煤化工产业科技发展状况综述
煤化工产业发展现状及发展方向
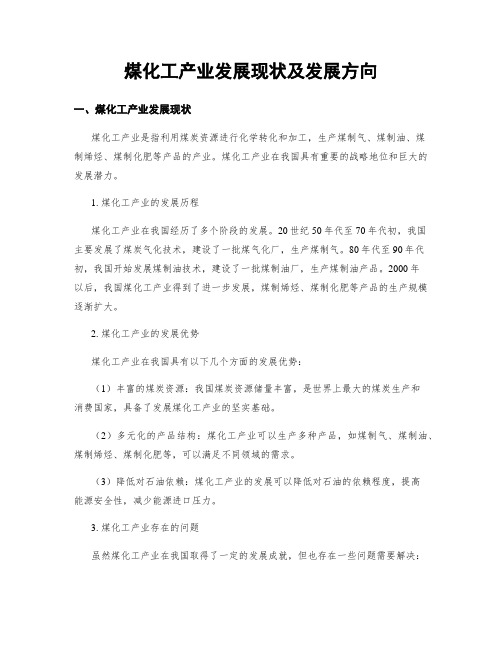
煤化工产业发展现状及发展方向一、煤化工产业发展现状煤化工产业是指利用煤炭资源进行化学转化和加工,生产煤制气、煤制油、煤制烯烃、煤制化肥等产品的产业。
煤化工产业在我国具有重要的战略地位和巨大的发展潜力。
1. 煤化工产业的发展历程煤化工产业在我国经历了多个阶段的发展。
20世纪50年代至70年代初,我国主要发展了煤炭气化技术,建设了一批煤气化厂,生产煤制气。
80年代至90年代初,我国开始发展煤制油技术,建设了一批煤制油厂,生产煤制油产品。
2000年以后,我国煤化工产业得到了进一步发展,煤制烯烃、煤制化肥等产品的生产规模逐渐扩大。
2. 煤化工产业的发展优势煤化工产业在我国具有以下几个方面的发展优势:(1)丰富的煤炭资源:我国煤炭资源储量丰富,是世界上最大的煤炭生产和消费国家,具备了发展煤化工产业的坚实基础。
(2)多元化的产品结构:煤化工产业可以生产多种产品,如煤制气、煤制油、煤制烯烃、煤制化肥等,可以满足不同领域的需求。
(3)降低对石油依赖:煤化工产业的发展可以降低对石油的依赖程度,提高能源安全性,减少能源进口压力。
3. 煤化工产业存在的问题虽然煤化工产业在我国取得了一定的发展成就,但也存在一些问题需要解决:(1)环境污染:煤化工生产过程中会产生大量的污染物,如二氧化硫、氮氧化物等,对环境造成严重影响。
(2)能源消耗:煤化工生产需要大量的能源供应,会增加对能源的消耗,对能源资源造成压力。
(3)技术创新不足:我国在煤化工领域的核心技术和装备仍然依赖进口,技术创新能力相对较弱。
二、煤化工产业发展方向为了进一步推动煤化工产业的发展,我国可以从以下几个方面进行努力:1. 加强环境保护在煤化工产业发展过程中,应加强环境保护工作,采取有效措施减少污染物排放,推动煤化工产业向清洁、低碳发展方向转变。
可以通过改进工艺技术,提高能源利用效率,减少污染物排放;加强废气、废水、固体废物的治理和处置,实现资源化利用。
2. 推动技术创新加强煤化工领域的技术创新,提高核心技术和装备的自主研发能力,降低对进口技术的依赖。
我国煤化工技术的现状以及发展前景分析
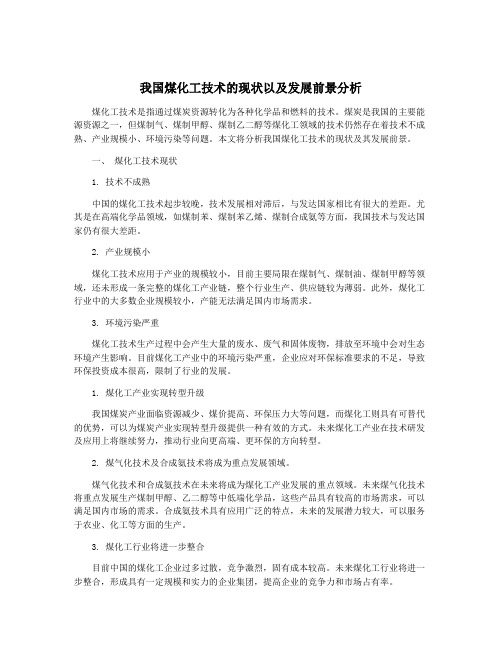
我国煤化工技术的现状以及发展前景分析煤化工技术是指通过煤炭资源转化为各种化学品和燃料的技术。
煤炭是我国的主要能源资源之一,但煤制气、煤制甲醇、煤制乙二醇等煤化工领域的技术仍然存在着技术不成熟、产业规模小、环境污染等问题。
本文将分析我国煤化工技术的现状及其发展前景。
一、煤化工技术现状1. 技术不成熟中国的煤化工技术起步较晚,技术发展相对滞后,与发达国家相比有很大的差距。
尤其是在高端化学品领域,如煤制苯、煤制苯乙烯、煤制合成氨等方面,我国技术与发达国家仍有很大差距。
2. 产业规模小煤化工技术应用于产业的规模较小,目前主要局限在煤制气、煤制油、煤制甲醇等领域,还未形成一条完整的煤化工产业链,整个行业生产、供应链较为薄弱。
此外,煤化工行业中的大多数企业规模较小,产能无法满足国内市场需求。
3. 环境污染严重煤化工技术生产过程中会产生大量的废水、废气和固体废物,排放至环境中会对生态环境产生影响。
目前煤化工产业中的环境污染严重,企业应对环保标准要求的不足,导致环保投资成本很高,限制了行业的发展。
1. 煤化工产业实现转型升级我国煤炭产业面临资源减少、煤价提高、环保压力大等问题,而煤化工则具有可替代的优势,可以为煤炭产业实现转型升级提供一种有效的方式。
未来煤化工产业在技术研发及应用上将继续努力,推动行业向更高端、更环保的方向转型。
2. 煤气化技术及合成氨技术将成为重点发展领域。
煤气化技术和合成氨技术在未来将成为煤化工产业发展的重点领域。
未来煤气化技术将重点发展生产煤制甲醇、乙二醇等中低端化学品,这些产品具有较高的市场需求,可以满足国内市场的需求。
合成氨技术具有应用广泛的特点,未来的发展潜力较大,可以服务于农业、化工等方面的生产。
3. 煤化工行业将进一步整合目前中国的煤化工企业过多过散,竞争激烈,固有成本较高。
未来煤化工行业将进一步整合,形成具有一定规模和实力的企业集团,提高企业的竞争力和市场占有率。
4. 鼓励技术创新我国政府一直鼓励企业加强科技研发,提高技术含量。
煤化工产业发展现状及发展方向

煤化工产业发展现状及发展方向一、引言煤化工产业是指利用煤炭资源进行化工加工,生产化学品、燃料和能源等产品的产业。
随着煤炭资源的日益紧缺和环境污染问题的加剧,煤化工产业的发展备受关注。
本文将对煤化工产业的发展现状进行分析,并提出相应的发展方向。
二、煤化工产业发展现状1. 产业规模目前,煤化工产业已经成为我国化工行业的重要组成部分。
据统计数据显示,我国煤化工产业在过去几年中保持了较快的增长速度。
2019年,煤化工产业的总产值达到了X亿元,同比增长X%。
煤化工产品的出口额也在逐年增加,达到了X 亿元。
2. 产品结构煤化工产业的产品结构多样化,主要包括煤制油、煤制气、煤制烯烃、煤制乙二醇等。
其中,煤制油是煤化工产业的核心产品之一,占据了产业总产值的X%。
此外,煤制气和煤制烯烃也是煤化工产业的重要产品,分别占据了产业总产值的X%和X%。
3. 技术水平煤化工产业的技术水平在不断提高。
近年来,我国在煤化工领域取得了一系列重要的技术突破,如煤间接液化技术、煤直接液化技术等。
这些技术的突破为煤化工产业的发展提供了强大的支撑。
4. 环境问题煤化工产业的发展也面临着一些环境问题。
煤化工生产过程中产生的废水、废气和固体废弃物对环境造成了一定的污染。
此外,煤化工产业的高能耗和高排放也给环境带来了一定的压力。
三、煤化工产业发展方向1. 提高煤化工产品附加值目前,我国煤化工产品的附加值相对较低,主要集中在初级产品上。
未来的发展方向是提高产品附加值,加大对高附加值产品的研发和生产力度。
例如,开发煤基新材料、煤基化学品等高附加值产品,提高产品质量和技术含量。
2. 推进煤化工技术创新技术创新是煤化工产业发展的关键。
应加大对煤化工技术研发的投入,提高技术创新能力。
重点发展煤化工新工艺、新装备和新材料,提高煤化工生产过程的效率和环保性。
3. 加强煤化工产业链协同发展煤化工产业链的协同发展对于提高产业整体竞争力至关重要。
应加强与煤炭开采、煤炭洗选、煤炭运输等环节的协同,实现资源的优化配置和产业链的高效运作。
煤化工产业发展现状及发展方向

煤化工产业发展现状及发展方向一、煤化工产业发展现状煤化工产业是指利用煤炭作为原料进行化学加工,生产各类化工产品的产业。
煤化工产业在我国具有重要的地位和作用,对于促进煤炭资源的合理利用、推动经济转型升级、保障能源安全等方面都有着重要的意义。
1. 产业规模与产值我国煤化工产业规模庞大,产值巨大。
根据统计数据显示,2022年全国煤化工产业总产值达到X亿元,较上年增长X%。
其中,煤制烯烃、煤制气体和煤制油等产品产量和销售额均居全国前列。
2. 技术水平与创新能力我国煤化工产业在技术水平和创新能力方面取得了长足的进步。
通过引进消化吸收国外先进技术、自主研发创新等手段,我国煤化工产业已经具备了一定的自主创新能力,部份关键技术已经达到国际先进水平。
3. 环境保护与可持续发展近年来,我国煤化工产业在环境保护和可持续发展方面加大了力度。
通过推进煤化工产业绿色化改造,加大环保投入,优化工艺流程,大幅减少了污染物排放,提高了资源利用效率,实现了煤炭资源的可持续利用。
二、煤化工产业发展方向1. 提高产品附加值未来,煤化工产业需要加大对高附加值产品的研发和生产。
通过提高产品质量和技术含量,增加产品附加值,提高企业竞争力和盈利能力。
例如,开辟绿色环保的高级煤制油技术,生产高品质的石油替代品,满足市场需求。
2. 推动绿色可持续发展煤化工产业需要加大对绿色化改造的力度,推动绿色可持续发展。
通过引进节能环保技术,减少能源消耗和污染物排放,提高资源利用效率。
同时,加强对废弃物的处理和回收利用,实现资源循环利用。
3. 加强国际合作与交流煤化工产业需要加强与国际合作与交流,吸收国外先进技术和管理经验。
通过与国外企业合作,共同开展研发合作项目,推动煤化工产业的国际化发展。
同时,积极参预国际标准制定和国际组织活动,提升我国煤化工产业的国际影响力。
4. 加大政策支持力度政府需要加大对煤化工产业的政策支持力度。
通过出台相关政策和法规,鼓励企业增加研发投入,提高技术水平和创新能力。
煤化工产业发展现状及发展方向
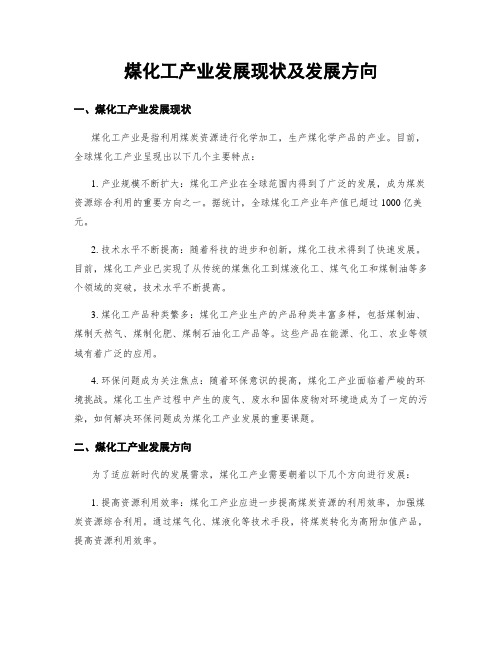
煤化工产业发展现状及发展方向一、煤化工产业发展现状煤化工产业是指利用煤炭资源进行化学加工,生产煤化学产品的产业。
目前,全球煤化工产业呈现出以下几个主要特点:1. 产业规模不断扩大:煤化工产业在全球范围内得到了广泛的发展,成为煤炭资源综合利用的重要方向之一。
据统计,全球煤化工产业年产值已超过1000亿美元。
2. 技术水平不断提高:随着科技的进步和创新,煤化工技术得到了快速发展。
目前,煤化工产业已实现了从传统的煤焦化工到煤液化工、煤气化工和煤制油等多个领域的突破,技术水平不断提高。
3. 煤化工产品种类繁多:煤化工产业生产的产品种类丰富多样,包括煤制油、煤制天然气、煤制化肥、煤制石油化工产品等。
这些产品在能源、化工、农业等领域有着广泛的应用。
4. 环保问题成为关注焦点:随着环保意识的提高,煤化工产业面临着严峻的环境挑战。
煤化工生产过程中产生的废气、废水和固体废物对环境造成为了一定的污染,如何解决环保问题成为煤化工产业发展的重要课题。
二、煤化工产业发展方向为了适应新时代的发展需求,煤化工产业需要朝着以下几个方向进行发展:1. 提高资源利用效率:煤化工产业应进一步提高煤炭资源的利用效率,加强煤炭资源综合利用。
通过煤气化、煤液化等技术手段,将煤炭转化为高附加值产品,提高资源利用效率。
2. 发展清洁煤技术:煤化工产业应加大对清洁煤技术的研发和应用,减少煤炭燃烧过程中产生的污染物排放。
同时,推动煤炭洗选技术的发展,提高煤炭的质量,减少煤炭资源的浪费。
3. 推进煤化工与新能源的融合:煤化工产业应与新能源产业相结合,推动煤化工与风能、太阳能等新能源的融合发展。
通过煤炭气化、合成气体制备等技术手段,将新能源与煤炭资源有机结合,实现资源的高效利用。
4. 加强环境保护措施:煤化工产业应加强环境保护工作,采取有效措施减少污染物排放。
加强废气、废水和固体废物处理,推动煤化工产业向绿色、环保方向发展。
5. 加强国际合作与交流:煤化工产业应加强国际合作与交流,吸收国际先进技术和经验,推动煤化工产业的创新发展。
煤化工产业发展现状及发展方向
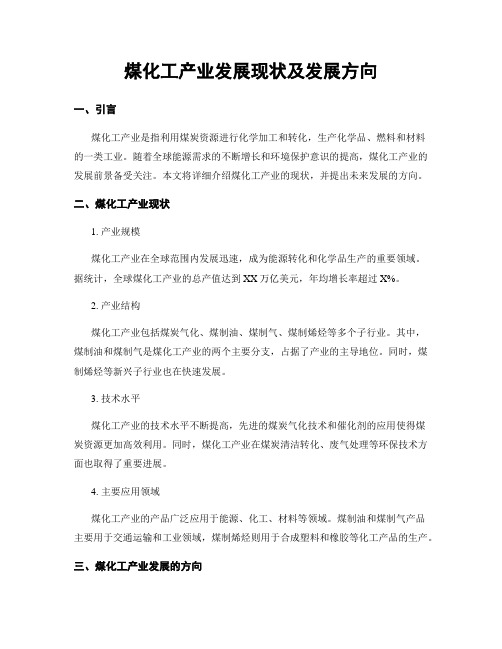
煤化工产业发展现状及发展方向一、引言煤化工产业是指利用煤炭资源进行化学加工和转化,生产化学品、燃料和材料的一类工业。
随着全球能源需求的不断增长和环境保护意识的提高,煤化工产业的发展前景备受关注。
本文将详细介绍煤化工产业的现状,并提出未来发展的方向。
二、煤化工产业现状1. 产业规模煤化工产业在全球范围内发展迅速,成为能源转化和化学品生产的重要领域。
据统计,全球煤化工产业的总产值达到XX万亿美元,年均增长率超过X%。
2. 产业结构煤化工产业包括煤炭气化、煤制油、煤制气、煤制烯烃等多个子行业。
其中,煤制油和煤制气是煤化工产业的两个主要分支,占据了产业的主导地位。
同时,煤制烯烃等新兴子行业也在快速发展。
3. 技术水平煤化工产业的技术水平不断提高,先进的煤炭气化技术和催化剂的应用使得煤炭资源更加高效利用。
同时,煤化工产业在煤炭清洁转化、废气处理等环保技术方面也取得了重要进展。
4. 主要应用领域煤化工产业的产品广泛应用于能源、化工、材料等领域。
煤制油和煤制气产品主要用于交通运输和工业领域,煤制烯烃则用于合成塑料和橡胶等化工产品的生产。
三、煤化工产业发展的方向1. 绿色发展随着环境保护意识的提高,煤化工产业需要加大环保投入,推动绿色发展。
在煤炭气化过程中,应加强废气处理和二氧化碳捕集技术的研究,减少对环境的负面影响。
同时,发展可再生能源与煤化工产业的结合,如生物质气化和太阳能氢制气等,将是未来的发展方向。
2. 创新技术煤化工产业需要不断推动技术创新,提高煤炭资源的利用效率和产品的附加值。
在煤炭气化领域,应加大煤气净化和催化剂研发的力度,提高气化效率和产品质量。
同时,应加强煤制油和煤制气技术的研究,提高产品的稳定性和适应性。
3. 产业协同发展煤化工产业应与其他相关产业进行协同发展,形成产业链和价值链的整合。
例如,与石油化工和新能源产业的合作,可以实现资源共享和技术共进,提高整个产业的竞争力。
同时,应加强与高校和科研机构的合作,共同推动煤化工产业的创新发展。
煤化工产业发展现状及发展方向

煤化工产业发展现状及发展方向一、煤化工产业发展现状煤化工产业是指利用煤炭资源进行化学转化和加工,生产出煤化工产品的产业。
随着全球能源需求的不断增长以及对环境保护的要求,煤化工产业在能源转型和绿色发展方面具有重要的意义。
下面将从煤化工产业的发展规模、技术水平和市场前景等方面进行详细介绍。
1. 发展规模目前,全球煤化工产业规模庞大。
以中国为例,中国是煤炭资源大国,煤炭资源储量丰富,是世界上最大的煤炭生产国和消费国。
中国煤化工产业发展迅速,已形成为了以煤炭气化、煤制油、煤制气、煤制烯烃等为主要技术路线的煤化工产业体系。
2022年,中国煤化工产业总产值达到XX亿元,占全国化工行业总产值的XX%。
2. 技术水平煤化工产业的技术水平是衡量其发展水平的重要指标。
目前,煤化工产业在技术创新和装备更新方面取得了一定的发展。
以煤炭气化技术为例,目前已经发展出了多种气化技术,如固定床气化、流化床气化、煤浆气化等。
这些技术在提高煤炭利用率、降低污染排放等方面具有重要意义。
3. 市场前景煤化工产品具有广泛的市场需求。
煤制油、煤制气、煤制烯烃等产品在能源、化工、交通等领域有着重要的应用。
随着全球能源需求的不断增长以及对环境保护的要求,煤化工产品具有较大的市场潜力。
估计未来几年,煤化工产业将保持较快的增长速度。
二、煤化工产业发展方向为了实现煤化工产业的可持续发展,需要在以下几个方面加强工作:1. 提高技术水平煤化工产业应加大技术研发力度,推动关键技术的突破和创新。
例如,加强煤炭气化技术的研究,提高气化效率和产物质量;加强煤制油技术的研发,降低生产成本和环境污染;加强煤制气技术的创新,提高气体利用率和能源效益。
2. 推动产业升级煤化工产业应加强与其他相关产业的合作,推动产业链的延伸和升级。
例如,与石油化工产业合作,发展煤炭与石油的协同加工技术;与新能源产业合作,推动煤炭资源的清洁高效利用。
3. 加强环境保护煤化工产业应加强环境保护工作,减少污染物排放,提高资源利用效率。
煤化工产业发展现状及发展方向 (2)
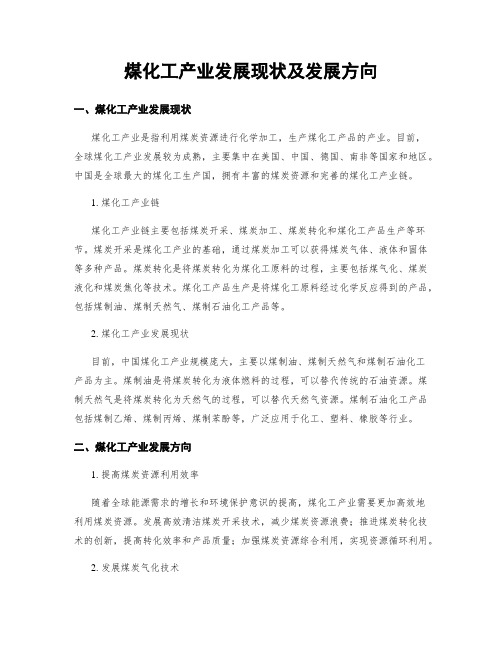
煤化工产业发展现状及发展方向一、煤化工产业发展现状煤化工产业是指利用煤炭资源进行化学加工,生产煤化工产品的产业。
目前,全球煤化工产业发展较为成熟,主要集中在美国、中国、德国、南非等国家和地区。
中国是全球最大的煤化工生产国,拥有丰富的煤炭资源和完善的煤化工产业链。
1. 煤化工产业链煤化工产业链主要包括煤炭开采、煤炭加工、煤炭转化和煤化工产品生产等环节。
煤炭开采是煤化工产业的基础,通过煤炭加工可以获得煤炭气体、液体和固体等多种产品。
煤炭转化是将煤炭转化为煤化工原料的过程,主要包括煤气化、煤炭液化和煤炭焦化等技术。
煤化工产品生产是将煤化工原料经过化学反应得到的产品,包括煤制油、煤制天然气、煤制石油化工产品等。
2. 煤化工产业发展现状目前,中国煤化工产业规模庞大,主要以煤制油、煤制天然气和煤制石油化工产品为主。
煤制油是将煤炭转化为液体燃料的过程,可以替代传统的石油资源。
煤制天然气是将煤炭转化为天然气的过程,可以替代天然气资源。
煤制石油化工产品包括煤制乙烯、煤制丙烯、煤制苯酚等,广泛应用于化工、塑料、橡胶等行业。
二、煤化工产业发展方向1. 提高煤炭资源利用效率随着全球能源需求的增长和环境保护意识的提高,煤化工产业需要更加高效地利用煤炭资源。
发展高效清洁煤炭开采技术,减少煤炭资源浪费;推进煤炭转化技术的创新,提高转化效率和产品质量;加强煤炭资源综合利用,实现资源循环利用。
2. 发展煤炭气化技术煤炭气化是将煤炭转化为合成气的过程,是煤化工产业的核心技术之一。
发展煤炭气化技术,可以实现煤炭资源的高效利用,并产生丰富的合成气体,用于煤制油、煤制天然气和煤制石油化工产品的生产。
同时,煤炭气化还可以减少对大气环境的污染,符合环保要求。
3. 推进煤化工产品结构升级当前,煤化工产品以煤制油、煤制天然气和煤制石油化工产品为主,产品结构相对单一。
为了适应市场需求和环境要求,需要推进煤化工产品结构的升级。
发展高附加值的煤化工产品,如煤基新材料、煤基碳纤维等,提高产品附加值和市场竞争力。
煤化工产业发展现状及发展方向
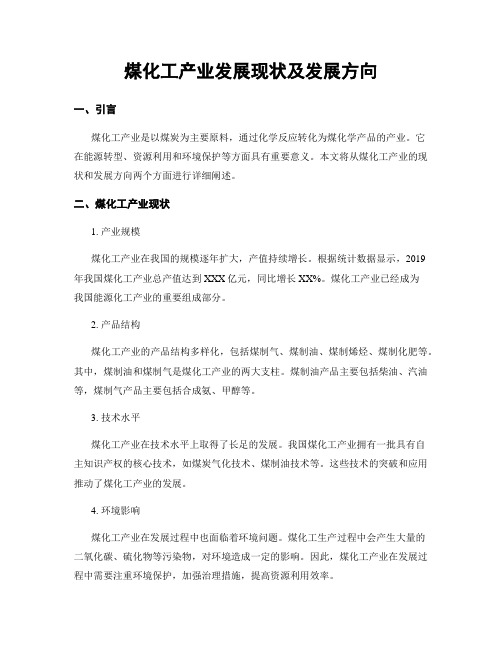
煤化工产业发展现状及发展方向一、引言煤化工产业是以煤炭为主要原料,通过化学反应转化为煤化学产品的产业。
它在能源转型、资源利用和环境保护等方面具有重要意义。
本文将从煤化工产业的现状和发展方向两个方面进行详细阐述。
二、煤化工产业现状1. 产业规模煤化工产业在我国的规模逐年扩大,产值持续增长。
根据统计数据显示,2019年我国煤化工产业总产值达到XXX亿元,同比增长XX%。
煤化工产业已经成为我国能源化工产业的重要组成部分。
2. 产品结构煤化工产业的产品结构多样化,包括煤制气、煤制油、煤制烯烃、煤制化肥等。
其中,煤制油和煤制气是煤化工产业的两大支柱。
煤制油产品主要包括柴油、汽油等,煤制气产品主要包括合成氨、甲醇等。
3. 技术水平煤化工产业在技术水平上取得了长足的发展。
我国煤化工产业拥有一批具有自主知识产权的核心技术,如煤炭气化技术、煤制油技术等。
这些技术的突破和应用推动了煤化工产业的发展。
4. 环境影响煤化工产业在发展过程中也面临着环境问题。
煤化工生产过程中会产生大量的二氧化碳、硫化物等污染物,对环境造成一定的影响。
因此,煤化工产业在发展过程中需要注重环境保护,加强治理措施,提高资源利用效率。
三、煤化工产业发展方向1. 绿色发展未来煤化工产业的发展方向是绿色发展。
通过技术创新和工艺改进,减少对环境的污染,提高资源利用效率。
发展低碳、清洁的煤化工技术,推动煤炭资源高效利用,减少对传统能源的依赖。
2. 产业升级煤化工产业需要加大科技创新力度,加强与其他行业的融合,推动煤化工产业的升级。
发展高附加值产品,提高产品质量和技术含量,提升产业竞争力。
3. 国际合作加强国际合作,借鉴和引进国外先进的煤化工技术和管理经验。
与国外企业开展技术合作、项目合作,推动我国煤化工产业的国际化发展。
4. 产业布局根据不同地区的资源禀赋和优势,合理规划煤化工产业的布局。
发展集约化、规模化的煤化工生产基地,实现资源的优化配置和产业的集聚效应。
煤化工产业发展现状及发展方向

煤化工产业发展现状及发展方向一、煤化工产业发展现状煤化工产业是指利用煤炭资源进行化学加工,生产煤化工产品的产业。
以煤为原料,通过煤气化、煤炭液化等技术手段,将煤转化为煤化工产品,如合成氨、甲醇、二甲醚、煤油等。
煤化工产业具有煤炭资源丰富、技术门坎高、市场需求广泛等特点。
目前,我国煤化工产业发展取得了长足的进步。
首先,煤化工产品的产量稳步增长。
以甲醇为例,2022年我国甲醇产量达到了1.2亿吨,位居全球第一。
其次,煤化工技术不断创新。
我国在煤气化、煤炭液化等关键技术方面取得了重要突破,提高了煤化工产品的质量和效率。
再次,煤化工产业链不断完善。
从煤炭开采到煤化工产品的生产和销售,形成为了完整的产业链条,促进了煤化工产业的可持续发展。
然而,煤化工产业也面临一些挑战。
首先,煤炭资源的有限性。
虽然我国煤炭资源丰富,但其开采和利用也面临一系列环境和安全问题。
其次,煤化工产业的环境污染问题。
煤化工生产过程中会产生大量的二氧化碳、氮氧化物等有害气体,对环境造成严重影响。
再次,煤化工产品的市场竞争激烈。
随着新能源和清洁能源的发展,煤化工产品面临着来自替代品的竞争压力。
二、煤化工产业发展方向为了促进煤化工产业的可持续发展,我们可以从以下几个方面进行努力:1. 提高煤化工技术水平。
加大对煤气化、煤炭液化等关键技术的研发投入,提高技术的稳定性和效率。
同时,加强煤化工技术的创新,推动煤化工产业向高效、低污染、低能耗的方向发展。
2. 加强环境保护和管理。
煤化工产业应积极采取措施减少二氧化碳、氮氧化物等有害气体的排放,加强废水和废气的处理,提高煤化工生产的环境友好性。
同时,加大对煤炭资源的保护和合理利用,推动煤化工产业向清洁、低碳的方向转变。
3. 拓宽煤化工产品的应用领域。
煤化工产品具有广泛的应用前景,可以用于化肥、能源、化工等多个领域。
煤化工产业应积极开展产品研发和推广应用,拓宽产品的市场空间,提高产品的附加值。
4. 加强国际合作与交流。
煤化工产业发展现状及发展方向

煤化工产业发展现状及发展方向引言概述:煤化工产业是指利用煤炭资源进行化学转化和加工,生产出煤化工产品的产业。
随着能源结构转型和环境保护要求的提高,煤化工产业在我国的发展前景备受关注。
本文将从煤化工产业的现状出发,分析其发展面临的挑战,并提出相应的发展方向。
一、资源丰富性1.1 煤炭资源储量丰富:中国是世界上煤炭资源最丰富的国家之一,煤炭资源储量居全球首位。
1.2 煤炭利用率低:目前我国煤炭资源的利用率较低,大量煤炭仍以燃煤形式使用,存在资源浪费问题。
1.3 煤炭资源开发利用需求:煤炭资源的开发利用是我国能源结构调整和绿色发展的重要方向。
二、环境压力与治理2.1 煤化工产业环境污染:传统煤化工产业存在大气污染、水污染等环境问题,对生态环境造成严重影响。
2.2 煤化工产业治理压力:随着环境保护要求的提高,煤化工产业面临严格的环境监管和治理压力。
2.3 煤化工产业绿色发展:煤化工产业需要加强环境治理,推动绿色发展,实现资源高效利用和污染减排。
三、技术创新与升级3.1 煤化工技术创新:煤化工产业需要加强技术创新,推动高效、清洁、低碳的煤化工技术研发和应用。
3.2 煤化工装备升级:煤化工装备水平需要提升,加大装备更新力度,提高生产效率和产品质量。
3.3 煤化工产业链延伸:煤化工产业应加强与其他行业的协同创新,形成完整的产业链,提升产业附加值。
四、市场需求与发展机遇4.1 煤化工产品市场需求:煤化工产品广泛应用于化工、能源、医药等领域,市场需求潜力巨大。
4.2 煤化工产业升级需求:随着经济发展和能源结构调整,煤化工产业需要升级转型,满足市场需求。
4.3 煤化工产业发展机遇:我国“一带一路”倡议和新型城镇化进程为煤化工产业发展提供了广阔的市场机遇。
五、发展方向与政策支持5.1 煤化工绿色发展:加强环境治理,推动煤化工产业绿色发展,实现资源高效利用和污染减排。
5.2 技术创新与升级:加大技术创新投入,推动煤化工技术的升级和装备的更新,提高产业竞争力。
煤化工产业发展现状及发展方向
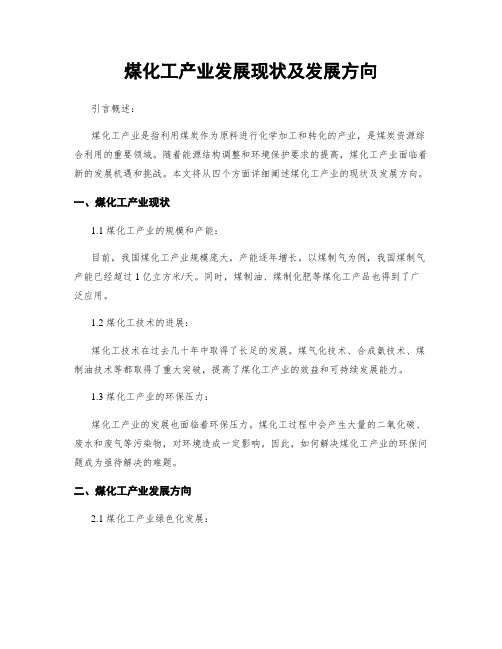
煤化工产业发展现状及发展方向引言概述:煤化工产业是指利用煤炭作为原料进行化学加工和转化的产业,是煤炭资源综合利用的重要领域。
随着能源结构调整和环境保护要求的提高,煤化工产业面临着新的发展机遇和挑战。
本文将从四个方面详细阐述煤化工产业的现状及发展方向。
一、煤化工产业现状1.1 煤化工产业的规模和产能:目前,我国煤化工产业规模庞大,产能逐年增长。
以煤制气为例,我国煤制气产能已经超过1亿立方米/天。
同时,煤制油、煤制化肥等煤化工产品也得到了广泛应用。
1.2 煤化工技术的进展:煤化工技术在过去几十年中取得了长足的发展。
煤气化技术、合成氨技术、煤制油技术等都取得了重大突破,提高了煤化工产业的效益和可持续发展能力。
1.3 煤化工产业的环保压力:煤化工产业的发展也面临着环保压力。
煤化工过程中会产生大量的二氧化碳、废水和废气等污染物,对环境造成一定影响。
因此,如何解决煤化工产业的环保问题成为亟待解决的难题。
二、煤化工产业发展方向2.1 煤化工产业绿色化发展:未来煤化工产业的发展方向是绿色化。
通过技术创新和工艺改进,减少对环境的污染,提高资源利用效率。
例如,开发高效节能的煤化工技术,推广清洁能源替代传统能源,减少二氧化碳排放。
2.2 煤化工产业的综合利用:煤化工产业应加强与其他产业的协同发展,实现资源的综合利用。
例如,将煤化工废弃物作为资源进行再利用,提高资源的利用率。
同时,通过与化工、能源等行业的深度融合,实现煤化工产业的升级和转型。
2.3 煤化工产业的国际合作:煤化工产业应积极拓展国际市场,加强与国外企业的合作与交流。
借鉴国外先进技术和管理经验,提高我国煤化工产业的竞争力。
同时,加强国际合作,共同应对全球气候变化等环境问题。
三、煤化工产业发展的政策支持3.1 制定煤化工产业发展规划:政府应制定明确的煤化工产业发展规划,明确发展目标和政策措施。
通过引导资金、技术和人才等要素向煤化工产业集聚,推动煤化工产业的快速发展。
煤化工产业发展现状及发展方向

煤化工产业发展现状及发展方向一、煤化工产业发展现状煤化工产业作为我国能源化工产业的重要组成部份,在国家经济发展中具有重要地位。
目前,煤化工产业在我国的发展取得了显著成绩,但也存在一些问题和挑战。
1. 产业规模和产能煤化工产业在我国的规模不断扩大,产能逐年增加。
目前,我国煤化工产业已经形成为了以煤炭气化、煤制油、煤制气、煤制甲醇等为主要产业链条的发展格局。
根据统计数据,我国煤化工产能已经达到XX万吨/年。
2. 技术水平和创新能力我国在煤化工领域的技术水平和创新能力也得到了显著提升。
在煤炭气化技术方面,我国已经掌握了多种气化技术,包括固定床气化、流化床气化、煤水浆气化等。
同时,我国在煤制油、煤制气、煤制甲醇等领域的技术也取得了重要突破。
3. 环境保护和可持续发展煤化工产业在环境保护和可持续发展方面面临一些挑战。
煤炭气化和煤制油等过程会产生大量的二氧化碳和其他污染物,对环境造成一定压力。
同时,煤化工产业对煤炭资源的依赖程度较高,对资源的可持续利用也提出了一定要求。
二、煤化工产业发展方向为了进一步推动煤化工产业的发展,我国可以从以下几个方面进行努力:1. 提高技术水平和创新能力通过加大科研投入,加强技术研发和创新,提高煤化工产业的核心竞争力。
可以加强煤炭气化技术的研究,提高气化效率和产物质量。
同时,加强煤制油、煤制气、煤制甲醇等领域的技术研发,提高产品质量和降低生产成本。
2. 推动产业结构升级和转型发展加大对煤化工产业的支持力度,鼓励企业进行技术改造和装备升级,提高产业的整体水平。
同时,加强与其他相关产业的协同发展,推动煤化工产业向高端、智能化方向发展。
3. 加强环境保护和资源节约在煤化工产业发展的过程中,要注重环境保护和资源的可持续利用。
加大对环境管理设施建设和运行的投入,减少污染物排放,提高环境保护水平。
同时,加强对煤炭资源的综合利用,提高资源利用效率。
4. 加强国际合作和市场开辟积极参预国际合作,吸收国外先进技术和管理经验,推动煤化工产业的国际化发展。
煤化工产业发展现状及发展方向

煤化工产业发展现状及发展方向一、介绍煤化工产业的背景和意义煤化工产业是指利用煤炭资源进行化学转化和加工,生产煤化学产品的产业。
煤炭是我国重要的能源资源,而煤化工产业的发展不仅可以提高煤炭资源的综合利用率,还可以促进经济发展,增加就业机会,改善环境质量等。
因此,煤化工产业的发展具有重要的战略意义。
二、煤化工产业的现状分析1. 产业规模:目前,我国煤化工产业已经初具规模,形成了以煤制油、煤制气、煤制化肥等为主要产品的产业链。
截至目前,全国共有XX个煤化工企业,年产值达到XX亿元。
2. 技术水平:我国在煤化工技术方面已经取得了一定的突破,例如煤直接液化、煤间接液化等技术已经达到国际先进水平。
同时,我国在煤化工催化剂、反应器等关键设备方面也有了一定的自主研发能力。
3. 产品结构:目前,我国煤化工产品以煤制油为主导,其他产品如煤制气、煤制化肥等也有一定的市场份额。
煤制油产品主要用于交通运输、化工等领域,煤制气主要用于城市燃气供应,煤制化肥则用于农业生产。
4. 环境问题:煤化工产业的发展也带来了一些环境问题,如废水、废气、固体废弃物的处理和排放等。
因此,在煤化工产业的发展过程中,必须加强环境保护,提高资源利用效率,减少对环境的影响。
三、煤化工产业的发展方向1. 创新技术:煤化工产业的发展需要依靠创新技术的支撑。
应加大对煤化工技术的研发投入,提高技术水平,提升产品质量和降低生产成本。
例如,可以加大对煤直接液化技术的研究,提高煤直接液化的效率和产品质量。
2. 优化产品结构:在煤化工产业的发展过程中,应优化产品结构,增加高附加值产品的比重。
可以发展生物燃料、高级石化产品等,提高产品附加值和市场竞争力。
3. 推动产业升级:应加大对煤化工产业的技术改造和装备升级力度,提高生产效率和资源利用效率。
可以引进先进的生产设备和技术,提高产业的整体竞争力。
4. 加强环境保护:在煤化工产业的发展过程中,必须加强环境保护工作,减少废水、废气、固体废弃物的排放,提高资源利用效率。
煤化工产业的发展现状
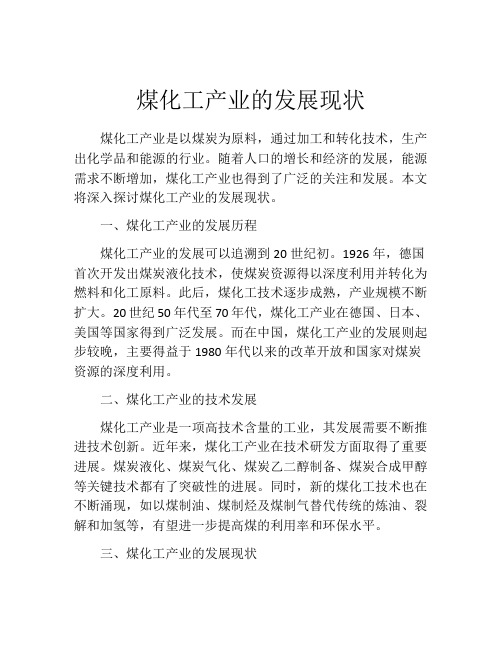
煤化工产业的发展现状煤化工产业是以煤炭为原料,通过加工和转化技术,生产出化学品和能源的行业。
随着人口的增长和经济的发展,能源需求不断增加,煤化工产业也得到了广泛的关注和发展。
本文将深入探讨煤化工产业的发展现状。
一、煤化工产业的发展历程煤化工产业的发展可以追溯到20世纪初。
1926年,德国首次开发出煤炭液化技术,使煤炭资源得以深度利用并转化为燃料和化工原料。
此后,煤化工技术逐步成熟,产业规模不断扩大。
20世纪50年代至70年代,煤化工产业在德国、日本、美国等国家得到广泛发展。
而在中国,煤化工产业的发展则起步较晚,主要得益于1980年代以来的改革开放和国家对煤炭资源的深度利用。
二、煤化工产业的技术发展煤化工产业是一项高技术含量的工业,其发展需要不断推进技术创新。
近年来,煤化工产业在技术研发方面取得了重要进展。
煤炭液化、煤炭气化、煤炭乙二醇制备、煤炭合成甲醇等关键技术都有了突破性的进展。
同时,新的煤化工技术也在不断涌现,如以煤制油、煤制烃及煤制气替代传统的炼油、裂解和加氢等,有望进一步提高煤的利用率和环保水平。
三、煤化工产业的发展现状目前,中国是世界上最大的煤炭生产和消费国,拥有丰富的煤炭资源。
煤炭资源的深度利用对中国经济的发展非常重要。
在当前世界经济走势下,煤化工产业的发展面临一些困难和挑战,但仍然具有广阔的发展前景。
1.煤化工产业规模不断扩大随着国家对煤炭资源深度利用的重视,中国煤化工产业规模不断扩大。
根据统计,中国煤化工产业总产值已超过1万亿元,2019年煤化工产品总产量已达到7亿吨,在国家的经济中占据了重要的地位,同时也为国家能源安全和经济发展提供了重要支持。
2.煤化工产业技术创新水平不断提高中国一直在加大对煤化工技术的研发和创新,不断提高产业技术水平。
目前,中国的煤化工技术正在向高效、低能耗、低污染方向发展,创新型企业正在崛起。
同时,煤化工周期长、技术要求高,产业链也比较长,但是目前科技的进步也能帮助人们更好地应对这些挑战。
煤化工产业发展现状及发展方向

煤化工产业发展现状及发展方向一、引言煤化工产业作为我国能源化工产业的重要组成部份,具有巨大的发展潜力和战略意义。
本文将从煤化工产业的现状和发展方向两个方面进行详细阐述。
二、煤化工产业现状1. 产业概况煤化工产业是指利用煤炭资源进行化学转化,生产煤制油、煤制气、煤制化肥、煤制石化等化工产品的产业。
目前,我国煤化工产业已经形成为了较为完善的产业链,涵盖了煤炭开采、煤炭洗选、煤制气、煤制油、煤制化肥、煤制石化等环节。
2. 发展现状(1)技术水平:我国煤化工产业在技术水平上已经取得了一定的突破,特殊是在煤制气和煤制油方面,已经具备了较为成熟的技术和装备。
例如,煤制气技术已经实现了从传统的焦炉煤气到现代煤制气的转变,煤制油技术也实现了从间接液化到直接液化的发展。
(2)产业规模:我国煤化工产业的产能不断扩大,已经成为全球煤化工产业的重要参预者。
据统计,2022年我国煤化工产业总产值超过1.5万亿元,占全国化工产业总产值的比重超过20%。
(3)环境问题:煤化工产业在发展过程中也面临着环境问题。
由于煤炭资源的高污染性,煤化工产业的发展对环境造成为了一定的压力。
因此,如何解决煤化工产业的环境问题,成为了当前亟待解决的难题。
三、煤化工产业发展方向1. 转型升级为了解决煤化工产业的环境问题,我国煤化工产业应该加快转型升级,采用清洁高效的生产技术和装备。
例如,可以推广煤制气和煤制油的现代化技术,提高产品的质量和效率,并降低对环境的影响。
2. 创新发展煤化工产业应该加大科技创新力度,加强技术研发和创新能力,推动煤化工产业向高端化、智能化和绿色化方向发展。
例如,可以研发新型催化剂和高效反应器,提高煤化工产业的技术水平和经济效益。
3. 产业协同煤化工产业应该加强与其他相关产业的协同发展,形成产业链的完整闭环。
例如,可以与煤炭开采、煤炭洗选、煤炭运输等环节进行深度合作,实现资源的高效利用和产业的协同发展。
4. 国际合作煤化工产业应该加强与国际间的合作交流,借鉴先进技术和管理经验,提高我国煤化工产业的国际竞争力。
煤化工产业现状及技术发展趋势
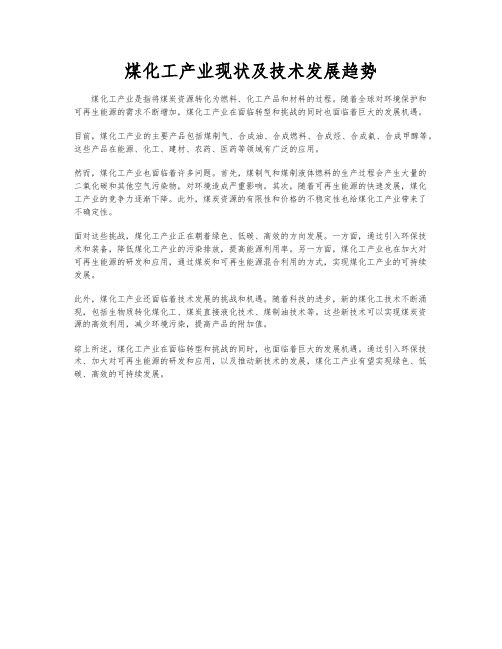
煤化工产业现状及技术发展趋势
煤化工产业是指将煤炭资源转化为燃料、化工产品和材料的过程。
随着全球对环境保护和可再生能源的需求不断增加,煤化工产业在面临转型和挑战的同时也面临着巨大的发展机遇。
目前,煤化工产业的主要产品包括煤制气、合成油、合成燃料、合成烃、合成氨、合成甲醇等。
这些产品在能源、化工、建材、农药、医药等领域有广泛的应用。
然而,煤化工产业也面临着许多问题。
首先,煤制气和煤制液体燃料的生产过程会产生大量的二氧化碳和其他空气污染物,对环境造成严重影响。
其次,随着可再生能源的快速发展,煤化工产业的竞争力逐渐下降。
此外,煤炭资源的有限性和价格的不稳定性也给煤化工产业带来了不确定性。
面对这些挑战,煤化工产业正在朝着绿色、低碳、高效的方向发展。
一方面,通过引入环保技术和装备,降低煤化工产业的污染排放,提高能源利用率。
另一方面,煤化工产业也在加大对可再生能源的研发和应用,通过煤炭和可再生能源混合利用的方式,实现煤化工产业的可持续发展。
此外,煤化工产业还面临着技术发展的挑战和机遇。
随着科技的进步,新的煤化工技术不断涌现,包括生物质转化煤化工、煤炭直接液化技术、煤制油技术等。
这些新技术可以实现煤炭资源的高效利用,减少环境污染,提高产品的附加值。
综上所述,煤化工产业在面临转型和挑战的同时,也面临着巨大的发展机遇。
通过引入环保技术、加大对可再生能源的研发和应用,以及推动新技术的发展,煤化工产业有望实现绿色、低碳、高效的可持续发展。
煤化工产业发展现状及发展方向
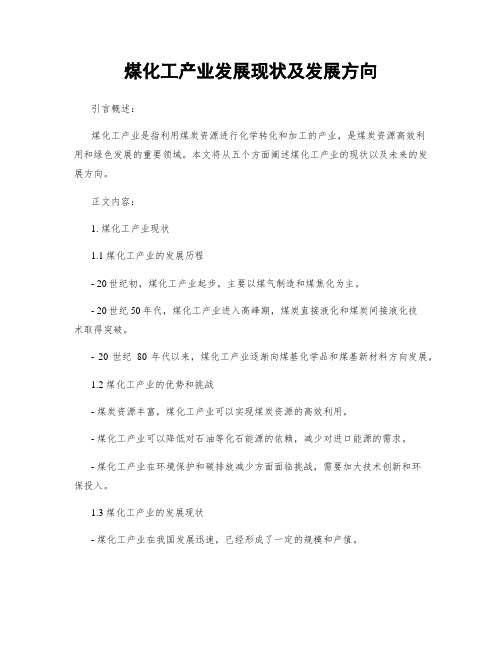
煤化工产业发展现状及发展方向引言概述:煤化工产业是指利用煤炭资源进行化学转化和加工的产业,是煤炭资源高效利用和绿色发展的重要领域。
本文将从五个方面阐述煤化工产业的现状以及未来的发展方向。
正文内容:1. 煤化工产业现状1.1 煤化工产业的发展历程- 20世纪初,煤化工产业起步,主要以煤气制造和煤焦化为主。
- 20世纪50年代,煤化工产业进入高峰期,煤炭直接液化和煤炭间接液化技术取得突破。
- 20世纪80年代以来,煤化工产业逐渐向煤基化学品和煤基新材料方向发展。
1.2 煤化工产业的优势和挑战- 煤炭资源丰富,煤化工产业可以实现煤炭资源的高效利用。
- 煤化工产业可以降低对石油等化石能源的依赖,减少对进口能源的需求。
- 煤化工产业在环境保护和碳排放减少方面面临挑战,需要加大技术创新和环保投入。
1.3 煤化工产业的发展现状- 煤化工产业在我国发展迅速,已经形成了一定的规模和产值。
- 煤基化学品、煤基新材料、煤基液体燃料等领域取得了一系列技术突破和产业化进展。
- 煤化工产业在能源化工、化学工程与技术等领域具有广阔的应用前景。
2. 煤化工产业发展方向2.1 优化煤化工技术- 加强煤炭气化和煤炭液化等核心技术研发,提高煤化工产业的技术水平和竞争力。
- 推动煤炭气化技术的发展,提高气化效率和产品质量。
- 加强煤炭液化技术的研究,提高液化产物的利用率和降低成本。
2.2 发展煤基化学品和煤基新材料- 加大对煤基化学品和煤基新材料的研发力度,提高产品质量和降低生产成本。
- 推动煤基化学品的应用,扩大市场份额。
- 加强煤基新材料的研究和开发,提高产品性能和应用领域。
2.3 推动煤化工产业绿色发展- 加大环保投入,推动煤化工产业向清洁生产和低碳发展方向转变。
- 提高煤化工产业的环境管理水平,减少污染物排放和资源浪费。
- 加强煤化工产业的循环经济建设,实现资源的高效利用和能源的清洁转化。
总结:煤化工产业作为煤炭资源高效利用和绿色发展的重要领域,具有巨大的发展潜力。
- 1、下载文档前请自行甄别文档内容的完整性,平台不提供额外的编辑、内容补充、找答案等附加服务。
- 2、"仅部分预览"的文档,不可在线预览部分如存在完整性等问题,可反馈申请退款(可完整预览的文档不适用该条件!)。
- 3、如文档侵犯您的权益,请联系客服反馈,我们会尽快为您处理(人工客服工作时间:9:00-18:30)。
煤化工产业科技发展状况综述(2)煤炭液化。
煤炭液化分为间接液化和直接液化。
煤间接液化是将煤首先经过气化制得合成气(CO +H2),合成气再经催化合成(F-T合成等)转化成有机烃类。
煤间接液化的煤种适应性广,并且间接液化过程的操作条件温和,典型的煤间接液化的合成过程在250℃、15~40个大气压下操作。
此外,有关合成技术还可以用于天然气以及其他含碳有机物的转化,合成产品的质量高,污染小。
煤间接液化合成油技术在国外已实现大规模工业化。
南非基于本国丰富的煤炭资源优势,建成了年耗煤近4200万吨、生产合成油品约500万吨和200万吨化学品的合成油厂。
在技术方面,南非SASOL公司经历了固定床技术(1950~1980)、循环流化床(1970~1990)、固定流化床(1990~)、浆态床(1993~)4个阶段。
20世纪90年代中期,我国在加紧开发合成汽油固定床工艺的动力学和软件包的同时,开展了合成柴油催化剂和先进的浆态床合成汽油工艺的研究。
1998年以后,自主开发了铁催化剂(ICC-IA),合成效率接近SASOL水乎,有望在大规模生产后使成本从8万元/吨降到3万元/吨。
还开发出可以大规模廉价生产的新型铁催化剂ICC-IB,催化剂各项指标超过国外同等催化剂,预计工业化后,结合浆态床工艺的低成本可以使煤基合成油具有很强的经济竞争力。
目前,国内技术已经发展到可以产业化的阶段,包括反应器在内的所有设各和控制系统均可在国内制造。
直接液化是煤直接通过高压加氢获得液体燃料。
1913年,德国柏吉乌斯首先研究了煤的高压加氢,并获得世界上第一个煤炭液化专利。
到1944年,德国煤炭直接液化工厂的油品生产能力已达到423万吨/年,为第二次世界大战中的德国提供了2/3的航空燃料和50%的汽车、装甲车用油。
20世纪50年代起中东地区发现大量廉价石油,使煤炭直接液化暂时失去了竞争能力,70年代的世界石油危机又使煤炭液化技术开始活踩。
世界上有代表性的煤直接液化工艺是德国的新液化(IGOR)工艺,美国的HTI工艺和日本的NEDOL工艺。
这些新液化工艺的共同特点是煤炭液化的反应条件比老液化工艺大为缓和,生产成本有所降低,中间放大试验已经完成。
目前还未出现工业化生产厂,主要原因是约为25美元/桶的生产成本仍竞争不过廉价石油。
今后的发展趋势是通过开发活性更高的催化剂和对煤进行顶处理以降低煤的灰分和惰性组分,进一步降低生产成本。
我国从20世纪70年代末开始研究煤炭直接液化技术,已建成具有国际先进水平的煤炭直接液化、液化油提质加工和分析检验实验室,开展了基础研究和工艺开发,取得了一批科研成果。
目前,从煤一直到合格产品的全流程已经打通,有关的基础性研究将为进一步工艺放大和建设工业化生产厂奠定基础。
3.洁净煤发电技术洁净煤发电技术主要有常规煤粉发电机组加烟气污染物控制技术、循环流化床燃烷(CFBC)、增压流化床燃烧(PFBC)以及整体煤气化联合循环(IGCC)等。
(1)常规燃煤发电机组加烟气净化。
现代化的燃煤超超临界蒸汽循环通过提高蒸汽参数来提高机组效率,目前最高蒸汽参数约为300bar/600℃,净热效率约为45%。
与现有亚临界电厂相比,每单位发电量CO2排放量降低15%左右。
超临界蒸汽循环发电技术与现有亚临界电厂几乎相同,技术成熟度和设备可利用率相当高,电厂成本相当。
在采用现代烟气净化设备后,SO2氮氧化物(NOx)及粉尘排放能满足很高的环保标准。
我国已能成批生产亚临界机组,在超临界、超超临界汽轮机的试验研究工作中形成了一支有相当实力的科技队伍。
我国引进2×600MWe、4×500MWe、2~800MWe共8台超临界机组,为开发研制超临界、超超临界机组提供了有益的借鉴,国内各大制造厂正在积极进行超临界、超超临界汽轮机开发的前期技术准备工作。
常规燃煤发电机组要达到洁净发电,还必须在系统中增加烟气净化设备,通过烟气脱硫、脱硝和除尘,达到降低SO2、NO2和烟尘排放的目的。
发达国家大型燃煤锅炉都配备效率达95%以上的湿法烟气脱硫设备,中小锅炉也采用经济可行的炉内喷钙及增湿活化脱硫工艺。
我国目前在燃煤锅炉电站烟气脱硫方面有较大差距,先后引进了几套燃煤电厂的脱硫装置,但引进设备价格贵、运行成本较高。
国内进行了许多脱硫技术的研究开发,出现了具有自主知识产权的循环流化床烟气脱疏、湿法烟气脱硫、新型电子束-半干法烟气净化等工艺,但总体上还属于起步阶段。
国外大多在大型锅炉上安装低NO2燃烧器,使NO2排放水平控制在500mg/(N.m3),降低40%左右。
对于挥发份较高的煤种,采用低NOX燃烧器配合空气分级燃烧,最大可降低60%-70%的NO2排放量,但对低挥发份煤种的效果有限。
国外新研制的再燃烷技术可以大幅度地降低NO2排放量(对于烟煤锅炉,可低于200mg/m3),并且对主燃料的煤种适应性广。
该技术是美国能源部洁净煤技术的一项重要成果,正在美国电站煤粉锅炉上进行大面积推广。
国产引进型300MW以上机组都装有低NO2燃烧器,基本能符合当前排放标准,而300MWe以下机组尚无脱硝控制措施。
国内,还没有采用再燃烧技术降低煤粉锅炉NO2排放的系统研究报道或工业示范。
一些高校和科研院所从稳燃角度出发,开发设计出一些新型浓淡燃烧器,具有良好的NO2减排特性。
发达国家大型燃煤锅炉都配各5个甚至更多个电场的高效电除尘器或多室的布袋除尘器,除尘效率达到99.9%。
我国近年来建设的大型燃煤锅炉一般配3~4个电场的电除尘器,效率低于99%,大量中小火电机组的除尘设备落后。
(2)循环流化床燃烧(CFBC)循环流化床锅炉可以高效率地燃烧各种燃料(特别是劣质煤),通过加人脱硫剂控制在燃烧过程中SO2的排放,流化床低温燃烧也控制了NO2的生成。
自20世纪70年代以来,国际上CFBC的大型化取得了长足进步,现有CFBC锅炉的容量已经发展到电站锅炉的等级,250MWE的循环流化床在法国己投人商业运行,300~400MWE等级循环流化床锅炉已签订合同。
大型循环流化床锅炉已走向技术成熟阶段,发展大容量、高参数(超临界)循环流化床锅炉有可能成为一个新的发展方向。
我国CFBC技术的研究开发基础较强。
采用自有技术开发,已具备设计制造410t/h以下等级循环流化床锅炉的能力,占据国内大部分75t/h等级以下的循环流化床锅炉市场。
国内已经启动自主技术的150MWE级超高压再热和引进300MWe等级CFBC锅炉示范工程。
(3)增压流化床燃烷(PFBC)PFBC除具有与CFBC相似的优势外,加压流化床燃烧产生的高温烟气经过除尘,进人燃气轮机作功,由此构成增压流化床燃烧联合循环(PFBC-CC)。
其发电能力比相同蒸汽参数的单汽轮机发电增加20%,效率提高3%~4%,特别适于改造现有常规燃煤电站。
蒸汽循环还可采用高参数包括超临异汽轮机以提高效率。
世界上目前已建成的PFBC-CC电站有8座,除一座电站容量为360MWe外,其他电站容量为80~100MWE等级。
但第一代PFBC-CC技术受到流化床燃烧温度的限制,采用两级高温旋风分离除尘后的烟气含尘浓度仍然较高,因此不能采用已有的高温、高效常规燃气轮机,联合循环供电效率难于进一步提高。
我国对PFBC技术的研究开发己有近20年的历史,特别是在“八五”、“九五”期间,采用国内技术和装备在徐州贾汪发电厂建成PFBC-CC中间试验电站(15MWe),标志着已从实验室基础研究走向了工业化试验。
为加快PFBC-CC技术的开发,国家计划建造100MWe等级的PFBC-CC示范电站,拟引进国外部分先进技术,除燃气轮机需直接引进国外制造设备外,大部分设备将由国内制造。
第二代PFBC(PFCB)-CC技术采用部分气化和前置燃烧的方法把燃气轮机的入口温度提高到1100~1300℃,同时可采用超临界蒸汽参数,使联合循环效率有可能达到45%~48%。
这种先进的发电系统尚处于中试阶段,如美国能源部支持Foster Wheeler公司牵头开发的APFBC技术正在进行中试规模的试验研究,并已开始商业示范电站的设计工作。
英国原煤炭研究所(CoaL Research Establishment)开发的前置循环(topping cycle)及气化炉技术已转让给三井巴布科克(Mitsui Babcock,简称MB)公司,改称为空气气化循环(Air Blown Gasfication Cycle,简称ABGC)。
MB也在寻求包括中国在内的其他合作伙伴,推进该技术的示范和商业化进展。
由于部分气化燃烧联合循环技术难度小,投资低,顶计在2010前有可能实现商业化应用,从而成为一种可与IGCC竞争的新型燃煤联合循环技术。
对于第二代PFBC-CC,我国在“八五”期间,进行了部分关键技术的初步研究,如喷动流化床部分气化炉、低热值煤气燃烧室、过滤式高温除尘器等。
在煤炭热解气化、流化床燃烧、高温煤气和烟气净化技术的试验研究方面已有大量的工作基础,现有水平与国外相关研究开发相比,差距并不太大。
在国家重点基础研究发展规划“973”的资助下,国内在相关研究开发有基础的单位联合起来,正在进行煤热解、气化和高温净化过程的基础性研究,项目进展较好。
(4)整体煤气化联合循环(IGCC)。
IGCC发电技术通过将煤气化生成燃料气,驱动燃气轮机发电,其尾气通过佘热锅炉产生蒸汽驱动汽轮机发电,构成联合循环发电,具有效率高、污染排放低的优势。
但其系统复杂、投资高。
IGCC需要与电能、热能、城市煤气以及化工产品的生产相结合,构成以煤气化为基础的多联产后,才能使不利因素转化为有利条件。
IGCC技术已走过了概念验证和技术示范运行阶段,目前已进人250~300MWE大容量机组的商业示范阶段。
世界上主要的煤气化工艺和燃气轮机技术均进行了示范,煤气化、油气化和煤油混合气化及多种燃料供给方式都有示范经验。
目前,我国及韩国、曰本、美国、德国、意大利、印度、苏格兰、法国、捷克、新加坡等国家正在筹建以煤或渣油(或垃圾)气化的IGCC电站达十几座,容量从60~550MWe不等。
国内对IGCC的关键技术研究起步较晚,在“九五”期间才启动有关IGCC工艺、煤气化、煤气净化、燃气轮机和余热系统等方面的关键技术研究。
目前,国内在IGCC系统研究和一些关键技术开发方面取得了进步,已得到一批中间成果,形成了较好的技术基础。
四、煤制甲醇技术发展状况1. 甲醇生产工艺的发展1923年德国BASF公司首先用合成气在高压下实现了甲醇的工业化生产,直到1965年,这种高压法工艺是合成甲醇的唯一方法。
1966年英国ICI公司开发了低压法工艺,接着又开发了中压法工艺。
1971年德国的Lurgi公司相继开发了适用于天然气—渣油为原料的低压法工艺。