1-7刀具补偿功能
刀尖圆弧补偿(详细介绍)

刀尖圆弧补偿数控车削加工是以假想刀尖进行编程,而切削加工时,由于刀尖圆弧半径的存在,实际切削点与假想刀尖不重合,从而产生加工误差。
为满足加工精度要求,又方便编程,需对刀尖圆弧半径进行补偿。
本文对刀尖半径补偿的概念,刀尖方位的确定、补偿方法和参数设置进行了介绍。
同时阐述了刀尖半径补偿的过程并分析了实例,就应用过程中出现的问题加以介绍。
数控机床是按照程序指令来控制刀具运动的。
众所周知,我们在编制数控车床加工程序时,都是把车刀的刀尖当成一个点来考虑,即假想刀尖,如图1所示的A点。
编程时就以该假想刀尖点A来编程,数控系统控制A点的运动轨迹。
但实际车刀尤其是精车刀,在其刀尖部分都存在一个刀尖圆弧,这一圆角一方面可以提高刀尖的强度,另一方面可以改善加工表面的表面粗糙度。
由于刀尖圆弧的存在,车削时实际起作用的切削刃是圆弧各切点。
而常用的对刀操作是以刀尖圆弧上X、Z方向相应的最突出点为准。
如图1所示,这样在X向、Z向对刀所获得的刀尖位置是一个假想刀尖。
按假想刀尖编出的程序在车削外圆、内孔等与Z轴平行的表面时,是没有误差的,即刀尖圆弧的大小并不起作用;但当车右端面、锥面及圆弧时,就会造成过切或少切,引起加工表面形状误差,如图2所示为以假想刀尖位置编程时的过切及少切现象。
编程时若以刀尖圆弧中心编程,可避免过切和少切的现象,但计算刀位点比较麻烦,并且如果刀尖圆弧半径值发生变化,还需改动程序。
数控系统的刀具半径补偿功能正是为解决这个问题所设定的。
它允许编程者不必考虑具体刀具的刀尖圆弧半径,而以假想刀尖按工件轮廓编程,在加工时将刀具的半径值R存入相应的存储单元,系统会自动读入,与工件轮廓偏移一个半径值,生成刀具路径,即将原来控制假想刀尖的运动转换成控制刀尖圆弧中心的运动轨迹,则可以加工出相对准确的轮廓。
这种偏移称为刀尖半径补偿。
如图3所示。
一、刀尖半径补偿的方式现代机床基本都具有刀具补偿功能,为编程提供了方便。
刀尖圆弧半径补偿是通过G41、G42、G40代码及T代码指定的假想刀尖号加入或取消的,如表所示。
刀具半径补偿原理及补偿规则

刀具半径补偿原理及补偿规则在加工过程中,刀具的磨损、实际刀具尺寸与编程时规定的刀具尺寸不一致以及更换刀具等原因,都会直接影响最终加工尺寸,造成误差。
为了最大限度的减少因刀具尺寸变化等原因造成的加工误差,数控系统通常都具备有刀具误差补偿功能。
通过刀具补偿功能指令,CNC系统可以根据输入补偿量或者实际的刀具尺寸,使机床自动加工出符合程序要求的零件。
1.刀具半径补偿原理(1)刀具半径补偿的概念用铣刀铣削工件的轮廓时,刀具中心的运动轨迹并不是加工工件的实际轮廓。
如图所示,加工内轮廓时,刀具中心要向工件的内侧偏移一定距离;而加工外轮廓时,同样刀具中心也要向工件的外侧偏移一定距离。
由于数控系统控制的是刀心轨迹,因此编程时要根据零件轮廓尺寸计算出刀心轨迹。
零件轮廓可能需要粗铣、半精铣和精铣三个工步,由于每个工步加工余量不同,因此它们都有相应的刀心轨迹。
另外刀具磨损后,也需要重新计算刀心轨迹,这样势必增加编程的复杂性。
为了解决这个问题,数控系统中专门设计了若干存储单元,存放各个工步的加工余量及刀具磨损量。
数控编程时,只需依照刀具半径值编写公称刀心轨迹。
加工余量和刀具磨损引起的刀心轨迹变化,由系统自动计算,进而生成数控程序。
进一步地,如果将刀具半径值也寄存在存储单元中,就可使编程工作简化成只按零件尺寸编程。
这样既简化了编程计算,又增加了程序的可读性。
刀具半径补偿原理(2)刀具半径补偿的数学处理①基本轮廓处理要根据轮廓尺寸进行刀具半径补偿,必需计算刀具中心的运动轨迹,一般数控系统的轮廓控制通常仅限于直线和圆弧。
对于直线而言,刀补后的刀具中心轨迹为平行于轮廓直线的一条直线,因此,只要计算出刀具中心轨迹的起点和终点坐标,刀具中心轨迹即可确定;对于圆弧而言,刀补后的刀具中心轨迹为与指定轮廓圆弧同心的一段圆弧,因此,圆弧的刀具半径补偿,需要计算出刀具中心轨迹圆弧的起点、终点和圆心坐标。
②尖角处理在普通的CNC装置中,所能控制的轮廓轨迹只有直线和圆弧,其连接方式有:直线与直线连接、直线与圆弧连接、圆弧与圆弧连接。
刀具补偿指令及其编程方法

G94是什么指令?—————— 5.对于FUNNC系统,( D )指令不能取消长度补 偿。 A.G49 B G44 H00 C G43 H00 D G41
端面切削循环
• 6..刀具长度补偿值的地址是( B ) • A D×× B H×× C R×× D J××
• 7..执行G90 G01 G44 H02 Z-50 F100(H02为2mm)程序后,刀具的实际 移动距离为(48mm )
N170 N180 N190 N200 N210 N220 N230 N240 N290 N300 N310 N320 N330
G01 X15 Z0 F40 ; X30 Z-20 ; Z-35 ; 精车A—B—C—D—E 的外轮廓 X50 ; Z-59 ; G0 X50 Z50 ; 返回起刀点(即安全位置方便换刀) T0303 ; 换2号切断刀 G0 X52 Z-58 ; 快速定位 G01 X-0.1 F40 ; 切断 G0 X50 ; Z50 ; T0100 M05 ; M30 ; 返回起刀点(即安全位置方便换刀 换回基准刀,主轴停止 程序结束
N-- G0 X60 Z2; 快速定位
D C H)
N-- G94 X60 Z-10 R-1 F60; 走刀路线:(A
N-N-N--
R-4; 走刀路线:(A
R-7; 走刀路线:(A
E
F B
C
C
H)
H) C H)
R-10; 走刀路线:(A
A、B 点Z方向加刀宽 (分析图) O0001 ; N T0303 S02 M03 ; N G0 X52 Z-30 ; N G94 X20.3 Z-30 F50 ;
61刀具半径补偿?无论车削还是铣削在对轮廓加工时用刀具补偿功能编程当刀具尺寸车刀的圆弧半径铣刀的直径因更换磨损等原因发生变化时不需要重新编程只要修改刀具半径值即可从而简化了编程
深圳市众为兴数控技术 ADT-CNC4840 铣床控制系统 说明书

ADT-CNC4840 铣床控制系统 用 户 手 册深圳市众为兴数控技术有限公司 地址:深圳市南山区马家垅工业区36栋5楼 邮编:518052 目录第一篇:编程.......................................41. 综述 (4)1.1 可编程功能 (4)1.2 准备功能 (9)1.3 辅助功能 (11)2. 插补功能 (11)2.1 快速定位(G00) (11)2.2 直线插补(G01) (12)2.3 圆弧插补(G02/G03) (12)3. 进给功能 (14)3.1 进给速度 (14)3.2 自动加减速控制 (14)3.3 暂停( G04 ) (15)4. 参考点和坐标系 (15)4.1 机床坐标系 (15)4.2 关于参考点的指令( G27、G28、G29 ) (15)4.3 工件坐标系 (17)4.4 平面选择 (19)5. 坐标值和尺寸单位 (19)5.1 绝对值和增量值编程(G90和G91) (19)6. 辅助功能 (20)6.1 M代码 (20)6.2T代码 (21)6.3 主轴转速指令(S代码) (21)7. 程序结构 (21)7.2 程序正文结构 (21)7.2.5文件结束 (23)8. 简化编程功能 (23)8.1 孔加工固定循环(G73,G74,G76,G80 ̄G89) (23)9.刀具补偿功能 (35)9.1 刀具长度补偿(G43,G44,G49) (35)9.2 刀具半径补偿B (37)第二篇 操 作 篇...................................751.概要 (75)1.1手动操作 (75)1.2刀具按程序移动─自动运转 (76)1.3自动运转的操作 (76)1.4程序调试 (77)1.5程序的编辑 (78)1.6数据的显示及设定 (78)1.7显示 (79)2.操作面板说明 (79)2.1LCD面板 (79)2.2显示页面选择 (81)2.3操作方式选择 (81)2.4键盘的说明 (81)3.手动操作 (84)3.1手动返回参考点 (84)3.2手动连续进给 (85)3.3单步进给 (85)3.4手轮进给 (85)3.5手动辅助机能操作 (86)4.自动运行 (87)4.1自动运转 (87)4.2自动运转的停止 (87)4.3进给倍率 (88)5.调试 (88)5.1单程序段 (88)5.2跳过任选程序段(或机床软操作面板) (88)5.3输入信号检测输出信号测试 (88)6.安全操作 (88)6.1急停 (88)6.2超程 (89)7.报警处理 (89)8.程序存储、编辑、下载、显示 (89)8.1程序存储、编辑操作前的准备 (89)8.2把程序存入存储器中 (89)8.3程序检索 (89)8.4程序的删除 (90)8.5删除全部程序 (90)8.6字的插入、修改、删除 (90)8.7存储程序的个数 (91)8.8存储容量 (91)8.9程序下载 (91)8.10程序显示编辑界面 (93)9.数据的显示、设定 (93)9.1系统参数 (93)9.2刀补参数设定显示 (93)9.3工件坐标系设定 (93)9.4参数的显示 (96)9.5参数的设定和查询 (96)9.6机床软操作面板的显示及设置 (97)9.7设置参数设定 (97)9.8诊断显示设定 (98)10.显示 (99)10.1状态显示 (99)10.2程序显示 (100)10.3位置显示及清零 (101)第三篇 连 接 篇..................................1031、系统结构 (103)1.1CNC4840数控系统的组成 (103)2、外部连接 (104)2.1外部接口图 (104)2.2电机驱动器控制接口 (106)对应外壳定义:机床输出扩展接口 (119)附录1规格一览表 (122)附录2参数一览表 (125)附录4错误代码一览表 (132)附录5G功能一览表 (133)附录6工件坐标系设定及对刀 (135)第一篇:编程 1. 综述 1.1 可编程功能 通过编程并运行这些程序而使数控机床能够实现的功能我们称之为可编程功能。
数控设备刀具补偿技术讲解

刀具长度补偿:
补偿刀具长度方向尺寸的变化.
三、刀具补偿的方法
• •
人工预刀补:人工计算刀补量进行编程 机床自动刀补:数控系统具有刀具补偿功能。
四、刀具半径补偿功能
1、刀具半径补偿的作用
在数控铣床上进行轮廓铣削时,由于刀具半径的 存在,刀具中心轨迹与工件轮廓不重合。
从上述程序可以大致了解钻孔加工的走刀路线及钻孔的基本 编程方法,当所使用的数控铣床不具备更高级的钻孔专用指令 时,通常都需要这样一步步地编程,更方便的钻孔编程方法将 在后面的章节中逐步介绍。
返回上层
3、刀具长度补偿指令
刀具长度补偿G43,G44,G49 (1)格式
G43
G44 G49
G00
G01
Z— H—
G00
G01
Z—
G43 刀具长度正补偿
G49取消刀长补偿
G44 刀具长度负补偿
G43 G44 G49 均为模态指令
其中Z 为指令终点位置,H为刀补号地址,用H00~ H99来指定,它用来调用内存中刀具长度补偿的数值。
t01t02t031010刀补引入刀补取消采用刀座对刀后来安装刀具h0145d010004g92x1500y1600z1200g90g00x1000y600g43z20h01s100m03g42g01x750d01f100x350g02x150r100g01y700g03x150r150g01y600g02x350r100g01x750g09y0主程序号建立工件坐标系绝对值方式快进到x100y60指令高度z2实际到达高z43处刀径补偿引入插补至x75y60直线插补至x35y60顺圆插补至x15y60直线插补至x15y7015y70直线插补至x15y6035y60直线插补至x75y60直线插补至x75y0处程序单g01x450x750y200y650g40g00x1000y600g49z1200x1500y1600m05m30直线插补至x45y45直线插补至x75y20直线插补至x75y65轮廓切削完毕取消刀补快速退至10060的下刀处快速抬刀至z120的对刀点平面主轴停程序结束复位
数控车工中级理论知识考核试卷(五-十)
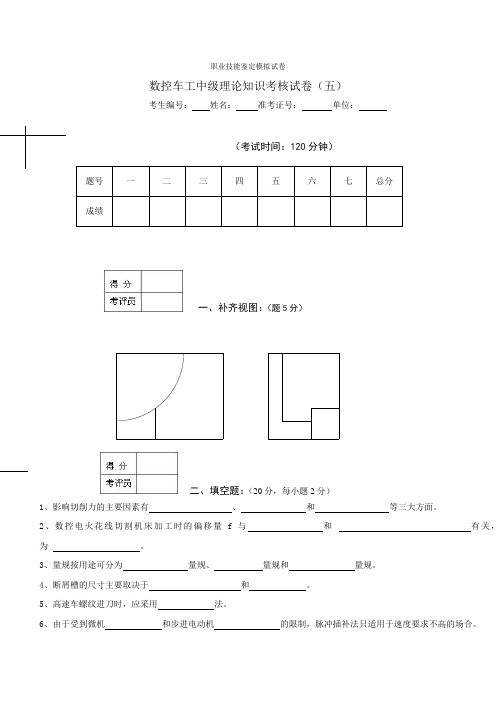
职业技能鉴定模拟试卷数控车工中级理论知识考核试卷(五)考生编号:姓名:准考证号:单位:(考试时间:120分钟)题号一二三四五六七总分成绩一、补齐视图:(题5分)二、填空题:(20分,每小题2分)1、影响切削力的主要因素有、和等三大方面。
2、数控电火花线切割机床加工时的偏移量f与和有关,为。
3、量规按用途可分为量规、量规和量规。
4、断屑槽的尺寸主要取决于和。
5、高速车螺纹进刀时,应采用法。
6、由于受到微机和步进电动机的限制,脉冲插补法只适用于速度要求不高的场合。
7、为了防止强电系统干扰及其它信号通过通用I/O接口进入微机,影响其工作,通常采用方法。
8、一个简单的车削固定循环程序段可以完成、、、,常见的加工顺序动作。
9、在编制数控机床加工程序时,应考虑工件原点、刀具相关点和机床原点之间的的相互关系。
工件原点是指在工件上建立原点,刀具相关点是指,机床原指。
10、FUANC系统G50指令的含义是:。
如在程序中,用G50指令一般应放在程序置)。
三、选择题:(每题2分,共20分)1 安全管理可以保证操作者在工作时的安全或提供便于工作的()。
A.生产场地B.生产环境 C 生产空间2 加工()零件,宜采用数控加工设备。
A.大批量 B 多品种中小批量 C 单件3 通常数控系统除了直线插补外,还有()。
A.正弦插补 B 圆弧插补 C 抛物线插补4 数控机床进给系统减少摩擦阻力和动静摩擦之差,是为了提高数控机床进给系统的()。
A.传动精度 B 运动精度和刚度 C 快速响应性能和运动精度 D 传动精度和刚度5 为了保证数控机床能满足不同的工艺要求,并能够获得最佳切削速度,主传动系统的要求是()。
A.无级调速 B 变速范围宽 C 分段无级变速 D 变速范围宽且能无级变速6 圆弧插补指令G03 X Y R 中,X、Y后的值表示圆弧的()。
A.起点坐标值 B 终点坐标值 C 圆心坐标相对于起点的值7 ()使用专用机床比较合适。
数控铣床与加工中心刀具补偿讲解

欢迎阅读数控铣床与加工中心5.4 刀具补偿和偏置功能刀具补偿可分为刀具长度补偿和刀具半径补偿,其内容和方法已在前面章节中作了详细说明,本章拟用另外一种指令格式对刀具长度补偿功能进行介绍,目的在于进一步强调不同的数控系统对同一编程功能可能采用不同的指令格式。
5.4.1B型刀G41G42XY、ZX 或YZ时,迹。
偏置计算在由G17、G18和G19确定的平面内进行,该平面称之为偏置平面。
例如在已经选择了XY平面时,仅对程序中(X、Y)或(1、J)计算偏置量,并计算偏置矢量。
不在偏置平面内的轴的坐标值不受偏置的影响。
在3轴联动控制中,投影到偏置平面上的刀具轨迹才得到偏置补偿。
(4).刀补的建立与刀补的取消刀补的建立是进入切削加工前的一个辅助程序段,刀补的取消是加工完成时要写入到程序中的辅助程序段,如果处理得好则有利于简捷快速而又安全地使刀具进入切入位置和加工完了时退出刀具。
刀补建立时的核心问题是刀具从何处下刀并进入到工件加工的起始位置,刀补取消时则主要应考虑刀具沿何方向退离工件。
系统操作说明书中讨论了各种可能遇到的情况,为简化叙述,下面仅根据习惯的编程方法讨论刀补建立与刀补取消的问题。
不使用这些方法一般也可以正确地完成刀补建立与刀补取消的过程,但特殊情况下可能出现过切或报警。
1)使用GOO或G01的运动方式均可完成刀补建立或取消的过程,事实上使用G01往往是出于安全的考虑。
而如果不把刀补的建立(包括刀补的取消)建立在加工时的Z轴高度上,而采取先建立补偿再下刀或先提刀再取消补偿的方法,则既使在GOO的方式下建立(或取消)刀补也是安全的。
2)为了便于计算坐标,可以按图5-18所示两种方式来建立刀补,图5-18a为切线进入方式,图5-18b为法线进入方式。
同样取消刀补通常也采用这种切线或法线的方式。
图5-18 两种刀补建立方式图5-19 内圆轮廓的补偿3)在不便于直接沿着工件的轮廓线切向切入和切向切出时,可再增加一个圆弧辅助程序段。
刀具位置补偿
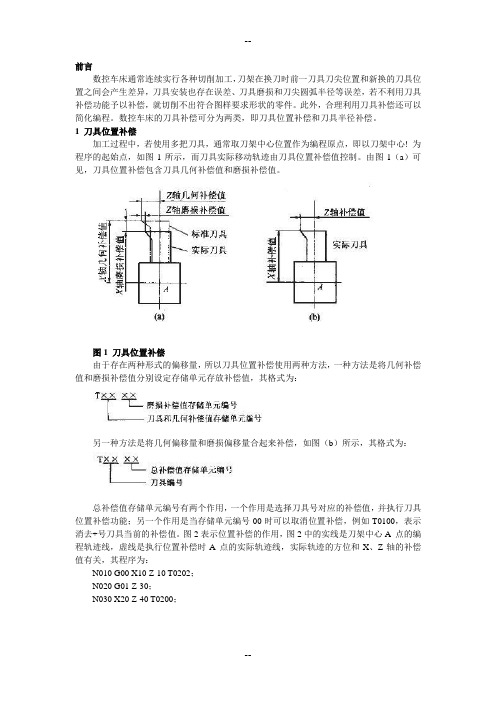
前言数控车床通常连续实行各种切削加工,刀架在换刀时前一刀具刀尖位置和新换的刀具位置之间会产生差异,刀具安装也存在误差、刀具磨损和刀尖圆弧半径等误差,若不利用刀具补偿功能予以补偿,就切削不出符合图样要求形状的零件。
此外,合理利用刀具补偿还可以简化编程。
数控车床的刀具补偿可分为两类,即刀具位置补偿和刀具半径补偿。
1 刀具位置补偿加工过程中,若使用多把刀具,通常取刀架中心位置作为编程原点,即以刀架中心! 为程序的起始点,如图1所示,而刀具实际移动轨迹由刀具位置补偿值控制。
由图1(a)可见,刀具位置补偿包含刀具几何补偿值和磨损补偿值。
图1 刀具位置补偿由于存在两种形式的偏移量,所以刀具位置补偿使用两种方法,一种方法是将几何补偿值和磨损补偿值分别设定存储单元存放补偿值,其格式为:另一种方法是将几何偏移量和磨损偏移量合起来补偿,如图(b)所示,其格式为:总补偿值存储单元编号有两个作用,一个作用是选择刀具号对应的补偿值,并执行刀具位置补偿功能;另一个作用是当存储单元编号00时可以取消位置补偿,例如T0100,表示消去+号刀具当前的补偿值。
图2表示位置补偿的作用,图2中的实线是刀架中心A 点的编程轨迹线,虚线是执行位置补偿时A 点的实际轨迹线,实际轨迹的方位和X、Z轴的补偿值有关,其程序为:N010 G00 X10 Z-10 T0202;N020 G01 Z-30;N030 X20 Z-40 T0200;图2 刀具位置补偿作用数控车床系统刀具结构如图3所示,图3中P为假想刀尖,S为刀头圆弧圆心,r为刀头半径,A为刀架参考点。
图3 车刀结构车床的控制点是刀架中心,所以刀具位置补偿始终需要。
刀具位置补偿是用来实现刀尖圆弧中心轨迹与刀架参考点之间的转换,对应图3中A与S之间的转换,但是实际上我们不能直接测得这两个中心点之间的距离矢量,而只能测得假想刀尖! 与刀架参考点$ 之间的距离。
为了简便起见,不妨假设刀头半径r=0,这时可采用刀具长度测量装置测出假想刀尖点P相对于刀架参考点的坐标和,并存入刀具参数表中。
刀具补偿功能概述

刀具补偿功能概述刀具补偿是数控加工中一项关键的技术,它可以有效地提高加工精度和效率。
本文将对刀具补偿功能进行概述,介绍其原理、应用和优势。
一、刀具补偿的原理刀具补偿是通过在数控系统中对工具轨迹进行校正来实现的。
由于刀具的尺寸、形状和磨损等因素,工件的加工结果可能会与预期有所偏差。
刀具补偿基于工具几何和轨迹偏差的关系,通过调整数控程序中的刀具路径,使实际切削轨迹与期望轨迹保持一致,从而实现精准加工。
二、刀具补偿的应用领域刀具补偿广泛应用于各种数控加工领域,如铣削、车削、钻削等。
在这些加工过程中,刀具补偿能够提高零件的尺寸精度、表面质量和加工效率。
1. 铣削中的刀具补偿:在铣削过程中,刀具补偿可以根据刀具直径和偏移量来自动调整切削轨迹,确保切削结果符合要求。
同时,通过刀具补偿,还可以实现铣削过程中不同刀具的自动更换,提高生产效率。
2. 车削中的刀具补偿:车削过程中,刀具补偿可以针对工件的尺寸偏差进行调整,使加工后的工件尺寸与期望尺寸保持一致。
刀具补偿可以通过修正刀具位置或调整进给速度来实现,大大提高了车削加工的精度和稳定性。
3. 钻削中的刀具补偿:在钻削过程中,刀具补偿可以根据刀具尺寸和磨损情况来调整刀具的位置和轨迹。
通过刀具补偿,可以有效控制钻孔的直径误差和圆度误差,提高钻削加工的质量。
三、刀具补偿的优势刀具补偿具有许多优势,使其在数控加工中得到广泛应用。
1. 提高加工精度:刀具补偿可以消除工具尺寸和磨损等因素对加工精度的影响,实现更加精确的加工结果。
2. 提高加工效率:通过刀具补偿,可以使切削轨迹与工件的实际形状相匹配,减少加工过程中的空刀时间,提高生产效率。
3. 增强加工稳定性:刀具补偿可以对工具的位置和轨迹进行校正,减少切削力的变化,有助于提高加工过程的稳定性。
四、结论刀具补偿功能在数控加工中起到至关重要的作用,它通过调整刀具路径,确保加工结果与期望一致,提高加工精度和效率。
刀具补偿在铣削、车削、钻削等加工过程中广泛应用,并具有诸多优势,如提高加工精度、效率和稳定性。
刀具半径补偿的方法
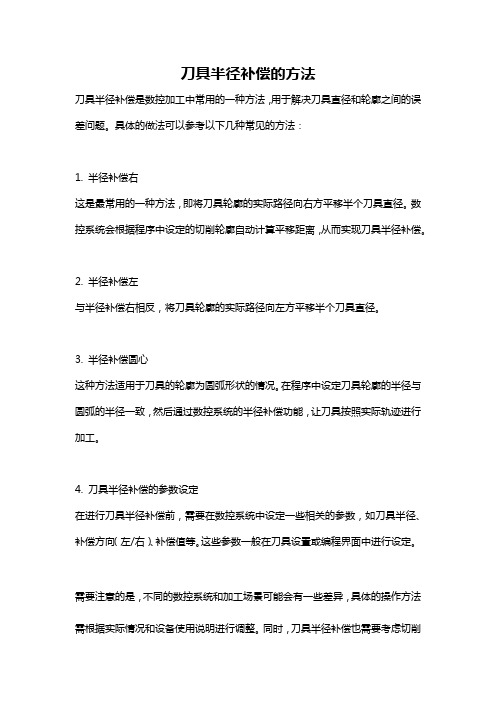
刀具半径补偿的方法
刀具半径补偿是数控加工中常用的一种方法,用于解决刀具直径和轮廓之间的误差问题。
具体的做法可以参考以下几种常见的方法:
1. 半径补偿右
这是最常用的一种方法,即将刀具轮廓的实际路径向右方平移半个刀具直径。
数控系统会根据程序中设定的切削轮廓自动计算平移距离,从而实现刀具半径补偿。
2. 半径补偿左
与半径补偿右相反,将刀具轮廓的实际路径向左方平移半个刀具直径。
3. 半径补偿圆心
这种方法适用于刀具的轮廓为圆弧形状的情况。
在程序中设定刀具轮廓的半径与圆弧的半径一致,然后通过数控系统的半径补偿功能,让刀具按照实际轨迹进行加工。
4. 刀具半径补偿的参数设定
在进行刀具半径补偿前,需要在数控系统中设定一些相关的参数,如刀具半径、补偿方向(左/右)、补偿值等。
这些参数一般在刀具设置或编程界面中进行设定。
需要注意的是,不同的数控系统和加工场景可能会有一些差异,具体的操作方法需根据实际情况和设备使用说明进行调整。
同时,刀具半径补偿也需要考虑切削
力、切削速度等因素,确保加工质量和切削稳定性。
项目二 数控系统硬件连接
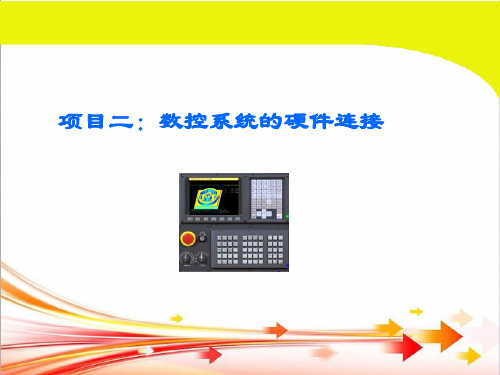
任务二:数控系统的硬件连接训练 6) 伺服电机动力电源连接
主要包含伺服主轴电机与伺服进给电机的动力电源连接,伺服主轴电 机的动力电源是采用接线端子的方式连接,伺服进给电机的动力电源是采
用接插件连接,在连接过程中,一定要注意相序的正确。
任务一:数控机床的组成(FANUC)
主 轴 电 动 机
普通型和变频专用电动机
串行数字主轴电动机
任务一:数控机床的组成(FANUC)
主 轴 传 动 机 构
带传动(经过一级降速)
经过一级齿轮的带传动
任务一:数控机床的组成(FANUC)
主 轴 传 动 机 构
内装式电机主轴单元 (电主轴) 几级降速齿轮传动
6.αi伺服模块(SVM2)
TB1: DC300V直 流母线 CXA2B:DC 24V工作电 源与控制信 号总线
CXA2A:DC 24V工作电 源与控制信 号总线
COP10B: 驱动器 FSSB总线
JF1:伺服电 机位置编码 器反馈 CZ2L/2M: 伺服电动机 电源输出
COP10A: 驱动器FSSB 总线 JF2:伺服电 机位置编码 器反馈
CM65: SA1信 号输入
CA65: 强电信号 输出(急停)
任务一:数控机床的组成(FANUC)
CE57/53: I/O LINK 总线接口
开/关 程序保护
XS1: SS01J信号 输入
急停 开关
SS01N: 进给轴倍率 波段开关
SS01J: 主轴倍率 波段开关
XS2: SS01N信号 输入
任务一:数控机床的组成(FANUC) 三.PMC单元与I/O LINK连接
FANUC0系统部分参数功能说明

FANUC0系统部分参数功能说明1.刀具半径补偿(CUTTER_R_COMP):该参数决定刀具半径补偿的大小。
当刀具在加工过程中出现偏差时,可以通过调整这个参数来使刀具路径与期望的路径更加接近。
2.预置刀具半径补偿(PRESET_R_COMP):该参数用于设置预置刀具半径补偿的大小。
预置刀具半径补偿是在程序中设置的,用于预先补偿刀具半径误差。
可以通过调整这个参数来改变刀具对工件的加工效果。
3.进给速度修正(FEED_SPEED):该参数用于修正进给速度的大小。
当切削条件或刀具磨损改变时,可以通过调整这个参数来使进给速度与期望的速度一致。
4.回转半径(RADIUS):该参数用于设置回转半径的大小。
当机床执行圆弧插补运动时,可以通过调整这个参数来改变圆弧的半径,从而实现不同大小的加工。
5.光滑度(SMOOTHNESS):该参数用于调整运动的光滑度。
光滑度越大,机床运动的曲线越平滑。
可以通过调整这个参数来改变机床的运动轨迹,从而实现更精确的加工。
6.切削力限制(FORCE_LIMIT):该参数用于限制切削力的大小。
当机床在加工过程中出现过大的切削力时,可以通过调整这个参数来限制切削力的大小,以保护机床和刀具的安全。
7.加工系数(PROCESS_COEFFICIENT):该参数用于调整加工的精度和速度。
可以通过调整这个参数来改变加工的速度和精度,以满足不同的加工需求。
8.安全高度(SAFE_HEIGHT):该参数用于设置安全高度的大小。
安全高度是机床在加工过程中离开工件的高度,以确保机床和刀具的安全。
可以通过调整这个参数来改变安全高度的大小。
9.原点补偿(ORIGIN_OFFSET):该参数用于补偿机床运动轴的原点位置。
可以通过调整这个参数来校正运动轴的原点位置,以保证加工的精度。
10.加速度(ACCELERATION):该参数用于调整机床的加速度。
加速度越大,机床的加工速度越快。
可以通过调整这个参数来改变机床的加工速度,以提高生产效率。
刀具半径补偿方向的判定原则

刀具半径补偿方向的判定原则(最新版)目录1.刀具半径补偿的定义和作用2.刀具半径补偿方向的判定原则3.刀具半径补偿的实际应用案例4.刀具半径补偿的注意事项正文一、刀具半径补偿的定义和作用刀具半径补偿是数控加工中的一种技术,用于在加工过程中自动调整刀具与工件之间的距离,以保证加工精度。
刀具半径补偿分为左补偿和右补偿,其作用是防止刀具在加工过程中与工件发生碰撞,提高加工效率和精度。
二、刀具半径补偿方向的判定原则1.刀具前进方向左侧进行补偿,称为左刀补。
左刀补的原则是:当刀具在加工过程中,其前进方向的左侧距离工件表面较近时,需要进行左刀补。
此时,刀具的半径补偿值为负数。
2.刀具前进方向右侧进行补偿,称为右刀补。
右刀补的原则是:当刀具在加工过程中,其前进方向的右侧距离工件表面较近时,需要进行右刀补。
此时,刀具的半径补偿值为正数。
三、刀具半径补偿的实际应用案例在加工中心的刀具补偿功能中,刀具半径补偿是一个非常重要的环节。
以下为例:假设有一个直径为 100mm 的圆柱形工件,需要用一个直径为 20mm的刀具进行加工。
此时,刀具的半径为 10mm。
为了避免刀具与工件发生碰撞,需要进行刀具半径补偿。
根据刀具半径补偿的原则,当刀具在加工过程中,其前进方向的左侧距离工件表面较近时,需要进行左刀补。
此时,刀具的半径补偿值为负数,即 -10mm。
同理,当刀具在加工过程中,其前进方向的右侧距离工件表面较近时,需要进行右刀补。
此时,刀具的半径补偿值为正数,即 +10mm。
四、刀具半径补偿的注意事项1.刀具半径补偿的值应根据实际加工情况进行调整,避免补偿过大或过小,影响加工精度。
2.在进行刀具半径补偿时,应注意刀具的旋转方向与补偿方向的一致性,以保证加工效果。
3.在使用刀具半径补偿功能时,应正确设置刀具的长度补偿和半径补偿,避免因设置不当导致的加工误差。
总之,刀具半径补偿方向的判定原则对于保证加工精度和提高加工效率具有重要意义。
数控机床补偿功能

三、铣刀刀具半径补偿
数控铣床在切削中,由于刀具总有一定的半径,刀具中 心的运动轨迹与加工零件的实际轮廓并不重合。如图所示, 在加工内轮廓时,刀具中心偏离零件内轮廓表面一个刀具半 径值。在加工外轮廓时,刀具中心又偏离零件外轮廓表面一 个刀具半径值。此现象习惯上称为刀具半径补偿。根据ISO 标准,当刀具中心轨迹在编程轨迹前进方向的右侧时,称为 右刀补,用G42表示。反之,称为左刀补,用G41表示。取 消刀尖半径补偿使用G40指令。使用时,编程人员只是在零 件程序中指明补偿要求即可。铣刀刀具半径补偿执行过程分 为刀补建立、刀补进行和刀补撤消三步,刀补仅在指定的两 维坐标平面进行。铣刀半径补偿应注意事项同车刀刀具补偿 要求。
五、数控误差补偿
数控机床在加工时,指令的输入、译码、计 算以及控制电机的运动都是由数控系统统一 控制完成的,从而避免了人为误差。但是, 由于整个加工过程都是自动进行的,人工几 乎不能干预,操作者无法对误差加以补偿, 这就需要数控系统提供各种补偿功能,以便 在加工过程中自动地补偿一些有规律的误差, 提高零件的精度。根据数控机床上加工误差 的主要来源其主要的解决方法如下。
刀具刀尖半径补偿的过程分为三步:刀补 的建立,刀具中心从与编程轨迹重合过渡到 与编程轨迹偏离一个偏置量的过程;刀补进 行,执行有G41、G42指令的程序段后,刀具 中心始终与编程轨迹相距一个偏置量;刀补 的取消,刀具离开工件,刀具中心轨迹要过 渡到与编程重合的过程。如图为刀补的建立 与取消过程。
8.刀尖圆弧半径补偿还与车刀形状、刀尖位 置有关。车刀形状、刀尖位置各种各样,他 们决定加工时刀尖圆弧在工件的什么位置, 所以刀尖圆弧半径包括刀尖圆弧半径、车刀 形状和刀尖位置。车刀形状和刀尖位置共有9 种,如图 所示。车刀形状和刀尖位置分别用 参数L1~L9表示,并通过手工操作在参数设 置方式下输入到系统中。
第五章 刀具参数补偿功能指令

图5-1
G41、G42指令示意图
Байду номын сангаас
表5-1 刀具半径补偿指令格式说明
指令代码 G41 G42 G40 X、Y、Z D 说 明
左偏刀具半径补偿,是指沿着刀具运动方向向前看, 刀具位于零件左侧的刀具半径补偿(通常顺铣时采用 左侧补偿)。如图5-1所示 右偏刀具半径补偿,是指沿着刀具运动方向向前看, 刀具位于零件右侧的刀具半径补偿(通常逆铣时采用 右侧补偿)。如图5-1所示 刀具半径补偿取消。使用该指令后,使G41、G42指令 无效。 刀具移至终点时,轮廓曲线(编程轨迹)上点的坐标 值 刀具半径补偿寄存器地址字,后面一般用两或三位数 字表示偏置量的代号,偏置量可用MDI方式输入。有 些数控系统用H指令这个值。
将在终点B处形成一个与直线AB相垂直的新矢量BC BC ,刀具中心由A移至C点。沿着刀具前进方向观察, 用G41指令时,形成的新矢量在直线左边,刀具中 心偏向编程轨迹左边;而用G42指令时,刀具中心 偏向右边。 圆弧情况时,如图5-3所示,B点的偏移矢量垂直 于直线AB,圆弧上B点的偏移矢量与圆弧过B点的切 线相垂直。圆弧上每一点的偏移矢量方向总是变化 的,由于直线AB和圆弧相切,所以在B点,直线和 圆弧的偏移矢量重合,方向一致,刀具中心都在C 点。若直线和圆弧不相切,则这两个矢量方向不一 致,此时要进行拐角偏移圆弧插补。 最后一段刀具半径补偿轨迹加工完成后,与建立刀 具半径补偿类似,也应有一直线程序段或G01指
图5-8 G39指令举例
Y
b
a
c
d
与 H01对 应 的 补 偿 量
o
图5-9 刀补动作
加工程序见表5-2。 表5-2 加工程序单
程 序 内 容 O0001(OFFSET INC.); N1 G91 G17 G00 M03 S1000; N2 G41 X20.0 Y10.0 D01; N3 G01 Y40.0 F100; N4 X30.0; N5 Y-30.0; N6 X-40.0; N7 G00 G40 X-10.0 Y-20.0 M05; N8 M30; 说 明 程序名及注释 由G17指定刀补平面 刀补启动
刀具长度补偿和半径补偿
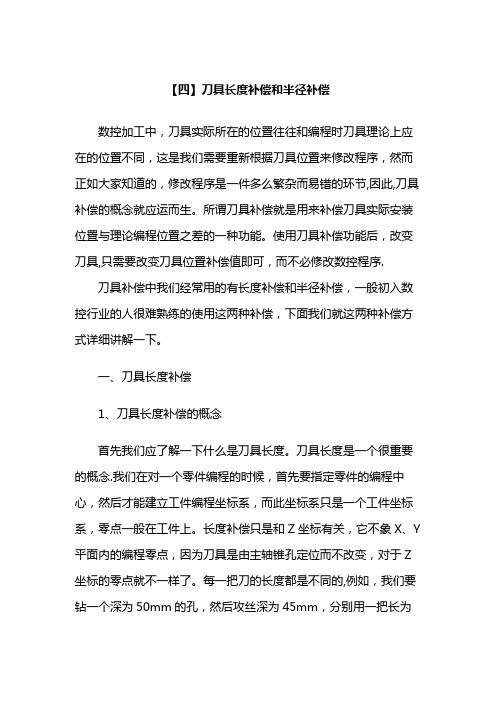
【四】刀具长度补偿和半径补偿数控加工中,刀具实际所在的位置往往和编程时刀具理论上应在的位置不同,这是我们需要重新根据刀具位置来修改程序,然而正如大家知道的,修改程序是一件多么繁杂而易错的环节,因此,刀具补偿的概念就应运而生。
所谓刀具补偿就是用来补偿刀具实际安装位置与理论编程位置之差的一种功能。
使用刀具补偿功能后,改变刀具,只需要改变刀具位置补偿值即可,而不必修改数控程序.刀具补偿中我们经常用的有长度补偿和半径补偿,一般初入数控行业的人很难熟练的使用这两种补偿,下面我们就这两种补偿方式详细讲解一下。
一、刀具长度补偿1、刀具长度补偿的概念首先我们应了解一下什么是刀具长度。
刀具长度是一个很重要的概念.我们在对一个零件编程的时候,首先要指定零件的编程中心,然后才能建立工件编程坐标系,而此坐标系只是一个工件坐标系,零点一般在工件上。
长度补偿只是和Z坐标有关,它不象X、Y 平面内的编程零点,因为刀具是由主轴锥孔定位而不改变,对于Z 坐标的零点就不一样了。
每一把刀的长度都是不同的,例如,我们要钻一个深为50mm的孔,然后攻丝深为45mm,分别用一把长为250mm的钻头和一把长为350mm的丝锥。
先用钻头钻孔深50mm,此时机床已经设定工件零点,当换上丝锥攻丝时,如果两把刀都从设定零点开始加工,丝锥因为比钻头长而攻丝过长,损坏刀具和工件。
此时如果设定刀具补偿,把丝锥和钻头的长度进行补偿,此时机床零点设定之后,即使丝锥和钻头长度不同,因补偿的存在,在调用丝锥工作时,零点Z坐标已经自动向Z+(或Z)补偿了丝锥的长度,保证了加工零点的正确。
2、刀具长度补偿指令通过执行含有G43(G44)和H指令来实现刀具长度补偿,同时我们给出一个Z坐标值,这样刀具在补偿之后移动到离工件表面距离为Z的地方。
另外一个指令G49是取消G43(G44)指令的,其实我们不必使用这个指令,因为每把刀具都有自己的长度补偿,当换刀时,利用G43(G44)H指令赋予了自己的刀长补偿而自动取消了前一把刀具的长度补偿。
数控刀补教程
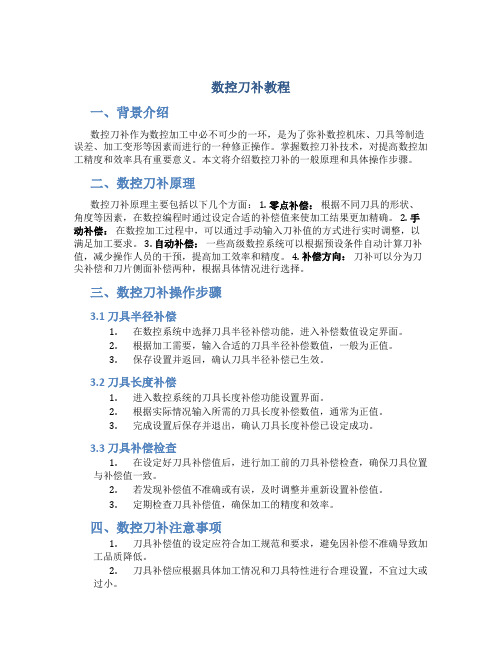
数控刀补教程一、背景介绍数控刀补作为数控加工中必不可少的一环,是为了弥补数控机床、刀具等制造误差、加工变形等因素而进行的一种修正操作。
掌握数控刀补技术,对提高数控加工精度和效率具有重要意义。
本文将介绍数控刀补的一般原理和具体操作步骤。
二、数控刀补原理数控刀补原理主要包括以下几个方面: 1. 零点补偿:根据不同刀具的形状、角度等因素,在数控编程时通过设定合适的补偿值来使加工结果更加精确。
2. 手动补偿:在数控加工过程中,可以通过手动输入刀补值的方式进行实时调整,以满足加工要求。
3. 自动补偿:一些高级数控系统可以根据预设条件自动计算刀补值,减少操作人员的干预,提高加工效率和精度。
4. 补偿方向:刀补可以分为刀尖补偿和刀片侧面补偿两种,根据具体情况进行选择。
三、数控刀补操作步骤3.1 刀具半径补偿1.在数控系统中选择刀具半径补偿功能,进入补偿数值设定界面。
2.根据加工需要,输入合适的刀具半径补偿数值,一般为正值。
3.保存设置并返回,确认刀具半径补偿已生效。
3.2 刀具长度补偿1.进入数控系统的刀具长度补偿功能设置界面。
2.根据实际情况输入所需的刀具长度补偿数值,通常为正值。
3.完成设置后保存并退出,确认刀具长度补偿已设定成功。
3.3 刀具补偿检查1.在设定好刀具补偿值后,进行加工前的刀具补偿检查,确保刀具位置与补偿值一致。
2.若发现补偿值不准确或有误,及时调整并重新设置补偿值。
3.定期检查刀具补偿值,确保加工的精度和效率。
四、数控刀补注意事项1.刀具补偿值的设定应符合加工规范和要求,避免因补偿不准确导致加工品质降低。
2.刀具补偿应根据具体加工情况和刀具特性进行合理设置,不宜过大或过小。
3.定期对刀具补偿值进行检查和调整,确保加工精度和稳定性。
五、结语数控刀补是数控加工中至关重要的环节,掌握良好的数控刀补技术能够提高加工精度和效率,减少加工误差和废品率。
通过本文的介绍,相信读者已经对数控刀补有了更深刻的理解,希望能够在实际加工中加以运用,取得更好的效果。
数控项目6刀具补偿

采用刀具半径补偿功能,刀具运动轨迹
指的不是刀尖,而是刀尖上刀刃圆弧中心 位置的运动轨迹。
2.刀尖圆弧半径补偿的方法
刀尖圆弧半径补偿的方法是键盘输入刀 具参数,并在程序中采用刀具半径补偿指令。 刀具参数主要包括刀尖半径、车刀形状、刀 尖圆弧位置等,这些都与工件的形状有关, 必须用参数输入刀具数据库。
二、对刀及刀具偏置补偿设置
对刀是数控加工中的主要操作和重 要技能。对刀的准确性决定了零件的加 工精度,同时,对刀效率还直接影响数 控加工效率。对刀的实质是确定编程原 点在机床坐标系中的位置。对刀的主要 工作是建立准确的工件坐标系,同时考 虑不同的刀具尺寸对加工的影响。
1.常用的对刀方法
a)
b)
c)
一、刀具功能T的设定
刀具功能包括刀具选择功能和刀具偏置补 偿、刀尖半径补偿功能。刀具功能又称为T功 能,由地址T和其后的四位数字组成,其中前 两位数为刀具号,后两位数为刀补号,用于 选择刀具和设定刀具补偿值。刀具号与刀架 的刀位之间的对应关系由机床制造厂设定。 刀补号和刀具补偿值的对应关系是在程序自 动运行前,在指定界面将刀具补偿值输入数 控系统后建立的。
O0009; T0101; G00 X100.0 Z100.0; M03 S600; G00 X52.0 Z2.0 G71 U1.0 R0.3 G71 P10 Q20 U0.3 W0.05 F150 N10 G0 G42 X0 F60 G01 Z0; G03 X16.0 Z-8.0 R8.0; G01 X20.0; X34.0 Z-18.0; Z-28.0; N20 G02 X50.0 Z-36.0 R8.0 G70P10Q20 G00 G40 X100.0 Z100.0
刀具半径补偿量可以通过刀具补偿设定 画面来设定;T指令要与刀具补偿编号相对应, 并且要输入假想刀尖位置序号。其中,假想刀 尖位置序号共有10 (0~9)个。
刀具补偿 文档

言1.刀具半径补偿的基本概念2.在轮廓加工过程中,由于刀具总有一定的半径(如铣刀半径或线切割机的钼丝半径等),刀具中心的运动轨迹与所需加工零件的实际轮廓并不重合。
如在图1中,粗实线为所需加工的零件轮廓,点划线为刀具中心轨迹。
由图可见在进行内轮廓加工时,刀具中心偏离零件的内轮廓表面一个刀具半径值。
在进行外轮廓加工时,刀具中心又偏离零件的外轮廓表面一个刀具半径值。
这种偏移,称为刀具半径补偿。
3.采用刀具半径补偿的作用和意义数控机床一般都具备刀具半径补偿的功能。
在加工中,使用数控系统的刀具半径补偿功能,就能避开数控编程过程中的繁琐计算,而只需计算出刀具中心轨迹的起始点坐标值就可。
同时,利用刀具半径补偿功能,还可以实现同一程序的粗、精加工以及同一程序的阴阳模具加工等功能。
4.刀具半径补偿指令的使用方式根据ISO 标准规定,当刀具中心轨迹在编程轨迹前进方向的左边时,称为左刀补,用G41表示;刀具中心轨迹在编程轨迹前进方向的右边时,称为右刀补,用G42表示;注销刀具半径补偿时用G40表示。
2 刀具半径补偿过程1.刀具半径补偿建立:当输入BS缓冲器的程序段包含有G41/G42命令时,系统认为此时已进入刀补建立状态。
当以下条件成立时,加工中心以移动坐标轴的形式开始补偿动作。
1.有G41或G42被指定;2.在补偿平面内有轴的移动;3.指定了一个补偿号或已经指定一个补偿号但不能是D00;4.偏置(补偿)平面被指定或已经被指定;5.G00或G01模式有效。
2.补偿模式:在刀具补偿进行期间,刀具中心轨迹始终偏离编程轨迹一个刀具半径值的距离。
此时半径补偿在G00、G01、G02、G03情况下均有效。
3.取消补偿:使用G40指令消去程序段偏置值,使刀具撤离工件,回到起始位置,从而使刀具中心与偏程轨迹重合。
当以下两种情况之一发生时加工中心补偿模式被取消。
①给出G40同时要有补偿平面内坐标轴移动。
②刀具补偿号为D00。
3 刀具半径补偿在加工中心中的应用有了刀具半径自动补偿功能,除可免去刀心轨迹的人工计算外,还可利用同一加工程序去完成粗、精加工及阴阳模具加工等。
- 1、下载文档前请自行甄别文档内容的完整性,平台不提供额外的编辑、内容补充、找答案等附加服务。
- 2、"仅部分预览"的文档,不可在线预览部分如存在完整性等问题,可反馈申请退款(可完整预览的文档不适用该条件!)。
- 3、如文档侵犯您的权益,请联系客服反馈,我们会尽快为您处理(人工客服工作时间:9:00-18:30)。
1-7刀具补偿功能
福建省鸿源技工学校课时授课计划
(2013 —2014 学年度第2学期)
课程名称:数控机床编程与操作任课教师:王公海章节内容1-7刀具补偿功能
授课班级12数控授课日期
授课方式讲授作业练习习题册对应部分
目的要求掌握刀具补偿功能原理
重点难点G40/G41/G42
复习题巩固上节课知识点
仪器教具粉笔黑板
审批意见
审批人:20 年月日
讲授内容和过程方法与指导一、数控车床用刀具的交换功能
1.刀具的交换
指令格式一:T0101;
该指令为FANUC系统转刀指令,前面的T01表示换1号刀,后
面的01表示使用1号刀具补偿。
福建省劳动和社会保障厅制
课时授课计划(副页)
第页
讲授内容和过程方法与指导二、刀具补偿功能
1.刀具补偿功能的定义
定义:数控机床根据刀具实际尺寸,自动改变机床坐标轴或刀
具刀位点位置,使实际加工轮廓和编程轨迹完全一致的功能。
分类:刀具偏移(也称为刀具长度补偿)、刀尖圆弧半径补偿。
2.刀位点的概念
概念:指编制程序和加工时,用于表示刀具特征的点,也是对
刀和加工的基准点。
数控车刀的刀位点
三、刀具偏移补偿
1.刀具偏移的含义
含义:用来补偿假定刀具长度与基准刀具长度之长度差的功
能。
车床数控系统规定X轴与Z轴可同时实现刀具偏移。
分类:刀具几何偏移、刀具磨损偏移。
刀具偏移补偿功能示例
第页
讲授内容和过程方法与指导
数控车床的对刀过程
(3)利用刀具几何偏移进行对刀操作的实质
利用刀具几何偏移进行对刀的实质就是利用刀具几何偏
移使工件坐标系原点与机床原点重合。
3.刀具偏移的应用
利用刀具偏移功能,可以修整因对刀不正确或刀具磨损等原因
造成的工件加工误差。
例加工外圆表面时,如果外圆直径比要求的尺寸大了0.2mm,
此时只需将刀具偏移存储器中的X值减小0.2,并用原刀具及
原程序重新加工该零件,即可修整该加工误差。
同样,如出现
Z方向的误差,则其修整办法相同。
四、刀尖圆弧半径补偿(G40、G41、G42)
1.刀尖圆弧半径补偿的定义
为确保工件轮廓形状,加工时不允许刀具刀尖圆弧的圆心运动
轨迹与被加工工件轮廓重合,而应与工件轮廓偏移一个半径
值,这种偏移称为刀尖圆弧半径补偿。
圆弧形车刀的刀刃半径
偏移也与其相同。
2.假想刀尖与刀尖圆弧半径
在理想状态下,我们总是将尖形车刀的刀位点假想成一个点,
该点即为假想刀尖(图中的A点)。
假想刀尖示意图
第页
讲授内容和过程方法与指导所谓刀尖圆弧半径是指车刀刀尖圆弧所构成的假想圆半径(图
中的r)。
实践中,所有车刀均有大小不等或近似的刀尖圆弧,
假想刀尖在实际加工中是不存在的。
3.未使用刀尖圆弧半径补偿时的加工误差分析
(1)加工台阶面或端面时,对加工表面的尺寸和形状影响不
大,但在端面的中心位置和台阶的清角位置会产生残留误差,
如图所示。
(2)加工圆锥面时,对圆锥的锥度不会产生影响,但对锥面
的大小端尺寸会产生较大的影响,通常情况下,会使外锥面的
尺寸变大,而使内锥面的尺寸变小,如图所示。
(3)加工圆弧时,会对圆弧的圆度和圆弧半径产生影响。
加
工外凸圆弧时,会使加工后的圆弧半径变小,其值=理论轮廓
半径R–刀尖圆弧半径r,如图所示。
加工内凹圆弧时,会使加工后的圆弧半径变大,
其值=理论轮廓半径R+刀尖圆弧半径r,如图所示。
4.刀尖圆弧半径补偿指令
(1)指令格式
G41 G01/G00 X Y F ;(刀尖圆弧半径左补偿)
G42 G01/G00 X Y F ;(刀尖圆弧半径右补偿)
G40 G01/G00 X Y ;(取消刀尖圆弧半径补
偿)
2)指令说明
刀尖圆弧半径补偿偏置方向的判别:
课时授课计划(副页)
第页讲授内容和过程方法与指导
刀尖圆弧半径补偿偏置方向的判别
a)后置刀架,+Y轴向外b)前置刀架,+Y轴向内
5.圆弧车刀刀沿位置的确定
数控车刀的刀沿位置
a)后置刀架,+Y轴向外b)前置刀架,+Y轴向内c)具体
刀具的相应刀沿号
P–假想刀尖点S–刀沿圆心位置r–刀尖圆弧半径
课时授课计划(副页)
第页
讲授内容和过程方法与指导
部分典型刀具的刀沿号
a)后置刀架的刀沿位置号b)前置刀架的刀沿位置号
6.刀尖圆弧半径补偿过程
刀尖圆弧半径补偿的过程分为三步:即刀补的建立,刀补的
进行和刀补的取消。
刀尖圆弧半径补偿过程
FC—刀补建立CDE—刀补执行EF—刀补取消
课时授课计划(副页)
第页
讲授内容和过程方法与指导
7.进行刀具半径补偿时应注意的事项
(1)刀具圆弧半径补偿模式的建立与取消程序段只能在G00或G01移动指令模式下才有效。
(2)G41/G42不带参数,其补偿号(代表所用刀具对应的刀尖半径补偿值)由T指令指定。
该刀尖圆弧半径补偿号与刀具偏置补偿号对应。
(3)采用切线切入方式或法线切入方式建立或取消刀补。
对于不便于沿工件轮廓线方向切向或法向切入切出时,可根据情况增加一个过渡圆弧的辅助程序段。
(4)为了防止在刀具半径补偿建立与取消过程中刀具产生过切现象,在建立与取消补偿时,程序段的起始位置与终点位置最好与补偿方向在同一侧。
(5)在刀具补偿模式下,一般不允许存在连续两段以上的补偿平面内非移动指令,否则刀具也会出现过切等危险动作。
(6)在选择刀尖圆弧偏置方向和刀沿位置时,要特别注意前置刀架和后置刀架的区别。
8.使用刀具补偿功能时的加工实例
例试用刀具补偿功能等指令编写图所示工件外轮廓的加工程序(内轮廓已加工完成, 以内孔定位与装夹)。
刀具补偿功能编程实例
a) 零件图b) 三维立体图
程序参见课本。