橡胶的塑炼与混炼(精选)
橡胶混炼过程常见问题塑化、焦烧、黏附和分散

橡胶混炼过程常见问题:塑化、焦烧、黏附和分散在橡胶加工工艺过程中(包括塑炼、混炼及压出、压延和粘贴成型在内),以下4个问题需要在配合上引起注意。
塑化性与塑解剂天然橡胶等门尼黏度高的生胶,除通常采用的机械塑化法外亦常使用塑解剂促进性增加。
过去曾用各种硫酚及其锌盐。
现今,已开始使用特制的高级不饱和脂肪酸锌盐、金属盐的酯类、橡胶促进剂、橡胶硫化剂等。
加入3-5份,可使天然橡胶、氯丁橡胶及乙丙橡胶的塑化效果提高20%-100%。
然而,由于目前的天然橡胶大部分转为容易塑化的标准胶,合成橡胶也因由多种不同门尼粘度的牌号可供选用,所以塑解剂的使用越来越少。
焦烧性与防焦剂为保证橡胶加工操作的安全性,防止因早期硫化而产生焦烧现象,市场上出现了不少防焦剂。
最主要的是苯甲酸和苯二甲酸一类的衍生物。
此外,还有几种硝基、亚硝基的化合物,氯代和硫代三聚氰胺等。
然而除CTP、MTP极少数品种外,其余皆有利有弊,使用较少。
提倡使用的是一举多得的脂肪酸及其各种盐类和蜡类,使之通过抑制外部及内部生热达到防止焦烧的目的。
黏附性与防粘剂或增黏剂橡胶加工时,要求有一定黏性。
但黏性太大或太小都不利于操作,因此对某些橡胶需做防粘或增黏配合处理。
氯丁橡胶极易粘辊,其他含氯橡胶也因与金属的黏着性大而难于操作。
对于这类橡胶,添加5份左右的脂肪酸金属盐或石蜡,即可使粘辊问题迅速得到解决。
乙丙橡胶、丁二烯橡胶等容易脱辊,不好操作。
解决办法是与其他橡胶并用,亦可适当加入增黏剂予以改善。
实际生产上,以古马隆、萜烯、酚醛、石油炭化氢等树脂及松香衍生物最为有效。
分散性与分散剂、软化剂硬脂酸既是硫化活性剂,又是极为良好的软化分散剂,尤其是它具有使炭黑迅速分散的作用,至今仍为大家所普遍采用。
然而,由于硬脂酸用量超过5份时往往对硫化速度有影响,且有喷出现象,放近年来又出现了中性的脂肪酸酯类(RC0()R7)o如今,这种脂肪酸酯类已成为橡胶常用的多功能型加工助剂。
在10份之内时,效果超过了石油系统的操作油。
橡胶的工艺流程

橡胶的工艺流程(精品)2014—10—22橡胶技术网橡胶工艺流程开始1 综述橡胶制品的主要原料是生胶、各种配合剂、以及作为骨架材料的纤维和金属材料,橡胶制品的基本生产工艺过程包括塑炼、混炼、压延、压出、成型、硫化6个基本工序.橡胶的加工工艺过程主要是解决塑性和弹性矛盾的过程,通过各种加工手段,使得弹性的橡胶变成具有塑性的塑炼胶,在加入各种配合剂制成半成品,然后通过硫化是具有塑性的半成品又变成弹性高、物理机械性能好的橡胶制品。
2 橡胶加工工艺2.1塑炼工艺生胶塑炼是通过机械应力、热、氧或加入某些化学试剂等方法,使生胶由强韧的弹性状态转变为柔软、便于加工的塑性状态的过程.生胶塑炼的目的是降低它的弹性,增加可塑性,并获得适当的流动性,以满足混炼、亚衍、压出、成型、硫化以及胶浆制造、海绵胶制造等各种加工工艺过程的要求.掌握好适当的塑炼可塑度,对橡胶制品的加工和成品质量是至关重要的。
在满足加工工艺要求的前提下应尽可能降低可塑度。
随着恒粘度橡胶、低粘度橡胶的出现,有的橡胶已经不需要塑炼而直接进行混炼。
在橡胶工业中,最常用的塑炼方法有机械塑炼法和化学塑炼法。
机械塑炼法所用的主要设备是开放式炼胶机、密闭式炼胶机和螺杆塑炼机。
化学塑炼法是在机械塑炼过程中加入化学药品来提高塑炼效果的方法.开炼机塑炼时温度一般在80℃以下,属于低温机械混炼方法.密炼机和螺杆混炼机的排胶温度在120℃以上,甚至高达160-180℃,属于高温机械混炼。
生胶在混炼之前需要预先经过烘胶、切胶、选胶和破胶等处理才能塑炼.几种胶的塑炼特性:天然橡胶用开炼机塑炼时,辊筒温度为30—40℃,时间约为15—20min;采用密炼机塑炼当温度达到120℃以上时,时间约为3-5min。
丁苯橡胶的门尼粘度多在35—60之间,因此,丁苯橡胶也可不用塑炼,但是经过塑炼后可以提高配合机的分散性顺丁橡胶具有冷流性,缺乏塑炼效果。
顺丁胶的门尼粘度较低,可不用塑炼.氯丁橡胶得塑性大,塑炼前可薄通3-5次,薄通温度在30-40℃。
橡胶制品生产工艺流程

橡胶制品生产工艺流程一、橡胶制品基本工艺流程伴随现代工业尤其是化学工业的迅猛发展,橡胶制品种类繁多,但其生产工艺过程,却基本相同。
以一般固体橡胶 ( 生胶 ) 为原料的制品,它的生产工艺过程主要包括:原材料准备→塑炼→混炼→成型→硫化→休整→检验二、橡胶制品原材料准备橡胶制品的主要材料有生胶、配合剂、纤维材料和金属材料。
其中生胶为基本材料 ; 配合剂是为了改善橡胶制品的某些性能而加入的辅助材料 ; 纤维材料 ( 棉、麻、毛及各种人造纤维、合成纤维 ) 和金属材料 ( 钢丝、铜丝 ) 是作为橡胶制品的骨架材料,以增强机械强度、限制制品变型。
在原材料准备过程中,配料必须按照配方称量准确。
为了使生胶和配合剂能相互均匀混合,需要对某些材料进行加工:生胶要切胶、破胶成小块 ;块状配合剂如石蜡、硬脂酸、松香等要粉碎 ;粉状配合剂若含有机械杂质或粗粒时需要筛选除去 ;液态配合剂 ( 松焦油、古马隆 ) 需要加热、熔化、蒸发水分、过滤杂质;配合剂要进行干燥,不然容易结块、混炼时旧不能分散均匀,硫化时产生气泡,从而影响产品质量;三、橡胶制品的塑炼生胶富有弹性,缺乏加工时的必需性能 ( 可塑性 ) ,因此不便于加工。
为了提高其可塑性,所以要对生胶进行塑炼 ; 这样,在混炼时配合剂就容易均匀分散在生胶中 ; 同时,在压延、成型过程中也有助于提高胶料的渗透性 ( 渗入纤维织品内 ) 和成型流动性。
将生胶的长链分子降解,形成可塑性的过程叫做塑炼。
生胶塑炼的方法有机械塑炼和热塑炼两种。
机械塑炼是在不太高的温度下,通过塑炼机的机械挤压和摩擦力的作用,使长链橡胶分子降解变短,由高弹性状态转变为可塑状态。
热塑炼是向生胶中通入灼热的压缩空气,在热和氧的作用下,使长链分子降解变短,从而获得可塑性。
四、橡胶制品的混炼为了适应各种不同的使用条件、获得各种不同的性能,也为了提高橡胶制品的性能和降低成本,必须在生胶中加入不同的配合剂。
混炼就是将塑炼后的生胶与配合剂混合、放在炼胶机中,通过机械拌合作用,使配合剂完全、均匀地分散在生胶中的一种过程。
橡胶加工工艺
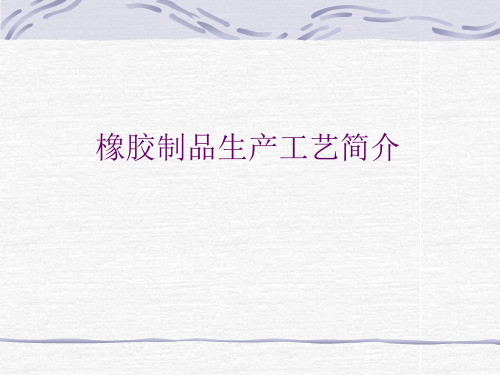
➢ 化学塑解剂:塑解剂的用量,在NR中一般为生胶重量的0.1~0.3%,合 成橡胶则应增大到2~3%。
橡胶制品生产工艺简介-塑炼工艺塑炼工艺
不同胶料开炼机混炼时辊筒温度
胶种
天然胶 丁苯胶 氯丁胶 丁基胶 丁腈胶 顺丁胶 三元乙丙胶 氯磺化聚乙烯 氟橡胶23—27 丙烯酸酯橡胶
橡胶制品生产工艺简介-塑炼工艺塑炼工艺
常用橡胶的塑炼特性
2. SBR ➢ 软SBR的初始门尼粘度一般在54~64之间,不需进行塑炼。 ➢ SBR采用机械塑炼效果不大,比较有效的方法时采用高温
塑炼法,以130~140℃温度最好,温度过高易生成凝胶。 3.BR ➢ BR一般不需要进行塑炼。 4.CR ➢ CR的初始门尼粘度都较低,一般不需要进行塑炼。但在储
➢ 物料在密炼室中主要受到几种作用: 转子间及转子与混炼室内壁间的作用;
转子棱间的搅拌作用;
转子轴向的往复切割作用。
➢ 优点:自动化程度高,生产效率高,节能,劳动强度低
➢ 缺点:温度高,冷却困难,易过炼,出料为无定形状
橡胶制品生产工艺简介-塑炼工艺塑炼工艺
密炼机
橡胶制品生产工艺简介-塑炼工艺塑炼工艺
存过程中其可塑性会下降,因此CR仍需经过塑炼加工,才 能获得所要求的可塑性。 ➢ CR宜采用开炼机进行塑炼,低温薄通塑炼效果最好。
橡胶制品生产工艺简介-塑炼工艺塑炼工艺
常用橡胶的塑炼特性
5.IIR ➢ 门尼粘度在38~75之间的品种一般不需要塑炼。 ➢ IIR采用机械塑炼效果不大,但用密炼机在120℃以上,并
且加入塑解剂进行高温塑炼则可取得较好的塑炼效果。 6.NBR ➢ NBR的塑炼应采用开炼机在低温(40℃以下)、小辊距
橡胶生产工艺简介
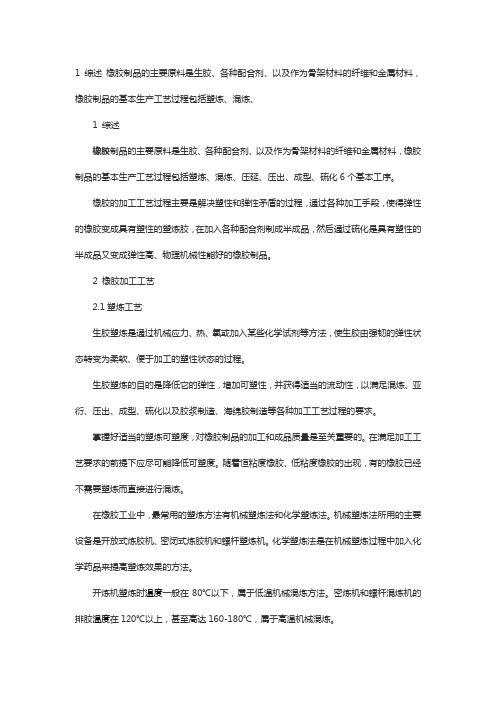
1 综述橡胶制品的主要原料是生胶、各种配合剂、以及作为骨架材料的纤维和金属材料,橡胶制品的基本生产工艺过程包括塑炼、混炼、1 综述橡胶制品的主要原料是生胶、各种配合剂、以及作为骨架材料的纤维和金属材料,橡胶制品的基本生产工艺过程包括塑炼、混炼、压延、压出、成型、硫化6个基本工序。
橡胶的加工工艺过程主要是解决塑性和弹性矛盾的过程,通过各种加工手段,使得弹性的橡胶变成具有塑性的塑炼胶,在加入各种配合剂制成半成品,然后通过硫化是具有塑性的半成品又变成弹性高、物理机械性能好的橡胶制品。
2 橡胶加工工艺2.1塑炼工艺生胶塑炼是通过机械应力、热、氧或加入某些化学试剂等方法,使生胶由强韧的弹性状态转变为柔软、便于加工的塑性状态的过程。
生胶塑炼的目的是降低它的弹性,增加可塑性,并获得适当的流动性,以满足混炼、亚衍、压出、成型、硫化以及胶浆制造、海绵胶制造等各种加工工艺过程的要求。
掌握好适当的塑炼可塑度,对橡胶制品的加工和成品质量是至关重要的。
在满足加工工艺要求的前提下应尽可能降低可塑度。
随着恒粘度橡胶、低粘度橡胶的出现,有的橡胶已经不需要塑炼而直接进行混炼。
在橡胶工业中,最常用的塑炼方法有机械塑炼法和化学塑炼法。
机械塑炼法所用的主要设备是开放式炼胶机、密闭式炼胶机和螺杆塑炼机。
化学塑炼法是在机械塑炼过程中加入化学药品来提高塑炼效果的方法。
开炼机塑炼时温度一般在80℃以下,属于低温机械混炼方法。
密炼机和螺杆混炼机的排胶温度在120℃以上,甚至高达160-180℃,属于高温机械混炼。
生胶在混炼之前需要预先经过烘胶、切胶、选胶和破胶等处理才能塑炼。
几种胶的塑炼特性:天然橡胶用开炼机塑炼时,辊筒温度为30-40℃,时间约为15-20min;采用密炼机塑炼当温度达到120℃以上时,时间约为3-5min。
丁苯橡胶的门尼粘度多在35-60之间,因此,丁苯橡胶也可不用塑炼,但是经过塑炼后可以提高配合机的分散性顺丁橡胶具有冷流性,缺乏塑炼效果。
橡胶的工艺流程
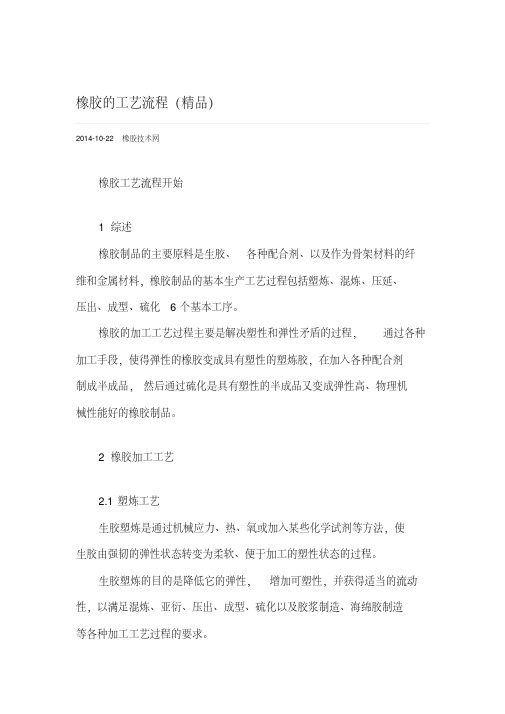
橡胶的工艺流程(精品)2014-10-22橡胶技术网橡胶工艺流程开始1 综述橡胶制品的主要原料是生胶、各种配合剂、以及作为骨架材料的纤维和金属材料,橡胶制品的基本生产工艺过程包括塑炼、混炼、压延、压出、成型、硫化6个基本工序。
橡胶的加工工艺过程主要是解决塑性和弹性矛盾的过程,通过各种加工手段,使得弹性的橡胶变成具有塑性的塑炼胶,在加入各种配合剂制成半成品,然后通过硫化是具有塑性的半成品又变成弹性高、物理机械性能好的橡胶制品。
2 橡胶加工工艺2.1塑炼工艺生胶塑炼是通过机械应力、热、氧或加入某些化学试剂等方法,使生胶由强韧的弹性状态转变为柔软、便于加工的塑性状态的过程。
生胶塑炼的目的是降低它的弹性,增加可塑性,并获得适当的流动性,以满足混炼、亚衍、压出、成型、硫化以及胶浆制造、海绵胶制造等各种加工工艺过程的要求。
掌握好适当的塑炼可塑度,对橡胶制品的加工和成品质量是至关重要的。
在满足加工工艺要求的前提下应尽可能降低可塑度。
随着恒粘度橡胶、低粘度橡胶的出现,有的橡胶已经不需要塑炼而直接进行混炼。
在橡胶工业中,最常用的塑炼方法有机械塑炼法和化学塑炼法。
机械塑炼法所用的主要设备是开放式炼胶机、密闭式炼胶机和螺杆塑炼机。
化学塑炼法是在机械塑炼过程中加入化学药品来提高塑炼效果的方法。
开炼机塑炼时温度一般在80℃以下,属于低温机械混炼方法。
密炼机和螺杆混炼机的排胶温度在120℃以上,甚至高达160-180℃,属于高温机械混炼。
生胶在混炼之前需要预先经过烘胶、切胶、选胶和破胶等处理才能塑炼。
几种胶的塑炼特性:天然橡胶用开炼机塑炼时,辊筒温度为30-40℃,时间约为15-20min;采用密炼机塑炼当温度达到120℃以上时,时间约为3-5min。
丁苯橡胶的门尼粘度多在35-60之间,因此,丁苯橡胶也可不用塑炼,但是经过塑炼后可以提高配合机的分散性顺丁橡胶具有冷流性,缺乏塑炼效果。
顺丁胶的门尼粘度较低,可不用塑炼。
氯丁橡胶得塑性大,塑炼前可薄通3-5次,薄通温度在30-40℃。
第三章 塑炼混炼
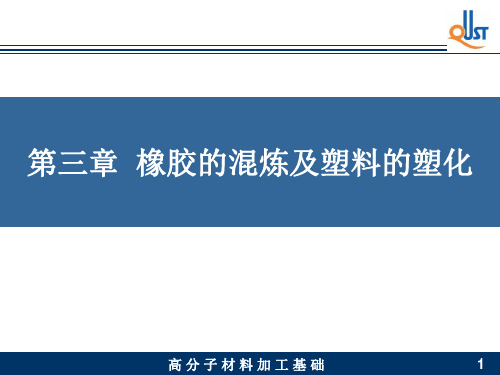
(-)混炼理论
混炼不是生胶和配合剂简单的机械混合过程,混 炼胶也不是生胶与配合剂的简单机械混合物; 混炼的实质是橡胶的改性过程。期间,机械力/化 学反应起着重要作用; 混炼胶是由生胶和各种配合剂组成的一种复合体。
(1)、准备工作
为了便于塑炼 加工,生胶需 要经过烘胶、
切胶和破胶等
塑炼前的准备 工艺。
生胶,长期储存后,粘度很高, 且在冬天常因结晶而硬化。 切胶后的NR、CR一 为便于使用,把烘好的 在切胶和塑炼前把生胶放在烘房 般要在破胶机上进 大胶包用切胶机切成小 中预先对胶包进行加温,便于切 行破胶,以便进行 块 割和进一步的加工。 塑炼。 烘胶的温度和时间视生胶的种类 与季节而定。
高分子材料加工基础 18
2、塑炼的原理
熔体粘度——加工温度、切变速率、分子量。 分子量越小,可塑度越大。生胶经机械塑炼后, 分子量降低,粘度下降,可塑性增加。 生胶在塑炼过程中可塑性的提高是通过分子量的
降低来实现的。
塑炼的实质是使橡胶大分子链断裂,大分子链由
长变短的过程。
高分子材料加工基础
高分子材料加工基础 6
工作原理:
两个辊筒以不同的表面速度
相对回转,物料由于与辊筒
表面的摩擦和粘附作用,以
及物料之间的粘接作用,被
拉入两辊筒之间的间隙之内。
高分子材料加工基础
7
工作原理:
受到强烈的挤压与剪切,使物料在辊隙内形成楔形 断面的料片,从辊隙中排出的料片由于两个辊筒表 面速度和温度的差异而包在一个辊筒上,重新返回 两辊间。
高分子材料加工基础
21
剪切力作用于橡胶时,分子链将沿流动方向伸展;
橡胶塑炼与混炼—塑炼(橡胶加工课件)

保持变形后的形状
降低弹性、增大塑性 塑炼
塑炼
1、塑炼概念与原理
讨论:塑炼、塑炼目的及不利面
分组汇报: 教师点评 1、塑炼: 炼:炼胶、炼胶作业,在炼胶机完成的作业过程。
简要:提高橡胶塑性的炼胶
详细:将橡胶经过机械加工、热处理或加入某些化学助剂,使其由强韧的弹性状态转变为柔 软而便于加工的塑性状态的工艺过程称之为塑炼。
塑炼
1、塑炼概念与原理 2、生胶塑炼前的准备 3、塑炼的工艺方法 4、影响塑炼的工艺因素 5、开炼机塑炼实训 6、常见塑炼胶质量分析
1、塑炼概念与原理
引入新课 F 塑性
F 弹性
F 刚性
1、塑炼概念与原理
引入新课 橡胶具有高弹性 优点:
缓冲、减震、柔软
缺点:
产品加工过程是受力变形并定型,如发生弹性回复,尺寸形状不能保持
2、生胶塑炼前的准备-烘胶
目的
对象
“两保证两可以” (1)保证切胶机的安全操作和
工作效率; (2)保证炼胶机的安全操作和
工作效率; (3)可以烘去水份; (4)可以解除结晶(对结晶橡
胶) 。
(1)硬橡胶 如:硬NBR等 (NBR3606)
(2)结晶橡胶 如:NR、CR 等
实物展示 ( NBR 、NR、CR、 EPDM、SBR、BR)
2、生胶塑炼前的准备-破胶
使块状的橡胶变为碎胶 (1)便于称量; (2)便于塑炼; (3)保护设备; (4)提高效率(塑
炼)。
用于开炼机塑混炼的大块橡胶, 如:NR和CR。 说明: ❖ 1、用密炼机塑混炼的NR和CR, 一般无需破胶而直接进行塑混炼。 ❖ 2、其它合成橡胶,一般无需破 胶而直接进行塑混炼。
6、常见塑炼胶质量分析
浅说几种典型的橡胶加工混炼技术

浅说几种典型的橡胶加工混炼技术陆 刚众所周知,橡胶混炼是用炼胶机将生胶或塑炼生胶与配合剂炼成混炼胶的工艺,本质来说是各种配合剂借助炼胶机机械力的作用均匀分散于橡胶中的工艺过程,以形成一个以橡胶为介质或者以橡胶与某些能和它相容的配合组分(配合剂、其它聚合物)的混合物为介质,以与橡胶不相容的配合剂(如粉体填料、氧化锌、颜料等)为分散相的多相胶体分散体系的过程,也是橡胶加工最重要的生产工艺。
橡胶的混炼一般大都采用开放式炼胶机,最大特点是灵活、机动性大,对于橡胶变种频繁、硬质胶、海绵胶等的混炼特别适用。
对混炼工艺的具体技术要求是:配合剂分散均匀,使配合剂特别是炭黑等补强性配合剂达到最好的分散度,以保证胶料性能一致。
混炼后得到的胶料称为“混炼胶”,其质量对进一步加工和制品质量有重要影响。
防老剂先加入能防止高温炼胶时发生的热老化现象,而有些促进剂对胶料有增塑作用,因此值得业内人士的重视。
1. 丁苯橡胶的混炼丁苯橡胶(S B R)又称聚苯乙烯丁二烯共聚物,其物理机构性能,加工性能及制品的使用性能接近于天然橡胶,有些性能如耐磨、耐热、耐老化及硫化速度较天然橡胶更为优良,可与天然橡胶及多种合成橡胶并用,广泛用于轮胎、胶带、胶管、电线电缆、医疗器具及各种橡胶制品的生产等领域,是最大的通用合成橡胶品种,也是最早实现工业化生产的橡胶品种之一。
丁苯橡胶由丁二烯和苯乙烯进行乳化共聚而得。
用松香酸皂或脂肪酸皂为乳化剂,用过硫酸盐为催化剂,必要时另加适宜的分子量调节剂和适宜的反应速度调节剂。
由此所得者为液状胶乳。
如进一步在加热釜中(亦可同时加入其他食用级配料)进行凝聚,凝聚物经压榨除去浆液后,用加碱的热水进行洗涤,并用水淋洗,一直到成为中性,最后将凝聚体加以干燥,以除去可挥发性物质。
此为由乳胶制成的固体状橡胶。
75/25固体状橡胶亦可由丁二烯和苯乙烯在己烷溶液中用丁基锂为催化剂,进行溶体共聚而成。
共聚后残存的溶剂和挥发性物质可用热水处理法或滚筒干燥法除去。
橡胶的塑炼及混炼

橡胶的塑炼及混炼发布时间:2011年9月8日此新闻已被浏览2976次陈秦阳(西北橡胶塑料研究设计院陕西咸阳712023)前言随着改革开放的不断深入,我国的各行业都得到了迅速的发展,橡胶工业也不例外。
但是有些企业由于缺乏必需的技术人员和熟练的操作工人往往又限制了他们的发展。
因此迅速培养这些企业的技术人员和提高操作工人的生产技能是当务之急。
众所周知,橡胶加工工业是一门专业性很强的技术性工作。
它不但需要技术人员除具有较高的业务水平外,同时还应具备广阔的其他学科领域的知识。
不断地消化吸收国内外橡胶工业的新技术、新工艺和新原材料。
只有这样才能设计出比较经济的、最佳综合平衡性能的配方。
但是,这仅仅是橡胶加工的一半,而另一半则是由操作工人来完成。
如果有好的配方,而没有操作工人来圆满的完成配料、混炼、压出、压延以及硫化等等一系列工序。
那么再好的配方也无法生产出好的产品。
因此,提高操作工人的业务水平是提高产品质量的有力保证。
只有技术人员和操作工人的完善结合,才能使我国的橡胶加工工业上升到一个新的水平。
作者通过十几年的工作实践经验,着重讨论利用开炼机对橡胶的塑炼、混炼等方面的问题。
一、橡胶的塑炼对于橡胶制品来说,要求生胶具有一定的可塑度。
例如,对于模压工业制品的橡胶要求生胶可塑度在0.25~0.35左右。
对于压延、压出、海绵胶、胶浆等胶料的可塑度要求在0.4~0.6左右。
如果升胶达不到所需的可塑度,会给混炼带来很大的困难,同时无法保证制品的质量。
因此,对于门尼粘度较高的生胶必须进行塑炼,并获得所需的可塑度,保证其后各项工序的顺利进行。
可塑度过高或过低会对橡胶加工和制品有何不良影响呢?如果生胶混炼不足,可塑度达不到要求,则混炼困难,会发生脱辊等现象;另外胶料的收缩率增大。
生胶过度塑炼则混炼胶的硬度、拉伸强度下降,则耐介质耐老化性能下降。
所以,按照不同的制品要求,来搞好生胶的塑炼,是非常重要的。
并非每种生胶都要进行塑炼。
橡胶的工艺流程
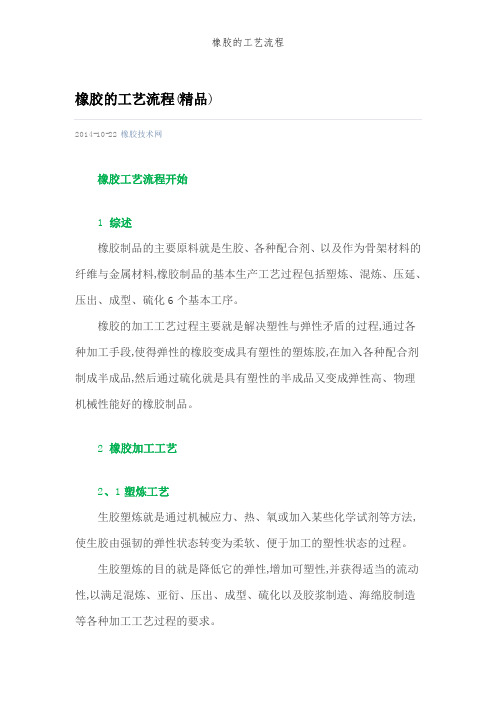
橡胶的工艺流程(精品)2014-10-22橡胶技术网橡胶工艺流程开始1 综述橡胶制品的主要原料就是生胶、各种配合剂、以及作为骨架材料的纤维与金属材料,橡胶制品的基本生产工艺过程包括塑炼、混炼、压延、压出、成型、硫化6个基本工序。
橡胶的加工工艺过程主要就是解决塑性与弹性矛盾的过程,通过各种加工手段,使得弹性的橡胶变成具有塑性的塑炼胶,在加入各种配合剂制成半成品,然后通过硫化就是具有塑性的半成品又变成弹性高、物理机械性能好的橡胶制品。
2 橡胶加工工艺2、1塑炼工艺生胶塑炼就是通过机械应力、热、氧或加入某些化学试剂等方法,使生胶由强韧的弹性状态转变为柔软、便于加工的塑性状态的过程。
生胶塑炼的目的就是降低它的弹性,增加可塑性,并获得适当的流动性,以满足混炼、亚衍、压出、成型、硫化以及胶浆制造、海绵胶制造等各种加工工艺过程的要求。
掌握好适当的塑炼可塑度,对橡胶制品的加工与成品质量就是至关重要的。
在满足加工工艺要求的前提下应尽可能降低可塑度。
随着恒粘度橡胶、低粘度橡胶的出现,有的橡胶已经不需要塑炼而直接进行混炼。
在橡胶工业中,最常用的塑炼方法有机械塑炼法与化学塑炼法。
机械塑炼法所用的主要设备就是开放式炼胶机、密闭式炼胶机与螺杆塑炼机。
化学塑炼法就是在机械塑炼过程中加入化学药品来提高塑炼效果的方法。
开炼机塑炼时温度一般在80℃以下,属于低温机械混炼方法。
密炼机与螺杆混炼机的排胶温度在120℃以上,甚至高达160-180℃,属于高温机械混炼。
生胶在混炼之前需要预先经过烘胶、切胶、选胶与破胶等处理才能塑炼。
几种胶的塑炼特性:天然橡胶用开炼机塑炼时,辊筒温度为30-40℃,时间约为15-20min;采用密炼机塑炼当温度达到120℃以上时,时间约为3-5min。
丁苯橡胶的门尼粘度多在35-60之间,因此,丁苯橡胶也可不用塑炼,但就是经过塑炼后可以提高配合机的分散性顺丁橡胶具有冷流性,缺乏塑炼效果。
顺丁胶的门尼粘度较低,可不用塑炼。
橡胶的塑炼和混炼
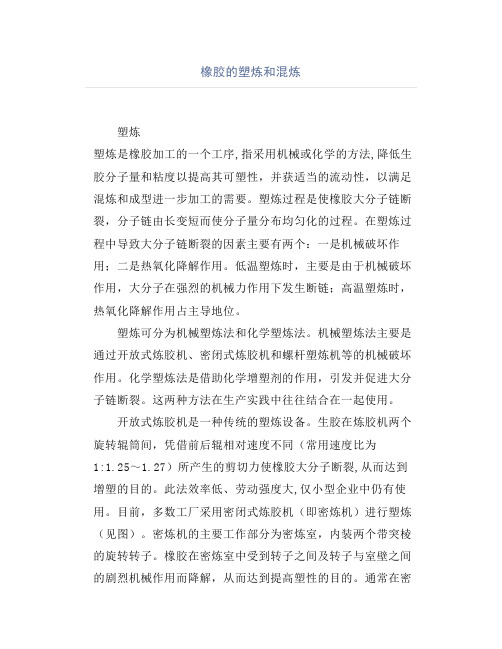
橡胶的塑炼和混炼塑炼塑炼是橡胶加工的一个工序,指采用机械或化学的方法,降低生胶分子量和粘度以提高其可塑性,并获适当的流动性,以满足混炼和成型进一步加工的需要。
塑炼过程是使橡胶大分子链断裂,分子链由长变短而使分子量分布均匀化的过程。
在塑炼过程中导致大分子链断裂的因素主要有两个:一是机械破坏作用;二是热氧化降解作用。
低温塑炼时,主要是由于机械破坏作用,大分子在强烈的机械力作用下发生断链;高温塑炼时,热氧化降解作用占主导地位。
塑炼可分为机械塑炼法和化学塑炼法。
机械塑炼法主要是通过开放式炼胶机、密闭式炼胶机和螺杆塑炼机等的机械破坏作用。
化学塑炼法是借助化学增塑剂的作用,引发并促进大分子链断裂。
这两种方法在生产实践中往往结合在一起使用。
开放式炼胶机是一种传统的塑炼设备。
生胶在炼胶机两个旋转辊筒间,凭借前后辊相对速度不同(常用速度比为1:1.25~1.27)所产生的剪切力使橡胶大分子断裂,从而达到增塑的目的。
此法效率低、劳动强度大,仅小型企业中仍有使用。
目前,多数工厂采用密闭式炼胶机(即密炼机)进行塑炼(见图)。
密炼机的主要工作部分为密炼室,内装两个带突棱的旋转转子。
橡胶在密炼室中受到转子之间及转子与室壁之间的剧烈机械作用而降解,从而达到提高塑性的目的。
通常在密炼机塑炼时还加入增塑剂(如五氯硫酚等)以缩短塑炼时间,提高塑炼效zx0塑炼胶的可塑性直接影响橡胶制品的性能,它主要根据混炼胶工艺性能和制品性能要求来确定。
一般来说,涂胶、浸胶、刮胶、擦胶用的胶料可塑性宜高些;模压用的胶料可塑性宜低些;供压出用的胶料,则介于两者之间。
生胶和塑炼胶的可塑性测试方法很多,中国最常用的方法为威氏塑性计和门尼粘度计。
威氏塑性计是将试样置入两块平行的板中,在一定负荷作用下,测定其压缩形变的大小,以及除去负荷后保持形变的能力。
所得的可塑度值在0~1之间;数值越大,表明可塑性也越大。
门尼粘度计是测定胶料在模腔内对粘度计转子转动所产生的剪切阻力,通常用ML来表示(1为胶料预热时间1min,4为转子转动时间4min,100为测试温度100℃),门尼粘度值一般为0~100,其数值越大,表明可塑性越小。
橡胶加工流程(原料-塑炼-混炼-硫化)

橡胶加工流程(原料-塑炼-混炼-硫化)1.基本工艺流程伴随现代工业尤其是化学工业的迅猛发展,橡胶制品种类繁多,但其生产工艺过程,却基本相同。
以一般固体橡胶(生胶)为原料的制品,它的生产工艺过程主要包括:原材料准备→塑炼→混炼→成型→硫化→修整→检验2.原材料准备橡胶制品的主要材料有生胶、配合剂、纤维材料和金属材料。
其中生胶为基本材料;配合剂是为了改善橡胶制品的某些性能而加入的辅助材料;纤维材料(棉、麻、毛及各种人造纤维、合成纤维)和金属材料(钢丝、铜丝)是作为橡胶制品的骨架材料,以增强机械强度、限制制品变型。
在原材料准备过程中,配料必须按照配方称量准确。
为了使生胶和配合剂能相互均匀混合,需要对某些材料进行加工:1.基本工艺流程伴随现代工业尤其是化学工业的迅猛发展,橡胶制品种类繁多,但其生产工艺过程,却基本相同。
以一般固体橡胶(生胶)为原料的制品,它的生产工艺过程主要包括:原材料准备→塑炼→混炼→成型→硫化→休整→检验2.原材料准备橡胶制品的主要材料有生胶、配合剂、纤维材料和金属材料。
其中生胶为基本材料;配合剂是为了改善橡胶制品的某些性能而加入的辅助材料;纤维材料(棉、麻、毛及各种人造纤维、合成纤维)和金属材料(钢丝、铜丝)是作为橡胶制品的骨架材料,以增强机械强度、限制制品变型。
在原材料准备过程中,配料必须按照配方称量准确。
为了使生胶和配合剂能相互均匀混合,需要对某些材料进行加工:生胶要在60--70℃烘房内烘软后,再切胶、破胶成小块;块状配合剂如石蜡、硬脂酸、松香等要粉碎;粉状配合剂若含有机械杂质或粗粒时需要筛选除去;液态配合剂(松焦油、古马隆)需要加热、熔化、蒸发水分、过滤杂质;配合剂要进行干燥,不然容易结块、混炼时旧不能分散均匀,硫化时产生气泡,从而影响产品质量;3.塑炼生胶富有弹性,缺乏加工时的必需性能(可塑性),因此不便于加工。
为了提高其可塑性,所以要对生胶进行塑炼;这样,在混炼时配合剂就容易均匀分散在生胶中;同时,在压延、成型过程中也有助于提高胶料的渗透性(渗入纤维织品内)和成型流动性。