精品表面加工技术
精品板式家具加工工艺流程资料及作业标准

板式家具加工工艺流程资料及作业标准机制部分:1.开料设备:精密度裁板机、推台锯、排锯加工标准:1.1长度、对角线公差为小于+1mm,宽度公差为小于+0.5mm;1.2板料无空心、气泡、松散、发霉、虫蛀以及破烂等现象;1.3板面平整度应≤0.2mm,三聚氢胺板开料后,表面应无刮花、碰伤等现象;1.4开料后部件切面应垂直,不允许有明显的崩缺(0.5mm内)、锯痕等现象;附表(电子锯)8、钻孔设备:六排钻、三排钻、单排钻、台钻工具:卷尺、游标卡尺检验方法:工具测量、目视加工标准:◎孔径、孔位、孔深符合图纸的质量要求:孔径公差为+0.5mm,孔位公差为小于+0.5mm,孔深公差0.5mm;◎部件表面无划花(程度在10mm内)、刮(碰)伤;◎孔位无钻穿、钻爆、孔边无崩缺;◎必须分清部件的前后与正反,以及木纹纹理方向,不得搞错方向。
◎经加工的零部件表面无木屑、压痕、刮花、划伤和碰崩现象。
◎坐标定位尺寸和孔深与要求的最大偏差≤0.5mm。
◎钻孔的孔边无崩缺、发黑及毛刺等。
注意事项:◎加工过程中,必须对面板、侧板、抽面板及散装件进行选面和分清正反面,同时注意部件的左右数量是否配套,并分类摆放整齐;木皮件板件间要用垫条间隔。
◎每加工20-30个部件应检查一次,避免因挡位松动或钻头跳出而影响孔位精度。
◎每加工一种部件,必须进行首检(由班长进行确认)。
9、封边分为:机封、手工封设备:直封机、曲封机加工标准:◎封边带的型号、颜色符合要求,相邻封边带无色差、实木封边带比板材高出0.5mm◎部件表面无明显划花,刮(碰)伤、压痕和胶痕等缺陷,且要保持干净,不许有多余的封边条屑和余胶。
◎封边后边部要严密、平整、胶合牢固、无脱胶、溢胶、漏封、叠封和跑边现象。
◎接口部位要求平整、密合,不能在显眼位置;◎修边要求整齐、平顺、不得有撕裂等现象。
注意事项:◎部件长度小于1000mm,由一人送料,一人接料;部件大于1000mm,由两人送料,两人接料;◎封边带厚度尺寸范围为6-68,直封机为50mm以下,曲封机为68mm以下;◎每加工一种部件,必须进行首检(由班长进行确认);◎异型部件封边前,先用180#砂纸磨去毛刺,封边时要注意用力均匀;◎接料员在堆放部件前,应先用鸡毛掸子将灰尘扫去。
表面处理QPQ
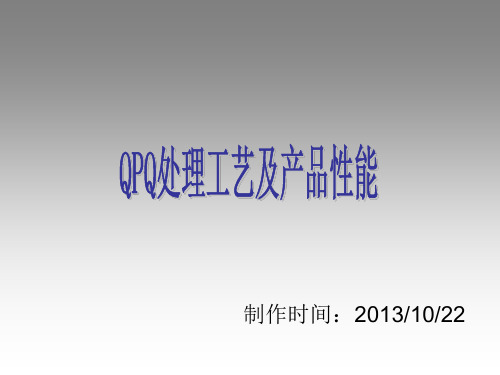
磨损值 相对磨 /mg 损比
1 45 QPQ处理 650HV 0.57 1
2 45 镀硬铬
813HV 45.7 -
3 20 渗碳淬火高 63.5 5.5
HRC
4 45 高频感应淬火 60.7 9.2
HRC
5 45 常规淬火 59.8 9.3
HRC
9.6 16.2 16.3
QPQ技术特点
• 2、良好的耐腐蚀性
20131022精品文档qpq处理的完整工艺曲线精品文档qpq技术的生产设备精品文档qpq处理操作程序1清洗剂脱脂2清水漂洗3预热4氮化5氧化6冷水洗去盐7热水清洗8干燥浸油123445678精品文档qpq技术的应用精品文档qpq技术特点?1良好的耐磨性序号材料处理方法硬度磨损值mg相对磨损比145qpq处理650hv0571245镀硬铬813hv457320渗碳淬火高635hrc5596445高频感应淬火607hrc92162545常规淬火598hrc93163精品文档qpq技术特点?2良好的耐腐蚀性002244668810121420um镀铬20um镀猛盐浴氮化氧化氮化氧化氮化抛光qpq几种方法的盐雾耐蚀实验比较注
2. 对第II组样品进行退火处理。当炉内加热温度 为730℃,开始保温,保温1小时后随炉缓慢冷 却(冷却速度20-40℃/h)至600℃左右,再取出 在空气中冷却。
3. 对第III组样品进行退火处理。当炉内加热温度为 760℃,开始保温,保温1小时后随炉缓慢冷却 (冷却速度20-40℃/h)至600℃左右,再取出在 空气中冷却。
QPQ处理渗层的形貌
• 1)氧化膜 • 2)化合物层 • 3)扩散层 • 4)疏松层
14
12
10
8
6
4
2
木材表面处理
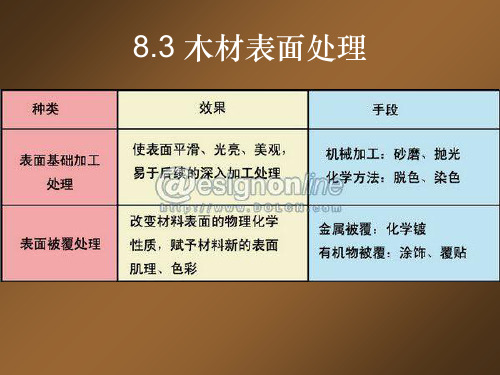
b
38
休闲椅 EASY CHAIR
1971 设计师/Designer POUL KJAERHOLM 材料:枫木,皮
b
39
方椅 SIDE CHAIR
1976 设计师/Designer POUL KJAERHOLM
材料:枫木
b
40
国王椅 KING‘S CHAIR
1968 Designer RUD THYGESEN JOHNNY SQRENSEN 材料:橡木,藤条
常用的覆贴材料: PVC膜、人造革、木纹纸、薄木等
c.化学镀
定义:
化学镀是指在没有外加电流的条件下, 利用处于同一溶液中的金属盐和还原剂可 在具有催化活性的基体表面上进行自催化 氧化还原反应的原理,在基体表面形成金 属或合金镀层的一种表面处理技术,亦称 为不通电镀或自催化镀。木材主要是镀铜 或金。
8.3 木材表面处理
1.表面基础加工处理
a.砂磨
定义:用木砂纸在木材表面进行顺木纹方
向的来回研磨的工艺。
效果:去除在木加工过程中由于锯、削、
刨时将木纤维切割断裂而残留在木材表面 上的木刺,使木材表面更平滑。
手段:机械砂磨(利用机器进行抛光、擦
亮)、手工砂磨(利用砂纸)。
• b.脱色
定义:
用具有氧化-还原作用的化学药剂对木材 进行漂白处理。
效果:
电磁屏蔽性能,装饰性,增加木制品
的附加值。
b
19
8.4 木材在设计中的应用 8.4.1设计木材的选用
8.4.2木材的感觉特性
视感:木纹、色彩 触感:冷暖感、干湿感
b
27
8.4.3 木材设 计实例
b
28
“贝壳”浴缸
smt表面组装技术-SMT、DIP生产流程介绍 精品

氮气回流焊
在回流焊工艺中使用惰性气体(通常是氮气)已经有一段时间了,但对于成本效益的 评估还有很多争论。在回流焊工艺中,惰性气体环境能减少氧化,而且可以降低 焊膏内助焊剂的活性,这一点对一些低残留物或免洗焊膏的有效性能来讲,或者 在回流焊工艺中需要经过多次的时候(比如双面板),可能是必需的。如果涉及到多 个加热过程,带OSP的板子也会受益,因为在氮气里底层铜线的可焊性会得到比 较好的保护。氮气工艺其它好处还包括较高表面张力,可以扩宽工艺窗口(尤其对 超细间距器件)、改善焊点形状以及降低覆层材料变色的可能性。
2 温度曲线分析与设计
温度曲线是指SMA 通过回流炉,SMA 上某一点的温度随时间变化的曲线;其本 质是SMA在某一位置的热容状态。温度 曲线提供了一种直观的方法,来分析某个 元件在整个回流焊过程中的温度变化情 况。这对于获得最佳的可焊性,避免由于 超温而对元件造成损坏以及保证焊接质 量都非常重要。
1.1表面安装的工艺流程
1.1.1表面安装组件的类型: 表面安装组件(Surface Mounting Assembly) (简称:SMA)
类型: 全表面安装(Ⅰ型) 双面混装 (Ⅱ型) 单面混装(Ⅲ型)
a.全表面安装(Ⅰ型): 全部采用表面安装元器件,安装的印制电
路板是单面或双面板.
表面安装示意图
a.单面全表面安装
单面安装流程
b.双面全表面安装 双面安装流程
c.单面混合安装 单面混合安装流程
d、双面混合安装 双面混合安装流程
1.1.3 锡膏印刷
锡膏印刷工艺环节是整个SMT流程的重 要工序,这一关的质量不过关,就会造 成后面工序的大量不良。因此,抓好印 刷质量管理是做好SMT加工、保证品质 的关键。
b.双面混装(Ⅱ型): 表面安装元器件和有引线元器件混合
喷砂工艺_精品文档

喷砂工艺简介喷砂工艺喷砂设备的选择1、一般而言,喷砂效果主要由零件材料及喷砂磨料决定。
根据零件材料的不同,喷砂磨料范围可从效果强烈的金属磨料到效果柔和的树脂磨料,同时干喷砂与液体喷砂亦是重点考虑的因素。
2、生产效率确定设备种类:根据加工能力选择自动化喷砂生产线、半自动化喷砂设备、压入式喷砂机、吸入式喷砂机。
3、工件尺寸确定设备规格:根据工件尺寸选择机舱大小,以便有足够的空间完成处理工作。
4、压缩空气要求:根据设备规格确定空压机容量,并留20%余量,以保护空压机使用寿命。
一、功能或用途1 .工件表面的清理可用作对金属的锈蚀层、热处理件表面的残盐和氧化层、轧制件表面的氧化层、锻造件表面的氧化层、焊接件表面的氧化层、铸件表面的型砂及氧化层、机加件表面的残留污物和微小毛刺、旧机件表面等进行处理,以去除表面附着层,显露基体本色, 表面清理质量可达到Sa3 级。
2 .工件表面涂覆前的预处理可用作各种电镀工艺、刷镀工艺、喷涂工艺和粘接工艺的前处理工序,以获得活性表面,提高镀层、涂层和粘接件之间的附着力。
3 .改变工件的物理机械性能可以改变工件表面应力状态,改善配合偶件的润滑条件,降低偶件运动过程中的噪音。
可使工件表面硬化,提高零件的耐磨性和抗疲劳强度。
4 .工件表面的光饰加工可以改变工件表面粗糙度Ra 值。
可以产生亚光或漫反射的工件表面,以达到光饰加工的目的。
二、主要参数影响喷砂加工的主要参数:磨料种类、磨料粒度、磨液浓度、喷射距离、喷射角度、喷射时间、压缩空气压力等。
三、环保特点1 .极大地改善了粉尘对环境的污染和对工人健康的危害。
2 .可直接安装在生产线上,节省生产面积, 有利工件周转。
3 .工作方法灵活,工艺参数可变,能适应不同材质和不同精度零件的光饰加工要求。
4 .在工作过程中磨料循环使用,消耗量些5 .主要零部件使用寿命长,且便于维修。
常用喷砂工艺参数获得表面结果的三要素:压缩空气对喷射流的加速作用(喷砂压力大小的调节)P磨料的类型(S)喷枪的距离(H)、角度(θ)1.压力大小的调节对表面结果的影响在S、H 、θ三个量设定后,P值越大,喷射流的速度越高,喷砂效率亦越高,被加工件表面越粗糙,反之,表面由相对较光滑。
UV转印技术概述与应用
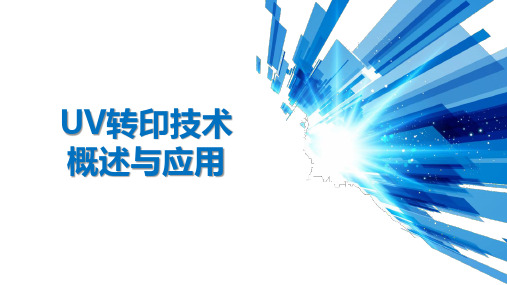
2、光固化转印技术
光固化转印技术则以光固化油墨来印刷制作转印膜或转印纸,然后将印有图案和文字的转印膜 或转印纸,通过热转印或水转印方式将图案和文字转印到承印物上,实现承印物的表面涂装。 水转印异型承印物干燥后,往往喷涂UV上光油,进行上光处理。
采用光固化转印加工技术印制的仿真大理石、仿真玉石、仿真术纹、镭射(激光)图案,效果自 然逼真,质感强烈,是低成本无机装饰板进行高档化装饰、代替天然石材、木材装饰的最佳选 择。
17、UV冷烫金工艺流程图
水转印纸
网印UV烫金底油
水转贴
网印可撕封面油
烘烤
烫金玻璃瓶成 品
UV固化ห้องสมุดไป่ตู้冷烫金
18、UV烫金技术
UV烫金技术是最近几年在印刷及水转印行业中流行的新科技成果,它克服了传统烫金工艺 中需要依靠烫金凸版和热压来转移电化铝的技术缺陷,而使用直接冷压技术来转移电化铝 箔,烫金后直接UV固化。UV 烫金新技术解决了印刷行业许多过去难以解决的工艺问题, 拓宽了烫金产品的应用范围,还节约了能源,提高了生产效率,并避免了制作金属凸版过 程中对环境产生的污染。传统的烫金工艺使用的电化铝背面预涂有热熔胶,烫金时,依靠 热滚筒的压力使热熔胶熔化而实现铝箔转移。在UV烫金工艺中,UV 烫金光油的作用相当 于热熔胶,直接网印在水转印纸或需烫金的产品上,烫金图案是印刷出来的,而不是用烫 金凸版压出来的。烫金膜上可以有热熔胶,也可以没有热熔胶,热熔胶在 UV 烫金新工艺 中成了多余的东西,UV 冷烫金底油起黏合剂的作用,直接被印刷在需要烫金的位置上, 烫金时,电化铝同UV冷烫金底油接触,被黏附在水转印纸表面。UV 烫金光油经 UV 光照 射后,变成了热固性物质,再遇热也不会发生烫金膜迁移,烫金图形也不会发生形变,而 传统烫金工艺中的热熔胶遇热后又会熔化,烫金箔可以从产品上轻易再剥离掉,而 UV 烫 金尤其是UV冷烫金,则很难剥掉。
最新塑胶件表面处理咬花精品课件

七.塑料與咬花深度
1. 脫模度預留 0.5 度或 0.005 mm 深/安全量 2. tolerance is +/- 0.0025mm (Hommel Tester T1000 精密測試)
3. PS
(0.005mm)
(0.005mm)
0.0002
0.0002
ABS
PC
[ 黏度 (viscosity) / 流動長度 ]
Hommer Tester T1000 C - 320
Dat:-------------Nr:----------------
Lt = 15 mm Lc = 2.5 mm Ra = 09.81 Um Rz = 56.24 Um Rm = 64.32 Um Nr = 00032/cm
15 mm
Hommer Tester T1000 C - 320
4. exp: apple G-1 texture minimum draft required:3.5度 for ABS & PC, 2.5度 for PVC
PLASTIC SPECIFICATION
STEEL SPECIFICATION
=====================================
Dat:-------------Nr:----------------
Lt = 15 mm Lc = 2.5 mm Ra = 23.79 Um Rz = 91/.16Um Rm = 92.64 Um Nr = 00012/cm
15 mm
MOLD-TECH 咬花製作參考資料
TEXTURE # DRAFT
DEPTH
NR
DEPTH NR
(in/1000)
表面粗糙度(精品 值得参考)
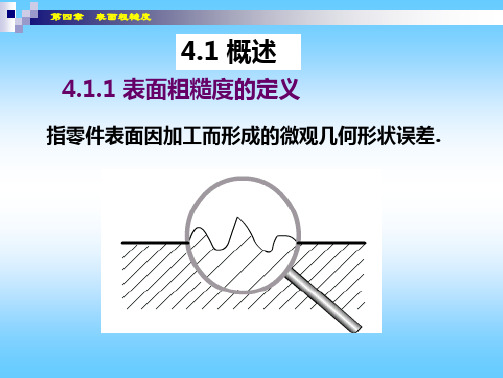
的下限值为6.3m。
第四章
表面粗糙度
四、表面粗糙度在图样上的标注
零件图上所标注的表面粗糙度代(符)号是指该表面完工后 的要求。
3.2
C×45
3.2
表面粗糙度符号、 代号一般注在可见轮 廓线、尺寸界线、引 出线或它们的延长线 上。符号的尖端必须 从材料外指向表面
0.4
1.6
表面粗糙度
三、表面粗糙度标注示例
铣 Ra 3.2 用去除材料的方法获得的表面, Ra的上限值为3.2m,加 工方法为铣削。 采用不去除材料的方法获得的表面, Rz的上限值为0.4m。
Rz 0.4
Rzmax 0.4
用去除材料的方法获得的表面, Rz的最大值为0.4m。
用去除材料的方法获得的表面, Ra的上限值为25m, Ra
4)对接触刚度的影响:
表面越粗糙,峰值越大,实际接触面小,单位面积受力增加。
5)对耐腐蚀性能的影响:
表面越粗糙容易将腐蚀物存于谷中,造成对工件表面的腐蚀。
第四章
表面粗糙度
表面粗糙度标准
《产品几何技术规范 表面结构 轮廓法 表面结构的术
语、定义及参数》(GB/T 3505-2000) 《表面粗糙度 参数及其数值》(GB/T1031-1995) 《机械制图 表面粗糙度符号、代号及其注法》(GB/T 131-2006)
10 15 20 25 30 40 50 60 70 80 90
第四章
表面粗糙度
第四章
表面粗糙度
Ra数值(常用)
Ra(系列)(μ m) 0.012 0.025 0.05 0.1 0.2 0.4 0.8 1.6 3.2 6.3 12.5 25 50 100
印刷击凸工艺基础知识-精品文档
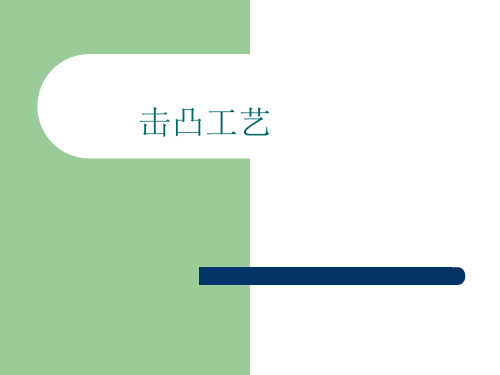
击凸工艺
4、表面斑点 A、产生原因 石膏粉或胶水中有杂质 印刷品表面有杂质 印刷黏附上石膏屑及杂质
击凸工艺
B、解决方法 配石膏浆之前,仔细检查剔除杂质 清除杂质 检查并清除石膏屑
击凸工艺
5、压印途中走版 A、产生原因 压力不均匀 印版粘接牢固度不够
击凸工艺
B、解决方法 检查凸版平整度 检查粘合牢固度,或重新粘牢印版
击凸工艺
7、做击凸版时,根据产品的材料不同, 做击凸版。如一般小彩盒,在350g以下 的纸张用一般击凸版。做对裱产品的, 则做加厚版,特别是裱坑的产品,必须 做到3.0以上,否则无效果。
击凸工艺
击凸工艺 一、击凸(凹)的定义: 是印刷品表面整饰加工中一种特殊 的工艺技术,它适用阴(凹)、阳 (凸)模具,以机械作用施以超过 印刷品基材弹性极限的压力,在印 刷品表面上进行艺术加工。
击凸工艺
二、击凸(凹)的目的: 增强印刷图文的立体感
击凸工艺
三、击凸(凹)印版(俗称击凸版) A、概念: 1、凹凸印版:是由阴、阳两块彼此的高精度相 配的印版组成。 2、凹版(阴版):加工图文部分的凹、凸加工 后产品方向相反。 3、凸版(阳版,也称垫板):加工图文部门的 凹、凸同加工后产品方向相同。
击凸工艺
3、石膏凸版压印中破碎 A、产生原因 调石膏浆时,加入的胶水过少 石膏粉质量不好,牢度及粘性不够 压印中突然增加压力 双张或印刷品表面粘有杂物 压印压力调整不适合
击凸工艺
B、解决方法 适当增加胶水用量 更换石膏粉 避免突然增加压力 避免双张及粘杂物的印刷品输入 调整压力
击凸工艺
B、解决方法 1适当增加压力,调整垫版 2用石膏浆修补 3调整机械精度和石膏版位置 4修补石膏版 5杜绝双张,调换纸张
现代表面技术

11-磁四极聚焦透镜;12-静电扫描;13-靶室; 14-密封转动马达;15-滚珠夹具
面上,再经过扫描系统扫描轰击
工件表面。
精品PPT
离子注入机实物(shíwù)照片
精品PPT
在离子进入工件表面(biǎomiàn)后,与工件内原子和电 子发生一系列碰撞,这一系列的碰撞包括三个独立的过程: (1)电子碰撞:荷能离子进入工件后,与工件内围绕原子核 运动的电子或原子间运动的电子非弹性碰撞。其结果,可 能引起离子激发原子中的电子或原子获得电子、电离或X射 线发射等。 (2)核碰撞:荷能离子与工件原子核弹性碰撞(又称核阻止), 碰撞的结果是使工件中产生的离子大角度散射和晶体中产 生辐射损伤等。 (3)离子与工件内原子作电荷交换:碰撞会损失离子自身能
精品PPT
喷丸强化不仅用于汽车工业领域的弹簧、连杆、曲轴、齿轮、 摇臂、凸轮轴等承受交变(jiāo biàn)载荷的部件,还广泛用于其他 工业领域。如喷丸强化可以提高电镀零件的疲劳强度和结合力;各 种合金钢经过任何一种电镀处理后,一般均会导致疲劳强度下降10 %~60 % ,而喷丸强化则可有效提高疲劳强度, 同时还可以增加电 镀层的结合力, 防止起泡。
腐蚀与防护理论
表面涂镀层
表面摩擦与磨损理论 成分结构设计
表面界面理论
表面复合
表面强化与失效理论 表面结合与复合理论
功能膜层设计 表面涂镀层
的选择和应用设计
多层表面与界面结合 施工设计
表面膜层的电迁移 设备设计
低维材料结构理论 车间生产线的设计
表面涂镀层的材料 加工技术
表面分析与检测 试验方法与标准 表面质量的评估
表面层特性及其综合利用 ’ 表面层材料及加工技术 表面层标准及检验 表面界面维修与再造 表面质量与工艺过程控制 表面工程管理与经济分析
- 1、下载文档前请自行甄别文档内容的完整性,平台不提供额外的编辑、内容补充、找答案等附加服务。
- 2、"仅部分预览"的文档,不可在线预览部分如存在完整性等问题,可反馈申请退款(可完整预览的文档不适用该条件!)。
- 3、如文档侵犯您的权益,请联系客服反馈,我们会尽快为您处理(人工客服工作时间:9:00-18:30)。
表面成型加工技术电火花成型加工电火花加工是利用浸在工作液中的两极间脉冲放电时产生的电蚀作用蚀除导电材料的特种加工方法,又称放电加工或电蚀加工.1943年,苏联学者拉扎连科夫妇研究发明电火花加工,之后随着脉冲电源和控制系统的改进,而迅速发展起来。
最初使用的脉冲电源是简单的电阻-电容回路。
50年代,改进为电阻-电感-电容等回路。
同时,还采用脉冲发电机之类的所谓长脉冲电源,使蚀除效率提高,工具电极相对损耗降低。
随后又出现了大功率电子管、闸流管等高频脉冲电源,使在同样表面粗糙度条件下的生产率得以提高。
60年代,出现了晶体管和可控硅脉冲电源,提高了能源利用效率和降低了工具电极损耗,并扩大了粗精加工的可调范围。
70年代,出现了高低压复合脉冲、多回路脉冲、等幅脉冲和可调波形脉冲等电源,在加工表面粗糙度、加工精度和降低工具电极损耗等方面又有了新的进展。
在控制系统方面,从最初简单地保持放电间隙,控制工具电极的进退,逐步发展到利用微型计算机,对电参数和非电参数等各种因素进行适时控制。
电火花加工工作原理进行电火花加工时,工具电极和工件分别接脉冲电源的两极,并浸入工作液中,或将工作液充入放电间隙。
通过间隙自动控制系统控制工具电极向工件进给,当两电极间的间隙达到一定距离时,两电极上施加的脉冲电压将工作液击穿,产生火花放电.在放电的微细通道中瞬时集中大量的热能,温度可高达一万摄氏度以上,压力也有急剧变化,从而使这一点工作表面局部微量的金属材料立刻熔化、气化,并爆炸式地飞溅到工作液中,迅速冷凝,形成固体的金属微粒,被工作液带走。
这时在工件表面上便留下一个微小的凹坑痕迹,放电短暂停歇,两电极间工作液恢复绝缘状态。
紧接着,下一个脉冲电压又在两电极相对接近的另一点处击穿,产生火花放电,重复上述过程。
这样,虽然每个脉冲放电蚀除的金属量极少,但因每秒有成千上万次脉冲放电作用,就能蚀除较多的金属,具有一定的生产率。
在保持工具电极与工件之间恒定放电间隙的条件下,一边蚀除工件金属,一边使工具电极不断地向工件进给,最后便加工出与工具电极形状相对应的形状来。
因此,只要改变工具电极的形状和工具电极与工件之间的相对运动方式,就能加工出各种复杂的型面。
电火花加工工具电极常用导电性良好、熔点较高、易加工的耐电蚀材料,如铜、石墨、铜钨合金和钼等。
在加工过程中,工具电极也有损耗,但小于工件金属的蚀除量,甚至接近于无损耗。
电火花加工工作液作为放电介质,在加工过程中还起着冷却、排屑等作用。
常用的工作液是粘度较低、闪点较高、性能稳定的介质,如煤油、去离子水和乳化液等。
电火花加工分类按照工具电极的形式及其与工件之间相对运动的特征,可将电火花加工方式分为五类:利用成型工具电极,相对工件作简单进给运动的电火花成形加工;利用轴向移动的金属丝作工具电极,工件按所需形状和尺寸作轨迹运动,以切割导电材料的电火花线切割加工;利用金属丝或成形导电磨轮作工具电极,进行小孔磨削或成形磨削的电火花磨削;用于加工螺纹环规、螺纹塞规、齿轮等的电火花共轭回转加工;小孔加工、刻印、表面合金化、表面强化等其他种类的加工。
电火花加工的加工特性1:电火花加工速度与表面质量模具在电火花机加工一般会采用粗、中、精分档加工方式。
粗加工采用大功率、低损耗的实现,而中、精加工电极相对损耗大,但一般情况下中、精加工余量较少,因此电极损耗也极小,可以通过加工尺寸控制进行补偿,或在不影响精度要求时予以忽略。
2:电火花碳渣与排渣电火花机加工在产生碳渣和排除碳渣平衡的条件下才能顺利进行。
实际中往往以牺牲加工速度去排除碳渣,例如在中、精加工时采用高电压,大休止脉波等等。
另一个影响排除碳渣的原因是加工面形状复杂,使排屑路径不畅通。
唯有积极开创良好排除的条件,对症的采取一些方法来积极处理。
3:电火花工件与电极相互损耗电火花机放电脉波时间长,有利于降低电极损耗。
电火花机粗加工一般采用长放电脉波和大电流放电,加工速度快电极损耗小。
在精加工时,小电流放电必须减小放电脉波时间,这样不仅加大了电极损耗,也大幅度降低了加工速度。
电火花加工是与机械加工完全不同的一种新工艺。
随着工业生产的发展和科学技术的进步,具有高熔点、高硬度、高强度、高脆性,高粘性和高纯度等性能的新材料不断出现。
具有各种复杂结构与特殊工艺要求的工件越来越多,这就使得传统的机械加工方法不能加工或难于加工。
因此,人们除了进一步发展和完善机械加工法之外,还努力寻求新的加工方法。
电火花加工法能够适应生产发展的需要,并在应用中显示出很多优异性能,因此,得到了迅速发展和日益广泛的应用。
电火花加工的主要特点1、能加工普通切削加工方法难以切削的材料和复杂形状工件;2、加工时无切削力;3、不产生毛刺和刀痕沟纹等缺陷;4、工具电极材料无须比工件材料硬并不受热处理状况影响;5、直接使用电能加工,便于实现自动化;6、脉冲放电持续时间极短,放电产生的热量传导扩散范围小,材料受热影响范围小;7、加工后表面产生变质层,在某些应用中须进一步去除;8、工作液的净化和加工中产生的烟雾污染处理比较麻烦;9、不能加工不导电的材料;10、加工过程中,有因为使用控制不良,引起火灾的安全隐患;11、加工效率较低(相对机械加工来讲);12、加工过程造成被加工件的内应力增加而变形,加工尺寸精度不高;13、可以改革工件结构,简化加工工艺,提高工件使用寿命,降低工人劳动强度。
电火花加工的主要用途①加工具有复杂形状的型孔和型腔的模具和零件;②加工各种硬、脆材料如硬质合金和淬火钢等;③加工深细孔、异形孔、深槽、窄缝和切割薄片等;④加工各种成形刀具、样板和螺纹环规等工具和量具。
电火花加工的应用领域电火花加工主要用于模具生产中的型孔、型腔加工,已成为模具制造业的主导加工方法,推动了模具行业的技术进步。
电火花加工零件的数量在3000件以下时,比模具冲压零件在经济上更加合理。
按工艺过程中工具与工件相对运动的特点和用途不同,电火花加工可大体分为:电火花成形加工、电火花线切割加工、电火花磨削加工、电火花展成加工、非金属电火花加工和电火花表面强化等。
(1)电火花成形加工该方法是通过工具电极相对于工件作进给运动,将工件电极的形状和尺寸复制在工件上,从而加工出所需要的零件。
它包括电火花型腔加工和穿孔加工两种。
电火花型腔加工主要用于加工各类热锻模、压铸模、挤压模、塑料模和胶木膜的型腔。
电火花穿孔加工主要用于型孔(圆孔、方孔、多边形孔、异形孔)、曲线孔(弯孔、螺旋孔)、小孔和微孔的加工。
近年来,为了解决小孔加工中电极截面小、易变形、孔的深径比大、排屑困难等问题,在电火花穿孔加工中发展了高速小孔加工,取得良好的社会经济效益.(2)电火花线切割加工该方法是利用移动的细金属丝作工具电极,按预定的轨迹进行脉冲放电切割。
按金属丝电极移动的速度大小分为高速走丝和低速走丝线切割。
我国普通采用高速走丝线切割,近年来正在发展低速走丝线切割,高速走丝时,金属丝电极是直径为φ0.02~φ0.3mm的高强度钼丝,往复运动速度为8~10m/s。
低速走丝时,多采用铜丝,线电极以小于0.2m/s的速度作单方向低速运动。
线切割时,电极丝不断移动,其损耗很小,因而加工精度较高。
其平均加工精度可达0.0lmm,大大高于电火花成形加工。
表面粗糙度Ra值可达1.6 或更小。
电火花加工具有如下特点:可以加工任何高强度、高硬度、高韧性、高脆性以及高纯度的导电材料;加工时无明显机械力,适用于低刚度工件和微细结构的加工:脉冲参数可依据需要调节,可在同一台机床上进行粗加工、半精加工和精加工;电火花加工后的表面呈现的凹坑,有利于贮油和降低噪声;生产效率低于切削加工;放电过程有部分能量消耗在工具电极上,导致电极损耗,影响成形精度。
国内外数控电火花线切割机床都采用了不同水平的微机数控系统,实现了电火花线切割数控化。
目前电火花线切割广泛用于加工各种冲裁模(冲孔和落料用)、样板以及各种形状复杂型孔、型面和窄缝等。
电火花成形加工技术的发展现状目前在电火花加工基础理论研究领域,由于放电过程本身的复杂性、随机性以及研究手段缺乏创新性,迄今尚未取得突破性进展。
但在加工工艺和控制理论研究领域,由于研究成果可直接应用于生产实践,因此已成为目前电火花成形加工技术研究中较为活跃的领域,其研究热点主要集中在高效加工技术、高精密加工技术(如镜面加工技术)、低损耗加工技术、微细加工技术、非导电材料加工技术、电火花表面处理技术、智能控制技术(如人工神经网络技术、模糊控制技术、专家系统等)以及操作安全、环境保护等方面。
在工艺设备开发方面,目前的新型电火花成形加工机床在加工功能、加工精度、自动化程度、可靠性等方面已全面改善,许多机床已具备了在线检测、智能控制、模块化等功能,已不再是传统意义上的特种加工机床,而更像切削加工中的数控机床甚至加工中心。
电火花成形加工技术的发展趋势先进制造技术的快速发展和制造业市场竞争的加剧对电火花成形加工技术提出了更高要求,同时也为电火花成形加工技术加工理论的研究和工艺开发、设备更新提供了新的动力。
今后电火花成形加工的加工对象应主要面向传统切削加工不易实现的难加工材料、复杂型面等加工,其中精细加工、精密加工、窄槽加工、深腔加工等将成为发展重点。
同时,还应注意与其它特种加工技术或传统切削加工技术的复合应用,充分发挥各种加工方法在难加工材料加工中的优势,取得联合增值效应。
相对于切削加工技术而言,电火花成形加工技术仍是一门较年轻的技术,因此在今后的发展中,应借鉴切削加工技术发展过程中取得的经验与成果,根据电火花成形加工自身的技术特点,选用适当的加工理论、控制原理和工艺方法,并在己有成果的基础上不断完善、创新。
电火花成形加工机床向数控化方向发展的趋势已不可逆转,但应注意不可盲目追求“大而全”,应以市场为导向,建立具有开放性的数控体系。
总体而言,电火花成形加工技术今后的发展趋势应是高效率、高精度、低损耗、微细化、自动化、安全、环保等。
电火花成形加工理论的发展趋势近年来,电火花成形加工的基础理论研究尚未取得实质性进展,虽然一些学者对加工过程的放电痕迹、材料蚀除原理等提出了一些新看法,但在电火花加工机理研究方面并未取得重大突破。
较为活跃的研究领域主要集中在加工工艺理论和控制理论方面。
在加工工艺理论研究方面,研究热点主要是如何提高电火花成形加工的表面质量和加工速度,降低损耗,拓展电火花加工的范围,以及探索复杂、微细结构的加工方法等。
通过将研究成果应用于生产实践,全面提高了电火花成形加工的加工性能。
在控制理论研究方面,智能控制一直是研究重点。
国内外生产的新型电火花成形加工机床大多采用了智能控制技术,此项技术的应用使机床操作更容易,对操作人员要求更低。
同时,智能控制系统具有自学习能力,可在线自动监测、调整加工过程,以实现加工过程的最优化控制。