机械加工中用到的重要公式
切削速度值计算公式

切削速度值计算公式在机械加工领域,切削速度是一个非常重要的参数,它直接影响着加工效率和加工质量。
切削速度值的计算对于机械加工过程中的刀具选择、切削参数确定等方面都具有重要的意义。
本文将从切削速度值的定义、计算公式以及影响因素等方面进行介绍。
一、切削速度值的定义。
切削速度是指刀具在加工过程中相对于工件表面的线速度,通常用Vc来表示,单位是m/min。
切削速度的大小直接影响着切削热量的产生和刀具的磨损情况,因此在实际加工中需要根据工件材料和刀具材料等因素来确定合适的切削速度值。
二、切削速度值的计算公式。
切削速度值的计算公式通常采用下面的公式来表示:Vc = π× D × n。
其中,Vc表示切削速度,π表示圆周率,D表示刀具直径,n表示主轴转速。
由此可见,切削速度值与刀具直径和主轴转速有直接的关系,通过调整这两个参数可以控制切削速度的大小。
三、影响切削速度值的因素。
1. 刀具材料。
不同的刀具材料对切削速度的要求也不同。
通常来说,硬度较高的刀具材料可以承受更高的切削速度,而且还能够提高刀具的使用寿命。
因此在选择刀具材料时需要考虑到切削速度的要求。
2. 工件材料。
不同的工件材料对切削速度的要求也不同。
一般来说,硬度较高的工件材料需要较低的切削速度,而硬度较低的工件材料则可以采用较高的切削速度。
因此在加工不同材料的工件时需要根据具体情况来确定切削速度的数值。
3. 主轴转速。
主轴转速是影响切削速度的重要因素之一。
通过调整主轴转速可以改变切削速度的大小,从而适应不同的加工要求。
在实际加工中需要根据刀具直径和工件材料等因素来确定合适的主轴转速。
四、切削速度值的应用。
切削速度值的计算对于机械加工过程中的刀具选择、切削参数确定等方面都具有重要的意义。
合理的切削速度值可以提高加工效率,减少刀具磨损,提高加工质量。
因此在实际加工中需要根据具体情况来确定合适的切削速度值,以达到最佳的加工效果。
总之,切削速度值的计算是机械加工中的重要内容,它直接影响着加工效率和加工质量。
机械加工时间定额的计算公式和方法

机械加工时间定额的计算公式和方法2、刨削、插削所用符号加工中心tj——机动时间(min)L——切刀或工作台行程长度(mm)1——被加工工件长度(mm)11——切入长度(mm)12——切出长度(mm)13——附加长度(mm)14——行程开始超出长度(mm)15——行程结束时超出长度(mm)B——刨或插工件宽度(mm)h——被加工槽的深度或台阶高度(mm)U——机床平均切削速度(m/min)f——每双行程进给量(mm)i——走刀次数n——每分钟双行程次数n=(1000×VC)/L×(1+K)注:龙门刨:K=0.4-0.75插床:K=0.65-0.93牛头刨:K=0.7-0.9单件生产时上面各机床K=1①插或刨平面tj=(B+12+13)×i/(f×n)=2×(B×11+12+13)×i/(f×Um×1000)(min)②刨或插槽tj=(h+1)×i/(f×n)=(h+1)×i×L/(f×Um×1000)(min)注:龙门刨:14+15=350mm牛头刨:14+15=60mm(各取平均值)③刨、插台阶tj=(B+3)×i/(f×n)(横向走刀刨或插)(min)tj=(h+1)×i/(f×n)(垂直走刀刨或纵向走刀插)(min)3、钻削或铰削所用符号加工中心tj——机动时间(min)1——加工长度(mm)11——切入长度(mm)11——切出长度(mm)f——每转进给量(mm/r)n——刀具或工件每分钟转数(r/min)Φ——顶角(度)D——刀具直径(mm)L——刀具总行程=1+11+12(mm)钻削时:11=1+D/[2×tg(Φ/2)]或11≈0.3P(mm)①一般情况tj=L/f×n(min)②钻盲孔、铰盲孔tj=(1+11)/(f×n)(min)③钻通孔、铰通孔tj=(1+11+12)/(f×n)(min)4、齿轮加工所用符号tj——机动时间(min)B——齿轮宽度(mm)m——齿轮模数(mm)Z——齿轮齿数B——螺旋角(度)h——全齿高(mm)f——每转进给量(mm/r)vf——进给速度(mm/r)g——铣刀线数n——铣刀每分钟转数(r/min)i——走刀次数11——切入长度(mm)12——切出长度(mm)D0——铣刀直径(mm)d——工件节圆直径(mm)f1——工件每转径向进给量(mm)f2——每双行程圆周进给量(mm)t——每齿加工时间(min)nz——加工每齿双行程次数n分——每分钟双行程次数①用齿轮铣刀铣削圆柱齿轮1)铣直齿轮tj=(B+11+12)×Z×i/vf(min)注:(11+12)=d0/(3~4)(mm)2)铣螺旋齿轮加工中心tj=(B/cosβ+11+12)×Z×i/vf(min)注:(11+12)=d0/(3~4)(mm)②用齿轮滚刀滚削圆柱齿轮(1)滚切直齿轮tj=(B+11+12)×Z/(g×f×n)(min)注:(11+12)=d0/(3~4)(2)滚切螺旋齿轮tj=(B/cosβ+11+12)×Z/(g×f×n)(min) 注:(11+12)=d0/(3~4)③用模数铣刀铣蜗轮tj=(h+11)×Z/f(min)④用蜗轮滚刀径向滚切蜗轮tj=3×m×Z/(g×n×f)(min)⑤用指状铣刀成形铣齿轮tj=(B+0.5d0+12)/(f×n)=(B+0.5d0+12)/vf(min)注:12=2—5(mm)⑥插圆柱齿轮tj=h/(f1×n)+π×d×i/(f2×n)(min)⑦刨齿机刨圆锥齿轮tj=t×Z×i注:式中,t=nZ/n分(min)n分=1000×Vc/2×LL——刀具行程长度(mm)⑧磨齿tj=Z[L/n0(i/f1+212/f2+213/f)+iτ1+2i2τ2+2i3τ3] 将上式查表简化并取平均值为下式tj=Z[L/n0×3.18+0.33](min)式中,L=1+2[h(D-h)+10]1/2——砂轮行程长度(mm) n0——每分钟范成次数D——砂轮直径(mm)h——全齿高i1、i2、i3——粗、半精、精行程次数f1、f2、f3——粗、半精、精每次范成纵向进给量5、铣削加工中心所用符号tj——机动时间(min)L=1+11+12工作台行程长度(mm)1——加工长度(mm)11——切入长度(mm)12——切出长度(mm)Vf——工作台每分钟进给量(mm/min)n——铣刀每分钟转数(r/min)B——铣削宽度(mm)i——走刀次数d0——铣刀直径(mm)D——铣削圆周表面直径(mm)αp——切削深度(mm)β——螺旋角或斜角(度)①圆柱铣刀、圆盘铣刀铣平面、面铣刀铣平面tj=(1+11+12)×i/Vf(min)注:(11+12)=d0/(3~4)(mm)②铣圆周表面tj=D×π×i/vf(min)③铣两端为闭口的键槽tj=(1-d0)×i/vf(min)④铣一端为闭口键槽tj=(1+11)×i/vf(min)⑤铣两端为开口的槽tj=(1+11+12)×i/vf(min)注:11=d0/2+(0.5-1)(mm)12=1-2(mm)⑥铣半圆键槽tj=(1+11)/vf(min)注:1=h——键槽深度(mm)11=0.5-1(mm)⑦按轮廓铣tj=(1+11+12)×i/vf(min)注:1——铣削轮廓长度(mm)11=αp+(0.5-2)12=0-3(mm)⑧铣齿条加工中心1)铣直齿条tj=(B+11+12)×i/vf(min)2)铣斜齿条tj=(B/cosβ+11+12)×i/vf(min)注:以上两式中11+12=d0/(3~4)(mm)⑨铣螺纹1)铣短螺纹tj=L/V周(min)注:式中,L=7πd/6(mm)V周——圆周进给速度(mm/min)d——螺纹外径(mm)2)铣长螺纹tj=d×π×L×g×i/(V周×P)(min)注:式中,L——螺纹长度(mm)g——螺纹头数(mm)p——螺纹升程(度)3)外螺纹旋风铣削tj=L×i/(nW×p)(min)4)内螺纹旋风铣削tj=L×i/(nW×p)(min)注:上两式式中L——被加工螺纹长度(mm)i——走刀次数nW=fZ×n/(d×π)——工件转数P——螺纹升程(mm)fZ——每齿(刀头)的圆周进给量(mm/z)n——铣刀转数(r/min)d——螺纹外(mm)6、用板牙或丝锥加工螺纹tj=[(1+11+12)/p×n+(1+11+12)/p×n1]×i=2×(1+2p)×i/(p×n)(mm)式中,tj——机动时间(mm)1——加工长度(mm)11——切入长度(mm)12——切出长度(mm)p——螺距(mm)n——刀具或工件转数(r/min)n1——刀具或工件返回转数(r/min)7、拉削t1——H/(1000×VC)(min)式中,H——机床调整的冲程长度(mm)8、磨削加工中心所用符号tj——机动时间(min)h——每面加工余量(mm)B——磨轮宽度(mm)f纵——纵向进给量(mm/r)ft——磨削深度进给量(mm)n——工件每分钟转数(r/min)A——切入次数K——光整消除火花修正系数=1.3τ——光整时间(min)L——工件磨削长度(mm)11——工件磨削表面长度(mm)b——工件磨面宽度(mm)VW——工作台往复速度(m/min)fB——磨削宽度进给量(mm)Z——同时加工工件数①外、内圆磨削1)纵向进给磨削tj=2×L×h×K/(n×f纵×ft)(min)2)切入法磨削tj=[h×A/ft+τ]×K=(0.25×A/0.005+0.15)×1.3(min)②平面磨削1)周磨tj=2×L×b×h×K/(1000×VW×FB×ft×Z)(min)注:L=11+20(mm)fB=平均15(mm)ft=0.003-0.085(mm)VW=5-20(m/min)2)端磨t j=h×i/(f双×n双)(min)注:f双——双行程轴向进给量(mm)n双——每分钟双行程数(双程/min)3)无心磨tj=L×i/(0.95×Vf)(min)式中,Vf——轴向进给速度(mm/min)L=1+B(单件)L=n工×1+B(多件连续进给)(mm) 1——工件长度(mm)nZ——连续磨削工件数。
切削用量三要素的定义及公式

切削用量三要素的定义及公式好的,以下是为您生成的关于“切削用量三要素的定义及公式”的文章:在咱们日常的机械加工领域中,切削用量三要素那可是相当重要的角色。
这就好比是烹饪中的盐、糖和酱油,用量合适,才能做出美味的菜肴;在机械加工里,切削用量三要素调配恰当,才能加工出合格又精致的零件。
咱先来说说切削速度,这可是三要素中的“速度担当”。
切削速度就是刀具切削刃上选定点相对于工件的主运动的瞬时速度。
想象一下,你拿着一把锋利的刀,快速地在一块木头上划过,这个划过的速度就是切削速度。
公式是 v = πdn/1000 ,这里的 v 表示切削速度,d 是工件待加工表面或刀具的最大直径,n 是主运动的转速。
给您举个小例子吧,我之前在工厂实习的时候,有一次师傅让我加工一个圆柱形的零件。
我一开始没太注意切削速度,就按照自己的想法随便调了机器的转速。
结果呢,加工出来的零件表面那叫一个粗糙,简直没法看。
师傅过来一看,就指出是切削速度不对。
后来在师傅的指导下,我重新计算并调整了切削速度,加工出来的零件那表面光滑得跟镜子似的,我当时心里那个美啊!接下来聊聊进给量,它就像是你一步一步往前走的步伐大小。
进给量是刀具在进给运动方向上相对工件的位移量。
用 f 来表示,单位通常是 mm/r 或者 mm/行程。
比如说车床上车削螺纹,每转一圈刀具沿着轴向移动的距离就是进给量。
有一回,我们车间接到一个紧急订单,要加工一批细小的轴类零件。
我负责其中一部分,为了赶进度,我把进给量调得过大。
结果零件的尺寸偏差超出了允许范围,差点就造成了损失。
这让我深刻认识到,进给量可不能随意乱调,得根据具体的加工要求来。
最后说说背吃刀量,这是刀具切入工件的深度。
就好比你切西瓜,切下去的厚度就是背吃刀量。
用 ap 表示,单位是 mm 。
记得有一次,我在加工一个比较厚的金属板,一开始背吃刀量设置得太小,加工效率特别低,半天也没弄出个样子来。
后来我大胆地增加了背吃刀量,效率一下子就提上去了,但同时也要注意刀具的承受能力,不能一味地加大,不然刀具可能会受损。
进给量计算公式

进给量计算公式应用在机械加工中,进给量是衡量刀具对工件表面形状工艺性能的最重要参数之一。
它是描述机床切削过程中刀具与工件表面接触时切削深度及其它参数的数字。
进给量是刀具滑移刀边直线滑动距离,单位几何尺寸单位叫“毫米/刀”,它决定了机械加工件的表面精度,铣削深度和刀具滑动频率。
进给量的计算是一个复杂的工程设计过程,它能够帮助设计者在等时间内实现最大的滑动深度和刀具滑动速度。
其计算公式主要有以下几部分组成:(1)滑动线距离:滑动线距离=刀具的滑动频率×刀具的滑动速度;(2)有效滑动距离:有效滑动距离=每层所需时间×刀具的滑动速度;(3)有效沉积厚度:有效沉积厚度=每层所需时间×刀具的滑动速度;(4)刀具滑动时间:刀具滑动时间=每层所需时间×刀具的滑动频率;(5)刀具滑动距离:刀具滑动距离=刀具的滑动频率×每层所需时间;(6)进给量:进给量=刀具滑动距离/刀具滑动时间。
根据上述公式,我们可以求出机械加工中的进给量。
进给量的大小直接影响到机械加工件的外形精度,若进给量太小,将会影响加工件的外形精度;若进给量太大,将会影响刀具的使用寿命,甚至导致机械故障。
因此,在机械加工过程中,对进给量的控制是至关重要的。
此外,进给量的计算也需要考虑到其它因素,例如运动原理、减速比、传动系统精度、刚性等。
运动原理决定了工件表面精度,减速比影响到刀具的滑动频率、传动系统精度决定刀具的滑动速度,而刚性则决定刀具的滑动深度。
总结而言,计算出的进给量是确定机械加工件的表面精度和刀具的使用寿命的重要参数。
因此,在机械加工过程中,精确的计算进给量,以确保加工件高质量,也是一项重要的责任。
机加工价格计算公式自动化公司

机加工价格计算公式自动化公司1.加工时间:机加工的价格计算中,首先需要考虑到的是加工所需的时间。
不同的零部件、复杂程度和机床的类型等都会对加工时间产生影响。
通常,机加工的时间可以用以下公式来计算:加工时间=(加工长度/车削进给速度)+紧急停机时间2.加工方式:机加工的方式也会对价格产生影响。
常见的机加工方式有铣削、车削、钻孔等,每种方式都有不同的设备和加工难度,因此需要根据具体情况进行计算。
3.刀具刃数和寿命:刀具在机加工过程中扮演着至关重要的角色,刃数和寿命的选择也会影响价格的计算。
刃数多的刀具通常可以提高加工效率,但价格也会相应提高。
4.其他费用:除了上述基本因素外,还需要考虑一些其他费用,例如人工费用、能源费用、车削刀片成本等。
这些费用通常是根据实际情况进行估算和计算的。
除了上述基本因素外,还有一些其他因素可能会对机加工价格的计算产生影响,例如加工材料的成本、加工的工艺要求(如精度要求、表面处理等)、生产批量等。
对于机加工价格计算的自动化,可以通过建立适当的软件或工具来实现。
这些软件或工具可以根据用户输入的相关参数,自动计算出机加工价格,并提供详细的报价单或价格明细。
在实际应用中,为了准确计算机加工价格,并提高计算的自动化水平,可以建立包括机床数据、刀具数据、加工数据和成本数据等在内的数据库,并通过合理的算法和模型来进行计算和预测。
同时,结合数据分析和机器学习等技术,还可以对历史数据进行分析和挖掘,以改进价格计算的准确性和自动化水平。
总之,机加工价格的计算涉及多个因素,可以通过合理的公式和自动化工具来实现。
通过建立适当的软件或工具,并结合数据分析和机器学习等技术,可以实现机加工价格计算的自动化,并提高计算的准确性和效率。
机械加工常用计算公式

Vc= 3.14 xD xRPM 1000 V=Vc xap xfr(mm3/min) L Time= fr xN Vc xap xfr xkc P= 60037.2 F力=Kc xfr xap
举例:车削奥氏体不锈钢外圆,工件硬度HB200, 工 件直径75mm,切深3mm,走刀量0.2mm/r, 切削速度 230m/min, 材料单位切削力为2900N/mm2,加工长度 为100mm RPM=(230X1000)/(3.14X75)=976转每分钟 金属去除率V=230x2x0.2=92 立方厘米每分 钟 每加工一个零件的时间=100/(0.2x976)=0.51 分钟 车削功率P=(230x3x0.2x2900)/60037.2=6.7 千瓦 车削力=2900 x0.2 x3=1740牛顿=177.5公斤 车削扭矩T=1740 x37.5=65牛顿米
铣削功率和扭矩的计算 铣削三要素 Cutting data formulas
铣削功率和扭矩的计算 Power consuming and Torque force
Torque (Nm) = kW (nett) x 9549 RPM
铣削功率和扭矩的计算 Power consuming and Torque force 面铣刀直径80mm, 6个刀片刃口,铣削的材料分别为铸 铝合金(kc:800) 和奥氏体不锈钢(kc:2400), 若刀片的切 削速度为600m/min和150m/min, 每齿进刀为fz=0.2mm/z, 切深ap=4mm, 切宽ae=60mP x9549/RPM
镗削功率和扭矩计算
计算镗削功率时注意Vc减半, 即Vc镗=1/2Vc车
举例:镗削奥氏体不锈钢,工件硬度HB200, 工 件直径75mm,切深3mm,走刀量0.2mm/r, 切削速 度115m/min, 材料单位切削力为2900N/mm2,加 工长度为100mm RPM=(115X1000)/(3.14X75)=488转每分钟
孔的最大实效尺寸的公式

孔的最大实效尺寸的公式
(实用版)
目录
1.孔的最大实体尺寸的概念
2.孔的最大实体实效尺寸的公式
3.孔的最大实体实效尺寸的应用
正文
孔的最大实体尺寸是指在孔的尺寸中,最大的实际尺寸,它是控制加工精度的重要参数。
在机械加工中,孔的最大实体实效尺寸的公式可以通过以下步骤计算得出:
1.首先,根据设计图纸,确定孔的基本尺寸,即孔的直径。
2.其次,根据加工工艺和设备能力,确定孔的最大实体尺寸,即孔的最大直径。
3.最后,根据孔的最大实体尺寸和基本尺寸,使用以下公式计算孔的最大实体实效尺寸:
最大实体实效尺寸 = 最大实体尺寸 - 直线度公差
其中,直线度公差是指孔的直线度允许偏差的最大值。
孔的最大实体实效尺寸在机械加工中具有重要的应用。
它可以用于控制加工精度,保证产品的质量。
还可以用于确定加工工艺和设备的能力,以满足生产需要。
第1页共1页。
机械加工常用的10个质量指标,你知道几个?

机械加⼯常⽤的10个质量指标,你知道⼏个?机械⼯作每天会接触很多指标,但是天天挂在嘴上的指标,⾟苦⼀个⽉,师傅们到⼿发现薪资⾥,废品率就扣⼀⼤笔费⽤,于是师傅纷纷跳槽。
很多⼈不理解为啥会扣这么多费⽤,明明没有做报废多少产品,凭啥?今天给⼤家讲讲这些数据都是如何计算出来的,看完就明⽩了!⼀、废品率定义:该百分⽐由废品材料费⽤除以总⽣产成本或由废品总数量除以产品总⽣产数量得到。
⽬的:⽤作结果度量,来确定过程是否按照规范化进⾏零件⽣产和装配。
公式:废品率%=(废品的材料⾦额/总⽣产成本)×100%或(废品总数量/产品总⽣产数量)×100%。
相关术语废品材料⾦额:是废品所使⽤的材料的价值。
总⽣产成本:是劳动⼒,材料和⼯⼚负担(⽔、电等)的总和。
应⽤/信息:废品计算是直接从本单位的财务系统中得到其数值。
若公司的财务系统不能从劳动⼒和负担费⽤中分离出废品材料价值,应尽快与相关部门协调解决。
⼆、返⼯率定义:花费在返⼯活动中时间的⽐例,由返⼯⼯时除以⽣产劳动⼯时或返⼯(返修)品的总数量除以总的⽣产数量得到。
⽬的:⽤作结果度量,来强调那些在第⼀次质量中需要改进的操作⼯位。
公式:返⼯率%=(返⼯⼯时/总⽣产劳动⼯时)×100%或(返⼯(返修)品的总数量/总的⽣产数量)×100%。
相关术语返⼯⼯时:是指再次加⼯,分拣,修复那些将成为废品的⼯件所花费的时间。
这些时间可以是⽤在在制品,成品和外购部件或材料上。
返⼯时间包括诸如修复,重新包装,再分拣,附加的检查活动和遏制等。
返⼯时间包括内部的或外部的活动。
应包括直接时间加上加班时间中的直接时间部分。
⽣产⼯时:直接/⽣产劳动⼯⼈⼯作时间总和(包括直接时间加上加班时间中的直接时间部分)。
应⽤/信息:直接劳动⼯⼈的偶尔检查不应认为是返⼯。
任何再进⼊⽣产过程的产品应被认为返⼯。
⽣产线的总劳动内容的⼀部分应认为是返⼯。
该部分将根据返⼯的产品情况确定,在最终检查时,涂漆⽣产线有10%的产品不合格,⽽该涂漆⽣产线共有20名操作员,返⼯的产品(10%)需要再次涂漆,涂漆⽣产线总⼯作时间的10%被认为是⽤来返⼯。
机械加工常用计算公式
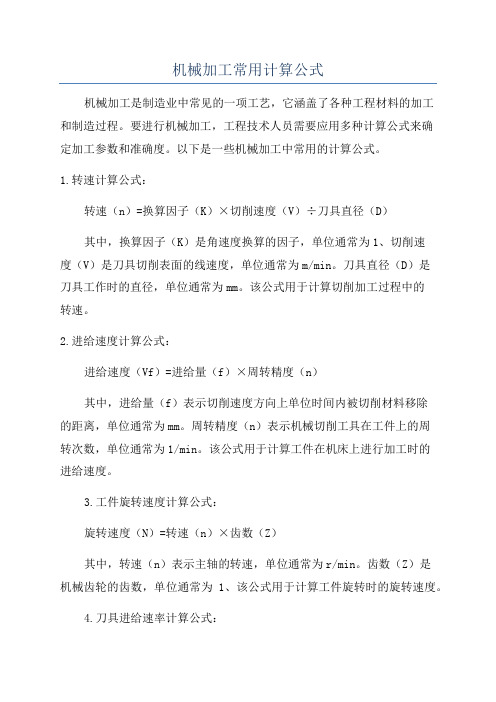
机械加工常用计算公式机械加工是制造业中常见的一项工艺,它涵盖了各种工程材料的加工和制造过程。
要进行机械加工,工程技术人员需要应用多种计算公式来确定加工参数和准确度。
以下是一些机械加工中常用的计算公式。
1.转速计算公式:转速(n)=换算因子(K)×切削速度(V)÷刀具直径(D)其中,换算因子(K)是角速度换算的因子,单位通常为1、切削速度(V)是刀具切削表面的线速度,单位通常为m/min。
刀具直径(D)是刀具工作时的直径,单位通常为mm。
该公式用于计算切削加工过程中的转速。
2.进给速度计算公式:进给速度(Vf)=进给量(f)×周转精度(n)其中,进给量(f)表示切削速度方向上单位时间内被切削材料移除的距离,单位通常为mm。
周转精度(n)表示机械切削工具在工件上的周转次数,单位通常为1/min。
该公式用于计算工件在机床上进行加工时的进给速度。
3.工件旋转速度计算公式:旋转速度(N)=转速(n)×齿数(Z)其中,转速(n)表示主轴的转速,单位通常为r/min。
齿数(Z)是机械齿轮的齿数,单位通常为1、该公式用于计算工件旋转时的旋转速度。
4.刀具进给速率计算公式:进给速率(Fr)=齿数(Z)×螺旋线的累积前进角度(α)×主轴速度(N)其中,齿数(Z)是一次加工过程中所涉及的刀具齿数,单位通常为1、螺旋线的累积前进角度(α)表示刀具旋转一周时前进的角度,单位通常为度或弧度。
主轴速度(N)是主轴的转速,单位通常为r/min。
该公式用于计算刀具进给速率。
5.焊接变形计算公式:变形量(Δ)=γ×L×t其中,γ是金属的线膨胀系数,单位通常为1/℃。
L表示焊缝的长度,单位通常为mm。
t是焊接材料的温度差,单位通常为℃。
该公式用于计算焊接过程中产生的变形量。
总结:上述公式仅是机械加工中常用的一部分计算公式,具体应用时还需要根据具体情况选择合适的公式进行计算。
机械设计知识点口诀

机械设计知识点口诀机械设计是一门涉及多个学科的综合性工程学科,它在工业制造中起着重要的作用。
为了帮助学习者更好地掌握机械设计的基本知识点,下面将为大家总结一些机械设计知识点的口诀,希望对大家的学习有所帮助。
1. 材料选择:优环保,强韧性,便加工,降成本。
杂种铝,碳纤维,塑料棉,钢铁铜。
2. 力学公式:力等于质量乘加速度,弯矩等于力乘距离。
压弯扭剪,拉伸压缩,设计合理,保安全。
3. 运动副分类:平动回转,回转平动,回转回转,平动平动。
滚子轴承,滑动轴承,齿轮传动,机构构造。
4. 运动分析:速度位置,加速度,相互运动,力的传递。
好机构,稳精度,力平衡,牛顿定律。
5. 传动链设计:齿轮带链,带齿轮链,摩擦带链,胶带联结。
传动比,传动效率,工作可靠,操作简易。
6. 零部件设计:标准件选择,设计合理,加工容易,尺寸精确。
轴承支撑,紧固件固定,润滑副润滑,密封防护。
7. 结构强度:式计应力,研材料强度,安全系数,可靠性。
疲劳寿命,预紧压力,刚度系数,结构轻量。
8. 制造工艺:图纸设计,加工工艺,装配顺序,质量控制。
加工精度,设备选型,工艺先进,工期缩短。
9. 试验验证:载荷试验,振动试验,温湿试验,可靠性试验。
数据分析,结论总结,改进优化,产品成功。
10. 创新发展:掌握基础知识,开拓思维,勇于探索,不断创新。
学以致用,实践经验,发现问题,解决难题。
以上是一些机械设计知识点的口诀,通过无压力的背诵和记忆,能够帮助大家更好地理解和掌握机械设计的基本知识。
希望这些口诀能够对大家的学习和工作有所帮助,让我们一起努力,成为优秀的机械设计师!。
切削进给率计算公式
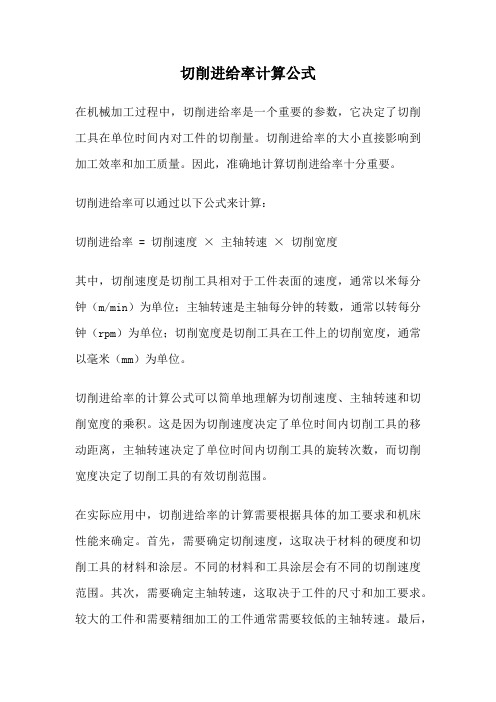
切削进给率计算公式在机械加工过程中,切削进给率是一个重要的参数,它决定了切削工具在单位时间内对工件的切削量。
切削进给率的大小直接影响到加工效率和加工质量。
因此,准确地计算切削进给率十分重要。
切削进给率可以通过以下公式来计算:切削进给率 = 切削速度× 主轴转速× 切削宽度其中,切削速度是切削工具相对于工件表面的速度,通常以米每分钟(m/min)为单位;主轴转速是主轴每分钟的转数,通常以转每分钟(rpm)为单位;切削宽度是切削工具在工件上的切削宽度,通常以毫米(mm)为单位。
切削进给率的计算公式可以简单地理解为切削速度、主轴转速和切削宽度的乘积。
这是因为切削速度决定了单位时间内切削工具的移动距离,主轴转速决定了单位时间内切削工具的旋转次数,而切削宽度决定了切削工具的有效切削范围。
在实际应用中,切削进给率的计算需要根据具体的加工要求和机床性能来确定。
首先,需要确定切削速度,这取决于材料的硬度和切削工具的材料和涂层。
不同的材料和工具涂层会有不同的切削速度范围。
其次,需要确定主轴转速,这取决于工件的尺寸和加工要求。
较大的工件和需要精细加工的工件通常需要较低的主轴转速。
最后,根据切削宽度的要求确定切削宽度的数值。
在实际应用中,切削进给率的计算还需要考虑到切削工具的切削力和切削热。
切削力与进给率成正比,过大的切削进给率可能导致切削工具的磨损和断裂。
切削热与进给率成正比,过大的切削进给率可能导致工件表面的热影响区域扩大,影响加工质量。
在实际操作中,为了保证切削进给率的准确性,通常会使用专用的切削力和切削热传感器进行实时监测。
根据监测结果,可以及时调整切削进给率,以保证加工效率和加工质量。
切削进给率是机械加工过程中必须考虑的重要参数,它直接影响到加工效率和加工质量。
通过准确地计算切削进给率,可以实现高效、精确的机械加工。
因此,在实际应用中,需要根据具体的加工要求和机床性能来确定切削进给率的计算公式,并结合切削力和切削热的监测结果进行调整,以达到最佳的加工效果。
选择切削参数和常用计算公式
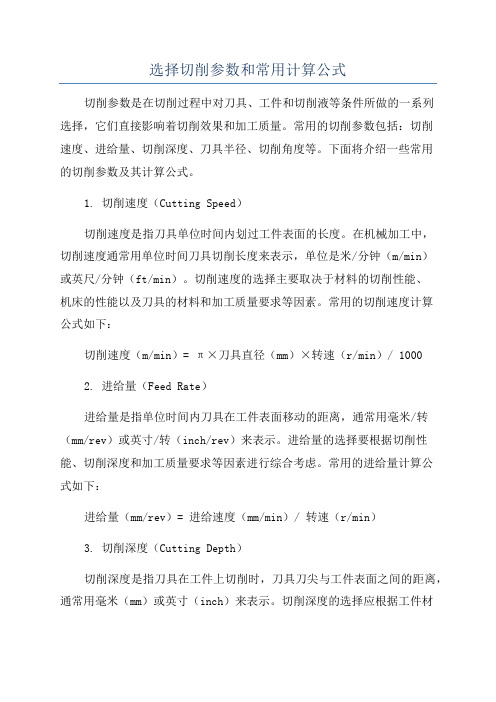
选择切削参数和常用计算公式切削参数是在切削过程中对刀具、工件和切削液等条件所做的一系列选择,它们直接影响着切削效果和加工质量。
常用的切削参数包括:切削速度、进给量、切削深度、刀具半径、切削角度等。
下面将介绍一些常用的切削参数及其计算公式。
1. 切削速度(Cutting Speed)切削速度是指刀具单位时间内划过工件表面的长度。
在机械加工中,切削速度通常用单位时间刀具切削长度来表示,单位是米/分钟(m/min)或英尺/分钟(ft/min)。
切削速度的选择主要取决于材料的切削性能、机床的性能以及刀具的材料和加工质量要求等因素。
常用的切削速度计算公式如下:切削速度(m/min)= π×刀具直径(mm)×转速(r/min)/ 10002. 进给量(Feed Rate)进给量是指单位时间内刀具在工件表面移动的距离,通常用毫米/转(mm/rev)或英寸/转(inch/rev)来表示。
进给量的选择要根据切削性能、切削深度和加工质量要求等因素进行综合考虑。
常用的进给量计算公式如下:进给量(mm/rev)= 进给速度(mm/min)/ 转速(r/min)3. 切削深度(Cutting Depth)切削深度是指刀具在工件上切削时,刀具刀尖与工件表面之间的距离,通常用毫米(mm)或英寸(inch)来表示。
切削深度的选择应根据工件材料的切削性能、机床的性能以及刀具的材料和加工质量要求等因素进行综合考虑。
4. 刀具半径(Tool Radius)刀具半径是指刀具切削边界上切削物质经过切削力的作用下被切除的物质所产生的刀具延伸部分的半径,通常用毫米(mm)或英寸(inch)来表示。
刀具半径直接影响刀具与工件之间的剪切角度和切削力的大小。
5. 切削角度(Cutting Angle)切削角度是指刀具刃口与工件表面之间的夹角,它的大小对切削力、切屑形态和切削温度等具有显著的影响。
常见的切削角度有正角、负角和零角等。
进给速度计算公式

进给速度计算公式好的,以下是为您生成的关于“进给速度计算公式”的文章:在机械加工的世界里,进给速度可是个相当重要的概念。
就好像我们跑步的时候,步伐的快慢决定了我们能跑多远一样,在机械加工中,进给速度的选择直接影响着加工的效率和质量。
那啥是进给速度呢?简单来说,就是刀具在加工过程中沿着工件移动的速度。
比如说,我们用铣床铣一个平面,刀具从这头移动到那头的快慢,就是进给速度。
进给速度的计算公式是:Vf = n × f × z 。
这里的 Vf 就是进给速度啦,n 表示主轴转速,f 是每齿进给量,z 呢则是刀具的齿数。
我记得有一次在工厂实习的时候,碰到了一个加工零件的任务。
师傅让我根据图纸要求计算一下进给速度。
我当时心里那叫一个紧张,深怕算错了影响整个加工过程。
我拿着图纸,对照着公式,一点点地把数据往里套。
那个零件是个小圆柱,要求表面粗糙度比较高。
我先确定了主轴转速,这得根据材料和刀具的性能来选。
然后是每齿进给量,这可不好定,得考虑加工精度和刀具的承受能力。
最后再算上刀具的齿数,这才算出了进给速度。
我把算好的结果小心翼翼地交给师傅,师傅看了看,点了点头,说:“不错,小子,算对了。
但是啊,这只是理论值,实际加工的时候还得根据情况微调。
” 我当时就松了一口气,同时也明白了,理论和实际总是有差距的,得不断摸索和调整。
在实际的加工中,影响进给速度的因素那可多了去了。
材料的硬度就是一个重要因素。
如果材料特别硬,像一些高强度的合金钢,那进给速度就得慢一点,不然刀具磨损得太快,加工出来的表面也不光滑。
要是材料比较软,像铝合金啥的,就可以适当提高进给速度,提高加工效率。
刀具的类型和尺寸也会有影响。
大尺寸的刀具通常能承受更高的进给速度,而小尺寸的刀具就得小心点,速度太快容易折断。
还有,不同类型的刀具,比如立铣刀和钻头,它们适用的进给速度也不一样。
加工工艺的要求也得考虑进去。
要是追求高精度的加工,进给速度就得慢下来,精雕细琢;要是只是粗加工,为了赶时间,就可以把速度提上去。
机械加工常用的10个质量指标
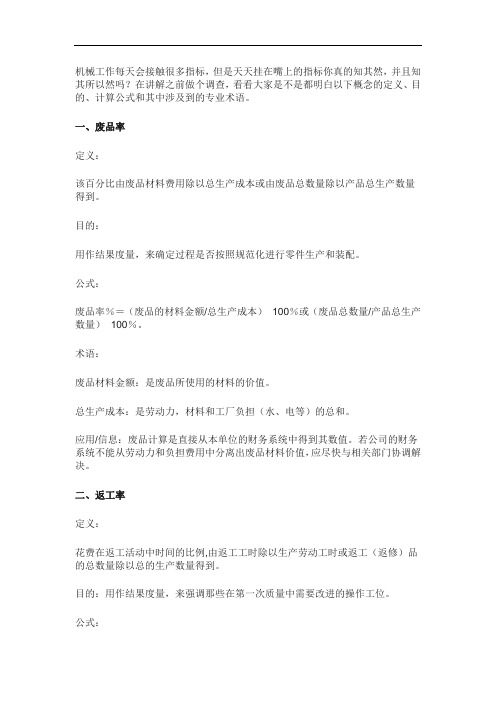
机械工作每天会接触很多指标,但是天天挂在嘴上的指标你真的知其然,并且知其所以然吗?在讲解之前做个调查,看看大家是不是都明白以下概念的定义、目的、计算公式和其中涉及到的专业术语。
一、废品率定义:该百分比由废品材料费用除以总生产成本或由废品总数量除以产品总生产数量得到。
目的:用作结果度量,来确定过程是否按照规范化进行零件生产和装配。
公式:废品率%=(废品的材料金额/总生产成本)×100%或(废品总数量/产品总生产数量)×100%。
术语:废品材料金额:是废品所使用的材料的价值。
总生产成本:是劳动力,材料和工厂负担(水、电等)的总和。
应用/信息:废品计算是直接从本单位的财务系统中得到其数值。
若公司的财务系统不能从劳动力和负担费用中分离出废品材料价值,应尽快与相关部门协调解决。
二、返工率定义:花费在返工活动中时间的比例,由返工工时除以生产劳动工时或返工(返修)品的总数量除以总的生产数量得到。
目的:用作结果度量,来强调那些在第一次质量中需要改进的操作工位。
公式:返工率%=(返工工时/总生产劳动工时)×100%或(返工(返修)品的总数量/总的生产数量)×100%。
术语:返工工时:是指再次加工,分拣,修复那些将成为废品的工件所花费的时间。
这些时间可以是用在在制品,成品和外购部件或材料上。
返工时间包括诸如修复,重新包装,再分拣,附加的检查活动和遏制等。
返工时间包括内部的或外部的活动。
应包括直接时间加上加班时间中的直接时间部分。
生产劳动工时:直接/生产劳动工人工作时间总和(包括直接时间加上加班时间中的直接时间部分)。
应用/信息:直接劳动工人的偶尔检查不应认为是返工。
任何再进入生产过程的产品应被认为返工。
生产线的总劳动内容的一部分应认为是返工。
该部分将根据返工的产品情况确定。
譬如,在最终检查时,涂漆生产线有10%的产品不合格,而该涂漆生产线共有20名操作员,返工的产品(10%)需要再次涂漆,涂漆生产线总工作时间的10%被认为是用来返工。
车床刀具切削参数计算公式
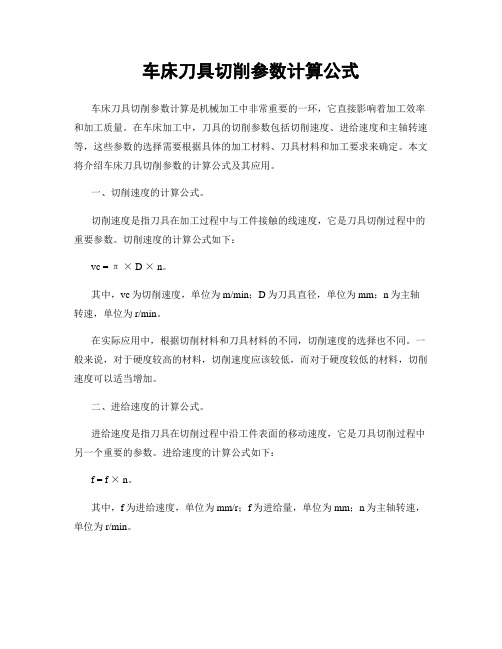
车床刀具切削参数计算公式车床刀具切削参数计算是机械加工中非常重要的一环,它直接影响着加工效率和加工质量。
在车床加工中,刀具的切削参数包括切削速度、进给速度和主轴转速等,这些参数的选择需要根据具体的加工材料、刀具材料和加工要求来确定。
本文将介绍车床刀具切削参数的计算公式及其应用。
一、切削速度的计算公式。
切削速度是指刀具在加工过程中与工件接触的线速度,它是刀具切削过程中的重要参数。
切削速度的计算公式如下:vc = π× D × n。
其中,vc为切削速度,单位为m/min;D为刀具直径,单位为mm;n为主轴转速,单位为r/min。
在实际应用中,根据切削材料和刀具材料的不同,切削速度的选择也不同。
一般来说,对于硬度较高的材料,切削速度应该较低,而对于硬度较低的材料,切削速度可以适当增加。
二、进给速度的计算公式。
进给速度是指刀具在切削过程中沿工件表面的移动速度,它是刀具切削过程中另一个重要的参数。
进给速度的计算公式如下:f = f × n。
其中,f为进给速度,单位为mm/r;f为进给量,单位为mm;n为主轴转速,单位为r/min。
在实际应用中,进给速度的选择需要考虑到切削材料、刀具材料和加工要求等因素。
一般来说,对于粗加工,进给速度可以适当增加,而对于精加工,则需要降低进给速度。
三、主轴转速的计算公式。
主轴转速是指车床主轴的转速,它是刀具切削过程中的另一个重要参数。
主轴转速的计算公式如下:n = (vc × 1000) / (π× D)。
其中,n为主轴转速,单位为r/min;vc为切削速度,单位为m/min;D为刀具直径,单位为mm。
在实际应用中,主轴转速的选择需要根据切削材料和刀具材料的不同来确定。
一般来说,对于硬度较高的材料,主轴转速应该较低,而对于硬度较低的材料,则可以适当增加主轴转速。
四、切削力的计算公式。
切削力是指刀具在切削过程中对工件施加的力,它是刀具切削过程中的另一个重要参数。
切削三要素的计算公式
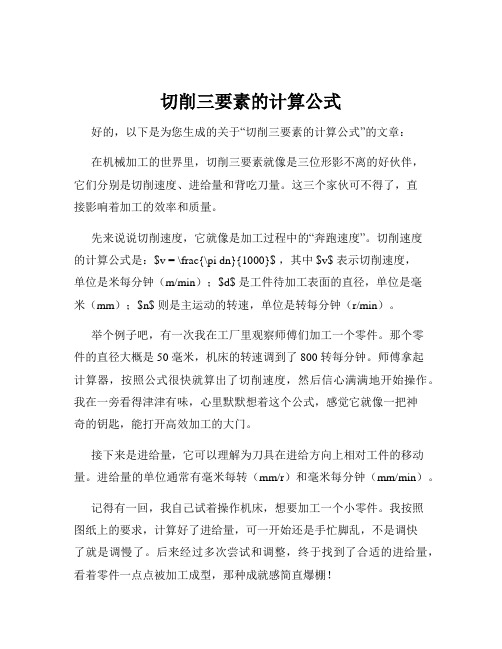
切削三要素的计算公式好的,以下是为您生成的关于“切削三要素的计算公式”的文章:在机械加工的世界里,切削三要素就像是三位形影不离的好伙伴,它们分别是切削速度、进给量和背吃刀量。
这三个家伙可不得了,直接影响着加工的效率和质量。
先来说说切削速度,它就像是加工过程中的“奔跑速度”。
切削速度的计算公式是:$v = \frac{\pi dn}{1000}$ ,其中 $v$ 表示切削速度,单位是米每分钟(m/min);$d$ 是工件待加工表面的直径,单位是毫米(mm);$n$ 则是主运动的转速,单位是转每分钟(r/min)。
举个例子吧,有一次我在工厂里观察师傅们加工一个零件。
那个零件的直径大概是 50 毫米,机床的转速调到了 800 转每分钟。
师傅拿起计算器,按照公式很快就算出了切削速度,然后信心满满地开始操作。
我在一旁看得津津有味,心里默默想着这个公式,感觉它就像一把神奇的钥匙,能打开高效加工的大门。
接下来是进给量,它可以理解为刀具在进给方向上相对工件的移动量。
进给量的单位通常有毫米每转(mm/r)和毫米每分钟(mm/min)。
记得有一回,我自己试着操作机床,想要加工一个小零件。
我按照图纸上的要求,计算好了进给量,可一开始还是手忙脚乱,不是调快了就是调慢了。
后来经过多次尝试和调整,终于找到了合适的进给量,看着零件一点点被加工成型,那种成就感简直爆棚!最后是背吃刀量,它指的是已加工表面与待加工表面之间的垂直距离。
这个家伙在加工中也起着至关重要的作用。
在学习这部分知识的时候,我曾经做过一个实验。
我准备了一块材料,然后根据不同的背吃刀量进行切削。
结果发现,背吃刀量的大小直接影响着切削力和加工表面的粗糙度。
总之,切削三要素的计算公式虽然看起来有点复杂,但只要我们多实践、多琢磨,就一定能掌握其中的奥秘,让机械加工变得更加高效和精确。
就像我们在生活中解决各种难题一样,只要有耐心、有方法,就没有什么能难倒我们!所以呀,小伙伴们,别害怕这些公式,勇敢地去探索机械加工的奇妙世界吧!。
工作机轴转数计算公式

工作机轴转数计算公式在工程领域中,工作机轴的转数是一个非常重要的参数。
它可以用来确定机器的工作效率、速度和功率等。
因此,正确地计算工作机轴转数对于工程师和技术人员来说至关重要。
在本文中,我们将介绍工作机轴转数的计算公式,并且讨论一些常见的应用。
工作机轴转数是指工作机械或设备在单位时间内旋转的圈数。
它通常用转/分钟(rpm)来表示。
工作机轴转数的计算公式可以通过以下方式来推导得到。
首先,我们需要知道工作机轴的直径(D)和主轴的转速(N)。
根据这两个参数,我们可以使用以下公式来计算工作机轴的转数:N = (1000 V) / (π D)。
其中,N表示工作机轴的转数,V表示主轴的线速度,π表示圆周率。
主轴的线速度可以通过以下公式来计算:V = π D n。
其中,V表示主轴的线速度,D表示工作机轴的直径,n表示主轴的转速。
通过以上两个公式,我们可以得到工作机轴转数的计算公式:N = (1000 π D n) / (π D) = 1000 n。
这个公式非常简单,但是非常有用。
通过这个公式,我们可以很容易地计算出工作机轴的转数。
在实际应用中,工程师和技术人员可以根据这个公式来确定工作机轴的适当转速,从而达到最佳的工作效果。
工作机轴转数的计算公式在工程领域中有着广泛的应用。
例如,在机械加工中,工程师可以通过这个公式来确定车床、铣床、钻床等工作机械的转速,从而确保工件可以得到精确的加工。
在风力发电领域,工程师可以使用这个公式来确定风力发电机的转速,从而提高发电效率。
在汽车工程中,工程师可以使用这个公式来确定汽车发动机的转速,从而提高汽车的动力性能。
除了以上的应用,工作机轴转数的计算公式还可以用于教学和研究。
通过这个公式,学生可以更好地理解工作机轴转数的概念,并且可以通过计算实例来加深对这个概念的理解。
在研究领域,工程师和科研人员可以使用这个公式来设计新的工作机械或设备,从而提高工作效率和性能。
总之,工作机轴转数的计算公式是工程领域中非常重要的一个公式。
机械加工纸公差计算公式

机械加工纸公差计算公式在机械加工中,公差是一个非常重要的概念。
公差是指零件尺寸允许的最大偏差和最小偏差之间的差值。
在机械加工中,需要根据设计要求和工艺要求来确定零件的公差,以保证零件的质量和性能。
纸公差是指在纸张的加工过程中,为了保证纸张的尺寸精度和平整度而设置的公差。
纸公差的计算是纸张加工过程中的重要环节,它直接影响着纸张的质量和加工效率。
纸公差的计算公式是根据纸张的加工要求和工艺要求来确定的。
一般来说,纸公差的计算公式包括以下几个方面:1. 纸张的厚度公差计算公式。
纸张的厚度公差是指纸张在加工过程中允许的最大厚度偏差和最小厚度偏差之间的差值。
纸张的厚度公差计算公式一般为:Δt = tmax tmin。
其中,Δt为纸张的厚度公差,tmax为纸张的最大厚度,tmin为纸张的最小厚度。
2. 纸张的长度公差计算公式。
纸张的长度公差是指纸张在加工过程中允许的最大长度偏差和最小长度偏差之间的差值。
纸张的长度公差计算公式一般为:ΔL = Lmax Lmin。
其中,ΔL为纸张的长度公差,Lmax为纸张的最大长度,Lmin为纸张的最小长度。
3. 纸张的宽度公差计算公式。
纸张的宽度公差是指纸张在加工过程中允许的最大宽度偏差和最小宽度偏差之间的差值。
纸张的宽度公差计算公式一般为:ΔW = Wmax Wmin。
其中,ΔW为纸张的宽度公差,Wmax为纸张的最大宽度,Wmin为纸张的最小宽度。
4. 纸张的角度公差计算公式。
纸张的角度公差是指纸张在加工过程中允许的最大角度偏差和最小角度偏差之间的差值。
纸张的角度公差计算公式一般为:Δθ = θmax θmin。
其中,Δθ为纸张的角度公差,θmax为纸张的最大角度,θmin为纸张的最小角度。
5. 纸张的平整度公差计算公式。
纸张的平整度公差是指纸张在加工过程中允许的最大平整度偏差和最小平整度偏差之间的差值。
纸张的平整度公差计算公式一般为:Δf = fmax fmin。
其中,Δf为纸张的平整度公差,fmax为纸张的最大平整度,fmin为纸张的最小平整度。
铣刀转速和进给公式

铣刀转速和进给公式引言:在机械加工中,铣刀转速和进给是两个关键参数,对于加工效率和加工质量具有重要影响。
本文将介绍铣刀转速和进给的概念、计算公式以及影响因素,帮助读者更好地理解和应用这两个参数。
一、铣刀转速的概念及计算公式1. 铣刀转速的概念铣刀转速是指铣刀在单位时间内旋转的圈数,通常以转/分(rpm)表示。
合理的铣刀转速可以确保切削过程的稳定性和切削效率。
2. 铣刀转速的计算公式铣刀转速的计算公式如下:转速 = (刀具直径×3.14×切削速度)/ 1000其中,刀具直径是指铣刀刀尖的直径大小,切削速度是指铣刀与工件接触面上的相对速度。
3. 铣刀转速的影响因素铣刀转速的选择需要考虑以下几个因素:(1)材料的硬度和切削性能:硬度高的材料通常需要较低的转速,而切削性能良好的材料可以选择较高的转速。
(2)刀具类型和材质:不同类型和材质的刀具有不同的最大转速限制,需要根据刀具的性能参数来选择合适的转速。
(3)切削深度和进给量:较大的切削深度和进给量通常需要较低的转速,以保证切削过程的稳定性和切削质量。
二、进给的概念及计算公式1. 进给的概念进给是指铣刀在单位时间内在工件上移动的距离,通常以毫米/转(mm/rev)表示。
合理的进给可以控制切削过程的速度和加工表面的质量。
2. 进给的计算公式进给的计算公式如下:进给 = 切削速度 / (转速×刀具齿数)其中,切削速度是指铣刀与工件接触面上的相对速度,刀具齿数是指铣刀上的切削齿数。
3. 进给的影响因素进给的选择需要考虑以下几个因素:(1)切削深度和切削速度:较大的切削深度和切削速度通常需要较大的进给,以保证切削过程的稳定性和加工效率。
(2)刀具类型和材质:不同类型和材质的刀具有不同的最大进给限制,需要根据刀具的性能参数来选择合适的进给。
(3)工件材料和形状:不同材料和形状的工件对进给的要求也不同,需要根据实际情况进行调整。
结论:铣刀转速和进给是机械加工中的两个重要参数,对于加工效率和加工质量具有重要影响。
- 1、下载文档前请自行甄别文档内容的完整性,平台不提供额外的编辑、内容补充、找答案等附加服务。
- 2、"仅部分预览"的文档,不可在线预览部分如存在完整性等问题,可反馈申请退款(可完整预览的文档不适用该条件!)。
- 3、如文档侵犯您的权益,请联系客服反馈,我们会尽快为您处理(人工客服工作时间:9:00-18:30)。
0.6403*(25.4/每吋牙数)
(牙角55度)
PS 3/4-14 (直形管螺纹)
PF1 1/8-16 (直形管螺纹)
牙
1 1/8英吋管用,每英吋16牙
管螺纹(美制NPT)
(牙角60度)
NPT 3/4-14 (锥形管螺纹)锥形管螺纹,锥度比1/16
(1B 2B 3B内牙公差配合等级)
UNC美制统一标准粗牙螺纹
外径3/4英吋,每英吋10牙
外牙2级公差配合
管螺纹(英制PT)
牙深=
0.6403*(25.4/每吋牙数)
(牙角55度)
PT 3/4-14 (锥度管螺纹)锥度管螺纹,锥度比1/16
3/4英吋管用,每英吋14牙
管螺纹
(PS直螺纹)(PF细牙)
T0101
G97 S1575 M3
G0 X23. Z8. M8 ?车牙循环起始点
G0 X18.5 ?1.下刀
G32 Z-19. F2.54 ? 2.车牙进给
G0 X23. ?3.起刀
G0 Z8. ?4.退回起始点G92 X18.5 Z-19. F2.54 ?车牙循环
X18.
X17.6
X17.2
G0 X18.0? 1.下刀
X15.8
X15.75 M9
G0 X17.2
G32 Z-19. F2.54
G0 X23.
G0 Z8. G0 X16.
G32 Z-19. F2.54
G0 X23.
G0 Z8. G0 Z20. M5
G0 X120. Z120. T0
M30
G0 X16.9
G32 Z-19. F2.54
G0 X23.
G0 Z8. G0 X15.9
N = 1000V / pD = 1000 * 120 / (3.1416*19.05)
=2005 rpm (转/分)
因为机器结构所决定的转速
刀座快速移动的影响车牙最高转速N = 4000 / P
N = 4000/2.54 = 1575 rpm
综合工件材料刀具及机械结构
所决定的转速N = 1575转N = 2005转
(内螺纹配合等级6H)
(外螺纹配合等级7g)
左-双头-M20x1.5 (左手)-(双头螺纹)-(公制细牙)
(公称直径20mm) (牙距1.5mm)
美制螺纹
(统一标准螺纹)
牙深=
0.6495*(25.4/每吋牙数)
(牙角60度)
3/4-10UNC-2A
(UNC粗牙)(UNF细牙)
(1A 2A 3A外牙公差配合等级)
G32 Z-19. F2.54 ?2.车牙
G0 X23. ?3.起刀
G0 Z8.?4.退回起始点X16.9X16.65
X16.4
X16.2
G0 X17.6
G32 Z-19. F2.54
G0 X23.
G0 Z8. G0 X16.1
G32 Z-19. F2.54
G0 X23.
G0 Z8.X16.
X15.9
G00 X31.3 1.下刀(用G00取消车牙状态) G00 X31.3 1.下刀(用G00取消车牙状态)
G32 Z-28. F28. 2.车牙(前进) G32 Z-28.F26. 2.车牙(前进)
Z9. 3.车牙(往回) Z9. 3.车牙(往回)
......
G0 Z20. M5G0 Z20. M5
G0 X31. 1.下刀Z2.车牙起始点(X30. Z-2.)
G32 Z-28. F28. 2.车牙前进G01 X31. 1.下刀
G32 Z9.F28. 3.车牙往回(在-14MM处有交叉) G32 Z-28. F26. 2.车牙前进(-28+26/2)
(-28+28/2) G32 Z2.F26. 3.车牙往回(在-15MM处有交叉)
3/4英吋管用,每英吋14牙
梯形螺纹
(30度公制)
TM40*6公称直径40mm牙距6.0mm
梯形螺纹
(29度爱克姆螺纹)
TW26*5外径26mm,每英吋5牙
方形螺纹
车牙的计算
考虑条件计算公式
公制牙与英制牙的转换每吋螺纹数n = 25.4 /牙距P
牙距P = 25.4 /每吋螺纹数n
因为工件材料及刀具所决定的转速转速N = (1000周速V ) / (圆周率p *直径D )
机械加工中用到的重要公式
螺纹的加工和计算
2008-03-22 13:17:24
螺纹的加工和计算
纹的种类
名称标注方式说明
公制螺纹(MM牙)
牙深=0.6495*牙距P
(牙角60度)
内牙孔径=
公称直径-1.0825*P
M20x2.5-6H/7g (右手)-(单头螺纹)-(公制粗牙)
(公称直径20mm) (牙距2.5mm)
牙深及牙底径d牙深径d =公称外径D-2*h =19.05-2*1.65 = 15.75mm
车牙的程式
O1905 (3/4”-10UNC用G32车牙) O1905 (3/4”-10UNC用G92车牙)
N1 G0 X120. Z120. T0
T0101
G97 S1575 M3
G0 X23. Z8. M8 ?车牙起始点N1 G0 X120. Z120. T0
G97 S1575 M3
G0 X23. Z8. M8 ?车牙循环起始点
G0 X16.4
G32 Z-19. F2.54
G0 X23.
G0 Z8. G0 X15.75
G32 Z-19. F2.54
G0 X23. M9
G0 Z8. M5 G76 P000060 Q50 R50
G76 X15.75 Z-19. P1650 Q350 F2.54
X50. Z120. T0X50. Z120.T0
M1M1
G0 Z8. 4.退回起始点
车8字油沟(单8字有出口)
车8字油沟(单8字无出口)
N3 G0 X50. Z120. T0 N3 G0 X50. Z120. T0
T0101 T0101
G97 S140 M3 G97 S160 M3
G0 X30. Z9. M8车牙起始点(X30. Z9.) G00 X30. Z20. M8
G32 Z-19. F2.54
G0 X23.
G0 Z8. O1905 (3/4”-10UNC用G76车牙)
G0 X16.65
G32 Z-19. F2.54
G0 X23.
G0 Z8. G0 X15.8
G32 Z-19. F2.54
G0 X23.
G0 Z8. N1 G0 X120. Z120. T0
T0101
G32 X(终点座标) Z(终点座标) F(导程)
<G32螺纹程式范例>
G0 X23. Z8. M8
车牙起始点
G0 X18.5 1.下刀
G32 Z-19. F2.54 2.车牙进给
G0 X23. 3.起刀
G0 Z8. 4.退回起始点
G0 X18.0 1.下刀
G32 Z-19. F2.54 2.车牙
G0 X23. 3.起刀
因为机器结构所决定的转速
刀座快速移动的影响车牙最高转速N = 4000/ P
刀座快速移动加减速的影响
下刀点与退刀点的计算
(不完全牙的计算)下刀最小距离L1
L1 = (牙距P ) * (主轴转速S ) / 500
退刀最距离L2
L2 = (牙距P ) * (主轴转速S ) / 2000
牙深及牙底径d牙深h =0.6495 * P
牙底径d =公称外径D - 2 * h
例题: 车制外牙3/4"-10UNC20mm长
公制牙与英制牙的转换牙距P = 25.4 / (吋螺纹数n)
P = 25.4 / 10 = 2.54mm
因为工件材料及
刀具所决定的转速外径D = 3 / 4英吋= 25.4 * (3/4) =19.05MM
转速N = (1000周速V) / (圆周率p *直径D )
G0 Z20. M5
G0 X120. Z120. T0 M9
G0 X16.2
G32 Z-19. F2.54
G0 X23.
G0 Z8. G0 X120. Z120. T0
M30 M30
螺纹切削(G32)
除了等导程直螺纹外,斜螺纹和涡形螺纹亦能用G32指令切削。
以下列指令切削螺纹,导程以数字接在位址F后面来指定。F轴向导程
两者转速选择较低者,即1575转
刀座快速移动加减速的影响
下刀点与退刀点的计算
(不完全牙的计算)下刀最小距离L1
L1 = (牙距P) * (主轴转速S) / 500
L1 = 2.54*1575/500=8.00mm
退刀最小距离L2
L2 = (牙距P) * (主轴转速S) / 2000
L2 = 2.54*1575/2000=2.00mm