第二章 薄膜制备的物理方法课件
合集下载
薄膜制备方法
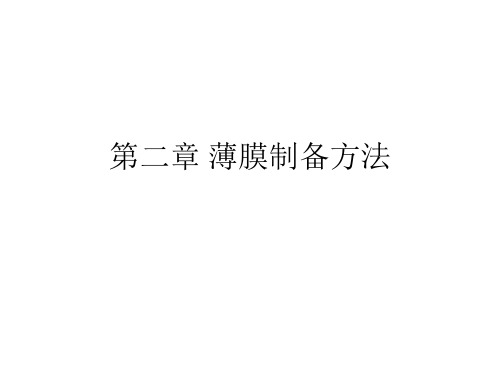
尔质量。
要想制备高纯的薄膜材料,一方面需要改善沉积的真空条件,另一 方面需要提高物质的蒸发以及薄膜的沉积速率。蒸发法可以做到。
真空蒸发装置
电阻式蒸发装置
使用温度高,在高温下的蒸汽压较低, 不与被蒸发物质发生化学反应、无放 气现象或造成其他污染、具有合适的 电阻率。
难熔金属:W,Mo,Ta
应用各种材料,如高熔点氧化物、高 温裂解BN、 石墨、难熔金属等制成 的坩埚也可以作为蒸发容器。 电阻加热,高频感应。
§2.1 真空蒸发镀膜
真空蒸发镀膜(简称真空蒸镀)是在真空室中,加热蒸发容器中欲形成薄膜 的原材料,使其原子或分子从表面气化逸出,形成蒸气流,入射到固体(一般 为衬底或基片)表面,凝结形成固态薄膜的方法。
真空蒸镀法的主要物理过程是通过加热使蒸发材料变成气态,故该法又称 为热蒸发法。
这是1857年首先出Farady采用的最简单的制膜方法,现在巳获得广泛应用。 近年来,该方法的改进主要集中在蒸发源上。 ❖ 为了抑制或避免薄膜原材料与蒸发加热皿发生化学反应,改用耐热陶瓷坩埚,
其它办法
• 使用较多的蒸发物质作为蒸发源,即尽量 减小组元成分的相对变化率。
• 采用向蒸发容器中每次只加入少量被蒸发 物质的方法,使不同的组元能够实现瞬间 的同步蒸发。
• 利用加热至不同温度的双源或多源的方法, 分别控制和调节每一组元的蒸发速率。
瞬间蒸发法
采用这种方法的关键是要求以均 匀的速度将蒸发材料供给蒸发源, 以及选择合适的粉末粒度、蒸发 温度和落下粉尘料的比率。钨丝 锥形筐是用作蒸发源的比较好的 结构。如果使用蒸发舟和坩埚, 瞬间未蒸发的粉体颗粒就会残存 下来,变为普通蒸发。这种蒸发 法已用于各种合金膜(如Ni-Cr合 金膜)、III-V族及II-VI族半导体化 合物薄膜的制备。
要想制备高纯的薄膜材料,一方面需要改善沉积的真空条件,另一 方面需要提高物质的蒸发以及薄膜的沉积速率。蒸发法可以做到。
真空蒸发装置
电阻式蒸发装置
使用温度高,在高温下的蒸汽压较低, 不与被蒸发物质发生化学反应、无放 气现象或造成其他污染、具有合适的 电阻率。
难熔金属:W,Mo,Ta
应用各种材料,如高熔点氧化物、高 温裂解BN、 石墨、难熔金属等制成 的坩埚也可以作为蒸发容器。 电阻加热,高频感应。
§2.1 真空蒸发镀膜
真空蒸发镀膜(简称真空蒸镀)是在真空室中,加热蒸发容器中欲形成薄膜 的原材料,使其原子或分子从表面气化逸出,形成蒸气流,入射到固体(一般 为衬底或基片)表面,凝结形成固态薄膜的方法。
真空蒸镀法的主要物理过程是通过加热使蒸发材料变成气态,故该法又称 为热蒸发法。
这是1857年首先出Farady采用的最简单的制膜方法,现在巳获得广泛应用。 近年来,该方法的改进主要集中在蒸发源上。 ❖ 为了抑制或避免薄膜原材料与蒸发加热皿发生化学反应,改用耐热陶瓷坩埚,
其它办法
• 使用较多的蒸发物质作为蒸发源,即尽量 减小组元成分的相对变化率。
• 采用向蒸发容器中每次只加入少量被蒸发 物质的方法,使不同的组元能够实现瞬间 的同步蒸发。
• 利用加热至不同温度的双源或多源的方法, 分别控制和调节每一组元的蒸发速率。
瞬间蒸发法
采用这种方法的关键是要求以均 匀的速度将蒸发材料供给蒸发源, 以及选择合适的粉末粒度、蒸发 温度和落下粉尘料的比率。钨丝 锥形筐是用作蒸发源的比较好的 结构。如果使用蒸发舟和坩埚, 瞬间未蒸发的粉体颗粒就会残存 下来,变为普通蒸发。这种蒸发 法已用于各种合金膜(如Ni-Cr合 金膜)、III-V族及II-VI族半导体化 合物薄膜的制备。
第二章薄膜的制备ppt课件

在信息显示技术中的应用
在信息存贮技术中的应用
• 第二是在集成电路等电子工业中的应用, 其中,从外延薄膜的生长这一结晶学角 度看也具有显著的成果。
在计算机技术中的应用
在计算机技术中的应用
• 第三是对材料科学的贡献。薄漠制 备是在非平衡状态下进行,和通常的热 力学平衡条件制备材料相比具有:所得 材料的非平衡特征非常明显;可以制取普 通相图中不存在的物质;在低温下可以制 取热力学平衡状态下必须高温才能生成 的物质等优点。
薄膜的主要特性
• 材料薄膜化后,呈现出的一部分主要特性:
•
几何形状效应
• 块状合成材料一般使用粉末的最小尺寸为 纳米至微米,而薄膜是由尺寸为1埃左右的原子
或分子逐渐生长形成的。采用薄膜工艺可以研
制出块材工艺不能获得的物质(如超晶格材料),
在开发新材料方面,薄膜工艺已成为重要的手
段之一。
非热力学平衡过程
无机薄膜制备工艺
• 单晶薄膜、多晶薄膜和非晶态薄膜在现代微 电子工艺、半导体光电技术、太阳能电池、光纤 通讯、超导技术和保护涂层等方面发挥越来越大 的作用。特别是在电子工业领域里占有极其重要 的地位,例如半导体集成电路、电阻器、电容器、 激光器、磁带、磁头都应用薄膜。
• 薄膜制备工艺包括:薄膜制备方法的选择; 基体材料的选择及表面处理;薄膜制备条件的选 择;结构、性能与工艺参数的关系等。
(2)双蒸发源蒸镀——三温度法
三温度-分子束外延法主要是用 于制备单晶半导体化合物薄膜。从 原理上讲,就是双蒸发源蒸镀法。 但也有区别,在制备薄膜时,必须 同时控制基片和两个蒸发源的温度, 所以也称三温度法。
三温度法 是制备化合物 半导体的一种 基本方法,它 实际上是在V族 元素气氛中蒸 镀Ⅲ族元素, 从这个意义上 讲非常类似于 反应蒸镀。图 示就是典型的 三温度法制备 GaAs单晶薄膜 原理。
薄膜物理课件2蒸发源的类型

航空航天等领域。
蒸发源在金属薄膜制备中,通过 控制蒸发速率和温度,可实现均
匀、连续的薄膜生长。
常用的金属蒸发源有铬、铜、镍 等,通过选择合适的蒸发源材料 ,可获得具有优异性能的金属薄
膜。
高温超导薄膜的制备
高温超导薄膜具有零电阻、高磁导率等特性,在电力传输、磁浮交通等 领域具有广阔的应用前景。
高温超导薄膜的制备需要高真空度和高温环境,蒸发源作为重要组成部 分,能够提供稳定的高温蒸发材料。
发材料。
它的优点是简单、可靠且成本低 ,适用于大多数金属和部分非金
属材料的蒸发。
缺点是加热速度慢,难以实现快 速蒸发,且难以控制蒸发的速率
。
电子束蒸发源
电子束蒸发源是利用高能电子束轰击材料表面,使其加热和蒸发。
它的优点是加热速度快,可以获得较高的蒸发速率,且加热区域较小,有利于实现 局部蒸发。
缺点是需要高真空环境,设备成本较高,且对某些材料(如绝缘材料)不适用。
激光诱导蒸发源
激光诱导蒸发源是利用高能激 光束照射材料表面,使其加热 和蒸发。
它的优点是加热速度快,可以 获得较高的蒸发速率,且对材 料的适应性较强。
缺点是需要高真空环境,设备 成本较高,且对某些材料(如 透明材料)的透过率较低。
等离子体辅助蒸发源
等离子体辅助蒸发源是利用等离子体 (高度电离的气体)轰击材料表面, 使其加热和蒸发。
通过优化蒸发源的加热方式和材料选择,可提高高温超导薄膜的结晶质 量和均匀性。
光学薄膜的制备
光学薄膜在光学仪器、显示技术等领域具有重要作用,要求具有高透明度、低反射率等特性 。
蒸发源在光学薄膜制备中,能够实现薄膜的高精度控制和均匀性生长。
通过选择合适的光学材料作为蒸发源,结合精密的控制技术,可获得具有优异光学性能的光 学薄膜。
蒸发源在金属薄膜制备中,通过 控制蒸发速率和温度,可实现均
匀、连续的薄膜生长。
常用的金属蒸发源有铬、铜、镍 等,通过选择合适的蒸发源材料 ,可获得具有优异性能的金属薄
膜。
高温超导薄膜的制备
高温超导薄膜具有零电阻、高磁导率等特性,在电力传输、磁浮交通等 领域具有广阔的应用前景。
高温超导薄膜的制备需要高真空度和高温环境,蒸发源作为重要组成部 分,能够提供稳定的高温蒸发材料。
发材料。
它的优点是简单、可靠且成本低 ,适用于大多数金属和部分非金
属材料的蒸发。
缺点是加热速度慢,难以实现快 速蒸发,且难以控制蒸发的速率
。
电子束蒸发源
电子束蒸发源是利用高能电子束轰击材料表面,使其加热和蒸发。
它的优点是加热速度快,可以获得较高的蒸发速率,且加热区域较小,有利于实现 局部蒸发。
缺点是需要高真空环境,设备成本较高,且对某些材料(如绝缘材料)不适用。
激光诱导蒸发源
激光诱导蒸发源是利用高能激 光束照射材料表面,使其加热 和蒸发。
它的优点是加热速度快,可以 获得较高的蒸发速率,且对材 料的适应性较强。
缺点是需要高真空环境,设备 成本较高,且对某些材料(如 透明材料)的透过率较低。
等离子体辅助蒸发源
等离子体辅助蒸发源是利用等离子体 (高度电离的气体)轰击材料表面, 使其加热和蒸发。
通过优化蒸发源的加热方式和材料选择,可提高高温超导薄膜的结晶质 量和均匀性。
光学薄膜的制备
光学薄膜在光学仪器、显示技术等领域具有重要作用,要求具有高透明度、低反射率等特性 。
蒸发源在光学薄膜制备中,能够实现薄膜的高精度控制和均匀性生长。
通过选择合适的光学材料作为蒸发源,结合精密的控制技术,可获得具有优异光学性能的光 学薄膜。
《材料物理薄膜物理》课件
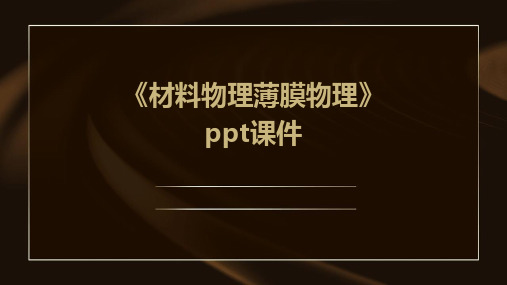
《材料物理薄膜物理》 ppt课件
CONTENTS 目录
• 材料物理与薄膜物理概述 • 材料的基本性质 • 薄膜的制备与生长机制 • 薄膜的物理性能与应用 • 材料与薄膜物理与薄膜物理概述
材料物理的定义与重要性
定义
材料物理是一门研究材料结构、性能和应用的科学,主要关注材料的基本组成 、微观结构和宏观性质之间的关系。
CHAPTER 03
薄膜的制备与生长机制
薄膜的制备方法
01
02
03
物理气相沉积法
利用物理过程将材料蒸发 或溅射到基底上形成薄膜 ,包括真空蒸发、溅射和 离子束沉积等。
化学气相沉积法
通过化学反应将气体转化 为固态薄膜,包括热化学 气相沉积和等离子体增强 化学气相沉积等。
液相外延法
在单晶基底上通过控制温 度和成分,使溶质从溶液 中析出,形成单晶薄膜。
介电性能
薄膜的介电常数和介质损耗是其电学 性能的重要参数,影响其在电子和微 波器件中的应用。
薄膜的磁学性能
磁导率与磁损耗
磁性薄膜的磁导率和磁损耗特性决定了其在磁记录、磁传感 器等领域的应用。
磁各向异性
不同方向的磁化行为,影响磁性薄膜的磁学性能和应用。
薄膜的应用领域
光学仪器制造
高反射、高透过的光学薄膜广 泛应用于各种光学仪器制造。
材料在循环应力作用下抵抗断裂的能力, 与其使用寿命密切相关。
材料的热学性质
热容与热导率
描述材料在温度变化时吸收或释放热量的能 力,以及热量在材料内部的传导速度。
热稳定性
材料在温度变化时保持其物理和化学性质稳 定的能力。
热膨胀
材料在温度升高时体积增大的现象。
热辐射
材料发射或吸收电磁辐射的能力,与温度和 波长有关。
CONTENTS 目录
• 材料物理与薄膜物理概述 • 材料的基本性质 • 薄膜的制备与生长机制 • 薄膜的物理性能与应用 • 材料与薄膜物理与薄膜物理概述
材料物理的定义与重要性
定义
材料物理是一门研究材料结构、性能和应用的科学,主要关注材料的基本组成 、微观结构和宏观性质之间的关系。
CHAPTER 03
薄膜的制备与生长机制
薄膜的制备方法
01
02
03
物理气相沉积法
利用物理过程将材料蒸发 或溅射到基底上形成薄膜 ,包括真空蒸发、溅射和 离子束沉积等。
化学气相沉积法
通过化学反应将气体转化 为固态薄膜,包括热化学 气相沉积和等离子体增强 化学气相沉积等。
液相外延法
在单晶基底上通过控制温 度和成分,使溶质从溶液 中析出,形成单晶薄膜。
介电性能
薄膜的介电常数和介质损耗是其电学 性能的重要参数,影响其在电子和微 波器件中的应用。
薄膜的磁学性能
磁导率与磁损耗
磁性薄膜的磁导率和磁损耗特性决定了其在磁记录、磁传感 器等领域的应用。
磁各向异性
不同方向的磁化行为,影响磁性薄膜的磁学性能和应用。
薄膜的应用领域
光学仪器制造
高反射、高透过的光学薄膜广 泛应用于各种光学仪器制造。
材料在循环应力作用下抵抗断裂的能力, 与其使用寿命密切相关。
材料的热学性质
热容与热导率
描述材料在温度变化时吸收或释放热量的能 力,以及热量在材料内部的传导速度。
热稳定性
材料在温度变化时保持其物理和化学性质稳 定的能力。
热膨胀
材料在温度升高时体积增大的现象。
热辐射
材料发射或吸收电磁辐射的能力,与温度和 波长有关。
《薄膜材料的制备》PPT课件

m为气体分子的质量
www.theme先ga进ller材y.co料m 制L备O技G术O
1.2.1 真空蒸发镀膜
• 蒸发速率 1 m J7.75M 2pPa k/g(m 2s) T 从蒸发源蒸发出来的分子在向基片沉积的过程中,还 不断与真空中的残留气体分子相碰撞,使蒸发分子失去 定向运动的动能,而不能沉积于基片。为保证80-90% 的蒸发元素到达基片,一般要求残留气体的平均自由程 是蒸发源至基片距离的5-10倍。
《薄膜材料的制备》PPT 课件
1 薄膜材料的制备
1.1 薄膜的形成机理 1.2 物理气相沉积 1.3 化学气相沉积 1.4 化学溶液镀膜法 1.5 液相外延制膜法 1.6 膜厚的测量与监控
www.theme先ga进ller材y.co料m 制L备O技G术O
1.1 薄膜的形成机理
薄膜材料在现代科学技术中应用十分广泛,制 膜技术的发展也十分迅速。 制膜方法—分为物理和化学方法两大类; 具体方式上—分为干式、湿式和喷涂三种, 而每种方式又可分成多种方法。
www.theme先ga进ller材y.co料m 制L备O技G术O
1 薄膜材料的制备
1.1 薄膜的形成机理 1.2 物理气相沉积 1.3 化学气相沉积 1.4 化学溶液镀膜法 1.5 液相外延制膜法 1.6 膜厚的测量与监控
www.theme先ga进ller材y.co料m 制L备O技G术O
1.2 物理气相沉积
如果势垒很低,形核率高,形成很多的小聚集体,这时薄 膜的厚度虽然很薄,但它会成为连续的。
• 高的脱附能Ed和低的扩散激活能ES都有利于气相原 子在衬底表面的停留和运动,因而会提高形核率。
www.theme先ga进ller材y.co料m 制L备O技G术O
薄膜材料物理之薄膜的形成ppt(共25页)
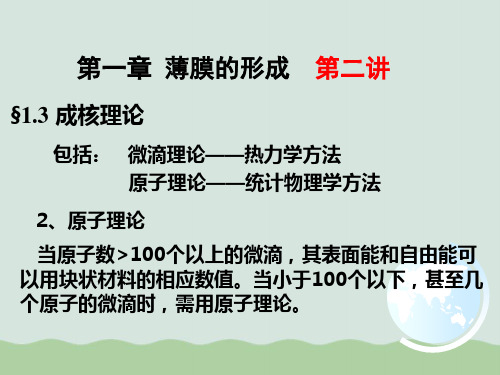
淀 积 速 率 淀 积 的 材 料 量
1、核的饱和密度
初始:每个稳定核(原子对)的捕获面积为:S=m(a
1 n0
)
ma
v p
v1
exp(Epx
/
kT
)
1 v0
exp( EP
/ kT )
是每个吸附原子迁移接触到的吸附点(并成核)
n0 基片单位面积上的吸附点数
1 n0
S ma
S=m(a
1 n0
)
若 有 n个 稳 定 核 , 其 捕 获 面 积 为 : S1nm n0a 显 然 , 单 位 面 积 上 非 捕 获 区 为 : S21S11nm n0a.
初
始
不
完
全
凝
结
区
域
:
在
S
内
2
,
成
稳
定
核
的
成
核
速
率
为
:
dn
d
IS2
物理模型:
临界核
4-7个 原子团
最小稳定核
4-7个 原子团
结合能
临界核和最小 稳定核随基片 温度的变化。
E2
E3= 2E2 E4= 4E2~5E2
E4= 6E2 E5= 8E2
4-7个 原子团
T1
T2
(111)//基片表面 (100)//基片表面
T3
T
当基片表面吸附弱而三个 原子团被吸附的不牢时, 动态平衡却有利于四原子 结构→(100)//基片表面
n (n0 R / v1 )1/2 exp( E Px / 2kT ) T n
1、核的饱和密度
初始:每个稳定核(原子对)的捕获面积为:S=m(a
1 n0
)
ma
v p
v1
exp(Epx
/
kT
)
1 v0
exp( EP
/ kT )
是每个吸附原子迁移接触到的吸附点(并成核)
n0 基片单位面积上的吸附点数
1 n0
S ma
S=m(a
1 n0
)
若 有 n个 稳 定 核 , 其 捕 获 面 积 为 : S1nm n0a 显 然 , 单 位 面 积 上 非 捕 获 区 为 : S21S11nm n0a.
初
始
不
完
全
凝
结
区
域
:
在
S
内
2
,
成
稳
定
核
的
成
核
速
率
为
:
dn
d
IS2
物理模型:
临界核
4-7个 原子团
最小稳定核
4-7个 原子团
结合能
临界核和最小 稳定核随基片 温度的变化。
E2
E3= 2E2 E4= 4E2~5E2
E4= 6E2 E5= 8E2
4-7个 原子团
T1
T2
(111)//基片表面 (100)//基片表面
T3
T
当基片表面吸附弱而三个 原子团被吸附的不牢时, 动态平衡却有利于四原子 结构→(100)//基片表面
n (n0 R / v1 )1/2 exp( E Px / 2kT ) T n
薄膜的制备工艺ppt课件

➢ ⑤制备纳米结构薄膜材料; ➢ ⑥用料省,成本较低。
24
2.3.2溶胶-凝胶方法制备薄膜工艺
有机途径
通过有机金属醇盐的水解与缩聚而形成溶 胶。在该工艺过程中,因涉及水和有机物, 所以通过这种途径制备的薄膜在干燥过程 中容易龟裂(由大量溶剂蒸发而产生的残 余应力所引起)。客观上限制了制备薄膜 的厚度。
① 由单个的 原子、离子、原 子团无规则地入 射到基板表面, 经表面附着、迁 徙、凝结、成核、 核生长等过程而 形成的一薄层固 态物质。
Vacuum Thin Film
Atom
Substrate
3
②夹在两个平行平面间的薄层。
上平面:空气
固体膜、液体膜
下平面:固体表面、液体表面、空气
4
③ 采用特定的制备方法在基板表面上生长得到的 一薄层固态物质 。
只要是气相沉积,其基本过程都包括三个步骤;
提供气相镀料;镀料向所镀制的工件(或基片) 输送;镀料沉积在基片上构成膜层。
17
2.2.1金属有机化学气相沉积MOCVD
又称金属有机气相外延(Metal organic vapor phase epitaxy, MOVPE ),它是利用有机金属热分解进 行气相外延生长的先进技术,目前主要用于化合 物半导体(III-V簇、II-VI簇化合物)薄膜气相
光CVD、热丝CVD
化学镀(CBD)、电镀(ED)、溶胶-凝胶(Sol-
液 Gel)、金属有机物分解(MOD)、液相外 相 延(LPE)、水热法(hydrothermal 法 method)、喷雾热解(spray pyrolysis)、喷
雾水解(spray hydrolysis)、LB膜及自组装
(self-assemble)
24
2.3.2溶胶-凝胶方法制备薄膜工艺
有机途径
通过有机金属醇盐的水解与缩聚而形成溶 胶。在该工艺过程中,因涉及水和有机物, 所以通过这种途径制备的薄膜在干燥过程 中容易龟裂(由大量溶剂蒸发而产生的残 余应力所引起)。客观上限制了制备薄膜 的厚度。
① 由单个的 原子、离子、原 子团无规则地入 射到基板表面, 经表面附着、迁 徙、凝结、成核、 核生长等过程而 形成的一薄层固 态物质。
Vacuum Thin Film
Atom
Substrate
3
②夹在两个平行平面间的薄层。
上平面:空气
固体膜、液体膜
下平面:固体表面、液体表面、空气
4
③ 采用特定的制备方法在基板表面上生长得到的 一薄层固态物质 。
只要是气相沉积,其基本过程都包括三个步骤;
提供气相镀料;镀料向所镀制的工件(或基片) 输送;镀料沉积在基片上构成膜层。
17
2.2.1金属有机化学气相沉积MOCVD
又称金属有机气相外延(Metal organic vapor phase epitaxy, MOVPE ),它是利用有机金属热分解进 行气相外延生长的先进技术,目前主要用于化合 物半导体(III-V簇、II-VI簇化合物)薄膜气相
光CVD、热丝CVD
化学镀(CBD)、电镀(ED)、溶胶-凝胶(Sol-
液 Gel)、金属有机物分解(MOD)、液相外 相 延(LPE)、水热法(hydrothermal 法 method)、喷雾热解(spray pyrolysis)、喷
雾水解(spray hydrolysis)、LB膜及自组装
(self-assemble)
第二章-薄膜制备的物理方法课件(1)
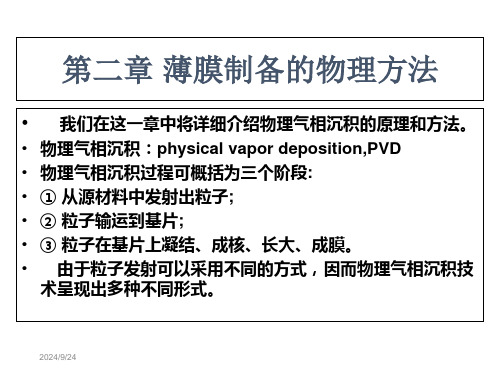
合物时,其组分之间发生反应,其中有些组分以气态或蒸气进
入蒸发空间。
(2)气化原子或分子在蒸发源与基片之间的输运,即这些粒子在
环境气氛中的飞行过程。
飞行过程中与真空室内残余气体分子发生碰撞的次数,取决
于蒸发原子的平均自由程及蒸发源到基片之间的距离,常称源
—基距。
(3)蒸发原子或分子在基片表面上的淀积过程,
即是蒸气凝聚、成核、核生长、形成连续薄膜。由于基板温
度远低于蒸发源温度,因此,沉积物分子在基板表面将直接发
生从气相到固相的相转变。
2024/9/24
6
2.1.2 蒸发热力学
1.饱和蒸汽压
一定温度下,真空室内蒸发物质的蒸气与固
体或液体平衡过程中所表现的压力称为该物质
的饱和蒸气压。
物质的饱和蒸气压随温度的上升而增大,
4. 锥形篮式蒸发源在各圈间隔很小时,其发射特性与平面蒸发
源近似。
5. 坩埚蒸发源可看成表面蒸发源或高度定向的蒸发源。
6. 磁控靶源可看成大面积(平面或圆柱面)蒸发源。
蒸发源的发射特性是比较复杂的问题,为了得到较均匀的膜厚
还必须注意源和基板的配置,或使基板公转加自转等。
2024/9/24
33
6). 热蒸发镀膜的阴影效应
dA
s
c
scos
2
2
M
4
r
4
r
e
2024/9/24
dM
dA
M
s
c
ecos
2
2
dA
4
r
4
r
s
薄膜厚度:
dM s
d
dAs
入蒸发空间。
(2)气化原子或分子在蒸发源与基片之间的输运,即这些粒子在
环境气氛中的飞行过程。
飞行过程中与真空室内残余气体分子发生碰撞的次数,取决
于蒸发原子的平均自由程及蒸发源到基片之间的距离,常称源
—基距。
(3)蒸发原子或分子在基片表面上的淀积过程,
即是蒸气凝聚、成核、核生长、形成连续薄膜。由于基板温
度远低于蒸发源温度,因此,沉积物分子在基板表面将直接发
生从气相到固相的相转变。
2024/9/24
6
2.1.2 蒸发热力学
1.饱和蒸汽压
一定温度下,真空室内蒸发物质的蒸气与固
体或液体平衡过程中所表现的压力称为该物质
的饱和蒸气压。
物质的饱和蒸气压随温度的上升而增大,
4. 锥形篮式蒸发源在各圈间隔很小时,其发射特性与平面蒸发
源近似。
5. 坩埚蒸发源可看成表面蒸发源或高度定向的蒸发源。
6. 磁控靶源可看成大面积(平面或圆柱面)蒸发源。
蒸发源的发射特性是比较复杂的问题,为了得到较均匀的膜厚
还必须注意源和基板的配置,或使基板公转加自转等。
2024/9/24
33
6). 热蒸发镀膜的阴影效应
dA
s
c
scos
2
2
M
4
r
4
r
e
2024/9/24
dM
dA
M
s
c
ecos
2
2
dA
4
r
4
r
s
薄膜厚度:
dM s
d
dAs
薄膜材料制备的PVD法ppt课件
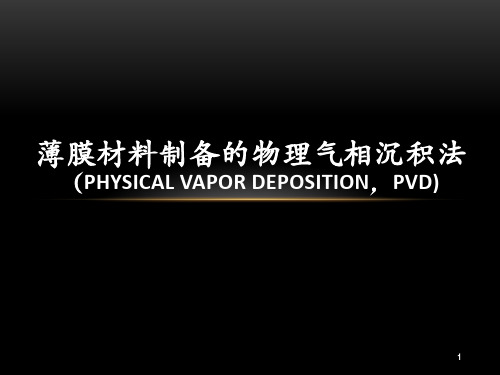
直接蒸发金属,装置无需熔池,原理如图所示。电弧的引燃 依靠引弧阳极与阴极的触发,弧光放电仅仅在靶材表面的一 个或几个密集的弧斑处进行。
特 点:直接从阴极产生等离 子体,不用熔池,阴极靶可 根据工件形状在任意方向布 置,使夹具大为简化。
27
(3)离子束辅助沉积
低能的离子束1用于轰击靶材, 使靶材原子溅射并沉积在基 底上; 离子束2起轰击(注入)作用, 同时,可在室温或近似室温 下合成具有良好性能的 合金、 化合物、特种膜层,以满足 对材料表面改性的需要。
25
(1) 空心阴极离子镀(HCD)
• HCD法利用空心热阴极的弧光放
电产生等离子体(空心钽管为阴 极,辅助阳极)
• 镀料是阳极 • 弧光放电时,电子轰击阳极镀料,
使其熔化而实现蒸镀
• 蒸镀时基片上加负偏压即可从等
离子体中吸引Ar离子向基片轰击, 实现离子镀
26
(2)多弧离子镀 多弧离子镀是采用电弧放电的方法,在固体的阴极靶材上
蒸镀合金膜时,较溅射成分难保证。 镀纯金属时速度快,多用来(90%)制备铝膜。 铝膜的用途广泛,在制镜业代替银,在集成电路
镀铝进行金属化后刻蚀出导线。
12
13
产生:气体放电:电子与气体分子发生碰撞,产生 等离子体 维持:等离子体中的离子与其他气体分子继续碰撞
14
• 过程图
15
• 溅射的过程
7
8
组成合金薄膜的各元素,各自在单独的蒸发源 中加热,蒸发,并按薄膜材料组分比例成膜。
9
例如: 在空气或氧气中
蒸 发 Si 来 制 备 SiO2薄膜; 在氮气气氛中蒸 发 Zr 制 备 ZrN 薄膜;
10
例如: GaAsP半导体薄膜的制备
特 点:直接从阴极产生等离 子体,不用熔池,阴极靶可 根据工件形状在任意方向布 置,使夹具大为简化。
27
(3)离子束辅助沉积
低能的离子束1用于轰击靶材, 使靶材原子溅射并沉积在基 底上; 离子束2起轰击(注入)作用, 同时,可在室温或近似室温 下合成具有良好性能的 合金、 化合物、特种膜层,以满足 对材料表面改性的需要。
25
(1) 空心阴极离子镀(HCD)
• HCD法利用空心热阴极的弧光放
电产生等离子体(空心钽管为阴 极,辅助阳极)
• 镀料是阳极 • 弧光放电时,电子轰击阳极镀料,
使其熔化而实现蒸镀
• 蒸镀时基片上加负偏压即可从等
离子体中吸引Ar离子向基片轰击, 实现离子镀
26
(2)多弧离子镀 多弧离子镀是采用电弧放电的方法,在固体的阴极靶材上
蒸镀合金膜时,较溅射成分难保证。 镀纯金属时速度快,多用来(90%)制备铝膜。 铝膜的用途广泛,在制镜业代替银,在集成电路
镀铝进行金属化后刻蚀出导线。
12
13
产生:气体放电:电子与气体分子发生碰撞,产生 等离子体 维持:等离子体中的离子与其他气体分子继续碰撞
14
• 过程图
15
• 溅射的过程
7
8
组成合金薄膜的各元素,各自在单独的蒸发源 中加热,蒸发,并按薄膜材料组分比例成膜。
9
例如: 在空气或氧气中
蒸 发 Si 来 制 备 SiO2薄膜; 在氮气气氛中蒸 发 Zr 制 备 ZrN 薄膜;
10
例如: GaAsP半导体薄膜的制备
第二章薄膜制备技术修改优秀课件
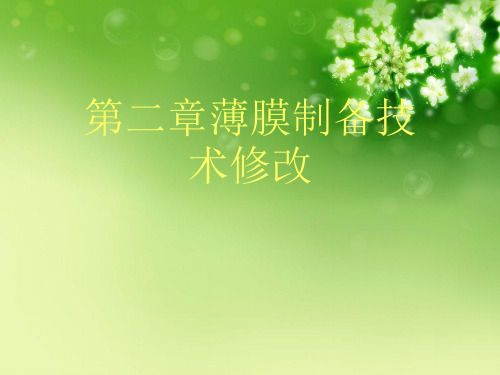
2.1 真空的基本知识
2.1.1 真空的基本概念及特点
真空的含义
在真空科学里所定义的真空是压强“低于一个标准大 气压(101.325kPa)的气体状态”。 真空是一种气体状态(并非一无所有)。所以有人把 真空认为是什么物质也不存在的,即所谓的“绝对真 空”那是错误的。 如在标准状态,即0℃,1标准大气压下每立方厘米有 2.687×1019个气体分子,而在超高真空极限10-11~ 10-12Pa压强下,每立方厘米中仍有33~330个气体分 子,可见“真空”并不真空。
为了研究真空和实际使用方便,常常根据各压 强范围内不同的物理特点,把真空划分为以下 几个区域。
粗真空区域:1×105~1×102Pa (760~1 Torr) 低真空区域:1×102~1×10-1Pa (1~10-3 Torr) 高真空区域:1×10-1~1×10-5Pa (10-3~10-7 Torr) 超高真空区域:<1×10-5Pa (<10-7 Torr)
超高真空 <10-5 Pa <10-7 Torr
气体性质 气体状态与常压相比较,只有分子数目由多变少的变
化,而无气体分子空间特性的变化,分子间相互碰 撞频繁。 气体分子间,分子与器壁间的相互碰撞不相上下,气 体分子密度较小。
分子间相互碰撞极少,分子与器壁间碰撞频繁。气体 分子密度小。
气体分子密度极低与器壁碰撞的次数极少,致使表面 形成单分子层的时间增长。气态空间中只有固体本 身的原子,几乎没有其它原子或分子存在。
2.1.2 真空度测量单位
真空容器中气体分子时刻对器壁进行弹性碰撞,即 产生气体压强。气压的大小在标准状态下与气体分 子密度有关,因此,用测量气体压强的方法来衡量 容器达到真空的程度,称为真空度。
第2章 薄膜的物理制备方法(2)

以磁场来改变电子的运动方向,并束缚和延长电子的运动轨迹,从而提高 了电子对工作气体的电离几率和有效地利用了电子的能量。因此,使正离 子对靶材轰击所引起的靶材溅射更加有效。同时,受正交电磁场束缚的电 子,又只能在其能量要耗尽时才沉积在基片上。这就是磁控溅射具有“低 温”、“高速”两大特点的道理。
6.对向靶溅射
5.磁控溅射 –低温高速溅射
溅射沉积方法缺点:沉积速度低、工作气压较高引起污染。 磁控溅射:提高沉积速率,降低工作气体压力。 磁控溅射中引入了正交电磁场,使离化率提高了5~6%,于是溅射速率可比三极溅射 提高10倍左右。对许多材料,溅射速率达到了电子束蒸发的水平。
二次电子一旦离开靶面,就同时受到电场和磁 场的作用。近似认为,二次电子在阴极暗区只 受电场作用,一旦进入辉光区就只受磁场作用。 (1)阴极暗区:受电场力—直线运动。 (2)辉光区:受磁场力—旋转。 (3)半周后—进入阴极暗区,减速,到靶面时, 降为0. 往复运动。
但:用不同的入射离子溅射同一靶材时,所呈现的溅射率的差异,大大低 于用同一种离子去轰击不同靶材所得到的溅射率的差异。
(4)入射离子的入射角 与溅射率的关系
入射角是指离子入射方向与被溅射靶材表面法线之间的夹角。 不同 入射角θ的溅射率值S(θ),垂直入射时的溅射率值S(0) 。
随入射角增大,溅射率逐渐增大,在0600之间的相对溅射率基本上服从1/cos(θ)
(1)靶材料与溅射率的关系 a.溅射率S 随靶材元素原子序数增加而增大(相同条件, 同一种离子轰击不同元素的靶材料)。 b.晶格结构不同,S不同。 c.与表面清洁度有关,清洁度高,S大。 d.升华热大,S小。
(2)入射离子能量与溅射率的关系
当入射离子能量较小时,溅射率 随入射离子能量的增加而呈指数 上升;
薄膜材料物理之薄膜的形成PPT(25张)
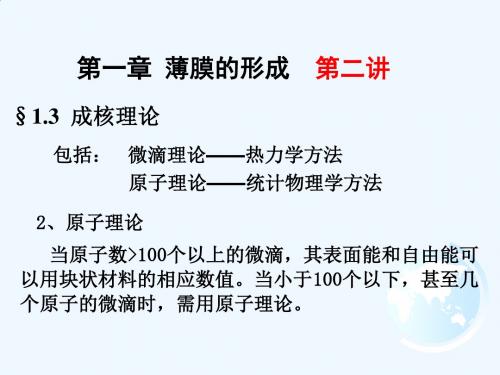
•
2、身材不好就去锻炼,没钱就努力去赚。别把窘境迁怒于别人,唯一可以抱怨的,只是不够努力的自己。
•
3、大概是没有了当初那种毫无顾虑的勇气,才变成现在所谓成熟稳重的样子。
•
4、世界上只有想不通的人,没有走不通的路。将帅的坚强意志,就像城市主要街道汇集点上的方尖碑一样,在军事艺术中占有十分突出的地位。
淀 积 速 率 淀 积 的 材 料 量
1、核的饱和密度
初始:每个稳定核(原子对)的捕获面积为:S=m(a
1 n0
)
ma
v p
v1
exp(Epx
/
kT
)
1 v0
exp( EP
/ kT )
是每个吸附原子迁移接触到的吸附点(并成核)
n0 基片单位面积上的吸附点数
/ kT
)
S
n
,
即在初始完全不凝结的情况下,基片温度升高时,成核数增加.
而在初始完全凝结的情况下,基片温度升高时,
成核数减小(但稳定核线度变大).
证明如下:
n m c n0 , n R c ,
ma P
mc c
v
v1 exp( E Px
/ kT
),
v吸附原子迁移速度
Ii niAV
=n0(vR 0n0)i exp(iEP/kT)exp(Ei /kT)ARa0(vv10)exp[(EP EPX)/kT]
Ra0An0(vR 0n0)i
exp((i1)EPEi EPX kT
)
应用: 改变基片温度,可使临界核从一种原子团过渡到另一种原子团.
因为在转变温度时,两种临界核长成为稳定的速率是相等的. 例如:单原子核双原子核I1I2,求出转变温度T1.
- 1、下载文档前请自行甄别文档内容的完整性,平台不提供额外的编辑、内容补充、找答案等附加服务。
- 2、"仅部分预览"的文档,不可在线预览部分如存在完整性等问题,可反馈申请退款(可完整预览的文档不适用该条件!)。
- 3、如文档侵犯您的权益,请联系客服反馈,我们会尽快为您处理(人工客服工作时间:9:00-18:30)。
第二章 薄膜制备的物理方法
第二章 薄膜制备的物理方法
真空蒸发原理
上述过程都必须在空气非常稀薄的真空环境中进行。否则: • 蒸发物质原子或分子将与大量空气分子碰撞,使膜层受到严重污
染,甚至形成氧化物; • 或者蒸发源被加热氧化烧毁; • 或者由于空气分子的碰撞阻挡,难以形成均匀连续的薄膜。
第二章 薄膜制备的物理方法
沉积速率和膜厚分布
• 在真空蒸发镀膜过程中,能否在基片上获得厚度均匀分布的薄膜, 是制膜的关键。
• 因此,薄膜在基片上的沉积速率以及其膜厚分布是我们十分关心 的问题。
• 基片上不同蒸发位置的膜厚,取决于蒸发源的蒸发特性、基片与 蒸发源的几何形状、相对位置以及蒸发物质的蒸发量。
第二章 薄膜制备的物理方法
• 由于粒子发射可以采用不同的方式,因而物理气相沉积技术呈现 出多种不同形式。
第二章 薄膜制备的物理方法
第二章 薄膜制备的物理方法
• 真空蒸发法 • 溅射法 • 离子镀 • 分子束外延
第二章 薄膜制备的物理方法
真空蒸发原理
• 真空蒸发镀膜法(简称真空蒸镀)是在真空环境 下,加热蒸发源材料,使其原子或分子从表面汽 化逸出,形成蒸汽流,入射到衬底(基片)表面, 凝结形成固态薄膜的方法。
• 假设蒸发膜的密度为 ,dm 则基4m片e 上cro任2s意d一S点的膜厚:
d
me
4
cos
பைடு நூலகம்r2
第二章 薄膜制备的物理方法
沉积速率和膜厚分布
• 基片上的各处膜厚分布状况由下式给出:
d
1
d0 1l/h2 3/2
其中d0是在点源正上方h处的沉积膜厚度。 • 如果蒸发源为一平行于基片的小平面蒸发源,则膜厚分布为:
• 由于真空蒸发法主要物理过程是通过加热蒸发材 料而产生,所以又称热蒸发法。
• 采用这种方法制备薄膜已有几十年的历史,用途 十分广泛。近年来,该方法的主要改进是蒸发源 上。
第二章 薄膜制备的物理方法
第二章 薄膜制备的物理方法
真空蒸发原理
• 真空蒸发镀膜法是应用最广泛的薄膜制备技术,其简单便利、操 作容易、成膜速度快、效率高;但制备的薄膜与基片结合较差, 工艺重复性不好,不容易获得结晶结构的薄膜。
• 如果真空度足够高N , 平N 均0自e由x程足p l/够(大),满足条
件,则被碰撞的分子比率 :
• 对于25℃的空气f,1N/N 0,l则/
• 由此可以看出,为保证0.6镀6 (膜c7 质m )/量P,在f要1求.50lP 时,
若蒸发源与基片距离l=25cm,真空压强P必须f 小0.1于 3×10-3Pa。
蒸发源是蒸发装置的关键部件
• 由于大多数金属材料都要求在1000-2000℃的高温 下蒸发。因此,必须将蒸发材料加热到很高的蒸 发温度。
• 为了避免污染薄膜材料,蒸发源中所用的支撑材 料在工作温度下必须具有可忽略的蒸汽压,以避 免支撑材料原子混入蒸发气体中。
• 通常所用的支撑材料为难熔的金属和氧化物。
d
1
d0 1l /h2 2
第二章 薄膜制备的物理方法
沉积速率和膜厚分布
第二章 薄膜制备的物理方法
第二章 薄膜制备的物理方法
沉积速率和膜厚分布
• 实际蒸发过程中,蒸发粒子都要受到真空室中残 余气体分子的碰撞,碰撞次数取决于分子的平均 自由程。设有N0个蒸发分子,飞行距离l后,未受 到残余气体分子碰撞的数目N为:
• 同时,选择某一特殊支撑材料时,一定要考虑蒸 发物与支撑材料之间可能发生的合金化和化学反 应、相互润湿程度等问题。
• 支撑材料的形状则主要取决于蒸发物。
第二章 薄膜制备的物理方法
第二章 薄膜制备的物理方法
真空蒸发技术
• 电阻加热蒸发法 • 闪烁蒸发法 • 电子束蒸发法 • 激光蒸发法 • 反应蒸发法 • 射频蒸发法 • 电弧蒸发法 • 热壁法
第二章 薄膜制备的物理方法
(一)电阻加热蒸发法
• 采用钽、钼、钨等高熔点金属,做成适当形状的 蒸发容器,让电流通过,对蒸发材料进行直接加 热蒸发,或者把蒸发材料放入坩埚中进行间接加 热蒸发。
• 蒸发容器材料必须满足:(1)熔点高;(2)饱 和蒸汽压低;(3)化学性能稳定;(4)与被蒸 发材料浸润,Ag在钨丝上容易脱落。(5)原料丰 富,经济耐用。
实质就是设每一个蒸发原子或分子,在入射到基片表面 上的过程中,均不发生任何碰撞,而且到达基片后又全部 凝结。
第二章 薄膜制备的物理方法
沉积速率和膜厚分布
质量蒸发速率 : • 大多数蒸发材料是液相蒸发,也有一些是直接固
相蒸发。在单位时间dt内,从表面A蒸发的最大粒 子数dN为:
dN(2mk)T1/2P • 其中,P是平衡压A强d;t m为粒子质量;k为波尔兹曼
第二章 薄膜制备的物理方法
真空蒸发技术
• 真空蒸发装置主要部分有: (1)真空室:为蒸发过程提供必要的真空环境; (2)蒸发源:放置蒸发材料并对其进行加热; (3)基片:用于接收蒸发物质并在其表面形成固态蒸发薄膜。 外围还要有真空系统和机械、电路系统。
第二章 薄膜制备的物理方法
第二章 薄膜制备的物理方法
常数;T为绝对温度。乘以原子或分子质量,便得 到了单位面积上的质量蒸发速率:
me mA dN dt5.83 10 2
MP T
第二章 薄膜制备的物理方法
沉积速率和膜厚分布
第二章 薄膜制备的物理方法
沉积速率和膜厚分布
• 考虑理想的点蒸发源,设每个蒸发粒子入射到基片上时不发生任 何碰撞,而且到达基片后又全部凝结,则基片上dS面积的沉积速 率dm满足余玄定律:
第二章 薄膜制备的物理方法
第二章 薄膜制备的物理方法
物理气相沉积
• 薄膜沉积的物理方法主要是物理气相沉积法,物理气相沉积 (Physical Vapor Deposition,简称PVD)是应用广泛的一系列薄膜 制备方法的总称,包括真空蒸发法,溅射法,分子束外延法等。
• 物理气相沉积过程可概括为三个阶段: (1)从源材料中发射出粒子; (2)粒子输运到基片; (3)粒子在基片上凝结、成核、长大、成膜。
第二章 薄膜制备的物理方法
沉积速率和膜厚分布
为了对沉积速率和膜厚进行理论计算,找出其分布规律, 首先对蒸发过程作如下假设:
(1)蒸发原子或分子与残余气体分子之间不发生碰撞; (2)在蒸发源附近的蒸发原子或分子之间也不发生碰撞; (3)蒸发沉积到基片上的蒸发原子不再发生再蒸发现象,
即第一次碰撞就凝结在基片表面上。
第二章 薄膜制备的物理方法
真空蒸发原理
上述过程都必须在空气非常稀薄的真空环境中进行。否则: • 蒸发物质原子或分子将与大量空气分子碰撞,使膜层受到严重污
染,甚至形成氧化物; • 或者蒸发源被加热氧化烧毁; • 或者由于空气分子的碰撞阻挡,难以形成均匀连续的薄膜。
第二章 薄膜制备的物理方法
沉积速率和膜厚分布
• 在真空蒸发镀膜过程中,能否在基片上获得厚度均匀分布的薄膜, 是制膜的关键。
• 因此,薄膜在基片上的沉积速率以及其膜厚分布是我们十分关心 的问题。
• 基片上不同蒸发位置的膜厚,取决于蒸发源的蒸发特性、基片与 蒸发源的几何形状、相对位置以及蒸发物质的蒸发量。
第二章 薄膜制备的物理方法
• 由于粒子发射可以采用不同的方式,因而物理气相沉积技术呈现 出多种不同形式。
第二章 薄膜制备的物理方法
第二章 薄膜制备的物理方法
• 真空蒸发法 • 溅射法 • 离子镀 • 分子束外延
第二章 薄膜制备的物理方法
真空蒸发原理
• 真空蒸发镀膜法(简称真空蒸镀)是在真空环境 下,加热蒸发源材料,使其原子或分子从表面汽 化逸出,形成蒸汽流,入射到衬底(基片)表面, 凝结形成固态薄膜的方法。
• 假设蒸发膜的密度为 ,dm 则基4m片e 上cro任2s意d一S点的膜厚:
d
me
4
cos
பைடு நூலகம்r2
第二章 薄膜制备的物理方法
沉积速率和膜厚分布
• 基片上的各处膜厚分布状况由下式给出:
d
1
d0 1l/h2 3/2
其中d0是在点源正上方h处的沉积膜厚度。 • 如果蒸发源为一平行于基片的小平面蒸发源,则膜厚分布为:
• 由于真空蒸发法主要物理过程是通过加热蒸发材 料而产生,所以又称热蒸发法。
• 采用这种方法制备薄膜已有几十年的历史,用途 十分广泛。近年来,该方法的主要改进是蒸发源 上。
第二章 薄膜制备的物理方法
第二章 薄膜制备的物理方法
真空蒸发原理
• 真空蒸发镀膜法是应用最广泛的薄膜制备技术,其简单便利、操 作容易、成膜速度快、效率高;但制备的薄膜与基片结合较差, 工艺重复性不好,不容易获得结晶结构的薄膜。
• 如果真空度足够高N , 平N 均0自e由x程足p l/够(大),满足条
件,则被碰撞的分子比率 :
• 对于25℃的空气f,1N/N 0,l则/
• 由此可以看出,为保证0.6镀6 (膜c7 质m )/量P,在f要1求.50lP 时,
若蒸发源与基片距离l=25cm,真空压强P必须f 小0.1于 3×10-3Pa。
蒸发源是蒸发装置的关键部件
• 由于大多数金属材料都要求在1000-2000℃的高温 下蒸发。因此,必须将蒸发材料加热到很高的蒸 发温度。
• 为了避免污染薄膜材料,蒸发源中所用的支撑材 料在工作温度下必须具有可忽略的蒸汽压,以避 免支撑材料原子混入蒸发气体中。
• 通常所用的支撑材料为难熔的金属和氧化物。
d
1
d0 1l /h2 2
第二章 薄膜制备的物理方法
沉积速率和膜厚分布
第二章 薄膜制备的物理方法
第二章 薄膜制备的物理方法
沉积速率和膜厚分布
• 实际蒸发过程中,蒸发粒子都要受到真空室中残 余气体分子的碰撞,碰撞次数取决于分子的平均 自由程。设有N0个蒸发分子,飞行距离l后,未受 到残余气体分子碰撞的数目N为:
• 同时,选择某一特殊支撑材料时,一定要考虑蒸 发物与支撑材料之间可能发生的合金化和化学反 应、相互润湿程度等问题。
• 支撑材料的形状则主要取决于蒸发物。
第二章 薄膜制备的物理方法
第二章 薄膜制备的物理方法
真空蒸发技术
• 电阻加热蒸发法 • 闪烁蒸发法 • 电子束蒸发法 • 激光蒸发法 • 反应蒸发法 • 射频蒸发法 • 电弧蒸发法 • 热壁法
第二章 薄膜制备的物理方法
(一)电阻加热蒸发法
• 采用钽、钼、钨等高熔点金属,做成适当形状的 蒸发容器,让电流通过,对蒸发材料进行直接加 热蒸发,或者把蒸发材料放入坩埚中进行间接加 热蒸发。
• 蒸发容器材料必须满足:(1)熔点高;(2)饱 和蒸汽压低;(3)化学性能稳定;(4)与被蒸 发材料浸润,Ag在钨丝上容易脱落。(5)原料丰 富,经济耐用。
实质就是设每一个蒸发原子或分子,在入射到基片表面 上的过程中,均不发生任何碰撞,而且到达基片后又全部 凝结。
第二章 薄膜制备的物理方法
沉积速率和膜厚分布
质量蒸发速率 : • 大多数蒸发材料是液相蒸发,也有一些是直接固
相蒸发。在单位时间dt内,从表面A蒸发的最大粒 子数dN为:
dN(2mk)T1/2P • 其中,P是平衡压A强d;t m为粒子质量;k为波尔兹曼
第二章 薄膜制备的物理方法
真空蒸发技术
• 真空蒸发装置主要部分有: (1)真空室:为蒸发过程提供必要的真空环境; (2)蒸发源:放置蒸发材料并对其进行加热; (3)基片:用于接收蒸发物质并在其表面形成固态蒸发薄膜。 外围还要有真空系统和机械、电路系统。
第二章 薄膜制备的物理方法
第二章 薄膜制备的物理方法
常数;T为绝对温度。乘以原子或分子质量,便得 到了单位面积上的质量蒸发速率:
me mA dN dt5.83 10 2
MP T
第二章 薄膜制备的物理方法
沉积速率和膜厚分布
第二章 薄膜制备的物理方法
沉积速率和膜厚分布
• 考虑理想的点蒸发源,设每个蒸发粒子入射到基片上时不发生任 何碰撞,而且到达基片后又全部凝结,则基片上dS面积的沉积速 率dm满足余玄定律:
第二章 薄膜制备的物理方法
第二章 薄膜制备的物理方法
物理气相沉积
• 薄膜沉积的物理方法主要是物理气相沉积法,物理气相沉积 (Physical Vapor Deposition,简称PVD)是应用广泛的一系列薄膜 制备方法的总称,包括真空蒸发法,溅射法,分子束外延法等。
• 物理气相沉积过程可概括为三个阶段: (1)从源材料中发射出粒子; (2)粒子输运到基片; (3)粒子在基片上凝结、成核、长大、成膜。
第二章 薄膜制备的物理方法
沉积速率和膜厚分布
为了对沉积速率和膜厚进行理论计算,找出其分布规律, 首先对蒸发过程作如下假设:
(1)蒸发原子或分子与残余气体分子之间不发生碰撞; (2)在蒸发源附近的蒸发原子或分子之间也不发生碰撞; (3)蒸发沉积到基片上的蒸发原子不再发生再蒸发现象,
即第一次碰撞就凝结在基片表面上。