注塑成型介绍
注塑成型工艺特点及应用

注塑成型工艺特点及应用注塑成型工艺特点及应用注塑成型是一种常见的塑料加工工艺,广泛应用于制造各种塑料制品。
它的主要特点如下:1. 高效率:注塑成型工艺能够快速地将熔融状态的塑料注入模具中进行制品成型。
注塑成型机的工作周期短,能够实现连续生产,提高生产效率。
2. 复杂形状:注塑成型工艺可以制造各种形状复杂的产品,包括中空构件、薄壁构件等。
通过合理设计模具结构,可以精确地复制模具的细节,使得成型的制品具有高精度和高质量。
3. 材料广泛:注塑成型工艺适用于广泛的塑料材料,包括热塑性塑料和热固性塑料。
根据产品需要,可以选择不同的塑料材料进行注塑成型,满足不同产品的性能需求。
4. 自动化程度高:注塑成型工艺可以实现全自动化生产,降低劳动成本。
注塑成型机自动化程度高,通过模具开关、温度控制、压力和速度调节等功能实现稳定的生产过程。
注塑成型工艺广泛应用于各个领域,下面以几个典型的应用为例进行介绍:1. 日用品:注塑成型工艺可以制造各种塑料日用品,如牙刷、塑料杯、塑料梳子等。
注塑成型的高效率和成本优势,使得塑料日用品在市场上具有竞争力。
2. 电子产品:注塑成型工艺广泛应用于电子产品的制造过程中,如手机壳、电视外壳等。
注塑成型可以制造出具有良好外观和高精度的塑料制品,满足电子产品对外观和尺寸要求。
3. 汽车零部件:注塑成型工艺在汽车工业中得到广泛应用。
注塑成型可以制造汽车零部件,如车灯壳、内饰件等。
通过注塑成型,可以实现汽车零部件的大规模生产和质量保证。
4. 医疗器械:注塑成型工艺应用于医疗器械的制造过程中。
医疗器械对产品的精度和卫生要求较高,注塑成型工艺可以制造出符合要求的塑料器械。
5. 塑料包装:注塑成型工艺广泛应用于塑料包装行业,如食品包装、制药包装等。
通过注塑成型,可以制造出不同形状和尺寸的塑料包装容器,满足不同产品的包装需求。
总结起来,注塑成型工艺具有高效率、复杂形状、材料广泛、自动化程度高等优点,适用于各个领域的制造过程中。
注塑成型介绍及工艺介绍

b.射速、射出、保压、背压、螺杆转速分段控制。
c.搅拌性、寿命长的螺杆装置。
d.料管互换性,自动清洗。
e.油泵之平衡、稳定性。
2.锁模系统
a.高速度、高钢性。
b.自动调模、换模装置。
c.自动润滑系统。
d.平衡、稳定性。
基本结构: 1.公模(下模) 公模固定板、公模辅助板、顶针板、公模板。 2.母模(上模) 母模板、母模固定板、进胶圈、定位圈。 3.衡温系统 冷却.稳(衡)定模具温度。
四、 注塑机
主要由塑化、注射装置,合模装置和传动机构组成; 电气带动电机,电机带动油泵,油泵产生油压, 油压带动活塞,活塞带动机械,机械产生动作;
公司产品主要用于油汀,如:部分油汀的面板.烘衣架.电子油汀透明罩等等;
100度 2.干燥条件:100度至120度4小时以上。 3.料管温度:250度至300度 4.热变形温度:130度左右; 5.模具收缩率:0.5%-0.7%
PC材料之流动性随温度升高则越高,因温度调节在成型上占比重较大。
目前大部分使用的塑料有:PP ABS PBT PC PA PPS POM 等。
1、 PP料:(聚丙烯polypropylene) 目前大部分使用的厂牌有:
中国石化 台湾化纤 镇海炼化 韩国现代 新加坡mytex 印度SEETEC
特性: 比重较轻,流动性好,无色.无味.无臭.无毒,光泽度.拉伸强度.耐热性能好,二次加工性能好,有良好的绝缘性.化学稳定性;加上价格低廉,主要适用于编织袋.玩具.周转箱.家电.管材.板材等。
增高密度,这时螺杆对塑料施加的压力叫保压;
3.锁模力: (吨位)
锁模机构对模具所能施加的最大夹紧力;
注塑成型的概念

注塑成型的概念
注塑成型(Injection Molding)是一种常用的塑料加工方法,通过将熔化的塑料注入模具中,并在模具中冷却和固化,最终得到所需的塑料制品。
注塑成型的概念包括以下几个方面:1. 注塑机:注塑成型过程中使用的设备,用于将塑料加热熔化并注入模具中。
注塑机通常由注射装置、锁模装置、液压系统和控制系统等部分组成。
2. 模具:注塑成型过程中塑料制品的形状和尺寸由模具决定。
模具由上模板和下模板组成,通过锁模装置固定在注塑机中。
3. 塑料材料:注塑成型使用的塑料材料通常是以颗粒状或粉末状存在的塑料原料。
常见的塑料材料包括聚丙烯(PP)、聚乙烯(PE)、聚氯乙烯(PVC)、聚苯乙烯(PS)等。
4. 注塑成型工艺:注塑成型工艺包括以下几个步骤:首先将塑料颗粒放入注塑机的料斗中,通过加热和融化使其成为熔融态,然后使用注射装置将熔融塑料注入模具的腔道中,待冷却固化后,通过开模装置将成型的塑料制品从模具中取出。
注塑成型具有生产周期短、生产效率高、成本相对较低等优点。
它被广泛应用于制造各种塑料制品,如塑料零件、容器、包装材料、电子产品外壳等。
注塑成型工艺介绍
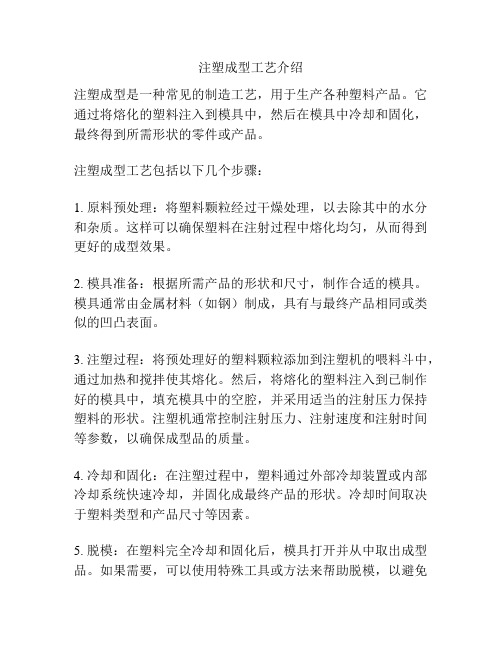
注塑成型工艺介绍注塑成型是一种常见的制造工艺,用于生产各种塑料产品。
它通过将熔化的塑料注入到模具中,然后在模具中冷却和固化,最终得到所需形状的零件或产品。
注塑成型工艺包括以下几个步骤:1. 原料预处理:将塑料颗粒经过干燥处理,以去除其中的水分和杂质。
这样可以确保塑料在注射过程中熔化均匀,从而得到更好的成型效果。
2. 模具准备:根据所需产品的形状和尺寸,制作合适的模具。
模具通常由金属材料(如钢)制成,具有与最终产品相同或类似的凹凸表面。
3. 注塑过程:将预处理好的塑料颗粒添加到注塑机的喂料斗中,通过加热和搅拌使其熔化。
然后,将熔化的塑料注入到已制作好的模具中,填充模具中的空腔,并采用适当的注射压力保持塑料的形状。
注塑机通常控制注射压力、注射速度和注射时间等参数,以确保成型品的质量。
4. 冷却和固化:在注塑过程中,塑料通过外部冷却装置或内部冷却系统快速冷却,并固化成最终产品的形状。
冷却时间取决于塑料类型和产品尺寸等因素。
5. 脱模:在塑料完全冷却和固化后,模具打开并从中取出成型品。
如果需要,可以使用特殊工具或方法来帮助脱模,以避免损坏或变形。
6. 后处理:根据产品的要求,可能需要进行后处理工艺,如修边、打磨、修整等,以获得最终的产品质量和外观效果。
注塑成型工艺的优点在于可以生产复杂形状的产品,并具有良好的尺寸稳定性和表面质量。
此外,注塑成型可以批量生产,提高生产效率和降低成本。
然而,注塑成型也存在一些限制,如模具制作成本较高、制作周期长、塑料材料的选择受限等。
因此,在进行注塑成型之前,需要仔细评估产品设计和成本效益,以确保工艺的可行性。
总而言之,注塑成型是一种常用、高效且灵活的制造工艺,广泛应用于各个行业,从电子产品到家具、汽车零部件等。
它为生产高质量和复杂形状的塑料产品提供了可靠的解决方案。
注塑成型是一种常见的制造工艺,广泛应用于各个行业。
它能够生产出各种形状复杂、尺寸稳定的塑料制品,包括塑料壳体、容器、零部件、玩具等。
注塑成型概念
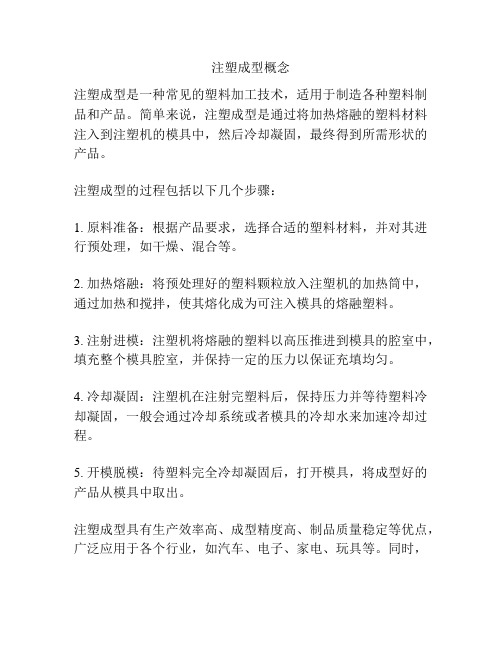
注塑成型概念
注塑成型是一种常见的塑料加工技术,适用于制造各种塑料制品和产品。
简单来说,注塑成型是通过将加热熔融的塑料材料注入到注塑机的模具中,然后冷却凝固,最终得到所需形状的产品。
注塑成型的过程包括以下几个步骤:
1. 原料准备:根据产品要求,选择合适的塑料材料,并对其进行预处理,如干燥、混合等。
2. 加热熔融:将预处理好的塑料颗粒放入注塑机的加热筒中,通过加热和搅拌,使其熔化成为可注入模具的熔融塑料。
3. 注射进模:注塑机将熔融的塑料以高压推进到模具的腔室中,填充整个模具腔室,并保持一定的压力以保证充填均匀。
4. 冷却凝固:注塑机在注射完塑料后,保持压力并等待塑料冷却凝固,一般会通过冷却系统或者模具的冷却水来加速冷却过程。
5. 开模脱模:待塑料完全冷却凝固后,打开模具,将成型好的产品从模具中取出。
注塑成型具有生产效率高、成型精度高、制品质量稳定等优点,广泛应用于各个行业,如汽车、电子、家电、玩具等。
同时,
注塑成型也可以通过调整注塑机的参数和模具设计来实现不同形状和尺寸的产品生产。
塑料注塑成型教程
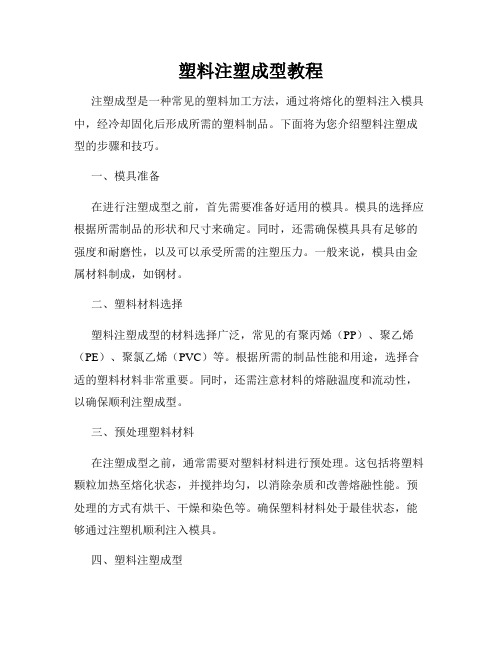
塑料注塑成型教程注塑成型是一种常见的塑料加工方法,通过将熔化的塑料注入模具中,经冷却固化后形成所需的塑料制品。
下面将为您介绍塑料注塑成型的步骤和技巧。
一、模具准备在进行注塑成型之前,首先需要准备好适用的模具。
模具的选择应根据所需制品的形状和尺寸来确定。
同时,还需确保模具具有足够的强度和耐磨性,以及可以承受所需的注塑压力。
一般来说,模具由金属材料制成,如钢材。
二、塑料材料选择塑料注塑成型的材料选择广泛,常见的有聚丙烯(PP)、聚乙烯(PE)、聚氯乙烯(PVC)等。
根据所需的制品性能和用途,选择合适的塑料材料非常重要。
同时,还需注意材料的熔融温度和流动性,以确保顺利注塑成型。
三、预处理塑料材料在注塑成型之前,通常需要对塑料材料进行预处理。
这包括将塑料颗粒加热至熔化状态,并搅拌均匀,以消除杂质和改善熔融性能。
预处理的方式有烘干、干燥和染色等。
确保塑料材料处于最佳状态,能够通过注塑机顺利注入模具。
四、塑料注塑成型1. 通过注塑机将预处理后的塑料材料注入模具中。
注塑机根据预先设定好的注塑参数,控制塑料的温度和压力。
2. 塑料材料在模具中充满整个腔室,填充完毕后,需要保持一段时间以确保完全凝固。
3. 模具冷却后,通过顶出装置将塑料制品从模具中顶出。
4. 塑料制品经过去闪边、修整等处理,以获得最终的成品。
五、技巧和注意事项1. 控制制品尺寸:通过调整注塑机的注塑参数和模具的结构,可以控制制品的尺寸和精度。
2. 避免缺陷:注塑成型过程中常见的缺陷有气泡、缩水、翘曲等。
通过调整熔融温度、充模速度和模具结构等因素,可减少或避免这些缺陷的发生。
3. 循环利用废料:塑料注塑成型会产生一定数量的废料和废品,可以选择回收和回炉利用,以减少资源浪费。
4. 定期维护设备:保持注塑机和模具的清洁和良好状态,定期进行维护和保养,以延长使用寿命和确保注塑成型的质量。
六、性能测试和质量控制完成塑料注塑成型后,还需要对制品进行性能测试和质量控制。
注塑成型的原理

一.注塑成型的原理:1.注塑成型:指将注射用的置于能加热的料筒内,受热、塑化,再施加压力,使熔体塑料注入到所需形状的模具中,经过冷却定型后脱模,得到所需形状的制品。
2.注塑成型三要素:注塑机、模具、原料3.注塑成型条件五大要素:压力-时间-速度-位置-温度。
二.注塑机:1.注塑机的种类:b.按传动方式分液压式、机械式、液压机械式c.按外型分卧式、立式、角式目前我们公司使用的注射机为卧式、螺杆塑化、液压传动式注射机。
2.注射机的结构:a.注射系统:主要使塑料塑化和使熔体塑料注入模具功能b.合模系统:主要模具的开模、锁模、调模、顶出功能c.传动系统:主要控制注射机的动作能力。
如油压阀、电动机d.电气控制系统:主要注射机内部电路、开关、电路板3.注射机的操作:a.打开注射机总电源及各开关,旋开紧急停止键b.按下操作板上马达启动键与电热键,开启马达与料筒温度〔按1次左上角灯亮为开启,再按1次左上角灯灭为停止〕c-1点动:上下模时使用,又称调模使用c-2手动:选用此方式时操作板上的相应开关,只在按下时作相应动作,手指放开即停止c-3半自动:选用此方式时,只需开关安全门一次,机器即做关模射出储料〔冷却〕开模顶出顶退,循环动作,再开安全门一次,再做一次循环c-4.全自动:选用此方式操作,关上安全门后,机器重复关模顶出顶退〔制品取出确认〕关模至打开安全门或选用其它方式操作,生产有斜顶/滑块模具禁止使用。
d.开关模动作设定:开模一般设定为慢快慢,关模一般设定为快速低压低速高压锁模。
低压压力最大不可以大于15kg/cm2低压与高压之间位置不可大2mm,快速与低压间位置一般在50mme.成型温度设定:根据各种原料成型所需温度设定,在改变设定温度时一次不可超过5°,加料段温度比熔融段温度最少要低10°,待机器上显示实际温度到达设定温度时,在改变设定温度时一次不可超过5°再过二十分钟才可进行熔胶,射出射退动作。
注塑模具成型系统介绍
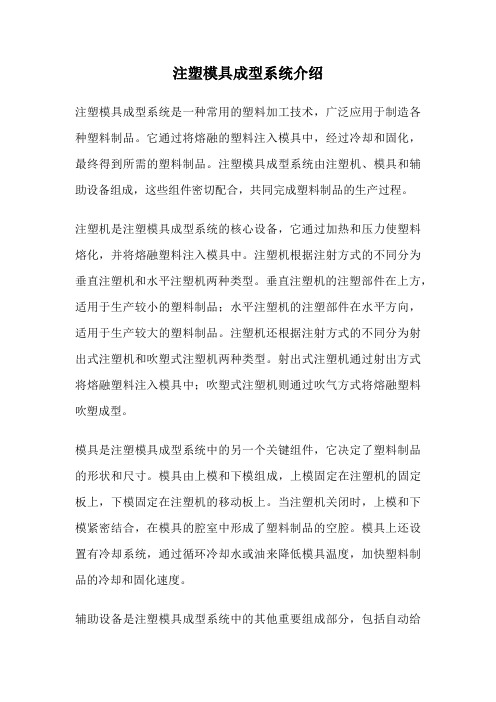
注塑模具成型系统介绍注塑模具成型系统是一种常用的塑料加工技术,广泛应用于制造各种塑料制品。
它通过将熔融的塑料注入模具中,经过冷却和固化,最终得到所需的塑料制品。
注塑模具成型系统由注塑机、模具和辅助设备组成,这些组件密切配合,共同完成塑料制品的生产过程。
注塑机是注塑模具成型系统的核心设备,它通过加热和压力使塑料熔化,并将熔融塑料注入模具中。
注塑机根据注射方式的不同分为垂直注塑机和水平注塑机两种类型。
垂直注塑机的注塑部件在上方,适用于生产较小的塑料制品;水平注塑机的注塑部件在水平方向,适用于生产较大的塑料制品。
注塑机还根据注射方式的不同分为射出式注塑机和吹塑式注塑机两种类型。
射出式注塑机通过射出方式将熔融塑料注入模具中;吹塑式注塑机则通过吹气方式将熔融塑料吹塑成型。
模具是注塑模具成型系统中的另一个关键组件,它决定了塑料制品的形状和尺寸。
模具由上模和下模组成,上模固定在注塑机的固定板上,下模固定在注塑机的移动板上。
当注塑机关闭时,上模和下模紧密结合,在模具的腔室中形成了塑料制品的空腔。
模具上还设置有冷却系统,通过循环冷却水或油来降低模具温度,加快塑料制品的冷却和固化速度。
辅助设备是注塑模具成型系统中的其他重要组成部分,包括自动给料机、干燥机、冷却机、热流道控制系统等。
自动给料机用于将塑料颗粒自动送入注塑机的料斗中,确保塑料供给的连续性和准确性;干燥机用于去除塑料颗粒中的水分,以保证注塑过程中的塑料质量;冷却机则用于冷却注塑机和模具,以控制注塑过程中的温度;热流道控制系统是一种高级的注塑模具技术,通过加热模具中的通道,使塑料在注塑过程中保持较高的温度,从而避免塑料制品的缺陷。
注塑模具成型系统的工作原理是:首先,将塑料颗粒加入自动给料机中,经过干燥处理后,由自动给料机输送到注塑机的料斗中;然后,注塑机通过加热和压力使塑料颗粒熔化,并将熔融的塑料注入模具中;接着,塑料在模具中进行冷却和固化,最终形成所需的塑料制品;最后,打开模具,取出成品,完成整个注塑模具成型的过程。
常用的十大塑料成型工艺(优缺点介绍)
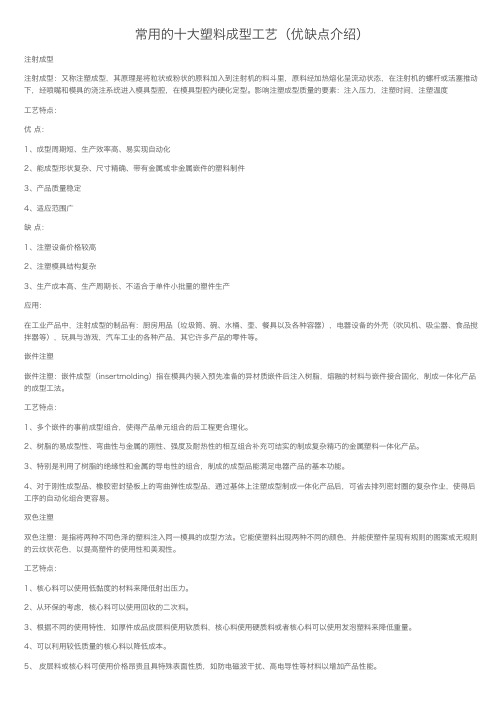
常⽤的⼗⼤塑料成型⼯艺(优缺点介绍)注射成型注射成型:⼜称注塑成型,其原理是将粒状或粉状的原料加⼊到注射机的料⽃⾥,原料经加热熔化呈流动状态,在注射机的螺杆或活塞推动下,经喷嘴和模具的浇注系统进⼊模具型腔,在模具型腔内硬化定型。
影响注塑成型质量的要素:注⼊压⼒,注塑时间,注塑温度⼯艺特点:优 点:1、成型周期短、⽣产效率⾼、易实现⾃动化2、能成型形状复杂、尺⼨精确、带有⾦属或⾮⾦属嵌件的塑料制件3、产品质量稳定4、适应范围⼴缺 点:1、注塑设备价格较⾼2、注塑模具结构复杂3、⽣产成本⾼、⽣产周期长、不适合于单件⼩批量的塑件⽣产应⽤:在⼯业产品中,注射成型的制品有:厨房⽤品(垃圾筒、碗、⽔桶、壶、餐具以及各种容器),电器设备的外壳(吹风机、吸尘器、⾷品搅拌器等),玩具与游戏,汽车⼯业的各种产品,其它许多产品的零件等。
嵌件注塑嵌件注塑:嵌件成型(insertmolding)指在模具内装⼊预先准备的异材质嵌件后注⼊树脂,熔融的材料与嵌件接合固化,制成⼀体化产品的成型⼯法。
⼯艺特点:1、多个嵌件的事前成型组合,使得产品单元组合的后⼯程更合理化。
2、树脂的易成型性、弯曲性与⾦属的刚性、强度及耐热性的相互组合补充可结实的制成复杂精巧的⾦属塑料⼀体化产品。
3、特别是利⽤了树脂的绝缘性和⾦属的导电性的组合,制成的成型品能满⾜电器产品的基本功能。
4、对于刚性成型品、橡胶密封垫板上的弯曲弹性成型品,通过基体上注塑成型制成⼀体化产品后,可省去排列密封圈的复杂作业,使得后⼯序的⾃动化组合更容易。
双⾊注塑双⾊注塑:是指将两种不同⾊泽的塑料注⼊同⼀模具的成型⽅法。
它能使塑料出现两种不同的颜⾊,并能使塑件呈现有规则的图案或⽆规则的云纹状花⾊,以提⾼塑件的使⽤性和美观性。
⼯艺特点:1、核⼼料可以使⽤低黏度的材料来降低射出压⼒。
2、从环保的考虑,核⼼料可以使⽤回收的⼆次料。
3、根据不同的使⽤特性,如厚件成品⽪层料使⽤软质料,核⼼料使⽤硬质料或者核⼼料可以使⽤发泡塑料来降低重量。
注塑成型的四大要素(3篇)

第1篇一、塑料原料1. 塑料种类注塑成型所使用的塑料种类繁多,常见的有聚乙烯(PE)、聚丙烯(PP)、聚氯乙烯(PVC)、聚苯乙烯(PS)、聚碳酸酯(PC)、ABS等。
不同种类的塑料具有不同的性能特点,如强度、硬度、韧性、耐热性、耐化学性等。
选择合适的塑料种类是保证注塑产品质量的前提。
2. 塑料特性(1)熔体流动性能:熔体流动性能是指塑料在熔融状态下流动的能力。
良好的熔体流动性能有利于提高注塑成型速度,降低能耗,减少废品率。
(2)热稳定性:热稳定性是指塑料在高温下保持性能的能力。
热稳定性好的塑料在注塑成型过程中不易发生降解,保证产品性能。
(3)耐化学性:耐化学性是指塑料抵抗化学腐蚀的能力。
耐化学性好的塑料适用于接触化学品或腐蚀性物质的场合。
(4)阻燃性:阻燃性是指塑料在燃烧过程中不易蔓延的能力。
具有阻燃性的塑料适用于防火、防爆的场合。
3. 塑料粒度塑料粒度是指塑料颗粒的尺寸。
粒度大小对注塑成型质量有一定影响,一般来说,粒度越小,熔体流动性越好,但同时也增加了能耗和设备磨损。
二、模具设计1. 模具结构模具是注塑成型过程中必不可少的工具,其结构主要包括定模、动模、流道系统、冷却系统、导向系统、锁模机构等。
(1)定模和动模:定模和动模是模具的主体部分,分别固定在注塑机的前后两腔。
定模用于固定模具和注塑物料,动模用于实现模具的闭合和开启。
(2)流道系统:流道系统是连接注射系统和模具腔的通道,其作用是引导熔体流动,减少熔体压力损失。
(3)冷却系统:冷却系统用于冷却模具腔,使熔体快速固化,提高成型速度。
(4)导向系统:导向系统用于保证模具各部分在闭合和开启过程中的准确对位。
(5)锁模机构:锁模机构用于保证模具在注塑成型过程中的稳定性和安全性。
2. 模具材料模具材料是影响模具寿命和注塑产品质量的重要因素。
常见的模具材料有钢、铝合金、铜合金等。
选择合适的模具材料应考虑以下因素:(1)模具材料的热稳定性:热稳定性好的材料在高温下不易变形,保证模具精度。
注塑成型工艺基本知识

注塑成型工艺根底知识一、注塑成型所谓注塑成型〔Injection Molding〕是指将已加热融化的材料喷射注入到模具内,经由冷却与固化后,得到成形品的方法。
也叫射出成型,适用于量产与形状复杂产品等成形加工领域。
二、注塑成形过程是以以下七大顺序执行成型过程几个步骤:1、关门2、锁模3、注射保压4、冷却5、开模6、翻开平安门7、取出产品。
重复执行这种作业流程,就可连续消费产品。
1、关门半自动需开关平安门,全自动平安门设置在关的状态。
2、锁模将挪动侧的挪动板前进,使得模具关闭,模具关闭以后确实地把模具锁紧。
3、射出〔包括保压〕螺杆快速地往前推进,把熔融之成型材料注入模腔内填充成型,填充之后压力要必须继续保持,这个动作特别取名为“保压〞。
在刚充填时模具承受的压力,一般叫做射出压或者叫做“一次压〞。
4、冷却〔以及下个动作的“可塑化过程〞〕模腔内之成型材料等待冷却凝固之过程叫“冷却〞。
在这时候射出装置也准备下次工作,这个过程叫做“可塑化过程〞。
放在料斗里的成型材料,流入加热的料管内加热,是根据螺杆旋转剪切把原料变成熔融状态,螺杆像拨取螺丝的原理一样,一面转一面后退,螺杆前端会储存熔融之成型材料,螺杆旋转时,抵抗螺杆向后退的压力称之为螺杆的“背压〞。
5、翻开模具将挪动侧的挪动板向后退,模具跟着翻开。
6、翻开平安门平安门翻开,这时成型机处于待机状能。
7、取件将成品取出,然后检视确认模具内未残留任何物件再关门.以上整个成型作业叫做一个成型周期。
成品是由模具的形状成型出来。
模具是由母模及公模组合成,公母模模仁之间留有空隙,材料在此流入压缩形成产品。
成型材料要流入公母模之前的通路有主流道〔SPRUE〕流道〔RUNNER〕闸门〔GATE〕等。
三、射出成型机射出成型机以较大工程来区分,可分为两项,锁模装置和射出装置。
1、锁模装置将模具关闭不被翻开,成型材料在模腔内冷却凝固后,模具才翻开然后取出成品等等动作的设备装置之锁模装置。
几种常用塑料的成型工艺介绍
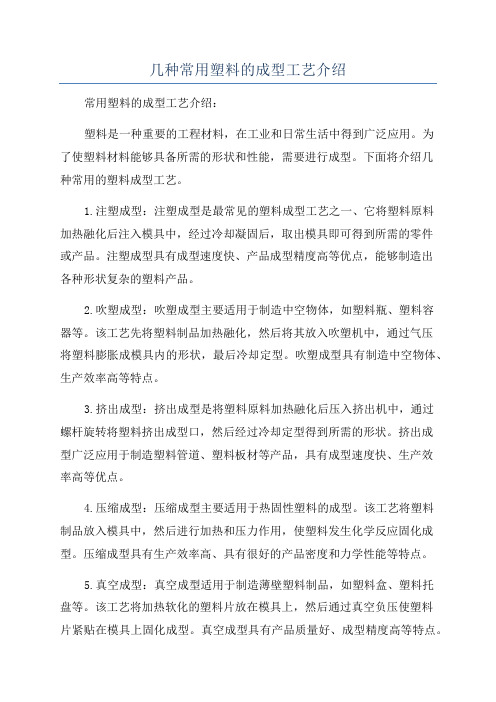
几种常用塑料的成型工艺介绍常用塑料的成型工艺介绍:塑料是一种重要的工程材料,在工业和日常生活中得到广泛应用。
为了使塑料材料能够具备所需的形状和性能,需要进行成型。
下面将介绍几种常用的塑料成型工艺。
1.注塑成型:注塑成型是最常见的塑料成型工艺之一、它将塑料原料加热融化后注入模具中,经过冷却凝固后,取出模具即可得到所需的零件或产品。
注塑成型具有成型速度快、产品成型精度高等优点,能够制造出各种形状复杂的塑料产品。
2.吹塑成型:吹塑成型主要适用于制造中空物体,如塑料瓶、塑料容器等。
该工艺先将塑料制品加热融化,然后将其放入吹塑机中,通过气压将塑料膨胀成模具内的形状,最后冷却定型。
吹塑成型具有制造中空物体、生产效率高等特点。
3.挤出成型:挤出成型是将塑料原料加热融化后压入挤出机中,通过螺杆旋转将塑料挤出成型口,然后经过冷却定型得到所需的形状。
挤出成型广泛应用于制造塑料管道、塑料板材等产品,具有成型速度快、生产效率高等优点。
4.压缩成型:压缩成型主要适用于热固性塑料的成型。
该工艺将塑料制品放入模具中,然后进行加热和压力作用,使塑料发生化学反应固化成型。
压缩成型具有生产效率高、具有很好的产品密度和力学性能等特点。
5.真空成型:真空成型适用于制造薄壁塑料制品,如塑料盒、塑料托盘等。
该工艺将加热软化的塑料片放在模具上,然后通过真空负压使塑料片紧贴在模具上固化成型。
真空成型具有产品质量好、成型精度高等特点。
6.3D打印成型:3D打印成型是近年来快速发展的塑料成型工艺之一、它通过从计算机模型中将物体分解为薄层,然后逐层累积加工,最终形成所需的塑料产品。
3D打印成型具有高度灵活性和个性化定制能力,适用于制造小批量、复杂结构的塑料产品。
以上是几种常用的塑料成型工艺的介绍。
不同的工艺适用于不同的塑料材料和产品形状需求,可以根据具体需求选择合适的成型工艺。
注塑成型技术

80%
未来发展
未来注塑成型技术将朝着智能化 、绿色化、自动化等方向发展, 进一步提高生产效率和产品质量 。
02
注塑成型原理及工艺流程
注塑成型原理
注塑成型是一种热塑性塑料加工方法,通过高温熔融塑料颗粒, 然后在高压下注入模具,冷却固化后得到产品。
注塑成型原理基于塑料的物理性质,如热塑性、流动性、热传导 性等,以及模具设计和注塑机的工作原理。
注塑成型技术
目
CONTENCT
录
• 注塑成型技术概述 • 注塑成型原理及工艺流程 • 注塑成型材料 • 注塑模具设计与制造 • 注塑成型设备 • 注塑成型技术的应用与发展趋势
01
注塑成型技术概述
定义与特点
定义
注塑成型技术是一种塑料加工方法,通过高温将塑料原料熔化, 然后注入模具中,冷却后形成所需的塑料制品。
注塑成型技术正与工业自动 化和人工智能技术相结合, 实现智能化生产,提高生产 效率和产品质量。
环保可持续发展
随着环保意识的提高,注塑 成型技术正朝着更加环保和 可持续发展的方向发展,减 少生产过程中的环境污染。
定制化生产
随着消费者需求的多样化, 注塑成型技术正朝着能够快 速生产定制化产品的方向发 展。
经济效益
注塑成型技术能够实现大规模生产,提高生产效率 ,降低生产成本,为企业带来经济效益。
注塑成型技术的发展历程
80%
早期注塑机
早期的注塑机采用液压系统,体 积较大,操作复杂,但能够完成 简单的塑料制品生产。
100%
现代注塑机
随着技术的不断发展,现代注塑 机采用电气控制系统和新型的液 压系统,具有更高的精度和效率 。
定期保养
对液压系统进行清洗、更换油 滤、检查加热器等。
注塑成型的原理
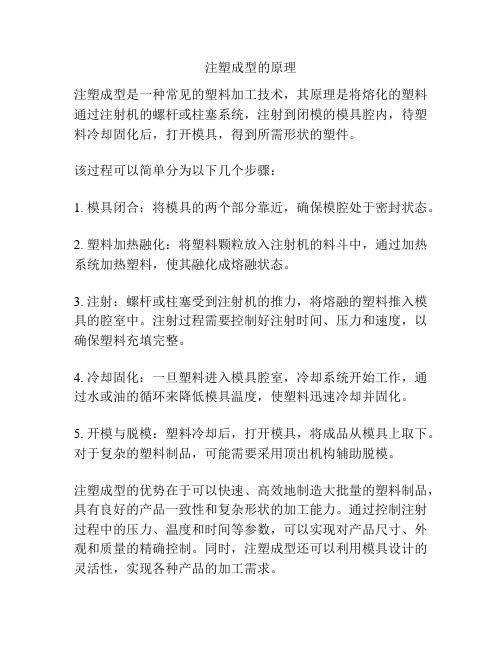
注塑成型的原理
注塑成型是一种常见的塑料加工技术,其原理是将熔化的塑料通过注射机的螺杆或柱塞系统,注射到闭模的模具腔内,待塑料冷却固化后,打开模具,得到所需形状的塑件。
该过程可以简单分为以下几个步骤:
1. 模具闭合:将模具的两个部分靠近,确保模腔处于密封状态。
2. 塑料加热融化:将塑料颗粒放入注射机的料斗中,通过加热系统加热塑料,使其融化成熔融状态。
3. 注射:螺杆或柱塞受到注射机的推力,将熔融的塑料推入模具的腔室中。
注射过程需要控制好注射时间、压力和速度,以确保塑料充填完整。
4. 冷却固化:一旦塑料进入模具腔室,冷却系统开始工作,通过水或油的循环来降低模具温度,使塑料迅速冷却并固化。
5. 开模与脱模:塑料冷却后,打开模具,将成品从模具上取下。
对于复杂的塑料制品,可能需要采用顶出机构辅助脱模。
注塑成型的优势在于可以快速、高效地制造大批量的塑料制品,具有良好的产品一致性和复杂形状的加工能力。
通过控制注射过程中的压力、温度和时间等参数,可以实现对产品尺寸、外观和质量的精确控制。
同时,注塑成型还可以利用模具设计的灵活性,实现各种产品的加工需求。
注塑成型定义
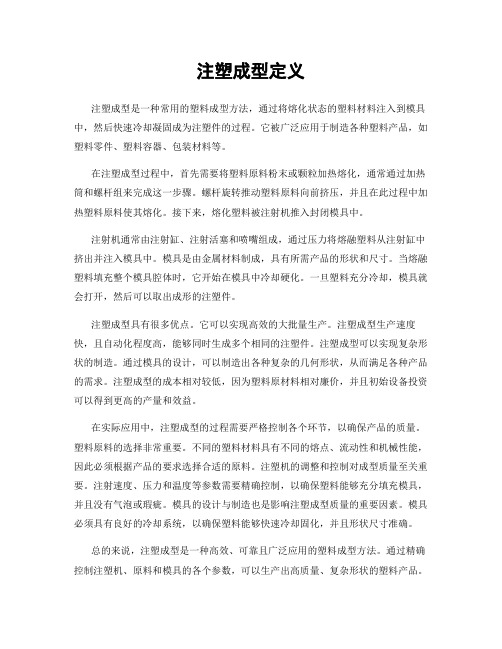
注塑成型定义注塑成型是一种常用的塑料成型方法,通过将熔化状态的塑料材料注入到模具中,然后快速冷却凝固成为注塑件的过程。
它被广泛应用于制造各种塑料产品,如塑料零件、塑料容器、包装材料等。
在注塑成型过程中,首先需要将塑料原料粉末或颗粒加热熔化,通常通过加热筒和螺杆组来完成这一步骤。
螺杆旋转推动塑料原料向前挤压,并且在此过程中加热塑料原料使其熔化。
接下来,熔化塑料被注射机推入封闭模具中。
注射机通常由注射缸、注射活塞和喷嘴组成,通过压力将熔融塑料从注射缸中挤出并注入模具中。
模具是由金属材料制成,具有所需产品的形状和尺寸。
当熔融塑料填充整个模具腔体时,它开始在模具中冷却硬化。
一旦塑料充分冷却,模具就会打开,然后可以取出成形的注塑件。
注塑成型具有很多优点。
它可以实现高效的大批量生产。
注塑成型生产速度快,且自动化程度高,能够同时生成多个相同的注塑件。
注塑成型可以实现复杂形状的制造。
通过模具的设计,可以制造出各种复杂的几何形状,从而满足各种产品的需求。
注塑成型的成本相对较低,因为塑料原材料相对廉价,并且初始设备投资可以得到更高的产量和效益。
在实际应用中,注塑成型的过程需要严格控制各个环节,以确保产品的质量。
塑料原料的选择非常重要。
不同的塑料材料具有不同的熔点、流动性和机械性能,因此必须根据产品的要求选择合适的原料。
注塑机的调整和控制对成型质量至关重要。
注射速度、压力和温度等参数需要精确控制,以确保塑料能够充分填充模具,并且没有气泡或瑕疵。
模具的设计与制造也是影响注塑成型质量的重要因素。
模具必须具有良好的冷却系统,以确保塑料能够快速冷却固化,并且形状尺寸准确。
总的来说,注塑成型是一种高效、可靠且广泛应用的塑料成型方法。
通过精确控制注塑机、原料和模具的各个参数,可以生产出高质量、复杂形状的塑料产品。
这种成型方法应用广泛,从汽车零件到电子产品外壳,从日常用品到医疗器械,注塑成型在各个领域都扮演着重要的角色。
随着科技的不断发展,注塑成型技术也将不断改进和创新,为人们创造更多高性能、高品质的塑料产品。
注塑成型原理

注塑机根据塑化方式分为柱塞式注塑机和螺杆式注塑机;按机器的传动方式又可分为液压式、机械式和液压—机械(连杆)式;按操作方式分为自动、半自动、手动注塑机。 按开闭模方向与射胶方向分卧式注塑机、立式注塑机、角式注塑机、多模转盘式注塑机等。
1) 卧式注塑机:其合模部分和注射部分处于同一水平中心线上,且模具是沿水平方向打开的。其特点是:机身矮,易于操作和维修;机器重心低,安装较平稳;制品顶出后可利用重力作用自动落下,易于实现全自动操作。目前,市场上的注塑机多采用此种型式。
⑴ 注射装置:
主要作用是使塑料均匀地塑化熔融,以足够压力和速度将一定量的熔料注入模具的型腔中。并对模腔中的熔料进行保压、补缩。当树脂在模具内流动时,则控制螺杆的移动速度(射出速度),并在填充树脂後用压力(保压压力)进行控制。
当达到一定的螺杆位置或射出压力时,则从速度控制切换成压力控制。 它主要由塑化部件(螺杆、机筒、螺杆头、喷嘴等)、料斗、计量装置、传动装置、注射和注射座移动油缸等组成。 注射螺杆的特点:注射螺杆与挤出螺杆有许多相似之处,但由于注射成型机与挤出成型机操作条件不同,所以有很多区别如下:
1、螺杆具有塑化和注射两种功能 2、注射螺杆在塑化时,对制品不 发生直接的联系,仅作预塑用; 3、塑料在塑化过程中,所经历的热历程要比挤出时长; 4、注射螺杆在塑化和注射时,均要发生轴向位移,同时螺杆又处于时转时停的间歇式工作状态,形成了注射螺杆塑化过程的非稳定性。
因此从结构上对比,注射螺杆挤出螺杆有以下几点不同: 1、注射螺杆的长径比和压缩比比较小; 2、注射螺杆均化段的螺槽较深; 3、注射螺杆的加料段较长,而均化段较短 4、注射螺杆的头部结构具有特殊形式。
注塑成型工艺原理
第一节 注塑成型概述
注塑成型定义
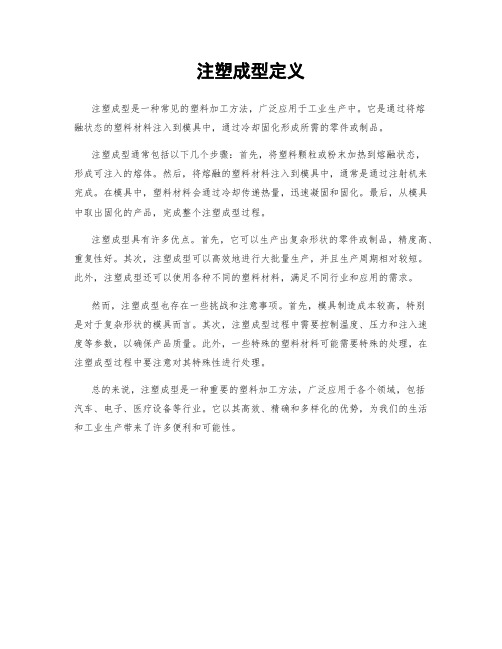
注塑成型定义
注塑成型是一种常见的塑料加工方法,广泛应用于工业生产中。
它是通过将熔
融状态的塑料材料注入到模具中,通过冷却固化形成所需的零件或制品。
注塑成型通常包括以下几个步骤:首先,将塑料颗粒或粉末加热到熔融状态,
形成可注入的熔体。
然后,将熔融的塑料材料注入到模具中,通常是通过注射机来完成。
在模具中,塑料材料会通过冷却传递热量,迅速凝固和固化。
最后,从模具中取出固化的产品,完成整个注塑成型过程。
注塑成型具有许多优点。
首先,它可以生产出复杂形状的零件或制品,精度高、重复性好。
其次,注塑成型可以高效地进行大批量生产,并且生产周期相对较短。
此外,注塑成型还可以使用各种不同的塑料材料,满足不同行业和应用的需求。
然而,注塑成型也存在一些挑战和注意事项。
首先,模具制造成本较高,特别
是对于复杂形状的模具而言。
其次,注塑成型过程中需要控制温度、压力和注入速度等参数,以确保产品质量。
此外,一些特殊的塑料材料可能需要特殊的处理,在注塑成型过程中要注意对其特殊性进行处理。
总的来说,注塑成型是一种重要的塑料加工方法,广泛应用于各个领域,包括
汽车、电子、医疗设备等行业。
它以其高效、精确和多样化的优势,为我们的生活和工业生产带来了许多便利和可能性。
注塑成型的原理
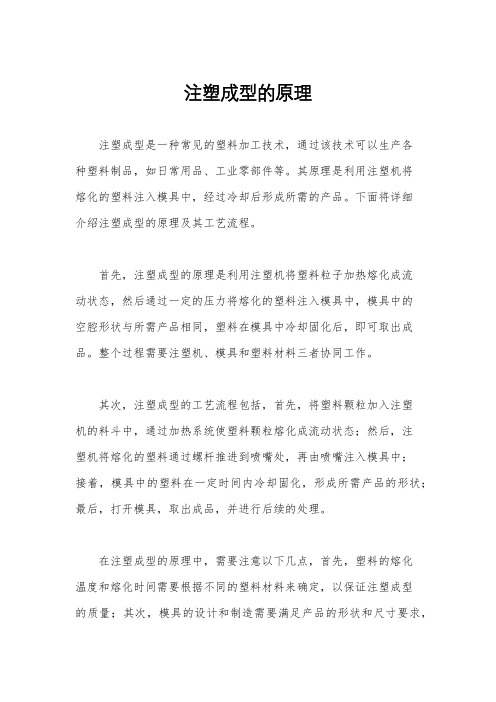
注塑成型的原理
注塑成型是一种常见的塑料加工技术,通过该技术可以生产各
种塑料制品,如日常用品、工业零部件等。
其原理是利用注塑机将
熔化的塑料注入模具中,经过冷却后形成所需的产品。
下面将详细
介绍注塑成型的原理及其工艺流程。
首先,注塑成型的原理是利用注塑机将塑料粒子加热熔化成流
动状态,然后通过一定的压力将熔化的塑料注入模具中,模具中的
空腔形状与所需产品相同,塑料在模具中冷却固化后,即可取出成品。
整个过程需要注塑机、模具和塑料材料三者协同工作。
其次,注塑成型的工艺流程包括,首先,将塑料颗粒加入注塑
机的料斗中,通过加热系统使塑料颗粒熔化成流动状态;然后,注
塑机将熔化的塑料通过螺杆推进到喷嘴处,再由喷嘴注入模具中;
接着,模具中的塑料在一定时间内冷却固化,形成所需产品的形状;最后,打开模具,取出成品,并进行后续的处理。
在注塑成型的原理中,需要注意以下几点,首先,塑料的熔化
温度和熔化时间需要根据不同的塑料材料来确定,以保证注塑成型
的质量;其次,模具的设计和制造需要满足产品的形状和尺寸要求,
同时要考虑到塑料的流动性和冷却性能;最后,注塑机的选型和操
作也对成型质量有重要影响,需要根据产品要求选择合适的注塑机,并进行正确的操作。
总之,注塑成型是一种常见的塑料加工技术,其原理是利用注
塑机将熔化的塑料注入模具中,经过冷却后形成所需的产品。
了解
注塑成型的原理及其工艺流程对于塑料加工行业的从业人员具有重
要意义,可以帮助他们更好地掌握注塑成型技术,提高生产效率和
产品质量。
同时,注塑成型技术也在不断发展和完善,未来将会有
更多的创新和应用。
注塑成型技术简介

注塑成型技术简介注塑成型技术是一种常见的塑料成型工艺,通过将熔化后的塑料注入模具中,再经过冷却凝固而得到所需形状的制品。
该技术具有高效、经济、精确和多样化的特点,广泛应用于日常生活和工业生产中。
注塑成型技术包括模具设计、原料选择、熔融加工、注塑成型和后处理等步骤。
首先,根据所需产品的形状和尺寸,设计制造相应的模具。
模具通常由金属材料制成,具有空腔和流道。
原料选择对成品的质量和性能至关重要,目前常用的塑料原料有聚丙烯(PP)、聚乙烯(PE)和聚氯乙烯(PVC)等。
在熔融加工阶段,将塑料原料通过熔化和混合的过程,使其变成可注入模具的熔融物料。
这通常通过将塑料颗粒放入注塑机中进行加热和融化完成。
注塑机由注射装置和锁模装置组成,注射装置负责将熔融物料注射到模具中,并在一定的压力下将模具封闭。
注塑成型是指将熔融物料注入到模具的过程。
在注塑期间,塑料将填充模具的空腔和流道,随后通过冷却水或其他冷却介质进行冷却,促使塑料凝固。
凝固后,模具开启,制品可取出。
最后,根据产品要求进行后处理。
这可能包括去除模具留下的毛刺,修整边缘,上色或上漆等。
注塑成型技术的优点包括:生产效率高,可进行连续生产;制品精确,形状符合设计要求;成品质量稳定,表面光滑;适用范围广泛,可生产各种材质的制品;自动化程度高,劳动力成本低。
注塑成型技术广泛应用于日常生活中,如塑料容器、玩具、电器外壳等产品的制造,也应用于工业生产中,如汽车零部件、电子元器件等。
随着科技进步,注塑成型技术不断创新改进,为各种行业带来了更多的应用前景。
注塑成型技术作为一种高效、经济、精确和多样化的塑料成型工艺,已经成为现代工业发展不可或缺的重要技术之一。
在过去几十年间,注塑成型技术经历了飞速的发展,从最初的手工操作到现在的全自动化注塑机,不断提高生产效率和产品质量。
注塑成型技术的优点之一是可以实现高效率的大规模生产。
由于注塑成型可以通过自动化生产线实现连续生产,能够迅速地制造大量相同尺寸、相同形状的产品。
- 1、下载文档前请自行甄别文档内容的完整性,平台不提供额外的编辑、内容补充、找答案等附加服务。
- 2、"仅部分预览"的文档,不可在线预览部分如存在完整性等问题,可反馈申请退款(可完整预览的文档不适用该条件!)。
- 3、如文档侵犯您的权益,请联系客服反馈,我们会尽快为您处理(人工客服工作时间:9:00-18:30)。
Injection Molding Equipment
CLAMP SIZE 锁模力
Material Selection
选料
Projected Area
投影面积 3~5吨/平方英寸
Part Design
产品设计
Wall Thickness
壁厚
Flow Length
流动长度
Injection Pressure & Speed 注射压力和速度
Hot Cylinder to Colder Mold 提供从热的料筒到相对冷的模具的机械和热连接
Injection Molding Equipment
e
GEAM Plastics
INJECTION MOLDING 注射模塑技术
GE塑料提供非常广泛的工程塑料选择
Ultem* 树脂 heat resistance
Lexan*树脂 impact sistance
= 由 GE 塑料生产
高性能 工程级
普通级
PEI
PSO
LCP PPS
PEI/PC PPO/PA PBT
Injection Molding Equipment
Screw Type Machines Are Recommended 推荐采用的螺杆类型
•Uniform Plasticizing 均匀塑化
•Uniform Stock Temperature 均匀储料温度
•Less Pressure Loss 低压力损耗
Injection Molding Introduction
Disadvantages of Injection Molding
Tooling Costs are High High Machinery and Auxiliary Costs High Pressure Process Limited Large Part Capability
MACHINE SHOT SIZE 机器注射容量
Part Weight = 30 - 80 % of Machine Shot Size 制件重量 = 30 - 80 % 机器注射容量 Optimal Part Weight = 40 ~ 60 % of Machine Shot Size 制件重量 = 40- 60 % 机器注射容量
•Provides Injection and Packing Pressure •Provides Torque to Turn the Screw
The Screw Barrel
•Melting and Homogenizing the Resin •Injection of the Plastic Into the Mold
Clamping Mechanisms Double Toggle Clamping System
Injection Molding Equipment
Clamping Mechanisms Hydraulic Clamping System
Injection Molding Equipment
PC
PC/PBT
PPO
POM
PA
PC/ABS
PC/ASA
ASA
ABS PS
PP
PET
PVC PE
无定形
结晶性
Cycolac*树脂 colorability and visualfx
Xenoy*树脂 impact resistance chemical resistance
Noryl*树脂 impact resistance hydrolytic stability processability
•Compression Ratio压缩比 = hf / hm =2.5:1 (2.0:1 ~ 3 .0:1)
•Cylinder bi-metallic for Abrasion Resistance 双金属料筒
Injection Molding Equipment
往复式螺杆头结构
检查环类型: 止回环
Injection Molding Equipment
The Clamping Unit
•Open and Closes Mold •Holds the Mold Closed During Injection •Cools and Solidifies Part
Injection Molding Equipment
•Streamlined Melt Flow 线性熔融流动
•Faster Cycles 更快成型周期
Injection Molding Equipment
hm
D
hf
Metering 计量
Transition 过渡
Feed 进料
L
Screw and Cylinder Design 螺杆和料筒设计
•L/D = 20:1 (18 ~ 24 :1)
Injection Molding Introduction注塑成型介绍
Material 材料
Tooling 模具
Processing 工艺
GOOD PART
好产品
Design设计
注塑成型介绍
注塑成型优点
生产速度高 可以大批量生产 人工成本低 容易自动化 2次加工量小 可以生产很小的零件
废品损失小 尺寸变化小 Molded-in Inserts Available Glass, Carbon, etc. Fillers Complex Part Capability Good Decoration Possible
Injection Molding Equipment
Equipment 设备
Injection Molding Equipment
Clamp Unit
Screw & Barrel Injection Unit
Injection Molding Equipment
The Injection Unit
熔融树脂流过 开放检查环
检查环关闭, 防止在 注塑过程中料的回流
建议采用止逆阀
Injection Molding Equipment
Standard Cylinder Nozzles 标准料筒喷嘴
Heating Band 加热环
To Mold 到模具
Cylinder Bore料筒 主体
Provides Mechanical and Thermal Connection From