压力管道无损检测技术应用分析.
浅析长输压力管道无损检测技术
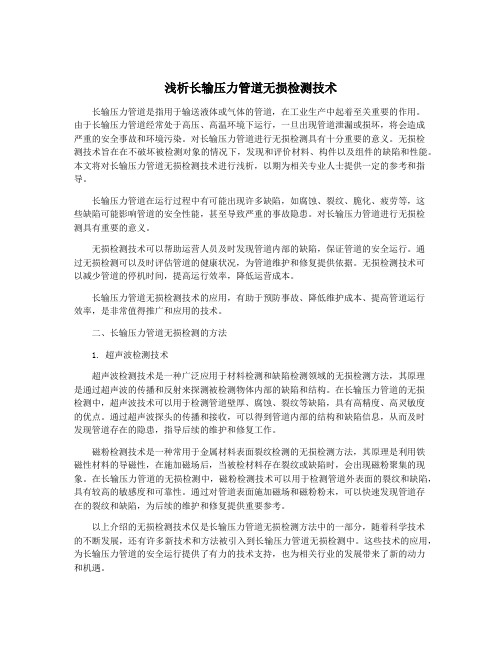
浅析长输压力管道无损检测技术长输压力管道是指用于输送液体或气体的管道,在工业生产中起着至关重要的作用。
由于长输压力管道经常处于高压、高温环境下运行,一旦出现管道泄漏或损坏,将会造成严重的安全事故和环境污染。
对长输压力管道进行无损检测具有十分重要的意义。
无损检测技术旨在在不破坏被检测对象的情况下,发现和评价材料、构件以及组件的缺陷和性能。
本文将对长输压力管道无损检测技术进行浅析,以期为相关专业人士提供一定的参考和指导。
长输压力管道在运行过程中有可能出现许多缺陷,如腐蚀、裂纹、脆化、疲劳等,这些缺陷可能影响管道的安全性能,甚至导致严重的事故隐患。
对长输压力管道进行无损检测具有重要的意义。
无损检测技术可以帮助运营人员及时发现管道内部的缺陷,保证管道的安全运行。
通过无损检测可以及时评估管道的健康状况,为管道维护和修复提供依据。
无损检测技术可以减少管道的停机时间,提高运行效率,降低运营成本。
长输压力管道无损检测技术的应用,有助于预防事故、降低维护成本、提高管道运行效率,是非常值得推广和应用的技术。
二、长输压力管道无损检测的方法1. 超声波检测技术超声波检测技术是一种广泛应用于材料检测和缺陷检测领域的无损检测方法,其原理是通过超声波的传播和反射来探测被检测物体内部的缺陷和结构。
在长输压力管道的无损检测中,超声波技术可以用于检测管道壁厚、腐蚀、裂纹等缺陷,具有高精度、高灵敏度的优点。
通过超声波探头的传播和接收,可以得到管道内部的结构和缺陷信息,从而及时发现管道存在的隐患,指导后续的维护和修复工作。
磁粉检测技术是一种常用于金属材料表面裂纹检测的无损检测方法,其原理是利用铁磁性材料的导磁性,在施加磁场后,当被检材料存在裂纹或缺陷时,会出现磁粉聚集的现象。
在长输压力管道的无损检测中,磁粉检测技术可以用于检测管道外表面的裂纹和缺陷,具有较高的敏感度和可靠性。
通过对管道表面施加磁场和磁粉粉末,可以快速发现管道存在的裂纹和缺陷,为后续的维护和修复提供重要参考。
渗透检测在压力容器、管道无损检测中的应用
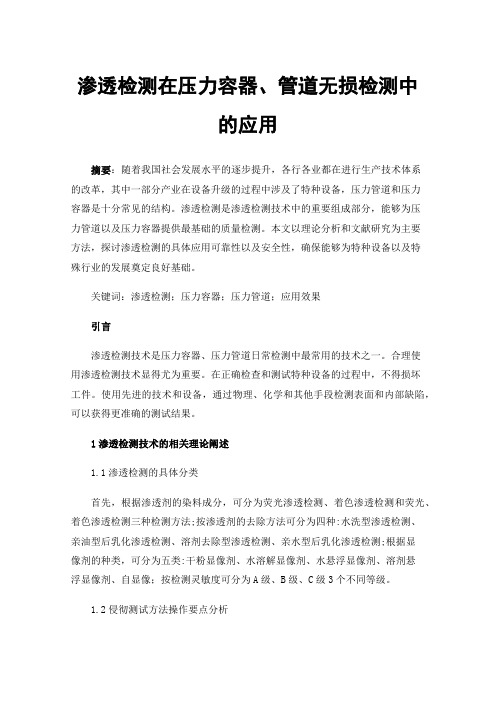
渗透检测在压力容器、管道无损检测中的应用摘要:随着我国社会发展水平的逐步提升,各行各业都在进行生产技术体系的改革,其中一部分产业在设备升级的过程中涉及了特种设备,压力管道和压力容器是十分常见的结构。
渗透检测是渗透检测技术中的重要组成部分,能够为压力管道以及压力容器提供最基础的质量检测。
本文以理论分析和文献研究为主要方法,探讨渗透检测的具体应用可靠性以及安全性,确保能够为特种设备以及特殊行业的发展奠定良好基础。
关键词:渗透检测;压力容器;压力管道;应用效果引言渗透检测技术是压力容器、压力管道日常检测中最常用的技术之一。
合理使用渗透检测技术显得尤为重要。
在正确检查和测试特种设备的过程中,不得损坏工件。
使用先进的技术和设备,通过物理、化学和其他手段检测表面和内部缺陷,可以获得更准确的测试结果。
1渗透检测技术的相关理论阐述1.1渗透检测的具体分类首先,根据渗透剂的染料成分,可分为荧光渗透检测、着色渗透检测和荧光、着色渗透检测三种检测方法;按渗透剂的去除方法可分为四种:水洗型渗透检测、亲油型后乳化渗透检测、溶剂去除型渗透检测、亲水型后乳化渗透检测;根据显像剂的种类,可分为五类:干粉显像剂、水溶解显像剂、水悬浮显像剂、溶剂悬浮显像剂、自显像;按检测灵敏度可分为A级、B级、C级3个不同等级。
1.2侵彻测试方法操作要点分析由于大多数压力容器和压力管道都是特殊设备,虽然在质量检测过程中渗透检测方法可以实现渗透检测,但为了进一步提高检测结果的准确性和检测过程的安全性,对工作点的严格控制也是必要的。
根据目前国内绝大多数压力管道和压力容器的侵彻试验经验,可以从以下几个方面进行调整。
首先,压力管道和压力设备在日常使用中存在着许多干扰因素,如日常清洗中残留的化学清洗剂、生产安装过程中的焊接位置质量、使用过程中附着在设备表面的污染物等,会影响渗透测试的准确性。
这些因素不仅影响渗透检测的准确性,还可能与渗透剂发生化学反应,影响最终灵敏度。
压力管道的无损检测

图D.3 源在外单壁 透照环向对接焊接 接头,透照厚度比 K=1.1时的透照次 数
精品课件
6.像质计的选择
压力管道射线检测按JB/T4730标准规定所选择 的像质计有三种即:
JB/T 7902—1999 线型像质计 (普通型) HB 7684—2000 射线照相用线型像质计(特殊
型) JB/T4730·2-2005等径像质计(专用型)
头
精品课件
(3)射线和超声波应用原则
GC1、GC2级管道的焊接接头一般应进行射线 或超声波检测抽查
GC3级管道的焊接接头,如未发现异常情况, 一般不进行焊接接头的射线和超声波的抽查
射线和超声波的抽查比例按有关规定进行。
精品课件
需要掌握的问题
1、压力管道表面检测方法的选择原则? 2、在用工业管道表面无损检测的重点部位有
对评定范围内的黑度D>4.0的底片,如有
计量检定报告证明底片评定范围内的亮度 能够满足4.10.3的要求,允许进行评定。
部位进行表面检测。精品课件
(2)射线和超声波重点检测的部位 a.制造、安装中返修过的焊接接头和固定口 b.错口、咬边严重超标的焊接接头 c.表面检测发现裂纹的焊接接头 d.泵、压缩机进出口第一道焊接接头 e.支吊架损坏部位附近的焊接接头 f.异种钢焊接接头 g.硬度检测发现硬度异常的焊接接头 h.使用中发生泄漏附近的焊接接头 i.检验人员和使用单位认为有必要抽查的焊接接
精品课件
7.像质计的摆放与观察
(1)一般摆放
《4.7.1 》 像质计一般应放置在工件源侧表面焊
接接头的一端(在被检区长度的1/4左右位置), 金属丝应横跨焊缝,细丝置于外侧。当一张胶 片上同时透照多条焊接接头时,像质计应放置在 透照区最边缘的焊缝处。
压力管道无损检测技术及应用
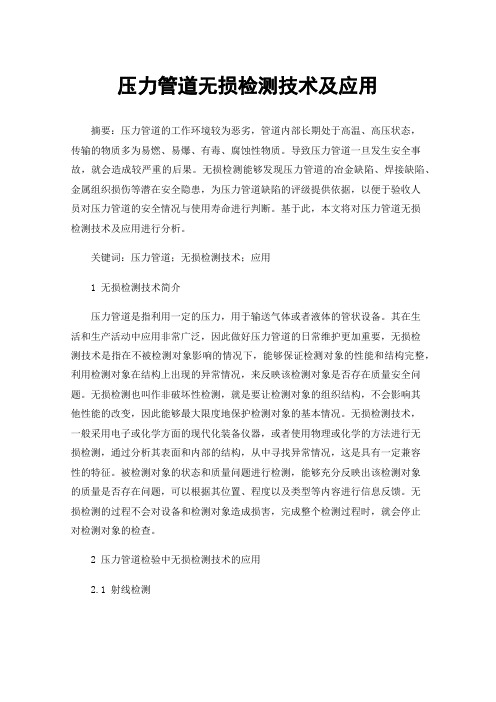
压力管道无损检测技术及应用摘要:压力管道的工作环境较为恶劣,管道内部长期处于高温、高压状态,传输的物质多为易燃、易爆、有毒、腐蚀性物质。
导致压力管道一旦发生安全事故,就会造成较严重的后果。
无损检测能够发现压力管道的冶金缺陷、焊接缺陷、金属组织损伤等潜在安全隐患,为压力管道缺陷的评级提供依据,以便于验收人员对压力管道的安全情况与使用寿命进行判断。
基于此,本文将对压力管道无损检测技术及应用进行分析。
关键词:压力管道;无损检测技术;应用1 无损检测技术简介压力管道是指利用一定的压力,用于输送气体或者液体的管状设备。
其在生活和生产活动中应用非常广泛,因此做好压力管道的日常维护更加重要,无损检测技术是指在不被检测对象影响的情况下,能够保证检测对象的性能和结构完整,利用检测对象在结构上出现的异常情况,来反映该检测对象是否存在质量安全问题。
无损检测也叫作非破坏性检测,就是要让检测对象的组织结构,不会影响其他性能的改变,因此能够最大限度地保护检测对象的基本情况。
无损检测技术,一般采用电子或化学方面的现代化装备仪器,或者使用物理或化学的方法进行无损检测,通过分析其表面和内部的结构,从中寻找异常情况,这是具有一定兼容性的特征。
被检测对象的状态和质量问题进行检测,能够充分反映出该检测对象的质量是否存在问题,可以根据其位置、程度以及类型等内容进行信息反馈。
无损检测的过程不会对设备和检测对象造成损害,完成整个检测过程时,就会停止对检测对象的检查。
2 压力管道检验中无损检测技术的应用2.1 射线检测射线检测法主要是利用X射线或其他放射性元素具有的较强放射线来穿透压力管道,检测管道内部是否存在结构缺陷或功能缺陷,并以胶片记录检测结果。
射线检测法主要适用于焊接构件的对接接头和角接接头。
射线检测法的优点是能够通过胶片直观地看清楚质量缺陷的类型、数量、尺寸和位置。
射线检测法的缺点是检测速度较慢,而且X射线和放射性元素对人体有害,需要做好检测防护,避免检测人员过度辐射。
压力管道无损检测
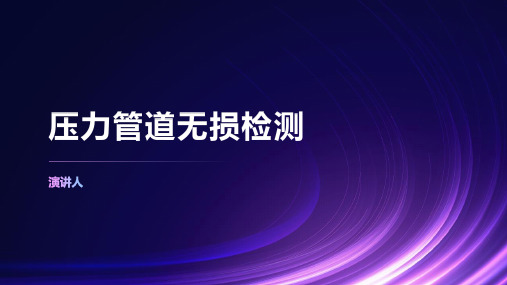
免管道损坏造成的损失 无损检测可以减少停机时间,提
03
高生产效率 无损检测可以延长管道使用寿命, 04 降低更换成本
智能化检测技术
利用人工智能 技术进行数据 分析和处理
采用自动化检 测设备,提高 检测效率和准 确性
利用物联网技 术实现远程监 控和实时数据 传输
结合大数据技 术,实现检测 结果的智能分 析和预测
输电线路检测:检测输电线路腐蚀、 02 磨损等情况,保障线路安全
变电站检测:检测变电站设备及管 0 3 道的缺陷,确保变电站安全运行
核电站检测:检测核电站设备及管 0 4 道的缺陷,保障核电站安全运行
安全性高
D
降低维修成本,避免不必要的管道更换
C 检生有害物质
压力管道无损检测
目录
01. 无损检测技术 02. 无损检测的应用 03. 无损检测的优势 04. 无损检测的发展趋势
超声波检测
原理:利用超声波在介质中的传播 0 1 和反射特性,检测管道内部缺陷
优点:检测精度高,可检测微小缺 02 陷
应用:广泛应用于压力管道、锅炉、 03 储罐等设备的检测
注意事项:需要选择合适的检测频 0 4 率和探头,以获得最佳的检测效果
电磁检测:利用电 磁波对管道进行无 损检测,减少对环 境的影响
激光检测:利用激 光对管道进行无损 检测,减少对环境 的影响
红外检测:利用红 外线对管道进行无 损检测,减少对环 境的影响
射线检测:利用射 线对管道进行无损 检测,减少对环境 的影响
超声波-电磁复合检 测:利用超声波和 电磁波对管道进行 复合检测,减少对 环境的影响
远程检测技术
STEP1
STEP2
STEP3
压力管道缺陷产生原因及无损检测
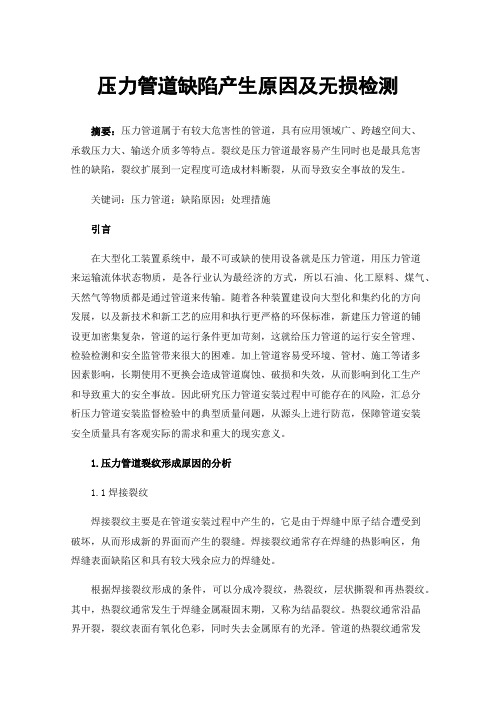
压力管道缺陷产生原因及无损检测摘要:压力管道属于有较大危害性的管道,具有应用领域广、跨越空间大、承载压力大、输送介质多等特点。
裂纹是压力管道最容易产生同时也是最具危害性的缺陷,裂纹扩展到一定程度可造成材料断裂,从而导致安全事故的发生。
关键词:压力管道;缺陷原因;处理措施引言在大型化工装置系统中,最不可或缺的使用设备就是压力管道,用压力管道来运输流体状态物质,是各行业认为最经济的方式,所以石油、化工原料、煤气、天然气等物质都是通过管道来传输。
随着各种装置建设向大型化和集约化的方向发展,以及新技术和新工艺的应用和执行更严格的环保标准,新建压力管道的铺设更加密集复杂,管道的运行条件更加苛刻,这就给压力管道的运行安全管理、检验检测和安全监管带来很大的困难。
加上管道容易受环境、管材、施工等诸多因素影响,长期使用不更换会造成管道腐蚀、破损和失效,从而影响到化工生产和导致重大的安全事故。
因此研究压力管道安装过程中可能存在的风险,汇总分析压力管道安装监督检验中的典型质量问题,从源头上进行防范,保障管道安装安全质量具有客观实际的需求和重大的现实意义。
1.压力管道裂纹形成原因的分析1.1焊接裂纹焊接裂纹主要是在管道安装过程中产生的,它是由于焊缝中原子结合遭受到破坏,从而形成新的界面而产生的裂缝。
焊接裂纹通常存在焊缝的热影响区,角焊缝表面缺陷区和具有较大残余应力的焊缝处。
根据焊接裂纹形成的条件,可以分成冷裂纹,热裂纹,层状撕裂和再热裂纹。
其中,热裂纹通常发生于焊缝金属凝固末期,又称为结晶裂纹。
热裂纹通常沿晶界开裂,裂纹表面有氧化色彩,同时失去金属原有的光泽。
管道的热裂纹通常发生在杂质较多的碳钢,奥氏体不锈钢以及低合金钢等材料的焊缝中。
冷裂纹指在焊缝冷却至马氏体转变温度点以下而产生的裂纹,通常在焊后一段时间后发生,因此又称为延迟裂纹。
钢的淬硬倾向、拘束应力和焊接接头中的扩散氢含量是致使冷裂纹发生的原因。
冷裂纹的开裂方式分为穿晶开裂,沿晶开裂以及二者混合出现。
压力管道缺陷产生原因及无损检测
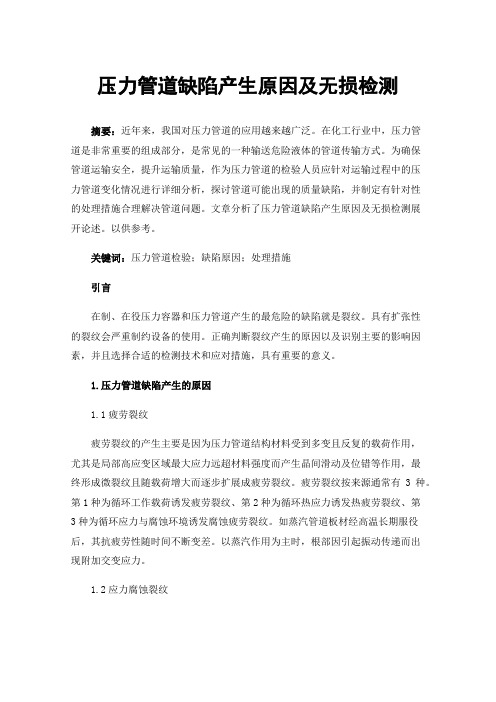
压力管道缺陷产生原因及无损检测摘要:近年来,我国对压力管道的应用越来越广泛。
在化工行业中,压力管道是非常重要的组成部分,是常见的一种输送危险液体的管道传输方式。
为确保管道运输安全,提升运输质量,作为压力管道的检验人员应针对运输过程中的压力管道变化情况进行详细分析,探讨管道可能出现的质量缺陷,并制定有针对性的处理措施合理解决管道问题。
文章分析了压力管道缺陷产生原因及无损检测展开论述。
以供参考。
关键词:压力管道检验;缺陷原因;处理措施引言在制、在役压力容器和压力管道产生的最危险的缺陷就是裂纹。
具有扩张性的裂纹会严重制约设备的使用。
正确判断裂纹产生的原因以及识别主要的影响因素,并且选择合适的检测技术和应对措施,具有重要的意义。
1.压力管道缺陷产生的原因1.1疲劳裂纹疲劳裂纹的产生主要是因为压力管道结构材料受到多变且反复的载荷作用,尤其是局部高应变区域最大应力远超材料强度而产生晶间滑动及位错等作用,最终形成微裂纹且随载荷增大而逐步扩展成疲劳裂纹。
疲劳裂纹按来源通常有3种。
第1种为循环工作载荷诱发疲劳裂纹、第2种为循环热应力诱发热疲劳裂纹、第3种为循环应力与腐蚀环境诱发腐蚀疲劳裂纹。
如蒸汽管道板材经高温长期服役后,其抗疲劳性随时间不断变差。
以蒸汽作用为主时,根部因引起振动传递而出现附加交变应力。
1.2应力腐蚀裂纹应力腐蚀裂纹金属材料在一定腐蚀环境下受到拉伸应力作用所产生的开裂,其典型代表之一就是含氯离子奥氏体不锈钢压力管。
1.3晶间腐蚀晶间腐蚀主要受某些介质的腐蚀影响,最常见的是不锈钢管道的焊接表面,特别是熔合线和热影响区,晶间贫铬是一个主要的促成因素,因此结构的连续性受到严重影响。
1.4局部腐蚀局部腐蚀多指点状腐蚀,即当金属材料暴露在腐蚀性溶液中时,金属材料的表面会逐渐发生局部腐蚀现象,随后腐蚀不断发展,腐蚀孔不断加深。
局部腐蚀也普遍存在于磨损腐蚀之中,磨损腐蚀表现为金属材料兼具磨损与腐蚀两种功能,促使磨损与腐蚀迅速发展,从而使金属材料的破坏速度与破坏程度加大。
无损检测技术应用及JB4730标准介绍

由于本次修订既包括了金属材料制锅炉、压力容器及压力
管道原材料、零部件和设备的制造、安装检测。同时也包括了
金属材料制锅炉、压力容器及压力管道的在用检测。此外从本
质上看其它承压类设备采用本标准进行检测也不存在任何技术
障碍。因此本标准的标题改为《承压设备无损检测》应该说是
比较合适的。
9
承压设备无损检测重要意义
五、无损检测:JB/T4730-2005《承压设备无损检测》。
六、试验方法标准:GB/T10180-98《工业锅炉热工试验规范》、GB/T10184-98
《电站锅炉性能试验规程》、GB10180-88《工业锅炉热工试验规范》、
GB/T13311-91《锅炉受压元件焊接接头机械性能试验方法》、 JB/T1612-94《锅
2、公用管道:GB50028-93《城镇燃气设计规范》、CJJ28-89《城市供 热管网工程施工及验收规范》、CJJ33-89《城镇燃气输配工程施工及验收 规范》等。
3、长输管道:GB50251-94《输气管道工程设计规范》、GB50253-94 《输油管道工程设计规范》、SY0401-98《输油输气管道线路工程施工及
炉水压试验技术条件》等。
8
JB/T4730标题《承压设备无损检测》
JB4739-94标准主要用于压力容器及部分压力管道设 计制造、安装无损检测,属于制造检验标准的范畴,当时锅炉 系统、建设部、电力系统、长输管道系统都有自己一套相对独 立检测标准,标准使用比较乱,而且缺口比较大。
由于锅炉、压力容器及压力管道都是承压设备,有比较深 刻的内在联系,美国ASME《锅炉压力容器规范》第Ⅴ篇就是将 其检测内容放在一起考虑的,2003年国务院颁布的《特种设备 安全监察条例》也将锅炉、压力容器及压力管道等通称为承压 类特种设备。从这个角度考虑,将承压类特种设备的无损检测 标准统一在一起,一方面检验检测单位使用起来比较方便和明 确,另一方面安全监察机构管理起来也比较清楚。(标准的制 定思路)
探究TOFD检测技术在压力管道无损检测中的运用
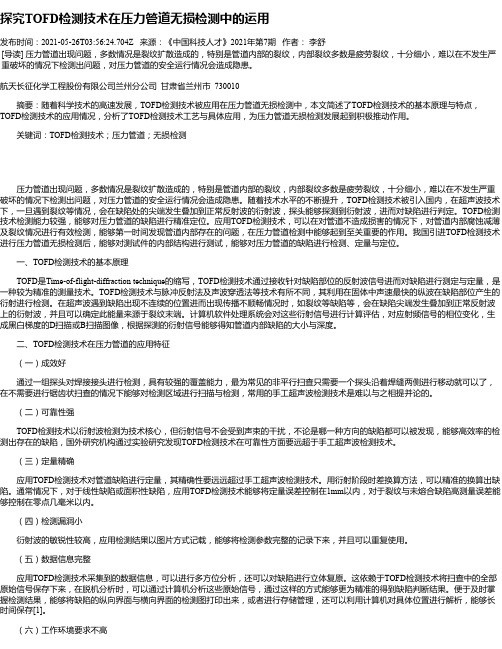
探究TOFD检测技术在压力管道无损检测中的运用发布时间:2021-05-26T03:56:24.704Z 来源:《中国科技人才》2021年第7期作者:李舒[导读] 压力管道出现问题,多数情况是裂纹扩散造成的,特别是管道内部的裂纹,内部裂纹多数是疲劳裂纹,十分细小,难以在不发生严重破坏的情况下检测出问题,对压力管道的安全运行情况会造成隐患。
航天长征化学工程股份有限公司兰州分公司甘肃省兰州市 730010摘要:随着科学技术的高速发展,TOFD检测技术被应用在压力管道无损检测中,本文简述了TOFD检测技术的基本原理与特点,TOFD检测技术的应用情况,分析了TOFD检测技术工艺与具体应用,为压力管道无损检测发展起到积极推动作用。
关键词:TOFD检测技术;压力管道;无损检测压力管道出现问题,多数情况是裂纹扩散造成的,特别是管道内部的裂纹,内部裂纹多数是疲劳裂纹,十分细小,难以在不发生严重破坏的情况下检测出问题,对压力管道的安全运行情况会造成隐患。
随着技术水平的不断提升,TOFD检测技术被引入国内,在超声波技术下,一旦遇到裂纹等情况,会在缺陷处的尖端发生叠加到正常反射波的衍射波,探头能够探测到衍射波,进而对缺陷进行判定。
TOFD检测技术检测能力较强,能够对压力管道的缺陷进行精准定位。
应用TOFD检测技术,可以在对管道不造成损害的情况下,对管道内部腐蚀减薄及裂纹情况进行有效检测,能够第一时间发现管道内部存在的问题,在压力管道检测中能够起到至关重要的作用。
我国引进TOFD检测技术进行压力管道无损检测后,能够对测试件的内部结构进行测试,能够对压力管道的缺陷进行检测、定量与定位。
一、TOFD检测技术的基本原理TOFD是Time-of-flight-diffraction technique的缩写,TOFD检测技术通过接收针对缺陷部位的反射波信号进而对缺陷进行测定与定量,是一种较为精准的测量技术。
TOFD检测技术与脉冲反射法及声波穿透法等技术有所不同,其利用在固体中声速最快的纵波在缺陷部位产生的衍射进行检测。
压力管道的无损检测技术
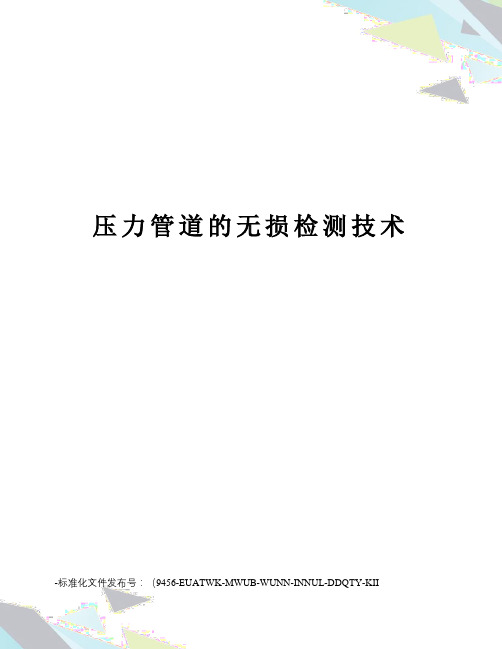
压力管道的无损检测技术-标准化文件发布号:(9456-EUATWK-MWUB-WUNN-INNUL-DDQTY-KII压力管道的无损检测技术一:二:基本方法:射线、超声、磁粉、渗透教材:P281,P381一:磁粉检测(MT)磁粉探伤原理:铁磁性材料和工件被磁化后,由于不连续性的存在,使工件表面和近表面的磁力线发生局部畸变而产生漏磁场,吸附施加在工件表面的磁粉,形成在合适光照下目视可见的磁痕,从而显示出不连续性的位置、形状和大小。
磁粉探伤的适用范围:磁粉探伤适用于检测铁磁性材料表面和近表面尺寸很小,间隙极窄(如可以检测出长0.1mm/宽为微米级的裂纹)目视难以看出的不连续性。
磁粉探伤不能检测奥氏体不锈钢材料和用奥氏体不锈钢焊条焊接的焊缝,也不能检测铜、铝、钛等非磁性材料。
马氏体不锈钢和沉淀硬化不锈钢具有磁性,可以进行磁粉探伤。
磁粉探伤可以发现裂纹、夹杂、发纹、白点、折叠、冷隔和疏松等缺陷,但对于表面浅的划伤、埋藏较深的孔洞和与工件夹角小于20度的分成及折叠难以发现。
磁粉探伤的基本操作步骤:1:预处理;2:磁化被检工件表面;3:施加磁粉和磁悬液;4:在合适的光照下观察和评定磁痕;5:退磁;6:后处理:思考题:1:叙述磁粉探伤的原理和适用范围。
2:写出磁粉探伤的基本操作步骤。
二:渗透探伤(PT)渗透探伤原理:渗透探伤是基于液体的毛细管作用(或毛细管现象)和固体染料在一定条件下的发光现象。
渗透探伤的工作原理是:被检工件在被施涂含有荧光染料或着色染料的渗透液后,在毛细管作用下,经过一定时间的渗透,渗透液可以渗进表面开口的缺陷中;经过去除被检工件表面多余的渗透液和干燥后,再在被检工件表面施涂吸附介质——显象剂;同样,在毛细管作用下,显象剂将吸附缺陷中的渗透液,使渗透液回渗到显象剂中;在一定光源下(黑光或白光),缺陷处之渗透液痕迹被显示(黄绿色荧光或鲜艳红色),从而检测处缺陷的形貌及分布状态。
渗透探伤可以检查金属和非金属材料的表面开口缺陷,例如:裂纹、疏松、气孔、夹渣、冷隔、折叠和氧化斑疤等。
压力管道无损检测与安全评估技术
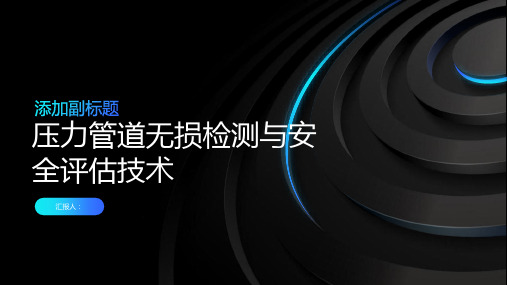
无损检测技术的应用范围
压力管道
石油化工
航空航天
核工业
无损检测技术的优缺点
优点:无损检测技术可以在不损伤管道的情况下进行检测,能够及时发现管道的缺陷和潜在问题,提高检测的准确性和可靠性。 缺点:无损检测技术需要专业的技术人员和设备,检测成本较高,同时对于一些微小缺陷的检测效果可能不如有损检测技术。
体系。
压力管道化工行业的应用
压力管道无损检测与安全评估技术用于检测石油化工管道的裂纹、腐蚀等缺陷 该技术能够评估管道的剩余寿命和可靠性,确保管道安全运行 在石油化工行业中,该技术有助于预防事故发生,降低生产风险 压力管道无损检测与安全评估技术为石油化工行业的安全生产提供了有力保障
在电力行业的应用
压力管道无损检测与安全评估技术用于检测电力行业中的管道设备,确保其安全运行。 该技术能够检测出管道的缺陷和损伤,为电力行业的安全生产和设备维护提供保障。 在电力行业中,该技术的应用提高了设备检测的准确性和可靠性,降低了事故发生的概率。 压力管道无损检测与安全评估技术为电力行业的发展提供了重要的技术支持和保障。
案例的启示与借鉴意义
案例选择:具有代表性,能够反映无损检测与安全评估技术的实际应用情况。 案例分析:深入剖析,总结出实践中的经验教训和问题所在。 启示:从案例中获得启示,为今后的工作提供借鉴和参考。 借鉴意义:将案例的成功经验应用到实际工作中,提高无损检测与安全评估技术的水平。
感谢您的观看
汇报人:
在城市供水管网中的应用
压力管道无损检测与安全评估技术可以检测出供水管网的缺陷和损伤,确保供水安全。
该技术可以对管网进行实时监测,及时发现潜在的安全隐患,避免事故发生。
通过压力管道无损检测与安全评估技术,可以评估管网的寿命和可靠性,为管网的维护和更新提 供依据。
压力管道无损检测

射线照相设备可分为:X射线探伤机;γ射线探伤机;高能射线探伤设备三大类。X射线探伤机管电压在450 kV以下,可分为携带式,移动式两类。最大穿透钢铁厚度可达100 mm。γ射线探伤机的射线能量取决于放射性同位素的种类,常用γ源有C060、Irl92、Se75三种,最大穿透钢铁厚度可达200 mm。高能射线探伤设备由电子加速器(包括直线加速器、回旋加速器)产生能量为1~24 MeV射线。最大穿透钢铁厚度可达500 mm。
②象质计(透度计)的应用 为了评定底片的灵敏度,需要采用象质计,象质计是用来检查透照技术和胶片处理质量的。衡量该质量的数值是象质指数,它等于底片上能识别出的最细钢丝的线编号。用底片上必须显示的最小钢丝直径与相应的象质指数来表示照相的灵敏度。所谓射线照相的灵敏度是射线照相能发现最小缺陷的能力。射线照相灵敏度分为绝对灵敏度和相对灵敏度。绝对灵敏度是指射线透照某工件时能发现最小缺陷的尺寸,射线照相的相对灵敏度K用透照方向上所能发现缺陷的最小厚度尺寸AD与该处的穿透厚度d的百分比表示,即 目前标准规定的象质指数,换算成相对灵敏度,其值大约在1%~2%之间。
(1). 射线照相法的原理
X射线和γ射线通过物质时,其强度逐渐减弱。射线强度的衰减由以下公式表示: 通过物体后的射线强度减弱主要与物质的衰减系数和物体厚度有关。一般认为是由光电效应引起的吸收、康普顿效应引起的散射和电子对效应引起的吸收三种原因造成的。 射线还有一个重要性质,就是能使胶片感光。当X射线或γ射线照射胶片时,与普通光线一样,能使胶片乳剂层中的卤化银产生潜象中心,经过显影和定影后就黑化,接收射线越多的部位黑化程度越高,这个作用叫做射线的照相作用。因为X射线或γ射线使卤化银感光作用比普通光线小得多,所以必须使用特殊的X射线胶片。这种胶片的两面都涂敷了较厚的乳胶。此外,还使用一种能加强感光作用的增感屏。增感屏通常用铅箔做成。了解射线穿过物质的衰减作用和照相作用后,就不难理解射线检测的原理。
对压力管道检验的分析
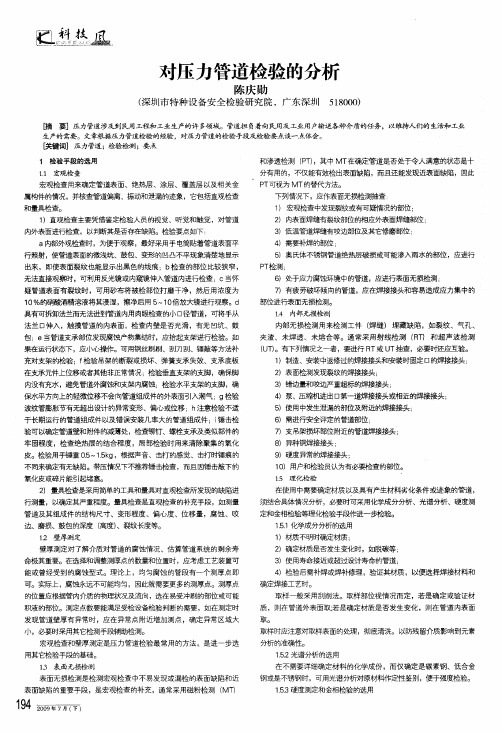
瞪塑整i二取对压力管道检验的分析陈庆勋(深圳市特种设备安全检验研究院,广东深圳518000)日商要]压力管道涉及到民用工程和工业生产的许多领域。
管道担负着向民用及工业用户输送各种介质的任务,以维持从们的生活和.x-,A k 生产的需要。
文章憾据压力管道检验的经验,对压力管道的捡啥手段技检睑要点谈一点体会。
暌键词]压力管道;检验检测;荑最1检验手段的选用1.1宏观检查宏观检查用来确定管道表面、绝热层、涂层、覆盖层以及相关金属构件的情况,并核查管道偏离、振动和泄漏的迹象,它包括直观检查和量具检查。
1)直观检查主要凭借鉴定检验人员的视觉、听觉和触觉,对管道内外表面进行检查,以判断其是否存在缺陷。
检验要点如下:a内部外观检查时,为便于观察,最好采用手电筒贴着管道表面平行照射,使管道表面的微浅坑、鼓包、变形的凹凸不平现象清楚地显示出来,即使表面裂纹也能显示出黑色的线痕;b检查的部位比较狭窄,无法直接观察时,可利用反光镜或内窥镜伸入管道内进行检查;c当怀疑管道表面有裂纹时,可用砂布将被检部位打磨干净,然后用浓度为10%的硝酸酒精溶液将其浸湿,擦净后用5~10倍放大镜进行观察。
d 具有可拆卸法兰而无法进到管道内用肉眼俭查的小口径管道,可将手从法兰口伸入,触摸管道的内表面,检查内壁是否光滑,有无凹坑、鼓包:e当管道支承部位发现腐蚀产物集结时,应抬起支架进行检验。
如果在运行状态下,应小心操作。
可用钢丝刷刷、刮刀刮、锤敲等方法补充对支架的检验;f检验吊架的断裂或损坏、弹簧支承失效、支承底板在支承元件上位移或者其他非正常情况;检验垂直支架的支脚,确保脚内没有充水,避免管道外腐蚀幂13支架内腐蚀;检验水平支架的支脚,确保zk,z g方向上的轻微位移不会向管道组成件的外表面引入潮气;g检验波纹管膨胀节有无超出设计的异常变形、偏心或位移;h注意检验不适于长期运行的管道组成件以及错误安装几率大的管道组成件;i锤击检验可以确定管道壁和附件的减薄处,检查铆钉、螺栓支承及类似部件的牢固程度,检查绝热层的结合程度,局部检验时用来清除聚集的氧化皮。
无损检测技术在压力管道检验中的运用

无损检测技术在压力管道检验中的运用摘要:在压力管道检验过程中,磁粉检测作为一项有效的无损检测方法,能够有效发现表面及近表面缺陷。
本文针对压力管道使用过程中存在的主要损伤模式、重点检测部位,结合相关标准,制定合理的磁粉检测工艺并有效实施,及时发现并消除了安全隐患,保障了压力管道安全可靠运行。
关键词:磁粉检测;压力管道;检验应用引言压力管道不仅与人民生活息息相关,也是国民经济的重要基础装备,广泛用于石油、石化、电力等行业及城市燃气和供热等工程中,一旦出现问题,往往会引发重大事故,影响人民生命财产安全。
因此应积极开展对压力管道的检验工作,通过有效的检测手段,保障压力管道安全运行。
1.磁粉检测要求及管道损伤模式铁磁性材料管道的表面缺陷检测应当优先采用磁粉检测,具体要求包括:宏观检查中发现裂纹或者可疑情况的相应部位、长期承受明显交变载荷管道焊接接头和应力集中部位应进行表面磁粉检测;检验人员认为有必要时,应对支管角焊缝等部位进行表面磁粉检测抽查,并按规定做好现场检测记录。
根据压力管道使用工况,其主要损伤模式为遗留缺陷扩展、缝隙腐蚀、大气腐蚀、机械疲劳、振动疲劳;主要失效模式为腐蚀穿孔、机械损伤等。
2.磁粉检测工艺制定针对压力管道使用过程中容易产生疲劳损伤、腐蚀减薄等情况,为了确保压力管道磁粉检测工作质量,有效发现并消除使用中存在的安全隐患,参照《承压设备无损检测》(NB/T47013—2015)标准,根据压力管道的结构尺寸、表面状态、材质以及缺陷的性质、方向、位置等,选择适当的磁化方法和磁化规范,制定切实可行的管道磁粉检测工艺,有效提高磁粉检测灵敏度和检出率。
管道磁粉检测工艺一般包含预处理、磁化、施加磁悬液、观察记录、缺陷评定、后处理6个程序。
2.1预处理(1)预处理部位:防腐层脱落局部腐蚀部位;支吊架倾斜失载应力集中部位;管道弯头、三通、阀门附件振动频率高并长期承受交变载荷作用部位;检验时认为有必要的支管角焊缝部位。
新型无损检测技术在压力管道在线检测中的应用
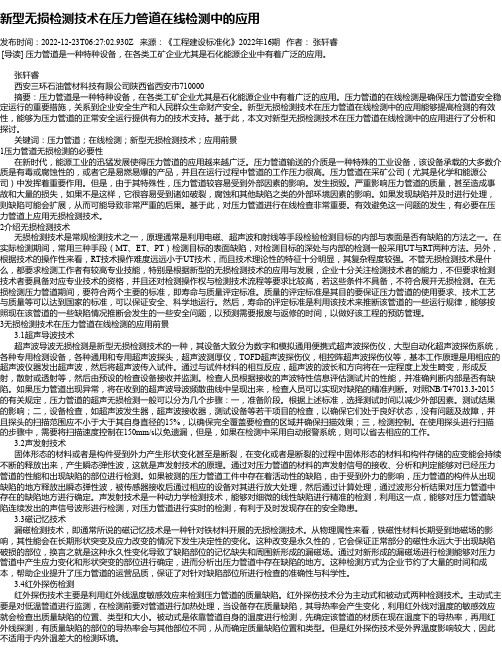
新型无损检测技术在压力管道在线检测中的应用发布时间:2022-12-23T06:27:02.930Z 来源:《工程建设标准化》2022年16期作者:张轩睿[导读] 压力管道是一种特种设备,在各类工矿企业尤其是石化能源企业中有着广泛的应用。
张轩睿西安三环石油管材科技有限公司陕西省西安市710000摘要:压力管道是一种特种设备,在各类工矿企业尤其是石化能源企业中有着广泛的应用。
压力管道的在线检测是确保压力管道安全稳定运行的重要措施,关系到企业安全生产和人民群众生命财产安全。
新型无损检测技术在压力管道在线检测中的应用能够提高检测的有效性,能够为压力管道的正常安全运行提供有力的技术支持。
基于此,本文对新型无损检测技术在压力管道在线检测中的应用进行了分析和探讨。
关键词:压力管道;在线检测;新型无损检测技术;应用前景1压力管道无损检测的必要性在新时代,能源工业的迅猛发展使得压力管道的应用越来越广泛。
压力管道输送的介质是一种特殊的工业设备,该设备承载的大多数介质是有毒或腐蚀性的,或者它是易燃易爆的产品,并且在运行过程中管道的工作压力很高。
压力管道在采矿公司(尤其是化学和能源公司)中发挥着重要作用。
但是,由于其特殊性,压力管道较容易受到外部因素的影响。
发生损毁。
严重影响压力管道的质量,甚至造成事故和大量的损失,如果不是这样,它很容易受到诸如破裂,腐蚀和其他缺陷之类的外部环境因素的影响。
如果发现缺陷并及时进行处理,则缺陷可能会扩展,从而可能导致非常严重的后果。
基于此,对压力管道进行在线检查非常重要。
有效避免这一问题的发生,有必要在压力管道上应用无损检测技术。
2介绍无损检测技术无损检测技术是常规检测技术之一,原理通常是利用电磁、超声波和射线等手段检验检测目标的内部与表面是否有缺陷的方法之一。
在实际检测期间,常用三种手段(MT、ET、PT)检测目标的表面缺陷,对检测目标的深处与内部的检测一般采用UT与RT两种方法。
另外,根据技术的操作性来看,RT技术操作难度远远小于UT技术,而且技术理论性的特征十分明显,其复杂程度较强。
分析压力管道的无损检测技术 孙明慧

分析压力管道的无损检测技术孙明慧摘要:压力管道无损检测(NDT)技术是一项新技术。
由于NDT技术开发时间较短,在压力管道中的应用还不够成熟,许多测试方法也存在许多缺陷。
因此,采用压力管道无损检测技术和方法是维护管道安全的重要措施。
本文主要介绍压力管道无损检测技术,并针对其缺点和优点进行简要分析,为压力管道无损检测部门提供参考。
关键词:压力管道;无损检测;在线检测1 引言如今,根据中国的无损检测技术用于压力管道,有超声波探伤技术、磁粉检测技术、放射线检测技术以及渗透检测技术。
射线检测技术在工业中有广泛的应用,包括γ和X射线,它们属于电磁波的范畴,它们在真空环境中以光速在直线上传播。
它本身没有电,磁场和电场不影响它。
仅存在在材料漫反射、折射指数大概为1,和折射的方向不是很明显。
衍射和干涉仅在晶体光栅存在。
它是看不见的,但它能穿透一些能见度。
不能穿透光的物质。
穿透某些物体或者物质的过程中发生复杂的化学和物理相互作用,如荧光、电离、光化学和热相互作用等。
根据射线的性质,它可以用来探测材料的更深的部分。
2 何谓压力管道所谓压力管是指在一定压力下输送气体或液体的管状装置。
其范围被定义为最大工作压力大于或等于0.1兆帕(表压),并且所述介质是液化气体。
蒸汽或易爆、易燃、、有腐蚀性、有毒,最高操作温度大于或等于所述标准沸点和公称直径大于或等于50mm。
3 介绍无损检测技术无损检测(NDT)是传统的检测技术之一,其原理通常是用电磁、超声和射线等方法来检测目标的内部和表面是否存在缺陷。
在实际检测阶段,常用三种方法(MT、ET、PT)来检测目标的表面缺陷。
UT和RT通常用于检测目标的深度和内部。
此外,根据技术的操作中,RT技术的操作难度比UT技术的小得多,并为技术理论的特殊证书是非常明显的,而复杂性是非常强的。
无论是什么无损检测技术,都必须使检测人员具备更高的专业技能,尤其是随着无损检测新技术的应用和发展,企业对检测技术人员的能力十分关注。
关于压力管道检验检测方法分析
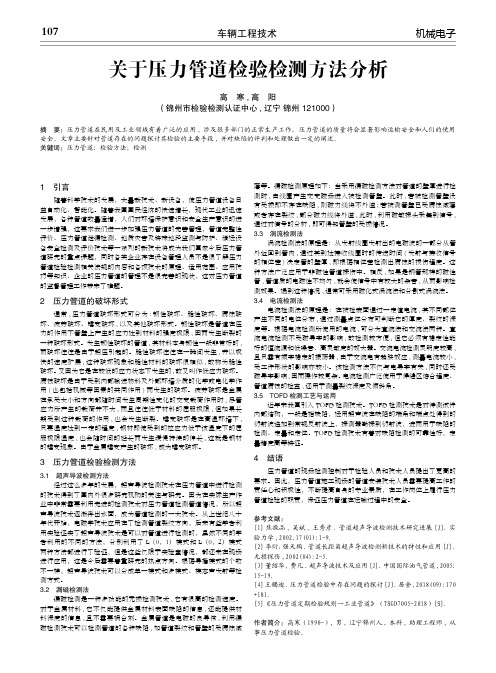
车辆工程技术107机械电子1 引言 随着科学技术的发展,大量新技术、新设备,使压力管道设备日益自动化、智能化。
随着我国国民经济的快速增长,现代工业的迅速发展,各种管道数量猛增,人们对环境保护意识和安全生产意识的进一步增强,这要求我们进一步加强压力管道的完善管理,管道完整性评价、压力管道泄漏检测、地质灾害及特殊地段监测与防护、储运设备安全检测及评价技术等一系列的新技术将成为我们国家今后压力管道研究的重点课题,同时各类企业存在设备管理人员不是很了解压力管道检验检测相关法规的内容和各项技术的原理、适用范围、应用技巧等知识、企业的压力管道的管理不是很完善的现状,这对压力管道的监督管理工作带来了难题。
2 压力管道的破坏形式 通常,压力管道破坏形式可分为:韧性破坏、脆性破坏、腐蚀破坏、疲劳破坏、蠕变破坏,以及其他破坏形式。
韧性破坏是管道在压力的作用下管壁上产生的应力达到材料的强度极限,因而发生断裂的一种破坏形式。
发生韧性破坏的管道,其材料本身韧性一般非常好的,而破坏往往是由于超压引起的。
脆性破坏往往在一瞬间发生,并以极快的速度扩展,这种破坏现象和脆性材料的破坏很相似,故称为脆性破坏。
又因为它是在较低的应力状态下发生的,故又叫作低应力破坏。
腐蚀破坏是由于受到内部输送物料及外部环境介质的化学或电化学作用(也包括机械等因素的共同作用)而发生的破坏。
疲劳破坏是金属在承受大小和方向都随时间发生周期性变化的交变载荷作用时,尽管应力所产生的载荷并不大,而且往往低于材料的屈服极限,但如果长期受到这种载荷的作用,也会发生断裂。
蠕变破坏是在高温环境下,只要温度达到一定的程度,钢材即使受到的拉应力低于该温度下的屈服极限温度,也会随时间的延长而发生缓慢持续的伸长,这就是钢材的蠕变现象。
由于金属蠕变产生的破坏,成为蠕变破坏。
3 压力管道检验检测方法3.1 超声导波检测方法 经过这么多年的发展,超声导波检测技术在压力管道中进行检测的技术得到了国内外很多研究机构的关注与研究。
- 1、下载文档前请自行甄别文档内容的完整性,平台不提供额外的编辑、内容补充、找答案等附加服务。
- 2、"仅部分预览"的文档,不可在线预览部分如存在完整性等问题,可反馈申请退款(可完整预览的文档不适用该条件!)。
- 3、如文档侵犯您的权益,请联系客服反馈,我们会尽快为您处理(人工客服工作时间:9:00-18:30)。
压力管道无损检测技术应用分析
【摘要】文章首先对石油化工压力管道的破坏进行了分析,针对压力管道无损检测技术及其应用问题进行了探讨。
【关键词】压力管道;无损检测;技术;应用
压力管道具有运行压力高,使用介质多为有毒,可燃,或具有腐蚀性的特点,在使用过程中,容易出现裂纹、腐蚀坑等缺陷,从断裂力学的角度,微小缺陷若不及时发现,扩展后将直接导致管道不可逆的损坏,影响压力管道的安全使用。
因此,有必要提高压力管道检验检测时缺陷的发现率。
随着无损检测技术的发展,越来越多的新型无损检测技术应用到压力管道的检验检测中,在一定程度上提高了压力管道检测安全的时效性和可靠性。
一、石油化工压力管道的破坏分析
1.腐蚀破坏
腐蚀破坏通常包括:均匀腐蚀、点腐蚀、缝隙腐蚀、晶间腐蚀、应力蚀、氢腐蚀和磨损腐蚀等七种形式。
2.疲劳破坏
管道疲劳破坏是材料经长期反复载荷以后而引起的破坏,破坏时没有明显的塑性变形,破坏总是经多次反复载荷以后产生,裂纹的形成发展较为缓慢,其根源在于管道系统中疲劳源的产生和存在。
通常大型往复式空气压缩机、汽轮机、泵等,由于机械本身的构造、损伤、安装的不平衡,
当其开启停止时,其机械传动不平衡引起的机械振动往往会传递给予联接的配管系统,使之产生疲劳裂纹及断裂。
管路系统中,当压力和流速变化增大到一定程度时,也会引起振动。
通常认为造成管道振动最为严重的因素是压力脉动和涡流,这种情况也很容易引起疲劳裂纹及破坏。
管路的热膨胀和热收缩也是引起管路振动的原因之一,它也会造成管道的疲劳破坏。
循环载荷作用是指压力循环、热循环和其它循环所产生的载荷对管道抗疲劳性能的影响。
从实际检验情况和事故分析结果发现,承受交变循环载荷的管道,在几何不连续处及存在焊接缺陷处,常常是疲劳破坏的起裂点。
为防止疲劳破坏,通常在运行中应尽量避免频繁加载、过大的压力波动和温度变化;设计时应注意管道的局部峰值应力的控制。
3.蠕变破坏
在一定的温度和载荷作用下,压力管道随时间而伸长和变形的破坏现象称之为蠕变破。
石油化工压力管道的破坏和无损检测破坏。
高温高压管道由于长期处于高温和高应力作用下,如果管材选用不当,设计布置不合理,热处理不当,往往容易引起管道抗蠕变性能恶化,而导致管道蠕变破坏。
蠕变破坏具有明显的塑性变形,金相组织发生明显的变化,破坏时的应力低于材料在使用温度下的强度极限值,在用检测起来一般比较困难。
通常应在设计、制造和使用中加以控制,如根据化工压力管道的使用温度选用抗蠕变性能合适的材料,在制造中要防止焊接和冷加工时降低材料的抗蠕变性能,在管道运行中要防止超温现象。
4.脆性破坏
脆性破坏是在低应力状态下发生的破坏,与低温有直接的关系。
破坏时断裂速度极快,往往在一瞬间发生,没有或只有很小的塑性变形,一般都裂成碎片。
脆性破坏主要是由于管道存在缺陷和材料韧性不足所致。
通常在低温状态下,钢的断裂韧性降低,对缺口敏感性增大,这时若存在应力集中产生的裂纹,或焊接缺陷及热处理不当,很容易产生管道脆性破坏。
因此在制造中,就应该对低温化工压力管道提出比较高的制造要求,同时在使用中更应尽可能进行较彻底的检测,尤其是材料性能方面的检测。
二、压力管道无损检测技术及其应用
(一)焊接缝的无损检测
1、射线探伤
射线探伤是利用射线能穿透物质并在物质中发生能量衰减的特性来检验物质内部缺陷的一种检测方法。
射线探伤的方法有射线照相法、荧光屏观察法和工业x射线电视法等类型,但工程设计中最常用的是射线照相法。
它的工作原理是:当射线透过材料内部的缺陷时,由于缺陷(如气孔、裂纹、非金属夹杂等)处吸收射线的能力较差,故投射到材料底部照相底片上相应部位的感光度较大,根据底片上的不同感光度可以鉴别出缺陷的存在与否及缺陷的外型和大小。
JB4730标准为一综合性的无损检测标准,其中的第二篇为射线探伤标准。
标准中它将对接焊缝的缺陷共分成了基本缺陷(包括裂纹、未熔合、未焊透)、圆形缺陷、条状夹渣等四类,并针对这些缺陷给出了I级、Ⅱ级、Ⅲ级、Ⅳ级共四个质量评定等级,每级都规定了详细的缺陷允许尺寸和数量。
射线检测主要是检测与射线束同方向上的缺陷情况,如裂纹,当其与
射线同方向时,则在底片上容易显现。
但同样一种缺陷,当其与射线成垂直情况时则难以发现,所以某一部件是否可以采用射线检验,1)要分析缺陷产生的情况是否有利于射线透照,2)要看射线的透照能力,如x射线机的kV值,3)看有无透照的环境或空间。
一般情况下在电站所用压力容器中,如无支撑架之类的结构件,其纵环焊缝均可采用RT检验方法进行检验。
射线能够对人体产生生物效应,所以正常情况下,在进行RT检验时检验人员应进行必要的防护,在进行检验的周围区域进行警示。
2、超声检测焊接缝
超声检测具备着诸多优点,比如能够检出平面线形缺陷如裂纹等,并且成本较低、操纵灵活,但是超声检测无法像射线检测那样提供直观缺陷记录,同时缺陷种类需要具备熟练技术的操作人员判断。
GB50235与HG20225标准规定,若将射线检测采用超声检测取代,则应当经过建设单位的批准,其检验数量必须等同于射线检验。
SH3501标准指出,如果设计规定必须应用射线检测,那么就根据具体规定需要加以执行,而如果应用超声波检验有规定时,也必须严格的按照规定执行。
但是需要用超声检测取代,因为受到条件的束缚时,应当取得设计单位的批准。
(二)原材料的无损检测
1、磁粉探伤
它是在磁场中利用铁磁性材料被磁化后,在表面或近表面的缺陷处产生漏磁的现象进行探伤的。
当铁磁性材料置于磁铁的N、S极之间时,便有磁力线通过。
对于均匀一致的材料,磁力线是平行均匀分布的,如果材料表面或近表面有裂纹、气孔、夹渣等缺陷时,由于这些缺陷本身是非磁
性的,其磁阻很大,磁力线不易穿过它而是绕过它,从而在缺陷处产生弯曲而将缺陷显示出来,根据这样的显示特征可以判断缺陷是否存在。
磁粉探伤时被检测件表面有一定的粗糙度要求,一般不低于Ra12.5μm。
被检件磁化时可以用交流电,也可以用直流电,前者由于电流的集肤效应,而表现为检测表面缺陷时灵敏度较高,后者则由于磁化场较均匀而能发现浅表面下较深的缺陷。
另外,磁化被检件时既要进行周向磁化,又要进行纵向磁化,以免不同方向的缺陷被漏检,检测过程中还应注意由于材料晶粒大小和组织不均匀等带来的假缺陷现象。
2、涡流检测
采取穿过式线圈探头进行涡流检测管材的通孔缺陷,此外,在不同磁场强度的情况下,铁磁性管材的磁导率也不同,所以,应当对磁饱和装置加以设置,在检测铁磁性管材时,同时于检测线圈的检测区域施加足够的磁场,使其导磁率大致与常数一致。
一般介于1MHZ至500MHZ之间铁磁性钢管涡流检测频率。
涡流检测进行的过程当中,应当采用对比试样进行调节涡流仪的检测灵敏度,确保验收水平和检测结果的准确性。
对比试样应当和被检对象有相近或相同的表面状态、电磁性能、牌号和规格、热处理状态,大部分标准规定刻槽和通孔是对比试样中的人工缺陷。
三、结束语
现代检测与诊断系统在工业上的应用日益繁荣,而其也必然朝着自动化智能化的方向发展,相信在未来社会里,随着信息检测与处理技术的提高,无损检测技术将广泛应用于工业、农业、家庭、医学、军事和空间科学技术等许多科学领域,而信息智能化、数字无线通信等技术的运用必然
使其如虎添翼,其应用前景是相当乐观。