筛板精馏塔设计方案
海川化工论坛-筛板精馏塔设计

化工原理课程设计设计项目:筛板精馏塔系别:化学工程系班级:化工工艺 03 姓名: 625521学号:……指导老师:张老师设计时间: 2006.7.25-8.2第一章概述高径比很大的设备称为塔器.塔设备是化工、炼油生产中最重要的设备之一.它可使气(或汽)液或液液两相之间进行紧密接触,达到相际传质及传热的目的.常见的、可在塔设备中完成的单元操作有:精馏、吸收、解吸和萃取等。
此外,工业气体的冷却与回收,气体的湿法净制和干燥,以及兼有气液两相传质和传热的增湿、减湿等.在化工或炼油厂中,塔设备的性能对于整个装置的产品产量质量生产能力和消耗定额,以及三废处理和环境保护等各个方面都有重大的影响.据有关资料报道,塔设备的投资费用占整个工艺设备投资费用的较大比例(见下表).因此,塔设备的设计和研究,受到化工炼油等行业的极大重视.化工生产装置中各类工艺设备所占投资的比例1作为主要用于传质过程的塔设备,首先必须使气(汽)液两相充分接触,以获得较高的传质效率.此外,为了满足工业生产的需要,塔设备还得考虑下列各项传质效率.此外,为了满足工业生产的需要,塔设备还得考虑下列各项要求:(1)生产能力大.在较大的气(汽)液流速下,仍不致发生大量的雾沫夹带、拦液或液泛等破坏正常操作的现象.(2)操作稳定、弹性大.当塔设备的气(汽)液负荷量有较大的波动时,仍能在较高的传质效率下进行稳定的操作.并且塔设备应保证能长期连续操作.1化工设备设计全书,塔设备设计,第1页.(3)流体流动的阻力小.即流体通过塔设备的压力降小.这将大大节省生产中的动力消耗,以及降低经常操作费用.对于减压蒸馏操作,较大的压力降还使系统无法维持必要的真空度.(4)结构简单、材料耗用量小、制造和安装容易.这可以减少基建过程中的投资费用.(5)耐腐蚀和不易堵塞,方便操作、调节和检修.事实上,对于现有的任何一种塔型,都不可能完全满足上述所有要求,仅是在某些方面具有独到之处.根据设计任务书,此设计的塔型为筛板塔.筛板塔是很早出现的一种板式塔.五十年代起对筛板塔进行了大量工业规模的研究,逐步掌握了筛板塔的性能,并形成了较完善的设计方法.与泡罩塔相比,筛板塔具有下列优点:生产能力大20-40%,塔板效率高10-15%,压力降低30-50%,而且结构简单,塔盘造价减少40%左右,安装、维修都较容易.从而一反长期的冷落状况,获得了广泛应用.近年来对筛板塔盘的研究还在发展,出现了大孔径筛板(孔径可达20-25mm),导向筛板等多种形式.筛板塔盘上分为筛孔区、无孔区、溢流堰及降液管等几部分.工业塔常用的筛孔孔径为3-8mm,按正三角形排列.空间距与孔径的比为2.5-5.近年来有大孔径(10-25mm)筛板的,它具有制造容易,不易堵塞等优点,只是漏夜点低,操作弹性小.筛板塔的特点如下:(1)结构简单、制造维修方便.(2)生产能力大,比浮阀塔还高.(3)塔板压力降较低,适宜于真空蒸馏.(4)塔板效率较高,但比浮阀塔稍低.(5)合理设计的筛板塔可是具有较高的操作弹性,仅稍低与泡罩塔.(6)小孔径筛板易堵塞,故不宜处理脏的、粘性大的和带有固体粒子的料液.第二章 主要基础数据(1)苯和氯苯的物理性质2(2)常压下苯和氯苯的蒸汽压4(3)饱和蒸汽压P O苯和氯苯的饱和蒸汽压可用Antoine 方程 求算,即 CT BA p o+-=ln 式中 T —物系温度,K , P O—饱和蒸汽压,mmHgA 、B 、C —Antoine 常数,其值见下表52 化学化工物性数据手册,有机卷,第290页.3化学工程手册,第1篇化工基础数据,第174页 4 石油化工基础数据手册,第457页5 化学工程手册,第1篇化工基础数据,第175和177页第三章设计方案的确定及流程说明苯和氯苯混合液经原料预热器加热至泡点后送入精馏塔。
化工原理课程设计筛板和浮阀精馏塔设计

设计评价标准与方法
设计合理性评价
评价设计是否满足工艺要求、操作条件是否合理、设备选型是否恰当等。
经济性评价
评估设计的投资成本、运行费用、经济效益等,以判断设计的经济性。
创新性评价
评价设计是否具有创新性,是否采用了新的设计理念、方法或技术等。
实用性评价
评价设计在实际应用中的可行性、可操作性和可维护性等。
环保法规及标准
遵守国家环保法规
在项目设计、建设和运行过程中,必须严格遵守国家相关 环保法规,确保各项环保指标达标排放。
01
污染物排放标准
根据国家和地方污染物排放标准,对废 气、废水、固废等污染物进行严格控制 和处理,确保达标排放。
02
03
环保验收
在项目竣工后,必须按照国家和地方 环保要求进行环保验收,确保项目符 合环保要求后方可投入运行。
培养学生运用化工原 理知识解决实际问题 的能力。
设计任务及要求
设计一座筛板或浮阀精馏 塔,用于分离特定的二元 或多元混合物。
确定精馏塔的主要操作参 数,如进料量、进料浓度 、回流比、塔顶和塔底产 品浓度等。
进行塔板水力学计算,确 定塔板间距、堰高、降液 管面积等参数。
完成精馏塔的详细设计, 包括塔体结构、塔板布置 、接管和阀门配置等。
化工原理课程设计筛板 和浮阀精馏塔设计
contents
目录
• 课程设计概述 • 筛板精馏塔设计 • 浮阀精馏塔设计 • 精馏过程模拟与优化 • 设备选型与计算 • 安全与环保考虑 • 课程设计成果展示与评价
01
课程设计概述
目的与意义
掌握筛板和浮阀精馏 塔的基本原理和设计 方法。
提高学生的工程设计 能力和实践操作能力 。
筛板精馏塔设计

目录1、符号说明 (2)2.主要物性数据 (4)2.1苯、乙苯的物理性质 (4)2.2苯、乙苯在某些温度下的表面张力 (4)2.3苯、乙苯在某些温度下的粘度 (4)2.4苯、乙苯的液相密度 (4)2.5不同塔径的板间距 (4)3.工艺计算 (5)3.1精馏塔的物料衡算 (5)3.2塔板数的确定 (5)3.3实际塔板数的求取 (6)3.4相关物性参数的计算 (7)3.4.1操作压强 (7)3.4.2平均温度 (8)3.4.3平均摩尔质量 (8)3.4.4平均密度 (9)3.4.5液体平均表面张力 (11)3.4.6气液相负荷 (11)3.5塔和塔板的主要工艺尺寸计算 (13)3.5.1塔径 (13)3.5.2溢流装置 (16)3.5.3弓形降液管宽度 (16)3.5.4降液管底隙高度 (17)3.5.5塔板布置 (17)3.5.6筛孔计算及其排列 (18)3.6筛板的流体力学计算 (18)3.6.1液面落差 (20)3.6.2液沫夹带 (20)3.6.3漏液 (20)3.6.4液泛 (21)3.7塔板负荷性能图 (21)3.7.1漏液线 (21)3.7.2雾沫夹带线 (22)3.7.3液相负荷下限线 (22)3.7.4液相负荷上限线 (23)3.7.5液泛线 (23)6.参考文献 (27)1、符号说明1.1英文字母∆P——气体通过每层筛板的压降,kPa——塔的截面积,m2ATC——负荷因子,无因次t——筛孔的中心距,m——表面张力为20mN/m的C20u——空塔气速,m/s——筛孔直径,mdo——塔板开孔区面积,m2Aan——筛孔数目——降液管截面积,m2AfP——操作压力,kPa——筛孔区面积,m2Aou——漏液点气速,m/sominD——塔径,m'——液体通过降液体系的速度,m/suoe——液沫夹带量,kg液/kg气vV——气体体积流量,m/snR——回流比——气体体积流量,m/sVs——最小回流比Rmin——边缘无效区宽度,mWcM——平均摩尔质量,kg/kmolW——弓形降液管高度,md——平均温度,℃Tm——破沫区宽度,mWsg——重力加速度,m/s2Z——板式塔有效高度,mF——筛孔气相动触因子o——出口堰与沉降管距离,mhl——与平板压强相当的液柱高度,mhcτ——液体在降液管内停留时——与液体流过降液管压强降hd相当的液柱高度,mh——板上清液高度,m f——堰上液层高度,mhowH——出口堰高度,mwH'——进口堰高度,mwhσ——与克服表面张力压强降相当的液柱高度,mL——液相H——板式塔高度,mV——气相H——降液管内清夜层高度,m dL——液体体积流量,m3/hsHF——进料处塔板间距,m HP——人孔处塔板间距,mT——理论板层数δ——筛板厚度,mμ——粘度,mPa·sρ——密度,kg/m3α——质量分率,无因次φ——开孔率,无因次——降液管的底隙高度,mhoσ——表面张力,mN/mmax——最大min——最小2.主要物性数据2.1苯、乙苯的物理性质2.2苯、乙苯在某些温度下的表面张力2.3苯、乙苯在某些温度下的粘度2.4苯、乙苯的液相密度2.5不同塔径的板间距3.工艺计算3.1精馏塔的物料衡算W D F +=W D F Wx Dx Fx +=苯的摩尔质量: 78/A M kg kmol = 乙苯的摩尔质量: 106/B M kg kmol = 原料液及塔顶,塔底产品的平均摩尔质量:()150%7850%10692/F M kg kmol =-⨯+⨯=因为5%F D W x x x ==50%、=98%、分别为原料、塔顶、产品中的苯的摩尔分数所以:5000500054.35/92F F kmol h M === ()54.35(0.50.05)26.30/0.980.05F W D W F X X D kmol h X X ⨯-⨯-===--54.3526.3028.05/W F D kmol h =-=-=3.2塔板数的确定查化工手册得苯和乙苯的t-x-y 关系T/℃ x y - 1 1 84 0.86 0.974 88 0.74 0.939 92 0.635 0.906 96 0.541 0.864 100 0.485 0.816 104 0.4 0.8 108 0.318 0.7 110.6 0.278 0.654 115 0.217 0.571 120 0.156 0.463 125 0.103 0.344 130 0.055 0.205 135 0.01 0.042 136.2 0 0由上图可得q 线与平衡线的交点坐标q q x y (,)为(0.5,0.82)则最小回流比为:min 0.980.820.50.820.5D q q qx y R y x --===--取回流比:min 1.8 1.80.50.9R R ==⨯= 则精馏塔的气液负荷: 精馏段:(1)(0.81)26.3047.34kmol/h V R D =+=+⨯=0.826.3021.04kmol/h L RD ==⨯= 提馏段:'47.34kmol/h V V =='21.0454.3575.39kmol/h L L F =+=+= 求取操作线方程精馏段操作线方程:10.440.5411D n n n x Ry x x R R +=+=+++提馏段操作线方程:1' 1.490.002''m m W m L Wy x x x V V +=-=-由x-y 图,画梯级可得理论板数为7(不包含塔釜),进料板为第4块板。
筛板精馏塔设计
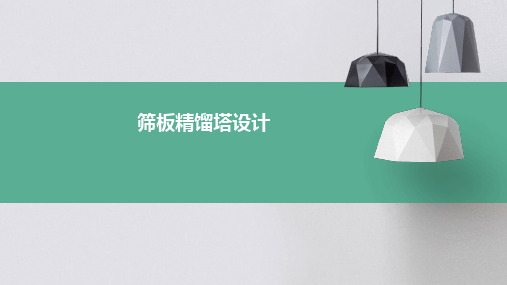
布局规划
将精馏塔布置在洁净区域 内,避免外界污染;塔体 周围设置洁净通道和操作 间,方便操作人员日常操 作和清洁维护;塔顶设置 冷凝器和回流罐,实现闭 路循环操作。
06
控制系统设计与实现
控制策略选择及原理介绍
控制策略选择
针对筛板精馏塔的特点,选择适当的 控制策略,如PID控制、模糊控制或 神经网络控制等。
筛板类型及参数确定
筛板类型
根据介质性质、操作条件和分离要求,选择合适的筛板类型,如泡罩筛板、浮阀筛板等。
筛板参数
确定筛板的孔径、孔距、开孔率等参数,以满足流体力学和传质要求。
筛板布置
根据塔内流体流动和传质情况,合理布置筛板,如设置进料板、侧线采出板等。
辅助设备配置
加热/冷却装置
根据操作条件和分离要求,配置合适 的加热/冷却装置,如再沸器、冷凝 器等。
以及塔内各部分的热损失等因素。
控制塔顶和塔底产品的采出量等。
03
筛板精馏塔结构设计
塔体结构选型
1 2
3
塔体形状
根据处理量、场地限制和操作要求,选择合适的塔体形状, 如圆柱形、方形等。
塔体材质
根据介质性质、温度和压力等条件,选用合适的材料,如碳 钢、不锈钢等。
塔体高度与直径
根据处理量、分离要求和场地限制,确定塔体的高度和直径 。
背景
精馏技术作为化工领域重要的分离手段,广泛应用于石油、 化工、制药、环保等行业。筛板精馏塔作为一种常见的精馏 设备,具有结构简单、操作方便、分离效率高等优点,因此 在实际生产中得到了广泛应用。
设计范围和要求
设计范围
本次设计涉及筛板精馏塔的整体设计,包括塔体结构、塔内件(如筛板、降液管等 )设计、进料和出料方式选择、操作条件优化等。
乙醇水筛板精馏塔工艺设计

乙醇水筛板精馏塔工艺设计
一、前言
乙醇水筛板精馏塔是一种常用的化工设备,广泛应用于乙醇制备、石
油化工、医药等行业。
本文将详细介绍乙醇水筛板精馏塔的工艺设计。
二、设备介绍
乙醇水筛板精馏塔由筛板、填料层和冷凝器组成。
其中,筛板分为平
板和斜板两种,填料层主要包括金属填料和塑料填料。
冷凝器则有管
壳式和管束式两种。
三、工艺流程
1. 原料准备
将乙醇和水按照一定比例混合后送入精馏塔中。
2. 加热
通过加热方式使混合物达到沸点,开始蒸发。
3. 蒸发分离
在精馏塔中,由于不同组分的沸点不同,会使得混合物中低沸点组分优先蒸发出来。
同时,在填料层中也会发生传质作用,促进组分之间的分离。
4. 冷凝回收
蒸发出来的气体在冷凝器中被冷却成液体,然后被收集起来。
5. 分离
重复以上步骤,直到达到所需的纯度。
四、工艺参数
1. 筛板间距:一般为0.45-0.6m。
2. 填料层高度:一般为1-3m。
3. 冷凝器冷却面积:根据生产需求确定。
4. 加热方式:蒸汽加热或电加热。
五、注意事项
1. 精馏塔内部应保持清洁,避免杂质进入影响分离效果。
2. 操作时应注意安全,避免发生爆炸等意外事故。
3. 根据实际情况调整工艺参数,以达到最佳分离效果。
六、总结
乙醇水筛板精馏塔是一种常用的化工设备,在乙醇制备、石油化工、医药等行业有广泛的应用。
本文对其工艺流程、设备参数和注意事项进行了详细介绍,希望对读者有所帮助。
【优秀毕设】化工原理课程设计筛板精馏塔的设计

化工原理课程设计任务书班级:生工081姓名:丁尚************陈国钰************设计题目:乙醇水溶液筛板精馏塔的工艺设计一.基础数据1.原料液量:8000kg·h-12.原料液组成:乙醇:22.6% ,水:77.4%3.原料液温度:25℃4.馏出液组成:乙醇含量大于:93.2%釜液组成:乙醇含量小于:1.1%(以上浓度均指质量分率)5.操作压力:常压二.设计范围1.精馏系统工艺流程设计,绘流程图一张2.筛板精馏塔的工艺计算3.筛板精馏塔塔板结构的工艺设计,绘制塔板负荷性能图,塔板结构图和整体设备结构图4.附属设备选型计算2011.7.8目录第一章:概述 (2)第二章:精馏工艺流程确定 (4)第三章:精馏塔的物料衡算 (5)第四章:塔板数的确定 (10)第五章:塔板结构的工艺设计 (19)第六章:塔板流体力学校核 (29)第七章:塔板负荷性能图 (33)第八章:塔的总体结构的确定 (39)第九章:馏塔附属设备选型计算 (46)参考文献 (51)附录 (52)第一章概述塔设备是化工,石油化工和炼油等生产中最重要的设备之一。
它可使气液或液液两相之间进行紧密接触,达到相际传质及传热的目的。
它是实现精馏,吸收,解吸和萃取等化工单元操作的主要设备。
塔设备在化工过程中有时也用来实现工业气体的冷却与回收,气体的湿法净制和干燥,以及兼有气液两相传质和传热的增湿,减湿等。
在板式塔中,塔内装有一定数量的塔盘,气体以鼓泡或喷射的形式穿过塔板上的液层使两相密切接触,进行传质,两相的组分浓度沿塔高呈阶梯式变化。
在填料塔中,塔内装填一定段数和一定高度的填料层,液体沿填料表面成膜状向下流动,作为连续相的液体自下向上流动,与液体逆流传质。
两相的组分浓度沿塔高呈阶梯式变化。
不管是何种塔型,除了首先要能使气(汽)液两相充分接触,获得较高的传热效率外,还希望能综合满足下列要求:(1)生产能力大。
在较大的气(汽)液流速下,仍不致发生大量的物沫夹带及液泛等破坏正常操作的现象。
乙醇-水筛板精馏塔设计

化工原理课程设计设计题目乙醇-水筛板精馏塔设计学生姓名学号班级指导教师设计时间完成时间 2化工原理课程设计任务书(一)设计题目:乙醇-水筛板精馏塔设计(二)设计任务完成精馏塔工艺优化设计、精馏塔结构优化设计以及有关附属设备的设计和选用,绘制带控制点的工艺流程图、精馏塔工艺条件图,并编制工艺设计说明书。
年产量: 10000t ;原料液浓度: 40% (乙醇质量分数);产品浓度: 93% (乙醇质量分数);乙醇回收率: 99% 。
(三)操作条件1.塔顶压强4 kPa(表压);2.进料热状况,泡点进料;;3.塔顶全凝器,泡点回流,回流比R=(1.1~2.0)Rmin4.塔釜加热蒸汽压力245 KPa(表压);5.单板压降不大于0.7 kPa;6.塔板类型筛板塔;7.工作日每年330天,每天24h连续运行;8.厂址:徐州地区。
(四)设计内容1.精馏塔的物料衡算;2.塔板数的确定;3.精馏塔的工艺条件及有关物性数据的计算;4.精馏塔的塔体工艺尺寸计算;5.塔板主要工艺尺寸的计算;6.塔板的流体力学验算;7.塔板负荷性能图;8.精馏塔接管尺寸计算,附属设备的确定;9.绘制带控制点工艺流程图(A2)、精馏塔工艺条件图(A2);10.符号说明;11.对设计过程的评述和有关问题的讨论;12.参考文献。
摘要精馏塔是进行精馏的一种塔式气液接触装置,又称为蒸馏塔。
有板式塔与填料塔两种主要类型。
根据操作方式又可以分为连续精馏塔与间歇精馏塔。
化工生产常需进行液体混合物的分离以达到提纯或回收有用组分的目的,精馏操作在化工、石油化工、轻工等工业生产中占有重要的地位。
为此,掌握气液平衡关系,熟悉各种塔形的操作特性,对选择、设计和分析分离过程中的各种参数是非常重要的。
在本设计中我使用了筛板塔,筛板塔的突出优点是结构简单、造价低。
当有合理的设计和适当的操作,筛板塔能满足分离要求的操作弹性,而且效率高。
精馏是最常用的分离液液混合物方式之一,是组成化工生产过程的主要单元操作,也是典型的化工操作设备之一。
化工原理课程设计精馏塔设计9724
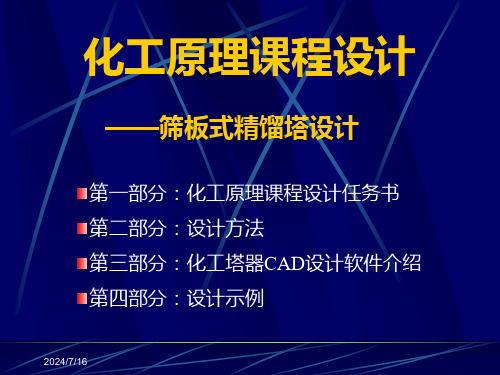
塔顶塔底的温度,进而求取全塔的平均温度,从而可以根据全
塔平均温度求取全塔平均相对挥发度。
式中: R ---回流
R m in —最小回流比
—全塔平均相对挥发度
3.理 论 板 数 和 实 际 板 数 的 确 定
(1)逐板法计算理论板数,交替使用操作线方程和相平衡关系。
精馏段操作线方程: yn1
L LD
3. 附属设备设计和选用 (1)加料泵选型,加料管规格选型
加料泵以每天工作3小时计(每班打1小时)。 大致估计一下加料管路上的管件和阀门。 (2)高位槽、贮槽容量和位置 高位槽以一次加满再加一定裕量来确定其容积。 贮槽容积按加满一次可生产10天计算确定。 (3)换热器选型 对原料预热器,塔底再沸器,塔顶产品冷却器等进行选型。 (4)塔顶冷凝器设计选型 根据换热量,回流管内流速,冷凝器高度,对塔顶冷凝器进 行选型设计。
0.735
lW hn
hOW
5 2
hOW
hn
5 2
LS —塔内液体流量, m3 S hn —齿深, m;可取为 0.015m
(3).堰高 hW
堰高与板上液层高度及堰上液层高度的关系:
hW hL hOW
2024/7/16
5、降液管的设计
(1)、降液管的宽度Wd 与截面积 Af
可根据堰长与塔径比值 lW ,查图求取。 D
塔径
流体 流 量 m3/h
Mm
U 形流型 单流型 双流型 阶梯流型
600
5 以下
5~25
900
7 以下
7~50
1000 1200
7 以下 9 以下
45 以下 9~70
1400
9 以下
70 以下
乙醇-正丙醇连续筛板式精馏塔的设计方案

乙醇-正丙醇连续筛板式精馏塔的设计方案乙醇-正丙醇连续筛板式精馏塔的设计方案流程的设计及说明1 设计思路蒸馏方式的确定蒸馏装置包括精馏塔,原料预热器,精馏釜(再沸器),冷凝器,釜液冷却器和产品冷却等设备,蒸馏过程按操作方式不同可分为连续蒸馏和间歇蒸馏两种流程,连续蒸馏具有生产能力大,产品质量稳定等优点,工业生产中以连续精馏为主,间歇蒸馏具有操作灵活,适应性强等优点,适合小规模,多品种或多组分物系的初步分离。
本次设计采用连续筛板精馏塔,常压精馏。
2 装置流程的确定 (1)物料的储存和输送在流程中设置原料罐,产品罐及离心泵。
原料可泵直接送入塔内,使程序连续稳定的进行。
(2)参数的检测和调控流量,压力和温度是生产中的重要参数,必须在流程中的适当位置装设仪表,以测量这些参数。
同时,在生产过程中,物料的状态。
加热剂和冷却剂的状态都不可能避免的会有一些波动,因此必须在流程中设置一定的阀门。
(3)冷凝装置的确定本设计采用塔顶全凝器,以便于准确地对控制回流比。
(4)热能的利用精馏过程是组分多次部分汽化和多次部分冷凝的过程,耗能较多,因此选择适宜的回流比使过程处于最佳条件下进行,可使能耗至最低。
3 操作条件的确定 (1) 操作压力的选取本次设计采用常压操作。
除热敏性物料外,凡通过常压精馏不难实现分离要求,并能利用江河水或循环水将镏出物冷凝下来的系统。
(2)加料状态的选择本设计选择q=1时进料,原因是使塔的操作稳定,精,提镏段利用相同塔径,便于制造。
(3) 加料方式蒸馏大多采用间接蒸汽加热,设置再沸器。
(4)回流比的选择一般经验值为min )0.21.1(R R -=。
本设计采用min 5.1R R =,初步设定后经过流体力学验算,负荷条件,故选择合理。
塔顶冷凝器的冷凝方式与冷却介质的选择塔顶冷凝温度不要求低于30℃,工业上多用水冷 (5)板式塔类型的选择本次设计采用连续筛板式精馏塔 4 设计方案的确定(1)满足工艺和操作要求(2)满足经济上的要求,安全生产,保护环境。
化工原理筛板塔设计方案

化工原理筛板塔设计方案第一部分概述一、设计题目:筛板塔设计二、设计任务:苯-甲苯精馏塔设计三、设计条件:1、年处理含苯41%(质量分数,下同)的苯-甲苯混合液3万吨;2、产品苯含量不低于96%;3、残液中苯含量不高于1%;4、操作条件:精馏塔的塔顶压力:4kPa(表压)进料状态:自选回流比:自选加热蒸汽压力:101.33kPa(表压)单板压降:不大于0.7kPa(表压)全塔效率:E T=52%5、设备型式:筛板塔6、设备工作日:300天/年,24h连续运行四、设计内容和要求:五、工艺流程图原料液由高位槽经过预热器预热后进入精馏塔内。
操作时连续的从再沸器中取出部分液体作为塔底产品(釜残液)再沸器中原料液部分汽化,产生上升蒸汽,依次通过各层塔板。
塔顶蒸汽进入冷凝器中全部冷凝或部分冷凝,然后进入贮槽再经过冷却器冷却。
并将冷凝液借助重力作用送回塔顶作为回流液体,其余部分经过冷凝器后被送出作为塔顶产品。
为了使精馏塔连续的稳定的进行,流程中还要考虑设置原料槽。
产品槽和相应的泵,有时还要设置高位槽。
且在适当位置设置必要的仪表(流量计、温度计和压力表)。
以测量物流的各项参数。
见附图。
第二部分工艺设计计算一、设计方案的确定本设计任务书为分离苯-甲苯混合物。
对于二元混合物的分离,应采用连续精馏流程。
设计中采用泡点进料,将原料液通过预热器加热至泡点后送入精馏塔内,其余部分经产品冷却器冷却后送至储罐。
该物系属易分离物系,最小回流比较小,故操作回流比取最小回流比的2倍。
塔釜采用间接蒸汽加热,塔底产品经冷却后送至储罐。
二、精馏塔的物料衡算1.原料液及塔顶、塔底产品的摩尔分数苯的摩尔质量 M =78.11kg /mol A 甲苯的摩尔质量 M =92.13kg /mol BF 0.41/78.11X 0.4500.41/78.110.59/92.13==+ D 0.96/78.11X 0.9660.96/78.110.04/92.13==+W 0.01/78.11X 0.0120.01/78.110.99/92.13==+ 2.原料液及塔顶、塔底产品的平均摩尔质量()0.45078.1110.45092.1385.82kg /mol F M =⨯+-⨯=()0.96678.1110.96692.1378.59kg /mol D M =⨯+-⨯= ()W M 0.01278.1110.01292.1391.96kg /mol =⨯+-⨯= 3.物料衡算原料处理量33000101F=48.72kmol /h 30002485.52⨯⨯=⨯总物料衡算 48.72D W =+苯物料衡算 48.720.450.9660.012D W ⨯=+联立解得 22.37kmol /h25.21kmol /h D W ==三、塔板数的确定 1.理论板层数T N 的求取苯-甲苯属理论物系,可采用图解法求理论板层数。
分离甲醇水混合液的筛板精馏塔的设计计算
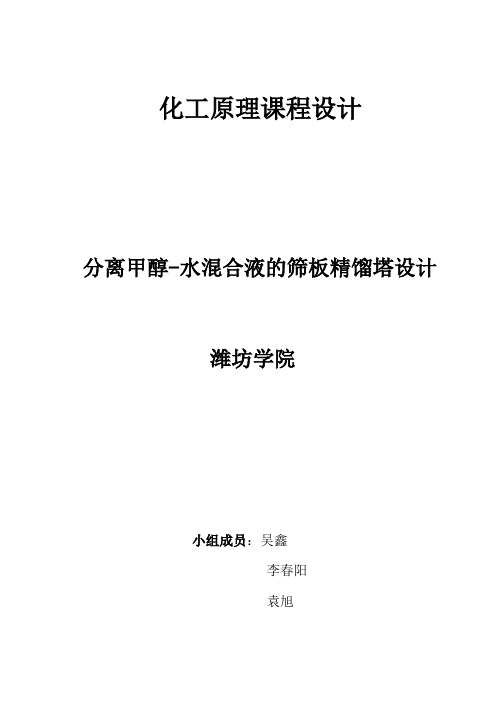
化工原理课程设计分离甲醇-水混合液的筛板精馏塔设计潍坊学院小组成员:吴鑫李春阳袁旭目录第一章设计题目 (6)第二章工艺计算 (7)2.1精馏塔的物料衡算 (7)2.2塔板数的确定 (8)N的求取 (9)2.2.1理论板数T2.3工艺条件及有关物性数据计算 (10)2.3.1 图解法求理论塔板数 (10)2.3.2操作压力计算 (11)2.3.3 操作温度计算 (11)2.3.4相对挥发度的计算 (12)2.3.5平均摩尔质量计算 (12)2.3.6平均密度的计算 (13)2.3.7体平均表面张力计算 (15)2.3.8液体平均黏度计算 (16)2.3.9实际塔板数的计算 (17)2.4塔的主要工艺尺寸计算 (18)2.5塔板主要工艺尺寸的计算 (19)2.5.1溢流装置计算 (19)2.5.2塔板板面布置 (21)2.5.3筛孔计算及排列 (21)2.6筛板的流体力学验算 (22)2.6.1液面落差 (23)2.6.2液沫夹带 (23)2.6.3漏液 (23)2.7负荷性能图 (24)2.7.1漏液线(气相负荷下限线) (24)2.7.2 液体流量下限线 (24)2.7.3液体流量上限线 (25)2.7.4 过量液沫夹带线 (25)2.7.5 液泛线 (25)2.7.6塔板工作线 (28)第三章设计总结 (29)第四章附属设备的选型与设计 (31)4.1冷凝器的选择 (31)4.2再沸器的选择 (32)第五章塔附件的设计 (33)5.1接管的计算与选择 (33)5.1.1进料管 (33)5.1.2回流管 (33)5.1.3塔底出料管 (33)5.1.4塔顶蒸汽出料管 (34)5.1.5塔底进气管 (34)5.2 筒体 (34)5.3 封头 (34)5.4法兰的选取 (34)5.5裙座 (35)5.6人孔 (35)第六章塔总高度设计 (36)6.1塔顶部空间高度 (36)6.2塔总体高度计算 (36)第七章设计心得 (37)参考文献 (38)前言精馏是利用液体混合物中各组分挥发性的差异对其进行加热,然后进行多次混合蒸气的部分冷凝和混合液的部分加热汽化以达到分离目的的一种化工单元操作。
苯-甲苯混合液筛板精馏塔设计-化工原理课程设计

设计任务书题目:苯-甲苯混合液筛板精馏塔设计原始数据:年处理量:35000进料组成:45%(苯质量分数)塔顶产品浓度:98%(苯质量分数)塔底釜液含甲苯量不低于98%(以质量计)每年实际生产天数:330天(24小时/天)冷却水温度:30℃饱和水蒸气压力:2.5kgf/cm2(表压)泡点进料,塔顶压强为4kPa(表压),单板压降<0.7kPa,塔顶全凝,泡点回流。
R /Rmin = 1.3 。
设计内容:1.确定全套精馏装置的流程,绘出工艺流程示意图;2.精馏塔的工艺计算与结构设计:1)物料衡算确定理论板数和实际板数;(可采用计算机编程)2)按精馏段首、末板计算塔径并圆整;3)确定塔板和降液管结构;4)按精馏段的首、末板进行流体力学校核;5)绘制精馏段塔板的负荷性能图;6)进行全塔优化,要求操作弹性大于2。
3.计算塔高;4.估算冷却水用量和冷凝器的换热面积、选出冷凝器型号;估算塔顶回流泵流量、扬程,初选泵型号。
5.绘制精馏塔装配图、塔板结构布置图;6.设计结果概要或塔设计计算结果汇总;7.设计小结和参考文献。
设计基础数据表1 苯和甲苯的物理性质表2 气液相平衡数据苯-甲苯溶液,p=101.3kPa ,(p82,表3-21数据更多些)1.饱和蒸汽压:苯和甲苯的饱和蒸汽压可由Antoine方程式求算。
Logp0=A-B/(t+C)式中 t——物系温度,℃P0——饱和蒸汽压,kPa;表3 A、B、C——Antoine常数。
表4 苯和甲苯的液相密度ρ(kg/m3)表5 液体表面张力σ(mN/m)表6 液体粘度μ(mPa*s)表7 液体汽化热r(kJ/kg)(kJ/kg·K)表8 液体热容Cp=A+BT+CT2+DT3,式中T——物系温度,K;A、B、C、D——常数。
Cp目录一序言............................................................ 二流程说明、工艺流程图绘制......................................... 三设计计算.........................................................3.1 精馏塔的物料衡算.............................................3.2 塔板数的确定.................................................3.3 精馏塔的工艺条件及有关物性数据的计算.........................3.4 精馏塔的塔体工艺尺寸计算.....................................3.5 塔板主要工艺尺寸的计算.......................................3.6 筛板的流体力学验算...........................................3.7 塔板负荷性能图............................................... 四板式塔得结构与附属设备...........................................4.1附件的计算....................................................4.1.1接管.....................................................4.1.2冷凝器...................................................4.1.3 再沸器 ..................................................4.1.4 泵的选型 ................................................4.2 板式塔结构.................................................. 五设计心得体会..................................................... 六参考文献......................................................... 七评分表........................................................... 八附录(板式塔工艺条件图、塔板结构布置图).........................一序言化工原理课程设计是综合运用《化工原理》课程和有关先修课程(《物理化学》,《化工制图》等)所学知识,完成一个单元设备设计为主的一次性实践教学,是理论联系实际的桥梁,在整个教学中起着培养学生能力的重要作用。
乙醇—水筛板精馏塔工艺设计(化工原理设计)
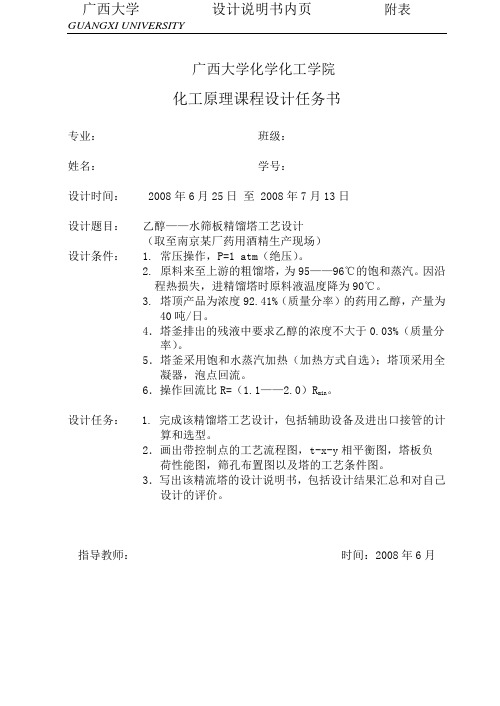
广西大学化学化工学院化工原理课程设计任务书专业:班级:姓名:学号:设计时间: 2008年6月25日至 2008年7月13日设计题目:乙醇——水筛板精馏塔工艺设计(取至南京某厂药用酒精生产现场)设计条件: 1. 常压操作,P=1 atm(绝压)。
2. 原料来至上游的粗馏塔,为95——96℃的饱和蒸汽。
因沿程热损失,进精馏塔时原料液温度降为90℃。
3. 塔顶产品为浓度92.41%(质量分率)的药用乙醇,产量为 40吨/日。
4.塔釜排出的残液中要求乙醇的浓度不大于0.03%(质量分率)。
5.塔釜采用饱和水蒸汽加热(加热方式自选);塔顶采用全凝器,泡点回流。
6.操作回流比R=(1.1——2.0)R。
min设计任务: 1. 完成该精馏塔工艺设计,包括辅助设备及进出口接管的计算和选型。
2.画出带控制点的工艺流程图,t-x-y相平衡图,塔板负荷性能图,筛孔布置图以及塔的工艺条件图。
3.写出该精流塔的设计说明书,包括设计结果汇总和对自己设计的评价。
指导教师:时间:2008年6月1设计任务1.1 任务1.1.1 设计题目乙醇—水筛板精馏塔工艺设计(取至南京某厂药用酒精生产现场)1.1.2 设计条件 1.常压操作,P=1 atm(绝压)。
2.原料来至上游的粗馏塔,为95-96℃的饱和蒸气。
因沿程热损失,进精馏塔时原料液温度降为90℃。
3.塔顶产品为浓度92.41%(质量分率)的药用乙醇,产量为40吨/日。
4.塔釜排出的残液中要求乙醇的浓度不大于0.03%(质量分率)。
5.塔釜采用饱和水蒸气加热(加热方式自选);塔顶采用全凝器,泡点回流。
6.操作回流比R=(1.1—2.0)R。
min1.1.3 设计任务1.完成该精馏塔工艺设计,包括辅助设备及进出口接管的计算和选型。
2.画出带控制点的工艺流程示意图,t-x-y相平图,塔板负荷性能图,筛孔布置图以及塔的工艺条件图。
3.写出该精馏塔的设计说明书,包括设计结果汇总和对自己设计的评价。
乙醇_水连续精馏筛板塔的设计说明
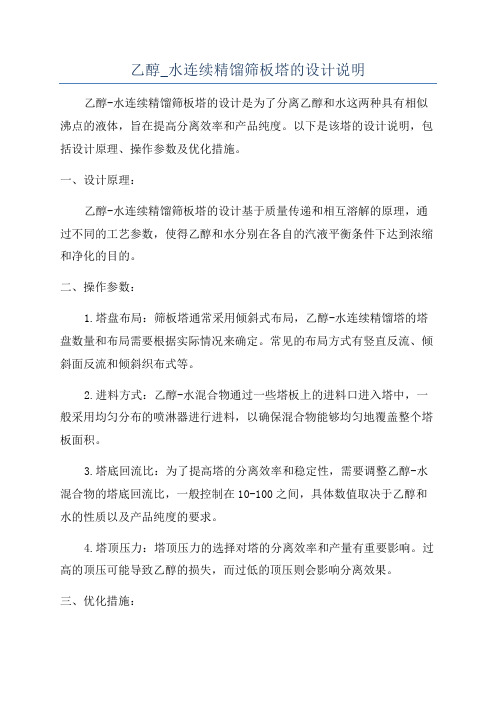
乙醇_水连续精馏筛板塔的设计说明乙醇-水连续精馏筛板塔的设计是为了分离乙醇和水这两种具有相似沸点的液体,旨在提高分离效率和产品纯度。
以下是该塔的设计说明,包括设计原理、操作参数及优化措施。
一、设计原理:乙醇-水连续精馏筛板塔的设计基于质量传递和相互溶解的原理,通过不同的工艺参数,使得乙醇和水分别在各自的汽液平衡条件下达到浓缩和净化的目的。
二、操作参数:1.塔盘布局:筛板塔通常采用倾斜式布局,乙醇-水连续精馏塔的塔盘数量和布局需要根据实际情况来确定。
常见的布局方式有竖直反流、倾斜面反流和倾斜织布式等。
2.进料方式:乙醇-水混合物通过一些塔板上的进料口进入塔中,一般采用均匀分布的喷淋器进行进料,以确保混合物能够均匀地覆盖整个塔板面积。
3.塔底回流比:为了提高塔的分离效率和稳定性,需要调整乙醇-水混合物的塔底回流比,一般控制在10-100之间,具体数值取决于乙醇和水的性质以及产品纯度的要求。
4.塔顶压力:塔顶压力的选择对塔的分离效率和产量有重要影响。
过高的顶压可能导致乙醇的损失,而过低的顶压则会影响分离效果。
三、优化措施:为了提高乙醇-水连续精馏筛板塔的分离效率和产品纯度,可以采取以下优化措施:1.适当增加塔盘数量:增加塔盘数量可以增加物质在塔中的停留时间,有利于乙醇和水的分离。
2.优化塔盘布局:选择合适的塔盘布局,使得气液流动均匀、阻力小,有利于提高分离效果。
3.控制塔底回流比:根据乙醇和水的性质和产品纯度要求,选择适当的塔底回流比,以提高分离效率并减少乙醇的损失。
4.精确控制塔顶和塔底温度:通过控制塔顶和塔底温度的变化,可以调整两种液体在塔中的沸点差异,提高分离效果。
5.使用适当的填料:填料是影响乙醇-水连续精馏筛板塔性能的重要因素,选择适当的填料可以提高传质效率和阻力噪声比。
6.操作控制:严格控制进料流量、塔顶流量和塔底回流比,合理调整操作参数,以达到最佳的分离效果和产品纯度。
总结:乙醇-水连续精馏筛板塔的设计是为了分离乙醇和水这两种具有相似沸点的液体。
分离乙醇-水混合液的筛板精馏塔设计_化工原理与化工机械课程设计(可编辑)

化工原理-化工设备机械基础课程设计设计题目分离乙醇-水混合液的筛板精馏塔设计化工原理?化工设备机械基础课程设计任务书设计题目分离乙醇?水混合液的筛板精馏塔设计二. 原始数据及条件生产能力:年处理量8万吨(开工率300天/年),每天工作24小时;原料:乙醇含量为20%(质量百分比,下同)的常温液体;分离要求:塔顶,乙醇含量不低于90%,塔底,乙醇含量不高于 8%;塔顶压强进料热状况回流比塔釜加热蒸汽压力单板压降建厂地址4 KPa(表压) 饱和液体1.5 Rmin 0.5MPa(表压) ≤0.7KPa 重庆操作条件: 三. 设计要求:(一)编制一份设计说明书,主要内容包括:1. 前言2. 设计方案的确定和流程的说明3. 塔的工艺计算4. 塔和塔板主要工艺尺寸的设计 a. 塔高、塔径及塔板结构尺寸的确定 b. 塔板的流体力学验算c. 塔板的负荷性能图5. 附属设备的选型和计算6. 设计结果一览表7. 注明参考和使用的设计资料8. 对本设计的评述或有关问题的分析讨论。
(二)绘制一个带控制点的工艺流程图(2#图)(三)绘制精馏塔的工艺条件图(1#图纸) 四. 设计日期:2013年 11月25日至 2013年12 月15日推荐教材及主要参考书:1.王国胜, 裴世红,孙怀宇化工原理课程设计. 大连:大连理工大学出版社,20052.?贾绍义,柴诚敬. 化工原理课程设计. 天津:天津科学技术出版社,2002.3、马江权,冷一欣. 化工原理课程设计. 北京:中国石化出版社,2009.4、《化工工艺设计手册》,上、下册;5、《化学工程设计手册》;上、下册;6、化工设备设计全书编辑委员会.化工设备设计全书-塔设备;化学工业出版社:北京. 2004,017、化工设备设计全书编辑委员会.化工设备设计全书-换热器;化学工业出版社:北京. 2004,018、化工设备设计全书编辑委员会.化工设备设计全书-管道;化学工业出版社:北京. 2004,019?陈敏恒. 化工原理第三版. 北京:化学工业出版社,2006摘要课程设计是化工原理课程的一个非常重要的实践教学内容。
- 1、下载文档前请自行甄别文档内容的完整性,平台不提供额外的编辑、内容补充、找答案等附加服务。
- 2、"仅部分预览"的文档,不可在线预览部分如存在完整性等问题,可反馈申请退款(可完整预览的文档不适用该条件!)。
- 3、如文档侵犯您的权益,请联系客服反馈,我们会尽快为您处理(人工客服工作时间:9:00-18:30)。
筛板精馏塔设计方案1绪论1.1课题研究意义、研究现状及拟采用的技术路线1.1.1课题研究意义、研究现状在化工或炼油厂中,塔设备的性能对于整个装置的产品产量,质量,生产能力和消耗定额,以及三废处理和环境保护等各个方面都有重大的影响。
据有关资料报道,塔设备的投资费用占整个工艺设备投资费用的较大比例。
因此,塔设备的设计和研究,受到化工、炼油等行业的极大重视[6]。
塔设备是化工、石油等工业中广泛使用的重要生产设备。
它可使气(或汽)液或液液两相之间进行紧密接触,达到相际传质及传热的目的。
常见的、可在塔设备中完成的单元操作有:精馏、吸收、解吸和萃取等[2]。
此外,工业气体的冷却与回收,气体的湿法净制和干燥,以及兼有气液两相传质和传热的增湿、减湿等。
化工生产中所处理的原料,中间产物,粗产品几乎都是由若干组分组成的混合物,而且其部分都是均相物质。
生产中为了满足储存,运输,加工和使用的需求,时常需要将这些混合物分离为较纯净或几乎纯态的物质。
塔设备的基本功能就是提供气、液两相以充分接触的机会,使传热、传质两种传递过程能够迅速有效的进行;还能使接触之后的气、液两相及时分开,互不夹带。
筛板塔是最早应用于工业生产的设备之一,五十年代之后,通过大量的工业实践逐步改进了设计方法和结构。
近年来与浮阀塔一起成为化工生产中主要的传质设备。
筛板塔普遍用作H2S-H2O双温交换过程的冷、热塔,应用于蒸馏、吸收和除尘等。
筛板精馏塔属于板式塔,筛板精馏塔具有结构简单,造价低,板上液面落差小,气体压降小,生产能力大,气体分散均匀,传质效率高的优点,是化工生产中常见的单元操作设备之一。
筛板塔始于1830年,是结构最简单的一种板型。
由于其操作弹性小,当气量过小或过大时,易发生严重漏液或过量液沫夹带现象;而且易堵塞,不宜处理粘度大、易结焦的物料,一度时间曾影响到它的应用推广。
20世纪50年代后,随着林德塔板、导向塔板的应用推广,筛板塔又重新启用并日趋广泛。
导向筛板是60年代由美国联合碳化物公司林德子公司开发应用的,国有化工大学进行系统研究,他们认为导向筛板从导向喷出的水平气速均匀稳定的推动板上液流前进,大大增加了塔的抗污性和抗堵能力,克服了液面梯度和非活化区,提高了传质效率和生产能力。
在酒精工业,导向筛板使固含率达10%的粘稠成熟醪在塔板上均匀稳定流动,解决了长期存在的赌塔和液泛问题,并增产约筛板塔始于1830年,是结构最简单的一种板型。
由于其操作弹性小,当气量过小或过大时,易发生严重漏液或过量液沫夹带现象;而且易堵塞,不宜处理粘度大、易结焦的物料,一度时间曾影响到它的应用推广。
20世纪50年代后,随着林德塔板、导向塔板的应用推广,筛板塔又重新启用并日趋广泛。
导向筛板是60年代由美国联合碳化物公司林德子公司开发应用的,国有化工大学进行系统研究,他们认为导向筛板从导向喷出的水平气速均匀稳定的推动板上液流前进,大大增加了塔的抗污性和抗堵能力,克服了液面梯度和非活化区,提高了传质效率和生产能力。
在酒精工业,导向筛板使固含率达10%的粘稠成熟醪在塔板上均匀稳定流动,解决了长期存在的赌塔和液泛问题,并增产约50%;在邻、对硝基氯苯精馏过程中,导向筛板解决了要求理论塔板数多、压降低的难题。
这种塔板还具有结构简单,维修方便,造价低廉的特点,该类塔板经过深入研究和大力推广,目前已广泛应用于石油、化工、轻工、香料的领域。
近年来,国际上涌现出来了一些新型板式塔,如新型垂直筛板塔(New-VST),是世界上第三代(最新一代)板式塔技术之一,它是喷射型板式塔,与后者相比具有传质效率高、处理能力大、阻力小、操作弹性好等优异性能[6]。
此外,具有优良特性的新型筛板还有STONE-WEBSTER工程改善开发的波纹筛板,瑞士KUHNI公司的SLIT筛板,此就不一一阐述了。
在塔设备的技术改造中,国多种性能优良的新型板式塔已经得到成功的应用,随着科学技术的进步,需要更多、更好的板式塔来进行生产,这就要求板式塔向着低耗损,低成本,高效率和环保的方向发展。
塔板效率是实际传质过程进行的反映,是衡量塔板性能和塔板设计的主要依据,由于其影响因素多而且复杂,准确预测有一定的难度,目前解决的办法是采用经验方法或建立在较简单的传质模型(例如双膜理论)基础上的半经验计算方法。
为了衡量塔板的传质性能,研究人员提出了塔板点效率的概念,并对塔板的点效率进行了深入研究。
板式塔作为重要的传质设备之一,在各种分离工艺过程中广泛应用,开发新型传质效率高、压降小、通量大的板式塔,塔件始终是板式塔技术的发展方向[6]。
1.1.2精馏塔设计的拟采用的技术路线设计是典型的塔设备设计,其主要任务是参数选择和结构设计、计算及强度校核等。
拟采用以下设计步骤:一、筛板精馏塔工艺设计计算部分1.设计方案的确定;2.精馏塔的物料衡算;3.塔板数的确定;4.精馏塔的工艺条件及有关物性数据的计算;5.精馏塔的塔体工艺尺寸计算;6.塔板主要工艺尺寸的计算;7.筛板的流体力学验算;8.塔板负荷性能图。
二、筛板精馏塔结构设计计算部分1.计算塔体和封头壁厚;2.选取塔的附件,确定塔高;3.人孔及接管补强计算;4.接管、法兰的设计5.塔体的强度校核;三、绘制精馏塔装备图,塔板结构图2工艺设计2.1设计方案的确定及工艺流程的说明原料液经卧式列管式预热器预热至泡点后送入连续板式精馏塔(筛板塔),塔顶上升蒸汽流采用循环式列管全凝器冷凝后一部分作为回流液,其余作为产品经冷却后送至苯液贮罐;塔釜采用热虹吸立式再沸器提供汽相流,塔釜产品经卧式列管式冷却器冷却后送入氯苯贮罐。
2.2 全塔的物料衡算2.2.1 料液及塔顶底产品含苯的摩尔分率苯的相对分子质量为78.11kg/kmol ,甲苯的相对分子量为92.13 kg/kmol 进料组分:x F = 13.9255.011.7845.011.7845.0+ = 0.491顶液组分:x D =13.9202.011.7898.011.7898.0+ = 0.983 釜残液组分: x W =13.9298.011.7802.011.7802.0+ = 0.0240 2.2.2平均摩尔质量 ()kg/km ol 85.2513.920.49110.49111.78=⨯-+⨯=F M()kg/km ol 35.7813.92983.01983.011.78=⨯-+⨯=D M()kg/km ol 79.9113.92024.01024.011.78=⨯-+⨯=W M2.2.3全塔物料衡算依题给条件:年处理量10万吨,一年以330天,一天以24小时计,有:m F = 24330101000003⨯⨯ = 12626.3 h Kg F = kg/kmol 25.85kg/h 3.12626 = 148.11 h Kmol全塔物料衡算:W D F +=易挥发组分:W D F Wx Dx Fx +=联立方程组:148.11 =W D + (2-2-1) 148.11×0.491 =D ×0.983+W ×0.024 (2-2-2) 解方程组(2-2-1)和(2-2-2)得:D = 72.12 h KmolW = 75.99 h Kmol2.3塔板数的确定2.3.1理论塔板数的确定苯-甲苯物系属于理想物系,可以采用图解法来求得理论塔板数。
(1)绘制苯-甲苯的T-X-Y 图查阅文献3,得苯甲苯的汽液相组分。
绘制图形如下:图2-1 苯-甲苯T-X-Y 图(2)确定操作的回流比R在Y-X 图上,因q=1,查得:712.0=q y491.0==F q x x故有:23.1491.0712.0712.0983.0min =--=--=q q qD x y y x R 考虑到精馏段操作线离平衡线较近,故取实际操作的回流比为最小回流比的2倍:46.223.122min =⨯==R R(3)求精馏塔的气、液相负荷42.17712.7248.2=⨯==RD L h Kmol=+=D R V )1((2.48+1)×72.12 = 249.54 h Kmol qF L L +='= 177.42 + 148.11×1 = 325.53 h Kmol V V ='= 249.54 h Kmol(4)求理论塔板数精馏段操作线方程:284.0711.011+=+++=x R x x R R y D 提馏段操作线方程为过点(0.024,0.024)和(0.491,0.712)两点的直线。
图2-2 理论塔板图图解得理论塔板数为13块(包括再沸器),理论进料板为第七块板。
2.3.2实际塔板数的计算( 1 )塔效率的计算当983.0==D x y 时,D t =81.02℃,1x =0.959,当024.0==W x x 时,27.109=W t ℃,0618.0=W y 。
塔的平均温度为:11.952=+W D t t ℃ 查阅文献2,在塔的平均温度下,苯和甲苯的黏度为:s m Pa 26.0⋅=A μ,s m Pa 28.0⋅=B μ。
所以进料液的平均黏度为:()()s m Pa 27.0491.0128.0491.026.01⋅=-⨯+⨯=-+=F B F A m x x μμμ 塔顶相对挥发度:()()47.2959.0959.01983.01983.01111=--=⎪⎭⎫ ⎝⎛-⎪⎭⎫ ⎝⎛-=x x x x D D D α塔底相对挥发度:()()97.2024.0024.010681.010681.011=--=⎪⎭⎫ ⎝⎛-⎪⎭⎫ ⎝⎛-=W W W W W x x y y α 精馏塔的平均相对挥发度为:71.2=⋅=W D ααα用奥康奈尔关联公式计算全塔效率,对于筛板塔,k=0.9,所以: ()()61.4727.071.29.049.049.0245.0245.0=⨯⨯⨯=⋅=--m T k E μα﹪( 2 )实际塔板数精馏段:6/47.61﹪=12.6,圆整为13块;提馏段:6/47.61﹪=12.6,圆整为13块。
加料板在第十四块板,全塔实际总共有26块板。
2.4塔的精馏段操作工艺条件及相关物性数据的计算2.4.1操作压力取每层塔板压降为0.7kPa 计算。
塔顶压力:kPa 3.10543.101=+=D p加料板压力:kPa 4.114137.03.105=⨯+=F p塔釜压力:kPa 5.123267.03.105=⨯+=W p精馏段平均压强:()kPa 85.1092/4.1143.105=+=m p提馏段平均压强:()kPa 95.1182/5.1234.114=+='mp 2.4.2操作温度由苯甲苯的T-X-Y 图,查得塔顶温度为81.02℃,进料板为92.04℃,塔釜为109.27℃。