压机械在对金属板材进行冲击时,可能会引起金属碎片的脱落和飞散,如果操作人员没有佩戴好安全防护用品,如安全眼镜、防护面罩等,容易造成面部、眼部的刺伤。
另外,操作人员的操作不当也可能导致冲压过程中的安全事故。
比如,操作人员在对冲压机械进行调试和维护时,未按要求使用专用工具和个人防护设备,容易发生意外伤害;或者操作人员对冲压过程中的工艺参数设置不正确,导致机械设备异常工作,增加了事故发生的风险。
针对以上安全风险点,可以采取一系列的安全措施来进行防范和控制。
首先,针对冲压机械设备本身,可以加强设备的安全防护装置,如安全门、安全栅栏等,确保操作人员在设备运行时无法接触到危险区域;同时,需要加强设备的定期检修和维护工作,保证设备的正常运行和安全性能。
其次,应加强对操作人员的培训和安全教育,提高其安全意识和操作技能。
操作人员应严格按照操作规程进行操作,使用专用工具和个人防护用品,确保自身的安全。
另外,应建立健全的安全管理制度和操作规程,明确冲压过程中的安全要求和操作流程。
冲压作业危险分析
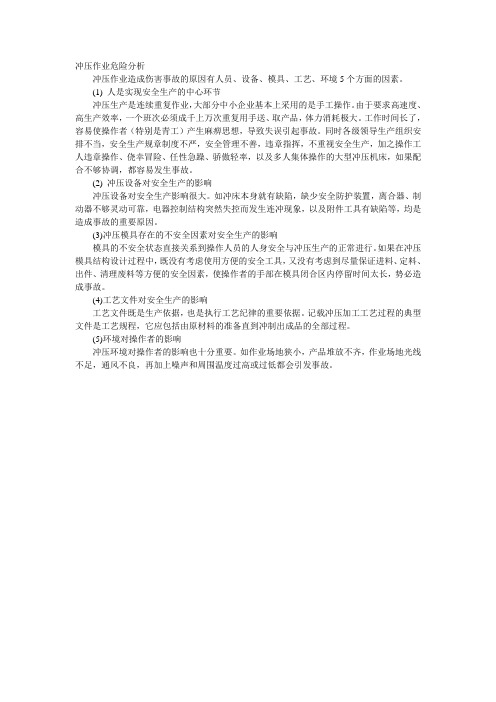
冲压作业危险分析
冲压作业造成伤害事故的原因有人员、设备、模具、工艺、环境5个方面的因素。
(1) 人是实现安全生产的中心环节
冲压生产是连续重复作业,大部分中小企业基本上采用的是手工操作。
由于要求高速度、高生产效率,一个班次必须成千上万次重复用手送、取产品,体力消耗极大。
工作时间长了,容易使操作者(特别是青工)产生麻痹思想,导致失误引起事故。
同时各级领导生产组织安排不当,安全生产规章制度不严,安全管理不善,违章指挥,不重视安全生产,加之操作工人违章操作、侥幸冒险、任性急躁、骄傲轻率,以及多人集体操作的大型冲压机床,如果配合不够协调,都容易发生事故。
(2) 冲压设备对安全生产的影响
冲压设备对安全生产影响很大。
如冲床本身就有缺陷,缺少安全防护装置,离合器、制动器不够灵动可靠,电器控制结构突然失控而发生连冲现象,以及附件工具有缺陷等,均是造成事故的重要原因。
(3)冲压模具存在的不安全因素对安全生产的影响
模具的不安全状态直接关系到操作人员的人身安全与冲压生产的正常进行。
如果在冲压模具结构设计过程中,既没有考虑使用方便的安全工具,又没有考虑到尽量保证进料、定料、出件、清理废料等方便的安全因素,使操作者的手部在模具闭合区内停留时间太长,势必造成事故。
(4)工艺文件对安全生产的影响
工艺文件既是生产依据,也是执行工艺纪律的重要依据。
记载冲压加工工艺过程的典型文件是工艺规程,它应包括由原材料的准备直到冲制出成品的全部过程。
(5)环境对操作者的影响
冲压环境对操作者的影响也十分重要。
如作业场地狭小,产品堆放不齐,作业场地光线不足,通风不良,再加上噪声和周围温度过高或过低都会引发事故。
冲压工艺危险源辨识与风险评价方案
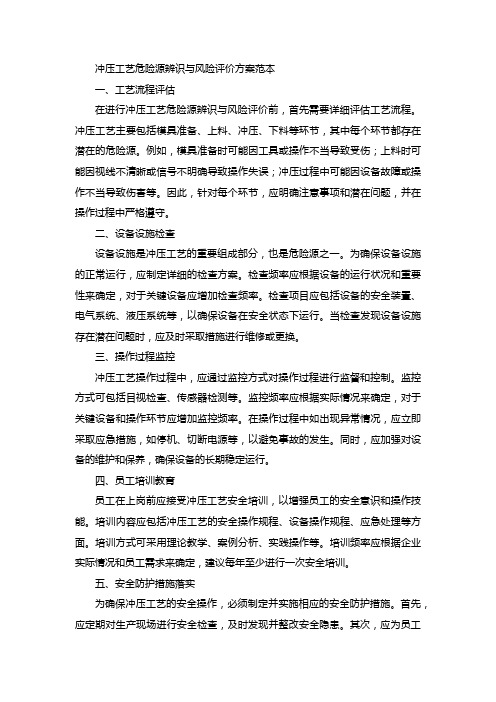
冲压工艺危险源辨识与风险评价方案范本一、工艺流程评估在进行冲压工艺危险源辨识与风险评价前,首先需要详细评估工艺流程。
冲压工艺主要包括模具准备、上料、冲压、下料等环节,其中每个环节都存在潜在的危险源。
例如,模具准备时可能因工具或操作不当导致受伤;上料时可能因视线不清晰或信号不明确导致操作失误;冲压过程中可能因设备故障或操作不当导致伤害等。
因此,针对每个环节,应明确注意事项和潜在问题,并在操作过程中严格遵守。
二、设备设施检查设备设施是冲压工艺的重要组成部分,也是危险源之一。
为确保设备设施的正常运行,应制定详细的检查方案。
检查频率应根据设备的运行状况和重要性来确定,对于关键设备应增加检查频率。
检查项目应包括设备的安全装置、电气系统、液压系统等,以确保设备在安全状态下运行。
当检查发现设备设施存在潜在问题时,应及时采取措施进行维修或更换。
三、操作过程监控冲压工艺操作过程中,应通过监控方式对操作过程进行监督和控制。
监控方式可包括目视检查、传感器检测等。
监控频率应根据实际情况来确定,对于关键设备和操作环节应增加监控频率。
在操作过程中如出现异常情况,应立即采取应急措施,如停机、切断电源等,以避免事故的发生。
同时,应加强对设备的维护和保养,确保设备的长期稳定运行。
四、员工培训教育员工在上岗前应接受冲压工艺安全培训,以增强员工的安全意识和操作技能。
培训内容应包括冲压工艺的安全操作规程、设备操作规程、应急处理等方面。
培训方式可采用理论教学、案例分析、实践操作等。
培训频率应根据企业实际情况和员工需求来确定,建议每年至少进行一次安全培训。
五、安全防护措施落实为确保冲压工艺的安全操作,必须制定并实施相应的安全防护措施。
首先,应定期对生产现场进行安全检查,及时发现并整改安全隐患。
其次,应为员工提供符合国家标准的劳动保护用品,如安全鞋、手套、头盔等。
此外,应在设备周围设置安全防护栏、警示标识等,以避免员工误操作或意外触碰危险部位。
冲压安全生产事故分析及预防措施

冲压安全生产事故分析及预防措施冲压安全生产事故是指在冲压工艺中出现的各种伤害员工生命和财产的意外事件。
这些事故一般由于疏忽、操作不当、设备故障等原因引起。
为了确保冲压工作场所的安全和员工的健康,必须对冲压安全生产事故进行全面分析,并采取相应的预防措施。
一、冲压安全生产事故分析1.人为疏忽:冲压工艺存在许多紧急状态和危险环境,如果员工没有足够的警惕和专注,就很容易出现疏忽行为,导致事故发生。
2.操作不当:冲压机操作需要掌握一定的技术和经验,如果员工没有经过专业的培训和指导,就可能出现错误操作,引发事故。
3.设备故障:冲压机在运行过程中可能会出现各种故障,如传感器失灵、控制系统故障等,如果没有及时发现和排除,就可能导致事故发生。
4.缺乏安全管理:一些冲压厂家对安全管理不重视,没有制定相应的安全规范和操作规程,员工没有明确的安全作业流程和安全技术培训,容易引发事故。
二、冲压安全生产事故预防措施1.建立完善的安全管理系统:冲压厂家必须建立起一套完善的安全管理体系,包括制定安全规章制度、安全操作规程、安全防护措施等,确保员工安全作业。
2.加强员工培训:冲压厂家应对所有从事冲压工作的员工进行全面的安全技术培训,使他们具备应对紧急情况的能力,提高他们识别危险和采取应急措施的能力。
3.定期设备检查和维护:冲压机的安全性能与定期检查和维护密切相关,冲压厂家应制定检查和维护计划,对冲压设备进行定期检查和维护,确保设备正常运行。
4.加强管理监督:应建立健全的安全生产管理监督体系,加强对冲压厂家的管理监督,定期进行安全生产检查和评估,发现安全隐患及时整改,确保冲压工作场所的安全和员工的健康。
5.完善安全防护设施:冲压厂家应在工作场所设置各种安全防护设施,如防护网、安全警示标识、应急疏散通道等,提高员工的安全意识和安全防范能力。
6.加强事故管理和应急预案:冲压厂家应建立健全的事故报告和应急预案,事故发生后及时进行事故原因分析和教训总结,制定相应的预防措施,避免类似事故再次发生。
冲压作业的危险因素及安全措施分析

• 88 •内燃机与配件冲压作业的危险因素及安全措施分析李晓静(河北省石家庄市栾城区安全生产监督管理局)摘要:冲压作业过程中存在许多危险因素,且危险性较大。
本文旨在通过对这些危险因素的分析,找到有效的应对措施,以减少冲 压作业中的伤害事故。
关键词院冲压;危险因素;防范措施0引言冲压作业具有较大危险性和事故多发性的特点,且事 故造成的伤害一般都较为严重,在作业过程中,应采取多 种形式的安全防范措施,尽可能减少或避免伤害事故。
1物的危险因素及防范措施1.1设备结构的危险性常用的冲压机械设备由剪板机、曲柄压力机和液压机 等部件组成。
许多冲压设备采用的是刚性离合器,利用凸 轮机构使离合器接合或脱开,一旦接合运行,就一定要完 成一个全环后才会停止,这个特性极易导致伤害事故的发 生。
比如:光电保护和操纵装置失灵,引起设备动作失控,导致人体进入冲模区,或者开□处未设置联锁装置或联锁 装置失灵导致人体进入冲模区,而滑块在下降过程中无法 及时停止,造成机械伤害。
设备零部件在使用中因磨损和 强烈冲击产生松动变形或损坏,引起零部件脱落飞出,引发伤害事故等。
1.2模具的危险性冲压事故多数发生在冲头下取料和冲模中取冲件时,而模具结构设计不合理,既没有考虑使用方便的安全工 具,又没有考虑到尽量保证进料、定料、出件、清理废料等 方面的安全因素,使操作者的手部在模具闭合区内停顿时 间太长,造成事故。
另外,模具在使用中因磨损和强烈冲击 造成变形或损坏,引起模具掉落伤人等,造成事故。
1.3杜绝设备、模具的不安全状况要采取多种应对措施,杜绝设备、模具的不安全状况。
配置一种或多种安全装置,多个侧面接触危险区域则应在 每个侧面提供安全装置,设置的光电保护装置和双手操纵 装置应分别符合规定;冲压生产线工作区域防护栅栏的开 □处应与主机联锁,确保主机运动停止后防护栅栏的门才 能够打开,设备维护检修时应使用能量锁定装置。
开机前检查设备的润滑系统、机械系统、安全防护装 置是否齐全、完好;各连接螺栓及零件是否紧固,离合器、制动器是否完整,操作灵活;检查模具是否紧固,有无裂 纹,保险装置等是否完好有效;暴露在机床外的转动部件,如果在没有安全防护装置的情况下开车或试车,容易造成 身体伤害事故;松动的螺栓或零部件、模具在设备运行中,极易脱落,造成人身伤害,此时发现转动部件松动、模具松 动或有缺陷,应立即停止进行修理。
冲压作业伤害分析及标识管理(4篇)

冲压作业伤害分析及标识管理冲压作业是指通过冲裁、剪裁、拉伸等方式,将金属板材加工成所需形状的工艺。
由于冲压作业涉及到各种复杂的冲击、挤压和拉伸过程,工人在进行冲压作业时往往面临着一定的伤害风险。
本文将对冲压作业的伤害问题进行分析,并提出相应的标识管理措施。
冲压作业的伤害问题主要有以下几个方面:1. 机械伤害:在冲压作业中,机械设备的运动部件如冲头、刀具等可能造成工人的损伤。
例如,当金属板材被冲头冲击时,如果操作不规范,很容易夹伤手指或者手部其他部位。
此外,由于冲压作业速度较快,工人也可能被冲击产生的金属屑或者碎片击伤。
2. 物理伤害:冲压作业时,金属板材的弯曲、挤压和拉伸等过程会产生大量的能量释放,如切割时产生的淋巴浮沫等。
这些能量释放会导致工人受到切、割、挤、夹等物理伤害。
3. 化学伤害:在冲压作业中,涉及到的金属板材和润滑油等材料可能对工人造成化学伤害。
例如,金属板材中可能含有有害物质,如铅、氟等,长期接触这些物质可能对工人的健康产生不良影响。
此外,冲压作业中所使用的润滑油等化学物质也可能对工人造成伤害。
为了防止冲压作业中的伤害问题,可以采取以下标识管理措施:1. 设置警示标识:对于可能造成机械伤害的设备和工作区域,应设置明显的警示标识,警示工人注意安全。
标识应清晰明了,易于辨认,并应进行定期检查和维护,确保其有效性。
2. 安装安全护栏:对于冲压作业中涉及到的危险区域,应设置安全护栏或隔离带,阻止未经授权人员进入,并用明显的标识标明危险区域。
3. 提供个人防护装备:为了防止工人在冲压作业中受伤,应提供适当的个人防护装备,如安全帽、防护眼镜、手套等。
同时,应对工人进行相应的培训,确保其正确使用个人防护装备。
4. 定期维护设备:对于用于冲压作业的设备,应定期进行维护和检修,确保其正常运行。
设备维护记录应详细记录,包括维护时间、内容以及维护人员等信息。
5. 使用安全材料:为了防止冲压作业中的化学伤害问题,应选用符合相关标准的金属板材和润滑油等材料,并确保其质量和供应来源可靠。
金属冲压行业安全管理与风险评估方法探讨
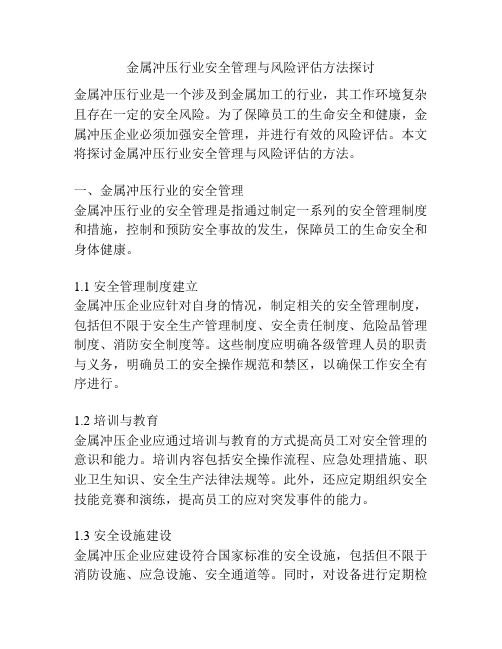
金属冲压行业安全管理与风险评估方法探讨金属冲压行业是一个涉及到金属加工的行业,其工作环境复杂且存在一定的安全风险。
为了保障员工的生命安全和健康,金属冲压企业必须加强安全管理,并进行有效的风险评估。
本文将探讨金属冲压行业安全管理与风险评估的方法。
一、金属冲压行业的安全管理金属冲压行业的安全管理是指通过制定一系列的安全管理制度和措施,控制和预防安全事故的发生,保障员工的生命安全和身体健康。
1.1 安全管理制度建立金属冲压企业应针对自身的情况,制定相关的安全管理制度,包括但不限于安全生产管理制度、安全责任制度、危险品管理制度、消防安全制度等。
这些制度应明确各级管理人员的职责与义务,明确员工的安全操作规范和禁区,以确保工作安全有序进行。
1.2 培训与教育金属冲压企业应通过培训与教育的方式提高员工对安全管理的意识和能力。
培训内容包括安全操作流程、应急处理措施、职业卫生知识、安全生产法律法规等。
此外,还应定期组织安全技能竞赛和演练,提高员工的应对突发事件的能力。
1.3 安全设施建设金属冲压企业应建设符合国家标准的安全设施,包括但不限于消防设施、应急设施、安全通道等。
同时,对设备进行定期检修和维护,确保设备的安全性和可靠性。
二、金属冲压行业的风险评估方法风险评估是指对工作环境和工作过程中可能存在的危险进行识别、分析和评估的过程,以确定相应的控制措施。
2.1 风险识别通过在金属冲压企业中进行现场观察和访谈,识别可能存在的危险。
包括但不限于机械设备的安全性、电气设备的安全性、危险品的存储和使用、作业环境的危险因素等。
2.2 风险分析对识别出的风险进行分析,包括可能导致的伤害、事故的频率和后果等。
通过分析,可以确定潜在风险的严重性和紧急性。
2.3 风险评估根据风险分析的结果,对风险进行评估,确定其优先级。
一般可以使用如下四个级别进行评估:极高风险、高风险、中风险和低风险。
根据评估结果,制定相应的控制措施。
2.4 风险控制根据风险评估的结果,制定相应的控制措施,包括工作环境改善、工艺流程改进、安全设施配备等。
- 1、下载文档前请自行甄别文档内容的完整性,平台不提供额外的编辑、内容补充、找答案等附加服务。
- 2、"仅部分预览"的文档,不可在线预览部分如存在完整性等问题,可反馈申请退款(可完整预览的文档不适用该条件!)。
- 3、如文档侵犯您的权益,请联系客服反馈,我们会尽快为您处理(人工客服工作时间:9:00-18:30)。
冲压生产的危险性分析与风险控制冲压生产属于产品精致成型工艺,普遍应用于机械、电子和轻工产品生产。
但由于冲压生产具有较大作业危险和事故多发的特点,且事故造成伤害一般都较为严重,不少人对冲压工作心存畏惧,以至目前在一些地方招收冲压工都比较困难。
防止冲压伤害事故的安全技术措施有多种形式,但就单机人工作业而言,目前尚不可能确认任何一种防护措施绝对安全。
应该看到,单纯让作业人员接受防护装置的被动保护并不能完全有效地防止事故。
要减少或避免事故,必须加强冲压生产的技术安全管理,重要的是要让作业人员消除畏惧心理,以良好的心态上岗工作,提高作业人员的技能水平和安全意识,使他们能够识别冲压生产过程中的危险所在。
据对一些冲压作业人员所进行的调查了解,多数人对冲压生产危险的畏惧心理是盲目的,较少有人能从主观上对这些危险进行正确认识。
而不能正确认识危险就不能有效地控制危险,这是目前冲压事故多发的主要原因。
一、冲压伤害事故的主要发生原因冲压工作主要危险是冲指伤害事故。
一般普通冲床的冲指事故以发生在模具上下行程间为绝大多数,伤害部位主要是作业者的手部,即当操作者手部处于模具行程间时模块下落,就造成了冲手事故。
伤害事故也可能发生在冲压设备的其他危险部位,如转动和传动机构绞伤,模具安装、拆卸时砸伤、挤伤及工件挤飞或冲模、工具崩碎伤人等情况。
我们仅以冲指伤害事故为典型,将“手在模具内”和“模块下落”作为造成冲压事故的主要因素,按事故致因理论进行系统分析后可以看出,设备缺陷和人的行为错误是发生事故的主要原因和危险。
二、冲压作业中的主要危险源分析根据冲压伤害事故发生的原因分析,冲压作业中的危险主要有以下几个方面:1.冲压设备的危险冲压设备由其本身结构和功能特点所决定,运行中具有明显的危险性。
目前所使用的普通冲床,相当一部分采用的是刚性离合器。
这种刚性离合器结构是用凸轮机构使离合器接合或断开,一旦接合,就要完成一个全循环过程,即滑块从上死点下行经下死点返回上死点才能停止,中途滑块无法停止运行。
假如在此循环过程的模具下行阶段,恰好手在模具中,就必然会发生伤手事故。
其次,设备在运行中还会受到经常性的强烈冲击和震动,使一些零部件变形、磨损以至碎裂,引起设备动作失控而发生危险的连冲现象。
而设备的开关控制系统由于人为或外界因素也可能引起意外的误动作,这样的危险性更大。
另外设备的转动、传动部位具有可能造成机械性伤害事故的明显危险。
这些危险对作业人员的安全构成了客观威胁。
除此以外,使用带病运行的设备很难保证安全。
2.模具的危险模具是整个冲压加工系统的重要组成部分,它担负着使工件加工成型的主要功能,是整个系统能量的集中释放部位。
绝大部分冲压伤害事故就发生在这里,可以说是冲压作业的“老虎口”。
许多冲压伤害事故发生的主要原因,也在于模具设计或有缺陷。
如果技术人员在设计模具时仅考虑工作的完成,而没有考虑到操作人员工作时可能因模具而导致出现不安全动作,操作者的手要直接或经常性地伸进模具间才能完成一个作业过程,那么这副模具安全性就低。
模具经长期使用,也可能会因磨损、变形或损坏等缺陷,而在正常运行条件下发生意外导致事故。
3.作业环境的危险在发生的冲压伤害事故中,有相当一部分是由于作业环境中的某些危险性因素所致。
作业环境中的危险性因素是多方面的,但从导致冲压伤害事故的可能性来看,主要是以下几个方面:⑴设备布局不合理。
一般冲压车间的设备布局应按产品的工艺流程布置,但笔者在不少企业的冲压车间看到,各种冲压设备是按类型排列的,这样就使工件和原材料在车间内重复周转,容易造成生产场地拥挤,安全通道和设备间隔被占,作业空间缩小,作业者的正常操作动作受到影响。
另外一种情况是设备排列过于拥挤,相邻工位互相影响,造成操作者工作时思想不集中,以至操作失误的可能性大大提高。
⑵工位器具和材料摆放无序。
造成此种情况可能是上述场地拥护、混乱所致,也可能是作业者人为的原因。
在此情况下作业人员的操作动作无规则,难以达到标准化要求,由此可能手脚配合失调而出现操作失误和其他意外。
⑶机台附近产品或原材料堆放过多、过乱。
由于工件和材料不能及时转送,废料不及时清理,特别是机台附近产品码放过多、过高,可能会因这些物品突然倒塌而砸碰脚踏开关,造成冲床误动作。
这是冲压生产中最危险的现象,有不少血的教训。
⑷座位不稳,高度不当。
这会使作业人员操作时动作勉强、重心不稳,从而易于疲劳或身体失衡发生意外。
这几方面的危险性都很容易造成事故。
笔者所在单位就发生过因工件倒塌砸碰脚踏开关和因座椅晃动失衡手脚配合失调而造成的严重冲手事故。
除此以外,车间里的震动和噪声、天车过空行驶及其作业信号,其他工种的作业干扰等,对冲压作业人员的安全操作都有明显的影响,都具有引发冲压伤害事故的危险。
4.作业行为的危险大量的冲压伤害事故表明,作业者的不安全行为是造成事故的最危险因素。
一般来说,事故都是违反操作者本身意志的。
实际作业中操作者因自己的行为而引发的事故,主要在于他们对自己不正确行为的危险性认识不够,安全意识缺失。
操作者由于个人素质差别,在生产中可能因安全生产知识不足、安全技能水平不高、作业态度不端正以及身体不佳等原因而出现违章、冒险、蛮干等不安全行为。
这些不安全行为具体表现为:工作准备不充分,操作方法不当,作业位置不安全,操作姿势不正确,动作不协调,辅助工具和防护用品使用不当等。
作业者也可能因不良的生理、心理状态和性格特点等原因产生一些不安全行为。
不良的生理状态直接表现为生理缺陷,如视力、听力不佳及其他功能失常等都会使作业者在工作中判断失误或动作失调。
不良的心理状态则表现为心理疲劳、情绪不稳,操作者可能因此而产生一些不自主的下意识行为和动作失误,也可能出现明知故犯、违章作业等非理智行为。
不良心态还会使作业者表现出责任心不强,心理紧张、精力不集中。
在这种心态下,作业者的行为不可能是安全的。
而从不良的性格特点来看,则无论是马虎愚钝型还是急躁轻浮型,其表现在作业行为上都有一定的危险性。
三、作业危险与事故风险大多数冲压作业人员对上述作业危险的存在没有清楚认识,人们仅因大量发生的冲压伤害事故而对冲压作业产生畏惧心理。
然而上述这些危险是否都必然会转化为伤害事故呢?一般来说,上述危险只是冲压作业系统中潜在的事故源,它并不可能都转化为事故,只有在一定的条件下危险才会导致事故。
而危险向事故转化的可能性与系统的安全性(安全措施)有关。
这种可能性就是系统的事故风险,它与系统潜在危险成正比,与系统所采取的安全措施成反比。
冲压生产系统具有明显的较高事故风险,但系统的高危险性并不一定意味着事故的必然。
就同一冲压作业系统而言,其本身所具有的危险,对有的人来说可以永远不会转化为事故,而对另一些人而言,危险则会使他们付出血的代价。
这是因为前者对系统有着充分的了解,能识别出并能有效地控制住系统的危险,且始终遵循安全第一、质量第二、生产第三的冲压作业原则,可以保持长时期安全生产而不出事故。
而后者或许没有经过岗前安全技术培训,对系统没有深入的了解,作业时不能严格遵守安全操作规程,更不能识别出和控制住系统中的潜在危险,可能上岗不久就会发生事故。
因此,同一作业系统对这些人就有很大的事故风险,而对前者则事故风险为“零”。
四、作业场所危险标识管理由于冲压作业过程中客观存在着上述危险,操作者如能及时和充分识别并控制这些危险,对安全作业有很重要的实际意义。
如何提高作业人员对危险的识别能力呢?笔者认为,除了对他们进行经常性的和专门的冲压安全技术培训以提高安全技能水平外,企业能够容易做到的工作就是对冲压作业系统中的危险进行标识管理。
一般标识管理工作应从以下几个方面考虑:1.车间标识:对于集中作业的冲压车间,应进行专门的安全管理。
车间必须有明显的安全警语和安全标志牌,以作危险标识。
车间要制订严格的安全管理制度和安全操作规程,这些规章制度力求简明扼要,并用醒目文字展示于车间合适地方。
2.区域标识:按国家有关标准要求,车间通道和作业场所应以区域线分开。
车间通道用白色粗线按标准要求划出,划出的通道应保持畅通,不得任意挤占。
作业场所用黄色区域线划出,范围应以作业点为中心,以操作空间大小为基准,划出合适的作业区域。
3.设备标识:按国家相关规定,冲压设备上应有铭牌、各种操作指示、安全与警告性指示,这是设备的基本标识。
冲压设备形式多样,也可从其吨位大小、运行速度、技术状况和使用频数等综合安全性能考虑进行分类挂牌标识。
分类办法可与设备管理相结合,采用ABC分类管理方法,对综合危险性较大的在用设备挂黄色A牌,次之挂蓝色B牌,一般不易发生事故的设备挂绿色C牌,并让职工了解三种牌子的含义,以便上岗即可看出设备的危险性。
4.模具标识:可按国家标准要求,对使用的模具分别涂红、黄、蓝、绿色,对无防护装置而手又经常要伸入模具间的危险模具涂以红色。
一般模具涂黄色;对附有防护装置或可用辅助送料工具的模具涂蓝色;安全模具涂绿色。
为方便模具管理和易于识别,色标应涂在下模底部的正前方。
5.工艺标识:根据有关工艺制定标准规定,冲压作业工艺制定应考虑到操作时的安全。
对工艺过程中可能出现的危险,要编写相应的工艺措施。
并在工艺文件中突出标出。
但目前不少冲压工艺人员没有做到这一点,某些不合理的工艺可能导致事故。
因此,工艺人员在制定加工工艺时,必须对所用设备和模具以及所用材料等都要做到心中有数。
限于条件必须要采取具有危险的特殊工艺步骤时,必须要在工艺文件上突出标明其危险,并对所采取的安全措施作出具体要求。