模流分析成型条件设定依据
模流分析(MOLDFLOW)

一. 压力條件对产品的影响1.高保压压力能夠降低產品收縮的機會补充入模穴的塑料越多,越可避免產品的收縮高保压压力通常會造成产品不均勻收縮,而导致產品的翹曲变形对薄殼產品而言,由於壓力降更明顯,上述之情況更加嚴重2.Over packing 過保壓保壓壓力高,澆口附近體積收縮量少遠離澆口處保壓壓力低且體積收縮量較大導致產品翹曲變形,產品中央向四周推擠形成半球形(Dome Shape)3. Under packing 保壓不足澆口附近壓力低遠離澆口處壓力更低導致產品翹曲變形,產品中央向四周拉扯形成馬鞍形Twisted shape保壓時間如果夠長,足夠使澆口凝固,則可降低體積收縮的機會澆口凝固後,保壓效果就無效果一、澆口位置的要求:1.外观要求(浇口痕跡, 熔接线)2.產品功能要求3.模具加工要求4.產品的翹曲变形5.澆口容不容易去除二、对生产和功能的影响:1.流長(Flow Length)決定射出壓力,鎖模力,以及產品填不填的滿流長縮短可降低射出壓力及鎖模力2.澆口位置會影響保壓壓力保壓壓力大小保壓壓力是否平衡將澆口遠離產品未來受力位置(如軸承處)以避免殘留應力澆口位置必須考慮排氣,以避免積風發生不要將澆口放在產品較弱处或嵌入处,以避免偏位(Core Shaft)三、选择浇口位置的技巧1.將澆口放置於產品最厚處,從最厚處進澆可提供較佳的充填及保壓效果。
如果保壓不足,較薄的區域會比較厚的區域更快凝固避免將澆口放在厚度突然變化處,以避免遲滯現象或是短射的發生2.可能的話,從產品中央進澆將澆口放置於產品中央可提供等長的流長流長的大小會影響所需的射出壓力中央進澆使得各個方向的保壓壓力均勻,可避免不均勻的體積收縮射出量/切换点的影响射出量可由螺杆行程距离的設定決定射出量包括了填滿模穴需要的塑胶量以及保压時須填入模穴的塑膠量切換點是射出機由速度控制切換成壓力控制的點螺桿前进行程過短(切換點過早)會導致保壓壓力不足假如保压压力比所需射出壓力還低,產品可能发生短射PVT特性p –压力; v –比容; T –溫度描述塑胶如何随着压力及溫度的变化而发生体积上的变化。
模流分析资料

塑料流动行为一、塑料如何充填模穴射出成型射出成型的过程可分为三个阶段:●充填阶段;●加压阶段;●补偿阶段。
1、充填阶段充填阶段时塑料被射出机的螺杆挤入模穴中直到正好填满。
当我们要设计一个产品必须要使用到射出成型的制程时,最重要的是了解塑料充填的过程。
当塑料进入模穴时,塑料接触模壁时会很快的凝固,这会在模壁和熔融塑料之间形成凝固层。
下列的图显示塑料波前如何随着塑料往前推挤时而产生的扩张。
当流动波前到达模壁并凝固时,塑料分子在凝固层中没有很规则排列,一旦凝固,排列的方向性也无法改变。
红色箭头代表熔融塑料的流动方向,蓝色层代表凝固层,而绿色箭头代表熔融塑料向模具的传热方向。
2、加压阶段:在模穴充填满之后紧接着是加压阶段,虽然所有的流动路径在上一个阶段都已经充填完成,但其实边缘及角落都还有空隙存在。
为了完全充填整个模穴,所以必须在这个阶段加大压力将额外的塑料挤入模穴。
在下列图标中显示,模穴在充填阶段未期及加压阶段未期的差异,我们可以在左图的蓝色圆圈内看到未充填的死角。
注意:有时候“Confidence of Fill”的结果不能正确地预测短射,仍然显示良好的充填品质,但事实上可能有些区域不能被完全的充填。
这是因为浇口位置不适当而不能使全部的区域都能得到足够的保压。
3、补偿阶段:塑料从熔融状态冷凝固到固体时,会有大约25%的高收缩率,因此必须将更多的塑料射入模穴以补偿因冷却而产生的收缩,这是补偿阶段。
二、产品肉厚如何影响塑料流动“A flow leader and A flow deflector”定义:“A flow leader” 是指增加流动路径的肉厚以增加该路径的塑料流速。
“A flow deflector” 是指减少流动路径的肉厚以减少该路径的塑料流速。
Flow leaders 和Flow deflectors:Flow leaders 及Flow deflectors常常用来使模穴内各流动路径能在相同的时间内充填完(即流动平衡)。
成型条件设定与分析

三.射塑能力(Working Capacity)
unit:Kg:cm=射膠壓力(p Kg cm 2 )*行程容積
四.射出率:CM3/SEC
8/23
五.螺杆
三 二 一
47% 計量段
33% 壓縮段
19% 進料段
9/23
五.螺杆
螺杆應有一足夠長度以保証塑料的塑化均勻以 及為熱敏感材料保持一漸進之溫度差,一般L/D比為 16-22,較高之L/D比帶來額外之時間能源浪費,L/D 比小具有 效長度受影響,會影響塑化之均勻效果.
四.容模量
開模行程再加模具厚度即容模量
6/23
射出系統介紹
一.射塑量
實際射膠量=理論射膠量*行程效率(P) P 0.8-0.95(依塑膠流動性而言)
另止逆閥也無法達到100%的功能
一般成型制品重量約為最大注射量之30%-70%
二.射塑壓力
對相同之油壓系統而言,小螺杆之射壓高於大螺杆之 射壓.
7/23
上課對象﹕成型加工與模具維修職系師4以下人員
講 師:模具維修師1(含)以上資位 職系 上課時間:共2小時 課程特色:成型條件設定的基本觀念,成型條件的優化.
3/23
成型系統介紹
成型四要素:
成型品
鎖模體統
模具
材料
射出系統
電控系統
4/23
鎖模系統介紹
一.鎖模力(Clamping Force)
鎖模力F=P1*投影面積 鎖模力F=P1*投影面積
七.螺杆轉速
塑料供應商一般均會提供適當之RPM以供參考,而螺 杆之尺寸大小也會影響RPM的選擇. 小螺杆:槽深較淺所以塑料吸收熱源快,足夠促使逆料 在壓縮段段的軟化.另螺杆與料管壁間摩擦熱能低.所以可 用較高的RPM增加塑化能力. 大螺杆:反之,不適合高RPM應免塑化不均勻及造成過 大摩擦熱. 11/23
模流分析(CAE)管理制度

5-3-2. 模具设计阶段的分析优化流程5-3-3. 注塑成型阶段的分析优化流程5-4. 制作模流分析报告分析优化结束后,需将分析结果及改善建议,以Powerpoint的格式制作成《模流分析报告》,以供相关人员查阅和参考。
5-4-1. 报告的主要内容标准的模流分析报告一般应包含以下内容:5-4-1-1.报告封面:需注明产品名称、模具编号、CAE工程师、报告日期,并附产品图片;5-4-1-2. 分析说明:需注明分析目的、分析内容,以及分析所使用的塑胶材料名称;5-4-1-3. 产品介绍:需对产品做详细的壁厚分析,并提出设计不合理的地方;5-4-1-4. 材料介绍:需详细列出材料物性的各项数据;5-4-1-5. 浇注系统:进浇位置、浇口类型、流道排布情况;5-4-1-6. 冷却系统:水路温度、水路排布情况;5-4-1-7. 成型条件:温度设定、充填设定、保压设定;5-4-1-8. 充填时间:产品成型时的流动情况(须为动画图档);5-4-1-9. 最大注射压力:产品成型时所需的最大注射压力;5-4-1-10. 熔胶波前温度:产品成型时熔胶波前温度的分布情况;5-4-1-11.注射压力曲线:注射咀位置压力变化曲线;5-4-1-12.锁模力曲线:锁模力变化曲线;5-4-1-13.顶出时体积收缩:产品成型后顶出时的体积收缩大小;5-4-1-14.困气:产品成型后的困气位置;5-4-1-15.熔接线:产品成型后的熔接线位置;5-4-1-16.变形:产品成型后的变形大小和方向;5-4-1-17.总结:将所有的分析结果进行概括总结,并指出各方案的优劣;5-4-1-18.建议:明确提出建议方案,针对相关问题点提出改善建议。
5-4-2. 报告的命名规则模具编号(如:H1001)+产品名称+版次(如:A、B、C…)5-4-3. 报告的存放路径文件服务器\CAE\模具编号\5-5. 案例统计每个分析任务结束后,需将《CAE分析需求单》装订存档,并及时更新《CAE分析案例统计表》,以便今后对其进行查询和跟踪。
塑料零件模流分析教程
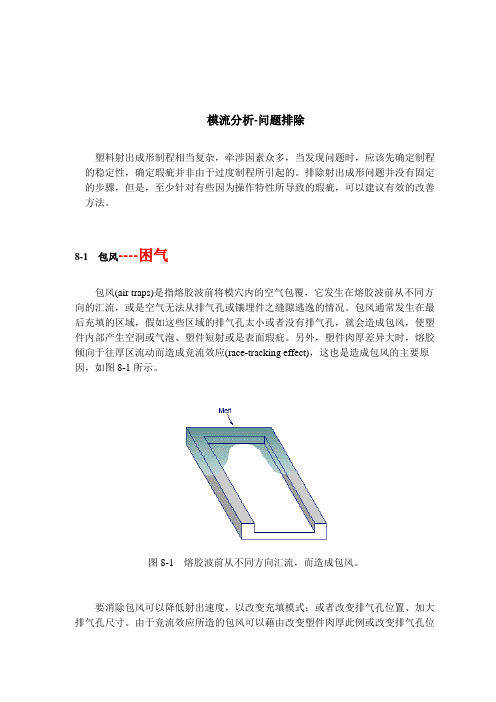
模流分析-问题排除塑料射出成形制程相当复杂,牵涉因素众多,当发现问题时,应该先确定制程的稳定性,确定瑕疵并非由于过度制程所引起的。
排除射出成形问题并没有固定的步骤,但是,至少针对有些因为操作特性所导致的瑕疵,可以建议有效的改善方法。
8-1 包风----困气包风(air traps)是指熔胶波前将模穴内的空气包覆,它发生在熔胶波前从不同方向的汇流,或是空气无法从排气孔或镶埋件之缝隙逃逸的情况。
包风通常发生在最后充填的区域,假如这些区域的排气孔太小或者没有排气孔,就会造成包风,使塑件内部产生空洞或气泡、塑件短射或是表面瑕疪。
另外,塑件肉厚差异大时,熔胶倾向于往厚区流动而造成竞流效应(race-tracking effect),这也是造成包风的主要原因,如图8-1所示。
图8-1 熔胶波前从不同方向汇流,而造成包风。
要消除包风可以降低射出速度,以改变充填模式;或者改变排气孔位置、加大排气孔尺寸。
由于竞流效应所造的包风可以藉由改变塑件肉厚此例或改变排气孔位置加以改善排气问题。
包风的改善方法说明如下:(1)变更塑件设计:缩减肉厚比例,可以减低熔胶的竞流效。
(2) 应变更模具设计:将排气孔设置在适当的位置就可以改善排气。
排气孔通常设在最后充饱的区域,例如模具与模具交接处、分模面、镶埋件与模壁之间、顶针及模具滑块的位置。
重新设计浇口和熔胶传送系统可以改变充填模式,使最后充填区域落在适当的排气孔位置。
此外,应确定有足够大的排气孔,足以让充填时的空气逃逸;但是也要小心排气孔不能太大而造成毛边。
建议的排气孔尺寸,结晶性塑料为0.025厘米(0.001英吋),不定形塑料为0.038厘米(0.0015英吋)。
(3)调整成形条件:高射出速度会导致喷射流,造成包风。
使用较低的射出速度可以让空气有充足的时间逃逸。
8-2 黑斑、黑纹、脆化、烧痕、和掉色黑斑(black specks)和黑纹(black streaks)是在塑件表面呈现的暗色点或暗色条纹,如图8-2所示。
Moldflow成型条件设定
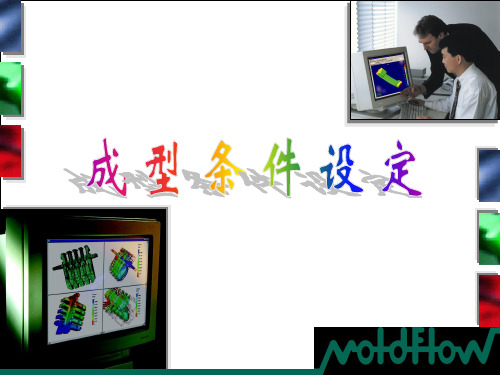
产品内外表面的冷却不均,导致产品产生翘曲,减小此翘曲的方法是使 公母模的冷却均匀,解决方法: 调整冷却水管排布 调整冷却液温度 在积热的地方加强冷却
收 缩 不 均
产品不同区域的收缩大小不一,所以不同区域之间产生内应力,致使产 品产生翘曲。
中间收缩大于四周,产生马鞍形翘曲。
产品各区域收缩不均导致变形, 解决方法: 调整保压曲线 修改产品设计
判断结果
在Buckling和Automatic的分析结果Screen out中会给出一个叫 Lambda的参数,根据这个参数,按照下列原则就可以判断材料是否 屈服:
Lambda<1: 材料出现屈服,用Large Deflection Lambda>1: 材料未出现屈服,用Small Deflection
•Flow - Cool - Flow - Warp (FCFW)
–冷却分析采用料到达此元素时的即时温度做为初始的 料温
–即时温度是用假设的恒定及统一的模温计算出来的
最佳分析序列
哪个序列是最佳的分析序列?
•FCFW 在流动分析的初始时假设恒定的模温
•CFW 假设冷却分析时的初始料温为常温 •对于翘曲的预测,假设恒定的料温比假设恒定模 温预测的更精确
变形的原因
塑料在成形过程中,由于温度、压力等因素 的影响,在材料分子之间产生很大的内应力,在 这种内应力的作用下,产品就产生了变形翘曲。 在应力和应变之间存在着一种特定的关系, 每种材料都不相同。 下面首先从理论上讲述一下应力和应变的关 系。
理想弹性变形
材料在受到应力的作用下会发 生变形,理想的弹性材料应力-应变 如右图所示,应变随着应力的增大 而增大,且成正比(线性)关系。
–因此CFW 是首选的运行序列
Moldflow设计原则

注塑成型流动行为设计原则注塑成型流动行为设计原则注射成型注射成型注塑成型机注塑成型机锁模单元液压单元Hopper 漏斗Screw (Ram)螺杆Barrel 料筒Heaterbands电热器来自外部单元的模具冷却在料筒和模具之间的喷嘴Nozzle (不显示)冷却时间开模时间充填时间保压时间注塑成型周期注塑成型周期周期时间充填时间保压时间冷却时间开模时间22秒19102注塑成型周期注塑成型周期充填Filling–模具闭合,螺杆快速向前移动,在模穴壁形成凝固塑料皮层保压Packing(保持Holding)–模穴填满,保压开始,冷却开始漏斗料筒螺杆模具螺杆对熔融塑料施加一定的压力使更多的塑料进入模穴内,这也称为“补偿阶段”。
注塑成型过程注塑成型过程冷却Cooling–保压完成,浇口凝固关闭,冷却继续–螺杆快速后移,开始为下一次注射塑炼树脂 开模Mold Open –冷却完成,模具打开注塑成型过程注塑成型过程注塑模具注塑模具固定侧可动侧流动行为流动行为在注塑模具中一个塑料分子会做些什么?充填阶段加压阶段补偿阶段Filling ,计量的充填模穴Pressurization ,建立模穴压力Compensation ,挤入额外的塑料以减少收缩成型各阶段成型各阶段喷泉流动喷泉流动描述塑料在一个模具中的流动现象首先进入的材料出现在浇口附近的表面最后进入模穴的材料,在中心层的熔融塑料下游出现对分子和在产品表面的纤维配向有直接的影响分子配向由剪切流动引起。
在凝固层剪切量高,因此导致最高的配向。
流动截面/分子配向流动截面/分子配向剪切率最小最大张力张力低配向高配向由剪切流动产生的热输入和进入模具的热损失之间应该是平衡的。
冷的模具热的熔融塑料热损失进入模具高剪切率热输入塑料流凝固层较快的注射速率较慢的注射速率对比流动截面/热交换流动截面/热交换注射时间/凝固层厚度注射时间/凝固层厚度较短的注射时间将会生产较薄的凝固层及较大的流动通道。
模流分析实验报告(3篇)
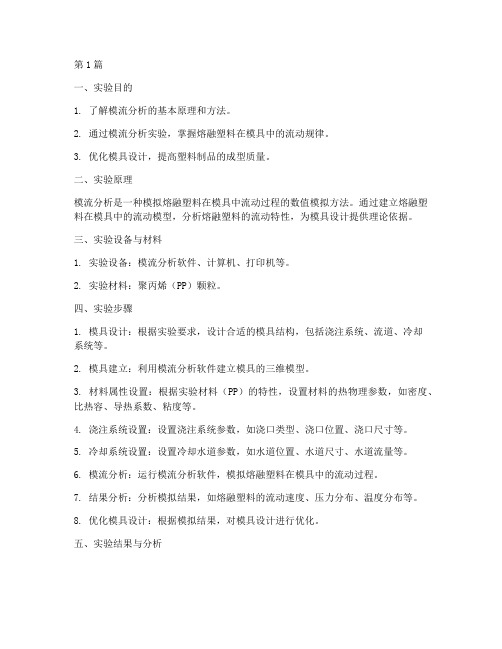
第1篇一、实验目的1. 了解模流分析的基本原理和方法。
2. 通过模流分析实验,掌握熔融塑料在模具中的流动规律。
3. 优化模具设计,提高塑料制品的成型质量。
二、实验原理模流分析是一种模拟熔融塑料在模具中流动过程的数值模拟方法。
通过建立熔融塑料在模具中的流动模型,分析熔融塑料的流动特性,为模具设计提供理论依据。
三、实验设备与材料1. 实验设备:模流分析软件、计算机、打印机等。
2. 实验材料:聚丙烯(PP)颗粒。
四、实验步骤1. 模具设计:根据实验要求,设计合适的模具结构,包括浇注系统、流道、冷却系统等。
2. 模具建立:利用模流分析软件建立模具的三维模型。
3. 材料属性设置:根据实验材料(PP)的特性,设置材料的热物理参数,如密度、比热容、导热系数、粘度等。
4. 浇注系统设置:设置浇注系统参数,如浇口类型、浇口位置、浇口尺寸等。
5. 冷却系统设置:设置冷却水道参数,如水道位置、水道尺寸、水道流量等。
6. 模流分析:运行模流分析软件,模拟熔融塑料在模具中的流动过程。
7. 结果分析:分析模拟结果,如熔融塑料的流动速度、压力分布、温度分布等。
8. 优化模具设计:根据模拟结果,对模具设计进行优化。
五、实验结果与分析1. 熔融塑料的流动速度:在模具入口处,熔融塑料的流动速度较大,随着流动距离的增加,流动速度逐渐减小。
在模具的狭窄部位,流动速度较大,而在宽大部位,流动速度较小。
2. 压力分布:在模具的狭窄部位,压力较大,而在宽大部位,压力较小。
在浇口处,压力最大。
3. 温度分布:在模具的冷却水道附近,温度较低,而在模具的加热部位,温度较高。
4. 优化模具设计:根据模拟结果,对模具设计进行优化,如调整浇口位置、改变冷却水道尺寸等。
六、实验结论1. 模流分析实验能够有效地模拟熔融塑料在模具中的流动过程,为模具设计提供理论依据。
2. 通过对模拟结果的分析,可以优化模具设计,提高塑料制品的成型质量。
3. 模流分析实验有助于缩短新产品开发周期,降低产品开发成本。
压铸模具模流分析报告解析
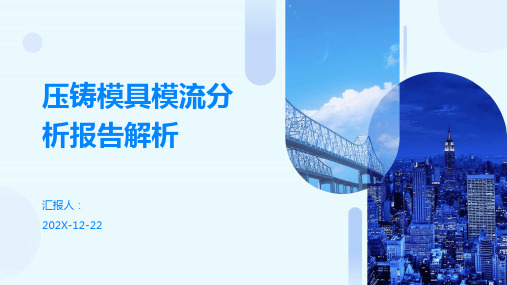
热处理可以改善模具材料的力学性能和耐热性,提高模具的使用寿命。报告中 应分析热处理工艺是否合理,是否达到预期的力学性能和使用寿命等。
模具制造工艺分析
粗加工工艺
粗加工是模具制造的第一道工序,其工艺直接影响到后续的精加工和装配。报告 中应分析粗加工工艺是否合理,是否能够保证模具零件的精度和表面质量等。
压铸模具模流分析将与多个领域进行交 叉融合,如机械、材料、电子等,形成 跨行业的合作模式,共同推动压铸模具 技术的发展。
VS
多元化应用
压铸模具模流分析不仅应用于汽车、摩托 车等制造领域,还将拓展到航空航天、新 能源等领域,实现多元化应用。
绿色环保和可持续发展要求
环保材料应用
随着环保意识的提高,压铸模具将更多地采 用环保材料,如可回收材料、生物降解材料 等,降低对环境的影响。
智能化和自动化程度提高
智能化技术应用
随着人工智能、大数据等技术的不断发展,压铸模具模流分析将更加智能化,实现自动 化数据收集、处理和分析,提高分析效率和准确性。
自动化生产流程
通过引入自动化设备和系统,实现压铸模具生产流程的自动化,减少人工干预,提高生 产效率和产品质量。
多领域交叉融合发展
跨行业合作
提高产品质量
通过优化模具设计和调整工艺参数,提高产 品质量和稳定性。
降低生产成本
通过减少废品率、提高生产效率等手段,降 低生产成本。
缩短产品研发周期
通过模流分析,可以更快地确定模具设计方 案和工艺参数,缩短产品研发周期。
03
CATALOGUE
压铸模具模流分析报告解析
模具结构分析
模具类型
分析报告中应包含模具类型的详细描述,例如单分型面模 具、多分型面模具等。
注塑模具的模流分析

注塑模具的模流分析注塑模具的模流分析是指在注塑模具设计阶段,通过模具的数值模拟计算和分析,得出注塑成型过程中的流动状态。
模流分析可以帮助制造商预测并优化注塑成型过程,以确保产品质量和生产效率。
下面将介绍注塑模具的模流分析的重要性、分析内容及步骤,并分享一些模流分析的实际应用案例。
一、注塑模具模流分析的重要性1.预测成型缺陷通过模流分析,可以预测成型缺陷,如短射、气泡、翘曲等,帮助制造商在实际生产前就能够发现潜在的问题并加以改进,减少不良品率。
2.优化模具结构模具结构对注塑成型过程的影响很大,通过模流分析可以确定最佳的模具结构,如冷却系统的设计、料斗和浇口的位置等,从而提高成型效率和产品质量。
3.提高产品质量模流分析能够帮助设计师预测和优化填充过程,从而避免成型缺陷,提高产品质量。
4.节约成本通过模流分析可以调整注塑工艺参数,如注射速度、注射压力等,达到最佳注塑效果,减少成本。
二、注塑模具模流分析的内容1.塑料材料流动模拟模流分析可预测塑料在模腔内部的流动速度、温度分布和填充情况,以及预测和防止可能出现的缺陷,如短射、气泡、翘曲等。
2.模具温度分析通过模流分析,可以优化模具的冷却系统设计,确保模具在注塑过程中能够保持合适的温度,提高成型效率和产品质量。
3.油压分析注塑模具中的油压对模具的开合速度和稳定度影响很大,模流分析可以帮助设计师优化油压系统,确保模具运行平稳。
三、注塑模具模流分析的步骤1.准备模具CAD模型和相关参数首先需要准备注塑模具的CAD模型及相关参数,如材料特性、注射机参数等。
2.进行模型网格划分将模具CAD模型划分成网格,以便进行计算和分析。
3.设置材料和物理参数设置塑料材料的流变性能和热物理参数。
4.设定模具填充流动条件设定注塑过程中的注射速度、压力、温度等参数。
5.进行模流计算和分析通过计算机软件进行模流计算和分析,得出注塑成型过程中的填充情况、温度分布、压力分布等信息。
6.优化设计和参数调整根据模流分析结果,对模具结构和工艺参数进行优化和调整,以改进产品质量和生产效率。
模流分析解析(详细)-by-heyy
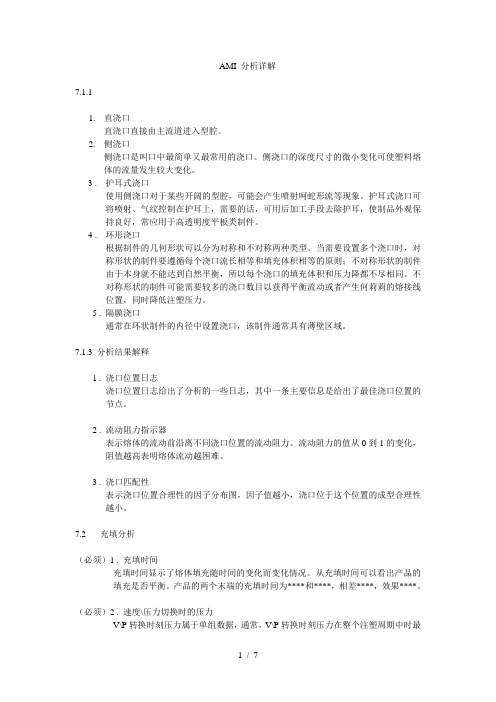
AMI 分析详解7.1.11.直浇口直浇口直接由主流道进入型腔。
2.侧浇口侧浇口是叫口中最简单又最常用的浇口。
侧浇口的深度尺寸的微小变化可使塑料熔体的流量发生较大变化。
3 . 护耳式浇口使用侧浇口对于某些开阔的型腔,可能会产生喷射呵蛇形流等现象。
护耳式浇口可将喷射、气纹控制在护耳上,需要的话,可用后加工手段去除护耳,使制品外观保持良好,常应用于高透明度平板类制件。
4 . 环形浇口根据制件的几何形状可以分为对称和不对称两种类型。
当需要设置多个浇口时,对称形状的制件要遵循每个浇口流长相等和填充体积相等的原则;不对称形状的制件由于本身就不能达到自然平衡,所以每个浇口的填充体积和压力降都不尽相同。
不对称形状的制件可能需要较多的浇口数目以获得平衡流动或者产生何莉莉的熔接线位置,同时降低注塑压力。
5 . 隔膜浇口通常在环状制件的内径中设置浇口,该制件通常具有薄壁区域。
7.1.3 分析结果解释1 . 浇口位置日志浇口位置日志给出了分析的一些日志,其中一条主要信息是给出了最佳浇口位置的节点。
2 . 流动阻力指示器表示熔体的流动前沿离不同浇口位置的流动阻力。
流动阻力的值从0到1的变化,阻值越高表明熔体流动越困难。
3 . 浇口匹配性表示浇口位置合理性的因子分布图,因子值越小,浇口位于这个位置的成型合理性越小。
7.2充填分析(必须)1 . 充填时间充填时间显示了熔体填充随时间的变化而变化情况。
从充填时间可以看出产品的填充是否平衡。
产品的两个末端的充填时间为****和****,相差****,效果****。
(必须)2 . 速度\压力切换时的压力V\P转换时刻压力属于单组数据,通常,V\P转换时刻压力在整个注塑周期中时最高的,此时的压力大小和分布可以在图中读出,同时,未填充区域在图中以灰色显示。
(必须)3 . 流动前沿温度流动前沿温度是指熔体充填前沿中间层的温度,是熔体达到某节点的瞬时温度。
此温度要求分布均匀。
4 . 总体温度是中间结果数据,在静止状态时,是简单平均温度,在流动状态时,是考虑剪切速率的加权平均温度。
成型条件分析与设定课件
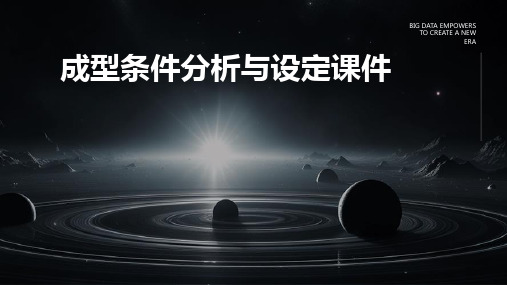
01
成型条件分析的重要性
BIG DATA EMPOWERS TO CREATE A NEW
ERA
定义与特点
成型条件分析是指对产品制造过程中各种因素的影响程度进行分析,以确定最佳的 成型工艺和条件。
成型条件分析需要考虑材料、工艺、设备、环境等因素,以及它们之间的相互作用 。
成型条件分析的特点包括系统性、综合性、实践性等。
05
成型条件与模具设计的关系
BIG DATA EMPOWERS TO CREATE A NEW
ERA
模具类型与成型条件的关系
注塑模具
适用于热塑性塑料,可快速生产 ,但模具成本高,不合适小批量
生产。
压铸模具
适用于铝合金、锌合金等金属材 料,生产效率高,但模具成本也
较高。
挤出模具
适用于塑料、橡胶等材料的连续 生产,成本低,但生产效率相对
公道安排生产计划
根据设备能力和生产需求,公道安排生产计划,避免设备闲置和过 度使用。
提高员工技能水平
通过培训和技能提升,提高员工的操作技能水平,减少操作失误和设 备故障。
07
成型条件与产品成本的关系
BIG DATA EMPOWERS TO CREATE A NEW
ERA
材料成本的控制方法
优化产品设计
成型条件分析与设定课件
BIG DATA EMPOWERS TO CREATE A NEW
ERA
• 成型条件分析的重要性 • 成型条件分析的方法 • 成型条件对产品性能的影响 • 成型条件的设定与调整 • 成型条件与模具设计的关系 • 成型条件与生产效率的关系 • 成型条件与产品成本的关系
目录
CONTENTS
优化模具设计和成型工艺条件,以提 高制品的表面质量和光洁度。对于外 观要求高的制品,可以采用抛光、喷 涂、贴膜等后处理工艺来提高其美观 度和使用感受。同时,注意控制原材 料的质量和稳定性,以避免因原材料 波动导致的产品外观问题。
《模流分析》课程标准
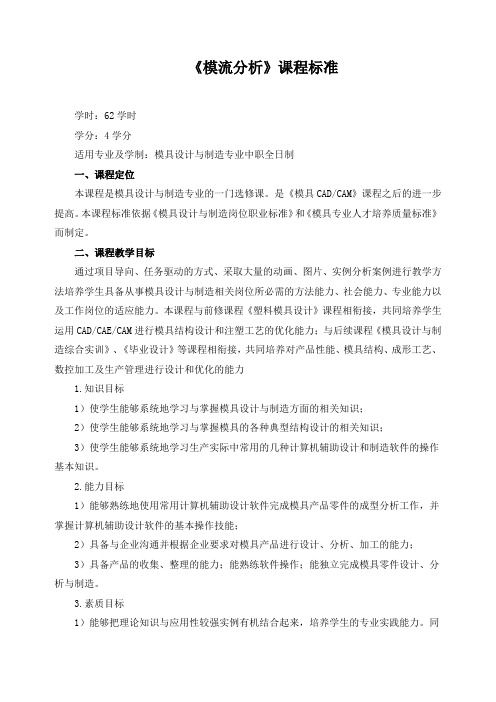
《模流分析》课程标准学时:62学时学分:4学分适用专业及学制:模具设计与制造专业中职全日制一、课程定位本课程是模具设计与制造专业的一门选修课。
是《模具CAD/CAM》课程之后的进一步提高。
本课程标准依据《模具设计与制造岗位职业标准》和《模具专业人才培养质量标准》而制定。
二、课程教学目标通过项目导向、任务驱动的方式、采取大量的动画、图片、实例分析案例进行教学方法培养学生具备从事模具设计与制造相关岗位所必需的方法能力、社会能力、专业能力以及工作岗位的适应能力。
本课程与前修课程《塑料模具设计》课程相衔接,共同培养学生运用CAD/CAE/CAM进行模具结构设计和注塑工艺的优化能力;与后续课程《模具设计与制造综合实训》、《毕业设计》等课程相衔接,共同培养对产品性能、模具结构、成形工艺、数控加工及生产管理进行设计和优化的能力1.知识目标1)使学生能够系统地学习与掌握模具设计与制造方面的相关知识;2)使学生能够系统地学习与掌握模具的各种典型结构设计的相关知识;3)使学生能够系统地学习生产实际中常用的几种计算机辅助设计和制造软件的操作基本知识。
2.能力目标1)能够熟练地使用常用计算机辅助设计软件完成模具产品零件的成型分析工作,并掌握计算机辅助设计软件的基本操作技能;2)具备与企业沟通并根据企业要求对模具产品进行设计、分析、加工的能力;3)具备产品的收集、整理的能力;能熟练软件操作;能独立完成模具零件设计、分析与制造。
3.素质目标1)能够把理论知识与应用性较强实例有机结合起来,培养学生的专业实践能力。
同时使学生对专业知识职业能力有深入的理解,尤其使学生对计算机辅助设计与制造模具的理念与实际技能有明显提高;2)通过知识教学的过程培养学生爱岗敬业、乐于吃苦、勇于奉献与团队合作的基本素质;3)提高拓展学习模块(课外),培养学生自学和举一反三的创新思维能力。
三、课程教学单元及学时安排四、课程教学设计1.整体教学设计本课程遵循学生职业能力培养的基本规律,基于模具岗位职业标准和工作过程,以校企合作中典型模具为载体,在“做中教、做中学”的理念,让学生在完成任务过程中教会学生运用模具CAD/CAM知识完成制品的几何造型、模具结构的三维设计后运用模流分析进行工程试验、分析、文件生成。
Moldflow设计指南——MF充模图与MF设计原则
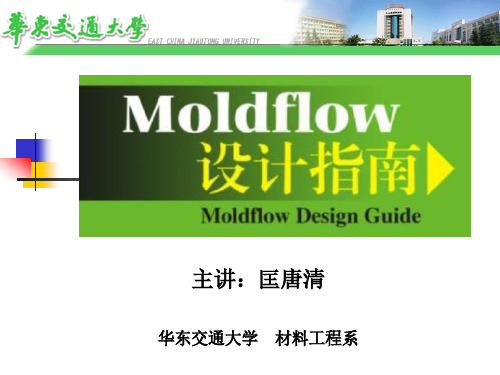
熔体在复杂模腔内的流动
注射速率
慢速充填,传热主导,流动路径形 成较厚冻结层,流动阻力增大,薄 壁区充填困难,易引发困气
快速充填,流动主导,冻结层较 薄,利于薄壁区充填
可通过提高料温/模温从而 减少充填过程中冻结层的 厚度,保证顺利充填
熔体充模图
熔体在复杂模腔内的流动
潜流现象
熔接线形成后,冻结层厚度增加,冻 结层下的熔体继续流动,其方向发生 改变,与充模等值线不垂直,表明内 外取向不一致,即为潜流 潜流会影响制件表观质量,也影响其 结构性能
Moldflow流动观
平衡熔体流动
模腔内所有的流动路径应同时等压完成充填 多腔模各型腔同时充满 自然平衡(几何平衡)
在喷嘴和所有模腔之间的距离和状况相同 成型窗口更宽
Moldflow 设计原则
Moldflow流动观
平衡熔体流动
人工平衡
通过改变流道尺寸获得流动平衡 比自然平衡具有更小的流道体积 成型窗口比自然平衡一般要小得多。通常注射时间是主要 限制因素。最长流长与最短流长之比越大,潜在问题越大 。
充模图简介
表示熔体的充模过程,充模分析的关键指标之 一,是发现充模问题的重要依据
等值线图,线间距的疏密 表明充填的快慢
云图
熔体充模图
熔体在复杂模腔内的流动
过压
熔体流动不平衡导致,熔体总是优先充填阻力小的 区域,先充填区域即处于过保压 是引发翘曲变形的重要原因之一
过保压区缓慢充填,冻结层厚度稳步增加,流动与冻结同 时存在,横截面上具有不同的分子取向,形成局部应力 过保压区分子取向高,未过保压区分子取向低,造成整体 收缩不均和应力分布不均,导致最终的翘曲
MOLDFLOW模具分析技术基础

MOLDFLOW模具分析技术基础1.1注塑成型基础知识所谓注塑成型是指将已加热熔化的材料喷射注入到模具内,经由冷却与固化后,得到成品的方法.在树脂原料经由注塑机注塑成型变为塑料制品的整个过程中,包含下列几个部分.1.计量:为了成型一定大小的塑件,务必使用一定量的颗粒状塑料,这就需要计量.2.塑化:为了将塑料充入模腔,就务必使其变为熔融状态,流过充入模腔.3.注塑充模:为了将熔融塑料充入模腔,就需要对熔融塑料施加注塑压力,注入模腔.4.保压增密:熔融塑料充满模腔后,向模腔内补充因制品冷却收缩所需的物料.5.制品冷却:保压结束后,制品开始进入冷却定型阶段.6.开模:制品冷却定型后,注塑机的合模装置带动模具动模部分与定模部分分离.7.顶件:注塑机的顶出机构顶出塑件.8.取件:通过人力或者机械手取出塑件与浇注系统冷凝料等.9.闭模:注塑机的合模装置闭合并锁紧模具.1.2注塑成型机注塑成型机可分为柱塞式与螺杆式两种,这两种注塑成型机都是由注塑系统,锁模系统与模具构成..1.2.1注塑系统注塑系统是注塑机的要紧构成部分.它能够使树脂原料在注塞或者螺杆的推动或者旋转推进下均匀塑化,在高压下快速注入模具,注塑系统包含加料装置,料筒,螺杆或者柱塞,喷嘴,加压与驱动装置等.1.2.2锁模系统注塑机上实现锁合模具,启闭模具与顶出制件的机构称之锁模系统.熔料在高压下注入模具,务必施加足够大的锁模力才能保证模具严密闭合不溢料,锁模结构还应保证模具启闭灵活,准确,迅速与安全,并防止损坏模具与制件,避免机械受到强烈震动,达到安全运行以延长机器与模具的使用寿命.1.2.3模具模具是为了将树脂原料做成某种形状而用来承接射出树脂的部件.注塑模具要紧由浇注系统,成型零件与结构零件构成.1.3注塑成型过程在注塑过程的塑化,填充,保压与冷却这四个要紧阶段中,起要紧作用的工艺参数也随着注塑过程的变化而变化.1.塑化塑化是指塑料在料筒内经加热达到良好可塑性的流淌状态的全过程.塑化是注塑成型的准备阶段.熔体在进入模腔之前应达到规定的成型温度,并能在规定时间内达到足够数量,熔体温度应均匀一致,不发生或者极少发生热分解以保证生产的连续进行.2.填充这一阶段从柱塞或者螺杆开始向前移动起,直至模腔被塑料熔体充满为止.填充过程中包含的重要工艺参数有:熔体温度,注塑压力,填充时间.充模刚开始一段时间内模腔中没有压力,待模腔充满时,料流压力迅速上升达到最大值.充模的时间与模塑压力有关,充模时间长,先进入模内的塑料受到较多的冷却,粘度增大,后面的塑料就需要在较高的压力下才能进入模腔,反之,所需的压力则较小.在前一情况下,由于塑料受到较高的剪切应力,分子定向程度比较大.这种现象假如保留到料温降低至软化点以后,则制品中冻结的定向分子将使制品具有各向异性.这种制品在温度变化较大的使用过程中会出现裂纹,裂纹的方向与分子定向方向是一致的.而且,制品的热稳固性也较差,这是由于塑料的软化点随着分子定向程度增高而降低.高速充模时,塑料熔体通过喷嘴,主流道,分流道与浇口时产生较多的摩擦而使料温升高,这样当压力达到最大值时,塑料熔体的温度就能够保持较高的值,分子定向程度可减少,制品熔接强度也提高.充模过快时,在嵌件后部的熔接往往不好,致使制品强度变劣.3.保压这是指从熔体充满模腔时起,至柱塞或者螺杆撤回时为止的一段时间.保压阶段包含的重要工艺参数有:保压压力,保压时间.保压阶段中,塑料熔体因受到冷却而发生收缩,但因塑料仍然处于柱塞或者螺杆的稳压下,料筒内的熔料会被继续注入模腔内补足因收缩而留出的空隙,假如柱塞或者螺杆停在原位不动,压力曲线就会略有衰减;假如柱塞或者螺杆保持压力不变,也就是随着熔料入模的同时向前做少许移动,则在此段中模内压力维持不变.如今压力曲线与时间轴平行.压实阶段关于提高制品的密度,降低收缩与克服制品表面缺陷都有影响.此外,由于塑料还在流淌,而且温度又在不断下降,定向分子容易被冻结,因此这一阶段是大分子定向形成的要紧阶段.这一阶段拖延时间愈长,分子定向程度也将愈大.4.冷却这一阶段是指从浇口的塑料完全冻结时起,到制品从模腔中顶出时为止.冷却阶段包含的重要工艺参数是冷却时间冷却时模腔内压力迅速下降,模腔内塑料在这一阶段内要紧是继续冷却,以便制品在脱模时具有足够的刚度而不致发生扭曲变形.在这一阶段内,虽无塑料从浇口流出或者流入,但模内还可能有少量的塑料流淌,因此到制品脱模时,模内压力不一定等于外界压力,模内压力与外界压力的差值成为残余压力.残余压力的大小与压实阶段的时间长短有密切关系.残余压力为正值时,脱模比较困难,制品容易被刮伤或者破裂;残余压力为负值时,制品表面容易有陷痕或者内部有真空泡.因此,只有大残余压力接近零时,脱模才比较顺利,并能够获得满意的制品.1.4注塑成型工艺条件注塑成型工艺条件要紧包含温度,压力与时间等1.温度注塑成型过程中的温度要紧有熔料温度与模具温度.熔料温度影响塑化与注塑充模,模具温度影响充模与冷却定型.熔料温度指塑化树脂的温度与从喷嘴射出的熔体温度,前者称之塑化温度,后都称之熔体温度.由此看来,熔料温度取决于料筒与喷嘴两部分的温度.熔料温度的高低决定熔体流淌性能的好坏.熔料温度高,熔体的粘度小,流淌性能好,需要的注塑压力小,成型后的制件表面光洁度好,出现熔接痕,缺料的可能性就小.反之熔料温度低,就会降低熔体的流淌性能,会引起表面光洁度低,缺料,熔接痕明显缺陷.但是熔料温度过高会引起材料热降解,导致材料物理与化学性能降低.模具温度是指与制品接触的模腔表面温度.模具温度直接影响熔体的充模流淌行为,制件的冷却速度与制件最终质量.提高模具温度能够改善熔体在模腔内的流淌性,增强制件的密谋与结晶度与减小充模压力与制件中的压力.但是,提高模具温度会增加制件的冷却时间,增大制件收缩率与脱模后的翘曲,制件成型周期也会由于冷却时间的增加而变长,降低了生产效率.降低模具温度,尽管能够缩短冷却时间,提高生产率,但是,会降低熔体在模腔内的流淌能力,并导致制件产生较大的内应力或者者形成明显的熔接痕等制件缺陷.2.压力注塑过程中的压力要紧有注塑压力,保压压力与背压注塑压力是指螺杆或者者柱塞沿轴向前移时,其头部向塑料熔体施加的压力.它要紧用于克服熔体在成型过程中的流淌阻力,还对熔体起一定程度的压实作用.注塑压力对熔体的流淌,充模及制件质量都有很大影响.注塑压力的大小取决于制件成型树脂原料的品种,制件的复杂度,壁厚,喷嘴的结构形式,模具浇口的类型与尺寸与注塑机类型等因素.保压压力是指对模腔内树脂熔体进行压实与保护向模腔内进行补料流淌所需要的压力.保压压力是重要的注塑工艺参数之一,保压压力与保压时间的选择直接影响注塑制品的质量,保压压力与注塑压力一样由液压系统决定.在保压初期,制品重量随保压时间而增加,达到一定时间不再增加.延长保压时间有助于减少制品的收缩率,但过长的保压时间会使制品两个方向上的收缩率程度出现差异.令制品各个方向上的内应力差异增大,造成制品翘曲,粘模.在保压压力及熔体温度一定时,保压时间的选择应取决于浇口凝固时间.背压是指螺杆顶部熔料在螺杆转动后退时对其施加的反向压力.增大背压能够排出原料中的空气,提高熔体密实程度,还会增大熔体内的压力,螺杆后退速度减小,塑化过程的剪切作用加强,摩擦热增多,熔体温度上升,塑化效果提高.但是背压增大后,假如不相应提高螺杆转速,那么,熔体在螺杆计量段螺槽中将会产生较大的逆流与漏流,从而使塑化能力下降.背压的大小与制件成型树脂原料品种,喷嘴种类与加料方式有关.3.时间注塑成型周期要紧由注塑时间Ti,保压时间Tp,冷却时间Tc,开模时间To构成.th为TP与TC之与.注塑时间是指注塑活塞在注塑油缸内开始向前运动直至模腔被全部充满为止所经历的时间.保压时间为从模腔充满后开始,到保压结束为止所经历的时间.注塑时间与保压时间由制件成型树脂原料的流淌性能,制件几何形状,制件尺寸大小,模具浇注系统的形式,成型所用的注塑方式与其他工艺条件等到因素决定.冷却时间指保压结束到开启模具所经历的时间.冷却时间的长短受熔体温度,模具温度,脱模温度与冷却剂温度等因素的影响.在保证取得较好制件质量的前提下,应当尽量缩短冷却时间的大小,否则,会延长制件成型周期,降低生产效率,还可能造成具有复杂几何形状的制件脱模困难.开模时间为模具开启取出制件到下个成型周期开始的时间.注塑机自动化程度高,模具复杂度低,则开模时间短;否则,开模时间较长.1.5常见制品缺陷及产生原因1.5.1短射短射是指由于模具模腔填充不完全造成制品不完整的质量缺陷,即熔体在完成填充之前就已凝聚。
模流分析成形条件
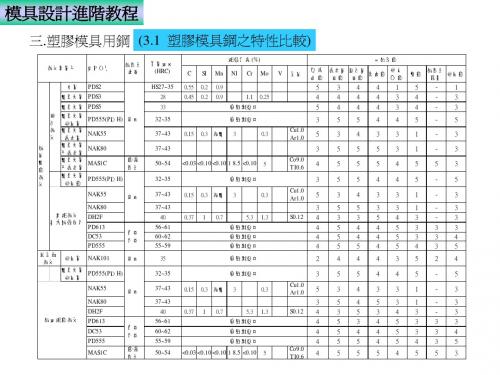
三.塑膠模具用鋼 (3.1 塑膠模具鋼之特性比較)
ð × Î Î ~ ¾¯ ¤ ¥ ³ x Î ª ¥ j P O¹ ¤ ¦ ° ¸ PDS2 ö Bz ¼³ ² ø ó ± ¥ Ï Î w× ¨ ¥µ « (HRC) HS27~35 28 33 32~35 37~43 37~43 ÉÄ ®® Bz ³ ² 50~54 32~35 £ n ¤ 37~43 37~43 40 f õ ² ¤ ^ õ ¦ ¤ £ n ¤ 56~61 60~62 55~59 35 32~35 £ n ¤ 37~43 37~43 40 f õ ² ¤ ^ õ ¦ ¤ ÉÄ ®® Bz ³ ² 56~61 60~62 55~59 50~54 0.37 1 0.7 5.3 Ó Ð MQ ¤ ¥ ½± § Ó Ð MQ ¤ ¥ ½± § Ó Ð MQ ¤ ¥ ½± § <0.03 <0.10 <0.10 1 8.5 <0.10 5 Co9.0 T I0.6 1.3 S0.12 0.15 0.3 A q ¾¶ 0.37 1 0.7 5.3 Ó Ð MQ ¤ ¥ ½± § Ó Ð MQ ¤ ¥ ½± § Ó Ð MQ ¤ ¥ ½± § Ó Ð MQ ¥ ½± § ¤ Ó Ð MQ ¥ ½± § ¤ 3 0.3 Cu1.0 Ar1.0 1.3 S0.12 0.15 0.3 A q ¾¶ <0.03 <0.10 <0.10 1 8.5 <0.10 Ó Ð MQ ¥ ½± § ¤ 3 0.3 Cu1.0 Ar1.0 5 Co9.0 T I0.6 0.15 0.3 A q ¾¶ Æ Ç ¨ À (%) ¤ ¾¦ ¤ C 0.55 0.45 SI 0.2 0.2 Mn 0.9 0.9 1.1 Ó Ð MQ ¥ ½± § ¤ Ó Ð MQ ¥ ½± § ¤ 3 0.3 Cu1.0 Ar1.0 0.25 NI Cr Mo V ä ¦¥ ¨ Q ¤ ³ Á d Ê « © ~ è S Ê « ½¯ © @ i ¿ è ± [ Dè [ à ¥ à ¨ ¥ k µ Ê ² ± © u Ê ¤ © u Ê ¤ © Ó Ê ¯ © ´ Ê ¶ © ö Bz ¼³ ² ÜΠŧ @k Ê » ©
塑料模流分析附录A-射出机成形条件设定

附录A 射出机成形条件之设定塑件品质受成形条件的影响甚巨。
从图A-1的成形窗口可知,当降低工作温度,就必须提高压力来将熔胶输送到模穴;假如工作温度太高,可能造成塑料热裂解。
另一方面,假如射压太低可能造成短射;射压太高则会产生毛边。
图A-1 成形窗口显示压力与温度的影响在设定成形条件之前,你应该先确定射出机的性能正常,模具是否设计给特定的射出机使用。
以下提供设定射出机的详细步骤:1.设定熔胶温度。
2.设定模具温度。
3.设定充填转保压位置。
4.设定螺杆转速。
5.设定背压。
6.设定射出压力为机器的最大射出压力。
7.射定保压为0 MPa。
8.设定射出速度为机器的最大射出速度。
9.设定保压时间。
10.设定足够的冷却时间。
11.设定开模时间。
12.逐渐增加射出量以进行一系列的短射实验。
13.切换成自动操作。
14.设定开模行程。
15.设定顶出行程、起始位置及速度。
16.设定射出量为99%的充填。
17.逐渐增加保压压力。
18.最小化保压时间。
19.最小化冷却时间。
步骤1. 设定熔胶温度熔胶温度是成形条件最重要的参数之一。
熔胶温度太低,使塑料无法完全熔化,或太黏而无法流动;熔胶温度太高,可能使塑料裂解,特别是POM或PVC 树脂更是如此。
熔胶与模具的建议温度可以请树脂供货商提供,或是使用表A-1的建议值。
大部份的树脂因为螺杆在料筒内旋转产生摩擦热而熔化。
料筒上通常会3~5组加热区域或加热片,主要功用是维持树脂在适当的温度。
设定加热片温度的规则为:●应该让温度从喷嘴到料斗附近逐渐降低。
●最接近料斗的加热片设定温度应该比计算之熔胶温度低40~50℃(72~80 °F),使塑料颗粒于塑化过程仍可以顺利地输送。
在喷嘴区的加热片应设定为计算之熔胶温度,并且保持均匀的温度。
设定不当的加热片温度会导致喷嘴处垂涎、塑料裂解或变色,特别是PA材料。
例如,C-mold软件建议使用235 ℃(455 °F)为PA材料的熔胶温度,则可以设定加热片的温度如下:●喷嘴区235 ℃(455 °F)●前段235 ℃(455 °F)●第一中段210 ℃(410 °F)●第二中段195 ℃(383 °F)●后段180 ℃(356 °F)因为旋转螺杆的摩擦热及背压对于熔胶的影响,真实的熔胶温度(或空射温度)通常比加热片的设定温度高。
上海汽车模流分析要求

上海汽车Moldflow分析要求、内容和格式1.网格划分与网格质量:1)对于FUSION网格质量要求:Free edges=0Non-manifold edges=0Element intersections=0Fully overlapping elements=0 注:针对产品,浇注系统可以不为0.Duplicate beams=0Elements not oriented=0Mesh match ratio大于85%,特殊产品,如格栅类产品放宽至75%Maximum aspect ratio小于10:1(COOL&WARP)特殊结构可放宽至15:1,但需特别说明。
Average aspect ratio 小于3:1 (COOL&WARP)2)对于MIDPLANE网格质量要求:Element intersections=0Fully overlapping elements=0 注:针对产品,浇注系统可以不为0.Duplicate beams=0Elements not oriented大于0时,应检查网格取向的一致性(WARP)。
Maximum aspect ratio小于10:1(COOL&WARP)特殊结构放宽至15:1,但需特别说明。
Average aspect ratio 小于3:1 (COOL&WARP)3)对于特殊形状的产品应用3D网格。
注:针对厚度大于5mm4)对产品上特殊结构,如喇叭孔,散热孔,应用合理的单元和属性。
5)网格壁厚的检查与处理网格质量符合要求后,应检查与处理网格壁厚,使其与实际CAD数据壁厚一致。
6)格式选择:使用MIDPLANE和FUSION模型可根据实际情况选择,中小零件推荐使用fusion模型。
7)材料信息:为了查看模拟分析使用的材料与产品要求的材料一致,模流分析报告需要反映材料的信息。
用于模流分析的材料参数原则上由材料供应商提供。