PLC编程与伺服控制系统
基于PLC的伺服系统的运动控制系统设计毕业论文设计

南京化工职业技术学院毕业论文设计题目:基于PLC的伺服系统的运动控制系统设计毕业设计(论文)原创性声明和使用授权说明原创性声明本人郑重承诺:所呈交的毕业设计(论文),是我个人在指导教师的指导下进行的研究工作及取得的成果。
尽我所知,除文中特别加以标注和致谢的地方外,不包含其他人或组织已经发表或公布过的研究成果,也不包含我为获得及其它教育机构的学位或学历而使用过的材料。
对本研究提供过帮助和做出过贡献的个人或集体,均已在文中作了明确的说明并表示了谢意。
作者签名:日期:指导教师签名:日期:使用授权说明本人完全了解大学关于收集、保存、使用毕业设计(论文)的规定,即:按照学校要求提交毕业设计(论文)的印刷本和电子版本;学校有权保存毕业设计(论文)的印刷本和电子版,并提供目录检索与阅览服务;学校可以采用影印、缩印、数字化或其它复制手段保存论文;在不以赢利为目的前提下,学校可以公布论文的部分或全部内容。
作者签名:日期:学位论文原创性声明本人郑重声明:所呈交的论文是本人在导师的指导下独立进行研究所取得的研究成果。
除了文中特别加以标注引用的内容外,本论文不包含任何其他个人或集体已经发表或撰写的成果作品。
对本文的研究做出重要贡献的个人和集体,均已在文中以明确方式标明。
本人完全意识到本声明的法律后果由本人承担。
作者签名:日期:年月日学位论文版权使用授权书本学位论文作者完全了解学校有关保留、使用学位论文的规定,同意学校保留并向国家有关部门或机构送交论文的复印件和电子版,允许论文被查阅和借阅。
本人授权大学可以将本学位论文的全部或部分内容编入有关数据库进行检索,可以采用影印、缩印或扫描等复制手段保存和汇编本学位论文。
涉密论文按学校规定处理。
作者签名:日期:年月日导师签名:日期:年月日指导教师评阅书指导教师评价:一、撰写(设计)过程1、学生在论文(设计)过程中的治学态度、工作精神□优□良□中□及格□不及格2、学生掌握专业知识、技能的扎实程度□优□良□中□及格□不及格3、学生综合运用所学知识和专业技能分析和解决问题的能力□优□良□中□及格□不及格4、研究方法的科学性;技术线路的可行性;设计方案的合理性□优□良□中□及格□不及格5、完成毕业论文(设计)期间的出勤情况□优□良□中□及格□不及格二、论文(设计)质量1、论文(设计)的整体结构是否符合撰写规范?□优□良□中□及格□不及格2、是否完成指定的论文(设计)任务(包括装订及附件)?□优□良□中□及格□不及格三、论文(设计)水平1、论文(设计)的理论意义或对解决实际问题的指导意义□优□良□中□及格□不及格2、论文的观念是否有新意?设计是否有创意?□优□良□中□及格□不及格3、论文(设计说明书)所体现的整体水平□优□良□中□及格□不及格建议成绩:□优□良□中□及格□不及格(在所选等级前的□内画“√”)指导教师:(签名)单位:(盖章)年月日评阅教师评阅书评阅教师评价:一、论文(设计)质量1、论文(设计)的整体结构是否符合撰写规范?□优□良□中□及格□不及格2、是否完成指定的论文(设计)任务(包括装订及附件)?□优□良□中□及格□不及格二、论文(设计)水平1、论文(设计)的理论意义或对解决实际问题的指导意义□优□良□中□及格□不及格2、论文的观念是否有新意?设计是否有创意?□优□良□中□及格□不及格3、论文(设计说明书)所体现的整体水平□优□良□中□及格□不及格建议成绩:□优□良□中□及格□不及格(在所选等级前的□内画“√”)评阅教师:(签名)单位:(盖章)年月日教研室(或答辩小组)及教学系意见教研室(或答辩小组)评价:一、答辩过程1、毕业论文(设计)的基本要点和见解的叙述情况□优□良□中□及格□不及格2、对答辩问题的反应、理解、表达情况□优□良□中□及格□不及格3、学生答辩过程中的精神状态□优□良□中□及格□不及格二、论文(设计)质量1、论文(设计)的整体结构是否符合撰写规范?□优□良□中□及格□不及格2、是否完成指定的论文(设计)任务(包括装订及附件)?□优□良□中□及格□不及格三、论文(设计)水平1、论文(设计)的理论意义或对解决实际问题的指导意义□优□良□中□及格□不及格2、论文的观念是否有新意?设计是否有创意?□优□良□中□及格□不及格3、论文(设计说明书)所体现的整体水平□优□良□中□及格□不及格评定成绩:□优□良□中□及格□不及格(在所选等级前的□内画“√”)教研室主任(或答辩小组组长):(签名)年月日教学系意见:系主任:(签名)年月日摘要本文采用运动控制系统,完成三菱电机杯竞赛的关于伺服电机如何实现系统的运动控制系统。
基于PLC与HMI的伺服电机运动控制系统设计与实现

基于PLC与HMI的伺服电机运动控制系统设计与实现摘要:随着计算机技术、可编程控制器及触摸屏科技的进步,现在机械制造行业几种控制系统越来越多的被应用到处理复杂事务中使其变得处理简易,在生活中,几种控制系统的应用提高了生产效率,使我们生活变得简单化,提高了机械产品的安全性和可操作性。
本文提出了选用S7-200SMARTCPUST30PLC为主控制器,发送脉冲指令作为伺服驱动器的输入信号,通过伺服驱动器实现对伺服电机前/后点动及连续运转、相对/绝对位置的精确控制以及自动查找参考点等操作,由SMART1000IEV3触摸屏搭建监控画面的思路。
关键词:伺服电机;PLC;运动控制;HMI1、系统总体方案设计1.1PLC和HMI简介1.1.1可编程里辑控制器简介可编辑逻辑控制器简称PLC,能够适应工作环境较为恶劣的条件,适用范围较广。
另外,PLC的维护较为方便,使用可靠性比较高。
CPU的运行状态是决定系统流畅的重要保证,而PLC的工作状态就是通过软件控制CPU的运行情况,当然通过硬件开关进行强制控制也是一种有效的控制手段,比如在进行测试阶段或者对系统进行检修时,硬件控制是一种较为方便的方式。
1.1.2 HMI简介随着我国工业水平提高,在生产过程中生产工艺越来越复杂,生产设备也在不断更新换代,生产控制人员不仅仅要对生产的每个流程熟知,还要对设备运行状况了解,做到设备运转的透明化。
HMI便是实现人机互通的关键技术,它实现了工作人员与机器之间的可靠连接。
在工作人员与Wincc flexible之间,HMI是实现二者链接的重要接口。
在控制器与Wincc flexible之间也同样需要这样的接口。
1.2 总体方案设计整个系统分为硬件设计、PLC程序设计、HMI与PLC通讯、系统实验调试共4部分。
硬件方面,主控制器选用S7-200SMARTCPUST30PLC,发送脉冲指令作为台达伺服驱动器(ASDA-B2-0121-B)的输入信号;通过伺服驱动器实现控制伺服电机(ASDAB2)的旋转速度和驱动丝杆滑台的移动位置[1]。
一文看懂西门子PLC控制的伺服控制系统

一文看懂西门子PLC控制的伺服控制系统
伺服控制系统用来精确地跟随或复现某个过程的反馈控制系统。
在很多情况下,伺服系统专指被控制量(系统的输出量)是机械位移或位移速度、加速度的反馈控制系统,其作用是使输出的机械位移(或转角)准确地跟踪输入的位移(或转角)。
伺服系统的结构组成和其他形式的反馈控制系统没有原则上的区别。
伺服控制系统的优点1、精度:实现了位置,速度和力矩的闭环控制;克服了步进电机失步的问题;刚筋成品的尺寸和弯曲角度的精度均在±1;
2、转速:高速性能好,一般额定转速能达到2000~3000转;
3、适应性:抗过载能力强,能承受三倍于额定转矩的负载,对有瞬间负载波动和要求快速起动的场合特别适用;
4、稳定:低速运行平稳,低速运行时不会产生类似于步进电机的步进运行现象。
适用于有高速响应要求的场合;
5、及时性:电机加减速的动态相应时间短,一般在几十毫秒之内;
6、舒适性:发热和噪音明显降低。
西门子PLC控制的伺服控制系统以SINAMICS V80系统为例说明。
SINAMICS V80伺服驱动系统包括伺服驱动器和伺服电机两部分,伺服驱动器总是与其对应的同等功率的伺服电机一起配套使用。
SINAMICS V80伺服驱动器通过脉冲输入接口来接受从上位控制器发来的脉冲序列,进行速度和位置的控制,通过数字量接口信号来完成驱动器运行的控制和实时状态的输出。
驱动器上有一个脉冲设置旋转开关用来设计脉冲分辨率以及指令脉冲类型的。
本设计选择3,对应的分辨率是10000。
驱动器的四个连接器X1、X2、X10和X20相应的功能如图3所示:。
伺服控制器与PLC的联动控制技术

伺服控制器与PLC的联动控制技术现代工业生产中,机械设备的自动化程度不断提升,而伺服控制器和PLC(可编程逻辑控制器)成为了自动化控制的关键组成部分。
伺服控制器通过控制电机的运动实现精确的位置控制,而PLC则负责处理大量的输入输出信号和控制逻辑,实现对整个系统的自动控制。
伺服控制器与PLC的联动控制技术的应用,不仅提高了生产效率和产品质量,还降低了人力成本和故障率。
本文将介绍伺服控制器与PLC的联动控制技术的基本原理、应用场景以及实施步骤。
首先,我们来了解一下伺服控制器和PLC的基本概念。
伺服控制器是一种专用的控制器,它能够实时监测和控制电机的运动状态,通过PID控制算法来实现位置、速度和力矩的精确控制。
相比传统的开关控制,伺服控制器具有更高的精度和稳定性。
而PLC是一种通用的可编程控制器,它可以通过编程来实现不同的控制逻辑,适用于各种自动化控制场景。
PLC能够监测和控制各种传感器和执行器,通过输入输出模块与各种外部设备进行通信。
伺服控制器和PLC的联动控制技术主要通过PLC与伺服控制器的通信来实现。
通常使用一种称为“Pulse/Dir”接口的通信方式,即通过在PLC中产生脉冲和方向信号,控制伺服控制器的运动。
这种通信方式简单可靠,适用于各种控制需求。
实现伺服控制器与PLC的联动控制,可以通过以下步骤来进行:1. 确定系统需求:首先需要明确系统的运动需求和控制逻辑,确定伺服控制器和PLC的工作模式、协作方式和通信要求。
2. 搭建硬件平台:根据系统需求,选择适合的伺服控制器和PLC,并将它们连接起来。
通常使用数字信号输入输出模块、编码器模块和伺服控制器作为接口。
3. 编写PLC程序:使用PLC编程软件(如 ladder logic 或者函数块图)进行编程,实现控制逻辑。
根据需求生成脉冲和方向信号,发送给伺服控制器。
4. 编写伺服控制器程序:在伺服控制器中设置合适的运动参数和控制算法,接收来自PLC的信号,并通过闭环控制实现电机的精确运动。
PLC与伺服电机速度控制
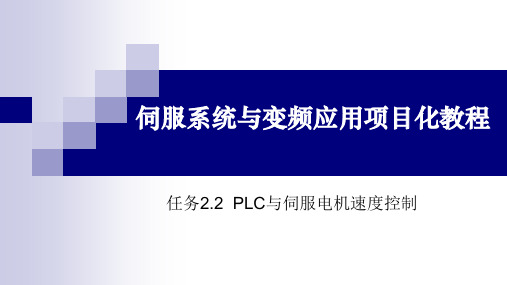
基础知识
(2)转子串电阻调速技术
转子串电阻调速是改变转子的电阻大小进而调节交流电动机的转速。这种调 速方法虽然简单方便,却存在着以下缺点:
(1)串联电阻通过的电流较大,难以采用滑线方式,更无法以电气控制的方 式进行控制,因此调速只能是有级的。 (2)串联较大附加电阻后,电动机的机械特性变得很软。低速运转时,只要 负载稍有变化,转速的波动就很大。 (3)电动机在低速运转时,效率甚低,电能损耗很大。
基础知识
(2)调制方式
在SPWM逆变器中,三角波电压频率ft与参照波电压频率(即逆变器的输出频 率)fr之比N=ft/fr称为载波比,也称调制比。根据载波比的变化与否,PWM调制方 式可分为:
➢同步式 ➢异步式 ➢分段同步式
基础知识
➢同步调制方式
载波比N等于常数时的调制方式称同步调制方式。
在逆变器输出频率变化的整个范围内,皆可保持输出波形的正、负半 波完全对称,只有奇次谐波存在,而且能严格保证逆变器输出三相波
(4)变频调速技术 交流电的交变频率是决定交流电动机工作转速的基本参数。因此,直接改变和
控制供电频率应当是控制交流伺服电动机的最有效方法,它直接调节交流电动机的 同步转速,控制的切入点最直接而明确,变频调速的调速范围宽,平滑性好,具有 优良的动、静态特性,是一种理想的高效率、高性能的调速手段。对交流电动机进 行变频调速,需要一套变频电源,相关技术有:
基础知识
➢ 速度指令输入增益的设定 使伺服电机速度为额定值的速度指令 (V-REF)所对应的模拟量电压值,可通过
Pn300 来设定,如表2-10所示。
表2-10 速度指令输入增益的设定
基础知识
速度指令电压与伺服电机转速的关系如图2-31所示。伺服电机旋转分为正转和反 转,对应的指令电压输入范围在-12V~+12V。
PLC与交流伺服在单轴控制系统中的应用

图 2 程 序 运 行 中的 监 控 画 面
(2)其他窗 口和界面。除路 口信号监控外 ,为保 证系统可靠运行 ,还设计 了系统报警窗 口。系统可在 报警变量超出预设值时 ,弹 出报警窗 口,显示报警信 息 ,方便操作人员检查故障 ,维护系统。
另外 ,利用组态王为系统提供的实时报告 ,可应 用历史数据利用 Report0函数 ,生成 固定格式 的历史 记录报告 。系统可根据统计报告 ,决策多个路 口的投
(4)机 械减 速 比为 72×2=144;
(5)伺服脉冲与直线位移的关系。伺服电机 1转
2 系统硬件设计 和技术性能
经 机 械减 速后 对 应 丝 杆 1/14 转 ,因丝 杆 螺 距 为 24 ITlln,所 以丝杆 1转对应直线位移 24 nlin。最终 ,伺
2.1 硬 件设 计 (1)PLC的选 用 。 CPU单元 AlsJCPu—S3; 输入模块 A1SX42 64点;
表 1 交 流 伺 服 系统 数 据 表
交流伺 服驱动器 型号 ASC-[50
交流伺服 电机 型号 AS .45
主回路输入电压 AC 220V 功率 4.5 kW
控制电压 0 ±10V
额定转矩 30N·m
额定转速 2OOO r/rain
最大转矩 95N·m
可驱动容量 4.5 kW Fra bibliotekSA4
X57 暂停 ,X57为 1 X57为 0
ZDA
X58 正向点动 。X58为 1 X58为 0
FDA
X59 反向点动 ,X59为 1 X59为 0
3 控 制 系统 的设计 与实现
<装备制造技术)2012年第 4期
PLC如何控制伺服电机
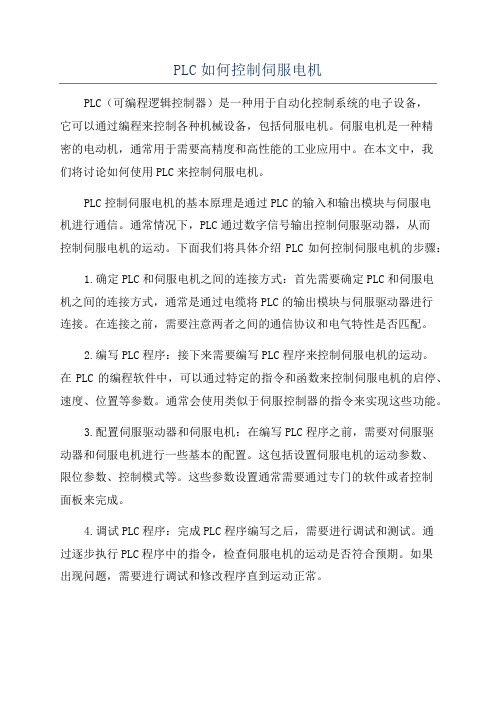
PLC如何控制伺服电机PLC(可编程逻辑控制器)是一种用于自动化控制系统的电子设备,它可以通过编程来控制各种机械设备,包括伺服电机。
伺服电机是一种精密的电动机,通常用于需要高精度和高性能的工业应用中。
在本文中,我们将讨论如何使用PLC来控制伺服电机。
PLC控制伺服电机的基本原理是通过PLC的输入和输出模块与伺服电机进行通信。
通常情况下,PLC通过数字信号输出控制伺服驱动器,从而控制伺服电机的运动。
下面我们将具体介绍PLC如何控制伺服电机的步骤:1.确定PLC和伺服电机之间的连接方式:首先需要确定PLC和伺服电机之间的连接方式,通常是通过电缆将PLC的输出模块与伺服驱动器进行连接。
在连接之前,需要注意两者之间的通信协议和电气特性是否匹配。
2.编写PLC程序:接下来需要编写PLC程序来控制伺服电机的运动。
在PLC的编程软件中,可以通过特定的指令和函数来控制伺服电机的启停、速度、位置等参数。
通常会使用类似于伺服控制器的指令来实现这些功能。
3.配置伺服驱动器和伺服电机:在编写PLC程序之前,需要对伺服驱动器和伺服电机进行一些基本的配置。
这包括设置伺服电机的运动参数、限位参数、控制模式等。
这些参数设置通常需要通过专门的软件或者控制面板来完成。
4.调试PLC程序:完成PLC程序编写之后,需要进行调试和测试。
通过逐步执行PLC程序中的指令,检查伺服电机的运动是否符合预期。
如果出现问题,需要进行调试和修改程序直到运动正常。
5.程序优化和调整:一旦PLC程序正常运行,可以进行程序优化和调整。
这包括对伺服电机的运动参数进行调整,以提高运动的稳定性和精度。
同时,还可以根据实际情况对程序进行优化,以满足不同的控制需求。
总的来说,PLC控制伺服电机需要对PLC程序和伺服电机进行充分的了解和配置。
只有通过正确的连接方式、编写程序和调试测试,才能实现对伺服电机的精准控制。
在实际应用中,需要根据具体的控制需求和系统要求来选择合适的PLC和伺服电机,并按照上述步骤进行操作,以确保系统的正常运行。
基于PLC的伺服电机运动控制系统设计

基于 PLC 的伺服电机运动控制系统设计摘要:近年来,我国各个行业及领域广泛应用了PLC,对企业实现生产自动化奠定了重要的基础。
特别是PLC伺服电机运行控制系统的设计及实施,使电机运动质量与效率得到了进一步提升。
本文结合PLC伺服电机运行控制系统设计标准,以S7-1200为例,利用对程序与硬件的设计,保证了运动控制的精准性。
关键词:PLC;伺服电机;运行控制前言:伺服电机具有多重优点,如扛过载能力强、运行稳定、高速性能好以及精准度高等,已广泛应用在企业生产中。
但由于伺服电机大多使用的是NC数控系统,不仅运行成本高,且控制系统极为复杂,无法有效对接以PLC为主的控制器生产线,使得经济效益不是十分可观。
故而,在生产自动化水平的进一步提升下,为了最大程度保障产品精度性,就必须重视基础设计,通过对伺服电机运行控制准确性的提升,全面改善系统的生产效率与性能,从而实现经济效益最大化,降低企业的生产成本。
1基于PLC伺服电机控制系统设计分析PLC控制系统是一种专门用于工业生产的数字运算操作电子装置,其应用了一类可编程存储器,可满足内部存储、执行逻辑运算、顺序控制、定时、技术以及算数操作等要求,可以说是工业控制的核心。
就我国工业生产现状来看,大部分依然是采用的步进电机运动系统,其应用的步进电机步距角最小为0.36°(与电机转动一圈需要1000个脉冲相当),精度比较低,并且经常会出现失步问题,难以满足高精度生产工艺。
相比来讲伺服电机无论是在精度、速度、抗过载性能、响应速度、运行稳定性以及运行温度等方面均具有更大优势。
基于PLC进行伺服电机控制系统的设计,可以在原来的步进电机运动系统基础上,做进一步的优化,使得系统能够更好的适应高精度生产要求。
其中需要就目前所应用NC数控系统进行优化,解决其与PLC主控制器生产线无法有效对接的难题,满足高效生产的核心要求。
2伺服电机控制系统分析2.1运行控制模型如图1所示,伺服电机运行控制模型可用于构建伺服电机运动控制系统。
台达PLC实例伺服控制实例参数设置及PLC程序
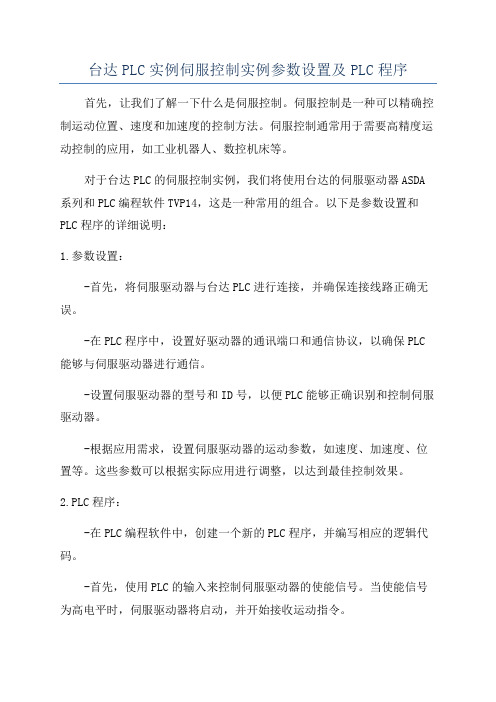
台达PLC实例伺服控制实例参数设置及PLC程序首先,让我们了解一下什么是伺服控制。
伺服控制是一种可以精确控制运动位置、速度和加速度的控制方法。
伺服控制通常用于需要高精度运动控制的应用,如工业机器人、数控机床等。
对于台达PLC的伺服控制实例,我们将使用台达的伺服驱动器ASDA 系列和PLC编程软件TVP14,这是一种常用的组合。
以下是参数设置和PLC程序的详细说明:1.参数设置:-首先,将伺服驱动器与台达PLC进行连接,并确保连接线路正确无误。
-在PLC程序中,设置好驱动器的通讯端口和通信协议,以确保PLC 能够与伺服驱动器进行通信。
-设置伺服驱动器的型号和ID号,以便PLC能够正确识别和控制伺服驱动器。
-根据应用需求,设置伺服驱动器的运动参数,如速度、加速度、位置等。
这些参数可以根据实际应用进行调整,以达到最佳控制效果。
2.PLC程序:-在PLC编程软件中,创建一个新的PLC程序,并编写相应的逻辑代码。
-首先,使用PLC的输入来控制伺服驱动器的使能信号。
当使能信号为高电平时,伺服驱动器将启动,并开始接收运动指令。
-接下来,编写代码来控制伺服驱动器的运动。
可以使用PLC的输出来控制伺服驱动器的运行方向和速度。
-使用PLC的输入来读取伺服驱动器的状态信息,如位置、速度等。
这些信息可以用于采取相应的控制策略和判断伺服运动是否达到预期目标。
-最后,使用PLC的输出来控制伺服驱动器的停止和复位功能。
当停止信号为高电平时,伺服驱动器将停止运动,并回到初始位置。
通过以上的参数设置和PLC程序,您可以实现对伺服驱动器的精确控制。
您可以根据实际应用要求,进行相应的参数调整和控制逻辑设计,以满足您的需求。
PLC控制伺服电机实例分析

PLC控制伺服电机实例分析PLC控制伺服电机是工业自动化领域中常见的一种应用,通过PLC控制器来实现对伺服电机的精准控制,使得生产线的运作更加高效和稳定。
在本文中,将以一个实际的应用案例来介绍PLC控制伺服电机的工作原理和实现过程。
一、系统结构本系统采用的是西门子PLC控制器和西门子伺服电机,系统主要由PLC控制器、伺服驱动器和伺服电机组成。
PLC控制器负责接收外部信号,进行逻辑控制,并向伺服驱动器发送控制指令,伺服驱动器则接收这些指令并控制伺服电机的运动。
二、PLC编程在PLC编程中,需要定义输入输出引脚、变量和逻辑控制程序。
首先需要定义输入引脚,用于接收外部传感器信号,比如光电传感器、开关等;然后定义输出引脚,用于控制伺服驱动器,实现对伺服电机的启停和速度调节;接着定义一些变量,用于存储中间状态和控制参数;最后编写逻辑控制程序,根据输入信号和变量状态来控制伺服电机的运动。
三、伺服电机控制伺服电机的控制主要包括位置控制、速度控制和力矩控制。
在PLC编程中,可以通过设定目标位置、目标速度和目标力矩来实现对伺服电机的控制。
通过调节PID控制器的参数,可以实现对伺服电机的精准控制。
四、系统调试在系统调试中,需要先进行参数设置和校准,确保伺服电机的运动符合预期。
然后通过PLC编程调试工具,监控伺服电机的运动状态和控制指令,发现问题并及时修复。
最后对整个系统进行测试,验证其性能和稳定性。
综上所述,PLC控制伺服电机是一种高效、稳定的控制方式,适用于各种需要精准位置和速度控制的场合。
通过合理的PLC编程和参数设置,可以实现对伺服电机的精确控制,提高生产效率和品质。
在实际应用中,需要根据具体情况进行调整和优化,确保系统的稳定性和可靠性。
plc控制伺服常用指令和程序段总结

plc控制伺服常用指令和程序段总结在工业自动化领域,PLC(可编程逻辑控制器)常用于控制伺服系统,以实现精确的运动控制。
PLC控制伺服系统的指令和程序段在传递运动命令、监测反馈信号和保护伺服系统方面起到至关重要的作用。
以下是对PLC控制伺服常用指令和程序段的总结。
1. 伺服控制指令:- 位置控制指令:用于将伺服系统定位到特定位置。
常用的指令包括MOVE、MOVEL、MOVES等,可以实现绝对位置控制和相对位置控制。
- 速度控制指令:用于调节伺服系统的运动速度。
常用的指令包括SPEED、ACCELERATE、DECELERATE等,可以实现平稳的速度控制。
- 力矩控制指令:用于调节伺服系统的输出力矩。
常用的指令包括TORQUE、GAIN等,可以实现精确的力矩控制。
2. 伺服控制程序段:- 位置控制程序段:在程序中定义伺服系统的目标位置,并根据反馈信号调节输出信号,使伺服系统准确到达目标位置。
程序段包括位置控制指令、位置误差计算和PID控制算法等。
- 速度控制程序段:在程序中定义伺服系统的目标速度,并根据反馈信号调节输出信号,使伺服系统保持平稳的运动速度。
程序段包括速度控制指令、速度误差计算和速度环控制算法等。
- 力矩控制程序段:在程序中定义伺服系统的目标力矩,并根据反馈信号调节输出信号,使伺服系统输出所需的力矩。
程序段包括力矩控制指令、力矩误差计算和力矩环控制算法等。
通过合理使用PLC控制伺服系统的指令和程序段,可以实现对运动的精确控制和保护。
在实际应用中,还需根据具体的控制要求和系统特点进行参数调整和优化,以获得最佳的控制效果。
总结:PLC控制伺服系统常用的指令包括位置控制指令、速度控制指令和力矩控制指令,而程序段则包括位置控制程序段、速度控制程序段和力矩控制程序段。
合理运用这些指令和程序段,可以实现精确的运动控制和保护。
基于PLC的伺服系统的运动控制系统设计
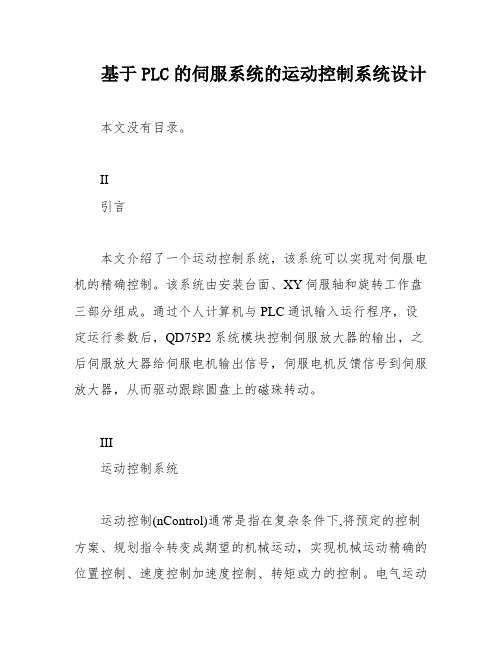
基于PLC的伺服系统的运动控制系统设计本文没有目录。
II引言本文介绍了一个运动控制系统,该系统可以实现对伺服电机的精确控制。
该系统由安装台面、XY伺服轴和旋转工作盘三部分组成。
通过个人计算机与PLC通讯输入运行程序,设定运行参数后,QD75P2系统模块控制伺服放大器的输出,之后伺服放大器给伺服电机输出信号,伺服电机反馈信号到伺服放大器,从而驱动跟踪圆盘上的磁珠转动。
III运动控制系统运动控制(nControl)通常是指在复杂条件下,将预定的控制方案、规划指令转变成期望的机械运动,实现机械运动精确的位置控制、速度控制加速度控制、转矩或力的控制。
电气运动控制是由电力拖动发展而来的,电力拖动或电气传动是对以电动机为对象的控制系统的通称。
从电力拖动开始,经历四十多年的发展过程,现代运动控制已成为一个以控制理论为基础,涵盖电机技术、电力电子技术、微电子技术、传感器检测技术、信息处理技术、自动控制技术、微计算机技术和计算机仿真和辅助制造技术等许多学科,且多种不同学科交叉应用的控制技术。
IV运动控制系统的构建该系统由两工位运动控制系统组成:2套伺服放大器及伺服电机、QD75系统模块、变频器、三菱可编程序控制器、触摸屏等组成。
构建“PLC+伺服放大器+伺服电机+触摸屏”的运动控制系统。
运动控制系统多种多样,但从基本结构上看,一个典型的现代运动控制系统的硬件主要由上位计算机、运动控制器、功率驱动装置、电动机、执行机构和传感器反馈检测装置等部分组成。
其中的运动控制器是指以中央逻辑控制单元为核心,以传感器为信号敏感元件,以电机或动力装置和执行单元为控制对象的一种控制装置。
它的主要任务是根据运动控制的逻辑、数学运算,为电机或其它动力和执行装置提供正确的控制信号。
V系统组成安装台面、XY伺服轴、旋转工作盘三大部分构成了运动控制模型。
图中上端为XY十字工作台(伺服电机控制),考虑到机械强度的问题,Y轴有两个平行轴固定,其中左侧的为主动驱动轴,右侧为从动轴;X轴平面装有霍尔传感器;上方为旋转工作台,工作盘由交流电机(电机的速度由变频器控制)带着转动工作时,在工作盘放入磁钢,当工作盘转动时,X轴上部安装的传感器须一直能够对应到磁钢(XY轴随动,传感器保持检测到磁钢而不脱开)。
开题报告-基于PLC的伺服电机控制系统开发

基于PLC的伺服电机控制系统开发1、课题背景PLC(Programmable Logic Controller)名为可编辑逻辑控制器,诞生于上个世纪,其功能强大、使用方便、性价比高、可靠性抗干扰能力强的优异特点使它成为了现代化工业改革中控制系统方面的一面旗帜。
而伺服电机是工厂自动化、数控机床、机器人等机电一体化中的重要驱动部件。
两者都广泛运用在工业领域,而它们的结合更是给整个现代工业带来了翻天覆地的变化。
伺服系统(servomechanism)又称随动系统,是用来精确地跟随或复现某个过程的反馈控制系统。
伺服系统使物体的位置、方位、状态等输出被控量能够跟随输入目标(或给定值)的任意变化的自动控制系统。
它的主要任务是按控制命令的要求、对功率进行放大、变换与调控等处理,使驱动装置输出的力矩、速度和位置控制非常灵活方便。
在很多情况下,伺服系统专指被控制量(系统的输出量)是机械位移或位移速度、加速度的反馈控制系统,其作用是使输出的机械位移(或转角)准确地跟踪输入的位移(或转角),其结构组成和其他形式的反馈控制系统没有原则上的区别。
伺服系统最初用于国防军工,如火炮的控制,船舰、飞机的自动驾驶,导弹发射等,后来逐渐推广到国民经济的许多部门,如自动机床、无线跟踪控制等纵观我国的工业自动化水平还依旧处于发展阶段,无论是控制系统还是网络化程度都和发达国家之间存在明显的差距。
其中有大多数工厂依旧使用传统机床和生产加工线,这些工厂和企业急需爆发出新的生命力来响应国家的政策。
并且近年来我国强调经济的可持续发现和现代工业化的转变,PLC伺服控制应用将是其中必不可少的一份子。
因此从它的发展趋势来看,它在我国工业应用领域的拓展和深入将是必然实现的。
而本课题基于PLC的伺服电机的控制系统,便是顺应时代的潮流。
在plc 深入改革工业世界的同时,运用自己所学的基础知识和专业知识来设计并解决问题。
2、文献调研2.1PLC伺服系统在国内发展现状2012年沈阳理工大学机械电子工程的王瑜硕士在导师陈白宁的辅导下研究以钢管切割生产线中的自动定长切割设备为对象,提出了锯片在高速旋转的过程中变速进给切削的新理念,研究开发了可以变速、定长切割,具有设备可靠性高、结构简单、易于调试等特点的冷切割设备控制系统。
16.PLC与伺服脉冲控制
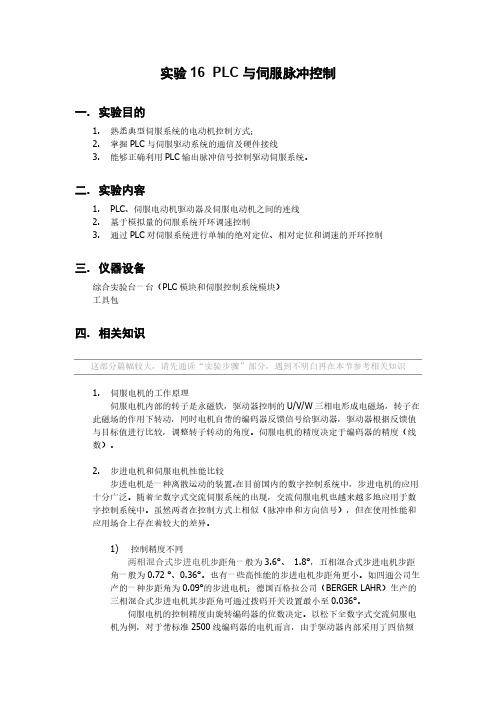
实验16PLC与伺服脉冲控制一.实验目的1.熟悉典型伺服系统的电动机控制方式;2.掌握PLC与伺服驱动系统的通信及硬件接线3.能够正确利用PLC输出脉冲信号控制驱动伺服系统。
二.实验内容1.PLC、伺服电动机驱动器及伺服电动机之间的连线2.基于模拟量的伺服系统开环调速控制3.通过PLC对伺服系统进行单轴的绝对定位、相对定位和调速的开环控制三.仪器设备综合实验台一台(PLC模块和伺服控制系统模块)工具包四.相关知识这部分篇幅较大,请先通读“实验步骤”部分,遇到不明白再在本节参考相关知识1.伺服电机的工作原理伺服电机内部的转子是永磁铁,驱动器控制的U/V/W三相电形成电磁场,转子在此磁场的作用下转动,同时电机自带的编码器反馈信号给驱动器,驱动器根据反馈值与目标值进行比较,调整转子转动的角度。
伺服电机的精度决定于编码器的精度(线数)。
2.步进电机和伺服电机性能比较步进电机是一种离散运动的装置.在目前国内的数字控制系统中,步进电机的应用十分广泛。
随着全数字式交流伺服系统的出现,交流伺服电机也越来越多地应用于数字控制系统中。
虽然两者在控制方式上相似(脉冲串和方向信号),但在使用性能和应用场合上存在着较大的差异。
1)控制精度不同两相混合式步进电机步距角一般为3.6°、 1.8°,五相混合式步进电机步距角一般为0.72 °、0.36°。
也有一些高性能的步进电机步距角更小。
如四通公司生产的一种步距角为0.09°的步进电机;德国百格拉公司(BERGER LAHR)生产的三相混合式步进电机其步距角可通过拨码开关设置最小至0.036°。
伺服电机的控制精度由旋转编码器的位数决定。
以松下全数字式交流伺服电机为例,对于带标准2500线编码器的电机而言,由于驱动器内部采用了四倍频技术,其脉冲当量为360°/10000=0.036°。
对于带17位编码器的电机而言,驱动器每接收217=131072个脉冲电机转一圈,即其脉冲当量为360°/131072=0.00275°(9.89秒)。
PLC控制的伺服电机控制系统参数设置与调试分析
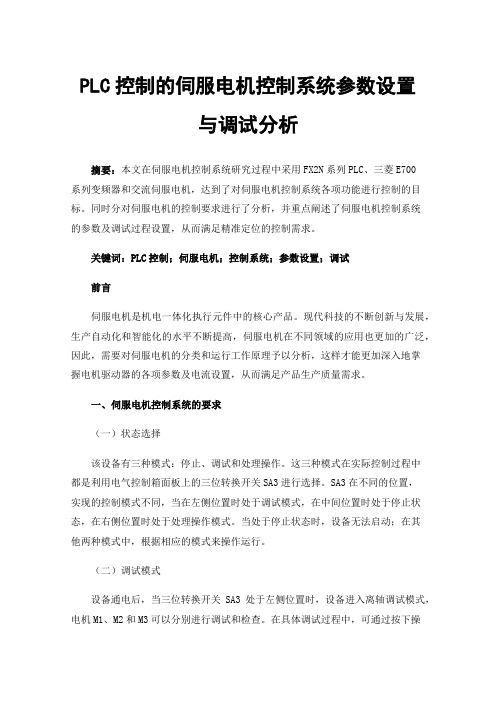
PLC控制的伺服电机控制系统参数设置与调试分析摘要:本文在伺服电机控制系统研究过程中采用FX2N系列PLC、三菱E700系列变频器和交流伺服电机,达到了对伺服电机控制系统各项功能进行控制的目标。
同时分对伺服电机的控制要求进行了分析,并重点阐述了伺服电机控制系统的参数及调试过程设置,从而满足精准定位的控制需求。
关键词:PLC控制;伺服电机;控制系统;参数设置;调试前言伺服电机是机电一体化执行元件中的核心产品。
现代科技的不断创新与发展,生产自动化和智能化的水平不断提高,伺服电机在不同领域的应用也更加的广泛,因此,需要对伺服电机的分类和运行工作原理予以分析,这样才能更加深入地掌握电机驱动器的各项参数及电流设置,从而满足产品生产质量需求。
一、伺服电机控制系统的要求(一)状态选择该设备有三种模式:停止、调试和处理操作。
这三种模式在实际控制过程中都是利用电气控制箱面板上的三位转换开关SA3进行选择。
SA3在不同的位置,实现的控制模式不同,当在左侧位置时处于调试模式,在中间位置时处于停止状态,在右侧位置时处于处理操作模式。
当处于停止状态时,设备无法启动;在其他两种模式中,根据相应的模式来操作运行。
(二)调试模式设备通电后,当三位转换开关SA3处于左侧位置时,设备进入离轴调试模式,电机M1、M2和M3可以分别进行调试和检查。
在具体调试过程中,可通过按下操作界面的“开始”按钮开展调试;当速度发生改变后,可以直接切换操作,如果需要改变方向,则必须先按下“停止”按钮,对具体的方向予以重新选择,然后开始调试;在处于调试变频电机M2时,通过选择或检查两个按钮来组合其三个速度段。
调试过程也是非常关键的环节。
进入加工操作模式前,需要对电机的运行方向和速度等实施合理的调整,并由专业人员检查是否存在错误的情况,最后进入到运行模式中。
(三)加工模式设备通电结束后,当SA3放置在正确位置时,设备进入耦合处理操作模式。
当SQ1检测到工作台在原来的位置(A点)时,将控制箱上的SB5启动按钮按下,则控制箱上HL5灯保持亮起,设备启动。
PLC如何控制伺服电机(伺服系统设计实例)
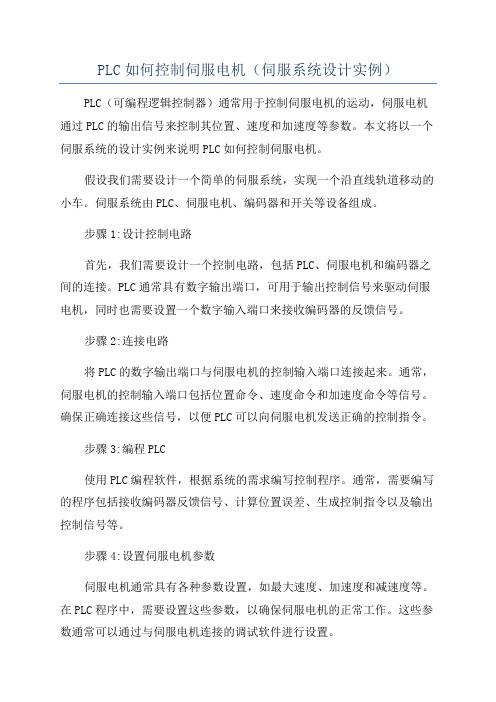
PLC如何控制伺服电机(伺服系统设计实例)PLC(可编程逻辑控制器)通常用于控制伺服电机的运动,伺服电机通过PLC的输出信号来控制其位置、速度和加速度等参数。
本文将以一个伺服系统的设计实例来说明PLC如何控制伺服电机。
假设我们需要设计一个简单的伺服系统,实现一个沿直线轨道移动的小车。
伺服系统由PLC、伺服电机、编码器和开关等设备组成。
步骤1:设计控制电路首先,我们需要设计一个控制电路,包括PLC、伺服电机和编码器之间的连接。
PLC通常具有数字输出端口,可用于输出控制信号来驱动伺服电机,同时也需要设置一个数字输入端口来接收编码器的反馈信号。
步骤2:连接电路将PLC的数字输出端口与伺服电机的控制输入端口连接起来。
通常,伺服电机的控制输入端口包括位置命令、速度命令和加速度命令等信号。
确保正确连接这些信号,以便PLC可以向伺服电机发送正确的控制指令。
步骤3:编程PLC使用PLC编程软件,根据系统的需求编写控制程序。
通常,需要编写的程序包括接收编码器反馈信号、计算位置误差、生成控制指令以及输出控制信号等。
步骤4:设置伺服电机参数伺服电机通常具有各种参数设置,如最大速度、加速度和减速度等。
在PLC程序中,需要设置这些参数,以确保伺服电机的正常工作。
这些参数通常可以通过与伺服电机连接的调试软件进行设置。
步骤5:运行系统完成PLC程序和伺服电机参数的设置后,可以通过PLC进行系统测试和调试。
运行系统并观察小车的运动是否符合设计要求。
如果需要调整运动轨迹或控制参数,可以修改PLC程序和伺服电机的参数设置。
通过以上步骤,我们可以实现一个简单的伺服系统,通过PLC控制伺服电机的运动。
当PLC接收到编码器的反馈信号时,它会计算出位置误差,并生成相应的控制信号发送给伺服电机。
伺服电机根据接收到的指令,调整自身的位置、速度和加速度等参数,实现沿直线轨道移动的小车。
需要注意的是,PLC控制伺服电机还可以实现更复杂的运动控制,如直线插补、圆弧插补等。
PLC触摸屏控制伺服电机程序实例【范本模板】

PLC触摸屏控制伺服电机程序设计摘要:以三菱公司的FX3U-48MT—ES—A作为控制元件,GT1155—QFBD—C作为操作元件直接控制三菱伺服电机的具体程序设计. 关键词:PLC;触摸屏;伺服电机伺服电机又称执行电机,它是控制电机的一种。
它是一种用电脉冲信号进行控制的,并将脉冲信号转变成相应的角位移或直线位移和角速度的执行元件.根据控制对象的不同,由伺服电机组成的伺服系统一般有三种基本控制方式,即位置控制、速度控制、力矩控制.本系统我们采用位置控制。
PLC在自动化控制领域中,应用十分广泛。
尤其是近几年PLC在处理速度,指令及容量、单轴控制方面得到飞速的发展,使得PLC在控制伺服电机方面也变得简单易行.1控制系统中元件的选型1。
1PLC的选型因为伺服电机的位移量与输入脉冲个数成正比,伺服电机的转速与脉冲频率成正比,所以我们需要对电机的脉冲个数和脉冲频率进行精确控制。
且由于伺服电机具有无累计误差、跟踪性能好的优点,伺服电机的控制主要采用开环数字控制系统,通常在使用时要搭配伺服驱动器进行控制,而伺服电机驱动器采用了大规模集成电路,具有高抗干扰性及快速的响应性。
在使用伺服驱动器时,往往需要较高频率的脉冲,所以就要求所使用的PLC能产生高频率脉冲.三菱公司的FX3U晶体管输出的PLC可以进行6点同时100 kHz高速计数及3轴独立100 kHz的定位功能,并且可以通过基本指令0.065 μs、PCMIX 值实现了以4。
5倍的高速度,完全满足了我们控制伺服电机的要求,所以我们选用FX3U-48MT—ES—A型PLC。
1。
2伺服电机的选型在选择伺服电机和驱动器时,只需要知道电机驱动负载的转距要求及安装方式即可,我们选择额定转距为2.4 N·m,额定转速为3 000 r/min,每转为131 072 p/rev分辨率的三菱公司HF—KE73W1-S100伺服电机,与之配套使用的驱动器我们选用MR—E —70A—KH003伺服驱动器。
台达PLC通讯控制伺服教程

台达PLC通讯控制伺服教程台达PLC(可编程逻辑控制器)是一种常用的自动控制设备,用于工业生产中的机器和设备控制。
PLC通讯控制伺服是一种常见的控制方案,它结合了PLC和伺服驱动器,实现对伺服系统的精确控制。
下面将从PLC 与伺服的基础知识、PLC通讯控制伺服的优势、PLC通讯控制伺服的流程等几个方面,介绍台达PLC通讯控制伺服的教程。
首先,需要了解PLC与伺服的基础知识。
PLC是一种以电子数字运算为基础,可编程存储器为控制内核,外围设有各种电气接口装置,专门用于工业自动控制的电子设备。
而伺服是一种精密的电机控制系统,通过伺服驱动器将输入指令转化为特定的电流、电压或脉冲信号,控制伺服电机转动,从而实现自动控制。
接下来,我们来介绍PLC通讯控制伺服的优势。
PLC通讯控制伺服可以实现高精度的位置、速度和力控制,对于需要精确控制的工业自动化设备非常重要。
另外,PLC具有较高的可编程性和灵活性,可以根据不同的控制需求进行编程,适用于各种复杂的控制应用。
此外,PLC还可以与其他设备进行通讯,实现数据共享和协同控制,提高生产效率和灵活性。
然后,我们来介绍PLC通讯控制伺服的流程。
首先,需要在PLC中设置与伺服驱动器的通讯参数,包括通讯协议、通讯地址等。
然后,编写PLC程序,实现对伺服驱动器的控制指令,包括位置控制、速度控制、力控制等。
在编写程序时需要考虑到伺服系统的特性和控制要求,以确保控制效果的准确和稳定。
接下来,运行PLC程序,与伺服驱动器建立通讯连接,发送控制指令,实现对伺服系统的控制。
在控制过程中,可以通过监控和调试功能对控制效果进行实时监测和调整,以达到预期的控制效果。
最后,需要注意的是,在实施PLC通讯控制伺服之前,需要充分了解伺服系统的技术规格和控制要求,选择适合的PLC和伺服驱动器,并进行相关的参数设置和通讯配置。
此外,在编写PLC程序时,需要考虑到系统的稳定性和可靠性,尽量避免因程序错误而导致设备故障或生产事故。
plc脉冲控制伺服原理

plc脉冲控制伺服原理PLC脉冲控制伺服原理伺服系统是现代工业自动化领域中广泛应用的一种控制系统。
PLC (Programmable Logic Controller)是一种可编程逻辑控制器,它通过接收输入信号、进行逻辑运算和控制输出信号,实现对各种设备和机械的控制。
PLC脉冲控制伺服原理即是指通过PLC控制发送脉冲信号,实现对伺服系统的运动控制。
在伺服系统中,PLC通过发送脉冲信号来控制伺服驱动器的运动。
脉冲信号的频率和脉宽决定了伺服电机的转速和位置。
PLC通过编程控制脉冲信号的频率和脉宽,实现对伺服电机的精确控制。
PLC脉冲控制伺服系统的原理如下:首先,PLC接收到外部输入信号,例如按钮开关、传感器信号等。
接着,PLC根据编程逻辑进行处理,判断所需的运动控制指令。
然后,PLC通过输出信号给伺服驱动器发送脉冲信号。
伺服驱动器接收到脉冲信号后,控制伺服电机按照指定的速度和位置进行运动。
PLC脉冲控制伺服系统的优点在于其灵活性和可编程性。
PLC可以根据实际应用需求进行编程,实现各种复杂的运动控制功能。
另外,PLC脉冲控制伺服系统还具有高精度、高稳定性和可靠性的特点,适用于对运动位置和速度要求较高的场合。
在实际应用中,PLC脉冲控制伺服系统广泛应用于各种自动化设备和机械,例如机床、印刷设备、包装机械等。
通过PLC脉冲控制伺服系统,可以实现对这些设备和机械的精确控制,提高生产效率和产品质量。
总结一下,PLC脉冲控制伺服原理是一种基于PLC控制发送脉冲信号来实现对伺服系统的运动控制的原理。
通过编程控制脉冲信号的频率和脉宽,可以实现对伺服电机的精确控制。
PLC脉冲控制伺服系统具有灵活性、可编程性、高精度、高稳定性和可靠性的特点,在各种自动化设备和机械中得到广泛应用。
通过PLC脉冲控制伺服系统,可以提高生产效率和产品质量,实现自动化生产。
- 1、下载文档前请自行甄别文档内容的完整性,平台不提供额外的编辑、内容补充、找答案等附加服务。
- 2、"仅部分预览"的文档,不可在线预览部分如存在完整性等问题,可反馈申请退款(可完整预览的文档不适用该条件!)。
- 3、如文档侵犯您的权益,请联系客服反馈,我们会尽快为您处理(人工客服工作时间:9:00-18:30)。
PLC编程与伺服控制系统
主要内容:
1、伺服控制系统的执行结构
2、伺服控制系统的检测单元
3、伺服控制系统
4、PLC及程序设计方法
5、PLC在伺服系统中的应用
伺服系统概念;也称随动系统,是一种能够跟踪输入的指令信号进行动作,从而获得精
确的位置、速度、及动力输出的自动控制系统,它用来控制被控对象的转角或者位移,使其自动、连续、精确地复现输入指令的变化。
伺服控制系统的组成:包括控制器,被控对象,执行环节,检测环节,比较环节等五部分。
伺服控制系统分类:
1、按照执行机构的分类
步进伺服系统即使用步进电机;直流伺服系统即直流电机;交流伺服系统即交流电机2、按照控制形式分类
开环伺服系统;半闭环控制系统;闭环系统
开环伺服系统构成框图:
半闭环控制系统构成图
闭环控制系统构成框图
3、按反馈比较方式分类
脉冲、数字比较伺服系统;相位比较伺服系统;幅值比较伺服系统;全数字伺服系统4、按控制参数分类
位置伺服系统;速度伺服系统;力矩伺服系统
伺服系统的技术要求
系统精度:伺服系统精度指的是输出量复现输入信号要求的精确程度,以误差的形式表现,可概括为动态误差,稳态误差和静态误差三个方面组成。
稳定性:伺服系统的稳定性是指当作用在系统上的干扰消失以后,系统能够恢复到原来稳定状态的能力;或者当给系统一个新的输入指令后,系统达到新的稳定运行状态的能力。
响应特性指的是输出量跟随输入指令变化的反应速度,决定了系统的工作效率.响应速度与许多因素有关,如计算机的运行速度,运动系统的阻尼和质量等。
工作频率通常是指系统允许输入信号的频率范围.当工作频率信号输入时,系统能够按技术要求正常工作;而其它频率信号输入时,系统不能正常工作。
伺服电机驱动器确定
根据伺服系统的总体控制方案及执行机构的选择来确定伺服驱动环节。
控制规律的确定
依据系统结构、控制精度、动态响应速度、超调限制等确定控制规律
其他
系统辅助元件的选取
四、PLC与伺服控制
1、PLC在伺服控制系统中的作用
1)作为主控单元与伺服单元(模块)一起完成较高精度的伺服控制。
2)完成一些低精度的直接控制
2、PLC的伺服控制功能
1)软件模块
为伺服控制应用专门设计的一些指令模块。
2)硬件模块
为伺服控制设计的一些硬件单元
3、PLC、运动控制器(卡)和数控系统
PLC:以逻辑判断,动作控制为主,对于复杂运算,尤其是曲线浮点运算能力较差。
PLC一般需要配置相应的伺服单元才可进行精确的运动伺服控制。
单独使用无伺服单元的PLC一般无法满足精度、速度等要求,一般用于精度要求不高的伺服系统
专用运动控制器(卡):专用针对运动控制的运算,更多的是在电机、转轴的运动控制上。
控制器通过通信接口与计算机一起完成伺服控制,控制卡为基于pc 的运动控制器,两者本质上没有太大的差别。
伺服控制器(卡)一般配有专门的软件用于系统配置监控。
基于pc的数控系统:结合运动控制及动作的逻辑控制,多参数的运算功能,结合了运动控制器(卡)及PLC的一些功能,成本较高。