提高加工中心使用效率实例一则
提高数控机床机械加工效率的有效措施

提高数控机床机械加工效率的有效措施数控机床是现代机械加工领域中的重要设备,其高效率和高精度的加工特性使其在工业生产中得到广泛应用。
为了提高数控机床的机械加工效率,可以采取以下有效措施:1. 优化刀具选择:选择合适的刀具材料和刀具类型并合理配置刀具数量,以提高切削力和加工速度,提高加工效率。
根据加工材料的不同选择适当的刀具涂层和刀具形状,以提高切削效果。
2. 优化切削参数:根据不同加工材料的特性和加工要求,合理选择切削速度、进给速度和切削深度等切削参数,以最大限度地提高切削效率。
3. 优化工艺路线:在设计加工工艺时,应尽量减少切削次数和换刀次数,合理安排切削路径和切削方法,以减少无效运动和切削时间,提高加工效率。
4. 提高机床刚性:加强机床的刚性设计和加工精度控制,以提高机床的稳定性和抗振能力,减少振动对加工质量的影响,提高加工效率。
5. 优化工件夹持方式:选择合适的夹具和夹具方式,以提高工件的定位精度和刚性,减少因工件变形而导致的加工误差和重复定位误差,提高加工效率。
6. 加强机床维护保养:定期对数控机床进行维护保养,保持机床的良好状态和稳定性,及时更换磨损零部件,减少故障发生,提高机床的可靠性和加工效率。
7. 加强操作人员培训:对操作人员进行专业培训,提高他们的操作技能和加工理论知识,使其熟练掌握数控机床的操作方法和各项功能,以提高加工效率。
8. 应用智能化技术:利用智能化技术,如人工智能和大数据分析等,对数控机床进行优化配置和智能化管理,提高加工过程的自动化水平,提高加工效率。
9. 采用高效的切削液和冷却系统:选择高效的切削液和冷却系统,有效降低切削温度,减少切削热对刀具和工件的影响,提高切削效率和加工质量。
10. 优化加工方案和工艺改进:通过不断的研究和实践,对加工方案进行优化和改进,采用新的加工方法和工艺,以提高加工效率和质量。
提高数控机床机械加工效率需要综合考虑刀具选择、切削参数、工艺路线、机床刚性、工件夹持、机床维护、操作人员培训、智能化技术、切削液和冷却系统等因素,通过适当的优化和改进措施,可以提高数控机床的机械加工效率。
提高数控机床机械加工效率的有效措施

提高数控机床机械加工效率的有效措施随着工业化的不断发展,数控机床在各种制造行业中发挥着重要的作用。
数控机床以其高精度、高效率、多功能等特点,越来越受到制造业的青睐。
要想发挥数控机床的最大作用,提高其机械加工效率,需要制定一系列有效的措施。
本文将重点介绍如何提高数控机床机械加工效率的有效措施。
一、合理规划生产工艺合理规划生产工艺是提高数控机床机械加工效率的基础。
在生产加工中,应该根据产品的材质、尺寸、形状和加工要求等因素,制定出科学合理的加工工艺流程。
这包括选择合适的刀具、切削参数、加工路线等。
通过合理规划生产工艺,可以有效地减少加工时间,提高数控机床的加工效率。
二、提高数控编程水平数控编程是数控机床加工的关键环节,直接影响到加工效率和加工质量。
提高数控编程水平,是提高数控机床机械加工效率的重要措施。
编程人员应该熟练掌握数控编程知识和技术,能够根据产品要求,合理编写加工程序,精准控制加工过程,提高加工效率和加工质量。
三、优化数控加工参数优化数控加工参数是提高数控机床机械加工效率的重要途径。
通过合理调整切削速度、进给速度、切削深度、切削宽度等参数,可以在保证加工质量的前提下,提高数控机床的加工效率。
在实际生产中,应该根据加工材料的性能特点和加工要求,不断优化数控加工参数,使之达到最佳状态,实现高效加工。
四、选择优质刀具和夹具刀具和夹具是数控机床加工过程中不可或缺的重要设备。
选择优质的刀具和夹具,对于提高数控机床机械加工效率具有至关重要的作用。
优质的刀具和夹具能够提高加工的稳定性和精度,降低刀具磨损,延长使用寿命,减少更换和调整时间,提高加工效率。
五、加强设备维护和保养设备维护和保养是保证数控机床长期稳定运行的关键。
合理的维护和保养措施可以有效地降低设备故障率,延长设备寿命,保证设备在高效运转。
定期对数控机床进行全面的保养,包括对润滑系统、冷却系统、传动系统、精密传感器等部件进行检查和调整,及时更换易损件,保持设备在最佳状态,以提高加工效率。
加工中心宏程序编程实例

加工中心宏程序编程实例在加工中心的自动化加工过程中,宏程序编程是一项重要的技术。
通过编写宏程序,我们可以实现多道工序的连续加工,提高加工效率和精度。
下面,我将通过一个实例来介绍加工中心宏程序的编程过程。
假设我们需要在一块钢板上进行钻孔、铣削和镗孔三道工序。
首先,我们需要确定加工中心的坐标系和参考点。
假设我们以钢板的左下角为原点,并将钢板的左侧边缘和下侧边缘作为加工中心的X轴和Y轴。
第一道工序是钻孔。
我们假设钻孔的位置为(100, 50),即以加工中心坐标系为基准,钻孔位于距离X轴100mm、距离Y轴50mm的位置。
钻孔的直径为10mm,我们可以使用G81指令来编写钻孔的宏程序。
G90 G54 G00 X100 Y50 ; 将坐标系移动到钻孔位置T01 ; 选择钻头G81 X100 Y50 Z-10 R2 F500 ; 钻孔指令,X、Y为钻孔位置,Z为钻孔深度,R为回退平面,F为进给速度M30 ; 结束程序接下来是铣削工序。
假设铣削的位置为(150, 80),即以加工中心坐标系为基准,铣削位于距离X轴150mm、距离Y轴80mm的位置。
铣削的宽度为20mm,我们可以使用G01指令来编写铣削的宏程序。
G90 G54 G00 X150 Y80 ; 将坐标系移动到铣削位置T02 ; 选择铣刀G01 X170 Y80 Z-5 F1000 ; 铣削进给指令,X、Y为终点位置,Z为下刀深度,F为进给速度G01 X170 Y80 Z-10 ; 铣削下刀指令,Z为下刀深度G01 X150 Y80 Z-10 ; 铣削上刀指令,Z为上刀位置M30 ; 结束程序最后是镗孔工序。
假设镗孔的位置为(200, 100),即以加工中心坐标系为基准,镗孔位于距离X轴200mm、距离Y轴100mm的位置。
镗孔的直径为15mm,我们可以使用G85指令来编写镗孔的宏程序。
G90 G54 G00 X200 Y100 ; 将坐标系移动到镗孔位置T03 ; 选择镗刀G85 X200 Y100 Z-20 R2 F500 ; 镗孔指令,X、Y为镗孔位置,Z为镗孔深度,R为回退平面,F为进给速度M30 ; 结束程序通过以上三段宏程序的编写,我们可以实现钻孔、铣削和镗孔三个工序的连续加工。
提高数控加工中心切削效率的途径

提高数控加工中心切削效率的途径作者:赵晓阳来源:《神州·中旬刊》2017年第12期摘要:近年来我国经济高速发展,各行各业的竞争力也越来越大。
企业为了提高自身在市场中的竞争力,不得不开始进行技术改革,力求用最少投资获取运行可靠、功能强、精度高的机床。
如何提高加工效率是每个加工企业应该思考的重要问题。
本文首先对数控加工进行概述,然后针对如何提高数控加工中心切削效率的策略进行探讨,以供参考。
关键词:数控加工;中心切削;提升效率随着科学技术的发展,各种高科技被广泛运用于各行各业。
在制造业当中,数控加工已经成为主要的生产力代表,模具、航空、机械等多方面均发挥着重要的作用。
为了进一步提高企业市场竞争力,企业相关人员也在不断思考提高数控加工中心切削效率的方法。
目前,工艺安排、切削用量、刀具材料等都是影响切削效率的重要因素,也是困扰我国制造行业的重要问题。
1.数控加工概述1.1国内外加工中心切削水平的差异切削速度是影响数控加工中心切削效率的重要因素,在先进国家,其中,机床主轴转速每分钟已经超过三万转,部分甚至高达十万转[1]。
而车削、铣削的切削速度也达到每分钟5000到8000转左右。
但是,国内的切削速度却远低于先进国家,正常速度仅为先进国家的1/12到1/15左右,导致国内切削效率远远低于先进国家。
因此,在国内很多加工企业,如何降低废品率,提高加工效率是一种重要问题。
此外,除了切削速度,国内数控加工中心还普遍存在工艺设备不配套、加工光洁度低、刀片跳动量大、刀具精度低等问题,严重影响加工效率。
1.2高速切削工艺在数控加工的优势数控加工当中,高速切削工艺已经被广泛应用,优势也表现的越来越明显。
首先,高速切削可以提高生产效率。
在高中切削工艺当中,一般给进率比较大,材料切除效率也能提高3到6倍左右。
第二,降低了切削力。
在高速切削工艺当中,切削宽度窄、切削深度浅、因此切削力比较小。
第三,提高了加工质量。
由于切削深度和宽度比较小,工件和刀具的变形量也会随之减小,尺寸的精确性和加工质量也会相应提高。
数控加工提升效率方案
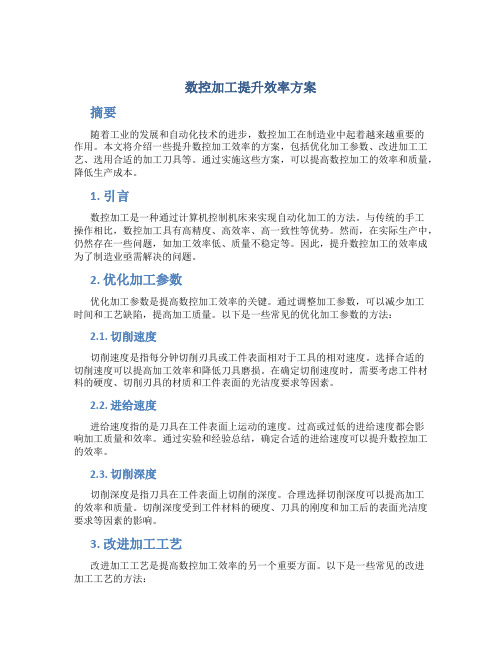
数控加工提升效率方案摘要随着工业的发展和自动化技术的进步,数控加工在制造业中起着越来越重要的作用。
本文将介绍一些提升数控加工效率的方案,包括优化加工参数、改进加工工艺、选用合适的加工刀具等。
通过实施这些方案,可以提高数控加工的效率和质量,降低生产成本。
1. 引言数控加工是一种通过计算机控制机床来实现自动化加工的方法。
与传统的手工操作相比,数控加工具有高精度、高效率、高一致性等优势。
然而,在实际生产中,仍然存在一些问题,如加工效率低、质量不稳定等。
因此,提升数控加工的效率成为了制造业亟需解决的问题。
2. 优化加工参数优化加工参数是提高数控加工效率的关键。
通过调整加工参数,可以减少加工时间和工艺缺陷,提高加工质量。
以下是一些常见的优化加工参数的方法:2.1. 切削速度切削速度是指每分钟切削刃具或工件表面相对于工具的相对速度。
选择合适的切削速度可以提高加工效率和降低刀具磨损。
在确定切削速度时,需要考虑工件材料的硬度、切削刃具的材质和工件表面的光洁度要求等因素。
2.2. 进给速度进给速度指的是刀具在工件表面上运动的速度。
过高或过低的进给速度都会影响加工质量和效率。
通过实验和经验总结,确定合适的进给速度可以提升数控加工的效率。
2.3. 切削深度切削深度是指刀具在工件表面上切削的深度。
合理选择切削深度可以提高加工的效率和质量。
切削深度受到工件材料的硬度、刀具的刚度和加工后的表面光洁度要求等因素的影响。
3. 改进加工工艺改进加工工艺是提高数控加工效率的另一个重要方面。
以下是一些常见的改进加工工艺的方法:3.1. 刀具路径优化刀具路径优化是通过对加工路径进行优化来实现提高加工效率的目的。
一种常用的优化方法是最优路径算法。
通过优化加工路径,可以减少刀具运动时间,提高加工效率。
3.2. 加工顺序优化加工顺序优化是通过调整加工工序的顺序来提高加工效率。
合理的加工顺序可以减少刀具换刀时间和夹持工件的次数,从而提高加工效率。
提高数控加工中心切削效率的途径
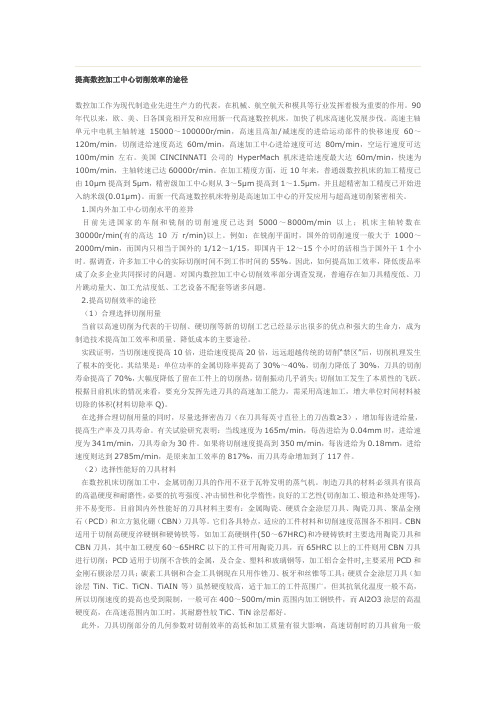
提高数控加工中心切削效率的途径数控加工作为现代制造业先进生产力的代表,在机械、航空航天和模具等行业发挥着极为重要的作用。
90年代以来,欧、美、日各国竞相开发和应用新一代高速数控机床,加快了机床高速化发展步伐。
高速主轴单元中电机主轴转速15000~100000r/min,高速且高加/减速度的进给运动部件的快移速度60~120m/min,切削进给速度高达60m/min,高速加工中心进给速度可达80m/min,空运行速度可达100m/min左右。
美国CINCINNATI公司的HyperMach机床进给速度最大达60m/min,快速为100m/min,主轴转速已达60000r/min。
在加工精度方面,近10年来,普通级数控机床的加工精度已由10μm提高到5μm,精密级加工中心则从3~5μm提高到1~1.5μm,并且超精密加工精度已开始进入纳米级(0.01μm)。
而新一代高速数控机床特别是高速加工中心的开发应用与超高速切削紧密相关。
1.国内外加工中心切削水平的差异目前先进国家的车削和铣削的切削速度已达到5000~8000m/min以上;机床主轴转数在30000r/min(有的高达10万r/min)以上。
例如:在铣削平面时,国外的切削速度一般大于1000~2000m/min,而国内只相当于国外的1/12~1/15,即国内干12~15个小时的活相当于国外干1个小时。
据调查,许多加工中心的实际切削时间不到工作时间的55%。
因此,如何提高加工效率,降低废品率成了众多企业共同探讨的问题。
对国内数控加工中心切削效率部分调查发现,普遍存在如刀具精度低、刀片跳动量大、加工光洁度低、工艺设备不配套等诸多问题。
2.提高切削效率的途径(1)合理选择切削用量当前以高速切削为代表的干切削、硬切削等新的切削工艺已经显示出很多的优点和强大的生命力,成为制造技术提高加工效率和质量、降低成本的主要途径。
实践证明,当切削速度提高10倍,进给速度提高20倍,远远超越传统的切削“禁区”后,切削机理发生了根本的变化。
运用科学方法提高数控机床加工效率
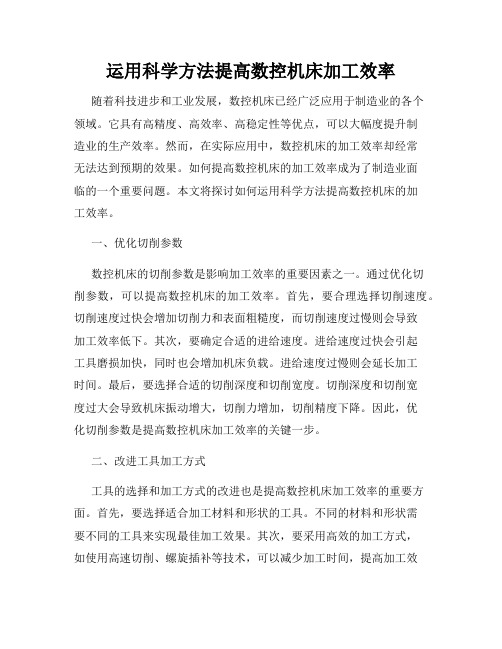
运用科学方法提高数控机床加工效率随着科技进步和工业发展,数控机床已经广泛应用于制造业的各个领域。
它具有高精度、高效率、高稳定性等优点,可以大幅度提升制造业的生产效率。
然而,在实际应用中,数控机床的加工效率却经常无法达到预期的效果。
如何提高数控机床的加工效率成为了制造业面临的一个重要问题。
本文将探讨如何运用科学方法提高数控机床的加工效率。
一、优化切削参数数控机床的切削参数是影响加工效率的重要因素之一。
通过优化切削参数,可以提高数控机床的加工效率。
首先,要合理选择切削速度。
切削速度过快会增加切削力和表面粗糙度,而切削速度过慢则会导致加工效率低下。
其次,要确定合适的进给速度。
进给速度过快会引起工具磨损加快,同时也会增加机床负载。
进给速度过慢则会延长加工时间。
最后,要选择合适的切削深度和切削宽度。
切削深度和切削宽度过大会导致机床振动增大,切削力增加,切削精度下降。
因此,优化切削参数是提高数控机床加工效率的关键一步。
二、改进工具加工方式工具的选择和加工方式的改进也是提高数控机床加工效率的重要方面。
首先,要选择适合加工材料和形状的工具。
不同的材料和形状需要不同的工具来实现最佳加工效果。
其次,要采用高效的加工方式,如使用高速切削、螺旋插补等技术,可以减少加工时间,提高加工效率。
另外,合理选择刀具刃数和刀具半径等参数也可以提高数控机床的加工效率。
三、优化加工路径加工路径是数控机床加工过程中工具移动的路径。
优化加工路径可以减少空行走时间,提高加工效率。
首先,要避免重复切削,减少工具来回移动的次数。
可以通过合理编写加工程序,考虑工具和工件的几何形状,避免刀具重复切削相同的区域。
其次,可以采用切削空间的优化技术,最大限度地减少空行走时间。
还可以考虑使用自动进给功能,在加工过程中自动调整加工路径,以减少加工时间。
四、提高机床的稳定性和精度机床的稳定性和精度直接影响加工效率。
首先,要加强机床的维护和保养工作,及时调整机床的精度,确保机床处于最佳状态。
提高数控机床使用效率的方法

提高数控机床使用效率的方法作者:庹海涛王军来源:《科学与财富》2019年第06期摘要:随着科技的进步,数控机床在机加工行业的使用越来越普及,本文通过生产组织、加工方法阐述了提高加工中心使用效率的方法。
关键词:数控机床、管理、加工路线、质量、效率随着科技的不断发展,数控机床在逐渐增加,如何用好数控机床,特别是如何提高数控机床的使用效率,在生产中显得尤为重要。
下面就我个人从事数控机床工作的一点经验,从生产组织和技术的角度谈谈提高数控机床使用效率的一点体会。
一、设置专人进行管理:目前,许多公司都有大量的数控设备,少则十几台,多则几百台,而这些机床的使用的效率的高低主要取决于数控机床操作人员。
多数情况下,1名操作工操作多台数控机床,这样机床加工过程中出现问题后,白班由较为熟悉的操作人员(主要是班长)进行处理,问题解决较快,对生产影响较小,有时由操作工自己进行处理,此时操作工操作的其它机床都有可能停止工作,而且操作工的素质参差不齐,问题解决快慢不一样,这样对生产影响就较大,甚至产生大量废品。
因此每班配备1-2名编程人员,主要处理机床加工中出现的问题,另外作一些辅助性的工作,如传输程序、更换工装,对更换加工零件的机床进行调试。
这样,操作人员只操作机床,即可提高机床的使用效率,又能减少零件加工过程中的废品。
二、减少更换工装的频次:要提高机床的使用效率,就要尽量减少工装的切换次数。
对于长线产品,加工时可以考虑把两、三个月的产品数量集中到一起进行加工,这样就减少了更换工装的频次,提高了加工中心的使用效率。
三、合理安排机床操作人员操作机床的数量:现在,许多公司加工中心的机床操作人员在工作时,一般操作3台或4台机床,对加工路线较长的产品,满足使用要求。
对于加工路线较短的产品,一个人操作3台或4台机床就忙不过来,降低了机床的使用效率。
因此,根据工件的加工节拍,合理安排每名操作人员操作机床的数量,能在一定程度上提高加工中心的使用效率。
加工中心g53详细用法

加工中心g53详细用法
G53是一种加工中心指令,可用于将刀具从加工区域迅速移动到工件起始点或机床零点,以提高加工效率和精度。
以下是G53指令的详细用法:
1.基本语法
G53 Xx Yy Zz Ff
其中X、Y、Z分别表示对应的坐标轴移动距离,F表示进给速度。
2.用法示例
例如,假设加工中心当前位置为X100 Y100 Z50,而需要将刀具移动到X0 Y0 Z0并以每分钟200毫米的速度进给,则可以输入以下指令:
G53 X-100 Y-100 Z-50 F200
该指令将刀具从当前位置迅速移动到X0 Y0 Z0的位置,并以200毫米/分钟的速度进给。
注意,由于G53指令不受加工区域限制,因此应特别注意防止与工件或夹具碰撞。
3.使用注意事项
- G53指令是机床控制程序中的非模态指令,与G0和G1指令不同,它只是临时性的移动而不影响后续指令。
- G53指令必须与绝对坐标指令G90配合使用。
- 应特别注意避免G53指令与夹具、工件碰撞,以及保护机床不受损坏。
- 在程序中使用多个G53指令时,应注意加工区域内的初始位置和刀具路径,以保证加工效率最大化。
- 对于某些加工类型(如螺纹加工),G53指令可能会导致刀具离开加工区域而无法再次进入。
- G53指令不支持圆弧运动,因此,在移动过程中的圆弧应该被分开,采用直线和圆弧的混合操作。
总的来说,G53指令的使用需要谨慎,并且需要根据实际加工需要进行选择和合理运用。
只有在合适的时间和地点使用G53指令,才能更好地提高加工效率和精度。
fanuc-oi数控铣床加工中心编程技巧与实例
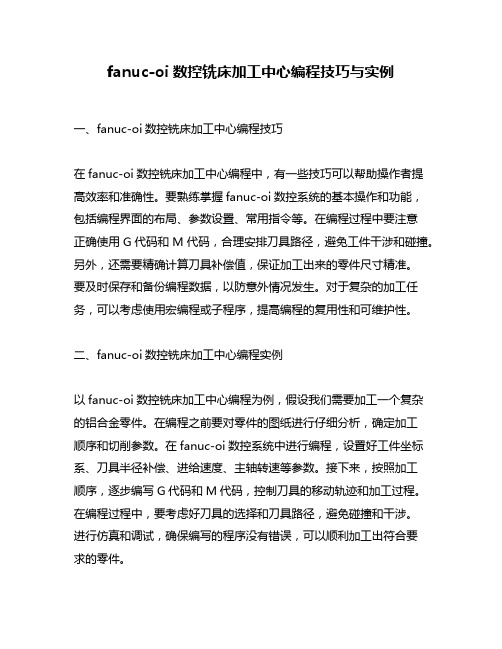
fanuc-oi数控铣床加工中心编程技巧与实例一、fanuc-oi数控铣床加工中心编程技巧在fanuc-oi数控铣床加工中心编程中,有一些技巧可以帮助操作者提高效率和准确性。
要熟练掌握fanuc-oi数控系统的基本操作和功能,包括编程界面的布局、参数设置、常用指令等。
在编程过程中要注意正确使用G代码和M代码,合理安排刀具路径,避免工件干涉和碰撞。
另外,还需要精确计算刀具补偿值,保证加工出来的零件尺寸精准。
要及时保存和备份编程数据,以防意外情况发生。
对于复杂的加工任务,可以考虑使用宏编程或子程序,提高编程的复用性和可维护性。
二、fanuc-oi数控铣床加工中心编程实例以fanuc-oi数控铣床加工中心编程为例,假设我们需要加工一个复杂的铝合金零件。
在编程之前要对零件的图纸进行仔细分析,确定加工顺序和切削参数。
在fanuc-oi数控系统中进行编程,设置好工件坐标系、刀具半径补偿、进给速度、主轴转速等参数。
接下来,按照加工顺序,逐步编写G代码和M代码,控制刀具的移动轨迹和加工过程。
在编程过程中,要考虑好刀具的选择和刀具路径,避免碰撞和干涉。
进行仿真和调试,确保编写的程序没有错误,可以顺利加工出符合要求的零件。
三、关于fanuc-oi数控铣床加工中心编程的个人观点和理解在fanuc-oi数控铣床加工中心编程中,技巧和实例只是基础,更重要的是理解加工原理和工艺要求。
在实际操作中,需要根据不同的零件特点和加工要求,灵活运用编程技巧,确保加工效率和加工质量。
保持对新技术和新工艺的学习和探索,不断提高自身的编程水平和创造力。
通过不断的实践和总结,形成自己的一套fanuc-oi数控铣床加工中心编程经验和方法,提高工作效率和竞争力。
总结:通过fanuc-oi数控铣床加工中心编程技巧与实例的介绍,我们可以更全面、深刻地理解在实际应用中,如何合理地进行加工中心编程。
熟练掌握fanuc-oi数控系统的基本操作和功能,合理选择加工策略和路径,对加工过程进行仿真和调试,将有助于提高加工效率和加工质量。
TPM之加工中心浪费分析案例

TPM之加工中心浪费分析案例加工中心是一种高精度、高效率的金属加工设备,广泛应用于机械制造、航空航天、汽车工业等领域。
然而,由于生产工序繁复、加工误差等原因,加工中心在使用中仍然存在一定的浪费现象。
本文以加工中心为例,分析其浪费现象并提出改进措施,以提高生产效率和降低资源浪费。
首先,生产过程中存在的浪费是指不增加产品价值的行为或过程。
在加工中心的生产中,常见的浪费包括等待时间、物料浪费、人员浪费、错误浪费等。
等待时间是指生产过程中因为前一道工序未完成而导致当前工序无法进行的时间。
在加工中心中,由于生产计划不合理和生产队伍不足,造成了前一道工序完成不及时的问题,导致加工中心产生了大量的等待时间浪费。
为解决这一问题,可以根据各道工序的产能和生产能力制定合理的生产计划,确保工序之间的衔接。
同时,增加生产队伍的数量和培训员工的技能,提高生产效率,减少等待时间浪费。
物料浪费是指在生产过程中由于材料的损坏、过剩或错误使用而造成的浪费。
在加工中心中,由于材料的管理不善和操作人员的不规范,造成了大量的物料浪费。
为解决这一问题,可以加强对材料的管理,制定材料的采购、储存和使用标准,避免过剩和损坏。
同时,加强对操作人员的培训,提高其操作技术和工作态度,减少错误使用材料的情况发生。
人员浪费是指在生产过程中由于人员的不合理安排、不合理使用或员工技能低下而造成的浪费。
在加工中心中,由于人员缺乏培训和技术更新,造成了大量的人员浪费。
为解决这一问题,可以开展员工技能培训和学习活动,提高员工的技术水平和工作能力。
同时,合理安排员工的工作,充分发挥其专业知识和经验,减少人员浪费。
错误浪费是指在生产过程中由于操作人员的不规范操作、设备故障等原因造成的浪费。
在加工中心中,由于操作人员的技术水平不高和设备的维护不规范,造成了大量的错误浪费。
为解决这一问题,可以加强对操作人员的培训,提高其操作技能和维护意识。
同时,加强对设备的维护和保养,定期检查设备的状态,及时处理故障,减少错误浪费的发生。
单位加工中心工作总结范文

单位加工中心工作总结范文
经过一段时间的努力,我们的单位加工中心取得了一定的成绩。
在这里,我将
对我们的工作进行总结,以便更好地指导未来的工作。
首先,我们在加工中心的生产效率方面取得了显著的提高。
通过优化生产流程、提高设备利用率和加强人员培训,我们成功地缩短了加工周期,提高了生产效率。
这为我们的单位节约了大量的时间和成本,也提高了我们的竞争力。
其次,我们在产品质量方面取得了长足的进步。
我们加强了对原材料的质量控制,严格执行了生产工艺标准,加强了对成品的检验。
这些措施使我们的产品质量得到了有效提升,受到了客户的一致好评。
再次,我们在团队建设方面取得了显著成效。
通过加强员工的培训和技能提升,我们的员工整体素质得到了提高,团队协作能力也得到了增强。
这为我们的单位提供了强大的人才保障,也为未来的发展奠定了坚实的基础。
最后,我们在市场开拓方面也取得了一定的成绩。
通过加强对市场的调研和分析,我们成功地开发了一些新的产品,并成功地拓展了一些新的市场。
这为我们的单位带来了新的业务机会,也为我们的发展注入了新的动力。
总的来说,我们的单位加工中心在过去一段时间的工作中取得了一定的成绩,
但同时也面临着一些挑战。
我们将继续努力,进一步提高生产效率,提高产品质量,加强团队建设,拓展市场,为我们的单位的发展创造更加美好的未来。
加工中心参数范文

加工中心参数范文加工中心是一种先进的数控机床,广泛应用于金属加工、模具制造、机械制造等行业。
它具有高精度、高效率、高刚性、高稳定性等优点,成为现代制造业中不可或缺的重要设备。
以下是加工中心的一些常见参数和技术指标。
1.高精度加工中心的高精度是其最重要的特点之一、通常,加工中心的定位精度可以达到0.01mm或更高,重复定位精度可以达到0.005mm或更高。
这意味着加工中心可以在很大程度上提高产品的加工精度,保证产品的质量。
2.高效率加工中心的高效率主要体现在其加工速度和加工周期上。
加工中心通常采用多轴联动控制,可以同时完成多个工序的加工。
此外,加工中心还可以进行高速切削,大大缩短了加工时间。
加工中心的高效率使得生产效率得到大幅提升。
3.高刚性加工中心的高刚性是指其在加工过程中抗振动、抗变形的能力。
加工中心通常采用铸铁、钢结构或其他高强度材料制成的床身,提供了良好的刚性和稳定性。
这种高刚性可以有效减少振动和变形,提高加工精度和表面质量。
4.多轴联动加工中心通常具有多轴联动的功能,即可以同时控制多个坐标轴的运动。
这样可以实现更加复杂的零件加工,如倾斜孔的加工、曲面加工等。
多轴联动的功能可以大大提升加工中心的加工能力和灵活性。
5.自动换刀加工中心通常配备自动换刀系统,可以根据加工需要自动切换刀具。
自动换刀系统可以大大提高加工效率和便利性,同时减少了操作人员的劳动强度。
6.编程灵活性加工中心通常采用数控系统进行编程,可以通过编程实现复杂零件的加工。
加工中心通常支持多种编程方式,如手动编程、自动编程、CAD/CAM编程等,使得操作和编程更加方便灵活。
7.良好的人机界面加工中心通常采用先进的数控系统和人机界面,使操作简便、直观。
操作员可以通过触摸屏、键盘、鼠标等设备进行操作,并可以监控加工过程、调整加工参数等。
8.安全保护措施为了确保操作人员的安全,加工中心通常还配备了一系列的安全保护措施。
例如,紧急停机按钮、防护罩、安全警示灯等,可以有效预防事故的发生。
提升多轴数控磨床效率

提升多轴数控磨床效率提升多轴数控磨床效率多轴数控磨床是一种高精度的机械设备,广泛应用于工业加工领域。
为了提高生产效率,我们可以采取以下步骤:1. 优化程序设计:首先,我们可以通过优化数控磨床的程序设计来提高效率。
合理安排切削路径和切削速度,减少切削时间,提高加工效率。
2. 使用高效刀具:选择高质量、高效率的刀具是提高多轴数控磨床效率的关键。
优质的刀具能够在短时间内完成加工任务,并且具有较长的使用寿命,减少了更换刀具的频率,提高了生产效率。
3. 提高机床刚性:增加多轴数控磨床的刚性可以提高其加工精度和稳定性。
通过采用优质的材料和合理的结构设计,可以增强机床的刚性,减少振动和变形,提高加工效率。
4. 自动化技术应用:引入自动化技术可以提高多轴数控磨床的运行效率。
例如,使用自动换刀系统可以减少人工换刀时间,提高生产效率。
此外,自动化技术还可以实现机床的自动化控制和监测,提高生产的稳定性和可靠性。
5. 定期维护保养:定期对多轴数控磨床进行维护保养是确保其高效运行的关键。
定期检查和清洁机床的各个部件,更换磨损严重的零部件,可以延长机床的使用寿命,保持其高效运行。
6. 增加操作人员培训:提高操作人员的技能水平可以进一步提高多轴数控磨床的效率。
通过培训操作人员熟练掌握多轴数控磨床的操作技巧和常见故障处理方法,可以减少操作失误和停机时间,提高生产效率。
通过以上的步骤,我们可以有效地提升多轴数控磨床的效率。
这不仅可以提高生产能力和产品质量,还可以降低生产成本,提升企业竞争力。
同时,我们也要意识到,每个步骤的具体实施需要根据具体情况进行调整和优化,以实现最佳的效果。
数控加工中心切削效率方法

数控加工中心切削效率方法数控加工中心是一种高效率、高精度的机床,广泛应用于制造业中的零件加工。
切削效率是衡量数控加工中心性能的重要指标之一,提高切削效率可以减少加工成本,并且提高产能。
本文将介绍几种提高数控加工中心切削效率的方法。
1.优化加工参数:数控加工中心通过改变切削速度、进给速度、切削深度和切削宽度等加工参数,可以实现不同类型零件的高效加工。
合理选择加工参数,可以在保证加工质量的前提下,提高加工速度和切削效率。
通常可以通过试切实验或者模拟加工来确定最佳加工参数。
2.提高进给速度:进给速度是指工件在数控加工中心上移动的速度。
提高进给速度可以减少切削时间,从而提高切削效率。
但是要注意,进给速度不能过快,否则可能导致切削过热、刀具磨损加快等问题。
因此,提高进给速度需要综合考虑切削条件、刀具材料和切削表面质量等因素。
3.选用合适的刀具:刀具是数控加工中心进行切削的关键工具,选择合适的刀具可以提高切削效率。
一方面要选择适合加工材料和加工工艺的刀具,另一方面要选用质量好、耐磨性强的刀具。
此外,选择刀具形状和结构时,也要综合考虑切削表面质量、切削力和切削稳定性等因素。
4.采用高速切削技术:高速切削技术是一种将刀具切削速度提高到很高的技术。
通过提高切削速度,可以提高切削效率和加工质量。
同时,高速切削技术还可以减少切削力、延长刀具使用寿命,提高切削稳定性。
但是高速切削技术对刀具和切削系统的要求较高,需要选用高速切削专用刀具,并且要进行刀具磨砺和刀具平衡等工艺控制。
5.采用精确的夹具和工艺装备:夹具和工艺装备的精度和稳定性直接影响数控加工中心的切削效率。
精确的夹具可以保证工件的精确定位和固定,避免振动和变形;而稳定的工艺装备可以保证刀具和工件之间的相对位置和运动准确性。
因此,选用合适的夹具和工艺装备,并进行必要的校准和调试是提高切削效率的必要手段。
6.合理安排切削刀具路径:数控加工中心可以根据加工轨迹自动控制刀具的运动,通过合理安排切削刀具路径,可以减少刀具在空转中的时间,提高切削效率。
CNC数控加工中心操作规程范文(三篇)
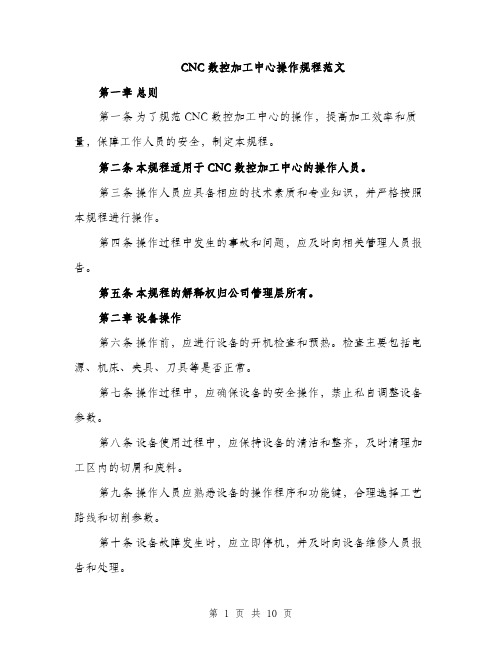
CNC数控加工中心操作规程范文第一章总则第一条为了规范CNC数控加工中心的操作,提高加工效率和质量,保障工作人员的安全,制定本规程。
第二条本规程适用于CNC数控加工中心的操作人员。
第三条操作人员应具备相应的技术素质和专业知识,并严格按照本规程进行操作。
第四条操作过程中发生的事故和问题,应及时向相关管理人员报告。
第五条本规程的解释权归公司管理层所有。
第二章设备操作第六条操作前,应进行设备的开机检查和预热。
检查主要包括电源、机床、夹具、刀具等是否正常。
第七条操作过程中,应确保设备的安全操作,禁止私自调整设备参数。
第八条设备使用过程中,应保持设备的清洁和整齐,及时清理加工区内的切屑和废料。
第九条操作人员应熟悉设备的操作程序和功能键,合理选择工艺路线和切削参数。
第十条设备故障发生时,应立即停机,并及时向设备维修人员报告和处理。
第三章刀具管理第十一条操作人员应按照规定的刀具管理制度使用刀具,禁止私自使用已经损坏的刀具和无标识的刀具。
第十二条刀具在使用前应检查其是否完好,确保没有损坏和变形。
第十三条刀具在使用过程中产生的刀具磨损应及时更换新的刀具,并做好记录。
第十四条刀具使用完毕后,应清洁刀具,并归还至刀具库。
第十五条刀具库应保持整洁,并做到刀具的分类和标识。
第四章加工操作第十六条加工前应仔细阅读工艺书,并根据工艺要求选择合适的夹具和刀具。
第十七条加工过程中应确保工件稳固夹紧,并保持加工区的整洁。
第十八条加工过程中应定期测量加工尺寸,确保加工精度符合要求。
第十九条加工完成后,应切断电源并清理加工区内的切屑和废料。
第五章安全操作第二十条操作人员应佩戴防护设备,并正确使用。
第二十一条操作人员应严禁在设备运行过程中活动,并保持集中注意力。
第二十二条操作人员应熟悉设备的紧急停机和急停按钮的位置,并掌握使用方法。
第二十三条发生事故时,应立即停机,排除隐患,并向相关人员报告。
第二十四条操作人员对设备的检修和维护应按照规定的程序进行。
CNC机床加工中的加工效率提升方法

CNC机床加工中的加工效率提升方法CNC(Computer Numerical Control)机床是通过计算机控制数值的机械设备,广泛应用于各个工业领域。
随着技术的不断发展,提高CNC机床加工效率成为了制造业重要的课题之一。
本文将探讨几种提升CNC机床加工效率的方法。
一、工艺优化工艺优化是提高CNC机床加工效率的关键。
通过合理的工艺安排和参数设定,可以减少加工时间,提高加工效率。
具体方法如下:1. 材料选择选择具有良好加工性能的材料可以显著提高加工效率。
应根据具体要求选择硬度适中、切削性好的材料,避免加工过程中出现断刀、断刃等问题。
2. 刀具选择选择合适的刀具也是提升加工效率的关键。
应根据加工要求选择切削速度高、耐磨性好的刀具,减少刀具更换次数,提高加工效率。
3. 切削参数设定合理的切削参数设定对加工效率有重要影响。
应根据材料、刀具等因素设定适当的进给速度、切削速度和切削深度,以减少加工时间。
4. 程序优化对机床的程序进行优化也是提高加工效率的重要手段。
通过合理的程序设计和优化,可以减少加工路径长度、减少空程时间,提高加工效率。
二、设备维护保持CNC机床设备的良好状态对提高加工效率至关重要。
以下几个方面需要特别注意:1. 定期保养定期保养机床,清洁润滑系统,检查各个零部件的磨损情况。
保持CNC机床设备的正常状态,减少设备故障和停机时间,确保加工效率。
2. 刀具管理合理管理刀具,包括定期检查刀具状态,保持刀具的锋利度,及时更换磨损、断裂的刀具。
这样可以保证刀具的加工效率和加工质量。
3. 升级更新对老旧的CNC机床设备进行升级更新,引入新的控制系统和技术,以提高加工效率。
同时,对新购买的设备要及时进行培训和试用,确保设备的正常运行。
三、操作技巧操作技巧的熟练程度直接关系到CNC机床的加工效率。
以下几个技巧可以提高操作效率:1. 快速编程熟练掌握编程技巧,减少编程的时间,提高编程效率。
可以运用编程软件的快捷键和宏指令,提高编程速度。
浅谈如何提升数控加工效率

浅谈如何提升数控加工效率专业:机械制造及自动化班级:09高数1姓名:《浅谈如何提升数控加工效率》[摘要]如何利用和发展数控加工,实现高效数控加工(High Efficiency NC Machining)已成为企业普遍关心的大事。
许多企业中数控加工效率低下,数控制造能力不足已成为较突出的共性问题。
如何通过高效数控加工技术的研究提高数控制造技术水平,提高数控加工的能力,是摆在我们面前的严峻课题。
实现高效数控加工对增强企业的综合竞争力,提高可持续发展能力都具有现实意义。
[关键词]提升效率数控机床切削刀具一、导语数控机床具有生产效率和加工自动化程度高,零件的加工精度和产品的质量稳定性好,能完成许多普通机床难以加工或根本无法加工的复杂型面加工,几乎不要专用的工装卡具、减少在制品,提高经济效益和大大减轻操作工人的劳动强度等一系列优点。
随着制造业的迅速发展,大力发展以数控机床为先导的装备制造业已成为我国政府的一项产业政策,将对数控机床的发展产生重大的影响。
用好数控机床提高数控机床的利用率具有重要的现实意义,它不仅能增加企业的效益,而且还有助于提高我国制造业的整体素质和加快建设制造强国的进程.二、影响数控加工效率的因素分析1.数控机床应用水平不高数控加工在中国制造业中已经有了较长的使用时间,虽然有严格的数控机床操作规范、良好的机床维护保养,但是其本身的精度损失是不可避免的.为了控制产品的加工质量,我们定期对数控设备进行检测维修,明确每台设备的加工精度,明确每台设备的加工任务.对于大批量成批生产的零件加工工厂,应严格区分粗、精加工的设备使用,因为粗加工时追求的是高速度、高的去除率、低的加工精度,精加工则相反,要求高的加工精度。
而粗加工时对设备的精度损害是最严重的,因此我们将使用年限较长、精度最差的设备定为专用的粗加工设备,新设备和精度好的设备定为精加工设备,做到对现有设备资源的合理搭配、明确分工,将机床对加工质量的影响降到了最低,同时又保护了昂贵的数控设备,延长了设备的寿命.2。
数控铣加工效率提升案例
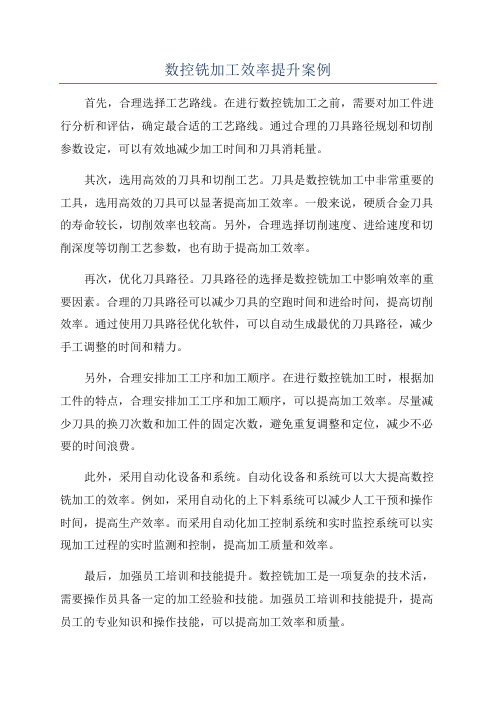
数控铣加工效率提升案例首先,合理选择工艺路线。
在进行数控铣加工之前,需要对加工件进行分析和评估,确定最合适的工艺路线。
通过合理的刀具路径规划和切削参数设定,可以有效地减少加工时间和刀具消耗量。
其次,选用高效的刀具和切削工艺。
刀具是数控铣加工中非常重要的工具,选用高效的刀具可以显著提高加工效率。
一般来说,硬质合金刀具的寿命较长,切削效率也较高。
另外,合理选择切削速度、进给速度和切削深度等切削工艺参数,也有助于提高加工效率。
再次,优化刀具路径。
刀具路径的选择是数控铣加工中影响效率的重要因素。
合理的刀具路径可以减少刀具的空跑时间和进给时间,提高切削效率。
通过使用刀具路径优化软件,可以自动生成最优的刀具路径,减少手工调整的时间和精力。
另外,合理安排加工工序和加工顺序。
在进行数控铣加工时,根据加工件的特点,合理安排加工工序和加工顺序,可以提高加工效率。
尽量减少刀具的换刀次数和加工件的固定次数,避免重复调整和定位,减少不必要的时间浪费。
此外,采用自动化设备和系统。
自动化设备和系统可以大大提高数控铣加工的效率。
例如,采用自动化的上下料系统可以减少人工干预和操作时间,提高生产效率。
而采用自动化加工控制系统和实时监控系统可以实现加工过程的实时监测和控制,提高加工质量和效率。
最后,加强员工培训和技能提升。
数控铣加工是一项复杂的技术活,需要操作员具备一定的加工经验和技能。
加强员工培训和技能提升,提高员工的专业知识和操作技能,可以提高加工效率和质量。
综上所述,通过合理选择工艺路线、选用高效的刀具和切削工艺、优化刀具路径、合理安排加工工序和加工顺序、采用自动化设备和系统、加强员工培训和技能提升等措施,可以有效地提高数控铣加工的效率。
这些措施可以降低加工成本、提高生产效率、提高产品质量,对企业的发展具有重要意义。
- 1、下载文档前请自行甄别文档内容的完整性,平台不提供额外的编辑、内容补充、找答案等附加服务。
- 2、"仅部分预览"的文档,不可在线预览部分如存在完整性等问题,可反馈申请退款(可完整预览的文档不适用该条件!)。
- 3、如文档侵犯您的权益,请联系客服反馈,我们会尽快为您处理(人工客服工作时间:9:00-18:30)。
提高加工中心使用效率实例一则
用加工中心批量加工精密的中小型工件,设计夹具时,考虑装夹多件工件,能减少换刀次数,节省换刀时间,也减少了因频繁换刀导致的换刀系统故障。
如使用气动或液压为夹紧动力,则能进一步提高效率。
利用加工中心加工工件有许多优点:产品重复精度高:可完成复杂曲线、曲面加工:可一机多用,完成多种加工工序,特别适用于精密、复杂、多工序的大中型工件。
但用加工中心
批量加工精密小型零件并不划算,因为与机床使用成本相比,加工效率太低。
影响加工效率的主要因素有:手动夹紧工件,机床执行换刀指令过频。
这些辅助工作的时间占总时间的比率过大。
另外,频繁换刀机床易出故障(加工中心的故障有40%~50% 出在换刀系统上)。
为提高加工中心的加工效率,笔者在夹具、工艺路线上作了改进,大大减少了换刀次数、装夹时间,取得了满意的效果。
图1
1 问题提出
如图1所示小型零件简图,由于尺寸精度,位置精度要求高,故选用加工中心加工。
在加工中心上完成的工序有:两个大孔、两个小孔、底面。
原夹具设计为装夹单个工件,手动夹紧,因此每次装夹只能加工一件。
工件以一面两销定位,在卧式加工中心上加工。
加工路线为:①换大孔粗铣刀:②进行圆插补粗铣大孔及底面:③工作台移位:④重复步骤“2”铣另一大孔及底面:⑤换小孔粗铣刀:⑥进行圆插补粗铣小孔:⑦工作台移位:⑧重复步骤“6”铣另一小孔。
至此,粗加工完成。
精加工所用为精铣刀。
一般加工中心,换刀时间都较长。
2 解决方案
为有效地减少辅助工作时间,笔者改进了夹具设计。
由于工件较小,为充分利用机床的行程,故安排在一个夹具上装夹8个工件,夹具如图2所示,工件仍以一面两销定位,由气动夹紧(图中未画出)。
在夹具设计制造时,应保证夹具上的每两个定位销之间位置准确(如“1”号工件的两个定位销与其它工件的定位销之间位置准确),这样能保证加工后的孔位置与工件外形不产生偏差。
如仍有偏差,可在程序中作适当修改来解决。
在卧式加工中心上加工路线,以粗加工大孔、底面为例:①换大孔粗铣刀:②粗铣1号工件下面大孔、底面:③移位:④粗铣2号工件下面大孔、底面:⑤多次移位,粗铣第3、4、5、6、7、8 号工件下面大孔、底面:⑥移位,粗铣第8、7、6、5、4、3、2、1 号工件上面的大孔、底面。
图2
可以看出,粗铣大孔、底面只换刀一次。
同样,精铣大孔、底面和粗、精铣小孔的换刀次数相同,故加工8 个工件总换刀次数为4次。
因此,平均加工每个工件的换刀时间为原来的1/8,虽然移位有所增加,但总的时间还是节约了很多。
总之,用加工中心批量加工精密的中小型工件,设计夹具时,考虑装夹多件工件,能减少换刀次数,节省换刀时间,也减少了因频繁换刀导致的换刀系统故障。
如使用气动或液压为
夹紧动力,则能进一步提高效率。