车身三维尺寸视觉检测系统
三坐标测量机在汽车整车检测中的应用
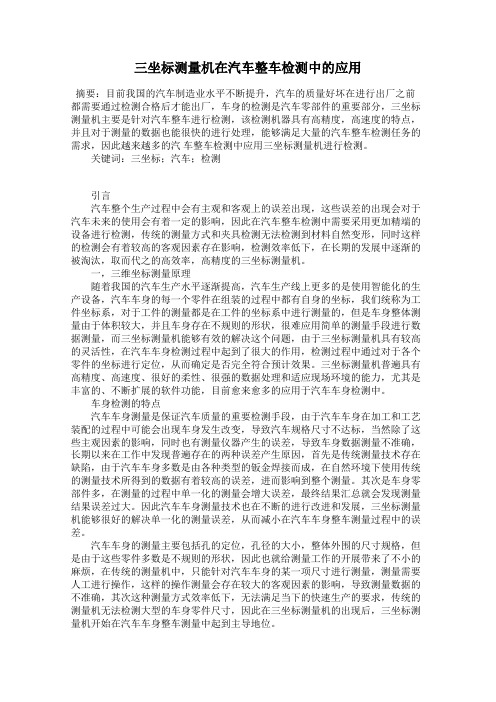
三坐标测量机在汽车整车检测中的应用摘要:目前我国的汽车制造业水平不断提升,汽车的质量好坏在进行出厂之前都需要通过检测合格后才能出厂,车身的检测是汽车零部件的重要部分,三坐标测量机主要是针对汽车整车进行检测,该检测机器具有高精度,高速度的特点,并且对于测量的数据也能很快的进行处理,能够满足大量的汽车整车检测任务的需求,因此越来越多的汽车整车检测中应用三坐标测量机进行检测。
关键词:三坐标;汽车;检测引言汽车整个生产过程中会有主观和客观上的误差出现,这些误差的出现会对于汽车未来的使用会有着一定的影响,因此在汽车整车检测中需要采用更加精端的设备进行检测,传统的测量方式和夹具检测无法检测到材料自然变形,同时这样的检测会有着较高的客观因素存在影响,检测效率低下,在长期的发展中逐渐的被淘汰,取而代之的高效率,高精度的三坐标测量机。
一,三维坐标测量原理随着我国的汽车生产水平逐渐提高,汽车生产线上更多的是使用智能化的生产设备,汽车车身的每一个零件在组装的过程中都有自身的坐标,我们统称为工件坐标系,对于工件的测量都是在工件的坐标系中进行测量的,但是车身整体测量由于体积较大,并且车身存在不规则的形状,很难应用简单的测量手段进行数据测量,而三坐标测量机能够有效的解决这个问题,由于三坐标测量机具有较高的灵活性,在汽车车身检测过程中起到了很大的作用,检测过程中通过对于各个零件的坐标进行定位,从而确定是否完全符合预计效果。
三坐标测量机普遍具有高精度、高速度、很好的柔性、很强的数据处理和适应现场环境的能力,尤其是丰富的、不断扩展的软件功能,目前愈来愈多的应用于汽车车身检测中。
车身检测的特点汽车车身测量是保证汽车质量的重要检测手段,由于汽车车身在加工和工艺装配的过程中可能会出现车身发生改变,导致汽车规格尺寸不达标,当然除了这些主观因素的影响,同时也有测量仪器产生的误差,导致车身数据测量不准确,长期以来在工作中发现普遍存在的两种误差产生原因,首先是传统测量技术存在缺陷,由于汽车车身多数是由各种类型的钣金焊接而成,在自然环境下使用传统的测量技术所得到的数据有着较高的误差,进而影响到整个测量。
车辆外廓测量系统方案
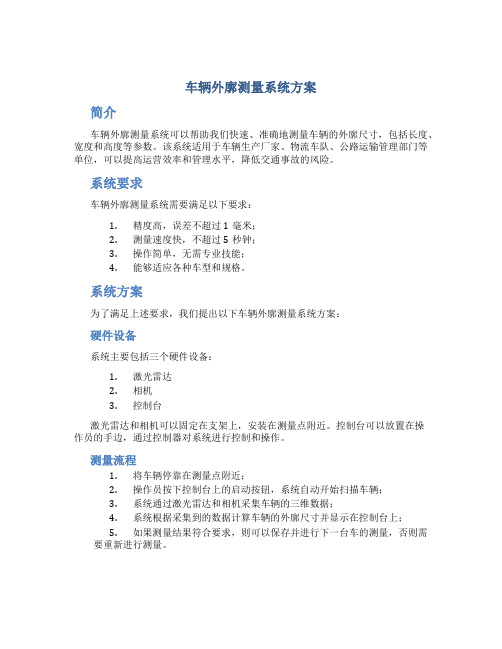
车辆外廓测量系统方案简介车辆外廓测量系统可以帮助我们快速、准确地测量车辆的外廓尺寸,包括长度、宽度和高度等参数。
该系统适用于车辆生产厂家、物流车队、公路运输管理部门等单位,可以提高运营效率和管理水平,降低交通事故的风险。
系统要求车辆外廓测量系统需要满足以下要求:1.精度高,误差不超过1毫米;2.测量速度快,不超过5秒钟;3.操作简单,无需专业技能;4.能够适应各种车型和规格。
系统方案为了满足上述要求,我们提出以下车辆外廓测量系统方案:硬件设备系统主要包括三个硬件设备:1.激光雷达2.相机3.控制台激光雷达和相机可以固定在支架上,安装在测量点附近。
控制台可以放置在操作员的手边,通过控制器对系统进行控制和操作。
测量流程1.将车辆停靠在测量点附近;2.操作员按下控制台上的启动按钮,系统自动开始扫描车辆;3.系统通过激光雷达和相机采集车辆的三维数据;4.系统根据采集到的数据计算车辆的外廓尺寸并显示在控制台上;5.如果测量结果符合要求,则可以保存并进行下一台车的测量,否则需要重新进行测量。
系统优势该系统方案具有以下优点:1.精度高:采用激光雷达和相机进行三维测量,精度可达到1毫米;2.测量速度快:自动扫描并计算,不超过5秒钟;3.操作简单:通过控制器进行操作,无需专业技能;4.适应性强:能够适应各种车型和规格;5.实时显示:测量结果实时显示在控制台上,方便操作员进行核对和实时控制。
总结总体而言,车辆外廓测量系统方案可以提高车辆外廓的测量精度和效率,简化操作流程,减少人工干预和误差,对于车辆生产、物流运输和公路管理等领域都具有重要的意义和应用价值。
视觉测量系统简易模式产品说明书
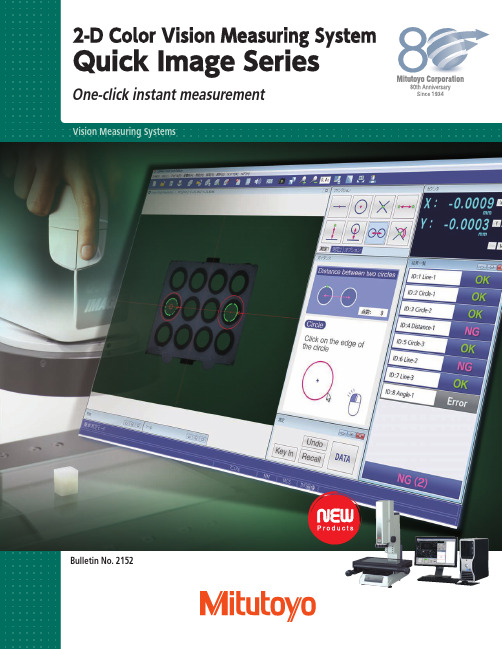
Renton, Washington
NoteM: Aalsl oinnfo, rOmhaiotion
regarding
our
products,
and
in
particular
the
Houston, Texas illustrations, drawings,
dimensional
and
performance
© 2014 Mitutoyo America Corporation, Aurora IL
1.5M 0614-07 Printed in USA, August 2014
O1-n8e88N-uMmITbUeTrOtoYOSe(r1v-e88Y8o-u64B8WH(eC-uote8ntrs8eptteo6rforr9asrtdv)ei,HllMeea,adsNqsuoaarrctthehrusCs)aertotslina
Plymouth, Michigan
Mason, Ohio
Transmitted light: Green LEDOnteeleNceunmtribceilrlutmoinSaetriovne; YCou-axBiaeltLteigrht: White LED; Ring light: quadrant white LED 1-888-MITUTOYO (1-8280±81-6ºC48-8869)
• Alignment of workpiece is automatically located via pattern recognition.
• Provides quick results of features (GO/NG/PASS/FAIL).
QIPAK Simple Mode
基于计算机视觉的汽车整车尺寸测量系统
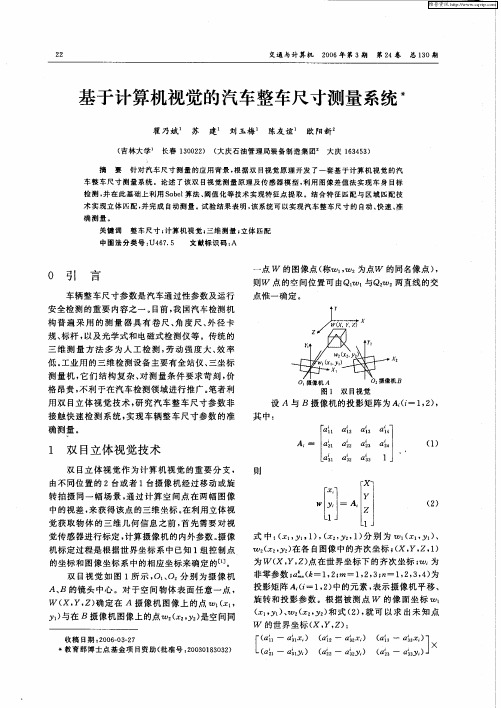
A tl 口 口 a 口 i i i z z 3 4 i z 2 2 I
。
ta a a 。 ]
1
() 1
J
X
y
转拍 摄 同 一 幅 场景 , 过 计 算 空 间点 在 两 幅 图像 通 中的视差 , 获得 该 点 的三 维 坐标 来 在利 用立 体视 觉 获取 物 体 的 三维 几 何 信 息之 前 , 先 需要 对 视 首
W ( Y ) z ,2在各 自图像 中的齐 次坐 标 ;x, Z, ) ( Y, 1
为 W ( Y, 点 在世 界坐标 下 的齐 次坐 标 1 为 X, z) w
的坐标 和 图像坐 标 系 中的相应 坐标 来确 定 的[ 。 双 目视 觉 如 图 1所 示 , O O 、 分 别 为 摄 像 机
的世 界 坐标 ( y, : x, z)
厂 口l一 日 l . ( 2 日 2 ( ( z ) 一 . ) 口 3一 3 .] z z)
1
Y) 在 B摄 像机 图像 上 的点 W ( Y) 与 z ,。是空 间 同
收稿 日期 :0 60 — 7 2 0 — 32
维普资讯
史通 与计 算 机
2 0 年 第 3期 第 2 06 4卷 总 1 0期 3
基于 计算机视觉 的汽车整车尺寸测量 系统 *
翟乃斌 苏 建 刘 玉梅 陈友 谊 欧 阳新。
( 吉林大学 长春 1 0 2 ) ( 30 2 大庆石油管理局装 备制造集团 大庆 1 3 5 ) 6 4 3 摘 要 针对 汽车尺寸测量 的应用 背景 , 根据双 目视觉原理开发 了一套 基于计算机视觉 的汽
*教育部博 士点 基金项 目资助 ( 批准号 :03 1 3 3 ) 2 0 0 8 02
车身三维尺寸视觉检测及其最新进展

基准坐标 系下( 即系统全局校准)传感器由系统 中 , 的计算机控制。 测量时 , 每个传感器测量相应点的三
维坐标, 并转换到基准坐标系中, 全部传感器给出车
身上所有被测点的测量结果 , 完成系统测量任务 。
2 车身三维尺 寸视觉检测原理
典型的车身三维尺寸视觉检测系统原理如图 1
邾继贵 , 杨学友 , 叶声华
( 天津大学工程精 密剥试技 术及仪嚣国家重点 弗验室 , 天津 307 ) 0 0 2
摘要 : 车身三维尺寸视觉检测技术是 近十几年发展起 来的一项 白车身尺寸测 试技术 , 具有非接 触 、 度 速
快 可在线等突出优点 , 为全面提高车身 的制造精度提供 了有效的检 测手段 。结台实 际科研经历 , 讨论了
传感器包括光平面投射器 和摄像机两部分 , 基 于三角法测量原理。 测量时, 光平面投射器投射出光 平面 , 光平面和被测物体表面相交形成光条 , 光条图
率和维护成本。 最新研制的视觉传感器采用 了基于立体视觉检 测原 理的 统一结 构 ,克服 了两种 传感器 结构及 校 准 方法不统一的缺点 , 传感器原理如图4所示。
维普资讯
邾继责等: 车身三雏足寸视觉检测厦 其最新进展
a 传感器校准困难 、 . 精度低。 传感器在使用前 ,
必须标定光平面和摄像机之间的空间关系 ,目前的 方法是使用细丝散射结合经纬仪的方法,这种方法 受散射光点无法精确瞄准的影响 ,校准精度难 以提
视觉传感器而言是两种不同类型的被测点 ,需要光
条结构光传感器和光栅结构光传感器 。光条结构光 传感器原理如图 2 所示 , 用于测量棱线点 ; 光栅结构 光传感器原理如图 3 所示 , 当于具有多个光平面 相 的光条传感器 ,一次测量可以同时得到多个不同空 间位置上点的三维坐标 ( 如测量圆孔时 , 可得到圆周 上多个点的坐标 )由此计算 出被测特征点 ( , 如圆孔
浅谈整车匹配测量与尺寸监控系统
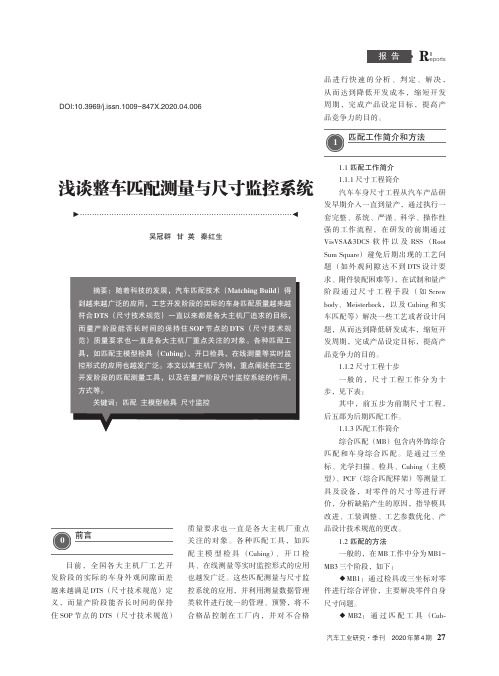
Reports汽车工业研究·季刊2020年第4期浅谈整车匹配测量与尺寸监控系统▶◀……………………………………………………………………………吴冠群甘英秦红生前言目前,全国各大主机厂工艺开发阶段的实际的车身外观间隙面差越来越满足DTS (尺寸技术规范)定义,而量产阶段能否长时间的保持住SOP 节点的DTS (尺寸技术规范)质量要求也一直是各大主机厂重点关注的对象。
各种匹配工具,如匹配主模型检具(Cubing )、开口检具、在线测量等实时监控形式的应用也越发广泛。
这些匹配测量与尺寸监控系统的应用,并利用测量数据管理类软件进行统一的管理、预警,将不合格品控制在工厂内,并对不合格品进行快速的分析、判定、解决,从而达到降低开发成本,缩短开发周期,完成产品设定目标,提高产品竞争力的目的。
匹配工作简介和方法1.1匹配工作简介1.1.1尺寸工程简介汽车车身尺寸工程从汽车产品研发早期介入一直到量产,通过执行一套完整、系统、严谨、科学、操作性强的工作流程,在研发的前期通过VisVSA&3DCS 软件以及RSS (Root Sum Square )避免后期出现的工艺问题(如外观间隙达不到DTS 设计要求、附件装配困难等),在试制和量产阶段通过尺寸工程手段(如Screw body 、Meisterbock ,以及Cubing 和实车匹配等)解决一些工艺或者设计问题,从而达到降低研发成本,缩短开发周期,完成产品设定目标,提高产品竞争力的目的。
1.1.2尺寸工程十步一般的,尺寸工程工作分为十步,见下表:其中,前五步为前期尺寸工程,后五部为后期匹配工作。
1.1.3匹配工作简介综合匹配(MB )包含内外饰综合匹配和车身综合匹配。
是通过三坐标、光学扫描、检具、Cubing (主模型)、PCF (综合匹配样架)等测量工具及设备,对零件的尺寸等进行评价,分析缺陷产生的原因,指导模具改进、工装调整、工艺参数优化、产品设计技术规范的更改。
基于机器视觉的车辆几何尺寸测量系统研究共3篇
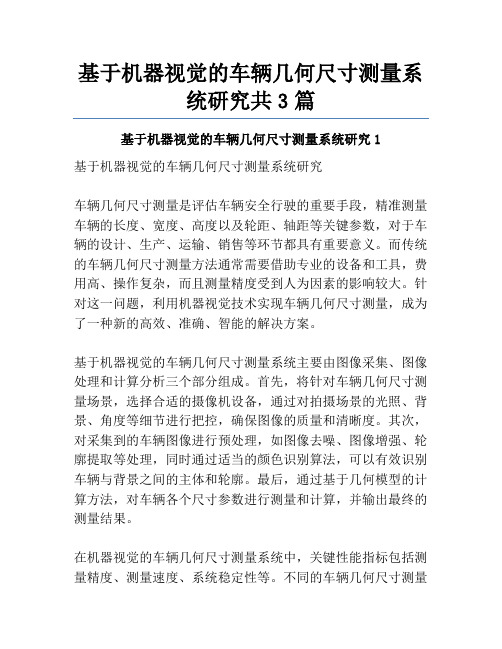
基于机器视觉的车辆几何尺寸测量系统研究共3篇基于机器视觉的车辆几何尺寸测量系统研究1基于机器视觉的车辆几何尺寸测量系统研究车辆几何尺寸测量是评估车辆安全行驶的重要手段,精准测量车辆的长度、宽度、高度以及轮距、轴距等关键参数,对于车辆的设计、生产、运输、销售等环节都具有重要意义。
而传统的车辆几何尺寸测量方法通常需要借助专业的设备和工具,费用高、操作复杂,而且测量精度受到人为因素的影响较大。
针对这一问题,利用机器视觉技术实现车辆几何尺寸测量,成为了一种新的高效、准确、智能的解决方案。
基于机器视觉的车辆几何尺寸测量系统主要由图像采集、图像处理和计算分析三个部分组成。
首先,将针对车辆几何尺寸测量场景,选择合适的摄像机设备,通过对拍摄场景的光照、背景、角度等细节进行把控,确保图像的质量和清晰度。
其次,对采集到的车辆图像进行预处理,如图像去噪、图像增强、轮廓提取等处理,同时通过适当的颜色识别算法,可以有效识别车辆与背景之间的主体和轮廓。
最后,通过基于几何模型的计算方法,对车辆各个尺寸参数进行测量和计算,并输出最终的测量结果。
在机器视觉的车辆几何尺寸测量系统中,关键性能指标包括测量精度、测量速度、系统稳定性等。
不同的车辆几何尺寸测量任务所面临的场景、车型、尺寸、速度等因素不同,需要对机器视觉算法、硬件设备进行不同的优化和调整。
例如,在低光、复杂背景的环境下需要使用更高灵敏度的摄像机设备、更有效的图像处理算法,而高速公路上的车辆几何尺寸监测则需要快速响应、高帧率的摄像机设备和算法。
在实际应用中,基于机器视觉的车辆几何尺寸测量系统已经被广泛应用于停车场管理、交通监控、场馆管理、公安安保等领域。
例如,停车场管理人员可以通过该系统实现自助停车位置查找和车位的分配管理;公安交通管理人员可以通过该系统快速有效地识别并记录车辆的违法停放情况;场馆管理人员可以通过该系统准确统计车辆通行数目和通行时间,优化场内停车位分配和流量控制等。
三坐标测量技术在汽车车身检测中的应用
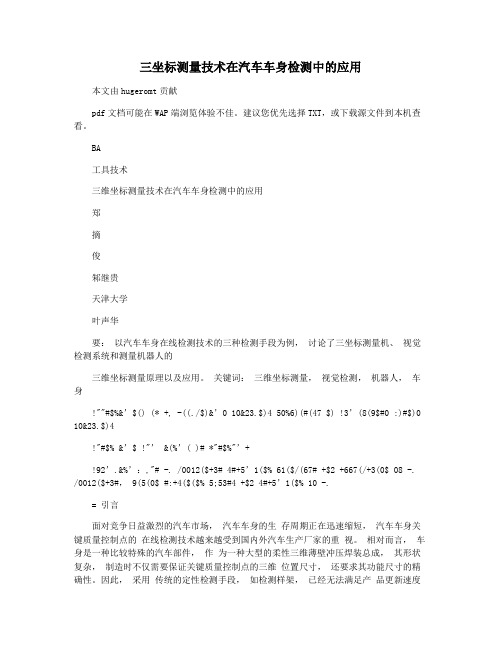
三坐标测量技术在汽车车身检测中的应用本文由hugeromt贡献pdf文档可能在WAP端浏览体验不佳。
建议您优先选择TXT,或下载源文件到本机查看。
BA工具技术三维坐标测量技术在汽车车身检测中的应用郑摘俊邾继贵天津大学叶声华要:以汽车车身在线检测技术的三种检测手段为例,讨论了三坐标测量机、视觉检测系统和测量机器人的三维坐标测量原理以及应用。
关键词:三维坐标测量,视觉检测,机器人,车身!""#$%&’$() (* +, -((./$)&’0 10&23.$)4 50%6)(#(47 $) !3’(8(9$#0 :)#$)0 10&23.$)4!"#$% &’$ !"’ &(%’( )# *"#$%"’+!92’.&%’:,"# -. /0012($+3# 4#+5’1($% 61($/(67# +$2 +667(/+3(0$ 08 -. /0012($+3#, 9(5(0$ #:+4($($% 5;53#4 +$2 4#+5’1($% 10 -.= 引言面对竞争日益激烈的汽车市场,汽车车身的生存周期正在迅速缩短,汽车车身关键质量控制点的在线检测技术越来越受到国内外汽车生产厂家的重视。
相对而言,车身是一种比较特殊的汽车部件,作为一种大型的柔性三维薄壁冲压焊装总成,其形状复杂,制造时不仅需要保证关键质量控制点的三维位置尺寸,还要求其功能尺寸的精确性。
因此,采用传统的定性检测手段,如检测样架,已经无法满足产品更新速度和产品质量的要求,现已有逐渐被淘汰的趋势。
近年来国内外汽车行业出现并采用的检测手段主要有:三坐标测量机、经纬仪、激光跟踪仪、以及测量机器人、三维激光视觉检测系统等,其中三坐标测量机、测量机器人和三维激光视觉检测系统应用最为广泛,在国外已经成功应用于车身生产线上,下面就各自的测量原理以及在车身生产线中的应用情况分别加以探讨。
基于机器视觉技术的白车身尺寸在线测量场景研究与应用
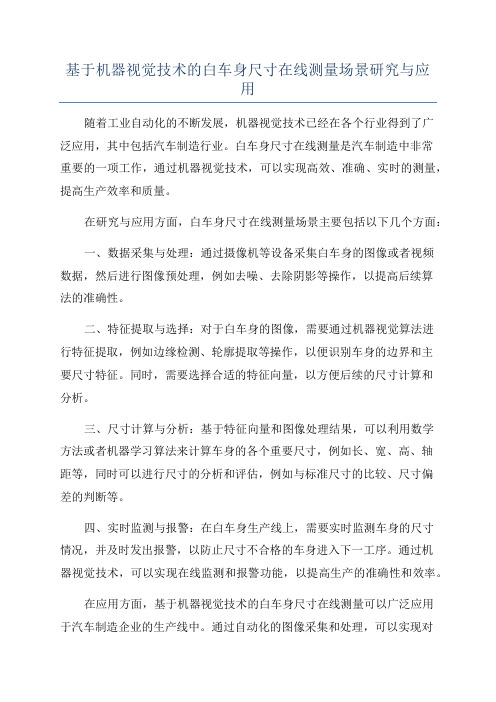
基于机器视觉技术的白车身尺寸在线测量场景研究与应用随着工业自动化的不断发展,机器视觉技术已经在各个行业得到了广泛应用,其中包括汽车制造行业。
白车身尺寸在线测量是汽车制造中非常重要的一项工作,通过机器视觉技术,可以实现高效、准确、实时的测量,提高生产效率和质量。
在研究与应用方面,白车身尺寸在线测量场景主要包括以下几个方面:一、数据采集与处理:通过摄像机等设备采集白车身的图像或者视频数据,然后进行图像预处理,例如去噪、去除阴影等操作,以提高后续算法的准确性。
二、特征提取与选择:对于白车身的图像,需要通过机器视觉算法进行特征提取,例如边缘检测、轮廓提取等操作,以便识别车身的边界和主要尺寸特征。
同时,需要选择合适的特征向量,以方便后续的尺寸计算和分析。
三、尺寸计算与分析:基于特征向量和图像处理结果,可以利用数学方法或者机器学习算法来计算车身的各个重要尺寸,例如长、宽、高、轴距等,同时可以进行尺寸的分析和评估,例如与标准尺寸的比较、尺寸偏差的判断等。
四、实时监测与报警:在白车身生产线上,需要实时监测车身的尺寸情况,并及时发出报警,以防止尺寸不合格的车身进入下一工序。
通过机器视觉技术,可以实现在线监测和报警功能,以提高生产的准确性和效率。
在应用方面,基于机器视觉技术的白车身尺寸在线测量可以广泛应用于汽车制造企业的生产线中。
通过自动化的图像采集和处理,可以实现对白车身尺寸的准确测量,避免了传统人工测量中的误差和主观因素。
同时,基于机器学习算法的尺寸计算和分析,可以提供更加细致和全面的尺寸数据,以供企业进行生产管理和质量控制。
总之,基于机器视觉技术的白车身尺寸在线测量场景的研究与应用,不仅可以提高汽车制造的生产效率和质量,还能够减少人力资源的投入和成本的浪费,具有非常广阔的应用前景和市场需求。
未来随着技术的不断发展和创新,机器视觉技术在汽车制造领域的应用还将继续深入和拓展。
一种车辆轮廓尺寸参数全自动测量系统

意 测 量 车 体 表 面两 点 距 离 . 系统 的 构成 如 图 12所 示 其 中 图 1 示 的 测 量 装 置 的 正 视 图 .图 2为 侧 视 所 图。图中设备分别 为 :、 量 支架 ; 、 电开 关 ;、 1测 2光 3 摄
备和测量装 置等设备
作 者 简 介 : 晓 昀 (9 8 ) 男 , 士 , 师 , 何 17 一 , 硕 讲 系统 分析 师 , 事 领 域 为计 算机 系 统 设 计 、 从 图像 处理 方 面教 学 与研 究
。 现 计 代 算机 21. 016 0
0 引
言
了纠 纷 . 响 了政 府 部 门执 法 的公 开性 和 公 正 性 影 为 了解 决 上 述 问题 .近 年 来 也 出 现 了一 些 测 量 车 辆 尺 寸 的 装 置 , 如 : 光 三 维 扫 描 仪 , 种 基 于 激 光 例 激 这
随 着 国 民社 会 经 济 的 发 展 .带 动 汽 车 行 业 迅 猛 发
用, 自动动态测量 车长 、 车宽 、 高 、 车 轴数 、 轮距 、 距 以 轴 及车身任意位 置距 离等参数 的全 自动测量 系统 该系
统 通 过 图 片 拼 接 技 术 和 传 感 器 技 术 获 取 带 有 标 尺 的 车
率低 、 成本高 、 准确性 不高 , 检测 过程 中也不 可避 免会
置 ; 、 距 测 量 雷 达 。另 外 还 包 括 计 算 机 、 线 传 输 设 7轮 无
工测量无法 对测量 的过程 和结果进行保存 .一 旦车 主
基于计算机视觉的汽车整车尺寸测量系统的研究

基于计算机视觉的汽车整车尺寸测量系统的研究一、本文概述随着汽车工业的飞速发展,汽车整车尺寸测量成为汽车制造过程中的重要环节。
传统的汽车尺寸测量方法大多依赖于人工操作,不仅效率低下,而且容易受到人为因素的影响,导致测量精度不稳定。
开发一种基于计算机视觉的汽车整车尺寸测量系统具有重要的现实意义和应用价值。
本文旨在研究基于计算机视觉的汽车整车尺寸测量系统,通过计算机视觉技术实现对汽车整车尺寸的自动、快速、精确测量。
本文首先介绍了汽车尺寸测量的背景和意义,分析了传统测量方法的不足和计算机视觉技术在汽车尺寸测量中的优势。
随后,详细阐述了基于计算机视觉的汽车整车尺寸测量系统的基本原理、系统架构和关键技术。
在基本原理方面,本文介绍了计算机视觉的基本原理和关键技术,包括图像采集、图像处理、特征提取和尺寸计算等。
在系统架构方面,本文设计了基于计算机视觉的汽车整车尺寸测量系统的整体架构,包括硬件平台和软件平台。
在关键技术方面,本文重点研究了图像预处理、边缘检测、特征匹配和三维重建等关键技术,以提高测量精度和效率。
本文通过实验验证了基于计算机视觉的汽车整车尺寸测量系统的可行性和有效性,并对实验结果进行了分析和讨论。
实验结果表明,该系统具有较高的测量精度和稳定性,能够满足汽车制造过程中对尺寸测量的要求。
同时,本文还指出了研究中存在的不足之处,并对未来的研究方向进行了展望。
通过本文的研究,旨在为汽车整车尺寸测量提供一种高效、精确、自动化的解决方案,推动汽车制造业的智能化发展。
二、系统设计与技术原理本节将详细介绍基于计算机视觉的汽车整车尺寸测量系统的设计和技术原理。
该系统设计分为几个关键部分:图像采集、预处理、特征提取、尺寸计算和结果输出。
每个部分都依赖于先进的技术和算法,以确保测量结果的准确性和系统的稳定性。
图像采集是整个系统的第一步,其质量直接影响到后续处理和最终测量结果的准确性。
本系统采用高分辨率工业相机,配合适当的照明系统,确保在各种环境下都能获得高质量的汽车图像。
车身三维尺寸视觉检测系统

车身三维尺寸视觉检测系统班级:自动化4班姓名:马晓明学号:30112031501.引言随着车辆在中国的普及,越来越多的家庭会拥有属于自己的轿车,但是车辆事故也不可避免的随之而来。
很多车主在发生一些小事故后会很自然的开去修理厂进行修理,但是目前中国大多数的修理厂只会进行一些简单的人工测量与修理,并不能对车辆进行科学,精准的测量与评估,因此会导致很多二次事故。
车辆发生事故后,如果采用简单的人工测量和修理,车辆在以后使用中还可能出现跑偏,共振,轮胎非正常磨损等故障,造成严重的生命财产损失。
但是如果我们采用车身三维尺寸视觉检测系统就可避免这些后续事故。
不仅如此,该视觉检测系统同样可以用于汽车生产现场,检测出场汽车是否满足质量要求。
这一技术的应用不仅能快速检测大量汽车样品,而且能节约很多人力,降低生产成本。
2.车身三维尺寸视觉检测原理典型的车身三维尺寸视觉检测系统原理如图所示。
该系统包括多个视觉传感器,全局校准,现场控制,测量软件等几部分。
每个视觉传感器是一个测量单元,对应车身上的一个被测点,系统组建时,所有的传感器均已统一到基准坐标系下( 即系统全局校准) ,传感器由系统中的计算机控制。
测量时,每个传感器测量相应点的三维坐标,并转换到基准坐标系中,全部传感器给出车身所有被测点的测量结果,完成系统测量任务。
3. 视觉检测系统步骤(1)图像获取双台相机获取:可有不同位置关系(2)相机标定确定空间坐标系中物体点同它在图像平面上像点之间的对应关系。
a)内部参数:相机内部几何、光学参数b)外部参数:相机坐标系与世界坐标系的转换(3)图像预处理和特征提取预处理:主要包括图像对比度的增强、随机噪声的去除、滤波和图像的增强、伪彩色处理等;特征提取:常用的匹配特征主要有点状特征、线状特征和区域特征等(4)立体匹配:根据对所选特征的计算,建立特征之间的对应关系,将同一个空间物理点在不同图像中的映像点对应起来。
立体匹配有三个基本的步骤组成:a)从立体图像对中的一幅图像如左图上选择与实际物理结构相应的图像特征;b)在另一幅图像如右图中确定出同一物理结构的对应图像特征;c)确定这两个特征之间的相对位置,得到视差。
车身三坐标测量技术

总结:车身三坐标测量技术的重要性和应用前景
车身三坐标测量技术的重要性 * 提高车身制造精度和产品质 量 * 降低生产成本和减少废品率 * 提升企业竞争力
* 提高车身制造业竞争力
车身三坐标测量技术的应用前景 * 未来将广泛应用于汽车制造领域 * 促进汽车行业的技术创新和发展 * 提高汽车产品的安全性和舒适性
三坐标测量系统组成:包括测量机、 测头、控制系统、测量软件等
三坐标测量原理
三坐标测量特点:高精度、高效率、 高可靠性
添加标题
添加标题
添加标题
添加标题
三坐标测量原理:通过测头接触被 测工件表面,获取三维坐标信息, 进而进行数据处理和分析
三坐标测量应用:汽车制造、航空 航天、模具制造等领域
测量误差来源及控制方法
,a click to unlimited possibilities
汇报人:
目录
定义与作用
定义:车身三坐标测量技术是一种通过测量车身各点在三维空间中的坐标位置,从而对车身进行精确测量和评价的技术。
作用:车身三坐标测量技术是汽车制造过程中不可或缺的环节,它能够提高车身制造的精度和质量,保证车身的几何尺寸和形状符合设计要求, 同时也有助于发现和解决车身制造过程中出现的问题。
数据分析与结果:对测量数据进行详细的分析,包括数据的准确性、可靠性等,并给出最终 的测量结果
结论与展望:总结该案例的测量结果,并探讨未来可能的应用和改进方向
案例二:某车型装配精度检测案例
案例背景:某车型在装配过程中出 现精度问题,需要进行三坐标测量 技术检测。
数据分析:对测量数据进行处理和 分析,找出装配精度问题所在,为 后续改进提供依据。
可重复性好:三坐标测量技术可以重复进行测量,保证测量结果的稳定性和可靠性。
基于机器视觉的零件尺寸检测系统设计与实现
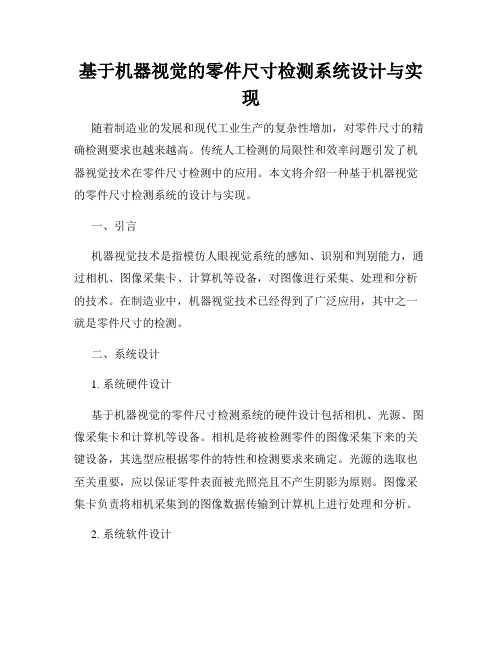
基于机器视觉的零件尺寸检测系统设计与实现随着制造业的发展和现代工业生产的复杂性增加,对零件尺寸的精确检测要求也越来越高。
传统人工检测的局限性和效率问题引发了机器视觉技术在零件尺寸检测中的应用。
本文将介绍一种基于机器视觉的零件尺寸检测系统的设计与实现。
一、引言机器视觉技术是指模仿人眼视觉系统的感知、识别和判别能力,通过相机、图像采集卡、计算机等设备,对图像进行采集、处理和分析的技术。
在制造业中,机器视觉技术已经得到了广泛应用,其中之一就是零件尺寸的检测。
二、系统设计1. 系统硬件设计基于机器视觉的零件尺寸检测系统的硬件设计包括相机、光源、图像采集卡和计算机等设备。
相机是将被检测零件的图像采集下来的关键设备,其选型应根据零件的特性和检测要求来确定。
光源的选取也至关重要,应以保证零件表面被光照亮且不产生阴影为原则。
图像采集卡负责将相机采集到的图像数据传输到计算机上进行处理和分析。
2. 系统软件设计基于机器视觉的零件尺寸检测系统的软件设计通常包括图像预处理、特征提取和尺寸计算三个主要步骤。
图像预处理是对采集到的图像进行噪声去除、平滑处理和图像增强等操作,以提高后续处理的准确性和稳定性。
特征提取是基于处理后的图像,通过算法提取图像中与零件尺寸相关的特征信息,如边缘、角点等。
常用的特征提取算法有Canny算法、Sobel算法等。
尺寸计算是根据所提取到的特征信息,结合已知的标定参数和尺寸测量原理,进行尺寸计算并给出结果。
常用的尺寸计算方法有比例尺寸计算法、基于几何关系的尺寸计算法等。
三、系统实现1. 硬件搭建在系统实现过程中,首先需要根据硬件设计的要求,搭建相应的硬件平台,包括安装相机、配置光源、连接图像采集卡和计算机等设备。
确保硬件设备的稳定性和可靠性。
2. 软件开发基于机器视觉的零件尺寸检测系统的软件开发需要根据所选用的开发平台和编程语言进行。
可以选择常见的开发平台,如OpenCV、MATLAB等,以及常用的编程语言,如C++、Python等。
基于机器视觉的零件尺寸检测与测量系统设计

基于机器视觉的零件尺寸检测与测量系统设计随着工业生产的发展,对零件的质量与精度要求越来越高,而传统的人工尺寸检测与测量方法已经无法满足这些要求。
因此,基于机器视觉的零件尺寸检测与测量系统应运而生。
本文将针对这一问题进行探讨。
一、介绍机器视觉技术是一门利用计算机视觉进行模式识别、目标检测和三维重建等方面的技术。
基于机器视觉的零件尺寸检测与测量系统利用计算机视觉技术,可以实现对零件尺寸的高精度检测与测量。
二、系统设计1. 摄像设备选择在设计基于机器视觉的零件尺寸检测与测量系统时,首先需要选择合适的摄像设备。
一般来说,高分辨率的摄像头能够提供更精确的检测结果。
2. 图像采集与处理图像采集是系统中的核心环节之一,通过摄像设备采集零件的图像,并对图像进行处理,提取出需要检测的特征。
图像处理算法可以采用边缘检测、二值化、滤波等方法,以提高图像的清晰度和信噪比。
3. 特征提取与分析在图像处理的基础上,需要进一步提取出零件的特征信息。
可以通过边缘检测算法提取零件的轮廓信息,或者利用模板匹配的方法提取出关键特征点。
4. 尺寸计算与结果输出根据零件的特征信息,结合相应的几何测量原理,可以计算出零件的尺寸参数。
一般来说,可以计算出零件的长、宽、高等尺寸参数,以及一些特殊形状的测量参数。
三、系统优势基于机器视觉的零件尺寸检测与测量系统相比传统的人工测量方法具有以下优势:1. 精度高:机器视觉系统可以实现对零件尺寸的高精度测量,减少了人为因素对测量结果的影响。
2. 自动化程度高:系统可以实现对多个零件的自动化测量,减少了人工测量的工作量,提高了工作效率。
3. 可靠性好:机器视觉系统的测量结果可靠性高,可以避免人工测量过程中的主观误差。
4. 数据可视化:测量结果可以通过电脑显示进行直观展示与分析,方便人们对零件质量进行评估。
四、应用领域基于机器视觉的零件尺寸检测与测量系统在很多领域都有广泛的应用,例如汽车制造、航空航天、电子电气等行业。
高精度的车身检具——三坐标测量机

所 以在 车身 等大型 焊接 件 的检 测及测
量 应 用 中 , 传 统 检 具 已 渐 渐 失 去 主 导
地位 ,取 而代之 的 是高 精度 的三坐 标
测量机 。
三 坐标 测 量机 在 车身 检 测 中的
应 用
三 坐 标 测 量 机 是 通 过 探 头 系 统 与 工 件 的 相 对 移 动 ,来 探 测 工 件 表 面 点 三 维 坐 标 的 测 量 系 统 。 除 测 量 机 主 体
B a o NT既 可 安 装 于地 表 以 下也 可 安 r v
装 于地面 上 ,配 有温 度传 感器 使控制
系统 能够 检测 并 动态地 补 偿温 度梯度 引起 的测量系统 的变形 。
活动桥式测量机
如 Bo rwn& S ap 集 团 的 Go a测 h re lbl
图 1 用于 生产 线 上的 双水 平 臂测 量机 图2 GL AL桥式测量机 OB
及 其 组 成 的 各 种 零 部 件 大 多 为 -金 件 , 取 多种 方式 ;以划 线方 式检 查工 件 的 三 坐标测 量机 已使 用在 生产 线上 ,而
工件 的刚性 一般 较差 ,且 车 身表 面上 轮 廓 ,情况与检查孔相似 ;待测零件需 不 是 使 用 在 远 离 现 场 的 测 量 问 内 。 在 的各种孔 和 相对 尺寸 受地 球 引力的 影 要 夹 紧 。 响 而处于 变形 状态 ,若 使 用传统 的测 冲压 件生产 车 间 中 ,采 用三 坐标 测量
之 二 。 用 于 生 产 过 程 中 检 测 的 三 坐 标 头增 加了两个 回转 坐标 ,并可以使用加 架 较 传 统 设 计 刚性 提 高 2 % ,x向 导轨 5 0 mm,这 种 形 式 的结 重 心 降 低 5 测 量 系 统 事 实 上 已 成 为 工 艺 过 程 的 一 长杆 ,最 长 可达 8 0 0%从 而 保 证 了 平 稳 、精 确 个组 成部分 。 构能 使 测 头 易 于 进 入 工 件 的 各 个 被 测 部 的 运动 ;移 动 桥 上 轴 承 跨 距 更 宽 ,降低 位 ,包 括 车 身 骨 架 的 内 部 区 域或 各 种 I 了 由于 桥 架 自 转 而 引 起 的 误 差 , 从 而
车体360度动态图像检测系统

技术与应用TECHNOLOGY AND APPLICATION车体360度动态图像检测系统◎郭其昌 梅劲松近年来,我国城市轨道交通行业快速发展,地铁客流量不断高升,地铁车辆的运行安全压力也越来越大,由于地铁长期运行受到风吹日晒雨淋刮擦等容易造成车侧身污损、车底部件异常损伤变形脱落等问题,长期以往有可能会给运营造成安全事故,影响到正常的运营。
国内第一套视觉车辆检测系统于2006年问世,其技术发展包括采用1394接口摄像结合氙气灯成像、网口面阵相机结合频闪灯成像、线阵相机结合线激光、线面结合三维成像,技术的创新改变了传统作业模式,使用至今为保障列车运行安全发挥了重大作用,也减轻了检车作业员检车强度,但系统依然存在以下问题:户外强光照射下,传统激光三角法三维成像受阳光干扰影响大;传统三维成像采用线面结合方式,由于2个相机位置不同,其所成像无法实现任意点完全重叠,导致细小部件定位不准识别准确率不高。
车体360度图像检测系统利用数字图像处理技术与自动控制技术相结合,车顶及车体两侧检测单元安装在龙门架及两侧的立杆上,车下走行部检测单元需要在整体道床内布置的底沉箱中安装,利用轨边三维图像检测装置采集运行车辆车顶、走行部、制动部件、底架悬吊件、钩缓连接、受电弓等可视部位三维图像,采用图像自动识别技术,对图像进行自动异常分析和分级预警。
系统利用图像传输与处理加速器技术,在占用较低网络带宽条件下将异常报警信息及大容量图像数据实时传输至本地或异地车辆检测所内报警终端,人工仅需对异常报警信息进行人工确认,系统实现了对车辆在线运行部件状态的监控,提高了故障产生初期的预警能力和联网追踪能力。
系统组成单元地铁车底车侧图像检测系统按照现场设备布局可分为轨边基本检测单元、现场控制中心、远程控制中心三部分组成。
基本检测单元(1)传感器及综合控制器组成:进离线光电开关、测速磁钢、相机触发光电开关和综合控制器;功能:进离线光电开关获得地铁列车进线和离线信号通过综合控制器控制系统工作和停止;测速磁钢获得地铁列车方向、速度、轴数、列车辆数控制检测相机和光源进行采集。
车身三维扫描成像系统技术参数

1.设备名称:车身三维扫描成像系统
2.设备清单及技术参数要求
设备名称
数量
主要技术参数及要求
使用范围
汽车车身扫描系统硬件
1台套
Байду номын сангаас参数:
(1)结构形式:采用无需机械辅助的自定位的CCD和激光束相结合的手持式扫描结构。
(2)激光等级:II级或以上
(3)扫描速度:≥480,000 次测量/秒;
(3)车身内部骨架及结构的测量
(4)汽车其他零部件的测量
配套软件
1套
配套扫描软件要求:
(1)可实现扫描系统的自定位;
(2)实时扫描时能实现实时动态拼接显示;
(3)扫描数据可以以点云模式及三角网格面数据两种模式直接显示;
(4)点云分辨率可以在扫描前设置,也可以在扫描后设置,确保获得合理密度的点云数据;
(5)数据文件以STL,Igs,等格式输出,兼容Catia V5、UGS、PRO-E、Imageware、Rapidform,3dmax,maya等软件,具备扫描表面、点云、目标点等多种扫描模式;
(6)可以单独获取和保存工件上定位目标点位置坐标,以便实现装配扫描和组合扫描功能。
(4)扫描景深不小于25cm;
(5)扫描精度:不低于0.03mmISO:0.02+0.06mm/m;
要求:
(1)支持动态扫描;
(2)支持组合装配或拆解扫描;
(3)能实现工件的正反面及内外扫描;
(4)正反面扫描时能实现自动的数据拼接,无需通过后期软件进行拼接。
(1)车身外表面的测量
(2)车身可拆卸零部件的测量
- 1、下载文档前请自行甄别文档内容的完整性,平台不提供额外的编辑、内容补充、找答案等附加服务。
- 2、"仅部分预览"的文档,不可在线预览部分如存在完整性等问题,可反馈申请退款(可完整预览的文档不适用该条件!)。
- 3、如文档侵犯您的权益,请联系客服反馈,我们会尽快为您处理(人工客服工作时间:9:00-18:30)。
车身三维尺寸视觉检测系统
班级:自动化4班姓名:马晓明学号:3011203150
1.引言
随着车辆在中国的普及,越来越多的家庭会拥有属于自己的轿车,但是车辆事故也不可避免的随之而来。
很多车主在发生一些小事故后会很自然的开去修理厂进行修理,但是目前中国大多数的修理厂只会进行一些简单的人工测量与修理,并不能对车辆进行科学,精准的测量与评估,因此会导致很多二次事故。
车辆发生事故后,如果采用简单的人工测量和修理,车辆在以后使用中还可能出现跑偏,共振,轮胎非正常磨损等故障,造成严重的生命财产损失。
但是如果我们采用车身三维尺寸视觉检测系统就可避免这些后续事故。
不仅如此,该视觉检测系统同样可以用于汽车生产现场,检测出场汽车是否满足质量要求。
这一技术的应用不仅能快速检测大量汽车样品,而且能节约很多人力,降低生产成本。
2.车身三维尺寸视觉检测原理
典型的车身三维尺寸视觉检测系统原理如图所示。
该系统包括多个视觉传感器,全局校准,现场控制,测量软件等几部分。
每个视觉传感器是一个测量单元,对应车身上的一个被测点,系统组建时,所有的传感器均已统一到基准坐标系下( 即系统全局校准) ,传感器由系统中的计算机控制。
测量时,每个传感器测量相应点的三维坐标,
并转换到基准坐标系中,全部传感器给出车身所有被测点的测量结果,完成系统测量任务。
3. 视觉检测系统步骤
(1)图像获取
双台相机获取:可有不同位置关系
(2)相机标定
确定空间坐标系中物体点同它在图像平面上像点之间的对应关系。
a)内部参数:相机内部几何、光学参数
b)外部参数:相机坐标系与世界坐标系的转换
(3)图像预处理和特征提取
预处理:主要包括图像对比度的增强、随机噪声的去除、滤波和
图像的增强、伪彩色处理等;
特征提取:常用的匹配特征主要有点状特征、线状特征和区域特征等
(4)立体匹配:根据对所选特征的计算,建立特征之间的对应关系,将同一个空间物理点在不同图像中的映像点对应起来。
立体匹配有三个基本的步骤组成:a)从立体图像对中的一幅图像如左图上选择与实际物理结构相应的图像特征;b)在另一幅图像如右图中确定出同一物理结构的对应图像特征;c)确定这两个特征之间的相对位置,得到视差。
其中的步骤b)是实现匹配的关键。
(5)深度确定
通过立体匹配得到视差图像之后,便可以确定深度图像,并恢复场景3D信息。
4.视觉传感器
基于双目立体视觉测量原理。
图像由摄像机经图像采集卡进入计算机,经计算机处理得到的图像,提取被测点对应的图像特征在像面上的坐标,由摄像机模型及三角法测量原理可以得到被测点的三维坐标。
双目立体视觉三维测量是基于视差原理①:
其中基线距B=两摄像机的投影中心连线的距离;相机焦距为f 。
设两摄像机在同一时刻观看空间物体的同一特征点(,,)c c c P x y z ,分别在“左眼”和“右眼”上获取了点P 的图像,它们的图像坐标分别为(,)left left left p X Y =,(,)right right right p X Y =。
现两摄像机的图像在同一个平面上,则特征点P 的图像坐标Y 坐标相同,即left right Y Y Y ==,则由三角几何关系得到:
()c left c c right c c c x X f z x B X f z y Y f z ⎧=⎪⎪⎪-=⎨⎪⎪=⎪⎩
则视差为:left right Disparity X X =-。
由此可计算出特征点P 在相机坐标系下的三维坐标为:
left c c c B X x Disparity B Y y Disparity B f z Disparity ⎧=⎪⎪⎪=⎨⎪⎪=⎪⎩
因此,左相机像面上的任意一点只要能在右相机像面上找到对应的匹配点,就可以确定出该点的三维坐标。
这种方法是完全的点对点运算,像面上所有点只要存在相应的匹配点,就可以参与上述运算,从而获取其对应的三维坐标。
5.全局校准
完整的车身三维尺寸视觉检测系统由多达几十个传感器组成,每个传感器均在自身的坐标系(传感器局部坐标系)中进行测量,必须将系统中全部传感器局部坐标系统一到一个全局坐标系(系统基准坐标系)中,才能实现系统功能,这就是全局校准技术②,如图:
采用经纬仪或激光跟踪仪作为中介工具,建立一个中间工具坐标系,将每一个摄像机坐标系以及工件坐标系统一至该中间坐标系下,从而间接地建立摄像机坐标系与工件坐标系之间的转换关系。
因此,通过此一系列的坐标变换,即可获得车身上相应被测点的坐标值。
以第i个摄像机为例,其坐标变换公式可以表示为
:
其中分别为工件坐标系下的齐次坐标及第i 个摄像机
坐标系下所采集到的被测点的齐次坐标,
为两坐标系之间的齐
次坐标变换矩阵,数学模型如下:
其中R(3×3矩阵)和T (3×1矩阵)分别为两坐标系之间的旋转矩阵平移矩阵。
6.系统控制
采用现场总线控制③:,如图:
该方案具有优良的扩展性能,能够在不改变现有系统结构的基础上,对系统进行平滑扩充,且布线规范,线缆需求量小,安全隐患少,标语维护。
系统使用RS-485中继器,可以扩展128个以上传感器。
7.测量软件
为保证系统功能的可靠性和达到设计测量精度,测量软件的设计必须考虑以下几点:a)选择可靠性高的操作系统。
视觉检测以图像处理为基础,涉及到大量算法和用算量,需要消耗大量的计算机资源。
b)设计算法时,应当着重考虑容错性。
图像的精确量化处理和一般的变化(几何变化,线性变化,颜色变化等)不同,常常伴随算法的不稳定,以至于产生很大的测量误差。
c)车身视觉监测系统在现场工作的实时状态应当在软件界面上有充分的体现,以便操作者脱离现场,减轻工作强度。
8.结语
综上所述,车身三维视觉检测不仅能对车辆进行高速在线测量,而且能根据不同车身的结构参数判断是否满足质量要求。
该检测原理原理简单,结构清晰,可以进行大批量的检测。
随着汽车市场的发展,该测量技术具有不可估量的市场前景。
9.参考文献
①周富强.CCD摄像机快速标定技术.光学精密工程,2002(2)
②王植槐等.汽车制造检测技术.北京理工大学出版社,2001(4)
③熊春宝.经纬仪工业测量系统的模型研究.武汉测绘科技大学学报,1998(9)出师表
两汉:诸葛亮
先帝创业未半而中道崩殂,今天下三分,益州疲弊,此诚危急存亡之秋也。
然侍卫之臣不懈于内,忠志之士忘身于外者,盖追先帝之殊遇,欲报之于陛下也。
诚宜开张圣听,以光先帝遗德,恢弘志士之气,不宜妄自菲薄,引喻失义,以塞忠谏之路也。
宫中府中,俱为一体;陟罚臧否,不宜异同。
若有作奸犯科及为忠善者,宜付有司论其刑赏,以昭陛下平明之理;不宜偏私,使内外异法也。
侍中、侍郎郭攸之、费祎、董允等,此皆良实,志虑忠纯,是以先帝简拔以遗陛下:愚以为宫中之事,事无大小,悉以咨之,然后施行,必能裨补阙漏,有所广益。
将军向宠,性行淑均,晓畅军事,试用于昔日,先帝称之曰“能”,是以众议举宠为督:愚以为营中之事,悉以咨之,必能使行阵和睦,优劣得所。
亲贤臣,远小人,此先汉所以兴隆也;亲小人,远贤臣,此后汉所以倾颓也。
先帝在时,每与臣论此事,未尝不叹息痛恨于桓、灵也。
侍中、尚书、长史、参军,此悉贞良死节之臣,愿陛下亲之、信之,则汉室之隆,可计日而待也。
臣本布衣,躬耕于南阳,苟全性命于乱世,不求闻达于诸侯。
先帝不以臣卑鄙,猥自枉屈,三顾臣于草庐之中,咨臣以当世之事,由是感激,遂许先帝以驱驰。
后值倾覆,受任于败军之际,奉命于危难之间,尔来二十有一年矣。
先帝知臣谨慎,故临崩寄臣以大事也。
受命以来,夙夜忧叹,恐托付不效,以伤先帝之明;故五月渡泸,深入不毛。
今南方已定,兵甲已足,当奖率三军,北定中原,庶竭驽钝,攘除奸凶,兴复汉室,还于旧都。
此臣所以报先帝而忠陛下之职分也。
至于斟酌损益,进尽忠言,则攸之、祎、允之任也。
愿陛下托臣以讨贼兴复之效,不效,则治臣之罪,以告先帝之灵。
若无兴德之言,则责攸之、祎、允等之慢,以彰其咎;陛下亦宜自谋,以咨诹善道,察纳雅言,深追先帝遗诏。
臣不胜受恩感激。
今当远离,临表涕零,不知所言。