焊接检验-PT
PT渗透检测相关标准

在所有按要求需要做的热处理工作都完成后,方可实施检测。对于有可能出现氢裂缝的敏感材料的焊缝
(例如,高强度钢)或其他有可能发生延时裂纹材料的焊缝,其检查工作的实施时间应是在焊接完成之后,
所要求的最短时段内,或由合同双方协议确定。
依照合同双方的协议条款,在最终的热处理完成之前,或经过一定的时间之后,检测可以在特殊条件下
钛对接接头
RT
(UT) 或 RT
钛 T 型接头
(UT)或 RT
UT 或(RT)
( )表示有限制的使用。
1)厚度,t,是用于要焊接的母材金属的厚度。
9.3 不完全焊透的对接和 T 型接头及角焊缝 对于部分焊透焊缝和角焊缝而言,当采用表 3 中所列的方法时,未熔的根部会妨碍实施令人满意的体积
检查。在协议中未同意采用特殊试验方法的情况下,焊接质量应以控制焊接工艺来做保证。
3.2 检测标准:用检测程度和参数设定值来选择检测方法,不同的值应对应检测装置不同灵敏度和/或不同 可能性,类似检测标准的选择是与质量要求息息相关的。
3.3 评定标准:依据检测标准,对显现的情况加以评估(见附录 B)。
3.4 记录水准:根据检测标准,对显现的情况进行记录(见附录 B)。
3.5 可接受的水准:达到检测水准的组成部分是可以接受的(见附录 B)。
在实施标准中,或在合同双方的协议中给出检查的内容。在附录 C 中给出了有关随机检测的指导。 5.3 材料 本标准适用于下列材料和其合金及其组合材料的熔焊焊缝:
○c 2009 WTI Harbin
EN473 无损检测人员培训教材
版权归哈尔滨焊接技术培训中心所有,未经许可不得翻录,翻录必究(注:教材中所列标准只适用于本次教学使用。)
3.6 检测组织:实施无损检测的内部或外部组织。
PT操作规范修

着色探伤操作规范
根据JB/T4730.5-2005的要求制定,制定本规范。
一、使用范围:
渗透检测适用于工件表面开口性缺陷的检测。
二、准备工作:
1、工件被检表面不得有影响渗透检测的铁锈、氧化皮、焊接飞溅、铁屑、毛刺等各种
防护层。
2、被检工件机加工表面粗糙度Ra≤12.5μm;被检工件非机加工表面的粗糙度克适当
放宽,但不得影响检验结果。
3、工作区域地面应干净整洁,环境温度应在10℃~50℃。
三、作业流程:
1、清洗被检工件部位表面,使表面清洁无油污。
2、检测表面干燥后喷涂着色剂,保持湿润态下渗透10-15min。
3、去除检测工件表面多余的渗透剂,并干燥。
4、在被检工件表面干燥后,用充分摇匀显像剂,喷涂于被检工件表面,显像时间不少
于7min,显像剂的施加应薄而均匀,不可再同一地方反复多次施加。
5、观察应在显像剂施加7-60min内进行,并对缺陷进行记录。
6、工件检测完毕后,应对工件进行清洗,保持工件洁净。
四、评定标准:
a焊接接头和坡口的质量分级
b其他部件的质量分级
编制:审核:批准:
时间:时间:时间:。
PT检测程序

检测对象:所有的对接焊缝及油密封焊缝渗透检测工艺基本步骤:1、表面准备和预清洗2、施加渗透剂3、多余渗透剂的去除4、干燥5、施加显像剂6、观察与评定7、后清洗及复验渗透检测的时机选择:1、机加工和热处理等操作,可能产生表面缺陷,渗透检测则应在这些工序后进行。
对有延迟裂纹倾向的材料,至少应在焊后24小时进行焊接接头的渗透检测。
2、表面处理工艺(喷漆、镀层、阳极化、涂层、氧化、喷丸和研磨)的操作,渗透检测应在这些工序前进行,表面处理后需机加工的,对该加工部位再次进行渗透检测。
一、表面准备和预清洗渗透检测成功与否,取决于被检表面的状况(污染程度及粗糙度)。
所有污染物都会阻碍渗透剂进入缺陷,清洗污染物的过程中的残留物反过来也能同渗透剂反应,影响渗透检测的灵敏度。
被检表面的粗糙度影响渗透检测效果。
内容:清理固体污染物+液体污染物固体污染物:铁锈、氧化皮、腐蚀产物、焊接飞溅、焊渣、毛刺、油漆及涂层等液体污染物:防锈油、机油、润滑油及有机组分的其它液体,强酸强碱及包括卤素在内的有化学活性的残留物基本要求:1、任何可影响渗透检测的污染物必须清除干净,不得损伤受检工件的工作功能:例如:不得用钢丝刷打磨铝、镁、钛等软合金。
密封面不得进行酸蚀处理等。
2、表面准备和预清洗范围:检测部位四周25mm。
▲ 通常情况下,焊缝、轧制件、铸件、锻件的表面状态,是可以满足渗透检验要求的。
▲ 如果焊缝、轧制件、铸件、锻件的表面出现不规则,影响渗透探伤效果。
则应用打磨方法或机械加工方法进行表面处理。
▲ 如果铁锈、型砂、积炭等物,可能遮盖拒收缺陷迹痕,或对检验效果产生干扰。
则应用打磨方法或机械加工方法进行表面处理。
▲打磨方法或机械加工方法可能堵塞表面缺陷的开口,降低渗透探伤效果;因此,打磨、机械加工后,应进行酸蚀处理。
▲喷丸后,也应进行酸蚀处理。
注意事项:防止表面准备和清洗不当,造成缺陷的堵塞。
在化学清洗或溶剂清洗时,不应浸、刷,杜绝压力水喷,易造成缺陷的浸润堵塞,残留的液体都会阻碍渗透剂的渗入。
焊接质量检验
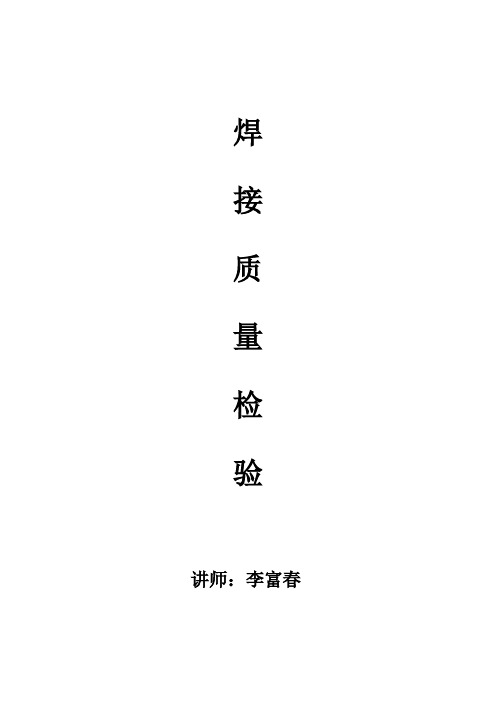
焊接质量检验讲师:李富春焊接质量检验焊接质量检验是保证焊接产品质量优良、防止废品出厂的重耍措施。
通过检验可以发现制造过程中发生的质量问题,找出原因,消除缺陷,使新产品或新工艺得到应用,质量得到保证;在正常生产中,通过完善的质量检验制度,可以及时消除生产过程中的缺陷,防止类似的缺陷重复出现,减少返修次数,节约工时、材料,从而降低成本。
所以说焊接质量检验是焊接生产必不可少的重要工序.7.1 焊接接头质量检验的内容和方法焊接质量检验贯穿整个焊接过程,包括焊前、焊接过程中和焊后成品检验三个阶段。
7.1。
1 焊接质量检验的内容和要求(1)焊前检验焊前检验是指焊件投产前应进行的检验工作,是焊接检验的第一阶段,其目的是预先防止和减少焊接时产生缺陷的可能性。
包括的项目有:①检验焊接基本金属、焊丝、焊条的型号和材质是否符合设计或规定的要求;②检验其他焊接材料,如埋弧自动焊剂的牌号、气体保护焊保护气体的纯度和配比等是否符合工艺规程的要求③对焊接工艺措施进行检验,以保证焊接能顺利进行;④检验焊接坡口的加工质量和焊接接头的装配质量是否符合图样要求;⑤检验焊接设备及其辅助工具是否完好,接线和管道联接是否合乎要求;⑥检验焊接材料是否按照工艺要求进行去锈、烘干、预热等;⑦对焊工操作技术水平进行鉴定;⑧检验焊接产品图样和焊接工艺规程等技术文件是否齐备。
(2)焊接生产过程中的检验焊接过程中的检验是焊接检验的第二阶段,由焊工在操作过程中,其目的是为了防止由于操作原因或其他特殊因索的影响而产生的焊接缺陷,便于及时发现问题并加以解决。
包括:①检验在焊接过程中焊接设备的运行情况是否正常;②对焊接工艺规程和规范规定的执行情况;③焊接夹具在焊接过程中的夹紧情况是否牢固;④操作过程中可能出现的未焊透、夹渣、气孔、烧穿等焊接缺陷等;⑤焊接接头质量的中间检验,如厚壁焊件的中间检验等。
焊前检验和焊接过程中检验,是防止产生缺陷、避免返修的重要环节.尽管多数焊接缺陷可以通过返修来消除,但返修要消耗材料、能源、工时、增加产品成本。
7.15 激光焊缝缺陷的PT检测讲解

9/30/2018
2.4
渗透检测特点
(或材料的表面开口缺陷,不受
零件化学成分、结构和形状限制。可以检测磁性和非磁性材料,可以检 测焊接件,铸件,锻件和机加工件,只需要一次探伤,即可把零件表面
各个方向及形状的缺陷全部检查出来。
(2)缺点 渗透探伤不适用于检测表面是吸收性的零件或材料,例如 粉末冶金
(1)表面准备和预清洗:确定检测范围并清洗表面油污等; (2) 施加渗透剂:应根据零件大小、形状、数量和检查部位来选择。所选方 法应保证被检部位完全被渗透液覆盖,并在整个渗透时间内保持润湿。渗透时 间一般不少于10min,温度控制在15~50°C。 (3) 去除多余的渗透液:要求从零件表面去除所有的渗透液,又不将渗入缺 陷中的渗透液清洗出来。
9/30/2018
图1 渗透检测焊缝缺陷原理示意图
9/30/2018
2.2
渗透检测分类
(1)根据染料分类: 荧光法、着色法和荧光着色法;
(2)根据去除方式分类: 水洗型、后乳化型和溶剂去除型; (3)根据显象方式分类: 干式、湿式和自显象;
9/30/2018
2.3
渗透检测方法
渗透检测工艺
基本步骤:表面准备和预清洗、渗透、去除、干燥、显象、观察(检验) 。
9/30/2018
(4) 干燥:溶剂去除法渗透探伤时,不必进行专门的干燥处理,应自 然干燥,不得加热干燥。用水清洗的零件,采用干式或非水基湿式显象 时,零件在显象前必须进行干燥处理; (5) 显象:显象的过程是用显象剂将缺陷处的渗透液吸附到零件表面, 产生清晰可见的缺陷图像。一般规定:显象时间一般不少于7min,显象 剂厚度为0.05-0.07mm。 (6) 观察和评定:着色观察和荧光观察时对灯光线有不同要求。
焊缝PT报告(双语版)
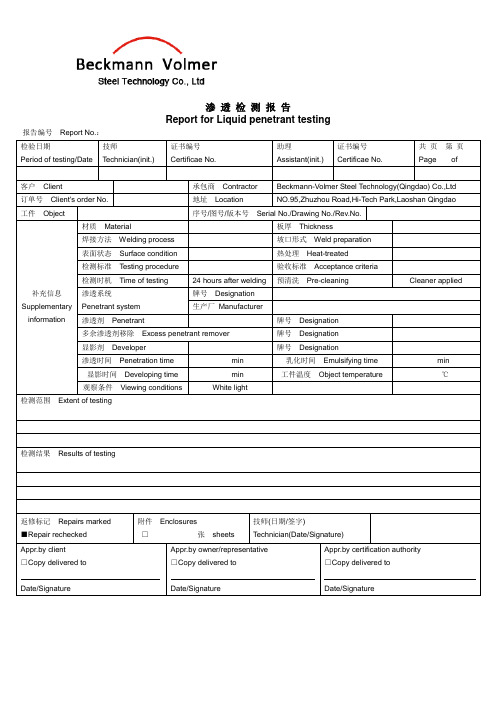
渗透检测报告Report for Liquid penetrant testing 报告编号Report No.:检验日期Period of testing/Date 技师Technician(init.)证书编号Certificae No.助理Assistant(init.)证书编号Certificae No.共页第页Page of客户Client 承包商Contractor Beckmann-Volmer Steel Technology(Qingdao) Co.,Ltd 订单号Client's order No. 地址Location NO.95,Zhuzhou Road,Hi-Tech Park,Laoshan Qingdao 工件Object 序号/图号/版本号Serial No./Drawing No./Rev.No.补充信息Supplementary information 材质Material 板厚Thickness焊接方法Welding process 坡口形式Weld preparation表面状态Surface condition 热处理Heat-treated检测标准Testing procedure 验收标准Acceptance criteria检测时机Time of testing 24 hours after welding 预清洗Pre-cleaning Cleaner applied 渗透系统Penetrant system牌号Designation生产厂Manufacturer渗透剂Penetrant 牌号Designation多余渗透剂移除Excess penetrant remover 牌号Designation显影剂Developer 牌号Designation渗透时间Penetration time min 乳化时间Emulsifying time min显影时间Developing time min 工件温度Object temperature ℃观察条件Viewing conditions White light检测范围Extent of testing 检测结果Results of testing返修标记Repairs marked ■Repair rechecked 附件Enclosures□张sheets技师(日期/签字)Technician(Date/Signature)Appr.by client□Copy delivered to Date/Signature Appr.by owner/representative□Copy delivered toDate/SignatureAppr.by certification authority□Copy delivered toDate/Signature附:焊缝位置示意图Enclosure:Position of welds。
PT检测规程
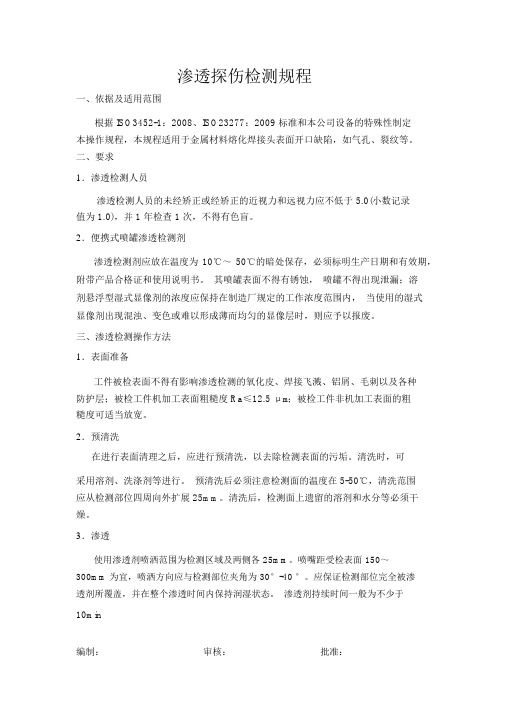
渗透探伤检测规程一、依据及适用范围根据 ISO3452-1:2008、ISO23277:2009 标准和本公司设备的特殊性制定本操作规程,本规程适用于金属材料熔化焊接头表面开口缺陷,如气孔、裂纹等。
二、要求1.渗透检测人员渗透检测人员的未经矫正或经矫正的近视力和远视力应不低于 5.0(小数记录值为 1.0),并 1 年检查 1 次,不得有色盲。
2.便携式喷罐渗透检测剂渗透检测剂应放在温度为10℃~50℃的暗处保存,必须标明生产日期和有效期,附带产品合格证和使用说明书。
其喷罐表面不得有锈蚀,喷罐不得出现泄漏;溶剂悬浮型湿式显像剂的浓度应保持在制造厂规定的工作浓度范围内,当使用的湿式显像剂出现混浊、变色或难以形成薄而均匀的显像层时,则应予以报废。
三、渗透检测操作方法1.表面准备工件被检表面不得有影响渗透检测的氧化皮、焊接飞溅、铝屑、毛刺以及各种防护层;被检工件机加工表面粗糙度 Ra≤12.5 μm;被检工件非机加工表面的粗糙度可适当放宽。
2.预清洗在进行表面清理之后,应进行预清洗,以去除检测表面的污垢。
清洗时,可采用溶剂、洗涤剂等进行。
预清洗后必须注意检测面的温度在 5-50℃,清洗范围应从检测部位四周向外扩展 25mm。
清洗后,检测面上遗留的溶剂和水分等必须干燥。
3.渗透使用渗透剂喷洒范围为检测区域及两侧各 25mm。
喷嘴距受检表面 150~300mm 为宜,喷洒方向应与检测部位夹角为 30°-40 °。
应保证检测部位完全被渗透剂所覆盖,并在整个渗透时间内保持润湿状态。
渗透剂持续时间一般为不少于10min4.中间清洗和干燥一般应先用干燥、洁净不脱毛的布依次擦拭,直至大部分多余渗透剂被去除后,再用蘸有清洗剂的干净不脱毛布或纸进行擦拭,直至全部擦净。
但应注意,不得往复擦拭,不得用清洗剂直接在被检面上冲洗。
5.显像使用溶剂悬浮显像剂喷涂,被检面在室温下自然干燥处理后,喷洒前必须摇动喷罐中的珠子,使显像剂均匀。
无损检测RT、UT、MT、PT

RT(Radiographic testing射线检测)、UT(Ultrasonic testing 超声波检测)、MT(Magnetic particle testing 磁粉检测)、PT(Penetrant flaw testing渗透检测)四种常规无损检测方法过去用切开、剖开、打磨等方法检测,叫做有损探伤,对工件有破坏,不能再用。
现在用无损方法检测,不影响工件使用。
检测没有所谓先后,它是随着加工工序进行的。
没有理由飞机制造完成后做探伤,那不经检测就可以告诉你不合格!就是说,每个过程都要有检测。
注意:检测不可能是逐个进行,那样成本太高,也不现实(时间要求、费用要求、人力要求、检测设备数量、作业空间都有限制)。
大规模生产时,零部件是采取抽检方式进行的,有专用的是科学方法。
不过,关键件、重要件要逐个检查,例如“神七”全部部件。
一般检测的金属工件分为:铸造锻压件、机加工件、钣金件、焊接件等。
这四种方法(严格讲是五种,还有声发射ET)中最常用的是UT和PT,原因是比较方便,但只适合局部检查。
全面检测最理想的设备当然是RT,但费用较高,现在已经能够在计算机屏幕上可视进行(过去只能拍摄胶片),检测结果可制成录像文件。
对于大型的铸件、锻压件只能用RT,UT超不动!当然,在流水线上作业是另外一回事,可以逐步进行、逐一检查,可以用任何可能的方式,因为摊在每个产品上的费用小到可以忽略的程度,多昂贵的装置都无所谓。
无损检测(无损探伤)nondestryctive testing(NDT)就是对焊接加工件进行非破坏性检验和测量。
1 渗透检验penetrant festing(PT)通过施加渗透剂,用洗净剂去除多余部分,如有必要,施加显像剂以得到零件上开口于表面的某些缺陷的指示。
2 磁粉检验maganetic particle testing(MT)利用漏磁和合适的检验介质发现试件表面和近表面的不连续性的无损检测方法。
焊接检验概述

焊接检验概述焊接检验是对焊接工艺的验证过程,贯穿于整个焊接生产过程中。
在不同阶段,焊接检验的目的也各不相同。
焊前检验主要是检查技术文件是否完整齐全,原材料的质量是否可靠,焊接设备和焊工的资格是否符合要求,对预防焊接缺陷的产生具有重要意义。
焊接过程中的焊接检验,主要是对焊接工艺的执行进行检查,可以防止焊接缺陷的产生,若出现焊接缺陷,也可以及时分析缺陷产生的原因,采取一定的纠错方案,保证工件在制造过程中的质量。
焊后检验是为了保证所焊接的焊缝各项性能指标完全满足工件的设计要求。
因此焊接检验是保证焊接结构获得可靠的质量的重要手段之一。
一、焊接检验的分类在特种设备制造过程中,焊接检验应根据焊接生产的特点,严格按照相关的法律、法规、设计图样、技术标准和检验文件规定的要求进行检验。
图样规定了材料、焊缝位置、坡口形状和尺寸及焊缝的检验要求。
而技术标准规定了焊缝的质量评定方法和要求。
工艺规程、质量检验计划具体规定了检验方法和检验程序,还包括检查工程中的检验记录、不良品处理单、更改通知单,如图样更改、工艺更改、材料代用、追加或改变检验要求等所使用的书面通知。
订货合同包括了用户对产品焊接质量的要求,也应作为图样和技术文件的补充规定。
常用的焊接检验方法分非破坏性检验和破坏性检验两大类。
破坏性检验包括力学性能、化学分析、金相和焊接性试验;非破坏性检验包括外观检验、无损检验、耐压试验和泄漏试验等项目,其详细分类见表6~1 o二、焊接接头的破坏性检验(一)焊接接头力学性能试验1.焊接接头拉伸试验焊接接头的拉伸试验一般都采用横向试样。
当焊缝金属的强度超过母材金属,缩颈和破坏会发生在母材金属区。
若焊缝金属强度远低于母材,塑性应变集中在焊缝内发生,在这种情况下,局部应变测得的断后伸长率将比正常标距低。
所以横向焊接接头拉伸试验只可以评定接头的抗拉强度Rm (MPa),不能评定接头的屈服强度和断后伸长率。
焊接接头的拉伸试验还可发现断口处有无气孔、裂纹、夹渣或其他焊接缺陷。
设备检测(VT、TM、MT、PT、硬度)

设备检测(VT、TM、MT、PT、硬度)作者:赣C者(qq:416978041)一、VT(目视检测)1、VT常常用于目视检查焊缝,焊缝本身有工艺评定标准,都是可以通过目测和直接测量尺寸来做初步检验,发现咬边等不合格的外观缺陷,就要先打磨或者修整,之后才做其他深入的仪器检测。
例如焊接件表面和铸件表面较多VT做的比较多,而锻件就很少,并且其检查标准是基本相符的。
2、检测步骤:用刷子除去内部的结晶(杂质)及锈迹。
仔细的观察设备内部,不能放过任何一个角落,光线不足时应使用白光手电筒照射,查看是否有裂缝,有穿孔的情况,有明显腐蚀的痕迹要用显眼的记号笔标出,并拍照记录,以便下一步做更详细的检测;换热器的管板是重点检查的区域,比较明显的穿孔,裂缝通过VT能够看出,特别是每根列管和管板之间的焊缝一般出现问题的概率大。
3、注意事项:检查过程中要仔细,避免漏掉每一个角落。
二、TM(厚度测定)1、仪器:超声波测厚仪(TT140,北京时代)测厚仪标定:按开机键(OFF/ON)后,在测厚仪的顶部的圆形标定铁块上涂上耦合剂,按下ZERO按钮,将测定探头按压在标定铁块上,显示屏上数字显示为4.0mm,标定结束。
2、注意事项:1)、若被测设备为不锈钢,则要用相应的不锈钢标定块标定;2)、耦合剂涂抹的原则是使探头与被测物之间紧密接触,不能留有空气,因为超声波不能在空气中传导,因此耦合剂的涂抹量自己把握。
3、测定方法:用砂轮机除去测定点的涂漆,使之平滑。
在测定点上涂抹耦合剂,将测厚仪(已标定)的探头按压在被测点上,若屏幕上的数值跳动,有必要稍微移动探头并将探头紧贴设备,直到屏幕左下角显“”标志并数值稳定,屏幕上显示的值即为测定值。
发现数值的问题较大应重复多次测量求均值。
4、测定点的确定:厚度的测定并不是随便在设备上找几个点测定,而是找有代表性或者是容易发生腐蚀的地方进行测定,***换热器设备一般测定的点为筒体的两端,上下封头,进出物料的法兰,都是测定这些位置的同一截面的四个方向,示意图如下:***二冷冷凝器检查规格图:测定的部位为图中的①②③④的东南西北四个方向,a、c、d上下东西(或者南北)四个方向。
RTUTMTPT无损探伤焊缝检测

RT、UT、MT、PT这四项就是国家质检总局举办特种设备无损检测人员考核的四项内容,该名词的使用就是根据使用的检测方法不同采用国际上行业通行标准简写,依次含义为:射线无损检测、超声波无损检测、磁粉无损检测、渗透无损检测;主要使用对压力容器金属材料的无损检测。
无损检测人员的级别分为:Ⅰ级(初级)、Ⅱx级(中级)、Ⅲ级(高级)。
从事特种设备无损检测工作的人员应当按本规则进行考核,取得国家质量监督检验检疫总局(以下称国家质检总局)统一颁发的证件,方可从事相应方法的特种设备无损检测工作。
无损检测人员报考申请分为取证考核(初试)申请与换证考核(复试)申请。
初试申请的人员应当同时满足以下条件: (一)年龄在18周岁以上,60周岁以下,身体健康; (二)双眼矫正视力与颜色分辨能力满足所申请无损检测工作的要求; (三)报考Ⅰ级应当具有初中(含)以上学历;报考Ⅱ级应当具有高中(含)以上学历,持无损检测专业大专(含)以上或理工科本科(含)以上学历可直接报考Ⅱ级。
无损检测初试、复试考核合格人员,将获得《特种设备检验检测人员证》,证件由国家质检总局统一制发。
证件有效期4年,实行全国统一编号。
如附件中图例。
特种设备无损检测持证人员不得同时在2个以上单位中执业,且只能从事与其证书所注明的方法与级别相适应的无损检测工作,其中: Ⅰ级人员可在Ⅱ、Ⅲ级人员指导下进行无损检测操作,记录检测数据,整理检测资料。
Ⅱ级人员可编制一般的无损检测程序,按照无损检测工艺规程或在Ⅲ级人员指导下编写工艺卡,并按无损检测工艺独立进行检测操作,评定检测结果,签发检测报告。
Ⅲ级人员可根据标准编制无损检测工艺,审核或签发检测报告,协调Ⅱ级人员对检测结论的技术争议。
过去用切开、剖开、打磨等方法检测,叫做有损探伤,对工件有破坏,不能再用。
现在用无损方法检测,不影响工件使用。
检测没有所谓先后,它就是随着加工工序进行的。
没有理由飞机制造完成后做探伤,那不经检测就可以告诉您不合格!就就是说,每个过程都要有检测。
作业指引——表面渗透检测 PT

文件名称 表面渗透检测(PT)作业指引 发布时间表面渗透检测(PT)作业指引编制人: 日期:审核人: 日期:批准人: 日期:修订记录日期修订状态修改内容修改人审核人批准人文件名称 表面渗透检测(PT)作业指引 发布时间1.质量控制流程图2.检验人员2.1.焊缝渗透检验人员必须持有中国船级社(CCS)颁发的资格证书,按有关规程的规定经过严格培训和考核,并持有相应考核组织颁发的等级资格证书,并在有效期范围内。
文件名称 表面渗透检测(PT)作业指引 发布时间2.2.焊缝渗透检验人员的视力应每年检查一次,校正视力不低于1.0,无色盲和色弱。
3.探伤液3.1.应使用同一厂家生产的同一系列配套探伤液,不允许将不同种类的探伤液混合使用。
3.2.用着色法检验后的焊缝,如果需要进行荧光检验,则必须在彻底清理之后才能进行。
3.3.为了控制渗透探伤液质量的需要,可根据ZBJ04003的规定,使用符合ZBH24002或者JB/T6064规定的铝合金试块或镀铬试块。
4.检验操作4.1.预处理4.1.1.预处理部位被检表面,它包括焊缝表面及焊缝两侧至少25mm的邻近区域表面。
4.1.2.采用机械方法(如打磨)清除被检表面的焊渣、焊接飞溅、铁锈和氧化皮;采用溶剂方法(如水或清洗剂)清洗被检表面的油脂、纤维屑等可能遮盖表面缺陷显示或干扰检验的外来物质。
不允许用喷砂喷丸等可能堵塞表面开口缺陷的清理方式。
4.1.3.当焊缝的焊波或其他表面部规则形状影响渗透检验时,应将其打磨平整。
4.1.4.清洗后的表面,依靠自然蒸发或用适当的强热风使其充分干燥。
4.2.渗透处理4.2.1.可用浸、刷、喷等任何一种方法施加渗透剂。
4.2.2.适合进行渗透处理的温度为15-50℃,渗透时间不得少于5min或使用渗透剂使用说明书中规定的渗透时间。
在渗透时间内,应保持渗透剂把被检表面全部润湿,当温度在3-15℃范围内,应根据温度情况适当增加渗透时间,低于3℃或高于50℃时,应另行考虑决定,并在检验报告中加以说明。
焊接中检验
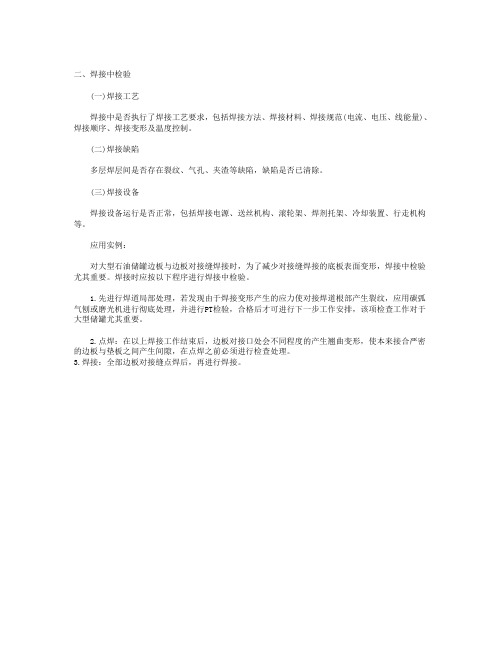
二、焊接中检验
(一)焊接工艺
焊接中是否执行了焊接工艺要求,包括焊接方法、焊接材料、焊接规范(电流、电压、线能量)、焊接顺序、焊接变形及温度控制。
(二)焊接缺陷
多层焊层间是否存在裂纹、气孔、夹渣等缺陷,缺陷是否已清除。
(三)焊接设备
焊接设备运行是否正常,包括焊接电源、送丝机构、滚轮架、焊剂托架、冷却装置、行走机构等。
应用实例:
对大型石油储罐边板与边板对接缝焊接时,为了减少对接缝焊接的底板表面变形,焊接中检验尤其重要。
焊接时应按以下程序进行焊接中检验。
1.先进行焊道局部处理,若发现由于焊接变形产生的应力使对接焊道根部产生裂纹,应用碳弧气刨或磨光机进行彻底处理,并进行PT检验,合格后才可进行下一步工作安排,该项检查工作对于大型储罐尤其重要。
2.点焊:在以上焊接工作结束后,边板对接口处会不同程度的产生翘曲变形,使本来接合严密的边板与垫板之间产生间隙,在点焊之前必须进行检查处理。
3.焊接:全部边板对接缝点焊后,再进行焊接。
无损检测报告格式(MT、PT、RT、UT)检验报告

无损检测报告格式(MT、PT、RT、U
T)查验报告
******企业
超声波探伤检测报告
产品名称:图号:
工件名称:工件编号:资
料:厚度:mm
焊缝种类:角焊缝焊接方法:融化焊
焊缝数目:2条探伤面:底板检测范围:焊缝四周200mm
查验规程:GB11345-89查收标
准:GB11345-89工艺卡编号:
仪器型号:EPOCH-Ⅲ藕合剂:(√)机油()甘油()浆糊
扫描调
理:()水平(√)深
度()声程比率:深度1:1试块:CSK-1A、RB-3
探伤面状
态:()修整(√)轧制()机加
探伤机遇:(√)焊后()热办理后()水压试验后
探伤方式:()垂直(√)斜
角()双探头面(
)串列探
头
探伤部位表示图:
一次返修二次返修说明:
焊缝编号查验长度显示状
况
缺点编号缺点编号
Ⅰ200mm ()NI
(√)RI()UI
NI:无应记录缺
点
Ⅱ1000mm()NI (√)RI()U I
()NI
()RI()UI
RI:有应记录缺
点
探伤结果
及返修情(
)NI
()RI()UI UI:有应返修缺
点
况()NI
()RI()UI
()NI
()RI()UI
查验焊缝总
长1200mm,一次返修总长0mm,
二次返修总长0mm,同一部位经0次返修后合格
附:查验及复验探伤记录页
备注:
结论: (√)合格( ) 不合格
查验: UTⅡ级审查: UTⅡ级。
RT、UT、MT、PT无损探伤焊缝检测(严选参考)

RT、UT、MT、PT这四项是国家质检总局举办特种设备无损检测人员考核的四项内容,该名词的使用是根据使用的检测方法不同采用国际上行业通行标准简写,依次含义为:射线无损检测、超声波无损检测、磁粉无损检测、渗透无损检测;主要使用对压力容器金属材料的无损检测。
无损检测人员的级别分为:Ⅰ级(初级)、Ⅱx级(中级)、Ⅲ级(高级)。
从事特种设备无损检测工作的人员应当按本规则进行考核,取得国家质量监督检验检疫总局(以下称国家质检总局)统一颁发的证件,方可从事相应方法的特种设备无损检测工作。
无损检测人员报考申请分为取证考核(初试)申请和换证考核(复试)申请。
初试申请的人员应当同时满足以下条件:(一)年龄在18周岁以上,60周岁以下,身体健康;(二)双眼矫正视力和颜色分辨能力满足所申请无损检测工作的要求;(三)报考Ⅰ级应当具有初中(含)以上学历;报考Ⅱ级应当具有高中(含)以上学历,持无损检测专业大专(含)以上或理工科本科(含)以上学历可直接报考Ⅱ级。
无损检测初试、复试考核合格人员,将获得《特种设备检验检测人员证》,证件由国家质检总局统一制发。
证件有效期4年,实行全国统一编号。
如附件中图例。
特种设备无损检测持证人员不得同时在2个以上单位中执业,且只能从事与其证书所注明的方法与级别相适应的无损检测工作,其中:Ⅰ级人员可在Ⅱ、Ⅲ级人员指导下进行无损检测操作,记录检测数据,整理检测资料。
Ⅱ级人员可编制一般的无损检测程序,按照无损检测工艺规程或在Ⅲ级人员指导下编写工艺卡,并按无损检测工艺独立进行检测操作,评定检测结果,签发检测报告。
Ⅲ级人员可根据标准编制无损检测工艺,审核或签发检测报告,协调Ⅱ级人员对检测结论的技术争议。
过去用切开、剖开、打磨等方法检测,叫做有损探伤,对工件有破坏,不能再用。
现在用无损方法检测,不影响工件使用。
检测没有所谓先后,它是随着加工工序进行的。
没有理由飞机制造完成后做探伤,那不经检测就可以告诉你不合格!就是说,每个过程都要有检测。
PT(渗透)检测作业程序

PT(渗透)检测作业程序一、表面准备1.1工件表面不得有影响渗透检测的铁锈、氧化皮、焊接飞溅、铁屑、毛刺以及各种防护层。
1.2局部检测时,准备工作范围应从检测部位四周向外扩展25mm。
二、预清洗:2.1检测部位的表面状况在很大程度上影响着渗透检测的检测质量,因此在表面清理之后,应进行预清洗,此去除检测表面的污垢。
2.2清洗时,可采用溶剂、洗涤剂等进行,清洗范围满足1.2要求。
2.3清洗后,检测面上遗留的溶剂和水分等必须干燥、且应保证在施加渗透剂前不被污染。
三、施加渗透剂:3.1施加方法应根据零件大小、形状、数量和检测部位来选择,所选方法应保证被检部位完全被渗透剂覆盖,并在整个渗透时间内保持润湿状态。
3.2施加方法:3.2.1喷涂3.2.2刷涂3.2.3浇涂3.2.4浸涂3.3渗透时间及温度3.3.1在10°C-50°C的温度条件下。
渗透剂持续时间一般不应少于10分钟。
四、去除多余的渗透剂:4.1.在清洗工件被检测表面以去除多余的渗透剂时,应注意防止过度去除而使检测质量下降,同时应注意防止去除不足而造成对缺陷显示识别困难。
4. 2溶剂去除型渗透剂,用清洗剂去除,除特别难清洗的地方外,一般应先用干燥、洁净不脱毛的布依次擦拭,直至大部分多余渗透剂被去除后,再用蘸有清洗剂的干净不脱毛布或纸进行擦拭,直至将被检面上多余的渗透剂全部擦净。
但应注意,不得往复擦拭,不得用清洗剂直接在被检面上冲洗。
五、干燥处理5.1施加干试显像剂、溶剂悬浮显像剂时,检测面应在施加前进行干燥、施加水湿式显像剂时,检测面应在施加后进行干燥处理。
5.2一般可用热风进行干燥或进行自然干燥。
5.3干燥时间通常为5-10分钟六、施加显像剂6.1悬浮式显像剂在使用前应充分搅拌均匀,显像剂施加应薄而均匀,不可在同一地点反复多次施加。
6.2喷涂显像剂时,喷嘴离被检测面距离为300mm-400mm。
喷涂方向与被检面夹角为30°-40°6.3显像时间取决于显像剂种类,需要检测的缺陷大小以及被检工件温度等,一般不 应少于7分钟。
无损检测RT、UT、MT、PT

资料收集于网络,如有侵权请联系网站删除只供学习与交流RT(Radiographic testing 射线检测)、UT (Ultrasonic testing 超声波检测)、MT (Magnetic particle testing 磁粉检测)、PT(Penetrant flaw testing 渗透检测)四种常规无损检测方法过去用切开、剖开、打磨等方法检测,叫做有损探伤,对工件有破坏,不能再用。
现在用无损方法检测,不影响工件使用。
检测没有所谓先后,它是随着加工工序进行的。
没有理由飞机制造完成后做探伤,那不经检测就可以告诉你不合格!就是说,每个过程都要有检测。
注意:检测不可能是逐个进行,那样成本太高,也不现实(时间要求、费用要求、人力要求、检测设备数量、作业空间都有限制)。
大规模生产时,零部件是采取抽检方式进行的,有专用的是科学方法。
不过,关键件、重要件要逐个检查,例如“神七”全部部件。
一般检测的金属工件分为:铸造锻压件、机加工件、钣金件、焊接件等。
这四种方法(严格讲是五种,还有声发射ET)中最常用的是UT和PT,原因是比较方便,但只适合局部检查。
全面检测最理想的设备当然是RT,但费用较高,现在已经能够在计算机屏幕上可视进行(过去只能拍摄胶片),检测结果可制成录像文件。
对于大型的铸件、锻压件只能用RT,UT 超不动!当然,在流水线上作业是另外一回事,可以逐步进行、逐一检查,可以用任何可能的方式,因为摊在每个产品上的费用小到可以忽略的程度,多昂贵的装置都无所谓。
无损检测(无损探伤)non destryctive test ing (NDT)就是对焊接加工件进行非破坏性检验和测量。
1 渗透检验penetrant festing (PT)通过施加渗透剂,用洗净剂去除多余部分,如有必要,施加显像剂以得到零件上开口于表面的某些缺陷的指示。
2 磁粉检验maganetic particle testing (MT)利用漏磁和合适的检验介质发现试件表面和近表面的不连续性的无损检测方法。
PT检测程序

检测对象:所有的对接焊缝及油密封焊缝渗透检测工艺基本步骤:1、表面准备和预清洗2、施加渗透剂3、多余渗透剂的去除4、干燥5、施加显像剂6、观察与评定7、后清洗及复验渗透检测的时机选择:1、机加工和热处理等操作,可能产生表面缺陷,渗透检测则应在这些工序后进行。
对有延迟裂纹倾向的材料,至少应在焊后24小时进行焊接接头的渗透检测。
2、表面处理工艺(喷漆、镀层、阳极化、涂层、氧化、喷丸和研磨)的操作,渗透检测应在这些工序前进行,表面处理后需机加工的,对该加工部位再次进行渗透检测。
一、表面准备和预清洗渗透检测成功与否,取决于被检表面的状况(污染程度及粗糙度)。
所有污染物都会阻碍渗透剂进入缺陷,清洗污染物的过程中的残留物反过来也能同渗透剂反应,影响渗透检测的灵敏度。
被检表面的粗糙度影响渗透检测效果。
内容:清理固体污染物+液体污染物固体污染物:铁锈、氧化皮、腐蚀产物、焊接飞溅、焊渣、毛刺、油漆及涂层等液体污染物:防锈油、机油、润滑油及有机组分的其它液体,强酸强碱及包括卤素在内的有化学活性的残留物基本要求:1、任何可影响渗透检测的污染物必须清除干净,不得损伤受检工件的工作功能:例如:不得用钢丝刷打磨铝、镁、钛等软合金。
密封面不得进行酸蚀处理等。
2、表面准备和预清洗范围:检测部位四周25mm。
▲ 通常情况下,焊缝、轧制件、铸件、锻件的表面状态,是可以满足渗透检验要求的。
▲ 如果焊缝、轧制件、铸件、锻件的表面出现不规则,影响渗透探伤效果。
则应用打磨方法或机械加工方法进行表面处理。
▲ 如果铁锈、型砂、积炭等物,可能遮盖拒收缺陷迹痕,或对检验效果产生干扰。
则应用打磨方法或机械加工方法进行表面处理。
▲打磨方法或机械加工方法可能堵塞表面缺陷的开口,降低渗透探伤效果;因此,打磨、机械加工后,应进行酸蚀处理。
▲喷丸后,也应进行酸蚀处理。
注意事项:防止表面准备和清洗不当,造成缺陷的堵塞。
在化学清洗或溶剂清洗时,不应浸、刷,杜绝压力水喷,易造成缺陷的浸润堵塞,残留的液体都会阻碍渗透剂的渗入。
- 1、下载文档前请自行甄别文档内容的完整性,平台不提供额外的编辑、内容补充、找答案等附加服务。
- 2、"仅部分预览"的文档,不可在线预览部分如存在完整性等问题,可反馈申请退款(可完整预览的文档不适用该条件!)。
- 3、如文档侵犯您的权益,请联系客服反馈,我们会尽快为您处理(人工客服工作时间:9:00-18:30)。
操作步骤
见图1‐1
润湿液体装在容器里,靠近容器壁处的液面呈凹面,不润湿液体
装容器里,零件容器壁处的液面呈凸面,容器的内径越小,这种现
象越显著。
见图2-2所示。
因为水或水溶液是特别常见的取代气体的液体,所以,
一般就把能增强水或水溶液取代固体表面空气的物质称为润湿剂。
2 润湿方程与接触角
2.4 毛细现象
2 毛细现象
(1)圆管中的毛细管现象
2.7 表面活性与表面活性剂
1 表面活性:凡能使溶剂的表面张力降低的性质。
2 表面活性剂:是这样一种物质,它在加入量很少时,
能大大将低溶剂(一般为水)表面张力或液-液界面张力,
改变体系界面状态,产生润湿、乳化、起泡及加溶等一系列作用,从而达到实际使用的要求。
在右图中,曲线1和2
为表面活性物质,曲线1
为表面活性剂,3为非
表面活性物质。
表面活性剂的种类
渗透检测常用非离子型
发光强度是指光源向某方向单位立体角发射的光通量,
光通量是指能引起眼睛视觉强度的辐射通量,单位是流明(lm)。
照度是指被照射物单位面积上所接受的光通量,单位是勒克斯
,照度是表示物体被照亮的程度。
渗透探伤时,工作场地保持一定的照度,对于确保探伤灵敏度
及提高工作效率是非常必要的。
一般要求,着色探伤时,被检物表
5 渗透探伤设备
5.1 便携式设备及压力喷罐渗透探伤剂(包括渗透液、
去除剂和显象剂),通常装
在密闭的喷罐内使用。
喷罐
一般由探伤剂的盛装容器和
探伤剂的喷射机构两部分组
成典型结构图
成。
典型结构见图10‐1。
罐内装有探伤剂和气雾剂,40°C左右可产生0.29~0.49 Mpa的压力。
显象剂喷罐内还装有玻璃
弹子,起搅拌作用。