管道施工技术方案word参考模板
水管施工方案(3篇)

第1篇一、工程概述1. 工程背景随着城市化进程的加快,我国各类建筑项目日益增多,水管施工作为建筑的重要组成部分,其质量直接关系到建筑的使用功能和安全性。
本方案旨在为水管施工提供一套科学、合理、高效的施工方案,确保工程质量,满足用户需求。
2. 工程概况(以下内容根据实际项目填写)工程名称:XX住宅小区供水管网改造工程工程地点:XX市XX区XX街道工程规模:总建筑面积约XX万平方米,供水管网改造长度约XX公里施工内容:包括给水管道铺设、排水管道铺设、消防管道铺设等施工期限:预计XX个月二、施工准备1. 技术准备(1)熟悉图纸:施工前,项目技术人员应全面了解施工图纸,包括给水、排水、消防等管道的布置、尺寸、材料等。
(2)技术交底:组织施工人员学习施工图纸和施工方案,明确施工要求、质量标准、安全措施等。
(3)施工工艺:根据工程特点,选择合适的施工工艺,如开挖埋管、顶管、管道焊接等。
2. 材料准备(1)管材:选择符合国家标准的给水管、排水管、消防管等,确保材质优良、规格齐全。
(2)管件:根据管道连接需求,准备各种规格的管件,如三通、弯头、阀门等。
(3)辅助材料:准备电缆、水泥、沙子、钢筋等辅助材料。
3. 人员准备(1)组织施工队伍:根据工程规模,组建专业的施工队伍,包括施工队长、技术员、施工人员等。
(2)人员培训:对施工人员进行专业技能培训,确保施工人员具备相应的操作技能。
(3)安全培训:对施工人员进行安全教育培训,提高安全意识,预防安全事故。
三、施工工艺1. 给水管道施工(1)开挖沟槽:按照设计要求,开挖沟槽,确保沟槽深度、宽度符合规范。
(2)基础处理:对沟槽底部进行夯实,确保基础牢固。
(3)铺设管道:将管道按照设计要求铺设在沟槽内,注意管道的平整度和坡度。
(4)管道连接:采用焊接、法兰连接等方式,将管道连接牢固。
(5)回填土:回填土时,分层夯实,确保管道稳定。
2. 排水管道施工(1)开挖沟槽:按照设计要求,开挖沟槽,确保沟槽深度、宽度符合规范。
(完整版)管道施工方案范本

施工方案目录一、编制依据 (2)二、工程概况 (2)三、施工部署 (2)四、主要分部分项施工方案 (3)五、质量保证措施 (18)六、工期保证措施 (18)七、安全施工保证措施 (19)八、文明施工保证措施 (21)一、编制依据1、鲁丰织染有限公司污水处理工程施工图(工艺)图纸。
2、《给排水构筑物施工及验收规范》GB50141-2008。
3、《纺织染整工业废水治理工程技术规范》HJ471-2009。
4、《工业金属管道工程施工及验收规范》GB20535-1997。
5、淄博市施工现场管理有关文件和标准。
6、施工现场状况及对周围环境的调查。
二、工程概况本工程为鲁丰织染有限公司二期工程污水处理站,设计规模为10000立方米/天,工程位于山东省淄博市淄川区,主要施工内容包括:工艺管道安装(污泥管道、污水管道、曝气管道、给水管道和加药管道)和设备安装(隔膜厢式压滤机、污泥泵、离心风机、污水提升泵、格栅机、冷却塔、加药泵、混合液回流泵、刮泥机、吸泥机、中心传动浓缩机以及泵房内离心泵的安装)。
污泥管道、污水管道采用无缝钢管,好氧池曝气主风管采用无缝钢管,水下曝气支管采用不锈钢管,水解酸化池布水管为UPVC管,站内给水管、加药管为PPR管。
三、施工部署3.1.组织机构:本工程按项目法组织施工,项目经理选派承担过大型工程项目管理,并具有丰富施工管理经验的一级项目经理担任;项目总工程师由技术管理水平较高、有创优管理经验、参加过优良工程施工并具有丰富施工经验的工程师担任。
根据本工程特点,组建精干项目经理部,对本项目的人、财、物按照项目法施工管理的要求实行统一组织,统一布置,统一计划,统一协调,统一管理,并认真执行ISO9002质量标准,充分发挥各职能部门、各岗位人员的职能作用,认真履行管理职责,确保本项目质量体系持续、有效的运行。
通过我们科学、严谨的工作质量和项目管理经验,确保实现合同规定的工期。
3.2.劳动力组织:主要技术工人配备表序号工种数量10 备注1 2 3 焊工安装工其他12123.3.技术准备①熟悉设计图纸和资料。
管道安装工程施工方案模板范本
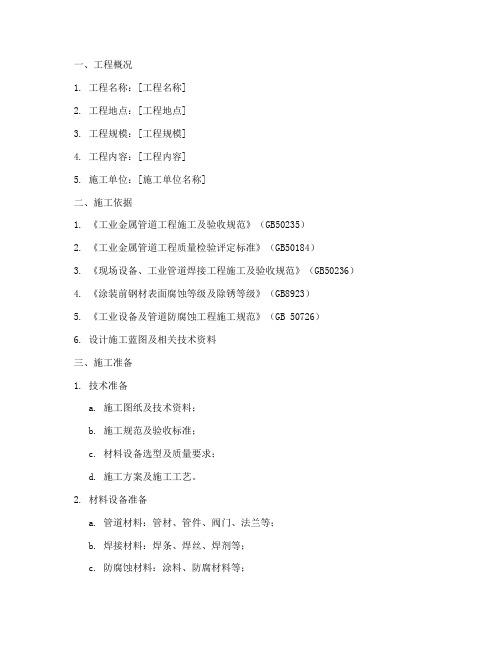
一、工程概况1. 工程名称:[工程名称]2. 工程地点:[工程地点]3. 工程规模:[工程规模]4. 工程内容:[工程内容]5. 施工单位:[施工单位名称]二、施工依据1. 《工业金属管道工程施工及验收规范》(GB50235)2. 《工业金属管道工程质量检验评定标准》(GB50184)3. 《现场设备、工业管道焊接工程施工及验收规范》(GB50236)4. 《涂装前钢材表面腐蚀等级及除锈等级》(GB8923)5. 《工业设备及管道防腐蚀工程施工规范》(GB 50726)6. 设计施工蓝图及相关技术资料三、施工准备1. 技术准备a. 施工图纸及技术资料;b. 施工规范及验收标准;c. 材料设备选型及质量要求;d. 施工方案及施工工艺。
2. 材料设备准备a. 管道材料:管材、管件、阀门、法兰等;b. 焊接材料:焊条、焊丝、焊剂等;c. 防腐蚀材料:涂料、防腐材料等;d. 施工工具:切割机、焊接机、吊装设备等。
3. 人员准备a. 施工队伍组织架构;b. 施工人员资质及技能;c. 施工人员培训及安全教育。
四、施工工艺及方法1. 管道安装施工工艺流程a. 施工准备;b. 管道预制;c. 管道运输及堆放;d. 管道安装;e. 管道焊接;f. 管道防腐;g. 管道试压;h. 管道验收。
2. 管道焊接工艺a. 焊接方法:手工电弧焊、气体保护焊、等离子弧焊等;b. 焊接参数:焊接电流、电压、焊接速度等;c. 焊接顺序:从下至上、从左至右、从里向外等。
3. 管道防腐工艺a. 防腐材料:环氧煤沥青涂料、聚氨酯涂料等;b. 防腐工艺:涂装前处理、涂装、固化等。
五、施工质量控制1. 材料设备质量检验a. 材料设备进场检验;b. 材料设备质量合格证明;c. 材料设备使用过程中的检验。
2. 施工过程质量控制a. 管道安装精度;b. 焊接质量;c. 防腐蚀质量;d. 管道试压质量。
3. 施工验收a. 管道安装工程验收;b. 管道焊接工程验收;c. 管道防腐工程验收。
管道施工方案范本
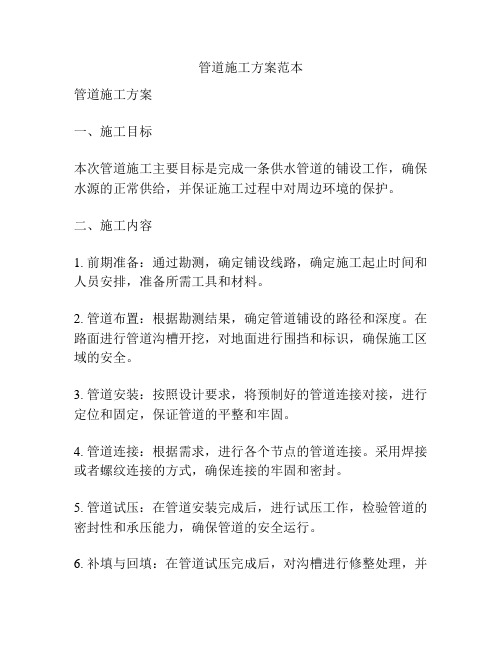
管道施工方案范本管道施工方案一、施工目标本次管道施工主要目标是完成一条供水管道的铺设工作,确保水源的正常供给,并保证施工过程中对周边环境的保护。
二、施工内容1. 前期准备:通过勘测,确定铺设线路,确定施工起止时间和人员安排,准备所需工具和材料。
2. 管道布置:根据勘测结果,确定管道铺设的路径和深度。
在路面进行管道沟槽开挖,对地面进行围挡和标识,确保施工区域的安全。
3. 管道安装:按照设计要求,将预制好的管道连接对接,进行定位和固定,保证管道的平整和牢固。
4. 管道连接:根据需求,进行各个节点的管道连接。
采用焊接或者螺纹连接的方式,确保连接的牢固和密封。
5. 管道试压:在管道安装完成后,进行试压工作,检验管道的密封性和承压能力,确保管道的安全运行。
6. 补填与回填:在管道试压完成后,对沟槽进行修整处理,并进行土方的补填,确保施工区域的平整和美观。
7. 环境恢复:施工结束后,清理施工现场,确保周边环境的整洁和安全,并修复施工期间可能造成的破坏。
三、施工方法和措施1. 施工方法:采用人工开挖或者机械开挖的方式进行管道沟槽的开挖工作,并使用合适的设备进行管道的安装和连接工作。
2. 施工措施:在施工过程中,要加强对周边环境的保护,采取防护措施,确保施工过程中不会危及周边房屋、道路等设施。
同时要严格遵守安全操作规程,防止人员和设备的意外伤害。
四、施工时间安排1. 前期准备:XX年XX月XX日-XX年XX月XX日2. 管道布置:XX年XX月XX日-XX年XX月XX日3. 管道安装:XX年XX月XX日-XX年XX月XX日4. 管道连接:XX年XX月XX日-XX年XX月XX日5. 管道试压:XX年XX月XX日-XX年XX月XX日6. 补填与回填:XX年XX月XX日-XX年XX月XX日7. 环境恢复:XX年XX月XX日-XX年XX月XX日五、安全防护措施1. 对施工区域进行围挡和标识,禁止未经授权人员进入施工区。
2. 坚守施工现场的安全生产规定,人员必须佩戴安全帽,严禁吸烟。
管道施工工程方案模板范本

管道施工工程方案模板范本一、工程概况1.1 项目名称:XXX管道施工工程1.2 工程地址:XXX市XXX区XXX街道1.3 工程性质:新建/改扩建/维修/其他1.4 工程规模:总长度XXkm,管道直径XXmm,涉及XXX个管段1.5 工程目的:满足城市供水/供气/供热/排水等需求二、工程内容2.1 工程范围:本工程涉及XXX个区域,主要包括XXX2.2 工程内容:主要包括XXX管道敷设、支架安装、阀门安装、管道连接、保温绝热、管道试压、防腐工程等三、施工组织3.1 施工单位:XXX公司3.2 施工人员:总工程师、安全员、质检员、机械操作工等3.3 管理人员:项目经理、工程监理、安全监督等3.4 协调配合:与相关单位协商合作,确保施工畅通四、工程施工方案4.1 施工方法:按照工程图纸要求,采用XXX方法进行施工4.2 施工步骤:分段施工,按道路条件和市政规划进行施工顺序安排4.3 关键工序:XXX环节的施工,如管道连接、阀门安装等4.4 安全保障:严格遵守安全规程,确保施工人员的安全4.5 质量保障:制定严格的质量控制标准,确保工程质量五、施工设备及材料5.1 施工设备:XXX设备5.2 施工材料:主要包括XXX,符合国家标准要求5.3 仓储及保管:严格按照材料规范要求进行仓储保管,确保材料的质量六、环境保护6.1 噪音控制:合理安排施工时间,减少对周边居民的影响6.2 扬尘治理:采取喷淋、覆盖等方式进行扬尘治理6.3 废物处理:对施工产生的废弃物进行分类处理,确保不会对环境造成污染七、工程安全7.1 施工安全:严格按照国家安全规范要求,加强对施工人员的安全培训和监督7.2 设施安全:保障施工设备及临时设施的安全可靠7.3 预防措施:对可能发生的安全事故进行预防和应急措施规划八、验收标准8.1 施工标准:保证施工符合国家相关标准和规范8.2 竣工验收:严格按照工程质量验收标准进行验收8.3 质量保证:对工程质量和管道使用性能进行保证以上为XXX管道施工工程方案,经审查无误后,即可进行实施。
管道施工工程施工方案(3篇)

第1篇一、工程概况本工程为XX管道施工项目,位于XX地区,全长XX公里。
工程内容包括管道铺设、防腐、试压、试运行等。
工程总投资约为XX万元,工期为XX个月。
二、施工组织1. 施工单位:XX有限公司2. 施工项目经理:XX3. 施工人员:共计XX人,分为施工队、技术组、质量组、安全组等。
4. 施工设备:挖掘机、推土机、压路机、吊车、防腐设备、试压设备等。
三、施工方案1. 施工准备(1)施工现场:清理施工场地,确保施工道路畅通,搭建施工营地。
(2)材料设备:提前采购管道、防腐材料、施工设备等,确保材料质量。
(3)施工人员:对施工人员进行技术培训和安全教育,提高施工人员素质。
2. 施工工艺(1)管道铺设1)测量放线:根据设计图纸,进行现场测量放线,确保管道走向准确。
2)开挖沟槽:按照设计要求,开挖沟槽,确保沟槽尺寸、坡度、深度符合规范。
3)管道铺设:将管道按顺序铺设在沟槽内,注意管道的连接和固定。
4)回填压实:回填沟槽,采用分层回填、分层压实的方法,确保回填质量。
(2)防腐处理1)表面处理:对管道表面进行打磨、清洗,确保防腐涂层粘结牢固。
2)防腐涂层:按照设计要求,选择合适的防腐材料,对管道进行防腐涂层施工。
(3)试压1)试压准备:安装试压设备,检查设备运行情况。
2)试压过程:按照设计要求,对管道进行试压,观察管道是否存在泄漏现象。
3)试压结果:根据试压数据,判断管道是否符合设计要求。
(4)试运行1)试运行准备:安装试运行设备,检查设备运行情况。
2)试运行过程:按照设计要求,对管道进行试运行,观察管道运行状态。
3)试运行结果:根据试运行数据,判断管道是否符合设计要求。
四、施工质量控制1. 材料质量控制:对采购的管道、防腐材料、施工设备等进行严格检验,确保材料质量。
2. 施工过程控制:严格按照施工规范和工艺要求进行施工,确保施工质量。
3. 质量检验:对施工过程中的关键环节进行检验,确保施工质量。
4. 成品保护:在施工过程中,采取有效措施保护管道、防腐涂层等成品。
管道施工方案范本
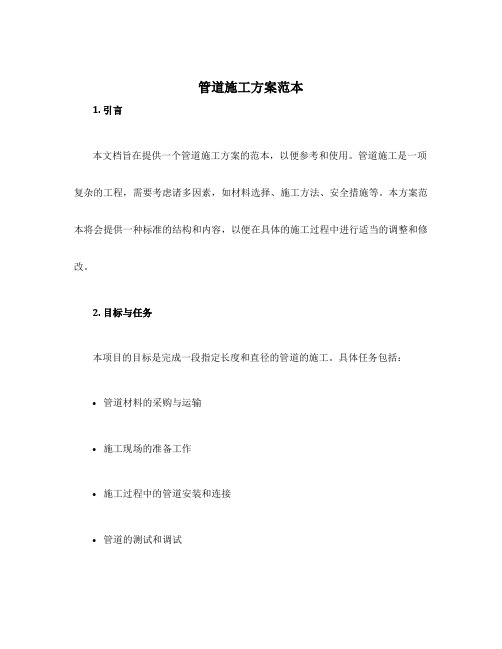
管道施工方案范本1. 引言本文档旨在提供一个管道施工方案的范本,以便参考和使用。
管道施工是一项复杂的工程,需要考虑诸多因素,如材料选择、施工方法、安全措施等。
本方案范本将会提供一种标准的结构和内容,以便在具体的施工过程中进行适当的调整和修改。
2. 目标与任务本项目的目标是完成一段指定长度和直径的管道的施工。
具体任务包括:•管道材料的采购与运输•施工现场的准备工作•施工过程中的管道安装和连接•管道的测试和调试•施工现场的清理和整理3. 管道材料的采购与运输根据项目要求,确定所需的管道材料。
考虑到管道的使用环境和功能,选择合适的材料,如钢、铜、铸铁等。
选择合适的供应商,从他们那里采购所需的管道材料。
安排合适的运输方式,确保管道材料的安全到达施工现场。
4. 施工现场的准备工作在施工现场进行必要的准备工作,以确保施工过程的顺利进行。
包括但不限于以下事项:•地面的平整和清理•施工现场的标识和围栏设置•确保所需的工具和设备齐全,并进行必要的检查和维修•确保施工过程中的安全措施已经准备就绪,如安全帽、手套、安全绳等5. 管道的安装和连接根据项目要求,在施工现场使用合适的工具和设备进行管道的安装和连接。
确保安装过程中的准确度和质量,避免漏水和其他质量问题。
按照相关的标准和规范进行施工,如焊接、螺纹连接等。
6. 管道的测试和调试在管道安装完成后,进行必要的测试和调试工作,以确保管道的正常工作和安全性。
测试内容包括但不限于以下方面:•管道的漏水测试•管道的耐压测试•管道的流量测试7. 施工现场的清理和整理在施工完成后,进行必要的清理和整理工作,以确保施工现场的安全和整洁。
清理工作包括但不限于以下方面:•清理施工过程中产生的垃圾和废料•整理和归置使用过的工具和设备•检查施工现场的设施和设备,确保其完好无损并进行必要的维修工作8. 总结本文档提供了一个管道施工方案的范本,可以作为参考和使用。
具体的施工方案需要根据项目的具体需求进行调整和修改。
管道工程施工技术方案范本

管道工程施工技术方案范本1. 引言管道工程是指为了运输液体、气体和固体颗粒等物质而在地下或地面铺设的管道系统。
管道工程的施工技术方案是施工单位在施工过程中根据设计要求和实际情况制定的具体施工措施和方法。
本文就某管道工程的施工技术方案进行分析和总结,以期为类似工程的施工提供参考。
2. 工程概况某管道工程是指一条长距离输送原油或天然气的管道,全长1000公里,跨越多个省市。
管道主要由钢管组成,直径为DN800,设计压力为10MPa。
管道设计温度为-40℃至70℃。
管道线路经过山区、平原和板块,地质条件复杂。
3. 技术方案(1)前期准备工作在进行管道施工前,首先要进行前期准备工作,包括:1)地质勘察:对管道线路的地质条件进行勘察,着重关注特殊地质条件(如山区、河流和特殊土质)对管道的影响。
2)设计方案确认:要确认管道的设计方案,包括管道线路、材料和安装等技术指标。
3)施工组织设计:确定施工组织架构、施工队伍配备和施工计划。
(2)施工准备在进行管道施工前,要进行施工准备工作,包括:1)人员培训:对施工人员进行安全操作培训,包括管道安装、焊接和防腐等技能培训。
2)设备调试:检查施工所需的设备和机械设备,保证设备工作正常。
3)材料采购:采购符合设计要求的管道材料,包括钢管、管道配件、焊接材料和防腐涂料等。
4)施工图纸制作:根据设计方案,制定细化的施工图纸和工艺流程图。
(3)施工工艺管道工程施工工艺主要包括以下几个方面:1)开挖和铺设:根据设计要求和现场情况进行开挖和铺设,保证管道线路的直线和平整。
2)焊接:使用符合要求的焊接工艺对钢管进行接头焊接,保证焊缝质量。
3)防腐处理:对接头和管道表面进行防腐处理,采用喷涂或涂刷方式进行防腐处理。
4)安装管道配件:按照设计要求对管道进行支架安装、阀门安装和测量仪表安装等。
5)试压和清洗:施工完成后进行管道试压和清洗,检测管道的质量和密封性。
(4)安全防护在进行管道工程施工过程中,要严格执行安全防护措施,包括:1)人员安全:施工人员要佩戴符合要求的安全防护装备,包括安全帽、安全鞋、防护眼镜和手套等。
某工程管道安装施工方案(3篇)

第1篇一、工程概况XX工程项目位于我国某城市,工程总建筑面积约XX万平方米,其中地下建筑面积约XX万平方米。
本项目管道安装工程主要包括给排水管道、消防管道、中水管道、空调水管道、燃气管道等。
为确保管道安装质量,保障工程顺利进行,特制定本施工方案。
二、施工准备1. 施工组织(1)成立管道安装项目部,负责施工过程中的组织、协调和管理工作。
(2)明确施工人员职责,确保各工种人员具备相应的技术水平和操作能力。
2. 施工材料(1)给排水管道:采用PE、PVC、PPR等材质的管道及配件。
(2)消防管道:采用不锈钢、镀锌钢管等材质的管道及配件。
(3)中水管道:采用PE、PVC等材质的管道及配件。
(4)空调水管道:采用不锈钢、镀锌钢管等材质的管道及配件。
(5)燃气管道:采用PE、PVC等材质的管道及配件。
3. 施工工具(1)电焊机、切割机、弯管机、焊接设备等。
(2)水准仪、经纬仪、全站仪等测量设备。
(3)手提式电动工具、扳手、螺丝刀等。
4. 施工方案编制(1)根据工程图纸、设计要求和相关规范,编制详细的施工方案。
(2)针对不同类型的管道,制定相应的施工工艺和质量控制措施。
(3)针对施工现场实际情况,调整施工方案,确保施工顺利进行。
三、施工工艺及质量控制1. 施工工艺(1)给排水管道安装:按照设计要求,确定管道走向、管径和管材。
采用热熔连接、电熔连接、承插连接等方法进行管道连接。
(2)消防管道安装:按照设计要求,确定管道走向、管径和管材。
采用焊接、法兰连接等方法进行管道连接。
(3)中水管道安装:按照设计要求,确定管道走向、管径和管材。
采用热熔连接、电熔连接、承插连接等方法进行管道连接。
(4)空调水管道安装:按照设计要求,确定管道走向、管径和管材。
采用焊接、法兰连接等方法进行管道连接。
(5)燃气管道安装:按照设计要求,确定管道走向、管径和管材。
采用焊接、法兰连接等方法进行管道连接。
2. 质量控制(1)严格控制管道材料的质量,确保符合国家相关标准。
管道施工方案范本

管道施工方案范本管道施工方案一、项目背景本项目计划施工一条长度为1000米的排水管道,用于排放雨水和污水。
该管道经过河道桥梁下方,地势较低,需要采取合理的施工方案确保工程质量和施工安全。
二、施工准备1. 设计方案确认:根据工程要求,确定施工工艺和流程,明确施工工艺参数。
2. 人员和机械调配:调配专业管道施工队伍,包括挖掘机、料车、输送设备等。
3. 材料采购准备:根据设计方案,采购所需的管材、管件、胶水等施工材料。
三、施工流程1. 地面整理:清理管道施工区域的垃圾和杂草,确保施工区域干净整洁。
2. 开挖井口:根据设计要求,使用挖掘机进行环形开挖,开挖井底的水平面与井口平齐。
3. 安装管道:先铺设管道,然后用胶水粘合管道接头,保证接口紧密无漏水。
4. 管道的调整和修整:根据设计要求,调整管道的高度和水平度,修整管道表面,确保管道的质量和美观。
5. 固定与封堵:使用水泥或其他固定材料,将管道固定在井底,确保管道不会变形或移位。
封堵井口,防止外界杂物进入管道。
6. 施工验收:进行管道施工的质量和安全验收,确保施工符合要求。
四、施工安全1. 安全宣传:对施工人员进行安全教育和培训,提高安全意识。
2. 道路保护:施工现场周围设置警示标志和围栏,保护通过道路的行人和车辆的安全。
3. 施工区域防护:在施工区域内设置安全警示标志,确保施工人员和设备的安全。
4. 施工设备检查:定期检查施工设备的工作状况,确保设备正常工作。
5. 紧急处理措施:制定和完善应急预案,以备发生意外或突发情况时快速应对。
五、施工质量1. 材料质量:采用符合国家标准的优质管材、管件和施工材料。
2. 工艺流程:严格按照设计方案和施工要求进行施工,保证管道的密封性能和稳定性。
3. 施工过程监控:设立监理人员监控施工过程,确保施工质量符合要求。
4. 材料检测:对所使用的管材和施工材料进行必要的质量检验,确保质量合格。
六、施工进度1. 制定详细的施工计划,合理安排施工流程和施工顺序。
工程管道施工方案(3篇)

第1篇一、项目背景随着城市化进程的加快,各类工程项目的建设日益增多,工程管道施工作为基础设施建设的重要组成部分,其质量直接影响到工程项目的整体质量和使用效果。
本方案针对某工程项目管道施工,制定详细的施工方案,以确保施工质量和进度。
二、施工范围及内容1. 施工范围:本工程管道施工包括给排水管道、消防管道、电缆管道等。
2. 施工内容:(1)管道测量与定位;(2)管道材料准备;(3)管道基础施工;(4)管道安装;(5)管道试压与冲洗;(6)管道验收。
三、施工准备1. 技术准备:组织施工技术人员进行技术交底,明确施工工艺、质量标准和操作规程。
2. 材料准备:根据设计要求,准备各类管道材料、配件及施工工具。
3. 人员准备:组织施工队伍,明确各岗位人员职责,确保施工人员具备相应的技能和素质。
4. 施工设备准备:检查施工设备,确保其正常运行,满足施工需求。
四、施工工艺1. 管道测量与定位:根据设计图纸,采用全站仪、水准仪等测量仪器进行管道测量,确保管道位置准确。
2. 管道材料准备:按照设计要求,对管道材料进行检验,确保其质量符合标准。
3. 管道基础施工:根据管道埋深要求,进行土方开挖、基础处理,确保基础稳定。
4. 管道安装:(1)按照设计要求,进行管道连接,确保接口严密;(2)管道安装时,注意管道坡度,确保排水畅通;(3)安装完毕后,对管道进行防腐处理。
5. 管道试压与冲洗:按照设计要求,对管道进行试压和冲洗,确保管道无渗漏、畅通。
6. 管道验收:完成管道施工后,组织相关人员对管道进行验收,确保管道质量符合要求。
五、施工质量控制1. 材料质量控制:严格按照国家标准和设计要求,对管道材料进行检验,确保材料质量。
2. 施工过程控制:加强对施工过程的监督,确保施工工艺、质量标准和操作规程得到严格执行。
3. 管道试压与冲洗:严格按照设计要求进行试压和冲洗,确保管道无渗漏、畅通。
4. 管道验收:对管道进行验收,确保管道质量符合要求。
管道施工方案范本
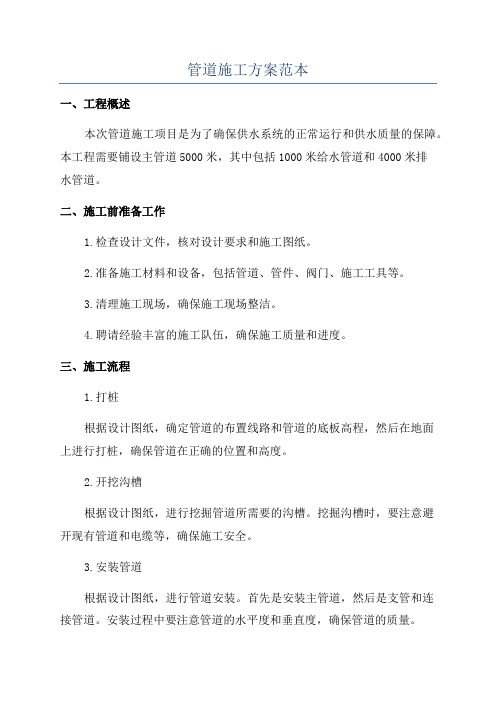
管道施工方案范本一、工程概述本次管道施工项目是为了确保供水系统的正常运行和供水质量的保障。
本工程需要铺设主管道5000米,其中包括1000米给水管道和4000米排水管道。
二、施工前准备工作1.检查设计文件,核对设计要求和施工图纸。
2.准备施工材料和设备,包括管道、管件、阀门、施工工具等。
3.清理施工现场,确保施工现场整洁。
4.聘请经验丰富的施工队伍,确保施工质量和进度。
三、施工流程1.打桩根据设计图纸,确定管道的布置线路和管道的底板高程,然后在地面上进行打桩,确保管道在正确的位置和高度。
2.开挖沟槽根据设计图纸,进行挖掘管道所需要的沟槽。
挖掘沟槽时,要注意避开现有管道和电缆等,确保施工安全。
3.安装管道根据设计图纸,进行管道安装。
首先是安装主管道,然后是支管和连接管道。
安装过程中要注意管道的水平度和垂直度,确保管道的质量。
4.连接管道在管道安装完成后,进行管道的连接。
连接方式可以采用焊接、螺纹连接或者橡胶密封连接。
连接过程中要注意密封性和连接牢固度,确保管道的使用寿命。
5.测试管道在管道连接完成后,进行管道的水压试验。
水压试验可以通过加水压力和观察管道是否漏水来判断管道的密封性和质量。
6.封闭沟槽在管道安装和测试完成后,进行沟槽的封闭工作。
封闭沟槽时,要确保沟槽的排水通畅,避免积水对管道造成影响。
7.清理工地在工程完工后,进行工地清理工作。
清理工作包括清理垃圾、整理设备和施工材料等,确保工地整洁。
四、安全措施1.施工现场设置明显的安全警示标志,提醒相关人员注意安全。
2.确保施工人员佩戴安全帽、安全鞋等个人防护装备。
3.施工现场设置防护网和安全通道,确保施工人员的人身安全。
4.严格遵守施工规范和操作规程,确保施工过程的安全性。
五、质量控制1.按照设计要求进行施工,保证管道的质量。
2.对管道材料进行质量检验,确保管道材料符合标准。
3.对施工过程进行质量检查,发现问题及时进行整改。
六、施工进度根据施工队伍的实际情况和施工资源的配备,制定详细的施工进度表。
管道施工方案范本

管道施工方案范本
一、项目概述
本方案旨在针对管道施工提供一个完整的范本,包括施工前的准备工作、具体施工步骤、质量控制措施等内容,以确保管道施工的顺利进行。
二、准备工作
1. 资料准备
•确认管道设计图纸
•准备施工所需材料清单
•确保施工人员具备相应资质和技能
2. 现场勘察
•对施工地点进行详细勘测
•制定施工方案和安全计划
三、施工步骤
1. 管道敷设
•根据设计图纸确定管道敷设位置
•进行管道的挖掘和铺设
•确保管道的平整和连接牢固
2. 管道连接
•对敷设好的管道进行连接
•使用适当的连接件和工具进行连接
•进行密封和测试,确保连接处无漏水
3. 管道固定
•对连接完毕的管道进行固定
•使用支架、吊架等固定设备进行固定
•确保管道的稳定性和安全性
4. 质量检验
•对施工完成的管道进行质量检验
•检查管道的平整度、连接牢固度等指标
•确保施工质量符合要求
四、质量控制
1. 定期检查
•设立定期检查制度
•对管道施工过程进行定期检查
•及时发现和解决问题
2. 质量验收
•在施工完成后进行质量验收
•确保管道施工符合相关标准和要求
•出具合格证明
五、总结
通过本方案的实施,可有效指导管道施工过程,在保证施工质量的前提下提高施工效率,确保管道工程顺利完成。
管道施工方案范本

管道施工方案范本管道施工方案一、项目背景本次施工项目位于某市某区,是一座新建的居民小区。
该小区规划建设有供水管道、排水管道、燃气管道和电力管道等基础设施。
本方案主要针对供水管道的施工,旨在确保管道的安全、高效、质量合格。
二、施工目标1. 安装供水管道,确保居民正常用水需求;2. 遵守相关建设规范和安全操作规程,保障施工过程的安全性;3. 保证管道质量,确保供水管道在使用期间不出现渗漏等问题;4. 施工期间,避免对周边环境造成污染和破坏。
三、施工步骤1. 调查勘测:根据设计图纸,安排专业人员进行管线走向、埋深等勘测工作,确定施工方案;2. 材料准备:按照设计要求,采购符合标准的管材、接头、阀门等相关材料,并进行出厂检验;3. 施工准备:成立施工班组,配备必要的施工设备和工具,保证施工人员的安全;4. 开挖沟槽:根据设计要求,在指定位置和深度进行沟槽开挖,保证施工质量;5. 敷设管道:安装管道前,先进行管道的清洗和检查,确保无杂质和破损。
按设计要求进行管道的敷设、连接和固定;6. 防腐处理:对敷设完毕的管道进行防腐处理,确保管道在使用过程中不受腐蚀;7. 接口处理:对每个接头进行密封处理,确保接头的安全和防漏;8. 系统测试:安装完毕后,进行系统的压力测试和泄漏检测,确保管道的质量和安全性;9. 竣工验收:按照相关规定进行竣工验收,并移交相关部门。
四、施工安全措施1. 施工人员必须持相关证件上岗,并接受安全教育和培训,熟悉安全操作规程;2. 施工现场设立相关警示标志,设置安全防护措施,保障施工人员的人身安全;3. 使用合格的施工设备和工具,定期进行检查和维护,确保设备的正常运转;4. 施工过程中,进行人员配备和协同操作,保障施工现场的安全和有序进行;5. 定期对施工人员进行安全工作检查和评估,发现安全隐患及时纠正。
五、质量控制措施1. 严格按照设计要求进行施工,材料符合相关标准,确保管道的质量;2. 对每个施工环节进行专人监督和检查,发现问题及时修复;3. 管道施工完成后,进行系统测试和验收,确保管道的安全、完好;4. 施工完成后,及时清理施工现场和周边环境,确保不污染环境。
管道施工方案doc.完整版

管道施工方案doc.完整版范本一:管道施工方案1. 项目概述1.1 工程位置1.2 工程规模1.3 工程目标2. 技术要求2.1 材料选用2.1.1 管道材料2.1.2 阀门、管件材料2.1.3 施工辅助材料2.2 施工工艺2.2.1 开挖与回填2.2.2 管道安装2.2.3 管道连接2.2.4 管道保护2.3 设备及机械2.3.1 挖掘机2.3.2 手持工具2.3.3 焊接设备2.3.4 检测设备3. 施工进度安排3.1 施工3.2 施工流程图3.3 施工工期4. 施工现场管理4.1 管道布置与标识 4.2 安全管理4.3 现场环境保护4.4 施工人员管理5. 质量控制5.1 施工过程质量控制 5.1.1 检查与测试5.1.2 焊接质量控制5.1.3 阀门、管件安装质量控制 5.2 管道试压5.2.1 试压试验计划5.2.2 试压试验报告5.3 质量问题处理6. 碰口变更及设计调整7. 施工安全与技术交底7.1 技术交底7.2 施工安全交底8. 管道竣工报告8.1 施工总结8.2 施工质量评定8.3 技术经济效果评价8.4 竣工图纸9. 附件范本二:管道施工方案1. 项目概述1.1 工程背景1.2 工程范围1.3 施工目标2. 工程分析2.1 施工环境分析2.1.1 地理条件2.1.2 气候条件2.1.3 土壤条件2.2 材料分析2.2.1 管道材料选用2.2.2 阀门、管件材料选用 2.2.3 施工辅助材料选用 2.3 施工工艺分析2.3.1 开挖与回填工艺2.3.2 管道安装工艺2.3.3 管道连接工艺2.3.4 管道保护工艺3. 施工方案3.1 施工方法选择3.1.1 开挖方法3.1.2 管道安装方法 3.1.3 管道连接方法 3.1.4 管道保护方法 3.2 施工工序安排3.2.1 开挖与回填工序 3.2.2 管道安装工序 3.2.3 管道连接工序3.2.4 管道保护工序4. 施工进度计划4.1 总体计划4.2 施工详细进度5. 施工管理5.1 施工组织管理5.2 施工现场管理5.2.1 施工现场布置 5.2.2 安全生产管理5.2.3 环境保护管理6. 质量控制6.1 施工质量控制计划 6.2 材料质量控制6.3 施工工艺质量控制6.4 施工工序质量控制7. 安全保障7.1 安全风险评估7.2 安全措施7.3 安全培训8. 管道试压8.1 试压计划8.2 试压方法8.3 试压试验结果9. 竣工交底与验收9.1 竣工报告9.2 施工质量验收9.3 安全技术交底9.4 管道竣工图纸10. 附件【附件】:1. 相关工程图纸2. 施工合同及附件3. 安全生产手册4. 监理意见书【法律名词及注释】:1. 授权法律文件:包括无损检测报告、焊接记录等2. 监理单位:指负责对施工工艺、质量、安全生产等进行监督的机构3. 安全生产法规:指相关安全生产法律法规和标准4. 施工质量验收:指对工程施工质量进行检验和确认的过程5. 竣工图纸:指记录工程实际施工情况的最终图纸。
工程排水管施工方案范本

工程排水管施工方案范本第一部分:项目概况1.1 项目名称:XXX工程排水管施工1.2 项目地点:具体地址1.3 项目内容:本项目为排水管的施工工程,包括管道安装、连接、测试等工作。
1.4 项目背景:工程排水管施工是为了解决工程场地排水问题,确保工程顺利进行。
第二部分:施工单位2.1 施工单位名称:XXX施工单位2.2 施工人员:具体人员名单及资质证书2.3 施工设备:列举出所需的具体施工设备第三部分:施工工艺3.1 施工方案:按照设计方案进行管道的安装、连接、测试等工作,确保施工质量。
3.2 施工流程:包括材料准备、施工现场布置、管道安装、连接、测试等具体流程。
3.3 施工要求:按照相关标准和规范执行工程排水管施工,确保工程质量。
第四部分:施工计划4.1 施工时间:具体施工时间安排4.2 施工进度:按照计划完成各项工程排水管施工任务4.3 施工安排:具体施工人员和设备的安排第五部分:安全措施5.1 安全防护:提前布置好安全警示标识,确保施工现场安全。
5.2 施工安全员:指定专人负责施工现场安全监督工作。
5.3 应急预案:制定施工现场应急预案,确保在突发状况下的应急处理。
第六部分:质量控制6.1 施工材料:按照设计要求选用合格的材料。
6.2 施工质量:保证施工质量符合相关标准和规范。
6.3 检验测试:对施工过程中的关键节点进行检验测试,确保施工质量。
第七部分:环境保护7.1 施工垃圾处理:合理处理施工垃圾,确保不对周边环境造成污染。
7.2 资源节约:合理使用施工资源,减少浪费。
7.3 环境保护措施:在施工过程中,采取措施保护周边环境。
第八部分:施工验收8.1 施工完成后,进行施工质量验收。
8.2 各项工程排水管施工项目验收合格后,方可进行下一步工作。
8.3 施工验收合格,交付使用。
第九部分:施工总结9.1 汇总各项工程排水管施工过程中的经验教训。
9.2 对施工过程中出现的问题进行总结分析。
9.3 提出下一步施工改进措施和建议。
管道工程施工技术方案
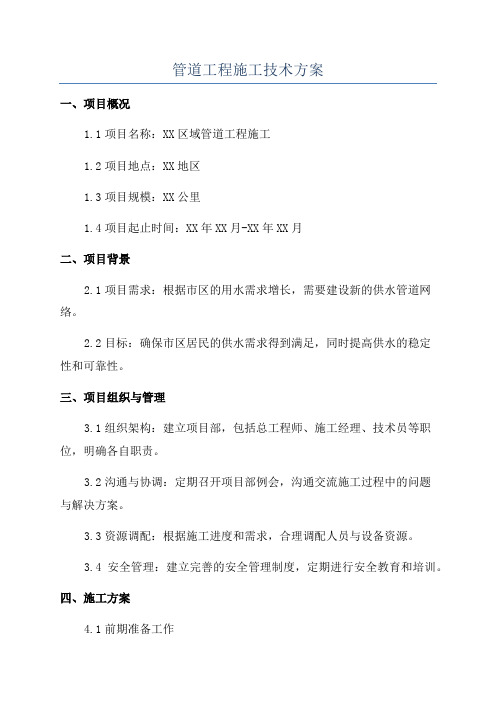
管道工程施工技术方案一、项目概况1.1项目名称:XX区域管道工程施工1.2项目地点:XX地区1.3项目规模:XX公里1.4项目起止时间:XX年XX月-XX年XX月二、项目背景2.1项目需求:根据市区的用水需求增长,需要建设新的供水管道网络。
2.2目标:确保市区居民的供水需求得到满足,同时提高供水的稳定性和可靠性。
三、项目组织与管理3.1组织架构:建立项目部,包括总工程师、施工经理、技术员等职位,明确各自职责。
3.2沟通与协调:定期召开项目部例会,沟通交流施工过程中的问题与解决方案。
3.3资源调配:根据施工进度和需求,合理调配人员与设备资源。
3.4安全管理:建立完善的安全管理制度,定期进行安全教育和培训。
四、施工方案4.1前期准备工作4.1.1地勘与测量:对工程所在地进行勘察和测量,确保施工的可行性。
4.1.2设计与方案论证:对管道工程的设计方案进行论证,确保符合需求。
4.1.3材料准备:制定材料购买计划,采购合格的管道材料和相关设备。
4.1.4土地征用:按照相关法律规定,办理土地征用手续。
4.2施工工艺4.2.1开挖与铺管:根据设计方案,采用适当的开挖方法进行土方开挖,然后进行管道的铺设与连接。
4.2.2焊接与安装:对管道进行焊接、安装与固定,确保管道的密封性和稳定性。
4.2.3集中供水池建设:根据设计方案,在合适的位置建设集中供水池,并与管道进行连接。
4.2.4施工设备操作:根据需要,配备适当的机械设备和工具,提高施工效率。
4.2.5环境保护措施:设立管道施工现场的临时围挡,采取相应的环境保护措施,减少对周围环境的影响。
4.3质量控制4.3.1材料质量:确保购买的管道材料符合国家标准和相关要求。
4.3.2施工工艺:严格按照设计方案和施工规范进行施工,避免违规操作。
4.3.3焊接质量:保证焊接工艺和人员的合格情况,确保焊缝的质量。
4.3.4检测与验收:在施工过程中进行检测和验收,确保工程的质量问题得到及时解决。
管道内工程施工方案模板
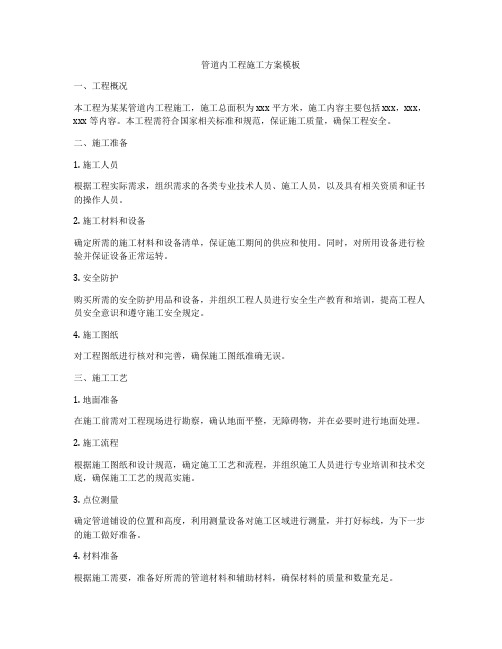
管道内工程施工方案模板一、工程概况本工程为某某管道内工程施工,施工总面积为xxx平方米,施工内容主要包括xxx,xxx,xxx等内容。
本工程需符合国家相关标准和规范,保证施工质量,确保工程安全。
二、施工准备1. 施工人员根据工程实际需求,组织需求的各类专业技术人员、施工人员,以及具有相关资质和证书的操作人员。
2. 施工材料和设备确定所需的施工材料和设备清单,保证施工期间的供应和使用。
同时,对所用设备进行检验并保证设备正常运转。
3. 安全防护购买所需的安全防护用品和设备,并组织工程人员进行安全生产教育和培训,提高工程人员安全意识和遵守施工安全规定。
4. 施工图纸对工程图纸进行核对和完善,确保施工图纸准确无误。
三、施工工艺1. 地面准备在施工前需对工程现场进行勘察,确认地面平整,无障碍物,并在必要时进行地面处理。
2. 施工流程根据施工图纸和设计规范,确定施工工艺和流程,并组织施工人员进行专业培训和技术交底,确保施工工艺的规范实施。
3. 点位测量确定管道铺设的位置和高度,利用测量设备对施工区域进行测量,并打好标线,为下一步的施工做好准备。
4. 材料准备根据施工需要,准备好所需的管道材料和辅助材料,确保材料的质量和数量充足。
根据设计要求和施工图纸,进行管道的铺设、连接和固定,保证管道的质量和稳定性。
同时,对接头进行检验,确保接头密封可靠。
6. 检测与验收在管道安装完成后,进行管道的压力测试和水质测试,确保管道的正常运行。
对管道的质量进行验收,做到合格交付。
四、施工安全与质量控制1. 安全措施施工过程中,加强作业现场管理,坚决按照相关安全标准和规定,严格执行安全操作规程。
2. 质量控制在施工过程中,加强对工程质量的控制,实行质量关键节点和质量检验制度,确保工程质量符合设计要求。
五、施工进度和验收1. 进度管理制定详细的施工计划,包括分阶段的工作计划和工期安排,严格按照计划要求推进工程施工,确保工程按时交付。
3管道施工技术方案

3管道施工技术方案一、项目背景和目标本管道施工技术方案针对XX工程项目,包括管道的设计、材料选择、施工工艺等内容,旨在确保管道施工过程的安全、高效和质量。
二、施工准备工作1.确定施工范围和管道走向,并画出详细的工程施工图纸。
2.根据设计要求,选择合适的材料,包括管道材料、焊接材料、密封材料等。
3.确定施工所需的人力、物资和设备,并制定详细的计划。
三、管道安装工艺1.基础处理:根据设计要求,对管道所需的基础进行处理,包括挖掘、平整和加固等工作。
2.管材切割:根据设计要求将管材进行切割,确保其长度和角度的准确性。
3.管道组装:采用焊接或螺纹连接的方式,将管材组装成预定的形状和长度,保证连接的牢固性和密封性。
4.管道安装:根据设计要求,将管道安装到预定的位置,并固定好。
5.管道测量和调试:在管道安装完成后,进行测量和调试,确保管道的准确性和流量的畅通。
四、施工安全措施1.施工现场应设置警示标志,并设置专人负责现场安全管理。
2.施工人员应佩戴安全防护装备,包括安全帽、安全鞋、防护眼镜等。
3.施工现场应设置专门的通风设备,确保气体的流通和防止有害气体积聚。
4.施工过程中,应严格按照相关安全操作规程进行作业,并定期组织安全培训。
五、质量控制措施1.管道材料应经过质量检验,符合相关标准和要求。
2.管材焊接应符合焊接工艺规范,确保焊缝的质量和强度。
3.管道安装应符合设计要求和施工规范,保证连接的紧密和牢固。
4.管道的防腐保温处理应符合设计要求,确保管道的使用寿命和外观质量。
六、环境保护措施1.施工现场应设立废弃物暂存区,并定期清理和处理废弃物。
2.施工过程中应采用环保材料和环保工艺,减少对环境的污染。
3.在施工过程中,应遵守相关环保法规和标准,确保施工对环境的影响最小化。
七、施工进度和质量控制1.制定详细的施工计划和进度表,并根据实际情况进行调整。
2.定期检查施工现场的安全状况和施工质量,及时发现和解决问题。
3.进行施工过程的质量检验,包括焊缝检测、管道尺寸测量等,确保施工质量符合要求。
- 1、下载文档前请自行甄别文档内容的完整性,平台不提供额外的编辑、内容补充、找答案等附加服务。
- 2、"仅部分预览"的文档,不可在线预览部分如存在完整性等问题,可反馈申请退款(可完整预览的文档不适用该条件!)。
- 3、如文档侵犯您的权益,请联系客服反馈,我们会尽快为您处理(人工客服工作时间:9:00-18:30)。
3 管道施工技术方案3.1 管材验收从防腐厂家领取材料时,应对管材的材料原质量和管材的防腐质量由供应、质检人员进行检查验收,不合格者不得运至施工现场。
验收、运输交接时应办理工序交接手续。
3.1.1 检查钢管的原材料质量证明书,合格证应符合《石油天然气工业输送钢管交货技术条件第一部分:A级钢管》(GB/T9711.1-1997)要求。
3.1.2 检查成品管的防腐质量应符合《钢质管道熔结环氧粉末外涂层技术标准》(SY/T0315-97)(1)在管端1m处应有标记,标明钢管的规格、材质、等级、生产厂名称、执行标准;外涂层的类型、等级、防腐管编号、检验员代号、涂装厂名称、生产日期、执行标准。
(2)成品管外表面无损伤。
3.1.3 冷、热弯管外观不得有裂纹、皱折,椭圆度不得大于2%,外防腐不得脱层等损伤,焊缝不得分布于内外侧。
3.2 测量、放线3.2.1 根据图纸及现场交桩情况,用全站仪依据沿线的水准点和坐标网,放出管道中心线及作业边界线,打出百米中间桩及拐点桩,并在施工作业面边界线上撒出白灰线。
3.2.2 根据业主和监理要求对拐点桩作出现场修改的,应重新测量。
3. 3 运输、吊装3.3.1 集散点的选择根据对管道沿线道路、桥梁、涵洞等地形地貌勘测情况,确定沿各集散点,选择在交通便利、靠近施工作业线的地段,集散点场地用机械或人工进行平整,摆好软土(袋)或道木。
3.3.2 管材的运输(防腐厂至集散点)(1)管材在防腐厂进行外防腐后运到各集散点。
装车使用专用吊装索具。
(2)管材装车不应超高、超宽。
每层之间铺垫胶皮。
封车用的绳索采用带胶皮外套的钢丝绳。
绳索与管材之间应垫上胶皮保护层。
(3)特别要保护好防腐绝缘层和管端,严禁摔、碰、撬等损伤绝缘层的操作。
3. 3. 3管材的运输(集散点至作业点)(1)管材从集散点运至各作业点,采用吊车、挖掘机、叉管机及人力进行布管。
(2)对于特殊(山坡、河流、水塘等)地段,采用大型吊车吊管、挖掘机吊管及人工抬运的办法进行布管。
(3)对于不便通行的地段,必要时修筑临时施工便道,便道应有一定的承载能力。
3. 4 布管3 .4. 1 布管前,应根据管道施工占地宽度采用机械和人工将占地范围内的杂草、树木石块等清除干净。
其沟、坎、陡坡等应予以平整,确保施工机具通行。
3 .4. 2 布管离沟边缘间距应大于0.5m,有条件的地段可用机械布管,采取灵活多变的方法,使布管工作顺利进行。
布管时相邻管口要错开一个管径,并成锯齿形。
3. 4 3管子应放在沙袋或软土包上,高度在0.4m左右,布管时应按图纸及现场测量放线要求布管,大开挖、穿越部位的管子布置在预制便于施工的一侧。
3. 4. 4布管前,应根据测量管口周长、直径、以便匹配。
3. 5 组对3.5.1 管道组对前,仔细检查管子是否有变形,变形超标及有其他严重缺陷的管子应更换,并做好标记,以免重复使用。
3.5.2 管道组对前,应将钢管内的脏物清理干净,管内不得有石头、泥土、棍棒、废铁等杂物,焊接的管段下班前应用临时盲板封堵,以防脏物进入管内。
3.5.3 管道的切割采用气割加工方法,气割后必须除去坡口内外表面的氧化皮,并进行打磨。
3.5.4 组对间隙为1.0-2.0mm,坡口角度为60±5°,钝边尺寸为1.0-1.6mm,对口错边量不大于1.6mm。
3.5.5 钢管组装前,应将管端20mm内的污油、铁锈、熔渣等清除干净。
钢管组装时直缝错开间距不得小于100mmm弧长。
3. 5. 6 组装时,应避免强力对口且应保护钢管绝缘层。
3.5. 7 管道组对使用外对口器,焊点应均匀,根部焊接达到周长的50%时,才能撤离外对口器。
3.5. 8 管道敷设变方向时,根据设计图纸及现场测量情况准确使用弹性敷设,冷弯弯头及热弯弯头。
3.5.9 管段采取沟上组对焊接,长距离组对有困难以及特殊地段,可采取沟下组对焊接。
3.6 焊接、检验3.6.1 焊前准备(1)按SY1052-92《油气管道焊接工艺评定》要求进行焊接工艺评定;(2)焊接前将焊接工艺评定报告及焊接操作规程提交监理工程师审核;(3)施焊的焊工必须按照规定进行考试,经监理工程师审查合格的持证焊工经上岗考试合格,方可进行上岗施焊。
(4)焊前应进行认真仔细的技术交底。
3.6.2 施焊工艺(1)管道焊接采用手工电弧下向焊工艺,焊条选用原则:打底热焊用AWS E6010 ¢ 3.2mm、填充盖面AWSE7010 ¢4.0mm。
(2)焊接施工执行《管道下向焊接工艺规程》SY/4071-93。
(3)管工组对完焊口时应及时写上管号及焊口号,焊工焊完焊口时应及时写上焊工号。
(4)若出现雨、雪天,风速大于8m/s,或空气湿度大于90%,应采取有效的防护措施。
(5)采用两人对称施焊,分根焊、热填充焊和盖面焊共计进行四遍施焊。
根焊完毕,立即对根焊表面进行打磨清理,填充焊后盖面焊按流水作业要求相继跟随。
每遍应连续焊完,每个焊口宜一次焊完。
环境温度在0℃以上可不预热,直接进行现场焊接。
0℃以下时,应进行100℃左右的预热;(6)焊接过程中,层与层间焊接接头应错开20—30mm,根焊与热焊的时间间隔不宜超过5min,其它层间间隔尽可能缩短,层间尤其是根焊后须进行认真清理;(7)施焊时不得在管子表面引弧或擦弧;(8)焊接完成后,应将焊缝及两侧的熔渣和飞溅及时清理干净。
焊口检验合格后,在接管下游离焊缝1000mm处,标上焊工号及焊缝号,并做焊接记录。
(9)每天下班前应将焊完的管端口做好临时封堵,以防污物或地下水进入管内。
3.6.3 检验(1)外观检验:焊缝表面不得有裂纹、气孔、未熔合等缺陷,咬边深度不得大于0.5mm,在任何300mm的连续焊长度中咬边长度不得大于50mm,焊缝宽度应比坡口宽2.5-3.5mm,余高为0-1.6mm,5点—7点处不得大于3mm,外表面不得低于母材。
焊后错边量不应大于0.15倍壁厚,局部不得大于1.5mm,因管子尺寸误差造成的任何较大错边都应均匀分布在管子整个圆周上,外观检验合格后,才能进行无损探伤。
(2)无损探伤:无损探伤按《石油天然气钢制管道对接焊缝射线照相及质量分级》(SY4056-93)和《石油天然气钢制管道对接焊缝超声波质量分级》(SY4065-93)中规定的II级检查执行。
大中型河流、公路、铁路穿越段、弯头与站内管道连接的焊缝及所有碰死口的焊缝要求100%X射线照相检验,其余焊缝要求进行100%起声波探伤,加15%X射线抽检。
3.6.4 焊缝返修(1)经外观检查不合格的焊缝,及时通知焊工本人进行修补;(2)经射线拍片不合格的焊缝应进行返修,同一部位的返修次数不得超过二次,经两次返修不合格的焊缝应将焊口割开重焊。
(3)返修工艺由焊接工程师制定,部位由无损检测人员确定,质检员指定焊工并监督返修。
3.7 管沟开挖1.开挖准备(1)管沟开挖前应向操作人员作好该沟断面,堆放位置,地下隐蔽工程分布情况及施工技术要求等交底工作。
并应指定专人配合。
(2)管沟开挖前,利用业主提供的地下障碍物清单,重新用超声波物探仪确认障碍物位置,并作出标识。
(3)管沟开挖前,应将控制桩移到堆土一侧的占地边界以内,靠边界线0.5m左右,堆土时不得将控制桩埋掉。
(4)开挖前,在放线定位的基础上进行现场踏勘,对地表影响施工的障碍物、建筑垃圾等采用机械加人工配合的方法进行清除,并运输至业主指定的场所。
并在布管侧修筑施工便道,施工便道应有一定的承载能力,与主线公路平缓接通。
●农田挖沟时熟土单独堆放,并靠近占地边缘,然后再将生土堆放在熟土里侧,对于地势平坦的地段,采用挖掘机开挖,人工修坡清底,沿沟底左侧纵向布置一条排水沟,根据开挖后的实际情况,布置排水泵。
对于有障碍物的地方先用人工挖沟,待情况名了后再改用挖掘机开挖。
●管沟开挖时,对易塌方、滑坡、过障碍物(浅水塘、电缆、小河流)地段采取打钢桩加固,钢桩间距1米,钢桩深入沟底1米,用竹排或钢管固定,并视情况加压土袋。
●开挖穿越小河时,采用双排木桩中间填筑粘土筑堤短流,开挖范围内打钢板桩护坡后再开挖,并采用合理的排水措施。
●庙江河管墩及固定墩的施工见施工详图后另行编制2.开挖管沟当中遇到地下构筑物及其它障碍设施时,应与其它主管单位协商制定安全技术措施,并派人到现场监督。
施工过程中,施工设备和临时工程不得影响任何公共设施,包括管道、排水沟、电缆、通道,也不得使任何地上地下的结构物失稳。
3.所有的沟槽的边坡一开始就要确保安全,以防地面沉陷,或影响附近的地面和构筑物,为安全起见,视情况加支撑。
4.在拐点及施工要求扩大处应加宽、加深管沟。
5.开挖时应特别注意安全,在大开挖、通道、陡坡等处加设围栏。
6.管沟挖完,经测量自检合格后,及时通知监理工程师验收,不符合要求时应及时修整,并作好竣工测量和记录,合格后办理交接。
7.施工场地周围的公用设施如排水管、水渠、架空供电线杆等应进行保护或修复。
3.8 管道下沟及回填1 管道下沟1.1管线的焊接、无损检测、补口完成后,应尽快下沟。
一个作业(机组)施工段,沟上放置管道的连续长度不宜超过1Okm。
1.2下沟前,应复查管沟深度,清除沟内塌方、石块、积水、冰雪等有损防腐层的异物。
石方或戈壁段管沟,应预先在沟底垫2OOmm厚细土,石方段细土的最大粒径不得超过lOmm,戈壁段细土的最大粒径不得超过20mm,对于山区石方段管沟宜用袋装土做垫层。
1.3管道下沟宜使用吊管机,严禁使用推土机或撬杠等非起重机具。
吊具宜使用尼龙吊带或橡胶辊轮吊篮,严禁直接使用钢丝绳。
起吊点距管道环焊缝距离不应小于2m。
起吊高度以1m为宜。
4.吊管机使用数量不宜少于3台。
吊点间距应符合表12.1.3的规定。
1.4管道下沟前,应使用电火花检漏仪检查管道防腐层,如有破损或针孔应及时修补,检测电压应符合设计或现行有关标准的规定。
1.5管道下沟时,应注意避免与沟壁挂碰,必要时应在沟壁突出位置垫上木板或草袋,以防止擦伤防腐层。
管道应放置到管沟中心位置,距沟中心线的偏差应小于250mm。
管子应与沟底妥帖结合,局部悬空应用细土填塞。
1.6管道下沟时,应由专人统一指挥作业。
下沟作业段的沟内不得有人,应采取切实有效的措施防止管道滚沟。
1.7 道下沟后应对管顶标高进行复测。
在竖向曲线段应对曲线的始点、中点和终点进行测量。
2.2 管沟回填2.1 一般地段管道下沟后应在lOd内回填。
回填前,如沟内积水无法完全排除,在完成回填时,应使管子不致浮离沟底。
山区易冲刷地段、高水位地段、人口稠密区及雨期施工等应立即回填。
2.2 作土地段的管沟应分层回填,应将表面耕作土置于最上层。
2.3 沟回填前宜将阴极保护测试引线焊好并引出地面,或预留出位置暂不回填。
2.4 道下沟后,石方段管沟细土应回填至管顶上方300mm。