ETCH工艺
pcb-etch

PCB外层电路的蚀刻工艺一.概述目前,印刷电路板(PCB)加工的典型工艺采用"图形电镀法"(Pattern plating)。
即先在板子外层需保留的铜箔部分上,也就是电路的图形部分上预镀一层铅锡抗蚀层,然后用化学方式将其余的铜箔腐蚀掉,称为蚀刻。
图1所示的,为图形电镀后板子横截面的情况。
在图1状态下,印制板的整体厚度是整个加工过程中之最,以后将逐渐减薄,直到阻焊涂覆工艺。
图1的下一道工艺是去膜,即将铜层上铅锡部分以外的感光保护膜剥离掉。
图2表示了去膜后板子的横截面。
接下去的工艺就是蚀刻。
要注意的是,这时的板子上面有两层铜.在外层蚀刻工艺中仅仅有一层铜是必须被全部蚀刻掉的,其余的将形成最终所需要的电路。
这种类型的图形电镀,其特点是镀铜层仅存在于铅锡抗蚀层的下面。
另外一种工艺方法是整个板子上都镀铜,感光膜以外的部分仅仅是锡或铅锡抗蚀层(见图3)。
这种工艺称为“全板镀铜工艺“。
与图形电镀相比,全板镀铜的最大缺点是板面各处都要镀两次铜而且蚀刻时还必须都把它们腐蚀掉。
因此当导线线宽十分精细时将会产生一系列的问题。
同时,侧腐蚀(见图4)会严重影响线条的均匀性。
在印制板外层电路的加工工艺中,还有另外一种方法,就是用感光膜代替金属镀层做抗蚀层。
这种方法非常近似于内层蚀刻工艺,可以参阅内层制作工艺中的蚀刻。
目前,锡或铅锡是最常用的抗蚀层,用在氨性蚀刻剂的蚀刻工艺中.氨性蚀刻剂是普遍使用的化工药液,与锡或铅锡不发生任何化学反应。
氨性蚀刻剂主要是指氨水/氯化氨蚀刻液。
此外,在市场上还可以买到氨水/硫酸氨蚀刻药液。
以硫酸盐为基的蚀刻药液,使用后,其中的铜可以用电解的方法分离出来,因此能够重复使用。
由于它的腐蚀速率较低,一般在实际生产中不多见,但有望用在无氯蚀刻中。
有人试验用硫酸-双氧水做蚀刻剂来腐蚀外层图形。
由于包括经济和废液处理方面等许多原因,这种工艺尚未在商用的意义上被大量采用.更进一步说,硫酸-双氧水,不能用于铅锡抗蚀层的蚀刻,而这种工艺不是PCB外层制作中的主要方法,故决大多数人很少问津。
ETCH(PCB蚀刻培训教材)解析

膜不净;药水浓度高,会导致板面氧化。
褪膜段喷嘴要及时清洗,防止碎片堵塞喷嘴,
影响褪膜质量
二.碱性蚀刻 1.工艺流程 褪膜 蚀刻 新液洗 褪锡
(整孔)
注:整孔工序仅适用于沉金制板
2.工艺原理 -褪膜
定义:用褪菲林液将线路板面上盖住的菲林褪去,露 出未经线路加工的铜面. 经电镀工序后的干膜在碱性褪膜液下溶解或部分成 片状脱落,我司使用的是3% 0.5%氢氧化钠溶液.
水池效应
在蚀刻过程中,线路板水平通过蚀刻机时, 因重力作用在板上面新鲜药液被积水阻挠,无 法有效和铜面反应,称之水池效应。而下面 则无此现象。
蚀刻因子
蚀刻液在蚀刻过程中,不仅向下而且对左右各 方向都产生蚀刻作用,侧蚀是不可避免的。侧蚀宽 度与蚀刻深度之比称之为蚀刻因子。
A 铜线路 B D C
抗蚀层
原理:
CO3-2 + Resist COOH
HCO3- + Resist COO-
CO3-2 主要为Na2CO3 或K2CO3 Resist TOOH为干膜及油墨中反应官能基团 利用CO3-2与阻剂中羧基(COOH)进行酸碱中和反应, 形成COO-和H CO3- ,使阻剂形成阴离子团而剥离。
-蚀刻
³ ° å å » ú × Ô ¶ ¯ Ó Ò ¼ © ¸ × ´ ¿ Ê Ì » ú
400(800) 500X2
Ê Ä Í ¤
480(800)
Na2CO3 ý Å ³ Ý ¼ Á Cu2+± È Ö Ø HCl « Ñ Ë õ Ë ® H2O2 NaOH ý Å ³ Ý ¼ Á
3.2kg 640ml(640ml)
¸× ± ¢
冲板、褪膜、褪菲林换药和补药标准
ETCH工艺培训

温度(℃)
蚀刻喷淋上压力(Kg/cm2) 蚀刻喷淋下压力(Kg/cm2)
50-52
2.4-2.8 1.8-2.2
统赢软性(珠海)有限公司
主要参数
项目 蚀刻速度m/min 氨水洗压力(Kg/cm2) 氨水洗浓度(%) 益流水洗(Kg/cm2) 控制范围 2-5 0.8-1.2 8-10 1.4-2.0
统赢软性(珠海)有限公司
三、蚀刻岗位故障分析及排除
脱膜不完全
可能原因:
1.药液不够 2.药液温度不够 3.喷嘴堵塞 4.干膜贴膜温度过高 5.过滤器堵塞导致喷 淋压力不够
解决方法:
1.添加新药水 2.加热药水至操作温度 3.清洗喷嘴 4.调节贴膜温度 5.清洗过滤器之堵塞物
统赢软性(珠海)有限公司
下工序
统赢软性(珠海)有限公司
退膜
一、目的:
除去铜板上覆盖的干膜,露出底铜层 。 二、控制点 退膜不净、溶锡的控制
统赢软性(珠海)有限公司
主要参数
项目 NaOH浓度(%) 控制范围 4-6
退膜温度(℃) 退膜喷淋压力(Kg/cm2)
水洗压力(Kg/cm2) 速度(m/min)
45-55 2.0-2.6
1.4-2.0 2.0-5.0
统赢软性(珠海)有限公司
注意事项
1.每班开工前用毛巾擦拭整机外表至干净,检查传送运转正常及行辘 是否粘胶,喷咀畅通无堵塞。 2.每班清洗退膜缸过滤器中过滤网及缸中的过滤网,防止膜渣堵塞过 滤网、喷管、喷嘴,并对退膜缸内四周及缸底清洗干净。每班更换 一次水洗缸清洗过滤网及过滤筒, 3.每天更换一次退膜缸药水,每班分析一次退膜液的含量。 4.巡线人员生产过程中检查退膜后的板面有无退膜不净、溶锡等品质 缺陷,每4个小时巡线检查所有的压力、温度、速度、液位是否正常。 生产过程中,巡线人员发现滤渣要满出网外必须及时清理,防止药 水溢出缸外。 5. 每周对退膜线做一次保养,检查喷嘴有无堵塞。
Wet Etch设备及工艺介绍
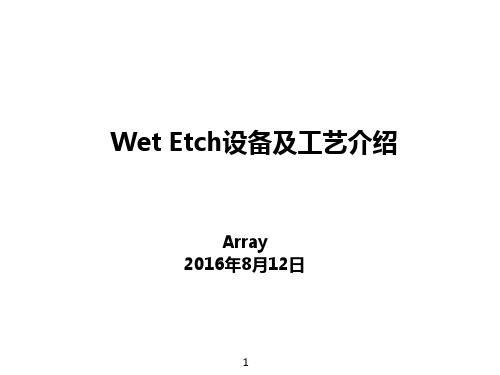
4. 选择比 同一Layer不同金属膜层间刻蚀速率差异,Profile控制关键。 Wet Etch不对此进行管控
5. CD Bias
CD Bias指Photo工艺后的线宽DICD与最终形成的Pattern线宽FICD的差值。 CD Bias是Wet Etch重点管控工艺参数
Wet Etch设备及工艺介绍
Array 2016年8月12日
1
课程内容介绍
Wet Etch科业务介绍 Wet Etch工艺介绍 Wet Etch设备介绍
2
课程内容介绍
Wet Etch科业务介绍 Wet Etch工艺介绍 Wet Etch设备介绍
3
1. Wet Etch业务介绍-主工艺
UV Light Photo Mask
Photo Resist
Thin Film
Glass
Exposure
Photo Resist (PR)
PR coating
Thin Film 镀膜(Sputter/PECVD)
Develop
Array工艺流程图
Glass IInnitial Clleeaann
Next Layer
Out CV AK
Plate Flow
Plate Flow
Rinse
Rinse
Rinse
Anneal
Index
传送单元
剥离
水洗
Index
Cooling Buffer
Anneal
干燥
26
3. Wet Etch设备介绍-Initial Cleaner
Initial Cleaner结构
Feeder C/V
etch back 工艺
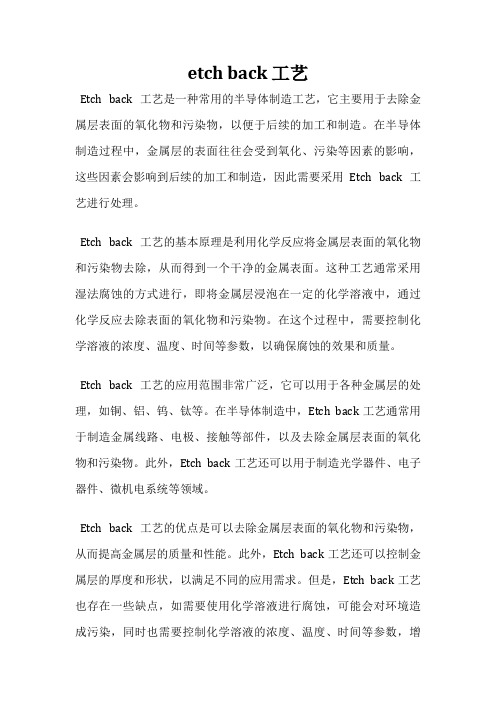
etch back 工艺Etch back工艺是一种常用的半导体制造工艺,它主要用于去除金属层表面的氧化物和污染物,以便于后续的加工和制造。
在半导体制造过程中,金属层的表面往往会受到氧化、污染等因素的影响,这些因素会影响到后续的加工和制造,因此需要采用Etch back工艺进行处理。
Etch back工艺的基本原理是利用化学反应将金属层表面的氧化物和污染物去除,从而得到一个干净的金属表面。
这种工艺通常采用湿法腐蚀的方式进行,即将金属层浸泡在一定的化学溶液中,通过化学反应去除表面的氧化物和污染物。
在这个过程中,需要控制化学溶液的浓度、温度、时间等参数,以确保腐蚀的效果和质量。
Etch back工艺的应用范围非常广泛,它可以用于各种金属层的处理,如铜、铝、钨、钛等。
在半导体制造中,Etch back工艺通常用于制造金属线路、电极、接触等部件,以及去除金属层表面的氧化物和污染物。
此外,Etch back工艺还可以用于制造光学器件、电子器件、微机电系统等领域。
Etch back工艺的优点是可以去除金属层表面的氧化物和污染物,从而提高金属层的质量和性能。
此外,Etch back工艺还可以控制金属层的厚度和形状,以满足不同的应用需求。
但是,Etch back工艺也存在一些缺点,如需要使用化学溶液进行腐蚀,可能会对环境造成污染,同时也需要控制化学溶液的浓度、温度、时间等参数,增加了制造成本和难度。
Etch back工艺是一种重要的半导体制造工艺,它可以去除金属层表面的氧化物和污染物,提高金属层的质量和性能,同时也可以控制金属层的厚度和形状,满足不同的应用需求。
在未来的半导体制造中,Etch back工艺将继续发挥重要作用,为半导体产业的发展做出贡献。
刻蚀(ETCH)工艺的基础知识
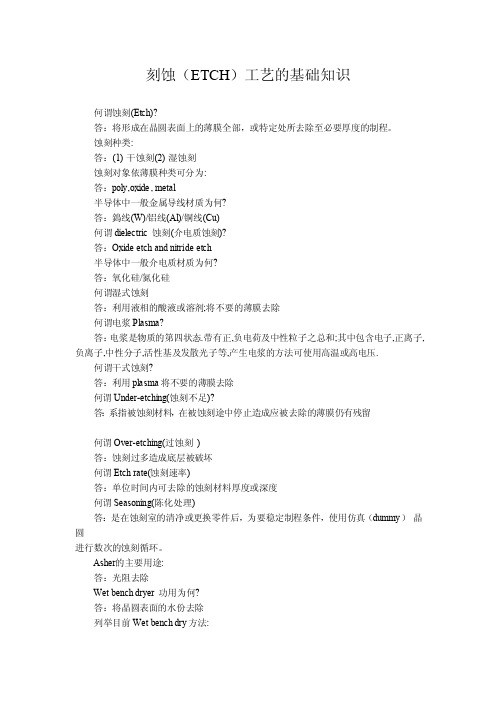
刻蚀(ETCH)工艺的基础知识何谓蚀刻(Etch)?答:将形成在晶圆表面上的薄膜全部,或特定处所去除至必要厚度的制程。
蚀刻种类:答:(1) 干蚀刻(2) 湿蚀刻蚀刻对象依薄膜种类可分为:答:poly,oxide, metal半导体中一般金属导线材质为何?答:鵭线(W)/铝线(Al)/铜线(Cu)何谓 dielec tric蚀刻(介电质蚀刻)?答:Oxideetch and nitrid e etch半导体中一般介电质材质为何?答:氧化硅/氮化硅何谓湿式蚀刻答:利用液相的酸液或溶剂;将不要的薄膜去除何谓电浆 Plasma?答:电浆是物质的第四状态.带有正,负电荷及中性粒子之总和;其中包含电子,正离子, 负离子,中性分子,活性基及发散光子等,产生电浆的方法可使用高温或高电压.何谓干式蚀刻?答:利用plas ma将不要的薄膜去除何谓Unde r-etchin g(蚀刻不足)?答:系指被蚀刻材料,在被蚀刻途中停止造成应被去除的薄膜仍有残留何谓Over-etchin g(过蚀刻)答:蚀刻过多造成底层被破坏何谓Etch rate(蚀刻速率)答:单位时间内可去除的蚀刻材料厚度或深度何谓Seas oning(陈化处理)答:是在蚀刻室的清净或更换零件后,为要稳定制程条件,使用仿真(dummy)晶圆进行数次的蚀刻循环。
Asher的主要用途:答:光阻去除Wet benchdryer功用为何?答:将晶圆表面的水份去除列举目前We t benchdry方法:答:(1) Spin Dryer(2) Marang oni dry (3) IPA VaporDry何谓 Spin Dryer答:利用离心力将晶圆表面的水份去除何谓 Marago ni Dryer答:利用表面张力将晶圆表面的水份去除何谓 IPA VaporDryer答:利用IPA(异丙醇)和水共溶原理将晶圆表面的水份去除测Parti cle时,使用何种测量仪器?答:Tencor Surfsc an测蚀刻速率时,使用何者量测仪器?答:膜厚计,测量膜厚差值何谓 AEI答:AfterEtchin g Inspec tion蚀刻后的检查AEI目检W afer须检查哪些项目:答:(1) 正面颜色是否异常及刮伤(2) 有无缺角及P artic le (3)刻号是否正确金属蚀刻机台转非金属蚀刻机台时应如何处理?答:清机防止金属污染问题金属蚀刻机台asher的功用为何?答:去光阻及防止腐蚀金属蚀刻后为何不可使用一般硫酸槽进行清洗?答:因为金属线会溶于硫酸中"Hot Plate"机台是什幺用途?答:烘烤Hot Plate烘烤温度为何?答:90~120 度C何种气体为P oly ETCH主要使用气体?答:Cl2, HBr, HCl用于Al 金属蚀刻的主要气体为答:Cl2, BCl3用于W金属蚀刻的主要气体为答:SF6何种气体为o xidevai/contac t ETCH主要使用气体?答:C4F8, C5F8, C4F6硫酸槽的化学成份为:答:H2SO4/H2O2AMP槽的化学成份为:答:NH4OH/H2O2/H2OUV curing是什幺用途?答:利用UV光对光阻进行预处理以加强光阻的强度"UV curing"用于何种层次?答:金属层何谓EMO?答:机台紧急开关EMO作用为何?答:当机台有危险发生之顾虑或已不可控制,可紧急按下湿式蚀刻门上贴有那些警示标示?答:(1) 警告.内部有严重危险.严禁打开此门(2) 机械手臂危险. 严禁打开此门(3) 化学药剂危险. 严禁打开此门遇化学溶液泄漏时应如何处置?答:严禁以手去测试漏出之液体. 应以酸碱试纸测试. 并寻找泄漏管路.遇IPA 槽着火时应如何处置??答:立即关闭IP A 输送管路并以机台之灭火器灭火及通知紧急应变小组BOE槽之主成份为何?答:HF(氢氟酸)与NH4F(氟化铵).BOE为那三个英文字缩写?答:Buffer ed OxideEtcher。
ETCH名词解释
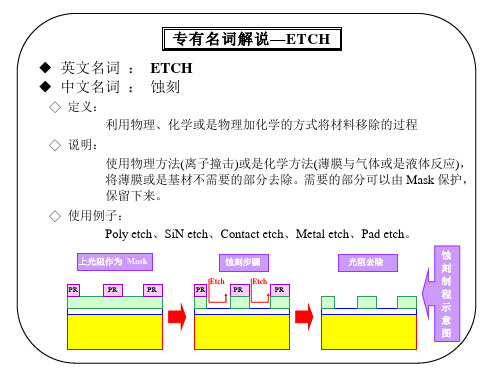
等向性蚀刻示意图
PR R
PR
PR
R
基材
非等向性蚀刻示意图
PR
R2 PR
R3
R1
基材
PR R4
PR
R1
基材
专有名词解说—ETCH
◆ 英文名词 : Selectivity ◆ 中文名词 : 选择比
◇ 定义: 蚀刻的选择比,指同一个蚀刻方法对于不同薄膜蚀刻率的比值
◇ 特性:
可以控制蚀刻时的方向性,得到平直的蚀刻剖面,但一般一次都只
能蚀刻一片芯片
1. 产生蚀刻所需的化学反应物 2. 扩散到表面
电浆层
3. 吸附
气体停滞层
流动气体层
6. 扩散到 Bulk Gas 5. 脱离
干蚀刻 电浆蚀刻
制程 示意图
4. 反应
Film
专有名词解说—ETCH
◆ 英文名词 : Wet Etch ◆ 中文名词 : 湿蚀刻
W2 W1
Aspect Ration 1(A1)=W1/T
T
Aspect Ration 2(A2)=W2/T
A1>A2
专有名词解说—ETCH
◆ 英文名词 : Chamber
◆ 中文名词 : 反应室
◇ 定义:
提供制程进行的反应环境,可控制环境的温度、气体与压力等参数
◇ 说明:
一部机台可能有一个或是多个的反应室,可以独立进行不同的制程。
◆ 英文名词 : End Point ◆ 中文名词 : 蚀刻终点
◇ 定义: 蚀刻制程到达完成点,称为蚀刻终点
◇ 说明: 一般蚀刻制程,会利用雷射光侦测薄膜厚度,或是利用光谱分析蚀 刻副产物原光谱的消失点,测得蚀刻终点。可避免蚀刻不足或是蚀 刻过度。
DryEtch工艺及设备介绍

• Dry Strip 反应气体(SF6/NF3) :
SF6/NF3
CxHy (PR胶) + O2 -----> COx↑ + H2O↑
Active GI
Active GI
1.2 Dry Etch 工艺介绍
2.5 温控系统
Chiller (Heater Exchanger)
Pt Sensor (热电偶):温度测量
Chiller Chiller Hose Connector
2.5 温控系统
TC & BC:
Plasma Connection
Glass
---------
+++++++ --------
+++++++
• Ashing 反应气体(SF6/NF3) :
SF6/NF3
CxHy (PR胶) + O2 -----> COx↑ + H2O↑
Active GI
Active GI
1.2 Dry Etch 工艺介绍
• N+ Etch & Dry Strip
N+ Etch:针对TFT Channel 区域a-Si进行反应,生产挥发性气体的过程。 Dry Strip:针对N+ Etch后Glass表面PR胶进行反应,生成挥发性气体的过程。
• Ash/Act or Act/Ash
Active Etch:针对Pixel 区域a-Si进行反应,生产挥发性气体的过程。 Ashing:针对TFT Channel区域PR胶进行反应,生成挥发性气体的过程。
晶圆制造工艺ETCH优选稿
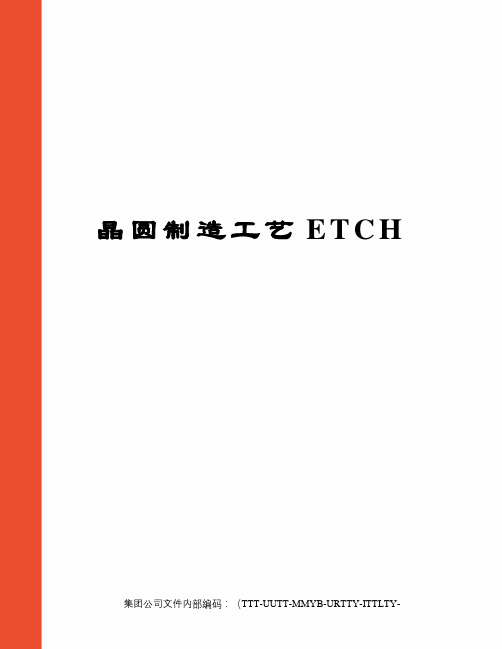
晶圆制造工艺E T C H 集团公司文件内部编码:(TTT-UUTT-MMYB-URTTY-ITTLTY-晶圆制造工艺流程1、表面清洗2、初次氧化3、CVD(ChemicalVapordeposition)法沉积一层Si3N4(HotCVD或LPCVD) 。
(1)常压CVD(NormalPressureCVD)(2)低压CVD(LowPressureCVD)(3)热CVD(HotCVD)/(thermalCVD)(4)电浆增强CVD(PlasmaEnhancedCVD)(5)MOCVD(MetalOrganicCVD)&分子磊晶成长(MolecularBeamEpitaxy)(6)外延生长法?(LPE)4、涂敷光刻胶?(1)光刻胶的涂敷?(2)预烘(prebake)(3)曝光(4)显影(5)后烘(postbake)(6)腐蚀(etching)(7)光刻胶的去除5、此处用干法氧化法将氮化硅去除6?、离子布植将硼离子(B+3)透过SiO2?膜注入衬底,形成P?型阱7、去除光刻胶,放高温炉中进行退火处理8、用热磷酸去除氮化硅层,掺杂磷(P+5)离子,形成N?型阱9、退火处理,然后用HF?去除SiO2?层10、干法氧化法生成一层SiO2?层,然后LPCVD?沉积一层氮化硅11、利用光刻技术和离子刻蚀技术,保留下栅隔离层上面的氮化硅层12、湿法氧化,生长未有氮化硅保护的SiO2?层,形成PN?之间的隔离区13、热磷酸去除氮化硅,然后用HF溶液去除栅隔离层位置的SiO2,并重新生成品质更好的SiO2薄膜,作为栅极氧化层。
14、LPCVD?沉积多晶硅层,然后涂敷光阻进行光刻,以及等离子蚀刻技术,栅极结构,并氧化生成SiO2?保护层。
15、表面涂敷光阻,去除P?阱区的光阻,注入砷(As)离子,形成NMOS?的源漏极。
用同样的方法,在N?阱区,注入B?离子形成PMOS?的源漏极。
16、利用PECVD?沉积一层无掺杂氧化层,保护元件,并进行退火处理。
Dry Etch 工艺基本原理及良率剖析(经典讲解)

【面板制程刻蚀篇】史上最全Dry Etch 分类、工艺Dry Etch工序的目的广义而言,所谓的刻蚀技术,是将显影后所产生的光阻图案真实地转印到光阻下的材质上,形成由光刻技术定义的图形。
它包含了将材质整面均匀移除及图案选择性部分去除,可分为湿式刻蚀(wet etching)和干式刻蚀(dry etching)两种技术。
湿式刻蚀具有待刻蚀材料与光阻及下层材质良好的刻蚀选择比(selectivity)。
然而,由于化学反应没有方向性,因而湿式刻蚀是各向同性刻蚀。
当刻蚀溶液做纵向刻蚀时,侧向的刻蚀将同时发生,进而造成底切(Undercut)现象,导致图案线宽失真,如下图所示。
底切现象自1970年以来,元件制造首先开始采用电浆刻蚀技术(也叫等离子体刻蚀技术),人们对于电浆化学性的了解与认识也就越来越深。
在现今的半导体集成电路或面板制造过程中,要求精确地控制各种材料尺寸至次微米大小,而且还必须具有极高的再现性,电浆刻蚀是现今技术中唯一能极有效率地将此工作在高良率下完成的技术,因此电浆刻蚀便成为半导体制造以及TFT LCD Array制造中的主要技术之一。
干式刻蚀通常指利用辉光放电(glow discharge)方式,产生包含离子、电子等带电粒子以及具有高度化学活性的中性原子、分子及自由基的电浆,来进行图案转印(pattern transfer)的刻蚀技术。
干法刻蚀是亚微米尺寸下刻蚀器件的最主要方法,广泛应用于半导体或面板前段制程。
Dry Etch 的分类及工艺的基本原理蚀刻技术中的术语1.各向同性与各向异性蚀刻( Isotropic and Anisotropic Etching)不同的蚀刻机制将对蚀刻后的轮廓(Profile)产生直接的影响。
如下图所示,纯粹的化学蚀刻通常没有方向选择性,上下左右刻蚀速度相同,蚀刻后将形成圆弧的轮廓,并在遮罩(Mask)下形成底切(Undercut),这种刻蚀被称为各向同性蚀刻。
ETCH工艺

工序潜力与展望
由于我司全板电镀较薄,且切匀性较好,故蚀刻的均匀性也相 对较好。随着未来PCB的发展,如挠性板、密的线路板的生产 将采取相应的措施,比如可将钻孔后之板适当蚀去1/3到1/2的 底铜,再做PTH全板,Dryfilm、图形电镀即可减少侧蚀,从 而保证线宽足够。
生产安全与环境保护
因蚀刻工序使用了强碱(如NaOH)、氨水等化学品,生 产过程中有较大气味产生,同时产生大量废液、废渣,故 应加强抽风以及及时将废液、废渣运走,同时可进行蚀刻 液循环利用。
为使之蚀铜反应进行更为迅速,蚀液中多加有助剂, 例如:
a. 加速剂( Accelerator) 可促使上述氧化反应更为快速, 并防止亚铜错离子的沉淀。
b. 护岸剂(Banking agent) 减少侧蚀。 c. 压抑剂(Suppressor )抑制氨在高温下的飞散,抑制铜
的沉淀加速蚀铜的氧化反应。
水池效应
在蚀刻过程中,线路板水平通过蚀刻机时, 因重力作用在板上面新鲜药液被积水阻挠,无 法有效和铜面反应,称之水池效应。而下面 则无此现象。
蚀刻因子
蚀刻液在蚀刻过程中,不仅向下而且对左右各 方向都产生蚀刻作用,侧蚀是不可避免的。侧蚀宽 度与蚀刻深度之比称之为蚀刻因子。
(=2H/(线底-线顶)
设备
4Cu(NH3)2Cl + 4NH3H2O + 4NH4Cl + O2 →
4Cu(NH3)4Cl2+6H2O 以上两反应重复进行,因此需要有良好抽气,使喷淋 形成 负压,使空气中的氧气与药液充分混合,从而利于 蚀刻反应进行。注意抽气不可过大,否则造成氨水消耗 量的增大.
二价铜离子在碱性环境下极易生成氢氧化铜沉淀, 需加入过量的氨水,使之生成稳定的氨铜错离子团; 过量的氨使反应生成的不稳定Cu(NH3)2Cl 再生成稳 定的具有氧化性的Cu(NH3)4Cl2 ,使反应不断的进行。
DRY蚀刻工艺简介

Load Lack
TM 真空
Gate Door
Port
大氣
乾蝕刻製程設備介紹
設備相關設計:
Plasma
1.Gas 2.反應室Chamber 3.RF Power 4.真空裝置 5.Temperature 6.other
Gas cylinder
乾蝕刻製程設備介紹
Gas Control System :
Gas out : APC / Turbo Pump / Dry Pump / Scrubber
Turbo Pump
Process Chamber
APC Turbo Pump
廠務
Scrubber
DRY Pump
Scrubber
乾蝕刻製程設備介紹
Gas Control System :
Gas in : Gas Box / MFC system
总结
➢ 本课程重点为:a. 蚀刻在Array制程中所扮演的角色。
b. 电将蚀刻的基本原理
➢ 清楚的熟记: a. Etch 机台设备原理
b. ETCH 设备控制机制
✓ 上完本课程, 您必须要有能力回答下列问题 ❖ DRY蚀刻工程以Power设计主要机台分为那几种? ❖ DRY蚀刻机台依不同的反应模式可分为哪几种?又有何不相同处? ❖ 如何知道已经蚀刻完成?
ETCH 反应机制: 物理 / 化学
物理ETCH
化学ETCH
機制:
1.)Gas in 2.)解離 3.)碰撞 4.)離子轟擊(非等向性蝕刻) 5.)吸附作用 6.)化學反應(等向性蝕刻) 7.)去吸附作用 8.)反應去除
干蚀刻设备原理
Power 區分ETCH 設備 :
半导体制程培训CMP和蚀刻pptx
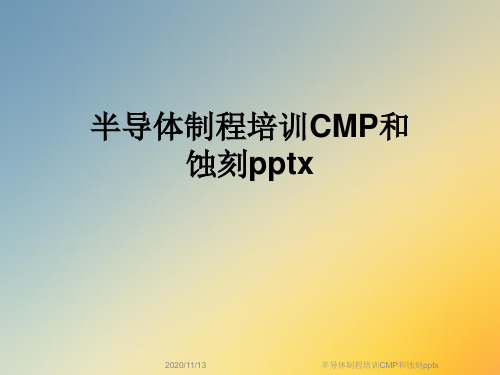
半导体制造工艺流程
化学机械平坦化原理图
磨头 硅片 转盘
向下施加力
抛光垫 磨料喷头
磨料
半导体制程培训CMP和蚀刻pptx
半导体制造工艺流程
研磨液
磨料是平坦化工艺中研磨材料和化学添加剂的混合物,研磨 材料主要是石英,二氧化铝和氧化铈,其中的化学添加剂则 要根据实际情况加以选择,这些化学添加剂和要被除去的材 料进行反应,弱化其和硅分子联结,这样使得机械抛光更加 容易。在应用中的通常有氧化物磨料、金属钨磨料、金属铜 磨料以及一些特殊应用磨料
半导体制程培训CMP和蚀刻pptx
半导体制造工艺流程
干法刻蚀
优点:各向异性好,选择比高,可控性、灵活性、重复性好, 细线条操作安全,易实现自动化,无化学废液,处理过程未引 入污染,洁净度高。
缺点:成本高,设备复杂。
干法刻蚀方式:①溅射与离子束铣蚀 ②等离子刻蚀(Plasma Etching) ③③高压等离子刻蚀 ④高密度等离子体(HDP)刻蚀 ⑤反应离子刻蚀(RIE)
SOG
1)
ILD-1
烘烤后的SOG
2)
ILD-1
ILD-2淀积
3)
ILD-1
半导体制程培训CMP和蚀刻pptx
半导体制造工艺流程
化学机械平坦化机理
有两种CMP机理可以解释是如何来进行硅片表面 平坦化的:
1) 表面材料与磨料发生化学反应生成一层相对 容易去除的表面层;
2)这一反应生成的硅片表面层通过磨料中研磨 机和研磨压力与抛光垫的相对运动被机械地磨 去。
半导体制程培训CMP和蚀刻pptx
半导体制造工艺流程
应用
化学机械抛光主要用于以下几个方面: ①深槽填充的平面化
半导体etch工艺

半导体etch工艺半导体etch工艺是半导体制造过程中的重要环节,也是最受关注的制备过程之一。
Etch工艺的灵活性可以用来实现复杂多变的半导体结构,而且还可以提高制造准确度,使得半导体表面更加精确。
本文将详细介绍半导体etch工艺的基本原理和重要技术,以及它对半导体元件制造过程中的重要影响。
一、导体etch工艺的基本原理半导体etch工艺是利用半导体物理学或化学学特性来有效地去除表面的薄膜或层的一种工艺。
它可以将半导体表面的薄膜重新形成更精细的图案或体积,从而形成所需要的晶体结构。
通常,目标物质一般是类似氧化层(如硅氧化层)和多层结构(如掩模层、源/汇层等)。
半导体etch工艺有两种基本实现方式:物理介质etch(PEE)和化学介质etch(CEE)。
PEE是利用物理介质(如电离及气体等)的动能来分解表面覆盖层的去除过程,而CEE则是通过化学反应来腐蚀表面覆盖层的下层的过程。
二、重要技术1、表面处理技术半导体etch工艺的成功执行取决于表面处理技术。
表面处理技术可以确保干净、无污染的表面,以及清洁和无污染的气体,以防止后续etch工艺出现不良影响。
2、模版技术模版技术是etch工艺中最重要的技术,它是控制etch过程中晶体结构形成的关键。
模板技术可以采取精确的掩模技术,以满足不同需求的复杂形状和尺寸,同时还可以提高etch的准确性、稳定性和效率。
3、腐蚀技术腐蚀技术是etch工艺中最关键的技术,可用于精确控制表面覆盖层的形状、大小以及厚度。
腐蚀技术可以使用溶剂(如水、氯化物、卤素等)或金属介质(如氘气、氩气、氯气等)来有效分解表面覆盖层的下层。
三、对半导体元件制造的影响1、提高制造精度半导体etch工艺可以有效地控制半导体元件表面的形状、大小和厚度,从而强化元件的功能性能,提高产品质量。
2、缩短制造时间半导体etch工艺可以有效地减少制造时间,从而缩短产品研发时间,降低生产成本,提高半导体元件制造效率。
etch工艺

etch工艺
刻蚀,英文为Etch,它是半导体制造工艺,微电子IC制造工艺以及微纳制造工艺中的一种相当重要的步骤。
是与光刻[1] 相联系的图形化(pattern)处理的一种主要工艺。
所谓刻蚀,实际上狭义理解就是光刻腐蚀,先通过光刻将光刻胶进行光刻曝光处理,然后通过其它方式实现腐蚀处理掉所需除去的部分。
刻蚀是用化学或物理方法有选择地从硅片表面去除不需要的材料的过程,其基本目标是在涂胶的硅片上正确地复制掩模图形。
随着微制造工艺的发展,广义上来讲,刻蚀成了通过溶液、反应离子或其它机械方式来剥离、去除材料的一种统称,成为微加工制造的一种普适叫法。
刻蚀(ETCH)工艺的基础知识

刻蚀(ETCH )工艺的基础知识f4 }" y# [7 N. @4 g何谓蚀刻(Etch)? 答:将形成在晶圆表面上的薄膜全部,或特定处所去除至必要厚度的制程。
蚀刻种类:答:(1)干蚀刻(2)湿蚀刻蚀刻对象依薄膜种类可分为: 答:poly,oxide, metal 半导体中一般金属导线材质为何?答:鵭线(W)/铝线(Al)/ 铜线(Cu) 8 n5 i! \; k5 ]& f |何谓dielectric 蚀刻(介电质蚀刻)?答:Oxide etch and nitride etch 半导体中一般介电质材质为何? 答:氧化硅/氮化硅何谓湿式蚀刻答:利用液相的酸液或溶剂;将不要的薄膜去除 4 E% e8 p3 A8 q6 F5 U 何谓电浆Plasma?答:电浆是物质的第四状态.带有正,负电荷及中性粒子之总和;其中包含电子,正离子, 负离子,中性分子,活性基及发散光子等,产生电浆的方法可使用高温或高电压.何谓干式蚀刻?答:利用plasma 将不要的薄膜去除何谓Under-etching(蚀刻不足)? $ a$ o2 k; j9 F; N答:系指被蚀刻材料,在被蚀刻途中停止造成应被去除的薄膜仍有残留 6 m9 d- c! W! `. `6 ?" D) ?0 h; l何谓Over-etching(过蚀刻)答:蚀刻过多造成底层被破坏何谓Etch rate(蚀刻速率) ! n* v/ r6 b0 ` 答:单位时间内可去除的蚀刻材料厚度或深度8 _5 F4 Q+ r) D8 n2 K何谓Seasoning(陈化处理)答:是在蚀刻室的清净或更换零件后,为要稳定制程条件,使用仿真(dummy )晶圆* L% r$ a5 L5 p, D N% C 进行数次的蚀刻循环。
& H2 O6 r2 K0 p6 u* W( @2 A9 b5 N Asher 的主要用途:答:光阻去除* m8 q" @; {* MWet bench dryer 功用为何? ; c* ?# M" a% d Q# G$ q3 k, Y' d. P 答:将晶圆表面的水份去除& q+ k& d+ p: m9 M% k( g' U2 M 列举目前Wet bench dry方法: 9 [* L b4 e+ ] O)T答:(1) Spin Dryer (2) Marangoni dry (3) IPA Vapor Dry ( }" C: r, A' w/ q/ T 何谓Spin Dryer " {6 n5 S4 |: ~0 Y+ I1 H$ p0 z: j8 b& M 答:利用离心力将晶圆表面的水份去除何谓Maragoni Dryer 答:利用表面张力将晶圆表面的水份去除- R( s3 v& r) Q( g7 p 何谓IPA Vapor Dryer 9 X4 R3 @* m% I2 I C% R 答:利用IPA(异丙醇)和水共溶原理将晶圆表面的水份去除0 q4 s$ e' Z' W* |测Particle 时,使用何种测量仪器?答:TencorSurfscan 测蚀刻速率时,使用何者量测仪器? 8 M6 d5 ~% \) g 答:膜厚计,测量膜厚差值 2 X, {1 M$ f& S 何谓AEI答:After Etching Inspection 蚀刻后的检查7 d J( [" | o8 T# ]AEI 目检Wafer 须检查哪些项目:答:(1) 正面颜色是否异常及刮伤(2) 有无缺角及Particle (3)刻号是否正确0 J- E7 |* b- Y" s, I' O: S' ~金属蚀刻机台转非金属蚀刻机台时应如何处理? : K% |+ m4 T2 a 答:清机防止金属污染问题( Y* G Z, S0 v7 `9 m5 i5 [ 金属蚀刻机台asher的功用为何? " ^/ m! u) E5 p7 V/ M2 r3 r 答:去光阻及防止腐蚀金属蚀刻后为何不可使用一般硫酸槽进行清洗? 答:因为金属线会溶于硫酸中7 z5 {0 @ A1 I+ s5 f9 _0 d "Hot Plate"机台是什幺用途? % Y& H. w2 p5 g/ b* n 答:烘烤, x1 | J% L# S4 K4 n) z, F- x Hot Plate 烘烤温度为何? 1 M) I4 o5 ~4 d0 F9 J: z 答:90~120 度 C 5 O& G$ V6 ?; |: o" K* ]3 u 何种气体为Poly ETCH 主要使用气体? ! q! \# {# K5 \/A 答:Cl2, HBr, HCl $ I% O* e$ |; s# T4 l 用于Al 金属蚀刻的主要气体为# N( {( @* l;W0 V% D 答:Cl2, BCl3 用于W 金属蚀刻的主要气体为答:SF6 , s0 r! a# b! R( D 何种气体为oxide vai/contact ETCH 主要使用气体? 答:C4F8, C5F8, C4F6 硫酸槽的化学成份为: 答:H2SO4/H2O2 $ ]% j) m6 ^4 E9 y* K& y AMP 槽的化学成份为: 答:NH4OH/H2O2/H2OUV curing 是什幺用途?答:利用UV 光对光阻进行预处理以加强光阻的强度- D Q* r0 F+ C2 h; W0 X"UV curing" 用于何种层次? $ b1 Z* ?5 U. K" b4 L5 M0 m 答:金属层何谓EMO? " d' F6 I/ a. x: b, I9 q" H: x! ` 答:机台紧急开关EMO 作用为何? 8 Q* s1 i( \1 o: ]&i; J 答:当机台有危险发生之顾虑或已不可控制,可紧急按下湿式蚀刻门上贴有那些警示标示?答:(1) 警告.内部有严重危险.严禁打开此门(2) 机械手臂危险. 严禁打开此门(38 f- A4 k" I; @/ F5 n) 化学药剂危险. 严禁打开此门遇化学溶液泄漏时应如何处置? - }, Y9 u; L( b. A7 g$ X2 n( q 答:严禁以手去测试漏出之液体. 应以酸碱试纸测试. 并寻找泄漏管路. 遇IPA 槽着火时应如何处置??答:立即关闭IPA 输送管路并以机台之灭火器灭火及通知紧急应变小组/ H X8 e! [-r0 M; P. }BOE 槽之主成份为何?答:HF(氢氟酸)与NH4F(氟化铵).BOE 为那三个英文字缩写?答:Buffered Oxide Etcher 。
- 1、下载文档前请自行甄别文档内容的完整性,平台不提供额外的编辑、内容补充、找答案等附加服务。
- 2、"仅部分预览"的文档,不可在线预览部分如存在完整性等问题,可反馈申请退款(可完整预览的文档不适用该条件!)。
- 3、如文档侵犯您的权益,请联系客服反馈,我们会尽快为您处理(人工客服工作时间:9:00-18:30)。
High Mix Low Volume High Tech.
2.溶液PH值的影响
-PH值过低,对金属抗蚀层不利;且溶液中的铜不 能完全被络合成铜氨络离子,溶液要出现沉淀,并 在槽底形成泥状沉淀。这些沉淀能结在加热器上形 成硬皮,可能损坏加热器,还会堵塞泵或喷嘴,对 蚀刻造成困难。
High Mix Low Volume High Tech.
High Mix Low Volume High Tech.
二价铜离子在碱性环境下极易生成氢氧化铜沉淀, 需加入过量的氨水,使之生成稳定的氨铜错离子团; 过量的氨使反应生成的不稳定Cu(NH3)2Cl 再生成稳 定的具有氧化性的Cu(NH3)4Cl2 ,使反应不断的进行。
生产过程中自动控制通过监测PH值,比重,进行 补加氨水和新液,而达到连续生产的目的。
High Mix Low Volume High Tech.
-新液洗 使用不含有铜离子的NH3.H2O, NH4Cl溶液清除板面 残留的药液以及反应生成物Cu(NH3)2Cl ,其极不稳定, 易生成沉淀。 -整孔
除去非镀通孔中的在沉铜工序所吸附上去的钯离子, 以防在沉金工序沉上金.
-褪锡
使用含铜保护剂的主要成分为硝酸的药液,褪去线 路上的锡铅层,露出线路
High Mix Low Volume High Tech.
蚀刻液种类:不同的蚀刻液化学组分不同,
蚀刻速度不同,侧蚀也不同。通常,碱性氯化铜 蚀刻液比酸性氯化铜蚀刻液蚀刻因子大。药水供 应商通常会添加辅助剂来降低侧蚀,不同的供应 商添加的辅助剂不同,蚀刻因子也不同。
High Mix Low Volume High Tech.
可根据实际生产情况调整不同位置喷液压力达到目
的。生产操作中,需定期对设备进行检测和调校。 -板边缘比板中间蚀刻速率快,也可通过调整压力解 决此问题,另外使喷淋系统摆动也是有效的。
High Mix Low Volume High Tech.
常见问题及改善
问题 退膜不尽 原因 1)药水浓度偏低 2)压力、温度不够,行速过快 3)喷嘴堵塞 解决方法 1)调整浓度到适当范围 2)即时调整 3)疏通喷嘴
-PH值过高,溶液中氨过饱和,游离到空气中污 染环境;且使侧蚀增大。
High Mix Low Volume High Tech.
3.氯化氨含量的影响
-从前面反应可知, Cu(NH3)2Cl的再生需要过量的 NH3和NH4Cl存在。若氯化氨过低, Cu(NH3)2Cl得不 到再生,蚀刻速率会降低。 -氯化氨过高,引起抗蚀层被浸蚀。
High Mix Low Volume High Tech.
蚀刻的目的 蚀刻的目的即是将前工序所做出有图形的线 路板上的未受保护的非导体部分铜蚀刻去,形成 线路。 蚀刻有内层蚀刻和外层蚀刻,内层采用酸性 蚀刻,干膜为抗蚀剂;外层采用碱性蚀刻,锡铅 为抗蚀剂。
High Mix Low Volume High Tech.
High Mix Low Volume High Tech.
生产安全与环境保护
因蚀刻工序使用了强碱(如NaOH)、氨水等化学品,生 产过程中有较大气味产生,同时产生大量废液、废渣,故 应加强抽风以及及时将废液、废渣运走,同时可进行蚀刻 液循环利用。
High Mix Low Volume High Tech.
High Mix Low Volume High Tech.
(=2H/(线底-线顶)
High Mix Low Volume High Tech.
设备
-对于碱性蚀刻,为增加蚀刻速度,需提高温度到46℃ 以上,因而有大量的氨臭味必须要有适当的抽风;抽风 太大则将氨气抽走比较浪费,在抽风管内增加节流阀, 控制抽风的强度。 -无论何种蚀刻液,都需采用高压喷淋;为获得较整齐 的线条侧边和高质量的蚀刻效果,须严格选择喷嘴的形 状和喷淋方式。但不论如何选择,都遵循一基本理论, 那就是以最快速度的让欲蚀刻铜表面接触愈多新鲜的蚀 刻液。
为维持药液的效果,需注意过滤的效果,及时过滤去片 状的干膜碎,防止堵塞喷嘴. 注:外层干膜厚为1.5mil左右,经图形电镀后,铜厚 和锡厚之和通常超过1.5mil,需控制图形电镀电流参数防止夹 膜,同时控制褪膜速度以防褪膜不净而短路。
High Mix Low Volume High Tech.
-蚀刻
High Mix Low Volume High Tech.
4.温度的影响
-蚀刻速率会随着温度的升高而加快; -蚀刻温度过低,蚀刻速度会降低,则会增大侧蚀量, 影响蚀刻质量。 -蚀刻温度高,蚀刻速度明显增大,但氨气的挥发量液 增大,既污染环境,有增加成本。
High Mix Low Volume High Tech.
ETCH工艺
编写人:叶云丰 2013年6月
High Mix Low Volume High Tech.
目
前言 基础部分:蚀刻目的Leabharlann 录蚀刻反应基本原理
蚀刻工艺流程及原理 名词解释 设备 技术提升部分:生产线简介 生产线维护 生产注意事项 影响蚀刻速率因素分析 蚀刻能力提高 工序潜力与展望
生产安全与环境保护
蚀刻反应基本原理 二.碱性氨类蚀刻液 1.特性 -不与锡铅发生任何反应 -易再生,成本低,易回收 -蚀铜速度快,侧蚀小,溶铜能力高,蚀刻
速率易控制
High Mix Low Volume High Tech.
2.主要反应原理
Cu+Cu(NH3)4Cl2 → 2Cu(NH3)2Cl
4Cu(NH3)2Cl + 4NH3H2O + 4NH4Cl + O2 → 4Cu(NH3)4Cl2+6H2O 以上两反应重复进行,因此需要有良好抽气,使喷淋 形成 负压,使空气中的氧气与药液充分混合,从而利于 蚀刻反应进行。注意抽气不可过大,否则造成氨水消耗 量的增大.
High Mix Low Volume High Tech.
-喷嘴的形状有锥形(空锥形,实锥形),扇形等, 我司采用的是扇形喷嘴。与锥形喷嘴相比,最佳的设 计是扇形喷嘴。注意集流管的安装角度,能对进入蚀 刻槽内的制板进行30度喷射。第二组集流管与第一组 比有所不同,因喷淋液互相交叉时会降低喷淋的效果, 尽量避免出现此种情况。 -蚀刻槽内集流管的安装与前进方向比有横置,竖置 和斜置,我司采用的安装方式有两种方式(见下 图) 。但摆动方向均垂直于运输方向。
High Mix Low Volume High Tech.
摆 动 方 向 板运输方向
High Mix Low Volume High Tech.
碱性氨类蚀刻液 蚀刻液的PH值,比重( Cu2+的浓度),氯化氨浓度 以及蚀刻液的温度等对蚀刻速度均有影响。 1.Cu2+含量的影响
-Cu2+过低,蚀刻速率低,且溶液控制困难;
底铜厚度:底铜厚度越大,板需在蚀刻液中 停留的时间也越长,侧蚀就越大。制作密集细小 线路的制板,尽量使用低厚度的铜箔,减小全板 镀铜厚度。
High Mix Low Volume High Tech.
二.提高板与板之间蚀刻速率的一致性 在连续生产过程中,蚀刻速率越一致,越能 获得蚀刻均匀的板,生产越容易控制。因此必 须保证溶液始终保持最佳状态。 -选择易再生,蚀刻速率易控制的药水;
蚀刻运输速率:运输速率慢会造成严重的 侧蚀。运输速率快,板在蚀刻液中停留的时间 越短,侧蚀量也越小。生产过程中,尽量提高 蚀刻的运输速度。
蚀刻液的PH值:碱性蚀刻液,PH值较高 时,侧蚀增大。一般控制PH值在8.5以下。
High Mix Low Volume High Tech.
蚀刻液的比重:碱性蚀刻液的比重太低,会 加重侧蚀,选择高铜浓度的蚀刻液对减少侧蚀是 有利的。
定义: 用蚀板液将多余的底铜蚀去剩下已加厚的线路。
控制:随着反应不断进行,药液中氨水不断降低,铜离子不断
增加,为保持蚀铜速度,必需维持药水的稳定.我司通过PH
计,比重计控制氨水和新液的自动添加,当PH值低时添加氨 水;当比重高时添加新液.
High Mix Low Volume High Tech.
为使之蚀铜反应进行更为迅速,蚀液中多加有助剂, 例如: a. 加速剂( Accelerator) 可促使上述氧化反应更为快速, 并防止亚铜错离子的沉淀。 b. 护岸剂(Banking agent) 减少侧蚀。 c. 压抑剂(Suppressor )抑制氨在高温下的飞散,抑制铜 的沉淀加速蚀铜的氧化反应。
板面氧化
蚀铜未净
1)药水浓度偏高
2)温度过高 1)蚀刻速度太快 2)药水成份不当
1)调整药水浓度
2)调整药水温度 1)适当调整运输速度 2)调整药水成份
3)铜面受污染
4)喷嘴堵塞 5)温度偏低 蚀铜过度 1)机速太慢 2)温度偏高
3)避免蚀铜前铜面受污染
4)清洗喷嘴 5)调整温度 1)调整机速 2)调整温度
High Mix Low Volume High Tech.
工序潜力与展望
由于我司全板电镀较薄,且切匀性较好,故蚀刻的均匀性也相 对较好。随着未来PCB的发展,如挠性板、密的线路板的生产 将采取相应的措施,比如可将钻孔后之板适当蚀去1/3到1/2的 底铜,再做PTH全板,Dryfilm、图形电镀即可减少侧蚀,从 而保证线宽足够。
5.喷液压力的影响
-蚀刻药水压力应在1.5 ~3.5kg/cm2,过低则蚀刻不尽,过 高则易打断药水的保护膜,造成蚀刻过度。
High Mix Low Volume High Tech.
蚀刻能力提高 一.减少侧蚀和突沿,提高蚀刻因子。 侧蚀造成突沿,侧蚀和突沿降低,蚀刻因子会提高; 突沿过度会造成导线短路,因为突沿会突然断裂下来, 在导线间形成电的连接。严重的侧蚀则使精细导线的制 作成为不可能。