汽柴油加制氢介绍.ppt
合集下载
制氢工艺简介PPT幻灯片课件

4
蒸气-烃类转化制氢法是由国外巴登苯胺 纯碱公司和法本公司于1913~1927年研究发 展起来的,目前国内制氢工艺应用发展较快, 至今全国共建近60多套制氢装置,目前国内 地方炼油为了增加效益,提高产品质量,争 先恐后建设制氢、加氢装置,这就更加促进制 氢工艺的应用及发展。
5
第二节 原料、产品性质及要求
3 氧化锌脱硫反应 H2S + ZnO → ZnS + H2O 4 脱氯反应:脱氯剂脱出HCI.
5 脱金属反应As Pb 吸附在催化剂上。
10
二、原料的脱硫与净化 原料净化的目的主要是脱除原料中的硫、氯,保
证转化催化剂的正常运行,其反应机理为,利用金 属氧化物在一定温度下与HCl、H2S反应生成金属 氯化物与金属硫化物,是原料中的氯、硫被固定下 来,脱除原料气。
随着炼油工艺的发展,特别是加氢工艺广泛的 应用,增大了对氢气的需求 ,同时促进了制氢工 艺的发展。现各种制氢工艺路线有干气制氢、电 解制氢、水煤气制氢、甲醇裂解制氢、轻油制氢、 重油制氢等。
制氢工艺技术多样化发展,各制氢工艺路线 不同,相应成本也不同。相比之下蒸汽-轻烃转化 制氢成本较其它制氢工艺要低得多。尤其是干气 制氢成本最低。
原料预加氢的ቤተ መጻሕፍቲ ባይዱ的就是在一定温度下使原料中的 烯烃加氢饱和及有机硫、氯的生成H2S、HCl以便 除去。其反应机理:
9
1 烯烃加氢饱和反应: 乙烯加氢:C2H4 + H2 → C2H6 +Q 热量 丙烯加氢:C3H6 + H2 → C3H8 +Q 热量
2 加氢脱硫反应 硫醇加氢:RSH + H2 → RH +H2S 硫醚加氢:R1SR2 + 3H2 → R1H+R2H+H2S 噻吩加氢:C4H4S + 4H2 → C4H10 + H2S
蒸气-烃类转化制氢法是由国外巴登苯胺 纯碱公司和法本公司于1913~1927年研究发 展起来的,目前国内制氢工艺应用发展较快, 至今全国共建近60多套制氢装置,目前国内 地方炼油为了增加效益,提高产品质量,争 先恐后建设制氢、加氢装置,这就更加促进制 氢工艺的应用及发展。
5
第二节 原料、产品性质及要求
3 氧化锌脱硫反应 H2S + ZnO → ZnS + H2O 4 脱氯反应:脱氯剂脱出HCI.
5 脱金属反应As Pb 吸附在催化剂上。
10
二、原料的脱硫与净化 原料净化的目的主要是脱除原料中的硫、氯,保
证转化催化剂的正常运行,其反应机理为,利用金 属氧化物在一定温度下与HCl、H2S反应生成金属 氯化物与金属硫化物,是原料中的氯、硫被固定下 来,脱除原料气。
随着炼油工艺的发展,特别是加氢工艺广泛的 应用,增大了对氢气的需求 ,同时促进了制氢工 艺的发展。现各种制氢工艺路线有干气制氢、电 解制氢、水煤气制氢、甲醇裂解制氢、轻油制氢、 重油制氢等。
制氢工艺技术多样化发展,各制氢工艺路线 不同,相应成本也不同。相比之下蒸汽-轻烃转化 制氢成本较其它制氢工艺要低得多。尤其是干气 制氢成本最低。
原料预加氢的ቤተ መጻሕፍቲ ባይዱ的就是在一定温度下使原料中的 烯烃加氢饱和及有机硫、氯的生成H2S、HCl以便 除去。其反应机理:
9
1 烯烃加氢饱和反应: 乙烯加氢:C2H4 + H2 → C2H6 +Q 热量 丙烯加氢:C3H6 + H2 → C3H8 +Q 热量
2 加氢脱硫反应 硫醇加氢:RSH + H2 → RH +H2S 硫醚加氢:R1SR2 + 3H2 → R1H+R2H+H2S 噻吩加氢:C4H4S + 4H2 → C4H10 + H2S
柴油加氢培训课件
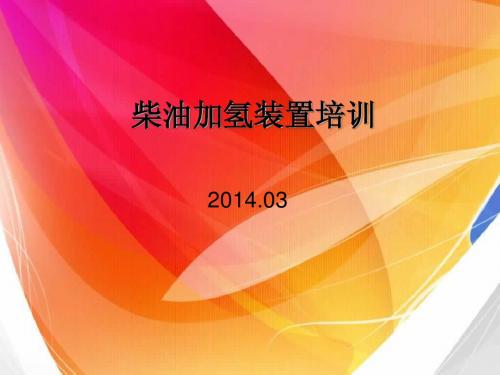
三、我厂柴油升级现状及升级方案
• 2、为满足柴油全部加氢和调整柴油产品结 构的要求,因此新建160万吨/年柴油加氢装 置。该装置主要加工催化柴油、焦化柴油 和I、Ⅱ套常减压的直馏柴油等,经过对原 料的加氢精制以满足平衡全厂柴油硫含量、 十六烷值和多环芳烃的需要。为了保障产 品的质量,因此全厂柴油加工路线设冬、 夏季工况,在冬季工况下通过侧线抽出部 分低凝柴油,以达到生产低凝柴油的目的。
120 160 160 2 100 180 4
改造 改造 新建 新建 新建 新建 新建
三、我厂柴油升级现状及升级方案
• 4、升级后的总加工流程及产品质量。
四、新建柴油加氢装置流程复述
• 1、新建一套160×104t/a柴油加氢精制装置。 采用中国石油石油化工研究院开发的PHF101P系列保护剂、PHF-101柴油加氢精制 催化剂,夏季加工直馏重柴油、催化柴油 和焦化柴油;冬季加工直馏重柴油、直馏 轻柴油、催化柴油和焦化柴油。主要生产 满足国V柴油质量要求的调和组分(冬季需 兼顾-35#低凝柴油调和组分生产),同时副 产部分石脑油和脱硫干气。
四、新建柴油加氢装置流程复述
• 3、具体工艺流程。
谢谢!
一、柴油质量升级
具体指标对比。
1、国三柴油标准 2、国四柴油标准 3、国五柴油标准 主要指标硫含量
国二 硫含量ppm 2000
国三 350
国四 50
国五 10
年份
2013.07
2015.01
2018.01
一、柴油质量升级
3、柴油质量升级难点(即柴油超深度脱硫的难点)是脱 除4,6-二甲基二苯并噻吩类有空间位阻效应影响的大分 子硫化物。 途径一:直接脱硫 途经二:先加氢再脱硫
柴油加氢工艺流程(精)ppt课件
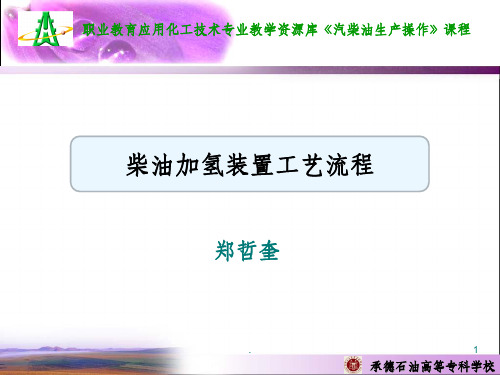
应。或者作为化工洁净原料。
分
馏
塔
反应油从低分罐来
原料泵
回流罐
瓦斯气 石脑油
柴油出装置
柴油加氢精制装置分馏系统工艺流程图
分馏塔底泵
.
6
职业教育应用化工技术专业教学资源库《汽柴油生产操作》课程
分离塔顶的气体产出量不应有
变化,如果其产量增高,说明在
反应器内发生的加氢裂化量增加,
需要调整反应温度、压力、剂油
.
2
职业教育应用化工技术专业教学资源库《汽柴油生产操作》课程
柴油加氢装置加氢精制反应器内发生的反应:
一、加氢脱硫反应: 三、加氢脱氧反应: 五、烯烃饱和反应:
二、加氢脱氮反应: 四、加氢脱金属反应:
但是与催化重整预加氢反应器不同的是,柴油加氢精制反应器内的 反应压力更高,约在8.6MPa左右。
这是因为精制反应器与后面的改质反应器是串联,改质反应是芳烃 开环的反应,需要较高的反应压力。
延迟焦化柴油 催化裂化柴油
装柴 置油
加 氢 改 质
燃料气 石脑油 加氢柴油
总厂燃料气管网 催化重整预分馏 油品调合罐区
加工原理:在柴油加氢精制改质装置,除了发生了加氢脱除杂质的反应,
还发生了改质反应,即使柴油中低十六烷值的组分在高压氢气和催化剂存在
的条件下转化成较高十六烷值的组分,进而提高整体柴油的十六烷值。
炉温的控制有何要求?
为什么是全回流?
组成有哪些?
.
17
职业教育应用化工技术专业教学资源库《汽柴油生产操作》课程
工艺操作参数与常减 压装置常压塔顶回流罐 相同么?
.
18
职业教育应用化工技术专业教学资源库《汽柴油生产操作》课程
加氢技术培训资料PPT汽油加氢技术ppt
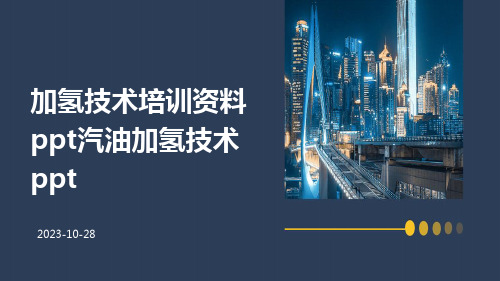
加氢技术培训资料 ppt汽油加氢技术 ppt
2023-10-28
目 录
• 加氢技术概述 • 汽油加氢技术简介 • 汽油加氢技术应用与案例 • 汽油加氢技术的未来发展与挑战 • 加氢技术的前沿动态与最新进展
01
加氢技术概述
加氢技术的定义与特点
定义
加氢技术是一种将劣质燃料油转化为高质量燃料油或化工原料的清洁能源技 术。通过向燃料油中加入氢气,使其经过加氢反应,实现燃料油的升级和转 化。
而提高汽油的辛烷值。
降低汽油烯烃含量
烯烃是汽油中的一种成分,可能 导致发动机磨损。通过加氢过程 ,可以降低汽油中烯烃的含量, 从而延长发动机寿命。
脱硫
加氢过程还可以脱除汽油中的硫化 物,减少硫对环境和发动机的影响 。
汽油加氢技术的优势与局限
优势
汽油加氢技术可以提高汽油的品质和性能,降低发动机磨损 和环境污染,同时提高燃料的利用率。
发展
目前,加氢技术已经成为一种成熟且广泛应用的能源转化技术。在国内外,许多炼油厂和化工厂都采用加氢技 术来处理劣质燃料油和化工原料。同时,随着技术的不断进步,加氢反应的条件逐渐变得温和,设备投资也得 到了降低,使得加氢技术在未来的发展前景更加广阔。
02
汽油加氢技术简介
汽油加氢技术的定义与流程
汽油加氢技术的定义
脱硫
加氢技术可用于降低汽油 中的硫含量,提高汽油的 环保性能。
脱氮
加氢技术可用于降低汽油 中的氮含量,提高汽油的 燃烧效率。
汽油加氢技术在不同类型汽油生产中的应用案例
普通汽油
通过加氢处理,调整生产 原料的组成,生产出符合 国家标准的普通汽油。
高级汽油
通过加氢处理和精细化调 整,生产出高级汽油,满 足高端市场需求。
2023-10-28
目 录
• 加氢技术概述 • 汽油加氢技术简介 • 汽油加氢技术应用与案例 • 汽油加氢技术的未来发展与挑战 • 加氢技术的前沿动态与最新进展
01
加氢技术概述
加氢技术的定义与特点
定义
加氢技术是一种将劣质燃料油转化为高质量燃料油或化工原料的清洁能源技 术。通过向燃料油中加入氢气,使其经过加氢反应,实现燃料油的升级和转 化。
而提高汽油的辛烷值。
降低汽油烯烃含量
烯烃是汽油中的一种成分,可能 导致发动机磨损。通过加氢过程 ,可以降低汽油中烯烃的含量, 从而延长发动机寿命。
脱硫
加氢过程还可以脱除汽油中的硫化 物,减少硫对环境和发动机的影响 。
汽油加氢技术的优势与局限
优势
汽油加氢技术可以提高汽油的品质和性能,降低发动机磨损 和环境污染,同时提高燃料的利用率。
发展
目前,加氢技术已经成为一种成熟且广泛应用的能源转化技术。在国内外,许多炼油厂和化工厂都采用加氢技 术来处理劣质燃料油和化工原料。同时,随着技术的不断进步,加氢反应的条件逐渐变得温和,设备投资也得 到了降低,使得加氢技术在未来的发展前景更加广阔。
02
汽油加氢技术简介
汽油加氢技术的定义与流程
汽油加氢技术的定义
脱硫
加氢技术可用于降低汽油 中的硫含量,提高汽油的 环保性能。
脱氮
加氢技术可用于降低汽油 中的氮含量,提高汽油的 燃烧效率。
汽油加氢技术在不同类型汽油生产中的应用案例
普通汽油
通过加氢处理,调整生产 原料的组成,生产出符合 国家标准的普通汽油。
高级汽油
通过加氢处理和精细化调 整,生产出高级汽油,满 足高端市场需求。
柴油加氢装置(汽柴油生产技术课件)
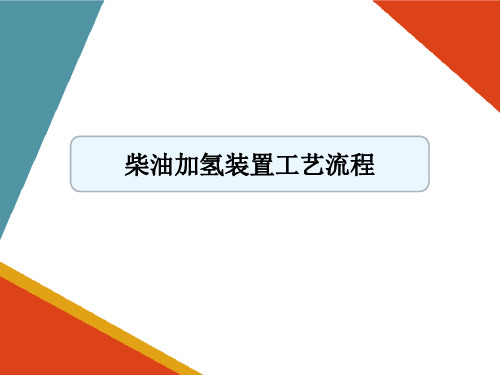
高分罐
LIC 排污
循环氢
LI 低分罐
图5—9 高分罐液位控制示意图
高分罐液位是油相液面高度。偏
高油相和气相分离效果将下降,偏低易形 成高压串低压导致分馏塔操作紊乱。
高分罐界位是水相与油相的界面
高度。偏高油带水,偏低水带油。
高分罐液位的影响因素:
1、高分罐与低分罐压差变化; 2、原料泵出口流量变化; 3、高分罐温度变化。
精制柴油十六烷值偏低,说明反应没有达到部分达到了第2步反应, 也即反应深度不够工艺要求。
1、反应温度偏低; 2、反应压力偏低;
3、催化剂活性偏低; 4、空速偏大。
1、塔顶压力偏 低; 2、塔顶温度偏 高;
精制油从低分罐来 原料泵
回流罐 粗汽油
分 馏 塔
粗汽油干点偏高?
柴油出装置
塔底的轻组分没有气化 上升到塔顶:
低分气
高
分
罐
低
分
分
馏
罐
塔
图5—10 低分罐压力控制示意图
低分罐的作用,一是分担些分馏塔
顶负荷,再是环节高压直接到低压而导致 分离塔的操作紊乱。
低分罐压力的影响因素:
1、高分罐压力变化; 2、分馏塔压力变化; 3、低分罐顶气体出口流量变化; 4、低分罐出口换热器的压降变化。
低分气
从高分罐来 低分罐
石脑油去催化重整装置
分
馏
塔
精制柴油溴价不合格的原
因?
柴油出装置
精制油从低分罐来 原料泵
回流罐
石脑油去催化重整装置
分馏Βιβλιοθήκη 塔精制柴油硫含量超标?
柴油出装置
循环氢压缩机
2、高分罐排污力度 不够工艺要求
新氢
汽油加氢装置原理简介ppt课件

平的情况下控制烯烃饱和率尽量低,使辛烷值损失在可允许范围内。加氢脱 硫反应器中主要发生如下反应。
汽油加氢装置
7 工艺流程说明 (1) 预加氢部分
来自装置外的催化裂化汽油首先经过催化汽油脱砷过滤器(SR9101/AB),滤除原料中大于10µm的固体颗粒后进入原料油聚结器(M9101) 后进入脱砷反应器(R-9101A/B)除去原料中的砷化物,然后进入原料油过 滤器(SR-9102A/B),再进入原料油缓冲罐(D-9102),经原料油进料泵 (P-9101A/B)升压至2.55 MPa,原料油缓冲罐(D-9102)设氢气气封设施, 使原料油不接触空气。来自膜分离装置的新氢经新氢分液罐(D-9101)分液, 然后经新氢压缩机(K-9101A/B)升压至2.93MPa。与原料油进料泵(P9101A/B)来的原料油,在流量比值控制下混合,混氢油经过预加氢进料/加 氢脱硫反应产物换热器(E-9102A/B)加热后进入预加氢反应器(R-9102)。
蒸汽至各服务点,至F-9201炉膛吹扫,至各伴热线返凝结水系统。
汽油加氢装置
柴油加氢装置
一、装置简介 1 设计能力 装置设计规模为30万吨/年,年开工时间为8400小时,运转周期按三年一大 修考虑。装置主要组成分为加氢反应单元、汽提脱硫单元、柴油精制单元 和公用工程四个部分。装置操作弹性为60%-110%。 2 装置特点 本装置由中国石油工程建设公司新疆设计分公司设计,采用中压加氢精制 工艺,催化剂选用中石油研究院开发的PHF-102催化剂,保护剂为PHF102P-2、PHF-102P-3,反应部分采用国内成熟的炉前混氢方案,高分部分 采用冷高分分离流程,分馏部分采用硫化氢汽提流程,催化剂的硫化采用 湿法硫化方案,催化剂的再生采用器外再生。
(5) 公用系统流程说明 ①净化风系统: 净化风自装置系统外来,送到仪表用风部位。送至各服务点,用于吹扫用。 ②水系统:
汽油加氢装置
7 工艺流程说明 (1) 预加氢部分
来自装置外的催化裂化汽油首先经过催化汽油脱砷过滤器(SR9101/AB),滤除原料中大于10µm的固体颗粒后进入原料油聚结器(M9101) 后进入脱砷反应器(R-9101A/B)除去原料中的砷化物,然后进入原料油过 滤器(SR-9102A/B),再进入原料油缓冲罐(D-9102),经原料油进料泵 (P-9101A/B)升压至2.55 MPa,原料油缓冲罐(D-9102)设氢气气封设施, 使原料油不接触空气。来自膜分离装置的新氢经新氢分液罐(D-9101)分液, 然后经新氢压缩机(K-9101A/B)升压至2.93MPa。与原料油进料泵(P9101A/B)来的原料油,在流量比值控制下混合,混氢油经过预加氢进料/加 氢脱硫反应产物换热器(E-9102A/B)加热后进入预加氢反应器(R-9102)。
蒸汽至各服务点,至F-9201炉膛吹扫,至各伴热线返凝结水系统。
汽油加氢装置
柴油加氢装置
一、装置简介 1 设计能力 装置设计规模为30万吨/年,年开工时间为8400小时,运转周期按三年一大 修考虑。装置主要组成分为加氢反应单元、汽提脱硫单元、柴油精制单元 和公用工程四个部分。装置操作弹性为60%-110%。 2 装置特点 本装置由中国石油工程建设公司新疆设计分公司设计,采用中压加氢精制 工艺,催化剂选用中石油研究院开发的PHF-102催化剂,保护剂为PHF102P-2、PHF-102P-3,反应部分采用国内成熟的炉前混氢方案,高分部分 采用冷高分分离流程,分馏部分采用硫化氢汽提流程,催化剂的硫化采用 湿法硫化方案,催化剂的再生采用器外再生。
(5) 公用系统流程说明 ①净化风系统: 净化风自装置系统外来,送到仪表用风部位。送至各服务点,用于吹扫用。 ②水系统:
加氢技术培训资料PPT汽油加氢技术ppt

汽油加氢技术的工艺流程
原料预处理
将原料油进行过滤、脱水和脱盐等 预处理,去除其中的杂质和有害物 质。
加氢反应
将预处理后的原料油加入加氢反应 器中,在高温高压和催化剂的作用 下进行加氢反应。
产品分离
反应后的产物经过冷却、分离和精 馏等工艺流程,得到精制汽油和其 他轻质油品。
催化剂再生
催化剂在使用过程中会逐渐失活, 需要定期进行再生处理,恢复其活 性。
ห้องสมุดไป่ตู้
生产效率和产品质量。
02
汽油加氢技术
汽油加氢技术的定义和原理
定义
汽油加氢技术是指在炼油过程中,将汽油通过加氢反应器,使用氢气作为催 化剂,使汽油中的杂质和有害物质在氢气的作用下转化为液态水和轻质油的 过程。
原理
汽油加氢技术的原理是利用氢气的还原性,将汽油中的氧化物、硫化物等杂 质还原成液态水和轻质油,同时将氮、氧等有害物质还原成氢气排出。
加氢技术原理
加氢技术主要基于氢气在高温高压下与油品中的硫、氮、氧 等杂质发生化学反应,生成水、氨、醇等物质,从而达到净 化油品的目的。
加氢技术在石油工业的应用
石油炼制领域
加氢技术在石油炼制领域广泛应用于常减压、催化裂化、重整等装置中,主要进行脱硫、 脱氮、脱氧等反应,提高产品质量和安定性。
燃料油领域
对排放的废气、废水、废渣进行治理,达到国家排放 标准;
加强环保意识教育,提高员工环保意识。
THANKS
谢谢您的观看
氢油比
氢油比是影响加氢反应的重要因素,比值过高或过低都不利 于反应的进行。
催化剂种类和剂量的影响
催化剂种类
催化剂种类对加氢反应的活性和选择性有很大影响,不同的催化剂具有不同 的活性中心和作用机理。
《加氢精制》课件

氢的用途
氢是工业和能源领域的重要原料,可 用于合成氨、甲醇、甲醛等化学品, 同时也是燃料电池的主要燃料。
加氢精制的定义与原理
定义
加氢精制是一种通过加氢反应提高油品质量和安定性的石油 加工过程。
原理
在加氢精制过程中,通过催化剂的作用,将油品中的硫、氮 、氧等杂质转化为相应的氢化物和氨,同时将烯烃和二烯烃 加氢饱和,以达到去除杂质和提高油品质量的目的。
社会效益的体现与影响
社会效益的来源
加氢精制技术能够提高油 品质量和环保标准,减少 对环境的污染和危害,从 而带来社会效益。
社会效益的体现
社会效益主要体现在改善 环境质量、保障人民健康 、促进社会和谐发展等方 面。
社会效益的影响
社会效益对企业的形象和 声誉有积极的影响,能够 提高企业的社会责任感和 公信力。
加氢精制在化学工业中广泛应用于生产农药、医药、染料等行业的中间体和原料。
在环保领域的应用
随着环保意识的提高,加氢精制 技术在环保领域的应用越来越广
泛。
通过加氢精制技术处理含硫、氮 等有害物质的废气和废水,能够 降低污染物排放,改善环境质量
。
加氢精制技术还可用于处理油品 燃烧产生的废气,减少空气污染
经济效益与社会效益的平衡业也需要关注社会效益,实现两者
的平衡与优化。
平衡与优化的方法
02
可以采用多种方法来实现平衡与优化,如制定合理的价格策略
、加强环保监管、推进技术进步等。
平衡与优化的效果
03
平衡与优化的效果主要体现在经济效益与社会效益的双赢,实
在石油工业中,加氢精制 主要用于处理原油,通过 去除硫、氮等杂质,提高 油品的安定性和环保性。
加氢精制技术能够生产出 符合标准的燃料油和润滑 油,满足市场需求。
氢是工业和能源领域的重要原料,可 用于合成氨、甲醇、甲醛等化学品, 同时也是燃料电池的主要燃料。
加氢精制的定义与原理
定义
加氢精制是一种通过加氢反应提高油品质量和安定性的石油 加工过程。
原理
在加氢精制过程中,通过催化剂的作用,将油品中的硫、氮 、氧等杂质转化为相应的氢化物和氨,同时将烯烃和二烯烃 加氢饱和,以达到去除杂质和提高油品质量的目的。
社会效益的体现与影响
社会效益的来源
加氢精制技术能够提高油 品质量和环保标准,减少 对环境的污染和危害,从 而带来社会效益。
社会效益的体现
社会效益主要体现在改善 环境质量、保障人民健康 、促进社会和谐发展等方 面。
社会效益的影响
社会效益对企业的形象和 声誉有积极的影响,能够 提高企业的社会责任感和 公信力。
加氢精制在化学工业中广泛应用于生产农药、医药、染料等行业的中间体和原料。
在环保领域的应用
随着环保意识的提高,加氢精制 技术在环保领域的应用越来越广
泛。
通过加氢精制技术处理含硫、氮 等有害物质的废气和废水,能够 降低污染物排放,改善环境质量
。
加氢精制技术还可用于处理油品 燃烧产生的废气,减少空气污染
经济效益与社会效益的平衡业也需要关注社会效益,实现两者
的平衡与优化。
平衡与优化的方法
02
可以采用多种方法来实现平衡与优化,如制定合理的价格策略
、加强环保监管、推进技术进步等。
平衡与优化的效果
03
平衡与优化的效果主要体现在经济效益与社会效益的双赢,实
在石油工业中,加氢精制 主要用于处理原油,通过 去除硫、氮等杂质,提高 油品的安定性和环保性。
加氢精制技术能够生产出 符合标准的燃料油和润滑 油,满足市场需求。
柴油加氢工艺流程课件(共 55张PPT)

9 仪表第四维护班
加氢反应系统
反应系统操作原则
加氢反应原料为催化、焦化柴油和焦化汽油
a 原料要求: 装置加工的焦化柴油和焦化汽油杂质和烯烃含量较高,原料先经过滤 质颗粒,为保证脱除效果降低过滤器的过滤负荷,要求罐区控制较高的柴 时间,汽油罐维持较低的汽油罐存,缩短停留时间,减加氢后的汽柴油,反应生成硫化氢以及加氢干气。 的硫、氮等杂质含量升高,则加氢反应条件应适当的提高,以确保精制产
原料油过滤装置内设置原料自动反冲洗过滤器,脱除大于25微米的固体颗粒。 原料油惰性气体保护原料油缓冲罐采用燃料气覆盖措施,以防止原料被氧化生成胶质。 高压空冷前注水在反应流出物进入空冷前注水,来溶解铵盐,避免铵盐结晶析出堵塞管路。 采用双壳程、螺纹锁紧环换热器,提高换热效率,减少换热面积,节省投资。 采用炉前混氢方案 ,提高换热效率和减缓结焦程度。 采用板焊结构热壁反应器,内设两个催化剂床层,中间设置了冷氢箱。 采用冷高分流程 分馏部分采用双塔蒸汽汽提流程。
1
仪表第四维护班
装置简介
设计能力
装置公称规模为120×104t/a,实际处理量为113.43×104t/a,投产于2003年7月,原设计能力 品有粗汽油、精制柴油,副产品为加氢干气。2004年6月进行掺炼焦化汽油改造,装置实际加工能 主要由反应和分馏两部分组成。
装置特点
a b c d e f g h
10
仪表第四维护班
加氢反应系统
加氢反应温度TRCA-8133A
控制范围:反应器入口温度TRCA-8133A:210-280℃ 控制目标:指令反应温度±2℃ 相关参数:加热炉出口温度点TRCA-8133B高高联锁温度为328℃。
控制方式:PIC-8102与TRCA-8133A串级控制,TRCA-8133A为主调,PIC-8102 压力来控制反应器入口温度TRCA-8133A。提高反应温度可促进加氢反应,有利于 高,会促进裂化反应,而使液收降低,而且催化剂积碳速度加快,缩短催化剂的 须足够高,使得进入反应器的物料100%的汽化,以保证物料在催化剂床层的均匀 效果的情况下,为得到最长的催化剂寿命,反应器入口温度应尽量的低。反应器 断下降而逐渐提高。
加氢反应系统
反应系统操作原则
加氢反应原料为催化、焦化柴油和焦化汽油
a 原料要求: 装置加工的焦化柴油和焦化汽油杂质和烯烃含量较高,原料先经过滤 质颗粒,为保证脱除效果降低过滤器的过滤负荷,要求罐区控制较高的柴 时间,汽油罐维持较低的汽油罐存,缩短停留时间,减加氢后的汽柴油,反应生成硫化氢以及加氢干气。 的硫、氮等杂质含量升高,则加氢反应条件应适当的提高,以确保精制产
原料油过滤装置内设置原料自动反冲洗过滤器,脱除大于25微米的固体颗粒。 原料油惰性气体保护原料油缓冲罐采用燃料气覆盖措施,以防止原料被氧化生成胶质。 高压空冷前注水在反应流出物进入空冷前注水,来溶解铵盐,避免铵盐结晶析出堵塞管路。 采用双壳程、螺纹锁紧环换热器,提高换热效率,减少换热面积,节省投资。 采用炉前混氢方案 ,提高换热效率和减缓结焦程度。 采用板焊结构热壁反应器,内设两个催化剂床层,中间设置了冷氢箱。 采用冷高分流程 分馏部分采用双塔蒸汽汽提流程。
1
仪表第四维护班
装置简介
设计能力
装置公称规模为120×104t/a,实际处理量为113.43×104t/a,投产于2003年7月,原设计能力 品有粗汽油、精制柴油,副产品为加氢干气。2004年6月进行掺炼焦化汽油改造,装置实际加工能 主要由反应和分馏两部分组成。
装置特点
a b c d e f g h
10
仪表第四维护班
加氢反应系统
加氢反应温度TRCA-8133A
控制范围:反应器入口温度TRCA-8133A:210-280℃ 控制目标:指令反应温度±2℃ 相关参数:加热炉出口温度点TRCA-8133B高高联锁温度为328℃。
控制方式:PIC-8102与TRCA-8133A串级控制,TRCA-8133A为主调,PIC-8102 压力来控制反应器入口温度TRCA-8133A。提高反应温度可促进加氢反应,有利于 高,会促进裂化反应,而使液收降低,而且催化剂积碳速度加快,缩短催化剂的 须足够高,使得进入反应器的物料100%的汽化,以保证物料在催化剂床层的均匀 效果的情况下,为得到最长的催化剂寿命,反应器入口温度应尽量的低。反应器 断下降而逐渐提高。
石油炼制技术之催化加氢介绍课件

能源储存:催化加氢技术在能源储存领域用于生产氢气,为燃料电池汽车等提供清洁能源
01
02
03
04
催化加氢技术的发展趋势
4
催化加氢技术的优化与改进
2019
提高催化剂活性和选择性
01
2020
优化反应条件,降低能耗和成本
02
2021
开发新型催化剂,提高催化效率
03
2022
研究催化加氢技术的新应用领域,拓展应用范围
04
催化加氢技术的环保与节能
03
减少废水排放:催化加氢技术可以减少废水排放,降低对环境的影响。
02
提高能源利用率:催化加氢技术可以提高能源利用率,降低能耗。
01
减少废气排放:催化加氢技术可以降低废气排放,减少环境污染。
04
降低生产成本:催化加氢技术可以提高生产效率,降低生产成本。
催化加氢技术的未来前景
催化加氢技术具有反应条件温和、选择性高、能耗低等优点,是一种绿色环保的工艺技术。
催化加氢技术在石油炼制中主要用于生产高质量的汽油、柴油、航空煤油等燃料,以及润滑油、石蜡等化工产品。
催化加氢技术的应用领域
石油炼制:提高油品质量,降低硫含量
化学工业:合成有机化合物,提高产品纯度
环境保护:处理工业废水,降低污染物排放
降低环境污染:催化加氢技术可以降低油品中的硫、氮、氧等杂质,减少环境污染。
提高炼油厂的竞争力:催化加氢技术可以提高炼油厂的技术水平和产品质量,提高炼油厂的竞争力。
催化加氢技术在化工生产中的应用
01
石油炼制:提高油品质量,降低硫含量
02
化学合成:生产精细化学品,如医药、农药、染料等
03
环境保护:减少污染物排放,提高废气、废水处理效果
01
02
03
04
催化加氢技术的发展趋势
4
催化加氢技术的优化与改进
2019
提高催化剂活性和选择性
01
2020
优化反应条件,降低能耗和成本
02
2021
开发新型催化剂,提高催化效率
03
2022
研究催化加氢技术的新应用领域,拓展应用范围
04
催化加氢技术的环保与节能
03
减少废水排放:催化加氢技术可以减少废水排放,降低对环境的影响。
02
提高能源利用率:催化加氢技术可以提高能源利用率,降低能耗。
01
减少废气排放:催化加氢技术可以降低废气排放,减少环境污染。
04
降低生产成本:催化加氢技术可以提高生产效率,降低生产成本。
催化加氢技术的未来前景
催化加氢技术具有反应条件温和、选择性高、能耗低等优点,是一种绿色环保的工艺技术。
催化加氢技术在石油炼制中主要用于生产高质量的汽油、柴油、航空煤油等燃料,以及润滑油、石蜡等化工产品。
催化加氢技术的应用领域
石油炼制:提高油品质量,降低硫含量
化学工业:合成有机化合物,提高产品纯度
环境保护:处理工业废水,降低污染物排放
降低环境污染:催化加氢技术可以降低油品中的硫、氮、氧等杂质,减少环境污染。
提高炼油厂的竞争力:催化加氢技术可以提高炼油厂的技术水平和产品质量,提高炼油厂的竞争力。
催化加氢技术在化工生产中的应用
01
石油炼制:提高油品质量,降低硫含量
02
化学合成:生产精细化学品,如医药、农药、染料等
03
环境保护:减少污染物排放,提高废气、废水处理效果
汽油加氢流程ppt课件

汽油加氢流程-二段反应单元
1、脱硫化氢汽提塔(C-3601)的目的在于通过降低在二段反应段内的H2S气体分压,去除部分H2S。 2、来自一段冷高分(D-3201)的一段反应产物首先通过一段高分油泵(P-3203 A/B)被送至H2S汽提塔(C-3601),采用二段反应产物的热量E-3603进行预热。C-3601塔顶物料在二段反应空冷(A-3601)中冷凝后进入二段冷高分(D-3602)。 3、脱硫化氢汽提塔底产物采用二段进料泵(P-3601 A/B)输送,与分馏塔塔底重汽油泵(P-3103 A/B)从分馏塔来(一段反应中未处理的)重汽油的混合,这些过量物料通过工段送出。
汽油加氢流程-全馏分加氢(SHU)
1、由装置外来的催化汽油首先被输送至反冲洗过滤器(FI-3101 A/B),以去除大于10微米的固体杂质,随后进入原料缓冲罐(D-3101)。由SHU反应器进料泵(P-3101 A/B)送至SHU反应段。 2、来自制氢装置的氢气(纯度至少达到99.50%体积含量),由新氢增压机K3001送至SHU反应段,,氢气量根据汽油进料量控制。 3、SHU反应进料与氢气混合,通过E-3001、E-3205、 E3002AB换热,最后经进料预热器(E-3003)进一步加热至要求的反应器进口温度。
ቤተ መጻሕፍቲ ባይዱ
汽油加氢流程-分馏单元
1、SHU稳定塔(C-3001)的目的是在分馏塔(C-3101)上游除去SHU反应剩余的氢气和原料中C4,被送至焦化装置(正常操作)或低瓦(非正常操作)。SHU稳定塔的塔底产物流至分馏塔(C-3101)。 2、分馏塔(C-3101)的目的在于分馏经SHU稳定塔(C-3001)稳定处理的SHU反应产物,得到轻汽油(LCN)和重汽油(HCN)。通过调节LCN/HCN 的切割比例生成低硫含量的LCN,同时回收大部分烯烃。 3、分馏塔的底部产物被分为两部分:第一部分:最大设计处理量去一段反应部分,经进料泵(P-3201 A/B)实现。第二部分:过量产物直接去二段反应,通过重汽油泵(P-3103 A/B)实现。
《柴油加氢培训包》课件——3柴油加氢催化剂

催化加氢催化剂
不同的非贵金属组分搭配产生的反应活性
反应活性
在H2S存在下
加氢脱氮活性 Ni- Mo-Co>Co-Mo>Co-W
无H2S存在下
加氢脱硫活性 Co-Mo>Ni- Mo>Ni-W>Co-W
加氢脱氧活性 Ni-Mo>Co-Mo>Ni-W>Co-W 芳烃饱和活性 Ni-W- Ni-Mo>Co-Mo>Co-W Ni-W- Ni-Mo>Co-Mo>Co-W
催化加氢催化剂
3.载体 载体具有高的表面积,可高度分散活性的金 属;具有理想的孔结构(孔体积和孔分布),有利 于反应分子的扩散;为容纳积炭提供空间,载体能 改善催化剂的导热性、防止活性组分因局部过热而 烧结失活;作为催化剂的骨架,提高催化剂的稳定 性和机械强度,并使催化剂具有一定的形状和大 小,以适应工业过程中流体力学的需求。
催化加氢催化剂
2.裂化组分 加氢裂化催化剂中的裂化组分就是载体,它为 催化剂提供酸性中心,提供合适的孔结构和增加有 效表面积,并且与活性金属组分形成新的化合物, 改善催化剂性质。 这些载体主要有:活性氧化铝(即γ-AI2O3)、 无定型硅酸铝 、沸石。
催化加氢催化剂
3.助剂 (1)结构性助催化剂
异构化活性 Ni-W>Ni-Mo>Co-Mo>Co-W Ni-W>Ni-Mo>Co-Mo>Co-W 加氢裂化活性 Ni-Mo>Ni-W>Co-Mo>Co-W Ni-Mo>Ni-W>Co-Mo>Co-W
催化加氢催化剂
贵金属组分反应活性与非贵金属组分反应活性的对比
反应活性 芳烃饱和性
无H2S存在下 Pt>Pd>Ni-W- Ni-Mo>Co-Mo>Co-W
催化加氢催化剂
(三)润滑油加氢催化剂 用以代替润滑油的溶剂精制和白土精制。 催化剂是催化加氢的技术核心。加氢装置的投
加氢工艺安全ppt课件

(1)将加氢反应釜内温度、压力与釜内搅拌
电流、氢气流量、加氢反应釜夹套冷却水进 水阀形成联锁关系,设立紧急停车系统。 (2)加入急冷氮气或氢气的系统。当加氢反应
釜内温度或压力超标或搅拌系统发生故 障时自动停止加氢,泄压,并进入紧急状态。 (3)安全泄放系统。
.
加氢设备
一、加氢反应器
加氢反应器一般可分为三种:固定床反应器、 滴流床反应器、其他反应器。下面就这三种反应 器进行简要的介绍。
部或外部)设有循环泵,使催化剂床层膨胀并维持处于
沸腾状态而完成加氢反应过程。此外在反应器上部还
需有能将汽、液、同三相进行分离的部件,所以反应
器内部结构比较复杂。
.
2、氢气压缩机
在加氢装置中主要有两种压缩机:一种是
将新鲜氢气加压输送到反应器系统中去,用以补
充反应所耗之氢气,这种压缩机称之为补充氢压
缩机,由于这种压缩机的进出口压差比较大,流
鼓泡床反应器因有很高的液一气体积比,所以单 位反应器体积的气一液接触比其他类型反应器的 大。由于气泡运动导致液体充分混合,促使整个 反应器内的温度较为均匀,这一点对温度敏感的 反应系统控制收率是合适的
.
2.滴流床反应器
在滴流床反应器中,气体和液体反应物通过分配 器向处于下部的静止固体催化剂均匀喷洒,并在 流经催化剂的过程中发生化学反应,生成所需的 目的产品。滴流床反应器结构简单,造价低,在 石油加氢装置上大量采用,在滴流床反应器中, 流体流向是以气、液两相并流向下运动的。滴流 床反应一般被看作为绝热、活塞流反应过程。转 化率随床层下移而增加,其温度也逐渐升高(放热 反应)或下降(吸热反应)。
(2)加氢为强烈的放热反应,氢气在高温高 压下与钢材接触,钢材内的碳分子易与氢气发 生反应生成碳氢化合物,使钢制设备强度降低, 发生氢脆;
电流、氢气流量、加氢反应釜夹套冷却水进 水阀形成联锁关系,设立紧急停车系统。 (2)加入急冷氮气或氢气的系统。当加氢反应
釜内温度或压力超标或搅拌系统发生故 障时自动停止加氢,泄压,并进入紧急状态。 (3)安全泄放系统。
.
加氢设备
一、加氢反应器
加氢反应器一般可分为三种:固定床反应器、 滴流床反应器、其他反应器。下面就这三种反应 器进行简要的介绍。
部或外部)设有循环泵,使催化剂床层膨胀并维持处于
沸腾状态而完成加氢反应过程。此外在反应器上部还
需有能将汽、液、同三相进行分离的部件,所以反应
器内部结构比较复杂。
.
2、氢气压缩机
在加氢装置中主要有两种压缩机:一种是
将新鲜氢气加压输送到反应器系统中去,用以补
充反应所耗之氢气,这种压缩机称之为补充氢压
缩机,由于这种压缩机的进出口压差比较大,流
鼓泡床反应器因有很高的液一气体积比,所以单 位反应器体积的气一液接触比其他类型反应器的 大。由于气泡运动导致液体充分混合,促使整个 反应器内的温度较为均匀,这一点对温度敏感的 反应系统控制收率是合适的
.
2.滴流床反应器
在滴流床反应器中,气体和液体反应物通过分配 器向处于下部的静止固体催化剂均匀喷洒,并在 流经催化剂的过程中发生化学反应,生成所需的 目的产品。滴流床反应器结构简单,造价低,在 石油加氢装置上大量采用,在滴流床反应器中, 流体流向是以气、液两相并流向下运动的。滴流 床反应一般被看作为绝热、活塞流反应过程。转 化率随床层下移而增加,其温度也逐渐升高(放热 反应)或下降(吸热反应)。
(2)加氢为强烈的放热反应,氢气在高温高 压下与钢材接触,钢材内的碳分子易与氢气发 生反应生成碳氢化合物,使钢制设备强度降低, 发生氢脆;
- 1、下载文档前请自行甄别文档内容的完整性,平台不提供额外的编辑、内容补充、找答案等附加服务。
- 2、"仅部分预览"的文档,不可在线预览部分如存在完整性等问题,可反馈申请退款(可完整预览的文档不适用该条件!)。
- 3、如文档侵犯您的权益,请联系客服反馈,我们会尽快为您处理(人工客服工作时间:9:00-18:30)。
2) 产品氢气压力
≥2.4 MPa.G
3) 产品氢温度
≤40 ℃
4) PSA部分解吸气排气压力
≥0.03 MPa
5) PSA部分氢气回收率(设计值) ≥83 %
3、30万吨/年催化汽油加氢装置 该装置设计点为28.80万吨/年催化汽油,最大加工量为36万吨/年,最小加工量为20
万吨/年。装置主要原料为催化汽油,其主要性质为 :
产品设计目标为: 1) 加氢后汽油产品硫含量<150PPm(主要由专利商保证)。 2) 加氢处理RON损失≯1.5个单位(主要由专利商保证)。 3) 重汽油加氢单元C5+以上液体收率>99.6 m %。 三套装置与一期项目装置共用一套公用工程,并在此基础上新增2台1000m3原料调合罐, 以保证装置进料的平稳性;新上10000m3气柜一台,以缓解火炬系统的压力,并能达到合 理利用装置废气的目的。
该装置设计点为38.56万吨/年,其中直馏柴油、催化柴油、直馏汽油的比例分别为 57.05%、35.17%、7.78%,最大加工量为46万吨/年,最小加工量为26万吨/年。装置原 料主要性质为:
装置产品设计目标为:
1) 精制柴油硫含量: 2) 精制汽油(石脑油)干点: 3) 精制柴油闪点:
≤350ppm ≤200℃ ≥55℃
2 、生产流程简述 1) 生产流程简述 ①反应部分
自罐区来的原料油,按预期的原料比例,首先进入原料调合罐进行调和,然
后在原料油缓冲罐(V3001)液面和流量控制下混合,经原料油脱水器 (SW3001)脱水(保证原料水含量低于350ppm),再通过原料油过滤器(FI3001) 滤去原料中大于25微米的颗粒,然后进入原料油缓冲罐(V3001)。原料油缓冲 罐采用燃料气进行保护。来自原料油缓冲罐(V3001)的原料油经加氢进料泵 (P3001A,B)增压至9.2MPa(G),在流量控制下,经反应流出物/原料油换热器 (E3003A,B)换热后,与混合氢混合进入反应流出物/反应进料换热器(E3001A、B、 C),然后经反应进料加热炉(F3001)加热至反应所需温度,进入加氢精制反应 器(R3001)。该反应器设置三个催化剂床层,床层间设有注急冷氢设施。来自 加氢精制反应器(R3001)的反应流出物,经反应流出物/反应进料换热器 (E3001A、B)、反应流出物/低分油换热器(E3002)、反应流出物/反应进料 换热器(E3001C)、反应流出物/原料油换热器(E3003A、B)依次与反应进料、 低分油、原料油换热,然后经反应流出物空冷器(A3001)冷却至50℃,最后经 反应流出物水冷器(E3011)冷却至45℃进入高压分离器(V3002)。为了防止 反应流出物中的铵盐在低温部位析出,通过注水泵(P3002A、B)将除盐水注至 反应流出物空冷器(A3001)上游侧的管道中。
二、装置平面布置
三套装置的平面布置综合考虑了全厂现有装置和空地,进行了合理布 置,具体位置见全厂平面布置图。装置位于10t/h酸性水汽提装置以东, 20万吨/年气分、4万吨/年MTBE装置以北(管廊以北),东临厂区中心路, 占地面积12248.5m3。新增2台1000m3原料调合罐及10000m3气柜位于 20万吨/年气分装置以北,管廊以南。
2、8000nm3/h催化干气制氢装置 该装置设计点为8000nm3/h,操作弹性为55~115%。原料为脱硫后的催化干气,备用
原料为丙烷。原料主要组成为:
产品设计目标为: 1) 产品氢纯度:
>99.9mol %
产品氢中CO+CO2: 产品氢中N2: 产品氢中CH4:
≤20 PPm ≤0.08 mol % ≤0.02 mol %
三、工艺流程叙述
(一)、40万吨/年汽柴油加氢精制装置工艺流程 (二)、8000nm3/h催化干气制氢装置工艺流程 (三)、30万吨/年催化汽油加氢精制装置工艺流程
பைடு நூலகம்
(一)、40万吨/年汽柴油加氢装置
1 、工艺流程特点 反应部分采用冷分流程;分馏部分采用柴油分馏塔加汽油稳定塔流程。 1)加氢精制反应器催化剂床层分三层设置。 2)用冷氢控制第二、三催化剂床层入口温度,提高反应器的操作灵活性,延长催化 剂使用周期。 3)采用炉前混氢方案,提高换热效率,减缓加热炉炉管结焦速度。 4)采用工程技术成熟的新型双壳程换热器,提高传热效率,降低投资。 5)原料油缓冲罐采用分馏塔顶气保护措施,避免原料油与空气接触。 6)采用三相(油、气、水)分离的立式高压分离器。 7)在反应流出物空冷器上游侧设置除盐水注入点,以防止低温部位硫化氢铵盐份析 出和沉积堵塞反应流出物空冷器和水冷器;在反应流出物/原料油换热器上游侧设置 除盐水注入点(间断注水),以防止氯化铵盐份析出,沉积堵塞反应流出物/原料油 换热器。 8)分馏塔设置重沸炉,使分馏塔具备精馏段和提馏段,实现汽油与柴油的清晰分割, 柴油收率高,与蒸汽汽提操作方式相比,可避免柴油雾浊问题,并因减少水存在量, 大大减弱了分馏塔顶系统和稳定塔顶系统有液态水存在位置的湿硫化氢腐蚀,有利于 保证分馏部分的“安、稳、长、满、优”操作;另一方面可确保稳定塔重沸器的热源 温位不低于240℃,即确保供热的可靠性从而确保稳定塔脱硫化氢操作的可靠性。
9)分馏塔塔顶设注缓蚀剂设施,以减轻塔顶流出物中硫化氢对分馏塔顶系 统的腐蚀。 10)粗汽油进入稳定塔,脱除硫化氢和戊烷以下轻组分,塔底得到脱除硫化 氢的稳定汽油,塔顶设注缓蚀剂设施,以减轻塔顶流出物中硫化氢对稳定塔 顶系统的腐蚀。 11)柴油产品先作稳定塔重沸器热源,然后与低分油换热,充分回收其热量。 12)新氢压缩机和循环氢压缩机均采用电动往复式,各设一台备机。 13)催化剂预硫化采用液相硫化方法,补硫设施与催化剂预硫化系统共用, 以保证催化剂所必需的硫化氢浓度(或分压)的反应条件,催化剂再生采用 器外再生方式。 14)设原料油脱水器,保证进入反应器原料含水低于350ppm,延长催化剂 寿命。 15)设原料油阻垢剂设施,延长装置运行周期。 16)设原料油自动反冲洗过滤器,过滤原料油中大于25 微米的颗粒,延缓 催化剂床层压降上升速度,保证装置运行周期。
加氢、制氢技改项目培训
一、装置概况
本项目包括3套装置,分别为40万吨/年汽柴油混合加氢装置、8000nm3/h催化干气制 氢装置和30万吨/年催化汽油加氢装置,其中40万吨/年汽柴油加氢装置和8000nm3/h催化 干气制氢装置联合布置。三套装置的设计寿命均为15年,年开工8000小时。 1、40万吨/年汽柴油混合加氢装置