先进高强钢和汽车轻量化
高强钢成形技术及其在汽车轻量化中的应用
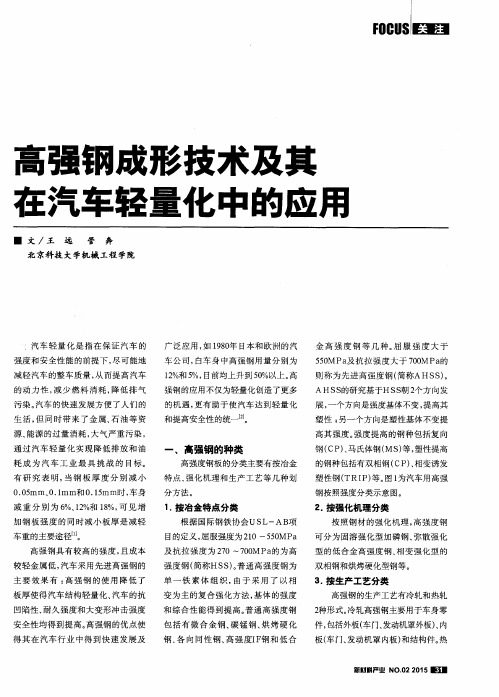
I t S I A: 高 强 度 低 合 金 钢 DF: 双相钢
C P: 复桕钢 TRI P: 相变诱 发性 钢
Ma r t : 马氏 体 钢 TW 1 I : 挛 品 诱 发 塑性 钢 S t a i n l e s s: 不 锈 钢 B S t e e l : 热 冲 压 用 钠
新和料产业 N O . 0 2 2 0 4 5圈
I I 圜 0 C U S
∞ m Βιβλιοθήκη 0 I r: 无 隙 原子 钢 Mi l d: 低 碳 铝 镇 静 钢 I I S S I F: 高强度1 F  ̄ 4 1 I { l I : 烘 烤 硬 化 钢 I s: 向 同性 钠
属H & 强 度 Mt a
图1 汽 车 用 高强 钢 按 照 强 度 分类 示 意 图
轧高强度钢板在载货 汽车上用量很 久,
不 良 为 了克服这 些 缺陷 , 欧 美及 L t
2 . 高强钢热冲压成形技术
当钢强度 超过 1 0 0 0 MPa 时, 一 些形 状 复杂 的零件 , 常 规 的冷冲 压 工 艺难 以成形 , 即使 可 以采 用冷冲 压工 艺, 所需 冲压 力大 、 成 型 件易 开裂 、 回
金高 强度钢等几 种。 屈 服 强 度 大 于 5 5 0 M Pa n t 抗 拉 强度 大于 7 0 0 MPa N 则称 为先 进 高 强度钢 ( 简 称AHS S ) 。
AHSS 的研 究基于 HS S 朝2 个方 向发
强度 和安 全性 能 的前提 下 , 尽可 能地 减轻 汽车 的整车 质量 , 从而 提高 汽车 的动 力 性 , 减少 燃 料 消 耗 , 降低 排 气 污染 。 汽 车 的快速 发展 方便 了人 们 的 生活 , 但 同 时 带来 了金 属 、 石 油 等 资 源、 能源 的过量 消 耗 , 大气 严重 污染 , 通 过 汽 车 轻量 化 实 现 降 低排 放 和 油 耗 成 为 汽 车 工 业 最 具 挑 战 的 目标 。 有研 究表 明, 当钢 板 厚 度 分 别 减 小 0 . 0 5 mm、 0 . 1 mm和 0 . 1 5 mm时 , 车身 减重 分别为 6 %、 l 2 %和 1 8 %, 可 见 增 加 钢 板 强度 的 同时 减小 板 厚 是 减 轻
先进高强钢(AHSS)汽车板
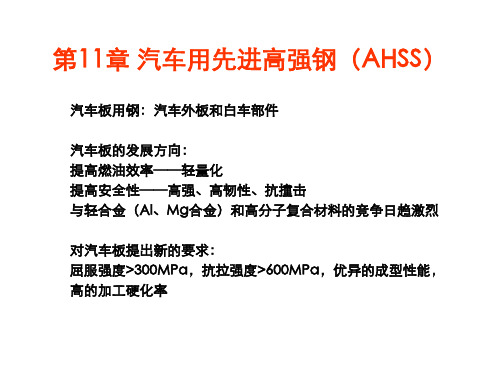
HSS与AHSS钢种
HSS: 软钢,IF钢,BH钢,HSLA钢 AHSS: DP钢,TRIP钢,Q&PT钢,TWIP钢,CFB钢
铁素体钢
冷轧深冲钢(后地板,轮罩) YS:120-160MPa,UTS:270-330MPa,E:≥40%
无间隙原子钢(发动机罩) YS:220-260MPa,UTS:340-400MPa,E:≥33%
760℃
热处理双相钢棒材的组织与性能
780℃
800℃
板条马氏体
820℃
840℃
08Mn2Nb钢不同温度加热淬火的SEM显微组织
911
760℃
780℃
800℃
板条马氏体
820℃
840℃
图8 11Mn2Nb钢不同温度加热淬火的SEM显微组织
14
亚温淬火温度对4种钢马氏体百分含量的影响
15
图14 四种钢最大力总伸长率和断后伸长率随亚温淬火温度的变化
连续退火工艺示意图
热轧
连续 退火
各步处理后的显微组织
冷轧
热轧和连续退火处理后的力学性能对比
不同强度级别的冷轧DP钢
实验钢的化学成分和轧制条件
BDP-590 3℃/s
BDP-780 8℃/s
BDP-780 15℃/s
连续镀锌模拟处理后各钢种的典型显微组织
BDP-780中的NbC析出相的TEM照片
冷轧C-Si-Al-Mn TRIP 钢
900℃×10m, 410℃×3m
900℃×5m, 410℃×3m
实验钢热处理后的显微组织
TEM分析结果
不同工艺处理后的XRD处理结果 不同工艺处理后的拉伸试验结果
冷轧C-Si-Al(P)-Mn TRIP 钢的合金化设计
先进高强钢应用优势及未来研究方向

先进高强钢应用优势及未来研究方向当前,由于环保和节能的需要,汽车的轻量化已经成为世界汽车发展的潮流。
轻量化这一概念最先起源于赛车运动,车身减重后可以带来更好的操控性,发动机输出的动力能够产生更高的加速度。
由于车辆轻,起步时加速性能更好,刹车时的制动距离更短。
汽车的轻量化,就是在保证汽车的强度和安全性能的前提下,尽可能地降低汽车的整备质量,从而提高汽车的动力性,减少燃料消耗,降低排气污染。
1轻量化意义汽车的油耗主要取决于发动机的排量和汽车的总质量,在保持汽车整体品质、性能和造价不变甚至优化的前提下,降低汽车自身重量可以提高输出功率、降低噪声、提升操控性、可靠性,提高车速、降低油耗、减少废气排放量、提升安全性。
有研究结果表明,若汽车整车重量降低10%,燃油效率可提高6%-8%;汽车整备质量每减少100公斤,百公里油耗可降低0.3—0.6升;若滚动阻力减少10%,燃油效率可提高3%;若车桥、变速器等装置的传动效率提高10%,燃油效率可提高7%。
汽车车身约占汽车总质量的30%,空载情况下,约70%的油耗用在车身质量上。
因此,车身变轻对于整车的燃油经济性、车辆控制稳定性、碰撞安全性都大有裨益。
2AHSS优势高强钢、铝合金、镁合金和塑料是当前汽车轻量化的4种主要材料。
高强度钢主要用于汽车外壳和结构件。
铝合金最适用于产生高应力的毂结构件,如罩类、箱类、歧管等。
镁合金具有良好的压铸成型性能,适应制造汽车各类压铸件。
塑料及其复合材料通过改变材料的机械强度及加工成型性能,以适应车上不同部件的用途要求。
钢铁材料在与有色合金和高分子材料的竞争中继续发挥其价格便宜、工艺成熟的优势,通过高强度化和有效的强化措施可充分发挥其强度潜力,迄今为止仍然是汽车制造中使用最多的材料。
随着安全性、燃油经济性和驾驶性能标准的不断提升,这对车用材料提出了更高的要求。
为应对这一挑战,全球钢铁工业成功研发了具有突出冶金性能和高成形性的先进高强度钢(AHSS)。
汽车轻量化的优缺点【全面解析】
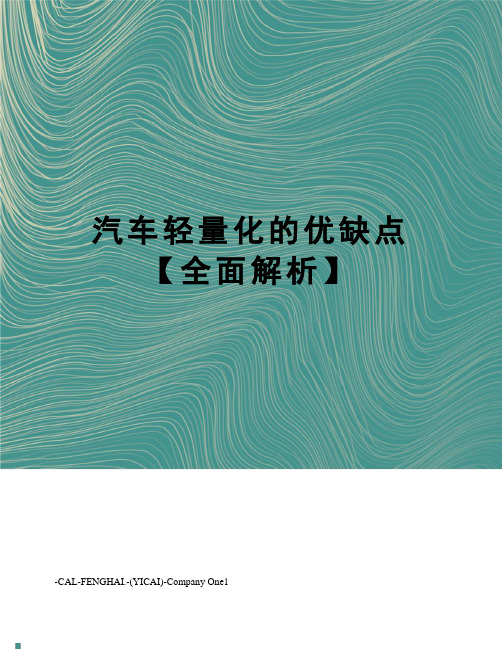
汽车轻量化的优缺点【全面解析】-CAL-FENGHAI.-(YICAI)-Company One1汽车轻量化的优缺点内容来源网络,由“深圳机械展(11万㎡,1100多家展商,超10万观众)”收集整理!更多cnc加工中心、车铣磨钻床、线切割、数控刀具工具、工业机器人、非标自动化、数字化无人工厂、精密测量、数控系统、3D打印、激光切割、钣金冲压折弯、精密零件加工等展示,就在深圳机械展.引言:为什么要推行轻量化基于环保的考虑世界各国均在推行强制汽车制造商降低汽车油耗的政策。
有研究数据显示,汽车整车重量降低10%,燃油效率可提高6%-8%;汽车整车重量,每减少100kg,百公里油耗可降低升,CO2排放量可减少约5g/km。
由此可见,汽车轻量化可以提高燃油效率和降低油耗,进而环保节能。
所以,汽车轻量化已成为汽车企业的共识。
倒逼汽车制造技术的升级换代如果不能保证行驶安全,汽车再轻再省油,没有谁敢开。
如果追求绝对的安全和耐撞,那就只能开重达数十吨的坦克,忍受每小时数百升的耗油量。
因此轻量化是汽车制造的趋势,目前轻量化主要是减少汽车自重,但是,车身作为汽车的主要承载件,需要保证足够的刚度、强度和疲劳耐久性能,从而使整车具有良好的安全、振动噪音和耐久性能,而轻量化无疑对上述要素提出了更高的要求,这对倒闭汽车制造技术升级换代无疑是一大刺激。
2 实现汽车轻量化的基本原理保证足够的刚度刚度指的是材料抵抗外力变形的能力,通常在车身开发中特指材料在屈服前的弹性特性,良好的刚度是整车NVH性能、车辆动力性能和疲劳耐久性能的基础,常见的评判指标有车身扭转刚度等。
刚度与材料的弹性模量相关,基本上材料种类确定,弹性模量也就确定了,比如采用高强钢并不会提升车身的刚性,因为钢的弹性模量都一样。
保证足够的强度。
强度是指零件受到冲击载荷发生屈服后仍能维持功能的能力,常用于车身碰撞安全性、耐冲击等性能的评估。
强度与材料的屈服强度和断裂强度相关,为了提升车子的安全性能,现代车身设计大量采用高强度钢材就是这个原因。
汽车高强度钢材技术的发展
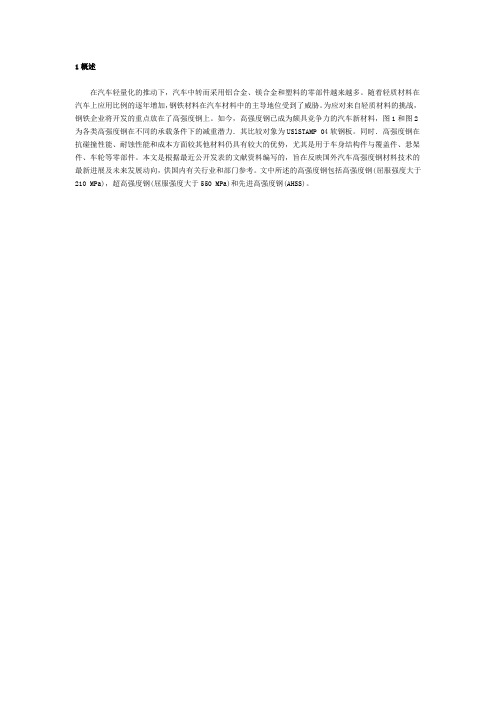
1概述在汽车轻量化的推动下,汽车中转而采用铝合金、镁合金和塑料的零部件越来越多。
随着轻质材料在汽车上应用比例的逐年增加,钢铁材料在汽车材料中的主导地位受到了威胁。
为应对来自轻质材料的挑战,钢铁企业将开发的重点放在了高强度钢上。
如今,高强度钢已成为颇具竞争力的汽车新材料,图1和图2为各类高强度钢在不同的承载条件下的减重潜力.其比较对象为USlSTAMP 04软钢板。
同时.高强度钢在抗碰撞性能、耐蚀性能和成本方面较其他材料仍具有较大的优势,尤其是用于车身结构件与覆盖件、悬架件、车轮等零部件。
本文是根据最近公开发表的文献资料编写的,旨在反映国外汽车高强度钢材料技术的最新进展及未来发展动向,供国内有关行业和部门参考。
文中所述的高强度钢包括高强度钢(屈服强度大于210 MPa),超高强度钢(屈服强度大于550 MPa)和先进高强度钢(AHSS)。
2主要技术进展超轻车身(ULSAB)、超轻覆盖件(ULSAC)、超轻悬架系统(ULSAS)和新概念超轻车身(ULSAB-AVC)等项目的成功实施,验证了高强度钢在减轻汽车自重和改善车辆性能中的有效性。
为了将这些项目所取得的技术成果转化为现实的生产力,近期的高强度钢技术研究,主要集中在支撑技术(Enabling Technologies)上。
2.1若干高强度钢的开发当前正处于新一代高强度钢开发的前夜。
从冶金学的角度看,近几年高强度钢材料的开发,大多只是对原有钢种牌号的补充或性能改善,厚度进一步减薄,材料本身并未取得突破性进展。
开发的难点是要针对不同的零件,力求在产品的强度、塑性和成本之间取得平衡。
SFGHITEN、NANOHITEN、ERW和HISTORY是日本JFE公司最近开发出的几种高强度钢。
其中SFGHITEN为含Nb系列高强度IF钢板,主要应用对象是汽车车身外板,研究用钢的化学成分见表1。
SFGHITEN利用析出的Nb(C,N)微粒和细化晶粒得到强化,其独特之处在于晶界附近存在所谓“无沉淀区”,它降低了材料的屈服强度。
高强钢在量产车型轻量化中的实际应用

0.28
7.85e-9
0.28
7.85e-9
0.28
7.85e-9
0.28
7.85e-9
厚度/mm
1.0 0.8 0.8 0.8
供最佳的选材方案,最终达到减小 车身质量的目的。
1.冲压件成形有限元数值 分析
M170P1、M210P1材料各20片,到 冲压车间进行试模验证。由于料 厚减薄,试冲高强板板料时,模 具闭合高度、压力需要重新调试 验证。试模结果表5所示,可以看 出,H340LA材料冲压零在边部出 现了开裂, 而M210P1和M170P1 材料试模零件均合格,该试模结果 与有限元模拟结果一致。冲压件精 度均符合要求(内板件精度要求 ≥95%)。
该冲压件原用材为1.0mm厚度 SPCEN材料,详细信息见表1所示。
表1 冲压件板料基本信息
料厚 长 宽 产品件名称 材质 /mm / mm / mm
左/右后包角 加强板
SPCEN
1.0
640
465
2. 左右后包角加强板轻量化 方案
针对该零件的轻量化方案, 拟采用高强钢进行替代。初步方 法将材料厚度降低到0.8mm厚度, 材质选用M170P1、M210P1以及 H340LA。
H340LA 340~420 410~510
≥21
备注:DC06、H340LA采用A80标距试样,M170P1、M210P1采用A50标距试样。
牌号
SPCEN M170P1 M210P1 H340LA
表3 材料其他性能参数
弹性模量E /MPa
1.9e5 2.0e5 2.1e5 2.12e5
性能参数
泊松比 密度/(t/mm3)
表2 材料力学性能
牌号
高强钢板的车身结构轻量化分析

区域治理综合信息高强钢板的车身结构轻量化分析刘阳 江勇 马新伟眉山中车物流装备有限公司,四川 眉山 620010摘要:汽车车身结构设计和制造业不断发展新材料和新技术以适应轻量化设计的要求。
而具有强度、刚度、抗冲击性、回收使用和低成本等方面综合优势的高强度钢板在车身轻量化设计中得到越来越广泛的关注。
基于此,文章就高强钢板的车身结构轻量化展开了研究,具体内容供大家参考和借鉴。
关键词:高强钢;车身结构;轻量化目前,应用高强度钢板实现车身轻量化和高强度,是车身轻量化三种途径结合的典型应用,对其进行性能研究、热成形性分析和应用高强度钢车身进行结构优化研究,完全符合车身轻量化技术的发展路线。
一、新材料实现车身轻量化车身用钢的种类主要包括普通低碳钢板、高强度钢板、镀层钢板、激光拼焊钢板、不等厚棍轧钢板、夹层钢板等。
高强度钢板的性能为:屈服强度在210以上,因其是经固溶强化、析出强化、晶粒细化强化和组织相变强化,使其屈服强度和抗拉强度均较高,具有抗撞性和抗凹性。
主要包括:碳锰钢、无间隙原子钢、烘烤硬化钢等普通高强度钢;双相钢、相变诱导塑性钢、马氏体刚等先进高强度钢。
因力学性能更均匀、回弹量波动小、更高抗撞性和疲劳寿命,故可降低板厚使汽车轻量化。
主要用于需高强度、刚度、抗撞性的汽车零部件,如防撞梁、车门防撞杆、加强板、悬挂系统和车轮等零部件,但强塑积大于20000Mpa%的超高强度钢板因成形性能差带来在汽车应用上的技术挑战。
二、基于高强度钢板的车身结构多目标优化1 高强度钢板车身结构轻量化优化问题分析随着结构分析能力和手段的不断完善与结构优化设计理论的不断发展,车身结构轻量化优化设计的研究范围已开始从单一方面的准则优化减重发展到考虑车身结构各个性能在内的多目标优化。
因此,需要建立包含多个目标的优化设计函数,合理分配各目标之间的权重,确定优化设计的约束条件和设计变量,并通过多目标优化设计算法的求解,得到同时满足多个性能目标要求的优化求解方案。
基于高强钢的城市客车车身骨架轻量化开发设计

作者简介:张财智(1985—),男,工程师,硕士,主要从事客车结构强度 CAE 分析与 NVH 仿真研究。
58
机电技术
2018 年 2 月
主要把高强钢材料应用到车身骨架的侧围立柱、 顶盖弧杆以及底盘车架结构上。
1.4 车身骨架优化设计
国内外在客车车身骨架优化方面的研究较 多,也取得了较为明显的效果。目前针对车身机 构的轻量化设计,有如下方法:1)尺寸优化。建立 客车车身骨架的有限元模型,以车身的总质量为 优化束条 件进行尺寸优化。2)结构优化。一般是借助于有 限元分析技术,通过结构的拓扑和形状等优化设 计来实现轻量化。3)混合材料车身结构设计。比 如设计一种多结构复合材料车身,利用神经网络 建立车身骨架的优化模型,采用遗传算法进行求 解。4)基于内力优化的车身设计。从构建受力分 析提出一种基于构件内力优化的车身结构轻量化 设计方法[7,8]。
关键词:高强钢;客车;轻量化 中图分类号:U463.82+2 文献标识码:A 文章编号:1672-4801(2018)01-057-04 DOI:10.19508/ki.1672-4801.2018.01.018
节约能源、减少排放是汽车行业急需面对的 问题之一,特别是在商用车领域,由于其燃油消耗 量高、行驶里程更长,其消耗的石油总量远高于其 所占汽车数量比例[1,2]。在客车产业,为了有效解 决节能与环保问题,主要有两条技术路径:一是节 能与新能源汽车技术,即不断提高整车动力总成 的性能(发动机排放水平和传动系统的效率)和大 力发展新能源客车;另一就是轻量化技术,即如何 在保证安全性能的前提下使汽车“瘦身”。这两条 途径其实也是相辅相成的,轻量化技术对于客车 续航里程的提高和整车性能的提高提供了方向。
汽车用传统高强钢和先进高强钢
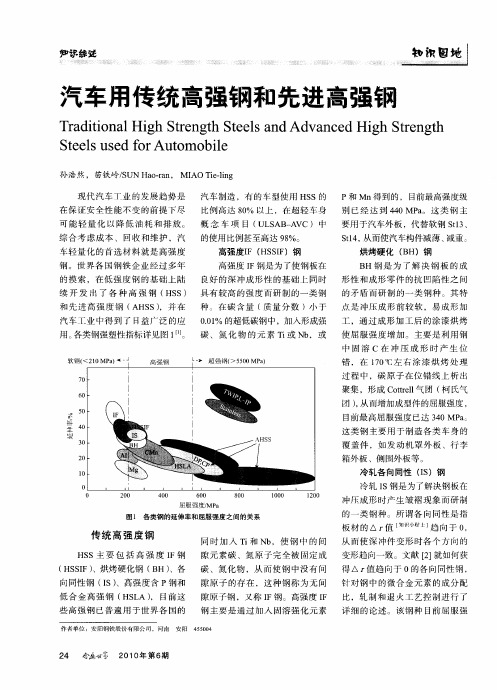
用。 各类钢强塑性指标详见 图 11 [ 碳 、氮 化 物 的元 素 T 或 N ,或 使 屈 服强度 增加 。主要是 利用钢 】 。 i b
中 固溶 C在 冲 压 成 形 时 产 生 位 错 ,在 10 7 ℃左 右 涂漆 烘 烤 处理 过程 中 ,碳原 子在 位错线 上析 出 聚集 ,形 成 C tel o rl气团 ( 氏气 t 柯 团 )从而增加成型件 的屈服强度 , ,
4 50 504
2 4
令蓬茁等 2 1 n 第 6 0 0 期
l 曰 地
. 1 _ . . 1 _
置
。
i
扣 缘 谬进
Fert — at n i ri M re st DP e e
度 级 别 有 2 0 6 、2 0 0 方 向 ,采用 的技术 主要 为相 变强 2 、2 0 8 、3 0
可 能 轻量 化 以降 低 油耗 和 排 放。 概 念 车 项 目 ( L A — vC)中 U S BA 要 用于汽车外板 ,代替软钢 Sl 、 t 3
综合 考虑 成本 、回收 和维护 ,汽 的使用 比例甚 至高达 9%。 8
车轻 量化 的首选材 料就 是高强 度 钢。世 界各 国钢铁企 业经 过多 年 的摸 索 ,在低 强度 钢 的基 础上 陆
低合 金 高强 钢 ( L ,目前 这 隙原子钢 ,又称 I 。高强度 I HS A) F钢 F
些 高强钢 已普遍用 于世 界各 国的
作者单位 :安阳钢铁股份有限公 司,河南 安阳
比 ,轧 制 和 退 火 工 艺 控 制 进 行 了
钢主要 是通过 加入 固溶强化 元素 详细 的论述 。该钢 种 目前 屈服 强
目前最高屈服强度 已达 3 0MP 。 4 a 这类 钢主要 用于制 造各类 车 身的
高强钢轻量化介绍

解决方案:优化设计,前期补偿,均匀变形
模具对策 高强钢 高强钢模具对策
模具设计与选材
•
超高强钢成形模具设计的主要关注点: – 冲压成形需要更大的力
– –
需要增加额外模具特征来进行回弹补偿 增加了成形时产生的热和模具的磨损
•
超高强钢成形所要求的高冲压力,增加了对模具材质的 关注,主要集中在 三个主要方面: – 模具基体需要更高的刚度和韧性以避免失效
– –
采用更硬的模具表面,以预防磨损 关注模具的表面粗糙度
焊接方案 高强钢 高强钢焊接方案
电阻焊: 焊接方案
•
如果任何一种类型的AHSS (DP, TRIP, CP或MS 钢) 在 首次使用时,使用者应参考软钢的焊接方案,然后: – 增加电极压力 约20% 或更多,这取决于屈服强度
– – – – –
国内外商用车自质量水平对比
自质量水平 牵引车(GCW=40吨)
几款国产车的自 重较Volvo FE 约重1/4左右
国内外商用车自质量水平对比
自质量水平 自卸车(GVW=25~26吨)
国内外商用车自质量水平对比
自质量水平 厢式车(GVW=12吨)
新车设计阶段技术降成本案例
SAPH400-2.0mm ,新车型设计碰撞安全性能要目标提 � 卡车车架一横梁标杆车为 车架一横梁标杆车为SAPH400-2.0mm SAPH400-2.0mm, 升; � 引导用户采用提升钢板强度和截面优化的技术策略,强度级别上升至 MPa ; 700 700MPa MPa; DP780 材料的设计定型。 � 提供了材料、成形、焊接等综合解决方案,实现了 提供了材料、成形、焊接等综合解决方案,实现了DP780 DP780材料的设计定型。 一横梁
2023年浅析我国汽车用钢市场发展前景大有可为
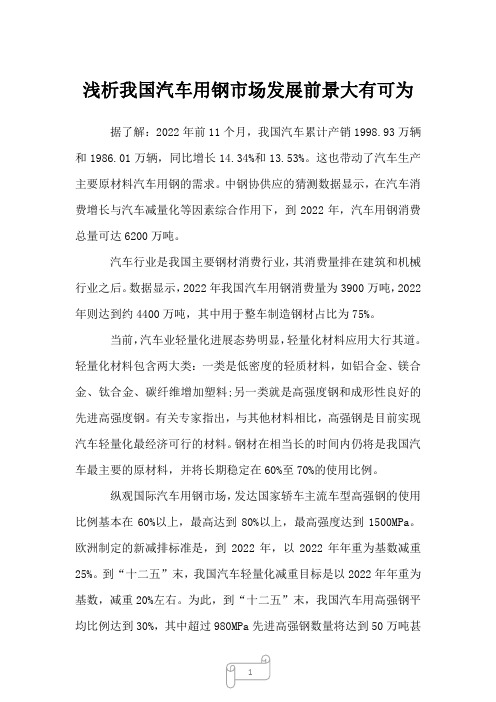
浅析我国汽车用钢市场发展前景大有可为据了解:2022年前11个月,我国汽车累计产销1998.93万辆和1986.01万辆,同比增长14.34%和13.53%。
这也带动了汽车生产主要原材料汽车用钢的需求。
中钢协供应的猜测数据显示,在汽车消费增长与汽车减量化等因素综合作用下,到2022年,汽车用钢消费总量可达6200万吨。
汽车行业是我国主要钢材消费行业,其消费量排在建筑和机械行业之后。
数据显示,2022年我国汽车用钢消费量为3900万吨,2022年则达到约4400万吨,其中用于整车制造钢材占比为75%。
当前,汽车业轻量化进展态势明显,轻量化材料应用大行其道。
轻量化材料包含两大类:一类是低密度的轻质材料,如铝合金、镁合金、钛合金、碳纤维增加塑料;另一类就是高强度钢和成形性良好的先进高强度钢。
有关专家指出,与其他材料相比,高强钢是目前实现汽车轻量化最经济可行的材料。
钢材在相当长的时间内仍将是我国汽车最主要的原材料,并将长期稳定在60%至70%的使用比例。
纵观国际汽车用钢市场,发达国家轿车主流车型高强钢的使用比例基本在60%以上,最高达到80%以上,最高强度达到1500MPa。
欧洲制定的新减排标准是,到2022年,以2022年年重为基数减重25%。
到“十二五”末,我国汽车轻量化减重目标是以2022年年重为基数,减重20%左右。
为此,到“十二五”末,我国汽车用高强钢平均比例达到30%,其中超过980MPa先进高强钢数量将达到50万吨甚至更高。
近年来,国内大型钢铁企业纷纷开展高强度汽车用钢研发生产,力求通过高附加值产品提升利润空间。
目前,国内企业生产的双相钢、复相钢、相变诱发塑性钢等先进的高强度汽车用钢产品已批量用于国内高等级汽车,其中800MPa级别冷轧和镀锌汽车板已实现批量供货,1200MPa、1500MPa级已具备批量生产力量,改写了知名品牌汽车用钢全部依靠进口的历史。
宝钢是国内最大的汽车冷轧板生产企业,特殊是在轿车面板生产方面表现突出,已成为国际上汽车板可供货品类最多的厂家之一。
[高强,汽车,技术]试论高强钢成形技术及其在汽车轻量化中的应用
![[高强,汽车,技术]试论高强钢成形技术及其在汽车轻量化中的应用](https://img.taocdn.com/s3/m/241a601289eb172dec63b703.png)
试论高强钢成形技术及其在汽车轻量化中的应用汽车轻量化是指在保证汽车的强度和安全性能的前提下,尽可能地减轻汽车的整车质量,从而提高汽车的动力性,减少燃料消耗,降低排气污染。
汽车的快速发展方便了人们的生活,但同时带来了金属、石油等资源、能源的过量消耗,大气严重污染,通过汽车轻量化实现降低排放和油耗成为汽车工业最具挑战的目标。
有研究表明,当钢板厚度分别减小0.05mm、0.1mm和0.15mm时,车身减重分别为6%、12%和18%,可见增加钢板强度的同时减小板厚是减轻车重的主要途径。
高强钢具有较高的强度,且成本较轻金属低,汽车采用先进高强钢的主要效果有:高强钢的使用降低了板厚使得汽车结构轻量化、汽车的抗凹陷性、耐久强度和大变形冲击强度安全性均得到提高。
高强钢的优点使得其在汽车行业中得到快速发展及广泛应用,如1980年日本和欧洲的汽车公司,白车身中高强钢用量分别为12%和5%,目前均上升到50%以上。
高强钢的应用不仅为轻量化创造了更多的机遇,更有助于使汽车达到轻量化和提高安全性的统一。
一、高强钢的种类高强度钢板的分类主要有按冶金特点、强化机理和生产工艺等几种划分方法。
1. 按冶金特点分类根据国际钢铁协会U S L - A B项目的定义,屈服强度为210 ~550MPa及抗拉强度为270 ~700M P a的为高强度钢(简称H S S)。
普通高强度钢为单一铁素体组织,由于采用了以相变为主的复合强化方法,基体的强度和综合性能得到提高。
普通高强度钢包括有微合金钢、碳锰钢、烘烤硬化钢、各向同性钢、高强度I F钢和低合金高强度钢等几种。
屈服强度大于550M P a及抗拉强度大于700M P a的则称为先进高强度钢(简称A H S S)。
A H S S 的研究基于H S S朝2个方向发展,一个方向是强度基体不变,提高其塑性;另一个方向是塑性基体不变提高其强度。
强度提高的钢种包括复向钢(C P)、马氏体钢(MS)等,塑性提高的钢种包括有双相钢(C P)、相变诱发塑性钢(T R I P)等。
汽车用先进高强度钢的特点和生产工艺
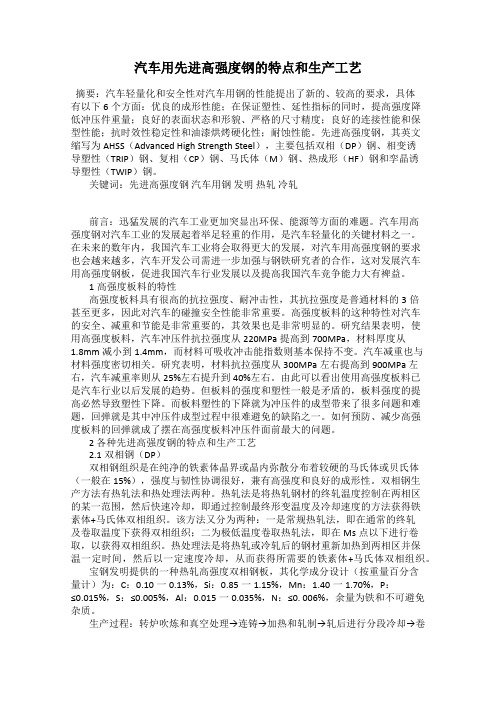
汽车用先进高强度钢的特点和生产工艺摘要:汽车轻量化和安全性对汽车用钢的性能提出了新的、较高的要求,具体有以下6个方面:优良的成形性能;在保证塑性、延性指标的同时,提高强度降低冲压件重量;良好的表面状态和形貌、严格的尺寸精度;良好的连接性能和保型性能;抗时效性稳定性和油漆烘烤硬化性;耐蚀性能。
先进高强度钢,其英文缩写为AHSS(Advanced High Strength Steel),主要包括双相(DP)钢、相变诱导塑性(TRIP)钢、复相(CP)钢、马氏体(M)钢、热成形(HF)钢和孪晶诱导塑性(TWIP)钢。
关键词:先进高强度钢汽车用钢发明热轧冷轧前言:迅猛发展的汽车工业更加突显出环保、能源等方面的难题。
汽车用高强度钢对汽车工业的发展起着举足轻重的作用,是汽车轻量化的关键材料之一。
在未来的数年内,我国汽车工业将会取得更大的发展,对汽车用高强度钢的要求也会越来越多,汽车开发公司需进一步加强与钢铁研究者的合作,这对发展汽车用高强度钢板,促进我国汽车行业发展以及提高我国汽车竞争能力大有裨益。
1高强度板料的特性高强度板料具有很高的抗拉强度、耐冲击性,其抗拉强度是普通材料的3倍甚至更多,因此对汽车的碰撞安全性能非常重要。
高强度板料的这种特性对汽车的安全、减重和节能是非常重要的,其效果也是非常明显的。
研究结果表明,使用高强度板料,汽车冲压件抗拉强度从220MPa提高到700MPa,材料厚度从1.8mm减小到1.4mm,而材料可吸收冲击能指数则基本保持不变。
汽车减重也与材料强度密切相关。
研究表明,材料抗拉强度从300MPa左右提高到900MPa左右,汽车减重率则从25%左右提升到40%左右。
由此可以看出使用高强度板料已是汽车行业以后发展的趋势。
但板料的强度和塑性一般是矛盾的,板料强度的提高必然导致塑性下降。
而板料塑性的下降就为冲压件的成型带来了很多问题和难题,回弹就是其中冲压件成型过程中很难避免的缺陷之一。
汽车轻量化技术方案及应用实例

汽车轻量化技术方案及应用实例一、汽车轻量化分析轻量化技术应用给汽车带来的最大优点就是油耗的降低,并且汽车轻量化对于环保,节能,减排,可持续发展也发挥着重大效用。
一般情况下,汽车车身的重量约占总重量的30%,没有承载人或物的情况下,大概70%的油耗是因为汽车自身的质量,由此可得到结论,车身的轻量化会减少油耗,提高整车的燃料经济性。
目前轻量化技术的主要思路是:在兼顾产品性能和成本的前提下,采用轻质材料、新成型工艺并配合结构上的优化,尽可能地降低汽车产品自身重量,以达到减重、降耗、环保、安全的综合指标。
二、新材料技术1、金属材料。
(1)高强度钢。
高强钢具有强度高、质量轻、成本低等特点,而普通钢是通过减薄零件来减轻质量的,它是汽车轻量化中保证碰撞安全的最主要材料,可以说高强钢的用量直接决定了汽车轻量化的水平。
另一方面,它与轻质合金、非金属材料和复合材料相比,制造成型过程相对容易,具有经济性好的优势。
(2)铝合金的密度小(2.7g/cm3左右),仅为钢的1/3,具有良好的工艺性、防腐性、减振性、可焊性以及易回收等特点,是一种非常优良的轻量化材料。
典型的铝合金零件一次减重(传统结构件铝替钢后的减重)效果可达30%~40%,二次减重(车身重量减轻后,制动系统与悬架等零部件因负载降低而设计的减重)则可进一步提高到50%,用作结构材料替换钢铁能够带来非常显著的减重效果。
(3)镁合金。
镁的密度仅为铝的2/3,是所有结构材料中最轻的金属,具有比强度和比刚度高、容易成型加工、抗震性好等优点。
采用镁合金制造汽车零件能在应用铝合金的基础上再减轻15%〜20%,轻量化效果十分可观,但成本偏高于铝合金和钢。
2、非金属材料。
(1)塑料是重要的非金属轻量化材料,具有比重小、成本低、易于加工、耐蚀性好等特点,在汽车行业中的应用前景被看好。
(2)树脂基复合材料根据增强体和基体材料不同分为多种类型增强基复合材料,如玻璃纤维增强复合材料、碳纤维增强复合材料、生物纤维增强复合材料等。
高强钢板在商用车轻量化车厢上的应用

高强钢板在商用车轻量化车厢上的应用
东风商用车技术 中心 东风商用车专用汽车厂 ( 湖北十堰 4 2 0 ) 欧 阳可居 刘永超 王德财 40 1 ( 湖北十堰 4 2 0 ) 张应龙 40 1
【 摘要l汽车轻量化是 目前汽车制造厂商关注的焦点。本文针对某商用 自卸车车厢 轻量化方面,对车厢结构
设计与轻量化材料的应 用等进行 了有效的尝试 。采用高强D 70 L 0材料 ,进行 了车厢 轻量化设计 ,对比轻量化前后
整个车厢的受载情况 ,进行 了多种不 同工况下的0 E A 模态分析,进行 了材料抗撞击模拟试验 。G E A 分析和物理模拟 试验结果 ,证明 了该轻量化车厢 设计的合理性 ,在实际运营过程中获得 了用户的好评。
减薄 实施 轻量化时 ,一股采用如下经验 公式 :
素之一 ,对商用车 车厢来说 ,减轻 自 重还可提高有效 载 重量 ,增加 了质量利用系数 ,从而提高 了运输效率 ,降 低 了运输 成本 , 对来说也降低 了燃油费用 。因此 ,实 相 现汽车轻 量化 ,降低燃油消耗 ,增加载货 质量 ,提高运
图1 使用中的某款 自卸车
车 厢在 满载 转 弯工 况下 ,对 比模 态CAE分析 结
参珈 … 旺—
! 皇 里 sc Alt 壅 壁 J eh pco Ra & pa er i i
果 。轻量化设计后 ,最大应力略大 于原设计 ,但低于材 料 屈服 强度 ( 见图3 、图4 )。其余 工况分析 结果具 体 见表 2 ,结果 表明 :轻量化设计后 ,整个车厢受 力状态
, — —
低强度钢的屈服强度 ; 高强度钢的屈服强度 。
先进高强度钢
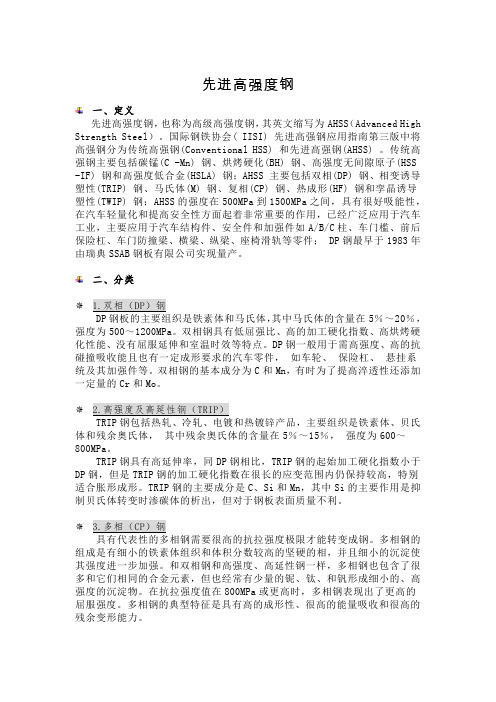
先进高强度钢一、定义先进高强度钢,也称为高级高强度钢,其英文缩写为AHSS(Advanced High Strength Steel)。
国际钢铁协会( IISI) 先进高强钢应用指南第三版中将高强钢分为传统高强钢(Conventional HSS) 和先进高强钢(AHSS) 。
传统高强钢主要包括碳锰(C -Mn) 钢、烘烤硬化(BH) 钢、高强度无间隙原子(HSS -IF) 钢和高强度低合金(HSLA) 钢;AHSS 主要包括双相(DP) 钢、相变诱导塑性(TRIP) 钢、马氏体(M) 钢、复相(CP) 钢、热成形(HF) 钢和孪晶诱导塑性(TWIP) 钢;AHSS的强度在500MPa到1500MPa之间,具有很好吸能性,在汽车轻量化和提高安全性方面起着非常重要的作用,已经广泛应用于汽车工业,主要应用于汽车结构件、安全件和加强件如A/B/C柱、车门槛、前后保险杠、车门防撞梁、横梁、纵梁、座椅滑轨等零件; DP钢最早于1983年由瑞典SSAB钢板有限公司实现量产。
二、分类1.双相(DP)钢DP钢板的主要组织是铁素体和马氏体,其中马氏体的含量在5%~20%,强度为500~1200MPa。
双相钢具有低屈强比、高的加工硬化指数、高烘烤硬化性能、没有屈服延伸和室温时效等特点。
DP钢一般用于需高强度、高的抗碰撞吸收能且也有一定成形要求的汽车零件,如车轮、保险杠、悬挂系统及其加强件等。
双相钢的基本成分为C和Mn,有时为了提高淬透性还添加一定量的Cr和Mo。
2.高强度及高延性钢(TRIP)TRIP钢包括热轧、冷轧、电镀和热镀锌产品,主要组织是铁素体、贝氏体和残余奥氏体,其中残余奥氏体的含量在5%~15%,强度为600~800MPa。
TRIP钢具有高延伸率,同DP钢相比,TRIP钢的起始加工硬化指数小于DP钢,但是TRIP钢的加工硬化指数在很长的应变范围内仍保持较高,特别适合胀形成形。
TRIP钢的主要成分是C、Si和Mn,其中Si的主要作用是抑制贝氏体转变时渗碳体的析出,但对于钢板表面质量不利。
汽车轻量化材料成型工艺分析

汽车轻量化材料成型工艺分析汽车轻量化是现代汽车工业发展的重要趋势之一,它能够显著提高汽车的燃油效率、降低排放、提升操控性能和安全性。
轻量化材料的应用和成型工艺是实现汽车轻量化的关键。
本文将探讨汽车轻量化材料的种类、成型工艺及其在汽车制造中的应用。
一、汽车轻量化材料的种类汽车轻量化材料主要包括高强度钢、铝合金、镁合金、复合材料等。
这些材料具有密度低、强度高、耐腐蚀性好等特点,是实现汽车轻量化的理想选择。
1.1 高强度钢高强度钢是汽车轻量化中应用最广泛的材料之一。
它通过优化合金成分和热处理工艺,实现了强度和韧性的双重提升。
高强度钢在汽车车身、底盘等关键部位的应用,可以有效降低整车重量,同时保持良好的安全性能。
1.2 铝合金铝合金以其低密度、高比强度和良好的铸造性能,成为汽车轻量化的另一重要材料。
铝合金可以通过铸造、锻造、挤压等工艺成型,广泛应用于汽车的发动机、变速箱、车身结构件等部件。
1.3 镁合金镁合金是所有结构材料中密度最低的金属,其密度仅为铝的2/3,钢的1/4。
镁合金的强度和刚度较高,且具有良好的阻尼性能和电磁屏蔽性能,适用于汽车的仪表板、座椅框架、轮毂等部件。
1.4 复合材料复合材料是由两种或两种以上不同材料组合而成的新型材料,具有重量轻、强度高、耐腐蚀等优点。
在汽车领域,常用的复合材料包括碳纤维增强塑料(CFRP)、玻璃纤维增强塑料(GFRP)等。
这些材料在汽车的车身、内饰、底盘等部位的应用,可以显著降低汽车的重量。
二、汽车轻量化材料的成型工艺汽车轻量化材料的成型工艺是实现材料性能的关键环节,不同的材料和应用场景需要采用不同的成型工艺。
2.1 铸造工艺铸造是将熔融金属倒入模具中,待其冷却凝固后形成所需形状的工艺。
对于铝合金和镁合金等材料,铸造工艺可以实现复杂形状的成型,且成本相对较低。
常见的铸造工艺包括砂型铸造、金属型铸造、低压铸造等。
2.2 锻造工艺锻造是通过施加外力使金属形成所需形状的工艺,它能够提高材料的密实度和强度。
汽车先进高强钢的应用与前景

先进高强钢吴文亚材料090120091590 先进高强钢的定义:先进高强度钢,也称为高级高强度钢,其英文缩写为AHSS (Advanced High Strength Steel)。
国际钢铁协会( IISI) 先进高强钢应用指南第三版中将高强钢分为传统高强钢(Conventional HSS) 和先进高强钢(AHSS) 。
传统高强钢主要包括碳锰(C -Mn) 钢、烘烤硬化(BH) 钢、高强度无间隙原子(HSS -IF) 钢和高强度低合金(HSLA) 钢;AHSS 主要包括双相(DP) 钢、相变诱导塑性(TRIP) 钢、马氏体(M) 钢、复相(CP) 钢、热成形(HF) 钢和孪晶诱导塑性(TWIP) 钢;AHSS的强度在500MPa到1500MPa之间,具有很好吸能性,在汽车轻量化和提高安全性方面起着非常重要的作用,已经广泛应用于汽车工业,主要应用于汽车结构件、安全件和加强件如A/B/C柱、车门槛、前后保险杠、车门防撞梁、横梁、纵梁、座椅滑轨等零件;DP钢最早于1983年由瑞典SSAB钢板有限公司实现量产。
先进高强钢的分类:双相钢:双相钢组成是铁素体基体包含一个坚硬的第二相马氏体。
通常强度随着第二相的体积分数的增加而增加。
在某些情况下,热轧钢需要在边缘提高抗拉强度(典型的措施是通过空穴的扩张能力),这样热轧钢便需要具有了大量的重要的贝氏体结构。
在双相钢中,在实际冷却速度中形成的马氏体中的碳式钢的淬硬性增加。
锰、铬、钼、钒、和镍元素单独添加或联合添加也能增加钢的淬硬性。
碳、硅和磷也加强了作为铁素体溶质的马氏体的强度。
高强度及高延性钢(TRIP):高强度及高延性钢的微观组织是在铁素体基体中还保留着残余奥氏体组织。
除了体积分数最少为5%的残余奥氏体外,还存在着不同数额的马氏体和贝氏体等坚硬组织。
多相钢:具有代表性的多相钢需要很高的抗拉强度极限才能转变成钢。
多相钢的组成是有细小的铁素体组织和体积分数较高的坚硬的相,并且细小的沉淀使其强度进一步加强。
鱼与熊掌兼得的艺术:三代先进高强钢

鱼与熊掌兼得的艺术:三代先进高强钢材料人轻量化专栏里很多次提到过高强钢,但往往是作为与碳纤维、铝合金比较而提及,今天,我们就为大家介绍经常被提起的产品。
不夸张地说,先进高强钢的应用和发展是危机下的产物。
在20世纪70年代之前,当时的汽车用钢主要性能指标是硬度。
在这一方面,高强钢与软钢没有什么区别,所以在汽车上应用很少。
而到了80年代,汽车业开始讲究燃油效率,迫使制造商们开始采用传统高强钢。
但到了90年代,危机来了!汽车设计者们开始采用铝合金、镁合金、纤维复合材来为汽车减重。
虽然这些材料的成本比钢铁要高,但是燃效和环保的压力让汽车制造商们觉得还是值得发展。
而当时先进高强钢成本高、难以焊接,虽然比起传统高强钢的韧性高,但是还是难以让汽车制造商引起兴趣。
于是,世界钢铁协会联合18个国家、34家钢企,组成“21世纪超轻量型汽车开发企业集团”,并启动了一系列项目,试图通过在以钢铁为基本材料的前提下,从结构设计、制造技术、零部件形状等多方面减轻汽车重量。
这里可能就要问一句了,为什么钢铁如此紧张汽车业呢?谁叫它俩爱得如此深沉呢!中钢协有数据称,汽车用钢目前占国内钢产量的8%,而国外是15%。
在基建市场疲软的大环境下,钢企普遍亏损,唯独几个生产汽车板的企业还能赚些钱。
要是汽车这块阵地也丢了,后果可想而知……当然,结果还是很理想的。
项目认为,先进高强钢预计使用比例超过 60%,在不增加成本的前提下,可实现车身减重 35%的目标,同时满足五星级安全碰撞标准。
此后,钢铁企业和协会,时不时地论证一番:先进高强钢才是汽车业轻量化的真爱。
车用钢材,通常可以分成:软钢、传统高强钢和第一代、第二代、第三代先进高强钢。
他们各自的伸长率和抗拉强度范围如下图:从这个表里可以看到,软钢具有很好的伸长率,意味着加工性能非常好,但抗拉强度最高不过300Mpa以内。
软钢主要有2个类别:低碳钢(Mild steel)和无间隙原子钢(IF steel)。
- 1、下载文档前请自行甄别文档内容的完整性,平台不提供额外的编辑、内容补充、找答案等附加服务。
- 2、"仅部分预览"的文档,不可在线预览部分如存在完整性等问题,可反馈申请退款(可完整预览的文档不适用该条件!)。
- 3、如文档侵犯您的权益,请联系客服反馈,我们会尽快为您处理(人工客服工作时间:9:00-18:30)。
汽车轻量化项目主要包括超轻车身( U L SA B) 、超轻覆盖件( U L SA C) 、超轻悬挂件( UL S AS) 和在此基础上的超轻概念车项目( ULS AB -AVC) , 均是以使用钢铁为基础.除了利用先进高强度钢板外 , 还大量采用了激光拼焊、激光焊接、液压成型和计算机模拟等技术来进行汽车的设计和制造。
AHSS 钢主要包括双相钢( D P)、相变诱发塑性钢( TRI P) 复相钢( CP )和马氏体钢( M)等,这类钢是通过相变组织强化来达到高强度的, 强度范围500 ~1500 MPa 。
具有高的减重潜力、高的碰撞吸收能、高的疲劳强度、高的成型性和低的平面各向异性等优点D P钢DP 钢板的商业化开发已近30,年包括热轧、冷轧、电镀和热镀锌产品。
主要组织是铁素体和马氏体, 其中马氏体的含量在5 %~20 %, 随着马氏体含量的增加, 强度线性增加, 强度范围为500~ 1 200 MPa 。
除了AHSS 钢的共性特点外, 双相钢还具有低的屈强比、高的加工硬化指数、高的烘烤硬化性能、没有屈服延伸和室温时效等特点。
DP 钢一般用于需高强度、高的抗碰撞吸收能且成形要求也较严格的汽车零件, 如车轮、保险杠、悬挂系统及其加强件等.热轧 D P 钢的生产是通过控制冷却来得到铁素体和马氏体的组织的, 冷轧和热镀锌DP 钢是通过铁素体和奥氏体两相区退火和随后的快速冷却来得到铁素体和马氏体组织的。
D P 钢的主要成分是C和Mn , 根据生产工艺的不同可适当添加Cr 、Mo 等元素使C曲线右移, 避免冷却时析出珠光体和贝氏体等组织。
复相钢复相(Complex Phase: CP)钢是指两相在数量和尺寸上有相同的数量级,其组织特点是细小的铁素体和高比例的硬质相如贝氏体、马氏体,含有铌、钛等元素。
复相钢基本上是在Mn-Cr-Si合金成分体系的基础上,通过马氏体、贝氏体以及Ti、Nb和V等微合金元素的晶粒细化效应和析出强化的复合作用,结合适当的卷取工艺而生产的,抗拉强度能够达到800~1000MPa。
具有很高的能量吸收能力和扩孔性能,广泛应用于汽车车身中车门的防撞杆、保险杠与B立柱等提高汽车安全性能的部件。
贝氏体钢贝氏体(Bainite: B)钢的微观组织为贝氏体,通过控制冷却速度或者空冷可以得到贝氏体组织。
贝氏体钢的化学成分主要由碳和微量铬、硼、钼、镍等合金元素组成,含碳量低于0.05%。
贝氏体钢的韧性好、强度高(530~1500MPa),并且随着贝氏体转变温度的降低,贝氏体钢的强度增加,贝氏体钢的成形能力和焊接性均很好,在航空航天、船舶与石油化工。
马氏体钢马氏体钢的微观组织为少量的铁素体和/或贝氏体均匀的分布在板条状的马氏体基体上。
通过在连续退火线或者出料辊道上的快速冷却作用,使奥氏体向马氏体完全转变从而得到马氏体钢。
向马氏体中加入碳元素能提高马氏体的淬硬性,起到强化的作用;为提高马氏体钢的淬透性可以加入不同比例的Mn、Mo、B、V、Ni、Si、Cr 等合金元素。
马氏体钢是先进高强钢中抗拉强度最高的钢种,最高能达到1700MPa。
相变诱发塑性钢相变诱发塑性(TRIP)钢是为了满足汽车工业对高强度、高塑性钢板的要求而开发研制的,微观组织主要为铁素体、贝氏体和残余奥氏体(体积分数一般为10%~20%)。
在冷成形过程中,残余奥氏体向硬的马氏体发生转变(形变诱导相变)的同时发生塑性变形。
这种硬化使得组织变形难以在局部集中并使应变分散,导致了整个组织中的塑性变形分布比较均匀,这种现象称为相变诱发塑性。
TRIP 钢具有强度高、延展性好、易冲压成形和能量吸收率高等特点,可以大幅度地减轻车身自重,降低油耗,同时能够抵御发生碰撞时的塑性变形,显著提高汽车的安全性能,在汽车制造领域有着巨大的优势。
TRIP 钢分为热轧型TRIP 钢和热处理型冷轧TRIP 钢。
热轧型TRIP 钢是通过控轧控冷获得大量的残余奥氏体组织。
热处理型冷轧TRIP 钢是在冷轧后采用临界加热,然后在下贝氏体转变温度范围内等温淬火。
快速加热至临界温度,形成铁素体-奥氏体混合组织。
与双相钢的热处理工艺最大的区别在于,为了在最终的组织中保留奥氏体,需要引入贝氏体等温淬火保持阶段(或缓冷)。
通过碳在未转变的奥氏体中的富集使马氏体转变温度降至低于零度,但仅通过铁素体形成时产生的碳富集是不够的,因此,贝氏体形成时会造成更多的碳富集。
通过添加硅或铝,不仅能起到固溶强化作用,而且还能阻止在贝氏体形成过程中碳化物析出。
孪生诱导塑性钢孪生诱导塑性(TWIP)钢是第二代先进高强钢的典型钢种,又称FeMn钢、高锰钢或现代轻质钢,成分特点是锰和铝含量较高,具有高强度、高加工硬化速率和优异的延展性(总延伸率可高达70%)。
主要有Fe-Mn-C钢、Fe-Mn-C-Al钢及Fe-Mn-C-Al-Si钢。
研究结果表明FeMn-TWIP钢加工硬化速率n值高且均匀,可承受局部应变峰值并具有良好的应变分布(抗颈缩),同时成形性能好,具有较好的能量吸收性能。
由于这类钢的处理工艺复杂、合金元素含量较高,虽然具有高强度和高韧性等良好的综合性能,但目前为止还没有商业化,在汽车工业上的应用还很有限。
相同成分DP钢和TRIP钢部分力学性能的比较对同一种钢板进行不同热处理分别制成具有相同铁素体含量的双相钢(DP钢)和相变诱发塑性变形钢(TRIP钢),并对其部分力学性能进行对比。
比较发现,铁素体基体上不同的第二相使得材料力学性能产生巨大差异:马氏体使DP钢具有很高的抗拉强度,残余奥氏体则赋予TRIP钢优良的伸长率;DP钢拥有更加优良的加工硬化能力,TRIP钢则具有较为理想的烘烤硬化能力。
试验表明,考察DP钢和TRIP钢的烘烤硬化能力时,除柯氏气团外,内应力的消除也应该考虑其中。
两种材料的组织有相似之处:F为基体,其上分布着较硬的第二相,不同之处在于第二相的种类和数量。
单轴拉伸试验,得到的负荷-应变曲线如图。
TRIP钢具有明显的屈服平台,而DP钢则呈现连续屈服的特点。
对两种材料的主要性能参数进行比较,结果见表DP钢淬火过程中,临界区保温形成的奥氏体转变成比容较大M,使周围的F受到压迫,在其内部生成大量位错,成为低应力下可激活的位错源因此其屈服强度(σ0.2)低于TRIP钢。
但是由于组织中存在40%M,其抗拉强度(σb)明显高于以B为主要第二相的TRIP钢。
虽然σb 不及DP钢,但TRIP钢的δ是DP钢的2.3倍,达到37%,TRIP钢优良的伸长率与形变过程中Ar转变为M有关,可从以下几点解释(1)拉伸变形时在最大变形部位首先诱发马氏体相变, 使局部强度提高, 难以继续变形, 变形向未发生马氏体相变的其他部位转移, 推迟了颈缩的形成。
(2)拉伸变形时局部应力集中因马氏体相变而松驰, 推迟了裂纹的产生。
(3)Ar与α呈共格关系, 高能界面不利于裂纹的扩展。
可看出,在相同应变下DP钢的WH值远远高于TRIP钢的,这与两种材料的组织密切相关,可从以下几点解释:(1)作为基体上的第二相,DP钢中的M和TRIP钢中的B起阻碍位错运动的作用。
M硬度远远高于B硬度, 因此其对位错具有更强的阻碍作用, 导致加工硬化很高。
由于M和B 含量很高, 因此这是导致两种材料加工硬化值性能差异的最主要原因。
(2) 变形过程中,TRIP钢中的Ar逐渐转变为M 释放了集中的内应力,降低了对位错阻碍作用,导致WH值下降。
(3)虽然TRIP钢中由A相转变得来的M会在继续变形时对位错起到较为强烈的阻碍作用,但是由于其含量很低因此对WH的贡献也较低。
在较低应变范围内(0%~2%),DP钢的加工硬化值很高(410MPa),而在较高应变范围内(>2%)给予相同应变,WH值增量显著降低。
原因:塑性变形之初,运动位错滑移到晶界处, 受到马氏体的阻碍停止运动, 强烈的阻碍作用使得必须产生新的位错或开动相邻晶粒中的滑移系才能保证塑变继续进行, 因此加工硬化值很高。
随着变形的进行, 大量位错在马氏体颗粒前塞积, 塞积的位错会对新产生的位错形成一定阻碍作用,而这一作用显著低于M的阻碍作用, 因此由其导致的WH增量明显降低。
高强钢的烘烤硬化能力成型后的汽车覆盖件在喷漆以后通常会置于170℃保温一段时间,称为烘漆。
烘漆后钢板屈服强度提高的现象称之为烘烤硬化(BakeHardening)。
烘烤硬化的机理是在烘烤过程中, 位错应力场中的碳(氮)原子受到热激活向位错偏聚, 形成柯氏气团,从而对位错起到钉扎作用,使其再次受载时需要更大的力才能摆脱气团或拖曳气团一起运动,宏观上表现为屈服强度的提高。
与固溶碳(氮)原子数目和位错密度密切相关。
Trip随着预变形量的增加,BH值先上升后下降。
因为塑变初期, 随着变形增加, 材料中位错密度增加,烘烤后被钉扎的位错数目增加, 因此BH值上升;但是由于材料中固溶碳原子有限, 当变形超过一定值后,形成的柯氏气团的饱和度下降,导致BH值降低。
对于DP钢的BH随预变形量增加而下降(10%预应变试样的BH值为-380MPa)。
DP钢的烘烤硬化能力差与其组织中存在一定含量M有关: 变形过程中,M强烈阻碍位错的同时产生很大的内应力,内应力对阻碍位错运动也起到很大作用, 而烘烤会使内应力部分释放,因此导致流变应力下降。
钢在奥氏体状态下加工变形以后再进行淬火,但为使钢在奥氏体状态下变形而不发生相变或析出第二相,钢中奥氏体应具有良好的热稳定性及机械稳定性这就需要在钢中加入较多的合金元素如C r、N i 等实际也就提高了钢的价格。
较高的锰含量有利于保持奥氏体的稳定性,而奥氏体的稳定性正是保持相变塑性的最重要因素。
很高的硅量可有效提高碳在渗碳体中的活度,抑制冷却过程及过时效中贝氏体转变期间渗碳体的析出使得奥氏体中碳含量的降低和随之而引起的稳定性降低。
钢中大量的硅易与退火炉气氛中的氧反应,生成二氧化硅附着于钢板表面而使热镀锌难以进行。
固溶的磷本身具有提高奥氏体稳定性的作用磷还可提高碳在渗碳体中的活度系数,抑制渗碳体的析出和奥氏体中碳含量的降低,结构钢中磷的晶界偏聚可引发钢的冷脆倾向。
Trip钢的屈服强度和抗拉强度均随应变率提高而呈指数形式增大。
均匀延伸率随应变率的提高总的趋势是逐渐减小。
因为残余奥氏体在拉伸过程中会应变诱发向马氏体转变,一方面有利于材料强度的提高,另一方面松弛了塑性变形引起的应力集中,延缓了微裂纹的形成,从而提高塑性。
高应变率变形的绝热温升提高了残余奥氏体的稳定性。
铁素体基体析出强化型高强热轧双相钢(14年参考文献)传统双相钢以组织强化为主要强化方式,通过组织强化虽然可提高强度降低屈强比,但由于软相铁素体与硬相马氏体的强度差较大,两相塑性应变不相容性加大,导致均匀变形能力降低不利于汽车零部件的成形,一定程度上限制了双相钢的应用。